辊弯成型CAD
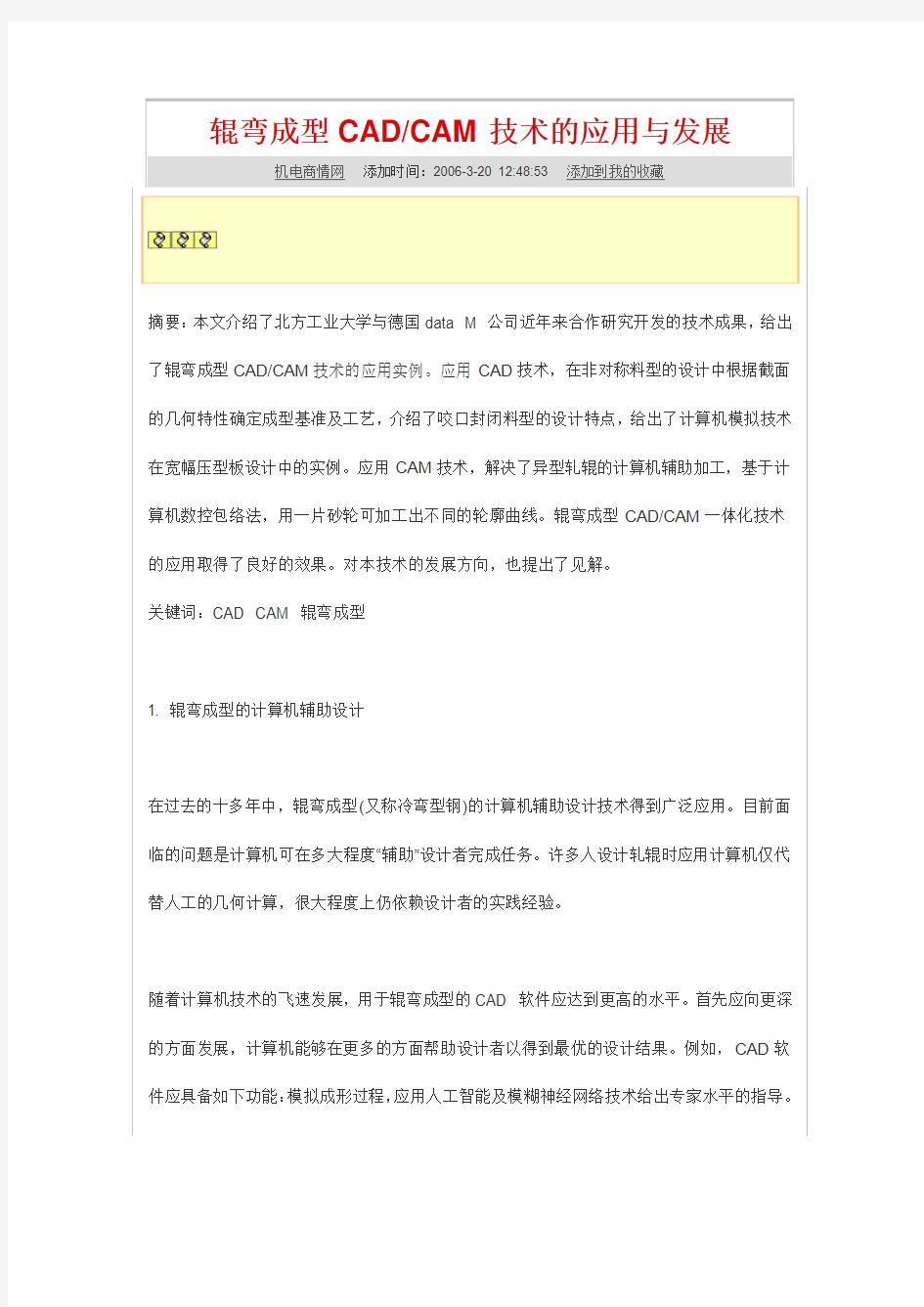

摘要:本文介绍了北方工业大学与德国data M 公司近年来合作研究开发的技术成果,给出了辊弯成型CAD/CAM技术的应用实例。应用CAD技术,在非对称料型的设计中根据截面的几何特性确定成型基准及工艺,介绍了咬口封闭料型的设计特点,给出了计算机模拟技术在宽幅压型板设计中的实例。应用CAM技术,解决了异型轧辊的计算机辅助加工,基于计算机数控包络法,用一片砂轮可加工出不同的轮廓曲线。辊弯成型CAD/CAM一体化技术的应用取得了良好的效果。对本技术的发展方向,也提出了见解。
关键词:CAD CAM 辊弯成型
1. 辊弯成型的计算机辅助设计
在过去的十多年中,辊弯成型(又称冷弯型钢)的计算机辅助设计技术得到广泛应用。目前面临的问题是计算机可在多大程度“辅助”设计者完成任务。许多人设计轧辊时应用计算机仅代替人工的几何计算,很大程度上仍依赖设计者的实践经验。
随着计算机技术的飞速发展,用于辊弯成型的CAD 软件应达到更高的水平。首先应向更深的方面发展,计算机能够在更多的方面帮助设计者以得到最优的设计结果。例如,CAD软件应具备如下功能:模拟成形过程,应用人工智能及模糊神经网络技术给出专家水平的指导。
其次CAD技术向更广的领域发展,计算机辅助制造,生产管理,成本核算,质量控制以及CAE和CIMS。由德国data M开发的COPRA是解决辊弯成型设计的集成软件。
以下是由COPRA完成的部分冷弯型钢断面的实例。
1.1 非对称断面
日本拓殖大学的小奈弘教授给出了非对称断面成型道次的估算方法。与对称断面相比,不平衡的扭矩会导致板带的扭曲。断面成型过程中板带的几何变形与其静力学特性紧密相关。作者发现若以截面的一个惯性轴作为展开的基准线,一些非对称断面可得到很好的成型质量。
1.1.1 以惯性主轴作为展开的基准
用于集装箱的部件(图1)是一非对称截面。某公司以最长的直线段作为成型的水平基准,共用12道次成型,并产生明显的扭屈。用COPRA可方便地计算出主惯性轴的角度,以其中一个惯性轴作为成型基准面,只需6道次就获得了比前方法质量更好的断面。
图1 集装箱部件的成型辊花图图2 两侧成形角不同的V型截面图2是天花板吊顶的部件,虽然它的形状简单,但它的成型却不容易,原因在于必须满足板厚0.4mm的情况下每米成型长度上的各向最大挠度不大于0.5mm。成型这一高精度的部件,作者采用的方法是以惯
性主轴之一为成型基准,两侧的变形角按不同的值给出,以使两侧的变形扭矩平衡。此外要保证它的脊线的平直度,轧辊的安装调整也是很重要的。采用上述措施,最终生产出的料型
达到每米长直线度误差小于0.3mm。
1. 1.2 以水平轴线作为展开的基准
图3是按用户要求生产的另一种天花板吊顶用的部件。这是由对称的"T" 型吊顶龙骨简化的。尽管它的左侧变形远大于右侧,但它的一个惯性主轴与水平面夹角接近于0度。这种情况下,作者采用了以最长的直线体素为水平位置的展开基准。
图3 T型断面的成形步骤图4是电控柜部件的截面静力学特性。两惯性主轴的交点靠近右侧体素,作者以右侧体素作为成形展开的第一基准,将底部的水平体素作为第二成形基准。
图4 电控柜部件的静力学特性
图5 非对称断面电控柜部件的成形辊花图1.2 咬口料型的成型
一些钢门窗料采用彩色涂层钢板为原料经辊弯成形工艺制成。为保证门窗的强度采用封闭截面。焊接方法将破坏钢板表面,因而广泛采用了咬口结构。为避免咬口过程中发生干涉,避
免对彩色涂层表面的损伤,同时也保证门窗的气密水密性及配合要求,要求辊型设计及制造达到较高的精度。辊的表面粗糙度Ra ≤ 0.63μm,辊的圆周速度尽可能接近驱动速度,若辊的线速度差较大时,设计上应采用空转结构。
