固定床、移动床、流化床
第九章 固定床反应器
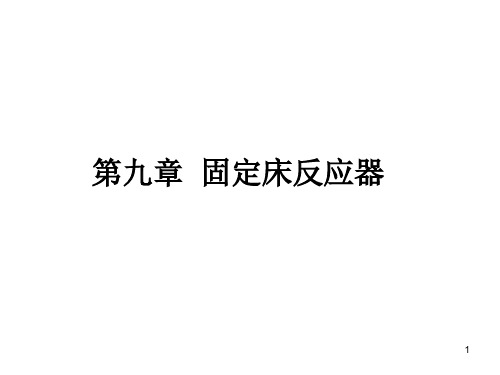
在非球颗粒充填的床层中,同一截面上的ε值, 除壁效应影响所及的范围外,都是均匀的。 但球形或圆柱形颗粒充填的床层,在同一横截面 上的 ε 值,除壁效应影响所及的范围外,还在一 平均值上下波动。 由于壁效应的影响,床层直径与颗粒直径之比越 大,床层空隙率的分布越均匀。 通常所说的床层空隙率指的是平均空隙率。
• 9.3固定床反应器内的传质与传热
• 9.4 固定床反应器的计算方法
5
9.1固定床反应器的特点及结构
• 定义*:凡是流体通过不动的固体物料所 形成的床层而进行反应的装臵都称作固定
床反应器。
• 其中尤以用气态的反应物料通过由固体催
化剂所构成的床层进行反应的气-固相催
化反应器占最主要的地位。
6
9.1.1固定床反应器的特点及工业应用
• 自热式反应器示意图
21
• 优、缺点:
• 逆流:优点是原料气进入床层后能较快地升温而接 近最佳温度,缺点是反应后期易于过冷。
• 无论逆流还是并流,反应前期放热速率都最大。 • 有些并流式催化反应器中设臵一绝热床,经预热后 的原料气先进入绝热床中反应,使反应气体迅速升 温,然后再进入与原料气进行换热的催化剂管中反 应,这样做既保留并流式后期降温速度慢的优点, 又克服了原料气进入床层后升温速度慢的缺点。
32
图9-6消除初始动能的方法示意图
33
图9-7附加导流装臵示意图
34
9.2.3固定床反应器的床层压力降
• 流过床层的流体,其径向流速分布是不均匀的。
• 径向流速分布:从床层中心处算起,随着径向位臵的增大, 流速增加,在离器壁的距离等于1~2倍颗粒直径处,流速最 大,然后随径向位臵的增大而降低,至壁面处为零。床层直 径与颗粒直径之比越小,径向流速分布越不均匀。
煤化工煤制气工艺方法及问题探讨

煤化工煤制气工艺方法及问题探讨发布时间:2021-04-30T07:48:41.049Z 来源:《福光技术》2021年1期作者:魏东平刘飞飞[导读] 则是以气化为龙头,以碳化学为基础,煤气化就是制备合成气的必要手段。
陕西长青能源化工有限责任公司陕西宝鸡 721400摘要:煤制气工艺是指利用原料煤经过气化反应生成合成气的工艺过程。
通过对我国煤炭资源进行了简述分析及现有的煤制气工艺现实背景,理论背景,煤制气分类介绍,全面的分析比较不难看出,煤气化技术在朝着洁净无污染或者污染少的复合型,清洁能源型,可再生能源型的方向发展。
关键词:煤制气;加压气化;气化工艺1.现实背景据世界能源组织估计,我国煤炭可采储量占探明储量的比例约为19%,即约为 1900 亿吨可采储量。
