选取氮化硅和二氧化硅作为薄膜材料
反应离子刻蚀氮化硅与二氧化硅工艺的研究
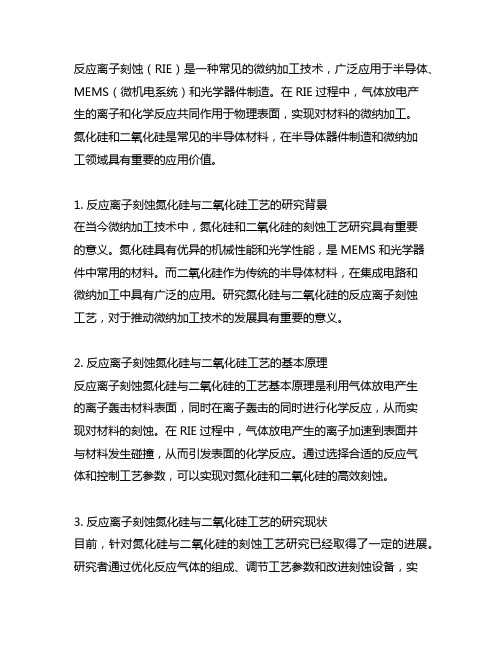
反应离子刻蚀(RIE)是一种常见的微纳加工技术,广泛应用于半导体、MEMS(微机电系统)和光学器件制造。
在RIE过程中,气体放电产生的离子和化学反应共同作用于物理表面,实现对材料的微纳加工。
氮化硅和二氧化硅是常见的半导体材料,在半导体器件制造和微纳加工领域具有重要的应用价值。
1. 反应离子刻蚀氮化硅与二氧化硅工艺的研究背景在当今微纳加工技术中,氮化硅和二氧化硅的刻蚀工艺研究具有重要的意义。
氮化硅具有优异的机械性能和光学性能,是MEMS和光学器件中常用的材料。
而二氧化硅作为传统的半导体材料,在集成电路和微纳加工中具有广泛的应用。
研究氮化硅与二氧化硅的反应离子刻蚀工艺,对于推动微纳加工技术的发展具有重要的意义。
2. 反应离子刻蚀氮化硅与二氧化硅工艺的基本原理反应离子刻蚀氮化硅与二氧化硅的工艺基本原理是利用气体放电产生的离子轰击材料表面,同时在离子轰击的同时进行化学反应,从而实现对材料的刻蚀。
在RIE过程中,气体放电产生的离子加速到表面并与材料发生碰撞,从而引发表面的化学反应。
通过选择合适的反应气体和控制工艺参数,可以实现对氮化硅和二氧化硅的高效刻蚀。
3. 反应离子刻蚀氮化硅与二氧化硅工艺的研究现状目前,针对氮化硅与二氧化硅的刻蚀工艺研究已经取得了一定的进展。
研究者通过优化反应气体的组成、调节工艺参数和改进刻蚀设备,实现了对氮化硅和二氧化硅的高质量刻蚀。
还有一些研究致力于在RIE 过程中减小残留应力、改善表面粗糙度和控制刻蚀剩余物等问题,以满足不同领域对于氮化硅和二氧化硅材料加工的要求。
4. 反应离子刻蚀氮化硅与二氧化硅工艺的发展趋势随着微纳加工技术的不断发展,反应离子刻蚀氮化硅与二氧化硅工艺将会朝着更加高效、精密和可控的方向发展。
未来的研究重点可能集中在以下几个方面:一是针对特定器件和应用领域的工艺优化,提高刻蚀质量和加工效率;二是开发新型的反应气体和刻蚀设备,拓展氮化硅与二氧化硅的刻蚀工艺窗口;三是结合表面修饰技术,实现对氮化硅和二氧化硅表面特性的精细调控。
氮化硅薄膜2007

等离子体增强化学气相沉积
1、PECVD工艺温度大约 在400°C。 低温工艺优点:淀积速 率高;容易获得比较均 匀的组分;通过改变气 流比可以使薄膜组分连 续变化;节省能源,降 低成本;提高产能;减 少了高温导致的硅片中 少子寿命衰减。
2、提高了膜厚及成分的 均匀性、得到的薄膜针 孔少、组织致密、内应 力小、不易产生裂纹。 3、薄膜对基体的附着力 大于普通CVD。
目前,氮化硅薄膜的主要制备技 术主要有: 1.常压化学气相沉积 (APCVD) 2.低压化学气相沉积 (LPCVD) 3.等离子体增强化学气相沉积 (PECVD)
常压化学气相沉积
I.
