同步器寿命性能试验中换档机械手结构设计
机械手设计已整理

机械手设计摘要本文简要地介绍了工业机器人的概念,机械手的组成和分类,机械手的自由度和座标型式,气动技术的特点,PLC控制的特点及国内外的发展状况。
本文对机械手进行了总体方案设计,确定了机械手的座标型式和自由度,确定了机械手的技术参数。
同时,分别设计了机械手的夹持式手部结构以及吸附式手部结构;设计了机械手的手腕结构,计算出了手腕转动时所需的驱动力矩和回转气缸的驱动力矩;设计了机械手的手臂结构,设计了手臂伸缩、升降用液压缓冲器和手臂回转用液压缓冲器。
设计出了机械手的气动系统,绘制了机械手气压系统工作原理图。
利用可编程序控制器对机械手进行控制,选取了合适的PLC型号,根据机械手的工作流程制定了可编程序控制器的控制方案,画出了机械手的工作时序图和梯形图,并编制了可编程序控制器的控制程序。
关键词:工业机器人;机械手;气动;可编程序控制器(PLC);机械手设计第一章绪论1.1机械手概述工业机器人由操作机(机械本体)、控制器、伺服驱动系统和检测传感装置构成,是一种仿人操作,自动控制、可重复编程、能在三维空间完成各种作业的机电一体化自动化生产设备。
特别适合于多品种、变批量的柔性生产。
它对稳定、提高产品质量,提高生产效率,改善劳动条件和产品的快速更新换代起着十分重要的作用。
机器人技术是综合了计算机、控制论、机构学、信息和传感技术、人工智能、仿生学等多学科而形成的高新技术,是当代研究十分活跃,应用日益广泛的领域。
机器人应用情况,是一个国家工业自动化水平的重要标志。
机器人并不是在简单意义上代替人工的劳动,而是综合了人的特长和机器特长的一种拟人的电子机械装置,既有人对环境状态的快速反应和分析判断能力,又有机器可长时间持续工作、精确度高、抗恶劣环境的能力,从某种意义上说它也是机器的进化过程产物,它是工业以及非产业界的重要生产和服务性设各,也是先进制造技术领域不可缺少的自动化设备.机械手是模仿着人手的部分动作,按给定程序、轨迹和要求实现自动抓取、搬运或操作的自动机械装置。
汽车手动换挡器耐久性测试试验装置研究

汽车手动换挡器耐久性测试试验装置研究作者:杨梦晨来源:《决策探索·收藏天下(中旬刊)》 2020年第3期杨梦晨摘要:文章介绍了换挡器在汽车换挡器台架上的疲劳耐久性试验,分析了汽车手动换挡器耐久性试验装置的技术要求和研究方案,提出了一种稳定可靠的试验结构装置,满足了汽车手动换挡器耐久性试验的要求。
关键词:疲劳寿命试验台;换挡器;耐久性测试随着汽车换挡器设计制造技术的发展,人们对汽车关键零部件的要求越来越高,也越来越趋向于选择经济适用的试验方法。
由于机械可靠性高、结构简单、动力性能好等特点,手动换挡器仍是换挡器领域的重要组成部分,技术和生产工艺先进的手动换挡器仍将有自己的发展空间[1]。
在各种车型的开发中,由于车辆重量、发动机输出功率和扭矩的变化,换挡器系统安装在新车型上是否会导致耐久性失效,成为车型开发中一个不确定的问题。
一、手动换挡器疲劳耐久性试验汽车换挡器疲劳试验应在产品设计定型前进行数百小时,并在专用试验台上完成QC/T 568-1999规定的试验内容,以测试其疲劳寿命性能。
常用的试验台有机械封闭式和电动封闭式[2]。
疲劳耐久性试验的关键是加载方式的选择。
电动封闭试验台通过调节励磁电压的大小来控制加载发电机。
发电机的电能在进入电机前通过小循环反馈到试验台的电控部分,或通过大循环直接进入电网。
电动封闭式试验台具有链条短、结构简单等特点,但电控部分的维修难度较大。
该项目是齿轮箱台架试验评估齿轮、轴、轴承和壳体疲劳耐久性所必需的。
其主要特点是试验耗费的时间长,试验的效果较为明显。
通过系统控制输入,比如在一定的转速和某一油温下,按额定扭矩对齿轮箱的各个齿轮循环运行,直至齿轮箱极限运行后损坏,然后分解齿轮箱并对其各部分进行分析,确定损坏情况和原因。