随着勘探工作的发展,还在逐年增加,按人均年消费煤炭 1.45t,即全国年产 20 亿吨煤炭估算,可以保证开采上百年。
较其他国家而言,我国是一个贫油、少气、煤炭资源相对而言比较丰富的国家,这就决定了煤炭在一次能源中的重要地位。
而发展现代煤化工产业,则是以气化为龙头,以碳化学为基础,煤气化就是制备合成气的必要手段。
煤炭气化是指煤或煤焦有在特定的设备内,在一定温度、压力条件下利用气化剂(蒸汽,空气或氧气)反应生成洁净合成气 (CO、H2的混合物即俗称水煤气 ) 的工艺方法,是对煤炭进行化学加工的一个重要方法,是实现煤炭洁净利用的关键。
煤炭气化技术,应用生产以来了为社会带来了良好的经济和社会效益,代表着发展趋势,是现阶段最清洁的煤利用技术,是洁净煤技术的关键。
2.研究目的和意义煤气化工艺技术很多,使选择煤气化工艺技术无从着手。
不过我们都知道煤气化工艺的好坏不仅与气化技术本身有关同时也与气化所用煤种有关,现今在世界上没有哪一种气化炉是万能气化炉,各种气化工艺技术都有其特点和优缺点,随着经济的发展以及人民生活水平的需要,面对我国富煤贫油少气的能源结构,我国掀起了一股煤制甲醇、煤制油、煤制焦油,煤制 LNG, 煤制天然气、煤制烯烃的浪潮。
固定床反应器结构及原理
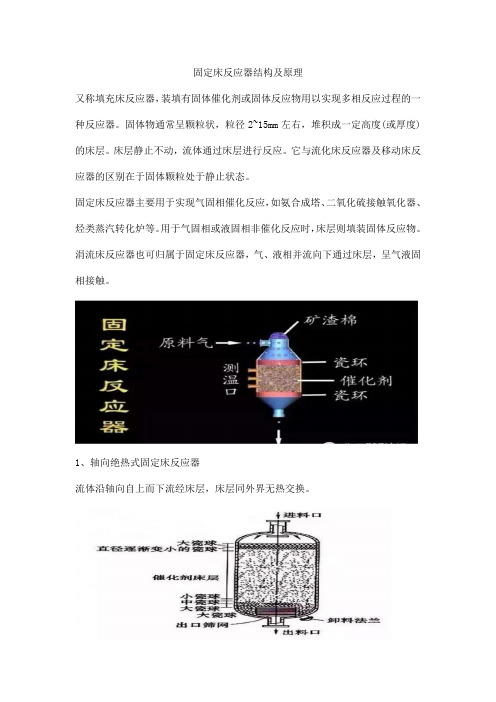
固定床反应器结构及原理又称填充床反应器,装填有固体催化剂或固体反应物用以实现多相反应过程的一种反应器。
固体物通常呈颗粒状,粒径2~15mm左右,堆积成一定高度(或厚度)的床层。
床层静止不动,流体通过床层进行反应。
它与流化床反应器及移动床反应器的区别在于固体颗粒处于静止状态。
固定床反应器主要用于实现气固相催化反应,如氨合成塔、二氧化硫接触氧化器、烃类蒸汽转化炉等。
用于气固相或液固相非催化反应时,床层则填装固体反应物。
涓流床反应器也可归属于固定床反应器,气、液相并流向下通过床层,呈气液固相接触。
1、轴向绝热式固定床反应器流体沿轴向自上而下流经床层,床层同外界无热交换。
下图是绝热式固定床反应器的示意图。
它的结构简单,催化剂均匀堆置于床内,床内没有换热装置,预热到一定温度的反应物料流过床层进行反应就可以了。
(1)径向绝热式固定床反应器流体沿径向流过床层,可采用离心流动或向心流动,床层同外界无热交换。
径向反应器与轴向反应器相比,流体流动的距离较短,流道截面积较大,流体的压力降较小。
但径向反应器的结构较轴向反应器复杂。
以上两种形式都属绝热反应器,适用于反应热效应不大,或反应系统能承受绝热条件下由反应热效应引起的温度变化的场合。
由多根反应管并联构成。