常压化学气相沉积是 在常压环境下,反应 气体受热后被N2或Ar 输运到高温基片上经 化合反应或热分解生 成固态薄膜。
薄膜选择 氮化硅薄膜的制备方法 LPCVD和PECVD的比较
总结
薄膜选择
当上式分子为0,即n0 ns =n12时,反射最小。 对于电池片,n0 =1, ns =3.42,则n1 =1.86。 对于组件, n0 =1.46,ns =3.42,则n1=2.23。 考虑到实际情况,一 般选择薄膜的折射率 在2.0~2.1之间。
II.
等离子体增强化学气相沉积
在真空下,加上射频或微波 电场,使反应室气体发生辉 光放电,在辉光放电所形成 的等离子体场中,由于电子 和离子的质量相差悬殊,两 者通过碰撞交换能量的过程 比较慢,所以在等离子体内 部没有统一的温度,就只有 电子气温度和离子温度。此 时,电子气的温度约比普通 气体分子的平均温度高10100倍,电子能量为1-10eV, 相当于温度100000K,而气 体温度都在1000K一下。 从宏观上看来,这种等离子 体温度不高,但其内部却处 于受激发状态,其电子能量 足以使分子键断裂,并导致 具有化学活性的物质(活化 分子、原子、离子、原子团 等)产生,使本来需要在高 温下才能进行的化学反应, 当处于等离子体场中时,在 较低温下甚至在常温下就能 在基片上形成固态薄膜。
薄膜材料之氮化硅薄膜的PECVD生长介绍

总结
氮化硅薄膜应用很广泛,且应用 PECVD方式生长较好。
谢 谢!
射频功率
射频功率是PECVD 工艺中最重要的参数之一。
当射频功率较小时, 气体尚不能充分电离, 激活效率低, 反 应物浓度小, 薄膜针孔多且均匀性较差, 抗腐蚀性能差;
当射频功率增大时, 气体激活效率提高, 反应物浓度增大, 并且等离子体气体对衬底有一定的轰击作用使生长的氮化 硅薄膜结构致密, 提高了膜的抗腐蚀性能;但射频功率不能 过大, 否则沉积速率过快, 会出现类似“溅射” 现象影响薄 膜性质
300~600K
高温对氮化硅薄膜制备工艺的影响:
高温不仅会使基板变形,而且基板中的缺陷会生 长和蔓延,从而影响界面性能
PECVD制膜的优点:
均匀性和重复性好,可大面积成膜;
可在较低温度下成膜;
台阶覆盖优良; 薄膜成分和厚度易于控制;
适用范围广,设备简单,易于产业化
生成氮化硅薄膜的反应如下:
薄膜分子热运动
设备
直接法生长设备
间接法生长设备
注意事项:
1.要求有较高的本底真空; 2.防止交叉污染; 3.原料气体具有腐蚀性、可燃性、爆炸性、易
燃性和毒性,应采取必要的防护措施。
检验
对薄膜来说, 折射率是薄膜成分以及致密程度的综合指标, 是检验薄膜制备质量的重要参数
不同腔体气压 射频功率 温度 NH3 流量
PECVD 法生长氮化硅薄膜
主要内容:
PECVD介绍 氮化硅薄膜介绍 生成
物理气相沉积(PVD) 离子束溅射镀膜
薄膜制备方式
脉冲激光沉积镀膜
化学气相沉积(CVD)
常压CVD 低压CVD
PECVD 激光增强CVD
CVD介绍
氮化硅薄膜窗格制备

氮化硅薄膜窗格制备简介氮化硅(Si3N4)薄膜窗格是一种常用的光学材料,具有高透明性和耐高温性能。
本文将详细介绍氮化硅薄膜窗格的制备方法和应用领域。
