铝合金热轧工艺
铝合金热处理
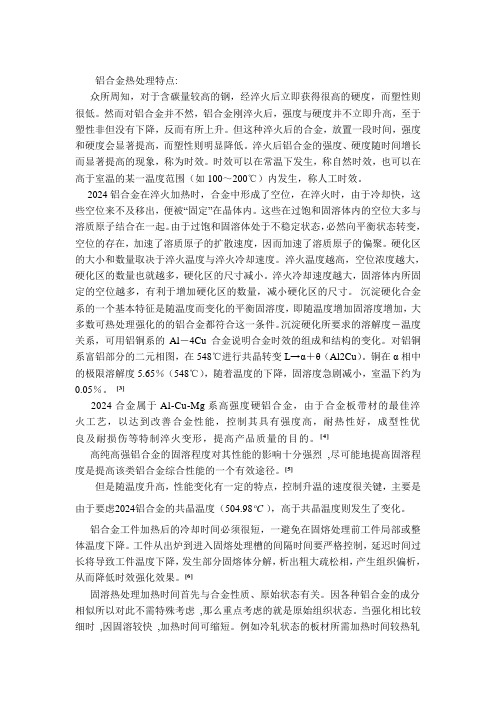
铝合金热处理特点:众所周知,对于含碳量较高的钢,经淬火后立即获得很高的硬度,而塑性则很低。
然而对铝合金并不然,铝合金刚淬火后,强度与硬度并不立即升高,至于塑性非但没有下降,反而有所上升。
但这种淬火后的合金,放置一段时间,强度和硬度会显著提高,而塑性则明显降低。
淬火后铝合金的强度、硬度随时间增长而显著提高的现象,称为时效。
时效可以在常温下发生,称自然时效,也可以在高于室温的某一温度范围(如100~200℃)内发生,称人工时效。
2024 铝合金在淬火加热时,合金中形成了空位,在淬火时,由于冷却快,这些空位来不及移出,便被“固定”在晶体内。
这些在过饱和固溶体内的空位大多与溶质原子结合在一起。
由于过饱和固溶体处于不稳定状态,必然向平衡状态转变,空位的存在,加速了溶质原子的扩散速度,因而加速了溶质原子的偏聚。
硬化区的大小和数量取决于淬火温度与淬火冷却速度。
淬火温度越高,空位浓度越大,硬化区的数量也就越多,硬化区的尺寸减小。
淬火冷却速度越大,固溶体内所固定的空位越多,有利于增加硬化区的数量,减小硬化区的尺寸。
沉淀硬化合金系的一个基本特征是随温度而变化的平衡固溶度,即随温度增加固溶度增加,大多数可热处理强化的的铝合金都符合这一条件。
沉淀硬化所要求的溶解度-温度关系,可用铝铜系的Al-4Cu合金说明合金时效的组成和结构的变化。
对铝铜系富铝部分的二元相图,在548℃进行共晶转变L→α+θ(Al2Cu)。
铜在α相中的极限溶解度5.65%(548℃),随着温度的下降,固溶度急剧减小,室温下约为0.05%。
[3]2024合金属于Al-Cu-Mg系高强度硬铝合金,由于合金板带材的最佳淬火工艺,以达到改善合金性能,控制其具有强度高,耐热性好,成型性优良及耐损伤等特制淬火变形,提高产品质量的目的。
[4]高纯高强铝合金的固溶程度对其性能的影响十分强烈,尽可能地提高固溶程度是提高该类铝合金综合性能的一个有效途径。
[5]但是随温度升高,性能变化有一定的特点,控制升温的速度很关键,主要是由于要虑2024铝合金的共晶温度(504.98C ),高于共晶温度则发生了变化。
铝合金应用手册(3篇)

第1篇第一章:概述1.1 铝合金的定义与特点铝合金是以铝为基础,加入其他元素制成的合金。
与纯铝相比,铝合金具有更高的强度、硬度和耐腐蚀性,同时保持了铝的轻质、导电、导热等优良性能。
铝合金广泛应用于航空、汽车、建筑、电子、包装等行业。
1.2 铝合金的分类铝合金按照合金元素的不同,可以分为以下几类:(1)纯铝:包括工业纯铝、半纯铝等。
(2)铝铜合金:包括铝青铜、铝黄铜等。
(3)铝镁合金:包括铝镁硅、铝镁锰等。
(4)铝硅合金:包括铝硅铜、铝硅镁等。
(5)铝锌合金:包括铝锌镁、铝锌锰等。
(6)铝锂合金:包括铝锂镁、铝锂铜等。
1.3 铝合金的应用领域铝合金因其优异的性能,广泛应用于以下领域:(1)航空航天:铝合金是航空航天工业的主要材料,用于制造飞机、火箭、卫星等。
(2)汽车制造:铝合金在汽车制造中的应用越来越广泛,如车身、发动机、悬挂系统等。
(3)建筑行业:铝合金门窗、幕墙、铝质装饰材料等在建筑行业中得到广泛应用。
(4)电子电器:铝合金在电子电器领域的应用主要体现在散热器、连接器、机壳等方面。
