纯电动汽车动力电池包结构静力分析及优化设计
纯电动汽车制冷工况下电池直冷优化设计

纯电动汽车制冷工况下电池直冷优化设计【原创】纯电动汽车制冷工况下电池直冷优化设计导语:纯电动汽车的快速发展使得电池技术成为了关注的焦点。
然而,在高温环境中,电池的温度过高会对其性能和寿命造成严重影响。
优化设计电池直冷系统成为了解决这一问题的关键。
本文将针对纯电动汽车制冷工况下电池直冷的优化设计,从深度和广度两个方面进行全面评估,为您呈现一篇有价值的文章。
一、电池直冷系统的重要性电池直冷系统是纯电动汽车中关键的热管理系统之一,其主要功能是通过冷却循环将电池温度维持在合适的范围内。
在高温环境中,电池温度过高会导致电池性能下降、寿命缩短甚至发生安全事故。
优化设计电池直冷系统对于提高纯电动汽车的性能和可靠性至关重要。
二、电池直冷系统的设计原则1. 整车设计考虑电池直冷系统的设计需要综合考虑整车结构及布局,以确保冷却的有效性和均匀性。
还需兼顾整车的空间利用率和重量控制,确保冷却系统可以适应各种复杂工况下的使用。
2. 制冷介质的选择制冷介质的选择对于电池直冷系统的效果及寿命有着重要影响。
目前主要有液冷和气冷两种选择,液冷方式能提供更好的冷却效果,但也增加了系统的复杂性、成本和维护难度,气冷方式则更为简单和经济。
3. 循环系统设计循环系统设计需要考虑冷却流量、压降以及泵和风扇的功耗等因素,并在优化设计中兼顾能效和降低系统成本。
4. 散热系统设计散热系统设计包括散热器的选型和布局。
合理的选型和布局能够提高冷却效果,保证散热器能够充分发挥作用,同时减少系统的重量和能耗。
三、电池直冷系统的优化设计1. 设计优化方法为了提高电池直冷系统的效果,可以采用计算流体力学(CFD)模拟等先进的设计方法来优化系统结构和参数。
通过CFD模拟可以分析流体流动特性、温度分布及压力损失等,从而优化冷却循环的设计。
2. 降低热源温度在电池直冷系统中,电池作为主要的热源,降低电池的温度是非常关键的。
可以通过优化散热系统的设计,提高热量传导效率,减少热量积聚,从而降低热源的温度。
新能源汽车电动汽车动力及控制技术设计_毕业设计论文
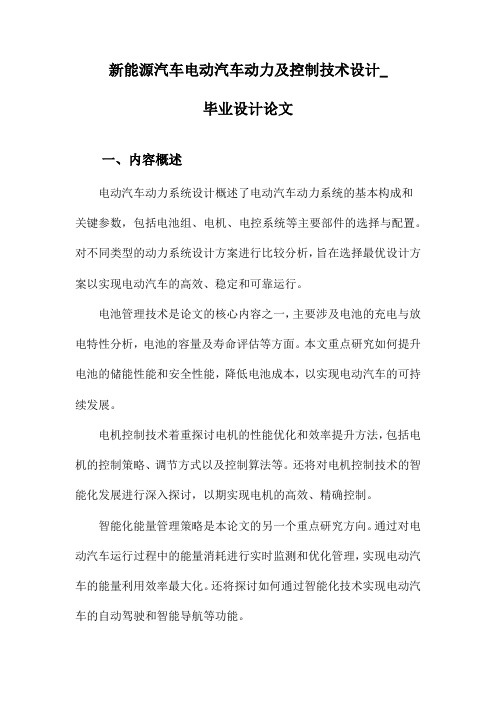
新能源汽车电动汽车动力及控制技术设计_毕业设计论文一、内容概述电动汽车动力系统设计概述了电动汽车动力系统的基本构成和关键参数,包括电池组、电机、电控系统等主要部件的选择与配置。
对不同类型的动力系统设计方案进行比较分析,旨在选择最优设计方案以实现电动汽车的高效、稳定和可靠运行。
电池管理技术是论文的核心内容之一,主要涉及电池的充电与放电特性分析,电池的容量及寿命评估等方面。
本文重点研究如何提升电池的储能性能和安全性能,降低电池成本,以实现电动汽车的可持续发展。
电机控制技术着重探讨电机的性能优化和效率提升方法,包括电机的控制策略、调节方式以及控制算法等。
还将对电机控制技术的智能化发展进行深入探讨,以期实现电机的高效、精确控制。
智能化能量管理策略是本论文的另一个重点研究方向。
通过对电动汽车运行过程中的能量消耗进行实时监测和优化管理,实现电动汽车的能量利用效率最大化。
还将探讨如何通过智能化技术实现电动汽车的自动驾驶和智能导航等功能。
1. 背景介绍:阐述新能源汽车的发展背景,电动汽车的重要性和发展趋势。
在当前社会,新能源汽车的发展已然成为全球汽车工业的大势所趋。
面对环境污染与能源短缺的双重压力,新能源汽车作为绿色、低碳、高效的交通方式,正日益受到全球各国的重视和推动。
尤其是电动汽车,由于其零排放、高效率的特性,已然成为新能源汽车领域中的领军角色。
发展背景:随着科技的进步和社会的发展,传统燃油汽车的排放问题日益凸显,对环境的污染和对资源的消耗引起了全球的关注。
为了应对这些问题,各国政府和企业纷纷转向新能源汽车的研发和生产。
新能源汽车应运而生,它的发展不仅是汽车工业技术进步的体现,更是人类社会对环境友好、可持续发展的追求。
电动汽车的重要性:电动汽车作为新能源汽车的一种,以其独特的优势在市场上占据了重要的地位。
电动汽车具有零排放的特点,它可以有效减少尾气排放,改善空气质量。
电动汽车的能效高,能源利用率远高于传统燃油汽车。
关于纯电动汽车动力传动系统匹配与整体优化

关于纯电动汽车动力传动系统匹配与整体优化摘要:发展新能源汽车成为未来汽车行业的主要趋势,纯电动汽车已经成为社会关注的重点问题。
但是当前纯电动汽车在关键技术等方面还是存在不足,主要集中在续航和充电等两个方面,而如何处理好纯电动汽车动力传动系统匹配,做好系统参数的设置,使汽车在规定电量当中最大限度地提升动力性,保障有效的续航里程成为主要目标。
解决纯电动汽车动力传动系统参数匹配与整体优化具有现实意义。
关键词:纯电动汽车;动力传动系统匹配;整体优化我国汽车尾气排放严重,能源消耗不断地加快,导致传统汽车节能环保问题突出。
而纯电动汽车在结构上更为简单,能源选择多样,与传统汽车相比不会产生加大的噪声,能够更好地控制尾气的排放,逐渐的受到了不同汽车企业的关注,加大了对纯电动汽车的研发力度。
1纯电动汽车结构原理动力系统、电气设备等共同构建成为纯电动汽车的基本结构,并且与内燃机在结构上进行比较,两者最大的差异主要集中在动力系统上,特别是纯动力汽车主要有电力驱动系统、电源管理系统以及辅助系统。