制备方法1. 材料准备•硅片:选择高纯度的硅片作为基底材料。
•氮化硅前驱体:常用的有SiH4和NH3。
•氮化硅薄膜沉积设备:如PECVD(等离子体增强化学气相沉积)设备。
2. 氮化硅薄膜沉积1.清洗硅片:将硅片放入酸性溶液中清洗,去除表面的杂质和氧化物。
2.硅片预处理:将清洗后的硅片放入PECVD设备中,在高温下进行表面处理,增加氮化硅薄膜的附着性。
3.氮化硅薄膜沉积:将氮化硅前驱体导入PECVD设备,通过高频电场激发产生等离子体,使氮化硅前驱体分解并沉积在硅片表面形成氮化硅薄膜。
4.氮化硅薄膜退火:将沉积好的氮化硅薄膜进行热退火处理,提高薄膜的致密性和光学性能。
3. 薄膜窗格制备1.薄膜切割:使用激光切割或机械切割等方法将氮化硅薄膜切割成所需的尺寸和形状。
2.边缘抛光:对切割好的氮化硅薄膜进行边缘抛光处理,提高窗格的光学质量。
3.清洗和检验:将窗格放入清洗液中去除切割和抛光过程中产生的污染物,并进行光学性能的检验。
应用领域1. 光学仪器氮化硅薄膜窗格在光学仪器中广泛应用,如激光器、光谱仪、显微镜等。
其高透明性和耐高温性能使其成为优秀的光学窗口材料,能够提供良好的光学性能和稳定的工作环境。
2. 光伏领域氮化硅薄膜窗格在光伏领域中用作太阳能电池的保护窗口材料,能够有效防止湿气和灰尘对太阳能电池的影响,提高太阳能电池的转换效率和长期稳定性。
3. 环境传感器氮化硅薄膜窗格还可用于制备气体传感器和湿度传感器等环境传感器。
其高透明性和耐腐蚀性能使其能够在恶劣环境下工作,并提供准确可靠的传感性能。
4. 生物医学领域氮化硅薄膜窗格在生物医学领域中用于制备生物传感器和生物芯片等。
其生物相容性和生物相互作用性能使其成为生物医学研究和临床应用的重要材料。
结论氮化硅薄膜窗格制备是一项关键的工艺技术,通过合理的材料选择和沉积工艺,可以得到高质量的氮化硅薄膜窗格。
CVD法氮化硅薄膜制备及性能

CVD法氮化硅薄膜制备及性能发表时间:2019-07-18T09:35:03.353Z 来源:《科技尚品》2019年第2期作者:王莉[导读] 氮化硅被作为一种高效的器件表面钝化层广泛应用于半导体器件工艺中。
本文论述了CVD法氮化硅薄膜制备及其性能。
中芯国际集成电路制造(天津)有限公司氮化硅薄膜是一种重要的精细陶瓷薄膜材料,它既是优良的高温结构材料,具有良好的抗冲击、抗氧化和高强度等特点;同时具有很多优良的性能,如硬度高、抗腐蚀、耐高温、化学惰性与绝缘性好、光电性能优良等,所以被广泛应用于微电子领域、光电子工业、材料表面改性等领域。
一、CVD法分类CVD法制备Si3N4薄膜是把含有薄膜元素的气体供到沉积炉中基质的表面,利用加热、等离子体、紫外光乃至激光等能源,使其相互反应沉积薄膜。
它具有薄膜形成方向性小,微观均匀性好,具有台阶覆盖性能,更适于复杂形状的基质;薄膜纯度高,残余应力小,延展性强;薄膜受到的辐射损伤较低等优点。
所以,CVD法成为人们最常用的制备氮化硅薄膜的方法。
常用的CVD法有以下几种:1、常压化学气相沉积法(APVCD)。
该法是在常压环境下,反应气体受热后被N2或Ar等惰性气体输运到加热的高温基片上,经化合反应或热分解生成固态薄膜。
