切削用量对切削力的影响比较
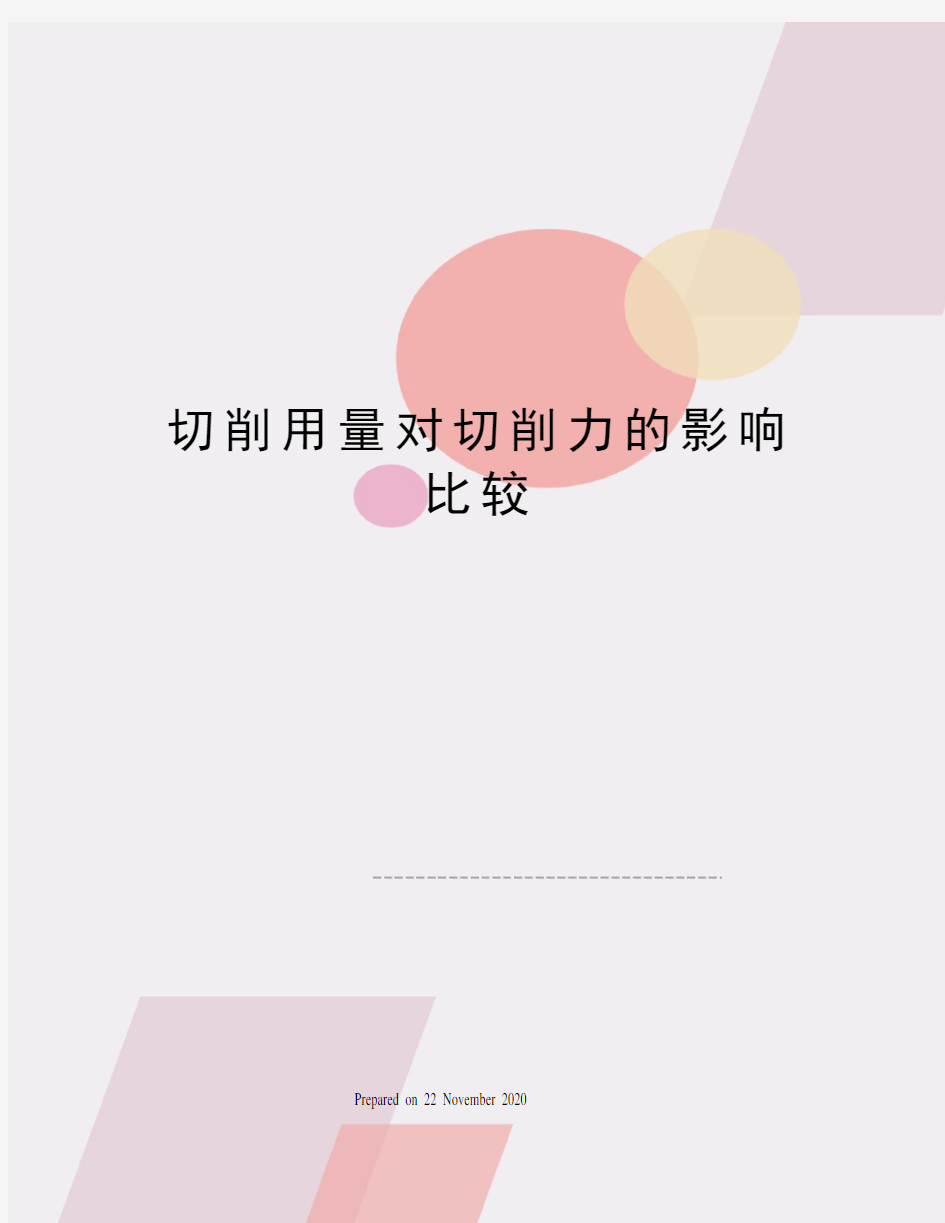

切削用量对切削力的影响
比较
Prepared on 22 November 2020
切削用量对切削力的影响比较
(陕西理工学院机械工程学院)
摘要:通过分析切削力单因素实验,探讨切削用量对切削力的影响规律;同时讨论刀具几何参数对切削力的影响,得出一般结论;进而对比说明精密切削切削力的特殊规律。
关键词:切削变形;切削力;刀具;精密切削;规律
1.引言
金属机械加工过程中,产生的切削力直接影响工件的粗糙度和加工精度,同时也是确定切削用量的基本参数。所以掌握切削用量对切削力的影响规律也显得重要。本文从一般切削和精密切削两个方面对切削用量对切削力的影响规律做初步探讨。
2.金属切削加工机理
金属切削加工是机械制造业中最基本的加工方法之一。金属切削加工是指在金属切削机床上使用金属切削刀具从工件表面上切除多余金属,从而获得在形状、尺寸精度及表面质量等方面都符合预定要求的加工。
切削加工原理
利用刀具与工件之间的相对运动,在材料表面产生剪切变形、摩擦挤压和滑移变形,进而形成切屑。
切削变形
根据金属切削实验中切削层的变形,如图1-2,可以将切削刃作用部位的切削层划分为3个变形区。
第Ⅰ变形区:剪切滑移区。该变
]
3[形区包括三个过程,分别是切削层弹 性变形、塑性变形、成为切屑。
第Ⅱ变形区:前刀面挤压摩擦区。 该变形区的金属层受到高温高压作用, 使靠近刀具前面处的金属纤维化。 第Ⅲ变形区:后刀面挤压摩擦区。 该变形区造成工件表层金属纤维化与 图1-2切削层的变形区
加工硬化,并产生残余应力。
3.切削力
切削力是指切削过程中作用在刀具或工件上的力,它是工件材料抵抗刀具切削所产生的阻力。
切削力来源
根据切削变形的不同,切削过程中刀具会受到三种力的作用,即: (1)克服切削层弹性变形的抗力 (2)克服切削层塑性变形的抗力
(3)克服切屑对刀具前面、工件对刀具后面的摩擦力
切削力的合成与分解
图2-2切削力合力和分力
图2-2为车削外圆时切削力的合力与分力示意图。图中字母分别表示:
N 1、F 1——作用在车刀前刀面的正压力、摩擦力
N 2、F 2——作用在车刀后刀面的正压力、摩擦力 Q 1、Q 2——N1与F 1、N 2与F 2的合力
F x
F y F z F xy F Z F 22222++=+=F ——Q 1与Q 2的合力,即总切削力
一般地,为了研究方便,将总切削力F 按实际运动效果分为以下三个分力:
切削力F z ——垂直于水平面,与切削速度的方向一致,且该分力最大。 径向切削力F y ——在基面内,与进给方向垂直,沿切削深度方向,不做功,但能使工件变形或造成振动。
轴向切削力F x ——在基面内,与进给方向平行。 由图2-2可知,合力与各分力之间的关系为:
其中:k r F xy F x sin =。式中:F xy ——合力在基面上的分力。 切削力的测定实验——单因素实验法
在切削过程中,影响切削力的因素很多,主要有工件材料、切削用量、刀具几何参数等。单因素实验法就是只改变一个因素,固定其它因素不变,进行试验;如此测得多组数据。最后综合考虑实验数据,得出包含多个可变因素的切削力实验公式。
以下是我搜集的部分实验数据处理后的关系曲线,如图2-3-1。从曲线中,可以得出结论:(1)背吃刀量a p 增大,切削力F z 增大
(2)进给量f 增大,切削力F z 增大
(3)不同的切削速度范围,切削力变化不同 (4)a p 与F z 和f 与F z 成某种函数关系
图2-3-1切削三要素对切削力的影响曲线
为了了解a p 、f 、v 与F z 可能成的函数关系,我们搜集了切削力单因素实验的部分原始数据,如下表所示。根据表中数据,利用MATLAB 编程可作出对应的散点图和曲线图,如图2-3-2所示。观察曲线图,猜测a p 、f 、v 与F z 可能
k r F xy
F y cos =
]
4[]
4[]
4[成指数函数关系或一次函数关系。
表1-1f=,v=100m/min
实验 f(mm) v(m/min) a p (mm)
F z (kN)
1
100
2 3 4 5 6 7
表1-2a p =1mm ,v=100m/min
实验 a p (mm)
v(m/min) f(mm) F z (kN)
1 1 100
2 3 4 5 6 7
表1-3a p =1mm ,f=100mm
实验 a p (mm)
f(mm) V(m/min) F z (kN)
1 1
25 2 50 3 75 4 100 5 125 6 150 7
175
图3-2-2实验散点图和曲线图
数据分析:(以a p 与F z 为例)
假设a p 与F z 成指数函数关系,即:a x p k F z 1
1= 为了便于计算,对上式两边同时取对数,可得:k a p x F z 1lg lg 1lg +=
对比一次函数y=kx+b ,lg F z 与lg a p 成一次函数关系。
同理:f x k F z 22=k f x F z 2lg lg 2lg +=
