T800级碳纤维复合材料抗冲击性能
碳纤维t的分级

碳纤维t的分级全文共四篇示例,供读者参考第一篇示例:碳纤维t是一种高性能的纤维材料,因其优异的力学性能和轻质化特性而被广泛应用于航空航天、汽车、体育用品等领域。
在碳纤维t的制备过程中,通常会根据其质量和性能特点进行分级,以便更好地满足不同领域的需求。
碳纤维t分级主要取决于以下几个方面:纤维的直径、纤维的长度、纤维的取向和纤维之间的结合状况。
根据这些特点,碳纤维t可以分为高强度碳纤维、高模量碳纤维和中间碳纤维。
高强度碳纤维是碳纤维t中力学性能最出色的一类,其主要特点是具有极高的拉伸强度和刚性。
这类碳纤维t通常在要求高强度和轻量化的应用领域中得到广泛应用,如航空航天领域的航空器结构件、导弹外壳等。
除了以上几类基础的碳纤维t分级外,还有一些衍生的特殊类型,如表面改性碳纤维、多向碳纤维等。
这些特殊类型的碳纤维t通常通过对碳纤维表面进行处理或改变纤维的布局方式来达到特定的性能要求,以满足一些特殊领域的需求。
第二篇示例:碳纤维是一种应用广泛的轻质高强材料,在航空航天、汽车、体育器材等领域都有着重要的应用。
碳纤维材料通常分为几个不同等级,其中碳纤维T级是其中的一种。
碳纤维T级是一种优质的碳纤维材料,具有较高的强度和刚度。
它通常被用于要求较高性能的领域,如航空航天、汽车赛车等。
碳纤维T 级的制备过程相对较为复杂,需要严格控制温度、压力等参数,以保证最终产品的质量。
碳纤维T级通常可以分为几个不同的等级,如T300、T700、T800等。
每种等级的碳纤维材料具有不同的性能指标,适合不同的应用场景。
下面我们将分别介绍几种常见的碳纤维T级。
碳纤维T级是一种非常重要的高性能材料,具有广泛的应用前景。
不同等级的碳纤维T级材料适合不同的应用场景,我们可以根据实际需求选择合适的等级。
希望未来随着技术的不断发展,碳纤维T级材料能够得到更广泛的应用,并为各行业带来更多的创新和发展。
【文章结束】。
第三篇示例:碳纤维是一种轻量、高强度、高刚性的材料,被广泛应用于航空航天、汽车、体育用品等领域。
碳纤维级别划分标准

碳纤维级别划分标准走在材料科学的前沿,碳纤维就像是科技界的轻盈舞者,以其卓越的性能,在航空航天、汽车制造乃至体育用品领域大放异彩。
可你知道吗?这看似简单的材料背后,其实隐藏着一套复杂的分级体系。
今天,咱们就来聊聊碳纤维级别的那些事儿,保证让你对这位“轻盈舞者”有更深刻的认识。
碳纤维的等级划分,就好比是挑选茶叶,不同的产地、制作工艺,决定了茶叶的品质高低。
碳纤维也是一样,根据其力学性能、密度、成本等因素,被细分为不同的等级。
这些等级,不仅影响着碳纤维的应用范围,还直接关系到产品的性能和价格。
先说说最常见的几种吧。
T300、T700、T800,这几个数字听起来是不是有点眼熟?它们就像是手机型号一样,代表了碳纤维的不同强度等级。
T300属于入门级选手,虽然性能不算顶尖,但在成本控制方面有着明显优势,非常适合大规模生产使用。
就像咱们平时买衣服,不一定非要追求名牌,适合自己的才是最好的嘛。
往上走,T700、T800就像是服装界中的轻奢品牌,性能更优,价格自然也水涨船高。
这类碳纤维常用于高端运动器材、高性能汽车等领域,追求极致体验的人士会更倾向于选择它们。
试想一下,用T800碳纤维制成的自行车,骑起来那叫一个轻快,仿佛能让人瞬间变成飞人乔丹,感受风一般的自由。
除了T系列,还有M系列,这是专门为高强度需求设计的碳纤维。
M40J、M55J等型号,就像是材料界的特种部队,专攻那些极端环境下的应用,比如火箭外壳、卫星部件等。
这类碳纤维不仅强度高,而且韧性好,能够承受极大的外力冲击而不轻易损坏。
用它来做点什么,绝对能让人刮目相看。
当然了,碳纤维的级别划分不仅仅局限于T系列和M系列,还有其他一些特殊的分类。
比如说,有些碳纤维是为了提高耐热性而设计的,适用于高温环境;有的则是为了增强电磁屏蔽效果,被广泛应用于电子设备中。
这些特殊用途的碳纤维,就像是材料界的多面手,能够满足不同行业的需求。
聊到这里,你是不是对碳纤维的级别有了更清晰的认识?其实,碳纤维的选择就像挑选食材做菜一样,不同的菜系需要不同的食材搭配,才能做出最美味的佳肴。
碳纤维——精选推荐

碳纤维今年3⽉⽇本东丽公司宣布成功研制出T1100G型⾼强⾼模碳纤维,我国企业近年来也不断传出突破⾼性能碳纤维研制和⽣产的报道。
碳纤维的关键⼒学指标包括拉伸强度、拉伸模量、断裂伸长率等。拉伸强度是指材料在拉伸过程中可承受的最⼤应⼒;拉伸模量是指材料拉伸时受到的应⼒与形变的⽐值,模量值越⾼,表⽰碳纤维的刚度越好;伸长率是指断裂前材料能被拉长的⽐例,伸长率越⾼,表⽰碳纤维的韧性越好。理论上碳纤维的拉伸强度可以达到180GPa,拉伸模量更是在1000GPa左右,虽然⽇本东丽公司已经研制出拉伸强度9GPa的⾼强碳纤维,拉伸模量也达到690GPa的⾼模碳纤维,但两者尤其是拉伸强度还有很⼤的发展潜⼒。碳纤维的断裂伸长率指标从早期的T300级别的1.5%增加到⽬前T1000级别的2.4%,有效缓解了碳纤维韧性不⾜的问题,进⼀步了扩展应⽤范围,如⽤于制造⼤型客机机体。
