石油化工脱硫方法
液化气脱硫工艺技术分析

液化气脱硫工艺技术分析作者:才涛来源:《科学与财富》2019年第16期摘要:在液化气石油化工生产中,脱硫工艺是一项重要技术应用,对于提高液化气生产质量及降低液化气使用环境污染问题具有重要意义。
本文对液化气脱硫工艺技术进行了探讨,旨在促进液化气脱硫工艺技术的发展,降低液化气含硫量,是现实社会经济与环境保护效益的共同发展。
关键词:液化气;脱硫工艺;脱硫醇液化石油气生产在社会经济发展中有着重要作用,但其在促进经济发展的同时,也带来较为严重的空气污染问题,尤其是液化石油气中硫物质的存在,如果不加以处理对环境带来的影响是非常大的。
随着社会环保意识的不断增强,国家对液化气中含硫量也有了更高要求,在这种形势下,液化气脱硫工艺技术应用受到进一步重视,如何不断优化脱硫工艺技术以在确保液化石油气质量的基础上降低含硫量成为了社会高度关注和不断探究的一个重要课题。
一、液化气脱硫必要性分析液化石油气中含有一定量的硫化氢、硫醇、羰基硫等成分,这些成分的存在不仅给液化气加工造成影响,而且在环境污染方面危害也较大。
液化气中硫化物超标就会出现产品异味、催化剂中毒等问题,因此为确保液化气加工过程安全性及降低化工生产对环境造成的影响,加强脱硫工艺技术应用具有非常大的必要性和重要性。
二、液化气脱硫工艺技术(一)液化气脱硫化氢工艺液化石油气中硫化氢是硫存在的一种主要形式,也是液化气脱硫工艺技术应用目的的一个重要方面。
目前液化气脱硫化氢主要有干法脱硫与湿法脱硫两种工艺。
干法脱硫主要是通过利用固体吸附剂的媳妇作用来达到脱出硫化氢的目的,氧化铁、氧化锌及活性炭等是常用的固体吸附剂。
这种工艺虽然操作比较简单,但是只能应用于含有少量硫化氢气体处理中,对于硫化氢含量较大的砌体并不适用,脱硫效果也并不理想。
湿法脱硫工艺是与干法相对的一种脱硫化氢技术,主要利用液体吸收剂对液化气气中硫化氢进行洗涤脱出,包括物理吸收法、直接氧化法及胺溶剂化学吸收法,其中胺法占据主要地位。
高含硫原油的脱硫与处理技术创新

高含硫原油的脱硫与处理技术创新摘要:高含硫原油的处理一直是石油工业中的重要课题。
本论文探讨了高含硫原油的脱硫与处理技术创新,重点介绍了传统和新型脱硫技术以及处理方法,并分析了这些创新对高含硫原油加工的影响。
通过这些技术的创新,可以提高环境友好性,降低生产成本,增加产量,实现高含硫原油的可持续开发和利用。
关键词:高含硫原油、脱硫技术、处理技术1. 研究背景和意义高含硫原油在世界各地都是常见的资源,但其处理和加工面临许多挑战。
硫元素在原油中的存在会导致燃烧产生二氧化硫等有害气体,对环境造成危害。
此外,高含硫原油的处理成本较高,影响了生产的经济性。
因此,寻找创新的脱硫和处理技术对于提高高含硫原油的可持续开发和利用至关重要。
2. 高含硫原油的脱硫技术创新2.1 传统高含硫原油脱硫方法传统的高含硫原油脱硫方法包括热氧化法、洗涤法和氢气脱硫法。