为了验证假设,依据②式,我先对原始数据取对数,再在对数坐标系中分别作出a p 、f 、v 与F z 的散点图和曲线图;为了验证该曲线为一次函数,分别在曲线上各取四点,两两求斜率,若对应斜率之差的绝对值近似为0(在误差允许范围内),则可认为该曲线为一次函数;然后取斜率的平均值为最终斜率,再代值求出截距,写出表达式;最后求反函数分别写出a p 、f 、v 与F z 的关系式。
按照上述思路,编写MATLAB 语言程序(附1),运行结果如下:
图3-3-3实验对数坐标图
K=
其中,K ——矩阵元素表示斜率,行分别表示x 1、x 2和x 3的值,最后一列为斜率的平均值。
h ——矩阵元素分别表示截距k 1lg 、k 2lg 和k 3lg 的值。 H ——矩阵元素分别表示系数k 1、k 2和k 3的值。 根据运行结果代值,分别写出函数关系表达式如下:
14.3lg 92.0lg -=a p F z a p F z 92.00432.0=③
55.0lg 70.0lg +=f F z f F z 70.07353.1=④ 34.2lg 14.0lg --=v F z
v F z 14.00961.0-=⑤
式③④⑤表明,在a p 、f 和v 只有一个因素改变时,切削力Fz 都与该可变因素
成指数函数关系。当综合考虑三个可变因素时,可得出:v x c
f x a x p K F z 321=。 式中,K 为综合系数。
类似的,可分别求出a p 、f 、v 和F y 、F x 的关系表达式。
4.切削用量对切削力的影响
一般性结论:(1)背吃刀量与切削力近似成正比;
(2)进给量增加,切削力增加,但不成正比;
(3)切削速度对切削力影响较复杂(与切削温度的变化和积屑瘤的产生和消失有关)。在无积屑瘤的切削速度范围内,随着切削速度的增大,切削力减小。
5.刀具几何参数对切削力的影响
图4-1刀具几何参数与切削力的关系曲线
一般性结论:(1)前角对切削力的影响最大。加工塑性材料时,增大前角,切削力降低;加工脆性材料时,由于切屑变形很小,前角对切削力影响的显着。
(2)主偏角对切削力影响较小,但对径向力和轴向力影响较大。径向力随着主偏角的增大而减小,轴向力随着主偏角的增大而增大。
(3)刃倾角在很大范围内变化时对切削力影响不大,但对径向力和轴向力影响较大,随着刃倾角的增大,径向力减小,轴向力增大。
6.精密切削加工切削用量对切削力的影响
精密切削过程中,就本质而言,切屑的变形与一般切削相同,所以其切削力的来源也相同。但是,由于精密切削采用的是微量切屑方法,与一般切削不同,所以可变因素对二者的影响就不同,,也就是说可变因素对精密切削切削力的影响具有独特规律。
进给量和背吃刀量的影响
为了探讨精密切削切削力的独有规律,搜集部分实验数据,如下表:
表6-1进给量对切削力的影响(HSS刀)
切削力进给量f/(mm/r)
(N)
60 100 350 570 900
240 280 410 580 700
表6-2进给量对切削力的影响(金刚石刀)
切削力
(N)
进给量f/(mm/r)
200 260 480 900 1030
40 50 120 170 200
表6-3切削深度对切削力的影响(HSS刀)
切削力
(N)
切削深度a p(mm)
80 150 370 520 670
250 270 330 370 390
表6-4切削深度对切削力的影响(金刚石刀)切削力
(N)
切削深度a p(mm)
100 170 260 450 500
20 30 50 70 90
以上数据的曲线图如图5-1所示。从曲线中可以清楚地看出,①精密切削采用HSS车刀(或硬质合金车刀)时,当进给量或背吃刀量小于一定值时,均有
F z F y>成立。而采用金刚石刀时,F
z
F y<
。这和一般切削F z总是大于F
y
是不同
的。②另外,在精密切削时,进给量对切削力的影响大于切削深度的影响。这和一般切削恰恰相反。
为了解释以上两条特殊规律,我查阅了相关资料文献,得知:a.规律①取决于切削用量(f、a p)同刀具刃口半径的比值。b.规律②与精密切削通常采用f大于a p的切削方式有关。
图5-1精密切削切削用量与切削力的关系曲线
切削速度的影响
如图5-2所示(考虑积屑瘤的影响),
低速时切削力随切削速度增加而急剧下降。
]
1[到200~300m/min 后,切削力基本保持不变, 这规律和积屑瘤高度随切削速度的变化规律 一致。即积屑瘤高时切削力大,积屑瘤小时 切削力也小,这和一般切削规律正好相反。
图5-2超精切削时的切削力
7.一般切削与精密切削切削力的对比
参考文献
[1]王贵成.精密与特种加工[M].2013年.第1版.
[2]周利平.现代切削刀具[M].重庆大学出版社.2013年.第1版. [3]何宁.机械制造技术基础[M].高等教育出版社.
[4]卞化梅,牛小铁.基于MATLAB 的切削力测量实验数据处理分析[J].煤矿机械.第29卷第2期.2008年2月
[5]李晓舟,于化东.微切削加工中切削力的理论与实验[J].长春理工大学机械工程学报.2008年2月
[6]吴立新.减小切削力有效途径的探讨[J].工程技术.2008年2月
[7]王洪祥,孙涛,张龙江,张昊.超精密切削切削力的试验研究[J].工具技术.第37卷第5期.2003年.
