金属热处理外文及翻译
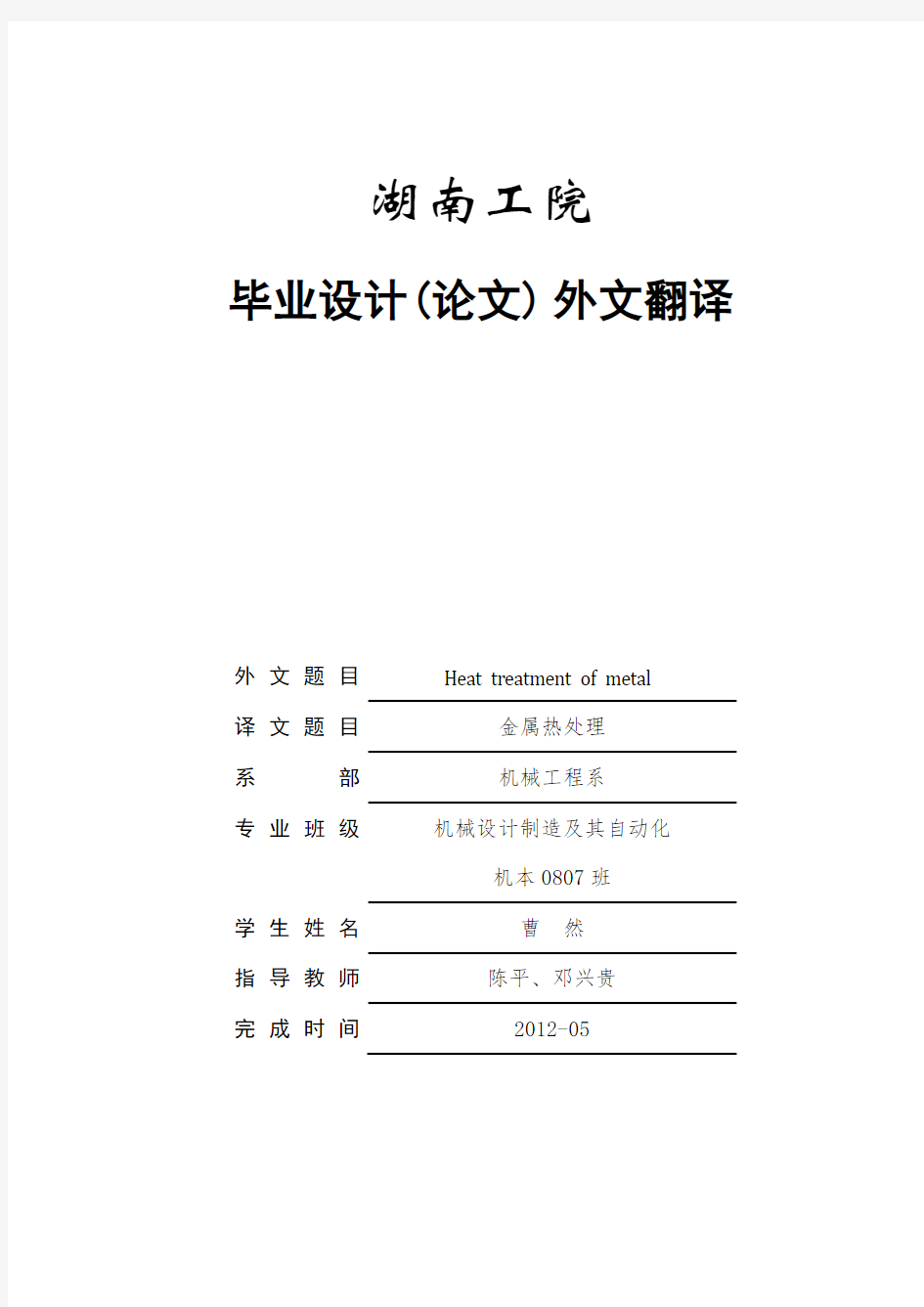

湖南工院
毕业设计(论文)外文翻译
外文题目Heat treatment of metal
译文题目金属热处理
系部机械工程系
专业班级机械设计制造及其自动化
机本0807班
学生姓名曹然
指导教师陈平、邓兴贵
完成时间2012-05
原文
Heat treatment of metal
The generally accepted definition for heat treating metals and metal alloys is “heating and cooling a solid metal or alloy in a way so as to obtain specific conditions or properties.”Heating for the sole purpose of hot working (as in forging operations) is excluded from this definition.Likewise,the types of heat treatment that are sometimes used for products such as glass or plastics are also excluded from coverage by this definition.
Transformation Curves
The basis for heat treatment is the time-temperature-transformation curves or TTT curves where,in a single diagram all the three parameters are plotted.Because of the shape of the curves,they are also sometimes called C-curves or S-curves.
To plot TTT curves,the particular steel is held at a given temperature and the structure is examined at predetermined intervals to record the amount of transformation taken place.It is known that the eutectoid steel (T80) under equilibrium conditions contains,all austenite above 723℃,whereas below,it is the pearlite.To form pearlite,the carbon atoms should diffuse to form cementite.The diffusion being a rate process,would require sufficient time for complete transformation of austenite to pearlite.From different samples,it is possible to note the amount of the transformation taking place at any temperature.These points are then plotted on a graph with time and temperature as the axes.Through these points,transformation curves can be plotted as shown in Fig.1 for eutectoid steel.The curve at extreme left represents the time required for the transformation of austenite to pearlite to start at any given temperature.Similarly,the curve at extreme right represents the time required for completing the transformation.Between the two curves are the points representing partial transformation. The horizontal lines Ms and Mf represent the start and finish of martensitic transformation.
Classification of Heat Treating Processes
In some instances,heat treatment procedures are clear-cut in terms of technique and application.whereas in other instances,descriptions or simple explanations are insufficient because the same technique frequently may be used to obtain different objectives.For example, stress relieving and tempering are often accomplished with the same equipment and by use of identical time and temperature cycles.The objectives,however,are different for the two processes.
The following descriptions of the principal heat treating processes are generally arranged according to their interrelationships.
Normalizing consists of heating a ferrous alloy to a suitable temperature (usually 50°F to 100°F or 28℃to 56℃) above its specific upper transformation temperature.This is followed by cooling in still air to at least some temperature well below its transformation temperature range.For low-carbon steels, the resulting structure and properties are the same as those achieved by full annealing;for most ferrous alloys, normalizing and annealing are not synonymous.
Normalizing usually is used as a conditioning treatment, notably for refining the grains of steels that have been subjected to high temperatures for forging or other hot working operations. The normalizing process usually is succeeded by another heat treating operation such as austenitizing for hardening, annealing, or tempering.
