甲烷化
甲烷化工艺
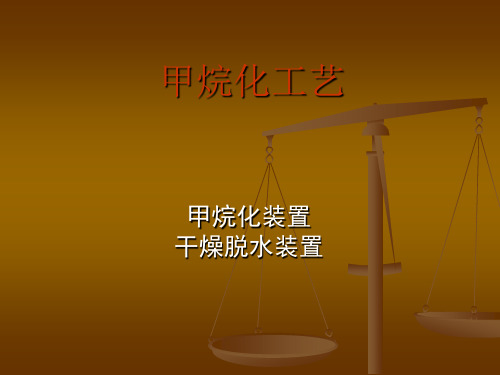
经净化后由甲烷化合成天然气的大型商业化工厂。
碎煤加压气化后净化煤气通过镍催化剂在 2.4~6MPa、300-700℃下,将H2、CO合成 天然气的技术,在美国大平原建成第一期 工程规模389万Nm3/d (相当于日产原油2 万桶)合成天然气工厂。于1980年7月破土 动工,1984年4月完工并投入试运转,1984 年7月28日生产出首批合成天然气并送入美 国的天然气管网。该厂至今还在正常运行。
b.从公用系统引出另一股净化空气经 自力式压力调节阀稳定阀后压力300kPag, 并经仪表风过滤器过滤后分配至各气动控 制仪表设备。 c. 过滤分离器、闪蒸罐均设置超压安 全泄放空系统。 d.从三甘醇再生塔塔顶排出的气体中 大部分为水蒸气,经过排出管线进入尾气 冷却器,冷取至环境温度后进入尾气焚烧 炉下部的气液分离腔,分离掉游离液体, 液体进入站内污水池后集中处理,分离出 的气体经焚烧炉燃烧后,转化成无污染环 境物质后排入大气。
此处加入高压蒸汽后温度为285℃和220℃ 的原料气汇合使得原料气被稀释,减弱放 热反应。混合后的气体温度255℃进入进入 R6002-1;R6002-1的另一股出口气和E6006 第一锅炉进料水预热器换热后温度为296℃ 和220℃的原料气汇合后温度为262℃进入 R6002-2(气体调节催化剂为GCC--2、 6×4mm、27.1m3;甲烷化催化剂为MCR、 11×5mm、17m3)主要反应为: CO+3H2=CH4+H2O CO+H2O=CO2+H4 CO2+4H2=CH4+2H2O C2H6+H2=2CH4,
2、在氨厂典型的甲烷化炉操作条件下,每 1% CO转化的绝热温升为72℃,每1% CO2转 化的绝热温升60℃,反应炉的总温升可由 下式计算: ΔT=72×[ CO]入+60×[ CO2]入 式中 ΔT--分别为进口气中CO、CO2的含 量,%(体积分数) (二)、甲烷化系统的主要设备有哪些?
(完整版)甲烷化操作规程

甲烷化操作规程甲烷化岗位作业指导书拟稿:审核:批准:公布日期:目录一、岗位任务 (2)二、工艺指标(2)三、工艺原理及流程 (2)四、主要设备 (3)五、正常开车步骤(4)六、正常停车步骤 (5)七、紧急停车步骤 (5)八、异常现象及处理方法(5)九、安全注意事项(6)一、本岗位任务甲烷化岗位的主要任务:在适当的压力、温度、催化剂的作用下把甲醇后的CO和CO2与H2合成为CH4和H2O,并把H2O分离下来,把CO+CO2含量控制在25ppm以下,送往合成岗位。
二、工艺指标(一)新鲜气温度30-40℃(二)催化剂热点温度250℃± 5 ℃(三)甲烷化塔一入温度≤130℃(四)塔壁温度≤150℃(五)甲烷化塔二入温度250℃-270℃。
(六)甲烷化塔二出温度≤190℃(七)出系统CO+CO2含量≤25PPM三、工艺原理及流程(一)工艺原理:本工段主要作用是脱除工艺气的CO和CO2。
