KATALCOJM型制氢转化催化剂的工业应用
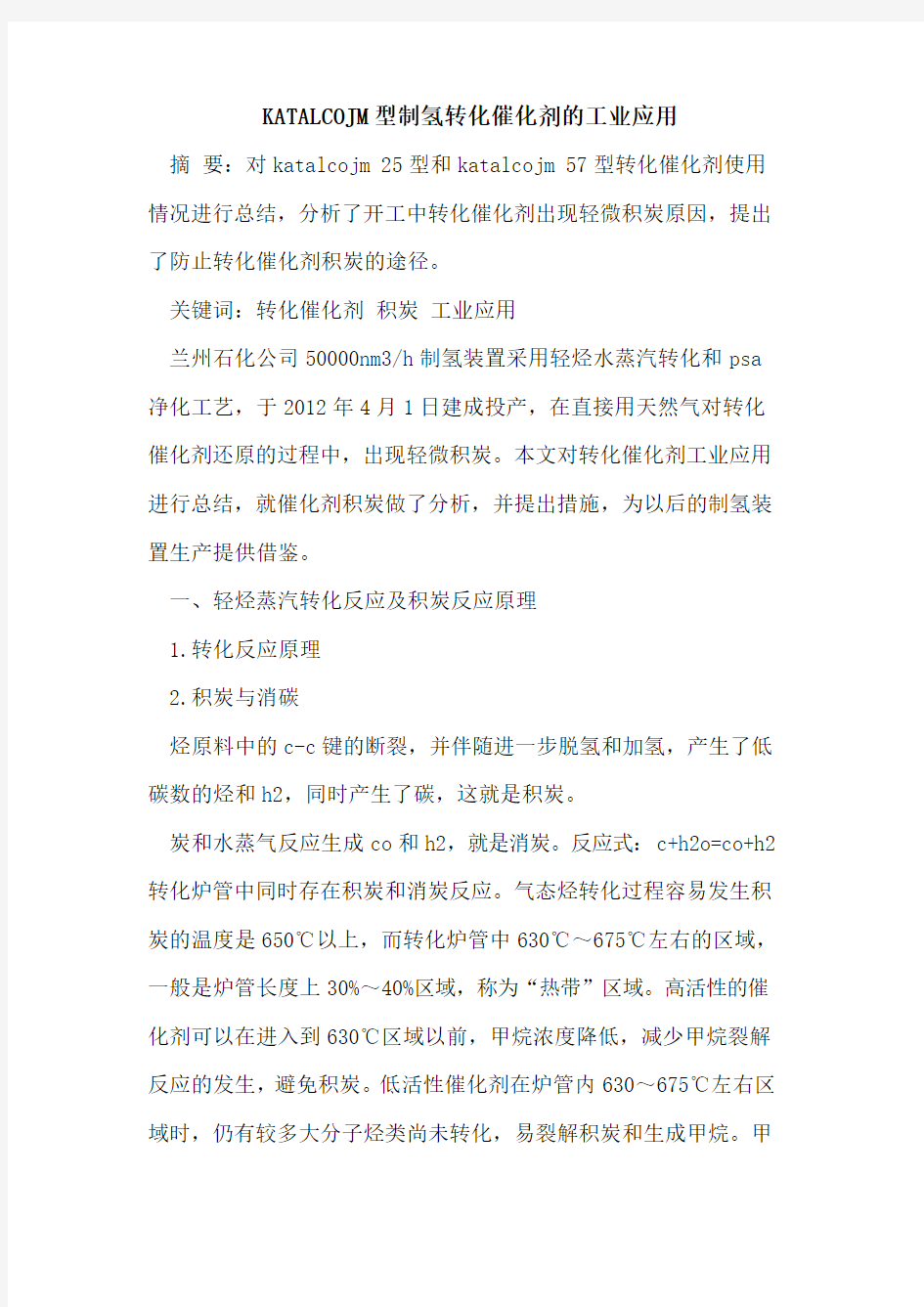
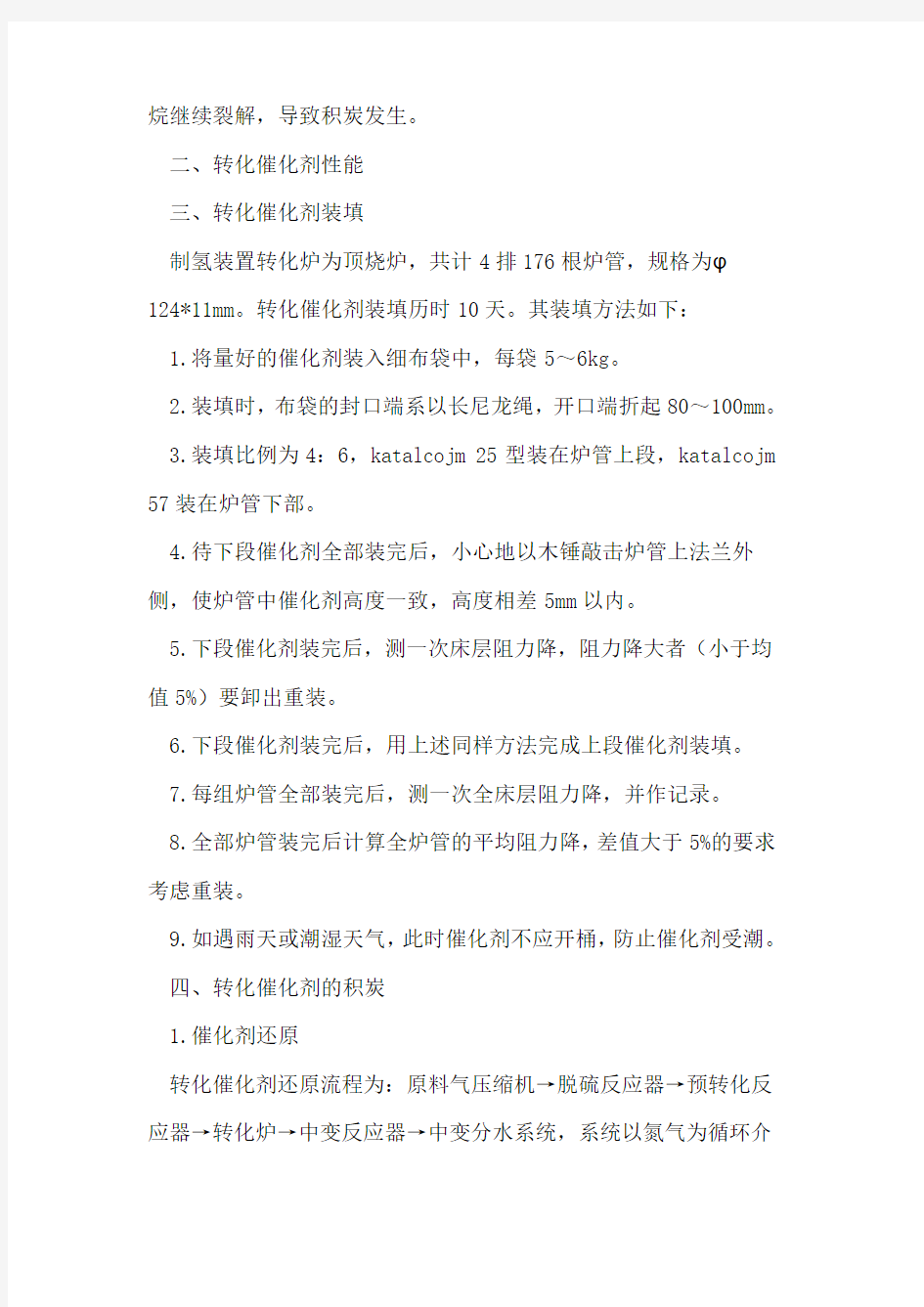
KATALCOJM型制氢转化催化剂的工业应用
摘要:对katalcojm 25型和katalcojm 57型转化催化剂使用情况进行总结,分析了开工中转化催化剂出现轻微积炭原因,提出了防止转化催化剂积炭的途径。
关键词:转化催化剂积炭工业应用
兰州石化公司50000nm3/h制氢装置采用轻烃水蒸汽转化和psa 净化工艺,于2012年4月1日建成投产,在直接用天然气对转化催化剂还原的过程中,出现轻微积炭。本文对转化催化剂工业应用进行总结,就催化剂积炭做了分析,并提出措施,为以后的制氢装置生产提供借鉴。
一、轻烃蒸汽转化反应及积炭反应原理
1.转化反应原理
2.积炭与消碳
烃原料中的c-c键的断裂,并伴随进一步脱氢和加氢,产生了低碳数的烃和h2,同时产生了碳,这就是积炭。
炭和水蒸气反应生成co和h2,就是消炭。反应式:c+h2o=co+h2转化炉管中同时存在积炭和消炭反应。气态烃转化过程容易发生积炭的温度是650℃以上,而转化炉管中630℃~675℃左右的区域,一般是炉管长度上30%~40%区域,称为“热带”区域。高活性的催化剂可以在进入到630℃区域以前,甲烷浓度降低,减少甲烷裂解反应的发生,避免积炭。低活性催化剂在炉管内630~675℃左右区域时,仍有较多大分子烃类尚未转化,易裂解积炭和生成甲烷。甲
大庆石化公司制氢装置用转化催化剂
大庆石化公司制氢装置用转化催化剂 招标采购技术要求 1、项目介绍: 制氢装置转化催化剂是一种高效的烃类水蒸气转化催化剂,活性组分是NiO,作用是将烃类与水在转化炉内反应转化为氢气。 2、买方的基础条件 2.1使用装置简介 制氢装置由原料精制、转化系统、中变及冷却分液系统、热工系统和公用工程等部分组成,原料精制部分采用湿法脱硫(MDEA溶液吸收)对原料进行初步净化,然后再用ZnO脱硫剂进行精脱硫的方法进行原料净化,转化部分采用烃类-水蒸汽转化法制氢、采用PSA净化提纯工艺提纯氢气。 2.2原料条件 制氢装置所用原料为加氢裂化干气、重整氢及加氢裂化低分气PSA提浓尾气、油田气、焦化干气,加氢精制干气、汽油脱硫塔顶不凝气、柴油脱硫干气,主要产品为纯度99%以上的工业氢气。 2.3设备条件 制氢装置需装转化催化剂的设备是转化炉,共计184根炉管,每根炉管直径103mm ,每根炉管有效装填高度12.4m。 2.4工艺条件 3、对卖方产品的要求 3.1规格要求: 转化催化剂技术指标要符合卖方企业标准。 3.2性能要求 3.2.1 卖方需保证提供的转化催化剂产品质量达到3.1条要求的质量指标。
3.2.2在2.4条操作条件下卖方需保证转化催化剂出口CH4≯7.0%(V)。 3.2.3 在2.4条操作条件下卖方需保证转化催化剂床层阻力降≯0.35MPa。 3.2.4在2.4条操作条件下卖方需保证提供的转化催化剂使用寿命在四年以上。 3.2.5在2.4条操作条件下卖方保证转化催化剂与装置内使用碳钢等材质不发生化学反应,不会对相邻设备管线造成腐蚀,不会产生结晶析出堵塞泵体、管线的现象。 4、对卖方产品方案的要求 4.1产品制造厂的简介 4.2产品的特点,专利技术等介绍 4.3产品的主要原材料及生产工艺简介 4.4产品的规格及执行标准 4.5产品的物化性质 4.6产品的保质期 4.7产品的安全环保性能 4.8产品使用方法及注意事项 4.9产品质量保证措施(包括原材料入厂质量、生产过程及出厂质量控制等)4.10对本技术要求的响应及偏离情况 4.11其它补充说明。 5、双方的责任义务 5.1买方 5.1.1卖方货物运抵买方后,买方负责入厂检验,检验内容包括本技术要求第二章第3.1条约定和卖方执行标准中未包含在第3.1条中的项目,买方入厂检验后,产品质量达不到以上要求时(同一质量指标以高标准为依据),买方有权拒收。 5.1.2买方对卖方资料的完整性、符合性有权进行检查验收,有权要求卖方对检查不合格的资料进行整改。 5.1.3买方负责按照卖方提供的4.7、4.8条约定文件编制的投用考核方案,并交卖方审查。 5.1.4首次装填和使用卖方产品前一周,买方负责通知卖方代表到买方现场,进行技术指导和现场见证。
制氢转化炉施工方案1概论
目录 一、工程概况 (1) 二、施工标准 (2) 三、适用范围 (3) 四、制氢转化炉钢结构施工要求 (4) 五、炉管及配件的制作 (12) 六、炉管的安装 (19) 七、炉管系统的试压 (21) 八、配件的安装 (22) 九、辐射室炉管的安装 (25) 十、安全措施和文明施工 (27) 十一、施工机具 (29) 十二、施工人员 (31) 十二、施工平面布置图 (35)
山东海化集团80万吨/年重油催化项目制氢转化炉施工方案 编制: 审核: 批准: 中国化学工程第十六建设公司 重油项目经理部 二OO六年十月十日
一工程概况: 山东海化集团80万吨/年重油催化项目气制氢装置的制氢转化炉炉体(辐射室部分)高为16.935米,端面宽为8.06米。炉型为立管式厢式炉,分为辐射室、对流室、烟风道三部分。 辐射室加热联合油及轻蜡油,炉管为单排管双面辐射,共72根炉管,分为4排,炉底30台新型小能量扁平火焰燃烧器分成5排,炉墙中间设置中间火墙将辐射室分为两部分。对流室4排炉管,每排14根,其中58根为翅片管,最下面一排炉管为光管。 二施工标准 1施工图纸 2 SH3070-1995《石油化工管式炉钢结构设计规范》 3 SH3526-1992《石油化工异种钢焊接规程》 4 JB4730-94 《压力容器无损检测》 5 SH3506-2000 《管室炉安装工程施工及验收规范》 6 SHT3523-1999《石油化工铬镍奥氏体、铁镍合金和镍合金管道焊接规程》 7 JBT-4730.1~4730.6-2005 《承压设备无损检测》 8 JB T6046-92 《碳钢、低合金钢焊接构件焊后热处理方法》 9 SHJ509《石油化工工程焊接工艺评定》
