多级可修备件库存的生灭过程建模与优化

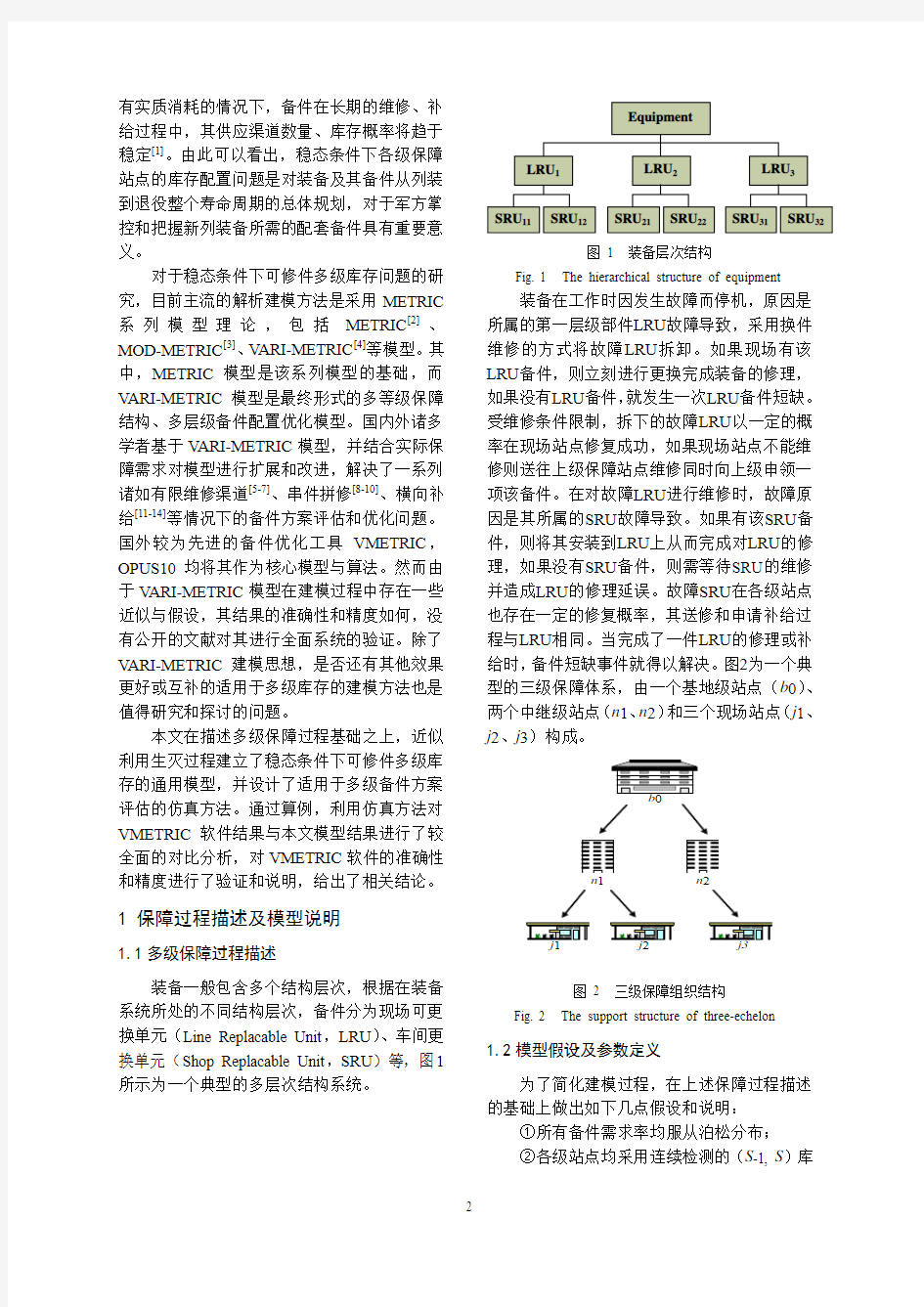
多级可修备件库存的生灭过程建模与优化*
刘任洋1,李华1,李庆民2,熊宏锦3
(1. 海军工程大学 兵器工程系,湖北 武汉 430033;2. 海军工程大学 科研部,湖北 武汉 430033;3. 海军装
备部驻重庆地区军事代表局,重庆 400042 )
摘要:V ARI-METRIC 模型是解决可修备件多级库存建模问题的主流方法,针对该模型在低可用度下结果不准确的问题,建立了基于生灭过程的任意等级任意层级可修件库存优化模型。首先通过各级站点、各类备件需求率与到达率的预测,对每个部件建立其生灭过程模型,并提出基于生灭过程的装备可用度计算方法。而后以整个保障系统的装备可用度为约束指标,以备件总购置费最低为目标,利用边际算法得到最优备件配置方案,并建立了仿真模型对所得优化方案进行评估与调整。最后结合算例,以仿真结果作为检验标准,选取权威的VMETRIC 软件与本文解析模型在优化性能、计算精度及适用性上进行了对比和说明,结果表明:无论解析模型还是VMETRIC 软件均存在一定的适用范围,而采用解析与仿真相结合的方法无疑具有更强的适应性。
关键词:生灭过程;可修复备件;可用度;库存优化;V ARI-METRIC
中图分类号:E911;TJ761.1;V125.7 文献标志码:A 文章编号:
Modeling and optimization of multi-echelon inventory for repairable spares based on birth and death process
LIU Renyang 1, LI Hua 1, LI Qingmin 2, XIONG Hongjin 3
(1. Department of Weaponry Engineering, Naval University of Engineering, Wuhan 430033, China ;2. Office of Research & Development, Naval University of Engineering, Wuhan 430033, China ;3. Military Representative Office of Naval
Equipment Department in Chongqing, Chongqing 400042, China)
Abstract: VARI-METRIC model is the main method to solve the problem of multi-echelon inventory modeling, for it is not accurate under the condition of low availability, the model of inventory optimization for multi-echelon multi-indenture repairable spares is built. Firstly, the birth and death process of each component are established by the prediction of demand rate and arrival rate of each spares in each sites; Then, computational method of availability is put forward based on birth and death process; With constrains of availability and objective of lowest cost, the optimal inventory distribution result is obtained by marginal algorithm and the simulation model is built to evaluate and adjust the result. In actual example, the analytic model and VMETRIC are compared and described in aspects of optimization performance, calculation precision and applicability by simulation verification, the results show that both analytic model and VMETRIC have certain scope of applicability and the method combined analytic model and simulation has stronger applicability.
Keywords: birth and death process; repairable spares; availability; inventory optimization; V ARI-METRIC
*收稿日期:2016-XX-XX
基金项目:国防预研项目基金(51304010206,51327020105)
作者简介:刘任洋(1989-),男,江西南昌人,博士研究生,E-mail :463572090@https://www.360docs.net/doc/5612151687.html, ; 李庆民(通信作者),男,教授,博士,博士生导师,E-mail :licheng001@https://www.360docs.net/doc/5612151687.html,
可修复性备件的配置问题是备件规划工作的重要环节。多级维修供应是较为科学的保障模式,目前国内外各军兵种大都采用该模式。由于装备使用现场的维修条件和备件储备能力有限,因此维修、备件储备及供应等保障活动在各级站点之间协调进行。从装备的全寿命周期角度看,由于可以得到包括工业部门或外部供应商在内的所有保障组织体系的支持,备件在供应过程中一般不存在实质性的消耗,具体表现为顶层站点具备较强的维修能力,能对所有故障件进行完全修复,或即使由于无法修复而报废但能通过采购方式得到补充。在这种没
有实质消耗的情况下,备件在长期的维修、补给过程中,其供应渠道数量、库存概率将趋于稳定[1]。由此可以看出,稳态条件下各级保障站点的库存配置问题是对装备及其备件从列装到退役整个寿命周期的总体规划,对于军方掌控和把握新列装备所需的配套备件具有重要意义。
对于稳态条件下可修件多级库存问题的研究,目前主流的解析建模方法是采用METRIC 系列模型理论,包括METRIC[2]、MOD-METRIC[3]、V ARI-METRIC[4]等模型。其中,METRIC模型是该系列模型的基础,而V ARI-METRIC模型是最终形式的多等级保障结构、多层级备件配置优化模型。国内外诸多学者基于V ARI-METRIC模型,并结合实际保障需求对模型进行扩展和改进,解决了一系列诸如有限维修渠道[5-7]、串件拼修[8-10]、横向补给[11-14]等情况下的备件方案评估和优化问题。国外较为先进的备件优化工具VMETRIC,OPUS10均将其作为核心模型与算法。然而由于V ARI-METRIC模型在建模过程中存在一些近似与假设,其结果的准确性和精度如何,没有公开的文献对其进行全面系统的验证。除了V ARI-METRIC建模思想,是否还有其他效果更好或互补的适用于多级库存的建模方法也是值得研究和探讨的问题。
本文在描述多级保障过程基础之上,近似利用生灭过程建立了稳态条件下可修件多级库存的通用模型,并设计了适用于多级备件方案评估的仿真方法。通过算例,利用仿真方法对VMETRIC软件结果与本文模型结果进行了较全面的对比分析,对VMETRIC软件的准确性和精度进行了验证和说明,给出了相关结论。
1 保障过程描述及模型说明
1.1多级保障过程描述
装备一般包含多个结构层次,根据在装备系统所处的不同结构层次,备件分为现场可更换单元(Line Replacable Unit,LRU)、车间更换单元(Shop Replacable Unit,SRU)等,图1所示为一个典型的多层次结构系统。
图 1 装备层次结构
Fig. 1 The hierarchical structure of equipment
装备在工作时因发生故障而停机,原因是所属的第一层级部件LRU故障导致,采用换件维修的方式将故障LRU拆卸。如果现场有该LRU备件,则立刻进行更换完成装备的修理,如果没有LRU备件,就发生一次LRU备件短缺。受维修条件限制,拆下的故障LRU以一定的概率在现场站点修复成功,如果现场站点不能维修则送往上级保障站点维修同时向上级申领一项该备件。在对故障LRU进行维修时,故障原因是其所属的SRU故障导致。如果有该SRU备件,则将其安装到LRU上从而完成对LRU的修理,如果没有SRU备件,则需等待SRU的维修并造成LRU的修理延误。故障SRU在各级站点也存在一定的修复概率,其送修和申请补给过
程与LRU相同。当完成了一件LRU的修理或补给时,备件短缺事件就得以解决。图2为一个典型的三级保障体系,由一个基地级站点(b0)、两个中继级站点(n1、n
2)和三个现场站点(j1、j2、j3)构成。
图 2 三级保障组织结构
Fig. 2 The support structure of three-echelon
1.2模型假设及参数定义
为了简化建模过程,在上述保障过程描述的基础上做出如下几点假设和说明:
①所有备件需求率均服从泊松分布;
②各级站点均采用连续检测的(S-1, S)库
存策略,即缺少一件就向上级申请一件;
③各级站点维修时间服从指数分布,维修渠道无限,不考虑故障单元之间的维修优先权,不考虑重测完好率、虚警率等维修参数的影响;
④LRU 的故障只是由于其所属SRU 之一故障所致,不考虑多个SRU 同时故障的情况;
⑤顶层站点具有较强的修复能力,能对所有故障件进行完全维修,不考虑报废问题;
⑥部署于现场站点的多台同型装备之间为独立关系,工作时相互不受影响;装备中同一层级部件之间为串联关系。
模型相关参数定义如下:
j :保障站点编号,j =1,2,…,J ,J 表示保障站点总数;
h :站点级别编号,h =1,2,…,H ,h =1表示顶层站点,h =H 表示底层站点(舰员级),h =2,3,…,H -1表示处于中间级别站点;