管内或管间置催化剂,载热体流经管间或管内进行加热或冷却,管径通常在25~50mm之间,管数可多达上万根。
列管式固定床反应器适用于反应热效应较大的反应。
此外,尚有由上述基本形式串联组合而成的反应器,称为多级固定床反应器。
例如:当反应热效应大或需分段控制温度时,可将多个绝热反应器串联成多级绝热式固定床反应器,反应器之间设换热器或补充物料以调节温度,以便在接近于最佳温度条件下操作。
(3)对外换热式固定床反应器对外换热式反应器以列管式为多。
通常是在管内放催化剂,管间走热载体(在用高压水或用高压蒸汽作热载体时,则把催化剂放在管间,而使管内走高压流体)。
(4)多段绝热式固定床反应器3、自身换热式反应器(自热式反应器)反应前后的物料在床层中自己进行换热称作自热式反应器。
固定床反应器的优缺点

固定床反应器的优缺点
固定床反应器的优缺点 优点 (1)流体的流动皆可看成是理想置换流动,因此化学反应速率较 快,在完成同样生产能力时,所需要的催化剂用量和反应器体积较小。 (2)气体停留时间可以严格控制,温度分布可以调节,因而有利于 提高化学反应的转化率和选择性。 (3)催化剂不易磨损,可以较长时间连续使用。 (4)适宜于在高温高压条件下操作。 缺点
(1)导热性差,温度分布复杂。 (2)不能使用细粒催化剂,催化剂的活性内表面得不到充分利用。 (3)催化剂的再生、更换均不方便。 列管式固定床反应器优缺点 优点: 1、返混小,流体同催化剂可进行有效接触,当反应伴有串联副反应 时可得较高选择性。 2、催化剂机械损耗小。 3、结构简单。
固体流化床特性曲线的测定
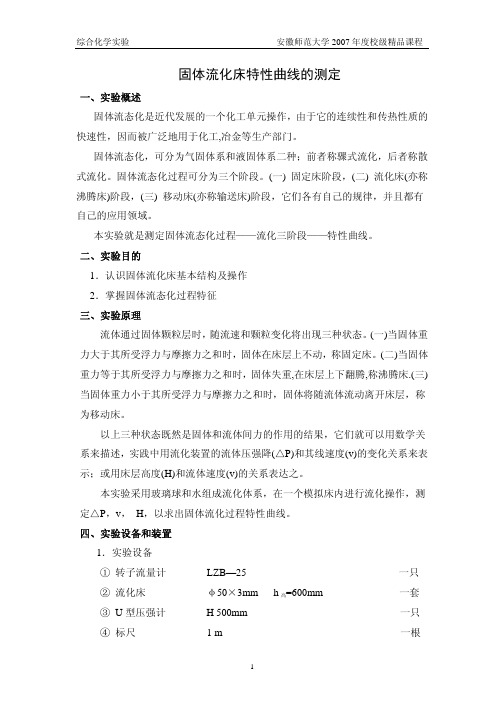
固体流化床特性曲线的测定一、实验概述固体流态化是近代发展的一个化工单元操作,由于它的连续性和传热性质的快速性,因而被广泛地用于化工,冶金等生产部门。
固体流态化,可分为气固体系和液固体系二种;前者称骤式流化,后者称散式流化。
固体流态化过程可分为三个阶段。
(一) 固定床阶段,(二) 流化床(亦称沸腾床)阶段,(三) 移动床(亦称输送床)阶段,它们各有自己的规律,并且都有自己的应用领域。
本实验就是测定固体流态化过程——流化三阶段——特性曲线。
二、实验目的1.认识固体流化床基本结构及操作2.掌握固体流态化过程特征三、实验原理流体通过固体颗粒层时,随流速和颗粒变化将出现三种状态。
(一)当固体重力大于其所受浮力与摩擦力之和时,固体在床层上不动,称固定床。
(二)当固体重力等于其所受浮力与摩擦力之和时,固体失重,在床层上下翻腾,称沸腾床.(三) 当固体重力小于其所受浮力与摩擦力之和时,固体将随流体流动离开床层,称为移动床。