在催化剂的作用下使少量CO、CO2加氢生成CH4和H2O,把工艺气的CO和CO2的含量脱除到25PPM 以下.由于该反应是放热反应,本工段充分利用其反应热以加热合成塔入口气体.甲烷化催化剂是以镍为活性组分,以稳定活性氧化铝为载体。
反应原理:CO+3H2= CH4+H2O +206.24kJ/molCO2+4H2= CH4+2H2O +165.4kJ/mol(二)流程:1、工艺介质主流程:从压缩机六段来的氢氮气进油分离器,油水分离后气体进入预热器与合成塔出口气体进行热量交换,加热后经合成塔环隙进塔底换热器与出口气体进一步换热,然后出合成塔进加热器,经蒸汽加热后再经合成塔心管到内件顶部进触媒层进行反应。
出口气体经塔底换热器换热后进预热器管内继续换热,然后进水冷排冷却,再进水分离器分离水后送合成。
注:(1)入工段阀门处增设旁路,主要目的是开停车时使用老系统的精练气。
(2)系统入口阀门前接循环机来气管线;增设放空管线。
(3)去合成阀门前增设去甲醇管线,为甲醇开车使用。
甲烷化技术
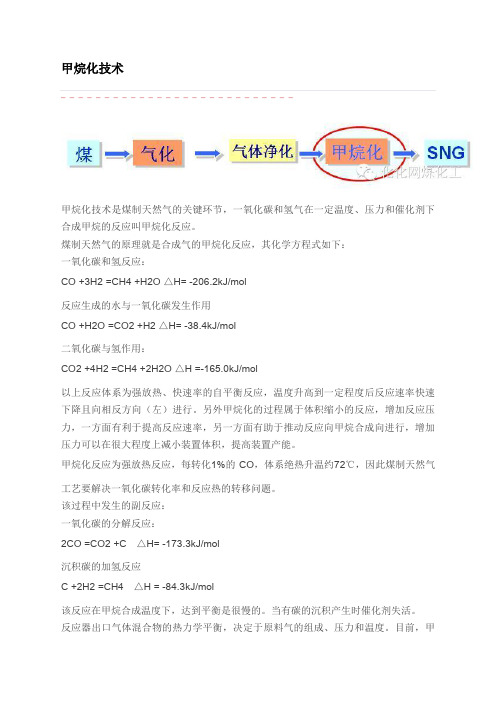
甲烷化技术¯ ¯ ¯ ¯ ¯ ¯ ¯ ¯ ¯ ¯ ¯ ¯ ¯ ¯ ¯ ¯ ¯ ¯ ¯ ¯ ¯ ¯ ¯ ¯ ¯ ¯ ¯甲烷化技术是煤制天然气的关键环节,一氧化碳和氢气在一定温度、压力和催化剂下合成甲烷的反应叫甲烷化反应。
煤制天然气的原理就是合成气的甲烷化反应,其化学方程式如下:一氧化碳和氢反应:CO +3H2 =CH4 +H2O △H= -206.2kJ/mol反应生成的水与一氧化碳发生作用CO +H2O =CO2 +H2 △H= -38.4kJ/mol二氧化碳与氢作用:CO2 +4H2 =CH4 +2H2O △H =-165.0kJ/mol以上反应体系为强放热、快速率的自平衡反应,温度升高到一定程度后反应速率快速下降且向相反方向(左)进行。
另外甲烷化的过程属于体积缩小的反应,增加反应压力,一方面有利于提高反应速率,另一方面有助于推动反应向甲烷合成向进行,增加压力可以在很大程度上减小装置体积,提高装置产能。
甲烷化反应为强放热反应,每转化1%的CO,体系绝热升温约72℃,因此煤制天然气工艺要解决一氧化碳转化率和反应热的转移问题。
该过程中发生的副反应:一氧化碳的分解反应:2CO =CO2 +C △H= -173.3kJ/mol沉积碳的加氢反应C +2H2 =CH4 △H = -84.3kJ/mol该反应在甲烷合成温度下,达到平衡是很慢的。
当有碳的沉积产生时催化剂失活。
反应器出口气体混合物的热力学平衡,决定于原料气的组成、压力和温度。
目前,甲烷化技术已经用在大规模的合成气制天然气上,最大的问题是催化剂的耐温和强放热反应器的设计制作上。
甲烷化工艺有两步法和一步法两种类型。
甲烷化法
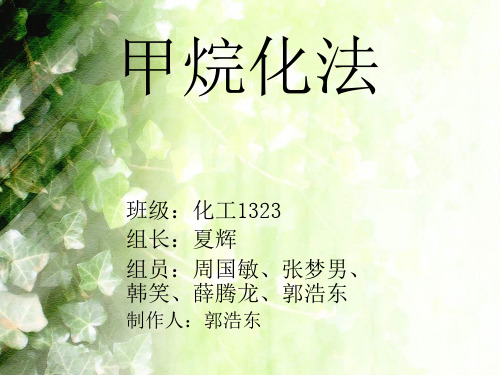
2.6粗氢中CO2杂质量 CO2 含量是造成甲烷化反应器超温的 最大潜在危害。因为正常生产中,一旦吸 收塔不正常,很容易使大量的CO2进入到 甲烷化反应器内,每增加1%的CO2,会 造成反应器床层温度升高60℃,CO2的增 加到20%的可能,这是生产中一个严重的 危害因素。
