AlN基片的薄膜金属化
金属化聚酯膜

m 自愈点(PCS/ 2 )
聚酯膜 1.395
≥150
≥4300 MD≥100 TD≥75 MD≤3.0 TD≤1.5 < 0.5
3.2 ≤ 50 ≥30,000 > 150 (≤3μm) > 200 (3~4μm) > 250 (≥4μm)
≤5
测试标准
150℃±2℃,30min 24h, 20℃
1kHz, 23℃±2℃ 1kHz, 23℃±2℃
b≤ 0.3 0.3 < b ≤ 1.0
1.0 < b ≤ 2.0 b > 2.0
±0.15 ±0.2 ±0.25 ±0.3
聚酯基膜技术指标 项目
密度(g/cm3) 抗拉强度(Mpa) 弹性模量(Mpa)
拉伸率(%) 热收缩率(%) 吸水性(%) 介电常数(%) 损耗角正切(×10-4) 绝缘电阻(MΩ·μF) 平均耐电压(VDC/μm)
铝金属化膜pea厚度厚度m1712偏差10宽度和留边宽度width45mm方块电阻方阻值偏差1024252430膜卷内径外径内径外径7574576155130160175135180240200250300260320薄膜宽度和留边的允许偏差薄膜宽度b及允许偏差mm留边宽度b及允许偏差mm64010301564300015031002300210200252003聚酯基膜技术指标项目聚酯膜测试标准密度gcm31395抗拉强度mpa150弹性模量mpa4300拉伸率md100td75热收缩率md30td15150230min吸水性0524h20介电常数321khz232损耗角正切104501khz232绝缘电阻mf30000平均耐电压vdcm100vdcm
偏差 ±25% ±30%
金属化
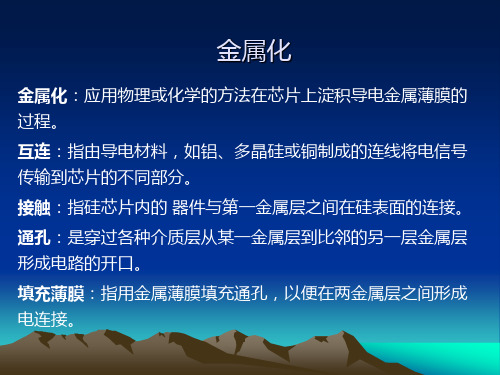
蒸发
• 蒸发是将待蒸发的材料放置进坩埚,在真空系统中加热并 使之蒸发,淀积在硅片表面。最典型的方法是利用电子束 加热放置在坩埚中的金属,在蒸发器中通过保持真空环境, 蒸气分子的平均自由程增加,并且在真空腔里以直线形式 运动,直到它撞到表面凝结形成薄膜。 • 蒸发的最大缺点是不能产生均匀的台阶覆盖,逐渐被拥有 很好台阶覆盖的溅射所取代。 • 另一缺点是对淀积合金的限制,为了淀积由多材料组成的 合金,蒸发器需要有多个坩埚,这是因为不同材料的蒸气 压是不同的
阻挡层金属
• 阻挡层金属是淀积在硅和金属塞之间的一层金属。可以阻 止上下层材料互相混合,消除浅结材料扩散或结尖刺的问 题,提高欧姆接触可靠性。常规的阻挡层金属有钨,钛, 钼,铂,钽。
可接受的阻挡层金属的基本特性
• • • • • • 1、很好的阻挡扩散特性。 2、高电导率具有很低的欧姆接触电阻。 3、在半导体和金属之间很好的附着。 4、抗电迁移。 5、在很薄并且高温下具有很好的稳定性。 6、抗侵蚀和氧化。