以上三种状态既然是固体和流体间力的作用的结果,它们就可以用数学关系来描述,实践中用流化装置的流体压强降(△P)和其线速度(v)的变化关系来表示;或用床层高度(H)和流体速度(v)的关系表达之。
本实验采用玻璃球和水组成流化体系,在一个模拟床内进行流化操作,测定△P,v,H,以求出固体流化过程特性曲线。
四、实验设备和装置1.实验设备①转子流量计LZB—25 一只=600mm 一套②流化床φ50×3mm h高③U型压强计H 500mm 一只④标尺 1 m 一根2.实验装置固体流态化特性曲线测定装置如教材212页图4.4-1所示,将流化床下端入口与水龙头通过导管连接起来,中间串接一个转子流量计,流化床两端支管分别与U 型压强计相接在一起。
流化床另一侧垂直竖立一个标尺以测床层高度。
五、实验步骤1.检查装置管线是否正确,有无漏气。
2.打开水龙头,用出水阀调节流量,进行设备充水排气。
3.校正U 型压强计零点,并记下零点误差。
催化裂化
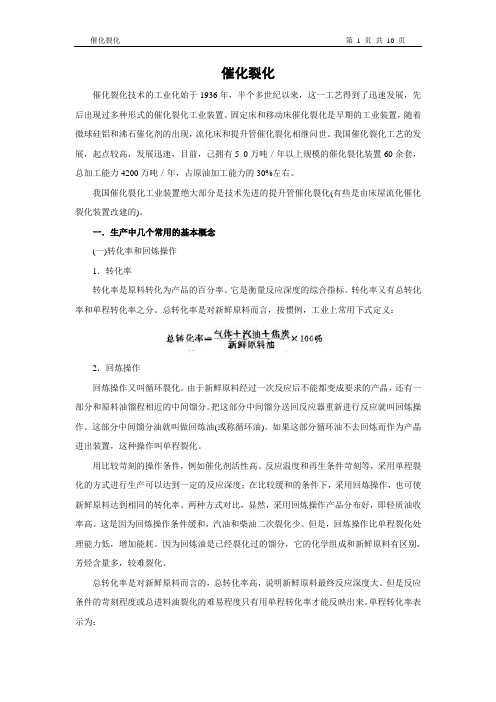
催化裂化催化裂化技术的工业化始于1936年,半个多世纪以来,这一工艺得到了迅速发展,先后出现过多种形式的催化裂化工业装置。
固定床和移动床催化裂化是早期的工业装置,随着微球硅铝和沸石催化剂的出现,流化床和提升管催化裂化相继问世。
我国催化裂化工艺的发展,起点较高,发展迅速,目前,己拥有5 0万吨/年以上规模的催化裂化装置60余套,总加工能力4200万吨/年,占原油加工能力的30%左右。
我国催化裂化工业装置绝大部分是技术先进的提升管催化裂化(有些是由床屋流化催化裂化装置改建的)。
一.生产中几个常用的基本概念(一)转化率和回炼操作1.转化率转化率是原料转化为产品的百分率。
它是衡量反应深度的综合指标。
转化率又有总转化率和单程转化率之分。
总转化率是对新鲜原料而言,按惯例,工业上常用下式定义:2.回炼操作回炼操作又叫循环裂化。
由于新鲜原料经过一次反应后不能都变成要求的产晶,还有一部分和原料油馏程相近的中间馏分。
把这部分中间馏分送回反应器重新进行反应就叫回炼操作。
这部分中间馏分油就叫做回炼油(或称循环油)。
如果这部分循环油不去回炼而作为产晶进出装置,这种操作叫单程裂化。
用比较苛刻的操作条件,例如催化剂活性高、反应温度和再生条件苛刻等,采用单程裂化的方式进行生产可以达到一定的反应深度;在比较缓和的条件下,采用回炼操作,也可使新鲜原料达到相同的转化率。
两种方式对比,显然,采用回炼操作产品分布好,即轻质油收率高。
这是因为回炼操作条件缓和,汽油和柴油二次裂化少。
但是,回炼操作比单程裂化处理能力低,增加能耗。
