SiC增强铝基复合材料
_TiB_2_SiC_ZL109复合材料的制备及其力学性能

Vol 53 No 2 铸造Feb. 2004 FOUNDRY ∀97 ∀( TiB2+ SiC)/ ZL109 复合材料的制备及其力学性能赵德刚, 刘相法, 边秀房( 山东大学材料液态结构及其遗传性教育部重点实验室, 山东济南250061)摘要:采用搅拌铸造和原位反应合成相结合的方法制备出( T iB2+ SiC) / ZL 109 复合材料。
对该复合材料的显微组织观测表明, SiC 颗粒与T iB2颗粒分布较均匀。
通过对材料的室温拉伸性能及硬度测试, 发现T iB2、SiC 两相颗粒增强Al-Si 基复合材料的硬度明显比单一颗粒增强复合材料提高, 而其拉伸强度也略有提高, 弥补了单一SiC 颗粒增强铝基复合材料U T S 降低的不足。
( T iB2+ SiC) / ZL 109 复合材料较基体合金ZL109 硬度提高了34 8% 。
关键词: 复合材料; 铝合金; TiB2粒子; SiC 粒子; 协同增强中图分类号: T B331 文献标识码: A 文章编号: 1001 4977 ( 2004) 02 0097 04Fabrication and Mechanical Properties of (TiB2+ SiC)/ ZL109CompositesZHAO De gang, LIU Xiang fa, BIAN Xiu fang( The Key Laboratory of Materials Liquid Structure and Heredity, Ministry of Education, ShandongUniversity, Jinan 250061, Shandong, China)Abstract: Fabrication technology of ( TiB2+ SiC) / ZL109 composites by stirring casting and in situ methodwas studied in this paper. The microanalysis of the composites revealed that TiB2 and SiC particles arewell distributed in the matrix. From the results of hardness tests and tensile experiments at room temperature, it is found that the hardness of the composites reinforced cooperatively by TiB2 and SiC, is obviouslyhigher than that of the ZL109 matrix, and the tensile strength of the composites is slightly higher than thematrix. The composites cover the shortage that UTS of composites reinforced by SiC particle declinessharply. It can be shown that the hardness of the ( TiB2+ SiC) / ZL109 was raised by 34 8% than that ofmatrix.Keywords: composites; aluminium alloy; TiC particle; TiB2 particle; cooperative reinforcement金属基复合材料( M MCs) 综合了金属基体的高延性、高韧性和增强相高强度、高模量的优点, 具有高比强度、高比刚度和热稳定性好等优良特性。