Annealing is a generic term denoting a heat treatment that consists of heating to and holding at a suitable temperature followed by cooling at a suitable rate. It is used primarily to soften metallic materials, but also to simultaneously produce desired changes in other properties or in microstructure. The purpose of such changes may be, but is not confined to, improvement of machinability, facilitation of cold work (known as in-process annealing), improvement of mechanical or electrical properties, or to increase dimensional stability. When applied solely to relive stresses, it commonly is called stress-relief annealing, synonymous with stress relieving.
When the term “annealing”is applied to ferrous alloys without qualification, full annealing is applied. This is achieved by heating above the alloy’s transformation temperature, then applying a cooling cycle which provides maximum softness. This cycle may vary widely, depending on composition and characteristics of the specific alloy.
Quenching is a rapid cooling of a steel or alloy from the austenitizing temperature by immersing the work piece in a liquid or gaseous medium. Quenching medium commonly used include water, 5% brine, 5% caustic in an aqueous solution, oil, polymer solutions, or gas (usually air or nitrogen).
Selection of a quenching medium depends largely on the hardenability of material and the mass of the material being treating (principally section thickness).
The cooling capabilities of the above-listed quenching media vary greatly. In selecting a quenching medium, it is best to avoid a solution that has more cooling power than is needed to achieve the results, thus minimizing the possibility of cracking and warp of the parts being treated. Modifications of the term quenching include direct quenching, fog quenching, hot quenching, interrupted quenching, selective quenching, spray quenching, and time quenching.
Tempering. In heat treating of ferrous alloys, tempering consists of reheating the austenitized and quench-hardened steel or iron to some preselected temperature that is below the lower transformation temperature (generally below 1300 ℃or 705 ℃). Tempering offers a means of obtaining various combinations of mechanical properties. Tempering temperatures used for hardened steels are often no higher than 300 ℃(150 ℃). The term “tempering”should not be confused with either process annealing or stress relieving. Even though time and temperature cycles for the three processes may be the same, the conditions of the materials being processed and the objectives may be different.
Stress relieving. Like tempering, stress relieving is always done by heating to some temperature below the lower transformation temperature for steels and irons. For nonferrous metals, the temperature may vary from slightly above room temperature to several hundred degrees, depending on the alloy and the amount of stress relief that is desired.
The primary purpose of stress relieving is to relieve stresses that have been imparted to the workpiece from such processes as forming, rolling, machining or welding. The usual procedure is to heat workpiece to the pre-established temperature long enough to reduce the residual stresses (this is a time-and temperature-dependent operation) to an acceptable level; this is followed by cooling at a relatively slow rate to avoid creation of new stresses.
The generally accepted definition for heat treating metals and metal alloys is “heating and cooling a solid metal or alloy in a way so as to obtain specific conditions or properties.”Heating for the sole purpose of hot working (as in forging operations) is excluded from this definition.Likewise,the types of heat treatment that are sometimes used for products such as glass or plastics are also excluded from coverage by this definition.
Transformation Curves
The basis for heat treatment is the time-temperature-transformation curves or TTT curves where,in a single diagram all the three parameters are plotted.Because of the shape of the curves,they are also sometimes called C-curves or S-curves.
To plot TTT curves,the particular steel is held at a given temperature and the structure is examined at predetermined intervals to record the amount of transformation taken place.It is known that the eutectoid steel (T80) under equilibrium conditions contains,all austenite above 723℃,whereas below,it is pearlite.To form pearlite,the carbon atoms should diffuse to form cementite.The diffusion being a rate process,would require sufficient time for complete transformation of austenite to pearlite.From different samples,it is possible to note the amount of the transformation taking place at any temperature.These points are then plotted on a graph with time and temperature as the
axes.Through these points,transformation curves can be plotted as shown in Fig.1 for eutectoid steel.The curve at extreme left represents the time required for the transformation of austenite to pearlite to start at any given temperature.Similarly,the curve at extreme right represents the time required for completing the transformation.Between the two curves are the points representing partial transformation. The horizontal lines Ms and Mf represent the start and finish of martensitic transformation.
Classification of Heat Treating Processes
In some instances,heat treatment procedures are clear-cut in terms of technique and application.whereas in other instances,descriptions or simple explanations are insufficient because the same technique frequently may be used to obtain different objectives.For example, stress relieving and tempering are often accomplished with the same equipment and by use of identical time and temperature cycles.The objectives,however,are different for the two processes.The following descriptions of the principal heat treating processes are generally arranged according to their interrelationships.
Normalizing consists of heating a ferrous alloy to a suitable temperature (usually 50°F to 100°F or 28℃to 56℃) above its specific upper transformation temperature.This is followed by cooling in still air to at least some temperature well below its transformation temperature range.For low-carbon steels, the resulting structure and properties are the same as those achieved by full annealing;for most ferrous alloys, normalizing and annealing are not synonymous.
Normalizing usually is used as a conditioning treatment, notably for refining the grains of steels that have been subjected to high temperatures for forging or other hot working operations. The normalizing process usually is succeeded by another heat treating operation such as austenitizing for hardening, annealing, or tempering.
Annealing is a generic term denoting a heat treatment that consists of heating to and holding at a suitable temperature followed by cooling at a suitable rate. It is used primarily to soften metallic materials, but also to simultaneously produce desired changes in other properties or in microstructure. The purpose of such changes may be, but is not confined to, improvement of machinability, facilitation of cold work (known as in-process annealing), improvement of mechanical or electrical properties, or to increase dimensional stability. When applied solely to relive stresses, it commonly is called stress-relief annealing, synonymous with stress relieving.
When the term “annealing”is applied to ferrous alloys without qualification, full annealing is applied. This is achieved by heating above the alloy’s transformation temperature, then applying a
cooling cycle which provides maximum softness. This cycle may vary widely, depending on composition and characteristics of the specific alloy.
Quenching is a rapid cooling of a steel or alloy from the austenitizing temperature by immersing the workpiece in a liquid or gaseous medium. Quenching medium commonly used include water, 5% brine, 5% caustic in an aqueous solution, oil, polymer solutions, or gas (usually air or nitrogen).
Selection of a quenching medium depends largely on the hardenability of material and the mass of the material being treating (principally section thickness).
The cooling capabilities of the above-listed quenching media vary greatly. In selecting a quenching medium, it is best to avoid a solution that has more cooling power than is needed to achieve the results, thus minimizing the possibility of cracking and warp of the parts being treated. Modifications of the term quenching include direct quenching, fog quenching, hot quenching, interrupted quenching, selective quenching, spray quenching, and time quenching.
