铜及其合金的腐蚀问题
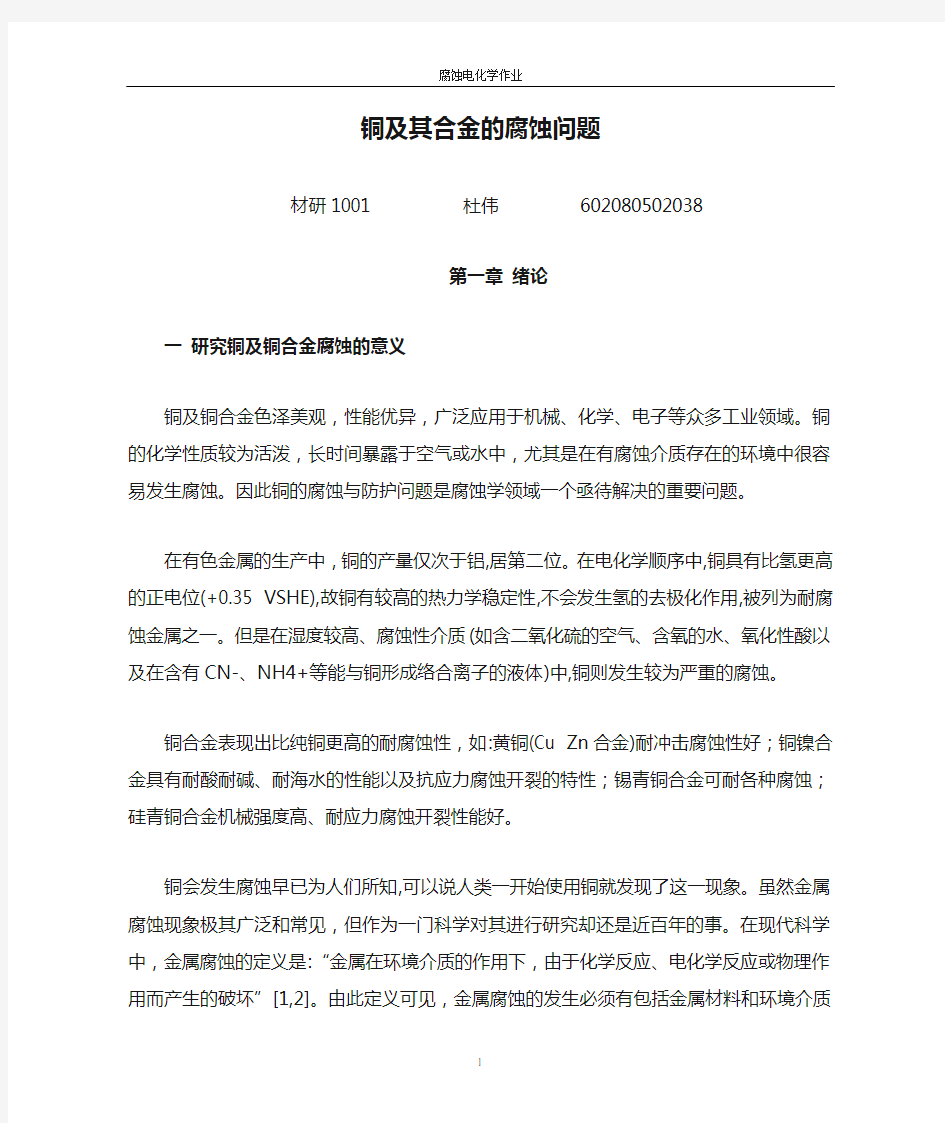

铜及其合金的腐蚀问题
材研1001 杜伟 602080502038
第一章绪论
一研究铜及铜合金腐蚀的意义
铜及铜合金色泽美观,性能优异,广泛应用于机械、化学、电子等众多工业领域。铜的化学性质较为活泼,长时间暴露于空气或水中,尤其是在有腐蚀介质存在的环境中很容易发生腐蚀。因此铜的腐蚀与防护问题是腐蚀学领域一个亟待解决的重要问题。
在有色金属的生产中,铜的产量仅次于铝,居第二位。在电化学顺序中,铜具有比氢更高的正电位(+0.35 VSHE),故铜有较高的热力学稳定性,不会发生氢的去极化作用,被列为耐腐蚀金属之一。但是在湿度较高、腐蚀性介质(如含二氧化硫的空气、含氧的水、氧化性酸以及在含有CN-、NH4+等能与铜形成络合离子的液体)中,铜则发生较为严重的腐蚀。
铜合金表现出比纯铜更高的耐腐蚀性,如:黄铜(Cu Zn合金)耐冲击腐蚀性好;铜镍合金具有耐酸耐碱、耐海水的性能以及抗应力腐蚀开裂的特性;锡青铜合金可耐各种腐蚀;硅青铜合金机械强度高、耐应力腐蚀开裂性能好。
铜会发生腐蚀早已为人们所知,可以说人类一开始使用铜就发现了这一现象。虽然金属腐蚀现象极其广泛和常见,但作为一门科学对其进行研究却还是近百年的事。在现代科学中,金属腐蚀的定义是:“金属在环境介质的作用下,由于化学反应、电化学反应或物理作用而产生的破坏”[1,2]。由此定义可见,金属腐蚀的发生必须有包括金属材料和环境介质在内的相界面上的作用体系,金属发生腐蚀需要外部环境。腐蚀是对金属材料的一种破坏,这种破坏使许多金属设备的使用寿命大为缩短甚至报废,带来巨大的经济损失,它会使生产停顿、物质流失、资源耗损、产品质量降低、环境受到污染、影响新技术的发展。
二铜的腐蚀环境
铜的腐蚀按铜的使用环境可分为气相腐蚀和液相腐蚀,而液相腐蚀可按酸碱度进一步分为酸性液体、中性液体和碱性液体中的腐蚀。在过去的数十年里,人们对铜在酸性溶液中、碱性溶液中和中性盐类溶液中以及自来水供水系统中的腐蚀进行了深入广泛的研究。铜及其合金暴露在通常的中性大气环境中,在其表面
可以生成氧化亚铜(低温)、氧化铜(高温)及碱式碳酸铜保护膜,但在含有腐蚀性气体的工业区大气中,则有明显腐蚀现象。SO2会使铜表面生成碱式硫酸铜[CuSO4·3Cu(OH)2] [3],使铜表面受到破坏,SO2浓度或空气的相对湿度越高,腐蚀速度越快。H2S能使铜表面生成硫化亚铜,然后进一步氧化成硫化铜。大气中的氨与铜作用生成铜氨化合物,当受到雨水的溶解冲洗,也会使铜腐蚀.J.Tidbald等[4]对空气中的腐蚀性气体对铜的腐蚀机理和产物进行了深入研究。在沿海的大气中,含量较高的Cl-与铜反应,生成绿色晶状的碱式氯化铜[CuCl2·3Cu(OH)2],接着会进一步腐蚀。Grant Skennerton等[5]研究了空气中Cl-含量较高,而SO2浓度较低的海岛地区的铜的腐蚀情况。研究表明,铜的表面腐蚀产物主要是氧化铜及碱式氯化铜,由于SO2浓度较低,因此没有碱式硫酸铜生成。
铜在酸性液体中的腐蚀因介质的不同,存在较大差异。按介质分为氧化性酸和非氧化性酸介质引起的腐蚀。无论何种酸性介质,氧气在腐蚀过程中都起着重要的作用。
铜在中性液体介质中的腐蚀,其介质可分为淡水、盐类溶液、海水溶液和有机试剂。铜在淡水中有较高的耐腐蚀性,但考虑到微量铜离子对人体的影响,人们对铜在饮用水系统中的腐蚀行为进行了大量的研究[6]。在工业热交换水系统中,随二氧化碳、溶解氧含量的增加或pH值的减小,铜的腐蚀速率增加。
铜在海水及盐类溶液中的腐蚀情况大致相同,盐的存在使海水的导电性提高,溶解氧含量增高。这些因素为铜的电化学腐蚀提供了条件。Cl-的存在会加剧铜的腐蚀,使铜在溶液中发生溶解。研究结果一致表明,铜的阳极溶解只与Cl-浓度有关而与PH值无关。当Cl-浓度小于1 mol/L时,铜的腐蚀机理如下: 阳极: Cu + Cl-→CuCl +e-
CuCl + Cl-→CuCl2+e-
阴极: O2+4 e- +2H2O →4OH-
当Cl-浓度大于1 mol/L时,将会有CuCl32-和CuCl43-的混合物形成。
在碱性液体中,由于构成金属腐蚀的阴极反应的氧、氢的电极电位较低,与金属铜阳极溶解反应的平衡电位之间电位差较小,在常温条件下,铜的腐蚀速率较低。但随着环境温度升高,溶液浓度增加以及溶液中存在溶解氧时,对铜及其
合金的腐蚀速率会加剧。
三铜及合金的腐蚀特征
铜及铜合金的腐蚀特征包括均匀腐蚀、电偶腐蚀、点蚀、晶间腐蚀、应力腐蚀开裂、腐蚀疲劳和脱合金腐蚀。
(1)均匀腐蚀。铜合金的均匀腐蚀常发生与周围介质的长时间接触,是铜基体的一种均匀减薄,其危害性小,可以用腐蚀失重法来精确定量的评定。
(2)电偶腐蚀。铜合金的电偶腐蚀主要是指铜与比它更正的金属或合金接触时发生的铜优先腐蚀,由于铜合金的电偶序比较靠后,这种情形很少发生。铜合金在诸多介质中常发生点蚀,它是一种危害性很大的腐蚀,常造成铜合金表面产生凹坑和空洞,降低其承载能力,造成应力集中。
(3)点蚀。铜合金点蚀的基本原因是金属表面一些邻近的地方由于金属离子或氧浓度的差别,产生局部的微电池反应,由于氧的去极化作用,氧浓度低的地方成为微电池的阳极,氧浓度高的地方成为阴极,从而造成阳极地方的金属优先溶解,成为点蚀坑。