铝互连
欧姆接触
• 概念:金属和半导体的接触,其接触面的电阻值远小于半 导体本身的电阻,使得组件操作时,大部分的电压降在活 动区(Active region)而不在接触面。
• 在改进欧姆接触早期工作遇到的困难是:在加热 过程中,铝和硅之间出现了不希望出现的反应, 该反应导致接触金属和硅形成微合金,这一过程 被称为结“穿通”。同时硅向铝中扩散,在硅中 留下了空洞,当纯铝和硅界面被加热时结尖刺发 生,导致结短路,
金属填充塞
• 多层金属化生产了对数以十亿计的通孔用金属填充塞的需 要,以便在两层金属之间形成电通路,接触填充塞也被用 与连接硅片中硅器件和第一层金属化,目前被用于填充的 最普遍的金属是钨,钨具有均匀填充高深宽比通孔的能力, 钨可以抗电迁移引起的失效,因此也被用于做阻挡层以禁 止硅和第一层金属之间的扩散反应,钨是难熔材料,熔点 3417°。
PVD 金属化工艺

目录:Chapter PVD1. 概述1.1 金属化工艺的作用1.2 金属化材料的要求1.3 合金材料的使用1.4金属化膜与半导体的接触1.5 薄膜沉积技术2.物理气相沉积2.1 溅射沉积2.2溅射腔体结构2.3 溅射的工艺条件2.4 膜的工艺参数及性质3.AL/SI接触及其改进3.1 AL中掺入少量的SI3.2 AL-阻挡层结构4.AL膜的电迁移4.1 提高AL膜沉积温度4.2 AL中掺入少量的Cu4.3 三层夹心结构5.金属膜的应用5.1 AL膜5.2 TI膜5.3 TIN膜5.4 金属硅化物膜6.多重内连接工艺6.1 回付法制作插塞6.2 高温AL7.台阶覆盖7.1台阶覆盖率定义7.2提高台阶覆盖率的方法8.Collimetor9.其它Chapter RTA1. RTA原理极其利用PVD 金属化工艺引言本文主要讲述了PVD的工作原理、工艺条件以及工艺参数,并结合实际列举了一些常见问题及解决方法。
讲述了金属化材料的一些性质极其在实际中的应用。
1.概述1.1 金属化工艺的作用金属化工艺的作用归纳起来有如下几点:(1)连接作用:将IC里的各元件连起来,形成一个功能完善而强大的IC。
(2)接触作用:在栅区及有源区形成欧姆接触。
(3)阻挡作用:阻挡AL与SI的互溶,防止结的穿通。
(4)ARC作用:降低AL表面反射率,有利暴光。
(5)湿润作用:在热AL工艺中,室温TI有利于AL的流动以及在WCD 工艺之前,要COLLIMETOR溅TI+TIN。
1.2 金属化材料的要求目前能用作IC金属化的材料很多,有单元金属、多元金属、合金、硅化物等。
但是,无论使用哪种材料,都必须满足如下要求:(1)电阻率要低。
(2)与n型和p型硅能形成欧姆接触。
(3)与SI和SIO2的粘附性好。
(4)抗电迁移能力强。
(5)抗腐蚀能力强。
(6)易刻蚀。