按照碳纤维丝束中的单丝数量,聚丙烯腈基碳纤维⼜可分为⼩丝束和⼤丝束两种。相⽐⼩丝束,⼤丝束的劣势在于,在制作板材等结构时,丝束不宜展开,导致单层厚度增加,不利于结构设计。此外,⼤丝束碳纤维粘连、断丝等现象更多,这样会使强度、刚度受影响,性能有所降低,性能的分散性也会较⼤。飞机、航天器⼀般只⽤⼩丝束碳纤维,因此⼩丝束碳纤维⼜被称为"宇航级"碳纤维,⼤丝束碳纤维被称为"⼯业级"碳纤维。
但是⼤丝束⽣产成本⽐⼩丝束低,⽽随着⽣产技术的进步,⼈们对碳纤维材料结构的熟悉,⼤丝束碳纤维越来越多⽤于对可靠性要求严苛的领域。这样,⼩丝束与⼤丝束之间区分也发⽣了变化,如早期曾以丝束中单丝数量12000根(12K)作为分界线,但⽬前单丝数量1K~24K的碳纤维被分为⼩丝束,⽽48K以上的的划为⼤丝束。⽽空客公司在制造A380超⼤型客机时已经开始使⽤了24K碳纤维,估计随着技术的进步,⼩丝束与⼤丝束之间的分界线还会向上推。
碳纤维材料具有诸多优点,但其⽣产⼯艺流程长,需要突破的技术障碍很多。碳纤维的制造,可以分为原丝制造和碳化两个关键过程。原丝制造,简单地说是先通过丙烯腈聚合和纺纱等⼯艺,先聚合制成聚丙烯腈,再纺丝制出聚丙烯腈纤维原丝。聚丙烯腈原丝随后进⾏预氧化、低温和⾼温碳化等步骤,最后进⾏表⾯处理、上浆烘⼲并收丝就得到了碳纤维。相对碳化,⽣产出⾼质量的聚丙烯腈原丝更加关键,即使是东丽公司也曾因为原丝质量在碳纤维研制过程中上摔过跟头。要⽣产处⾼质量的碳纤维,要降低⽣产成本,聚丙烯腈原丝须满⾜⾼纯化、⾼强化、均质化、细纤度化和表⾯光洁等要求,这长期以来⼀直是碳纤维批量⽣产中最⼤的拦路虎。
军工新材料行业系列报告二:主要新材料介绍及上市公司梳理:国防装备发展,材料是基础
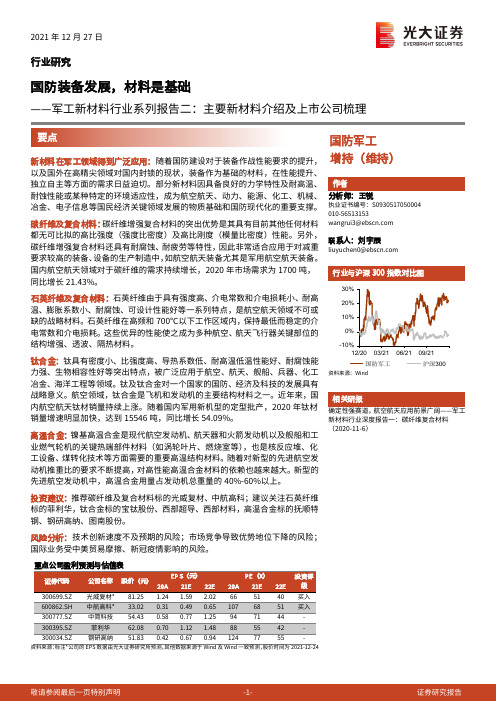
2021年12月27日行业研究国防装备发展,材料是基础——军工新材料行业系列报告二:主要新材料介绍及上市公司梳理国防军工新材料在军工领域得到广泛应用:随着国防建设对于装备作战性能要求的提升,以及国外在高精尖领域对国内封锁的现状,装备作为基础的材料,在性能提升、独立自主等方面的需求日益迫切。
部分新材料因具备良好的力学特性及耐高温、耐蚀性能或某种特定的环境适应性,成为航空航天、动力、能源、化工、机械、冶金、电子信息等国民经济关键领域发展的物质基础和国防现代化的重要支撑。
碳纤维及复合材料:碳纤维增强复合材料的突出优势是其具有目前其他任何材料都无可比拟的高比强度(强度比密度)及高比刚度(模量比密度)性能。
另外,碳纤维增强复合材料还具有耐腐蚀、耐疲劳等特性,因此非常适合应用于对减重要求较高的装备、设备的生产制造中,如航空航天装备尤其是军用航空航天装备。
国内航空航天领域对于碳纤维的需求持续增长,2020年市场需求为1700吨,同比增长21.43%。
石英纤维及复合材料:石英纤维由于具有强度高、介电常数和介电损耗小、耐高温、膨胀系数小、耐腐蚀、可设计性能好等一系列特点,是航空航天领域不可或缺的战略材料。
石英纤维在高频和700℃以下工作区域内,保持最低而稳定的介电常数和介电损耗。
这些优异的性能使之成为多种航空、航天飞行器关键部位的结构增强、透波、隔热材料。
钛合金:钛具有密度小、比强度高、导热系数低、耐高温低温性能好、耐腐蚀能力强、生物相容性好等突出特点,被广泛应用于航空、航天、舰船、兵器、化工冶金、海洋工程等领域。
钛及钛合金对一个国家的国防、经济及科技的发展具有战略意义。
航空领域,钛合金是飞机和发动机的主要结构材料之一。
近年来,国内航空航天钛材销量持续上涨。
随着国内军用新机型的定型批产,2020年钛材销量增速明显加快,达到15546吨,同比增长54.09%。
高温合金:镍基高温合金是现代航空发动机、航天器和火箭发动机以及舰船和工业燃气轮机的关键热端部件材料(如涡轮叶片、燃烧室等),也是核反应堆、化工设备、煤转化技术等方面需要的重要高温结构材料。
T800H级环氧基复合材料热力学性能测试

第1期纤维复合材料㊀No.1㊀252024年3月FIBER ㊀COMPOSITES ㊀Mar.2024T800H 级环氧基复合材料热力学性能测试乔㊀巍,贾佳乐,路明坤(中建材(上海)航空技术有限公司,上海200120)摘㊀要㊀开展了T800H 级树脂基复合材料的热力学性能测量㊂采用热膨胀分析仪测量了0ħ~170ħ温度范围内复合材料热膨胀系数;对E1806树脂进行了恒温和动态DSC 扫描,基于自催化模型,建立了E1806树脂的固化动力学方程;利用旋转流变仪测量出E1806树脂的凝胶固化度为0.62;采用TMA 法测量出凝胶后单向层合板厚度方向上的收缩应变为0.88%㊂关键词㊀热力学性能;固化动力学方程;收缩应变;试验Thermodynamic Performance Test of T 800H Grade EpoxyMatrix Composite MaterialsQIAO Wei,JIA Jiale,LU Mingkun(CNBM (Shanghai)Aviation Technology Co.,Ltd.,Shanghai 200120)ABSTRACT ㊀This article conducted thermodynamic performance measurements of T800H resin based