(4)晶间腐蚀。铜的晶间腐蚀常发生在有高压蒸汽的地方,其特征是腐蚀裂纹沿晶界扩展,穿入晶粒内部造成铜合金的失效。铜合金对晶间腐蚀的敏感性是不一样的,其中46黄铜、铝黄铜、硅青铜较为敏感。
(5)应力腐蚀开裂。黄铜在潮湿的大气中和淡水中都会有应力腐蚀开裂的现象发生其原因是内部存在由于装配工艺造成的外加应力或内部的残余应力造成的。黄铜应力腐蚀开裂的介质因素主要是氨、硫化氢、酸雾、氧和水汽的存在。可以通过选择对开裂不敏感的铜合金,采用消除内应力的热处理方式和改变周围环境介质等途径来抑制黄铜的应力腐蚀开裂。
(6)腐蚀疲劳。腐蚀(通常是点蚀)与周期应力的联合作用可以导致腐蚀的疲劳开裂。与普通疲劳裂纹一样,腐蚀疲劳裂纹在影响区是沿着与最大应力相垂直的方向扩展的,并且这种由于交变应力与腐蚀共同作用的裂纹扩展要比只有交变应力作用下快得多。此外在腐蚀疲劳破坏中常出现许多平行的裂纹,而在一般疲劳中很少超过一条裂纹的。
(7)脱合金腐蚀。铜合金的脱合金腐蚀是一种典型的成分选择性腐蚀,其特征是较活泼的金属组元被优先腐蚀,剩下电位较正的贵金属组元。例如黄铜脱
锌腐蚀,铜铝合金的脱铝腐蚀,铜镍合金在特殊条件下的脱镍腐蚀等,其中以黄铜脱锌最为常见。通过调整黄铜的成分,添加锡、磷、砷、锑等元素在一些黄铜中可以有效地抑制黄铜的脱锌腐蚀。
第二章目前国内外研究进展及及问题
人们很早就开始了对腐蚀及防护技术的研究应用。很多已发掘出的春秋战国时期的武器以及秦始皇时代的青铜剑和大量的箭镞迄今未锈。经过鉴定,发现这些物品表面有一层含铬的氧化层,而基体金属中并不含铬。该表面保护层很可能是用含铬的化合物人工氧化并经高温扩散处理取得的。由此可见早在两千多年以前,人们就创造了与现代铬酸盐(或重铬酸盐)钝化处理相似的防护技术。现代铬酸盐(或重铬酸盐)钝化处理曾作为主要方式长期应用于铜的腐蚀控制中。
长期以来,人们针对铜在不同条件下的腐蚀特点,采用了多种方法来控制铜的腐蚀,主要分为无机钝化技术、有机缓蚀技术、天然类缓蚀剂等。
一无机钝化技术
无机盐类缓蚀剂主要用于铜在中性溶液中的缓蚀。从20世纪20年代起,砷的化合物作为铜系金属缓蚀剂开始使用,后来应用的有亚硫酸钠、硫化钠、铬酸钠等。为了保护铜不受海水和冷却水的腐蚀,也使用过硅酸盐、铬酸盐、锢酸盐、六偏磷酸钠、偏磷酸钠和硝酸钠等作为铜系金属缓蚀剂。随着工业应用和研究的不断深人,相继出现磷酸盐系列、铁盐系列和无机复配系列缓蚀剂、正磷酸盐和偏磷酸盐混合使用可以有效抑制工业冷却水循环系统中铜的腐蚀。
我国工业生产中应用的较多的是采用铬酸盐系列,该工艺操作简单,生产效率高,而且钝化形成的保护膜具有抗腐蚀性强并保持铜及其合金本色等特点,应用很广。其钝化处理形成保护膜的机理是:铜和铜合金在钝化液中溶解,零件和溶液界面处pH值升高,生成碱式盐及氧化物,覆盖在零件表面形成致密钝化膜,随着pH值的不断升高,钝化膜生成速度加快,膜层加厚。还可以通过改变钝化液成分在金属表面上形成彩虹色、银白色或金黄色等多种铬酸盐钝化膜。这种无机钝化膜不仅表面光亮美观,而且与基体有较好的结合力、抗氧化性好,一直被广泛应用。
尽管铬酸盐钝化膜具有很好的耐腐蚀性,但是在处理过程中钝化膜需要的铬酸是微乎其微的,所投入的铬酐大部分都被排放到周围的环境中,一些铬化物是
致癌物质,而且有研究表明铬化物有致突变作用和细胞遗传毒性。因此近年来世界各国对铬酸盐的使用和废水排放做出严格的限定,这致使该技术势必被取代。二有机缓蚀技术
按照使用方式和化合物结构可将有机化合物类缓蚀剂进一步分为唑类缓蚀剂、聚合物膜型缓蚀剂和自组装膜型缓蚀剂三类。
(1)唑类缓蚀剂
早在40年代,人们就已经发现巯基苯并噻唑(MBT)对铜系金属具有较好的缓蚀效果,但由于其水溶性差,应用受到一定的限制。20世纪50年代以后,人们发现苯并三唑(BTAH)在工业水及循环冷却水等中性介质中对铜系金属具有优异的缓蚀性能,并开始了对BTAH的缓蚀机理的研究及其衍生物的开发应用。
研究发现:BTAH在铜表面生成的是多层膜,其组成为Cu/Cu2O/Cu+·BTAH,其中大部分为Cu+·BTAH,与部分因空气氧化变成的Cu2+·BTAH;BTAH的缓蚀效果在pH值为2~12时较好,在pH值为4~10效果更好[7,8];BTAH衍生物对铜具有优异的缓蚀性能:唑环上的氢被甲基取代后,缓蚀效果将大大降低,而苯环上引入烷基缓蚀效果将会增加。G.Brunoro等研究了5-甲基-1,2,3-苯并三唑,5-己基-1,2,3-苯并三唑,5-辛基-1,2,3-苯并三唑和-5甲氧基-1,2,3-苯并三唑对铜在中性或酸性雨中的缓蚀效果。研究表明,苯环上引入烷基缓蚀效果增强。R.Babié等合成了一种新的衍生物DBTO,并采用循环伏安法、电化学阻抗谱和表面增强拉曼光谱研究了其在pH=5.8的醋酸钠溶液中对铜的缓蚀效果和缓蚀机理。结果表明:在铜表面形成的薄膜为Cu/Cu2O/Cu+·DBTO结构,缓蚀剂浓度为0.5 mmol/L时,缓蚀效率就能达到95%以上,从0.5 mmol/L到5 mmol/L的变化过程中,缓蚀效率从95%逐渐接近100%。
