预浸料成型工艺
碳纤维复合材料的成型工艺

碳纤维复合材料的成型工艺一、碳纤维复合材料概述碳纤维复合材料是一种由碳纤维增强体和树脂基体组成的新型高性能材料。
它以其轻质、高强度、高刚度、耐疲劳、耐腐蚀等优异性能,在航空航天、汽车制造、体育器材、建筑结构等领域得到了广泛的应用。
本文将探讨碳纤维复合材料的成型工艺,分析其重要性、挑战以及实现途径。
1.1 碳纤维复合材料的特点碳纤维复合材料的特点主要包括以下几个方面:- 轻质高强:碳纤维具有很高的比强度和比模量,使得复合材料在保持轻质的同时,具有很高的承载能力。
- 高刚度:碳纤维复合材料的刚度远高于传统材料,可以提供更好的结构稳定性。
- 耐疲劳:碳纤维复合材料具有优异的耐疲劳性能,适用于承受反复循环载荷的应用。
- 耐腐蚀:碳纤维复合材料对多种腐蚀性介质具有很好的抵抗力,适用于恶劣环境。
1.2 碳纤维复合材料的应用领域碳纤维复合材料的应用领域非常广泛,包括但不限于以下几个方面:- 航空航天:用于飞机结构、发动机部件等,以减轻重量、提高性能。
- 汽车制造:用于车身、底盘等部件,以提高燃油效率和车辆性能。
- 体育器材:用于自行车、网球拍、高尔夫球杆等,以提供更好的运动性能。
- 建筑结构:用于桥梁、高层建筑等,以提高结构的承载能力和耐久性。
二、碳纤维复合材料的成型工艺碳纤维复合材料的成型工艺是实现其优异性能的关键环节。
不同的成型工艺会影响材料的性能和应用范围。
2.1 预浸料成型工艺预浸料成型工艺是一种常用的碳纤维复合材料成型方法。
该工艺首先将碳纤维与树脂基体预先混合,形成预浸料,然后在模具上铺设预浸料,通过热压或真空袋压等方法固化成型。
预浸料成型工艺具有成型效率高、产品质量好等优点。
2.2 树脂传递模塑成型工艺树脂传递模塑(RTM)成型工艺是一种先进的复合材料成型技术。
该工艺通过将树脂注入闭合模具中,使树脂在模具内流动并浸润碳纤维,最终固化成型。
RTM工艺可以实现复杂形状的制品成型,且具有较低的生产成本。
航空复合材料结构件常用的成型方法
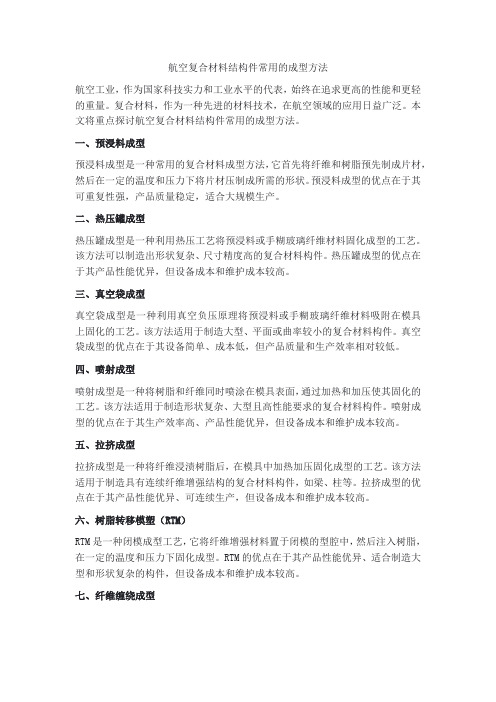
航空复合材料结构件常用的成型方法航空工业,作为国家科技实力和工业水平的代表,始终在追求更高的性能和更轻的重量。
复合材料,作为一种先进的材料技术,在航空领域的应用日益广泛。
本文将重点探讨航空复合材料结构件常用的成型方法。
一、预浸料成型预浸料成型是一种常用的复合材料成型方法,它首先将纤维和树脂预先制成片材,然后在一定的温度和压力下将片材压制成所需的形状。
预浸料成型的优点在于其可重复性强,产品质量稳定,适合大规模生产。
二、热压罐成型热压罐成型是一种利用热压工艺将预浸料或手糊玻璃纤维材料固化成型的工艺。
该方法可以制造出形状复杂、尺寸精度高的复合材料构件。
热压罐成型的优点在于其产品性能优异,但设备成本和维护成本较高。
三、真空袋成型真空袋成型是一种利用真空负压原理将预浸料或手糊玻璃纤维材料吸附在模具上固化的工艺。
该方法适用于制造大型、平面或曲率较小的复合材料构件。
真空袋成型的优点在于其设备简单、成本低,但产品质量和生产效率相对较低。
四、喷射成型喷射成型是一种将树脂和纤维同时喷涂在模具表面,通过加热和加压使其固化的工艺。
该方法适用于制造形状复杂、大型且高性能要求的复合材料构件。
喷射成型的优点在于其生产效率高、产品性能优异,但设备成本和维护成本较高。
五、拉挤成型拉挤成型是一种将纤维浸渍树脂后,在模具中加热加压固化成型的工艺。
