双导程蜗杆传动

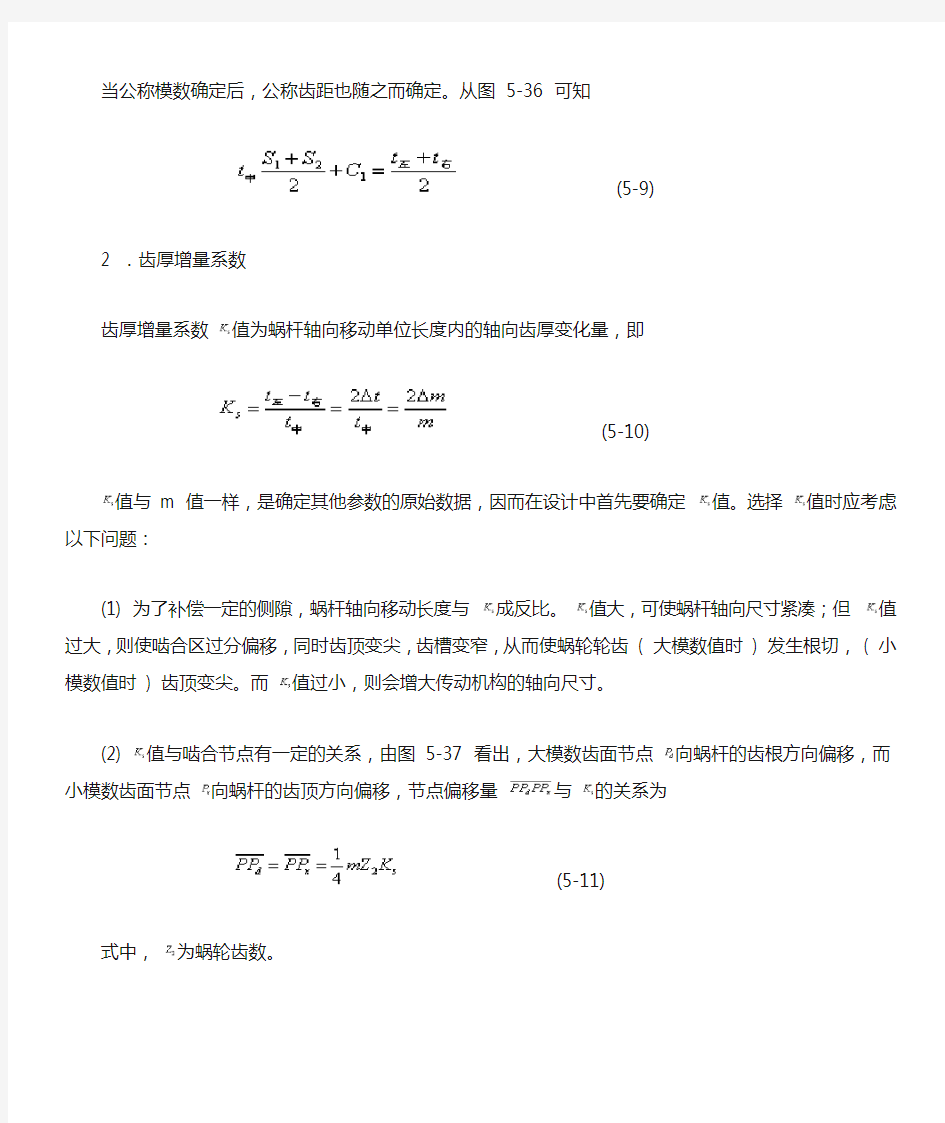
双导程蜗杆传动
双导程蜗杆传动具有改变啮合侧隙的特点,能够始终保持正确的啮合关系;并且结构紧
凑,调整方便,因而在要求连续精确分度的结构中被采用,以便调整啮合侧隙到最小程度。
双导程蜗杆副啮合原理与一般的蜗杆副啮合原理相同,蜗杆的轴向截面仍相当于基本齿条,蜗轮则相当于同它啮合的齿轮。双导程蜗杆齿的左、右两侧面具有不同的齿距 ( 导程 ) 或者说齿的左、右两侧面具有不同的模数 m(m=t /π ) ,但同一侧齿距则是相等的,因此,该蜗杆的齿厚从一端到另一端均匀地逐渐增厚或减薄,故又称变齿厚蜗杆,可用轴向移动蜗杆的方法来消除或调整啮合间隙。因为同一侧面齿距相同,没有破坏啮合条件,所以当轴向移动蜗杆后,也能保证良好的啮合。
双导程蜗杆的齿形如图 5-36 所示,图中,、分别为蜗杆左、右侧面轴向齿距;为公
称轴向齿矩;、分别为蜗杆左、右侧面齿形角; S 为齿厚; C 为齿槽宽。下面介绍
双导程蜗杆传动的特殊参数的选择。
图 5-36 双导程蜗杆齿形
1 .公称模数
双导程蜗杆传动的公称模数 m 可看成普通蜗杆副的轴向模数,用强度计算方法求得,并选取标准值,它一般等于左、右齿面模数的平均值。
当公称模数确定后,公称齿距也随之而确定。从图 5-36 可知
( 5-9)
2 .齿厚增量系数
齿厚增量系数值为蜗杆轴向移动单位长度内的轴向齿厚变化量,即
(5-10)
值与 m 值一样,是确定其他参数的原始数据,因而在设计中首先要确定值。选择值时应
考虑以下问题:
(1) 为了补偿一定的侧隙,蜗杆轴向移动长度与成反比。值大,可使蜗杆轴向尺寸紧凑;
但值过大,则使啮合区过分偏移,同时齿顶变尖,齿槽变窄,从而使蜗轮轮齿 ( 大模数值时 )
发生根切, ( 小模数值时 ) 齿顶变尖。而值过小,则会增大传动机构的轴向尺寸。
(2) 值与啮合节点有一定的关系,由图 5-37 看出,大模数齿面节点向蜗杆的齿根方向
偏移,而小模数齿面节点向蜗杆的齿顶方向偏移,节点偏移量与的关系为
(5-11) 式中,为蜗轮齿数。
图
5-37 啮合关系图
为了保证啮合质量,点不应超出蜗轮的齿顶高,点不应超出蜗杆的齿顶高,即
(5-12) 式中,为齿顶高系数。
因此,根据式 (5-11) 和式 (5-12) 得
(5-13)
3 .齿厚调整量
齿厚调整量ΔS 是为了补偿制造误差和蜗轮的最大允许磨损量所形成的侧隙而选取的。一般推荐ΔS=0.3~ 0.5mm 。对于数控回转工作台,ΔS 值应偏小。当传递动力时,ΔS 也可选为πmk 。
4 .模数差与节距差
模数差Δm 值为左、右齿面模数与公称模数 m 之差的绝对值。当已知 m 和值
时,有
(5-14) 因而
(5-15)
(5-16)
同样,节距差Δt 值、左面和右面齿距分别为
(5-17)
设计双导程蜗杆时,还要对齿槽变窄、齿顶变尖、蜗轮根切进行验算。
双导程蜗杆的优点是:啮合间隙可调整得很小,根据实际经验,侧隙调整可以小至 0.01~
0.015mm ,而普通蜗轮副一般只能达 0.03 ~ 0.08mm ,因此,双导程蜗杆副能在较小的侧隙下工作,这对提高数控回转工作台的分度精度非常有利。由于普通蜗杆是用蜗杆沿蜗轮径向移动来调整啮合侧隙,因而改变了传动副的中心距 ( 中心距的改变会引起齿面接触情况变差,甚至加剧磨损,不利于保持蜗轮副的精度 ) ;而双导程蜗杆是用蜗杆轴向移动来调整啮合侧隙,不会改变传动副的中心距,可避免上述缺点。双导程蜗杆是用修磨调整环来控制调整量,调整准确,方便可靠;而普通蜗轮副的径向调整量较难掌握,调整时也容易产生蜗杆轴线歪斜。
双导程蜗杆的缺点是:蜗杆加工比较麻烦,在车削和磨削蜗杆左、右齿面时,螺纹传动链要选配不同的两套挂轮,而这两种蜗距往往是烦琐的小数,对于精确配算挂轮很费时;同样,在制造加工蜗轮的滚刀时,应根据双导程蜗杆的参数设计制造,通用性差。
交错轴双滚子包络环面蜗杆传动啮合分析
交错轴双滚子包络环面蜗杆传动啮合分析 柳在鑫1,2,王进戈2,1, 张均富2,向中凡2 (1.四川大学制造科学与工程学院,四川成都610035;2. 西华大学机械工程与自 动化学院,四川成都610039) 摘要:为了消除环面蜗杆传动的齿侧间隙,提高其传动的精度和效率,分析了传统消隙蜗轮副的不足,在无侧隙双滚子包络环面蜗杆传动研究基础上提出一种交错轴双滚子包络环面蜗杆传动,采取双排滚子错位布置,且滚子轴线与蜗轮径向偏转一定角度。阐述了交错轴双滚子包络环面蜗杆传动的工作原理,依据空间齿轮啮合理论和微分几何理论,采用运动学法建立了蜗杆副的动静坐标系及接触点处的活动坐标系,推导了该新型环面蜗杆齿面方程和蜗轮齿面接触线方程,并导出了该传动的一界函数、诱导法曲率、润滑角及自转角等齿面啮合参数计算公式。最后运用matlab软件进行了数值仿真,并分析了滚柱偏置距离c2、滚柱半径R、交错角γ等参数对该蜗杆传动啮合性能的影响。仿真实例表明:要使该传动保持良好的接触性能和润滑性能,c2不宜超过10cm,R在8cm~15cm之间,γ在28o~50o之间。 