BTAH及其衍生物被证明是缓蚀效果最好的缓蚀剂之一,但BTAH主要缺点是有一定的毒性,使用受到限制。故研究工作注意到具有环境亲和性的咪唑类衍生物,研究表明,咪唑类衍生物对大气和酸性条件下的铜具有优异的缓蚀性能,且具有环境亲和性。通过对一系列咪唑类衍生物对中性氯化钠溶液中的铜缓蚀性能研究。结果表明,咪唑类分子在铜表面是物理吸附,含有苯环和不含苯环的衍生物存在不同的缓蚀机理,前者主要通过抑制阳极电化学反应起到缓蚀的效果,而后者是通过抑制阴极的电化学反应起到缓蚀的效果;在所研究的咪唑类衍生物
中,4-甲基-1苯基咪唑的缓蚀性能最为优异,且随着相对分子质量的增加,缓蚀效果逐渐增强。且随着相对分子质量的增加,缓蚀效果逐渐增强。
尽管BTAH在中性和碱性条件下对铜具有优异的缓蚀性能,但其在酸性溶液中的缓蚀效率却急剧下降。铜在氧化性酸中极不稳定,很快会被腐蚀溶解。研究人员研究了铜在硝酸溶液中的溶解动力学,并相继开发出一系列缓蚀剂。由于早期的缓蚀剂不能长期使用,因此,研究重点转向开发新的缓蚀剂或利用协同效应采用复配技术以提高缓蚀效率。
(2)聚合物膜型缓蚀剂
聚合物膜型缓蚀剂是以高分子聚合物作缓蚀剂或通过缓蚀剂组分在界面反应形成聚合物膜而起到缓蚀效果的一类缓蚀剂,如聚乙烯吡啶、聚乙烯胺、聚乙烯哌啶、聚乙炔等。B.Trachli等[9]对2﹣巯基苯并咪唑在铜表面电氧化聚合的动力学及聚合物膜层的缓蚀效果进行了研究。结果表明:2-巯基苯并咪唑首先吸附到铜的表面进而发生了阳极氧化聚合,然后溶液中更多的单体分子吸附到聚合物膜上发生阳极氧化聚合;电化学阻抗谱研究的结果表明铜表面形成的聚合物薄膜在0.5 mol/L的NaCl溶液中的缓蚀效率为99%以上。聚氨基薄膜具有较好的缓蚀效果,而BTAH的加入进一步增强了膜层的缓蚀效果。
(3)自组装膜型缓蚀剂
自组装技术是近20年发展起来的一种新型有机超薄膜技术。自组装单分子膜(self-assemble monolayers,SAMs)的生成是一个自发的过程,将金属或金属氧化物浸入含活性分子的稀溶液中,通过化学键自发吸附在基片上形成取向规整、排列紧密的有序单分子膜,制备方法简单且具有更高的稳定性。
自组装单分子膜的生成是一个自发的过程,将金属或金属氧化物基片浸入含活性分子的溶液或活性物质蒸气中,活性物质在基片表面发生自发的化学反应,通过化学键自发吸附在基片上形成的取向规整、排列紧密的有序单分子膜,制备方法简单且具有高的稳定性[10]。SAMs从结构上可分为三个部分:一是分子的头基,它与基片表面上的反应点以共价键或离子键结合,该反应为放热反应,活性分子会尽可能占据基片表面的反应点;二是分子的烷基链,链与链之间靠范德华力作用使活性分子在固体表面有序且紧密排列,分子链中间可通过分子设计引入特殊的基团和表面结构来获得预期的界面物理化学性质;三是分子末端基团,如
-CH3、-COOH、NH2、-SH,-CH2-CH3等,其意义在于通过选择末端基团以获得不同物理化学性能的界面或借助其反应活性组装多层膜。可选择的分子头基、尾基结构提供了研究基材与分子界面膜排列和生长、附着、润湿性、腐蚀等现象的良好体系。
自组装膜近年来在多个领域中广泛应用,如光学、电子学、生物传感学和机械工程学等,金属表面处理和保护是其重要的工业应用方向之一。自组装单层膜或多层膜在金属腐蚀与防护领域的前景广阔,因为它具有以下优点:
(a)实验方法简单,自组装膜的形成是一个自发的化学吸附过程,只要将底材浸入含活性分子的溶液或蒸汽中,即可形成。
(b)单分子膜结构稳定,堆积紧密。
(c)制备自组装膜过程能耗少,成本低。
(d)单分子层厚度为纳米级,肉眼不可见,不影响表面视觉效果,不会发生像普通涂层那样的脆裂、老化、变色等状况,适合用于贵金属的防护。
(e)自组装膜的形成是一个自发的化学吸附过程,自组装膜与金属表面具有很强的粘合力,被保护金属不论任何形状均可以形成自组装膜。
三天然类缓蚀剂
从天然植物中分离出的松脂和薰衣草油作为抑制酸液体中铜腐蚀的腐蚀剂是铜在酸液体的缓蚀剂的早期应用。后来发现一些胶体物质如阿拉伯胶、蛋白质、明胶、糊精和马铃薯淀粉对盐酸溶液中的铜具有较好的缓蚀效果。此外,采用涂覆润滑油脂的方法来防止腐蚀性气体反应或延缓腐蚀的发生。研究表明:天然蜂蜜对0.5 mol/L的NaCl溶液中的铜具有良好的缓蚀效果,并且蜂蜜在铜表面的吸附遵从Langmiur等温吸附规律,但由于蜂蜜的变质,缓蚀效果在几天后逐渐下降。
第三章铜及铜合金的腐蚀控制方法
防腐蚀,亦称腐蚀控制,其方法是根据腐蚀过程的影响因素来选择。在此基础上,选择那些能使腐蚀过程难以进行的方法,才能有效防止或控制腐蚀,防腐蚀方法根据腐蚀影响因素可分为提高体系热力学稳定性、增强阳极控制过程、增强阴极控制过程和增加电阻控制四种防蚀方法[11,12]。
上述每一种防腐蚀措施,都有其应用的范围和条件。对某种情况有效的措施,
在另一种情况下可能无效,甚至是有害的。在某些情况下,采用单一的防腐措施效果不明显,但如果采用两种或几种措施进行联合保护,其效果就要好得多。因此,对于一个具体的腐蚀体系,究竟采用什么措施,应根据腐蚀原因、环境条件、该措施的防蚀效果、施工难易及经济效益等综合考虑,不能一概而论。
防腐措施目前主要有:合理选用耐蚀材料(根据条件、类型、环境和要求)、阴极保护、阳极保护、介质处理(去除有害成分、调节pH值)、缓蚀剂、表面覆盖、氧化处理等。
一阴极保护