在电力驱动系统运行当中将电池化学能之间的转换为汽车动能,同时还能够在汽车减速等状态下降动能转换为电能直接的存储到电池当中。
功率转换器、机械传动系统、电子控制器等共同构建成为电力驱动系统,对于纯电动汽车整体动力与经济状况等有着直接的影响。
电源系统能够为汽车的行驶提供驱动能源,主要有能量管理系统、充电装置、蓄电池等。
并且能够检测电池的运行状态,开展及时的充电管理。
纯电动汽车辅助功能主要有照明系统、空调系统等。
同时还具有辅助动力源,能够为空调系统等提供及时的电源。
2纯电动汽车动力系统参数匹配设计2.1电机参数设计对于驱动电机纯电动汽车有着较高的要求,与传统电机相比在技术规范上更为严格,这是由于驱动电机关系到汽车的频繁起动和停车的过程有效性,将会承受较大的制动力,特别是纯电动汽车在电机使用上要凸显出瞬时功率、过载能力等特点,需要拥有较为突出的加速性能,要保障其使用寿命较长。
纯电动汽车制冷工况下电池直冷优化设计

纯电动汽车制冷工况下电池直冷优化设计引言纯电动汽车作为一种环保、节能的交通工具,在全球范围内得到了广泛的关注和推广。
然而,纯电动汽车的电池系统在高温环境下容易受到损害,影响其性能和寿命。
因此,如何在制冷工况下对电池进行优化设计,提高其工作效率和稳定性成为一个重要的研究课题。
目标本文旨在探讨纯电动汽车制冷工况下电池直冷的优化设计方案,以提高电池的工作效率和稳定性。
方法为了实现上述目标,我们将采取以下步骤: 1. 研究纯电动汽车电池直冷系统的工作原理和现有设计方案; 2. 分析现有设计方案的优缺点,找出存在的问题和改进空间; 3. 提出优化设计方案,并进行仿真和实验验证; 4. 根据验证结果对优化设计方案进行优化和调整; 5. 最后,总结优化设计方案的效果和应用前景。
研究纯电动汽车电池直冷系统的工作原理和现有设计方案纯电动汽车电池直冷系统的工作原理是通过将制冷剂直接注入到电池包中,通过循环流动的方式,将电池包内部的热量带走,从而降低电池的温度。
目前,纯电动汽车电池直冷系统的设计方案主要有两种:空气直冷和液体直冷。
空气直冷是通过将外界的空气通过风扇吹入电池包进行冷却,而液体直冷则是通过循环流动的制冷剂直接接触电池包进行冷却。
分析现有设计方案的优缺点空气直冷的优点是简单、成本低,但其冷却效果相对较差,特别是在高温环境下。
液体直冷的优点是冷却效果好,能够更有效地降低电池的温度,但其成本较高,且需要额外的冷却系统。
目前,纯电动汽车电池直冷系统存在以下问题: 1. 冷却效果不佳,在高温环境下容易导致电池过热; 2. 成本较高,增加了整车的制造成本; 3. 对冷却系统的要求较高,增加了设计和维护的难度。
提出优化设计方案针对上述问题,我们提出以下优化设计方案: 1. 采用液体直冷系统,以提高冷却效果; 2. 优化制冷剂的选择和循环流动方式,以提高制冷效率; 3. 设计合理的冷却系统,以降低成本和提高可靠性; 4. 结合智能控制技术,实现对电池温度的实时监测和控制,以保证电池的工作稳定性。
CRUISE纯电动车动力性能仿真及优化

虚 拟与仿 真CRU ISE 纯电动车动力性能仿真及优化姜海斌,黄宏成(上海交通大学汽车工程研究院汽车电子控制技术国家工程实验室,上海200240)Simulation and Optimization of the Electric Vehicle s Dynamic Perf ormance on CRUISEJIANG Hai bin,HUANG Hong cheng(N ational Eng ineer ing L abor ator y of Automo tiv e Elect ronics,I nstitute o f Automo tiv e Eng ineer ing,Shang hai Jiao T ong U niv ersity ,Shang hai 200240,China)摘要:以后轮驱动纯电动车为例,利用CRU ISE 软件建立了电动车的动力系统模型,并用此软件模拟得到其动力性能,验证了该模型分析车辆动力性能的可行性.分析了影响续驶里程及最大爬坡度的各种因素,提出的措施和方法能够很好地提高电动汽车动力性能.关键词:纯电动车;建模;CRUISE;续驶里程;优化中图分类号:U 469.7文献标识码:A 文章编号:10012257(2010)04006104收稿日期:20091203Abstract:T aking r earw heel dr iv e as an ex -am ple,the mo del of the electric vehicle is estab -lished in CRUISE.Also this softw are is used to simulate the perfo rmance of the vehicle.T he simu -lation results validate that CRU ISE can analyze the feasibility of vehicle per for mance.Then,various facto rs that affect continued driving range and lar -g est gr adeability ar e analyzed.The applied methods ar e all useful for the improvement of perform anceof the vehicle.Keywords:electricvehicle;m odeling;CRUISE;co ntinued driving rang e;optimization0 引言随着能源和环境对人类生活和社会发展的影响越来越大,全球石油危机和大气污染日趋严重,各种电动汽车也应运而生.