[8]赵岩,梁迎春,白清顺,等.微细加工中的微型铣床微刀具磨损及切削力的实验研究[J].光学精密工程.2007年
[9]蔺小军.金属切削刀具的有限元分析[D].西安:西北工业大学.1999年
[10]王殿龙,康德纯.球形铣刀切削力计算机预报模型的数值仿真.大连理工大学校报.第35卷第11期.2001年
切削用量试题有答案
单元四数控机床加工的切削用量习题 一判断题 1.切削用量包括进给量、背吃刀量和工件转速。( ) 2.用中等切削速度切削塑性金属时最容易产生积屑瘤。() 3.跟刀架是固定在机床导轨上来抵消车削时的径向切削力的。() 4.数控机床进给传动机构中采用滚珠丝杠的原因主要是为了提高丝杠精度。() 5.切削中,对切削力影响较小的是前角和主偏角。() 6.粗加工时,限制进给量提高的主要因素是切削力;精加工时,限制进给量提高的主要因素是表面粗糙度。() 7.铣削用量选择的次序是:铣削速度、每齿进给量、铣削层宽度,最后是铣削层深度。() 8.粗加工时,限制进给量提高的主要因素是切削力;精加工时,限制进给量提高的主要因素是表面粗糙度。() 9.切削用量中,影响切削温度最大的因素是切削速度。() 10.使用水性切削液可吸收热量,防止变形,并可提高切削速度。() 11.切削速度会显著的影响刀具寿命。() 12.一般车刀的前角愈大,愈适合车削较软的材料。() 13. 减小车刀的主偏角,会使刀具耐用度降低。() 14.刀具前角越大,切屑越不易流出,切削力越大,但刀具的强度越高。() 15.精加工时首先应该选取尽可能大的背吃刀量。() 16.主偏角减小,刀具刀尖部分强度与散热条件变好。() 17.在各方面条件足够时,应尽可能一次铣去全部的加工余量。() 二填空题 1.车削细长轴时,为了避免振动,车刀的主偏角应取。 2.切削用量三要素是指主轴转速, , 。对于不同的加工方法,需要不同的,并应编入程序单内。 3.切削用量中对切削温度影响最大的是,其次是,而影响最小。 4.为了降低切削温度,目前采用的主要方法是切削时冲注切削液。切削液的作用包括、、和清洗作用。 5.铣削过程中所选用的切削用量称为铣削用量,铣削用量包括铣削宽度、铣削深度、、进给量。 6.工件材料的强度和硬度较低时,前角可以选得些;强度和硬度较高时,
第四章 切削力 思考题
第四章切削力 4.1 必备知识和考试要点 4.1.1 切削力的来源,切削合力及其分解,切削功率 1.了解切削力的来源。 2.掌握切削力的合成与分解方法,明确切削力各分力的作用。 3.掌握根据已知条件计算切削功率并确定机床电动机功率的方法。 4.1.2 切削力的测量及切削力的计算机辅助测试 1.了解测量切削力的主要方法。 2.了解电阻应变片式测力仪的工作原理。 3.了解切削力的计算机辅助测试方法。 4.1.3 切削力的指数公式和切削力的预报及估算 1.熟悉切削力的指数公式及公式中各符号的意义。 2,掌握根据切削力计算公式计算单位切削力及单位切削功率的方法。 3.熟练掌握切削力经验公式的建立过程。 4.1.4 影响切削力的因素 1.掌握被加工工件材料对切削力影响的要点。 2.掌握切削用量对切削力影响的要点。 3.能够正确分析背吃刀量、进给量对切削力影响程度不同的原因。 4.能够正确分析切削速度对切削力影响产生的驼峰曲线关系的原因。 5.掌握刀具前角对切削力影响的要点。 6.正确分析主偏角对各切削分力影响程度不同的原因。 7.掌握刀具材料对切削力影响的要点。 8.掌握切削液对切削力影响的要点。 9.掌握刀具磨损对切削力影响的要点。 4.1.5 其它 1.了解切削力的理论公式建立。 2.了解切削力理论公式的不足。 4.2 典型范例和答题技巧 [例4.1] 车削时切削合力F r为什么常分为三个相互垂直的分力?说明这三个分力的作用。 [分析]作用在切削刃上的切削力是沿空间的某一方向,根据切削运动,可以将合力分解成沿各运动方向的分力。车削是按主运动(切削速度)方向、进给运动(进给量)方向、切深运动(背吃刀量)方向进行分解,三个方向的分力在车削时是互相垂直的。同时,车床完成上述三个方向运动的各运动机构也将以各分力为设计、计算的依据参数。而钻削加工是把切削力分解成轴向力和扭矩,同样也是为了便于设计、计算机床功率、运动机构强度等问题。 [答案] 切削合力方向为空间的某一方向,与切削运动中的三个运动方向均不重合,切削力是设计、计算机床功率、校验运动机构强度、合理选择切削用量、提高工件加工精度的一个重要参数或影响因素。所以按照车削的实际情况,将切削力沿车削时的三个运动方向分解成三个力(见例图4.1)。车削时的切削运动为:主运动(切削速度)、进给运动(进给量)、切深运动(背吃刀量)。三个运动方向在车削时是互相垂直的,所以车削时将切削力分解成沿三个运动方向、互相垂直的分力。 各分力的名称、定义及作用为: F t(新国标为F c)——切削力或切向力。它切于加工表面并与基面垂直。F x是计算车刀
金属切削用量选择原则
切削用量的选择原则 数控机床加工的切削用量包括切削速度V c (或主轴转速n)、切削深度a p和进给量f,其选用原则与普通机床基本相似,合理选择切削用量的原则是:粗加工时,以提高劳动生产率为主,选用较大的切削量;半精加工和精加工时,选用较小的切削量,保证工件的加工质量。 1. 数控车床切削用量 1)切削深度a p 在工艺系统刚性和机床功率允许的条件下,尽可能选取较大的切削深度,以减少进给次数。当工件的精度要求较高时,则应考虑留有精加工余量,一般为0.1~0.5mm。 切削深度ap计算公式:a p=2m w d d 式中:d w—待加工表面外圆直径,单位mm d m—已加工表面外圆直径,单位mm. 2)切削速度Vc ①车削光轴切削速度V c光车切削速度由工件材料、刀具的材料及加工性质等因素所确定,表1为硬质合金外圆车刀切削速度参考表。 切削速度Vc计算公式: Vc= 式中:d—工件或刀尖的回转直径,单位mm n—工件或刀具的转速,单位r/min 表1 硬质合金外圆车刀切削速度参考表 工件材料热处理状态 a p=0.3~2mm a p=2~6mm a p=6~10mm f=0.08~0.3mm/r f=0.3~0.6mm/r f=0.6~1mm/r Vc/m·min-1Vc/m·min-1Vc/m·min-1 低碳钢易切热轧140~180100~12070~90
钢 热轧130~16090~11060~80中碳钢 调质100~13070~9050~70 热轧100~13070~9050~70合金工具钢 调质80~11050~7040~60工具钢退火90~12060~8050~70 HBS<19090~12060~8050~70灰铸铁 HBS=190~22580~11050~7040~60高锰钢10~20 铜及铜合金200~250120~18090~120 铝及铝合金300~600200~400150~200 铸铝合金100~18080~15060~100注:表中刀具材料切削钢及灰铸铁时耐用度约为60min。 ②车削螺纹主轴转速n切削螺纹时,车床的主轴转速受加工工件的螺距(或导程)大小、驱动电动机升降特性及螺纹插补运算速度等多种因素影响,因此对于不同的数控系统,选择车削螺纹主轴转速n存在一定的差异。下列为一般数控车床车螺纹时主轴转速计算公式: n≤–k 式中:p—工件螺纹的螺距或导程,单位mm。 k—保险系数,一般为80。 3)进给速度 进给速度是指单位时间内,刀具沿进给方向移动的距离,单位为mm/min,也可表示为主轴旋转一周刀具的进给量,单位为mm/r。