电磁离心铸造B4C和SiC增强铝基复合材料的研究

Ma er l y Elc r m a e i n r u a s ig t i e to ab gn t Ce ti g l c f Ca t n
W ANG o c e 1ZHANG e— in , I n Ba . h n。 W i a 1 L U Da q
( o, io igT c nc l nv ri , u i 1 3 0 La nn , 1 Maei i c n n ie r c o lLa nn e h ia U i s y F xn 0 , i ig aS e n e t 2 o Chn ; . h n a gR s ac si t f o n r S e y n 0 2 , i nn , hn ) ia 2S e y n e e rhI tueo u dy, h n a g 1 0 1 La ig C ia n t F 1 o
m a eraI t i
金属 基 复合材 料 的研究 始于 2 世 纪6 年代 ,由于 0 0 金属 基 复合 材料 能 充分 发 挥 各组 分 材料 的协 同作 用 , 通 过合 成使 材料 的强度 、刚度 、硬度 、耐 蚀性 、耐 磨 性 、耐 高温 、导 电导热 性 、尺寸 稳定性 、抗 老化 性 等 性 能 得 到不 同程 度 的改 善 ,可广 泛应 用 于航 空航 天 、
Si p rce itiu eo t iewi e in ot g ; e h xt g v l g n a c dt 0V. h C a ilsds r t u sd t 0V xt gv l e wh n t ee in ot e e h n e 5 t e t b h i a i a o
反应烧结SiC三维刚性骨架增强金属基复合材料
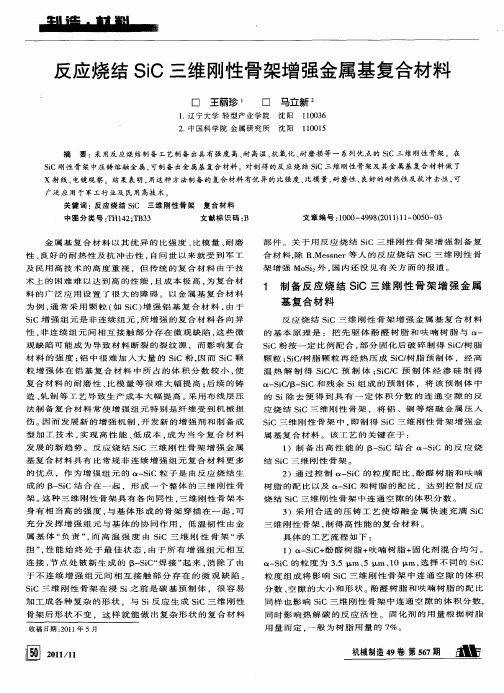
解碳 。
图 2是 浸 S 反 应 后 得 到 的 B SC 结 合 一 i 一 i —i SC( s c D— i 和 2 % 左 右 的 S i/ SC 0 i的 烧 结 体 的 X 射 线 衍 射 图 , 射 线 衍 射 图 反 映 出 B— i 结 合 仪一 i 和 2 % 左 x SC SC O 右 的 S 的 烧 结 体 由 原 来 加 入 的 仅一 i 和 浸 S 反 应 后 i SC i
观 缺 陷 可 能 成 为 导 致 材 料 断 裂 的 裂 纹 源 ,而 影 响 复 合 材 料 的 强 度 ; 中 很 难 加 入 大 量 的 SC 粉 。 而 SC 颗 铝 i 因 i 粒 增 强体 在 铝 基复 合 材料 中所 占的体 积分 数 较 小 , 使 复合 材料 的耐 磨性 、 模量 等很 难 大幅提 高 ; 续 的铸 比 后 造 、 制 等 _ 艺 导 致 生 产 成 本 大 幅 提 高 。采 用 布 线 层 压 轧 - I 2 法 制 备 复 合 材 料 常 使 增 强 组 元 特 别 是 纤 维 受 到 机 械 损
的 处 理 工 艺 中不 再 变 形 。
生 成 的 B SC 及 残 余 S 构 成 , 来 加 入 的 一 i 颗 粒 —i i 原 SC
表 面 全 部 由 新 生 成 的 B— i 包 裹 , 以 在 X 射 线 衍 射 SC 所
图 中 看 不 到  ̄ S C。 - i 图 3是 反 应 烧 结 S C 三 维 刚 性 骨 架 增 强 的 铝 基 复 i 合 材 料 的 扫 描 电 镜 照 片 .从 照 片 中 可 以 看 到 铝 液 完 全
SIC 复合材料的分类及应用前景
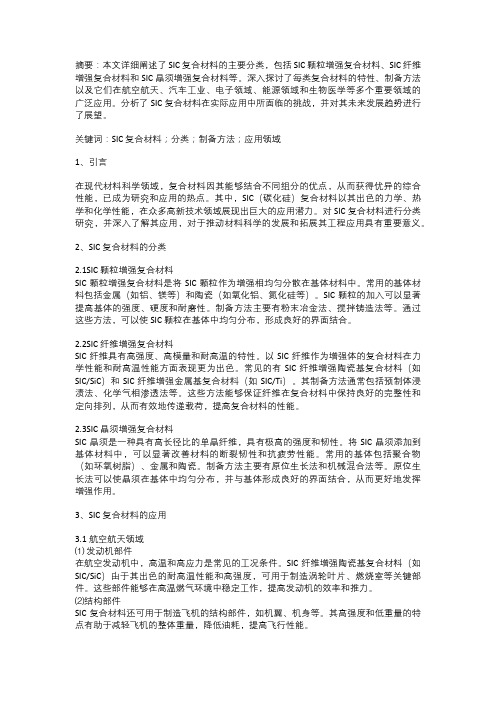
摘要:本文详细阐述了 SIC 复合材料的主要分类,包括 SIC 颗粒增强复合材料、SIC 纤维增强复合材料和 SIC 晶须增强复合材料等。