(7)便于超声或热压键合。
(8)膜的应力要低。
1.3 合金材料的使用由于纯AL材料的电阻率低,与SI(或SIO2)的粘附性又好,而且易刻蚀,是一种作为导电连线的好材料,因而得到广泛使用。
(第七章)金属化
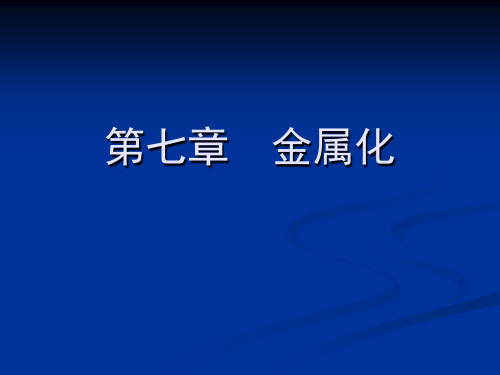
常用的硅化物 1. 硅化钛TiSi2 2. 硅化钴CoSi2 (0.25um及以下)
CMOS结构的硅化物
自对准金属硅化物的形成
金属填充塞
0.18μm STI 硅化钴 6层金属IC的逻辑器件
7.3 金属淀积系统
金属淀积系统: 1. 蒸发 2. 溅射 3. 金属CVD 4. 铜电镀
现代集成电路对金属膜的要求
1. 电阻率低:能传导高电流密度 2. 粘附性好:能够粘附下层衬底实现很好的电连接, 半导体与金属连接时接触电阻低 3. 易于淀积:容易成膜 4. 易于图形化:对下层衬底有很高的选择比,易于平 坦化 5. 可靠性高:延展性好、抗电迁徙能力强 6. 抗腐蚀性能好 7. 应力低:机械应力低减小硅片的翘曲,避免金属线 断裂、空洞。
半导体传统金属化工艺—物理气相淀积(PVD) SSI、MSI→蒸发 LSI以上→溅射
金属淀积系统——蒸发
蒸发是在高真空中,把固体成膜材料加热并使之变 成气态原子淀积到硅片上的物理过程。 蒸发的工艺目的
在硅片上淀积金属膜以形成金属化电极结构。
成膜材料的加热方式:蒸发器分为电阻加热、电子 束加热、高频感应加热等三种。在蒸发工艺中,本 底真空通常低于 10-6Torr。
RF(射频)溅射系统
磁控溅射是一种高密度等离子体溅射,是利用靶 表面附近的正交电磁场使电子平行靶表面做回旋 运动,从而大大增加了与氩原子的碰撞几率,显 著地提高了等离子体区的Ar离子密度,使溅射速 率成倍增加。
在溅射技术中,磁控溅射占主流。
蒸发和溅射的比较
特点
优
点
缺
半导体激光器腔面增透膜AlN薄膜的制备

导 致灾 变性光 学 损 伤 ( O 刮的发 生 。 高质 量 C D)
A 键, s 界面 O元素是与 A 元素结合的, l 有较好 的
界 面稳定 性 , 因此 , 1 膜 有 望对 G A 激 光 器 AN薄 as 起 到较好 的钝 化作用 。 本 文采 用 反 应 磁 控 溅 射 技 术 , 用 高 纯 A 利 l (999 ) 材 和 高纯 N 在 K 9 .9 % 靶 : 9玻 璃 片 上镀 制 AN薄膜 , 用 Flers 统测 试 薄膜 的光 学性 1 使 i tc 系 m i
半导体 激光器腔面增透膜 AN薄膜的制备 I
周 路, 王云华 ,贾宝 山,白端 元 , 张斯钰 , 忠 良,高 欣 ,薄报 学 乔
( 长春理工大学 高功率半导体激光 国家重点实验室 ,吉林 长春 10 2 3 02)