对于一般的辊弯成型,成形辊轴线为水平或垂直两种配置。咬口料型的成形广泛应用了空间结构的辅助辊,这种辅辊结构安装在两道主辊之间,轧辊轴线可为任意倾斜角度,它的结构形式不同于主辊及立辊。图6表示了一种辅助辊的装配关系示意。为得到精确的尺寸和形状,在最后的成型道次中采用了芯子。图7是一种彩色涂层钢窗料的成形工艺图。
图6 用于咬口料型的辅助辊装配示意图1.3 宽幅压型板
压型板大多是由又宽又大的薄板经辊弯成型的,极易出现各种缺陷。小奈弘教授依据他的实验给出了十分有用的结论:边浪、袋形波等缺陷是由于变形的应力过大或拉压应力的不同分布造成的。在设计过程中若能够计算出成形区域的应力、应变值,就可以避免缺陷的产生。应用有限元技术以及实验结果,已知在每个道次的成型过程中,板上变形区某一点的应变状态是拉应力和压应力交替变化的,即使很薄的板在不同的层面上应变状态也是不同的。一个重要的结论是:纵向变形是引起诸如残余内应力、边波等缺陷的主要原因[3]。
由data M及其合作者开发的变形技术模块(DTM)是在有限元法和大量实验基础上,根据几何变形条件和材料特性,就能在计算机上实现辊弯成型的变形模拟。DTM可给出每个道次的最大纵向应变,也可分别计算出板的上、中、下层的拉应变和压应变。如果最大的拉应变
超过材料的屈服点(对低碳钢最大值为0.35%),或最小压缩应变低于某一值(例如小奈弘教授给出的值为小于0.3*10-4),就会产生缺陷。根据在计算机屏幕上得到的结果,就可修改变形顺序和成型角度。用计算机模拟,我们可预测在那一变形道次上会产生缺陷,然后修改设计。应用DTM模拟技术,我们为很多企业作过辊弯成型的计算机优化。一些企业在试制中出现问题,我们将他们的设计数据输入计算机,发现在某些道次上应变峰值过大,这与试轧时该道次产生变形缺陷并伴随很大噪音的情况是完全一致的。经修改设计后,这些压型板顺利成型。图8给出了宽幅压型板计算机模拟的一个实例。
图8 一个压型板的计算机模拟结果2. 辊弯成型的计算机辅助制造
实现一个复杂断面的辊弯成型需要上百个形状各异的轧辊。轧辊的辊型轮廓与板料的成型密切相关,保证成型部位的几何坐标的准确性是十分重要的。轧辊的轴向精度要比起径向精度更重要。实际加工过程,使用通用量具,轧辊的径向测量要比轴向容易得多;使用传统的车床加工,轴向精度的控制要比径向难很多。计算机数控技术可很好地解决异型辊的加工问题。
2.1 CNC加工轧辊
使用8 工位刀台的数控车床,加工出硬度HRC58-62的轧辊(见图9)。使用特殊的陶瓷刀具,可得到相当好的表面质量。作者采用的是两坐标联动的、控制分辨率为0.001mm 的数控系
统。
图9 CNC 车床加工的轧辊由于每个轧辊的形状及尺寸均不相同,采用“首件试切法”检验数控程序是不可行的。一般情况下,手工编程的低效率会影响数控功能的发挥。数据运算和程序编制很难避免错误,而任何错误都可能会造成工件报废或严重的机床及人身事故。计算机辅助制造技术可自动生成数控程序,并检验模拟数控指令。COPRA 可根据CAD数据,按照不同的机床数控格式自动生成NC代码,并可在计算机屏幕上用动画的方式模拟刀具的
运行轨迹。
2.2 计算机通讯
作者将辊弯成型的CAD 和CAM 技术,从设计到制造的全过程实现计算机的无缝集成。过去数控程序的输入是靠手工方式一个码一个码地键入,一个较长的程序要10分钟左右,与完成一个零件的时间相差不多。人工输入很难避免错误,而任何错误都会造成工件的报废或机床事故。采用计算机与数控机床的通讯接口技术,可将编好的程序快速准确地送到数控机床,提高了机床的利用率。由于实现了计算机与数控机床之间的通讯,几秒钟之内可实现上千条语句的传送。一张3寸的小磁盘可存储2000-3000片轧辊的加工数据。对于复杂型面轧辊的精加工,可提高机床的利用率40-50%。辊片数据的保存、重复生产及辊片的修复