试验后的拆卸和评估项目包括:第一,各螺纹的拧紧力矩是否处于额定允许范围之内;第二,齿轮箱零件是否发生腐蚀生锈;第三,同步器摩擦面是否产生异常磨损缺陷,定位销是否脱落松动;第四,齿轮啮合面磨损痕迹是否均匀,平面度是否平整一致,是否有异常缺陷和磨损;第五,各轴承、壳上轴承孔等经常运动摩擦部位是否异常磨损、烧蚀或者发黑;第六,运动部件是否被碰撞磨损、损坏和偏移;第七,各齿轮齿侧间隙间隔是否在额定允许范围之内;第八,各齿轮轴向间隙范围是否在额定允许范围之内;第九,各同步器的备用行程范围是否在额定允许范围内,关键部位是否有断裂、裂纹或剥落情况。
变速箱插分档同步器结构设计改进

变速箱插分档同步器结构设计改进摘要:本文针对传统变速箱插分档同步器的结构设计存在的问题进行了研究,提出了一种新型的同步器结构设计方案。
该方案采用了新型的同步器锥头设计和新型的同步套结构,从而可以更好地实现插档时的同步作用,提高变速箱的换挡顺畅性。
同时,该方案的结构设计考虑了锥头和同步套的接触面积,减小了磨损和噪音问题。
试验结果表明,该方案可以有效地提高变速箱的换挡质量和可靠性,具有较好的应用前景。
关键词:变速箱,插分档同步器,结构设计,同步作用,换挡顺畅性。
正文:1. 背景变速箱作为汽车的一个核心部件,其可靠性和换挡质量直接影响着汽车的使用效果和品质。
在传统的变速箱结构中,插分档同步器是实现换挡的关键部件之一,其结构设计的合理性直接影响着变速箱的换挡顺畅性和可靠性。
2. 传统同步器结构的问题传统的同步器结构中,锥头和同步套的设计存在一些问题。
首先,锥头的设计过于粗糙,不能很好地贴合同步套,造成插档时无法完全实现同步作用。
其次,同步套的结构设计较为简单,在实际使用中容易出现磨损和噪音等问题。
3. 新型同步器结构设计方案为了实现更好的同步作用和换挡顺畅性,我们提出了一种新型的同步器结构设计方案。
该方案采用了新型的同步器锥头设计和新型的同步套结构,从而可以更好地实现插档时的同步作用,提高变速箱的换挡顺畅性。
同时,该方案的结构设计考虑了锥头和同步套的接触面积,减小了磨损和噪音问题。
4. 结果分析我们通过实验验证了该方案的效果。
在同等条件下,该方案相比传统方案可以提高变速箱的换挡质量和可靠性,具有较好的应用前景。
5. 总结本文介绍了传统变速箱插分档同步器结构设计存在的问题,并提出了一种新型的同步器结构设计方案。
该方案通过优化锥头和同步套的设计,实现了更好的同步作用和换挡顺畅性,具有较好的应用前景。
6. 设计思路针对传统插分档同步器的结构问题,我们提出了一种新的设计方案。
首先,我们对锥头的设计进行了优化。
采用了更为细致的锥头设计,可以更好地与同步套贴合。
机动车换挡机构设计指南
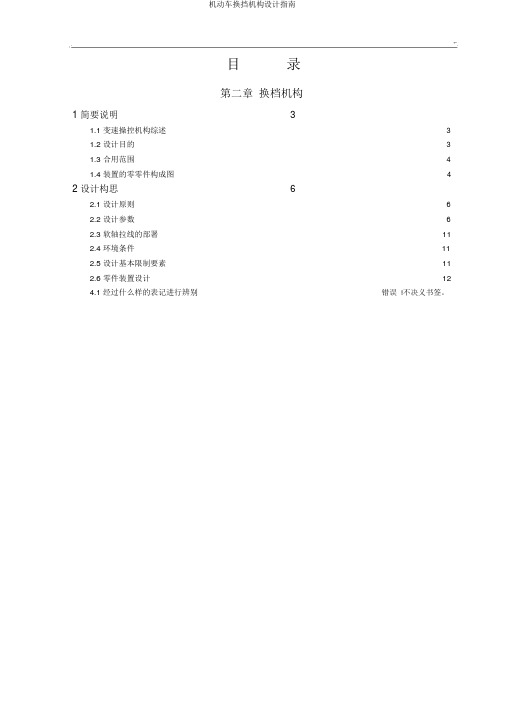
,.目录第二章换档机构1 简要说明 (3)1.1 变速操控机构综述 (3)1.2 设计目的 (3)1.3 合用范围 (4)1.4 装置的零零件构成图 (4)2 设计构思 (6)2.1 设计原则 (6)2.2 设计参数 (6)2.3 软轴拉线的部署 (11)2.4 环境条件 (11)2.5 设计基本限制要素 (11)2.6 零件装置设计 (12)4.1 经过什么样的表记进行辨别......................................................................................................................................... 错误!不决义书签。
,.第二章换档机构,. 1简要说明1.1 变速操控机构综述1 汽车变速操控机构分为手动变速操控机构(MT)、自动变速操控机构(AT&CVT&AMT)。