(5)包装行业:铝合金易加工、耐腐蚀,在包装行业得到广泛应用,如易拉罐、饮料瓶等。
第二章:铝合金加工工艺2.1 铝合金的熔炼铝合金的熔炼是生产过程中的关键环节,主要包括以下步骤:(1)准备熔炼设备:如熔炼炉、搅拌器等。
(2)准备原材料:按照配方要求,准备好铝锭、合金元素等。
(3)熔炼:将原材料放入熔炼炉,加热至熔化温度,进行搅拌、过滤等操作。
(4)合金化:在熔炼过程中,加入合金元素,调整成分。
(5)浇注:将熔化的合金倒入模具中,冷却固化。
2.2 铝合金的铸造铝合金的铸造是将熔化的合金倒入模具中,冷却固化成型的过程。
铸造方法包括:(1)砂型铸造:适用于形状复杂的零件。
(2)金属型铸造:适用于形状简单、精度要求较高的零件。
(3)压铸:适用于薄壁、复杂形状的零件。
2.3 铝合金的锻造铝合金的锻造是将加热后的合金在压力作用下,改变其形状和尺寸的过程。
铝合金线材生产工艺及车间设计
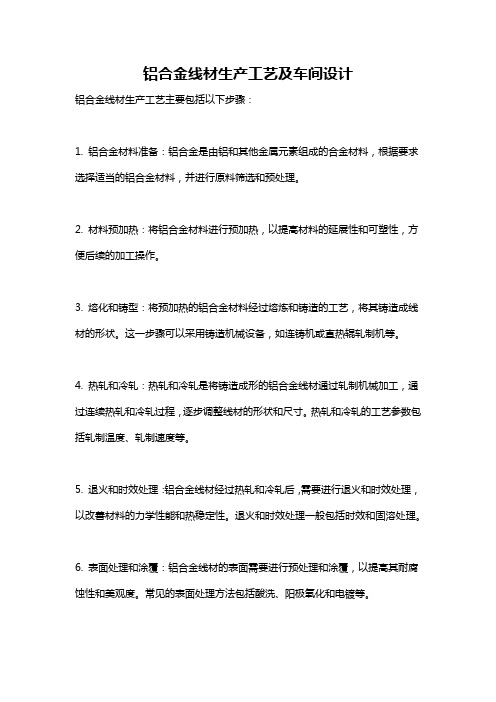
铝合金线材生产工艺及车间设计铝合金线材生产工艺主要包括以下步骤:1. 铝合金材料准备:铝合金是由铝和其他金属元素组成的合金材料,根据要求选择适当的铝合金材料,并进行原料筛选和预处理。
2. 材料预加热:将铝合金材料进行预加热,以提高材料的延展性和可塑性,方便后续的加工操作。
3. 熔化和铸型:将预加热的铝合金材料经过熔炼和铸造的工艺,将其铸造成线材的形状。
这一步骤可以采用铸造机械设备,如连铸机或直热辊轧制机等。
4. 热轧和冷轧:热轧和冷轧是将铸造成形的铝合金线材通过轧制机械加工,通过连续热轧和冷轧过程,逐步调整线材的形状和尺寸。
热轧和冷轧的工艺参数包括轧制温度、轧制速度等。
5. 退火和时效处理:铝合金线材经过热轧和冷轧后,需要进行退火和时效处理,以改善材料的力学性能和热稳定性。
退火和时效处理一般包括时效和固溶处理。
6. 表面处理和涂覆:铝合金线材的表面需要进行预处理和涂覆,以提高其耐腐蚀性和美观度。
常见的表面处理方法包括酸洗、阳极氧化和电镀等。
铝合金线材的车间设计需要考虑以下几个方面:1. 生产线布局:根据生产工艺流程,合理规划生产线的布局。
生产线之间应有足够的空间,以便设备的安装和维护。
同时,要确保生产线之间的物料和人员的流动线路畅通无阻。
2. 设备选择和摆放:根据生产工艺的要求,选择适当的设备。
设备摆放应合理,以便操作人员能够方便地进行操作和维护,同时要考虑安全和环保要求。
3. 设备安全:在生产车间中,应设置必要的安全设施,如防护网、防护栏等,以保障操作人员的安全。
此外,还需要设置紧急停机装置和灭火设备等应急设施。
4. 工艺参数控制:根据生产工艺的要求,合理设置工艺参数控制系统,以确保生产过程的稳定性和产品质量的一致性。
5. 环境管理:在车间设计中,还需要考虑环境管理,包括噪音控制、粉尘控制、废水处理等方面的工作。
总结起来,铝合金线材的生产工艺包括材料准备、熔化和铸型、热轧和冷轧、退火和时效处理、表面处理和涂覆等步骤。
铝合金热处理基本形式
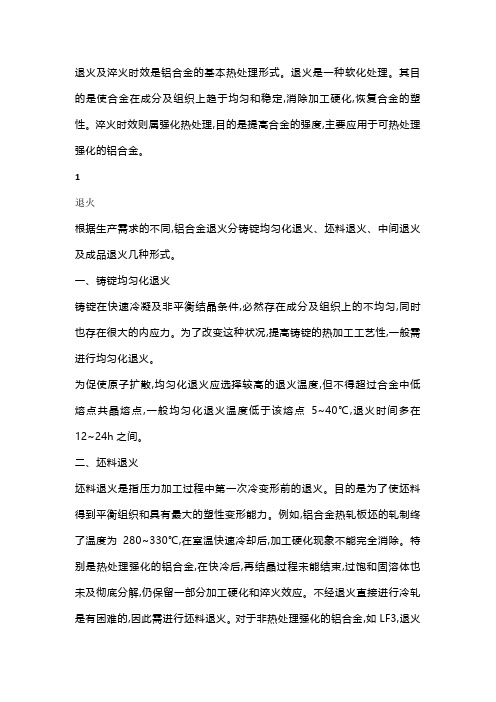
退火及淬火时效是铝合金的基本热处理形式。
退火是一种软化处理。
其目的是使合金在成分及组织上趋于均匀和稳定,消除加工硬化,恢复合金的塑性。
淬火时效则属强化热处理,目的是提高合金的强度,主要应用于可热处理强化的铝合金。