Tempering. In heat treating of ferrous alloys, tempering consists of reheating the austenitized and quench-hardened steel or iron to some preselected temperature that is below the lower transformation temperature (generally below 1300 ℃or 705 ℃). Tempering offers a means of obtaining various combinations of mechanical properties. Tempering temperatures used for hardened steels are often no higher than 300 ℃(150 ℃). The term “tempering”should not be confused with either process annealing or stress relieving. Even though time and temperature cycles for the three processes may be the same, the conditions of the materials being processed and the objectives may be different.
Stress relieving. Like tempering, stress relieving is always done by heating to some temperature below the lower transformation temperature for steels and irons. For nonferrous metals, the temperature may vary from slightly above room temperature to several hundred degrees, depending on the alloy and the amount of stress relief that is desired.
The primary purpose of stress relieving is to relieve stresses that have been imparted to the workpiece from such processes as forming, rolling, machining or welding. The usual procedure is to heat workpiece to the pre-established temperature long enough to reduce the residual stresses (this is a time-and temperature-dependent operation) to an acceptable level; this is followed by cooling at a relatively slow rate to avoid creation of new stresses.
The generally accepted definition for heat treating metals and metal alloys is “heating and cooling a solid metal or alloy in a way so as to obtain specific conditions or properties.”Heating for the sole purpose of hot working (as in forging operations) is excluded from this definition.Likewise,
the types of heat treatment that are sometimes used for products such as glass or plastics are also excluded from coverage by this definition.
Transformation Curves
The basis for heat treatment is the time-temperature-transformation curves or TTT curves where,in a single diagram all the three parameters are plotted.Because of the shape of the curves,they are also sometimes called C-curves or S-curves.
To plot TTT curves,the particular steel is held at a given temperature and the structure is examined at predetermined intervals to record the amount of transformation taken place.It is known that the eutectoid steel (T80) under equilibrium conditions contains,all austenite above 723℃,whereas below,it is pearlite.To form pearlite,the carbon atoms should diffuse to form cementite.The diffusion being a rate process,would require sufficient time for complete transformation of austenite to pearlite.From different samples,it is possible to note the amount of the transformation taking place at any temperature.These points are then plotted on a graph with time and temperature as the axes.Through these points,transformation curves can be plotted as shown in Fig.1 for eutectoid steel.The curve at extreme left represents the time required for the transformation of austenite to pearlite to start at any given temperature.Similarly,the curve at extreme right represents the time required for completing the transformation.Between the two curves are the points representing partial transformation. The horizontal lines Ms and Mf represent the start and finish of martensitic transformation.
Classification of Heat Treating Processes
In some instances,heat treatment procedures are clear-cut in terms of technique and application.whereas in other instances,descriptions or simple explanations are insufficient because the same technique frequently may be used to obtain different objectives.For example, stress relieving and tempering are often accomplished with the same equipment and by use of identical time and temperature cycles.The objectives,however,are different for the two processes.The following descriptions of the principal heat treating processes are generally arranged according to their interrelationships.
Normalizing consists of heating a ferrous alloy to a suitable temperature (usually 50°F to 100°F or 28℃to 56℃) above its specific upper transformation temperature.This is followed by cooling in still air to at least some temperature well below its transformation temperature range.For low-carbon steels, the resulting structure and properties are the same as those achieved by full annealing;for most ferrous alloys, normalizing and annealing are not synonymous.
Normalizing usually is used as a conditioning treatment, notably for refining the grains of steels that have been subjected to high temperatures for forging or other hot working operations. The normalizing process usually is succeeded by another heat treating operation such as austenitizing for hardening, annealing, or tempering.
Annealing is a generic term denoting a heat treatment that consists of heating to and holding at a suitable temperature followed by cooling at a suitable rate. It is used primarily to soften metallic materials, but also to simultaneously produce desired changes in other properties or in microstructure. The purpose of such changes may be, but is not confined to, improvement of machinability, facilitation of cold work (known as in-process annealing), improvement of mechanical or electrical properties, or to increase dimensional stability. When applied solely to relive stresses, it commonly is called stress-relief annealing, synonymous with stress relieving.
When the term “annealing”is applied to ferrous alloys without qualification, full annealing is applied. This is achieved by heating above the alloy’s transformation temperature, then applying a cooling cycle which provides maximum softness. This cycle may vary widely, depending on composition and characteristics of the specific alloy.
Quenching is a rapid cooling of a steel or alloy from the austenitizing temperature by immersing the workpiece in a liquid or gaseous medium. Quenching medium commonly used include water, 5% brine, 5% caustic in an aqueous solution, oil, polymer solutions, or gas (usually air or nitrogen).
Selection of a quenching medium depends largely on the hardenability of material and the mass of the material being treating (principally section thickness).
The cooling capabilities of the above-listed quenching media vary greatly. In selecting a quenching medium, it is best to avoid a solution that has more cooling power than is needed to achieve the results, thus minimizing the possibility of cracking and warp of the parts being treated. Modifications of the term quenching include direct quenching, fog quenching, hot quenching, interrupted quenching, selective quenching, spray quenching, and time quenching.
Tempering. In heat treating of ferrous alloys, tempering consists of reheating the austenitized and quench-hardened steel or iron to some preselected temperature that is below the lower transformation temperature (generally below 1300 ℃or 705 ℃). Tempering offers a means of obtaining various combinations of mechanical properties. Tempering temperatures used for hardened steels are often no higher than 300 oF (150 ℃). The term “tempering”should not be confused with either process annealing or stress relieving. Even though time and temperature cycles for the three processes may be the same, the conditions of the materials being processed and the objectives may be different.
Stress relieving. Like tempering, stress relieving is always done by heating to some temperature below the lower transformation temperature for steels and irons. For nonferrous metals, the temperature may vary from slightly above room temperature to several hundred degrees, depending on the alloy and the amount of stress relief that is desired.
The primary purpose of stress relieving is to relieve stresses that have been imparted to the workpiece from such processes as forming, rolling, machining or welding. The usual procedure is to heat workpiece to the pre-established temperature long enough to reduce the residual stresses (this is a time-and temperature-dependent operation) to an acceptable level; this is followed by cooling at a relatively slow rate to avoid creation of new stresses.