Meshing Analysis of Non-parallel Double-roller Enveloping Hourglass Worm Gearing Abstract:To eliminate the backlash of enveloping worm and improve the precision and efficiency, by analyzing the shortcomings in the existing non-backlash worm gear sets, non-parallel double-roller enveloping hourglass worm gearing was proposed based on the research of non-backlash double-roller enveloping hourglass worm gearing. Two rows of rollers were assigned to misplace and there was a certain defection angle between the roller axis and the radial. The working principle was introduced. According to the theories of differential geometry and space engagement theory, the dynamic and static coordinate system based on worm gear pair and the moving coordinate system based on the contacting point were established. The tooth surface equations of worm and contacting line equations of worm gear were deduced. The formulas of meshing limit function, induced normal curvature, lubrication angle and rotation angle of the non-parallel double-roller enveloping hourglass worm gearing were derived by means of the theory of differential geometry. The simulation was conducted using MATLAB software, c2、R and γwhich impacted the engagement performance of this transmission, were analyzed. The numerical example showed that c2 should not be more than 10 cm, R should be controlled within 8 to 15cm, γshould be controlled within 28o to 50o, for effectively improving the meshing performance of the non-parallel double-roller enveloping hourglass worm gearing. Key words:non-parallel ; double-roller; hourglass worm gearing; meshing performance 收稿日期:2011-10-20 基金项目:国家自然科学基金资助项目(50775190) 作者简介:柳在鑫(1978—),男,副教授,博士研究生,研究方向:机械传动. E_mail: zhanxinliu@https://www.360docs.net/doc/2815447365.html,. 随着现代传动技术的发展,对蜗杆传动的啮合侧隙提出越来越高的要求。国内外无侧隙或齿侧间隙可补偿的蜗杆传动主要有双导程圆柱蜗杆传动[1]、正平面一次包络环面蜗杆传动[2]、侧隙可调式变齿厚平面蜗轮传动[3]、无侧隙双滚子包络环面蜗杆传动[4-6]和双蜗杆传动[7]。其中双导程圆柱蜗杆加工麻烦,通用性差;正平面一次包络环面蜗杆传动效率低,齿侧间隙调整不方便;变齿厚平面蜗轮传动仅调整传动副磨损后的侧隙,
双导程蜗杆
双导程蜗杆传动 双导程蜗杆传动 双导程蜗杆传动具有改变啮合侧隙的特点,能够始终保持正确的啮合关系;并且结构紧凑,调整方便,因而在要求连续精确分度的结构中被采用,以便调整啮合侧隙到最小程度。 双导程蜗杆副啮合原理与一般的蜗杆副啮合原理相同,蜗杆的轴向截面仍相当于基本齿条,蜗轮则相当于同它啮合的齿轮。双导程蜗杆齿的左、右两侧面具有不同的齿距( 导程) 或者说齿的左、右两侧面具有不同的模数m(m=t /π ) ,但同一侧齿距则是相等的,因此,该蜗杆的齿厚从一端到另一端均匀地逐渐增厚或减薄,故又称变齿厚蜗杆,可用轴向移动蜗杆的方法来消除或调整啮合间隙。因为同一侧面齿距相同,没有破坏啮合条件,所以当轴向移动蜗杆后,也能保证良好的啮合。 …… 1 .公称模数 双导程蜗杆传动的公称模数m 可看成普通蜗杆副的轴向模数,用强度计算方法求得,并选取标准值,它一般等于左、右齿面模数的平均值。 当公称模数确定后,公称齿距也随之而确定。从图5-36 可知 2 .齿厚增量系数 …… 3 .齿厚调整量 齿厚调整量ΔS 是为了补偿制造误差和蜗轮的最大允许磨损量所形成的侧隙而选取的。一般推荐ΔS=0.3~ 0.5mm 。对于数控回转工作台,ΔS 值应偏小。当传递动力时,ΔS 也可选为π mk 。 4 .模数差与节距差 …… 双导程蜗杆的优点是:啮合间隙可调整得很小,根据实际经验,侧隙调整可以小至0.01~ 0.015mm ,而普通蜗轮副一般只能达0.03 ~0.08mm ,因此,双导程蜗杆副能在较小的侧隙下工作,这对提高数控回转工作台的分度精度非常有利。由于普通蜗杆是用蜗杆沿蜗轮径向移动来调整啮合侧隙,因而改变了传动副的中心距( 中心距的改变会引起齿面接触情况变差,甚至加剧磨损,不利于保持蜗轮副的精度) ;而双导程蜗杆是用蜗杆轴向移动来调整啮合侧隙,不会改变传动副的中心距,可避免上述缺点。双导程蜗杆是用修磨调整环来控制调整量,调整准确,方便可靠;而普通蜗轮副的径向调整量较难掌握,调整时也容易产生蜗杆轴线歪斜。 双导程蜗杆的缺点是:蜗杆加工比较麻烦,在车削和磨削蜗杆左、右齿面时,螺纹传动链要选配不同的两套挂轮,而这两种蜗距往往是烦琐的小数,对于精确配算挂轮很费时;同样,在制造加工蜗轮的滚刀时,应根据双导程蜗杆的参数设计制造,通用性差。 aaaa双导程蜗杆简单说就是蜗杆的齿厚是变化的,这样就可以调整蜗轮蜗杆的间隙达到最佳状态。另外,当使用过程造成蜗轮蜗杆的间隙变大,可以通过调整蜗杆的轴向位置,使蜗轮蜗杆的间隙变小。方法是先加工蜗杆的一条螺旋线,按标准模数来确定蜗杆的螺距,当加工快到尺寸时,留出一定的余量,要根据模数大小而定,这时在这个蜗杆的螺纹的另一面对刀,并根据设计要求将车床的螺距调到相应的新螺距,这个螺距与先加工的螺距相差非常小,以致,每个螺距只相差0.10左右,这样,几个螺距就会使齿厚逐渐变化了。加工时要注意:1、要有一个测量基准点,最好是画上线,保证每次都测的是