1退火根据生产需求的不同,铝合金退火分铸锭均匀化退火、坯料退火、中间退火及成品退火几种形式。
一、铸锭均匀化退火铸锭在快速冷凝及非平衡结晶条件,必然存在成分及组织上的不均匀,同时也存在很大的内应力。
为了改变这种状况,提高铸锭的热加工工艺性,一般需进行均匀化退火。
为促使原子扩散,均匀化退火应选择较高的退火温度,但不得超过合金中低熔点共晶熔点,一般均匀化退火温度低于该熔点5~40℃,退火时间多在12~24h之间。
二、坯料退火坯料退火是指压力加工过程中第一次冷变形前的退火。
目的是为了使坯料得到平衡组织和具有最大的塑性变形能力。
例如,铝合金热轧板坯的轧制终了温度为280~330℃,在室温快速冷却后,加工硬化现象不能完全消除。
特别是热处理强化的铝合金,在快冷后,再结晶过程未能结束,过饱和固溶体也未及彻底分解,仍保留一部分加工硬化和淬火效应。
不经退火直接进行冷轧是有困难的,因此需进行坯料退火。
对于非热处理强化的铝合金,如LF3,退火温度为370~470℃,保温1.5~2.5H后空冷,用于冷拉伸管加工的坯料、退火温度应适当高一些,可选上限温度。
对于可热处理强化的铝合金,如LY11及LY12,坯料退火温度为390~450℃,保温1~3H,随后在炉中以不大于30℃/h的速度冷却到270℃以下再出炉空冷。
三、中间退火中间退火是指冷变形工序之间的退火,其目的是为了消除加工硬化,以利于继续冷加工变形。
一般来说,经过坯料退火后的材料,在承受45~85%的冷变形后,如不进行中间退火而继续冷加工将会发生困难。
中间退火的工艺制度基本上与坯料退火相同。
根据对冷变形程度的要求,中间退火可分为完全退火(总变形量ε≈60~70%),简单退火(ε≤50%)和轻微退火(ε≈30~40%)三种。
热轧工艺流程范文
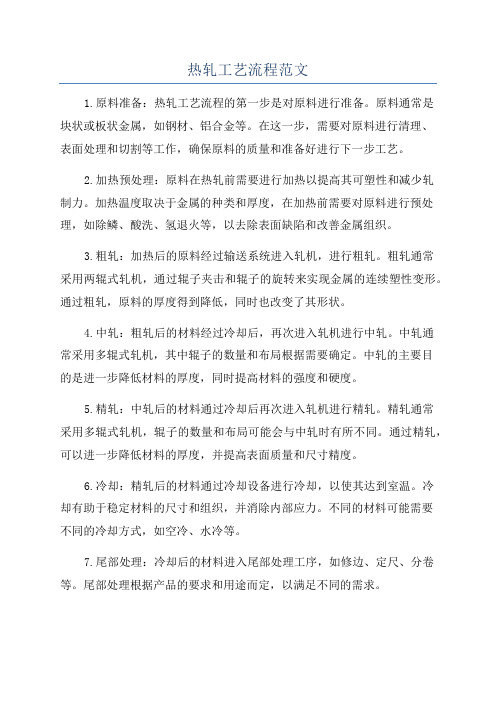
热轧工艺流程范文1.原料准备:热轧工艺流程的第一步是对原料进行准备。
原料通常是块状或板状金属,如钢材、铝合金等。
在这一步,需要对原料进行清理、表面处理和切割等工作,确保原料的质量和准备好进行下一步工艺。
2.加热预处理:原料在热轧前需要进行加热以提高其可塑性和减少轧制力。
加热温度取决于金属的种类和厚度,在加热前需要对原料进行预处理,如除鳞、酸洗、氢退火等,以去除表面缺陷和改善金属组织。
3.粗轧:加热后的原料经过输送系统进入轧机,进行粗轧。
粗轧通常采用两辊式轧机,通过辊子夹击和辊子的旋转来实现金属的连续塑性变形。
通过粗轧,原料的厚度得到降低,同时也改变了其形状。
4.中轧:粗轧后的材料经过冷却后,再次进入轧机进行中轧。
中轧通常采用多辊式轧机,其中辊子的数量和布局根据需要确定。
中轧的主要目的是进一步降低材料的厚度,同时提高材料的强度和硬度。
5.精轧:中轧后的材料通过冷却后再次进入轧机进行精轧。
精轧通常采用多辊式轧机,辊子的数量和布局可能会与中轧时有所不同。
通过精轧,可以进一步降低材料的厚度,并提高表面质量和尺寸精度。
6.冷却:精轧后的材料通过冷却设备进行冷却,以使其达到室温。
冷却有助于稳定材料的尺寸和组织,并消除内部应力。
不同的材料可能需要不同的冷却方式,如空冷、水冷等。
7.尾部处理:冷却后的材料进入尾部处理工序,如修边、定尺、分卷等。
尾部处理根据产品的要求和用途而定,以满足不同的需求。
8.质量检测和包装:完成尾部处理后,对材料进行质量检测,如尺寸测量、力学性能测试等。