Echelon (h ):处于第h 个级别的站点集合; Unit (j ):站点j 保障的所有下一级别站点集合;
Sup (j ):站点j 的上级站点;
i :部件项目编号,i =1,2,…,I ,I 表示部件类型总数;
c :部件层级编号,c =0,1,…,C ,c=0表示装备系统,c=1表示第一层级部件LRU ,c=C 表示处于装备中最底层部件;c =2,3,…,C -1表示处于中间结构层级部件;
Inden (c ):在装备结构中处于第c 层次的项目集合;
Sub (i ):部件i 所属下一层级的分组件集合; Aub (i ):部件i 上面所有层级的母体集合; MTBF i :部件i 的平均故障间隔时间; q iz :部件i 发生故障是由于其所属子部件z 故障导致的条件概率(z ∈Sub (i ));
S ij :站点j 第i 项备件的库存量;
Td ij :站点j 第i 项备件的平均短缺时间; EBO ij :站点j 第i 项备件的期望短缺数;
ij λ:单装备下站点j 第i 项备件的需求率;
ij μ:单维修渠道下站点j 第i 项备件的到达
率;
ij S
P :站点j 第i 项备件库存量为S 时的稳态
概率;
T ij :部件i 在站点j 的平均维修时间; r ij :部件i 在站点j 的维修概率;
O ij :站点j 第i 项备件的补给运输时间; Z i :部件i 在其母体中的单机安装数量; i τ:备件i 的单价;
M j :装备的站点j 的部署数量;
HD j :装备在站点j 平均天工作时间; A j :站点j 的装备可用度;
2 基于近似生灭过程的多级稳态库存建模
2.1可修件的生灭过程模型
生灭过程是更新过程的一种特例,其特征是:在很短的时间内,处于状态s 的系统只能转移到状态s +1或s -1或保持不变[15]。其中,系统从状态s 转移到状态s -1的概率称为死亡率;系统从状态s 转移到状态s -1称为出生率。如果将备件的现有库存数量S 定义为系统的状态,假设维修渠道无限,就能建立可修件的生灭过程模型。由于考虑各装备之间为独立关系,现场站点的备件库存数量最低为-M (短缺M 件),其生灭过程模型如图3所示。-1,…, -M 均为缺件状态,也表示装备停机数量。λ为单装备下的备件需求率,μ为单维修渠道下的备件到达率。对于单站点,备件到达即指故障件修复成功;对于多级站点,备件到达除了指本站点故障件修复成功外,还应包括上级站点备件的补给成功。
……
0000图 3 可修件的生灭过程模型
Fig. 3 The birth and death process model for repairable
spares
定义S P 表示库存数量为S 的稳态概率,可列出生灭过程的状态转移方程:
001S S M P P λμ-= (1)
00011()(1)S k S k S k M k P M P k P λμλμ--+--+=++
01,2,...,k S = (2)
()0
0011
(+)(++1)(1)S k S k S k M k S k P M k S P k P λμλμ--+---+=-++
00+1,...,+k S S M = (3)
10()M M P S M P λμ-+-=+ (4)
结合正则条件
1S S S M
P =-=∑
求解上述方程,
可以得到系统在任意库存量下的稳态概率:
000001
1(1)120()(1)!1!!()!S S M S k k S k k k k S M M M P k k M S k λλμμ-+++==+??-=++ ? ?--??
∑∑
(5)
0000
0(1)
000()1,2,...,1!(1)!2,...,!()!k
S k
S k
S k
S k M P k S k P M M P k S S M
k M S k λμλμ-+? =+??
=?-? =++?--?
(6)
则期望备件短缺数为:
1M
k M
k EBO kP --==∑ (7)
以上建模过程均针对现场站点(底层站点)的备件,对于上级站点,其生灭过程的缺件状态数为该站点所属下级站点的缺件数之和。通过以上分析,对于任意级别站点的任意层级部件,如果可以求得单装备备件需求率λ和单维修渠道下的备件到达率μ,则可利用生灭过程建立稳态条件下的多级库存模型。然而需要指出的是,生灭过程的应用条件为出生率和死亡率均服从泊松分布,由于假设部件寿命和维修时间均服从指数分布,因此对于单部件而言,其严格满足生灭过程的应用条件,而对于多等级、多层级部件,由于需考虑运输时间、维修延误等因素影响,其出生率(备件到达率)不再服从泊松分布。故本文利用生灭过程建模为一种近似方法。 2.2备件需求率预测
备件需求率的计算需要综合考虑保障站点的级别和备件所处的结构层次。不考虑重测完好率、虚警率等维修参数的影响,对于底层站点j 的顶层部件LRU i ((),(1))j Echelon H i Inden ∈∈,其备件需求率为:
24j i ij i
HD Z MTBF λ=
? (8)
对于其它层级部件i ((1))i Inden ?,需求由维修其母体组件(())l l Aub i ∈产生。在所有需要维修的母体组件l 中,只有一部分比例li q 会产生对i 的需求,则底层站点j 对备件i ((),(1))j Echelon H i Inden ∈?的需求率为:
ij lj l li j q r λλ= (9)
其中,由维修母体组件l 产生对i 的需求的
概率li q 可根据平均故障间隔时间计算得到:
l li i MTBF q MTBF = (10) 对于其它等级站点j (())j Echelon H ?,顶层部件LRU i ((1))i Inden ∈的需求由j 所属的下一级别站点(())d d Unit j ∈因无法维修故障件i 而需要向j 送修和申领备件产生,则有:
()
ij id id d Unit j r λλ∈=
?∑
(11)
对于站点j 的其它层级备件
i ((),(1))j Echelon H i Inden ??,需求除了下级站点对备件i 的申领外,还需考虑对其母体l 维修时产生的对i 的需求:
()
()
ij id id lj lj d Unit i i j l Au l b r q r λλλ∈∈=
?+
∑
∑
(12)
由此,按照(8)~(12)式逐项递推计算可以得到整个保障体系中各级站点各项备件的需求率,其中站点递推从底层开始,备件递推从顶层开始。
2.3备件到达率预测
对于单站点单层级部件而言,备件到达率仅与故障件的维修时间有关;当部件扩展为多层级时,备件到达率除了考虑故障件的维修时间外,还需考虑由于缺少子备件而产生的维修延误时间;当保障站点扩展为多等级时,备件到达率则还需考虑上级站点的补给时间和补给延误时间。因此,与备件需求率类似,备件到达率的计算也需考虑保障站点的级别以及备件所处的结构层次。但与备件需求率不同的是,备件到达率的递推计算过程由顶层站点的底层部件开始。
对于顶层站点j 的底层部件i ((1),())j Echelon i Inden C ∈∈,由于始终能修复成功,其备件到达率为:
1
ij ij
T μ=
(13)
对于其它
层级部件
i ((1),())j Echelon i Inden C ∈?,除了自身的维修外,还需考虑由于缺少子备件而产生的维修延误,备件到达率为:
()
1
ij ij iz zj
z Sub i T q Td μ∈=
+
?∑
(14)
(1/)
zj
zj zj zj j EBO Td EBO M λ=
- (15)
式(15)分母项因子(1/)zj j EBO M -为需求率zj λ的修正因子。因为由2.2节计算得到的备件需求率是在装备持续正常工作下的需求率,而实际上当备件发生短缺而导致装备停机时,在停机期间备件需求不会发生。故以(1/)zj zj j EBO M λ-代替
zj λ作为对需求率的修正,后文均按此法处理。
对于非顶层站点j ((1))j Echelon ?,部件以ij
r 的概率在本站点修复成功,以(1)ij r -的概率由上级站点u (())u Sup j ∈完成补给,因此,对于底层备件(())i Inden C ∈,其到达率为:
1
(1)()
ij ij ij ij ij iu r T r O Td μ=
+-+ (16)
()
(1/
)
iu
iu iu iu j j Unit u EBO Td EBO M λ∈=
-∑
(17)
iu Td 为备件i 在上级站点u 的平均短缺时间,视为
对站点j 的补给延误。
对于其它层级备件i ((1),())j Echelon i Inden C ??,其到达率为:
()
1
(1)()
ij ij ij ij ij iu iz zj z Sub i r T r O Td q Td μ∈=
+-++
?∑
(18)
2.4装备可用度的计算
通过备件需求率、到达率的预测及生灭过程建模,最终得到底层站点j (())j Echelon H ∈顶层LRU i ((1))i Inden ∈的期望短缺数:
1j
M ij
ij k k EBO k P -==∑ (19)
V ARI-METRIC 模型在求出LRU 的期望短缺数(可用度)后,直接利用各LRU 可用度的乘积计算装备可用度,这将导致结果偏小。本
节对装备再次利用生灭过程建模,如图4所示,由于装备不配备件,因此对装备的建模包含(M j +1)个状态:0代表所有装备正常工作,-1代表有一台装备停机,-M j 代表所有M j 台装备均停机。其需求率0j μ和到达率0j λ分别为:
00(1)
ij
j i
i Inden ij
EBO q μλ∈=
∑
(20)
0(1)
j ij i Inden λλ∈=
∑
(21)
……
0(j j 0j
-1
0j 0j
0j j
j
M -
图 4 装备的生灭过程模型
Fig. 4 The birth and death process model for equipment
则现场站点j (())j Echelon H ∈的装备可用度为:
0011/1()/j
M j
j j j j k k A EBO M k M P -==-=-∑ (22)
从而整个保障系统的可用度为:
()
()
j j
j j Echelon H j Echelon H A M A M ∈∈=
∑
∑
(23)
3 库存优化模型与算法
对于长期稳态下的备件配置问题,建立优化模型时一般以规定的保障效能指标(如装备可用度、备件满足率等)为约束条件,以寻求整个保障体系内备件总费用的最低值。本文选取部队常用的可用度作为保障效能指标,数学模型如下[16]:
0min ..