composite materials.The thermal expansion coefficient of composite materials was measured using a thermal expansion analyzer within the temper-ature range of 0ħto 170ħ;The constant temperature and dynamic DSC scanning were performed on E1806resin,and the curing kinetics equation of E1806resin was established based on an autocatalytic model;The gel curing degree of E1806resin was 0.62measured by rotary rheometer;The shrinkage strain in the thickness direction of unidirectional laminates af-ter gel is 0.88%measured by TMA method.KEYWORDS ㊀thermodynamic performance;curing kinetics equation;shrinkage strain;test基金项目:中国建材集团攻关专项资助(2021YCJS02)通讯作者:乔巍,博士㊂研究方向为复合材料结构设计及固化变形控制㊂E -mail:qiaow@1㊀引言复合材料具有高比强度,高比刚度,且具有良好的可设计性,因此,复合材料越来越多地应用于飞机机身㊁机翼等结构中[1-3]㊂复合材料热力学性能是复合材料固化过程模拟㊁残余应力和固化变形预测的基础,因此需要通过试验获得复合材料热力学性能及在固化过程中的固化反应行为㊂固化动力学方程主要描述固化过程中树脂基体固化反应程度与温度和时间的函数关系㊂众多学者对不同树脂体系固化反应行为进行了大量的理论和试验研究㊂李伟东等[4]和张晨乾等[5]研究了热压罐固化的双马聚酰亚胺树脂固化动力学行为,并绘制了树脂的时间-温度-转变(TTT)图㊂李自强等[6]在Kamal 动力学模型的基础上,通过差示扫描量热分析法(Differential Scanning Calorimetry,纤维复合材料2024年㊀DSC)获得了微波固化的环氧树脂固化反应动力方程㊂江天等[7]研究了热压罐固化的T800/环氧树脂体系的复合材料性能,其中树脂固化动力学方程和玻璃化转变温度方程的研究方法为DSC法㊂贾丽杰[8]利用江天试验测量的材料性能和固化动力学方程建立了复合材料固化变形的有限元模型,研究了结构因素对固化变形的影响㊂在固化过程中,复合材料化学收缩反应会产生收缩应变,目前获得树脂化学收缩应变的方法主要是试验法㊂Li等[9]采用重量法测量了MY750树脂凝胶前后的化学收缩率㊂杨喜等[10]采用王荣秋教授发明的毛细管膨胀计法实时监测了环氧树脂固化过程中化学收缩率的变化㊂丁安心[11]和Hu等[12]将光纤布拉格光栅传感器埋入预浸料内部,测量了固化过程中材料内应变的变化情况㊂Garstka等[13]采用静态热机械分析仪(Thermomechanical Analy-sis,TMA)测量了AS4/8552复合材料的收缩应变,江天等[7]采用了相同的方法监测了T800/环氧预浸料固化过程中的厚度变化情况㊂TMA法是目前比较主流的化学收缩应变测量方法,预浸料在一定的温度历程(复合材料厂推荐的固化工艺温度曲线)下,且在预浸料表面的特定方向上施加一定的机械力以模拟固化压力,这时测量在该方向上预浸料尺寸变化量随温度和时间的变化情况㊂目前研制的T800H环氧基复合材料的材料性能和固化动力学参数等尚不完善,亟需进行相关试验测量材料参数,为后续复合材料固化变形模拟提供输入条件㊂本文利用电液伺服试验机和热膨胀仪分别测量了复合材料力学性能和热膨胀系数,通过差示扫描量热分析仪和旋转流变仪分别研究了E1806环氧树脂的固化动力学方程和凝胶固化度,采用静态热机械分析仪研究了固化过程中T800H/E1806单向预浸料在厚度方向上的收缩应变㊂2㊀热膨胀系数测量复合材料试验件的材料牌号为T800H/E1806,纤维为T800级增强碳纤维,基体为E1806环氧基树脂,采用热压罐固化工艺成型㊂采用MST370系列电液伺服试验机测量复合材料的力学性能,其中复合材料纵向(沿着纤维方向)和横向(垂直纤维方向)弹性模量的试验标准为ASTM D3039,复合材料剪切模量和泊松比的试验标准为ASTM D7078㊂通过NETZSCH公司的DIL402Expedis热膨胀分析仪测量不同温度下复合材料热膨胀系数,试验件为固化好的单向层合板,试验标准为ASTM