纯电动汽车没有内燃机车辆工作时产生的废气,是目前最环保的车型之一[1].与传统的燃油汽车相比,由于电动车所具有的节能、环保优点,使其成为未来汽车产业发展的趋势之一.在研究和开发电动汽车的部件及选择最佳结构时,为缩短开发周期,降低开发成本,缩小研究范围,找到技术的突破口,特别是在技术方案的选择阶段,在系统和关键部件的选择上,可依靠高效的计算机对系统和关键部件进行建模,然后进行模拟仿真,从而找到最佳方案.1 纯电动汽车建模纯电动汽车的建模和动力总成系统的选择,对于整车系统的建立是非常重要的.电动汽车的运行性能主要由动力总成系统来决定.电动汽车动力总成系统的组成部分主要包括电池、电机、离合器、变速箱、减速器以及车轮.本文设计的纯电动车模型和动力总成系统如图1所示.图1 整车模型和动力系统1.1 电机模块电机是纯电动汽车惟一的驱动单元,它的技术性能直接影响到车辆的运行性和经济性.因此,必须按照电动车的技术要求合理地选择电机的参数和指标.在CRU ISE 中,电机的参数设置定义了电机的额定电压,电机在各种工作过程状态中的转矩和转速,电机效率关系以及其它一些参数[2].模型中电机的基本参数如表1所示.表1 电机的基本参数额定转速(r/m in)1430峰值转速(r/m in)5600额定转矩(N m)20峰值转矩(N m)40额定功率(kW)3峰值功率(kW)6额定电压(V)481.2 电池模块电池是制约电动汽车发展的关键因素,目前可采用的电池有铅酸电池、镍镉电池、镍氢电池、锂电池和燃料电池等.铅酸电池虽然比能量比较低,但其技术可靠,生产工艺成熟,成本低,拥有适合电动汽车使用的良好的大电流输出性能以及多种型号和尺寸.考虑到整车的成本,本车型选用了铅酸电池作为动力源.在CRU ISE中,根据电池建模的参数做出电池的SOC与电池电压之间的关系曲线,SOC 值的大小直接反映了电池所处的状态,由此可限定电池的最大放电电流,并可在仿真过程中更精确地计算各种工况下电动车的续驶里程.所选用的电池在试验室经过不同状态下的充放电试验,根据在试验中测得电池电压、电流和放电时间等参数,推断出SOC与电压的关系.2 CRU ISE中建模与仿真CRUISE软件可以用于车辆的动力性,燃油经济性以及排放性能的仿真,其模块化的建模理念使得用户可以便捷地搭建不同布置结构的车辆模型,其复杂完善的求解器可以确保计算的速度.它可用于汽车开发过程中的动力和传动系统的匹配、汽车性能预测和整车仿真计算;可以进行发动机、变速器、轮胎的选型及其与车辆的匹配优化;可以用于混合动力汽车、纯电动汽车的动力、传动及控制系统的开发和优化[3].CRUISE软件的主要特点是:a.模块化的设计思想使得用户能够便捷地进行车辆的整车模型和动力总成系统的建模,并且能够方便地进行修改和优化.b.智能化的驾驶员模块,能够很好的模拟驾驶员的意图.c.M atlab接口模块,使得用户能够使用比较复杂的控制算法.2.1 CRUISE中车辆模型按照上述结构,在CRUISE中进行建模. CRU ISE采用图形化的界面,用户可以从已有的模型箱中选择自己想要的模型.将电池、电机、离合器、变速箱、驾驶员模块以及车轮等模块拖入CRUISE 的工作区中,建立模型.输入系统中各个模块的参数,如车辆模块的满载重量、迎风面积和阻力系数等;电机的电压、转矩和转速等;车轮的摩擦系数;主减速器的主减速比等.在CRUISE仿真时,系统会提示所有必须要输入的参数,按照这个要求,把参数一一输入即可.建立系统的物理连接和信号连接.首先完成物理连接,当各子系统模型选定之后,应根据汽车配置方案和部件连接关系建立模型的物理连接.只需用connect连接功能建立物理连接.传动系各部件之间有直接的物理连接关系,车轮和制动器之间也有物理连接关系,但驾驶室与动力传动系和制动系之间没有物理连接.在仿真过程中,它们之间是通过信号连接来传递信息.信号连接是汽车建模过程中比较关键内容之一,也有较大难度.要想正确建立汽车各子模型之间的信号连接关系,必须对汽车系统内部各部件之间的连接、控制关系以及信息传递关系,有比较深刻的理解.如驾驶员模块需要连接来自电机的转速信号,变速箱的档位信号等;制动器需要连接制动压力信号;摩擦离合器需要来自驾驶员期望的结合程度[4].系统需要把所需的信号连接全部定义准确,如果有一个错误,那么将无法运行仿真程序.2.2 仿真及结果分析根据纯电动汽车仿真的要求,选择和编辑相应的任务及工况,设置合适的仿真步长和精度进行仿真计算.设定的计算任务有:在任务Cycle Run中仿真续驶里程;在任务Climbing Per for mance中仿真最大爬坡度;在任务Constant Dr iv e中仿真最高速度.运行CRUISE,得到仿真结果如下所述.a.续驶里程.建立一个25km/h匀速行驶工况,通过对电池SOC的变化对应的时间来得到纯电动车的续驶里程所需要的电量值.