通过检测,确认产品的质量是否符合要求。
最后,将产品进行包装,以便储运和使用。
总结:热轧工艺流程是一系列先进的金属加工工艺的组合,通过逐步减小金属坯料的尺寸并改变其形状,最终获得具有高强度和良好表面质量的金属制品。
同时,热轧工艺流程也需要对产品进行严格的质量控制和检测,以确保产品的质量和性能。
铝合金哈兹列特连铸连轧工艺发展

铝合金哈兹列特连铸连轧工艺发展哈兹列特连铸连轧生产线是美国哈兹列特公司开发、研制成功的。
从第一台商业化的哈兹列特铸机投入使用, 迄今为止全球已有60多台设备分别用于铜、铝、锌的带坯及条坯生产。
哈兹列特双带铸造机哈兹列特铸造机是在双辊式板带铸造机工艺进行改进的基础上发展起来的,获得专利。
这种双带式铸造机的工作原理采用运动铸模,即用两条完全张紧的上下平行运动的环形钢带和两侧同步运行的链式矩形金属挡块形成一副铸造模腔。
带坯宽度的调整是通过变动两侧挡块(活动块链)来实现的, 按照所需宽度将档块隔开构成模腔的侧壁。
冷却采用哈兹列特自身开发的专用技术―高效快速水膜冷却技术。
根据合金品种不同, 铸造速度、带坯铸模的长度也不尽相同。
现一般铸模的标准长度为1900mm, 对高速铸机铸模的长度最大可达2360mm。
现可提供的最大铸造宽度为1930mm。
铝带坯铸坯厚度一般为18~ 19mm。
哈兹列特双带铸造机主要应用自身研发的新技术包括:(1)钢带感应预加热技术。
即在铸造时为防止钢带进入模腔突然发生弯曲和热变形影响带坯的板形质量, 在钢带进入模腔前通过感应加热方式将钢带瞬时加热至150℃,同时将钢带表面的水汽驱除殆尽,避免了水汽对热传输的不良影响;(2)永磁辊式支承钢带技术。
由于钢带接触高温铝液必将产生一定的热变形。
采用Nd-Fe-B复合材料作磁体制成的支承辊有效地消除了钢带受热可能产生的微变形;(3)惰性气体保护技术。
较低压力的惰性气体从陶瓷铸嘴的小孔中喷出注入到铝水与铸模之间的表面, 不仅有效地防止了铝液(铸锭)表面的氧化, 且对热传输速度起到很好的控制作用;(4)钢带(铸模) 表面涂层技术。
采用永久性Matrix型陶瓷涂层工艺将纳米级二氧化硅材料用火焰或等离子喷涂在钢带表面。
此技术可方便脱模, 并可获得最佳的铸坯表面质量。
据报道, 哈兹列特公司为美铝( Alcoa) 公司设计制造的2500mm连铸机也已投入使用, 用于汽车蒙皮带坯的生产。
轧制生产工艺

轧制生产工艺轧制生产工艺是一种重要的金属加工方式,常用于生产钢材、铝材等材料。
本文就轧制生产工艺的原理、设备和应用进行详细介绍。
轧制生产工艺是通过将金属材料放置在轧机上,通过轧辊的压力和摩擦力对金属材料进行压制和塑性变形,使原始坯料变成所需的产品形状。
轧制生产工艺主要分为冷轧和热轧两种方式。
冷轧是在室温下进行的轧制生产工艺,适用于生产精密的薄板、带材和线材等产品。
冷轧的优点是能够获得高度的表面光洁度和尺寸精度,同时还可以提高金属材料的强度和硬度。
冷轧的设备主要包括冷轧轧机和冷轧机组,其中轧机是通过多个轧辊的转动来对金属材料进行冷轧加工。
热轧是在较高温度下进行的轧制生产工艺,适用于生产较厚的钢板、型材和大型金属材料等产品。
热轧的优点是能够减小金属材料的变形阻力,提高轧制效率和降低能耗。
热轧的设备主要包括热轧轧机和热轧机组,其中轧机通过多个辊子的旋转和轧制来对金属材料进行热轧加工。