2 按传达行程和力的方式可分为拉索式换档操控装置、杆系换档操控装置及电讯号直接驱动换档装置 ; 如图 2, 杆系换档操控装置它是由一根或许两根修长的(空心)刚性杆件构成的。
因为是空间运动杆系,其运动剖析和自由度确实定,不论是用作图法,或用分析法都是比较复杂的;运动件自己的干预,及其与相邻件干预的校核也是相当繁琐的;还好,此刻能够借助于 CAE使设计剖析工作简化和靠谱。
同时,这类构造还有一个很难战胜的问题,就是因为其运动链长,杆件刚度弱,铰接处存在空隙,且润滑不便等原由,简单产生振动、噪声、档位不清楚、换档操控手感不良等现象。
于是,一种拉索式换档操控装置应运而生,并将渐渐代替杆系换档操控装置 .如图 1, 为拉索式换档操控装置 . 所谓拉索式换档操控装置,是用一种柔性的推拉软轴代替空间运动的刚性的杆件。
这类换档操控装置战胜了上述刚性空间杆系存在的那些问题。
同时柔性推拉软轴的走向“自如” ,给汽车的整体部署和变速器操控装置的安排带来诸多方便。
电动车两档变速器换挡机构设计讲解
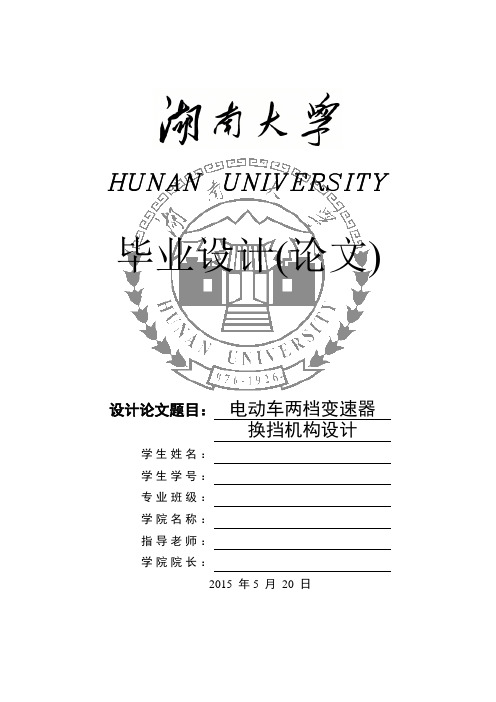
HUNAN UNIVERSITY 毕业设计(论文)设计论文题目:电动车两档变速器换挡机构设计学生姓名:学生学号:专业班级:学院名称:指导老师:学院院长:2015 年5 月20 日电动车两档变速器换挡机构设计摘要变速器已经因为其对性能较大的提升逐渐成为一个电动车不可或缺的一部分,目前最常用的是AMT变速器。
本论文为此类型变速器设计一个换档机构(包括电机驱动的换挡执行机构),主要重点有:1,根据对电动汽车变速器的受力分析,对换挡机构进行结构设计,从而保证换挡机构性能,保证换挡过程中不可与其他零件产生干涉,结构紧凑。
准确地实现换挡电机对同步器的控制功能。
2,保证换挡电机符合要求。
需要计算同步器力矩和换挡力的大小,可以通过对换挡同步过程进行分析,通过约束换挡速度和拨叉行程这两个参数在合理范围内,根据不同换挡时刻主从动齿轮的转速差,由此计算出换挡力,以此为依据完成选换挡电机及传动机构的参数设计。
3,要选择合适的电动执行机构的结构形式,保证电动执行机构可以可靠平稳的换挡,并且通过结构设计对换挡过程进行优化,达到减小换挡时的冲击,保证寿命,减小换挡电机功率,减小成本的优点。
关键词:电动车两档变速器,换挡机构,结构设计,换挡过程优化,三维建模Electric car two speed transmission shift mechanism designAbstractbecause of its great performance,Transmission is becoming an integral part of an electric car, the most commonly used is the AMT transmission. this thesis is about designing a shift mechanism for this type of transmission (including amotor-driven shift actuator), the main focus are:1, based on stress analysis of electric vehicle transmission, the shift mechanism is designed to ensure that the performance of the shift mechanism to ensure that the shift process can not interfere with other parts, compact structure. Achieving the