其中,热氧化法是一种常见的方法,它通过将高含硫原油在高温下与氧气反应,将硫化合物氧化为二氧化硫和水。
虽然这种方法可以有效去除硫元素,但却存在着显著的能耗问题。
高温反应需要大量的热能供应,这会导致生产过程的能源消耗大幅上升,增加了生产成本。
洗涤法是另一种传统的脱硫方法,它利用洗液来吸附和去除硫化合物。
这个过程需要大量的洗液,通常是含有碱性物质的溶液,如氢氧化钠。
虽然这可以有效地去除硫元素,但废液的处理成为了一个关键问题。
含有硫的洗液必须经过处理才能安全排放或重新利用,这增加了废物处理的复杂性和成本。
氢气脱硫法是最常用的传统脱硫方法之一,它通过将高含硫原油与氢气反应,将硫化合物转化为氢硫酸盐。
然后,通过沉淀或吸附等方式将硫元素从产生的氢硫酸盐中去除。
虽然这种方法在去除硫元素方面效果良好,但它需要大量的氢气,氢气的制备和输送成本高昂,因此增加了生产的能源成本。
2.2 新型脱硫技术的原理和优势新型脱硫技术采用了不同的原理和方法,以有效去除高含硫原油中的硫元素,并具有众多优势。
低温甲醇洗脱硫脱碳的原理
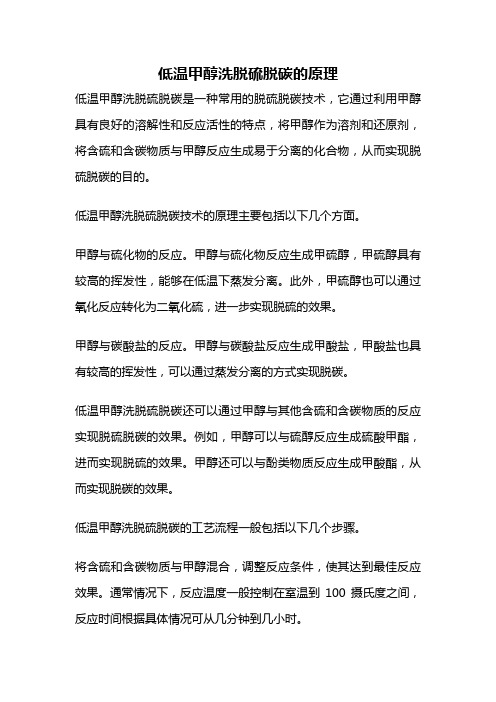
低温甲醇洗脱硫脱碳的原理低温甲醇洗脱硫脱碳是一种常用的脱硫脱碳技术,它通过利用甲醇具有良好的溶解性和反应活性的特点,将甲醇作为溶剂和还原剂,将含硫和含碳物质与甲醇反应生成易于分离的化合物,从而实现脱硫脱碳的目的。
低温甲醇洗脱硫脱碳技术的原理主要包括以下几个方面。
甲醇与硫化物的反应。
甲醇与硫化物反应生成甲硫醇,甲硫醇具有较高的挥发性,能够在低温下蒸发分离。
此外,甲硫醇也可以通过氧化反应转化为二氧化硫,进一步实现脱硫的效果。
甲醇与碳酸盐的反应。
甲醇与碳酸盐反应生成甲酸盐,甲酸盐也具有较高的挥发性,可以通过蒸发分离的方式实现脱碳。
低温甲醇洗脱硫脱碳还可以通过甲醇与其他含硫和含碳物质的反应实现脱硫脱碳的效果。
例如,甲醇可以与硫醇反应生成硫酸甲酯,进而实现脱硫的效果。
甲醇还可以与酚类物质反应生成甲酸酯,从而实现脱碳的效果。
低温甲醇洗脱硫脱碳的工艺流程一般包括以下几个步骤。
将含硫和含碳物质与甲醇混合,调整反应条件,使其达到最佳反应效果。
通常情况下,反应温度一般控制在室温到100摄氏度之间,反应时间根据具体情况可从几分钟到几小时。
将反应混合物进行分离。
由于甲硫醇、甲酸盐等产物具有较高的挥发性,可以通过蒸发分离的方式将其与甲醇分离。
同时,还可以利用溶剂萃取、析出等方法将产物与甲醇分离。
对分离后的产物进行处理。
分离后的产物通常需要进一步处理,以满足环境排放或资源回收的要求。
例如,甲硫醇可以通过氧化反应转化为二氧化硫,然后进行进一步处理或直接排放。
甲酸盐等产物也可以通过适当的处理方法,实现资源的回收利用。
低温甲醇洗脱硫脱碳技术具有操作简单、脱硫脱碳效率高、产物易于分离等优点。
同时,由于甲醇是一种廉价的溶剂和还原剂,该技术也具有经济性好的特点。
因此,低温甲醇洗脱硫脱碳技术在工业生产中得到了广泛应用,特别是在石油化工、化学制药等领域。