i ij j i S s t A A τ????≥?∑∑ (24) 边际分析法是求解上述模型的常用方法,其操作简单,运算效率高,迭代过程中通过对增加单项备件导致的成本增量和收益增量进行综合分析以选择效益最高的备件项目。具体步骤如下:
步骤1:构造I 行J 列备件方案矩阵S ,并令=S 0;
步骤2:计算站点j 第i 项备件的边际效应值:
((,))()
(,)i
A i j A i j δτ+-=
S ones S (25)
(,)i j ones 表示第i 行第j 列元素为1,其余元素全
为0的矩阵;()A S 表示备件方案S 下的装备可用度;
步骤3:将(,)i j δ值最大者所对应的站点j max 上的备件i max 库存量加1,由此得到新的库存量矩阵max max (,)i j =+S S ones ;
步骤4:计算在新库存方案S 下的装备可用度A ,并与规定的可用度指标0A 比较,如果0A A ≥,算法结束,此时的S 即为最优库存配置结果;反之则转入步骤2继续迭代。
4 仿真算法设计
采用MATLAB 平台构造仿真模型对多等级多层级下的备件方案进行评估。仿真采用事件调度法,以故障发生作为原始驱动事件,由此引发后续一系列的维修、更换活动。由于故障发生后是否有备件更换取决于之前的故障维修情况,因此,采用与实际维修保障活动相反的事件顺序进行建模。对于多层级装备,建模顺序为:底层故障件的维修→底层备件数量更新→底层故障件的更换/上层故障件的维修→上层备件数量更新→上层故障件的更换→……直至顶层故障LRU 的更换。对于多等级保障组织,如果故障件最终在顶层站点修复成功,建模顺序为:顶层站点故障件的维修→顶层站点备件数量更新→顶层站点备件下拨/下级站点备件数量更新→下级站点备件下拨→……直至底层站点备件数量更新和故障件的更换。
图 5 单次仿真主流程
Fig. 5 The main simulation process of single time
为了便于描述,以装备包含LRU 、SRU ,保障体系为三等级结构为例,对仿真模型进行说明。其主流程如图5所示,包括库存信息模块、故障LRU 的现场维修模块、故障LRU 的中继级维修模块、故障LRU 的基地级维修模块、统计模块和故障时刻更新模块。为了保证模型进入稳态和仿真结果的稳定性,保障周期T 和仿真次数取值应足够大。当一次仿真结束后,Td 中储存了每个装备的累积停机时间_sys i Td ,则各装备可用度为__1/sys i sys i A Td T =-,现场站点j 的可用度为站点所部署装备可用度的平均值:
_j sys i j i
A A =∑ (25)
整个保障系统的可用度计算方法同(23)式。
5 算例分析
5.1案例想定与结果分析
假设由图2所示的三级保障体系,对飞机上的某型装备开展维修供应保障,现要求制定
各级站点的备件配置方案使整个保障系统的装备可用度值不低于0.95。装备的组成结构如图1所示。装备在三个现场站点的配备数量分别为2、2、3,平均每天工作时间均为12小时。中继级站点至三个现场站点的补给运输时间分
别为4天、5天、6天,基地级站点至两个中继级站点的补给运输时间分别为8天、10天。备件及站点的相关可靠性、维修性等参数如表1所示。
表 1 备件输入参数
Table 1 Input parameters of the spare parts
Item
MTBF i /(h)
Z i
i
/(ten thousand)
T ij 1 /(d) T ij 2 /(d) T ij 3 /(d) T in 1 /(d) T in 2 /(d) T ib 0 /(d) r ij 1 r ij 2 r ij 3 r in 1 r in2 r ib 0 LRU 1 682.7 1 15 5 5 5 8 8 10 0.45 0.45 0.45 0.65 0.65 1 LRU 2 333.3 1 20 8 8 8 10 10 12 0.60 0.60 0.60 0.70 0.70 1 LRU 3 600 1 30 7 7 7 9 9 11 0.55 0.55 0.55 0.75 0.75 1 SRU 11 2200 2 4 4 4 4 7 7 10 0.30 0.30 0.30 0.55 0.55 1 SRU 12 1800 1 7 5 5 5 6 6 9 0.40 0.40 0.40 0.60 0.60 1 SRU 21 1500 2 5.5 7 7 7 10 10 12 0.35 0.35 0.35 0.50 0.50 1 SRU 22 1200 2 4.5 6 6 6 9 9 10 0.45 0.45 0.45 0.65 0.65 1 SRU 31 2000 2 10 3 3 3 5 5 8 0.20 0.20 0.20 0.45 0.45 1 SRU 32
3000
2 5
5
5
5
7
7
9
0.25
0.25
0.25
0.50
0.50
1
边际算法历经43次迭代,得到最优备件配置方案,如表2所示,迭代曲线如图6所示,此时的总购置费用C =547.5万元,整个保障系统的装备可用度A =0.9506。从该备件方案可以看出:现场站点配备的LRU 数量较多而SRU 数量较少;基地级站点配备的LRU 数量较少而SRU 数量较多;中继级站点配备的LRU 、SRU 数量则居于现场站点和基地站点之间。由此可知,模型所得备件方案符合多级保障模式下的备件配置规律。
备件总购置费用(万元)
装备可用度
图 6 边际算法迭代曲线
Fig. 6 The iterative curve by using marginal
algorithm 表 2 最优配置方案
Table 2 The optimization result of spare parts
configuration
Item b 0 n 1 n 2 j 1 j 2 j 3 LRU 1 0 1 0 1 1 3 LRU 2 0 1 1 2 2 3 LRU 3 0 1 0 1 1 2 SRU 11 1 1 1 0 1 0 SRU 12 1 0 0 0 0 0 SRU 21 1 1 1 0 1 1 SRU 22 1 1 1 1 1 1 SRU 31 1 1 0 0 0 1 SRU 32
1
1
1
1
将最优备件方案输入仿真模型,得到各现场站点和整个保障系统的装备可用度结果如表3所示,表中加入了解析模型的结果进行对比。从表中可以看出,解析模型的计算结果比仿真模型略微偏高,但误差均在合理的范围内,产生误差的原因是在多级保障模式下,备件到达率并没有严格的满足生灭过程的使用条件,因此利用生灭过程建模是一种近似方法,但从算例结果看,该近似方法合理有效,所得的备件优化方案基本能满足保障要求。另外,通过大量算例表明:本节算例中解析模型的结果偏高并非个例,而是一种普遍现象(详见5.2节)。
表 3 解析模型与仿真模型的可用度结果对比 Table 3 The contrast of availability between analytic
model and simulation
Availability A j1A j2A j3 A Analytic model 0.9366 0.9387 0.9679 0.9506 Simulation 0.9140 0.9181 0.9450 0.9258 Relative error 2.47% 2.24% 2.42% 2.68% 为了进一步提高保障的精确性,可采取解析与仿真相结合的方法对优化方案进行调整。由于解析模型对可用度的评估结果偏高,调整方法为适当增加边际算法的可用度指标值,使边际算法在初次所得优化方案的基础上继续迭代计算从而得到新的优化方案,并利用仿真模型检验其是否达到原始可用度指标要求,若不满足还可继续调整迭代直到满足为止。这样可通过若干次微调得到更为精准和满意的结果。例如,算例中优化方案的仿真可用度评估结果为0.9285,与0.95的指标要求仍存在近0.02的差距,将边际算法中的可用度指标值增加0.02(设为0.97),使边际算法在原备件方案基础上历经6次迭代,得到新的优化方案如表4所示。经过仿真模型验证,该方案的“真实”可用度结果为0.9535,达到了0.95的指标要求,则该方案为调整后的最终备件方案,此时的总购置费增加至623万元。
表4调整后的最优配置方案
Table 4 The optimization result of spare parts
configuration after adjustment
Item b0n1n2j1j2j3 LRU10 1 0 2 2 3 LRU20 1 1 2 2 3 LRU30 1 0 1 1 3 SRU11 1 1 1 0 1 0 SRU12 1 0 0 0 0 0 SRU21 1 1 1 1 1 1 SRU22 1 1 1 1 1 1 SRU31 1 1 0 0 0 1 SRU32 1 1 1 1 1 1 5.2 VMETRIC软件的验证与对比分析
VMETRIC[16]是美国TFD公司开发的多等级多层级备件优化工具,该软件以V ARI-METRIC模型为基本内核,可以实现对多个维修供应等级、多个层次备件配置方案的优化,曾多次用于美国各军兵种的装备采办、保障性分析、维修保障方案决策等,具有一定的权威性。本节利用仿真模型对VMETRIC软件和本文解析模型进行综合对比分析,对VMETRIC软件的准确性和精度进行验证和讨论。
5.2.1优化性能对比分析
以5.1节中的案例为例,在VMETRIC软件中建立相关模型和想定。将可用度上限设为0.98,分别利用本文解析模型与VMETRIC软件进行计算,得到的可用度迭代曲线如图7所示。从图中可以看出,在可用度不高的迭代前期,两条曲线的差异较大。特别的,在迭代起始点,当备件费用为0时(不配备件),本文模型的可用度计算结果为0.34,而VMETRIC软件的结果为0.02。但在迭代后期,当备件费用超过400万元、可用度大于0.8后两者结果逐渐接近,最终在费用为700万元左右时,迭代相继结束,达到0.98的规定指标值。
备件总购置费用(万元)
装
备
可
用
度
(a) Analytic model
(b)VMETRIC
图7 本文解析模型与VMETRIC软件的可用度迭代
曲线对比
Fig.7 The contrast of iterative curve for availability
between analytic model and VMETRIC
由于与VMETRIC软件结果存在明显的差异,分别选取两条曲线上可用度迭代值达到0.4、0.6、0.9、0.98的备件优化方案输入仿真模型进行评估和验证,所得结果如表5~8所示。表中加入了利用仿真模型对解析模型修正后的结果(解析-仿真模型)。从表中结果可以看出:1)在可用度较低时(0.4、0.6),VMETRIC 软件与仿真结果差异很大,最大相对误差为27.06%,具有极强的保守性;而解析模型的相对误差较小,最大值为3.83%;
2)在可用度较高时(0.9、0.98),VMETRIC 软件和解析模型的误差均在合理范围内,但VMETRIC软件的误差无疑更小,优化性能强于解析模型。
3)采用仿真模型对解析模型进行修正的方法可以得到比VMETRIC软件更符合指标要求的结果,且能找到费效比更优的备件方案。如当A0 = 0.9时,本文模型计算得到的备件方案以498万元的费用使可用度达到0.9038,而VMETRIC的备件方案在500万元更多耗费的情况下其可用度仅为0.8933。
由此可以看出,VMETRIC软件在高可用度时(0.8以上)计算结果精确,而在低可用度下计算结果明显偏低,并不能对备件方案进行准确的定量评估。究其原因,是VMETRIC软件的核心算法——VARI-METRIC模型导致,因为V ARI-METRIC模型算法中存在两个关键近似:一是用各LRU可用度的乘积去计算装备可用度,将导致结果偏低;二是对需求率的计算没有考虑装备停机时的影响(装备钝化)使需求率的估计比实际偏高,也将导致可用度结果偏低。以上两个因素在可用度较高时,影响微乎其微,而当可用度逐渐降低时,影响会越来越明显。这与算例结果完全吻合。尽管如此,但从实际使用的角度,由于保障人员关心的一般是高可用度指标下的备件方案,在此情况下,VMETRIC不失为一款实用、优化性能优良、计算结果精确的软件。而本文解析模型在此案例中不论对于低可用度还是高可用度,其计算结果与仿真评估值相差均在4%以内,因此可以对任意备件方案下的可用度进行较准确的评估。
表5A0=0.4时各模型方法对比
Table 5 The contrast of results among different
methods when A0=0.4
Method
Analytic
model
Analytic-
Simulation
VMETRIC Computing
result
0.4177 0.4030 0.4094 Simulation
evaluation
0.4030 —0.5613 Relative error 3.65% —27.06% Total cost 48 48 167
表6A0=0.6时各模型结果对比
Table 6 The contrast of results among different
methods when A0=0.6
Method
Analytic
model
Analytic-