车蜗杆
项目三车蜗杆 一、学习要求: 1.掌握蜗杆有关车削的计算方法和齿厚测量法。 2.掌握蜗杆车刀的刃磨及装夹方法。 3.掌握蜗杆的车削方法。 二、使用工、量具 90°车刀45°车刀车槽刀梯形螺纹刀角度样板 三、学习过程 学习过程:观察不同种类的滚花刀,认识不同滚花刀的滚花花纹效果,最后练习滚花的方法。用锉刀、砂布进行圆球面修整抛光操作练习,掌握成形面的抛光方法,教师应重点示范锉刀的握法及锉销姿势,手捏砂布的姿势,注意防范学生的操作安全。 四、相关工艺知识 蜗杆与蜗轮啮合原理如图6-17。蜗杆的齿形与梯形螺纹相似。蜗杆一般分米制蜗杆(齿形角为20°)和英制蜗杆(齿形角为20°)两种。我国常用米制蜗杆。由于蜗杆的齿型较深,切削面积较大,因此车削时比一般梯形螺纹要困难些。 1.蜗杆各部分尺寸计算 米制蜗杆的工作图及各部分尺寸计算见表6-1
2.蜗杆车刀 蜗杆车刀与梯形螺纹车刀相似,但蜗杆车刀两侧切削刃之间的夹角应磨成两倍齿形角。蜗杆
车刀一般选用高速钢材料车刀,在刃磨时,其纵进给方向一侧的后角必须相应加上螺纹升角。由于蜗杆的导程角较大,车削时会产生一定的困难,为此常采用可按导程调节的刀柄(图6-18)进行车削、由于具有弹性,不易产生扎刀现象。 (1) 蜗杆粗车刀(见图6-19) 粗车刀的要求是: 1) 为给精车留有加工余量,刀头宽度应小于齿根槽宽。 2) 车刀左右两侧切削刃之间的夹角要小于两倍齿形角。 3) 纵向前角γp =10°~15°。 4) p α=6°~8°。 5) 左后角L f α=(3°~5°)+γ;右后角R f α=(3°~5°)-γ。 (2)蜗杆精车刀 (见图6-20) 精车刀的要求是: 1) 切削刃直线度好,刀面光洁。 2) 车刀左右两侧切削刃之间的夹角要等于两倍齿形角。
基于solidworks的双导程蜗杆参数设计系统的开发与分析
目录 目录 1 绪论 (1) 1.1课题研究的背景 (1) 1.2国内外研究进展 (3) 1.3本课题研究的主要内容及意义 (4) 2 双导程蜗杆设计参数及其几何特征 (5) 2.1双导程蜗杆设计的基本参数与传动原理 (5) 2.2双导程蜗杆螺旋长度的设计与根切计算 (7) 2.3双导程蜗杆轴向齿厚的分析与计算 (13) 2.4本章小结 (14) 3 不同类型双导程蜗杆的数学模型 (15) 3.1阿基米德双导程蜗杆的数学模型 (15) 3.1.1坐标系的建立与坐标变换 (15) 3.1.2 阿基米德双导程蜗杆齿面的数学模型 (18) 3.1.3双导程蜗轮齿面的数学模型 (20) 3.2渐开线双导程蜗杆数学模型 (24) 3.2.1 渐开线曲线的几何原理 (24) 3.2.2 渐开线双导程蜗杆齿面的数学模型 (26) 3.2.3渐开线双导程蜗轮齿面数学模型 (30) 3.3延长渐开线双导程蜗杆数学模型 (32) 3.3.1延长渐开线曲线几何学及导圆柱的计算 (33) 3.3.2 延长渐开线双导程蜗杆齿面的数学模型 (37) 3.4本章小结 (39) 4 双导程蜗杆参数设计系统的设计与开发 (41) 4.1系统总体设计 (41) 4.1.1系统总体结构 (42) 4.1.2模块划分 (42) 4.2双导程蜗杆参数设计系统的开发 (44) 4.2.1双导程蜗杆参数设计系统的人机界面设计 (44) 4.2.2双导程蜗杆参数设计系统分析 (46) I
西安理工大学硕士学位论文 4.3本章小结 (49) 5 系统运行实例与验证分析 (51) 6 结论与展望 (55) 6.1结论 (55) 6.2展望 (55) 致谢 (57) 参考文献 (59) 附录 (63) 附录A:双导程蜗杆参数选择表 (63) 附录B:在校期间发表的论文 (65)
双导程蜗杆传动
双导程蜗杆传动 双导程蜗杆传动具有改变啮合侧隙的特点,能够始终保持正确的啮合关系;并且结构紧 凑,调整方便,因而在要求连续精确分度的结构中被采用,以便调整啮合侧隙到最小程度。 双导程蜗杆副啮合原理与一般的蜗杆副啮合原理相同,蜗杆的轴向截面仍相当于基本齿条,蜗轮则相当于同它啮合的齿轮。双导程蜗杆齿的左、右两侧面具有不同的齿距 ( 导程 ) 或者说齿的左、右两侧面具有不同的模数 m(m=t /π ) ,但同一侧齿距则是相等的,因此,该蜗杆的齿厚从一端到另一端均匀地逐渐增厚或减薄,故又称变齿厚蜗杆,可用轴向移动蜗杆的方法来消除或调整啮合间隙。因为同一侧面齿距相同,没有破坏啮合条件,所以当轴向移动蜗杆后,也能保证良好的啮合。 双导程蜗杆的齿形如图 5-36 所示,图中,、分别为蜗杆左、右侧面轴向齿距;为公 称轴向齿矩;、分别为蜗杆左、右侧面齿形角; S 为齿厚; C 为齿槽宽。下面介绍 双导程蜗杆传动的特殊参数的选择。 图 5-36 双导程蜗杆齿形 1 .公称模数 双导程蜗杆传动的公称模数 m 可看成普通蜗杆副的轴向模数,用强度计算方法求得,并选取标准值,它一般等于左、右齿面模数的平均值。 当公称模数确定后,公称齿距也随之而确定。从图 5-36 可知 ( 5-9) 2 .齿厚增量系数 齿厚增量系数值为蜗杆轴向移动单位长度内的轴向齿厚变化量,即 (5-10)
