颗粒增强铝基复合材料的研究
颗粒增强铝基复合材料的研究开发与应用
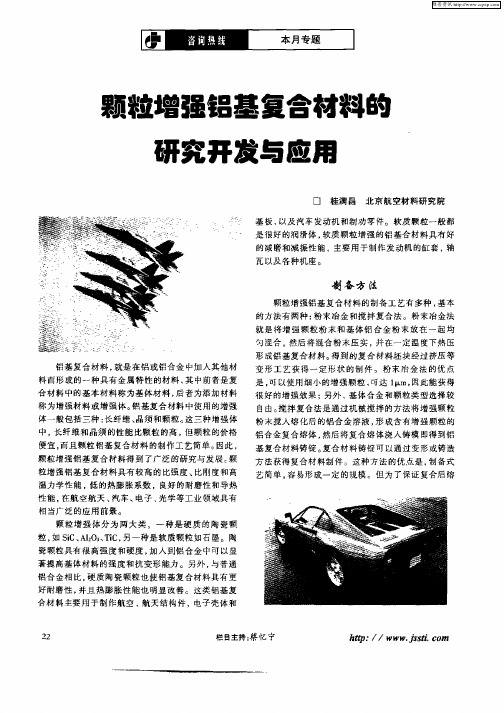
损 害最 终复合 材料 的性 能 。 一个成 功 的复合 材料制 备
过 程 , 须保 证颗 粒和 铝之 间达 到很好 结合 ,以及 颗 必 粒 和铝之 间没 有发 生 明 显 有 害 的化学 反应 。搅 拌 复 台 方 法发 展 的 初期 是 在 大 气 或气 体 保护 下 用搅 拌 产 生 的涡 流将 颗 粒 引入熔 体 ,由于搅 拌过 程 中吸人 气 体 和卷 入 氧 化夹 杂 .制备 的
高 3 的 密度 ,基 本 保 持 了铝 合 金 轻 质 、优 良导 热 % 性 能 的优 点 。此 外 ,颗 粒增 强 明显地 改善 了铝台 金 的耐磨 性 能 ,尤 其 是 在 有 润滑 条 件 下 的 耐磨 性 。 据 介 绍 。2v1%SC颗 粒 增 强 的铝 基 复台 材料 的耐磨 0o. i
粒 , SC、 l T C 另一种是 软 质颗粒如 石 墨 。陶 如 i Az O i, 瓷颗粒 具有 很 高强度 和硬度 , 入 到铝合 金 中可 以显 加 著提 高基体 材料 的强度 和抗 变形 能力 。另外 , 与普通 铝合 金相 比, 质陶 瓷颗粒 也 使铝基 复合材 料具 有更 硬 好耐磨 性 , 并且 热膨胀 性 能也 明显改 善 。这类 铝基复 合材料 主要用 于 制作航 空 、 航天结 构 件 ,电子壳 体和
温 力学性 能 , 的热膨 胀系数 ,良好的耐 磨性 和导 热 低 性能, 在航 空航天 、 汽车 、 电子 、 光学 等工 业 领域具有 相 当广 泛的应 用前 景。
艺简 单 , 易形成 一 定的规模 。但为 了保证 复合后 熔 容
颗粒 增 强 体 分 为 两大 类 ,一种 是 硬质 的陶 瓷颗
制备方 法
颗粒增 强铝基 复合材 料 的制 各工 艺有 多种 , 基本 的方法有两 种 : 粉末 冶金 和搅拌 复合 法 。粉末 冶金法
TiC颗粒增强铝基复合材料耐磨性能研究

力 图使 复合 材料 达 到较 低 的强 度 、较 高 的塑性 及 良好 的 表 1复合材料设计成 份表
T b 1C m p st ae il e inc m p n n a . o o i m t r sd sg o e a o et 合 金 号
1 2 2 l V0 %Ti C Al .Cu-0 6 -1 2 i 0.Mn一 . Ce -22 . Mg . S - 6 0 01 - 3 3 l Vo % C Al 2 2 一 . Cu一 6 g . S 一 . Mn一0 01 一 0.M 一1 2 i 0 6 . Ce 4 5 1 TC V0% i 5 C 一3 Zn 2. u 8 一 2Mn 2 2 b 一 .P 58 — —2 2 L + Vo %Ti D5 5 l C LD5 3 l T C + Vo % i