深入探讨了每类复合材料的特性、制备方法以及它们在航空航天、汽车工业、电子领域、能源领域和生物医学等多个重要领域的广泛应用。
分析了 SIC 复合材料在实际应用中所面临的挑战,并对其未来发展趋势进行了展望。
关键词:SIC 复合材料;分类;制备方法;应用领域1、引言在现代材料科学领域,复合材料因其能够结合不同组分的优点,从而获得优异的综合性能,已成为研究和应用的热点。
其中,SIC(碳化硅)复合材料以其出色的力学、热学和化学性能,在众多高新技术领域展现出巨大的应用潜力。
对 SIC 复合材料进行分类研究,并深入了解其应用,对于推动材料科学的发展和拓展其工程应用具有重要意义。
2、SIC 复合材料的分类2.1SIC 颗粒增强复合材料SIC 颗粒增强复合材料是将 SIC 颗粒作为增强相均匀分散在基体材料中。
常用的基体材料包括金属(如铝、镁等)和陶瓷(如氧化铝、氮化硅等)。
SIC 颗粒的加入可以显著提高基体的强度、硬度和耐磨性。
制备方法主要有粉末冶金法、搅拌铸造法等。
通过这些方法,可以使 SIC 颗粒在基体中均匀分布,形成良好的界面结合。
2.2SIC 纤维增强复合材料SIC 纤维具有高强度、高模量和耐高温的特性。
以 SIC 纤维作为增强体的复合材料在力学性能和耐高温性能方面表现更为出色。
常见的有SIC 纤维增强陶瓷基复合材料(如SIC/SiC)和 SIC 纤维增强金属基复合材料(如 SIC/Ti)。
其制备方法通常包括预制体浸渍法、化学气相渗透法等。
这些方法能够保证纤维在复合材料中保持良好的完整性和定向排列,从而有效地传递载荷,提高复合材料的性能。
2.3SIC 晶须增强复合材料SIC 晶须是一种具有高长径比的单晶纤维,具有极高的强度和韧性。
将 SIC 晶须添加到基体材料中,可以显著改善材料的断裂韧性和抗疲劳性能。
SiCP_Al基复合材料的研究与进展

SiCP/Al基复合材料的研究与进展罗洪峰 林 茂 陈致水 廖宇兰(海南大学机电工程学院 海南 570228)摘 要: 综述了SiCP/Al基复合材料的国内外研究现状,从材料的选择、制备技术和性能等方面,分析了该材料发展过程中存在的一些问题,并且展望了该材料今后的发展。
关键词:铝基复合材料 碳化硅颗粒 研究进展1、前言SiC P/Al基复合材料具有较高的比强度、比刚度、弹性模量、耐磨性和低的热膨胀系数等优良的物理性能,且制造成本低,可用传统的金属加工工艺进行加工,引起了材料研究者们的极大兴趣,在航空航天、军事领域及汽车、电子仪表等行业中显示出巨大的应用潜力。
从80年代初开始,国外投入了大量财力致力于颗粒增强铝基复合材料的研究,并已在航空航天、体育、电子等领域取得应用。
如DWA公司生产的25V ol%SiC P/6061Al基复合材料仪表支架已用于Lockheed飞机的电子设备。
美国海军飞行动力试验室研制成SiC P/Al基复合材料薄板并应用于新型舰载战斗机。
俄罗斯航空、航天部门将SiC P/Al基复合材料应用于卫星的惯导平台和支承构件。
国内从80年代中期开始在863计划的支持下,经过十几年的努力,SiC P/Al基复合材料的研究方面有了很大提高,在材料组织性能、复合材料界面等方面的研究工作己接近国际先进水平。
2、SiC P/Al基复合材料的制备工艺目前用于生产颗粒增强铝基复合材料的工艺方法大体可分为四类:液态工艺(搅拌铸造、液态金属浸渗、挤压铸造等)、固态法(粉末冶金等)、双相(固液)法(喷射共沉积、半固态加工等)、原位复合法。
2.1、搅拌铸造法搅拌铸造法是通过机械搅拌装置使增强体颗粒与固态或半固态的合金相互混合,然后浇注成锭子的技术。
与其它制备技术相比,该方法工艺设备简单、制造成本低廉,可以进行大批量工业生产,而且可制造各种形状复杂的零件,因此是目前最受重视、用得最多的制备铝基复合材料的实用方法。
mmc
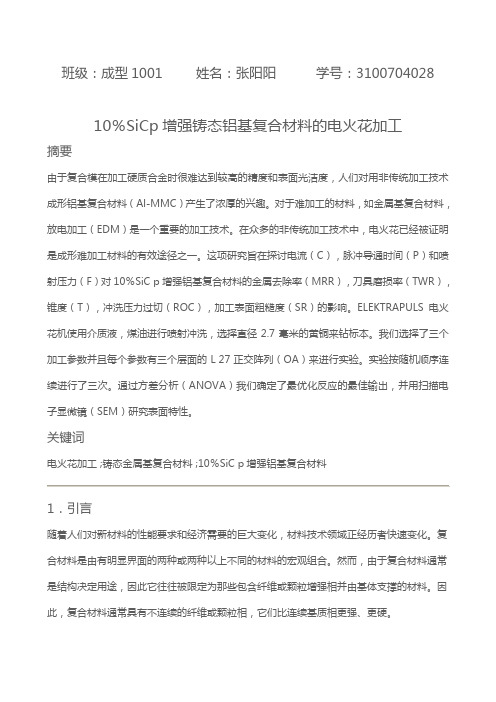
