陶瓷 粉体制备燃烧法
真空烧结法

真空烧结法
真空烧结法是一种高温固相反应制备陶瓷材料的方法。
该方法是将陶瓷粉末置于真空或惰性气体环境中,通过高温烧结使粉末颗粒结合为致密的块状体。
这种方法可以制备出高密度、高强度、高硬度、高耐磨性的陶瓷材料。
真空烧结法的工艺过程主要包括以下几个步骤:首先是粉末制备,将所需的陶瓷粉末按照一定的配比进行混合,并进行球磨或干燥处理,以获得均匀的颗粒大小和分布。
然后是模具成型,将粉末填充到模具中,进行压制,制成所需形状的坯体。
接着是烧结处理,在真空或惰性气体环境中进行高温烧结,使粉末颗粒结合成致密的块状体。
最后是后处理,对于需要进行表面处理的陶瓷材料,可以进行抛光、打磨等处理,以提高其表面质量和光洁度。
真空烧结法具有烧结温度低、烧结时间短、成型过程简单等优点,可以制备出高品质的陶瓷材料,广泛应用于电子、光电、航空、军工等领域。
- 1 -。
气窑烧制技术

气窑烧制技术气窑烧制技术是陶瓷生产中重要的烧制方法之一。
随着陶瓷工业的发展和技术的进步,气窑烧制技术在烧制温度、气氛控制、节能减排等方面得到了广泛的应用和改进。
本文将从气窑烧制技术的原理、分类、特点、优缺点、节能减排等方面进行介绍和分析。
一、气窑烧制技术的原理气窑烧制技术是利用燃烧产生的高温气体将陶瓷原料加热到一定的温度,使其物理、化学性质发生改变,实现陶瓷制品的成型和烧结。
气窑烧制过程中,熔体可流动,充分融合,且可通过气氛控制实现不同色泽和光泽等效果。
气窑烧制技术适用于釉瓷、粗陶、精细陶、珐琅彩等各种类型的烧制。
二、气窑烧制技术的分类1. 直燃式气窑烧制技术:直燃式气窑是利用天然气、煤气等直接燃烧进行热能转化,陶瓷制品在直燃式气窑中进行烧制。
2. 间接式气窑烧制技术:间接式气窑是利用燃烧室和加热室隔离的方式,通过燃烧室的燃烧产生高温气体,再经过加热管加热陶瓷制品进行烧制。
三、气窑烧制技术的特点1. 温度均匀:气窑烧制技术利用气流的对流作用,使得热能能够均匀地传递到烧制的陶瓷制品表面,从而实现温度的均匀分布。
2. 烧结效果好:气窑烧制技术具有高温、氧化还原,有利于熔化和烧结陶瓷原料,从而实现制品的致密性、强度和耐磨性等性能的改善。
3. 精细成型:气窑烧制技术利用气流的作用,使得烧制过程中可实现制品表面的润滑、研磨和抛光等处理,从而实现更加精细的成型。
4. 节能减排:气窑烧制技术可以通过气流的控制实现节能减排,降低能源的消耗和环境污染物的排放。
四、气窑烧制技术的优缺点1. 优点:(1) 温度控制精密,能够实现较高的烧结温度和均匀的温度分布。
(2) 可通过气氛控制实现不同色泽、光泽和陶瓷品质的改良。
(3) 通过气流的作用,使得烧制出的陶瓷制品形状精细,加工过程简单,生产效率高。
(4) 可通过气流调节进行能耗控制和排放减少,有利于环保和节能。
2. 缺点:(1) 燃料成本较高,占用了一定的空间。
(2) 烧制过程中需要消耗大量氧气,容易造成酸雨等环境污染。
凝胶燃烧法制备KNbO_3纳米粉体