液化石油气脱硫工艺探讨及应用
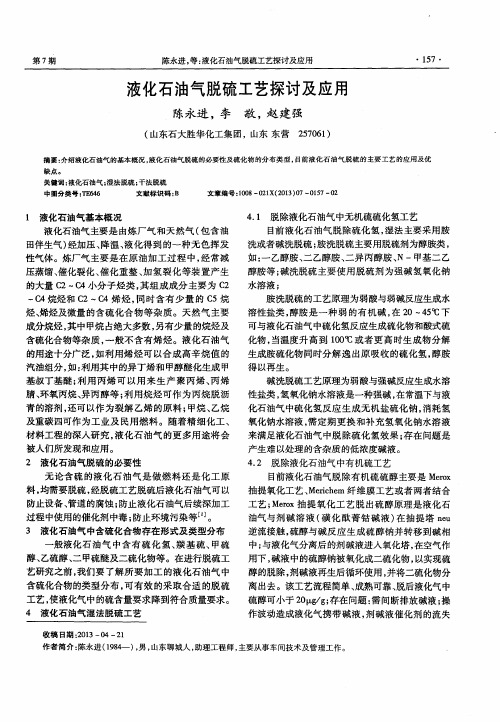
青的溶剂 , 还可以作为裂解 乙烯 的原料 ; 甲烷、 乙烷 及重碳四可作 为工业及 民用燃料 。随着精细化工、 材料工程的深入研究 , 液化石油气 的更 多用途将会 被人们所发现和应用 。
2 液化 石 油气脱 硫 的必 要性
无论含硫 的液化石油气 是做燃 料还是化工原 料, 均需要脱硫 , 经脱硫工艺脱硫后液化石油气可以 防止设备、 管道的腐蚀 ; 防止液化石油气后续深加工 过程中使用的催化剂 中毒 ; 防止环境污染等… 。
山 东 化 工 S H A N D O N G C H E M I C A L I N D U S nt Y
Zn O +H2 S— —— + Zn S+H2 O
2 0 1 3年第 4 2卷
等。
Me r i c h e m 纤维 膜 工 艺 脱 出硫 醇 原 理 为 纤 维 膜
溶性盐类 , 醇胺是一种弱 的有机碱 , 在2 O一 4 5 o 【 = 下 可与液化石油气中硫化氢反应生成硫化物和酸式硫
含硫化合物等杂质 , 一般不含有烯烃 。液化石油气 的用途十分广泛 , 如利用烯烃可 以合成高辛烷值的 汽油组分, 如: 利用其 中的异丁烯和 甲醇醚化生成 甲 基叔丁基醚 ; 利用丙烯 可 以用 来生产 聚丙烯、 丙烯
4 . 1 脱除液化石油气 中无机硫硫化氢工艺 目前 液 化 石 油 气 脱 除 硫 化 氢 , 湿法 主要 采用 胺
洗 或者 碱洗 脱硫 ; 胺 洗 脱硫 主要 用脱 硫剂 为醇胺类 , 如: 一 乙醇胺 、 二 乙醇胺 、 二异 丙 醇 胺 、 N一甲基 二 乙
田伴生气) 经加压、 降温、 液化得到的一种无 色挥 发 性气体 。炼厂气 主要是在原油加工过程 中, 经常减 压蒸馏 、 催化裂化、 催化重整 、 加氢裂化等装 置产生 的大 量 C 2一C 4小 分 子 烃 类 , 其组成成分主要为 C 2
湿法脱硫技术

湿法脱硫技术湿法脱硫技术是一种环保的烟气脱硫方法,它广泛应用于工业和电力行业,用于减少大气中的二氧化硫排放,降低空气污染。
本文将从湿法脱硫技术的原理、工艺和应用等方面进行详细介绍。
一、湿法脱硫技术的原理湿法脱硫技术是利用溶液中的碱性物质与二氧化硫发生化学反应,将二氧化硫转化为可溶于水中的硫酸盐。
主要的反应方程式为:SO2 + Ca(OH)2 → CaSO3 + H2O湿法脱硫技术有两种主要方式,分别是石灰石石膏法和海水脱硫法。
石灰石石膏法是将石灰石干燥研磨成粉末后与烟气中的二氧化硫反应,产生石膏,而海水脱硫法则是通过将海水喷洒到烟气中,利用海水中的碱性物质进行反应。
二、湿法脱硫技术的工艺湿法脱硫技术主要包括烟气净化系统和废水处理系统两部分。
烟气净化系统主要由除尘器、喷射塔和循环泵等设备组成。
烟气通过除尘器进行初步的净化,去除其中的颗粒物和粉尘。