3、甲烷化催化剂
3.1甲烷化催化剂的物理性质和化学组成
(4)如果脱碳系统故障,吸收塔吸收二氧化碳吸 收不彻底,造成粗氢中二氧化碳含量一场升高,
我们就要检查脱碳系统各操作环节,脱碳溶液浓
度、、溶液循环量、溶液再生情况、吸收压力、
吸收塔温度等参数,尽快使脱碳系统恢复正常。
3.5甲烷化催化剂使用寿命 甲烷化催化剂活性较好,按照技术要求操作,脱 碳工序稳定,甲烷化入口气中H2S等毒 使用寿命的终止是由于催化剂活性的丧失或由于催化 剂强度破坏造成催化剂破碎粉化,床层阻力降明显增 大的缘故。影响甲烷化催化剂活性主要因素是由于中 毒或烧结。砷、卤素是镍催化剂的毒物,最常见的毒 物是硫。硫是一种累积性毒物,即使浓度很小但也会 使催化剂中毒,影响催化剂的使用寿命。催化剂只要 吸收了0.1-0.2%的硫即能导致活性明显地降低。
(3)在用上游来的工艺气还原时,要严格控制工 艺气中碳的氧化物含量,因为在床层温度达
250℃后还原与甲烷化反应会同时进行,因此要
特别注意防止超温。 (4)还原过程中氢耗并不明显,在床层温度达到 预定计划指标后,维持一定时间,以出口气体中 碳的氧化物符合设计指标后稳定数小时,即可认 为还原基本结束,转入正常生产。
甲烷化催化剂的硫中毒是分层进行的。起初, 入口气中H2S几乎完全被上层催化剂所吸收,引起其 活性衰退,而下层催化剂仍处于无硫气氛下。当上 层催化剂吸硫达0.2%,活性衰退大半,但这部分催
甲烷化技术综合篇
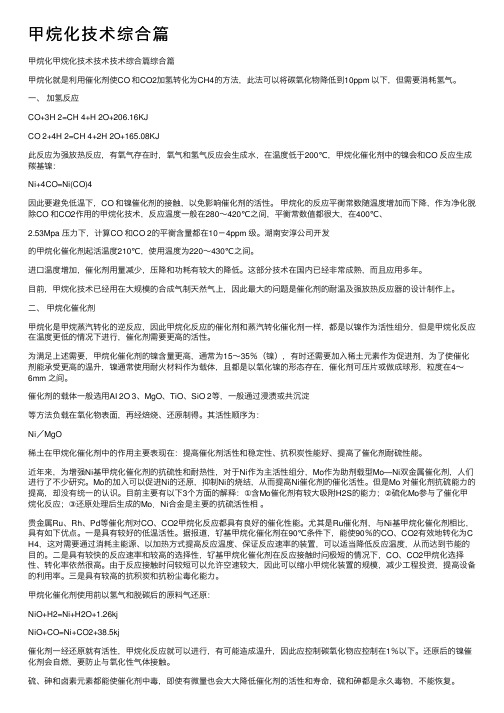
甲烷化技术综合篇甲烷化甲烷化技术技术技术综合篇综合篇甲烷化就是利⽤催化剂使CO 和CO2加氢转化为CH4的⽅法,此法可以将碳氧化物降低到10ppm 以下,但需要消耗氢⽓。
⼀、加氢反应CO+3H 2=CH 4+H 2O+206.16KJCO 2+4H 2=CH 4+2H 2O+165.08KJ此反应为强放热反应,有氧⽓存在时,氧⽓和氢⽓反应会⽣成⽔,在温度低于200℃,甲烷化催化剂中的镍会和CO 反应⽣成羰基镍:Ni+4CO=Ni(CO)4因此要避免低温下,CO 和镍催化剂的接触,以免影响催化剂的活性。
甲烷化的反应平衡常数随温度增加⽽下降,作为净化脱除CO 和CO2作⽤的甲烷化技术,反应温度⼀般在280~420℃之间,平衡常数值都很⼤,在400℃、2.53Mpa 压⼒下,计算CO 和CO 2的平衡含量都在10-4ppm 级。
湖南安淳公司开发的甲烷化催化剂起活温度210℃,使⽤温度为220~430℃之间。
进⼝温度增加,催化剂⽤量减少,压降和功耗有较⼤的降低。
这部分技术在国内已经⾮常成熟,⽽且应⽤多年。
⽬前,甲烷化技术已经⽤在⼤规模的合成⽓制天然⽓上,因此最⼤的问题是催化剂的耐温及强放热反应器的设计制作上。
⼆、甲烷化催化剂甲烷化是甲烷蒸汽转化的逆反应,因此甲烷化反应的催化剂和蒸汽转化催化剂⼀样,都是以镍作为活性组分,但是甲烷化反应在温度更低的情况下进⾏,催化剂需要更⾼的活性。