随着人们对新材料的性能要求和经济需要的巨大变化,材料技术领域正经历者快速变化。
复合材料是由有明显界面的两种或两种以上不同的材料的宏观组合。
然而,由于复合材料通常是结构决定用途,因此它往往被限定为那些包含纤维或颗粒增强相并由基体支撑的材料。
因此,复合材料通常具有不连续的纤维或颗粒相,它们比连续基质相更强、更硬。
MMC是那些以金属为基体,通常是铝,并以碳化硼、氧化铝或碳化硅的陶瓷纤维,颗粒或晶须为增强体的材料。
它们要么用电镀金刚石砂轮或碳化物,要么用多晶金刚石(PCD)刀具进行加工。
鉴于传统机械加工刀具磨损高、模具成本高,非接触的材料去除工艺中提供了一个有吸引力的替代方案。
在众多的非传统加工技术中,电火花加工被证明是处理复合材料行之有效的方法。
这项研究报告了与10%SiCp增强铸态铝基复合材料电火花加工相关的、一些正在进行的实验调查结果。
2.研究目的本研究的目的是探讨和报告对10%SiC p增强铝基复合材料进行电火花加工时,电流(C),脉冲导通时间(P)和喷射压力(F)对金属去除率(MRR),刀具磨损率(TWR),锥度(T),冲洗压力过切(ROC),加工表面粗糙度(SR)的影响3.实验过程3.1加工参数和响应变量确定三个加工参数和各级大小,如表1中给出。
响应变量就是金属去除率(MRR),刀具磨损率(TWR),锥度(T),冲洗压力过切(ROC),加工表面粗糙度(SR)。
表1. 加工参数和各级大小实验发现金属去除率(MRR)随着电流和脉冲导通时间的增加而增加(图3)。
同样很明显的是表面粗糙度值随着电流和脉冲导通时间的增加而增加(图6)较大的电流会导致两个电极(刀具和工件)间更高的热负载,随之而来的是两个电极材料被去除的量较高,因此也会导致高金属去除率和刀具磨损率。
这也将导致较大的缺口,因此表面也越粗糙。
此外,脉冲持续时间较长也导致一个大的放电去除量,从而导致更大的缺口大小和更大的表面粗糙度。
这些结果获得了Muller,Monaghan,Thomson和Hocheng的认同[9] ,而Hung 等人并不赞同,他们认为只有电流是表面光洁度主导因素。
粉末冶金法制备铝基复合材料的研究
粉末冶金法制备铝基复合材料的研究粉末冶金法是一种制备金属基复合材料的有效方法,具有制备的复合材料成分均匀、性能优异、成本低廉等优点。
铝基复合材料作为一种高性能的金属基复合材料,在航空、汽车、机械等领域得到了广泛应用。
本文将围绕粉末冶金法制备铝基复合材料展开,探讨其制备工艺、性能评价、应用领域及未来发展趋势。
粉末冶金法制备铝基复合材料的工艺流程主要包括以下几个步骤:原材料准备:选用纯度较高的铝粉、增强相(如SiC、Al2O3等)及适量的粘结剂。
混合与压制:将原材料按照一定的比例混合,加入适量的润滑剂,然后压制成型。
烧结:将压制成型后的生坯在高温下进行烧结,使得铝粉与增强相充分融合。
热处理:对烧结后的材料进行热处理,以进一步优化材料的性能。
通过以上步骤,制备出具有特定形状和性能的铝基复合材料。
与传统的铸造方法相比,粉末冶金法具有更高的成分均匀性、更细的晶粒结构和更好的力学性能。
铝基复合材料因其具有优异的力学性能、耐腐蚀性和抗高温性能,在航空、汽车、机械等领域得到了广泛应用。
在航空领域,铝基复合材料主要用于制造飞机发动机零部件、机身结构件等。
其轻质高强的特点使得飞机能够减轻重量,提高飞行效率。
在汽车领域,铝基复合材料主要用于制造汽车零部件,如发动机缸体、活塞、齿轮等。
其高强度和抗疲劳性能能够提高汽车的安全性和使用寿命。
在机械领域,铝基复合材料可用于制造各种高强度、轻质的机械零件,如传动轴、支架、齿轮等。
其优良的耐腐蚀性和高温稳定性使得铝基复合材料成为理想的机械零件材料。
铝基复合材料的性能取决于其组成和制备工艺。
在力学方面,粉末冶金法制备的铝基复合材料具有高强度、高硬度、低塑性等特点,其力学性能优于传统铸造铝材。