金属热处理
对于热处理金属和金属合金普遍接受的定义是“加热和冷却的方式了坚实的金属或合金,以获得特定条件或属性为唯一目的。”暖气热加工(如锻造操作)被从这个定义排除.例如,热处理的是某些产品,如玻璃或塑料制品使用的类型也被排除在这个定义范围。
转变曲线
对热治疗的基础是时间温度曲线或倾斜试验曲线改造的地方,在一个图所有三个参数是该曲线的形状。因为,他们有时也称为C -曲线或S -曲线。
TTT治疗绘制曲线,特别是钢材举行一个给定的温度和结构是在预定的时间间隔检查,以记录转换采取量是已知的共析钢在平衡条件下(T80)包含,以上723奥氏体℃,而下面,它是珠光体,碳原子扩散,形成应该是一个扩散率的过程中,将需要完成的奥氏体转变为不同的样本足够的时间,有可能要注意转换的数额采取任何点进行,然后在一个随时间和温度的这些点绘制图表,曲线可以绘制转型所示的共析制成,曲线图极端离开代表着奥氏体转变所需的时间珠光体开始在任何温度.相似地,在极右曲线代表的完成的两条曲线的点代表局部改造所需的时间。横线代表女士和MF的开始和完成马氏体相变。
分类处理过程中的热
在某些情况下,热处理程序是明确的技术条款和应用.否则在其他情况下,简单的解释说明或削减是不够的,因为同样的方法经常可以用来获得不同物体.例如,压力正在缓解,回火往往具有相同的设备和相同的时间和温度使用旋回目标完成,然而,对于不同的两个过程。
处理过程中的主要热下面的说明,一般安排根据它们的相互关系。
规范包括由静止空气冷却到一定温度至少远低于遵循有色合金加热到适当温度高于其特定的上转换温度.This(通常为50 ℃到100 ℃或28℃至56℃)其相变温度range.For低碳钢,由此产生的结构和性质是完全退火所取得的相同;对大多数铁合金,正火,退火不是同义词。
规范通常被用作调理治疗,特别是用于提炼已受到锻造或其他热工操作,高温钢的晶粒。正火过程通常是成功的另一个热处理操作,如奥氏体的硬化,退火,回火等方式。
退火是一种通用术语表示一个热处理的加热并在合适的速率通过在适当的温度冷却后举行组成。它主要用于金属材料软化,但也同时产生其他财产或组织期望的变化。这种变化的目的可能是,但不仅限于,改善可加工性,促进工作的冷(如进程退火已知),机械或电气性能的提高,或增加尺寸稳定性。当应用仅重温讲,它通常被称为压力缓解压力救济退火,同义。
当术语“退火”是适用于无资格铁合金,完全退火应用。这是通过加热上述合金的相变温度,然后涂上冷却循环,提供了最大的柔软性。这个周期可能有很大的不同,这取决于具体的组成和合金的特点。
淬火是一个从奥氏体钢或高温合金,浸在液体或气体介质中的工件快速冷却。淬火中常用的包括水,5%盐水,水溶液,油,聚合物溶液或气体(通常是空气或氮气)5%烧碱。
淬火介质的选择很大程度上取决于材料的淬透性和正在治疗(主要部分厚度)材料的质量。
上述淬火介质的冷却能力相差很大。在选择淬火介质,它是最好的解决方案,以避免有更多的冷却能力比需要达到的结果,从而减少了开裂和变形的部分正在接
受治疗的可能性。一词的修改包括直接淬火淬火,淬火雾,热淬火,淬火中断,选择性淬火,喷雾淬火,淬火和时间。
回火。在黑色金属热处理合金,回火加热炉的奥氏体和淬火硬化钢或铁的一些预选的温度低于下转变温度(一般低于1300℃或705℃)组成。回火提供了一个获取力学性能的各种组合方式。为硬化钢回火温度通常采用不高于300℃(150℃)。术语“回火”不应该被混淆或者消除应力退火或过程。尽管这三个过程的时间和温度周期可能是相同的,这些材料被处理的条件和目标可能会有所不同。
消除应力。像回火,消除应力总是被加热到下面的一些钢材和铁的转变温度低的温度进行。有色金属,气温可能会有所不同温度高于室温稍微几百度,取决于合金和缓解压力的数量是需要的。
纾缓压力的主要目的是减轻压力已经从这些进程传授到工件的成形,轧制,加工或焊接。通常的程序是工件加热到预定的温度足够长的时间,以减少残余应力(这是一个时间和温度相关的操作)到一个可接受的水平,这是由处于相对缓慢的速度冷却,以避免创造遵循新的压力。
机械毕业设计英文外文翻译50材料的热处理
外文资料 HEAT TREATMENT OF METALS The understanding of heat treatment is embrace by the broader study of metallurgy .Metallurgy is the physics, chemistry , and engineering related to metals from ore extraction to the final product . Heat treatment is the operation do heating and cooling a metal in its solid state to change its physical properties. According to the procedure used, steel can be hardened to resist cutting action and abrasion , or it can be softened to permit machining .With the proper heat treatment internal ductile interior . The analysis of the steel must be known because small percentages of certain elements,notably carbon , greatly affect the physical properties . Alloy steels owe their properties to the presence of one or more elements other than carbon, namely nickel, chromium , manganese , molybdenum , tungsten ,silicon , vanadium , and copper . Because of their improved physical properties they are used commercially in many ways not possible with carbon steels. The following discussion applies principally to the heat treatment of ordinary commercial steel known as plain-carbon steels .With this proves the rate of cooling is the controlling factor, produces the opposite effect . A SIMPLIFIED IRON-CARBON DAGRAM If we focus only on the materials normally known as steels, a simplified diagram is often used . Those portions of the iron-carbon diagram near the delta region and those above 2% carbon content are of little importance to the engineer and are deleted. A simplified diagram, such as the one in Fig . 2.1 focuses on the eutectoid region and is quite useful in understanding the properties and processing of steel.