D696,测量范围为0ħ~170ħ,试验结果如图1所示㊂试验结果表明,复合材料横向热膨胀系数β2远大于纵向热膨胀系数β1,且β1的值很小,这是由于复合材料的纵向性能主要是由纤维性能决定的,且纤维的热膨胀系数很小㊂β1的试验结果随温度变化很小,因此可取均值-0.35με/ħ㊂β2的试验结果随温度的增加而增大,采用一次函数拟合该试验数据,拟合结果如公式(1)所示,拟合优度R2为0.978,接近于1,表明拟合效果良好㊂β2=(0.018T+30.642)με/ħ(1)式中,T为温度㊂图1㊀T800H复合材料热膨胀系数的试验结果3㊀固化动力学方程采用DSC法研究E1806树脂的固化动力学方程,获得树脂在固化过程中固化度随温度和时间的变化历程,为后续的固化变形仿真分析奠定试验基础㊂首先,采用德国NETZSCH公司的DSC200F3型号设备对树脂样品进行变温扫描,DSC试验测量设备如图2所示,样品质量为3mg,流速设定为50ml/min,时间设定为50min,升温速率有两种,分别为5ħ/min和10ħ/min㊂变温下DSC测量的热流-时间曲线如图3所示,获得了单位质量树脂固化反应释放的总热量Hr为452kJ/kg㊂在此基础上,采用DSC进行等温扫描,树脂样品质量约562㊀1期T800H 级环氧基复合材料热力学性能测试mg,流速设定为50ml /min,时间设定为60min,温度分别为165ħ㊁175ħ及185ħ,测量获得的热流-时间曲线如图4所示㊂图2㊀DSC试验测量设备图3㊀DSC 测量的热流-时间曲线图4㊀恒温下DSC 测量的热流-时间曲线假设树脂的固化率与热流变化率成正比,即[14]如公式(2)所示㊂dαdt =1H r dHdt(2)式中,t 为时间;α为固化度;dα/dt 为固化率;H 为热量;dH /dt 为热流变化率㊂将图4中的瞬时热量除以总热量Hr,再对时间进行积分,得到了固化度-固化率曲线,如图5所示㊂目前,固化动力学模型主要有宏观尺度上的唯象模型和细观尺度上的机理模型㊂由于固化反应过程过于复杂,采用机理模型进行建模和计算的难度高,因此现有的固化动力学研究主要以唯象模型为基础,再通过非线性拟合得到模型参数㊂目前常用的固化动力学模型主要有n 级动力学模型㊁Kamal 模型及自催化模型等㊂本文采用自催化模型对E1806树脂的固化反应进行动力学分析,自催化模型的表达式如公式(3)所示㊂dαdt =A exp (-ΔERT)αm (1-α)n (3)式中,A 为频率因子;ΔE 为活化能;m 和n 为动力学常数;R 为普适气体常数㊂根据图5中的固化度-固化率试验结果,采用神经网络优化算法对公式(3)进行非线性拟合,即可得到固化动力学参数㊂拟合优度R 2㊂图5同时给出了试验结果和自催化模型的拟合结果,结果表明,在固化反应阶段,自催化模型的拟合结果与试验结果吻合良好,拟合得到的E1806树脂固化动力学参数如表1所示㊂图5㊀不同温度下固化度-固化率的自催化模型拟合结果与试验结果对比表1㊀拟合的E1806树脂自催化模型固化动力学参数A /minΔE /(J /mol)mn4.824ˑ104 6.544ˑ1040.1636 1.33264㊀凝胶固化度测量随着固化的进行,树脂黏度逐渐增大,基体分子链逐渐增长,开始形成三维网状结构,此时会出72纤维复合材料2024年㊀现凝胶现象,其中树脂的凝胶点是固化反应到达一定程度的标准㊂在等温凝胶试验中,将固化反应到达凝胶点所需要的时间定义为凝胶时间t gel ,此时的固化度称为凝胶固化度αgel ㊂本文采用旋转流变仪研究了E1806树脂的凝胶固化度㊂采用美国TA 仪器公司的ARES -G2旋转流变仪在170ħ和180ħ两种温度下对树脂进行了等温扫描,获得的E1806树脂存储模量和损耗模量变化曲线如图6所示㊂结果表明,随着固化反应的进行,树脂存储模量E 和损耗模量Eᶄ均逐渐增加㊂此外,固化反应开始时E 小于Eᶄ,但到达某个时间点后E 将超过Eᶄ,且通常将E =Eᶄ对应的时刻定义为该温度下树脂的凝胶时间t gel [7],这样170ħ和180ħ对应的凝胶时间t gel 分别为31.05min 和21.12min㊂利用E1806树脂的固化动力学公式(3),计算出在170ħ和180ħ恒温下的凝胶固化度αgel 分别为0.61和0.63,因此本文通过旋转流变仪法测量得到的E1806树脂凝胶固化度取值为0.62㊂图6㊀旋转流变仪测量的E1806树脂存储模量和损耗模量曲线化学收缩应变测量采用TMA 法测量固化过程中T800H /E1806复合材料的化学收缩应变㊂试验所用TMA 为美国热流变科学仪器公司的Q400,如图7(a)所示,其温度精度为ʃ1ħ,位移精度为ʃ0.5nm㊂试验件为单向铺层的预浸料,如图7(b)所示,其面内尺寸4mm ˑ4mm,初始厚度为4.04mm㊂T800H /E1806复合材料的固化工艺温度曲线为:从室温升温至130ħ,保温一个小时,再升温至185ħ,保温两个小时,最后降至室温,升温和降温速率分别为2ħ/min 和-2ħ/min,如图8所示㊂此外,热压罐的固化压力为0.6MPa,真空袋压力为0.1MPa㊂采用TMA 进行测试时,将测量频率设定为1Hz,压头施加压强设定为0.7MPa,温度历程按工艺温度曲线,测量固化过程中试验件在厚度方向上的收缩应变历程㊂图7㊀TMA 试验仪器和试验件通过E1806树脂的固化动力学方程,计算得到135min 时的树脂固化度为0.62,即135min 时树脂将发生凝胶反应㊂由于凝胶前树脂的流动性较好,通常认为凝胶前复合材料内部的残余应变和残余应力都会随着树脂的流动而消失[13],因此可合理假设135min 时的应变为0㊂在此基础上,通过TMA 