将被保护金属作为阴极,施加外部电流进行阴极极化,或用电化序低的易蚀金属做牺牲阳极,以减少或防止金属腐蚀的方法。阴极保护技术有两种:牺牲阳极阴极保护和外加电流阴极保护。
(1)牺牲阳极阴极保护
牺牲阳极阴极保护技术是用一种电位比所要保护的金属还要负的金属或合金与被保护的金属电性连接在一起,依靠电位比较负的金属不断地腐蚀溶解所产生的电流来保护其它金属。
我们可以在铜及铜合金表面镀一层阳极性镀层。例如,我们可以配方氯化亚锡20g/L,次亚磷酸钠10g/L,硫脲40g/L,柠檬酸40g/L在黄铜表面得到一层致密的镀锡层(图1),来提高黄铜的耐蚀性。
(镀锡前)(镀锡后)
图1 镀锡前后黄铜表面SEM照片
在SEM图片中可以看出,黄铜表面镀锡可以的到一层致密的镀层。
Fig 1 黄铜镀锡和黄铜的阳极极化曲线
在图中可以看到,黄铜镀锡的自腐蚀电流比黄铜的自腐蚀电流,从而可以看到在黄铜表面镀锡可以提高黄铜的耐蚀性。
我们还可以在铜表面镀Zn,目前轮船普遍使用的,可以一定的程度防止电化学腐蚀。
(2)外加电流阴极保护
外加电流阴极保护技术是在回路中串入一个直流电源,借助辅助阳极,将直流电通向被保护的金属,进而使被保护金属变成阴极,实施保护。
图1金属储罐外加电流阴极保护原理示意图
我们可以按照上图来对铜及铜合金产品进行外加电流的阳极保护的设计。二缓蚀剂协同效应
研究表明,单独采用无机类缓蚀剂或有机类缓蚀剂对铜及其合金缓蚀处理还存在某些不易解决的问题,所以众多的研究者试图将各种缓蚀剂复配使用(产生
协同效应)。缓蚀剂技术的近代发展,与研究缓蚀剂之间的协同效应是分不开的。许多工业应用的商品缓蚀剂都是利用协同效应研制的多组分配方。协同效应的作用机理:存在活性阴离子时,活性离子的协同效应指活性离子一金属偶极的负端朝向溶液的架桥作用,有利于有机吸附。有的是缓蚀物质在金属表面形成吸附层,吸附物相互促进吸附层的稳定性。有的是物质间相同的吸附机理通过加合作用产生协同效应。协同效应的研究对于降低铜缓蚀剂的成本,提高缓蚀效率,减少缓蚀剂的负面效应有重要的意义。
近几年来,缓蚀剂协同效应的研究也取得了很大进展。如黄铜材在硫酸酸洗时添加CrO3或K2Cr07进行钝化,早就成为传统生产工艺。为了增强其钝化效果,近年来发展成BTA-CrO3(或铬酸盐)等复合配方,经研究表明:其钝化效果比单一处理得到明显加强。张大全[l3]通过电化学极化曲线和电化学阻抗谱研究了BTA 和8-经基喳琳对铜的缓蚀协同作用,二者复配使用后提高了电极的膜电阻,降低了电极的膜电容,增强了对铜腐蚀的抑制作用,在铜表面形成了更为致密的保护膜从而增加了对金属铜的保护能力。陈一胜等[14,l5]通过失重悬挂法和中性盐雾等腐蚀试验,研究了多种添加剂对铜及其合金的缓蚀作用,结果表明,溶液中加人一定量的有机竣酸和稀土盐后,由于三者的协同效应,显著提高了钝化膜的性能。此外,与碘离子在硫酸的酸性溶液中具有强烈的协同作用,碘离子提高了对铜的缓蚀效果和在铜表面的吸附效率,并在铜表面形成了一层膜。
罗胜联等[16]采用体声波传感技术就卤素离子与BTA协同成膜的动力学及相应复合膜的稳定性进行了研究。结果表明,卤素离子中仅I-与BTA具有协同效应,能有效提高BTA的缓蚀效果和膜层稳定性。张大全等通过静态失重法、电化学极化曲线和电化学阻抗谱研究了BTA和8-羟基喹啉(HQ)对铜的缓蚀协同作用。BTA和HQ复配使用后提高了电极的膜电阻,降低了电极的膜电容,增强了对铜腐蚀的抑制作用,在铜表面形成了更为致密的保护膜,从而增加了对金属铜的保护能力。
第四章研究展望
随着工业和科学技术的进步和发展,铜的腐蚀和保护的研究也日益引起人们更多的重视。综上所述,今后对铜的腐蚀和防护的工作中,开展新的缓蚀剂的研究重点主要是:
(1)利用现有缓蚀剂品种。研究缓蚀剂之间的协同缓蚀机理。以提高缓蚀效果和减少使用量。
(2)加强缓蚀剂的无毒化研究,减少对环境造成污染的缓蚀剂的使用,以减少缓蚀剂对环境和生态造成的不良影响。
(3)利用现代先进的分析测试仪器和计算机技术,从分子和原子水平上研究缓蚀剂在铜表面上的行为及作用机理,开发出高效低毒的和具有环境亲和性的高分子型有机缓蚀剂。
参考文献
[1] 杨文治.缓蚀剂[M].北京:化学工业出版社,1989.135
[2] 周稚狐.缓蚀剂及其应用技术[M].武汉:华中理工大学出版社,1987.211
[3] Brusic V,Frisch M A,Frankel G S.Copper corrosion with and without
inhibitors[J].J Electrochem Soc,1991,138(8):2253—2259
[4] Tidblad J, Graedel T E. Gildes model study ofaqueous chemistry.
Ⅲ. initial SO2induces atmospheric corrosion of copper[J].Corro Sci,1996,38(12):2201— 2224
[5] Grant Skennerton, Jason Nairn. Atmospheric corrosion of copper at
Heron [J]. Island, Material Leters,1997,30(5):141-146.