因为回炼油是已经裂化过的馏分,它的化学组成和新鲜原料有区别,芳烃含量多,较难裂化。
总转化率是对新鲜原料而言的,总转化率高,说明新鲜原料最终反应深度大。
但是反应条件的苛刻程度或总进料油裂化的难易程度只有用单程转化率才能反映出来。
单程转化率表示为:式中回炼比是回炼油(包括回炼油浆)与新鲜原料重量之比,即:(二)空速和反应时间回炼比的大小由原料性质和生产方案决定,通常,多产汽油方案采用小回炼比,多产柴油方案用大回炼比。
固体流态化的流动特性实验

固体流态化的流动特性实验一、实验目的1.通过实验观察固定床向流化床转变的过程,及聚式流化床和散式流化床流动特性的差异。
2.测定流化曲线和临界流化速度。
3.验证固定床压降和流化床临界流化速度的计算公式。
4.初步掌握流化床流动特性的实验研究方法,加深对流体经固体颗粒层的流动规律和固体流态化原理的理解。
二、实验原理在化学工业中,经常有流体流经固体颗粒的操作,诸如过滤、吸附、浸取、离子交换以及气固、液固和气液固反应等。
凡涉及这类流固系统的操作,按其中固体颗粒的运动状态,一般将设备分为固定床、移动床和流化床三大类,近年来,流化床设备得到越来越广泛的应用。
固体流态化过程按其特性可分为密相流化和稀相流化。
密相流化床又分为散式流化床和聚式流化床。
一般情况下,气固系统的密相流化床属于聚式流化床,而液固系统密相流化床属于散式流化床。
当流体流经固定床内固体颗粒之间的空隙时,随着流速的增大,流体与固体颗粒之间所产生的阻力也随之增大,床层的压强降则不断升高。
为表达流体流经固定床时的压强降与流速的函数关系,曾提出过多种经验公式。
一种较为常用的公式可以仿照流体流经空管时的压降公式(Moody 公式)列出。
即:22u d H p p m m ρλ⋅⋅=∆(4-1)式中H m ——固定床层的高度,m ;d p ——固体颗粒的直径,m ; u 0——流体的空管速度,m /s ; ρ——流体的密度,kg/m 3; λm ——固定床的摩擦系数。
由固定床向流化床转变时的临界速度u mf ,也可由实验直接测定。
实验测定不同流速下的床层压降,再将实验数据标绘在双对数坐标上,由作图法即可求得临界流化速度,如图4-1所示。
为计算临界流化速度,我们可采用下面这种半理论半经验的公式mms pmf d u εεμρρ-⨯-⨯=1)(15032(4-2) 式中μ——流体的黏度,Pa /s ;d p 一一平均粒径,m ; ρs ——填料密度,kg/m 3; εm ——空隙率。
固定床反应器
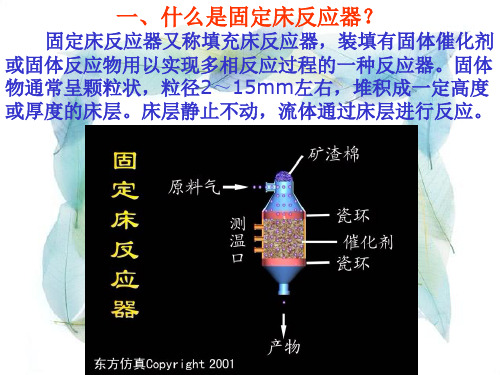
四,固定床反应器的结构? 固定床反应器的结构?