获得了固化过程中试验件厚度方向上的收缩应变变化曲线,如图8所示㊂结果表明,135min 前试验件厚度方向上的收缩应变为0;135min 至245min 时,试验件厚度方向上的收缩应变绝对值逐渐增加,需要注意的是,这里的收缩应变不仅包含了化学收缩应变,还包含了该时间段内产生的少量热应变;245min 后收缩应变保持恒定,试验件厚度方向上的收缩应变最终达到了-0.88%㊂采用一个三次多项式拟合固化过程中收缩应变的试验结果,获得的拟合式如公式(4)所示,图8表明拟合曲线与试验结果吻合较好㊂εsh 2=εsh3=0,tɤ135min -9.1076ˑ10-9t 3+6.025ˑ10-6t 2-0.00136t +0.0962,135<t <245min -0.0088,tȡ245minìîíïïïïï(4)式中,εsh 2和εsh3分别为复合材料面内横向和厚度方向上的化学收缩应变㊂由于纵向化学收缩应变εsh1主要由纤维性能决定,而纤维发生化学收缩,82㊀1期T800H 级环氧基复合材料热力学性能测试因此εsh1的值非常小,通常取为0㊂图8㊀固化过程中试验件厚度方向上的收缩应变变化曲线6㊀结语采用试验方法研究了T800H 级树脂基复合材料的热力学性能,结论如下:(1)采用热膨胀分析仪测量了E1806树脂0ħ~170ħ温度范围内复合材料热膨胀系数;(2)对E1806树脂进行了恒温和动态DSC 扫描,基于自催化模型,建立了E1806树脂的固化动力学方程;(3)利用旋转流变仪测量出E1806树脂的凝胶固化度为0.62;(4)采用TMA 法测量出凝胶后单向层合板厚度方向上的收缩应变为0.88%㊂参考文献[1]杜善义,关志东.我国大型客机先进复合材料技术应对策略思考[J].复合材料学报,2008(01):1-10.[2]王衡.先进复合材料在军用固定翼飞机上的发展历程及前景展望[J].纤维复合材料,2014,31(04):41-45.[3]张兴金,邓忠林.浅谈纤维复合材料与中国大飞机[J].纤维复合材料,2009,26(02):24-26.[4]李伟东,张金栋,刘刚,等.高韧性双马来酰亚胺树脂的固化反应动力学和TTT 图[J].复合材料学报.2016,33(07):1475-1483.[5]张晨乾,陈蔚,叶宏军,等.具有双峰反应特性的高韧性双马来酰亚胺树脂固化动力学和TTT 图[J].材料工程.2016,44(10):17-23.[6]李自强,湛利华,常腾飞,等.基于微波固化工艺的碳纤维T800/环氧树脂复合材料固化反应动力学[J].复合材料学报.2018,35(09):162-168.[7]江天,徐吉峰,刘卫平,等.整体化复合材料结构分阶段固化变形预报方法及其实验验证[J].复合材料学报.2013,30(5):61-66.[8]贾丽杰,叶金蕊,刘卫平,等.结构因素对复合材料典型结构件固化变形影响[J].复合材料学报.2013(s1):261-265.[9]Li C,Potter K,Wisnom M R,et al.In -situ measurement of chem-ical shrinkage of MY750epoxy resin by a novel gravimetric method [J].Composites Science &Technology.2004,64(1):55-64.[10]杨喜,李书欣,王继辉,等.一种实时监测环氧树脂固化过程中化学收缩的方法[J].玻璃钢/复合材料.2016(1):74-78.[11]丁安心.热固性树脂基复合材料固化变形数值模拟和理论研究[D].武汉理工大学,2016.[12]Hu H,Li S,Wang J,et al.Monitoring the gelation and effectivechemical shrinkage of composite curing process with a novel FBG ap-proach [J].Composite Structures.2017,176:187-194.[13]Garstka T,Ersoy N,Potter K D,et al.In situ measurements ofthrough -the -thickness strains during processing of AS4/8552com-posite [J].Composites Part A:Applied Science &Manufacturing.2007,38(12):2517-2526.92。
T800碳纤维复合材料混合连接层合板钉载分布及有限元计算

本 文 系统探 索 了连 续 B F及 其 B R F P筋 在 不 同
温度蒸馏水 、 碱溶液等环境下 的性能退化规律与机 理, 目的是 为 B R F P筋 在 上 述 土 木 环 境 下 的设 计 与
应用 提供基 础 实验数 据 。
( 4 r 4 m 10 m) 约 0 m X 0 m X . m 粘结到纤维束两端, a 作 为锚固片 , 如图 2所示 。纤维束 的拉伸性能用 电子
万能试 验 机 ( 南 , W.0 E) 试 , 伸 速 率 为 济 WD 10 测 拉
5mm/mi n。
1 试 验部 分
1 1 原材 料 .