运行这个任务,得到纯电动车的SOC变化图.考虑到电池的输出效率为85%,得到当电动汽车以25km/h行驶100km 后,电池所消耗的电量约为130.6A h,行驶120km所消耗的电量为156.8A h.和理论所求得结果一致.b.爬坡性能.根据CRUISE软件result的报告,可以得到最大爬坡度和最高速度确切值.爬坡表现:档位,1;最大爬坡度,15.43%;车速,5.00km/ h;电机转速,602.86r/min;速度率,0.00.最大车速理论值,51.41km/h;实际值,43.71km/h.从仿真结果可以看出,根据目前车辆的参数,当电池的容量为160A h时,在25km/h的匀速运行工况下,电动汽车的续驶里程约为120km.电动汽车的最大爬坡度为16.05%,最高速度为43.71 km/h.与通过汽车理论计算得到以及车辆所要求的性能参数基本一致.这证明了利用CRU ISE软件对车辆整车性能仿真和分析是可行的.3 整车性能影响因素分析3.1 续驶里程设f为滚动阻力系数;r为轮胎滚动半径;m为汽车总质量;i g为传动系速比;C D为迎风阻力系数; t为传动系效率;A为迎风面积;Q为电池的额定容量;U E为电池的端电压; 为电机效率.则汽车以速度v等速行驶时所需的电机输出扭矩M和功率P 分别为:M=(f m+C D A v2/21.15)ri g t(1)P=(f m+C D Av2/21.15)(v/3.6)ri g t(2)电池携带的额定总能量为:W0=QU E(3)理想状态下等速行驶的续驶里程s为:s=W0vP/=QU E vP(4)从式(4)可以看出,在整车携带的电池总量和电池比能量不变的条件下,续驶里程指标与行驶阻力功率P有关[5].而行驶阻力功率又与滚动阻力系数f,迎风阻力系数C D,整车总质量m,迎风面积A,车速v,传动系效率 t,车轮半径r和传动系速比i g 有关.以电动车参数(总质量m=1100kg;f= 0 012;A=3m2;C D=0.45; t=0.9;r=0.26m)为例作分析.a.不同等速v对续驶里程的影响.在不同速度的匀速状态下运行,车辆的续驶里程是不同的[6].设置电池的电量为160A h(为确保安全,视电量剩20%时一次运行结束),不同匀速行驶状态对车辆的续驶里程的影响,如图2所示.图2 不同匀速行驶状态下车辆续驶里程的影响从图2中可以看到,各种不同的匀速行驶中,以速度接近零行驶时,车体所消耗的能量最小,对于拥有固定能量的系统来讲,其续驶里程也最长.因此,若想增加续驶里程,应尽可能以低速行驶.b.整车参数对续驶里程的影响.图3,图4和图5分别表示在匀速25km/h行驶下,迎风阻力系数C D,滚动阻力系数f和整车总质量m对一次充图3 迎风阻力系数对续驶里程的影响图4轮胎滚动阻力系数对续驶里程的影响图5 整车总质量对续驶里程的影响电续驶里程的影响.可见携带能源极为有限的电动汽车对降低滚动阻力系数、迎风阻力系数和整车总质量的要求非常迫切.c.电池参数对续驶里程的影响.由式(4)可知,电动汽车携带的电池总量以及电池的端电压的大小都会影响续驶里程,并且它们与续驶里程成正比.可见提高电池的最大容量及电池端电压,对提高电动汽车续驶里程意义重大.另外,电池放电效率同样对续驶里程有着重要的影响,电池放电效率越高,续驶里程的数值也越大.d.电机对续驶里程的影响.电机参数中电机的效率 对续驶里程的影响最大.效率越高,续驶里程的数值越大.同时在各种工况下的效率对续驶里程的影响更大.因此对电动车用电机而言,不仅要求电机在额定状态下具有较高的效率,而且要求电机具有很宽的高效率区域,这样才能在各种行驶工况下充分利用有限的能量.对此,提出了增加一次充电续驶里程的措施:尽可能选择较低的行驶速度;降低轮胎的滚动阻力系数,选用低阻力轮胎;降低迎风阻力系数,进行车身的流线型改进;减轻汽车总质量;扩大电机的高效区范围及提高电机效率.3.2 最大爬坡度汽车的最大爬坡度,是指汽车满载时在良好路面上用第一档克服的最大坡度,它表征汽车的爬坡能力.爬坡度用坡度的角度值(以度数表示)的百分数来表示.设T tq为电机最大转矩;i g为变速器加速档传动比;i0为主减速器传动比; t为传动系的机械效率;r 为轮胎半径.则对于电动汽车来说,车辆的最大驱动力为[7]:F t=T tq i g i0 tr(5)而车辆的滚动阻力F f=mf cos ,坡度阻力为F i=m sin ,加速阻力.同时由于在计算最大爬坡度时车速很小,故可忽略空气阻力F W.由驱动力行驶阻力平衡公式F t= F=F f+F W+F i+F j,得到最大爬坡度 max的计算公式为:T tq i g i0 tr=mf cos max+m sin max(6)由式(6)可以看出,最大爬坡度与电机最大转矩T tq、轮胎半径r、整车总质量m和滚动摩擦系数f 等参数有关.a.电机参数对最大爬坡度的影响.在电机参数中,电机最大转矩的大小与车辆最大爬坡度的大小有着直接的联系[8].电机的最大转矩越大,最大爬坡度也越大.因此,从电机方面来说,若想提高车辆的爬坡性能,可以通过提高电机的最大转矩来实现.b.车辆参数对最大爬坡度的影响.图6,图7分别表示轮胎滚动阻力系数f和整车总质量m对车辆最大爬坡度的影响.从图6,图7中可见,轮胎滚动阻力系数和整车总重量都对最大爬坡度有很大的影响[9].