由于这种沉积在常压下进行,且仅依靠热量来激活反应气体实现薄膜的沉积,所以与其它CVD相比,其设备简单,操作方便,是早期制备氮化硅薄膜的主要方法。
但由于反应在常压下进行,在生成薄膜材料的同时各种副产物也将同时生产;常压下分子的扩散速率小,不能及时排出副产物,这限制了沉积速率,还加大了膜层污染的可能性,从而导致薄膜的质量下降。
2、低压化学气相沉积(LPCVD)。
人们在APCVD的基础上研制出了LPCVD。
LPCVD克服了APCVD沉积速率孝膜层污染严重等缺点,因而所制备氮化硅薄膜的均匀性好,缺陷少,质量高;并可同时在大批量的基板上沉积薄膜,易于实现自动化,效率高,现已成为半导体工业中制备氮化硅薄膜的主要方法。
氮化硅薄膜制备技术

氮化硅薄膜的制备技术摘要氮化硅薄膜是一种重要的精细陶瓷薄膜材料,具有优秀的光电性能、钝化性能、稳定性能和机械性能,在微电子、光电和材料表面改性等领域有着广阔的应用前景。
关键词氮化硅,薄膜,制备1 氮化硅薄膜的性质氮化硅薄膜具有高的化学稳定性、高电阻率、绝缘性好、硬度高、光学性能良好等特性,在半导体器件、化工、微电子工业、光电子工业、太阳能电池等方面具有广泛的应用。
近年来,氮化硅薄膜作为太阳能电池的减反射膜越来越引起人们的关注。
利用氮化硅薄膜作为减反射膜、绝缘层以及钝化层等已取得了较好的效果。
作为减反射膜,氮化硅薄膜具有良好的光学性能(其折射率在2.0左右,比传统的二氧化硅减反膜具有更好的减反效果。
同时,氮化硅薄膜还具有良好的钝化效果,对质量较差的硅片能起到表面和体内的钝化作用,并且由于其良好的表面钝化和体内钝化作用还可以进氮化硅薄膜制备及其相关特性研究一步提高太阳能电池的短路电流。
因此,近年来采用氮化硅薄膜作为太阳能电池的减反射膜己经成为光伏界研究的热点。
氮化硅薄膜是一种重要的薄膜光学材料,它不仅具有透光率高、透光谱宽、折射率变化范围大等优良的光学性质,还具有耐磨损、耐腐蚀、应力小等优良的力学、化学性质,因而在薄膜光学器件以及光学器件的表面保护膜方面,有着广阔的应用前景。
此外,氮化硅薄膜还有着卓越的抗氧化和绝缘性能,同时具有良好的阻挡钠离子、掩蔽水蒸气和金属扩散的能力。
2 氮化硅薄膜的制备方法2.1 物理气相沉积(PVD)法PVD主要的方法有真空蒸镀(V acuum evaporation)、溅射镀膜(V acuum sputterng)、离子镀(Ton plating)2.1.1 真空蒸镀真空蒸镀是将镀料在真空中加热、蒸发,使蒸发的原子或原子团在温度较低的基板上析出,形成薄膜。
这与水壶煮开水时,冒出的水蒸气使玻璃窗蒙上一层模糊的水汽相似。
它是利用电阻加热,高频感应的加热或高能束(电子束、激光束、离子束等)轰击使镀膜材料转化为气相而沉积到基体表面的一种成熟技术。
氮化硅薄膜窗口制备

氮化硅薄膜窗口制备概述氮化硅薄膜窗口是一种常用于高温、高压等特殊条件下的透明窗口材料。
本文将从材料选择、制备方法、性能测试等方面全面介绍氮化硅薄膜窗口的制备方法及其相关内容。
材料选择选择合适的材料对于制备氮化硅薄膜窗口至关重要。