主 要 成 份
L D5 LD5 2 l T C + Vo % i
表 2 复合材料在 不同状 态下的硬度值
T b2 R s l f ad e si v r u tt s a . e ut o r n s n a i s s a e s h o
所 用复 合 材料 采 用 自蔓延 高 温合 成 原位 生 成法 ,通过 合
金 中 的元 素相 互作 用 而生 成 TC颗 粒 。这 两 种 方 法生 产 i
工 艺 较 简单 ,生成 TC颗 粒 性 质稳 定 ,与基 体 之 间界 面 i
干 净 ,结 合 良好 圄 。
2 实验 结 果
( )实验 材 料 的硬 度 。合 金 的硬 度值 与 强 度及 耐 磨 1 损 性 能 之 间存 在一 定 的关 系 。一 般说 ,硬度 愈 高 ,其 力 学 性 能 愈好 ,所 以通过 测 定合 金 的硬 度 值可 以快速 了解
SiC颗粒增强铝基复合材料磨削温度的研究

响, 为进一步深入研究颗粒增强铝基复合材料磨削 加工技术及其应用奠定基础.
1 实验 设 计
采用人工热电偶法测量磨削温度. 实验时在工 件 上加 工 直径为 3m 的盲孔 , 底 距 离被 加 工 表 m 孔
磨削是加工金属和陶瓷材料的重要方法 , 但应 用于颗粒增强金属基复合材料加工的研究较少 , 在 磨削温度 、 磨削加工机理等方面有待于进行系统深 入 的 研 究 . 文 通 过 人 工 热 电 偶 法 测 量 本
第2卷 第4 7 期
2 1 年8月 0 1
哈 尔 滨 商 业 大 学 学 报( 自然科 学版 )
J u n l fHabnUnv ri fC mmec Nau a S i c s dt n o r a r i iesy o o o t re( trl c n e io ) e E i
面 05m 将 K类 热 电偶 装 入 孔 中 , 证 热 电偶 . m. 保
口 , 图 1所示 . 如
金属丝 与孔 底 紧密接触 , 室温 固化胶 35封 闭 孔 用 0
热电势信号采集装置由计算机 、 / A D卡 , 采集
A2 2/ ip 1 4 S 复合材料的磨削温度 , 0 C 分析加工参数
卡.
越
赠
距离/ m m 图 1
户 50rm/ i,p O0 0 a r na = . a 5mm
、
实验材料主要参数见表 1 电镀金刚石砂轮参 .
图 3 主轴 转 速 对 磨 削 温 度 的 影 响
数见 表 2 .
增大进 给 速度 , 磨屑 厚 度 增 大 , 形 力 和 摩 擦 变
.