以催化干气的制氢工艺特点
1、以催化干气为原料的制氢工艺流程特点: 催化干气的烯烃含量一般在10?20%之间,以催化干气为原料的制氢装置工艺流程简图为: 气体原料压缩-原料预热|丄等(变)温加氢丄绝热加氢卜脱氯、 脱硫卜配蒸汽]-蒸汽转化| -高(中)温变换斗热回收T PSA-H2 图1、高烯烃含量烃类为原料的制氢工艺流程 该工艺特点为:(1)与传统烃类制氢原料不同,催化干气烯烃含量太高,不能直接用作制氢原料,须将其中的烯烃全部转化为饱和烃。该工艺增加等(变)温加氢反应器,以满足高烯烃含量原料烯烃加氢饱和的放热要求。部分烯烃在等(变)温加氢反应器完成加氢饱和。 (2)部分新鲜原料通过跨线与等(变)温加氢反应器出口原料气混合,调配其中的烯烃含量,以满足绝热加氢反应器床层温度达到 350?380C的要求。 (3)经过加氢后的原料中的有机氯、有机硫转化为氯化氢和硫化氢,在脱硫反应器被脱氯剂、脱硫剂脱除。脱硫反应器为两反应器串联使用,可在线切换和更换脱硫剂。 (4)转化部分采用原料适用性强的转化催化剂,适应不同烃类原料 的转化要求。将各种烃类转化为富氢气体,转化出口CH含量一般小 于6%(v/v )。 (5)转化工艺气经高(中)温变换,将在部分CC转化为CO2同时产生更多的氢。
(6)中变气经过多级热回收及冷却,降温至40C以下,满足PSA进料要求。(7)通过PSA制得纯度99.5 %以上的工业氢,解吸气作为低热值燃料返回转化炉作燃料。 2 装置开工过程提要烃类蒸汽转化制氢装置的开工过程,就是将各种催化剂活化的过程,其中原料加氢催化剂需要预硫化处理,转化及中变催化剂需要还原处理。脱硫、脱氯剂要进行适当的干燥脱水处理。以下分别论述。 2. 1 加氢催化剂预硫化 制氢原料加氢催化剂投入正常使用前,一般需要将氧化态的活性组分先变成具有催化活性的金属硫化态形态,称为预硫化,本文不对加氢催化剂的详细预硫化过程进行论述,各用户可参考催化剂供应商提供的催化剂硫化方案,本文主要介绍硫化介质及硫化过程的流程控制。硫化介质 硫化介质是指催化剂硫化所需的气体氛围,一般由N2、H2、H2S 组成。工业上一般不直接采用H2S 作硫化介质,而是采用液态的CS2、DMDS (二甲基二硫)等作为硫化剂。这类硫化剂在氢存在条件下,在150?250C很容易生成HS。硫化剂可米用外购方式获得,贮存在专门的硫化剂贮罐内。 使用液态硫化剂,离不开H2。氢气的来源有以下几个,各厂可根据各自情况决定
催化剂的制备和应用
摘要: 均匀、连续、致密分子筛膜的合成和应用受到广泛关注。利用分子筛膜具有的筛分和催化作用,在传统颗粒催化剂或载体表面包覆分子筛膜形成复合型催化剂,可以实现膜基分离和催化过程的耦合,增加反应物选择性,提高目标产物收率。本文综述了近年来在不同类型颗粒催化剂或载体表面合成分子筛膜的制备方法,描述了分子筛膜包覆型复合催化剂用于不同催化反应体系的研究结果。同时,在归纳和总结已有研究成果基础上展望了分子筛膜包覆型催化剂的研究发展趋势。 关键词: 分子筛膜包覆载体膜催化反应器 Coated with molecular sieve membrane preparation and application of the catalyst Abstract:uniform, continuous, the synthesis and application of dense molecular sieve membrane is widely https://www.360docs.net/doc/998319026.html,ing molecular sieve membrane is screening and catalysis, in traditional particle catalyst or carrier cladding molecular sieve membrane formation on the surface of composite catalyst, can realize the coupling of membrane separation and catalytic process, increase the selectivity of reactants, improve the target product yield.In recent years was reviewed in this paper in different types of particle catalyst or carrier surface preparation methods of synthesis of molecular sieves membrane, describes the molecular sieve membrane coated type composite catalyst used for the results of different catalytic reaction system.At the same time, on the basis of induction and summary of existing research results discussed coated with molecular sieve membrane research and development trend of catalyst. Keywords:molecular sieve membrane coated carrier membrane catalytic reactor 1引言 分子筛膜具有较高的热稳定性,较好的化学稳定性。