为满⾜上述需要,甲烷化催化剂的镍含量更⾼,通常为15~35%(镍),有时还需要加⼊稀⼟元素作为促进剂,为了使催化剂能承受更⾼的温升,镍通常使⽤耐⽕材料作为载体,且都是以氧化镍的形态存在,催化剂可压⽚或做成球形,粒度在4~6mm 之间。
催化剂的载体⼀般选⽤AI 2O 3、MgO、TiO、SiO 2等,⼀般通过浸渍或共沉淀等⽅法负载在氧化物表⾯,再经焙烧、还原制得。
其活性顺序为:Ni/MgO稀⼟在甲烷化催化剂中的作⽤主要表现在:提⾼催化剂活性和稳定性、抗积炭性能好、提⾼了催化剂耐硫性能。
煤制天然气甲烷化课件
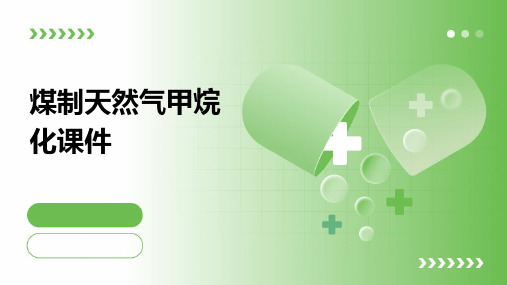
煤制天然气甲烷化技术具有高效、环保、可实现煤炭资源的 高附加值利用等优点,但也存在投资大、技术复杂等挑战。
煤制天然气甲烷化技术的历史与发展
历史
煤制天然气甲烷化技术最早起源于 20世纪初,经过多年的研究和发展 ,技术逐渐成熟。
发展
近年来,随着环境保护意识的提高和 能源结构的调整,煤制天然气甲烷化 技术得到了快速发展,成为煤炭清洁 利用的重要方向之一。
煤制天然气甲烷 化课件
目录
• 煤制天然气甲烷化技术概述 • 煤制天然气甲烷化技术原理 • 煤制天然气甲烷化技术设备 • 煤制天然气甲烷化技术经济分析 • 煤制天然气甲烷化技术安全与环
保 • 煤制天然气甲烷化技术未来发展
展望
01
煤制天然气甲烷化技术概 述
定义与特点
定义
煤制天然气甲烷化技术是一种将煤炭转化为天然气的过程, 通过一系列化学反应将煤中的碳、氢元素转化为甲烷(CH4 )。
煤制天然气甲烷化催化剂
煤制天然气甲烷化催化剂是实现 高效甲烷化的关键因素之一。
常用的催化剂有镍基催化剂、铬 基催化剂和铁基催化剂等,其中 镍基催化剂具有较高的活性和稳
定性。
催化剂的制备方法、活性组分和 载体对催化剂的性能有重要影响 ,选择合适的催化剂可以提高甲 烷化效率和降低副反应的发生。
03
煤制天然气甲烷化技术设 备
04
煤制天然气甲烷化技术经 济分析
投资成本分析
固定资产投资
包括甲烷化装置、配套设 施和辅助设备的购置、安 装费用。
流动资金投入
涉及原材料、燃料、水、 电等物资的采购和储备。
土地费用
获取项目所需土地的使用 权所需要支付的费用。
运行成本分析
01
甲烷化反应的压力

甲烷化反应的压力
将压力增加到四点五九兆帕,温度降到负八十二点六摄氏度,甲烷可液化。
甲烷是无色、无味的气体,溶解性,微溶于水,溶于醇、乙醚。
沸点为负一百六十一点五摄氏度,熔点负一百八十二点四八摄氏度。
常压下温度降到负一百六十一点五摄氏度以下,甲烷也可液化成液态。
常温下,水和甲烷的沸点大小比较为:水的沸点大于甲烷的沸点。
具体分析如下:在标准状态下甲烷是一无色无味气体,甲烷是最简单的有机物,是天然气,沼气,坑气等的主要成分,俗称瓦斯。
甲烷的物理性质为:无色、无味、熔点:-182.5℃;沸点:-161.5℃。
水,化学式为H₂O,是由氢、氧两种元素组成的无机物,无毒,可饮用。
在常温常压下为无色无味的透明液体,被称为人类生命的源泉。
水的物理性质:常温下为无色、无味无臭的液体。
在标准大气压下,纯水的沸点为100℃,凝固点为:0℃。