s ls i dc td t tt e g i d n e e aur n ra e t n r a i g o p n l p e , f e u t n iae ha h rn i g t mp r t e i c e s d wih i c e sn fs i d e s e d e d
碳化硅颗粒增强铝基复合材料的制备和性能研究的开题报告

碳化硅颗粒增强铝基复合材料的制备和性能研究的开题报告一、选题背景和研究意义随着工业领域对强度、硬度以及耐磨性等性能要求的日益提高,金属材料面临严峻的挑战。
传统的单一金属材料已经不能满足工业要求。
因此,铝基复合材料应运而生。
铝基复合材料具有优良的机械性能、高的耐腐蚀性、良好的热稳定性等优点,被广泛应用于汽车、航空航天、电子、能源等领域。
目前,铝基复合材料制备方法多种多样,其中碳化硅颗粒增强铝基复合材料受到人们的广泛关注。
碳化硅具有高强度、高硬度、高耐磨性等特点,能够有效增强铝基复合材料的力学性能,提高其耐磨性和抗疲劳性能,因此具有广阔的应用前景。
二、研究内容本研究旨在制备碳化硅颗粒增强铝基复合材料,并对其力学性能、热稳定性、耐磨性等性能进行研究。
具体包括以下内容:1. 碳化硅颗粒的制备:采用化学气相沉积法制备高纯度的碳化硅颗粒。
2. 铝基复合材料的制备:将碳化硅颗粒加入到铝合金熔体中,采用压力铸造方法制备铝基复合材料。
3. 材料性能测试:对制备的铝基复合材料进行力学性能、热稳定性、耐磨性等性能测试。
4. 微观结构分析:对铝基复合材料进行微观结构分析,探究碳化硅颗粒与铝基矩阵的相互作用机制。
三、研究方法1. 碳化硅颗粒的制备采用化学气相沉积法,通过改变反应条件来控制颗粒的尺寸和形貌。
2. 铝基复合材料的制备采用压力铸造法,可以提高材料的密实度和连续性。
3. 物理性能测试采用扫描电子显微镜、X射线衍射、热重分析等分析测试手段。
4. 微观结构分析采用透射电镜和扫描电镜等手段进行分析观察。
四、预期结果预计研究结果将优化碳化硅颗粒增强铝基复合材料的制备工艺,进一步提高材料的力学性能、热稳定性、耐磨性等性能,为该领域的研究提供新的理论依据和实验数据。
五、研究进度安排第一年1. 确定碳化硅颗粒的制备工艺;2. 制备铝基复合材料;3. 开展铝基复合材料的物理性能测试;4. 进行微观结构分析。
第二年1. 优化铝基复合材料的制备工艺;2. 继续进行铝基复合材料的物理性能测试;3. 开展铝基复合材料的力学性能和耐磨性测试;4. 继续进行微观结构分析。
搅拌铸造颗粒增强铝基复合材料颗粒分散性研究
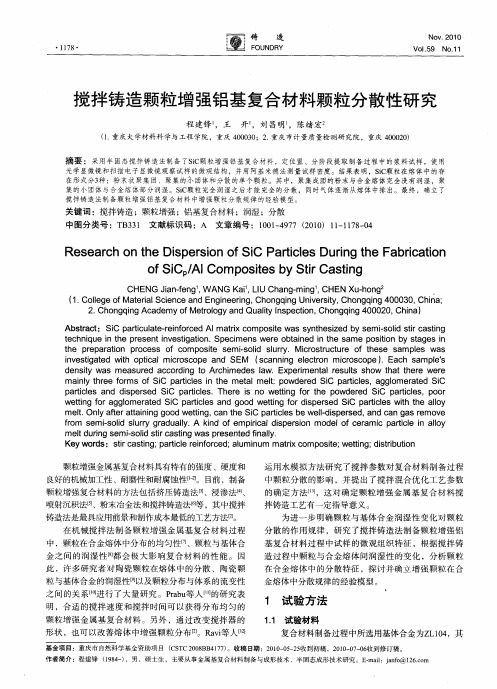
we t g f ra go r t d Si p rce n o d wet g f rds e s d Si a ils wi h l y tn o g lme ae C a ils a d g o ti o ip r e C p rce t t e al i t n t h o m et Ony at r t iig g o tig, a h C a ilsb lds e s d a d c ng sr mo e l . l f t nn o dwet e a a n c nt e Si p r ce ewel ip re , n a a e t - v
o CpAI f Si / Com o i sb i Ca t g p st y St si e r n
CHENG in f n ’ W ANG i L U Ch n - ig , Ja — g , e Ka’ I a g m n ’ CHEN Xu h n , —o g