流体力学中英文对照外文翻译文献
中英文对照外文翻译(文档含英文原文和中文翻译)
14选择的材料取决于于高流动速度 降解或材料由于疲劳,腐蚀,磨损和气蚀故障糜烂一次又一次导致泵运营商成本高昂的问题。这可能通过仔细选择材料的性能以避免在大多数情况下发生。一两个原因便可能导致错误的材料选择:(1)泵输送的腐蚀性液体的性质没有清楚地指定(或未知),或(2),由于成本的原因(竞争压力),使用最便宜的材料。 泵部件的疲劳,磨损,空化攻击的严重性和侵蚀腐蚀与流速以指数方式增加,但应用程序各种材料的限制,不容易确定。它们依赖于流速度以及对介质的腐蚀性泵送和浓度夹带的固体颗粒,如果有的话。另外,交变应力诱导通过压力脉动和转子/定子相互作用力(RSI)真的不能进行量化。这就是为什么厚度的叶片,整流罩和叶片通常从经验和工程判断选择。 材料的本讨论集中在流之间的相互作用现象和物质的行为。为此,在某些背景信息腐蚀和经常使用的材料,被认为是必要的,但是一个综合指南材料的选择显然是超出了本文的范围。在这一章中方法开发出促进系统和一致方法选择材料和分析材料的问题领域。四个标准有关,用于选择材料暴露于高流动速度: 1.疲劳强度(通常在腐蚀环境),由于高的速度在泵本身与高压脉动,转子/定子的相互作用力和交变应力。 2.腐蚀诱导高的速度,特别是侵蚀腐蚀。 3.气蚀,由于已广泛在章讨论。 4.磨耗金属损失造成的流体夹带的固体颗粒。 磨损和汽蚀主要是机械磨损机制,它可以在次,被腐蚀的钢筋。与此相反,腐蚀是一种化学金属,泵送的介质,氧和化学试剂之间的反应。该反应始终存在- 即使它是几乎察觉。最后,该叶轮尖端速度可以通过液压力或振动和噪声的限制。 14.1叶轮和扩散的疲劳性骨折 可避免的叶轮叶片,整流罩或扩散器叶片的疲劳断裂施加领域的状态;它们很少观察到。在高负荷的泵,无视基本设计规则或生产应用不足的医疗服务时,这种类型的伤害仍然是有时会遇到。的主要原因在静脉或罩骨折包括: ?过小的距离(间隙B或比D3*= D3/ D2)叶轮叶片之间扩散器叶片(表10.2)。 ?不足寿衣厚度。 ?不足质量:叶片和护罩之间的圆角半径缺失或过于引起的小,铸造缺陷,脆性材料(韧性不足)热处理不足。 ?可能地,过度的压力脉动引起的泵或系统,第一章。10.3。 ?用液压或声叶轮的固有模式之间共振激发。也可能有之间的一个流体- 结构交互叶轮的侧板,并在叶轮侧壁间隙流动.. 转子/定子的互动和压力脉动章中讨论。10产生交替在叶轮叶片的压力和所述整流罩以及在扩散器叶片。这些应力的准确的分析几乎是不可能的(甚至虽然各组分能很好通过有限元程序进行分析),因为叶轮由不稳定压力分布的水力负荷不能定义。它不仅取决于流在叶轮,集电极和侧壁的差距,同时也对声学现象,并可能在脉动系统(也指章。10.3)。为了开发一致的实证过程评估装载叶轮和扩散器,用于选择叶片和护罩厚度或对所述的损伤的分析中,可以使用下一个均匀的负荷的简单梁的模型作为起点。因此,封闭的叶轮或扩散器的叶片是通过夹紧在两端的梁建模。开式叶轮或扩散器的描述由光束夹紧在一端,但游离在其他。根据表14.1和14.2的计算是基于以下assumptions1: 1.考虑叶片的最后部分中,在所述叶轮出口处的束夹在两者的宽度为X =5×e和跨度L = B2(E =标称叶片端厚度没有可能配置文件)。如果刀片是异形,平均叶片厚度青霉用于确
金属材料与热处理教案
绪论 引入: 材料金属材料 机械行业本课程得重要性 主要内容:金属材料得基本知识(晶格结构及变性) 金属得性能(力学及工艺性能) 金属学基础知识(铁碳相图、组织) 热处理(退火、正火、淬火、回火) 学习方法:三个主线 重要概念 ①掌握 基本理论 ②成分 组织性能用途热处理 ③理论联系实际 引入:内部结构决定金属性能 内部结构? 第一章:金属得结构与结晶 §1-1金属得晶体结构 ★学习目得:了解金属得晶体结构 ★重点:有关金属结构得基本概念:晶面、晶向、晶体、晶格、单晶
体、晶体,金属晶格得三种常见类型. ★难点:金属得晶体缺陷及其对金属性能得影响. 一、晶体与非晶体 1、晶体:原子在空间呈规则排列得固体物质称为“晶体"。(晶体内得原子之所以在空间就是规则排列,主要就是由于各原子之间得相互吸引力与排斥力相平衡得结晶。) 规则几何形状 性能特点: 熔点一定 各向异性 2、非晶体:非晶体得原子则就是无规则、无次序得堆积在一起得(如普通玻璃、松香、树脂等)。 二、金属晶格得类型 1、晶格与晶胞 晶格:把点阵中得结点假象用一序列平行直线连接起来构成空间格子称为晶格. 晶胞:构成晶格得最基本单元 2、晶面与晶向 晶面:点阵中得结点所构成得平面。 晶向:点阵中得结点所组成得直线 由于晶体中原子排列得规律性,可以用晶胞来描述其排列特征。(阵点(结点):把原子(离子或分子)抽象为规则排列于空间得几何点,称为阵点或结点。点阵:阵点(或结点)在空间得排列方式称
晶体。) 晶胞晶面晶向 3、金属晶格得类型就是指金属中原子排列得规律。 7个晶系 14种类型 最常见:体心立方晶格、面心立方晶格、密排六方晶格 (1)、体心立方晶格:(体心立方晶格得晶胞就是由八个原子构成得立方体,并且在立方体得体中心还有一个原子)。 属于这种晶格得金属有:铬Cr、钒V、钨W、钼Mo、及α—铁α-Fe 所含原子数 1/8×8+1=2(个) (2)、面心立方晶格:面心立方晶格得晶胞也就是由八个原子构成得立方体,但在立方体得每个面上还各有一个原子。 属于这种晶格得金属有:Al、Cu、Ni、Pb(γ-Fe)等 所含原子数1/8×8+6×1/2=4(个) (3)、密排六方晶格:由12个原子构成得简单六方晶体,且在上下两个六方面心还各有一个原子,而且简单六方体中心还有3个原子。 属于这种晶格得金属有铍(Be)、Mg、Zn、镉(Cd)等。 所含原子数 1/6×6×2+1/2×2+3=6(个) 三、单晶体与多晶体 金属就是由很多大小、外形与晶格排列方向均不相同得小晶体组成得,
毕业设计外文翻译附原文
外文翻译 专业机械设计制造及其自动化学生姓名刘链柱 班级机制111 学号1110101102 指导教师葛友华
外文资料名称: Design and performance evaluation of vacuum cleaners using cyclone technology 外文资料出处:Korean J. Chem. Eng., 23(6), (用外文写) 925-930 (2006) 附件: 1.外文资料翻译译文 2.外文原文
应用旋风技术真空吸尘器的设计和性能介绍 吉尔泰金,洪城铱昌,宰瑾李, 刘链柱译 摘要:旋风型分离器技术用于真空吸尘器 - 轴向进流旋风和切向进气道流旋风有效地收集粉尘和降低压力降已被实验研究。优化设计等因素作为集尘效率,压降,并切成尺寸被粒度对应于分级收集的50%的效率进行了研究。颗粒切成大小降低入口面积,体直径,减小涡取景器直径的旋风。切向入口的双流量气旋具有良好的性能考虑的350毫米汞柱的低压降和为1.5μm的质量中位直径在1米3的流量的截止尺寸。一使用切向入口的双流量旋风吸尘器示出了势是一种有效的方法,用于收集在家庭中产生的粉尘。 摘要及关键词:吸尘器; 粉尘; 旋风分离器 引言 我们这个时代的很大一部分都花在了房子,工作场所,或其他建筑,因此,室内空间应该是既舒适情绪和卫生。但室内空气中含有超过室外空气因气密性的二次污染物,毒物,食品气味。这是通过使用产生在建筑中的新材料和设备。真空吸尘器为代表的家电去除有害物质从地板到地毯所用的商用真空吸尘器房子由纸过滤,预过滤器和排气过滤器通过洁净的空气排放到大气中。虽然真空吸尘器是方便在使用中,吸入压力下降说唱空转成比例地清洗的时间,以及纸过滤器也应定期更换,由于压力下降,气味和细菌通过纸过滤器内的残留粉尘。 图1示出了大气气溶胶的粒度分布通常是双峰形,在粗颗粒(>2.0微米)模式为主要的外部来源,如风吹尘,海盐喷雾,火山,从工厂直接排放和车辆废气排放,以及那些在细颗粒模式包括燃烧或光化学反应。表1显示模式,典型的大气航空的直径和质量浓度溶胶被许多研究者测量。精细模式在0.18?0.36 在5.7到25微米尺寸范围微米尺寸范围。质量浓度为2?205微克,可直接在大气气溶胶和 3.85至36.3μg/m3柴油气溶胶。
冲压模具技术外文翻译(含外文文献)
前言 在目前激烈的市场竞争中,产品投入市场的迟早往往是成败的关键。模具是高质量、高效率的产品生产工具,模具开发周期占整个产品开发周期的主要部分。因此客户对模具开发周期要求越来越短,不少客户把模具的交货期放在第一位置,然后才是质量和价格。因此,如何在保证质量、控制成本的前提下加工模具是值得认真考虑的问题。模具加工工艺是一项先进的制造工艺,已成为重要发展方向,在航空航天、汽车、机械等各行业得到越来越广泛的应用。模具加工技术,可以提高制造业的综合效益和竞争力。研究和建立模具工艺数据库,为生产企业提供迫切需要的高速切削加工数据,对推广高速切削加工技术具有非常重要的意义。本文的主要目标就是构建一个冲压模具工艺过程,将模具制造企业在实际生产中结合刀具、工件、机床与企业自身的实际情况积累得高速切削加工实例、工艺参数和经验等数据有选择地存储到高速切削数据库中,不但可以节省大量的人力、物力、财力,而且可以指导高速加工生产实践,达到提高加工效率,降低刀具费用,获得更高的经济效益。 1.冲压的概念、特点及应用 冲压是利用安装在冲压设备(主要是压力机)上的模具对材料施加压力,使其产生分离或塑性变形,从而获得所需零件(俗称冲压或冲压件)的一种压力加工方法。冲压通常是在常温下对材料进行冷变形加工,且主要采用板料来加工成所需零件,所以也叫冷冲压或板料冲压。冲压是材料压力加工或塑性加工的主要方法之一,隶属于材料成型工程术。 冲压所使用的模具称为冲压模具,简称冲模。冲模是将材料(金属或非金属)批量加工成所需冲件的专用工具。冲模在冲压中至关重要,没有符合要求的冲模,批量冲压生产就难以进行;没有先进的冲模,先进的冲压工艺就无法实现。冲压工艺与模具、冲压设备和冲压材料构成冲压加工的三要素,只有它们相互结合才能得出冲压件。 与机械加工及塑性加工的其它方法相比,冲压加工无论在技术方面还是经济方面都具有许多独特的优点,主要表现如下; (1) 冲压加工的生产效率高,且操作方便,易于实现机械化与自动化。这是