该方法具有工艺简单 , 成本相对较低 , 以及粒度可控 等优点。柠檬酸凝胶 一 燃烧制备过程中 , 柠檬酸既作
为螯合剂 , 又在硝酸盐和柠檬酸组成的燃烧体系 中作
4(+N 6 + H +4 - H l + bOl 8 OH =K, ̄ Ol土+ Hz 9 9 4 O
KM, bOl+1 H +l O =6 bO 5, K N ̄ 9 5  ̄ l N ( H)J +4  ̄
(- )3 9 3 2 5- : 2 - 3 6
6 HURREL .BOZI S D L JP NI G.T e fro lc r d n h e r ee ti mo e i c
算可知 , 产物的颗粒增加 , 计算结果 见表 l 。
图3 是不 同温度下退火得到产物 的 T M 照片。 E 从 图中可以看 出 , 当退火温度大于 60 0 ℃时 , 产物均 为粒径均匀 、 分散性较好 的长方体颗粒。当退火温度
L 上 ! L… 』一 L 竺 一^^
一
图 1 N前躯体的 T D C 曲线 K G— S
Fg 1TG- i. DSC u v so h mc mo c re f e KN p u m t
表 1 不同温度退火后得 到 K.r 占 aH N粉体的晶粒尺寸 r 目
凝胶燃烧法制备 K b 纳米粉体 N O3
陈积世 张俊计 吴秀娟 袁 晓曼 武 斌
( 大连交通大学材料科 学与工程 学院, 辽宁 大连 165) 108
摘 要
以自 制的水合氧化铌 n 25 H0为铌源 , b  ̄ ) 0 n 硝酸钾(N s K O) 为钾源 , 采用柠檬酸凝胶 一燃烧 法制 备出铌酸钾 (N 0,N 粉体。 K b。 ) K 通过 T /S GD C研究 了前躯体 粉末的热分解过 程 ; 助 X D和 T M 对 样品的晶体结 构 、 形貌和粒径进 行了表征 。 攘 明 , 借 R E 微观 结另 过多 的柠檬酸和羧酸盐在 30 3℃附近分解成碳酸盐 , 60 在 0℃时 K N相开始形成 , 没有中间相产生。煅烧温度大于 60 0℃即可获得
喷雾热解法资料.
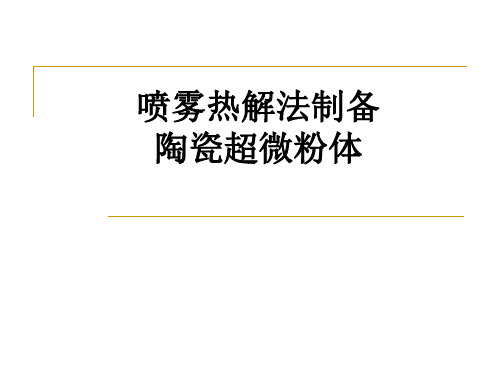
金属盐溶液
冻结液滴 溶剂升华
喷 雾 (10~20μm)
热风中溶 高温介质中 溶剂蒸发+
剂蒸发
溶剂蒸发
热分解
金属盐粒子
热分解
分类 冷冻干燥法
氧化物粒子 喷雾干燥法 热煤油法 喷雾热解法
喷雾干燥装置图
喷雾干燥法的特点
原料盐必须能溶于溶剂中 快速干燥,粉体呈球形; 粉体组分均一,纯度高; 可用于造粒。 如镍、铁、锌混合硫酸盐的制备,粒径约10~20μm
盐→200nm软铁氧体微粉
喷雾热解法
较为新颖的方法,最早出现于60年代末; 溶剂蒸发与金属盐热解在瞬间同时发生,生成产物与
原料盐具有不同的化学组成;也称为喷雾焙烧法,火 焰喷雾法,溶液蒸发分解法等。 喷雾可进入加热的反应器或喷至高温火焰两种方法, 一般用可燃性溶剂,以利用其燃烧热
喷雾热解装置图
1m 500nm
0.5M-g2-600
0.5M-g2-700
还原剂种类对粉体形貌的影响
1m
0.5M-g2-500
500nm 500nm
0.5M-u2-500
0.5M-u2-600
烧结体的SEM
0.5M-500
0.5M-g2-500 0.5M-u2-500 0.5M-u2-600
SDC样品的电导率与温度的关系
致密Ni的制备
改变以表面反应(沉淀)为主的反应方式,到以 体内反应(沉淀)为主的反应方式
方法:在Ni(NO3)3溶液中加入一定的氨水,使 之与Ni2+形成络合物
反应方程式
(a) T1 = 200 oC,
T2=400 oC, pure NiO;
(b) T1= 300 oC, T2 . =800oC, containing Ni and NiO;
一种陶瓷窑炉氢气燃料燃烧系统及节能工艺的制作方法