之后,烟气进入喷射塔,喷洒石灰石水浆或海水,与二氧化硫发生反应,形成硫酸盐溶液。
最后,循环泵将硫酸盐溶液回收,净化后再次喷洒到烟气中,循环利用。
废水处理系统用于处理湿法脱硫过程中产生的废水。
废水中含有大量的硫酸盐和其他污染物,需要进行化学处理和沉淀处理,以降低污染物的浓度,使其达到排放标准。
三、湿法脱硫技术的应用湿法脱硫技术被广泛应用于工业和电力行业的烟气净化中,主要用于减少二氧化硫的排放量,保护环境。
以下是湿法脱硫技术在不同领域的应用举例:1. 电力行业:湿法脱硫技术被广泛应用于火电厂和燃煤发电厂中,用于减少烟气中的二氧化硫排放,降低大气污染。
2. 钢铁行业:湿法脱硫技术可以应用于钢铁生产中的高炉和转炉烟气脱硫,减少二氧化硫的排放,减轻对大气环境的污染。
3. 化工行业:湿法脱硫技术可以用于化工厂废气的治理,降低二氧化硫的排放,保护周边的环境质量。
4. 石油行业:湿法脱硫技术可以应用于炼油厂中,减少烟气中的硫化氢等有害气体的排放,改善工作环境。
总之,湿法脱硫技术是一种重要的烟气脱硫方法,具有广泛的应用前景。
柴油脱硫技术及其进展
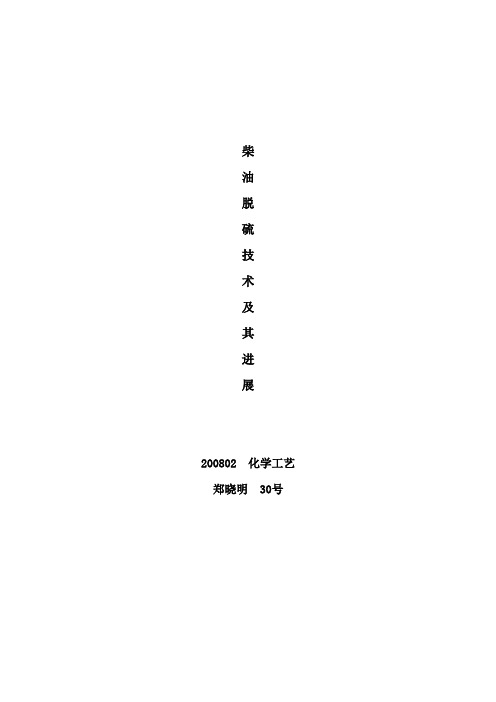
柴油脱硫技术及其进展200802 化学工艺郑晓明 30号柴油脱硫技术及其进展随着柴油发动机技术的发展,特别是电喷技术的应用,加上柴油的体积发热值大、耐用、高效、维修少等优势,柴油已广泛用作车、船及内燃机设备的燃料。
使得全球范围内的柴油总需求量越来越大,世界各国都在大力增产柴油。
我国对柴油需求增长的愿望也非常强烈。
近年来,国内市场对柴油的需求增长幅度都超过了汽油[1]。
但柴油中的硫在高温燃烧时生成硫的氧化物,不但腐蚀汽车发动机的零部件,而且是主要的汽车尾气污染物。
柴油中的硫含量直接影响到柴油车尾气中颗粒物的组成,这种颗粒物主要是碳、可溶性有机物和硫酸盐,对环境和人类健康有极大的危害。
因此降低柴油中的硫含量,生产清洁柴油,以满足日益严格的柴油标准的要求,是柴油生产企业必须关注和研究的问题。
柴油中的含硫化合物有硫醇、硫化物、噻吩、苯并噻吩和二苯并噻吩,其中噻吩占到柴油总硫的80%以上,苯并噻吩和二苯并噻吩又占噻吩类的70%以上。
活性硫(硫兀素、硫化氢、硫醇、二硫化物和多硫化物也归于此)相对容易脱除,非活性硫(硫醚、噻吩、苯并噻吩)则较难脱除;其中柴油中的4,6-二烷基二苯并噻吩,脱硫非常困难[2]。
近几年,柴油脱硫技术取得了一些新成就,出现了新的发展趋势。
本文综述了各种柴油脱硫技术及其最新研究进展。
1 柴油脱硫原理要使柴油深度脱硫,可以向两个方面发展:一方面,通过氧化将氧原子连到有机硫化物的硫原子上,增加其偶极矩,即增加硫化物在极性溶剂中的溶解度,从而将溶解在极性溶剂中的砜与不溶的有机物分开;另一方面,破坏有机硫化物的环状结构,消除其空间位阻,提高有机硫化物本身的极性或以硫化氢的形式出现,然后再通过萃取、吸附等手段,将其从柴油中脱出。