[6] Feng Y , Teo W K , Siow K S , et al . The corrosion behaveiour of
copper in neutral tap water part 1: corrosion mechanism[J].Corros Sci,1996,38(3):387-395
[7] Alkire R , Cangellari A . Effect of benzotriazole ondissolution of
copper in the presence of fluid flow:I Experimental[J].J Electrochem Soc,1989,136(4):913-919
[8] Modestov D,Zhou G D,Wu Y T,et al.Study of the electrochemical
formation of Cu(I) BTA films on copper electrodes and the mechanism of copper corrosion inhibition in aqueous chloride/benzotriazole solutions[J].Corros Sci,1994,36(5):1931-1946
[9] Trachli B, Keddam M. Protective effect of electropolymerized 2
mercatobenzimidazole upon copper corrosion[J].Progress in Organic Coatings,2002,44(1):17-23
[10] 崔晓莉,江志裕.自组装膜技术在金属防腐蚀中的应用研究[J].腐蚀与防
护,2001,22(8):335-338
[11] 周稚狐.缓蚀剂及其应用技术[M].武汉:华中理工大学出版社,1987.211.
[12] 曹楚南.腐蚀电化学原理[M].北京:化学工业出版社,1982.323.
[13] 张大全.聚合物缓蚀荆的研究开发及应用仁J〕.腐蚀与防护,2000
21(7):300-303
[14] 陈一胜,陈颗,李明茂.稀土在铜及其合金缓蚀剂中的研究[J].表面技术,
2003,32(2):36-37.
[15] 李锋,刘俊,陈颓.铜及其合金表面钝化新工艺研究[J].电镀与涂饰,2005,
24(2):15-17.
[16] 罗胜联,陈金华,陈凡,等.卤素离子与苯骈三氮唑协同成膜动力学的体
声波传感技术研究[J].湖南大学学报:自然科学版,2002,29(1):52-57.
生活饮用水系统零部件用铜合金铸锭
《生活饮用水系统零部件用铜合金铸锭》征求意见稿 编制说明 一、工作简况 根据中色协综字[2010]015号《关于下达2009年第二批有色金属国家标准制(修)订项目计划的通知》的要求,由路达(厦门)工业有限公司负责起草行业标准《生活饮用水系统零部件用铜合金铸锭》(项目序号2009-2042-T-YS)。 通过对生活饮用水系统零部件用铜合金铸锭应用状况的市场调查,我们发现目前由于各铜加工企业的规模、设备技术水平、质量意识不同,铸锭产品质量存在着较大的差别;同时市场上充斥着回收的各类铜合金废料,采用这些废料重熔生产的铜合金锭品质差异大;另外,由于铅黄铜在生产及使用过程中会污染环境,且铅在水中很容易浸出,长期饮用含有铅的自来水将对人的神经系统、骨髓造血机能、消化系统、生殖系统及人体其它功能都有明显毒害作用,特别对老年人、孕妇、婴儿和儿童的健康危害较大(如铅中毒将阻碍儿童的智力发育和骨骼生长,出现贫血、急性铅肾病,免疫力下降,缺锌、缺铁、缺钙等症状),因此其应用受到严格的控制。美日欧等政府已经立法,将逐步在饮用水管道配件中禁止使用含铅产品,且美国NSF/ANSI 61-2007a饮用水标准规定水中铅析出Q值不能超过5μg,因此之前广泛应用的铅黄铜将逐步退出饮用水系统领域,取而代之的是无铅黄铜材料。 随着我国成为世界铜加工中心,对铜及铜合金的需求量越来越大。虽然国内外都有一些的相应铜合金铸锭标准作参考,但这些标准内容比较多,范围比较大,查阅相对困难;同时生活饮用水系统零部件用铜合金铸锭作为铜合金铸锭需求的重要组成部份,目前国内外未见有相应的标准。如果有一个内容较为集中的标准,在客户定牌号及企业新产品试制时,就可以取得时间上的优势,增加竞争力。因此制定一个相应的行业标准十分必要。 接到标准制定任务后,我们成立了《生活饮用水系统零部件用铜合金铸锭》行业标准编制小组。编制小组成员根据标委会的制定精神,进行了全面的市场调
常用金相腐蚀剂
常用金相腐蚀剂(转)
低倍组织浸蚀剂 序号用途成份腐蚀方法附注 A101 大多数钢种 1:1(容积比工业盐酸水溶液 60-80℃热蚀时间: 易切削钢5-10min 碳素钢等5-20min 合金钢等15-20min 酸蚀后防锈方法: a. 中和法:用10%氨水溶液浸泡后再以热水冲洗。 b. 钝化法:浸入浓硝酸5秒再用热水冲洗。 c. 涂层保护法:涂清漆和塑料膜。 A102 奥氏体不锈钢.耐热钢盐酸 10份硝酸 1份水 10份 (容积比) 60-70℃热蚀时间: 5-25min A103 碳素钢合金钢高速工具钢盐酸 38份硫酸 12份水 50份 (容积比) 60-80℃热蚀时间: 15-25min A104 大多数钢种盐酸 500ml 硫酸 35ml 硫酸铜 150g 室温浸蚀在浸蚀过程中,用毛刷不断擦拭试样表面, 去除表面沉淀物可用 A108号浸蚀剂作冲刷液