常见的材料选择如下: 1. 硅基底材料:选择高纯度、低氧含量的硅基底材料,以确保薄膜质量和光学性能。
2. 氮化硅材料:选择高质量的氮化硅材料,以确保薄膜的机械强度和化学稳定性。
制备方法物理气相沉积法物理气相沉积法是制备氮化硅薄膜窗口的主要方法之一。
具体步骤如下: 1. 准备硅基底材料,并进行表面清洗和处理,以确保材料的纯净度和平整度。
2. 将硅基底材料放置于高温反应室中,同时加入适量的氮化硅前驱物。
3. 使用高温真空蒸发或等离子体激活等方法,使氮化硅前驱物逐渐在硅基底材料上沉积形成薄膜。
4. 控制沉积时间和温度,以获得所需的薄膜厚度和性能。
热分解法热分解法是另一种制备氮化硅薄膜窗口的常用方法。
具体步骤如下: 1. 准备硅基底材料,并进行表面清洗和处理,以确保材料的纯净度和平整度。
2. 将硅基底材料放置于高温反应室中,并加入适量的氨气和硅源(如SiH4)。
3. 在高温条件下,控制氨气和硅源的流量和反应时间,使其热分解反应产生氮化硅薄膜。
4. 经过一定的退火和后处理,获得所需的薄膜厚度和性能。
性能测试制备完成的氮化硅薄膜窗口需要进行性能测试,以确保其质量和可靠性。
常见的性能测试项目如下: 1. 光学透过率测试:使用光谱仪等设备测试氮化硅薄膜窗口的透过率,并进行光学性能分析。
2. 机械强度测试:使用万能材料测试机等设备测试氮化硅薄膜窗口的机械强度和耐磨性。
3. 热稳定性测试:将氮化硅薄膜窗口置于高温环境中,测试其热稳定性和耐高温性能。
4. 化学稳定性测试:将氮化硅薄膜窗口置于酸碱环境中,测试其化学稳定性和耐腐蚀性能。
结论氮化硅薄膜窗口制备是一项关键的技术,通过选择合适的材料和制备方法,并进行全面的性能测试,可以获得高质量、高性能的氮化硅薄膜窗口。
- 1、下载文档前请自行甄别文档内容的完整性,平台不提供额外的编辑、内容补充、找答案等附加服务。
- 2、"仅部分预览"的文档,不可在线预览部分如存在完整性等问题,可反馈申请退款(可完整预览的文档不适用该条件!)。
- 3、如文档侵犯您的权益,请联系客服反馈,我们会尽快为您处理(人工客服工作时间:9:00-18:30)。
选取氮化硅和二氧化硅作为薄膜材料,借助膜系设计软件对膜系结构进行优化,采用中频脉冲磁控溅射技术进行薄膜制备。
利用高反膜透射曲线拟合方法调整薄膜的实际沉积速率,减少膜厚控制误差,在树脂镜片CR39基底的凸面和凹面上分别镀制了符合设计要求的红外防护膜和可见光减反膜。
镀膜后树脂镜片在420~680 nm的平均透过率大于95%,在近红外800~1400 nm波段的平均透过率小于60%,薄膜性能稳定,能够满足红外防护树脂镜片的日常使用需要1)热固性材料1)普通树脂材料:(CR-39)学名碳本酸丙烯乙酸,或称烯丙基二甘醇酸脂(Dially Glycol Carbonates),是应用最广泛的生产普通树脂镜片的材料。
它于四十年代被美国哥伦比亚公司的化学家发现,是美国空军所研制的一系列聚合物中的第39号材料,因此,被称为CR-39(哥伦比亚树脂第39号)。
CR-39被用于生产眼用矫正镜片是在1955~1960年,是第一代的超轻、抗冲击的树脂镜片。
CR-39作为一种热固性材料,单体呈液态,在加热和加入催化剂的条件下聚合固化。