值与 m 值一样,是确定其他参数的原始数据,因而在设计中首先要确定值。选择值时应 考虑以下问题: (1) 为了补偿一定的侧隙,蜗杆轴向移动长度与成反比。值大,可使蜗杆轴向尺寸紧凑; 但值过大,则使啮合区过分偏移,同时齿顶变尖,齿槽变窄,从而使蜗轮轮齿 ( 大模数值时 ) 发生根切, ( 小模数值时 ) 齿顶变尖。而值过小,则会增大传动机构的轴向尺寸。 (2) 值与啮合节点有一定的关系,由图 5-37 看出,大模数齿面节点向蜗杆的齿根方向 偏移,而小模数齿面节点向蜗杆的齿顶方向偏移,节点偏移量与的关系为 (5-11) 式中,为蜗轮齿数。 图 5-37 啮合关系图 为了保证啮合质量,点不应超出蜗轮的齿顶高,点不应超出蜗杆的齿顶高,即 (5-12) 式中,为齿顶高系数。 因此,根据式 (5-11) 和式 (5-12) 得 (5-13) 3 .齿厚调整量
蜗轮蜗杆计算
蜗轮的计算公式: 1传动比=蜗轮齿数×蜗杆头数 2中心距=(蜗轮节圆直径+蜗轮节圆直径)△2 三。蜗轮中径=(齿数+2)×模数 4蜗轮齿数×蜗轮模数 5蜗杆螺距直径=蜗杆外径-2×模数 6蜗杆引线=π×元件×头数 7螺旋角(前角)TGB=(模数×头数)×蜗杆节径 基本参数: 蜗轮蜗杆模数m、压力角、蜗杆直径系数Q、导程角、蜗杆头数、蜗杆齿数、齿高系数(1)、间隙系数(0.2)。其中,模数m和压力角是蜗轮轴表面的模数和压力角,即蜗轮端面的模数和压力角,两者均为标准值。蜗杆直径系数q是蜗杆分度圆直径与其模数M的比值。 蜗轮蜗杆正确啮合的条件:
在中间平面,蜗杆和蜗轮的模数和压力角分别相等,即蜗轮端面的模数等于蜗杆轴线的模数,即标准值。蜗轮端面的压力角应等于蜗杆的轴向压力角和标准值,即==M。 当蜗轮的交角一定时,必须保证蜗轮和蜗杆的螺旋方向一致。 蜗轮结构通常用于在两个交错轴之间传递运动和动力。蜗轮相当于中间平面上的齿轮和齿条,蜗杆和螺钉的形状相似。 分类 这些系列大致包括:1。Wh系列蜗轮减速器:wht/whx/whs/whc2;CW系列蜗轮减速器:CWU/CWS/cwo3;WP系列蜗轮减速器:WPA/WPS/WPW/WPE/wpz/wpd4;TP系列包络蜗轮减速器:TPU/TPS/TPA/tpg5;PW型平面双包环面环面蜗杆减速器;另外,根据蜗杆的形状,蜗杆传动可分为圆柱蜗杆传动、环形蜗杆传动和斜蜗杆传动。[1] 组织特征 1该机构比交错斜齿轮机构具有更大的传动比。2两轮啮合齿面间存在线接触,其承载能力远高于交错斜齿轮机构。三。蜗杆传动相当于螺旋传动,即多齿啮合传动,传动平稳,
双导程蜗杆在CA6140车床上的加工难点解决方法
双导程蜗杆在CA6140车床上的加工难点解决方法 发表时间:2011-04-01T13:19:21.373Z 来源:《价值工程》2011年第3月中旬供稿作者:郭海燕[导读] 为保证蜗杆与其他表面的同轴度要求,工件采用两顶尖安装。加工中随时检测齿距和基准齿齿厚。郭海燕(烟台工程职业技术学院,烟台 264006) 摘要:针对双导程蜗杆在普通车床上加工中的实际困难,本文以生产中一产品为实例,从挂轮计算、刀具选择、操作方法三方面介绍了蜗杆部分在CA6140车床上的加工方法,解决了生产中的实际困难,起指导生产的作用。关键词:双导程蜗杆;挂轮计算;加工方法;刀具 中图分类号:TH16 文献标识码:A 文章编号:1006-4311(2011)08-0055-01 引言 双导程蜗杆因其啮合间隙可调整较小,传动精度高,目前在要求连续精确分度的结构中被采用。但因双导程蜗杆导程较大,基准齿左右两侧齿面的导程不相等,且大都为繁琐的小数,在加工过程中存在挂轮计算和操作两大困难。现以图1所示零件在C6140车床上的加工谈一下其难点解决方法。(技术参数见表1)。 . 1 挂轮计算 1.1 选一个与被加工基准齿左右两侧轴向齿距接近的一个标准导程Pn=12mm。加工时,将机床各手柄扳向铭牌中Pn=12mm所示档位。则挂轮箱中原A、B两轮挂轮比为:u原=A/B=63/75。 1.2 加工左右两侧不等导程时,挂轮箱中在保留原63、75挂轮基础上,需对齿轮C、D进行计算。 u左=C/D=Pn左/Pn=1 2.66/12=1.055=76/72; u右=C/D=Pn右/ Pn=12.473/12=1.0394=53/51。 1.3 对挂轮C/D进行误差检验:T左=76/72×12-1 2.66=+0.0067;T右=53/51×12-12.473=-0.0024。满足技术参数相邻轴向齿距极限偏差±0.008加工要求。 1.4 确定挂轮箱中齿轮,进行齿轮搭配验算加工左侧Pn左=1 2.66时u新左=A/B×C/D=63/75×76/72;加工右侧Pn右=12.473时u新右=A/B×C/D=63/75×53/51。经检验,左右两侧挂轮都符合挂轮搭配规则。见传动系统图2。 2 加工方法及刀具选择 2.1 按照标准导程Pn=12mm,先用直槽刀(如图3)采用直进法车一矩形螺旋槽,槽底车至尺寸。经过计算取刀宽a=2mm 刀长L=9mm。为增加工件刚性,防止加工中因背向力过大工件产生变形和产生“扎刀”现象,加工时,工件可采用一夹一顶或一夹一搭的装夹方式。 2.2 根据上述配换的左右两齿面挂轮,采用图四刀具用斜进法分别加工左右两齿面,并保证基准齿齿厚(留出磨削余量)。为保证蜗杆与其他表面的同轴度要求,工件采用两顶尖安装。加工中随时检测齿距和基准齿齿厚。 2.3 刀具角度要求因受螺纹升角ψ的影响,在加工过程中,刀具的实际工作后角会产生变化,为增加刀具刚性,并使加工顺利进行,刃磨刀具时,参数如下: 因工件为右旋: 车刀后角α(右)=(3°~5°)- ψ右=(3°~5°)- 5°9′22″ =-2°9′22″~0°9′22″ α(左)=(3°~5°)+ ψ左=(3°~5°)+ 5°14′0″ =8°9′22″~10°9′22″ 参考文献: [1]袁学柄.双导程圆柱蜗杆传动副的加工制造.组合机床与自动化加工技术,1999,(5). [2]严秀玲.双导程圆柱蜗杆传动的设计与应用.汽齿科技,2007,(1).