该方法适用于制造具有连续纤维增强结构的复合材料构件,如梁、柱等。
拉挤成型的优点在于其产品性能优异、可连续生产,但设备成本和维护成本较高。
六、树脂转移模塑(RTM)RTM是一种闭模成型工艺,它将纤维增强材料置于闭模的型腔中,然后注入树脂,在一定的温度和压力下固化成型。
RTM的优点在于其产品性能优异、适合制造大型和形状复杂的构件,但设备成本和维护成本较高。
七、纤维缠绕成型纤维缠绕成型是一种利用纤维缠绕机将纤维连续缠绕在芯轴上的工艺。
该方法适用于制造具有旋转对称性的复合材料构件,如压力容器、管道等。
smc模压成型工艺流程

SMC模压成型工艺流程SMC模压成型是一种常见的复合材料成型工艺,被广泛应用于汽车、航天、建筑等领域。
SMC(Sheet Molding Compound)是一种预浸有树脂的增强复合材料,主要由玻璃纤维、石墨、填料和热固性树脂等组成。
在SMC模压成型过程中,首先将预制好的SMC 预浸料加热软化,然后通过模具形成所需的零部件形状,最终在加热和压力的作用下固化成型,达到产品设计要求。
以下是SMC模压成型的工艺流程。
SMC模压成型工艺流程1. 准备工作在SMC模压成型之前,需要准备好所需的模具、预浸SMC料、加热设备以及压力设备等。
确保所有设备运行正常,符合操作规范。
2. 加热预浸料将预制的SMC料放入加热设备中,经过加热软化,使树脂充分熔化,增强纤维得到活化,便于后续成型。
3. 模具装配将加热后的SMC料放入模具中。
模具需要根据所需产品的设计图纸来选择,并确保模具表面干净平整,涂抹模具脱模剂以防粘连。
4. 模压成型开始进行模压成型工艺,将已经装配好的SMC料模具置于压力设备中,通过加压使SMC料充分填充模具腔体,并且确保均匀分布。
5. 施加压力在模具内加入适当的压力,使SMC料在热固化过程中得到充分压实,以确保产品密度和强度。
6. 加热固化通过加热设备对模具中的SMC料施加恒定的温度,使树脂充分固化,增强纤维和填料得到固定,从而形成产品的稳定结构。
7. 冷却脱模待SMC料在模具中充分固化后,关闭加热设备,待产品冷却至室温。
然后打开模具,取出成型产品,进行后续的修整和表面处理。
8. 检验和包装对成型的产品进行外观检验、尺寸检测以及性能测试,确保产品符合设计要求。
最后对产品进行包装,以防止在运输和储存过程中受到损坏。
以上就是SMC模压成型的工艺流程,通过严谨的操作和控制,可以生产出高质量的复合材料制品,满足各行业对材料性能和外观要求的不断提升。
碳纤维预浸料制作方法

碳纤维预浸料制作方法全文共四篇示例,供读者参考第一篇示例:碳纤维预浸料是一种常用的复合材料,在航空航天、汽车、建筑等领域得到广泛应用。
碳纤维预浸料的质量和性能对最终制品的质量和性能起着至关重要的作用。
今天我们就来介绍一下碳纤维预浸料的制作方法。
碳纤维预浸料的制作主要包括:树脂、碳纤维布、固化剂、界面处理剂等材料的选取和搅拌、固化工艺的确定等步骤。
选取适当的树脂。
目前常用的树脂有环氧树脂、聚酯树脂、酚醛树脂等。
各种树脂的性能各有不同,可以根据需要选择合适的树脂。
接下来是选择适当的碳纤维布。
碳纤维布的密度、纤维间的排列方式等都会对最终碳纤维预浸料的性能产生影响。
一般来说,碳纤维布的密度越高,强度越大。
碳纤维布的纤维排列方式也需要考虑到最终制品的使用要求。
然后是固化剂的选择。
固化剂是起到固化树脂的作用的化学品,也会对最终碳纤维预浸料的性能产生重要影响。