( . lg f tr l c n ea dE gn eig C o g i nv ri , h n qn 0 0 0 C ia 1 Col eo e i i c n n ie r , h n qn U i st C o g i 4 0 3 , hn ; e Ma a S e n g e y g 2 C o g i c d myo t lg n ai s e t n C o g i 0 0 0 C ia . h n qn A a e f g Mer o ya dQu l I p ci , h n qn 4 0 2 , hn ) o t n y o g
t e r p r t n r c s o o p st s m i o i su r .M ir s r c u e f t e e a pe s h p e a a i p o e s f c m o i o e e . l s d l ry c o tu t r o h s s m ls wa
颗粒增强铝基复合材料研究与应用发展

3、结构性能
通过观察复合材料的显微组织,分析碳化硅颗粒的分布情况和界面结合情况。 实验结果显示,随着碳化硅颗粒含量的增加,颗粒分布逐渐均匀,界面结合强度 也逐渐提高。Fra bibliotek结果分析
实验结果表明,碳化硅颗粒增强铝基复合材料的物理性能、化学性能和结构 性能均得到显著改善。随着碳化硅颗粒含量的增加,复合材料的密度、硬度和界 面结合强度逐渐提高,而热导率呈现先增加后减小的趋势。这些现象和结果与碳 化硅颗粒含量、分布情况以及界面结合情况密切相关。
材料选择
碳化硅颗粒增强铝基复合材料的制备方法主要包括搅拌铸造法、挤压铸造法、 粉末冶金法和喷射沉积法等。本次演示选取搅拌铸造法进行研究,具体实验过程 如下:
1、按照一定比例将铝材和碳化硅颗粒混合均匀; 2、将混合物放入坩埚中,加热至熔化;
3、搅拌熔融的混合物,确保碳化硅颗粒均匀分布; 4、浇注至预定的模具中,冷却凝固后得到碳化硅颗粒增强铝基复合材料。
然而,尽管颗粒增强铝基复合材料具有诸多优点,但在其研究与应用方面仍 存在一些问题和不足之处。首先,制备工艺复杂且成本较高,限制了其广泛应用。 其次,材料的各向异性较为明显,影响了其性能的进一步提升。此外,关于颗粒 增强铝基复合材料在复杂服役条件下的长期性能和可靠性方面仍需进一步研究和 验证。
未来,随着科学技术的不断进步和研究的深入,颗粒增强铝基复合材料将会 在更多领域得到应用和发展。为进一步提高其性能和降低成本,可以研究新的制 备工艺和优化现有工艺参数,探索新型增强颗粒和基体合金。针对其各向异性和 长期性能问题,可以开展深入的理论和实验研究,建立完善的性能评价体系,为 实际应用提供更加可靠的依据。
感谢观看
3、结构设计难度大:由于碳化硅颗粒增强铝基复合材料的力学性能与传统 的金属材料存在较大差异,因此在进行结构设计时需要考虑更多的影响因素,增 加了设计的难度。
颗粒增强铝基通讯复合材料研究进展

刚度高 、热稳定性好 、耐磨性 好 、抗 腐蚀 、抗 疲 劳、密度
小 、不吸潮 、不老 化等 优 点_ ,是一 种 优 良的 结构 材 料。 1 ] 它不仅满足 了航 空航天 、能 源、高精 度机床 、尖 端武 器及 汽车等高端领域对材 料高性 能的要求 ,而且材料 的各 向同 性还使得材料可 以使用 传统 的金属加 工工艺 进行加 工 。所 有这些优点都使 P AMC 在高 、精 、尖领域 以及通讯 设施 R s
高温合成 法、原位热压放热反应合成 法、放热 弥散技术 、反应 自发浸渗技术等工艺 。对各工艺做 了详细的介 绍 ,指 出了未
来 的发 展 方 向 。
关 键 词 :颗 粒 增 强 ;制 备 工 艺 ;强 制 加 入 ;原 位 反 应
中 图分 类 号 :TB 3 3
文 献 标 识 码 :A
越 大 。根 据 文献 _ 可 知 颗 粒 的 直 径 、 间 距 以 及 体 积 分 数 之 2 ]
2 1 2铸 造 法 ..