耐腐蚀性方面,由于增强相的加入,铝基复合材料的耐腐蚀性能得到显著提高。
抗高温性能方面,通过选用合适的增强相和热处理工艺,可以使得铝基复合材料在高温下保持优良的性能。
随着科技的不断发展,粉末冶金法制备铝基复合材料在未来将面临新的挑战和机遇。
铝基碳化硅复合材料加工刀具-PCD铣刀钻头
铝基碳化硅复合材料加工刀具-PCD铣刀/钻头铝基碳化硅,简称AlSiC(有的文献英文缩略语写为SICP/Al或Al/SiC、SiC/Al),是由碳化硅(SiC)和颗粒状的铝组成的一种颗粒增强金属基复合材料,凭借优异的高硬度,高韧性,高塑性,高模量等优势,在航空、航天、电子芯片、高铁、卫星等领域广泛应用。
航空航天行业高铁行业电子芯片行业卫星行业铝基碳化硅复合材料作为现代新型复合材料,有很多优势,但同样也有很明显的缺点,就是机械加工难度大,刀具磨损快,生产成本高,效率低。
难加工的主要原因在于铝基碳化硅复合材料中碳化硅增强颗粒硬度非常高,碳化硅的另一个名字是金刚砂,硬度仅次于金刚石,同时铝基碳化硅复合材料表面粗糙,碳化硅硬质点分布不均匀,在切削过程中刀具磨损较快,同时切削时会产生较大振动,影响加工精度。
因此在加工中刀具的选择和机床的选择尤为重要。
铝基碳化硅复合材料的加工方式(1)传统机械加工(车、铣、钻等):合金刀具,PCD金刚石刀具(2)铣磨加工:金刚石砂轮(3)激光加工:打孔,切割,划线(4)超声加工随着碳化硅颗粒体积分数的增大,切削性变差。
采用特种加工技术加工高体积分数碳化硅颗粒铝基复合材料,在去除率、表面质量、加工效率方面无法与车铣等常规传统机械加工方式相比。
因此,常规传统的机械加工方式仍是高体积分数碳化硅颗粒铝基复合材料的主要加工方式。
铝基碳化硅复合材料常见的加工方式有铣削、钻孔等,对曲面、孔、槽进行加工,为了更好的控制成本,粗加工可采用硬质合金刀具进行加工,精加工采用PCD刀具进行铣削和钻孔等,硬质合金刀具硬度虽低于铝基碳化硅,耐用度低,但可以大余量切削,PCD刀具硬度高,但切削余量小,适合精加工,保证铝基碳化硅复合材料零件的尺寸精度和表面粗糙度等要求。
PCD刀具是人工合成的一种多晶金刚石刀具,可以制作成PCD车刀、刀片、铣刀、铰刀、钻头等。
对于铝基碳化硅复合材料,常用的刀具有PCD铣刀、PCD钻头,常见的材质有CDW010,CDW025,CDW302,根据铝基碳化硅的成分选择不同的材质进行高效加工。
碳纤维增强铝基复合材料
检验抗氧化处理
抗氧化机理:外表包覆H3BO3的C/Cu复合丝在加入到铝 液的过程中,首先是H3BO3与O2接触,当温度较高时, H3BO3分解成熔融态的B2O3包覆在复合丝表面保护Cu 不被氧化。
XRD实验验证
结果:由图可知,复合材料中除了基体铝外,还出 现了Cu-Al合金相,但未检测到CuO、Al2O3、Cu的 存在,说明铜与铝发生了反应,生成了合金, H3BO3确实起到了保护作用,大大降低了铜的氧化
−
σ c = V f σ f F (lcr / l)C0 + (1 − V f )σ m
小结: 1)在硼酸存在下,大大降低了铜的氧化程度,碳纤维
分散均匀且没有损伤; 2)少量硼酸的加入,对基体的力学性能没有影响; 3)该复合材料的抗拉强度随碳纤维含量的增加而增 加,其抗拉强度较基体材料提高50%以上,但塑性却明
经过化学镀与电镀后碳纤维表面形貌
是复合 镀哦!
C/Al复合材料制备过程中防氧化处理
由于C/Al复合材料的制备是在700℃的高温条件下进行的,C/Cu复合 丝上的铜镀层在加入铝液中的瞬间就会被氧化成黑色的CuO。
2Cu+O2——2CuO 而CuO与Al不润湿,且与碳纤维结合力变差,因而,碳纤维在铝液中的分 散性和均匀性变差,根本得不到合格的C/Al复合材料.所以,必须对C/Cu 复合丝进行防氧化处理:将制备好的短C/Cu复合丝放入1.0%~1.5%的 硼酸水溶液中浸泡1 min,取出,于真空干燥箱中烘干,使其外表面包覆 一层硼酸.