A105 大多数钢种三氯化铁200g 硝酸 300ml 水 100ml 室温浸蚀或擦拭1-5min A106 大多数钢种盐酸 30ml 三氯化铁 50g 水 70ml 室温浸蚀 A107 碳素钢合金钢 10%-40%硝酸水溶液 (容积比室温浸蚀 25%硝酸水溶液为通用浸蚀剂 a.可用于球墨铸铁的低倍组织显示。 b.高浓度适用于不便作加热的钢锭截面等大试样。 A108 碳素钢合金钢显示技晶及粗晶组织 10%-20%过硫酸铵水溶液室温浸蚀或擦拭 A109 碳素钢合金钢三氯化铁饱和水溶液 500ml 硝酸 10ml 室温浸蚀 A110 不锈钢及高铬.高镍合金钢硝酸 1份盐酸 3份 A111 奥氏体不锈钢硫酸铜 100ml 盐酸 500ml 水 500ml 室温浸蚀也可以加热使用通用浸蚀剂 A112 精密合金高温合金硝酸 60ml 盐酸 200ml 氯化高铁 50g 过硫酸铵 30g 水 50ml 室温浸蚀 A113 钢的技晶组织工业氯化铜铵12g 盐酸 5ml 水 100ml 浸蚀30-60min后对表面稍加研磨则能获得好的效果 A114 显示铸态组织和铸钢晶粒度硝酸 10ml 硫酸 10ml 水 20ml 室温浸蚀 A115 高合金钢高速钢铁-钴和镍基高温合金盐酸 50ml 硝酸 25ml 水 25ml 稀王水浸蚀剂 A116 铁素体及奥氏体不锈钢重铬酸钾 25g (K2Cr2O7) 盐酸 100ml 硝酸 10ml 水 100ml 60-70℃热蚀时间:30-60min 碳钢、合金钢显微组织 序号用途成份腐蚀方法附注 A201 碳钢合金钢硝酸 1-10ml乙醇 90-99ml 硝酸加入量按材料选择,常用3%-4%溶液,1%溶液适用于碳钢中温回火组织及CN共渗黑色组织最常用浸蚀剂。但热处理组织不如苦味酸溶液的分辩能力强 A202 钢的热处理组织苦味酸 2-4g乙醇100ml必要时加入4-5滴润湿剂室温浸蚀浸蚀作用缓慢能清晰显示珠光体、马氏体、回火马氏体、贝氏体等组织,F3C染成黄色 A203 显示极细珠光体戊醇 100ml苦味酸 5g 通风柜内操作不能存放 A204 显示淬火马氏体与铁素体的反差苦味酸 1g水 100ml 70-80℃热蚀时间:15-20秒也可以使用饱和溶液 A205 显示铁素体与碳化物的组织苦味酸 1g盐酸 5ml乙醇 100ml 室温浸蚀 Vilella试剂经 300-500℃回火效果最佳,也可显示高铬钢中的板条马氏体与针状马氏体的区别 A206 显示合金钢回火马氏体 1%硝酸乙醇1份4%苦味酸乙醇1份室温浸蚀
铝合金应力腐蚀理论研究现状
经过一个多世纪的研究,对于引起SCC的机理学术界仍然存在分歧。目前被普遍接受的机理是氢致开裂和阳极溶解机理。 1、氢致开裂 七十年代中期以来,较多实验表明,7×××系高强铝合金的SCC属于氢致开裂机理。该理论认为:(1)氢通过位错迁移到晶界,积聚在析出相附近,使晶界的结合强度大大降低,弱化晶界,造成沿晶断裂;(2)由于氢积聚在裂纹内,形成的氢气压促使合金断裂;(3)氢促进合金形变而致使断裂;(4)形成的氢化物促使合金断裂.目前提出的氢致开裂机理主要有如下理论: (a)氢压理论:当金属中存在过饱和H时,将在各种显微缺陷处结合成H2,室温是不可逆反应,即H2不会再分解成H.随着缺陷处H2浓度增加,氢压也增大.当氢压大于屈服强度时就会产生局部塑性变形,使表层鼓起,形成氢气泡. (b)弱键理论:金属中的氢降低原子键结合力,当局部应力集中等于原子键结合力时原子键破裂,微裂纹形核. (c)氢降低表面能理论:氢降低键合力的同时必然降低表面能,反之亦然.氢吸附在金属裂纹内表面,使表面能降低,导致裂纹失稳扩展所需的临界应力下降.由于没有考虑塑性变形功,故对金属材料不适用. (d)氢致开裂综合机理:此机理综合考虑了氢促进局部塑性变形、氢降低原子键合力以及氢压作用. 2、阳极溶解 阳极溶解理论[7~9]认为阳极金属的不断溶解导致SCC裂纹的形核和扩展,造成合金结构的断裂.铝合金SCC的阳极溶解理论的主要观点如下: (1)阳极通道理论:腐蚀沿局部通道发生并产生裂纹,拉应力垂直于通道,在局部裂纹尖端上产生应力集中.铝合金中预先存在的阳极通道由晶界析出相与基体电位差引起,而应力则使裂纹张开暴露出新鲜表面.在此情形下,腐蚀沿晶界加速进行. (2)滑移溶解理论:发生SCC的铝合金表面氧化膜存在局部薄弱点,在应力作用下合金基体内部位错会沿滑移而产生移动,形成滑移阶梯.当滑移阶梯大、表面膜又不能随滑移阶梯的形成而发生相应变形时,膜就会破裂并裸露出新鲜表面,与腐蚀介质接触,发生快速阳极溶解. (3)膜破裂理论:腐蚀介质中金属表面存在保护膜,由于遭受应力或活性离子的作用而引起破裂,裸露的新鲜表面与其余表面膜构成小阳极大阴极的腐蚀电池,导致新鲜表面发生阳极溶解. 3、阳极溶解与氢致开裂共同作用 阳极溶解与氢致开裂是两个不同的概念,单纯的阳极溶解可通过阴极保护进行预防,而对
铜合金腐蚀
招专业人才上一览英才 铜合金腐蚀 铜合金具有优良的耐大气和海水腐蚀性能,在一般介质中以均匀腐蚀为主。在有氨存在的溶液中有较强的应力腐蚀敏感性,也存在电偶腐蚀、点蚀、磨损腐蚀等局部腐蚀形式。黄铜脱锌、铝青铜脱铝,白铜脱镍等脱成分腐蚀是铜合金独有的腐独形式。 铜合金在与大气和海洋环境相互作用的过程中,表面能生成钝态或半钝态的保护薄膜,使多种腐蚀受到抑制。因此,多数铜合金在大气环境中显示出优良的耐蚀性能。 铜合金的大气腐蚀金属材料的大气腐蚀主要取决于大气中的水汽和材料表面的水膜。金属大气腐蚀速度开始急剧增加时的大气相对湿度称为临界湿度,铜合金与其他很多金属的临界湿度在50%~70%之间,大气中的污染对铜合金的腐蚀有明显的增强作用。城市工业大气的C02,SO2,NO2等酸性污染物溶解于水膜中,发生水解,使水膜酸化和保护膜不稳定。植物的腐烂和工厂排放的废气,使大气中存在氨和硫化氢气体,氨明显加速铜和铜合金的腐蚀特别是应力腐蚀。 铜及铜合金在不同的大气腐蚀环境中腐蚀敏感性有较大差异。在一般的海洋、工业和农村等大气环境中的腐蚀数据报导已有16~20年历史。多数铜合金为均匀腐蚀,腐蚀速度为0.1~2.5μm/a。苛刻的工业大气、工业海洋大气对铜合金的腐蚀速度比温和的海洋大气、农村大气的腐蚀速度要高一个数量级。被污染的大气可使黄铜的应力腐蚀敏感性明显增强。根据环境因素来预测不同大气对铜合金腐蚀的速度并将其分级分类的工作正在开展之中。 海洋环境腐蚀铜合金在海洋环境的腐蚀除了海洋大气区之外,还有海水飞溅区、潮差区和全浸区等。 飞溅区腐蚀铜合金在海水飞溅区的腐蚀行为和在海洋大气区的十分接近。对苛刻的海洋大气具有良好抗蚀性的任何一种铜合金,在飞溅区也会有良好的耐蚀性。飞溅区提供了充分的氧气对钢的腐蚀起到加速作用,但可使铜及铜合金更容易保持钝态。暴露于飞溅区铜合金的腐蚀速度通常不超过5μm/a。 