Shifting motor to control the synchronization accurately.2, to ensure the shift motor compliance with the requirements. Need to calculate the synchronization torque and the shifting power. Through an analysis of shifting during synchronization.By constraining the shifting rate and shift fork movement within reasonable limits to calculate the shifting force,depending on these,we can choose the appropriate shifting motor and shifting mechanism.3,To select the appropriate electric shifting actuator form, guarantee electric shifting actuator smooth and reliable, and by the structural design to make the shifting process optimization, to reduce the impact of the shift time to ensure longevity, reduced shift motor power,to reducing costs.Key Words:Electric car two speed transmission,Shifting mechanism,Structural Design,Shifting Process Optimization,3-dimensional modeling目录1绪论 (1)1.1 课题背景及目的 (1)1.2 国内外研究状况 (2)1.3 课题研究方法 (3)2 换挡电机执行机构设计 (4)2.1 选换挡电机执行机构结构形式 (4)2.2 换挡过程优化 (5)3 换挡电机的设计计算…………………………….……………...………………………....3.1 计算方法和主要分析思路 (10)3.2 主要设计参数 (11)3.3 换挡力的计算 (11)3.4 确定电动机型号和确定减速比 (14)3.5 对换挡行程优化的结果经行验证 (14)4 换挡机构的受力分析与设计校核 (15)4.1 蜗杆蜗杆的设计 (15)4.2 蜗轮轴的设计 (18)4.3 凸轮轴的设计 (25)4.4 换挡拨叉的设计 (30)4.5 自锁轴的设计 (36)5结论 (38)6致谢 (42)7参考文献 (43)8附录 (44)一、绪论1.1 课题研究背景及目的随着油价的不断上涨和人们对环境污染问题的日益关注,电动汽车因其安全可靠,清洁环保的特点而成为未来汽车研究和发展的重要方向。
机械手毕业设计说明书

机械手毕业设计说明书一、设计目的本毕业设计旨在设计一种机械手,能够根据预先设定的程序自动执行各种操作。
通过该设计,可以提高工作效率,减少人力成本,同时具备高精度和高可靠性。
二、设计背景近年来,随着工业自动化的不断发展,机械手在工业生产中的应用越来越广泛。
机械手凭借其高速、高精度、高可靠性等优势,成为工厂生产线上的重要设备之一。
因此,设计一种功能强大的机械手对于工业生产的提升具有重要意义。
三、设计内容1.机械结构设计本设计采用七自由度机械手结构,包括基座、旋转关节、摇摆关节、剪切关节以及爪子等部分。
结构设计中要考虑刚性、稳定性以及重量平衡等因素,确保机械手能够准确地执行各种操作。