耐腐蚀性以及与特种材料的生物相容性,自首次支撑体分子筛膜专利报道至今,沸石分子筛膜的研究及生产已经成为膜科学技术领域的研究热点之一。图1分子筛膜论文和专利发表数量随年份的趋势图。支撑体分子筛膜的使用拓宽了分子筛的应用范围,避免了直接使用分子筛粉末床层带来的高压降及成型时加入粘结剂带来的使用效率降低等问题,使分子筛膜规模化的工业应用成为可能。加上分子筛具有筛分效应,较大的比表面积,可控的客体-吸附质相互作用,使其可用于膜催化和分离。分子筛膜在膜分离、膜催化反应器、化学传感器、电极材料、光电器件、低介电常数材料以及保护层方面均有潜在的应用前景。
制氢转化催化剂的使用与维护
制氢转化催化剂的使用与维护 本文对于制氢催化剂的日常使用以及维护进行了介绍,包括制氢催化剂的性质、制氢催化剂的装填、制氢催化剂的投用等。还详述了制氢催化剂在使用的过程中所存在的问题,催化剂的破碎、积碳、中毒以及催化剂有毒物质的产生等问题,并针对这些问题提出了相应的预防手段,为制氢催化剂的使用和维护提供了现实的技术基础。 标签:制氢催化剂装填投用问题措施 一、转化催化剂 制氢转化炉内的催化剂一般为Z111-4YA、Z111-6YQ、Z111、Z111B。催化剂的物理特性以及化学组成如表1和表2所示,转化催化剂一般优化为圆柱状,并在原来的的基础上在内部进行开孔处理,催化剂在使用的过程具有较大的接触的面积,其活性能够成倍的增加。制氢催化剂在使用的过程中要添加一种抗结碳的物质,使得催化剂在低温状态下还能够保持较好的活性,并且使得催化剂抗积碳的性能增加。下端的催化剂虽然具有很高的活性但是其抗积碳的能力较弱,所以一般来讲转化的反应大部分都是在上端完成的,上端对于活性催化剂的量要求较大。由于转化催化剂的作用主要是位于催化剂的外表面,所以催化剂的外表面越大那么越有利于转化。较小的颗粒由于气动扰动较大所以较利于反应。 表1常用催化剂及其物理性质 表2常用催化剂的化学组成 二、转化催化剂的使用 在制氢催化剂的使用过程中,制氢催化剂的装填需要考虑到转化炉的结构,在工艺流程气密检查合格之后,就将氮气冲入炉内进行循环和升温,在对制氢催化剂使用的过程中要控制加热速度,尽量将加热速度控制在50摄氏度每小时以内。在升温的出口的温度达到350摄氏度,转化管的温度大于350摄氏度,高变床的温度大于200摄氏度的时候,在配气点引入一定压力的蒸汽来对制氢转化过程进行加热,加热的速度要控制在30摄氏度每小时以内,然后采取相应的措施进行脱硫的操作。对天然气的进气以及配氢的流程进行改善,防止温度出现较大程度的扰动,在各参数调节正常之后连入PSA,对氢气进行提纯的操作,如果显示提纯的纯度达到100%的时候,设备正常运转,在这个时候催化剂的作用开始发挥。 三、转化催化剂使用过程中存在的问题 1.催化剂的破碎
制氢三剂性能及种类
制氢三剂性能及种类 制氢过程使用的催化剂有:钴-钼加氢脱硫催化剂、脱氯催化剂、氧化锌脱硫剂、烃类-水蒸汽转化催化剂、中温变换催化剂、低温变换催化剂。还有PSA吸附剂及磷酸三钠化学助剂。 1.1 钴-钼加氢转化催化剂 1.1.1 作用 制氢原料中含有不同数量的有机硫和无机硫,这些硫化物的存在,会增加原料气体对设备的腐蚀,尤其重要的是制氢过程所使用的含镍、含铜的催化剂极容易被硫中毒,失去活性,严重影响生产的顺利进行。但是,有机硫化物性能稳定,不容易被脱除,只有在钴-钼催化剂的作用下,与氢气快速反应生成硫化氢,才能被脱除。 1.1.2 特点 钴-钼加氢转化催化剂必须在有氢气存在的条件下,才能将有机硫转化无机硫,否则,将无法起作用。 1.1.3 物理化学特性(T205) 外观:灰蓝色条状物 几何尺寸:Φ3~3.5×3~10mm 堆密度:0.65~0.8kg/L 比表面:180~220m2/g 1.1.4 化学组成
C O O:2~4% M O O3:10~13% 载体:TiO2、AL2O3 1.2 氧化锌脱硫剂(T306) 1.2.1 作用 氧化锌与硫化氢作用生成难于解离的硫化锌,以此脱除制氢原料气中的硫化氢,一般用于精脱硫过程。 1.2.2 特点 氧化锌脱硫剂能脱除无机硫和一些简单的有机硫,硫容较高,能使原料中的硫含量降至0.2~0.02×10-6。反应温度范围较宽(180~400℃),是一种比较理想的脱硫剂,在较高温度(350~400℃)条件下使用效果更好。 1.2.3 物理化学特性 外观:白色条状 几何尺寸:Φ5mm×5~10 堆密度: 1.16kg/L 比表面:45.88m2/g 总孔容积:0.28ml/g 穿透硫容:>10% 1.2.4 化学组成 ZnO:≥ 85% 1.3 烃类-水蒸汽转化催化剂(Z402、Z405)
催化剂制备方法大全
催 化 剂 的 制 备 方 法 与 成 型 技 术 总 结 应用化学系1202班 王宏颖 2012080201