摘要 : 提出了一种新的半导体激光器增透膜——AN膜 , l 并用 m tb aa 软件模拟分析了不同腔面反射率对激 l
88n 0 m波长 AG A / a s 1a sG A 半导体激光器腔 面在激光器运转过程中需承受极高的激光功率密
度, 而且 有源 区含 A , 时间 运转 极 易 氧化 , 而 l长 从
伤阈值 和器件的输 出功率。陈堂胜等 在 AN 1/
G A 界 面 的 A S和 X S研 究 中报 道 AN G A as E P 1/ a s
收稿 日期 : 0 1 80 ;修订 日期 : 0 11 ・ 2 1- -3 0 2 1・O2 7 作者简介 : 周路( 9 7一) 女 ,吉林 长春人 ,博士 ,主要从事高功率半导体激光器 的研究 。 18 ,
AlNBN纳米结构多层膜微结构及力学性能
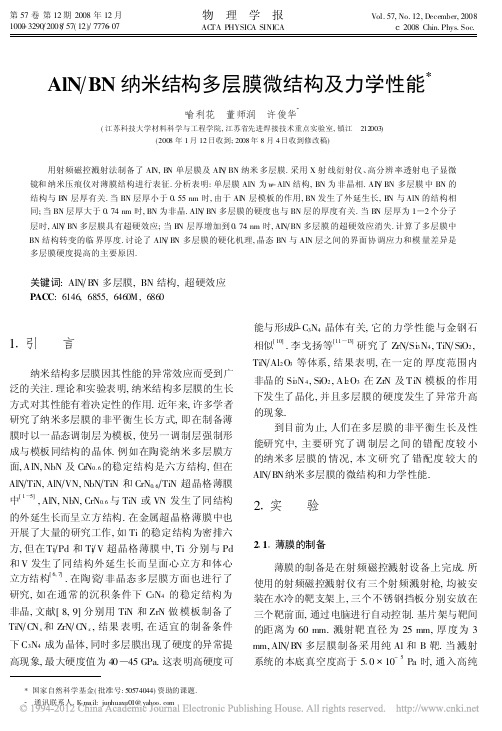
571 6
794 ) 900
271 0
790 ) 831
261 0
240
012504 013615 012553 013111
01 6660 )
01 4228 01 4979
对 AlN 和 BN 层 厚分 别 为 410 和 0132 nm 的 AlNPBN纳米结构多层膜的 HRTEM 分析表明, 多层 膜呈柱状晶, 图 2( a) 是经快速傅里叶变换( FFT ) 后 的形貌图. 从图 2( a) 可以看出, BN 以 AlN 为模板产 生了同结构 的共格外延 生长, 形成了纤 锌矿 w- BN 晶体结构, 此时的 BN 的晶 格常数与 AlN 的晶格常 数一样, 在其界面上没有形成位错. 薄膜的选区电子 衍射( SAED) 花样( 图 2( b) ) 是以电子束沿 Si[ 110] 晶 向拍摄的, 显示了一系列典型的纤锌矿结构, 具有很 强的( 0002) w-AlN M( 002) Si 结构的 AlN 布拉格反射. 多
图 2 AlN( 410 nm)PBN ( 01 32 nm) 多层膜显微形貌及电子衍 射花样 ( a) 截面 HRTEM 图像, ( b) SAED 花样
图 3 AlN 和 BN 的层厚分别为 51 45 和 01 55 nm 的 A lNPBN 多层膜的 HRTEM 图像
( 101) 和( 110) 环. 为了了解 AlN 层和 BN 层的界面情 况, 在高倍率下对该试样进行了观察( 图 5) , 表明部 分 BN 层转变为非晶, 部分 BN 层 尽管没有变成非 晶, 但在界面上晶格条纹发生了扭曲. 如在图 5 的区
到目前为止, 人们在多层膜的非平衡生长及性 能研究中, 主要研 究了调 制层 之间 的错配 度较 小 的纳米多 层膜的 情况, 本 文研 究了 错配度 较大 的 AlNPBN 纳米 多层 膜的 微结 构和 力学 性能 .