2.传感器系统设计为了使机械手具备自主感知能力,本设计将配备多种传感器,如力传感器、视觉传感器等。
通过传感器系统的设计,机械手可以根据实时的反馈信息进行运动控制,提高操作的准确性和安全性。
3.运动控制系统设计运动控制系统是机械手的核心部分,本设计将采用PLC (可编程逻辑控制器)作为控制器,结合伺服驱动器实现机械手的精确定位和协调运动。
通过编写程序,机械手可以根据预先设定的路径和信号执行各种操作。
四、设计过程1.需求分析针对机械手的应用场景和功能需求,进行需求分析。
确定机械手所需执行的任务类型、速度要求、负载能力等。
2.机械结构设计根据需求分析,设计机械手的结构,包括基座、旋转关节、摇摆关节、剪切关节和爪子等。
进行力学分析和模拟,确保结构设计的合理性和可靠性。
3.传感器系统设计根据需求分析,确定机械手所需的传感器类型和数量。
选择合适的传感器并安装在机械手上,设计传感器的接口电路和数据处理算法。
4.运动控制系统设计选择合适的PLC和伺服驱动器,进行硬件选型和连接。
编写控制程序,实现机械手的位置控制、速度控制和力控制等功能。
5.整体集成与测试将机械结构、传感器系统和运动控制系统进行整体集成。
进行系统测试,检验机械手的功能和性能是否满足设计要求。
机械手的设计详解

1 前言1.1 国内外发展概况]1[机械手首先是美国开始研制的。
1958年美国联合控制公司研制出第一台机械手。
它的结构是:机体上安装一个回转长臂,顶部装有电磁块的工件抓放机构,控制系统是示教型的。
1962年,美国联合控制公司在上述方案的基础上又试制成一台数控示教再现型机械手。
商名为Unimate(即万能自动)。
运动系统仿照坦克炮塔,臂可以回转、俯仰、伸缩、用液压驱动;控制系统用磁鼓作为存储装置。
不少球坐标通用机械手就是在这个基础上发展起来的。
同年该公司和普鲁曼公司合并成立万能自动公司,专门生产工业机械手。
1962年美国机械制造公司也实验成功一种叫Vewrsatran机械手。
该机械手的中央立柱可以回转、升降采用液压驱动控制系统也是示教再现型。
虽然这两种机械手出现在六十年代初,但都是国外工业机械手发展的基础。
1978年美国Unimate公司和斯坦福大学,麻省理工学院研究Unimate-Vicarm型工业机械手,装有小型电子计算机进行控制,用于装配作业,定位误差小于±1毫米。
联邦德国机械制造业是从1970年开始应用机械手,主要用于喷涂、起重运输、焊接和设备的上下料等作业。
联邦德国KnKa公司还生产一种喷涂机械手,采用关节式结构和程序控制。
日本是机械手发展最快、应用最多的国家。
自1969年从美国引进两种机械手后大力从事机械手的研究。
前苏联自六十年代开始发展和应用机械手,至1977年底,其中一半是国产,一半是进口。
目前,工业机械手大部分还属于第一代,主要依靠工人进行控制;改进的方向主要是降低成本和提高精度。
第二代机械手正在加紧研制。
它设有微型电子计算控制系统,具有视觉、触觉能力,甚至听、想的能力。
研究安装各种传感器,把感觉到的信息反馈,是机械手具有感觉机能。
第三代机械手则能独立完成工作中过程中的任务。
它与电子计算机和电视设备保持联系,并逐步发展成为柔性制造系统FMS和柔性制造单元FMC中的重要一环。
同步器换挡原理

同步器换挡原理一、引言同步器换挡原理是指在机械系统中,通过同步器实现传动轴与驱动轴之间的切换,以实现不同的工作模式。
同步器换挡原理在各种机械设备中广泛应用,特别是在汽车、摩托车等车辆的变速器系统中。
本文将全面、详细、完整地探讨同步器换挡原理及其应用。
二、同步器换挡原理的定义和作用同步器是一种用于进行轴向连接和断开的装置,能够实现传动轴和驱动轴的精确同步。
同步器换挡原理是指通过同步器的切换,将发动机的动力传递到车辆的传动系统中,从而实现不同速度和扭矩的输出。