Simulation
VMETRIC Computing
result
0.6126 0.6001 0.6198 Simulation
evaluation
0.5900 —0.6933 Relative error 3.83% —10.60% Total cost 184 189 274
表7A0=0.9时各模型方法对比
Table 7 The contrast of results among different
methods when A0=0.9
Method
Analytic
model
Analytic-
Simulation
VMETRIC Computing
result
0.9011 0.9038 0.9101 Simulation
evaluation
0.8788 —0.8933 Relative error 2.54% — 1.88% Total cost 442.5 498 500 表8A0=0.98时各模型方法对比
Table 8 The contrast of results among different
methods when A0=0.98
Method
Analytic
model
Analytic-
Simulation
VMETRIC Computing
result
0.9823 0.9801 0.9817 Simulation
evaluation
0.9703 —0.9706 Relative error 1.24% — 1.14% Total cost 683 737 723 5.2.1参数对模型精度的影响分析
为了更全面了解模型的适应性,本节通过改变典型的输入参数值,分析它们对VMETRIC
软件和本文解析模型精度的影响。
(一)维修时间对模型精度的影响分析
仅以LRU在现场站点的维修时间为例,在5.1节的案例想定中保持其它参数不变,将所有现场站点LRU的维修时间T LRU分别均设为5、10、15、20、25、30天,在表4所示的备件方案下利用VMETRIC软件、解析模型、仿真模型对可用度进行评估计算,所得结果如表9所示。从表中可以看出,在一定区间内随着LRU维修时间的增加,VMETRIC软件误差逐渐增大,而解析模型误差反而逐渐减小。这是因为解析模型是近似利用生灭过程建模,由于仅假设维修时间服从指数分布,因此实际备件到达时间并不服从指数分布。而当维修时间较长,维修时间对备件到达时间的影响会更大,使备件到达时间更贴近指数分布,从而使生灭过程建模产生的误差更小。其他站点的其他部件其维修时间的影响与此相同,不再举例。
表9不同维修时间下各模型的可用度结果对比Table 9 The contrast of availability among models with different maintenance time
Method Analytic
model
Simulation VMETRIC
T LRU=5d 0.9792 0.9635 0.9739
T LRU=10d 0.9601 0.9421 0.9494
T LRU=15d 0.9349 0.9204 0.9145
T LRU=20d 0.9047 0.8917 0.8692
T LRU=25d 0.8710 0.8646 0.8140
T LRU=30d 0.8356 0.8352 0.7499 (二)运输时间对模型精度的影响分析
仅以中继级站点对现场站点的运输时间为例,在5.1节的案例想定中保持其它参数不变,将所有中继级站点至现场站点的运输时间O分别均设为5、10、15、20、25、30天,在表4所示的备件方案下利用VMETRIC软件、解析模型、仿真模型对可用度进行评估计算,所得结果如表10所示。从表中可以看出,在一定区间范围内当运输时间增大时,VMETRIC软件误差较小,而解析模型误差越来越大。这是因为运输时间也是备件到达时间的重要决定部分,由于假设其为常数,并非指数分布,因此运输时间越大,运输时间对备件到达时间的影响会更大,使备件到达时间与指数分布的贴近度较低,从而使生灭过程建模产生的误差更大。其他站点运输时间的影响与此相同,不再举例。表10不同运输时间下各模型的可用度结果对比Table 10 The contrast of availability among models with different transportation time
Method Analytic
model
Simulation VMETRIC
O=5d 0.9698 0.9529 0.9661
O=10d 0.9402 0.9166 0.9354
O=15d 0.9070 0.8733 0.8930
O=20d 0.8681 0.8265 0.8387
O=25d 0.8339 0.7813 0.7735
O=30d 0.8036 0.7436 0.6985
6 结论
本文针对长期稳态下可修件的多级配置优化问题进行研究,建立了基于近似生灭过程的多级备件解析优化模型和仿真评估模型。利用仿真评估模型对VMETRIC软件和解析模型在优化性能、评估精度以及适用性方面进行了较全面的对比分析与验证。所得结论如下:1)无论是本文解析模型还是VMETRIC 软件,在建模过程中采取了一些近似处理手段,因此均无法保证在任何情况下都能得到精确甚至是正确的结果。具体表现为:VMETRIC在高可用度时(0.8以上)计算结果精确,而在低可用度或维修时间过长时计算结果明显偏低,并不能对备件方案进行准确的定量评估;本文解析模型在运输时间相对较短(低于各部件平均故障间隔时间的最小值)或维修时间相对较长时,基本能保证结果的准确性(误差在4%以内),但当运输时间过长时,也无法对备件方案进行准确的定量评估。
2)虽然仿真模型结果更精确可信,但面对大批量备件的优化计算时,耗时将不可估量。因此,首先通过解析模型快速计算初始优化方案,再利用仿真模型对初始优化方案实施评估和调整从而得到最终优化方案(本文解析-仿真模型)无疑是更好的选择。
参考文献(References)
[1]Ruan M Z, Luo Y, Li H. Configuration model of
partial repairable spares under batching ordering policy on inventory state[J]. Chinese Journal of Aeronautics, 2014, 27(3): 558-567.
[2]Sherbrooke C C. METRIC: A multi-echelon
technique for recoverable item control[J]. Operations
Research, 1968, 16(2): 122-141.
[3]Muckstadt J. A model for a multi-item,
multi-echelon, multi-indenture inventory system[J].
Management Science, 1973(20): 472-481.
[4]Sherbrooke, C C. V ARI-METRIC: Improved
approximations for multi-indenture multi-echelon
availability models[J]. Operations Research,
1986(34): 311-319.
[5]Sleptchenko A, van der Heijden M C, van Harten A.
Using repair priorities to reduce stock investment in
spare part networks[J]. European Journal Of
Operational Research, 2005, 163(3): 733-750.
[6]Adan I J B F, Sleptchenko A, van Houtum G J.
Reducing cost of spare parts supply system via static
priorites[J]. Asia-Pacific Journal of Operational
Research, 2009, 26(4): 559-585.
[7]van der Heijden M C, Alvarez E M, Schutten J M J.
Inventory reduction in spare part networks by
selective throughput time reduction[J]. Int. J.
Production Economics, 2013, 143(8): 509-517. [8]Salman S, Cassady C R, Pohl E A, et al. Evaluating
the Impact of Cannibalization on Fleet
Performance[J]. Quality and Reliability Engineering
International, 2007, 23(4): 445-457.
[9]李羚伟, 张建军, 张涛, 等. 面向任务的拼修策略
问题及其求解算法[J]. 系统工程理论与实践, 2009, 29(7): 97-104.
Li L W, Zhang J J, Zhang T, et al. Mission oriented
cannibalization policy problem and its solving
algorithm[J]. Systems Engineering-Theory &
Practice, 2009, 29(7): 97-104. (in Chinese)
[10]罗祎, 阮旻智, 李庆民. 多级维修供应下不完全串
件系统可用度评估[J]. 系统工程与电子技术, 2012, 34(6): 1182-1186.
Luo Y, Ruan M Z, Li Q M. Evaluation of availability
for incomplete cannibalization system under
multi-echelon maintenance supply[J]. Systems
Engineering and Electronics, 2012, 34(6): 1182-1186.
(in Chinese)
[11]Olsson F. An inventory model with unidirectional
lateral transshipments[J]. European Journal of
Operations Research, 2010, 200: 725-732.
[12]Lorenzo T, Stefano S. Reducing the mean supply
delay of spare parts using lateral transshipments
policies[J]. Int J Production Economics, 2011, 133:
182-191.
[13]刘任洋, 李庆民, 李华. 基于横向转运策略的可修
件三级库存优化模型[J]. 航空学报, 2014, 35(12):
3341-3349.
Liu R Y, Li Q M, Li H. Optimal model of
three-echelon inventory for repairable spare parts
with lateral transshipments[J]. Acta Aeronautica et
Astronautica Sinica, 2014, 35(12): 3341-3349. (in
Chinese)
[14]刘任洋, 黎放, 李庆民, 等. 基于横向转运策略的
不完全修复件库存配置与订购模型[J]. 航空学报,
2015, 35(6): 1964-1974.
Liu R Y, Li F, Li Q M, et al. Modeling for inventory
distribution and ordering of imperfect repairable
spare parts with lateral transshipments[J]. Acta
Aeronautica et Astronautica Sinica, 2015, 35(6):
1964-1974. (in Chinese)
[15]任敏, 陈全庆, 沈震, 等. 备件供应学[M]. 北京:
国防工业出版社, 2013.
Ren M, Cheng Q Q, Shen Z, et al. The supplying of
the spare parts[M]. Beijing: National Defense
Industry Press, 2013. (in Chinese)
[16]Sherbrooke C C. Optimal Inventory Modeling of
System: Multi-Echelon Techniques[M]. 2nd ed.
Boston: Artech House, 2004.