是十分方便的。
2.3 计算机数控包络磨床
异型轧辊广泛应用于焊接钢管生产,过去它的磨削加工是件困难的事情。有些企业采用成型法磨削,每种圆弧采用一个规格的砂轮,不但砂轮的数量极多而且无法加工复杂轮廓的辊型。要实现高硬度异型辊面的精密磨削,基于包络原理的计算机数控可很好地解决这一问题。
根据共轭曲面中的包络原理,可在砂轮曲率半径不变的条件下,通过控制砂轮轨迹的方法得
到一条包络出的平面轮廓曲线(见图10)。
图10 包络曲线与磨床砂轮的控制轨迹设辊型轮廓为一平面曲线,而砂轮外轮廓为圆Γ的一
部分其方程为:
根据坐标变换及包络条件,包络曲面的一侧为:
该方程中的曲线Γ0 即为数控加工时控制的轨迹方程:
对于任意平面轮廓曲线,用包络法磨削不产生干涉及过切的判定条件如下:
对于凸的曲线:
则砂轮在磨削过程中可包络出全部曲线轮廓。
对于凹曲线:
则要求砂轮半径R≤ρmin
其中ρmin 是曲线上的最小曲率半径,任一点的曲率半径为:
在计算机数控包络磨床上,用一片砂轮可磨出各种曲率的凸曲线和曲率半径不小于砂轮半径的凹曲线。对于各种不同类型曲线的矫直辊的加工,只要编制不同的程序就可,这在普通磨床上是无法实现的。砂轮磨损后的修复可利用程序设定,用金刚石滚轮或刀头按程序修整。因而砂轮的修整也实现了程序化。这种计算机数控包络磨床已用于3个轧辊制造厂。
技术展望
作为一种新技术,辊弯成型CAD/CAM 的生命力也在于不断地创新和发展。我们的目标是根据市场需求,不断地开发新技术,将成熟的技术应用于生产实际,为客户提供优质服务。众所周知,在辊弯成型领域尚有很多亟待解决的问题,我们还未完全实现从“空缺的艺术”向科学的转变。因其涉及到复杂的塑性三维变形、材料特性、轧机及辅助设备、轧制的操作工艺参数、冷却润滑等诸多方面因素。单纯用一个数学模型是无法解决的,人工智能和专家系统是解决这一问题的方向。建立一个完整的系统,目前的困难在于专家知识的积累和获取。我们愿将这些专家知识转化为经计算机推理可供实际应用的软件。将专家知识变为共同经验,避免重复的探索和弯路,促进全行业的发展和繁荣,我们应当将此作为当前及今后工作
的目标。
参考文献
[1] H. Ona, T. Jimma and H. Kozono: A Computer Aided Design System for Cold Rollforming Proc. 1st Int. Conf. Technology of Plasticity. Sept.(1984).pp.508-513 [2] H. Ona, T. Jimma, H. Kozono, T. Nakako: A Computer Aided Design System fo r Forming Wide profile Section and pipe Sections. Bull. P.M.E. No.59.March 1987 p
p.1-9
[3] A. Sedlmaier: Reverse Engineering & Simulation Technologies for the Design an
d Manufactur
e o
f Tube Mill Rolls. Tube 2000 Toronto June 11-14,1996
[4] A. Sedlmaier: Forming Round Tube to Special Shapes; Software Solution for De termining and Designing High Quality Roll Tools and Drawing Rings, Tube and Pip
e Technology, March/April 1998, pp.66-69.