不同的固化剂具有不同的固化速度、固化温度等,制作时需要根据具体情况选择合适的固化剂。
还需要添加界面处理剂。
界面处理剂主要是用来增强碳纤维和树脂间的粘接力,减少界面应力,提高碳纤维预浸料的性能。
通常界面处理剂可以分为物理吸附界面活性剂和共价键界面活性剂,根据具体情况选择合适的界面处理剂。
在选取了适当的材料后,就需要进行搅拌和混合。
搅拌的目的是将树脂、碳纤维和固化剂等材料均匀混合,确保每个部分的配比准确。
搅拌的时间和速度也需要掌握好,以免造成过度混合或不充分混合的情况。
混合完成后,就可以进行浸渍了。
浸渍就是将碳纤维布浸泡在搅拌好的树脂混合物中,确保碳纤维均匀覆盖树脂。
浸渍的时间也很重要,应根据具体情况调整,以保证碳纤维和树脂的充分浸透。
浸渍完成后,需要进行固化。
固化的温度、时间也需要根据具体情况确定,以保证碳纤维预浸料的性能。
在固化的过程中,需要注意控制温度和湿度,避免出现不均匀固化的情况。
可以根据需要进行加工和表面处理。
加工可以包括切割、成型和打磨等步骤,以获得符合要求的形状和尺寸。
预浸料模压工艺

预浸料模压工艺预浸料模压工艺是一种先将预浸料与基材进行预处理,然后再进行模压成型的工艺。
预浸料是指将树脂浸渍到玻璃纤维布或碳纤维布等增强材料中,形成预浸料片材。
预浸料模压工艺在航空航天、汽车、电子、体育器材等领域有着广泛的应用。
一、预处理预浸料片材需进行干燥处理,以去除其中的水分。
然后,将预浸料片材与基材进行搭配,选取合适的排列方式,以提高材料的性能。
此外,还需要对预浸料进行预切割和定型处理,以适应后续的模压过程。
二、模具设计与制造在预浸料模压工艺中,模具是至关重要的工具。
模具的设计需要考虑到产品的形状、尺寸以及模具的材质和加工工艺等因素。
常用的模具材料有金属和石膏等,而制造模具的工艺则包括数控加工、电火花加工和磨削加工等。
三、模压过程在模压过程中,预浸料片材被放置在模具的一侧,然后将另一侧的模具闭合。
随后,施加高压力使预浸料与基材充分接触,以保证其结合牢固。
同时,通过加热使预浸料中的树脂固化,从而形成最终的产品。
四、质量控制在预浸料模压工艺中,质量控制是非常重要的环节。
通过控制模具的温度、压力和固化时间等参数,可以确保产品的质量稳定。
同时,还需要对成品进行外观检查、尺寸测量和性能测试等,以确保产品符合设计要求。
五、优点与应用预浸料模压工艺具有以下优点:1. 生产效率高:预浸料片材可以提前进行干燥和切割,减少了生产周期。
2. 产品质量稳定:预浸料片材经过预处理后,树脂的含量和分布均匀,产品性能稳定。
3. 适用范围广:预浸料模压工艺适用于各种形状和尺寸的产品制造,如飞机零部件、汽车外壳和体育器材等。
预浸料模压工艺在航空航天领域得到广泛应用。
例如,飞机的机身、机翼和尾翼等部件常采用预浸料模压工艺进行制造,以提高产品的强度和耐久性。
此外,在汽车制造中,预浸料模压工艺也被用于制造车身和内饰部件,以提高产品的轻量化和安全性能。
在电子领域,预浸料模压工艺可以用于制造电路板和电子封装材料,以提高电子产品的可靠性和性能稳定性。
预浸料使用方法

预浸料让你的DIY变得更加省心
随着时代的进步和人们对生活质量的不断追求,市面上的DIY家
居材料变得越来越多样化和丰富。
而其中,预浸料作为一种新型材料,成为了许多DIY爱好者的首选。
那么,什么是预浸料呢?预浸料是一种将树脂与增强材料事先混
合后制成的复合材料,其制备工艺和材料成分都比较简单。
首先,将