CNC加工中心刀具的选择与切削用量的确定
CNC加工中心刀具的选择与切削用量 的确定 收藏此信息打印该信息添加:佚名来源:未知 刀具的选择和切削用量的确定是数控加工工艺中的重要内容,它不仅影响数控机床的加工效率,而且直接影响加工质量。CAD/CAM技术的发展,使得在数控加工中直接利用C AD的设计数据成为可能,特别是微机与数控机床的联接,使得设计、工艺规划及编程的整个过程全部在计算机上完成,一般不需要输出专门的工艺文件。 现在,许多CAD/CAM软件包都提供自动编程功能,这些软件一般是在编程界面中提示工艺规划的有关问题,比如,刀具选择、加工路径规划、切削用量设定等,编程人员只要设置了有关的参数,就可以自动生成NC程序并传输至数控机床完成加工。因此,数控加工中的刀具选择和切削用量确定是在人机交互状态下完成的,这与普通机床加工形成鲜明的对比,同时也要求编程人员必须掌握刀具选择和切削用量确定的基本原则,在编程时充分考虑数控加工的特点。本文对数控编程中必须面对的刀具选择和切削用量确定问题进行了探讨,给出了若干原则和建议,并对应该注意的问题进行了讨论。 1.数控加工常用刀具的种类及特点 数控加工刀具必须适应数控机床高速、高效和自动化程度高的特点,一般应包括通用刀具、通用连接刀柄及少量专用刀柄。刀柄要联接刀具并装在机床动力头上,因此已逐渐标准化和系列化。数控刀具的分类有多种方法。 根据刀具结构可分为: 1)整体式; 2)镶嵌式,采用焊接或机夹式连接,机夹式又可分为不转位和可转位两种; 3)特殊型式,如复合式刀具,减震式刀具等。
根据制造刀具所用的材料可分为: 1)高速钢刀具; 2)硬质合金刀具; 3)金刚石刀具; 4)其他材料刀具,如立方氮化硼刀具,陶瓷刀具等 从切削工艺上可分为 : 1)车削刀具,分外圆、内孔、螺纹、切割刀具等多种; 2)钻削刀具,包括钻头、铰刀、丝锥等; 3)镗削刀具; 4)铣削刀具等。 为了适应数控机床对刀具耐用、稳定、易调、可换等的要求,近几年机夹式可转位刀具得到广泛的应用,在数量上达到整个数控刀具的30%~40%,金属切除量占总数的80%~90%。 数控刀具与普通机床上所用的刀具相比,有许多不同的要求,主要有以下特点: 1)刚性好(尤其是粗加工刀具),精度高,抗振及热变形小; 2)互换性好,便于快速换刀; 3)寿命高,切削性能稳定、可靠; 4)刀具的尺寸便于调整,以减少换刀调整时间; 5)刀具应能可靠地断屑或卷屑,以利于切屑的排除; 6)系列化,标准化,以利于编程和刀具管理。 2.数控加工刀具的选择
切削用量对切屑变形的影响word资料20页
切削用量对切屑变形的影响: 切削速度:切削塑性金属材料时,切削速度对切削变形的影响呈波浪形; 进给量:进给量增大,则切削厚度增大,切削变形减小,变形因数减小; 背吃刀量:对切屑变形的影响较小。 切屑卷曲和折断机理: 切屑沿刀具前面流出的过程中,受到前面的挤压和摩擦而进一步变形,使得切屑底部被挤而伸长,切屑背面相对缩短,切屑就自然会逆时针卷曲。 如果刀具的前角较小,则切屑流出过程中受到的挤压和摩擦变大,切屑就会卷得更紧。切屑卷曲过程中,若切屑中的弯曲应力达到材料的弯曲强度极限,则切屑就会自行折断。 切屑卷曲与折断的机理解释 ①自由切屑的卷曲机理 由于前刀面和剪切面上对切屑的作用力大小相等,方向相反,但是不共线,因而产生了弯矩,导致切屑卷曲。(刘培德) ②受控切屑的卷曲机理 图1-12a为带倒棱的全圆弧形卷屑槽的卷屑机理,图1-12b为直线形卷屑槽的卷屑机理。都采用卷屑槽的方式实现切屑卷曲的控制。 ③切屑折断的机理 图1-13分别为螺卷屑、发条状屑和C形屑折断的机理,其主要原因
是由于切屑环的内侧拉应力大于切屑材料的弯曲应力极限。 影响切屑卷曲和折断的主要因素: 工件材料性能:工件材料的屈服极限、弹性模量越小,塑性越低,越易折断; 切削用量:切削厚度小,背吃刀量大,切削速度高,断屑难; 刀具前角:前角小,变形大,易折。 影响切削力的因素: 工件材料的影响(系数CF 或单位切削力kc体现) 工件材料的强度、硬度、塑性和韧性越大,切削力越大。 (二)切削用量的影响 背吃刀量ap↑→Ac成正比↑, kc不变, ap的指数约等于1,因而切削力成正比增加; 进给量f↑→Ac成正比↑,但 kc略减小, f 的指数小于1,因而切削力增加但与f 不成正比。 速度v 对F 的影响分为有积屑瘤和无积屑瘤两种情况,在无积屑瘤阶段, v ↑→变形程度↓→切削力减小 切削温度的分布规律: 1.剪切面上各点的温度基本一致; 2.前、后刀面上的最高温度都处于离刀刃一定距离的地方;后刀面的温度降低和升高在极短时间内完成; 3.在剪切区域内,垂直于剪切方向上的温度梯度较大;垂直于前刀面的切屑底层的温度梯度较大;
切削用量对切削力的影响比较讲解
] 3[切削用量对切削力的影响比较 (陕西理工学院 机械工程学院 ) 摘 要:通过分析切削力单因素实验,探讨切削用量对切削力的影响规律; 同时讨论刀具几何参数对切削力的影响,得出一般结论;进而对比说明精密切削切削力的特殊规律。 关键词:切削变形;切削力;刀具;精密切削;规律 1.引言 金属机械加工过程中,产生的切削力直接影响工件的粗糙度和加工精度,同 时也是确定切削用量的基本参数。所以掌握切削用量对切削力的影响规律也显得重要。本文从一般切削和精密切削两个方面对切削用量对切削力的影响规律做初步探讨。 2.金属切削加工机理 金属切削加工是机械制造业中最基本的加工方法之一。金属切削加工是指在金属切削机床上使用金属切削刀具从工件表面上切除多余金属,从而获得在形状、尺寸精度及表面质量等方面都符合预定要求的加工。 2.1切削加工原理 利用刀具与工件之间的相对运动,在材料表面产生剪切变形、摩擦挤压和滑移变形,进而形成切屑。 2.2切削变形 根据金属切削实验中切削层的变形,如图1-2,可以将切削刃作用部位的切削层划分为3个变形区。 第Ⅰ变形区:剪切滑移区。该变 形区包括三个过程,分别是切削层弹 性变形、塑性变形、成为切屑。 第Ⅱ变形区:前刀面挤压摩擦区。 该变形区的金属层受到高温高压作用, 使靠近刀具前面处的金属纤维化。 第Ⅲ变形区:后刀面挤压摩擦区。 该变形区造成工件表层金属纤维化与 图1-2 切削层的变形区 加工硬化,并产生残余应力。
F x F y F z F xy F Z F 22222++=+ =] 1[3.切削力 切削力是指切削过程中作用在刀具或工件上的力,它是工件材料抵抗刀具切削所产生的阻力。 3.1切削力来源 根据切削变形的不同,切削过程中刀具会受到三种力的作用,即: (1)克服切削层弹性变形的抗力 (2)克服切削层塑性变形的抗力 (3)克服切屑对刀具前面、工件对刀具后面的摩擦力 3.2切削力的合成与分解 图2 - 2 切削力合力和分力 图2-2为车削外圆时切削力的合力与分力示意图。图中字母分别表示: N 1、F 1——作用在车刀前刀面的正压力、摩擦力 N 2、F 2——作用在车刀后刀面的正压力、摩擦力 Q 1、Q 2——N1与F 1、N 2与F 2的合力 F ——Q 1与Q 2的合力,即总切削力 一般地,为了研究方便,将总切削力F 按实际运动效果分为以下三个分力: 切削力F z ——垂直于水平面,与切削速度的方向一致,且该分力最大。 径向切削力F y ——在基面内,与进给方向垂直,沿切削深度方向,不做功,但能使工件变形或造成振动。 轴向切削力F x ——在基面内,与进给方向平行。 由图2-2可知,合力与各分力之间的关系为: 其中: k r F xy F x sin =。式中:F xy ——合力在基面上的分力。 k r F xy F y cos =