催化剂的制备方法与成型技术 一、固体催化剂的组成: 固体催化剂主要有活性组分、助剂和载体三部分组成: 1.活性组分:主催化剂,是催化剂中产生活性的部分,没有它催化剂就不能产生催化作用。 2.助剂:本身没有活性或活性很低,少量助剂加到催化剂中,与活性组分产生作用,从而显著改善催化剂的活性和选择性等。 3.载体:载体主要对催化活性组分起机械承载作用,并增加有效催化反应表面、提供适宜的孔结构;提高催化剂的热稳定性和抗毒能力;减少催化剂用量,降低成本。 目前,国内外研究较多的催化剂载体有:SiO2,Al2O3、玻璃纤维网(布)、空心陶瓷球、有机玻璃、光导纤维、天然粘土、泡沫塑料、树脂、活性炭,Y、β、ZSM-5分子筛,SBA-15、MCM-41、LaP04等系列载体。 二、催化剂传统制备方法 1、浸渍法 (1)过量浸渍法 (2)等量浸渍法(多次浸渍以防止竞争吸附) 2、沉淀法(制氧化物或复合氧化物)(注意加料顺序:正加法或倒加法,沉淀剂 加到盐溶液为正,反之为倒加) (1)单组分沉淀法 (2)多组分共沉淀法 (3)均匀沉淀法(沉淀剂:尿素) (4)超均匀沉淀法 (NH4HCO3和NH4OH组成的缓冲溶液pH=9) (5)浸渍沉淀法 浸渍沉淀法是在浸渍法的基础上辅以均匀沉淀法发展起来的,即在浸渍液中预先配入沉淀剂母体,待浸渍单元操作完成后,加热升温使待沉淀组分沉积在载体表面上。此法,可以用来制备比浸渍法分布更加均匀的金属或金属氧化物负载型催化剂。 (6)导晶沉淀法 本法是借晶化导向剂(晶种)引导非晶型沉淀转化为晶型沉淀的快速有效方法。举例:以廉价易得的水玻璃为原料的高硅酸钠型分子筛,包括丝光沸石、Y型、X型分子筛。 3、共混合法 混合法是将一定比例的各组分配成浆料后成型干燥,再经活化处理即可。如合成气制甲醇用的催化剂就是将氧化锌和氧化铬放在一起混合均匀(适当加入铬
5制氢催化剂的使用
第五章制氢催化剂的性质和使用 制氢过程使用的催化剂有如下几种: (1)钴——钼加氢转化脱硫催化剂; (2)脱氯催化剂; (3)氧化锌脱硫剂; (4)烃类——水蒸汽转化催化剂; (5)中温变换催化剂; (6)低温变换催化剂; (7)甲烷化催化剂; (8)吸附剂。 这些催化剂的使用条件非常苛刻,为了使装置实现安稳长满优生产,确保经济、合理、高效的生产目的,必须严格控制原料杂质的浓度,以避免杂质对催化剂的损害。 制氢所使用的原料一般都是轻油,近年一些装置掺用部份炼厂干气制氢,这些制氢原料中通常含有的对制氢催化剂有影响的杂质是硫、氯、有机金属化合物。 硫对含镍的转化催化剂和甲烷化催化剂,对含铜的低温变换催化剂都会造成毒害,一般转化炉入口原料中硫含量要求小于0.5ppm。硫中毒会使转化炉管产生“热带”,也会促使出口气体甲烷含量增高。 氯离子具有很高的迁移性,可随工艺气流迁移,对下游催化剂及设备造成威胁。许多合金钢受氯侵蚀后产生应力腐蚀,氯的侵蚀导致许多换热器破裂。氯会导致转化催化剂失活,对铜系低温变换催化剂的影响更大,氯与铜形成的新物质的熔点很低,易升华又易熔于水,在低变工艺条件下,这些氯化合物可以穿透整个床层。一般要求原料中含氯应低于5 ppb。 有机金属化合物会沉积在加氢脱硫及转化催化剂表面,导致催化剂活性的永久性衰退,一般要求原料中重金属含量应低于5ppb。 5.1加氢转化催化剂 制氢原料中含有不同数量的有机硫和无机硫,这些硫化物的存在,会增加原料气体对设备的腐蚀,尤其重要的是制氢过程所使用的含镍、含铜的催化剂极容易被硫中毒,失去活性,严重影响生产的顺利进行。但是,有机硫化物性能稳定,不容易被脱除,只有在加氢催化剂的作用下,与氢气反应将有机硫转化生成硫化氢,才能被脱除。传统加氢转化催剂的主要成份是υ-Al2O3担载的C O O和M O O3,即钴——钼加氢转化催化剂,近年来北京海顺德催化剂有限公司生产的加氢催化剂的载体改用钛的氧化物,这种催化剂也取得一定的实用业绩。5.1.1加氢剂的种类及物化性质 5.1.1.1国内常用加氢转化催化剂的型号及性能υ 国内加氢转化催化剂现有十几种型号,经常用于制氢装置上的仅有几种,如表5-1所示。大型氨厂加氢转化催化剂(如T201型)寿命最长超过十年,此类催化剂质量已不亚于国外催化剂的水平,因此,国产化率已达100%。
第二章催化剂制备、性能评价及使用技术
第二章催化剂的制备、性能评价及使用技术 1.多相催化剂常用哪些方法来制备?为什么制备固体催化剂都需要经过热处理,其目的是什么? 多相催化剂常用的制备方法有:(1)天然资源的加工,结构不同,含量不同的硅铝酸盐采用不同的方法和条件加工后能适用于某一特定的催化反应;(2)浸渍法,将载体置于含活性组分的溶液中浸泡,达到平衡后将剩余液体除去,再经干燥、煅烧、活化等步骤即得催化剂。此法要求浸渍溶液中所含活性组分溶解度大、结构稳定、受热后分解为稳定的化合物;(3)滚涂法和喷涂法,滚涂法是将活性组分先放在一个可摇动的容器中,再将载体布于其上,经过一段时间的滚动,活性组分逐渐粘附其上,为了提高滚涂效果,有时也添加一定的粘合剂。喷涂法与滚涂法类似,但活性组分不同载体混在一起,而是用喷枪附于载体上;(4)沉淀法,在含金属盐类的水溶液中,加进沉淀剂,以便生成水合氧化物、碳酸盐的结晶或凝胶。将生成的沉淀物分离、洗涤、干燥后,即得催化剂;(5)共混合法:将活性组分与载体机械混合后,碾压至一定程度,再经挤条成型,最后缎烧活化;(6)沥滤法(骨架催化剂的制备方法),将活性组分金属和非活性金属在高温下做成合金,经过粉碎,再用苛性钠来溶解非活性金属即得;(7)离子交换法: 是在载体上金属离子交换而负载的方法, 合成沸石分子筛一般也是先做成Na型,需经离子交换后方显活性;(8) 均相络合催化别的固载化: 将均相催化剂的活性组分移植于载体上, 活性组分多为过渡金属配合物,载体包括无机载体和有机高分子载体。优点是活性组分的分散性好,而且可根据需要改变金属离子的配体。制备各固体催化剂,无论是浸渍法,沉淀法还是共混合法,有的钝态催化剂经过缎烧就可以转变为活泼态,有的还需要进一步活化。 所以,催化剂在制备好以后,往往还要活化;除了干燥外,还都需要较高温度的热处理-煅烧的目的:1)通过热分解除掉易挥发的组分而保留一定的化学组成,使催化剂具有稳定的催化性能。2)借助固态反应使催化剂得到一定的晶型、晶粒大小、孔隙结构和比表面。3)提高催化剂的机械强度。 2.沉淀法制备催化剂的原理是什么?金属盐和沉淀剂的选择原则是什么? 沉淀法制备催化剂的原理是沉淀反应,金属盐一般首选硝酸盐来提供无机催化剂材料所需的阳离子;金、铂、钯等贵金属不溶于硝酸,但可溶于王水。 沉淀剂的选择原则是:(1)尽可能使用易分解并含易挥发成分的沉淀剂;(2)沉淀便于过滤和洗涤;(3)沉淀剂自身的溶解度要足够大;(4)沉淀物的溶解度应很小;(5)沉淀剂必须无毒,不造成环境污染。