1.绝热式固定床反应器 绝热式固定床反应器 1.1单段绝热式 单段绝热式
催化剂 冷却器 1-矿渣棉 瓷环 催化剂 1-催化剂 2-冷却器 矿渣棉2-瓷环 矿渣棉 瓷环3-催化剂
1.2多段绝热床 多段绝热床
(a),(b),(c)中间换热式 中间换热式;(d),(e)冷激式 中间换热式 冷激式
2,换热式固定床反应器 换热式固定床反应器 2.1,对外换热式固定床反应器 对外换热式固定床反应器
列管式固定床反应器
以加压热水作载热体的固定床反应装置 1-列管上花板;2-反应列管;3-膨胀圈; 4-汽水分离器;5-加压热水泵
以道生油作载热体的固定床反应装置 1-列管上花板 列管上花板;2,3-折流板 折流板;4-反应列管 反应列管; 列管上花板 折流板 反应列管 5-折流板固定棒 折流板固定棒;6-人孔 人孔;7-列管下花板 列管下花板; 折流板固定棒 人孔 列管下花板 8-载热体冷却器 载热体冷却器
三,固定床反应器的分类及其应用? 多段绝热式 二段 反应 三段 特征 四段 段间反应 原料气冷激式 气冷却或 加热方式 冷激式 非原料气冷激式 加压热水(< 加压热水(<240℃) (< 换 热 式 对外换热式 导热油(250~300 ℃) 导热油( 熔盐(> 熔盐(>300 ℃) (> 自热式 轴向流动固定床反应器 径向流动固定床反应器 中间间接换热式
二,固定床反应器的特点? 固定床反应器的特点?
1.固定床反应器的优点是:①返混小,流体同催化剂可进 固定床反应器的优点是: 返混小, 固定床反应器的优点是 行有效接触,当反应伴有串联副反应时可得较高选择性. 行有效接触,当反应伴有串联副反应时可得较高选择性. 催化剂机械损耗小. 结构简单. ②催化剂机械损耗小.③结构简单. 2.固定床反应器的缺点是:①传热差,反应放热量很大时, 固定床反应器的缺点是: 传热差,反应放热量很大时, 固定床反应器的缺点是 即使是列管式反应器也可能出现飞温(反应温度失去控制, 即使是列管式反应器也可能出现飞温(反应温度失去控制, 急剧上升,超过允许范围). ).② 急剧上升,超过允许范围).②操作过程中催化剂不能更 催化剂需要频繁再生的反应一般不宜使用, 换,催化剂需要频繁再生的反应一般不宜使用,常代之以 流化床反应器或移动床反应器. 流化床反应器或移动床反应器.
- 1、下载文档前请自行甄别文档内容的完整性,平台不提供额外的编辑、内容补充、找答案等附加服务。
- 2、"仅部分预览"的文档,不可在线预览部分如存在完整性等问题,可反馈申请退款(可完整预览的文档不适用该条件!)。
- 3、如文档侵犯您的权益,请联系客服反馈,我们会尽快为您处理(人工客服工作时间:9:00-18:30)。
固定床:当气体以较小的速度流过固定床时,流动气体的上升阻力不致使颗粒的运动
状态发生变化,床高维持不变;床层压降随流速对数增大而增大。
流化床:固体颗粒可以像水等液体一样在设备内有明显的界面,即使设备倾斜,界面
仍会保持水平;床层压降不随流速变化(基本不变)。
输送床:固体颗粒在设备内无明显界面;床层压力随流速增大而减小。
流化床和沸腾床可能只是叫法上不同。
流化床,也就是沸腾床,接触面大,传热传质效率高,时空产率高,但返混严重。
需要注意的是不能堵塞气体分布器,堵了很麻烦的。
固定床和移动床比较适合气-气、气-液和液-液反应,床层本身作为[wiki]催化剂[/wiki],优点是返混小,固相带出少,分离简单。
流化床的床型是设计中很重要的,与反应体系的匹配要求比较高。
此外,操作中的气速、带出量、与配套的旋风等分离设备设计比较严格。
流化床的传热和破汽泡、沟流措施也是研究比较多的。
固定床反应器是一种被广泛采用的多相催化反应器,反应器内填充有固定不动的固体颗粒,可以是固体催化剂也可以是固体反应物.例如管式固定床反应器,管内装催化剂,管内装催化剂,反应物料自上而下通过床层,管间为载热体与管内反应物进行换热,以维持所
需的温度条件.此外,固定床反应器也可用于气固及液固非催化反应.