树脂和固化剂按照一定比例混合均匀,再加入增强材料(如玻璃纤维、碳纤维等)进行搅拌和预浸润,待材料表面的气泡飞去后,将其晾干,并在一定的温度和时间下进行固化处理即可。
那么,预浸料又有哪些优势呢?首先,它的制备过程简单,而且
操作便捷,可以满足DIY家居爱好者对于材料耐用性、强度、刚度和
耐腐蚀性的要求。
其次,它具有良好的加工性能,可以进行轮廓加工、成型加工、粘接等多种加工方式,大大方便了DIY家居材料的制作。
使用预浸料时,我们需要注意一些细节。
首先,需要注意对树脂
固化剂的配比,否则可能会导致材料的性能下降。
其次,需要在加工
之前进行充分测试,确保材料的强度和刚度符合使用要求。
最后,需
要注意做好个人防护工作,如戴手套、口罩等,避免对人体产生不良
影响。
总体来说,预浸料是一种性能优异、制作方便的新型材料,它的使用可以大大提高DIY家居的制作效率和质量,并成为您美化家居的得力助手。
预浸料模压工艺流程

预浸料模压工艺流程预浸料模压工艺是一种常见的复合材料制备工艺,广泛应用于航空航天、汽车、船舶等领域。
该工艺通过将纤维和树脂预先浸渍,然后在模具内进行热压,最终形成具有优异性能的复合材料制品。
下面将详细介绍预浸料模压工艺的流程。
材料准备在进行预浸料模压工艺之前,首先需要准备好纤维材料和树脂。
常用的纤维材料包括碳纤维、玻璃纤维、芳纶纤维等,而树脂则通常选用环氧树脂、酚醛树脂等具有优异性能的树脂。
在准备材料时,需要注意保持干燥,确保材料的质量。
预浸料制备接下来是预浸料的制备过程。
首先,将纤维材料按照设计要求进行切割和排列,然后将它们置入树脂中进行浸渍。
浸渍的过程需要根据纤维种类和树脂性质来确定浸渍时间和压力,确保纤维充分浸透树脂。
完成浸渍后,需要对预浸料进行固化处理,使树脂充分固化,形成具有一定强度和形状的复合材料半成品。
模具设计在进行模压之前,需要设计好模具结构。
模具设计的好坏直接影响到复合材料制品的成型效果,包括表面质量、尺寸精度等。
通常模具会根据产品的形状和结构来设计,确保在模压过程中纤维的排列和树脂的分布均匀,避免产生气泡、破损等缺陷。
模压工艺模压是整个预浸料工艺的核心环节。
在进行模压时,首先将预浸料放置在模具中,然后施加一定的温度和压力进行成型。
温度和压力的控制需要根据具体的预浸料和产品要求来确定,在保证树脂充分流动和纤维不受损伤的情况下完成成型。
完成模压后,需要适当的冷却时间,使复合材料制品充分固化和冷却。
后处理工艺最后,进行后处理工艺以提高复合材料制品的性能。
后处理工艺通常包括修边、表面处理、热处理等环节,以确保产品的外观和性能达到设计要求。
在进行后处理工艺时,需要注意操作规范,避免对产品造成二次损伤。
综上所述,预浸料模压工艺是一项复杂而关键的制备工艺,需要严谨的操作和科学的控制。
只有通过严格的工艺流程和技术要求,才能制备出具有优异性能的复合材料制品,满足各个领域的需求。
预浸料质量要求、使用特点及生产工艺
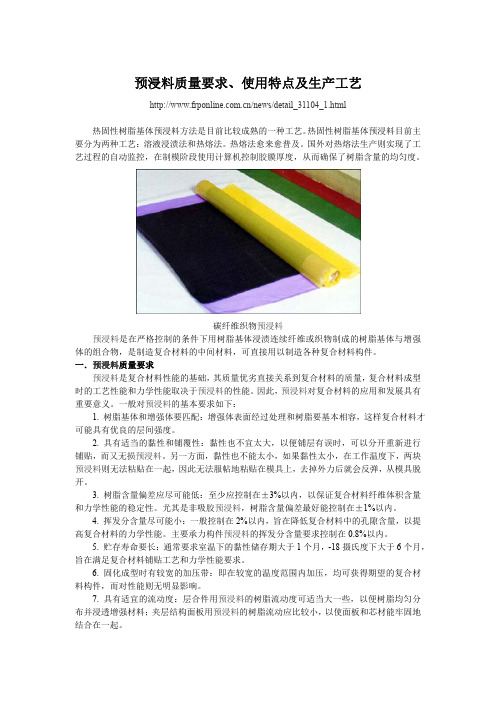
预浸料质量要求、使用特点及生产工艺/news/detail_31104_1.html热固性树脂基体预浸料方法是目前比较成熟的一种工艺。
热固性树脂基体预浸料目前主要分为两种工艺:溶液浸渍法和热熔法。
热熔法愈来愈普及。
国外对热熔法生产则实现了工艺过程的自动监控,在制模阶段使用计算机控制胶膜厚度,从而确保了树脂含量的均匀度。