即在我看来,抗氧化处理成了决定此次试验复合材料力学性能的一个重要 因素。
铝基复合材料的制备
主要制备方法有:液态法、固态法。 而C/Al复合材料制备方法主要是液态法:液态搅拌法(不连续纤维)、 液态挤压铸造法(连续纤维)等等。
粉末冶金法制备铝基复合材料的研究
粉末冶金法制备铝基复合材料的研究一、本文概述本文旨在探讨粉末冶金法制备铝基复合材料的工艺过程、性能特点及其应用前景。
铝基复合材料作为一种新型的高性能材料,以其轻质、高强、耐磨、抗腐蚀等特性在航空航天、汽车制造、电子信息等领域具有广泛的应用价值。
粉末冶金法作为一种制备铝基复合材料的常用方法,具有工艺简单、成本低廉、材料利用率高等优点,因此受到了广泛的关注和研究。
本文首先介绍了铝基复合材料的基本概念和分类,概述了粉末冶金法制备铝基复合材料的原理和方法。
接着,详细分析了粉末冶金法制备过程中影响铝基复合材料性能的关键因素,包括粉末的选择、复合剂的添加、成型工艺、烧结工艺等。
在此基础上,本文进一步探讨了粉末冶金法制备铝基复合材料的性能特点,如力学性能、热学性能、电磁性能等,并分析了其在实际应用中的潜力和挑战。
本文总结了粉末冶金法制备铝基复合材料的研究现状和发展趋势,提出了未来研究的重点和方向。
通过本文的研究,旨在为铝基复合材料的制备和应用提供理论支持和实践指导,推动铝基复合材料在更多领域的应用和发展。
二、铝基复合材料的理论基础铝基复合材料作为一种先进的轻质高强材料,其理论基础主要建立在金属学、材料科学、复合材料力学以及粉末冶金学等多个学科的基础上。
铝基复合材料以其低密度、高比强度、良好的导热和导电性、出色的抗腐蚀性以及优异的可加工性而广受关注。
铝基复合材料的性能提升主要得益于增强相的选择与加入。
增强相可以是颗粒状、纤维状或晶须状,其种类和性能直接影响复合材料的力学、热学、电磁等性能。
常见的增强相包括SiC、Al₂O₃、TiC等陶瓷颗粒,以及碳纤维、玻璃纤维等。
这些增强相在铝基体中通过阻碍位错运动、提高基体强度等方式,显著提升了复合材料的综合性能。
铝基复合材料的制备工艺对其性能有着至关重要的影响。
粉末冶金法作为一种重要的制备工艺,通过控制粉末的粒度、形貌、分布以及烧结过程中的温度、压力等参数,可以实现对复合材料微观结构和性能的精确调控。
- 1、下载文档前请自行甄别文档内容的完整性,平台不提供额外的编辑、内容补充、找答案等附加服务。
- 2、"仅部分预览"的文档,不可在线预览部分如存在完整性等问题,可反馈申请退款(可完整预览的文档不适用该条件!)。
- 3、如文档侵犯您的权益,请联系客服反馈,我们会尽快为您处理(人工客服工作时间:9:00-18:30)。
碳化硅增强铝基复合材料班级:gj材料102姓名:陈琨指导老师:张小立2012年6月6日SiC增强铝基复合材料摘要:SiC增强铝基复合材料能充分发挥SiC颗粒和金属基体的各自优势,而且可以进行成分设计,与基体合金相比,具有优异的机械性能和物理性能、高的比强度和比模量、良好的抗疲劳性能、低的热膨胀系数和良好的热稳定性,而且材料各向异性小,成本低廉,是一种具有广阔应用前景的先进材料,自问世以来一直受到材料科学及工程应用领域极大的重视,正在部分取代传统的金属材料而应用在航空航天、汽车、电子封装和体育器械等对材料性能要求较高的领域。
本文将综合介绍和分析影响其导热性能、热膨胀系数及热稳定性的主要因素;SiC增强铝基复合材料的研究和进展,并比较了几种该复合材料的制备工艺,包括搅拌铸造法、压力铸造法、无压渗透法、喷雾沉积法、离心铸造法和粉末冶金法等;SiC增强铝基复合材料断裂韧性的影响因素,其影响因素有增强相的尺寸、形状以及含量,热处理工艺,基体与增强相具有不同的膨胀系数,金属基体的化学成分等,并在前人研究的基础上提出了几点设想。
关键词:SiC 颗粒;铝基复合材料;研究方法;导热性;热膨胀性;断裂韧性;影响因素前言近年来在金属基复合材料中,以颗粒、短纤维、晶须等非连续相增强的铝基复合材料(SiC Reinforced Aluminium Matrix Composite)因其良好的可再加工性和各向同性而倍受重视。
由于其具有高的比强度、比刚度、导热性, 优良的摩擦性能,与铝合金密度相当,以及可调配的热膨胀系数等优点而成为目前国内外专家学者研究的热点之一。
而SiCp 价格低廉,来源广泛,用它作为增强相,可以改善铝基或铝合金基体的高、低温强度,提高其弹性模量,增强其耐磨性能。