因此可以看出,水的沸点是100℃,甲烷的沸点是-161.5℃,所以常温下,水的沸点大于甲烷的沸点。
相关内容解释:
甲烷的化学性质:通常情况下,甲烷比较稳定,与高锰酸钾等强氧化剂不反应,与强酸、强碱也不反应。
但是在特定条件下,甲烷也会发生某些反应。
甲烷对环境的影响:甲烷也是一种温室气体以单位分子数而言,甲烷的温室效应要比二氧化碳大上25倍。
二氧化碳甲烷化反应机理

二氧化碳甲烷化反应机理
二氧化碳甲烷化反应是一种将二氧化碳和甲烷转化为甲醇的反应。
该反应机理涉及多个步骤,以下是其中一种可能的机理描述:
1. 吸附和激活步骤,首先,二氧化碳和甲烷分别吸附在催化剂表面,通常使用过渡金属催化剂如铜、镍、铁等。
吸附可以通过弱的物理吸附或化学吸附来实现。
在吸附后,二氧化碳和甲烷分子被激活,形成吸附态的中间体。
2. 表面反应步骤,在催化剂表面,吸附的二氧化碳和甲烷分子发生反应。
一种可能的反应路径是甲烷与吸附态的二氧化碳发生氢迁移,生成甲醇和一个活性的表面中间体。
3. 表面中间体转化步骤,活性的表面中间体进一步发生转化,形成甲醇。
这个过程可能涉及多个步骤,如氧化、还原、脱氢等。
具体的转化路径取决于催化剂的种类和反应条件。
4. 解吸步骤,生成的甲醇从催化剂表面解吸,释放出来。
需要注意的是,二氧化碳甲烷化反应机理是一个复杂的过程,
目前仍然存在争议和研究。
不同的催化剂、反应条件和实验方法可能导致不同的机理描述。
因此,上述机理仅代表其中一种可能的反应路径,实际情况可能会有所不同。
总结起来,二氧化碳甲烷化反应的机理涉及吸附和激活、表面反应、表面中间体转化和解吸等步骤。
具体的反应路径取决于催化剂和反应条件。
- 1、下载文档前请自行甄别文档内容的完整性,平台不提供额外的编辑、内容补充、找答案等附加服务。
- 2、"仅部分预览"的文档,不可在线预览部分如存在完整性等问题,可反馈申请退款(可完整预览的文档不适用该条件!)。
- 3、如文档侵犯您的权益,请联系客服反馈,我们会尽快为您处理(人工客服工作时间:9:00-18:30)。
目录一、岗位说明书二、生产原理三、工艺流程四、主要设备一览表(见附图)五、工艺指标六、系统开车程序七、系统停车程序八、不正常现象及处理措施九、生产正常操作方法及注意事项十、常见事故及处理措施十一、岗位存在的主要危险因素辨识十二、安全环保和职业卫生危害防护十三、附图、附表一、岗位说明书单位名称:净化车间甲烷化岗位岗位名称甲烷化所在部门直接上级定员人数工作职责负责甲烷化炉、甲烷化换热器、净化气水冷器、净化气分离器等设备的开停车和正常生产操作;管道、阀门及仪表的维护保养;负责系统的缺陷检查登记,消除及联系处理,防止系统泄漏污染环境。
做好设备检修前的工艺处理工作,检修后的试运行和验收工作,负责本岗位消防器材,防毒面具等的使用保管和更换,负责本系统安全稳定生产。
岗位任务在甲烷化触媒作用下,将碱洗气中残余的CO和CO2反应生成甲烷,使CO+CO2≤20×10-6,为合成氨提供合格的净化气。
任职要求推荐学历:高中以上学历。
专业技能要求:掌握初级计算机知识、懂化工生产原理。
经验要求:能解决处理本岗位各项事宜并具有实际工作经验。