蜗杆
双线蜗杆的两级优化设计 双导程蜗杆蜗轮传动是一个方便的消隙机构,它可用于精密机械工具和导向装置。目的是尽量减少蜗杆和齿轮之间的摩擦力。约束条件包括蜗杆几何体,应力,位移和蜗杆的固有频率。为了避免困难的三维优化问题,本文介绍一种两阶段优化方法。第一级优化使用一个近似模型,在这阶段蜗杆的线程是近似的元素。蜗杆和蜗轮的节圆直径、模数以及左右侧模块的差异是设计变量。第二级优化使用真正的三维实体模型与连续螺旋线确定最佳形状的蜗杆线程。实例表明这是可行的和有效的。 关键词:机械设计;双导程蜗杆;两阶段优化 引言 蜗轮蜗杆齿轮组是一个重要的机械传动机构,这一装置优点在于其较高减速比和紧凑的尺寸。这一机构的缺点是功率的损失相对其他类型的齿轮组高。工业上蜗杆蜗轮组主要用于减速器、导向和定位装置。因为蜗杆蜗轮组几何性质和动力传输机构不同于其他类型的齿轮,很多运动学和接触蜗杆和蜗轮齿的研究已经进行了1–[7]。 由于近年来高科技产业的蓬勃发展,对精密的机器和精密的制造工艺的需求迅速增加。精确定位的切割工具或工件的关注重点精密机械制造工艺。在机械领域精密齿轮和滚珠丝杠实现这些目标的关键部件。但是众所周知,即使在最高级别的精密齿轮中齿间间隙仍不能消除。反弹是影响定位精度的主要因素之一。黑尔和斯洛克姆[ 8]提到一些美国隙设计专利。其中之一是用于蜗轮蜗杆齿轮传动。其设计理念是类似于一个滚珠螺杆。在蜗杆的线程和蜗轮的齿牙之间插入滚珠,尽量减小蜗杆蜗轮之间反弹间隙。这种设计成本高。一种更便宜的方法,这是本文提到的,使用的是双导程蜗杆蜗轮组。蜗杆的双引线是特别设计的,有两种不同导致双向的蜗杆线程。由于不同的引导线,两侧的线程在轴向方向的厚度不同。这种设计的优点是蜗杆蜗轮之间的间隙可以通过旋转蜗杆轴调整最适宜的线程确保蜗杆与蜗轮齿配合来减小。拜尔和纂[ 9]讨论了几何型双导程蜗轮蜗杆。先进的数学模型可以用来做接触分析与研究。本文拜尔和纂[ 10 ]提出另外讨论接触牙齿,接触比率和双导程蜗轮蜗杆传动运动误差。它揭示了该型双导程蜗杆蜗轮传动高接触比率。 由于双导程蜗杆齿轮传动主要用于精密机械和导向机构,静态和动态变形接触线程必须减少或限制在可接受的水平。不像其他类型的齿轮带动,蜗杆的线程与蜗轮齿牙的滑动接触在蜗轮蜗杆传动中起重要作用。总之,滑动接触减小的摩擦力是精密蜗杆的设计的一个主要重点。此外,如果驱动器的速度非常低,高摩擦力有时可能导致运动部分发生静摩擦,这反过来将严重影响精密定位性能。因此,用于精密机器的双导程蜗轮蜗杆传动应该优化,降低摩擦力和线程变形量。本文研究动机是设计一个以c轴为回转中心的双导程蜗轮蜗杆传动机构。在铣削操作时,c轴以一个很低的速度旋转;准确定位、平稳旋转的是回转中心c轴关键问题。考虑到C轴需求的,设计的目的是尽量减少之间蜗杆线程与蜗轮齿牙
蜗轮蜗杆传动原理
蜗轮蜗杆传动 蜗轮蜗杆传动用于两轴交叉成90度,但彼此既不平行又不相交的情况下,通常在蜗轮传动中,蜗杆是主动件,而蜗轮是被动件。 蜗轮蜗杆传动有如下特点: 1)结构紧凑、并能获得很大的传动比,一般传动比为7-80。 2) 工作平稳无噪音 3) 传动功率范围大 4)可以自锁 5)传动效率低,蜗轮常需用有色金属制造。蜗杆的螺旋有单头与多头之分。 传动比的计算如下: I=n1/n2=z/K n1-蜗杆的转速 n2-蜗轮的转速 K-蜗杆头数 Z-蜗轮的齿数 蜗轮及蜗杆机构 一、用途: 蜗轮蜗杆机构常用来传递两交错轴之间的运动和动力。蜗轮与蜗杆在其中间平面内相当於齿轮与齿条,蜗杆又与螺杆形状相似。 二、基本参数: 模数m、压力角、蜗杆直径系数q、导程角、蜗杆头数、蜗轮齿数、齿顶高系数(取1)及顶隙系数(取0.2)。其中,模数m和压力角是指蜗杆轴面的模数和压力角,亦即蜗轮轴面的模数和压力角,且均为标准值;蜗杆直径系数q为蜗杆分度圆直径与其模数m的比值, 三、蜗轮蜗杆正确啮合的条件 1 中间平面内蜗杆与蜗轮的模数和压力角分别相等,即蜗轮的端面模数等於蜗杆的轴面模数且为标准值;蜗轮的端面压力角应等於蜗杆的轴面压力角且为标准值,即 ==m ,== 2 当蜗轮蜗杆的交错角为时,还需保证,而且蜗轮与蜗杆螺旋线旋向必须相同。 四、几何尺寸计算与圆柱齿轮基本相同,需注意的几个问题是: 蜗杆导程角()是蜗杆分度圆柱上螺旋线的切线与蜗杆端面之间的夹角,与螺杆螺旋角的关系为,蜗轮的螺旋角,大则传动效率高,当小於啮合齿间当量摩擦角时,机构自锁。 引入蜗杆直径系数q是为了限制蜗轮滚刀的数目,使蜗杆分度圆直径进行了标准化m一定时,q大则大,蜗杆轴的刚度及强度相应增大;一定时,q小则导程角增大,传动效率相应提高。 蜗杆头数推荐值为1、2、4、6,当取小值时,其传动比大,且具有自锁性;当取大值时,传动效率高。 与圆柱齿轮传动不同,蜗杆蜗轮机构传动比不等於,而是,蜗杆蜗轮机构的中心距不等於,而是。 蜗杆蜗轮传动中蜗轮转向的判定方法,可根据啮合点K处方向、方向(平行於螺旋线的切线)及应垂直於蜗轮轴线画速度矢量三角形来判定;也可用「右旋蜗杆左手握,左旋蜗杆右手握,四指拇指」来判定。 五、蜗轮及蜗杆机构的特点 可以得到很大的传动比,比交错轴斜齿轮机构紧凑
蜗轮和蜗杆
蜗杆蜗轮 蜗杆蜗轮用于两交叉轴(交叉角一般为直角)间的传动。通常蜗杆主动,蜗轮从动,用于减速,可获得较大的传动比。 蜗杆蜗轮传动中(图9-60),最常用的蜗杆为圆柱形阿基米德蜗杆。这种蜗杆的轴向齿廓是直线,轴向断面呈等腰梯形,与梯形螺纹相似。蜗杆的齿数称为头数,相当于螺纹的线数,常用单头或双头。 图9-60 蜗杆蜗轮传动 蜗轮相当于斜齿圆柱齿轮,其轮齿分布在圆环面上,使轮齿能包住蜗杆,以改善接触状况,这是蜗轮形体的一个特征。 (一)蜗杆蜗轮的主要参数与尺寸计算 1、齿距p与模数m 在包含蜗杆轴线并垂直于蜗轮轴线的中间平面内(图9-60),蜗杆的轴向齿距p x应与蜗轮的端面齿距P t相等(p x=p t=p),所以蜗杆的轴向模数m x与蜗轮的端面模数m t也相等(m x=m t=m),并规定为标准模数。蜗轮分度圆直径d2、喉圆直径d a2、齿根圆直径d f2均在中间平面内度量。 2、蜗杆直径系数q 蜗杆直径系数是蜗杆特有的一个重要参数,它等于蜗杆的分度圆直径d1与轴向模数m的比值,即 q=d1/m 或d1=mq 对应于不同的标准模数,规定了相应的q值。引入这一系数的目的,主要是为了减少加工刀具的数目。