所以铝基复合材料受到人们越来越广泛的关注, 国内外已对其进行了大量的研究报道。
1.SiC增强铝基复合材料的制备工艺【1】目前生产SiCp增强铝基复合材料的方法主要有搅拌铸造法、压力铸造法、无压渗透法、喷雾沉积法、离心铸造法和粉末冶金法等。
1.1 搅拌铸造法搅拌铸造法突出的优点是对设备要求低、工艺简单、易于实现,是制造铝基颗粒增强复合材料最常用的方法。
图1 为其示意图。
搅拌铸造法分为液相法和半固态法两类。
液相法是利用电磁或机械搅拌,在基体金属完全是液相的状态时向旋涡中逐渐投入颗粒,使其分散,待颗粒等增强物得到润湿、分散均匀后浇入金属模型中(或再进行挤压),制成复合材料。
用搅拌铸法制备SiCp增强铝基复合材料是先将铝锭放入坩埚,待其熔化后加入镁块,急速搅拌使之形成快速流动的旋涡。
在旋涡中心投入SiCp( SiCp 的质量分数为12%—20% ),继续搅拌10—20 min(搅拌速度为950 r/ min, 熔体温度约730℃),然后迅速倒入通水激冷的铸模,得到复合材料。
文献【2】对处于熔点以上的铝液及SiCp 施加一定时间的电脉冲,由此制得的复合材料,增强相颗粒分布均匀,基体合金晶粒细小,致密度、强度、耐磨性均较高。
半固态铸造法是金属在熔点附近,液相及非枝晶固相共存状态下,把增强物加入到剧烈搅动的含有一定组分固相粒子的金属液中,这时,即使增强物和金属液润湿不好,但由于金属液中固相粒子的作用,也可使之得到较好的分散,然后铸造成近终形复合材料。
使铝在760℃熔化后,降温至固相线与液相线之间,搅拌熔体,并加入SiCp。
因SiCp 的加入,会使熔体的粘度上升,随着粘度的上升再适当提高温度。
待SiCp加完后,再升温至760℃,短时间急速搅拌使颗粒均匀地分布在熔体中,然后浇铸成型。
该方法制得的材料凝固组织晶粒细小、均匀,没有粗大的树枝晶,可以消除颗粒在熔体中的偏析。
由于金属温度接近固相线温度,因此能消除金属从液相到固相凝固收缩引起的收缩缺陷,以及避免熔体因剧烈翻腾而大量吸入气体,但残留在半固态金属液中的气体和夹杂物不易排除。
1.2 压力铸造法压力铸造法被认为是适合大规模生产铝基复合材料的主要工艺之一,近年来得到了很快的发展,在颗粒、晶须或短纤维增强的实用铝基复合材料的制造中应用最多,且最为成功。
图2为压力铸造法示意图。
压力铸造法制备SiCp、晶须或短纤维增强铝基复合材料的工艺过程是首先把SiCp制成预制块,让铝或铝合金液在压力作用下渗入到预制块内制成复合材料。
将SiCp与水及粘结剂充分搅拌混合后放入模具内加压至5MPa,随后在80℃恒温箱内烘48h出模,获得具有一定强度的预制块,其孔隙度为60%。
压铸模和预制块预热至500℃,铝液加热至800℃浇注, 然后立即加压使铝液渗入预制块, 在125 MPa 的压力下保压3 min,除去压力待其自然冷却后出模。
制得的复合材料中含SiCp 的体积分数为40%。
压力铸造法制备复合材料工艺难度相对较大,主要是制备SiCp或粉末预成形坯块比较困难,强度不高,预制块在压渗过程中易崩溃,而且金属熔体不易充分地渗入到颗粒或粉末预成形坯内,最近的研究表明,通过增大压力的方法可以实现熔铝在粉末或颗粒预成形坯中的渗透。
1.3 无压渗透法无压渗透法是预先把增强体用适当的粘结剂粘结,做成所需形状的预制坯, 然后将预制坯放在金属模具型腔内的适当位置,浇注金属液,利用金属液体的自重压力和表面张力,使其渗透到有增强体的预制坯中,凝固后即成所要求的金属基复合材料。
这种方法主要适用于颗粒增强体和金属基材料的界面润湿性良好的金属基复合材料的制备。
图3为无压渗透法示意图。
由于此方法中的金属液体能较好地浸润增强相的表面,为获得良好的界面结合创造了条件,且工艺相对压力铸造法简单,便于操作。
但这种方法的关键是解决渗透气氛和颗粒之间润湿性的问题。
同时还存在预制坯预热临界温度不好控制,浸渗时压力和金属液温度也不易掌握等问题。
1.4 喷射沉积法喷射沉积法是将液态金属在高压下雾化,当液态金属从漏斗中流出的同时,将增强体粒子喷入金属液流中,两相混合的雾化液滴沉积在容器中形成复合材料。
图4 为喷射沉积法示意图。
采用工业纯铝(纯度为99.9%)与平均粒度为2—3um 的SiCp,喷射沉积制得SiCp的体积分数为35% 的SiCp增强铝基复合材料。
材料中,孔隙数量少、尺寸小,SiCp 分布均匀。