超薄镀锌板辊弯成形回弹工艺
第6期(总第175期) 2012年12月机械工程与自动化 MECHANICAL ENGINEERING & AUTOMATIONNo.6 Dec. 文章编号:1672-6413(2012)06-0042-0 3超薄镀锌板辊弯成形回弹工艺分析 范 琦 (北方工业大学机电研究院,北京 100144 )摘要:对于超薄镀锌板,厚度薄回弹量大难以控制是运用辊弯成形方法中的难点之一。基于ABAQUS有限元软件建立了超薄板辊弯成形仿真模型,以单波模型为例,运用正交试验方法分析了压型板的回弹,详细分析了相对弯曲半径变化对回弹的影响。研究表明,材料厚度增加、弯角半径减小时,回弹角度会减小;在一定范围内较少道次数也能减小回弹角度;板材回弹角度与r/t值成线性关系。关键词:辊弯成形;数值模拟;回弹 中图分类号:TG386.3+ 1 文献标识码:A 收稿日期:2012-05-30;修回日期:2012-06-2 0作者简介:范琦(1986-) ,男,新疆乌鲁木齐人,在读硕士研究生,主要从事辊弯成形CAD/CAE/CAM一体化方面的研究。0 引言 超薄镀锌板多见于建筑中的轻钢结构。其板厚小于1mm,屈服强度不低于550MPa,最显著的特点是强度高、 塑性差,屈服强度和抗拉强度非常接近,在屈服后几乎无应力强化阶段。辊弯成形是一种重要的板材成形技术,具有连续生产、节约成本、工艺稳定、成形 精度高等优点[1,2] ,因此辊弯成形适合规模化生产,但 其成形过程复杂,影响因素多,所以对辊弯成形回弹特点还有待进一步研究。本文以超薄镀锌板成形为对象,基于ABAQUS有限元软件,建立有限元简化模型,并设计正交试验,研究压型板成形特点及回弹规律。1 有限元模型的建立 本文对3种厚度板材进行单向拉伸试验,由试验 结果计算后得到材料参数,见表1[3] 。材料密度取7 850kg /m3 。表1 拉伸试验结果 厚度(mm)弹性模量(MPa)屈服强度(MPa)抗拉强度(MPa)泊松比0.3 165 755 561 620 0.30.48 212 572 590 650 0.30.6 202 770 670 755 0.3 板材成形后的最终截面见图1。有限元模型建立 如下:道次间距250mm,上、下辊间距180mm;对单波成形进行模拟,将轧辊设为解析刚体,轧辊与板料间摩擦系数设为零,限制轧辊的转动,轧辊与板材间采用面-面接触;板材长宽尺寸为750mm×120mm;将轧辊完全约束,在板料纵向加载一段位移,限制板料前端部的纵向位移,限制板料中心线前、后两端点的横向位 移;选用S4R壳单元,厚度方向取5个积分点,网格在弯角处加密。共划分19 000个网格、19 539个节点。成形过程采用显式算法,后导入隐式算法计算回弹。 图1 最终截面图 2 成形模拟过程分析 辊弯过程中板材逐一经过机架,板料中间部分受上辊的压力而向下运动,两边受下辊压力被抬起并向中间运动,相对中心线而言两边为扭转变形。变形幅度越大,应力应变也越大。成形过程中板料不同位置不同时间可能受到横向弯曲、横向扭转、纵向弯曲、纵向拉压、横向剪切等作用,变形极为复杂。取四道次成形为例,图2为前两道次应力分布。当板料进入轧辊后,在弯角处和中间腹板部分产生较大的应力集中,这些区域出现大变形。从第一道次开始,弯曲段就存在塑性变形。由于板料薄厚方向刚度小,应力波对板材影响大。选择板料的中部成形时刻,每道次变形发生在板料与轧辊接触及附近区域,最大应力出现在进入轧辊前,而板料被带出轧辊后,应力迅速减小并进入卸载阶段。其后的每道次成形与第一道次相似。由于第二道次的下山量和成形角度最大,需要更大的纵向弯曲和横向弯曲,故应力较大。 在板料中段3个弯曲段各取特征节点A、B、C,其等效应力、应变随成形过程变化见图3和图4。图3
弯管常见的缺陷及其解决措施