能力要求:对生产工艺、设备故障有一定的判断解决能力。
证件要求:上岗证、安全消防证。
二、生产原理2.1 主要物料性质甲烷: 甲烷是无色、可燃和无毒的气体。
沸点为-161.49℃。
甲烷对空气的重量比是0.54,比空气约轻一半。
甲烷溶解度很少,在20℃、0.1千帕时,100单位体积的水,只能溶解3个单位体积的甲烷。
2.2 主反应原理和反应特点1甲烷化反应机理CO+3H2=CH4+H2O+206.16KJCO2+4H2=CH4+2H2O+165.08KJ甲烷化反应是可逆、放热、体积缩小的反应。
2甲烷化工艺条件的选择(1)温度:温度低对甲烷化反应平衡有利,但温度过低,CO会与镍生成羰基镍,而且催化剂达不到起活温度反应速度慢,催化剂不能充分发挥作用。
提高温度,可以加快甲烷化反应速度,但温度太高对化学平衡不利,也会使催化剂超温,活性降低。
实际生产中,温度低限应高于生成羰基镍的温度。
J105触媒的操作温度一般控制在280℃—420℃。
(2)压力:甲烷化反应是体积缩小的反应,提高压力有利于化学平衡向生成甲烷的方向移动,使反应速率加快,从而提高设备和催化剂的生产能力,实际生产中,甲烷化操作压力由合成氨总流程确定,一般为1 Mpa—3Mpa。
(3)原料气成份:甲烷化反应是强烈的放热反应,随CO和 CO2浓度的增大,甲烷化床层温度升高。
在绝热情况下,原料中每增加0.1%的CO转化为CH4原料气的温度会升高7.4℃, 原料中每增加0.1%的CO2转化成CH4原料气的温度会升高6℃左右。
原料气中CO和CO2含量高,易造成催化剂超温,同时使进入合成系统的甲烷含量增加,所以要求原料气中CO+CO2的体积分数小于0.7%(一般小于0.5%)。
原料气中水蒸气含量增加,可使甲烷化反应逆向进行,并影响催化剂的活性,所以,原料气中水蒸气含量越少越好。
3甲烷化反应的副反应(1)当燃料气中有O2存在时,有以下反应:O 2+2H2=2H2O+484KJ如果原料气中含微量的氧其温升要比CO 和CO2高得多,每1%的O2会使甲烷化炉床层温度升高165℃,所以原料气中应严格控制氧的进入,否则引起甲烷化炉严重超温导致催化剂失活(2)在某种条件下,还会有以下副反应:2CO=C+CO2Ni+4CO=Ni(CO)4(羰基镍)分解析碳反应,是一种有害的副反应,会影响催化剂的活性,在甲烷化正常操作的条件下,是不会发生的,但温度超过500℃有可能发生这种反应。
生成羰基镍的反应,也是放热和体积缩小的反应,低温、高压有利于生成羰基镍,压力在1.4MP,CO为1%的条件下生成羰基镍的最高温度为121℃,而甲烷化反应正常操作温度都在300℃以上,实际生产中不会有羰基镍生成。
但在升温、降温或事故停车时,甲烷化炉温度可能低于200℃,这时若遇到含CO的原料气就会生成羰基镍。
羰基镍不仅会造成催化剂活性组分镍的损失,而且是剧毒物质,人吸入会中毒。
主要症状为头痛,恶心呕吐,呼吸困难,甚至昏迷。
空气中允许的最高含量为0.001mg/m3,实际生产中必须采取措施加以防范。