单片芯片背面金属化工艺研究

单片芯片背面金属化工艺研究发表时间:2020-08-05T07:16:56.664Z 来源:《中国科技人才》2020年第8期作者:姚吉豪[导读] 本文研究了单芯片的背面金属化技术,为小芯片的背面金属化提供了有效的途径。
深圳市创智成功科技有限公司摘要:本文研究了单芯片的背面金属化技术,为小芯片的背面金属化提供了有效的途径。
鉴于单个芯片的体积小和易碎的特性,设计了一种特殊的模具来夹紧芯片,并使用软掩膜来避免芯片侧面和正面的金属化污染。
通过实验和分析,确定了芯片背面的金属化膜系统(Ti Ni AU)的结构和厚度,并评估了样品的剪切力,热稳定性和焊接性能。
实验结果表明,该工艺制备的单芯片背面的金属化产品符合要求,性能稳定可靠。
关键词:单片芯片;背面金属化;软掩模;Ti—Ni—Au1引言晶圆背面金属化工艺(以下简称“背面金工艺”)是一种与其他物理和化学工艺相结合的综合技术。
降低功率器件的功率损耗,提高电子产品的功率利用率是一项重要技术。
它还为新产品(例如太阳能电池,微计算机处理(MEMS))奠定了基础。
目前,军事,航空,航天等领域的电路中的许多模块要求芯片和其他基本电子部件的背面具有可焊接性,以满足焊接和组装后的高可靠性要求。
晶圆背面金属化技术在中国已经相当成熟,但仍处于单芯片开发阶段。
鉴于上述情况,本文设计了一种特殊的模具来夹紧单芯片,并使用软掩模保护芯片的侧面和正面免受金属化污染。
单个芯片背面的金属化层是通过溅射制造的。
2背金工艺设计2.1掩模设计与制作与传统晶圆背衬相比,单芯片最大的困难在于如何固定单芯片以及如何确保芯片的侧面和正面不被金属化。
这就要求设计一个特殊的模具来固定单个芯片,并通过掩膜的方式来确保芯片的非背面区域不被金属化。
掩膜有两种方案,即软掩膜和硬掩膜。
由于单芯片尺寸小(小于5mm×5mm),难以保证硬掩模方案的对准精度,因此本文采用软掩模。
软掩膜的第一种方案:将模具设计为“凹形”,凹坑的大小根据单个芯片的大小而变化,从而使芯片和模具处于同一水平面,然后将芯片固定在凹坑中以进行光刻胶涂层。
【精品文章】一文了解陶瓷基板表面金属化技术

2μm 以内)、粘结相(粘结剂)和有机载体所组成。
厚膜导电浆料 SEM 图片(银 60-80%,玻璃料 5-25%,有机料 10-20%)
功能相金属粉末一般为 Au、Pt、Au/Pt、Au/Pd、Ag、Ag/Pt、Ag/Pd、
Cu、Ni、Al 及 W 等金属,其中 Ag、Ag/Pd 和 Cu 浆料居多。粘结剂一般
一文了解陶瓷基板表面金属化技术
随着微电子产品发展趋向于功能多样化、高性能化和产品小型化,特 别是 5G 通信技术发展要求通信设备(网络基站、大型滤波器)等有更高的 功率,因而陶瓷基板以其低热阻、耐高压、高散热、寿命长等优良特性, 在大功率 LED 产业、高频电子设备、大型网络基站、滤波器件等领域具有 非常广泛的应用前景。而陶瓷基板表面金属化是决定其实际应用的重要前 提。目前,陶瓷基板表面金属化方法主要有共烧法、厚膜法、直接敷铜 法、直接敷铝法及薄膜法等,下面小编做简要介绍。 一、共烧法 共烧多层陶瓷基板因利用厚膜技术将信号线、微细线等无源元件埋入基 板中能够满足集成电路的诸多要求,目前得到了广泛的关注。 共烧多层陶瓷基板 共烧法分为高温共烧和低温共烧。两者工艺流程基本相同,首先将陶瓷 粉体与有机粘接剂混合形成浆料,再利用刮刀把浆料加工成片状,经干燥 后形成陶瓷生坯,然后根据设计要求在生坯上加工导通孔并填充金属粉 末,利用丝网印刷技术在生坯表面涂布形成线路图形,最后将各层生坯层 叠后进行压合,在共烧炉内完成烧结并成型。具体如下: 共烧法工艺流程 高温共烧温度为 1300~1600 ℃,而低温烧结温度则为 850~900℃,造成 这种差别的主要原因在于低温烧结浆料中加入了可以降低烧结温度的玻璃 材料。 共烧法用于陶瓷基板表面金属化优点是:在增加组装密度、缩短互连长