弯管常见的缺陷及其解决措施 从工艺分析可知,常见的弯管缺陷主要有以下几种形式:圆弧处变扁严重(椭圆形)、圆弧外侧管壁减薄量过大、圆弧外侧弯裂、圆弧内侧起皱及弯曲回弹等。随着弯管半径的不同,前四种缺陷产生的方式及部位有所不同,而且不一定同时发生,而弯曲工件的弹性回弹却是不可避免的。弯管缺陷的存在对弯制管件的质量会产生很大的负面影响。管壁厚度变薄,必然降低管件承受内压的能力,影响其使用性能;弯曲管材断面形状的畸变,一方面可能引起横断面积减小,从而增大流体流动的阻力,另一方面也影响管件在结构中的功能效果;管材内壁起皱不但会削弱管子强度,而且容易造成流动介质速度不均,产生涡流和弯曲部位积聚污垢,影响弯制管件的正常使用;回弹现象必然使管材的弯曲角度大于预定角度,从而降低弯曲工艺精度。因此,应在弯制之前采取对应措施防止上述缺陷的产生,以获得理想的管件,保证产品的各项性能指标和外观质量。在通常情况下,对于前面提到的几种常见缺陷,可以有针对性地采取下列措施: (1) 对于圆弧外侧变扁严重的管件,在进行无芯弯管时可将压紧模设计成有反变形槽的结构形式:在进行有芯弯管时,应选择合适的芯棒(必要时可采用由多节段芯棒组装而成的柔性芯棒),正确安装之,并在安装模具时保证各部件的管槽轴线在同一水平面上。 (2) 小半径弯管时圆弧外侧减薄是弯曲的工艺特点决定的,是不可避免的。为了避免减薄量过大,常用的有效方法是使用侧面带有助推装置或尾部带有顶推装置的弯管机,通过助推或顶推来抵消管子弯制时的部分阻力,改善管子横剖面上的应力分布状态,使中性层外移,从而达到减少管子外侧管壁减薄量的目的。 (3) 对于管子圆弧外侧弯裂的情况,首先应保证管材具有良好的热处理状态,然后检查压紧模的压力是否过大,并调整使其压力适当,最后应保证芯棒与管壁之间有良好的润滑,以减少弯管阻力及管子内壁与芯棒的摩擦力。 (4) 对于圆弧内侧起皱,应根据起皱位置采取对应措施。若是前切点起皱,应向前调整芯棒位置,以达到弯管时对管子的合理支撑:若是后切点起皱,应加装防皱块,使防皱块安装位置正确,并将压模力调整至适当;若圆弧内侧全是皱纹,则说明所使用的芯棒直径过小,使得芯棒与管壁之间的间隙过大,或者就是压模力过小,不能使管子在弯曲过程中很好地与弯管模及防皱块贴合。因此,应更换芯棒,并调整压紧模使压模力适当。
卷板预弯工艺的对中操作介绍共10页
卷板预弯工艺的对中操作介绍 Three bending process 1 卷板由预弯(压头)、对中和卷弯三个过程组成。 1 roll plate by bending (head), and roll bending of three process. 2 预弯(压头)在三棍卷板机或预弯压力机上进行。当预弯板厚不超过20mm的情况下,可采用预弯也一块钢板作为弯模,其厚度不应大于板厚的两倍,长度应比板略长,将弯曲模放入辊筒中,将板料置于弯模上,压下上辊并使弯模来回滚动使板料边缘达到所要求的弯曲半径。同时采用弯模预弯时,必须控制弯曲功率不超过设备能力60%,操作时应严格控制上辊的压下量,以防过载损坏设备。在压力机上用模具预弯适用于各种板厚,用长度比板料短的通用模具,预弯时必须分段进行,预弯两端,预弯尺寸根据工件卷圆卷板机种类而定。如20*2000卷板机端面预弯尺寸是250-300;8*2000卷板机端面预弯尺寸是150-200。 2 bending (pressure head) in three stick machine or bending machine. When bending thickness under the condition of less than 20 mm, bending can be used also as a steel plate bending die, its thickness should not be greater than twice the thickness, length should be slightly longer than the board, the bending die is put into the roller, puts sheet metal bending mold, pressure roller and the bending modulus back and forth
(完整word版)辊弯成形技术与装备-教学大纲