三、工艺流程由脱碳塔顶出来的碱洗气温度≤80℃,经碱洗气分离器分离掉气体中夹带的溶液及冷凝水后,进入甲烷化换热器壳程,温度升至250℃~270℃,进入中变换热器壳程继续换热至280℃~300℃左右,然后经甲烷化炉入口温度调节阀进入在甲烷化触媒作用下转化成甲烷和水蒸汽,使出口净甲烷化炉,把残余的CO、CO2化气中CO+CO≤20×10-6,温度约300℃~320℃的净化气进入甲烷化换热器管内2与碱洗气进行换热,温度降至110℃~146℃,进入净化气水冷器冷却至40℃以下,再经净化气分离器分离掉冷凝液后,送高压机供合成使用。
四、主要设备一览表(见附图)五、工艺指标1 温度甲烷化换热器出口碱洗气 250℃~270℃甲烷化炉入口碱洗气 270℃~320℃甲烷化炉触媒层热点 280℃~420℃甲烷化换热器出口净化气≤146℃出工段净化气≤40℃2 压力入甲烷化炉碱洗气 1.50 MPa~1.55MPa出工段净化气 1.43 MPa~1.55MPa,甲烷化炉压差≤135KPa3 液位净化气分离器液位 20%~40%4 分析≤20×10-6甲烷化炉出口CO+CO2六、系统开车程序6.1 甲烷化岗位原始开车6.1.1 甲烷化岗位吹扫1 吹扫的目的意义吹扫的目的:在管道设备安装过程中,会残留灰尘、泥沙、焊渣和锈蚀物等杂物。
通过空气或蒸汽等介质,把管道设备中的这些杂物吹出。
以防在开车过程中堵塞设备、管道,卡住阀门。
确保顺利试车和长周期安全生产。
2 吹扫前的准备工作⑴所有设备、管道、阀门、盲板、仪表均安装完工,经质量验收合格,负责人签字。
⑵现场所有不用的架子,临时的梯子,均已拆除,现场清理干净。
⑶准备好吹扫用的工器具⑷所有仪表均已调试完毕,且灵敏、准确、好用。
⑸所有阀门、导淋阀、压力表阀、取样阀处于关闭状态。
⑹脱碳岗位所有设备管道吹除完毕并合格。
⑺现场需要依次拆开的法兰:①甲烷化换热器壳程进口阀前法兰;②中变换热器壳程进口阀前法兰;③拆下冷激副线上自调阀;④甲烷化炉出口阀前法兰;⑤净化气水冷器进口法兰;⑥净化气分离器进口法兰;⑦放空总管阀前法兰。
3 吹除流程:放空碱洗气分离器甲烷化换热器(管间)中变换放空放空热器(管间)甲烷化炉甲烷化换热器(管内)放空净化气水冷器净化气分离器高压机进口放空低压机进口放空4 吹扫操作方法脱碳工段吹扫合格后,断开甲烷化换热器壳程进口阀前法兰,在法兰断开处插铁皮盲板,联系调度通知低压机送空气,吹扫干净,用棉纱布擦拭拆开口,无杂物锈迹后恢复,吹扫合格后恢复。
拆下冷激副线上自调阀分别打开前后截止阀吹扫合格后,装好自调阀,关闭前后截止阀。
断开甲烷化炉出口阀前法兰,插上铁皮盲板,吹扫合格后恢复。
断开净化气分离器出口阀前法兰,插上铁皮盲板,吹扫合格后恢复。
断开放空总管阀前法兰插上铁皮盲板,吹扫合格后恢复。
吹扫时用木槌敲打焊缝。
在吹除过程中不能憋压,吹除时压力为0.3 Mpa - 0.5Mpa。
吹除完后检查导淋、排污、取样点、阀门是否堵塞,如有堵塞应立即疏通。
5吹扫注意事项⑴注意所有设备付线、冷激线和放空线的吹除;⑵控制吹扫压力不大于0.5Mpa用设备前阀门控制压力;⑶吹除过程中应关闭压力表阀、取样阀、导淋阀,所有自调阀前后截止阀,防止堵塞阀门或卡住自调阀。