要想获得合适的最大爬坡度,就必须合理地设置这2个参数.图6轮胎滚动阻力系数对最大爬坡度的影响图7 整车总质量对最大爬坡度的影响对此,提出了增加爬坡性能的措施:选择拥有较高最大转矩的电机;降低轮胎的滚动阻力系数,选用低阻力轮胎;减轻汽车总重量.4 结束语运用CRUISE软件对纯电动车进行建模和动力性能的仿真,得到了续驶里程、最大速度及最大爬坡度等指标,仿真结果验证了CRU ISE仿真动力性能的可行性.通过本文的仿真和分析,为电动汽车的参数选择以及结构优化提供了依据.参考文献:[1] 康龙云.电动汽车最新技术[M].北京:机械工程出版社,2008.[2] 王 斌,李 征,等.CR U ISE 软件在混合动力汽车性能仿真中的应用[J].计算机应用,2007,9(3):1-3.[3] 赵海峰.基于CR U ISE 软件的AM T 车辆性能仿真分析与实验研究[D].重庆:重庆大学,2005.[4] 王保华,罗永革.基于CRU ISE 的汽车建模与仿真[J].湖北汽车工业学院学报,2005,19(2):2-3.[5] 李国良,初 亮,鲁和安.电动汽车续驶里程的影响因素[J].吉林工业大学自然科学学报,2000,30(3):1-3.[6] 杜发荣,吴志新.电动汽车传动系统设计与续驶里程研究[J].农业机械学报,2006,37(11):3-4.[7] 余志生.汽车理论.3版[M ].北京:机械工程出版社,2000.[8] Cheng Chang T ing.H y br id electric vehicle design tominimize ener gy use [C].T he U niv ersity of T ex as at A rling ton,2000.[9] Sha Y L.T he pow er desig n and calculation o f EV S[A].T he 16t h Inter nat ional Batter y,H ybrid and F uel Cell Elect ric Vehicle Symposium &Ex hibitio n [C ].Beijing ,1999.作者简介:姜海斌 (1985-),男,江苏张家港人,硕士研究生,研究方向为汽车动力系统仿真以及汽车系统控制等;黄宏成 (1972-),男,江苏苏州人,副教授,研究方向为汽车系统控制以及底盘开发.ARM 7参数自整定模糊PID 控制器的仿真及设计王朝宁1,姜学东1,马立刚2(1.北京交通大学电气工程学院,北京100044;2.山西省电力公司吕梁供电分公司,山西吕梁033000)Design and Simulation of Self tuning PID type Fuzzy Controller Based on A RM 7ProcessorWANG C hao ning 1,JIANG Xuedong 1,MA Li gang 2(1.Schoo l o f Electrica l Eng ineering ,Beijing Jiaoto ng U niver sity,Beijing 100044;2.Shanx i L vliang P ower Supply Co mpany ,L v liang 033000,China)摘要:常规PID 控制器参数设定之后,运行环境改变时不能实现参数的在线整定,这样会影响系统的控制效果.本设计以误差e 和误差变化率ec 作为输入,经过一定的模糊推理规则,对PID 控制器的参数进行自动整定.在M atlab 环境下对系统进行了仿真,从仿真的结果可以看出,添加模糊控制环节后,系统的动静态性能得到了提高.同时基于ARM 7处理器完成了该控制器的软硬件设计.关键词:参数自整定模糊控制PID;M atlab;ARM 7处理器中图分类号:T P273文献标识码:A 文章编号:10012257(2010)04006505收稿日期:20091203Abstract:When operating environmentchang ed,the traditio nal PID contro ller can t online regulate its parameters,w hich are co nfigured w ellat the beginning.And that w ould affect contro l per for mance o f system.Taking erro r and decay r ate of err or as inputs in the desig n,arg um ents o f PID contro ller can reach self tuning function,as to some accurate fuzzy sets.From the result of simu -latio n done w ith M atlab,dy namic and static per -formances of system added fuzzy controller are im -proved.T he autho r also com pleted the hardw are and so ftw are desig n of the contro ller based on ARM7processor.Key words:self tuning PID type fuzzy con -troller;M atlab;ARM7processor0 引言模拟PID 闭环控制在常规的电源控制技术中应用很普遍,效果比较理想并且稳定,但其缺点是一。