同步器换挡原理的作用是在车辆行驶过程中,根据驾驶员的需求,将发动机的动力传到车轮上,以实现不同的行驶速度和动力输出。
三、同步器的结构和工作原理同步器通常由同步套、同步器齿圈、同步器齿环以及多个同步器齿块等组成。
同步器的工作原理是通过将同步套和同步器齿圈插入,使其齿与动力齿轮的齿互相啮合,从而实现传动轴和驱动轴的同步。
同步器工作的基本过程如下: 1. 同步器的初始状态为断开状态。
2. 当驾驶员需要进行换挡时,将离合器踏板踩下,使发动机与传动系统断开。
3. 同时,将换挡杆从当前挡位移到目标挡位,并且此时同步器开始工作。
4. 同步器齿环和同步套齿互相啮合,通过齿的咬合作用,实现传动轴和驱动轴的同步。
5. 当同步器齿环和同步套齿完全啮合时,发动机动力可以传递到车轮,并且换挡过程完成。
6. 最后,释放离合器踏板,发动机与传动系统重新连接。
四、同步器的优点和应用同步器作为传动系统中重要的组成部分,具有以下优点: - 实现换挡平稳:同步器能够使传动轴和驱动轴的转速同步,避免了换挡过程中的冲击和颤动,使车辆的换挡更加平稳。
- 增强可靠性:同步器通过齿的咬合作用,确保换挡过程中传动轴和驱动轴的准确同步,提高了传动系统的可靠性。
- 提高换挡速度:同步器的工作原理使得换挡过程更加简便快捷,提高了换挡速度,从而提升了车辆的性能。
同步器换挡原理广泛应用于各种机械设备中,特别是在汽车、摩托车等车辆的变速器系统中。
- 1、下载文档前请自行甄别文档内容的完整性,平台不提供额外的编辑、内容补充、找答案等附加服务。
- 2、"仅部分预览"的文档,不可在线预览部分如存在完整性等问题,可反馈申请退款(可完整预览的文档不适用该条件!)。
- 3、如文档侵犯您的权益,请联系客服反馈,我们会尽快为您处理(人工客服工作时间:9:00-18:30)。
长春大学 毕业设计任务书
题目 同步器寿命性能试验中换档机械手结构设计 性 质: □毕业设计 □毕业论文 教 学 院 机械学院 专业班级 机械0841112 学生姓名 罗斌
下发 09年 3月 1日 完成 09年 6月 1日 同步器寿命性能试验中换档机械手结构设计 一、课题研究的目的和意义 21世纪是汽车工业飞速发展的时代,汽车工业逐步成为许多国家的支柱产业。为了控制汽车产品质量,提高汽车品质,势必对其总成及零部件提出更高更严格的要求。 变速器是汽车传动系中一个重要总成。同步器是汽车变速器的重要部件,主要用于汽车行驶中平稳变速换挡,操纵轻便灵活,消除冲击噪音和降低汽车油耗。同时,防止变速箱齿轮的损坏,直接影响变速器寿命。因此,研制先进的同步器试验系统,对提高汽车试验技术有着重要意义。 同时,汽车是一个由许多种零部件组成的复杂的机械系统。对于产品开发所需的许多技术资料,目前尚不能通过理论计算得到,只能通过试验,因此有人说“汽车是试验出来的”。国外汽车工业由于发展时间较长,且对试验检测工作十分重视,在资金上给予了巨大的投入,一般都有较为齐全的试验装备。再加上严格管理和精良的加工设备,与国内形成了较大的差距。所以,我国汽车厂必须加大对试验检测设备的投入,才能大大缩短同国外同类厂家在试验手段上的差距,有利于我国汽车产品在国内外的竞争能力。 本课题正是基于上述情况,利用驱动机械手代替手动换挡来研究变速器总成中同步器寿命试验。