沿蜗杆分度圆柱面展开,螺旋线展成倾斜 直线,如图9-61所示,斜线与底线间的夹角γ, 称为蜗杆的导程角。当蜗杆直径系数q和头数z1选 定后,导程角丁就惟一确定了。它们之间的关系为 tanγ=p x z1/πd1=πmz1/πm q=z1/q 一对相互啮合的蜗杆和蜗轮,除了模数和齿形 图9-61 蜗杆的导程角角必须分别相同外,蜗杆导程角γ与蜗轮螺旋角卢 应大小相等、旋向相同,即γ=β。 蜗杆与蜗轮各部分尺寸与模数m、蜗杆直径系数q、导程角γ和齿数 z1、z2有关,其具体关系见表9-15。 表9-15 标准蜗杆、蜗轮各部分尺寸计算公式
双导程蜗杆传动
四、双导程蜗杆传动 双导程蜗杆传动具有改变啮合侧隙的特点,能够始终保持正确的啮合关系;并且结构紧凑,调整方便,因而在要求连续精确分度的结构中被采用,以便调整啮合侧隙到最小程度。 双导程蜗杆副啮合原理与一般的蜗杆副啮合原理相同,蜗杆的轴向截面仍相当于基本齿条,蜗轮则相当于同它啮合的齿轮。双导程蜗杆齿的左、右两侧面具有不同的齿距( 导程) 或者说齿的左、右两侧面具有不同的模数m(m=t /π ) ,但同一侧齿距则是相等的,因此,该蜗杆的齿厚从一端到另一端均匀地逐渐增厚或减薄,故又称变齿厚蜗杆,可用轴向移动蜗杆的方法来消除或调整啮合间隙。因为同一侧面齿距相同,没有破坏啮合条件,所以当轴向移动蜗杆后,也能保证良好的啮合。 双导程蜗杆的齿形如图5-36 所示,图中,、分别为蜗杆左、右侧面轴向齿距; 为公称轴向齿矩;、分别为蜗杆左、右侧面齿形角;S 为齿厚;C 为齿槽宽。下面介绍双导程蜗杆传动的特殊参数的选择。 图5-36 双导程蜗杆齿形 1 .公称模数 双导程蜗杆传动的公称模数m 可看成普通蜗杆副的轴向模数,用强度计算方法求得,并选取标准值,它一般等于左、右齿面模数的平均值。 当公称模数确定后,公称齿距也随之而确定。从图5-36 可知 (5-9)
2 .齿厚增量系数 齿厚增量系数值为蜗杆轴向移动单位长度内的轴向齿厚变化量,即 (5-10) 值与m 值一样,是确定其他参数的原始数据,因而在设计中首先要确定值。选择 值时应考虑以下问题: (1) 为了补偿一定的侧隙,蜗杆轴向移动长度与成反比。值大,可使蜗杆轴向尺 寸紧凑;但值过大,则使啮合区过分偏移,同时齿顶变尖,齿槽变窄,从而使蜗轮轮齿 ( 大模数值时) 发生根切,( 小模数值时) 齿顶变尖。而值过小,则会增大传动机构的轴向尺寸。 (2) 值与啮合节点有一定的关系,由图5-37 看出,大模数齿面节点向蜗杆的齿 根方向偏移,而小模数齿面节点向蜗杆的齿顶方向偏移,节点偏移量与的关系为 (5-11) 式中,为蜗轮齿数。
变齿厚蜗杆是普通蜗杆的一种变形
变齿厚蜗杆是普通蜗杆的一种变形,由于左、左两部分的导程不相等,齿厚逐渐变小或变大,利用挂轮增大或减少导程的大小以形成不同齿厚的方法,根据其左、右侧导程Lf和Lr分别计算挂轮的齿数,调整机床分别进行加工,其它操作与普通蜗杆的车削方法基本相同. 双导程蜗轮蜗杆测绘与计算 曹可虎,王立娅,王娟,刘永红 摘要:盘环加工厂高速拉床12″分度盘精度降低,分解后发现蜗轮、蜗杆已磨损。通过测绘、计算,确定了设计参数采用旧件修复,以消除间隙为主的方法,使分度盘恢复定位精度功能。 关键词:双导程蜗轮副;测绘与计算;确定参数 中图分类号:TG57 文献标识码:B 分度盘分度精度的高低主要取决于蜗轮、蜗杆的加工精度和啮合间隙。经长期使用,蜗轮、蜗杆已磨损,精度降低的分度盘,必须对已磨损的蜗轮、蜗杆进行测绘、计算,确定蜗杆类型及设计参数,选用适当的刀具,加工蜗轮,配加工蜗杆,重新调整间隙,以恢复原有精度。 一、双导程蜗轮副的工作原理 双导程蜗轮副与普通蜗轮副的区别是,双导程蜗杆齿的左、右两侧面具有不同的导程,而同一侧的导程则是相等的。因为该蜗杆的齿
厚从蜗杆的一端向另一端均匀地逐渐增厚或减薄,所以双导程蜗杆又称变齿厚蜗杆。故可用轴向移动蜗杆的方法来消除或调整蜗轮副的啮合间隙。 双导程蜗轮副的啮合原理与一般蜗轮副的啮合原理相同。蜗杆的轴向截面相当于基本齿条,蜗轮则相当于与其啮合的齿轮。虽然蜗杆齿左右侧面具有不同的齿距(即不同的模数,),但因同一侧面的齿距相同,故没有破坏啮合条件,当轴向移动蜗杆后,也能保证良好啮合。 二、双导程蜗轮副的特点 1.优点 双导程蜗轮副在具有旋转进给运动或分度运动的数控机床上应用广泛,是因为其具有以下突出优点。 (1)啮合间隙可调整得很小。根据经验,侧隙可调整至 0.01~0.015mm,而普通蜗轮副一般只能达到0.03~0.08mm,再小就容易咬死。因此双导程蜗轮副能在较小的侧隙下工作,对提高数控转台的分度精度非常有利。 (2)普通蜗轮副是以蜗杆作径向移动来调整啮合侧隙,从而改变传动副的中心距,从啮合原理角度看,是不合理的因为改变中心距会引起齿面接触情况变差,甚至加剧磨损,不利于保持蜗轮副的精度。双导程蜗轮副则是用蜗杆轴向移动来调整啮合侧隙,不会改变中心距。 (3)双导程蜗杆是用修磨调整环来控制调整量,调整准确,方便
蜗杆传动(含答案)