此法因在喷射沉积过程中冷却速度很快,界面反应受到抑制,使SiC 和铝界面之间有害的化学反应来不及完全进行,所以强化颗粒分布均匀。
由于增强体粒子在气流推动下高速射入熔体,所以对界面的润湿性要求不高,还可以消除颗粒偏析等不良组织。
但SiCp 与基体金属是机械结合,使得材料的抗拉强度有限。
另外还有孔洞,不适宜制备近终形产品。
1.5 离心铸造法离心铸造法是在高速旋转的SiCp 多孔预制形体中均匀浇铸金属铝熔体,使其在离心压力作用下渗入粒子的间隙,凝固后得到被SiC 粒子化的陶瓷颗粒增强铝基复合材料。
图5为离心铸造法示意图。
目前,国内外学者对用离心铸造法制备SiCp增强铝基复合材料还研究较少,但该方法可能会成为研制优质SiCp 增强铝基复合材料最有成效的技术之一。
1.6 粉末冶金法粉末冶金法制备SiCp增强铝基复合材料是先将SiCp、铝粉和成形剂混合后压制成形,经过脱脂、烧结成为近终形成品。
在文献【3】中用粉末冶金法制备SiCp增强铝基复合材料。
按设计成分,以酒精作分散剂进行球磨。
混合14h后烘干、除气,再冷压成坯,然后在自动化热压炉中热压,压力为23MPa。
热压时,采用流动高纯氩气保护。
为了便于脱模,先在400℃保温,20min后再升温600℃。
粉末冶金法的最大优点在于成分的自由度宽。
这种方法可以很好地控制复合材料的成分,从理论上讲是可以任意的配比,而且粉末冶金工艺也比较成熟。
用粉末冶金方法制备SiC 增强铝基复合材料时,SiCp 与铝基体可以良好地融合成一体,在SiC 含量不同层间没有明显的界面。
可将不同配比的粉末填铺模具中,冷压成形后再进行热压。
当疲劳裂纹从SiCp 的高含量层向低含量层扩展时会发生偏折和分枝,从而出现裂纹延滞现象。
但国内外学者用粉末冶金法来制备SiCp 增强铝基复合材料的不太多。
其原因是烧结过程不易控制,造成材料中孔隙多,而且在后续处理过程也不易消除,工业化成本较高。
但粉末冶金法生产SiCp增强铝基复合材料的前景十分广阔,很值得探索。
粉末冶金方法的优点还体现于在其他工艺中所起的作用。
例如在电子材料的封装壳体中所使用的SiCp增强铝基复合材料。
为了与基片材料的热膨胀系数的匹配,往往需要SiC 的体积分数达60% —70% ,而且,为了得到高的密度与性能,一般需要采用压力熔浸法来制造。
但是由于SiC 的含量多,所制备的材料往往难以进行后续加工。
这就需要预先将SiCp制备成近终使形的预制坯,再将Al 熔浸入预制坯内的孔隙,形成致密的复合材料。
而预制坯的制备采用的就是粉末冶金方法。
为了精确地控制预制坯在成形与预烧结过程中尺寸的变化、预制坯的微观组织及孔隙的分布,以得到符合外观、形状、组织与性能要求的复合材料,都需要相应的粉末冶金的知识。
2. SiC增强铝基复合材料断裂韧性的影响因素【4】不同屈服强度及应变硬化率的材料,在相同载荷条件下断裂形式可能完全不同;同种材料,复合比的变化、应力状态的改变,使裂端空穴扩展与断裂机制会发生重大改变,大量实验表明,材料在加载过程中,空穴的扩展与塑性应变的相互影响会使断裂过程变得复杂。
同时,试件在加载过程中裂端出现的塑性变形大小将不同,从而影响材料的断裂机制与断裂形式。
2.1 SiC增强铝基复合材料断裂形式(1)正拉断,当加载过程塑性应变不大、体积应变较大的情况下,空穴的成核与扩张易于进行,启裂位置发生在裂端钝化区应力三维度有极大值处。
启裂方向为该处最大拉应力作用面方向。
(2)剪切断裂,由于启裂点的位置不同,剪切实际存在两种情况一是当加载过程塑性应变较大时,虽然在钝化区域应力三维度有较大值,存在一定数目的成核空穴,但空穴扩张程度极小,正拉断不易发生,受空穴存在的影响,剪断发生在应力三维度有极大值处,启裂方向为该处最大剪应力方向。
二是当加载过程中塑性应变很大时,的塑性变形已使材料内的空穴成核受到阻碍,应力三维度最大处也较小有空穴成核形成,再成为危险点,启裂方向为该剪应力作用方向.在危险区域出现的局部化剪切变形形成的剪切带是导致剪断旋生的主要因素。
(3)混合型断裂,在许多情况下断裂面上正拉伸断口与剪切斜断口占一定区域,启裂先发生于试件厚度中心,以空穴扩展向表面及前方发展,由于试件表面应力三维度变小、塑性变形增大.引起断裂机制改变,近表面区域为剪断,启裂方向较为复杂。
2.2 影响SiC增强铝基复合材料断裂韧度的因素分析材料不同其屈服强度及应变硬化指数均可能不同,相同受力形式下,其断裂机制则可能不同。