动力电池包结构轻量化优化设计

动力电池包结构轻量化优化设计
王顺俗
【期刊名称】《机电技术》
【年(卷),期】2022()6
【摘要】动力电池包的轻量化是电动汽车续航里程的重要影响因素之一,文章对电池包结构进行了轻量化优化设计。
通过对电池包在3种典型测试工况中进行动静态分析,得出电池包结构的薄弱点;设计了以电池包单元节点位移、结构刚度以及低阶模态频率为约束条件的优化模型,对电池包箱体上盖进行轻量化设计。
结果表明:优化后的电池包箱体上盖在各工况下最大变形量均大幅度减小,低阶固有频率增大,规避了路面激励频率,同时箱体质量降低了11.25%,实现了动力电池包的轻量化优化。
【总页数】5页(P61-65)
【作者】王顺俗
【作者单位】东南(福建)汽车工业股份有限公司
【正文语种】中文
【中图分类】U469.72
【相关文献】
1.基于多学科优化的锂离子动力电池包轻量化设计
2.纯电动汽车动力电池包结构轻量化设计
3.动力电池包轻量化设计技术研究
4.车载动力电池包的有限元分析及轻量化设计
5.动力电池结构仿真分析及轻量化优化
因版权原因,仅展示原文概要,查看原文内容请购买。
某电动汽车电池包强度仿真分析与优化

某电动汽车电池包强度仿真分析与优化作者:夏宇锋来源:《科学与财富》2019年第08期摘要:通过对某电动汽车电池包结构强度仿真分析,探测电池包强度薄弱区域,找出电池包在整车工况载荷下结构容易失效的风险点。
通过电池包结构改进优化,消除电池包结构风险点,保证电池包及整车强度安全。
关键词:电池包;CAE;强度;失效0 引言新能源汽车、智能化汽车、互联网汽车是目前汽车发展的三大主流方向。
据统计截至2017年,我国汽车保有量2.17亿辆,燃油汽车已成为能源消耗的主要领域,为解决能源危机,中国政府对新能源汽车发展高度重视并大力扶持。
汽车行驶时,路面的凹凸不平会使电池包受到振动载荷。
电池包强度需要满足国家强制检测标准GB/T 31467.3-2015《电动汽车用锂离子动力蓄电池包和系统第3部分:安全性要求与测试方法》,电池包要经受X/Y/Z三个方向机械冲击载荷试验。
在工程设计阶段,若采用物理样机试验验证电池包结构强度破坏区域,开发周期不便于控制,经济成本也高。
使用CAE技术可以把试验时间压缩至原来的十分之一甚至百分之一,大大降低了开发成本,缩短了开发周期[1]。
当前,工程中常采用CAE技术进行电池包结构强度校核、改进,使开发周期和经济成本有利控制。
本文基于电池包的原始结构,按照试验工况,首先进行CAE结构仿真分析,探测电池包易破坏的风险区域,对风险区域提出结构优化改进方案,保证电池包的机械强度安全。
1 电池包CAE分析流程及建模1.1 CAE分析流程CAE技术的核心思想是结构的离散化[2]。
本文CAE分析流程如图1:1.2建立有限元模型(1)电池包三维模型处理电池包的初始三维模型如图2所示:(2)电池包三维模型几何清理清理电池包模型干涉问题,去除电池包模型中的尖角、圆角等细微特征,避免出现网格划分精度及网格畸异造成仿真结果失真。
(3)电池包载荷类型根据电池包国家强制检测标准GB/T 31467.3-2015《电动汽车用锂离子动力蓄电池包和系统第3部分:安全性要求与测试方法》,电池包要进行机械冲击试验,因此电池包需要进行垂直Z方向3g,水平X方向4g及水平Y方向4g冲击载荷,如下表1所示。
电动汽车动力电池管理系统的设计与研究

AUTOMOBILE DESIGN | 汽车设计时代汽车 电动汽车动力电池管理系统的设计与研究纪文煜无锡南洋职业技术学院 江苏省无锡市 214081摘 要: 能源危机和生态危机产生的人类生存压力越来越明显,汽车产业受能源危机和生态危机的双重影响,电动汽车的研发俨然是大趋势。
电动汽车的问世减少了环境污染,缓解了生态压力,而其也减少了能源消耗,在解决能源枯竭问题方面有着积极意义。
其研发与应用得益于其电池管理系统的设计优化,这也是新型能源汽车研发中的核心命题。
本文主要就电动汽车所对应的电池管理系统进行设计方面的系统研究,以通过硬件与软件的系优化设计,带来电池管理系统的优化,带来电动汽车研发的新革命,使得其性能逐步提升,助力新能源汽车产业的创新发展。
关键词:电动汽车 动力电池 管理系统 设计分析汽车产业是市场经济中的一大主导产业,其快速发展的背后也引发人类关于生态性问题、能源利用问题的深刻思考,当前生态危机加剧,能源紧张的现实让部分产业发展受限,而汽车产业首当其冲。
鉴于传统汽车产业发展的不足,研究新能源汽车成为备受瞩目的课题,而电动汽车的问世无疑为汽车行业的转型升级带来曙光。
对于电动汽车设计研发和性能发挥、来说,起核心作用的是电池,而其对应的系统设计是重中之重,电池作为其能量源泉,其系统则负责能量来源——电池运行情况的分析、数据的采集、故障的判断、运动控制等,系统性能优劣对汽车安全性和功能性发挥的影响是直接而深刻的。