蜗杆传动 一、判断题(正确 T ,错误 F ) 1. 两轴线空间交错成90°的蜗杆传动中,蜗杆和蜗轮螺旋方向应相同。 ( ) 2. 蜗杆传动的主平面是指通过蜗轮轴线并垂直于蜗杆轴线的平面。 ( ) 3. 蜗杆的直径系数为蜗杆分度圆直径与蜗杆模数的比值,所以蜗杆分度圆直径越大,其直径系数也 越大。 ( ) 4. 蜗杆传动的强度计算主要是进行蜗轮齿面的接触强度计算。 ( ) 5. 变位蜗杆传动中,是对蜗杆进行变位,而蜗轮不变位。 ( ) 二、单项选择题 1. 与齿轮传动相比,( )不能作为蜗杆传动的优点。 A 传动平稳,噪声小 B 传动比可以较大 C 可产生自锁 D 传动效率高 2. 在标准蜗杆传动中,蜗杆头数一定时,若增大蜗杆直径系数,将使传动效率( )。 A 降低 B 提高 C 不变 D 增大也可能减小 3. 蜗杆直径系数的标准化是为了( )。 A 保证蜗杆有足够的刚度 B 减少加工时蜗轮滚刀的数目 C 提高蜗杆传动的效率 D 减小蜗杆的直径 4. 下列公式中,用( )确定蜗杆传动比的公式是错误的。 A 21ωω>=i B 12z z i >= C 12d d i >= D 21n n i >= 5. 提高蜗杆传动效率的最有效方法是( )。 A 增加蜗杆头数 B 增加直径系数 C 增大模数 D 减小直径系数 三、填空题 1. 在蜗杆传动中,蜗杆头数越少,则传动效率越___________,自锁性越____________。 2. 有一普通圆柱蜗杆传动,已知蜗杆头数21 =z ,蜗杆直径系数8=q ,蜗轮齿数372=z ,模数mm 8=m , 则蜗杆分度圆直径_________________mm ,蜗轮的分度圆直径________________mm ,传动中心距________________mm ,传动比___________,蜗轮分度圆上的螺旋角_____________。 3. 阿基米德蜗杆传动变位的主要目的是为了_____________________和____________________。 四、简答题 1. 蜗杆传动的正确啮合条件是什么? 2. 为何连续工作的闭式蜗杆传动要进行热平衡计算?可采用哪些措施来改善散热条件? 3. 蜗杆传动为什么一般选择钢蜗杆和铜蜗轮作为配对材料? 4. 蜗杆传动的主要失效形式和计算准则? 5. 与齿轮传动相比,蜗杆传动的主要优、缺点有哪些? 五、分析计算题 1. 已知一带式运输机用阿基米德蜗杆传动,传递的功率均kW 8.81=P ,转速m in /r 9601=n ,传 动比18=i ,蜗杆头数21=z ,直径系数8=q ,蜗杆导程角01214'''?=γ,蜗轮端面模数 mm 10=m ,当蜗杆主动时的传动效率88.0=η,蜗杆右旋,转动方向如图所示。 试求:(1)蜗轮的转向及各力指向; (2)计算蜗杆和蜗轮所受个分力的大小。
蜗轮蜗杆-齿轮-齿条的计算及参数汇总
蜗轮蜗杆-齿轮-齿条的计算及参数汇总渐开线齿轮有五个基本参数,它们分别是: 标准齿轮:模数、压力角、齿顶高系数、顶隙系数为标准值,且分度圆上的齿厚等于齿槽宽的渐开线齿轮。 我国规定的标准模数系列表 注:选用模数时,应优先采用第一系列,其次是第二系列,括号内的模数尽可能不用.
系列(1)渐开线圆柱齿轮模数(GB/T 1357-1987)第一系列0.1 0.12 0.15 0.2 0.25 0.3 0.4 0.5 0.6 0.8 1 1.25 1.5 2 2.5 3 4 5 6 8 10 12 16 20 25 32 40 50 第二系列0.35 0.7 0.9 0.75 2.25 2.75 (3.25)3.5 (3.75) 4.5 5.5 ( 6.5)7 9 (11)14 18 22 28 (30)36 45 (2)锥齿轮模数(GB/T 12368-1990) 0.4 0.5 0.6 0.7 0.8 0.9 1 1.125 1.25 1.375 1.5 1.75 2 2.25 2.5 2.75 3 3.25 3.5 3.75 4 4.5 5 5.5 6 6.5 7 8 9 10 11 12 14 16 18 20 22 25 28 30 32 36 40 45 50 注: 1.对于渐开线圆柱斜齿轮是指法向模数。 2.优先选用第一系列,括号内的模数尽可能不用。 3.模数代号是m,单位是mm 名称含有蜗轮的标准 SH/T 0094-91 (1998年确认)蜗轮蜗杆油94KB SJ 1824-81 小模数蜗轮蜗杆优选结构尺寸206KB JB/T 8809-1998 SWL 蜗轮螺杆升降机型式、参数与尺寸520KB JB/T 8361.2-1996 高精度蜗轮滚齿机技术条件206KB JB/T 8361.1-1996 高精度蜗轮滚齿机精度261KB 名称含有蜗杆的标准 SH/T 0094-91 (1998年确认)蜗轮蜗杆油94KB QC/T 620-1999 A型蜗杆传动式软管夹子347KB QC/T 619-1999 B型和C型蜗杆传动式软管夹子83KB GB/T 19935-2005蜗杆传动蜗杆的几何参数-蜗杆装置的铭牌、中心距、用户提供给制造者的参数121KB SJ 1824-81 小模数蜗轮蜗杆优选结构尺寸206KB JB/T 9925.2-1999 蜗杆磨床技术条件160KB JB/T 9925.1-1999 蜗杆磨床精度检验244KB JB/T 9051-1999 平面包络环面蜗杆减速器922KB JB/T 8373-1996 普通磨具蜗杆砂轮250KB JB/T 7936-1999 直廓环面蜗杆减速器731KB JB/T 7935-1999 圆弧圆柱蜗杆减速器467KB JB/T 7848-1995 立式圆弧圆柱蜗杆减速器175KB JB/T 7847-1995 立式锥面包铬圆柱蜗杆减速器203KB JB/T 7008-1993 ZC1型双级蜗杆及齿轮蜗杆减速器548KB JB/T 6387-1992 轴装式圆弧圆柱蜗杆减速器679KB JB/T 5559-1991 锥面包络圆柱蜗杆减速器524KB JB/T 5558-1991 蜗杆减速器加载试验方法96KB JB/T 53662-1999 圆弧圆柱蜗杆减速器产品质量分等274KB JB/T 3993-1999 蜗杆砂轮磨齿机精度检验287KB
双导程蜗杆传动的设计与计算.