制氢装置转化炉设计简介
制氢装置转化炉简介 一、概述 随着炼油厂加氢装置的逐渐增多,所需要的氢气也越来越多,使得制氢装置相应的发展很快。目前大型工业装置采用的制氢方法均为烃类水蒸汽转化法,利用的原料主要有天然气、炼厂气、石脑油等轻质烃类。这些烃类在特定的温度、压力以及催化剂存在的条件下与水蒸汽发生反应,生成氢气及一氧化碳。 烃类化合物的水蒸汽转化反应是一个复杂的反应平衡系统,高分子烃类先裂解或转化成甲烷,最终与水蒸汽进行转化反应。大体上可用下列反应式表达: C n H m + 2H2O →C n-1H m-2 + CO2 + 3H2– Q CH4 + 2H2O = CO2 + 4H2– Q CO2 + H2 = CO + H2O - Q 转化炉是制氢装置中转化反应的反应器,属于装置的心脏设备。这是一种非常特殊的外热式列管反应器,由于转化反应的强吸热及高温等特点,这种反应器被设计成加热炉的形式,催化剂装在一根根的转化炉管内,在炉膛内直接加热,反应介质通过炉管内的催化剂床层进行反应。 转化炉苛刻的操作条件,使得这种炉子有很多有别于其它加热炉的特殊性,在炉子结构、炉管材料、管路系统支撑、管路系统应力、管路系统膨胀及补偿、燃烧、烟气流动及分配、耐火材料等各方面都必须精心考虑。 二、炉型及结构 1.炉型 制氢装置转化炉按辐射室供热方式进行分类,可分为以下四种方式: 1)顶烧炉:这是很多公司都采用的一种炉型。这种炉型的燃烧器布置在辐射室顶部,转化管受热形式为单排管受双面辐射,火焰与炉管平行,垂直向下燃烧,烟气下行,从炉膛底部烟道离开辐射室。这种炉型的对流室均布置在辐射室旁边。 2)侧烧炉:这种炉型以丹麦TOPSφE公司为代表。这种炉子的燃烧器布置在辐射室的侧墙,火焰附墙燃烧。早期转化管的受热形式多为炉膛中间的双排管受侧墙的双面辐射,由于受热形式不好,操作条件苛刻时,炉管易弯曲,现在大部分都改为单排管受双面辐射的形式。这种炉子的烟气上行,对流室置于辐射室顶部,大型装置的对流室考虑到结构及检修等原因,对流室经常放置在辐射室旁边。 3)梯台炉:这种炉型以美国FOSTER WHEELER公司为代表。这种炉子的辐射室侧墙呈梯台形,燃烧器火焰沿倾斜炉墙平行燃烧,通过炉墙向转化管辐射传热。与侧烧炉类似,转化管可以为双排或单排。这种炉子的对流室全部置于辐射室顶部,烟气上行,采用自然抽风,没有引风机。 4)底烧炉:这种炉型目前多用于小型装置。燃烧器位于辐射室底部,烟气上行。 2.炉型结构比较 2.1传热方式
制氢装置转化中变催化剂还原方案
制氢装置转化中变催化剂还原方案 注: 此过程还需催化剂厂家确认。 6.2.1转化催化剂还原的步骤 (M)-确认转化催化剂达到还原条件: 转化入口温度480-520℃,出口温度为820±10℃ 水蒸汽量为正常负荷的50%,约控制在8t/h左右 氢气纯度>90% 中变床层温度稳定在250℃ [P]-由管GH-2101引外来开工用氢入原料气压缩机入口分液罐D-2101,开始配氢量100-200Nm3/h,然后根据情况慢慢增加。 [I]-配氢后要密切注意系统压力,若由于配氢量增加造成系统压力升高时,要及时放空到火炬线。 [I]-分析转化入口气中氢气浓度,由2%开始,每次依次增加2%,若转化和中变温升都不明显则将氢气浓度继续提高2%,直到循环气中的氢气含量达到20%后,每次增加10%,继续配氢,直到循环气中的氢气含量达到60%以上。注意循环气中氢浓度达到20%以后,每次提高氢气浓度时都相应要把配蒸汽量提高,维持H2O/H2比值在5-7之间。
相应浓度下的配入蒸汽量可参考如下计算: 氮氢气循环量按5000Nm3/h计,H2O/H2比按 5-7计算 最小配汽量kg/h=5000×H2%×5×18/22.4 最大配汽量kg/h=5000×H2%×7×18/22.4 [I]-转化催化剂还原升温控制表: 温度范围(℃)升温速度 (℃/h) 时间(h) 累计时间 (h) 常温~130 10 10 10 130 恒温10 20 130~220 10-15 8 28 220 恒温10 38 220~350 10 12 50 350 恒温10 60 350~800 30 15 75 [I]-转化催化剂还原升温曲线:
催化剂在工艺中的作用