R180柴油机曲轴工艺及夹具外文文献翻译、中英文翻译、外文翻译
中国地质大学长城学院 本科毕业设计外文资料翻译 系别:工程技术系 专业:机械设计制造及其自动化 姓名:刘庆鹏 学号: 05211602 年月日
外文资料翻译原文 R180柴油机曲轴工艺设计及夹具设计 一、研究目的及意义 曲轴是柴油机的关键零部件之一,主要用于往复运动的机械中,与连杆配合将作用在活塞上的气体压力变为旋转的动力。而随着机械化生产逐渐成为当今主流,传统的制造工艺已经不能满足人们的需求。结合实际进行理论分析,在保证产品质量,提高生产效率,降低生产成本的的前提下,对R180柴油机曲轴工艺进行优化设计。 二、R180曲轴工艺现状 从目前的整体水平来看,R180柴油机曲轴基本都是两种材质:一是钢锻曲轴;二是球墨铸铁曲轴。根据材质选择的不同,其生产方式也不同。为了保证生产精度,铸造方式生产的曲轴已经广泛运用于R180柴油机的运行。球墨铸铁具有良好的切削性能,并且可以进行各种热处理以及表面强化处理,故球墨铸铁被广泛运用于曲轴的生产。但是,曲轴毛坯的铸造工艺生产效率低下,工艺装备参差不齐,性能不够稳定、精度低、报废率高居不下,这一系列的问题都需要优化。 从目前整体水平来看, 毛坯的铸造工艺存在生产效率低,工艺装备落后,毛坯机械性能不稳定、精度低、废品率高等问题。从以下几个工艺环节采取措施对提高曲轴质量具有普遍意义。①熔炼国内外一致认为,高温低硫纯净铁水的获得是生产高质量球铁的关键所在。为获得高温低硫磷的纯净铁水,可用冲天炉熔化铁水,经炉外脱硫,然后在感应电炉中升温并调整成分。②球化处理③孕育处理冲天炉熔化球铁原铁水,对铜钼合金球铁采用二次孕育。这对于防止孕育衰退,改善石墨形态,细化石墨及保证高强度球铁机械性能具有重要作用。④合金化配合好铜和钼的比例对形成珠光体组织十分有利,可提高球铁的强度,而且铜和钼还可大大降低球铁件对壁厚的敏感性。⑤造型工艺气流冲击造型工艺优于粘土砂造型工艺,可获得高精度的曲轴铸件,该工艺制作的砂型具有无反弹变形量的特点,这对于多拐曲轴尤为重要。⑥浇注冷却工艺采用立浇—立冷,斜浇—斜冷、斜浇—反斜冷三种浇注方式较为理想,其中后一种最好。斜浇—反斜冷的优点是:型腔排气充分,铁水充型平稳,浇注系统撇渣效果好,冒口对铸件的补缩效果好,适应大批量流水线生产。 目前,国内大部分专业厂家普遍采用普通机床和专用组合机床组成的流水线生产,生产效率、自动化程度较低。曲轴的关键技术项目仍与国外相差1~2个数量级。国外的机加工工艺大致可归纳为如下几个特点。①广泛采用数控技术和
金属材料与热处理课后习题答案
第1章金属的结构与结晶 一、填空: 1、原子呈无序堆积状态的物体叫,原子呈有序、有规则排列的物体称为。一般固态金属都属于。 2、在晶体中由一系列原子组成的平面,称为。通过两个或两个以上原子中心的直线,可代表晶格空间排列的的直线,称为。 3、常见的金属晶格类型有、和三种。铬属于晶格,铜属于晶格,锌属于晶格。 4、金属晶体结构的缺陷主要有、、、、、和 等。晶体缺陷的存在都会造成,使增大,从而使金属的提高。 5、金属的结晶是指由原子排列的转变为原子排列的过程。 6、纯金属的冷却曲线是用法测定的。冷却曲线的纵坐标表示,横坐标表示。 7、与之差称为过冷度。过冷度的大小与有关, 越快,金属的实际结晶温度越,过冷度也就越大。 8、金属的结晶过程是由和两个基本过程组成的。 9、细化晶粒的根本途径是控制结晶时的及。 10、金属在下,随温度的改变,由转变为的现象称为
同素异构转变。 二、判断: 1、金属材料的力学性能差异是由其内部组织结构所决定的。() 2、非晶体具有各向同性的特点。() 3、体心立方晶格的原子位于立方体的八个顶角及立方体六个平面的中心。() 4、金属的实际结晶温度均低于理论结晶温度。() 5、金属结晶时过冷度越大,结晶后晶粒越粗。() 6、一般说,晶粒越细小,金属材料的力学性能越好。() 7、多晶体中各晶粒的位向是完全相同的。() 8、单晶体具有各向异性的特点。() 9、在任何情况下,铁及其合金都是体心立方晶格。() 10、同素异构转变过程也遵循晶核形成与晶核长大的规律。() 11、金属发生同素异构转变时要放出热量,转变是在恒温下进行的。() 三、选择 1、α—Fe是具有()晶格的铁。 A、体心立方 B、面心立方 C、密排六方 2、纯铁在1450℃时为()晶格,在1000℃时为()晶格,在600℃时为 ()晶格。A、体心立方 B、面心立方 C、密排六方 3、纯铁在700℃时称为(),在1000℃时称为(),在1500℃时称为()。
智能照明系统的外文文献原稿和译文
智能照明系统的外文文献原稿和译文
Introduction Introduction With the continuous development of our economy, rapidly rising living standards, people working and living environment have become increasingly demanding, while the lighting system requirements have become more sophisticated, the traditional lighting technology has been a strong blow. On the one hand because of information technology and computer technology changes in lighting technology, providing technical support; the other hand, due to energy shortage, the state more and more attention on energysaving lighting, new lighting control technology to develop rapidly to meet with By energy conservation, comfort, convenience requirements. Lighting control lighting control from the traditional manual method, automated lighting control to today's intelligent lighting control. Intelligent lighting control system is based on computercontrolled alldigital platform, modular, distributed bus control system, the central processor modules communicate directly through the network bus, the bus makes use of lighting, dimming, blinds, scene control to achieve intelligent, and become a complete bus system. Can be based on changes in the external environment in the device automatically adjust the status of the bus to reach safety, energy conservation, human effects, and can use in the future, in accordance with the requirements of users through the computer Way to increase or modify the system's functionality, without having to relaying of cables, intelligent lighting control system, high reliability, flexible control, lighting control is the traditional way can not be done. The basic components and monitoring the contents of the system System The basic components and monitoring the contents of the system System components Intelligent lighting control system is usually dimmer module, switch module, input module, the control panel, liquid crystal display touch screen, smart sensors, PC interface, time management module, handheld programmer, monitoring computer (need to bridge a large network connection) and other components composition.
金属材料及热处理中英文专业词汇表