一种陶瓷窑炉氢气燃料燃烧系统及节能工艺的制作方法摘要本文介绍了一种关于陶瓷窑炉氢气燃料燃烧系统及节能工艺的制作方法。
该系统由氢气供应系统、燃烧系统和控制系统组成,能够有效地利用氢气作为燃料,在陶瓷窑炉内进行高效、清洁的燃烧,实现节能环保的目标。
1.引言陶瓷行业在生产过程中消耗大量的能源,传统的燃料燃烧方式存在能源浪费和环境污染的问题。
因此,研发一种高效、清洁的氢气燃料燃烧系统对于提高能源利用效率和降低环境负荷具有重要意义。
2.系统组成2.1氢气供应系统氢气供应系统是该燃烧系统的核心组成部分,主要包括氢气储存装置、气体输送管道和气体供应控制装置。
氢气储存装置采用高压气瓶,能够储存足够的氢气供应给窑炉燃烧系统。
气体输送管道将储存的氢气输送至燃烧系统,并通过气体供应控制装置实现氢气的稳定供应。
2.2燃烧系统燃烧系统是陶瓷窑炉中氢气燃烧的关键部分,主要包括燃烧室、喷枪和燃烧控制装置。
燃烧室是氢气与空气混合燃烧的空间,具有良好的密封性和隔热性能,确保氢气燃烧过程的安全性和高效性。
喷枪负责将氢气和空气按一定比例混合,并喷射到燃烧室内进行燃烧。
燃烧控制装置通过监测燃烧室内的气体组成和温度等参数,实现对燃烧过程的精确控制。
2.3控制系统控制系统是整个燃烧系统的大脑,负责对氢气燃料燃烧过程进行监控和调节。
控制系统通过传感器检测燃烧室内的气体排放浓度、温度等参数,并将数据传输给控制器。
控制器根据设定的工作参数,对燃烧系统中的氢气供应、气体混合比例和燃烧温度等进行自动调节,以实现燃烧过程的优化控制。
3.制作方法3.1设计氢气供应系统根据窑炉的燃烧需求和氢气消耗量,确定所需的氢气储存容量和储存装置类型,选用高压气瓶作为氢气储存装置,并确保气体输送管道的安全性和密封性。
3.2搭建燃烧系统根据窑炉的形状和尺寸设计燃烧室结构,选用耐高温材料进行构建,确保燃烧室具有良好的密封性和隔热性能。
选择合适的喷枪,确保氢气和空气能够按要求的比例混合并喷射到燃烧室内。
陶瓷艺术的烧成方法

陶瓷艺术的烧成方法陶瓷品制作完成后,还要经过烧制才能最终成为成品。
那么,你知道陶艺的烧成方法有哪些吗?以下是有我为大家整理的,希望能帮到你。
陶瓷的烧成方法1、素烧法:表面不上釉的作品,直接烧成称为素烧。
素烧可以保留陶瓷作品上的手工痕迹,显现材质的自然和本质的美。
陶的素烧温度为900~1150℃。
瓷的素烧温度为1100~1310℃。
2、本烧法:陶瓷作品坯体表面上釉后,用高温一次性烧成,使坯体完全烧结,釉料完全融化,称为本烧。
烧成温度为1100~1350℃。
3、釉烧法:釉烧分两次烧成,陶瓷坯体经过一次素烧后再上釉,用低温二次烧成,使釉完全融化,烧成温度为900~1000℃。
4、氧化焰法:调整烟道阀门,保证窑内空气充足,定时添加燃料,使燃料在空气中彻底烧尽,由于窑炉氧气充足,则形成氧化焰气氛5、还原焰法:当温度加速升温至高温阶段,放低烟道阀门,使窑炉供养不足,炉内碳素增加,形成还原焰气氛。
6、乐烧法:乐烧采用二次烧成的工艺技术。
第一次素烧,温度为700~900℃。
再上釉,用低温二次烧成。
7、盐烧法:坯体在高温时,将氯化钠直接撒入在燃烧的窑炉中,氯化钠开始挥发,产生纳蒸气,这种纳蒸汽同陶瓷坯体表面的铝与硅产生反应,熔融成釉形成带有肌理的透明釉。
8、熏烧法:熏烧采用素烧和烟熏二次完成的工艺技术。
在素烧完成后再选用木屑、树枝、报纸等作燃料产生浓烟,通过坯体表面的缝隙使碳素附着于作品表面,形成自然的斑迹效果。
9、柴烧法:一种用木柴直接烧陶的方法。
因柴火直接在体坯上留下自然的“火痕”和木柴燃烧后的灰烬落在作品表面形成的“落灰釉”,使得作品色泽温润且有变化。
烧制陶瓷工艺流程烧制陶瓷的关键因素是:泥、釉、火。
为什么有些陶、瓷器会莫明其妙的出现裂纹呢?为什么有时甚至会掉皮釉呢?这不外是在一定温度条件下泥和釉的收缩系数又称膨胀系数不相一致的结果。
有时人们亦会对这种缺陷特意加以利用,传统的开片釉及现代陶艺的一些肌理追求就是利用釉和泥收缩系数不相一致的原理配制出来的。
10.钛酸钡粉体制备方法(55)解析