⑷吹除人员应戴好防护用具及防尘口罩、眼罩。
⑸专人负责协调指挥。
6.1.2甲烷化反应触媒及填装1 组成及性能:甲烷化催化剂以NiO为主要成分、Ai2O3为载体、MgO或Cr2O3为促进剂。
为了提高催化剂的耐热性,有时还加入稀土元素作促进剂。
甲烷化催化剂含镍15%—30%,比甲烷蒸汽转化的镍含量高,这是为了提高它的低温活性。
2 还原与氧化:⑴还原:甲烷化催化剂在使用前,必须将NiO还原成金属Ni才具有催化活性。
一般用氢气或脱碳后的原料气还原,其反应如下:NiO+ H2 == Ni+ H2O+1.26 KJNiO+CO== Ni+ CO2+38.5 KJ⑵氧化:还原态的甲烷化催化剂能与氧发生剧烈的氧化反应:2Ni+O2=2NiO+484.88KJ ;Ni+H2O=NiO+H2+1.254KJ若催化剂与大量的空气接触,放出的反应热会把催化剂烧坏,因此,在长期停车时必须用预先氧化的方法使之钝化后,再与空气接触。
3 甲烷化催化剂的中毒:除羰基镍为甲烷化催化剂的毒物外,还有硫、砷和卤素也能使它中毒。
硫对催化剂的毒害时积累的,当吸附硫大于0.5%时,催化剂活性就完全丧失。
砷对催化剂的毒害更为严重,当吸附量达0.1%时催化剂活性即可丧失,因此,采用砷碱法时必须小心操作,以免把砷的溶液带入甲烷化系统。
为了保护催化剂,可在甲烷化催化剂上设置氧化锌或活性炭保护剂,为避免卤素对催化剂的毒害,在操作中应防止含氯的水或蒸汽进入甲烷化炉。
4 甲烷化炉装填情况表(J105):层数触媒型号装填高度(m)装填方数上层耐火球φ50 0.1m 0.7 m3丝网(8目两层)两层14 m2φ5×(5~6)催化剂J105 2.05m 14.5 m3丝网(8目两层)两层14 m2耐火球φ50 0.1m 0.7 m3丝网(8目两层)两层14 m2下层φ5×(5~6)催化剂J105 2.05m 14.5 m3丝网(8目两层)两层14 m2耐火球φ50 锅底铺平5 甲烷化触媒的装填方案⑴清理甲烷化炉内的杂物,检查篦子板是否结实完好。
⑵装填前先在炉内标出装填高度线,确保装填量。
装填前检查催化剂是否有粉尘及碎片,若有应用钢丝筛网筛过后填装。
⑶装填时先装下层,篦子板上先铺φ50mm耐火球一层,高度100mm,然后铺一层钢丝网,钢丝网要擦边,防止催化剂漏下,钢丝网规格为8目。
在钢丝网上装催化剂到指定高度。
⑷再装上层,篦子板上先铺φ50mm耐火球一层,高度100mm,然后铺一层钢丝网,钢丝网要擦边,防止催化剂漏下,钢丝网规格为8目。
在钢丝网上装催化剂到指定高度,再铺一层钢丝网,最后铺φ50mm耐火球一层⑸装填时应从较低的高度轻倒入,颗粒自由下落的高度不大于0.5m,装填过程催化剂应均匀分布铺开,不可集中成堆后再耙平,而导致气流分布不均匀产生偏流。
⑹催化剂装填完后将床层表面耙平,不可直接踩踏催化剂和热电偶,投料人员进入炉内应踩木板。
⑺催化剂装填应选择晴天一次性装完,防止受潮。
⑻装填工作完成后及时将炉体密封,准备试漏、置换、升温还原。
⑼装填时要有专人负责,对各种数据和参数及时测量并记录,存档备查(批量、容积、热电偶的相对位置)。