备品备件仓库
备品备件仓库 管理及流程鉴于河北五鑫花园制品有限公司管理和生产的需要,K3 财务管理软件中, 原材料仓库项下的备品备件仓库从中剥离出来,新增仓库一个,名称:备品备件仓库、代码为20。新仓库实行以实物入账的方法,做到账实相符。五鑫和鑫盛两个公司中所有备品备件物料的长代码统 该仓库流程如下: (1)入库;外部采购金额在200元以下凭采购部长签字入库,200 元以上凭采购主管经理签字、超500元以上须总经理批准的采购申请单入库,1000 元以上采购凭采购合同入库,粉末类凭采购单入库。供应商送货单中货物必须书写物料代码,方可入库;质检员检验货物质量(经费类备件除外),库管员核对入库数量,正确无误后,按月编制入库连续流水号,签发手工入库单,由仓库传递物流部入K3 账务,单据月末装订成册保存,供货商到物流部取回K3 数据中的入库单。凡车间自行采购货物,不经仓库检验数量,一律不得结算。 (2)生产部和销售部订单所采购物料需经质检 (或本部门有关人员)检验签字,持经审批的价格表或采购合同(金额等程序同上)入库,在排产范围内送货。 (3)物流部必须看账发货,物料出库单不得出现负库存,即时库存每出现一张单据为负结存数据,扣款一元,每月底兑现。劳保类,办公类,工具类, 维修配件类须由车间统计或主任到物流打单领取。 (4)各车间及协作单位须持物流部出库单到仓库领料,库管员发货必须核对单据代码、名称、数量,做到帐实相符,绩效考核库管员:
清库或发货时实物少于领料单,给公司财产造成损失,由主管经理报月末考核会考核,决定赔偿金额。 每张领料单领料完毕,库管员签字确认后退还领料人。 此规定呈报各经理,下发各部室及车间。 主管经理签字: 总经理签字: 2010-09-25 .25
备件库存管理
备件的库存管理是一项复杂而细致的工作,是备件管理工作的重要组成部分。制造或采购的备件,入库建账后应当按照程序和有关制度认真保存、精心维护,保证备件库存质量。通过对库存备件的发放、使用动态信息的统计、分析,可以摸清备品配件使用期间的消耗规律,逐步修正储备定额,合理储备备件。同时,在及时处理备件积压、加速资金周转方面,也有重要作用。 1.备件入库要求 入库备件必须逐件进行核对与验收。 ①入库备件必须符合申请计划和生产计划规定的数量、品种、规格; ②要查验入库零件的合格证明,并做适当的外观等质量抽验; ③备件入库必须由入库人填写入库单,并经保管员核查; 备件入库上架时要做好涂油、防锈保养工作。备件入库要及时登记,挂上标签(或卡片),并按用途(使用对象)分类存放。 2.备件保管要求 ①入库备件要由库管人员保存好、维护好,做到不丢失、不损坏、不变形变质、账目清楚、码放整齐(三清、两齐、三一致、四号定位、五五码放)。 ②定期涂油、保管和检查。 ③定期进行盘点,随时向有关人员反映备件动态。 3.备件发放要求 ①发放备件须凭领料票据。对不同的备件,厂内外要拟定相应的领用办法和审批手续。 ②领出备件要办理相应的财务手续。 ③备件发出后要及时登记和消账、减卡。 ④有回收利用价值的备件,要以旧换新,并制定相应的管理办法。 4.备件处理要求 ①由于设备外调、改造、报废或其他客观原因所造成的本企业已不需要的备件,要及时按要求加以销售和处理; ②因图纸、工艺技术错误或保管不善而造成的备件废品,要查明原因,提出防范措施和处理意见,并报请主管领导审批; ③报废或调出备件必须按要求办理手续。 设备备件的概念和管理意义 一、备件的概念和意义 在修理设备时用来更换磨损和老化零件的零件叫做配件。为了缩短设备修理停歇时间,在备件库内经常保存一定数量的配件,叫做备件。 配件和备件是做好设备维修工作的重要物质条件。配件和备件供应及时,不仅可以提高企业的设备完好率,而且还可以缩短设备修理停歇时间。所以每个企业必须做好配件、备件的供应工作,除配合设备保修
降低备件库存方法
钢铁企业降低资产负债率的几种办法 近2年多来,中国多数钢铁企业受美国次贷危机爆发的影响,经济效益都开始大幅下滑,转为亏损。同时,企业的资金流也随之下降,资产负债率逐渐上升。“扭亏增效,深层挖潜”一时成为所有钢铁企业的生产经营目标。为了实现这一目标,并在激烈的市场竞争中求生存、谋发展,就要求钢铁企业必须不断改进各个方面的工作。本文列举了通化钢铁股份有限公司在降低资产负债率工作中采用的几种办法,总结归 前言 近2年多来,中国多数钢铁企业受美国次贷危机爆发的影响,经济效益都开始大幅下滑,转为亏损。同时,企业的资金流也随之下降,资产负债率逐渐上升。“扭亏增效,深层挖潜”一时成为所有钢铁企业的生产经营目标。为了实现这一目标,并在激烈的市场竞争中求生存、谋发展,就要求钢铁企业必须不断改进各个方面的工作。本文列举了通化钢铁股份有限公司在降低资产负债率工作中采用的几种办法,总结归纳如下: 首先,我们来看资产负债率的定义:资产负债率(又称负债比率)=(负债总额/资产总额)╳100%。该指标表明了企业的负债状况和对债权的保障程度,该指标值越小,说明资产保障债权的程度越高,长期偿债能力越强;反之,则表明企业债务负担过重,资金实力不强。国际上通常认为资产负债率等于60% 时较为适当。而现今由于钢铁企业效益下滑,资产负债率一般都高于这个指标,要想使该指标下降,一方面要控制负债增加,另一方面要不断增加企业资金流入。在有效降低资产负债率方面,我公司开展了以下几方面的工作,并取得了一定的效果。 1 以财务管理为中心,加强资金管理。 一方面搞好资本运作,优化贷款结构,引进多家银行竞争,千方百计降低贷款利息,并通过加快结算和资金周转速度,多使用承兑汇票等方式,大大降低了财务费用;另一方面抓好货款回笼和外欠的清收工作,疏通资金来源。同时,进一步强化了内部资金的集中统一管理,对有限的资金根据轻重缓急,保证重点的原则,实行倾斜政策,找出资金管理中的漏洞,研究解决办法,减少资金外流,严格控制非生产性支出和预算外支出。仅通过积极组织清欠工作,我公司就于2009 清回各项欠款计324万元。 2 突破狭隘成本管理,进一步加强物资采购和仓库管理。 充分利用我公司周边铁矿产等资源,实现大宗原燃料全面本地化采购,确保直供化采购率达到96%,减少库存资金占用。在存货成本管理过程中,我公司突破了狭隘成本管理中往往只注重生产成本管理的局限,看到了存货周转率对企业资金周转情况以及企业生产经营正常与否的重要影响。一个合理的物料库存应该是在保证供应和正常生产工艺需要的前提下,物料库存占用资金量越少越好。而在各大钢厂的实际库存中,能实现合理库存量的少之又少。多数钢厂的库
如何加强备品备件的管理
如何做好备品备件管理 计划管理:1、备件管理人员要熟悉设备,了解设备的技术参数、原理结构,掌握设备的关键备件、易损备件,对备件的更换频次、数量进行统计,根据统计情况上报备件计划。2、依据“用则必报,报则比用”的原则,备件申报时,备件管理人员要加强备件上报的严肃性及准确性,对上报备件的数量、规格型号、所属设备要有准确的信息。 3、进备件时,尽量进同一厂家的备件,给检修提供方便。 库存管理:1、备件领回来之后,进行定置管理,并在电脑上进行登记详细信息,存放时挂上标签(或卡片),并按用途(使用对象)分类存放。卡片中包括备件的领取日期、规格型号、储存数量、所属设备、备件性质(易损件或关键件)。举例说明:备件领用过程中,生活服务公司备件库存管理,有详细的备件明细表,将备件存放的位置(第几货架、第几排、第几个)、存储的数量、型号规格、所属设备在表中注明。在需要调用备件时,对备件的存放数量级位置就很容易得到。 2、将同一台设备的备件分类储存在一起,能够对设备的备件使用情况做到心中有数。 3、备件在存放时,要保持备件的干净、整洁,做好防潮、防腐。避免备件因存放时间过长导致生锈。 4、定期(1个月或2个月一次)对设备的库存备件使用情况进行盘点,随时掌握备件的使用情况,将备件进行充分利用。 技术管理:对无图纸或图纸不清楚、不详细的备件,利用日常检
修、大中修的时间进行测绘,绘制图纸。完善备件的图纸技术资料,为备件供应、设备维修提供技术依据。 经济管理:1、加大修旧利废和技术革新力度,降低备件的管理成本。对设备出现故障较高或更换备件频繁的地方,车间组织人员进行分析原因,采取革新或其它措施,降低备件的消耗。 2、设备使用过程中,对设备的润滑及保养要做到位,降低设备故障率和停车率,从而降低备件的消耗。 面对强大的对手,明知不敌,也要毅然亮剑,即使倒下,也要化成一座山
配件库存分析与管理
增加销售或降低营运成本都可以扩大盈利,而增加盈利的最好方法之一,就必须有一个的良好的库存结构。(开源和节流) 一、库存分析 库存——是指响应客户需求,缓冲供需波动,降低成本,最终提高客户满意度为目的建立的存储体系。按照经济用途可以分为:商品库存和辅助材料库存,根据存在的作用又可以分为:周期性库存、在途库存、安全库存或缓冲库存、投机库存、季节性库存、地域性库存与冷背库存。 1、为什么要建立库存 l 库存是解决时空矛盾所必须的。既然存在时间和空间的差异,就必须有库存 l 所谓零库存是指“库存沉淀为零”,即:备件在采购、陪送、销售等一个或多个经营环节中,不以仓库存储的形式存在,而均是处于周转的状态。完全的零库存是不存在的,也不现实的(丰田创造的“TPS”管理)。 l 配件库存的作用:维持服务与销售的稳定,应付市场的变化和用户的需求 2、库存分析 库存分析与控制是计划人员的重要工作,探索与总结库存分析与控制方法是提高计划业务水平的重要途径。通过库存分析,将物料按不同的类别进行分析与控制,依据供需形势的准确判断,充分发掘它们不同的特点,进行计划细分,采取恰当的策略,实现公司经营的目标,解决降低库存投资(提高库存周转等)与为提高生产效率等对库存的需要的冲突。 l 库存结构分析方法 对一个存储系统来说,库存结构影响物流周转速度,所以它也是衡量库存质量的一种标准。根据库存周转率的相关概念和公司实际的维修特点,可以得到合理库存比例关系。进而利用这个比例关系,得出实际库存中不良库存的部分。 库存周转率= 12个月的出库总成本/平均库存 平均库存=(月初库存+月末库存)/2 通过控制库存结构,减少不同环节的库存浪费,就能提高库存周转率,在较低的库存水平下达到同样的客户需求满足率。 l 不良库存分析方法 关注库存中不合理部分,包括其所占整个库存的比例以及产生的原因分析,通过实际库存和理想库存的结构对比,将不良的库存从整个库存中提取出来。具体产生的原因有: (1)市场预测偏差 市场预测偏差会造成的额外库存资金。 l 为了满足发货,需要预备一定的库存,还必须有一定的在途库存和订货。 l 库存周转率必须达到合理指标(3-8) l 部分精品及配件实际的市场需求量比预计的要小,造成部分配件精品积压,如销售部中精品,资金占用较大 (2)配置切换 进行配置切换,基于切换的安全性考虑,各配件都有不同程度的重叠,对库存的影响较大。如安全气囊由内饰不同的演化等等。 (3)结构性偏差 为了应付个别车辆的维修冲击,对一些用量少的配件需做一定量的库存,一般来说这些配件的周转速度要远远低于其他备件,造成库存增大。这也是这6个月不动产中主要原因。(4)订货管理
关于优化库存管理的思考探讨方案