1 电动汽车动力电池工作原理当前汽车的动力电池多对为金属燃料,主要构成是铝,基于其材料选择和性能循环的优化考虑,电池负极为金属材料,正极则采用泡沫石墨烯,其电解液主要成分是四氯化铝,实现了充放电的有效循环,即使在常温条件下也可以正常循环运作。
其正极所对应的石墨烯材料属于典型的层状材料,其能有效容纳阳离子,实现电解液内阴离子的容纳,让动力电池放电形成良性循环。
2 电动汽车电池管理系统设计的三大技术支持2.1 参数检测与分析工作参数检测是动力电池管理系统设计中首先要考虑的问题,工作参数检测涵盖多个方面,从工作电力到电压再到电温等,在这些工作参数检测的过程中[1],重点是进行单体电池的电压具体数值的测量,进行电压稳定性分析,以此明确电池工作状态。
- 1、下载文档前请自行甄别文档内容的完整性,平台不提供额外的编辑、内容补充、找答案等附加服务。
- 2、"仅部分预览"的文档,不可在线预览部分如存在完整性等问题,可反馈申请退款(可完整预览的文档不适用该条件!)。
- 3、如文档侵犯您的权益,请联系客服反馈,我们会尽快为您处理(人工客服工作时间:9:00-18:30)。
纯电动汽车动力电池包结构静力分析及优化设计 纯电动汽车动力电池包结构静力分析及优化设计 摘要: 动力电池包作为纯电动汽车的唯一动力源,承受着电池组等模块的质量,因此其强度、刚度必须满足使用要求才可以保证行驶的安全性。在建立其有限元模型的基础上,分析了电池包结构在弯曲工况、紧急制动工况、高速转弯工况、垂直极限工况以及扭转工况下的强度、刚度。分析结果显示,在垂直极限工况下,电池包底板的受力情况最为恶劣,因此对原有模型做出了改进,改变底板加强筋的布置形式。经过相同工况的模拟,发现在力学性能提升的基础上,整体质量得以减轻,实现了轻量化的目标。
关键词: 动力电池包 有限元法 静力分析 优化设计 Abstract: As the only power source of pure electrical vehicle,the power battery pack bears the weight of several models such as the battery model. To ensure the safety,the pack’s strength and stiffness must meet the fundamental requirements. This paper mainly analyzed the strength and stiffness under different working conditons on the base of a finite element model. The rsult shows that and the corresponding stress and deformation graphs are obtained.The structure of the battery pack is improved after analyzing the causes of the stress concentration.Also, the performance of the new model is compared with the original one.The results show that the weight of the structure is reduced while the performance of the structure is improved, and the lightweight of the vehicle is realized.
Keywords: power battery pack finite element method static structural analysis optimal design DC01 210 270 7.85 0.30 2.07e5 1.4计算工况 由于此款电池包应用于微型纯电动汽车,其主要在城市路面上行驶,因此对其在行驶过程中可能遇到的五种工况进行分析。即弯曲、制动、转弯、垂直极限和扭转五种工况。 1.4.1弯曲工况分析 电池包满载静止工况主要是用来模拟电动汽车静止或者在路况较好的路面上行驶时的结构应力分布及变形情况。在这种工况下,电池包主要受到的载荷是包括电池包中的电池模块、控制模块以及连接部件等质量在重力加速度作用下所产生的重力。 1.对结构施加的载荷 由于电池包结构通过七个螺栓与车身相连接,所以电池包结构只需要承载电池包自身的重力即可而无需考虑到整车上的乘员以及货物的质量。该电池包的整备质量为140kg,取重力加速度g=9.8N/m2。因此要对结构施加的载荷为F=mg=140*9.8=1372N。在有限元模型中,将载荷施加在结构的重心上。 2.分析结果 经过ANSYS软件分析计算之后,得到了电池包结构的应力与应变云图,如图1.1。