催化剂在化学工艺中的作用 化学化工学院09级5班杨兴平学号:200910240535 摘要:20世纪特别是下半叶以来,由于催化科学和技术的飞速发展,使得数以 百计的工业催化剂开发成功,而数量更多的催化剂,在深刻认识的基础上,得以更新换代。新型催化剂正日益广泛和深入地渗透于石油炼制工业、化学工业、高分子材料工业、生物化学工业、食品工业、医药工业以及环境保护工业的绝大部分工艺过程中,起着举足轻重的作用。本文对催化剂在化学工艺中的作用进行一下简单介绍。 关键词:催化剂的用途;化学工业;分类;制作方法;纳米催化剂;展望 一、催化剂概述: (一) 定义 在化学反应里能改变其他物质的化学反应速率,而本身的质量和化学性质在反应前后都没有发生变化的物质叫做催化剂,又叫触媒。 (二) 基本特性 ①催化剂能够加快化学反应速率,但本身并不进入化学反应的计量。②催化剂对反应具有选择性,即催化剂对反应类型、反应方向和产物的结构具有选择性。 ③催化剂只能加速热力学上可能进行的反应,而不能加速热力学上不能进行的反应。④催化剂只能改变化学反应的速率,而不能改变化学平衡的位置。⑤催化剂不改变化学平衡,意味着对正方向有效的催化剂,对反方向的反应也有效。(三) 用途 在化工生产、科学家实验和生命活动中,催化剂都大显身手。例如,硫酸生产中要用五氧化二钒作催化剂。由氮气跟氢气合成氨气,要用以铁为主的多分组催化剂,提高反应速率。在炼油厂,催化剂更是少不了,选用不同的催化剂,就可以得到不同品质的汽油、煤油。汽车尾气中含有害的一氧化碳和一氧化氮,利用铂等金属作催化剂可以迅速将二者转化为无害的二氧化碳和氮气。酶是植物、动物和微生物产生的具有催化能力的蛋白质,生物体的化学反应几乎都在酶的催化作用下进行,酿造业、制药业等都要用催化剂催作。 1、催化剂在无机化工中的作用 在生产基本无机化工原料的领域中,主要以三酸两碱为核心,它们的产量巨大,是重要的化工原料。其中的硫酸和硝酸分别被称为“化学工业之母和炸药工业之母”,它们在工业和国防部门,都具有重要的价值。 生产硫酸过程中,SO2转化为SO3所用的催化剂,最初是NO2,但设备庞
制氢装置转化炉简介
一、 概述 随着炼油厂加氢装置的逐渐增多,所需要的氢气也越来越多,使得制氢装置相应的发展很快。目前大型工业装置采用的制氢方法均为烃类水蒸汽转化法,利用的原料主要有天然气、炼厂气、石脑油等轻质烃类。这些烃类在特定的温度、压力以及催化剂存在的条件下与水蒸汽发生反应,生成氢气及一氧化碳。 烃类化合物的水蒸汽转化反应是一个复杂的反应平衡系统,高分子烃类先裂解或转化成甲烷,最终与水蒸汽进行转化反应。大体上可用下列反应式表达:CnHm + 2H2O → Cn-1Hm-2 + CO2 + 3H2 – Q CH4 + 2H2O = CO2 + 4H2 – Q CO2 + H2 = CO + H2O - Q 转化炉是制氢装置中转化反应的反应器,属于装置的心脏设备。这是一种非常特殊的外热式列管反应器,由于转化反应的强吸热及高温等特点,这种反应器被设计成加热炉的形式,催化剂装在一根根的转化炉管内,在炉膛内直接加热,反应介质通过炉管内的催化剂床层进行反应。 转化炉苛刻的操作条件,使得这种炉子有很多有别于其它加热炉的特殊性,在炉子结构、炉管材料、管路系统支撑、管路系统应力、管路系统膨胀及补偿、燃烧、烟气流动及分配、耐火材料等各方面都必须精心考虑。 二、 炉型及结构 1. 炉型 制氢装置转化炉按辐射室供热方式进行分类,可分为以下四种方式: 1) 顶烧炉:这是很多公司都采用的一种炉型。这种炉型的燃烧器布置在辐射室顶部,转化管受热形式为单排管受双面辐射,火焰与炉管平行,垂直向下燃烧,烟气下行,从炉膛底部烟道离开辐射室。这种炉型的对流室均布置在辐射室旁边。 2) 侧烧炉:这种炉型以丹麦TOPSφE公司为代表。这种炉子的燃烧器布置在辐射室的侧墙,火焰附墙燃烧。早期转化管的受热形式多为炉膛中间的双排管受侧墙的双面辐射,由于受热形式不好,操作条件苛刻时,炉管易弯曲,现在大部分都改为单排管受双面辐射的形式。这种炉子的烟气上行,对流室置于辐射室顶部,大型装置的对流室考虑到结构及检修等原因,对流室经常放置在辐射室旁边。 3) 梯台炉:这种炉型以美国FOSTER WHEELER公司为代表。这种炉子的辐射室侧墙
制氢装置转化炉简介及制氢原理
制氢装置转化炉简介 一、炉型及结构 1.炉型 制氢装置转化炉按辐射室供热方式进行分类,可分为以下四种方式: 1)顶烧炉:这是很多公司都采用的一种炉型。这种炉型的燃烧器布置在辐射室顶部,转化管受热形式为单排管受双面辐射,火焰与炉管平行,垂直向下燃烧,烟气下行,从炉膛底部烟道离开辐射室。这种炉型的对流室均布置在辐射室旁边。 2)侧烧炉:这种炉型以丹麦TOPSφE公司为代表。这种炉子的燃烧器布置在辐射室的侧墙,火焰附墙燃烧。早期转化管的受热形式多为炉膛中间的双排管受侧墙的双面辐射,由于受热形式不好,操作条件苛刻时,炉管易弯曲,现在大部分都改为单排管受双面辐射的形式。这种炉子的烟气上行,对流室置于辐射室顶部,大型装置的对流室考虑到结构及检修等原因,对流室经常放置在辐射室旁边。 3)梯台炉:这种炉型以美国FOSTER WHEELER公司为代表。这种炉子的辐射室侧墙呈梯台形,燃烧器火焰沿倾斜炉墙平行燃烧,通过炉墙向转化管辐射传热。与侧烧炉类似,转化管可以为双排或单排。这种炉子的对流室全部置于辐射室顶部,烟气上行,采用自然抽风,没有引风机。 4)底烧炉:这种炉型目前多用于小型装置。燃烧器位于辐射室底部,烟气上行。 2.炉型结构比较 2.1传热方式 顶烧炉的燃烧器安装在辐射室顶部,火焰从上往下烧,烟气流动方向与转化管内介质流动方向相同,传热方式为并流传热。侧烧炉燃烧器安装在辐射室侧墙,火焰附墙燃烧,通过辐射墙对转化管传热,烟气流动方向与管内介质流动方向相反,传热方式错流传热。梯台炉的燃烧器排数比侧烧炉要少,是一种改进的错流传热。底烧炉为逆流传热。 2.2热强度及管壁温度温度分布 由于不同的传热方式,所以不同炉型具有不同的热强度和管壁温度分布。顶烧炉火焰集中在炉膛顶部,所以该处辐射传热能力非常强,具有非常高的局部热强度,同时该处的管壁温度也为最高。最高管壁温度和热强度同时在转化管顶部出现峰值是顶烧式转化炉的特点。该特点造成转化管有较高的设计壁温。对于侧烧和梯台转化炉,由于燃烧器均匀分布在沿管长方向的不同标高,辐射传热比较均匀,可避免该峰值,从而降低设计壁温,减少转化管壁厚,节约高合金炉管,或允许较高的转化气出口温度,以降低残余甲烷,提高氢的产率。