铸 造 法 是 液 态 法 ( 融 金 属 加 工 法 ) 的 主 要 方 法 ,其 熔
关键是把 固相增强 颗粒均匀 地散布 于液态铝 中 ,并使 其最 终弥散地 分布在所 形成 的固态基体 中。铸造法 按增强 材料 与金属液体的混合 方式 不同 ,可分 为搅拌铸造 、正 压铸造 、 负压铸造等方法 。 2121 . . . 搅拌铸造法 目前 所采用的有液态机械搅 拌法及半 固态机械搅 拌法 。 液态机械搅拌法是通过搅拌 器 的旋 转运动使 增强材料 均匀 分布在液体中 ,然后浇注 成型 。此 法所用设 备 简单 ,操作 方便 ,但增强颗粒不易与 基体材料 混合 均匀 ,且材 料的 吸 气较严重 。半固态搅拌法是 利用合 金在 同液 温度 区间经搅 拌后得到的流变性质 ,将 增强颗粒 搅人 半 固态 熔液 中 ,依 靠半固态金属的粘性阻止 增强颗粒 因密度 差而浮沉 来制备 复合材料 。此法能获得增 强颗粒均 匀分 布的复 合材料 ,但
原位自生TiB2颗粒增强铝基复合材料及其研究现状

随着 高新 技术 的快 速 发展 , 传统 的单 一 材 料 已满 足 不 了社 会 各行业 的需 求 , 新 材 料 的研 制 和 开 发 已成
为 当前研 究 的热点 , 特 别是 具有 特殊 性能 的新材 料. 铝
污染 、 界 面结合 强度 高等 特点 , 并 避 免 了外 加法难 以解
等 优点 ] , 在航 空 、 航天 、 汽车、 电子 和交 通运 输等 行业 具 有十分 广 阔 的应 用 前 景. 颗 粒 增 强铝 基 复 合 材料 因
具 有增强 颗粒 成本 低 、 复合 材料微 观结 构较 均匀 、 材料 性 能各 向 同性 以及 可采 用传 统 的金属 加工 工艺 进行加 工等优 点, 成 为 金 属 基 复 合 材 料 的 重 要 发 展 方 向之
决 的夹杂 物 、 界 面反 应及 润湿性 等 问题 , 因而原 位 自生 颗粒 增强 复合 材 料 日益 受 到 重 视¨ 3 ] . 由于 受 到 反应
基 复合材 料 相对 于传 统 铝合 金 材 料 而 言 , 具 有 高 比强
度、 高 比模量 、 良好 的耐 磨性 、 低膨 胀 系数 及 尺 强 相 与 基 体具 有 界 面 干 净 、 无
收 稿 日期 : 2 O 1 2 一l 1 —2 3
a n Me t a l l u r g i c a l 冶 金公 司根据 铝合 金 晶粒细 化剂 生产
基 金项 目 : 国家高技术研究发展计划 ( 8 6 3 计划 ) 项 目( 2 0 0 6 AA0 3 Z 5 6 8 )
.
颗粒 增 强铝 基 复 合 材 料 研 究 中 的 一个 重 要 环
节是 复合 材料 的制 备. 颗 粒增 强 复合材 料 的制备 方法 , 按 照颗粒 的加 人方 式分 为外 加法 ( 强制 加入 法 ) 和原位
- 1、下载文档前请自行甄别文档内容的完整性,平台不提供额外的编辑、内容补充、找答案等附加服务。
- 2、"仅部分预览"的文档,不可在线预览部分如存在完整性等问题,可反馈申请退款(可完整预览的文档不适用该条件!)。
- 3、如文档侵犯您的权益,请联系客服反馈,我们会尽快为您处理(人工客服工作时间:9:00-18:30)。
颗粒增强铝基复合材料的研究姓名:陈云班级:10161201 学号:1016120118【摘要】本文简要介绍了常见的几种颗粒增强铝基复合材料的增强颗粒和性质,以及颗粒增强铝基复合材料的制备方法和应用。