2 柴油脱硫技术2.1 加氢脱硫(HDS)技术加氢处理技术是工业上可行且已得到广泛应用的脱硫技术,是目前国内外生产清洁柴油的重要手段。
2.1.1 KF-757和KF-848加氢脱硫催化剂荷兰Akzo Nobel公司和日本Ketjen公司利用STARS(Ⅱ类超活性反应中心)技术开发出两种柴油加氢脱硫催化剂KF-757和KF-848,现已实现广泛应用。
钙基湿法脱硫测定标准_概述及解释说明

钙基湿法脱硫测定标准概述及解释说明1. 引言1.1 概述钙基湿法脱硫是一种常见的燃煤电厂烟气脱硫技术,通过将石灰石或石膏与烟气中的二氧化硫反应,形成不溶性的硫酸钙沉淀物,达到减少大气污染物排放的目的。
钙基湿法脱硫在环境保护和能源消耗方面具有重要意义,因此需要建立相应的测定标准来确保其有效性和可行性。
1.2 文章结构本文主要围绕钙基湿法脱硫测定标准展开阐述,分为引言、定义与原理、制定过程与应用范围、存在的问题及改进措施以及结论等部分。
通过对这些内容的详细解释和评估,可以更加全面地了解钙基湿法脱硫测定标准相关方面的知识。
1.3 目的本文旨在介绍钙基湿法脱硫测定标准及其重要性,并对其进行深入解析。
同时,通过对制定过程与应用范围以及存在问题及改进措施的探讨,旨在提出一些建议和改进措施以优化钙基湿法脱硫测定标准的实施效果。
最后,总结文章内容并指出后续需要进一步研究的方向,为该领域的相关研究提供参考。
2. 钙基湿法脱硫测定标准的定义与原理2.1 钙基湿法脱硫的概述钙基湿法脱硫是一种常用的烟气脱硫技术,主要用于降低燃煤电厂和工业锅炉排放的二氧化硫(SO2)含量。
它通过在烟气中喷洒含有钙质化合物(如石灰石或水合生石灰)的碱性吸收剂来捕集和吸收SO2,并形成硫酸钙(CaSO3)或石膏(CaSO4·2H2O)。
接下来,这些废物产物可以被处理或回收利用。
2.2 钙基湿法脱硫测定标准的含义及重要性钙基湿法脱硫测定标准是确定和规范钙基湿法脱硫过程中各项参数和要求的指导文件。
这些标准包括对吸收剂配比、反应温度、废物处理等方面的要求,以确保高效、可靠地从烟气中去除二氧化硫。
制定和遵守这些标准能够提高脱硫效率、降低能耗和减少对环境的不良影响。
2.3 钙基湿法脱硫测定标准的原理解释钙基湿法脱硫测定标准的原理涉及吸收剂与烟气中二氧化硫的反应,以及生成废物产物后的处理过程。
在钙基湿法脱硫过程中,钙质化合物与二氧化硫发生反应生成硫酸钙或石膏。
烟气脱硫方法介绍

2.脱硫技术脱硫技术包括:燃烧前脱硫、燃烧中脱硫和燃烧后脱硫(烟气脱硫)三种。
2.1燃烧前脱硫2.1.1机械浮洗法(MF)机械浮洗法是目前用得最多的一种燃烧前脱硫方法,它利用煤和含无机硫煤密度差异进行分离,采用跳汰机和摇床联合作业,脱硫率40%~50%,脱灰率30%~40%。
煤的浮选实际上是硫分在煤中的再分配,煤浮选后可获一半多一点的低硫煤,同时有10%的尾煤,尾煤可作为制硫酸的原料或在流化床内脱硫和燃烧。
2.1.2强磁分选(HMS)强磁分选利用无机硫顺磁性和煤反磁性来分离,用超导材料制成磁选机,在2万高斯磁场下可实现脱硫,总脱硫率可达45%。