国产 单 向 、 连续 玄 武岩纤 维 , 径 为 1 米 , 直 3微 纤
维束 内部 含约 70 20根纤维 单丝 。 玄武 岩 纤 维 增 强 环 氧 树 脂 筋 的 有 效 直 径 为
5 8
玄 武 岩 纤 维 及 其 复 合 筋 的 耐 久 性 能 研 究
玄武 岩 纤维 及 其 复合 筋 的 耐久 性 能研 究
吴敬 宇 ,成贵 军 ,李 惠
( 尔滨 工业 大 学 土 木 工 程 学 院 ,哈 尔滨 109 ) 哈 50 0
摘 要 :本文研 究 了连续玄武岩纤维( F 及其 复合材料 ( F P 筋在水 或碱液 浸泡环 境 下的长期 性能 退化规律 与机 理。 B) BR ) 结果表明 , 高温蒸馏水及碱液环境下 , 在 玄武岩 纤维表 面发生明显刻蚀 , 因此导致其拉伸强度发生显著退化 ; 并 浸泡 温度越 高 , B F强度 下降幅度越 大; 且在 强碱 溶液下 ,F强度的下降幅度远大于蒸馏水环境 。在 高温 蒸馏 水或碱溶 液环境下 , B 随着浸泡 时 间的延长 ,F P筋的拉伸 强度 显著 下降 , BR 但拉伸模量 变化较 小。 关键词 :玄武岩纤维 ;F P复合 筋 ;耐久性能 R 中图分类号 :T 32 B 3 文献标识码 :A 文章编号 :10 09 (0 1 0 0 5 0 0 3— 9 9 2 1 )5— 0 8— 4
日本东丽公司的碳纤维产品分类及应用
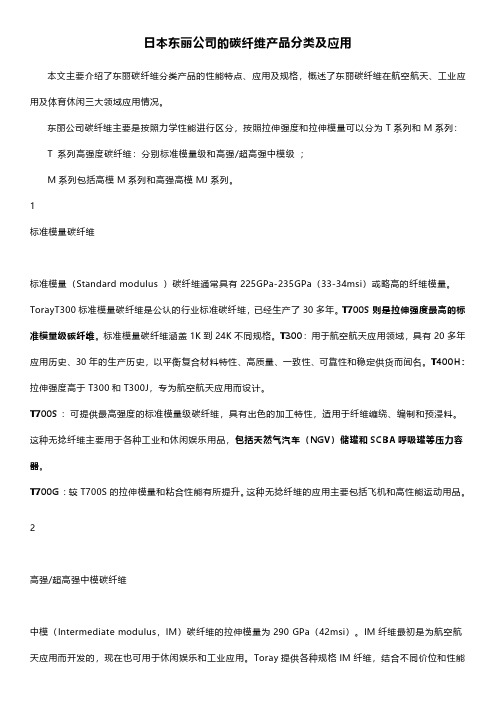
日本东丽公司的碳纤维产品分类及应用本文主要介绍了东丽碳纤维分类产品的性能特点、应用及规格,概述了东丽碳纤维在航空航天、工业应用及体育休闲三大领域应用情况。
东丽公司碳纤维主要是按照力学性能进行区分,按照拉伸强度和拉伸模量可以分为T系列和M系列:T系列高强度碳纤维:分别标准模量级和高强/超高强中模级;M系列包括高模M系列和高强高模MJ系列。
1标准模量碳纤维标准模量(Standard modulus)碳纤维通常具有225GPa-235GPa(33-34msi)或略高的纤维模量。
TorayT300标准模量碳纤维是公认的行业标准碳纤维,已经生产了30多年。
T700S则是拉伸强度最高的标准模量级碳纤维。
标准模量碳纤维涵盖1K到24K不同规格。
T300:用于航空航天应用领域,具有20多年应用历史、30年的生产历史,以平衡复合材料特性、高质量、一致性、可靠性和稳定供货而闻名。
T400H:拉伸强度高于T300和T300J,专为航空航天应用而设计。
T700S:可提供最高强度的标准模量级碳纤维,具有出色的加工特性,适用于纤维缠绕、编制和预浸料。
这种无捻纤维主要用于各种工业和休闲娱乐用品,包括天然气汽车(NGV)储罐和SCBA呼吸罐等压力容器。
T700G:较T700S的拉伸模量和粘合性能有所提升。
这种无捻纤维的应用主要包括飞机和高性能运动用品。
2高强/超高强中模碳纤维中模(Intermediate modulus,IM)碳纤维的拉伸模量为290GPa(42msi)。
IM纤维最初是为航空航天应用而开发的,现在也可用于休闲娱乐和工业应用。
Toray提供各种规格IM纤维,结合不同价位和性能特征,可满足各行各业的需求。
Toray的IM纤维规格包括6K,12K,18K和24K。
按照拉伸强度可以分为高强中模碳纤维(T800H、T800S、T1000G)和新一代超高强中模碳纤维(T1100G、T1100S)。
T800H:高强中模碳纤维,具有高水平和平衡复合特性。
纳米压痕技术表征T800碳纤维的弹性模量和硬度
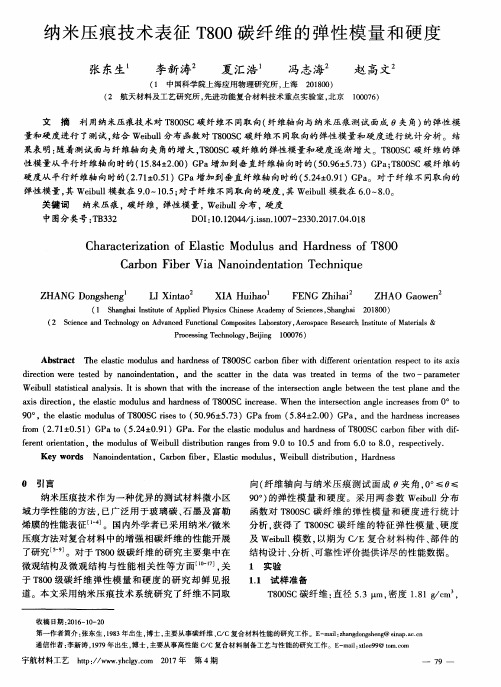
张 东生 李新涛 夏 汇浩 冯志海
2 0 1 8 0 0 )
赵 高文
1 0 0 0 7 6 )
( 1 中 国科 学 院 上 海 应 用 物 理 研 究 所 , 上海
( 2 航天材料及工艺研究所 , 先进功能复合材料技术重点实验室 , 北京
( 2 S c i e n c e a n d T e c h n o l o g y o n A d v a n c e d F u n c t i o n a l C o m p o s i t e s L a b o r a t o r y , A e r o s p a c e R e s e a r c h I n s t i t u t e o f Ma t e r i a l s &
9 0 。 , t h e e l a s t i c m o d u l u s o f T 8 0 0 S C r i s e s t o( 5 0 . 9 6  ̄ 5 . 7 3 )G P a f r o m( 5 . 8 4  ̄ 2 . 0 0 )G P a 。 a n d t h e h a r d n e s s i n c r e a s e s r f o m( 2 . 7 1 ± 0 . 5 1 )G P a t o( 5 . 2 4 ± 0 . 9 1 )G P a . F o r t h e e l a s t i c m o d u l u s a n d h rd a n e s s o f T S 0 0 S C c rb a o n i f b e r w i t h d i f -
文
摘
利 用纳米压 痕技 术对 T 8 0 0 S C碳 纤维不 同取 向 ( 纤维轴 向与பைடு நூலகம்纳 米压痕 测试 面成 夹角 ) 的弹 性模