【关键词】颗粒增强铝基复合材料碳化硅氧化铝碳化钛石墨粉末冶金原位反应合成0 前言金属基复合材料是以金属及其合金为基体,与一种或几种金属或非金属增强相人工结合成的复合材料。
铝基复合材料是金属基复合材料的一种,按照增强体形式不同可以分为长纤维增强铝基复合材料,短纤维增强铝基复合材料,晶须增强铝基复合材料及颗粒增强铝基复合材料。
颗粒增强铝基复合材料的增强颗粒克服了制备过程中出现的纤维损伤,微观组织不均匀,纤维与纤维相互接触,反应带过大等影响材料性能的缺点。
同时,颗粒增强铝基复合材料制备成本低廉,回收性和再利用性好,使其在各个领域都具有广泛应用。
因此,本文将简要介绍颗粒增强铝基复合材料的部分相关内容。
1 颗粒增强铝基复合材料颗粒增强铝基复合材料具有密度小,比强度、比刚度高,剪切强度高,热膨胀系数低,热稳定性和导热、导电性能良好,以及抗磨耐磨性能和耐有机液体和溶剂侵蚀优良等一系列优点。
颗粒的增强主要是弥散强化,颗粒越小,弥散强化的效果越好,材料的性能也就越佳。
颗粒增强铝基复合材料增强体的选择要求颗粒在基体中高度弥散均匀分散,尺寸大小要适度,与基体间要有一定粘结作用,而且它们之间各方面都要相匹配。
常见的增强颗粒有:碳化硅、碳化钛、氧化铝和石墨颗粒。
1.1 碳化硅颗粒增强铝基复合材料碳化硅颗粒增强铝基(SiC p/Al)复合材料是一种陶瓷颗粒增强金属基复合材料,它是用碳化硅颗粒作为增强体,采用铝或铝合金作基体,按设计要求,以一定形式、比例和分布状态,构成有明显界面的多组相复合材料。
通过改变碳化硅颗粒在复合材料中的含量,可以对材料的性能进行调整。
一般随碳化硅体积含量的增加,复合材料强度增加,塑性下降。
按SiC含量不同可将SiC p/Al复合材料的功能特性分为三类:SiC含量<20%,被用作结构级复合材料;SiC含量在35%~50%间,被用作光学仪表及功能级复合材料:SiC含量50%--80%,被用作电子级复合材料。
SiC p/Al复合材料的主要性能特点是高比强、高比刚度、耐高温、耐磨、耐疲劳、热膨胀系数小、尺寸稳定性好。
同时,SiC p/Al复合材料制造工艺设备简单,成本低,可以批量生产。
由于性能特点的多样性,SiC p/Al复合材料可以应用于各个不同的领域,耐磨性高,可以用于汽车制动盘和刹车转子、发动机活塞和齿轮箱;尺寸稳定性好,可以用于精密仪器构件、空间构件;比刚度高,可以用于航空航天的重要部件;膨胀系数低,使其可以很好地用在微电子热封装。
SiC p/Al复合材料常用的制备方法是粉末冶金法和铸造法,除此,还有,压喷射沉积法,压力熔渗法,无压熔渗法。
与欧美发达国家相比,我国SiC p/Al复合材料的研究起步较晚,技术工艺相对落后,但由于其发展潜力较大,相信在不久的未来,SiC p/Al复合材料会得到空前的发展与利用。
1.2 碳化钛颗粒增强铝基复合材料TiC p/Al复合材料是以碳化钛颗粒为增强体,铝或铝合金为基体的复合材料。
碳化钛颗粒在基体中较易分散,其增强效果较好,综合性能较高。
TiC p/Al复合材料由于TiC具有高硬度、高弹性模量、高耐磨性、高熔点和高热稳定性等特点被广泛应用。
随着TiC颗粒含量的增加,材料的耐磨性及硬度等性能也随之提升。
TiC p/Al复合材料的制备技术主要分两种类型。
一是外加预制的增强相,例如熔融搅拌法、压铸法和粉末冶金法。
此类方法在制取材料的过程中,有的存在严重的界面反应,有的基体与增强相间的相容性不良,难以达到理想的增强效果。