课程名称:辊弯成形技术与装备 课程编码:M683011 课程学分:2学分 适用学科:机械工程领域 辊弯成形技术与装备 Roll Forming Technology and Equipment 教学大纲 一、课程性质 《辊弯成形技术与装备》是针对机械工程领域专业所开设的一门专业选修课。 二、课程教学目的 其主要目的是使学生理解和掌握辊弯成形技术基本理论及装备的一般知识,通过本课程的学习,应掌握辊弯成形轧辊设计理论,金属板带的辊弯成形特性基本原理;培养具有初步辊弯成形产品设计以及轧机设计的能力;了解辊弯成形生产线上辅助加工,特种与未来的辊弯成形技术等;通过实验加深学生对所学理论基础知识的理解和认识,培养学生具备一定的辊弯成形工艺综合分析和处理成形实际问题的能力。 三、教学基本内容及基本要求 1、教学基本内容 (1)绪论 本课程研究的对象及内容,本课程的性质及要求,学习本课程的方法,辊弯成形工艺及应用概述。 (2)辊弯成形轧机 轧机概述,轧机的类型:悬臂式轧机、双端式轧机、标准轧机、双层轧机、成组快换式轧机、并列轧机、拉料成形轧机、螺旋管轧机、车载轧机、特种轧机,轧机的构成:床身、机架、轴、驱动、辅辊和插入式立辊道次、道次间导引、矫直头、润滑系统、轴肩定位、在轧机中安装其他装置。 (3)辊弯成形轧辊设计理论 轧辊设计过程,断面,产品成形方位和其他在线操作,材料,辊弯成形轧机,
模具设计的其他考虑,定位套和垫片,计算板带宽度,弯曲方法,道次数,辊花图,轧辊设计,人工设计轧辊尺寸,计算机辅助轧辊设计,轧辊标记系统,轧辊方向,安装图。 (4)辊弯成形产品设计 薄壁产品的开发,设计中要考虑的因素,辅助加工,制造不同尺寸的断面,特殊产品的设计,尺寸与公差。 (5)金属板带的辊弯成形特性 成形过程中的变形类型,冗余变形的原因及对产品缺陷的影响,金属板带变形的数学仿真,轧辊轮廓的计算机设计系统。 (6)辊弯成形生产线上辅助加工 辅助加工主要工作原理及功用,矫直,张紧或松弛的生产线:在成形前、中、后的切断,辅助加工的位置,固定冲模和飞冲模,冲孔、冲多孔、切口和斜切,穿孔和局部冲切,翻边、冲百叶孔和切缝,压纹和冲压,弯曲,弯圆,标记,搭扣,旋转冲模,不同板带和零件间的机械连接,胶接,锡焊和铜焊,电阻焊,喷漆,发泡,打包。 (7)特种与未来的辊弯成形技术 轧机特殊设计,新型辊弯成形方法,热辊弯成形所需的设备和工具,计算机控制的辊弯成形线等。 2、教学基本要求 (1)了解辊弯成形工艺特点; (2)了解辊弯型钢产品的类型、特点及应用情况; (3)掌握辊弯成形设备组成、结构与工作原理; (4)掌握板金属成形的基本理论知识; (5)掌握辊弯成形缺陷的分析及解决方法。 四、本课程与其他课程的联系与分工 本课程的先修课程主要有机械制图、理论力学、材料力学、高等数学、机械原理、机械设计、工程材料及成形技术基础、机械制造工艺学等。建议学生通过选修或自学的方式学习弹塑性力学理论等方面的一些基础知识。 五、实践环节教学内容的安排与要求 1、实验教学内容
辊弯生产中的缺陷分析
辊弯生产中的缺陷分析
摘要:辊弯成形工艺是加工连续截面的一种重要工艺,在世界上得到广泛应用。但是,辊弯生产中同样存在很多问题,多种因素的影响使得辊弯产品存在许多缺陷,例如纵向弯曲和扭曲,边波,袋形波,角部褶皱,边角裂纹和撕裂等,这些缺陷主要是由加工产品的冗余应变引起的,因此就需要对冗余应变的产生原因进行分析,进而找出解决或者改进方法。 关键字:辊弯成型,缺陷分析,冗余应变 辊弯成型是带材在辊式成形机上连续弯曲成具有规定形状和尺寸的截形的塑性变形工艺。在实际的辊弯生产中,金属板带受到不同的变形,包括横向变形和冗余变形。其中横向变形是辊弯成形过程中最重要,必不可少的变形。横向变形将加工材料变形为具有所要求的横截面的产品,它通过一系列具有轮廓的轧辊来逐渐成型。而冗余变形则是在加工过程中产生的多余的,不需要的变形。冗余变形包括:纵向弯曲和回复;纵向伸长和收缩;横向伸长和收缩;金属平面的剪切;金属厚度方向的剪切;以及以上各种变形的结合。 在辊弯生产过程中,纵向应变主要产生在边缘处。这是因为金属板带的横向边缘和临近部分通常沿着流线移动,这些边部流线比中心和中间部分更长。由于这个原因,中心部分通常沿着直线运动,边部通常为竖直上升,同时水平移向横截面中心,边部的垂直上升和水平移动使得边部在纵向伸长,而中心和中间部分在纵向收缩。在辊弯生产过程中产生的纵向应变以及剪切应变无法同时得到优化,只能在两者之间取得一个折中的解决办法。如纵向弯曲和扭曲,边波,袋形波,角部褶皱,边角裂纹和撕裂等缺陷问题主要是由这些冗余变形引起的。冗余变形极大地影响着或者所要求产品横截面所需的横向弯曲,也影响着金属板带中的应力应变,成型后的回弹变形,产品中残余应力的分布等。