在管壁设计温度相同时,侧烧炉和梯台炉可以允许较大的总平均管壁热强度,这样传热面积会相应减少,转化管数量有所下降。底烧炉在传热性能上,具有炉顶热强度低,炉底热强度高的特性,因而炉管壁温变化最大,特别是炉底处炉管壁温是所有炉型中最高,对炉管寿命十分不利,为了控制最高管壁热强度不超标,只能选用很低的平均热强度,造成管材的巨大浪费,所以大型装置都不采用底烧炉。 2.3结构特点 顶烧炉的所有转化管排均在同一炉膛内,排列比较紧凑,节省占地面积,适于大型化。侧烧炉和梯台炉由于是两个辐射室并列排列,所以在炉管数量相同时,占地面积较大,大型化有一定的困难。 顶烧炉的燃烧器数量较少,密集排列在炉顶,燃料配管及空气配管相应简化,但炉顶结构比较复杂。侧烧炉燃烧器数量较多,分布在辐射室侧墙,燃料配管及空气配管较多。 2.4对工况的适应情况
新型催化剂在精细化工过程中的应用
新型催化剂在精细化工过程中的应用 化工091班何宝坤学号090006050117 摘要:化工业的发展使得各种新型化工材料得到了广泛的运用,分子筛催化剂作为一种新型催化剂,其微孔结构十分均匀,并且能够让适当的分子进入内部,这种特性使得气体和液体分子分离、离子交换及催化反应在化工业生产上得到了广泛的运用,分子筛催化剂因此在化工原料中逐渐成为新型催化剂。根据实际经验和相关的化工知识本文对分子筛催化剂这种新型催化剂在精细化工过程中的应用情况进行分析。 关键词:新型脂肪醇;精细化工;运用 催化剂制备共性技术及新型催化材料的开发得到高度重视,催化剂制备精细化是改进和提高催化剂性能的重要途径,而催化新材料则是催化剂更新换代和品种多样化的物质基础。新型催化剂和相应的催化工艺的出现,往往以催化新材料和精细化制备工艺为重要前提。国际上自20世纪80年代以来,在此方面的研究十分活跃,政府和许多公司投入大量人力和物力从事研究开发,并在相关领域中长期坚持研究。如联碳公司的磷铝、磷硅铝、金属磷铝分子筛和铑催化体系的磷配体,飞马公司的ZSM分子筛、法国石油研究院的金属有机络合物、杜邦公司的白钨矿结构氧化物、海湾石油公司的层状硅酸盐和硅铝酸盐、英国石油公司的石墨插层化合物、埃克森公司的双、多金属簇团等。 随着纳米技术在催化剂领域的应用,新研制的催化剂的效能大大提高。如:粒径小于0.3nm的镍和铜-锌合金的纳米颗粒的加氢催化剂的效率比常规镍催化剂高10倍。美国科学家发现一种称为钛硅酸盐ETS-4的物质能够作为良好的分子筛。当温度升高时,ETS-4会逐渐脱水,微孔的尺寸随之减小。利用这种方法,可以在3到4埃的范围内精确地调整微孔尺寸。 在开发新材料的基础上,借助催化剂制造精细化技术,有效地调节催化剂孔结构、孔分布、晶粒尺寸、粒径分布、形貌等,并通过控制活性组分分析与载体间相互作用等方法,提高催化剂性能。由于精准控制分子筛的结构使其呈现多样性,以及工业应用取得了意想不到的辉煌成就,使人们更加注意新型催化材料和精细化制备技术的开发。目前,较为活跃的研究领域主要
制氢转化炉施工方案(修改版8.5)
延长石油(集团)公司煤-油共炼试验示范项目40000Nm3/h制氢装置制氢转化炉 安 装 施 工 方 案 编制: 审核: 江苏威达建设有限公司 2013年7月1日 目录
一、编制说明 0 二、工程概况 0 三、编制依据 (1) 四、施工准备 (2) 五、加热炉施工及衬里耐火砖砌筑流程图 (3) 6.1基础验收 (3) 6.2钢结构安装 (4) 6.3转化管安装 (7) 6.4烟囱、烟道、配件的安装 (8) 6.5平台梯子安装 (10) 6.6构件的预制 (10) 6.7 附件的安装 (16) 七、主要工序的施工方法及要求 (17) 7.1 材料检验 (17) 7.2 焊接 (18) 7.3钢结构施工重点、难点及采取的措施 (20) 7.4加热炉主要施工机具表 (20) 八、加热炉钢结构的防腐 (21) 8.1加热炉钢结构的除锈方法 (21) 8.2钢结构涂装施工 (21) 9.1工程质量目标 (22) 9. 2 工程质量保证的原则 (23) 9.3施工前的质量预控及材料验收: (24) 9.4质量控制措施: (25) 9.5施工材料现场保管相关规定 (25) 十、施工安全措施 (25) 10.1HSE管理目标: (25) 10.2 HSE组织责任 (26) 10.3 安全管理细则 (26) 十一、现场文明施工措施相关规定 (31)
一、编制说明 本方案适用于延长石油(集团)公司煤-油共炼试验示范项目40000Nm3/h制氢装置制氢转化炉的钢结构施工。为了较好地控制施工质量,确保安装工作的顺利进行,特制定本方案,作为指导性文件。施工中除应符合本方案的同时,还应符合设计图纸及相应的国家标准。 二、工程概况 2.1 本工程为延长石油(集团)公司煤-油共炼试验示范项目40000Nm3/h制氢装置制氢转化炉的现场安装。转化炉在工厂最大化预制,然后分片发至现场进行安装。转化炉主要由以下部分组成:辐射室、雨棚钢结构、对流室及余热回收系统。转化炉辐射室标高EL+25430mm,长19060mm;转化炉炉顶雨棚标高EL+29578mm;对流室主要由原料预热段、过热蒸汽段、高温板式预热器、蒸发段及低温板式预热器组成。制氢转化炉衬里耐火材料的施工,炉衬施工是炉子的关键工作之一,炉衬的施工直接关系到炉子的生产效率和使用寿命,因此对炉衬的施工应引起足够的重视。炉衬施工前必须做好充分的准备,合理的安排施工人员,与相关工种紧密配合,努力提高工作效率,克服困难,创造条件,高标准,严要求,建精品工程,保证工程按计划顺利进行。 2.2制氢转化炉的主要安装工作量见表 制氢转化炉主要安装工程量
制氢转化炉烘炉