沸腾床是流化床的一种,固体在流化床反应器内流动,流体和固体颗粒所构成的床层犹如沸腾的液体. 沸腾床反应器下部设有分布板,板上放固体颗粒,流体自分布板下送入,当流体速度达到一定数值后,固体颗粒开始松动,再增大流速就进入流化状态.反应器内
一般设有挡板,换热器,及流体与固体分离装置等内部部件.
移动床与固定床相似,不同的是固体颗粒自顶部连续加入,由底部卸出.
沸腾床因为固体处于运动状态,反应或传热效果好,但动力消耗大,而且在煤调湿中
粉尘携带量大.
固定床:
固定床反应器又称填充床反应器,装填有固体催化剂或固体反应物用以实现多相反应过程的一种反应器。
固体物通常呈颗粒状,粒径2~15mm左右,堆积成一定高度(或厚度)的床层。
床层静止不动,流体通过
床层进行反应。
它与流化床反应器及移动床反应器的区别在于固体颗粒处于静止状态。
固定床反应器主要
用于实现气固相催化反应,如氨合成塔、二氧化硫接触氧化器、烃类蒸汽转化炉等。
用于气固相或液固相
非催化反应时,床层则填装固体反应物。
涓流床反应器也可归属于固定床反应器,气、液相并流向下通过
床层,呈气液固相接触。
1、分类
固定床反应器有三种基本形式:①轴向绝热式固定床反应器。
流体沿轴向自上而下流经床层,床层同
外界无热交换。
②径向绝热式固定床反应器。
流体沿径向流过床层,可采用离心流动或向心流动,床层同
外界无热交换。
径向反应器与轴向反应器相比,流体流动的距离较短,流道截面积较大,流体的压力降较小。
但径向反应器的结构较轴向反应器复杂。
以上两种形式都属绝热反应器,适用于反应热效应不大,或反应系
统能承受绝热条件下由反应热效应引起的温度变化的场合。
③列管式固定床反应器。
由多根反应管并联构成。
管内或管间置催化剂,载热体流经管间或管内进行加热或冷却,管径通常在25~50mm之间,管数可
多达上万根。
列管式固定床反应器适用于反应热效应较大的反应。
此外,尚有由上述基本形式串联组合而
成的反应器,称为多级固定床反应器。
例如:当反应热效应大或需分段控制温度时,可将多个绝热反应器
串联成多级绝热式固定床反应器,反应器之间设换热器或补充物料以调节温度,以便在接近于最佳温度条
件下操作。
2、特点
固定床反应器的优点是:①返混小,流体同催化剂可进行有效接触,当反应伴有串联副反应时可得较高
选择性。
②催化剂机械损耗小。
③结构简单。
固定床反应器的缺点是:①传热差,反应放热量很大时,即
使是列管式反应器也可能出现飞温(反应温度失去控制,急剧上升,超过允许范围)。
②操作过程中催化
剂不能更换,催化剂需要频繁再生的反应一般不宜使用,常代之以流化床反应器或移动床反应器。
固定床反应器中的催化剂不限于颗粒状,网状催化剂早已应用于工业上。
目前,蜂窝状、纤维状催化
剂也已被广泛使用。
数学模型固定床反应器是研究得比较充分的一种多相反应器,描述固定床反应器的数学模型有多种,大致分为拟均相模型(不考虑流体和固体间的浓度、温度差别)和多相模型(考虑到流体和固体间的浓度、温度差别)两类,每一类又可按是否计及返混,分为无返混模型和有返混模型,按是否考虑反应器径向的
浓度梯度和温度梯度分为一维模型和二维模型。
固定床反应器是一种被广泛采用的多相催化反应器,反应器内填充有固定不动的固体颗粒,可以是固体催
化剂也可以是固体反应物.例如管式固定床反应器,管内装催化剂,管内装催化剂,反应物料自上而下通过床层,管间为载热体与管内反应物进行换热,以维持所需的温度条件.此外,固定床反应器也可用于气固及液固非催