轧制生产工艺的应用非常广泛,主要用于制造建筑材料、汽车零部件、机械设备等领域。
例如,轧制生产工艺可以将钢坯轧制成钢筋,用于建筑中的混凝土加固。
同时,轧制生产工艺还可以将铝坯轧制成铝合金板材,用于汽车制造中的车厢板和车身结构。
在轧制生产工艺中,工艺参数的控制非常重要。
例如,轧辊的加热温度、轧制速度、轧制力度等参数都会直接影响到产品的质量和性能。
因此,在实际生产中,需要严格控制这些参数,以确保产品的稳定性和一致性。
总之,轧制生产工艺是一种常用的金属加工方式,通过轧辊的压力和摩擦力对金属材料进行塑性变形,从而获得所需的产品形状。
冷轧和热轧是常用的轧制方式,应用领域广泛。
在实际生产中,需要严格控制工艺参数,以确保产品的质量和性能。
2400热轧机工艺操作规程

洛阳中色万基铝加工有限公司2400热轧机工艺操作规程JSG-R004-2005批准:审核:编制:发布:2005-7-08 实施:2005-7-082400热轧机工艺操作规程1、适用范围:本规程适用于铝及铝合金在热轧机上进行轧制。
2、生产前工作准备及有关规定:1) 开车前操作手要检查设备情况,检查方法和标准按《热轧机使用维护规程》制行。
检查设备各部件运转情况等是否正常后,通知有关人员送电。
2) 操纵手对各控制台的操作系统控制状态进行检查是否正常,应对影响板材表面质量的机列各辊道及与轧件接触的其他部分及时清理。
3) 检查合金牌号、规格是否与输入计算机的控制系统数据相吻合,有错误数据要及时修正。
4) 所有来料锭坯应符合热轧生产技术条件要求。
5) 轧制前认真检查乳液喷射系统,防止喷嘴堵塞。
6) 轧辊要预热,其方法为操作人员对轧辊进行检查后,向轧辊喷射乳液(乳液温度在50-65℃),喷液的同时轧辊要慢速转动,力求较好的热均匀性。
然后先轧制一两块纯铝,再进行铝及其合金热轧制的正常生产,以确保设备的正常运行。
7) 生产前,操作手要进行靠零操作,力求消除操作侧与传动侧的辊缝差。
8) 生产中,操作手之间要相互配合通过电视荧屏、灯光信号或音响信号密切注意监视轧制情况,若遇到异常情况时,应立即停车或采用手动干预进行处理。
9) 生产后,操作人员必须检查轧辊,并根据具体情况确定轧辊是否更换。
3、设备技术参数:1)轧制速度:260 m/min喂料(抛料)速度: ~30m/min2)轧机最大开口度: 700mm3)轧制力: 40000kN4)轧制力矩:额定静输出力矩2600KNM,最大轧制力矩为4400 KNM 5)轧辊规格:工作辊规格:Ф965 X 2600mm支承辊规格:Ф1530X2400mm6)工作辊正负弯辊力: 2000 kN7)卷取张力: 25--250 kN4、工艺技术参数:8)来料(铣面后)规格:铸锭厚度: 300~550mm(将来发展到720mm)铸锭宽度: 860 ~2060mm铸锭长度: 3500~5000mm(将来发展到7200mm)最大锭重: ~15320kg(7.44kg/mm)(将来发展到28830 kg,13.995 kg/mm)9) 成品规格:成品卷材厚度: 3.5~8.0 mm成品卷材内径: Ф610mm成品卷材最小外径:Ф1350mm成品卷材最大外径:Ф2050mm成品卷重:最大15300kg(~7.3 