另一类即是目前引起广泛关注的原位合成法,它是将能够反应合成增强相的原料粉末混合,在一定温度下通过自发反应合成增强相,采用该方法生成的增强颗粒细小均匀,形状规则,与基体相容性好,两者结合牢固,且界面干净,热力学性能稳定,利于提高了材料的综合性能。
此外,该方法工艺简便、成本低;可制备形状复杂、大尺寸的产品,产品质量高。
1.3 氧化铝颗粒增强铝基复合材料氧化铝颗粒的熔点、强度和硬度高,并具有低的热膨胀系数、高的弹性模量,它是离子键化合物,抗晶格畸变能力及阻碍位错运动的抗力较强,是一种性能良好的颗粒增强相。
氧化铝颗粒增强铝基复合材料是以氧化铝颗粒增强铝或铝合金为基体的复合材料。
氧化铝颗粒增强铝基复合材料的增强体与基体之间具有良好的化学相容性,该复合材料是可以大批量生产和应用的金属基复合材料品种之一。
它的制备方法有粉末冶金法和铸造法等,最常用的为半固态法。
半固态法克服了传统铸造成形过程中易产生缩孔、缩松、气孔及尺寸偏差等缺点,时具有成形温度低,延长模具寿命,降低能耗和成本,改善生产条件和环境,提高产品质量(减少气孔和凝固收缩)及性能,减少加工余量,提高产品竞争力等许多优点。
1.4 石墨颗粒增强铝基复合材料石墨颗粒是软增强体,由于具有独特的层状结构本身就是一种优良的固体润滑剂。
同时,石墨还具有良好的减磨性能,使得石墨颗粒增强铝基复合材料具有优良的摩擦稳定性、抗咬合和抗擦伤性,适用于制作汽车活塞、衬套、轴瓦等耐磨件。
石墨颗粒增强铝基复合材料的制备方法主要有粉末冶金法、喷射沉积法、自蔓延高温合成法和铸造复合法。
铸造复合法与其他制备方法相比具有设备与工艺简单、制造成本低、易于操作等优点,所制得的复合材料可采用常规二次加工的方法制成零件或型材,因此,适合工业化大规模生产。
但铸造复合法制备过程中也存在很多问题,如:碳在固态和液态铝中的溶解度,且石墨与铝不润湿因此很难将石墨颗粒加入铝熔体,同时,由于未经处理的石墨颗粒表面粘附有机物,吸附有气体水分等物质更加破坏了其与铝熔体的润湿性;石墨颗粒密度比铝的密度小,很易在铝熔体中上浮和团聚,难以均匀分布;墨颗粒与铝熔体间的过度界面反应会在铝基体和石墨表面间形成脆性相和脆性层,破坏复合材料力学性能。
除此之外,颗粒增强铝基复合材料的增强颗粒还有Zr2、Ti02、Cr203、WC、Si3N4、Mo、Cr、W、非金属颗粒C、轻石等。
在所有颗粒增强铝基复合材料中氧化铝和碳化硅的发展较快、较成熟,被广泛应用。
由于我国盛产钨,所以以WC颗粒作为增强颗粒的复合材料的研究也越来越引起人们的注意。
2 颗粒增强铝基复合材料的制备方法颗粒增强复合材料的品种繁多,应该根据基体金属的物理、化学性质和增强材料的几何形状、物理、化学性质来选择合适经济的制备方法,大体可以分为:液态法,两相法,固态法和原位复合合成法。
2.1 液态法液态法是指基体金属处于熔融状态下与固态的增强材料复合在一起的方法,主要包括无压浸渗法、真空压力浸渗法、搅拌铸造法、热喷涂法。
2.1.1无压浸渗法无压浸渗法是将基体合金放在可控制气氛的加热炉中加热到基体合金液相线以上的速度,在不加压力的情况下合金熔体自发渗透到颗粒层或预制块中,最终形成颗粒增强铝基复合材料。
该技术是由美国Lanxide公司于开发出来的,制备工艺简单便捷,具有可操作性,通过适当控制,如合金成分、温度、保温时间,可以取得良好额润湿,使自发渗透得以进行。