CuAlO2 或 Cu
- 1、下载文档前请自行甄别文档内容的完整性,平台不提供额外的编辑、内容补充、找答案等附加服务。
- 2、"仅部分预览"的文档,不可在线预览部分如存在完整性等问题,可反馈申请退款(可完整预览的文档不适用该条件!)。
- 3、如文档侵犯您的权益,请联系客服反馈,我们会尽快为您处理(人工客服工作时间:9:00-18:30)。
AlN基片的薄膜金属化
高能武 陆吟泉 秦跃利 吴云海
摘要:讨论了AlN基片的薄膜金属化。通过试验,确定了有效的清洗方法及优化溅射参数。实验证明,TiW-Au
是AlN的优良金属化体系。AlN材料经激光划片后出现导电物质,经稀盐酸处理可去掉导电物质。
关键词:AlN基片; 薄膜; 金属化
中图分类号:TN451 文献标识码:B 文章编号:1001-2028(1999)05-0022-02
目前国内的AlN基材制备还处于研究阶段〔1,2〕。电子工业部第43研究所已对AlN基片薄膜混合集成电
路进行了初步研制,且能小批量生产AlN基片,但性能和国外产品尚有差距〔3〕。笔者采用的AlN金属化体系
已成功地用于大功率开关及功分器等微波器件中。
1 试验
采用NiCr-Au、TiW-Au金属化结构对日本京瓷公司的AlN基片进行了金属化,并采用钨碳钢针对金属层
进行破坏性定性划痕试验。分别用NaOH、CE-9清洗剂、纯水(16 MΩ*cm,25℃)、铬酸洗液等几种不同清
洗剂对AlN基片进行了清洁处理;射频溅射后作附着力试验;激光切割后用稀盐酸处理。
2 结果与讨论
2.1 金属化体系的选择
AlN是六方晶纤锌矿结构,密堆间隙中的Al离子半径小,价态高,具有较强的极化作用,使AlN清洁表
面的不饱和氮具有较高的化学活性。通常氮因电负性大,电离势高而有很强的共价倾向,即使与低电负性金属
反应,也会因负离子负电荷高,离子半径较大而水解。故在一般状态下,氮不易与金属反应。Ti、Ta、W等金
属因能与氮形成高晶格能化合物,使其在AlN表面的附着性能很好,退火处理后效果更佳。这是选择TiW-Au
作金属化导带的原因。TiW是一种亚稳态结构低生成自由能合金,作为阻挡层、附着层是有利的。Ti-Au、Ti-Al
及Ti-N的良好结合保证了体系的稳定及各界面间的附着。TiW与AlN的热特性参数(热膨胀系数、热导率)
吻合得非常好,对消除热应力有利。TiW只能作附着层和扩散阻挡层。若需集成电阻,可以采用TaN-TiW-Au
结构。文献〔3〕中提到采用NiCr-Au制作AlN基薄膜集成电路,笔者进行了对比试验。
(1)NiCr-Au导带 直流磁控溅射NiCr,射频溅射Au。由于AlN表面粗糙,钨碳钢针不能将膜从基片剥落。
光刻、电镀、裂片后,用钨碳钢针可从导带断面将NiCr-Au卷起。采用AuSn或AuGe共晶焊后,施加剪切力
可将AlN推动,显微观察发现NiCr-Au与基片分离。超声带焊(westbond 7400c焊机)时,可将NiCr-Au从底
层拔起。显微观察卷起后的NiCr-Au,有一定的侧腐蚀,这与后工序中稀盐酸处理激光划片后出现的导电相有
关。
(2)TiW-Au导带 射频磁控溅射TiW,射频溅射Au。溅射后,钨碳钢针附着力试验合格,划片后,也不能
从断面剥离。用稀盐酸处理激光切割后的导电相,对常温惰性TiW膜层无影响。电路制作后,若采用适当腐蚀
液将Au和TiW腐蚀,基片上留下明显的电路图形印迹,该印迹不与一般的化学溶液反应,可能和Ti与AlN