全浸区腐蚀暴露于全浸区铜合金的腐蚀速度最快。其耐蚀性受海水温度、流速、海洋生物附着、泥沙冲刷沉积和海水污染情况的影响较大。材料的加工状态也是十分敏感的影响因素。铜镍合金、铝黄铜、铝青铜、锡青铜、海军黄铜等是在全浸区耐蚀性优良的铜合金材料。多数铜合金在全浸区都具有优良的抗海洋生物附着性能。而铝黄铜等其他抗污性能差的铜合金,在附着的海洋生物下容易产生局部腐蚀。铜和铜合金经16年全浸腐蚀的年均腐蚀速度为1.3~20μm/a,局部腐蚀深度要高一个数量级,最大局部腐蚀深度可达5mm以上。铜镍合金在高速流动海水中的耐蚀性优良。耐蚀性较差或对于环境因素的变化承受能力较差的铜合金,在全浸条件下可能出现脱成分腐蚀、点蚀、缝隙腐蚀,甚至应力腐蚀开裂等局部腐蚀,其力学性能也会因此有不同程度的下降。 潮差区腐蚀铜和铜合金在潮差区受到的腐蚀,比全浸区轻,比飞溅区重,以均匀腐蚀为主,也有局部腐蚀发生。有些现象,如在潮差区,紫铜出现坑蚀,高锌黄铜出现严重脱锌等,都和全浸区的腐蚀结果类似;锡青铜在潮差区的耐蚀性却不如其他铜合金,这情况与铜tong飞
常见的废铜种类
常见的废铜种类 2009-08-26 09:59:17来源: 富宝金属网作者:富宝采编点击次数:7341 废料名称ISRI废料手册要求废料代号 1号铜线No.1 Copper Wire 1级:包括裸露、无涂层、无合金的纯铜线,表面无氧化,不含毛丝,铜线直径不小于1.6mm。2级:包括洁净、无色泽、无涂层、无锡、无合金的纯铜线和铜电缆线,不含毛丝和烧过的易碎的铜线。BarleyBerry 2号铜线No.2 Copper Wire 无合金的废铜线,含有杂料,含铜量为96%(最小含量94%)。不得含有过分铅化和锡化的铜线、焊接过的铜线、黄铜和青铜线、过多的油、废钢铁和非金属、脆的过烧线、绝缘性铜线和过多的细丝线。需用适当方式清除尘垢。Birch 废漆包线—— 1级:纯漆包线,无杂质。2级:经过高温脱漆,表面有氧化层,无杂质。—— 特种紫杂铜各种纯铜废料,主要包括铜材加工厂和铜加工制造厂产生的纯铜的边角料、切头、废次材、半成品、线材、废品等;允许有报废的纯铜裸线和铜管等其它纯铜制品,但不许有水垢、油污、涂层等;废铜料中不允许含有任何杂质和铜合金,也不许含有毛丝、车屑、磨屑和厚度小于1 mm的铜板。 1号紫杂铜No.l Heavy Copper 应包括干净的、无合金、无涂层的加工下脚料、导电板以及直径大于1.6毫米的铜线,材料中允许带有洁净的铜管和其它纯铜块状料,含铜量为98%(最小含铜量大于96%)。不得有焚烧过的脆质铜线。Candy 2号紫杂铜No.2 Copper 应包括混杂纯铜废料,不含铜合金,含铜量为96%(最小含量94%)。不得含有过多的铅和锡、焊接过的废铜、过多的油、钢铁、非金属废料、带非铜接头的铜管或带有残渣的铜管、烧过的或有绝缘性的铜线、毛丝、焚烧后的脆质铜线、泥土等。Cliff 1号铜米No.1 Copper Wire Nodules 应包括1号裸露、无涂层、无合金的废铜线的铜米,最低含铜量为99%,不含毛丝。不含锡、铅、锌、铝、铁及其他金属杂质,无绝缘物,不含其他杂质。Clove 2号铜米Copper Wire NodulesNo.2 Copper Wire Nodules 1级:应包括无合金的废铜线铜米,最低含铜量为99%,不含其它非金属和绝缘物。金属杂质最大限量如下:铝0.05% 镍-0.05% 铁-0.05% 锡-0.25% 锑-0.01%2级:应包括2号无合金的废铜线加工的铜米。最低含铜量为97%,金属杂质铝含量不超过0.5%,其它金属或绝缘物均不超过1%。CocoaCobra
金相显微镜试样的腐蚀5种方法腐蚀剂
金相试样腐蚀5种方法及常用腐蚀剂全解析 金相组织反射能力差别必须至少为10%以上时,才能反射不同强度的光而被观察到,然而,抛光后的试样表面因为入射光线几乎均匀地被反射回来而不能显示金相组织。因此,为了看清楚,通常必须将组织造成反差。为得到这种反差,试样通常需要进行金相进行处理,常用的处理方法包括:化学浸蚀、电解浸蚀、阴极真空浸蚀、热腐蚀和薄膜干涉法。 1.化学浸蚀 18CrNiMo7-6钢,Beraha's 10/3浸蚀 纯金属及单相合金的化学浸蚀是一个化学溶解的过程。由于晶界上原子排列不规则,具有较高自由能,所以晶界易受腐蚀而呈凹沟,使组织显示出来,在显微镜下可以看到多边形的晶粒。若腐蚀较深,则由于各晶粒位向不同,不同的晶面溶解速率不同,腐蚀后的显微平面与原磨面的角度不同,在垂直光线照射下,反射进入物镜的光线不同,可看到明暗不同的晶粒。
镁铝合金化学腐蚀 多相合金的化学浸蚀,在腐蚀过程中腐蚀剂对各个相有不同程度的溶解。必须适用合适的腐蚀剂,如果一种腐蚀剂不能将全部组织显示出来,就应采取两种或更多的腐蚀剂依次腐蚀,使之逐渐显示出各相组织,这种方法也叫选择腐蚀法。另一种方法是薄膜染色法。此法是利用腐蚀剂与磨面上各相发生化学反应,形成一层厚薄不均的膜(或反应沉淀物),在白光的照射下,由于光的干涉使各相呈现不同的色彩,从而达到辨认各相的目的。 2.电解浸蚀 409不锈钢,草酸电解腐蚀 化学浸蚀是无外电源作用的,而电解浸蚀则是将抛光试样浸入合适的化学试剂的溶液中(电解浸蚀剂),通过较小的直流电进行浸蚀。电解浸蚀工作电压和工作电流通常较小,工作电压一般在2~6V之间,工作电流约0.05~0.3A/cm2。电解浸蚀主要用于化学稳定性较高的合金,如不锈钢,耐热钢,镍基合金等,这些合金用化学浸蚀很难得到清晰的组织。 稳定电势浸蚀: 电解浸蚀的一种改良方法称为稳定电势浸蚀。通常电解质中浓度变化而有不同电流负荷,致使试样电势经常变化,用电势稳定器使电势保持不变,就可以得到其它浸蚀方法所不能得到的清晰的反差。 恒电位蚀刻沉积法首先要确定某种金属在某一电解液中的极化曲线,根据极化曲线选取合适的蚀刻电位,然后根据合金中各相的成膜速率不同,利用恒电位仪使该金属在这一外加恒电位作用下完成全部的蚀刻沉积过程。因为各相晶格能不同,在一定电位下成膜速度不同,膜厚不同,因而出现了不同干涉色。 3.阴极真空浸蚀
铜的腐蚀及防护措施