聚合是一个化学反应,即由几个相同分子结构的单体组成的一个新的聚合体分子,具有不同的长度和性质。
作为光学镜片,CR-39材料性质的参数十分适宜:折射率为1.5(接近普通玻璃镜片)、密度1.32(几乎是玻璃的一半)、阿贝数为58~59(只有很少的色射)、抗冲高透光率,可以进行染色和镀膜处理。
它主要的缺点是耐磨性不及玻璃,需要镀抗磨损膜处理。
树脂镜片可采用模式压法加工镜片表面的曲率,因此很适用于非球面镜片的生产。
2)中高折射率树脂材料:今天大部分的中折射率和高折射率材料都是热固性树脂,其发展非常迅速。
它们的折射率可以使用以下任意一种技术来增加:改变原分子中电子的结构,例如:引入苯环结构;在原分子中加入重原子,诸如卤素(氯、溴等)或硫。
与传统CR-39相比,用中高折射率树脂材料制造的镜片更轻、更薄。
它们的比重与CR-39大体一致(在1.20到1.40之间),但色散较大(阿贝数45),抗热性能较差,然而抗紫外线较佳,同时也可以染色和进行各种系统的表面镀膜处理。
使用这些材料的镜片制造工艺与CR-39的制造原理大体一致。
现在1.67的树脂材料已广泛流行,而且象1.7的树脂材料也已在市场上有销售。
视光业的专业人员正不断研制开发新材料,改良原有材料,以期树脂材料在将来获得更好的性能。
3)染色树脂材料:用于制造太阳眼镜镜片的基本上都是聚合前加入染料而制成的,特别适合大批量制造各色平光太阳镜片,同时在材料中加入可吸收紫外线的物质。
现在的一项技术即是使用浸泡在溶有有机色素的热水中,常用的染料有红色、绿色、黄色、蓝色、灰色、和棕色,根据需求可任意调染,颜色的深浅也可以控制,可以将整片镜片染色成一种颜色,也可以染成逐渐变化的颜色,例如镜片上部深色,往下逐渐减浅,即俗称的双色或渐进色。
有机材料的出现,解决了屈光不正者配戴太阳眼镜的问题。
4)光致变色树脂材料:第一代光致变色树脂镜片大约出现在1986年,但是直到1990年第一代Transi-tion镜片面市后,它才真正开始普及。
光致变色效果是在材料中加入了感光的混合物而获得的,在特殊波段的紫外线辐射作用下,这些感光物质的结构发生变化,改变了材料的吸收能力。
这些混合物与的结合主要有两种方法:在聚合前与液态单体混合,或在聚合后渗入材料中(Transition镜片就采用后一种方法)。
光致变色树脂镜片采用几种光致变色物质,在最后的制造中使这些不同的变色效果结合起来,这使得镜片变色不但迅速,而且不完全受温度的控制。
一种新型的光致变色树脂镜片已于1993年投放市场,这种镜片采用树脂材料作片基,用渗透法在镜片的凸面渗透了一层光致变色材料,然后再镀上一层抗磨损膜,起保护和而磨作用。
这项工艺技术可以使镜片的变色不会随屈光度数的加深而出现镜片中央与周围深浅不一的情况,弥补了玻璃变色的不足。
再加上片基是树脂材料,轻且抗冲击,所以这种镜片特别适合用于各种屈光不正者使用。
(2)热塑性材料(聚碳酸酯,POLYCARBONATE,简称PC)热塑性材料如PMMA早在五十年代就被首次用于制造镜片,但是由于受热易变形及耐磨性较差的缺点,很快就被CR -39所替代。
然而今天,聚碳酸酯的发展将热塑性材料带回了镜片领域,并被视光业专业人士认可为21世纪的主导镜片材料。