转化炉(F1002)烘炉 1 烘炉目的 转化炉(F1002)炉墙及E1001内衬,是用耐火砖混凝土等筑砌而成,里面含有大量的水份。通过烘炉,可将炉墙中吸附水和结晶水慢慢脱除,以避免在使用过程中因水份急剧蒸发而引起炉墙衬里破坏。通过烘炉,了解炉管的热膨胀情况,掌握炉子的温度调节、E1001使用性能及锅炉系统的热态操作。 2 烘炉具备的条件 2.1 装置冲洗、吹扫合格,系统气密试验合格。 2.2 C1001A/B单机试车合格,负荷试车正常,处于备用状态;P1003A/B、P1004A/B单机试车合格,P1001、P1005标定完毕,负荷试车正常,处于备用状态。 2.3各岗位主要仪表具备投用条件。 2.4 废热锅炉系统建立水循环。 2.5 冷N 2循环时发现问题均已解决,转化炉负压力表已装好,炉区清理各种易燃易爆物品,备好消防器材。 3 转化炉点火前应具备的条件 3.1 用氮气置换燃料气系统至各火嘴小阀前,由F1002顶放空管放空。采样分析合格(O2<0.5%)后,引燃料气至火嘴小阀前。 3.2 启动F1002烟道风机,打开烟道挡板,抽20分钟后炉膛采样作爆炸分析,合格后,调整烟道挡板至合适开度.使炉膛保持合适的负压(-2~-5mmH 2O),F1002就可点火。 3.4 把E1001全部连入系统。 4 升温烘炉 4.1 升温速度见表,升温曲线见图。
升温曲线图 4.2 低温烘转化炉(F1002) 点燃F1001火咀,按升温曲线要求使F1002升温。但要控制F1001自身的温升≯50℃/h,出口温度≯380℃。同时兼顾各反应器的入口温度,防止温度过高损坏反应器。当F1001无法使F1002继续升温,或者F1002炉膛已达到120℃,并经过恒温,即可进行F1002点火。 4.3 F1002点火升温 点燃F1002火嘴应按下列顺序:先两边后中间。同时要使炉子两侧点燃的火嘴对称,避免炉管单侧受热。初始阶段,火焰尽量小些,以避免局部温升过快,以后可根据升温曲线的要求及时增减火嘴。F1002点火后,慢慢降低F1001温度,使其维持在350℃左右。 4.4 F1002升温说明 区域I主要考虑F1002烘炉,故温度以对流段入口的TIC4222为准。烘到950℃之前,要兼顾F1002出口温度(TICA4201)≯840℃,控制升温速度。区域Ⅱ是将测温点由炉膛改至炉管出口的过程,同时也是调整炉出口温度的过程,温度以F1002出口集合管上的TICA4201为准。区域Ⅲ主要考虑工艺上的调整操作和事故演习,故温度仍以TICA4201为准,此时要注意兼顾炉膛温度≯950℃。 5 烘炉注意事项 5.1 注意考察炉管、尾管和集合管的热膨胀,在整个升温阶段应测定并做好记录,了解火嘴燃烧情况以及有关仪表的性能。 5.2 在烘炉过程中,注意各反应器入口温度不要超高,同时外操加强现场管线、设备等的巡查,及时消除漏点,发现异常情况后,立即停止升温。 6 烘炉后的检查 当F1002降温到200℃熄火后,焖炉降温,任其自然降温到100℃以下,打开看火孔,人孔等进行通风降温。烟道风机视降温情况决定开或停,当炉膛温度<40℃后,进行炉膛内部检查,仔细检查炉管有无变形,炉墙衬里有无裂缝,耐火砖有无脱落等问题,查出问题后安排处理解决。F1002烘炉过程中,要兼顾E1001内衬的脱水
制氢装置催化剂的特殊处理
制氢装置催化剂的特殊处理 6.3.1钻钼加氢催化剂再生 钻钼加氢催化剂由于长期使用,表面的积炭量也会产生并 逐步增加,从而使催化剂转化活性下降,影响装置的正常操作,此时,应将钻钼加氢催化剂再生,以提高其活性。催化剂再生一般放在装置停工末期进行,具体步骤如下: 在装置停工末期加氢及脱硫系统通入蒸汽,当温度降至250C时,打开加氢反应器后放空,脱硫反应器通入氮气置换,保压。 加氢反应器的蒸汽流中通入工业风,初期控制混合汽流中氧含量(Q)为0.5 %左右,视床层温度变化调整空气配入量,当床温升至350-400 C时,烧焦速度很快,床层温升明显,因此,必须严格控制蒸汽中配空气量,保证床层不超温,以防破坏催化剂。 在催化剂再生过程中,测试放空气流中CQ及02含量, 监测催化剂再生程度,当放空气中氧含量与配入气流中氧含量相等时,再生完毕,可加大空气量继续吹扫同时切除蒸汽流,当床层温度以30?50 C /h降温速度降至200C左右量,引入N2置换保压。 6.3.2转化催化剂的处理 6.3.2.1转化催化剂钝化
转化催化剂钝化一般是在装置停车且需将催化剂卸出才进行的,所用氧化剂一般用蒸汽即可。 1)当原料气切除之后,转化炉继续通蒸汽对催化剂进 行钝化,温度维持在650 C左右(以不高于700 C为宜),大 约经过6-8小时,至出口气体中不含非冷凝气体为止(诸如氢气、烃类)等,这时可逐步降温,降温速度控制在50 -70 C /h,必要时可关闭部分火嘴。 2)当炉温降至450C左右时,停炉、熄火,通过氮气置换并自然通风冷却至环境温度。 632.2 转化催化剂的烧炭 转化催化剂在实际生产过程中,由于操作不当,例如水碳比过小、原料气净化不好,或者重质烃串入,造成催化剂积炭而失去活性,在催化剂轻微积炭时,可采用蒸汽烧炭的办法,即降低负荷至正常量的30%左右,增大水碳比至10左右,控制正常操作时的温度,以达到消除积炭的目的,同时可以保持催化剂还原态。积炭严重时。必须切除原料,用水蒸汽烧炭,蒸汽量为正常操作的30-40%,压力为0.98MPa左右,严格控制温度,一般温度低于运行时的温度,每半小时分析一次尾气CQ浓度,当其下降并稳定在一个低数值,烧炭结束。空气烧炭法热效应大,反应激烈,对催化剂危害大,一般不宜采用。 6.323 转化催化剂的中毒处理 1)当炉管内反应温度较高时,镍催化剂硫中毒是可逆