- 1、下载文档前请自行甄别文档内容的完整性,平台不提供额外的编辑、内容补充、找答案等附加服务。
- 2、"仅部分预览"的文档,不可在线预览部分如存在完整性等问题,可反馈申请退款(可完整预览的文档不适用该条件!)。
- 3、如文档侵犯您的权益,请联系客服反馈,我们会尽快为您处理(人工客服工作时间:9:00-18:30)。
T800级碳纤维复合材料抗冲击性能王 莉1, 熊 舒2, 肇 研2, 杨 利1(1.航空工业第一飞机设计研究院,西安 710089;2.北京航空航天大学,材料科学与工程学院,北京 100191)摘要:对相同铺层比例、不同厚度的A,B,C三组T800级碳纤维复合材料层板进行多种冲击能量的冲击实验,测试冲击后凹坑深度、剩余压缩强度及压缩破坏应变等性能。结果表明:复合材料的冲击能量-凹坑深度曲线和凹坑深度-剩余压缩强度曲线均存在拐点,A组拐点位置为0.70 mm,B组拐点位置为0.76 mm,C组拐点位置为0.45 mm,均小于目视勉强可见冲击损伤(BVID)对应的凹坑深度(1.3 mm);同一铺层比例下,复合材料层合板厚度越大,其抗冲击损伤性能越好。关键词:碳纤维复合材料;冲击后压缩;凹坑深度;拐点doi:10.11868/j.issn.1005-5053.2017.000160中图分类号:TB332 文献标识码:A 文章编号:1005-5053(2018)05-0147-06
碳纤维增强树脂基复合材料因其具有高比强、高比模、耐腐蚀以及可设计等特点而广泛应用于各类航空航天结构中[1-4],由于复合材料自身层合结构特点,在厚度方向受到冲击时,易产生冲击损伤,主要表现为内部基体开裂、分层以及纤维断裂,这些损伤在材料表面目视困难,却使得构件压缩性能明显下降,这对复合材料构件的使用安全造成巨大威胁[5-6]。在对飞行器进行结构设计及强度分析时,复合材料抗冲击性能是非常重要的设计依据,合理的设计值是飞行器复合材料结构安全的重要保证。复合材料抗冲击性能包括损伤阻抗性能和损伤容限性能,具有高损伤阻抗的材料其抵抗外界冲击的能力较强,产生特定的凹坑深度需要较大的冲击能量[7-10]。具有高损伤容限的材料冲击时可能会产生不同程度的损伤,但会具有很高的冲击后压缩强度。为了保证复合材料结构的耐久性和损伤容限,有必要在材料研制和结构选材阶段对材料体系的抗冲击性能进行评定。T800级碳纤维作为新一代高强中模碳纤维的代表,国外已越来越多地应用于航空航天领域[11-12],国内针对新一代航空装备对T800级碳纤维复合材料的需求,开展了国产T800级碳纤维匹配的树脂基体、预浸料制备和复合材料成型工艺研究[13],国产T800级碳纤维复合材料体系在航空结构上的应用正处于论证及设计阶段,因此,对国产T800级复
合材料材料许用值和结构设计许用值的研究很有必要。对于复合材料抗冲击性能,材料许用值研究关注冲击后压缩强度(CAI),即采用落锤冲击方法,冲击能量为6.7 J/mm冲击能量下得到的压缩强度。复合材料结构压缩设计许用值应包含目视勉强可见冲击损伤(BVID,凹坑深度1.3 mm左右)时的压缩强度。本研究结合材料许用值及设计许用值的要求开展国产T800碳纤维复合材料抗冲击性能的研究。采用改变冲击能量的方法,研究三种不同铺层厚度的国产T800级碳纤维环氧树脂复合材料层合板的抗冲击性能。
1 实验材料及方法
1.1 试件所用材料为国产T800级碳纤维环氧树脂复合材料。试件包括三种典型铺层[45/0/-45/90]3s,[45/0/-45/90]4s,[45/0/-45/90]5s;编号分别为A,B,
C;厚度分别为3.42 mm,4.46 mm,5.55 mm。试件编号、铺层形式、厚度及冲击能量等见表1。1.2 冲击实验参照ASTM D 7136—2007进行。采用Instron9350全自动落锤冲击试验机,实验装置如图1所示。落锤总质量为(5.5 ± 0.25) kg,冲击头直径为(12.7 ± 0.1) mm。每组试样按照10种不同冲击能量进行实验(表1)。冲击过程中确认防二次冲击装置正常开启,试样未发生二次冲击。在冲击实验结束后立即测量凹坑深度,冲击后的试件采用超声C扫描检测内部损伤情况。
收稿日期:2017-09-14;修订日期:2017-10-30通讯作者:王莉(1988—),女,硕士,工程师,研究方向为航空复合材料,(E-mail)wanglisdu@126.com。
2018 年第 38 卷航 空 材 料 学 报2018,Vol. 38第 5 期第 147 – 152 页JOURNAL OF AERONAUTICAL MATERIALSNo.5 pp.147 – 1521.3 冲击后压缩实验冲击后压缩实验参照ASTM D 7137—2007进行,在冲击后压缩试样正反两面背对背粘贴4个应变计,使应变片的中心距离试样上边缘和侧边缘25 mm,贴片位置如图2所示。冲击后压缩实验在INSTRON 5985试验机上进行,试样夹持状态如
图3所示。加载速率为1.25 mm/min,加载至最大值,并且载荷掉落至最大载荷的30%时,停止实验。