二、 同步器介绍 2.2.1同步器的作用 现代汽车上广泛采用活塞式内燃机作为动力源,其转矩和转速变化范围较小。而复杂的使用条件则要求汽车的牵引力和车速能在相当大的范围内变化。第一章绪论为解决这一矛盾,在传动系中设置了变速器。 变速器在换挡时,由于两齿轮轮齿不同步时的强制挂挡,使得因两轮齿间存在的速度差而发生冲击和噪音。这样,不但不易挂挡,而且影响了轮齿寿命,使齿端部磨损加剧,甚至使轮齿折断。所以在变速器换挡过程中,必须使所选挡位的一对待啮合齿轮轮齿的圆周速度相等(即同步),才能使之平顺地进入啮合而挂上挡位。因此,产生了同步器。 同步器是工业车辆机械变速箱的关键部件,直接影响车辆操纵换挡性能。它是在接合套换挡机构基础上发展起来的。其中包括接合套、花键毂、对应齿轮上的接合齿圈,以及使接合套与对应接合齿圈的圆周速度迅速达到并保持一致的机构,以及阻止两者在达到同步之前接合以防止冲击的结构。目前,同步器的型式主要有常压式、惯性式和自行增力式三种。其中以惯性式同步器的应用最为广泛。如CA1091中型载货汽车六挡变速器中五、六挡使用的是具有锁环装置的惯性同步器。东风EQ1090E型汽车五挡变速器使用的具有锁销装置的惯性同步器。 2.2.2同步器的工作原理 为避免机械变速箱在换挡时冲击噪声大,一般都采用惯性式同步器(以下简称同步器)。它与常压式同步器一样,都是依靠摩擦作用实现同步的。但它可以从结构上保证接合套与待接合的花键齿圈在达到同步之前不可能接触,以避免齿间冲击和发生噪声。按同步器摩擦面的形状分为锥形同步器,片形同步器和多锥形同步器。图1-1为典型的锥形同步器结构简图。此种类型的同步器也是本课题检测中所使用的同步器。在回位弹簧4作用下,接合套2保持在空挡位置(对应工作原理图1-2a)。挂挡时接合套移动,摩擦面接触,因接合元件即接合套与空转齿轮的转速不同,在摩擦面上产生摩擦力矩,使同步环转过一定角度,锁止面顶紧(对应工作原理图1-2b)。通过锁止面对摩擦面加压,在摩擦力矩作用下使接合套与空转齿轮同步。设计时,使锁止面的拔正力矩小于摩擦力矩,接合套不能进入啮合,只有在接合套与空转齿轮转速相同,摩擦力矩消失,同步环转过一定角度,锁止作用失效,接合套在轴向力作用下,继续移动才能与空转齿轮的花键啮合,完成换挡(对应工作原理图1-2c)。
图1-1锥型同步器结构示意图 1.同步环 2.结合套 3.空转齿轮 4.回位弹簧 5.锁止齿 6.啮合齿 7.锥型摩擦面 8.齿毂 图1-2同步器工作原理 (a)接合套空挡 (b)顶住锁止面 (c)接合套与空转齿轮的花键啮合 1.同步环 2.接合套 3.锁止面 4.空转齿轮的花 1.2.3同步器的使用 根据上述的同步器工作原理,我们可以进一步理解下列几个问题: 1)下长坡时要及早挂入低速挡,以充分利用发动机的辅助制动功能。千万不可熄火空挡滑行,否则安全性不易保证。此外,若换挡时间过晚,挂不上低速挡时,可以考虑踩制动踏板,再配合加油。 2)若离合器分离不彻底,所需挡位接合齿圈转速难以达到同步转速,会导致挂挡困难。 3)同步器锁环磨损严重,定位弹簧变软,滑块缺损等,易导致挂挡困难或出现异响。 4)应及时换挡,爬坡时不能拖挡,高挡不硬撑。 5)正常换挡要脚轻手快。从上述工作原理分析可知,同步器实质是一种强制同步装置。在换挡时,惯性作用通过摩擦力矩形式使所需挡位接合齿圈(升挡减速,降挡加速)迅速达到与接合套的惯性转速(即上一个挡位转速)相同,从而实现同步换挡。在未达到同步之前,不论对操纵手柄使多大力都难以挂入所需挡位。同步器损坏会导致挂挡困难,需要换件或整体更换。锁环式同步器若锁环磨损严重,即接合齿和内锥面磨损严重,失去锁止作用,会导致摩擦作用减弱,同步时间延长,致使挂挡困难,应更换新锁环。锁销式同步器若锥盘与锥环锥面磨损严重,会导致同步时间延长;锁销磨损严重会失去锁止作用。因锁销式同步器不可拆卸,应更换新同步器。 同步器在使用中应注意以下事项: 1)换挡时离合器踏板一定要踩到底,否则会加剧锁环内锥面或锥环外锥面的磨损,缩短同步器的寿命。 2)变速器内的齿轮油量要达到标准液面高度,以满足润滑需要。 3)合理使用两脚离合器换挡法,动作要熟练,时机要准确。 4)上、下坡时,要掌握挂入低速挡的时机,否则挂挡困难,会加剧同步器的磨损。