卧式数控车床如何合理选择切削用量
卧式数控车床如何合理选择切削用量 本文就卧式数控车床如何合理选择切削用量进行探讨。 一. 原始资料:无论编制加工工序卡-即制定工艺方案还是调装设计都需要掌握以下资 料,做为刀具选择.卡具设计以及选择切削用量的依据。 1 工件图:包括形状.尺寸.公差.形位公差.粗糙度和其他技术要求。特别强调的是本序 加工的部位必须明确,用于及可能影响装卡部位的形状要表示清楚。 2.毛坯图:毛坯形状.尺寸,加工余量,材料.硬度等。 3.生产纲领:即年产量或单件时间,这对招标项目尤为重要。 4.验收要求:机床验收时对工件考核什麽项目,有无Cp 值和其它要求。 5.用户对工件定位基准.卡紧面.辅助支承 等要求,或指定参考的卡具样式。 6. 对刀具选择要求:用国产刀具或国外指定厂家 的刀具,特殊刀具是否自备等。 7. 用户单位,件名.件号等也应标明,以便管理。 二 选择切削用量的原则: 1. 总的要求:保证安全,不致发生人身事故或设备事故;保证加工质量。在上述 两项要求的前提下充分发挥机床的潜力和刀具的切削性能,选用较大的切削用量以提高生产率;不应超负荷工作,不能产生过大的变形和震动。 2. 一般原则:切削用量选择的原则是提高生产率,即切削时间缩短。切削时间可按下式计算: . (min)1000p p a f V D L a f n L t ??????=??= πδδ………(1) 式中: L -每次走刀的行程长度 (mm ) δ-工件单边总余量 (mm ) n -主轴转数 (r/min ) D -工件直径 (mm ) αp -吃刀深 (mm ) f -进给量 (mm/r ) V -切削速度 (m/ min ) 从(1)式中可知要使切削时间最短,必须使 V ,f, αp 的乘积为最大。提高 V ,f, αp 都能提高生产率,且影响程度都是一样的。但是对刀具耐用度的影响三者是不相同的。 切削用量与刀具耐用度的一般关系式为: 式中: C R -刀具耐用度系数,与刀具. 工件材料和切削条件有关。 X.Y.Z -指数,分别表示各切削用量对刀具耐用度的影响程度。 用YT5硬质合金车刀切削σb =0.637GP α的低碳钢(f>0.7mm/r )切削用量与刀具耐用度的关 系为: T = 75 .025 .25 p R f V C α?? (3) 从(3)式中可以看出,切削速度V 对刀具耐用度的影响最大,进给量f 次之,吃刀深αp 影响最小。这与三者对切削温度的影响完全一致。反映出切削温度 对刀具耐用度有着很重要的影响。在优选切削用量以提高生产率时,其选择顺序应为:首先尽量选用最大吃刀深αp 然后根据加工条件选用最大的进给量f ,最后才在刀具耐用度或机床功率所允许的情况下选取最大切削速度V 。
浅议切削用量对加工精度的影响
浅议切削用量对加工精度的影响 机械零件的加工必须要保证零件达到图样的要求,满足其加工精度。而尺寸精度、形位精度和表面粗糙度是检验零件加工精度最主要的三个方面。三者任何一项达不到要求都会造成零件质量的下降或报废等问题。其中形状和位置精度可以通过设备,夹具,刀具,工艺等来加以保证,而尺寸精度和表面粗糙度的控制就成了很多人较为伤脑筋的难点!他们往往控制了表面粗糙度,尺寸精度却超差了,而控制了尺寸精度后,表面粗糙度又下降了。本人通过多年的实践总结及潜心研究,知道了造成零件加工误差的因素很多,以下是机械零件在切削加工时造成尺寸误差的原因分析,也是我综合较多书本资料后再结合自己的理解汇总叙述的(仅以车削加工为说明对象)。 1、尺寸计算错误或刻度盘操作错误 这里包含看错图纸;图纸尺寸链计算错误;机床刻度盘松动(不能与手柄作同步运动);操作刻度盘时,未消除其传动间隙等几个方面。 2、量具误差或测量技术误差 这里包含使用量具前未校准量具和没有正确学会使用量具造成的:
比方说常用量具游标卡尺的使用,其尺身上锁紧螺钉的松紧度是影响测量误差的关键因素;使用千分尺时,测量力的手感也很关键;测量时的量点位置是否正确和阅读数值时的视线是否正对刻线等等也会有误差。 以上两方面的误差是初学者容易产生的,下面的几方面的误差因隐蔽性较大,所以不容易引起切削加工人员注意,有时即使我们注意了,也不容易把握它的度。 3、刀具角度误差和刀具磨损钝了产生误差 刀具角度对切削加工的多方面影响都很大,刀具角度要根据其本身材料结合工件材料和加工性质等多方面综合选择的。刀具角度的改变对切削刃口的锋利程度,切削力的大小,切屑厚薄和切屑变形的大小,表面粗糙度的优劣影响都比较明显,对刀尖强度和散热性能的影响也较突出,但是其对尺寸精度的影响是比较隐蔽的,如刀具磨损钝了产生尺寸误差和刀尖装得是否对准机床的旋转中心,对尺寸和表面粗糙度的影响也是比较大的,在数控机床加工中,书上曾经特别提到过车刀要严格对准中心这一点。 4、加工系统的刚性不足导致误差; 加工系统的刚性包含机床、工件和刀具三个方面。机床的功率与切削
影响切削力和切削温度的因素
影响切削力和切削温度的因素 影响因素 被影响的因素力温度 工件材料强度、硬 度 材料的强度、硬度越高,则屈服强度越高,切削 力越大。 材料的强度、硬度越高,温度越高。 塑性、韧 性 在强度、硬度相近的情况下,材料的塑性、韧性 越大,则刀具前面上的平均摩擦系数越大,切削 力也就越大。脆性材料,切削时一般形成崩碎切 屑,切屑与前面的接触长度短,摩擦小,故切削 力较小。 导热系数导热系数越低,温度越高 切削用量背吃刀量 和进给量 进给量f 增大时,切削力有所增加;(程度小) 背吃刀量a p增大时,切削刃上的切削负荷也随之 增大,即切削变形抗力和刀具前面上的摩擦力均 成正比的增加。(程度大) 从切削力和切削功率角度考虑,加大进给量比加 大背吃刀量有利。 切削温度与切削用量的关系式为: ) (C K v f a c z c y x p θ θ θ θ θ θ= 三个影响指数zθ>yθ>xθ,说明切削 速度对切削温度的影响最大,背吃刀量对切削 温度的影响最小。 切削速度切削速度在5~17m/min区域内增加时,积屑瘤高 度逐渐增加,切削力减小; 切削速度继续在17~27m/min范围内增加,积屑 瘤逐渐消失,切削力增加; 在切削速度大于27m/min时,积屑瘤消失,由于 切削温度上升,摩擦系数减小,切削力下降。一 般切削速度超过90m/min时,切削力无明显变化。 在切削脆性金属工件材料时,因塑性变形很小, 刀屑界面上的摩擦也很小,所以切削速度υc 对 切削力F c无明显的影响。 在实际生产中,如果刀具材料和机床性能许可, 采用高速切削,既能提高生产效率,又能减小切 削力。 刀具几何参数前角前角: γo↑→切削变形↓→切削力↓(塑性材 料) 前角γo↑→塑性变形和摩擦↓→切削温度。 但前角不能太大,否则刀具切削部分的锲角过 小,容热、散热体积减小,切削温度反而上升。 前角超过 20 ~ 18后,对降低切削温度 并无明显作用 负倒棱负倒棱参数大大提高了正前角刀具的刃口强度, 但同时也增加了负倒棱前角(负前角)参加切削的 比例,负前角的绝对值↑→切削变形程度↑→切 削力↑; 基本无影响 主偏角Fp=F D cosKr F f=F D SinKr Kr ↑→Fp ↓, Ff ↑(课本P47图1-52) 主偏角κr↑→切削刃工作接触长度↓,切削宽 度b D↓,散热条件变差,故切削温度↑ 刀尖圆弧 半径 rε↑→切削刃圆弧部分的长度↑→切削变形↑ →切削力↑。此外rε增大,整个主切削刃上各点 主偏角的平均值减小,从而使Fp增大、Ff 减小。 基本无影响 刃倾角λs↓→Fp↑, Ff↓,Fc基本不变