摘要:随着市场竞争日益加剧,电力企业的“好日子”已经成为过去,粗放式经营已经退出历史舞台,企业的利润点已经转移到管理的各个细节。库存管理正是电力企业当前可以深挖掘的领域。本文以S电力公司为例,结合企业生产实际,分析当前库存管理过程中存在的问题,有针对性地提出优化方案,为企业在激烈的市场竞争中提供参考依据。 经济全球化为企业发展提供了广阔的舞台,也带来了全新的挑战。对于火电企业而言,不仅面临着产业过剩导致的竞争激烈,更有太阳能、风能等新能源快速发展带来的冲击。在不容乐观的形势面前,火电企业纷纷向管理要效益,在库存管理上做文章。如果单从生产的角度考虑,库存当然越充足越好,但是企业必须通盘考虑经济效益,库存积压过多就会占用过多的资金,导致库存管理成本和人工成本上升。还有,过高的库存量会掩盖了企业生产经营过程中存在的一些问题。因此,研究库存管理具有十分重要的意义。 1、S公司库存管理中存在的问题 1.1物资计划不够准确 目前,S公司物资需求计划实行统一管理,各基层单位根据基本建设、生产运营、技术改造项目的安排和物资消耗规律编制年度、季度、月度物资采购计划和临时性采购计划。需求计划统一通过物资管理信息系统上报采购中心,公司依据集采目录实施计划分交,其余委托各二级单位自行采购。虽然S公司已经建立了相对完善的工作流程,但是在执行的过程中依然存在不少问题。比如,部分单位物资管理经验不足,及时处理物资计划能力较弱。部分单位对设备运行及损耗情况掌握不准确,导致计划提报的及时性较差,没有预留合理的采购周期,给保障安全生产的物资供应带来困难。部分单位对物料的规格、型号、图号、材质等信息描述不清或不规范,导致计划流转周期长,延误采购,影响生产。部分单位对上报计划审核工作把关不严,没有对所需更换的设备配件种类及数量作出准确判断,没有对设备检修作出个性化分析,促使采购计划量增大,形成库存积压。 1.2库存管理不够科学 S公司不设物资实物库,由二级单位分别设实物库并自行管理,导致整体管理水平参差不齐。 (1)备品配件储备定额没有实施有效地管控,缺乏统一、准确的管理基础数据。在电厂机组投产运行初期,对设备运行、检修及备品消耗等信息掌握不全面,导致编报的备品配件储备定额的准确性、实用性较差,备品配件按定额标准完全储备后会造成大量的库存积压。 (2)库存资金增长较快,缺乏有效的管控措施。当前,公司的库存
备品备件管理办法
备品备件管理规定 第一章总则 第一条目的 为规范公司生产设备备品备件的时效性管理,确保备品备件既满足安全生产需要,又经济合理地储备,减少积压和浪费,提高备品备件利用率,降低采购成本和节约储备资金,特制定本规定。 第二章职责分工 第二条职责 (一)生产保障部职责: 1.负责制订完善备品备件、工器具管理制度,对各单位备品备件、工器具的消耗进行统计; 2.负责对各单位上报的备品备件、工器具计划进行审核,确保各单位备件、工器具建立合理的库存,降低备件、工器具成本; 3.负责牵头组织相关部门对公司备品备件计划、采购、仓储、领用、盘点的统一监督、检查考核管理。 (二)物资部职责: 1.负责审核备品备件、工器具采购计划是否有存货; 2.负责协助财务部进行备品备件、工器具的盘点工作; 3.负责备品备件、工器具的储备、保管及发放工作。
(三)采购部职责: 负责备品备件、工器具的采购。 (四)财务部职责: 负责牵头进行公司备品备件、工器具的盘点工作及账务处理。 (五)各分子公司管理职责: 1.建立各单位备品备件、工器具管理办法,明确各级、各类人员的职责; 2.负责备品备件储备定额的计划,设备各级检修备品备件的采购计划上报、到货质量验收、领用统计及制定相应的验收管理流程。 第三章具体管理内容 第三条备品备件定义: (一)为了及时满足设备的维修需要,缩短维修停机时间,减少停机损失,尽快恢复设备原有功能,需要将设备中容易磨损的各种零、部件,事先加工、采购和储备好。这些根据设备磨损规律和零件使用寿命实现按一定数量储备的零件称为备品备件。备品备件类型: 1.一般性备品备件 (1)正常运行情况下的易损备件、通用性大、消耗大的零部件(如:螺栓、垫片、密封填料、橡胶板、密封胶等);
配件库存主要分析数据的计算方法
首先必须对零件的ABC分类非常清楚 其次探讨零件计划的主要指标(KPI) 以上构成对库存分析必不可少的两部分,也是分析库存的基础数据来源 这里主要讲KPI的数据来源和计算方法,关于如何分析请参考自己的库存来做计算对比,各个指标的参考标准一般来说经过长时间的工作积累和比较同品牌其他维修站都可以制定比较合理的参考数据来对比分析。 A,讲到库存分析,首先要有几个前提 1,库存的物理数量和系统的存储数量要一致 2,零件和价格数据要保持最新 3,零件的替代关系在系统里必须及时更新 4,问题类零件以及无法正确分类的零件要及时在系统里做处理 B,主要数据的组成以及各数据评价和反映的问题 1,零件满足率-客户满意度 2,库存周转率-零件部门管理工作效率 3,紧急订货的百分比-订货效率和经济性 4,死库存零件占总库存比例-库存结构的优化性 5,服务水平-客户满意度 6,单车零件销售额-零件销售绩效 C,以下提供各类指标的参考数据 一,AB无库存的零件项占总零件项的指标 1,A=<1%
2, B=<10% 3,NA=<8% 4,NB=<15% 二,小于最低库存的零件项的指标1,A=<5% 2, B=<20% 3,NA=<10% 4,NB=<25% 三,订货状况的指标(品种) 1,紧急订货比例=<30% 2,A类零件占紧急订货的比例=<5% 四,超出最大库存的零件货值 1,A=<10% 2, B=<15% 3,NA=<15% 4,NB=<20% 五,C类零件的库存金额 1,C类零件年增长2-3% 六,NC类零件的库存金额 1,与NA+NB货值的比例=<20% 2,占总零件货值的比例=<2%
汽车售后备件库存优化分析
龙源期刊网 https://www.360docs.net/doc/5612151687.html, 汽车售后备件库存优化分析 作者:陆斌亿 来源:《科技资讯》2013年第05期 摘要:随着汽车行业的飞速发展,汽车售后服务在获取竞争优势、提高客户忠诚度和获 取利润等方面的重要性日益突出,而汽车售后服务的改进需要合理的备件库存管理作为基础,与此同时,车型更新换代的速度原来越快,对于停产的车型,如何在较长的承诺服务期内保证售后服务的需要,是汽车行业急需解决的问题。因此本文主要研究汽车的服务备件结构问题。 关键词:售后库存优化汽车行业 中图分类号:F274 文献标识码:A 文章编号:1672-3791(2013)02(b)-0181-03 本文以海马汽车为例,分析其服务备件管理中的问题,例如备件库存资金占用大、过多储备金额较大总成件、死库存现象严重等,采用基于服务水平的ABC分类法,结合备件供货采购周期及备件属性,即库存三位一体分析工具对其库存结构进行优化。 备件活动目的在于确保有功能或外观缺陷的产品能通过更换缺陷备件而重新获得使用价值。备件管理主要是针对企业在售出产品后,为了实现售后服务承诺,提高服务质量,必须维持备件以提供服务保证期内的服务,通称为服务备件。截至2012年6月份我国汽车保有量已达到2.33亿辆。如此巨大的汽车保有量,为我国汽车服务备件发展提供了巨大的市场空间。 目前,能否为用户提供可靠、及时的服务,就成为汽车服务企业首要考虑的因素。企业为了保证售后服务质量、维护企业形象,在服务备件方面往往采用过量库存,造成资金浪费。鉴于上述特点,传统的备件管理手段使汽车行业在备件管理上暴露出诸多问题,例如库存积压,“死库存”现象等。同时,对于停产的车型,要在一个较长的承诺服务期内保证售后服务的需要,服务部门必须确定末次订货时需要订购多少服务备件才能既保证服务水平又降低成本。因此,如何确定一个合理的备件库存量,既减少资金占用、又降低备件费用,确保向用户提供及时、高效的服务,己成为汽车服务行业的重要课题。 1 汽车行业服务备件库存分析法 1.1 备件ABC分类法 ABC分类法又称帕累托分类法或重点管理法,它是根据事物在经济或技术方面的主要特 征进行分类排队,分清重点和一般,从而有区别地确定管理方式的一种分析方法。该方法是在决定一个事物的众多因素中分清主次,识别出少数的但对事物起决定作用的关键因素和多数的但对事物影响较小的次要因素。由于它把被分析的对象分成A、B、C三类,所以又称为ABC 分类法。其基本思想是,首先收集各个备件的名称、规格、年需求量、备件单价等基本信息,然后用单价乘以年度使用量,最后从年度使用金额最高的开始将这些物品排序,重点分析控制
供应链管理环境下的库存管理与控制
供应链管理环境下的库存管理与控制 库存,它表示用于将来目的资源暂时处于闲置状态。一般情况下设置库存的目的是防止短缺,它还具有保持生产过程连续性、分摊订货费用、快速满足用户订货需求的作用。在企业生产中,尽管库存是出于种种经济考虑而存在的,但这也是一种无奈的结果。因为,库存的存在是由于人们无法预测未来的需求变化才不得已采用的应付外界变化的方法,也是由于人们无法使所有的工作都做的尽善尽美,才产生一些人们并不想要的冗余与囤积——不和谐的工作沉淀。 在库存管理理论中,一般根据物品需求的重复程度分为单周期需求问题和多周期需求问题,单周期需求也叫一次性订货问题,这种需求的特征是偶发性和物品生命周期短。多周期问题是在长时间内需求反复发生,库存需要不断补充。 一、供应链管理环境下的库存问题 (1)缺乏供应链的整体观念,库存管理思想落后 供应链不是一个单一的点,而是一个整体,含有很多环节,只有各个结合部的协调活动,才能使其运作效果达到最佳。供应链的绩效取决于各个节点的绩效,但是这些部门又都是独立的单元,担负着自己独立的目标和责任。一般的供应链系统只是单纯地以某一结合部的绩效作为其评价指标,而不能对全局供应链的绩效评价指标,这是普遍存在的问题。 (2)对用户服务的理解与定义不恰当 在现代企业“以顾客为本”的服务理念中,供应链管理的绩效由用户来评价是比较客观有效的,或者,管理者也可以通过对用户反应能力来评价供应链管理的好坏。对用户服务水平参差不齐,主要是因为对用户的服务的理解和定义各不相同,过去以订货满足率作为评价指标的模式已经不能对订货的延迟水平做出很好的评价。 (3)不准确的交货状态数据 当顾客下单时,他们总想知道什么时候能交货。在等待交货过程中,也可能会对订单状态修改,特别是当交货被延迟以后。我们并不否认一次性交货的重要性,但我们必须看到,许多企业并没有及时而准确地把推迟的交货单的修改数据提供给客户,其结果当然会使用户不满。
库存控制策略