离l 为 L, 0 二二二 : L 。‘ 一月 ~ 二, 1 2 , L资 (上式用于右齿面比左齿 味彝… 月面模数大时一尸一‘ ~ ~ , , 上尹代二、闷二子~ 一~ 二》 < 了一诀 : 飞了卜一厂忿夕流、份 \ \ \ \ \ 一二声J ’ 卜鑫~ 一一‘ ’ 勺 . 卜J ‘ . 目月~ . 介 l , 卜、‘ 、一‘‘ 李一 ~ 洲尹立?山一卜J 一一户产口目尸匕 l 刁、一尸尹洲匕一一, 、 . 1 \ \ 一 \ \ 、、_ ‘ 卜 L } } } 图 2 今了‘ 州‘ 寿{ { ’ 、、小双 , , , , , l , 乙‘ = 乙。十百“ ‘ 、闷、气一 (上式用于右齿面比左齿面模数小时 8 . 原始截面处蜗杆法向。 S 夯; , 弦齿厚用近似作图法求蜗杆啮合长度。双导程蜗杆的轴向齿厚沿其轴向测量 , 处处都是不等 (2 计算法 : 的 e , 2 、按下式确定 e , 2 e x : 、 e , : 及 , 少, , 准值 (即一~ 、一’ 而在螺旋长度中点截面处的轴向齿厚取标、 :一、 m 这样在原始截面 0 1 0 2 处。‘ 宜心二心一 , 杯d ja 知 , 二兹敛 ~ 公称分度圆上的轴向齿厚义计算公式(见图 3 一 ~ 要 2 , 一 z 矛~ , ’ 协闪 ~ ~ ~ 、孟‘ , 2 Z co s a 夕 f , o n 7 干△m 气 2 a o a : si n ( 当左齿面为小模数时取负号 , 反之取正号。 , 丫哪 2 2 了心一杯 d乡一d趾 , 2 Z c o s a o a : f 。, n 士△m 2 a o a z Z y ‘ si n 洽乙 ( 当右齿面为大模数时取正号 , , 反之取负号。图 3 蜗杆齿厚计算示意图式中 d o . —— e : 蜗轮左齿面基圆直径 = m 名 2 2 Co s a o a , ; 为 : d 。 , 蜗轮右齿面基圆直径 = m , 么 2 c o s a o a S :1一 n 合 / m 一 ( 合 1 ? L 一‘,K , , 比较 e y: 及 ; , 取大者为 l 二比较 ; e 夕l 因而及e ‘2 , S 夯‘S 二 : , co s 朴 1 二 , 取大者为l ; ’ b . , l。 = 飞十 z zp : : 蕊。〔汀 m 一百乙一“ 八令气少。、‘ , 』Co s 行调整长度 , 当 ; △S △s 按按 0 . 3~ 0 6 . 毫米 , 为便于检查和滚蜗轮时安装滚刀 , 应在蜗 , 选取时 z; = 、m c . l: = △ s , /K z , : 当‘m K , 选取时。杆和滚刀齿顶圆柱上离薄齿端 : 表示义的位置。 l: 处刻一圈线 l: 应加在蜗杆的厚齿端一边推荐 z : 工艺长度 * 二2 汀m 。计算并把 , 9 . a . 验算 l, 值平分后加于 O;O : 的两边蛛小的验算 : 原始截面。: 0 至蜗杆薄齿端端面的距为了便于蜗杆加工 , 需对其厚齿端 最小齿? 75 . 槽底部法向宽度3 ‘ b 最小进行验算 , 。验算公式见表 C。。其特点 是 : 可避免计算加工蜗杆大模数齿面的 , 中第。 38 项 , 公式中径向间隙系数值应不小于 2 ~ : 一般取非标准挂轮的麻烦杆完全一致。而其根切
蜗轮蜗杆计算
蜗轮蜗杆计算 蜗杆传动 当两根轴在90度相交,但它们既不平行也不相交时,采用蜗轮传动。在蜗轮传动中,蜗杆是主动部件,蜗轮是被动部件。蜗轮传动具有以下特点: 1)结构紧凑,可获得较大的传动比,一般传动比为7-80。2)运行稳定,无噪声3)传输功率范围大4)自锁 5)传动效率低,蜗轮蜗杆往往由有色金属制成。蜗杆的螺杆可分为单头螺杆和多头螺杆。传动比计算公式如下:I = N1 / N2 = Z / K N1为蜗杆转速,N2为蜗轮转速,K为蜗杆头数,Z为蜗轮齿数 蜗轮蜗杆机构 1、目的: 蜗轮蜗杆机构通常用于在两根交错轴之间传递运动和动力。蜗轮和蜗杆相当于中间平面上的齿轮和齿条,蜗杆和螺杆的形状相似。\ 二、基本参数: 模数m、压力角、蜗杆直径系数q、导程角、蜗杆头数、蜗轮齿数、齿顶高系数(取1)及顶隙系数(取0.2)。其中,模数m和压力角是指蜗杆轴面的模数和压力角,亦即蜗轮轴面的模数和压力角,且均为标准值;蜗杆直径系数q为蜗杆分度圆直径与其模数m的比值, 三、蜗轮蜗杆正确啮合的条件 1 中间平面内蜗杆与蜗轮的模数和压力角分别相等,即蜗轮的端面模数等於蜗杆的轴面模数且为标准值;蜗轮的端面压力角应等於蜗杆的
轴面压力角且为标准值,即m 2 当蜗轮蜗杆的交错角为时,还需保证,而且蜗轮与蜗杆螺旋线旋向必须相同。 四、几何尺寸计算与圆柱齿轮基本相同,需注意的几个问题是: 蜗杆导程角()是蜗杆分度圆柱上螺旋线的切线与蜗杆端面之间的夹角,与螺杆螺旋角的关系为,蜗轮的螺旋角,大则传动效率高,当小於啮合齿间当量摩擦角时,机构自锁。 引入蜗杆直径系数q是为了限制蜗轮滚刀的数目,使蜗杆分度圆直径进行了标准化m一定时,q大则大,蜗杆轴的刚度及强度相应增大;一定时,q小则导程角增大,传动效率相应提高。 蜗杆头数推荐值为1、2、4、6,当取小值时,其传动比大,且具有自锁性;当取大值时,传动效率高。 与圆柱齿轮传动不同,蜗杆蜗轮机构传动比不等於,而是,蜗杆蜗轮机构的中心距不等於,而是。蜗杆蜗轮传动中蜗轮转向的判定方法,可根据啮合点K处方向、方向(平行於螺旋线的切线)及应垂直於蜗轮轴线画速度矢量三角形来判定;也可用「右旋蜗杆左手握,左旋蜗杆右手握,四指拇指」来判定。 五、蜗轮及蜗杆机构的特点 可以得到很大的传动比,比交错轴斜齿轮机构紧凑 两轮啮合齿面间为线接触,其承载能力大大高於交错轴斜齿轮机构蜗杆传动相当於螺旋传动,为多齿啮合传动,故传动平稳、噪音很小具有自锁性。当蜗杆的导程角小於啮合轮齿间的当量摩擦角时,机构