切削用量三要素—7
课题切削用量三要素 教学目标1、了解切削用量三要素。 2、掌握切削用量计算公式。 教材分析重点削用量三要素、切削用量计算公式、切削用量的初步选择难点切削速度及其计算公式 教学方法讲授法教学用具 教学过程 切削用量是指背吃刀量p a qqqqc(或切削深度)、进给量f (或进给速度v f )、切削速度c v三者的总称,也称为切削用量三要素。它是调整刀具与工件间相对运动速度和相对位置所需的工艺参数。 一、背吃刀量(p a )(或切削深度) 背吃刀量是指切削时已加工表面与待加工表面之间的垂直距离,用符号ap 表示,单位为mm。 思考题:现有Φ30的毛坯,一次走刀加工成Φ26,试问背吃刀量是多少? p a =(30-26)/2=2mm 背吃刀量的选择: 余量不大,一次走刀切除多余的材料,只留下精加工余量。 1、粗加工 余量太大,可分多次切削,但第一次的背吃刀量尽可能大。 2、精加工粗加工后留下的余量,精加工时应一次进给切削完成。 2 m w p d d a - = w d:待加工表面直径mm m d:已加工表面直径mm
c v 教 学 过 程 二、进给量(f )(或进给速度 v f ) 进给量是指刀具在进给方向上相对工件的位移量,即工件每转一圈,车刀沿进给方向移动的距离,用符号 f 表示,单位为 mm/r ,如图所示。 进给量的选择: 1、为了缩短加工时间,提高效率: 粗加工时应选用较大的进给量。 2、为了保证表面质量及加工精度: 精加工时应选用较小的进给量。 三、切削速度(c v ) 切削速度是指切削刃上选定点相对于工件主运动的瞬时速度,用符号c v 表示,单位为m/min 。当主运动是旋转运动时,切削速度是指圆周运动的线速度,即: ——切削速度,m/min n ——主轴转速,r/min d ——工件待加工表面直径,mm π ——圆周率, 3.14 例1:车削直径为50mm 的工件,若选主轴转速为600r/min ,求切削速度的大小? 解:由公式得: 练习: 车削直径为300mm 的铸铁带轮外圆,若切削速度为60m/min ,求车床主轴转速? 解:由公式 得: d v n c π1000=min /2.94min /1000 5014.36001000m m d n V c =??==πmin /69.63min /300 14.36010001000r r d v n c =??==π
刀具后刀面磨损量对切削力及加工表面粗糙度的影响
4 李亚非.G C 杯形砂轮修整碟形金刚石砂轮实验研究.金刚石与磨料磨具工程,2003(10):28~30 5 阎秋生,田中宪司,庄司克雄.小直径C BN 砂轮的磨削特 性研究———砂轮修整方法及砂轮要素参数选择.制造技术与机床,1999,9 6 庄司克雄.陶瓷结合剂金刚石砂轮的修整研究Ⅲ(1).金 刚石与磨料磨具工程,1993(1) 第一作者:于晓娟,硕士研究生,北京理工大学机械与车辆工程学院,100081北京市 收稿日期:2004年10月 刀具后刀面磨损量对切削力及加工表面粗糙度的影响 吴泽群 刘亚俊 汤 勇 陈 平 华南理工大学 摘 要:通过切削试验探索了在相同的工件材料、刀具材料、切削参数(切削深度、进给量)和不同的刀具磨损状态(后刀面磨损量)下,刀具后刀面磨损量(VB )对切削过程中的切削力及工件表面粗糙度的影响,并对这些影响的产生机理进行了讨论。 关键词:后刀面磨损量, 切削力, 表面粗糙度 E ffect of Tool Flank Wear on Cutting Force and Surface R oughness Wu Z equn Liu Y ajun T ang Y ong et al Abstract :The effect of the tool flank wear (VB )on the cutting force and the sur face roughness is studied ,basing on the ex 2periments with the same w orkpiece materials ,same tool materials ,same cutting parameters (depth of cut ,feed rate )and different tool conditions (focusing on different tool flank wears ).The mechanism production of these effects is als o discussed. K eyw ords :tool flank wear , cutting force , sur face roughness 1 引言 切削力是描述切削过程的一个基本参数。近年来,随着加工过程自动控制技术的发展,切削力已成为适应和控制切削过程的一个重要反馈参数。切削力的变化直接决定着切削热的产生、分布,并影响刀具的磨损状况和使用寿命,进而影响零件被加工表面的加工精度和已加工表面质量。 影响切削力的因素有很多,诸如车床的转速、切削深度、进给量、后刀面磨损量等。刀具的磨损量不仅对切削力的大小有影响,而且在金属的切削过程中,刀具的磨损与破损是影响加工零件精度和表面质量的重要因素,严重的刀具磨损还会引起切削颤振,损坏机床、刀具、工件等。 国内外对切削力影响因素的研究大多数都着眼于车床转速、切削深度等参数的选择,对刀具磨损对切削力影响的研究相对较少,而且有关刀具磨损对工件表面质量影响的研究也不多,因此,研究刀具磨损对切削力和表面粗糙度的影响具有一定的现实意义。 2 切削试验 211 试验条件 (1)试验设备:C M6140车床; 刀具材料:硬质合金Y W ; 被切削材料:45钢;(2)测量仪器:K istler 9441测力仪、K istler 5019A 多通道放大器、TR200粗糙度仪 。 图1 试验系统 212 试验参数的选择 刀具后刀面磨损量VB 是刀具磨损的重要指标之一。在一定范围内选择VB 的六个值,分别为0(未磨损的)、011mm 、012mm 、013mm 、014mm 、015mm 。 图2 后刀面磨损量VB 7 32005年第39卷№5
数控加工中切削用量的合理选择
数控加工中切削用量的合理选择 【摘要】文章介绍了切削用量的三要素,并对数控机床加工时切削用量的合理选择进行了详细阐述,为数控机床编程与操作人员提供参考。 【关键词】切削用量;加工质量;刀具耐用度;选择原则。 前言:数控加工中切削用量的原则是,粗加工时,一般以提高生产率为主, 但也应考虑经济和加工成本;半精加工和精加工时,应在保证加工质量的前提下,兼顾切削效率、经济性和加工成本。具体数值应根据机床说明书、切削用量手册,并结合经验而定。切削用量是表示机床主运动和进给运动大小的重要参数。切削用量的确定是数控加工工艺中的重要内容,切削用量的大小对加工效率、加工质量、刀具磨损和加工成本均有显著影响 一、切削用量的选择原则 数控加工中选择切削用量,就是在保证加工质量和刀具耐用度的前提下,充分发挥机床性能和刀具切削性能,使切削效率最高,加工成本最低。 (一) 加工质量:加工质量分为加工精度和加工表面质量。 ⒈加工精度是指零件加工后实际几何参数(尺寸、形状和位置)与理想几何参数相符的程度。符合程度愈高,加工精度愈高。实际值与理想值之差称为加工误差,所谓保证加工精度,即指控制加工误差。 ⑴尺寸精度:加工表面的实际尺寸与设计尺寸的尺寸误差不超过一定的尺寸公差范围。在国标中尺寸公差分20级(IT01、IT0、IT1~IT18)。尺寸精度的获得方法: ①试切法:试切——测量——调整——再试切。用于单件小批生产。 ②调整法:通过预调好的机床、夹具、刀具、工件,在加工中自行获得尺寸精度。用于成批大量生产。 ③尺寸刀具法:用一定形状和尺寸的刀具加工获得。生产率高,但刀具制造复杂。 ④自动控制法:用一定装置,边加工边自动测量控制加工。切削测量补偿调整。 ⑵几何形状精度:加工表面的实际几何要素对理想几何要素的变动量不超过一定公差范围。在国标中形状公差有六项:直线度、平面度、圆度、圆柱度、线轮廓度、面轮廓度。几何形状精度的获得方法: 成形运动法 ①轨迹法:利用刀具与工件间的相对运动轨迹来获得形状。 ②成形法:利用成形刀具加工获得表面形状。 ③展成法:利用刀具与工件相对运动使工件被刀具切削成一定形状的包络线。 非成形运动法:人工修配、样板加工、划线加工等。 ⑶相互位置精度:加工表面的实际几何要素对由基准确定方向或位置的理想几何要素的变动量。在国标中位置公差有八项:平行度、垂直度、倾斜度、同轴度、对称度、位置度、圆跳动、全跳动。相互位置精度的获得主要由机床精度、
浅析切削加工中影响切削温度的主要因素
浅析切削加工中影响切削温度的主要因素 发表时间:2018-01-15T12:14:25.140Z 来源:《知识-力量》2017年10月上作者:潘勇吴志慧 [导读] 本文主要从切削用量、刀具几何参数、刀具磨损、工件材料等几个方面进行分析和阐述,从而了解这些因素在切削加工时所产生的切削温度所带来的影响。 潘勇吴志慧 重庆市机械高级技工学校 摘要:在金属切削加工中,切削温度是一个难以回避的重要问题,而影响切削温度的因素主要是刀具参数和被加工材料等。本文主要从切削用量、刀具几何参数、刀具磨损、工件材料等几个方面进行分析和阐述,从而了解这些因素在切削加工时所产生的切削温度所带来的影响。 关键词:切削用量几何参数刀具磨损工件材料 在金属切削的过程中刀具进行切削所消耗的功率大部分都转变为了热能。研究数据表明,切削过程中所需消耗掉的能量绝大部分都是要转换成热量的,而在这一过程中,所产生的切削热会让整个切削区域的温度逐渐地变高,进而影响到整个刀具的磨损和工件的尺寸精度并造成零件废品的出现。所以,我们对切削温度进行研究将对提高生产效率和产品质量有着重要的意义。下面就着手分析影响切削温度的主要因素。 一、切削用量对切削温度的影响 1.切削速度 切削时,我们将切削速度不断提高,这时切削温度数值会明显地上升。因为切屑在通过前刀面时高速的流出,它们之间会这个过程中发生剧烈的摩擦并随之产生大量的切削热能,如果将切削速度设定在很高的数值,就会在较短的时间范围内,因摩擦生成的热量就不能及时向切屑自身传导,而将大量切削热积聚在刀具和工件上,使它们之间相接触位置的切削温度极大地升高。 2.进给量 当我们增大进给量时,在一定的时间范围内金属材料的切除量将会不断地增多,这时切削热会急剧地增多,切削温度也就会不断地上升。与切削速度相比较,进给量在增大时,切削温度不会随着幅度值的升高而显著提高很多。 3.背吃刀量 研究表明,在切削用量中背吃刀量在切削时对切削温度的影响是非常小的。因为背吃刀量在增大之后,在切削区域所产生的热量虽然会成正比例的增加,但是整个切削刃的工作长度在这时会参与到切削加工中去,从而改善切削的散热条件,因此在这个过程中切削温度并不会显著地升高。 由上可知,刀具磨损和寿命受到切削温度的影响很较大,为能够有效地将切削温度控制在一定的范围内以提高刀具寿命,就需选择较大的背吃刀量和进给量,而选择一个合理的的切削速度来控制切削温度,提高刀具使用寿命,从而提升加工效率。 二、刀具几何参数对切削温度的影响 1.前角γo 切削过程中的工件的变形以及刀具之间的摩擦会因前角的大小而发生变化,当前角加大,切削温度就会降低;反之切削温度就会升高。当前角选择在20°左右时,此时切削温度的影响会小很多,原因是楔角发生变小的情况促使散热面积减小。所以刀具前角的选择将会对切削温度产生比较大的影响。 2.主偏角κr 当我们将主偏角进行加大后,这时刀具切削刃的实际工作长度就会变短,而造成切削热集中在一定的范围内;但如果刀尖角这时减小,就会使散热条件变差,造成切削温度上升。 由上可知,当增大刀具的前角,虽然可以使切屑变形加大,切屑与刀具前刀面之间的摩擦值减小,从而达到减少切削热,降低切削温度的效果。但如果前角选择过于太大,刀具自身的传导热条件也会变得很差,反而造成散热不利的情况,达不到降低切削温度的作用。而当主偏角选择较小时,切削时实际参与切削的刀刃长度就会增加,这样就能够形成利于散热的条件,从而降低切削温度。 三、刀具磨损对切削温度的影响 在切削进行到一定程度时,刀具慢慢地发生磨损,然后刀刃变钝,金属变形程度增大,此时加工刀具的后刀面在和工件相互接触处的摩擦也会大大的增加,所以,切削温度的上升往往发生在刀具磨损之后。当后刀面上的磨损量越来越大时,其上升的速度就会越来越快。我们通过试验得知,在车削加工的过程中,动态的切削温度会随着刀具的磨损增大而快速地升高。当刀具磨损较小时,动态的切削温度会随刀具的磨损而慢慢地上升,当刀具磨损程度达到一定数值时,在这个过程中会促使其动态切削温度加快上升的速度。 四、工件材料对切削温度的影响 1.当加工材料的硬度、强度数值都很高时,切削时需要消耗的功率自然就会越多,它在这时所产生的切削热也会越多,造成切削温度升高的情况出现。 2.工件材料自身的导热系数值,也会对散热产生直接且明显的影响。 3.在切削脆性材料时,比如说灰铸铁,它在切削时其金属变形的可能性很小,但从金属材料上切除的切屑会呈现出细小的崩碎形状,这样它与刀具前刀面之间产生的摩擦就会变小,故只会产生比较少的切削热,反之,切削塑性材料时产生的切削温度会比脆性材料时的温度高一些。 五、切削液对切削温度的影响 为积极改善刀具和工件之间的散热条件。在切削加工时,可以浇注一定数量的切削液来有效地降低切削温度。切削液在生产中除了能够起到冷却作用外,它还能够有效地起润滑、清洗和防生锈的作用。因此,合理使用切削液能有效地降低切削温度。 综上所述,切削用量、刀具几何参数、刀具磨损、工件材料、切削液对切削温度都会产生重要的影响,进而影响生产加工效率、产品质量以及增加加工成本。因此,在实际生产加工中,如何降低加工时的切削温度,以此来提高产品质量有着重要的现实意义。
数控车削切削用量的选择原则、方法及主要问题