弯管常见的缺陷及其解决措施
弯管常见的缺陷及其解决措施
弯管常见的缺陷及其解决措施 从工艺分析可知,常见的弯管缺陷主要有以下几种形式:圆弧处变扁严重(椭圆形)、圆弧外侧管壁减薄量过大、圆弧外侧弯裂、圆弧内侧起皱及弯曲回弹等。随着弯管半径的不同,前四种缺陷产生的方式及部位有所不同,而且不一定同时发生,而弯曲工件的弹性回弹却是不可避免的。弯管缺陷的存在对弯制管件的质量会产生很大的负面影响。管壁厚度变薄,必然降低管件承受内压的能力,影响其使用性能;弯曲管材断面形状的畸变,一方面可能引起横断面积减小,从而增大流体流动的阻力,另一方面也影响管件在结构中的功能效果;管材内壁起皱不但会削弱管子强度,而且容易造成流动介质速度不均,产生涡流和弯曲部位积聚污垢,影响弯制管件的正常使用;回弹现象必然使管材的弯曲角度大于预定角度,从而降低弯曲工艺精度。因此,应在弯制之前采取对应措施防止上述缺陷的产生,以获得理想的管件,保证产品的各项性能指标和外观质量。在通常情况下,对于前面提到的几种常见缺陷,可以有针对性地采取下列措施: (1) 对于圆弧外侧变扁严重的管件,在进行无芯弯管时可将压紧模设计成有反变形槽的结构形式:在进行有芯弯管时,应选择合适的芯棒(必要时可采用由多节段芯棒组装而成的柔性芯棒),正确安装之,并在安装模具时保证各部件的管槽轴线在同一水平面上。 (2) 小半径弯管时圆弧外侧减薄是弯曲的工艺特点决定的,是不可避免的。为了避免减薄量过大,常用的有效方法是使用侧面带有助推装置或尾部带有顶推装置的弯管机,通过助推或顶推来抵消管子弯制时的部分阻力,改善管子横剖面上的应力分布状态,使中性层外移,从而达到减少管子外侧管壁减薄量的目的。 (3) 对于管子圆弧外侧弯裂的情况,首先应保证管材具有良好的热处理状态,然后检查压紧模的压力是否过大,并调整使其压力适当,最后应保证芯棒与管壁之间有良好的润滑,以减少弯管阻力及管子内壁与芯棒的摩擦力。 (4) 对于圆弧内侧起皱,应根据起皱位置采取对应措施。若是前切点起皱,应向前调整芯棒位置,以达到弯管时对管子的合理支撑:若是后切点起皱,应加装防皱块,使防皱块安装位置正确,并将压模力调整至适当;若圆弧内侧全是皱纹,则说明所使用的芯棒直径过小,使得芯棒与管壁之间的间隙过大,或者就是压模力过小,不能使管子在弯曲过程中很好地与弯管模及防皱块贴合。因此,应更换芯棒,并调整压紧模使压模力适当。
辊弯成型技术国内外研究进展
辊弯成型技术国内外研究进展 摘要:简要介绍冷弯成型技术理论在国内及国外的发展过程,通过分析我国现有国情,阐述冷弯成型技术存在的现状和优势。指出冷弯成型技术现阶段在我国仍然存在的缺陷和问题,并提出相应的解决办法。最后,憧憬我国冷弯成型技术能有美好的前景。 ABSTRACT:Briefly introduce the cold roll forming technology theory in the domestic and foreign development process.Through the analysis of the existing situation, explained the advantages and the present situation of the cold roll forming technology.Pointing out that the cold roll forming technology at this stage in our country still exists defects and problems, and put forward the corresponding solution.Finally, we look forward to China's cold roll forming technology can have a bright future. 关键词:冷弯成型技术历史现状创新 Key Words:Cold Roll forming technology、history、current situation、innovation
辊弯成型CAD