实际上,聚碳酸酯也不是一种新材料,它大约在1995年就被发现了,但真正在视光领域的使用仅仅是近几年,它在历经了数年的研制和多次的改进之后尤其是应用于CD产业,其光学质量已其它镜片材料相媲美。
聚碳酸酯是直线形无定型结构的热塑聚合体,具有许多光学方面的优点:出色的抗冲击性(是CR-39的10倍以上),高折射率(ne=1.591,nd=1.586),非常轻(比重=1.20g/立方厘米),100%抗紫外线(385nm),耐高温(软化点为140 °C/280 °F)。
聚碳酸酯材料也可进行系统的镀膜处理。
它的阿贝数较低(Ve=31,Vd=30),但在实际中对配戴者并没有显著的影响。
在染色方面,由于聚碳酸酯材料本身不易着色,所以大多通过可染色的抗磨损膜吸收颜色树脂镜片镀膜三[post] 三.镜片镀膜一、耐磨损膜(硬膜)无论是无机材料还是有机材料制成的眼镜片,在日常的使用中,由于与灰尘或砂砾(氧化硅)的摩擦都会造成镜片磨损,在镜片表面产生划痕。
与玻璃片相比,有机材料制成的硬性度比较低,更易产生划痕。
通过显微镜,我们可以观察到镜片表面的划痕主要分为二种,一是由于砂砾产生的划痕,浅而细小,戴镜者不容易察觉;另一种是由较大砂砾产生的划痕,深且周边粗糙,处于中心区域则会影响视力。
(1)技术特征1)第一代抗磨损膜技术抗磨损膜始于20世纪70年代初,当时认为玻璃镜片不易磨制是因为其硬度高,而有机镜片则太软所以容易磨损。
因此将石英材料于真空条件下镀在有机镜片表面,形成一层非常硬的抗磨损膜,但由于其热胀系数与片基材料的不匹配,很容易脱膜和膜层脆裂,因此抗磨损效果不理想。
2)第二代抗磨损膜技术20世纪80年代以后,研究人员从理论上发现磨损产生的机理不仅仅与硬度相关,膜层材料具有“硬度/形变”的双重特性,即有些材料的硬度较高,但变形较小,而有些材料硬度较低,但变形较大。
第二代的抗磨损膜技术就是通过浸泡工艺法在有机镜片的表面镀上一种硬度高且不易脆裂的材料。
3)第三代抗磨损膜技术第三代的抗磨损膜技术是20世纪90年代以后发展起来的,主要是为了解决有机镜片镀上减反射膜层后的耐磨性问题。
由于有机镜片片基的硬度和减反射膜层的硬度有很大的差别,新的理论认为在两者之间需要有一层抗磨损膜层,使镜片在受到砂砾磨擦时能起缓冲作用,并而不容易产生划痕。
第三代抗磨损膜层材料的硬度介于减反射膜和镜片片基的硬度之间,其磨擦系数低且不易脆裂。
4)第四代抗磨损膜技术第四代的抗膜技术是采用了硅原子,例如法国依视路公司的帝镀斯(TITUS)加硬液中既含有有机基质,又含有包括硅元素的无机超微粒物,使抗磨损膜具备韧性的同时又提高了硬度。
现代的镀抗磨损膜技术最主要的是采用浸泡法,即镜片经过多道清洗后,浸入加硬液中,一定时间后,以一定的速度提起。
这一速度与加硬液的黏度有关,并对抗磨损膜层的厚度起决定作用。
提起后在100 °C左右的烘箱中聚合4-5小时,镀层厚约3-5微米。
(2)测试方法判断和测试抗磨损膜耐磨性的最根本的方法是临床使用,让戴镜者配戴一段时间,然后用显微镜观察并比镜片的磨损情况。