碳纤维织物预浸料预浸料是在严格控制的条件下用树脂基体浸渍连续纤维或织物制成的树脂基体与增强体的组合物,是制造复合材料的中间材料,可直接用以制造各种复合材料构件。
一.预浸料质量要求预浸料是复合材料性能的基础,其质量优劣直接关系到复合材料的质量,复合材料成型时的工艺性能和力学性能取决于预浸料的性能。
因此,预浸料对复合材料的应用和发展具有重要意义。
一般对预浸料的基本要求如下:1.树脂基体和增强体要匹配:增强体表面经过处理和树脂要基本相容,这样复合材料才可能具有优良的层间强度。
2. 具有适当的黏性和铺覆性:黏性也不宜太大,以便铺层有误时,可以分开重新进行铺贴,而又无损预浸料。
另一方面,黏性也不能太小,如果黏性太小,在工作温度下,两块预浸料则无法粘贴在一起,因此无法服帖地粘贴在模具上,去掉外力后就会反弹,从模具脱开。
3. 树脂含量偏差应尽可能低:至少应控制在±3%以内,以保证复合材料纤维体积含量和力学性能的稳定性。
尤其是非吸胶预浸料,树脂含量偏差最好能控制在±1%以内。
4. 挥发分含量尽可能小:一般控制在2%以内,旨在降低复合材料中的孔隙含量,以提高复合材料的力学性能。
主要承力构件预浸料的挥发分含量要求控制在0.8%以内。
5.贮存寿命要长:通常要求室温下的黏性储存期大于1个月,-18摄氏度下大于6个月,旨在满足复合材料铺贴工艺和力学性能要求。
6. 固化成型时有较宽的加压带:即在较宽的温度范围内加压,均可获得期望的复合材料构件,而对性能则无明显影响。
7. 具有适宜的流动度:层合件用预浸料的树脂流动度可适当大一些,以便树脂均匀分布并浸透增强材料;夹层结构面板用预浸料的树脂流动应比较小,以使面板和芯材能牢固地结合在一起。
- 1、下载文档前请自行甄别文档内容的完整性,平台不提供额外的编辑、内容补充、找答案等附加服务。
- 2、"仅部分预览"的文档,不可在线预览部分如存在完整性等问题,可反馈申请退款(可完整预览的文档不适用该条件!)。
- 3、如文档侵犯您的权益,请联系客服反馈,我们会尽快为您处理(人工客服工作时间:9:00-18:30)。
预浸料成型工艺在复合材料产业中的应用
预浸料简介
预浸料是树脂基体在严格控制条件下浸渍连续纤维或者纤维织物,制备成树脂基
体与增强体的一种组合物,是制造复合材料的中间材料。
预浸料按物理状态,化学性能有很多种分类方法:
按物理状态分类,预浸料分成单向预浸
料、单向织物预浸料、织物预浸料;按树脂基体不同,预浸料分成热固性树脂预浸料和热塑性树脂预
浸料;按增强材料不同,分成碳纤维(织物)预浸料、玻璃纤维(织物)预浸料、芳纶(织物)预浸料;根
据纤维长度不同,分成短纤维预浸料、预浸料和连续纤维预浸料;按固化温度不同,分成中温固化
(120℃)预浸料、高温固化(180℃)预浸料以及固化温度超过200℃的预浸料等。我司事业部在预浸料
方面应用也很广泛,根据不同的产品以及性能应用不同种类的材料,常用的预浸料有单向碳纤预浸料,
玻纤织物预浸料,碳纤织物预浸料,酚醛玻纤织物预浸料等等。
预浸料制备
预浸料的制备方法有干法和湿法两种。
干法有粉末法和热溶法之分。粉末预浸料是指树脂粉末附着于纤维,经过部分融化,形成树脂不连续,
纤维未被树脂充分浸透的一种复合物。热溶法预浸料将树脂体系加热熔融成为流动状态,用其浸渍纤
维或织物而制备的预浸料。
图1 干法制备预浸料示意图
湿法预浸料是通过树脂溶液浸渍纤维束或者织物制备的预浸料。
比较由干法预浸料和湿法预浸料制成的复合材料,一般前者外观更好,材料内树脂含量的控制精度更