2.1.3微波辐射法(MCD)微波辐射法是用一定波长电磁波照射经水、碱或FeCl3等盐类处理过的50~100℃煤粉,能使煤中的Fe-S,C-S化学键共振裂解,形成游离S并与H,O反应生成H2S、SO2或含氧、硫低分子气体从煤中逸出,脱硫率可达70%。
2.1.4煤的气化我国城市民用煤气,大城市用鲁奇加压气化技术;中小城市则应用水煤气两段炉气化技术(都已商品化);工业燃料气则用常压固定床发生炉煤气为主;化工原料气大厂用德士古气化技术;中小厂也以常压水煤气为主。
2.2燃烧中脱硫2.2.1型煤固硫添加固硫剂的型煤是工业锅炉实现炉内脱硫的主要方法之一。
它是向煤粉中加入粘结剂和固硫剂,然后加压成具有一定形状的块状燃料。
采用添加固硫剂的型煤燃烧后,脱硫率可达40%~60%,并可减少烟尘排放量60%,节约煤炭15%~27%。
型煤技术的攻关和研究方向一直集中在新的粘结剂和大型高压成型设备两方面。
粘结剂可分为两大类,一类是有机粘结剂,疏水性有机粘结剂,如焦油沥青、石油沥青、焦油渣,亲水性有机粘结剂则有淀粉类、纸浆废液、腐植酸盐碱液、糖醛渣液等,有机粘结剂粘结能力强,但疏水性有机粘结剂价格高,来源有限,亲水性有机粘结剂加入量大,不防水,热强度较差;另一类是无机粘结剂,常用的有石灰、不溶性水泥、粘土、水溶性水玻璃等,此类粘结剂来源广,价格便宜,有的粘结剂粘结能力强,还有固硫作用,缺点是加入量大,型煤灰分增加量多,后处理工艺复杂,多数产品不防水。
- 1、下载文档前请自行甄别文档内容的完整性,平台不提供额外的编辑、内容补充、找答案等附加服务。
- 2、"仅部分预览"的文档,不可在线预览部分如存在完整性等问题,可反馈申请退款(可完整预览的文档不适用该条件!)。
- 3、如文档侵犯您的权益,请联系客服反馈,我们会尽快为您处理(人工客服工作时间:9:00-18:30)。
石油化工脱硫方法
随着环保和市场对石化产品中硫含量要求越来越苛刻,石油化工中硫化物脱除,尤其是较难脱除的有机硫化物脱除方法已成为各石化企业和研究者关注的热点。
本文就近年来有机硫化物脱除方法的研究进展进行综述,介绍了加氢转化、生物脱除技术、超生婆脱硫、沸石脱硫、液相吸附脱硫、离子液脱硫等,展望了有机硫脱除技术发展远景。
关键词:有机硫;脱除;石油化工
随着世界范围环保要求日益严格,人们对石油产品质量要求也越来越苛刻,尤其是对燃烧后形成SO2、SO3继而与大气中水结合形成酸雾、酸雨严重影响生态环境和人们日常生活的硫化物含量限制。
世界各国对燃油中的硫提出了越来越严格的限制,以汽油为例,2005年欧美要求含硫质量分数降低到30×10-6~50×10-6,至2006年,欧洲、德国、日本、美国等国家和地区要求汽油中硫含量低于10~50µg/g,甚至提出生产含硫质量分数为5×10-6~10×10-6的“无硫汽油;”自2005年起,我国供应北京、上海的汽油招待相当于欧洲Ⅲ排放标准的汽油规格,即含硫质量分数低于150×10-6。