化反应。
当气体以较小的速度流过固定床时,流动气体的上升阻力不致使颗粒的运动状态发生变化,床高
维持不变;床层压降随流速对数增大而增大。
流化床:
流化床:流体向上流过一个微细颗粒的床层(塔体),当流速低的时候流体只是穿过静止的颗粒之间的
空隙,此时的床体称为固定床;随着流速的增加,颗粒互相离开,并可看到少量的颗粒在一定的区间进行
震动和游动,称为膨胀床;速度再升高达到使全部颗粒都刚好悬浮在向上流动的气体或者液体中,此时的
床层就是流化床起点。
固体颗粒可以像水等液体一样在设备内有明显的界面,即使设备倾斜,界面仍会
保持水平;床层压降不随流速变化(基本不变)。
简单的说固体颗粒在流体作用下表现出类似流体状态的
现象称为流态化。
流化床是流态化发生的设备。
流化床反应器中催化剂处于沸腾流化状态,被反应介质
与提升介质带动快速通过反应器,如FCC的提升管反应器。
输送床:固体颗粒在设备内无明显界面;床层压力随流速增大而减小。
沸腾床是流化床的一种,固体在流化床反应器内流动,流体和固体颗粒所构成的床层犹如沸腾的液体. 沸腾床反应器下部设有分布板,板上放固体颗粒,流体自分布板下送入,当流体速度达到一定数值后,固体颗粒开始松动,再增大流速就进入流化状态.反应器内一般设有挡板,换热器,及流体与固体分离装置等内部部件. 沸腾床接触面大,传热传质效率高,时空产率高,但返混严重。
沸腾床因为固体处于运动状态,反应或传热效果好,但动力消耗大,而且在煤调湿中粉尘携带量大。
移动床:
移动床与固定床相似,不同的是固体颗粒自顶部连续加入,由底部卸出. 移动床(moving bed)离子交换树脂在交换器、再生器和清洗塔之间,周期性流动的离子交换装置。
移动床与固定固定床的差别在于反应过程中催化剂从反应器入口向出口缓慢运动,新鲜催化剂(或再生好的催化剂)从反应器入口进入,失活的催化剂从反应器出口移出,进行再生。
催化剂运动速度较慢,没有达到流化状态。
如UOP与IFP连续重整工艺中的移动床反应器。
区别:
固定床可以处理高灰分,高灰熔点的煤,投资小,环保差……气流床产量最大,但对煤种有一定要求;硫化床现在压力加不上去,推广受限。
这三种床最关键的就是设计床体,现在在国内设计床体大多数是一种经验估算和模拟实验,扩大到工业生产上往往存在很多缺点。
它们的主要区别还得看用途,物料的性质,既是物理过程还是化学反应过程。
固定床和移动床比较适合气-气、气-液和液-液反应,床层本身作为催化剂,优点是返混小,固相带出少,分离简单。
流化床的床型是设计中很重要的,与反应体系的匹配要求比较高。
此外,操作中的气速、带出量、与配套的旋风等分离设备设计比较严格。
流化床的传热和破汽泡、沟流措施也是研究比较多的。
流化床需要注意的是不能堵塞气体分布器,堵了很麻烦的。
固定床、移动床和沸腾床的区分是依据向床层内通气量的大小而定的,随着通气量的增加,一次是固定床、鼓泡床(沸腾床),湍动床,输送床。
移动床严格意义上属于流化床的范畴,是颗粒整理向下移动,床层高度不变,例如炼油中的催化重整工艺,是典型的移动床工艺。
至于应用范围和优缺点,相对而言流化床技术具有良好的传质、传热和各项均匀性,生产规模大,应用的最广泛,例如基于循环流化床开发的各种煤气化、燃烧工艺等等。
固定床和移动床受传质传热的限制,规模小,但是装置投资小,例如鲁奇的碎煤气化技术,就是典型的固定床,通常需要几台炉子一起交替生产,实现整个过程的连续。