高。就目前航空用先进复合材料而言,常表现出热溶法复合材料的湿热稳定性优于溶液法复合材料:
同在沸水中煮48h,前者的力学性能(如弯曲模量与强度、层间剪切强度等)保持率,特别是高温力
学性能的保持率,明显高于后者。
图2 湿法制备预浸料示意图
预浸料的成型工艺
预浸料可用不同的成型方法,根据不同应用选择较为合适的成型方案。目前我们先进复合材料事业部
使用预浸料成型工艺主要有真空袋压工艺、热压罐工艺、缠绕成型工艺、模压工艺。
其中真空袋工艺主要应用在车辆,船舶,高铁等内饰件,热压罐工艺主要应用在航天、军工等高质量
复合材料,模压工艺主要应用在平板,管件等高质量,高精度的军工产品。
一、真空袋工艺
真空袋成型工艺就是将产品密封在模具和真空袋之间,通过抽真空对产品进行加压,加热,使产品
更加密实、力学性能更好的成型工艺。目前应用的预浸料主要有环氧玻纤(碳纤)预浸料、酚醛玻纤
预浸料、改性树脂预浸料、短纤维预混料
优点:
均匀加压,产品性能均匀
有效控制产品厚度和含胶量
减少产品中的气泡
可以成型复杂、大型制件
减少挥发对人员的损伤
缺点:
压力小,产品密实度差
只能一面光滑,且光滑面沙眼较多
力学性能相对较差
对劳动者操作技能要求高
下为真空袋工艺流程图:
二、热压罐成型工艺
热压罐成型工艺与真空袋工艺相似,但由于热压罐内压力以及空气温度均匀,可生产高精度,高质量
的产品。
优点:适用范围广泛,可成型各种复杂构建
罐内压力均匀,产品密实度高,力学性能较好
热压罐成型压力和温度均匀,孔隙率低,树脂含量均匀
缺点:热压罐成本较高,辅料的耗费较大
产品大小要基于热压罐的容积,一般不能制作大型产品
图3 世界上最大的热压罐
图4 热压罐内部运行系统
热压罐工艺流程图
剪
清理模
产品积层
铺脱模
铺隔离
原材料采
铺通气
粘贴密封胶
出厂检
抽真
检验真空度
安装真空阀、真空
升温固
产品脱
产品精
检验出
装模
积层
封真空袋
连接真空
剪裁预浸
清理模
三、模压工艺
模压成型(又称压制成型或压缩成型)是先将一定量的纤维预浸料放入金属对模
中,在一定温度和压力作用下,固化成型制品的方法。
其基本原理是:热固性树脂在模压成型加工中所表现的流变行为,要比热塑
性塑料复杂得多,在整个模压过程中始终伴随着化学反应,加热初期物料呈现低
分子粘流态,流动性尚好,随着官能团的相互反应,部分发生交联,物料流动性
逐步变小,并产生一定程度的弹性,使物料呈胶凝态,再继续加热使分子交联反
应更趋完善,交联度增大,物料由胶凝态变为玻璃态,树脂体内呈体型结构,成
型即告结束。
模压成型工艺的优点:
1、所得制品的内应力小,不易变形,稳定性较好;
2、产品尺寸精度高,重复性好;
3、表面光洁,无需二次修饰;
4、能一次成型结构复杂的制品;
5、模腔的磨损很小,模具的维护费用较低;
模压工艺的缺点:
1、前期投入成本较高,(金属模具、热压机、烘箱)
保压固化
降至室温
打磨毛刺
出厂检验
后处理
成品
升温加压
脱模
2、模具的升温及降温时间较长
3、对劳动者操作技能要求高
模压工艺的应用非常广泛:广泛应用于工业、农业、交通运输、电气、化工、
建筑、机械等领域。由于模压制品质量可靠,在兵器、飞机、导弹、卫星上也都
得到了应用。
在经济高速发展的今天,预浸料工艺在复合材料市场上扮演着越来越重要的角
色,在复合材料的成型,尤其在一些高端的产品方面方面也占了越来越大的比重。
我们也应该紧跟市场潮流,既要弘扬传统工艺,也要接触并发展新工艺,为我们
双一大家庭创造更美好的明天而努力。