库存控制策略 如何才能够保证产品有竞争力?控制运营成本是关键!而这其中合理、适当的库存规模又是重中之重! 现在商业的竞争早已经不再是单纯意义上的单个企业的商业行为,无论是策略化的企业联盟、Lean SCM(敏捷供应链)还是诸如ECR(高效客户化响应机制)等等新兴的管理技术的出现无疑都是因应这一趋势的产物;看一看我们的身边,一方面空前强大的制造机器在不停的制造着大量的产品,而另一方面面对琳琅满目的货架消费者又往往无所适从;消费者和我们面临着同样的选择,面对繁杂、多样的产品和过剩的信息我们究竟该何去何从?从本质上来看问题的核心是我们如何才能够在保证维持并尽可能提升有竞争力的客户化服务水平的前提下去控制我们的运营成本!而这其中合理、适当的库存规模又是重中之重! 正如同我们所熟知的7R原则一样,供应链系统的优化是一个长期、持续的行动而绝非是一时一地一组织的短期行为;这其中既有来自外部的竞争性变化因素和相关的社会化要素,又有来自企业内部对提升自身核心竞争能力诉求的内部因素。从企业内部要素来看:库存计划、需求计划预测、供应链响应速度、系统的准确性和差错率四个方面无疑是我们关注的焦点所在。 而库存状态的变化、跟踪、控制也早已经超出了我们通常概念下的纯粹数量的概念,从业内最新的一些管理技术动向来看,策略性合作伙伴关系联盟已经成为了我们共同的挑战。在国内竞争国际化、企业生存社会化、同业竞争残酷化的今天,“客户-企业-供应商”,已经不再是传统意义上的三个独立的运作单位,正如同我们的运作管理平台正在从传统的“ERP”跃升为“SCM”一样,没有我们合作伙伴的积极参与,我们的供应链系统就如同无源之水、无本之木,而库存计划的控制管理也同样有赖于我们对“客户-企业-供应商”三者关系的定义和策略性双赢联盟的形成和维系! ECR-高效客户响应 起源于美国的ECR(efficient customer response)最先是由全球的零售业巨头沃尔玛在QR快速响应(Quick Response)概念的基础上发展而来的,并最先在食品行业得到了推广(图2)。无论是ECR还是QR其产生的背景并不是问题的关键,问题的关键在于ECR概念背后的理念能给我们实际的运作带来什么? 应该说无论是ECR还是QR其产生并得到大规模推广的一个极其重要的前提就是IT信息技术的飞速发展,我们很难想象如果没有EDI、电子条码系统、前端的POS系统等基础平台的存在,ECR将如何去运作!ECR的核心正在于将原本各自独立的客户、企业、供应商三者整合为一个策略性的联合体,并以先进的IT资讯系统为平台,以快速满足客户化的服务需求为前提,形成一个从产品设计到生产制造、配送分拨乃至卖场布置、促销策略等等,形成覆盖整个业务流程的动态双赢的商业生态系统! 区别于传统的Push-推式作业系统的是ECR是典型的Pull-拉式作业系统,整个流程、链条上的作业始自客户的需求,并围绕这一核心整合整个系统的资源以最小的投入来满足客户化的服务需求进而获得预期的收益!正如同前面所述,EDI、Bar-code、RFID等基础平台技术的发展使ECR更加如鱼得水!因为ECR的核心是:协同、共享、双赢,而基于Bar-code、RFID等数据采集技术的电子资讯交换系统将使我们在终端平台上可以即时的得到卖场商品的销售变化情况,从而彻底杜绝库存过剩甚至需要降低安全库存的设置标准! CRP-连续补货系统 正如同前面所述,CRP(Continuous Replenishment Practice)是和ECR系统相伴生的运作策略,没有ECR系统作为平台,连续补货系统将无法运作。而资讯的共享显然是所有流程的核心所在(图3)!前端的POS系统数据通过Internet网络和EDI系统将直接或间接(这
储运部备品备件库存分析会议纪要
储运部备品备件库存分析 专题会议纪要 第1期 二〇一一年十月二十一日签发: 储运部备品备件库存分析专题会议 为降低备件库存,减少流动资金占有, 2011年10月20日,公司副总经理在一楼培训室主持召开专题会议,生产部长、副部长、财务部长、人事企管部长、储运部长、仓储主管、采购部备件主管及各车间主任、设备管理员等参加了会议。 首先,储运部长就目前的备件情况及仓储部门的下一步工作思路做了介绍: 至2011年9月30日,公司库存备件总金额755.43元,比7月31日的862.80元降低约107.37万元,降低的注要原因一是大修刚结束,大修备件已出库;二是目前公司上下加大对备件的管控力度。 近期仓储部门对库存备件进行初步筛选:现永远不用备件万元,基本不用备件万元;在用备件万元。 现在库存备件的存在问题: 1.库存备件金额大,占用公司流动资金; 2.部分退库设备占用库容; 3.长期不用备件较多;
4.由于沟通不及时,造成部分备件重复采购; 5.采购计划存在盲目性,部分采购备件长期不用; 6.部分仪表、电气备件由于设备升级,原先采购备件已无法使用; 7.采购计划不合理,部分备件采购数量大。 下一步工作思路: 1.人事企管部、财务部要加大考核力度,严格执行; 2. 仓储部门与车间加强沟通,加大老库存备件利用工作,尤其是贝斯特公司遗留备件; 3.设备维修要有计划性,采购计划应细致严谨,确保备件不长期库存,减少资金占用; 4.严格执行采购计划报批、入库检验、出库、退库、退货等工作制度及流程; 5.建立激励机制,充分利用公司现有的金加工设备,进行应急加工和简单备件加工; 6.出库材料要确保立即使用,二级库备件退回仓储部门,由各部门使用,做到资源共享。 目标: 1.9月份大修结束后将备件库存总金额降到万元以下。 2.2011年底备件库存总金额不超过万元。 3.2012年底备件库存总金额控制在万元以内。 参会人员通过激烈研讨,一致认为: 1.各部门采购计划应先经过仓储部门审核后再到采购部进行采购;及时停止因工艺、设备改变及采购周期与检修时间衔接不上等需终止的采购计划;
备件采购及库存管理优化措施
备件采购及库存管理优化措施 发表时间:2018-10-24T16:09:34.203Z 来源:《防护工程》2018年第12期作者:苗超军 [导读] 需要对备件的采购和储备进行决策。尤其企业在购买设备的昂贵部件时, 经常同时也以优惠价格买下备件, 需要确定采购多少备件,保持什么样的备件库存水平, 对备件储备进行正确决策。本文分析了备件采购及库存管理优化措施。 苗超军 安徽江淮汽车集团股份有限公司安徽合肥 230601 摘要:在市场竞争日益激烈地今天, 快速响应市场需求是企业在竞争中生存与发展的根本保证, 而快速响应用户不断变化的需求需要强有力的后勤保障与支持。备件是设备正常维护检修和应急处理的保障性物资,是保障设备处于良好状态的重要因素。企业在使用设备过程中, 为了保证设备的正常运转, 需要制定维修计划, 需要对备件的采购和储备进行决策。尤其企业在购买设备的昂贵部件时, 经常同时也以优惠价格买下备件, 需要确定采购多少备件, 保持什么样的备件库存水平, 对备件储备进行正确决策。本文分析了备件采购及库存管理优化措施。 关键词:备件采购;库存管理;优化措施; 备件管理是设备管理工作中的一项重要内容,它已成为降低维修成本的重要环节,也是充满挑战性和蕴含开发潜力的管理过程,它与企业正常生产及经济效益密切相关。 一、概述 1.备件定义。在设备维修工作中,为缩短修理的停歇时间,根据设备运行特点与零件失效规律,以及零件的设计使用寿命,对容易损坏的零件在故障发生前按一定数量进行储备,这部分用于维修而储备的零件称备件。 2.备件管理内涵。为了满足设备维修需要、保证生产正常进行和提高企业经营效益,而从事的对设备构成零件的统计与分析,确定需要储备、生产零件的种类、数量,制定备件自制加工、外购订货和储备供应工作计划和规章制度,以及对备件占用资金的统计分析与经济效益核算等一系列活动的总称。 二、备件库存控制策略与模型 1.实际上,对备件库存模型优化也有两类优化目标:一类是追求达到一定有效度水平的备件存储优化, 在给定使用可靠度和给定工作时间的情况下, 确定机械设备维修备件储备量的计算模型和方法。另一类优化目标是寿命周期或计划期成本最优,连续时间的动态规划决定使计划期的平均总的准备订货、单位生产采购、缺货和超储成本最小化的补充策略。总的来说这些文章所讨论的模型与策略主要考虑三个方面: 什么时候开始订货; 要订多少货; 如何权衡降低成本和增加系统有效度之间关系。 2.对于多级备件存储是否经济合理,他们考虑了两级、多个不可修部件系统, 补给站需求服从泊松分布, 采用以拉格朗日为基础的方法, 比较多级情况的不同分散与集中程度的库存数量, 结果表明多级库存情况较好。采用启发式算法扩展搜索空间, 解决库存集中与分散问题。他们也发现对于低需求备件采取多级库存更有益。多级备件库存所采取的策略及算法研究有不同的研究结果。运用相关回归技术寻找策略中最优批量和存储数量。他们还提出了采取补给策略的延迟订货的两参数近似值。备件存储系统的分析模型, 并采用拉格朗日乘法理论进行优化。分析了有限修理能力对库存控制的影响, 给出了受修理能力限制的多级可修备件库存系统模型。他们认为假定修理能力是充足的可能产生一个错误结论, 求得的库存水平可能低于实际要求。实际上, 很多行业对修理及时响应也是很困难的。他们建议用双负二项分布作为备件需求分布可以改进问题的分析精确度。 三、优化措施 1.设备备件采购注意。采购进口备件相对复杂。为了减少交易风险、保证备件质量,应处理好3 方面工作。(1)为保证备件供应的可靠、稳定以及良好的后续服务,选择进口备件供应商应考虑以下顺序:①进口设备原制造厂或直属专营供应机构;②进口设备制造厂在中国的分公司或备件经销部门;③进口设备制造厂在中国的授权代理经销商;④一般进口备件经销公司。(2)订购进口备件时,要提出准确的采购要素,包括进口设备订货合同号或生产厂家出厂序列号(它是制造厂产品编号的唯一代号,通过查询可知设备名称、规格和各种技术参数,以及生产日期等信息)、备件名称与件号、安装位置和订购数量等。(3)采购进口备件的付款、结算方式。首先核实、分析供货方资质、信誉与合作态度,以及合同标的和发货、到货地点与运输方式等项目。对于金额较大的合同应规避风险,一般采用信用证结算方式。这种方式是交易完成后由双方开户银行划拨,风险小;同时这种方式可以减少操作成本和管理成本。为了减少企业资金占用,应尽量在供方发货前夕开具信用证。此外,在付款时应扣留10%保质抵押金,在到货验收后支付。对于金额较少的合同,一般以现汇方式结算,但尽量争取到货后付款。 2.制定规范的备件库存管理制度。备件库存管理不仅对设备维修有保障作用,而且备件占用资金还是企业资产的一部分,应认真管理。(1)各种备件入库均应履行检验、清点、登记、建账、核资等手续。同时,领用备件也要办理出库手续,包括使用申请、批准、登记、记账、核资等项。(2)备件仓库要有专人保管,除办理日常入出库手续外,还要做好备件维护(防尘、防腐蚀、防磕碰、防变形、防老化等)工作和定期清点工作,以及失效、淘汰备件的处理,做到账、卡、物相符。 3.借用供应商的资金,采用新的库存方式。为了减少企业备件资金占用,要利用备件市场供应过剩的局面,要求供应商实行优惠供货及结算方式,其中之一即VMI,称之为供应商管理库存方式。(1)经双方协议供应商提供一定数量的常用备件,存放在企业的备件库中,暂不收费;待企业设备维修领用备件时,再办理出库、记账、付款等手续。再进一步,供应商不仅负责加工、运输、保管备件,还延伸掌握企业制定的设备维修计划和生产任务调整等业务情况,更主动安排备件供应。目前,一些企业实行的JIT 和寄售制等交易方式,均包括在VMI 范畴之中。新的备件仓储形式对供需双方都很有利。供方虽然占用了资金,但获得了稳定的备件销售渠道和销售利润;需方不仅有备件供应保证,更主要是大大减少备件资金占用。(2)推行备件精益化管理措施。①从选型开始,保证设备高可靠性,降低运行故障发生,减少备件消耗;同时在选购时,尽量减少机型种类,扩大备件的通用性,降低备件储备品种;②加强设备使用过程中对设备的维护与检查,采取以诊断技术为主的预防性措施,及时发现与排除隐患,防止引发设备故障;③实行ABC 分类管理,合理储备备件。对关键的A 类备件,优先保证储备。包括运转中容易磨损和疲劳损坏的零件,如高速运转的小模数齿轮,运动中受冲击的曲柄、连杆机构等。保证设备加工精度的重要零件,如机床主轴、高精度齿轮和丝杠副、采购周期长的进口设备常用备件等。对于不易损坏和采购方便的C 类备件,则可以不储备。包括新购置的正规设备,一般在3~5 年不会发生正常的运行故障,可以不存或少存关键备件;对有周期性故障的设备,平时