图1.1电池包满载弯曲工况应力云图 从图中的数据可以看出,结构中应力最大处的应力为85.775MPa,出现在吊耳和底部支撑加强筋的边缘,这主要是因为电池包尺寸较大,加强筋的跨度比较大加之处在电池包的两端,因此应力会比较集中。但是最大应力85.775MPa仍远小于材料的屈服极限, 因此结构是安全的。 图1.2电池包满载弯曲工况应变云图 从应变云图中,可以看出最大变形量为0.78823mm,出现在承重底板的中心处。这样的变形量虽然不是很大,不影响结构的使用功能,但是还有较大的优化空间。 1.4.2制动工况分析 电池包高速制动工况将模拟车辆在行驶过程中紧急制动时的载荷情况。车辆在制动时,电池包除了承受自身的重力外,还将受到纵向制动加速度引起的惯性力作用。而惯性力的大小则主要取决于制动加速度的大小以及电池包的重量这两个参数。 1.对结构施加的载荷 车辆的最大制动加速度可近似由如下关系式求得,即a=v2/2s,v为车辆的行驶速度,s为将制动踏板处于最大行程所得制动距离。测得最大制动加速度为0.8g=7.84m/s2。对电池包的重心施加载荷,载荷分为两部分,其一是电池包本身的重力F1=mg=140*9.8=1372N,其二则是作用在电池包上的惯性力F2=ma=140*0.8*9.8=1097.6N。 2.分析结果 经过分析,得到车辆在满载时高速制动工况下应力、应变分布云图。
图1.3电池包满载制动工况应力云图 图1.4电池包满载制动工况应变云图 从图中可以看出电池包的最大应变值为0.78897mm,最大变形的位置仍然在底板的中心位置,最大应力值为84.165MPa,主要集中与底部支撑加强筋的边缘与x方向的两个吊耳上。为了得出吊耳具体的受力应变应力情况,我们将对吊耳进行局部的有限元分析,对其进行单独的模型建立,并且划分网格,将吊耳所受到的载荷独立地施加在吊耳上,以此来分析吊耳的受力情况。对吊耳的上侧方形凸台面上受力的圆环面施加-Z方向,大小为F=20*9.8=196N的力,同时在受制动惯性力的圆柱面上施加-X方向,大小为156.8N的力。 由于吊耳通过点焊方式与电池包主体结构连接,所以对8个焊点连接处设置固定约束。
图1.5吊耳网格 图1.6制动工况下吊耳应力云图 由应力云图可以看出,吊耳最大应力为23.036MPa,应力比较集中的地方在吊耳下方的焊点处和上方方形凸台的外侧边缘,因为外缘的材料较少所以应力会比较集中,但还是远远小于材料的屈服极限的,因此结构是安全的。
1.4.3转弯工况分析 车辆在高速转弯时,车身因离心力作用而产生侧向载荷,由于动力电池包是与车身连接在一起的,所以在车辆高速转弯时,电池包也将承受一定的侧向载荷。离心加速度的大小由转弯半径与行驶车速的高低决定。在此工况下电池包需要承受的是自身的重力与离心力载荷。 1.对结构施加的载荷 对于高速转弯工况,在电池包上附加0.5g的侧向加速度来模拟转弯工况下电池包结构所受的载荷。所以要施加的载荷为两部分,其一是电池包的自重F1=140*9.8=1372N,其二是指向一侧的离心力,不妨取离心力方向是向左的,即F2=140*0.5*9.8=686N。 2.分析结果 图1.7转弯工况应变云图 由上图可以看出,应变较大的地方在支承电池组的地板中心处,应变最大值为0.79192mm。因此在之后的结构改进工作中要对此进行优化。
图1.8 吊耳应力云图 由于离心力载荷施加的是向左,所以位于电池包左右两侧的吊耳所受的拉压应力会略偏大。但是其最大应力值的为85.768Mpa,还是小于材料的屈服极限的。
1.4.4垂直极限工况分析 垂直极限工况是指车辆行驶在凹凸不平路面上时,发生垂直方向的颠簸从而产生垂直方向的载荷,引起结构发生变形的工况[1]。 1.对结构施加的载荷 在此工况下会发生的极限情况,就是车辆垂直方向载荷的变化,根据相关文献[2],此工况下可以达到的最大垂向加速度为1g,再加上电池包本身的重力加速度,因此要施加的载荷力F=2mg=2*140*9.8=2744N。 2.分析结果 图1.9 垂直极限工况结构应变云图 图1.10垂直极限工况结构应力云图 由上图可以看出,在2g垂向载荷作用下电池包底部的变形是相当明显的,最大应变值达到了1.5765mm,最大应力值达到了171.55MPa。因此加强支承底板中心处的强度是非常必要的。
4.3.5扭转工况分析 当电动汽车行驶在凹凸不平的路面上时,会发生某个车轮被抬高而另一个车轮悬空的情况。此时,由于车辆的左右两侧受力不对称,电池包会产生就比较剧烈的扭转,如果结构不能保证足够大的扭转刚度,那么电池包结构就会发生严重的变形,从而导致电池包内部的电池受到挤压,最终会发生电池组错位、电池溶液泄露、短路等危险现象[3]。 1.对结构施加的约束与载荷 当电池包的两侧受到不对称的载荷时,就会由于有扭矩的作用而使得电池包产生扭转变形,在此工况下,设置两边的受力差值为1500N,即在电池包的一侧施加大小为1500N的力,另一侧进行固定,对有两个吊耳的一侧施加固定约束,有三个吊耳的一侧的限制X、Y方向的自由度,最后分析受力一侧的挠度,从而可以求得电池包的扭转刚度。 2.分析结果 图1.11扭转工况应变云图 图1.12宽为93mm吊耳扭转工况应力云图 由图中可以看出,扭转工况下的最大应变出现在受力一侧最大应变值为0.36355mm,在1500N的集中力作用下,这样的变形量还不足以使得电池发生错位,因此,电池包结构具有足够的扭转刚度。而此时最大应力值为190.95MPa,主要集中于电池包的宽为93mm的吊耳上。
2.电池包结构优化设计 2.1结构存在问题综述 综合前述对电池包结构的静力学分析,我们可以发现2个共性的问题。 1.在四种工况下,电池包底部支承板加强筋的边缘应力都比较集中。 2.电池包底部支承板的中心变形较大。 2.2改进方案