反应生成TiN有关。而在Al2O3基板上,未留下导带图形印迹。经共晶焊、带焊等,未发现TiW与AlN间有
附着不良的情况。
2.2 清洗方法的选择
用1 000倍显微镜观察,发现清洗剂、时间、温度等对AlN表面的影响很大。几种常用清洗剂对AlN表面
的影响如表1所示。
表1 几种常用清洗剂对AlN表面的影响
清洗剂 操作条件 观察结果
纯水 100℃下煮10 min AlN水解,表面变粗糙
常温冲洗 无明显变化
CE-9(1) 10%,100℃下煮10 min AlN水解,表面变粗糙
10%,常温超声清洗 无明显变化
NaOH
水溶液 煮10 min AlN水解很明显,
表面粗糙不平
铬酸洗液 120℃,10 min AlN水解,表面粗糙
90℃,30 min 无明显变化
常温浸泡24 h 无明显变化
注:(1)四川力奇化工有限公司产。
从表可见,在中性及碱性介质中,加热时,AlN易水解,水解反应可能为:
AlN+2H2O─→AlOOH+NH3
通过对以上几种常用于Al2O3的清洗剂的比较,总结出适合AlN的清洗方法:
(1)CE-9 稀释液超声清洗;(2)去离子水(5 MΩ*cm,≥25℃)漂洗;(3)氮气吹干;(4)铬酸洗液加热
浸泡或浸泡12 h以上;(5)去离子水(5 MΩ*cm,≥25℃)漂洗,检查基片浸润性;(6)丙酮(AR)超声清洗;(7)
乙醇(AR)超声清洗;(8)烘箱烘烤,120℃。
2.3 溅射参数的优化
TiW与Au之间的附着性能对溅射参数(气氛、靶基距等)很敏感。Ti是阀金属,易于吸附H2O、O2、N2
等气体而生成稳定的化合物或固溶体。界面处的化合物或固溶体严重削弱了Au和TiW间金属键的形成。吸附
的气体不能扩散、渗透至膜内层,在以后的高温处理过程中,将出现放气或钝化阻挡层表层,使得Au层极易
剥落。因此,溅射前适当提高背景真空是有利的,通常采用10-4Pa。靶基距是影响TiW与Au间附着力的另
一溅射参数。通过不同靶基距对比试验发现,靶基距越大,附着强度越低。采用ALCATEL SCM450溅射台时,
靶基距以50 cm为宜。研究TiW与Au间附着力时发现,400℃下退火处理,可明显提高两者之间的附着,因部
分缺陷及应力的消除,溅射Au的柔韧性也有改善。
2.4 激光划片后的处理
激光切割是分裂薄膜阵列电路的重要手段。在相同YAG激光功率(30 W)条件下,分别对Al2O3和AlN
进行了激光划片。显微观察,划痕处Al2O3出现明显的熔融痕迹,而AlN则几乎没有。这和AlN导热快,高
温升华有关(Al2O3 的熔点为2 020℃,AlN 2 000℃开始蒸发,2 400℃升华)。划痕两边出现粉末堆积,其中
AlN上粉末具有良好的导电性,这是某些微波混合集成电路中所不允许的。采用稀盐酸处理,粉末处有大量小
气泡冒出。在超声状态下用稀盐酸处理,则更快更好。对重复使用的稀盐酸溶液,pH值应高于6,加热至70℃
左右,滴入铝试剂,有玫瑰色沉淀。通过以上现象,可推断出该导电物质为AlN升华分解后沉降下的Al。TiW
与稀盐酸在常温下几乎不反应,可用稀盐酸处理该导电相〔4〕。
3 结论
(1)AlN在pH值较高时不稳定,应在低pH值条件下进行清洗;(2)TiW-Au系复合导带与基材的附着性
能优良,实现了AlN的金属化,优选条件下制作的金属化层具有极好的粘着性;(3)激光切割后出现导电物质,
稀盐酸处理导电物质简便易行。
作者简介:高能武(1969-),男,四川郫县人,西南电子设备研究所工程师,硕士,主要从事电子材料、功能
材料、微波混合集成电路工艺等方面的研究。
作者单位:西南电子设备研究所,四川 成都 610036