《金属材料及热处理》课程中英文专业词汇表 (第二部分) 刘国权辑录整理 主要来源:全国材料科学名词委员会与中国材料研究学会组编的《材料科学名词》文稿; 国家标准GB/T 7232-1999 “金属热处理工艺术语”等。 材料热处理基础术语 热处理 heat treatment 采用适当的方式对材料或工件进行加热、保温和冷却以获得预期的组织结构与性能的工艺。 化学热处理 chemical heat treatment 将工件置于适当的活性介质中加热、保温,使一种或几种元素渗入它的表层,以改变其化学成分、组织和性能的热处理。 表面热处理 surface heat treatment 为改变工件表面的组织和性能,仅对其表面进行热处理的工艺。 局部热处理local heat treatment, partial heat treatment 仅对工件的某一部位或几个部位进行热处理的工艺。 预备热处理 conditioning heat treatment 为调整原始组织,以保证工件最终热处理或(和)切削加工质量,预先进行热处理的工艺。 真空热处理vacuum heat treatment, low pressure heat treatment在低于1×105Pa(通常是10-1~10-3Pa)的环境中进行的热处理工艺。 光亮热处理 bright heat treatment 工件在热处理过程中基本不氧化,表面保持光亮的热处理。磁场热处理 magnetic heat treatment 为改善某些铁磁性材料的磁性能而在磁场中进行的热处理。 可控气氛热处理controlled atmosphere heat treatment 将工件置于可控制其化学特性的气相氛围中进行的热处理。如无氧化、无脱碳、无增碳(氮)的热处理。 保护气氛热处理heat treatment in protective gases 在工件表面不氧化的气氛或惰性气体中进行的热处理。 离子轰击热处理plasma heat treatment, ion bombardment, glow discharge heat treatment 在低于1×105Pa(通常是10-1~10-3Pa)的特定气氛中利用工件(阴极)和阳极之 间等离子体辉光放电进行的热处理。 流态床热处理heat treatment in fluidized beds 工件由气流和悬浮其中的固体粉粒构成的流态层中进行的热处理。 高能束热处理high energy heat treatment 利用激光、电子束、等离子弧、感应涡流或火焰等高功率密度能源加热工件的热处理工艺总称。 稳定化热处理stabilizing treatment, stabilizing 为使工件在长期服役的条件下形状、尺寸、组织与性能变化能够保持在规定范围内的热处理。 形变热处理 thermomachanical treatment 将形变强化与相变强化相结合,以提高工件综合力学性能的一种复合强韧化工艺。 热处理工艺周期 thermal cycle 通过加热、保温、冷却,完成一种热处理工艺过程的周期。预热 preheating 在工件加热至最终温度前进行的一次或数次阶段性保温的过程。 奥氏体化 austenitizing工件加热至相变临界温度以上,以全部或部分获得奥氏体组织的操作。工件进行奥氏体化的保温温度和保温时间分别称为奥氏体化温度和奥氏体化 时间。
外文翻译原文
204/JOURNAL OF BRIDGE ENGINEERING/AUGUST1999
JOURNAL OF BRIDGE ENGINEERING /AUGUST 1999/205 ends.The stress state in each cylindrical strip was determined from the total potential energy of a nonlinear arch model using the Rayleigh-Ritz method. It was emphasized that the membrane stresses in the com-pression region of the curved models were less than those predicted by linear theory and that there was an accompanying increase in ?ange resultant force.The maximum web bending stress was shown to occur at 0.20h from the compression ?ange for the simple support stiffness condition and 0.24h for the ?xed condition,where h is the height of the analytical panel.It was noted that 0.20h would be the optimum position for longitudinal stiffeners in curved girders,which is the same as for straight girders based on stability requirements.From the ?xed condition cases it was determined that there was no signi?cant change in the membrane stresses (from free to ?xed)but that there was a signi?cant effect on the web bend-ing stresses.Numerical results were generated for the reduc-tion in effective moment required to produce initial yield in the ?anges based on curvature and web slenderness for a panel aspect ratio of 1.0and a web-to-?ange area ratio of 2.0.From the results,a maximum reduction of about 13%was noted for a /R =0.167and about 8%for a /R =0.10(h /t w =150),both of which would correspond to extreme curvature,where a is the length of the analytical panel (modeling the distance be-tween transverse stiffeners)and R is the radius of curvature.To apply the parametric results to developing design criteria for practical curved girders,the de?ections and web bending stresses that would occur for girders with a curvature corre-sponding to the initial imperfection out-of-?atness limit of D /120was used.It was noted that,for a panel with an aspect ratio of 1.0,this would correspond to a curvature of a /R =0.067.The values of moment reduction using this approach were compared with those presented by Basler (Basler and Thurlimann 1961;Vincent 1969).Numerical results based on this limit were generated,and the following web-slenderness requirement was derived: 2 D 36,500a a =1?8.6?34 (1) ? ??? t R R F w ?y where D =unsupported distance between ?anges;and F y =yield stress in psi. An extension of this work was published a year later,when Culver et al.(1973)checked the accuracy of the isolated elas-tically supported cylindrical strips by treating the panel as a unit two-way shell rather than as individual strips.The ?ange/web boundaries were modeled as ?xed,and the boundaries at the transverse stiffeners were modeled as ?xed and simple.Longitudinal stiffeners were modeled with moments of inertias as multiples of the AASHO (Standard 1969)values for straight https://www.360docs.net/doc/1619107817.html,ing analytical results obtained for the slenderness required to limit the plate bending stresses in the curved panel to those of a ?at panel with the maximum allowed out-of-?atness (a /R =0.067)and with D /t w =330,the following equa-tion was developed for curved plate girder web slenderness with one longitudinal stiffener: D 46,000a a =1?2.9 ?2.2 (2) ? ? ? t R f R w ?b where the calculated bending stress,f b ,is in psi.It was further concluded that if longitudinal stiffeners are located in both the tension and compression regions,the reduction in D /t w will not be required.For the case of two stiffeners,web bending in both regions is reduced and the web slenderness could be de-signed as a straight girder panel.Eq.