目前,该工艺只能在一定条件下才能实现,合金含镁和氮气是两个前提条件,因此无压浸渗工艺具有局限性。
受到无压浸渗的启发,国内学者开展了在空气气氛环境下制备氧化铝和碳化硅颗粒增强铝基复合材料的研究,发现在颗粒增强物体中添加某种助渗剂或在铝合金熔体中添加某种起到助渗的物质,可以实现在空气中Al2O3/Al复合材料的无压浸渗制备,取得了良好的成果。
2.1.2真空压力浸渗法真空压力浸渍法是在真空和高压惰性气体共同作用下,将液态金属压入增强材料的预制件中,制备金属基复合材料零件的一种方法。
主要工艺参数包括:预制件的预热温度,金属熔体的温度,浸渍压力和冷却速度。
其中,预制件的预热温度和金属熔体的温度是影响浸渍是否完全和界面反应的最主要因素。
真空压力浸渍法适用面广,可以用来制造混杂复合材料。
浸渍在真空中进行,在压力下凝固,无气孔、缩松、缩孔等铸造缺陷,组织致密,材料性能好,工艺简单,参数容易控制,可根据增强材料和基体金属的物理化学特性,严格控制温度、压力等参数,避免严重的界面反应。
该法设备比较复杂,工艺周期长,制造大尺寸的零件要求大型设备。
2.1.3搅拌铸造法搅拌铸造是指将增强陶瓷颗粒加入高速搅拌的完全或者部分溶化的基体金属熔体中,然后浇注成复合材料的一种工艺。
目前,搅拌铸造法所采用的有液态机械搅拌法和半固态机械搅拌法。
前者是通过搅拌器的旋转运动使增强材料均匀分布在液体中,然后浇注成型。
后者是利用合金在固-液两相温度区间经搅拌后得到的流变性质,将增强颗粒搅入半固态溶液中,依靠半固态金属的粘性阻止增强颗粒因密度差而浮沉来制备复合材料,这种方法能获得增强颗粒均匀分布的复合材料,但是,它只适用于具有固液相温度区间的基体合金材料。
搅拌铸造法由于成本低,操作简单而广泛被广大学者所关注。
近年来,在航空航天、汽车工业以及体育器械等方面已经有大量的实例,如传动轴承,压缩活塞等。
2.1.4热喷涂法常用的热喷涂法为等离子喷涂,虽然等离子喷涂设备要求较高,但是由于工艺参数和气氛容易控制,因此在颗粒增强铝基复合材料制备上经常被采用。
等离子喷涂是利用等离子弧的高温下将基体金属熔化后喷射到工件(增强材料)上,冷却并沉积下来的一种复合方法。
等离子喷涂法不能直接制成复合材料零件,只能制造预制片,且组织不够致密,必须进行二次加工。
2.2固态法固态法将金属粉末与增强颗粒按设计要求以一定的含量、分布、方向混合排布在一起,再经加热、加压,将金属基体与增强物复合粘结在一起,形成复合材料。
粉末冶金法、热压法、热等静压法、轧制法、挤压和拉拔法、爆炸焊接法,均属于固态法。
粉末冶金法是最早应用于复合材料的开发的,在此,只介绍该制备方法。
粉末冶金法是制备高熔点难成型金属材料的传统工艺,同时它也是最早开发用于制备颗粒金属基复合材料的工艺,工艺过程是将固体增强颗粒和铝基粉末用机械手段均匀混合,经过筛分、混合、冷压固结以及除气处理,然后加热到固液相区进行真空热压制成复合材料。
目前,粉末冶金法是一种比较成熟的工艺方法。
使用粉末冶金法制得的产品具有界面反应少,增强相的含量可以根据需要进行调节,并且增强相分布均匀,性能稳定可进行传统的机械加工,综合强度水平比用熔融金属工艺生产的同种材料的高,伸长率也较高,材料微观组织结构有所改善。
但该方法工艺复杂,成本较高,金属粉末与陶瓷颗粒混合时会因颗粒分布不均匀,除气不完全导致材料内部出现气孔,温度选择不当易造成汗析。
另外,制得的复合材料坯件还需要二次成型。
2.3 两相法两相法主要包括半固态复合铸造工艺和喷射共沉积工艺。