数控车削切削用量的选择原则、方法及主要问题 数控车削加工中的切削用量包括背吃刀量ap、主轴转速n或切削速度vc(用于恒线速度切削)、进给速度vf或进给量f。这些参数均应在机床给定的允许范围内选取。 切削用量的选用原则 (1)切削用量的选用原则 粗车时,应尽量保证较高的金属切除率和必要的刀具耐用度。 选择切削用量时应首先选取尽可能大的背吃刀量ap,其次根据机床动力和刚性的限制条件,选取尽可能大的进给量f,最后根据刀具耐用度要求,确定合适的切削速度vc。增大背吃刀量ap可使走刀次数减少,增大进给量f有利于断屑。 精车时,对加工精度和表面粗糙度要求较高,加工余量不大且较均匀。选择精车的切削用量时,应着重考虑如何保证加工质量,并在此基础土尽量提高生产率。因此,精车时应选用较小(但不能太小)的背吃刀量和进给量,并选用性能高的刀具材料和合理的几何参数,以尽可能提高切削速度。 (2)切削用量的选取方法 ①背吃刀量的选择粗加工时,除留下精加工余量外,一次走刀尽可能切除全部余量。也可分多次走刀。精加工的加工余量一般较小,可一次切除。在中等功率机床上,粗加工的背吃刀量可达8~10mm;半精加工的背吃刀量取0.5~5mm;精加工的背吃刀量取0.2~1.5mm。 ②进给速度(进给量)的确定粗加工时,由于对工件的表面质量没有太高的要求,这时主要根据机床进给机构的强度和刚性、刀杆的强度和刚性、刀具材料、刀杆和工件尺寸以及已选定的背吃刀量等因素来选取进给速度。精加工时,则按表面粗糙度要求、刀具及工件材料等因素来选取进给速度。进给速度νf 可以按公式ν f =f×n计算,式中f表示每转进给量,粗车时一般取0.3~0.8mm /r;精车时常取0.1~0.3mm/r;切断时常取0.05~0.2mm/r。 ③切削速度的确定切削速度vc可根据己经选定的背吃刀量、进给量及刀具耐用度进行选取。实际加工过程中,也可根据生产实践经验和查表的方法来选取。粗加工或工件材料的加工性能较差时,宜选用较低的切削速度。精加工或刀具材料、工件材料的切削性能较好时,宜选用较高的切削速度。切削速度vc确定后,可根据刀具或工件直径(D)按公式n=l000vc/πD 来确定主轴转速n(r/min)。在工厂的实际生产过程中,切削用量一般根据经验并通过查表的方式进行选取。常用硬质合金或涂层硬质合金切削不同材料时的切削用量推荐值见表1表2为常用切削用量推荐表,供参考。
第十一章 切削用量的制定
第十一章切削用量的制定 切削用量的制定直接影响生产效率和加工成本。学习本章后应能够根据具体条件和要求,正确地选择切削用量。 11.1 必备知识和考试要点 1.了解切削用量的制定原则。 2.掌握粗加工时切削用量的选择方法。 3.明确限制选择切削用量的因素和解决办法。 11.2 典型范例和答题技巧 [例11.1] 选择切削用量的原则是什么?从刀具耐用度出发时,按什么顺序选择切削用量?从机床动力出发时,按什么顺序选择切削用量?为什么? [答案] 选择切削用量的原则是:首先选取尽可能大的背吃刀量αp,其次要在机床动力和刚度允许,又能满足加工表面粗糙度的前提下,选取尽可能大的进给量厂,最后根据确定的刀具耐用度选取或计算切削速度v。 以刀具耐用度选择切削用量时,选择的顺序应为αp—f—v。其理由可从刀具耐用度表达式T=C T/v X f Yαp Z中,由于X>Y>Z,即切削速度v对刀具耐用度影响最大,其次是进给量f,背吃刀量αp的影响最小。按这个顺序选择切削用量,得到的生产率最高。如果生产率不变,按这个顺序选择切削用量,刀具耐用度最高。 根据机床动力选择切削用量时,选择的顺序应为.f—v—αp. 其理由从机床功率的计算 公中,由于 1=X Fz>Y Fz>n Fz; 当nF z=0时,影响切削功最小的是f,其次是v与αp;当nF z<0时,通常X,>1十nF,影响切削功率最小的是f,其次是v,最后是αp所以,从机床动力考虑,理论上首先应按影响功率最小的f、其次v、最后αp的顺序选择切削用量。但实际上,考虑αp取小值时,会增加走刀次数,从而增加了辅助工时,因此生产中一般仍按αp—f—v的顺序选择切削用量,即先选择尽可能大的αp,其次选择尽可能大的f, 最后确定v。 [例11.2] 粗加工时进给量选择受哪些因素限制?当进给量受到表面粗糙度限制时,有什么办法增加进给量,而保证表面粗糙度要求? [答案] 粗加工时切削力很大,合理的进给量应是工艺系统所能承受的最大进给量。最大进给量主要受以下因素限制:(1)机床进给机构的强度;(2)车刀刀杆的强度和刚度; (3)工件装夹刚度;(4)硬质合金或陶瓷刀片的强度。 半精加工和精加工时,进给量的选择受到表面粗糙度的限制。此时为减小加工表面粗糙度,可适当增大刀尖圆弧半径γε、减小副偏角κr9,采用修光刃等办法。此外,可增大前角γo,提高刀具刃磨质量,选用有效的切削液等措施,以减小积屑瘤和鳞刺的不利影响。 [例11.3] 如果选定切削用量后发现超过机床功率时,应如何解决? [答案] 理论上影响机床功率大小的因素排列顺序是αp—v—f,所以,选定的切削用量超过机床功率时,也应按上述顺序减小切削用量。但考虑减小αp,会增加走刀次数,增加辅助工时,所以在不希望增加走刀次数的情况下,首先应适当降低v,然后再考虑减小f。 [例11.4] 制定切削用量时,影响切削速度的因素有哪些?解释其原因。 [答案] 制定切削用量时,依次选择背吃刀量αp和进给量f后,可用计算或查表来选择切削速度v。从公式和表格中可以看出影响切削速度的因素有:(1)背吃刀量αp、进给量f与速度v成反比例关系,即粗加工时,由于αp和f均较大,故应选择较低的v;精加工时,αp 和f均较小,故应选择较高的v。(2)工件材料的性能影响切削速度v。 工件材料强度、硬度较高时,应选较低的v,反之则选较高的v;工件材料加工性愈差,则v也选得愈低。(3)刀具材料的性能影响切削速度v。刀具材料切削性能愈好,v可选得愈
影响切削用量的因素
影响切削用量的因素有: 机床切削用量的选择必须在机床主传动功率、进给传动功率以及主轴转速范围、进给速度范围之内。机床—刀具—工件系统的刚性是限制切削用量的重要因素。切削用量的选择应使机床—刀具—工件系统不发生较大的“振颤”。如果机床的热稳定性好,热变形小,可适当加大切削用量。 刀具刀具材料是影响切削用量的重要因素。表1是常用刀具材料的性能比较。 数控机床所用的刀具多采用可转位刀片(机夹刀片)并具有一定的寿命。机夹刀片的材料和形状尺寸必须与程序中的切削速度和进给量相适应并存入刀具参数中去。标准刀片的参数请参阅有关手册及产品样本。 表1 常用刀具材料的性能比较 工件不同的工件材料要采用与之适应的刀具材料、刀片类型,要注意到可切削性。可切削性良好的标志是,在高速切削下有效地形成切屑,同时具有较小的刀具磨损和较好的表面加工质量。较高的切削速度、较小的背吃刀量和进给量,可以获得较好的表面粗糙度。合理的恒切削速度、较小的背吃刀量和进给量可以得到较高的加工精度。 冷却液冷却液同时具有冷却和润滑作用。带走切削过程产生的切削热,降低工件、刀具、夹具和机床的温升,减少刀具与工件的摩擦和磨损,提高刀具寿命和工件表面加工质量。使用冷却液后,通常可以提高切削用量。冷却液必须定期更换,以防因其老化而腐蚀机床导轨或其他零件,特别是水溶性冷却液。
以上讲述了机床、刀具、工件、冷却液对切削用量的影响。切削用量的选择原则,下面主要论述铣削加工的切削用量选择原则。 铣削加工的切削用量包括:切削速度、进给速度、背吃刀量和侧吃刀量。从刀具耐用度出发,切削用量的选择方法是:先选择背吃刀量或侧吃刀量,其次选择进给速度,最后确定切削速度。 1.背吃刀量a p或侧吃刀量a e 背吃刀量a p为平行于铣刀轴线测量的切削层尺寸,单位为㎜。端铣时,a p为切削层深度;而圆周铣削时,为被加工表面的宽度。侧吃刀量a e为垂直于铣刀轴线测量的切削层尺寸,单位为㎜。端铣时,a e为被加工表面宽度;而圆周铣削时,a e为切削层深度,见下图。 铣削加工的切削用量图 背吃刀量或侧吃刀量的选取主要由加工余量和对表面质量的要求决定: ①当工件表面粗糙度值要求为Ra=12.5~25μm时,如果圆周铣削加工余量小于5㎜,端面铣削加工余量小于6㎜,粗铣一次进给就可以达到要求。但是在余量较大,工艺系统刚性较差或机床动力不足时,可分为两次进给完成。 ②当工件表面粗糙度值要求为R a=3.2~12.5μm时,应分为粗铣和半精铣两步进行。粗铣时背吃刀量或侧吃刀量选取同前。粗铣后留0.5~1.0㎜余量,在半精铣时切除。