(1)is currently used in the ‘‘Load Factor Design’’portion of the Guide Speci?cations ,and (2)is used in the ‘‘Allowable Stress Design’’portion for girders stiffened with one longitudinal stiffener.This work was continued by Mariani et al.(1973),where the optimum trans-verse stiffener rigidity was determined analytically. During almost the same time,Abdel-Sayed (1973)studied the prebuckling and elastic buckling behavior of curved web panels and proposed approximate conservative equations for estimating the critical load under pure normal loading (stress),pure shear,and combined normal and shear loading.The linear theory of shells was used.The panel was simply supported along all four edges with no torsional rigidity of the ?anges provided.The transverse stiffeners were therefore assumed to be rigid in their directions (no strains could be developed along the edges of the panels).The Galerkin method was used to solve the governing differential equations,and minimum eigenvalues of the critical load were calculated and presented for a wide range of loading conditions (bedding,shear,and combined),aspect ratios,and curvatures.For all cases,it was demonstrated that the critical load is higher for curved panels over the comparable ?at panel and increases with an increase in curvature. In 1980,Daniels et al.summarized the Lehigh University ?ve-year experimental research program on the fatigue behav-ior of horizontally curved bridges and concluded that the slen-derness limits suggested by Culver were too severe.Equations for ‘‘Load Factor Design’’and for ‘‘Allowable Stress Design’’were developed (respectively)as D 36,500a =1?4?192(3)? ?t R F w ?y D 23,000a =1?4 ?170 (4) ? ? t R f w ?b The latter equation is currently used in the ‘‘Allowable Stress Design’’portion of the Guide Speci?cations for girders not stiffened longitudinally. Numerous analytical and experimental works on the subject have also been published by Japanese researchers since the end of the CURT project.Mikami and colleagues presented work in Japanese journals (Mikami et al.1980;Mikami and Furunishi 1981)and later in the ASCE Journal of Engineering Mechanics (Mikami and Furunishi 1984)on the nonlinear be-havior of cylindrical web panels under bending and combined bending and shear.They analyzed the cylindrical panels based on Washizu’s (1975)nonlinear theory of shells.The governing nonlinear differential equations were solved numerically by the ?nite-difference method.Simple support boundary condi-tions were assumed along the curved boundaries (top and bot-tom at the ?ange locations)and both simple and ?xed support conditions were used at the straight (vertical)boundaries.The large displacement behavior was demonstrated by Mi-kami and Furunishi for a range of geometric properties.Nu-merical values of the load,de?ection,membrane stress,bend-ing stress,and torsional stress were obtained,but no equations for design use were presented.Signi?cant conclusions include that:(1)the compressive membrane stress in the circumfer-ential direction decreases with an increase in curvature;(2)the panel under combined bending and shear exhibits a lower level of the circumferential membrane stress as compared with the panel under pure bending,and as a result,the bending moment carried by the web panel is reduced;and (3)the plate bending stress under combined bending and shear is larger than that under pure bending.No formulations or recommendations for direct design use were made. Kuranishi and Hiwatashi (1981,1983)used the ?nite-ele-ment method to demonstrate the elastic ?nite displacement be-havior of curved I-girder webs under bending using models with and without ?ange rigidities.Rotation was not allowed (?xed condition)about the vertical axis at the ends of the panel (transverse stiffener locations).Again,the nonlinear distribu-