三、 课题任务 根据我国汽车行业标准,本课题要研制出变速器总成中同步器寿命性能试验台。通过操作该试验台,可手动亦可自动完成汽车变速器寿命及性能试验。 具体要求如下: 1)试验台可对变速器试验样品进行寿命及性能试验。 2)针对力及扭矩、转速、位移等参数,试验台可分别对以上参数进行检测。 3)要求匀速施加驱动力(静压力),驱动速度可调。 4)试验台具有连续运转能力,每次连续运转可达到1800小时。 5)驱动及检测全程微机控制。 具体设计技术指标如下: 1)换挡行程:0~±250mm。 2)选挡行程:0~±200mm。 3)换挡力测量范围及精度:0~±500N;±1.0%FS。 4)选挡力测量范围及精度:0~±300N;±1.0%FS。 5)换挡速度控制范围及精度:0~1.2m/s;±1.0%。 6)换挡频率:0.05~0.3Hz。 7)输出轴扭矩测量范围及精度:0~±1000Nm;±0.2%FS。 8)同步时间测量精度:±0.001s。 9)挡位位置控制精度:±2mm。
四、主要研究内容 针对以上课题研究的任务,本文在查阅大量参考资料和加以调研的基础上,对以下内容进行了重点研究。 1.系统总体方案的制定 其中包括机械系统、驱动系统、计算机检测系统、软件程序设计系统及其它部分设计的制定。 2.数学模型的建立 其中包括机械手空间模型、换挡接合过程的数学模型等的建立。 3.系统中的通讯接口 微机与变频器之间的通讯系统设计。 4.信号检测系统设计 其中包括输入轴转矩转速检测系统及同步器液压伺服控制系统等设计。 5.同步器性能和试验程序设计 其中包括性能试验、可靠性试验。 6.试验数据与结果分析 实验测到的数据并对结果进行分析。 下图为装配外观图 五、 系统总体方案介绍 课题研究的系统要求可以对同步器进行性能和可靠性两种方式的试验。通过手动操作可实现同步器的换挡过程;也可利用驱动系统来自动换挡,模拟人手对同步器进行的换挡过程。同时利用计算机检测系统,采集各种传感器发来的信号,对其处理分析后,来检测被试验同步器的性能与可靠性。本系统是典型的机电一体化系统。
5.1 试验系统的组成及控制原理 整个系统包括试验台,被测同步器变速箱总成,调速电机,驱动系统,机械手,传感器,电控柜,微机等部件。其中电控部分采用微机测控系统,系统整体框图如图2-1。 图2-1 系统结构框图 5.1.1 机械系统的工作原理 该系统分为手动操作和自动操作两种工作方式。在进行同步器性能试验,测量试验中的各项参数时,一般采用手动方式操作试验台。在进行同步器可靠性试验时,设定要执行的工况和工况数后,一般采用自动方式操作试验台。自动方式利用具有位置控制功能的机械手来模拟人手的换挡过程。机械手功能的实现利用一个滑动副及一个万向节联合实现,滑动副由在一套筒内嵌入的直线轴承和滑杆构成。如图2-2机械手基本构成所示。
图2-2 机械手基本构成 5.1.3驱动系统的工作原理: 同气动系统比较,采用电动系统具有机构简单,机械强度高,传动平稳,易实现无级调速,驱动力大等特点。因此,本设计最终采用了电动方式的驱动系统。以保证系统正常运行。由于本设计要求的精度高,两个电机通过机械滑台结构十字交叉的连接在一起,装置中的伺服系统提供反馈,用来控制操作杆的选挡运动和换挡运动。同时在滚珠丝杠上固定的位移传感器在电机运动时实时的采集位移信号,传送到计算机系统中。该系统采用位置闭环控制,由微机给定电压值,经D/A变换、伺服放大后,控制电机运动,同时不断的与位移传感器测到的电压值相比较,若不相等则有电压输出,该电压经调制、放大解调后驱动电动机。但是机械手是一个非线性的控制对象,单纯的伺服反馈控制难以满足模拟人手换挡时的动态性能及稳态精度的要求。因此在计算机检测系统中也加入了直接数字控制系统中常用的PID控制算法,从而很好的达到了模拟人手换挡的功能。
5.1.4计算机检测系统的组成 一个完整的计算机检测系统,需要在微机、被控制对象和操作者之间适时、