2 结果与分析2.1 损伤阻抗性能损伤阻抗性能是指抵抗冲击的能力,可用复合材料冲击后压缩实验的冲击能量-凹坑深度曲线表征。将A,B,C三组试件冲击后的凹坑深度与冲击能量作图,冲击能量-凹坑深度曲线如图4所示。从图4可看出,A,B,C三组试件的冲击能量-凹坑深度关系曲线均存在拐点,在拐点之前,冲击能量增大,凹坑深度增长缓慢,在拐点之后,随着冲击能量的增加,凹坑深度快速增长,表明复合材料在拐点附近损伤阻抗性能发生了突变。出现这种现象的原因为:在拐点以前,冲击损伤只引起层合板少量的分层,而在出现拐点之后,复合材料中出现纤维断裂的现象,导致复合材料层压板基本失去了继续抵抗冲击的能力,从而出现冲击能量增加,复合材料凹坑深度快速增长的现象。三组试件冲击能量-凹坑深度关系曲线拐点位置为:A组0.70 mm,B组0.76 mm,C组0.45 mm,均小于BVID对应的凹坑深度。从图4还可看出,同一冲击能量下,产生的凹坑深度为C组 < B组 < A组,表明相同铺层条件下,层合板厚度越大,抵抗冲击性能越好,即损
表 1 试件铺层、厚度及冲击能量Table 1 Specimen layer, thickness and impact energy
NumberLayer formThickness/mmImpact energy/JA[45/0/-45/90]3s3.4210,15,18,20,22,25,28,30,32,35B[45/0/-45/90]4s4.4615,22,30,35,38,40,42,45,50,55C[45/0/-45/90]5s5.5525,30,36,40,43,45,50,55,60,65Note: 3s, 4s, 5s—repeating 3, 4, 5 times according to lay-up in bracket, then laying up symmetrically.
图 1 Instron 9350全自动落锤冲击试验机Fig. 1 Instron 9350 automatic drop hammer impact testmachine
100.025
2525
0.8
0.8Strain gage location (both sides)
150.03.23.2Indentation/Impactlocation
Specimencenterline
图 2 应变片贴片位置示意图Fig. 2 Schematic diagram of patch position of strain slice
图 3 冲击后压缩实验夹持状态Fig. 3 Clamping state of compression test after impact
148航 空 材 料 学 报第 38 卷伤阻抗性能越好。将实验结果用数据分析软件进行拟合,拟合曲线如图4所示,拟合公式及相关性如表2所示。后续可根据拟合公式计算该材料在不同冲击能量下的凹坑深度。
2.2 损伤容限性能分析损伤容限是材料或结构在受到损伤后保证安全性的能力,即材料受到冲击损伤后剩余压缩强度或压缩破坏应变,可由凹坑深度-剩余压缩强度和凹坑深度-压缩破坏应变曲线表示。将A,B,C三组试件凹坑深度-剩余压缩强度、凹坑深度-破坏应变实验数据作图,并用数据分析软件进行拟合,凹坑深度-剩余压缩强度如图5所示,凹坑深度-破坏应变曲线图如图6所示。从图5可看出,A,B,C三组试件凹坑深度-剩余压缩强度曲线也存在拐点,在拐点之前,剩余压缩强度随着凹坑深度的增加而迅速下降,而拐点之后随凹坑深度的增加而缓慢下降后趋于不变,且A组拐点位置为0.70 mm,B组0.76 mm,C组0.45 mm,与损伤阻抗性能研究中的冲击能量-凹坑深度关系曲线中出现的拐点一致。对于冲击后产生同一凹坑深
度时,其剩余压缩强度表现为:C组 > B组 > A组,表明同一铺层比例条件下,复合材料层合板厚度越大,其损伤容限性能越好。图6中凹坑深度-破坏应变曲线与图5规律一致。将实验结果用数据分析软件进行拟合,凹坑深度(x)-剩余压缩强度(y)曲线拟合公式及相关性如表3所示,凹坑深度(x)-破坏应变(y)曲线拟合公式及相关性如表4所示。可根据拟合公式计算该材料在不同凹坑深度下的剩余压缩强度和破坏应变,方便结构设计。
表 2 试件冲击能量(x)-凹坑深度(y)曲线拟合公式Table 2 Fitting formula of impact energy (x)-dent depth(y) curve
NumberFitting formulaCorrelativity, R2
Ay=0.2310−3180.361+(x145.69)4.90+3180.360.9972
By=0.2309−3009.351+(x220.02)4.26+3009.350.9976Cy=0.2042−1083.641+(x254.48)4.75+1083.640.9967
表 3 凹坑深度(x)-剩余压缩强度(y)曲线拟合公式Table 3 Fitting formula of dent depth (x)-residualcompression strength (y) curve
NumberFitting formulaCorrelativity, R2
Ay=372.48−173.111+(x0.3568)1.08+173.110.9935
By=584.63−182.811+(x0.2225)1.01+182.810.9975Cy=9363.34−190.691+(x0.00094)0.6909+190.690.9894
4.03.53.02.52.01.51.00.50.0
Dent depth/mm
10152530354045505560657020Impact energy/J
ABC
图 4 冲击能量-凹坑深度关系曲线Fig. 4 Relation curves of impact energy vs. dent depth