kg/mm)5、工艺要求:1、操作人员在轧制过程中根据程序表应密切监视轧制状态和调节板形;2、在切头尾时,必须切去头尾的鳄鱼嘴及头尾部缺陷,以保证卷材质量;3、对于乳液系统要按照乳液管理《热轧乳液配制工艺及管理规程》执行;4、对于铸锭的压下,原则上要按照既定的《轧制规程表》进行的各种工艺方式的控制和调整,若出现异常情况,如在轧制过程中设备出现问题,导致铸锭温度下降较多,操作人员可以根据实际情况,灵活安排道次,保证生产的正常进行;5、为了避免因料头料尾跑偏而造成的头尾料塔形过大,应考虑将轻剪投入使用;6、根据要求选择热轧卷取样,检测卷材的中凸度、力学性能、高低倍晶粒度以及检查表面质量,并对检测结果做好记录,备查;7、轧制后的卷材要按合金品种状态、规格摆放在指定料区,指定料区必须清洁无凸起物,以防止硌伤料卷。
- 1、下载文档前请自行甄别文档内容的完整性,平台不提供额外的编辑、内容补充、找答案等附加服务。
- 2、"仅部分预览"的文档,不可在线预览部分如存在完整性等问题,可反馈申请退款(可完整预览的文档不适用该条件!)。
- 3、如文档侵犯您的权益,请联系客服反馈,我们会尽快为您处理(人工客服工作时间:9:00-18:30)。
. . 铝及铝合金热轧工艺 热轧坯料主要采用的是半连续、连续两种生产方式生产铝锭,现代化的热连轧大部分都是采用半连续铸造的生产方式生产铸锭,可生产出来的铸锭重量重,铸锭的尺寸、表面、化学成分和内部质量较高 一铸锭的制备和质量要求。 (1) 铸锭的选择应考虑到客户的质量需求和自身设备能力和工艺水平。(举例子) (2) 铸锭的厚度选择的依据:成品厚度和变形率 (3) 铸锭宽度选择的依据:成品的宽度和合金的切边量 (4) 铸锭长度的选择依据:热轧卷的卷径 二铸锭的断面形状: (1) 圆弧形 (2) 梯形 (3) V字形 (4) 长方形 三铸锭切头尾的目的 四热轧前铸锭头尾的处理方式 (1) 表面要求不高的产品可以对铸锭浇铸口和底部不做任何处理 (2) 对表面要求高的产品必须将头尾铸造缺陷部分全部切除 (3) 铸锭切头切尾长度的确定
合 金 用 途 膨胀端(≥mm) 浇口端(≥mm)
1××× 普料 250 0 1××× 阳极氧化 350 100 1235 铝箔坯料 250 100 3××× 普料 300 0 3××× 阳极氧化 350 100 5××× 普料 300 100 5××× 阳极氧化 350 100
五、热轧前铸锭的表面处理 1、铣面 铸锭铣面量的确定原则:产品的用途、合金特点。铸造技术,目前国内带侧面铣的的铣削量大面一般8-15mm.小面8-10 mm. 铣床的特点:干铣和湿铣 2铣面后的表面质量要求 (1) 铸锭小面弯曲不易过大 (2) 铣刀痕的控制,刀痕深度不得大于0.15MM (3) 表面无粘铝现象 (4) 无磕碰或存放时间过长 . . 六、铸锭的加热 (1)天然气加热炉的基本特点,加热速度快、温度均匀、 (2)加热制度:均热温度,加热温度和炉内气氛 (3)加热温度必须满足热轧温度的要求,保证合金塑性高,变形抗力低 (4)装炉要求:先宽后窄,先一次后二次,先低温后高温,先小吨位后大吨位 七热轧工艺 (1) 轧制方式和特点:纵轧、横轧、斜轧 (2) 影响轧制的几个重要因素:轧制过程包括粗轧和精轧,在轧制过程中主要是轧辊,轧件和乳液三者之间的作用过程 (3) 轧辊几个常用的术语 A:辊型 B:轧辊硬度 C表面粗糙度 D轧辊的基本结构 E轧辊的加工精度::尺寸精度、轧辊径向跳动、辊身两端直径差、配对辊径差,表面状况。 