摘要:本文介绍了北方工业大学与德国data M 公司近年来合作研究开发的技术成果,给出了辊弯成型CAD/CAM技术的应用实例。应用CAD技术,在非对称料型的设计中根据截面的几何特性确定成型基准及工艺,介绍了咬口封闭料型的设计特点,给出了计算机模拟技术在宽幅压型板设计中的实例。应用CAM技术,解决了异型轧辊的计算机辅助加工,基于计算机数控包络法,用一片砂轮可加工出不同的轮廓曲线。辊弯成型CAD/CAM一体化技术的应用取得了良好的效果。对本技术的发展方向,也提出了见解。 关键词:CAD CAM 辊弯成型 1. 辊弯成型的计算机辅助设计 在过去的十多年中,辊弯成型(又称冷弯型钢)的计算机辅助设计技术得到广泛应用。目前面临的问题是计算机可在多大程度“辅助”设计者完成任务。许多人设计轧辊时应用计算机仅代替人工的几何计算,很大程度上仍依赖设计者的实践经验。 随着计算机技术的飞速发展,用于辊弯成型的CAD 软件应达到更高的水平。首先应向更深的方面发展,计算机能够在更多的方面帮助设计者以得到最优的设计结果。例如,CAD软件应具备如下功能:模拟成形过程,应用人工智能及模糊神经网络技术给出专家水平的指导。
其次CAD技术向更广的领域发展,计算机辅助制造,生产管理,成本核算,质量控制以及CAE和CIMS。由德国data M开发的COPRA是解决辊弯成型设计的集成软件。 以下是由COPRA完成的部分冷弯型钢断面的实例。 1.1 非对称断面 日本拓殖大学的小奈弘教授给出了非对称断面成型道次的估算方法。与对称断面相比,不平衡的扭矩会导致板带的扭曲。断面成型过程中板带的几何变形与其静力学特性紧密相关。作者发现若以截面的一个惯性轴作为展开的基准线,一些非对称断面可得到很好的成型质量。 1.1.1 以惯性主轴作为展开的基准 用于集装箱的部件(图1)是一非对称截面。某公司以最长的直线段作为成型的水平基准,共用12道次成型,并产生明显的扭屈。用COPRA可方便地计算出主惯性轴的角度,以其中一个惯性轴作为成型基准面,只需6道次就获得了比前方法质量更好的断面。 图1 集装箱部件的成型辊花图图2 两侧成形角不同的V型截面图2是天花板吊顶的部件,虽然它的形状简单,但它的成型却不容易,原因在于必须满足板厚0.4mm的情况下每米成型长度上的各向最大挠度不大于0.5mm。成型这一高精度的部件,作者采用的方法是以惯
辊弯成型技术的应用与发展
辊弯成型技术的应用与发展 摘要:本文介绍了近年来合作研究辊弯成型开发的技术成果,给出了辊弯成型CAD/CAM 技术的应用实例。应用CAD技术,在非对称料型的设计中根据截面的几何特性确定成型基准及工艺,介绍了咬口封闭料型的设计特点,给出了计算机模拟技术在宽幅压型板设计中的实例。应用CAM技术,解决了异型轧辊的计算机辅助加工,基于计算机数控包络法,用一片砂轮可加工出不同的轮廓曲线。辊弯成型CAD/CAM一体化技术的应用取得了良好的效果。对本技术的发展方向,也提出了见解。 关键词:CAD CAM 辊弯成型 1. 辊弯成型的计算机辅助设计 在过去的十多年中,辊弯成型(又称冷弯型钢)的计算机辅助设计技术得到广泛应用。目前面临的问题是计算机可在多大程度“辅助”设计者完成任务。许多人设计轧辊时应用计算机仅代替人工的几何计算,很大程度上仍依赖设计者的实践经验。 随着计算机技术的飞速发展,用于辊弯成型的CAD 软件应达到更高的水平。首先应向更深的方面发展,计算机能够在更多的方面帮助设计者以得到最优的设计结果。例如,CAD 软件应具备如下功能:模拟成形过程,应用人工智能及模糊神经网络技术给出专家水平的指导。其次CAD技术向更广的领域发展,计算机辅助制造,生产管理,成本核算,质量控制以及CAE和CIMS。由德国data M开发的COPRA是解决辊弯成型设计的集成软件。 以下是由COPRA完成的部分冷弯型钢断面的实例。 1.1 非对称断面 日本拓殖大学的小奈弘教授给出了非对称断面成型道次的估算方法。与对称断面相比,不平衡的扭矩会导致板带的扭曲。断面成型过程中板带的几何变形与其静力学特性紧密相关。作者发现若以截面的一个惯性轴作为展开的基准线,一些非对称断面可得到很好的成型质量。 1.1.1 以惯性主轴作为展开的基准 用于集装箱的部件(图1)是一非对称截面。某公司以最长的直线段作为成型的水平基