39
七、双氧水共沉淀法
该法主要是以偏钛酸为钛原料,用 双氧水、氨水及硝酸钡为添加剂,经 转化共沉淀得到纳米晶或亚微米钛酸 钡前驱体,再经热分解制备纳米或亚 微米钛酸钡。
40
其反应方程式为:
H2TiO3+H2O2+2NH3→(NH4)2Ti4O4+H2O
(NH4)2Ti4O4+Ba(NO3)2→BaTiO4↓
34
工艺流程及原理为:将等摩尔 的氯化钡溶液及四氯化钛水溶液 混合后 , 与六摩尔当量的碳酸氢 铵反应 , 得到胶体二氧化钛和碳 酸钡沉淀相互包裹的沉淀 , 经分 离洗涤、烘干、煅烧后得到钛酸 钡粉体。
35
该方法工艺简单,但氯根很难洗 净,容易带入杂质,特别是钙离 子,纯度偏低。还有一问题是加 料速度过快,会产生大量的气泡, 反应难以于控制,同时前驱体的 过滤也较困难。
30
粉料中含少量碳酸钡。若制备过程在 惰性气氛中进行,则碳酸钡含量减少, 但不能完全消除。因为干燥过程中,粉 体与空气中的二氧化碳反应也能形成少 量碳酸钡,随煅烧温度的提高到 1000℃ 时,碳酸钡全部分解,粉体为纯的钛酸 钡相。 该方法的优缺点为:制备的颗粒团 聚较少,颗粒分散性好,粒径分布也较 均匀,但含少量碳酸钡。
18
水热合成法是把含有钡和钛的前体 (一般是氢氧化钡和水合氧化钛)水浆 体,置于较高的温度和压力下(相对于 常温、常压),使它们发生化学反应。 经过一定时间后,钛酸钡粉体就在这 种热水介质中直接生成。该法制备的 晶粒发育完整,粒度分布均匀,颗粒 之间很少团聚。
19
采用氢氧化钡和偏钛酸为原料合成钛 酸钡,在反应过程中会生成少量的BaCO3, 但在其后的煅烧阶段少量的碳酸钡会进一 步与偏钛酸反应,还有少量的碳酸钡用醋酸 洗涤,再水洗即可除掉;煅烧温度 600700℃,降低了煅烧温度;分析结果显 示,所得产品纯度高,粒径小,能满足电 子工业对高质量钛酸钡粉体的需求。
Sialon陶瓷

型:α型和β型。在Si-Al-O-N四元系统中,由于阳离子M
(Si4+、Al3+)与阴离子X(N、O)的比例不同,形成的固溶
体也不同,由相应相图可知,在该Si-Al-O-N四元系中存
在β’ -Sialon、 α’ -Sialon、O’ -Sialon、X-Sialon和
AlN多型体(8H、12H、15R、21R、27R等)。
Sialon(赛隆)。
Sialon陶瓷分类
• Sialon陶瓷的主要类别有β’-sialon、α’-sialon、
O’-sialon三种,尤以前两种最为常见。除此以外,
由于铝和氧的固溶状态不同,Sialon还有x型和
AIN多型体等晶体类型。
Sialon陶瓷结构
• Sialon的晶体构型与Si3N4相类似。理想的Si3N4结构 是三个[SiN4]四面体共角形成空间骨架,具有两种晶
中,用发热体点燃反应混合物顶端的钛颗粒,并产生
2 000℃以上的高温,使反应混合物开始燃烧(氮化
反应)。
Sialon陶瓷应用及发展
• Sialon陶瓷在高温下具有良好的机械性能、抗热
震性和良好的抗氧化性,膨胀系数小,化学稳定性
高,耐腐蚀,因此其应用领域广泛,可用在机械、
化工、冶金、航空航天、医学、生物、汽车等领
域。
• ①可利用其高硬度作耐磨材料;②利用其在高温
Sialon陶瓷应用及发展
• 下化学性质稳定、与熔融金属间相容性好的特点,
用来做有色金属合金的压延、热挤压或拉丝等成
型模具;③利用其好的抗热震性及韧性、扩散系
数小等特点,用作金属切削刀具;④ 还可用做热
机或其他热能设备,也是密封圈、轴承、阀体的理