八热轧制度设计 (1) 热轧速度的确定 A开始轧制阶段,铸锭短且厚,绝对压下量大,咬入困难,一般为了咬入采用低速轧制 B 中间轧制阶段为了控制终轧温度和提高生产效率,一般都采用高速轧制 C 最后轧制阶段,因为带材变得薄而长,轧制过程温度降得太快,但是也要控制表面所以要根据现场情况合理选择轧制速度。 热轧压下制度 热轧压下制度的确定主要包括热轧总加工率和道次加工率的确定 (2) 总加工率的确定原则 铝及铝合金板带材的热轧总加工率可达到90%以上,总加工率愈大,材料的组织越均匀,性能越好, A合金材料的性质。纯铝以及软合金,其高温塑性范围较宽,热脆性小、变形抗力低,因而其总加工率越大,硬合金则相反。 (3) 满足最终产品表面质量和性能的要求 供给冷轧的坯料,热轧总加工率应留足冷变形量,以利于控制产品性能和获得良好的冷轧表面质量;铝及铝合金热轧制品的总加工率应大于80%。 (4) 轧机能力及设备条件 轧机最大工作开口度和最小轧制厚度并差越大,铸锭越厚,热轧总加工率越大,但铸锭厚度受轧机开口度和辊道长度的限制。铸锭尺寸及质量,铸锭厚且质量好,加热均匀,热轧总加工率相应增加。 道次加工率的确定原则 制定道次加工率应考虑合金的高温性能、咬入条件、产品质量要求及设 备能力。不同轧制阶段加工率确定原则是: (1) 开始轧制阶段,道次加工率比较小,一般为2%~10%,因为前几道次主. . 要是变铸造组织加工组织,满足咬入条件。 (2) 中间轧制阶段,随金属加工性能的改善,如果设备条件允许,应尽量加大道次变开量,对硬铝合金道次加工率可达45%以上,软合金可达50% (3) 最后轧制阶段,一般道次加工率减小,为防止热轧制品产生粗大晶粒,热轧最后道次的加工率应大于临界变形量(15%~20%);最后两道次温度较低,变形抗力较大,其压下量分配应保持带材良好的板形,厚度偏差及表面质量。
(5) 热轧时的冷切和润滑 铝及铝合金具有较强的粘着工具的特点,轧制的时候必须采用冷切润滑。
在轧制铝板带时,采用金属轧制乳化液,可提高压下量,减少轧制压力,减少轧制道次,节约电能,人力,提高产品质量和数量。 使用金属轧制乳化液可以达到以下目的: 1)、减少变形区接触弧表面上的摩擦力和摩擦系数,在轧机上使用轧制用乳化液既可以增大道次压下量和减少道次数,同时还可以提高轧制速度,可减小最小可轧厚度)。 2)、是减少轧辊的磨损; 3)、防止金属粘(焊)在轧辊上。 4)、冷却功能。 5)、清洗功能。乳化液也起洗涤作用,他能从轧机的轧辊面和金属表面上冲掉金属微粒(磨损物)和其它污垢。 6)、在轧制过程中,应保证在辊面和金属表面上能均匀喷涂。如分布不均可产生波浪和飘曲。 7)、控制工作辊温度和辊型的分布等。
1、乳液的组成 乳液有几种主要的组成部分:基础油、润滑添加剂、乳化剂、润湿剂和抗氧化剂等。 基础油:具有一定的润滑作用,同时是其它润滑成分的载体。不同轧机基础油的粘度要求不同,粘度不同,意味着油膜厚度和油的流动性不同。好富顿公司选用特种基础油,其优点是粘温指数低,乳液平衡能力较好,具有一定的润滑能力,便于咬入。 润滑添加剂:在金属轧制过程中,要求金属轧制用油具有良好的减少摩擦和磨损的性能,润滑添加剂可以防止互相接触的金属产生磨损。为了减少摩擦表面间的摩擦力,防止产生干. . 摩擦而使用的添加剂称为润滑添加剂。润滑添加剂具有在摩擦表面上生成牢固油膜的能力及减少摩擦,改善润滑作用的能力。 乳化剂:具有易溶于油的亲油基和易溶于水的亲水基所组成。