当然,这通常是在这一新技术正式推广前所采用的方法,目前我们常用的较迅速、直观的测试方法是:1)磨砂试验将镜片置于盛有砂砾的宣传品内(规定了砂砾的粒度和硬度),在一定的控制下作来回磨擦。
结束后用雾度计测试镜片磨擦前后的光线漫反射量,并且与标准镜片作比较。
2)钢丝绒试验用一种规定的钢丝绒,在一定的压力和速度下,在镜片表面上磨擦一珲的次数,然后用雾度计测试镜片磨擦前后的光线漫反射量,并且与标准镜片作比较。
当然,我们也可以手工操作,对二片镜片用同样的压力磨擦同样的次数,然后用肉眼观察和比较。
上述两种测试方法的结果与戴镜者长期配戴的临床结果比较接近。
3)减反射膜和抗磨损膜的关系镜片表面的减反射膜层是一种非常薄的无机金属氧化物材料(厚度低于1微米),硬且脆。
当镀于玻璃镜片上时,由于片基比较硬,砂砾在其上面划过,膜层相对不容易产生划痕;但是减反射膜镀于有机镜片上时,由于片基较软,砂砾在膜层上划过,膜层很容易产生划痕。
因此有机镜片在镀减反射膜前必须要镀抗磨损膜,而且两种膜层的硬度必须相匹配。
二、减反射膜(1)为什么需要镀减反射膜?1)镜面反射光线通过镜片的前后表面时,不但会产生折射,还会产生反射。
这种在镜片前表面产生的反射光会使别人看戴镜者眼睛时,看到的却是镜片表面一片白光。
拍照时,这种反光还会严重影响戴镜者的美观。
2)"鬼影"眼镜光学理论认为眼镜片屈光力会使所视物体在戴镜者的远点形成一个清晰的像,也可以解释为所视物的光线通过镜片发生偏折并聚集于视网膜上,形成像点。
但是由于屈光镜片的前后表面的曲率不同,并且存在一定量的反射光,它们之间会产生内反射光。
内反射光会在远点球面附近产生虚像,也就是在视网膜的像点附近产生虚像点。
这些虚像点会影响视物的清晰度和舒适性。
3)眩光象所有光学系统一样,眼睛并不完美,在视网膜上所成的像不是一个点,而是一个模糊圈。
因此,二个相邻点的感觉是由二个并列的或多或少重叠的模糊圈产生的。
只要二点之间的距离足够大,在视网膜上的成像就会产生二点的感觉,但是如果二点太接近,那么二个模糊圈会趋向与重合,被误认为是一个点。
对比度可以用来反映这种现象,表达视力的清晰度。
对比值必须大于某一确定值(察觉阈,相当于1-2)才能够确保眼睛辨别二个邻近点。
对比度的计算公式为:D=(a-b)/(a+b) 其中C为对比度,二个相邻物点在视网膜上所成像的感觉最高值为a,相邻部份的最低值为b。
如果对比度C值越高,说明视觉系统对该二点的分辨率越高,感觉越清晰;如果二个物点非常接近,它们的相邻部分的最低值比较接近于最高值,则C值低,说明视觉系统对该二点感到不清晰,或不能清晰分辨。
让我们来模拟这样一个场景产:夜晚,一位戴眼镜的驾车者清晰地看见对面远处有二辆自行车正冲着他的车骑过来。
此时,尾随其后的汽车的前灯在驾车者镜片后表面上产生反射:该反射光在视网膜上形成的像增加了二个被观察点的强度(自行车车灯)。
所以,a段和b段的长度增加,即然分母(a+b)增加,而分子(a-b)保持不变,于是就引起了C值的减少。
对比减小的结果会令驾驶员最初产生的存在二个骑车人的感觉重合成为单一的像,就好比区分它们的角度被突然减小!4)透过量反射光占入射光的百分比取决于镜片材料的折射率,可通过反射量的公式进行计算。