为了满足人们对石油产品高质量的要求和维护生产安全稳定进行,石油化工各生产企业不断改进生产过程中的脱硫工气。
石油化工生产过程中涉及到的硫化物可分为无机硫化物和有机硫化物,无机硫化物较容易脱除,本文就比较难脱除的有机硫脱除技术新进展进行综述。
1 加氢转化脱硫
天然气、液化气、炼厂气、石脑油及重油中常含有二硫化碳、硫醇、硫醚、羰基硫和噻吩等有机硫化物,热分解温度较高,且不易脱除。
加氢转化脱硫技术是最有效的脱除手段之一。
有机硫在加氢转化催化剂作用下加氢分解生成硫化氢(H2S)和相应的烷烃或芳烃,生成的H2S可由氧化锌等脱硫剂脱除达到很好的脱除效果。
近年来,国外开发出几种典型的催化裂化(FCC)汽油脱硫新工艺,如ExxonMobil公司的SCANFining工艺和OCTGAIN工艺、LFP公司的Prime-G+工艺和UOP公司的ISAL工艺;在中内,中国石化抚顺石油化工研究院(FRIPP)针对我国FCC汽油的不同特点,开发出了OCT-M、FRS和催化裂化(FCC)汽油加氢脱硫/降烯烃技术并在国内石化企业得到成功应用;还开发了FH-DS柴油深度加氢脱硫催化剂,成功应用于福建炼油化工有限公司柴油加氢装置[1,2],此外洛阳石油化工工程公司工程研究院开发出催化裂化汽油加氢脱硫及芳构化工气技术Hydro-GAP[3]。
但加氢脱硫技术存在设备投资大,操作费用高,需要大量氢等局限,对于一些没有氢气或氢气资源紧张的中小型炼油企业而言,投资成本太大,转而寻求非加氢脱硫技术。
2 生物脱硫技术
加氢脱硫法对化石燃料中含有的典型有机硫化合物—二笨并噻吩(DBT)及其衍生物无能为力。
许多研究人员认为生物脱硫技术是化石燃料精度技术的替代或补充,可以运用需氧或厌氧细菌来完成微生物脱硫工艺过程。
生物催化的操作温度比较温和,大多数条件下都可以实现,具有很高的选择性,可降低能耗,减少排放物,不产生
杂质副产物。
林军章等从土壤中分离纯化得到能高效降解二笨并噻吩的高效菌,鉴定为红球菌[4]。
在一定的发酵条件下对抚顺石油二厂重油催化裂化柴油和南油催化裂化柴油中硫的脱除率分别达到24.5%和31.19%。
国外,Ohshiro T等也从Bacillus subtilis WU-S2B的野生型及其重组菌株中分离纯化出具有脱DBT活性的酶[5]。
3 超声波脱硫
超声波脱硫即将原料和少量氧化剂、催化剂溶液混合,利用超声波辐射,抽供能量使原料中的硫化物转化成易于溶剂脱出的硫酸盐或砜。
Hirai等研究以二笨并噻吩(DBT)与甲笨的模型化物和柴油作为研究对象,研究了超声波处理过程,结果表明,从DBT到二笨并噻吩氧化物(DBTO)的反应只需要1min和3min,转化率就分别可以达到85%和95%,7min就可全部氧化[6]。
而没有超声波时,从DBT 到DBTO的转化率仅为21%,7min达到80%,明显低于超声波1min 处理的转化率,这就充分说明超声波在氧化脱硫中的作用。