具有防止油水两相互相排斥的功能,而且将油和水两相连接起来,不使其分离的特殊功能。乳化剂具有降低油珠表面张力和降低油珠分散在水中的能量,同时由于乳化剂排列在油珠表面,亲水基都排列在油珠表面,由于同性相斥的作用,防止了油珠之间相互接近,聚集长大。乳化剂的主要作用:乳化、清洗、加溶、润湿、分散、起泡等作用。 润湿剂:润湿是固体表面的一种流体被另一种流体所取代的过程。润湿作用通常是指液体在固体表面上附着的现象。为使乳液能更均匀的附着在轧辊和轧件表面,即在轧辊和轧件表面形成的油膜和润滑膜均匀,所以乳液中需要添加适量合适的润湿剂。 抗氧化剂:能延长油品氧化反应的诱导期,减缓油品氧化速度,延长油品使用寿命的添加剂。由于油品不可避免的都会出现氧化过程,因此如何阻止油品氧化,或者说如何延长油品使用寿命就是所有油品产商关注的问题,所以必需选择合适的抗氧化剂添加到油品中减缓油品的氧化速度,延长使用寿命。
2、乳化原理 铝热轧使用的是水包油型的乳化液,这种乳化液结合了油良好的润滑性能和水良好的冷却能力。然而大家都知道,油和水互不相溶,如何可以让油相能相对均匀地分散在水中呢? 水分子是极性分子,油分子是非极性分子,根据“相似相溶(极性分子溶于极性溶剂,非极性分子溶于非极性溶剂)”的原理得知两者不相溶。“相似”是指溶质与溶剂在结构上相似,“相溶”是指溶质与溶剂彼此互溶。具体的说:油不溶于水,是因为不含有与水相溶的基团。若含有水溶性基团,并且,憎水基团不是太大的话,则一般是水溶性的,如果憎水基团太大,那也不溶于水。相反,没有水溶基团,则一般不溶于水。油主要是一些烷基组成,没有水溶性基团,所以不溶于水。 油水不互溶,如果借助机械力量将水中的油相分散成为细小的油珠形式,油珠的表面积迅速增大,分散产生的能量迅速增加,表面张力大,这样,分散到水中的细小油珠仍会迅速地聚集成大的油珠,恢复到最低能量状态。 . . 一般而言,乳化过程需要有化学品,热能和机械能来较好的完成。 首先,挑选合适的乳化剂,乳化剂分子由亲水基团和亲油基团组成,亲油基团与油珠结合,亲水基团会和水结合。这样能大大降低表面张力,降低分散所产生的高的能量,同时,也在油珠表面形成了保护层,防止油珠间的聚集长大。温度所提供的热能可以降低油珠表面张力,同时也为扩散提供一定的能量,所以,可以通过将水加热到一定温度,再进行加油配液,同时将乳液保持一定的温度也有助于乳化液稳定的运行。通过乳液泵的剪切来提供一定的机械能,为油珠分散提供所需要的机械能量,所以,乳液配液或使用是最好能保持循环和运动,也有助于乳化液油珠能均匀稳定的存在在水中。如下是乳化原理图:
3乳液的润滑原理 热分离性 铝轧制乳化液要具有适当的热分离效果,即在铝板带和轧辊表面要发生油水分离,在轧制咬入的高温高压作用下,分布在水中的油相分离出来,产生足够多的油性成分在轧辊表面形成良好的润滑膜。热分离很重要,它是润滑的先决条件。 热分离的好坏与轧辊温度,乳液自身性质及乳液的乳化状态有直接关系。当乳液和热的表面接触所分离的油量、乳液的润滑性能与热分离性能密切相关。通常乳粒尺寸越大,乳液越松,热分离量越大,反之亦然。 4液的维护和管理
物理管理主要包括:乳液的温度控制和乳液过滤、撇油、部分排放处理,清刷, 化学管理包括:溶度、PH值、电导率。 5清刷辊的使用
油相 水相
油分散在水中
机械能 化学品
热能 机械能
油珠分散在水中,形成水包油乳液