47-一种多级库存的优化控制策略
第29卷第4期2006年8月 鞍山科技大学学报 Journal of Anshan University of Science and Technology Vol.29No.4Aug.,2006 一种多级库存的优化控制策略 马东怡1,王 莉2 (1.鞍山科技大学理学院,辽宁鞍山 114044;2.鞍山科技大学电子与信息工程学院,辽宁鞍山 114044) 摘 要:针对供应链环境下的多级库存优化控制问题,以系列系统为例,应用级库存理论,并考虑到日常生 活中库存水平影响需求率这一现象,建立了一个需求率受库存水平影响的多级库存决策模型。然后,在遗传算法(G A )中加入叫行化操作,对模型进行求解。最后,以算例说明模型和算法的有效性。 关键词:级库存;多级库存控制;系列系统;需求率;遗传算法 中图分类号:O227 文献标识码:A 文章编号:167224410(2006)0420341206 现行的企业库存管理模式是从单一企业内部的角度考虑库存问题,因而并不能使供应链整体达到最优。要进行供应链的全局性优化与控制,必须采用多级库存优化与控制。最早开始研究多级库存的学者是Clark 和Scarf [1],他们提出“级库存”概念。随后,针对多级库存系统的优化控制,文献[2-7]做了大量的研究,提出非常有价值的控制策略。对许多商品来说,商品在货架上摆放的越多,就会吸引更多的顾客,这时的需求率显然与库存水平有关,这种现象被称作Inventory 2level 2dependent demand rate (库存水平影响需求率)。为此,文献[8-12]研究了需求率受库存水平影响而变化的单级库存模型。本文在需求率受库存水平影响的单级库存模型的基础上,应用级库存理论,建立了一个需求率受库存水平影响的多级库存决策模型,并且设计了遗传算法求解模型,从而获得该模型的优化控制策略。 1 问题描述 111 多级库存系统 定义1[11] 多级库存是指各个库存点通过供需关系连接起来,形成一个网络或者是一个有向图。 图1 系列系统结构模式 Fig.1 Structure mode of a series system 根据网络结构的不同,可以分为五种。其中,系列系统是最基本的多级库存结构,如图1所示,其他多级库存系统结构都可 以看成是系列系统的扩展。 定义2[11] 某节点的级库存是指从某一个库存点开始下游所有的库存。若令I ′i (t )为时刻t 节点i 的库存,I i (t )为时刻t 节点i 的级库存则有 I i (t )= ∑i k =1 I ′i (t ) i =1,2,…,N (1) 定义3[11] 令h ′i 为节点i 的库存费率,则节点i 的级库存费率定义为 h i =h ′i -h ′i +1 i =1,2,…,N (2) 其中,对于N +1阶段认为是外部供应者所承担,假定为h ′N +1=0。 为保证级库存费率非负,需假定下游的库存费率比上游的要高,即假设h ′i ≥h ′i +1(i =1,2,…,N -1)。 收稿日期:2005212203。 作者简介:马东怡(1980-),女,辽宁阜新人。
备品备件仓库管理制度
备品备件仓库管理规定 1.0 目的:在保障生产和机械保养需要的基础上,为降低采购成本和节约储备资金,通过科学有效的 管理提高整体经营绩效,特制定本办法。 2.0 适用范围:备品备件仓库所有仓库管理人员 3.0 术语: 备品备件:为了缩短设备待修时间,在设备维修之前予以储备的设备配件材料。 4.0职责:仓库负责人负责仓库一切事物的安排和管理,仓管员负责物料的收料、报检、入库、发 料、退货等日常管理。仓库负责人、采购人员及设备部人员共同负责对备品备件的检验、不良品处置方式的确定和废弃物的处置工作。 5.0 备品备件的仓库管理 5.1备品备件的申购 5.1.1备品备件的购买有设备部人员填写物料申购单,经各审批人员审批完成后交由采购人员采 购。 5.1.2备品备件的采购需经仓库管理人员确认仓库没有物料后物料不够,并在物料申请单上签字后 方可采购。做到既保证合理库存又满足维修需要,防止积压浪费,避免供不应求。 5.1.3备品备件的采购应力求采购成本和库存成本达到最佳组合。 5.2备品备件的入库管理流程 5.2.1备品备件进入公司后,采购人员应将经各相关人员签字后物料申购单交给验货的仓库管理人 员。 5.2.2拿到物料申购单后仓库管理人员必须进行初步检验:首先要核对实物名称、数量、规格、型 号等与送货人交付的单据及物料申购单是否一致,避免采购人员多买、少买或错买,造成不必要的损失。如果不一致仓库管理人员有权拒收。 5.2.3初步检验合格后,要求设备部有关人员进行进一步检验,经检验合格的备品备件方可入库。 检验不合格的备品备件,由仓库管理人员和采购人员共同组织退货。 5.2.4检验合格的备品备件仓库管理人员应经仓库负责人同意后及时入库,办理相关入库手续并要 求相关人员确认并签字后,第三联交给采购人员作为报账凭证。 5.2.5办理过相关入库手续的备品备件应及时根据分区、分类、定位管理的原则放到指定的货架上, 并更改物料卡上的相关信息确保信息的真实可靠。 5.2.6及时根据备品备件入库单上的信息登记账簿。 5.3备品备件的储存养护
库存合理控制订货优化管理
库存合理控制订货优化管理 库存的合理控制与订货的优化管理 销售人员与经销商在正常情况下常规、关键的工作接口点就是:库存的销货和再次订货的问题。”不识庐山真面目,只缘身在此山中”不少做了多年销售的业务员对这二项司空见惯的工作却不知道其中的奥妙,当然优秀的销售人员早就因人制宜地总结出一套行之有效的方法,本文仅就这二个问题从实用性的角度做一个总结和介绍。 库存的合理控制 怎样才能进行库存的合理控制?有几观念上的问题必须要解决:什么是安全库存?怎么样才能做到双赢?正常库存与特殊情况库存的辩证关系?如何运用好行进行出的原则?怎么样进行品类管理等等。 首先,作为厂家的业务员一般是客户库存的多少与自己没有多大直接的关系,关键是客户能够多进货自己的销售任务完成的好,才是最关心的;而站在客户的角度又担心库存的各积压,往往是喜欢少数多次的进货,宁可因库存不足减少一点销量也不愿意多进货而积压库存。这里就有一个合理度的控制问题。只有控制好这个合理的度,才能做到真正的双赢,不仅业务员任务完成得好,经销商没有库存积压风险,货卖的多,而且双方的合作是愉快,轻松的。那么怎么才能把握好这人度呢? 合理的正常库存控制 假定每日正常出库量为120件,即日最低安全库存量为160件,如果经销商习惯是6天向公司报一次订货,而路途运输时间是七天,那么合理的正常库存控制数应该是:120X (6+7)+160=1720件[公式是:日销量平均数X(定单间隔天数+运输途中天数)+日最低安全库存量=合理的正常库存控制数]。 根据这个合理的正常库存控制数双方就能做到心中有数,但是这仅仅是一个标准的参与数,具体情况还应考虑以下几个变数。 二批商和零售终端的库存情况 如果把经销商比喻为水库,那么二批商的仓库就是小水库,零售终端的仓库就是水箱。二批商和零售商的合理的正常库存控制数市场繁荣方法同上,应注意减去其订货和送达周期的快捷性,加上日平均销量的不准确性等因素,所以一般应该再加上20%左右的浮动数。经销商不能只计算自己的库存数量,要按整个区域的销售总量计算包括二批商、零售商的总体库存量,根据总体库存量要求调整经销商的库存数量,要按整个区域总量计算包括二批商、零售商的总体库存量,根据总体库存来调整经销商的库存,要做到深入了解它们的动作情况,定期对它们的销售及库存数据进行分析,避免出现太少的总体库存而影响销量,同时也要避免二批商零售商太多的库存,因为二批商、零售商过多的滞留库存最终会为经销商的定时炸弹。 季节和政策压库 以饮料为例,如遇五一节、国庆节等长假,必须考虑节假日的天气情况,天气好可能是正常的日销量的2至3倍,天气不好可能是平时的1.5倍,节前二批商、零售商库存是否已经吃饱,节日长假期内厂家是否可以正常订货发运,运输途中时间一般会加长等因素都要考虑在库存数的调整幅度之中。 在某一时间段厂家若有订货政策百送几,这时一般要考虑多订一点货,虽然超过了正常的库存数,但属为所能极的范围可以多订,同时要留有余地,不能贪多,万一政策或市场有变动以免造成积压。 还可以借助计算机系统进行科学的库存管理。 严格按照先进先出原则进行库存管理,以免商品批号过期。
钢铁企业备件库存管理的优化研究
钢铁企业备件库存管理的优化研究
天津理工大学本科毕业论文选题审批表 届:2010 学院:管理学院专业:物流管理2009年10月30日
注:(1)“选题理由”由拟题人填写。 (2)本表一式二份,一份院系留存,一份发给学生,最后装订在毕业论文中。 天津理工大学教务处制表 天津理工大学 本科毕业论文任务书 题目:钢铁企业备件库存管理的优化研究
学生姓名王宝平届2010 学院管理学院专业物流管理 指导教师陈力洁职称讲师 下达任务日期2009年11月9日 天津理工大学教务处制 一、毕业论文内容及要求 1、本论文研究的基本内容: 第一部分:绪论。主要介绍了本文课题的意义和国内外库存管理的发展。 第二部分:介绍了库存管理的相关概念及钢铁行业库存的特点及库存管理中存在的问题。 第三部分:提出了备件库存管理的一些问题并对其进行分析。 第四部分:对荣钢钢铁集团做出了相关介绍并分析了企业备件库存管理的现状。 第五部分:运用ABC分类法对荣钢备件进行分类管理并提出了备件供应商评价的方法。 第六部分:综合分析得出结论。 2、本论文的基本要求:
(1)对荣钢进行实地调研,了解该企业的备件库存现状; (2)理论要与实际相结合,分析该企业备件库存管理中存在的问题; (3)运用物流管理中的库存管理的相关知识,通过对该企业备件库存现状的分析,提出改善措施; (4)要求多方搜集资料,参考文献不得少于20篇,其中英文文献不得少于3篇。但严厉杜绝剽窃、抄袭等行为; (5)要求在充分资料调查的基础上进行有针对性地分析与研究,避免假、大、空现象; (6)要求论文写作文字通顺,用于准确,逻辑清晰,写作格式必须符合学校毕业论文的写作规范; (7)要求结合论文内容完成一篇不少于3000个汉字的英语翻译;论文字数要求不少于15000字。 (8)严格按计划进度完成各项工作任务,提交有关材料。 二、毕业论文进度计划及检查情况记录表