Sulphcog 公司和USC公司[7]合作开发出一种以过氧化氢为氧化剂,以超声波为动力的柴油脱硫法。
将原料油与少量的氧化剂、催化剂的水溶液混合,当有超声波辐射时,在水溶液中形成200µm的小气泡,发生破裂后,形成局部可达数千度的高温和1000Mpa的高压,与此同时还发生受激活性氧和自由基使含硫化合物氧化,形成硫酸盐和砜以溶剂除掉。
该方法可将硫含量几千µg/g的油品降低到15µg/g。
国内,景晓燕等研究了超声波条件下催化氧化柴油脱硫[8]。
在超声波条件下,以H2O2/甲酸体系为氧化催化体系,N,N—二甲基甲酰
胺(DMF)为萃取剂,油剂比为1:2时,脱硫率可达88%。
4 沸石脱硫
对于氢脱硫工艺难脱除的含硫芳香族单酚和噻吩衍生物来说,一种新脱除方法是使用吸收操作,在常温常压下利用含Cu+和Ag+沸石Y从工业燃料油中有选择性地脱除硫化物。
经此处理的工业柴油总硫含量可由430×10-6降低至0.2×10-6。
脱除机理是亚铜Cu+或银阳离子Ag+通过π轨道络合有选择性地吸附噻吩物,研究表明该类物质比笨(笨是针对噻吩硫化物所使用的典型芳香族脱硫剂)对噻吩有更强的吸附力[9]。
5 液相吸附脱硫
Merox液化石油气碱法脱臭精制工艺是炼油企业普遍采用的一种脱硫方法,能使液化石油气中有机硫化物转化为二硫化物,但该工艺存在产生碱渣和恶臭且碱液消耗高,液化石油气夹带碱液,总脱破效果差等问题。
2004年4月,荆门分公司以浙江大学和宁波中一公司等单位开发设计制造的液膜脱硫塔为核心,对液化石油气碱液抽提脱硫醇系统进行了改造,同时新建了一套处理量5t/h的焦化副产液化石油气脱硫装置。
解决了脱硫效率低等难题,取得明显经济和环保效益[10]。
为了避开Merox脱硫醇方法的弊端,满足石油气硫含量限制标准的不断提高,齐鲁分公司研究院开展了催化吸附脱除液化石油气中有机硫化物的研究,研制了一种用于液相法脱除液化石油气中有机硫化物的可再生脱硫剂,并就制备条件对脱硫性能的影响,以及吸附工气
条件和再生性能进行了考察,取得很好的试验效果[11]。
6 离子液体脱硫技术
Akzo Nobel Chemical公司开发了一种柴油脱硫新技术[12]。
该技术比加氢处理方法更廉价,在室温、无氢气条件下就可以完成反应。
同时该技术能够脱除所有的芳烃和硫化物,包括加氢方法难以脱除的二甲基二笨并噻吩(DMDBT)。
该技术主要采用三种离子液体,即1-丁基-3-甲基咪唑四氟合硼酸盐(EMIM+BF3-),1-丁基-3-甲基咪唑六氟合磷酸盐(BMIM+BF6-),1-丁基-3-甲基咪唑四合硼酸盐(BMIN+BF4-),所有这些物质在常温下均为液体,升温至约300℃仍然具有热稳定性。
这些液本和柴油混合,吸收其中的含硫组分,然后与柴油分离,含硫组分可以在大约110℃用蒸馏法与离子液体分开,离子液体可以再循环使用。
在实验中发现这种技术单程脱硫率为10%~30%。
该公司又对三氯化铝离子液体进行试验,效果与前述离子液体效果相当,所需原料价格也很低。