铜的腐蚀及防护措施 铜的腐蚀种类及腐蚀产物 影响铜及其合金腐蚀的因素有材料因素(包括成分、杂质、第二相及热处理、表面状态、变形和应力等)和环境因素(包括腐蚀环境如大气、土壤、海水、工业酸碱盐有机溶剂等及环境因素的影响如介质的pH值、介质的成分和浓度、介质的温度和压力、介质流动速度、电偶、环境的细节和可变化的影响等)。铜的腐蚀按照其使用地点和腐蚀介质可分为大气腐蚀、水中腐蚀、土壤腐蚀,铜的腐蚀产物一般为氧化物、硫酸盐和氯化物。 铜的腐蚀种类 大气腐蚀当铜暴露于大气之中,其表面通常形成绿棕色或者蓝绿色的腐蚀薄层,称为铜绿。铜在大气中的腐蚀主要受到气候条件、大气中有害气体及悬浮物的影响。气候条件包括大气相对湿度、气温及日光照射、风向、风速等。大气中有害气体及悬浮物主要指SO2、NH3、H2S等腐蚀性气体及盐的细小尘埃。Lobnig R E发现,如果大气中只含SO2或只含水分,铜的腐蚀行为没有多大变化,但如果二者都存在,且相对湿度超过75%,腐蚀是显著的。这主要是因为在铜表面上吸附水膜下SO2增加了阳极的去钝化作用,在高湿度条件下,由于水膜凝结增厚,SO2参与了阴极的去极化作用,尤其是当SO2的质量分数>0.5%时,此作用明显增大,因而加速了腐蚀的进行。虽然大气中SO2含量很低,但它在水溶液中的溶解度很大,SO2溶于水膜生成的H2SO3是强去极化剂,对大气腐蚀有加剧作用。 水中腐蚀:铜及铜合金在在水中的腐蚀可分为纯水腐蚀和海水腐蚀。铜及铜合金在含氧纯水中的腐蚀是吸氧腐蚀,在一定条件下,阳极反应产生的Cu2O可在铜表面形成完整的保护膜,其表层的Cu2O在水中溶解氧的作用下被部分氧化成CuO。因此,铜表面的氧化物保护膜具有双层结构,其内层为Cu2O,外层则由Cu2O 和CuO组成。铜表面这种保护膜的形成防止了铜在水中的进一步腐蚀,其完整性和稳定性也就决定了铜在水中的腐蚀速度。铜及铜合金在海洋环境中以均匀腐蚀为主,其中全浸区最重,潮汐区次之,飞溅区最轻。通过铜及其合金的长期暴露试验[7]发现,随着暴露时间增加,铜及铜合金平均腐蚀速度降低,然而随着海水温度升高,多数铜及其合金在全浸区平均腐蚀速度会增加,在潮汐和飞溅区,腐蚀速度会下降。 土壤腐蚀:铜是一种耐土壤腐蚀的材料,一般情况发生均匀腐蚀。王永红等人[8]采用试件自然埋藏法对内陆盐土地铜的腐蚀进行了研究,发现Cl-、SO42-及土壤微生物使铜表面发生了严重的点蚀,经过一的实验,试件表面布满蚀坑,最大腐蚀孔深度为0.36mm,平均腐蚀率为1.1884g/(dm2?a)。铜在内陆盐土中呈局部斑点腐蚀,同时还注意到铜的土壤腐蚀具有季节周期性,其腐蚀率最小值发生在秋冬季(11月至1月)。
铜冶炼铜电解铜废渣废物废泥铜合金硫化铜矿铜精矿回收处理工艺技术与设备专利技术资料汇编样本
4铜冶炼、铜电解、铜废渣泥、铜合金、硫化铜矿、铜精矿、回收处理工艺与方法、专利技术资料汇编( 全套80元) 1.铜锌物料鼓风炉熔炼铜锌分离方法 2.铜回收法 3.铜沉淀方法 4.印制线路板碱性蚀刻铜废液处理方法 5.分离回收镀白铜针铜锡的方法及其阳极滚筒装置 6.废铜箔回收的方法1 7.废铜箔的回收方法2 8.在印刷电路板制造中利用对铜箔的金属化处理来产生细线条并替代氧化过程 9.铜锌钴分离的熔炼法 10.用不污染环境的方法回收覆铜板的铜 11.一种铜电解液净化除杂质的方法 12.紫杂铜一步电解生产阴极铜方法 13.湿法提铜工艺 14.电解铜废液处理工艺 15.一种铜转炉烟灰矿渣成团冶炼铅的新工艺及其成团配方 16.铜回收的方法 17.由电解含铜萃取有机相制备高纯铜的方法 18.含砷硫化铜精矿湿法冶炼新工艺 19.冶炼炉渣中的有价金属细菌回收方法 20.一种废锌铜镍合金的湿法分离方法 21.黑铜提锡工艺 22.双金属银铜复合边角料分离回收法 23.氯化铜废液的处理方法 24.用碳铵溶液电解退除铁基体铜,镍镀层的方法 25.一种新的硫酸铜制备方法 26.不锈钢阳极框杂铜直接电解精炼法 27.铜系废催化剂的回收方法
28.氧化铜矿直接制取硫酸铜工艺 29.从稀溶液中电解回收铜或银的装置 30.液-液萃取法净化铜电解液 31.使用卤化物的铜蚀刻方法 32.从黄杂铜中分离铜、锌、铅、铁、锡的工艺方法 33.铜及铜合金制品表面上铅锡的回收 34.一种从氧化铜矿中回收铜的湿法冶金方法 35.湿法冶铜新工艺 36.铜矿石生产硫酸铜的方法 37.氨浸沉淀法处理低品位铜渣或氧化铜矿的工艺 38.铜精矿粉末冶炼备料新工艺 39.废复铜板回收工艺 40.从硫化物铜矿中浸提回收铜、银、金、铅、铁、硫的方法及设备 41.一种从含铜较高的金精矿中提取铜的方法 42.从炼铜废渣中回收锡、铜、铅、锌等金属的方法 43.含铜废料直接电解精炼的方法 44.一种铜精矿粉制块工艺 45.回收铜的方法 46.生产一水硫酸铜的方法 47.从矿石中水冶提取铜、镍、钴的简易方法及其装置 48.从铅阳极泥提取金、银及回收锑、铋、铜、铅的方法 49.从绕组回收铜的方法 50.一种硫化铜镍矿选矿方法 51.铜的回收方法 52.铜、镍硫化矿无污染火冶法 53.由硫化镍精矿中提取镍、铜、钴、镁及制造镍铁的工艺 54.一种湿法分离锌、铜、镉、铅冶金物料的方法及应用 55.回收铜和镍 56.电路板的铜箔回收方法
常用金相试样化学腐蚀剂
常用金相试样化学腐蚀剂 浸蚀剂名称成份适用范围及使用要点 硝酸酒精溶液硝酸2-4ml 酒精100ml 各种碳钢、铸铁等 苦味酸酒精溶液苦味酸4g 酒精100ml 珠光体、马氏体、贝氏体、渗碳 体 盐酸苦味酸盐酸5ml 苦味酸1g 水100ml 回火后马氏体或奥氏体晶粒 氯化铁盐酸水溶液氯化铁5g 盐酸50ml 水100ml 奥氏体-铁素体不锈钢 奥氏体不锈钢 混合酸甘油溶液硝酸10ml 盐酸30ml 甘油30ml 奥氏体不锈钢 高Cr Ni耐热钢 王水酒精溶液盐酸10ml 硝酸3ml 酒精100ml 18-8型奥氏体钢的δ相 三合一浸蚀液盐酸10ml 硝酸3ml 甲醇100ml 高速钢回火后晶粒 硫酸铜盐酸溶液盐酸100ml 硫酸5ml 硫酸铜5g 高温合金 氯化铁溶液氯化铁30g 氯化铜1g 氯化锡0.5g 盐酸50g 铸铁磷的偏析与枝晶组织 苦味酸钠溶液苦味酸1g 水100ml 区别渗碳体和磷化物 氯化铁盐酸水溶液氯化铁5g 盐酸15ml 水100ml 纯铜、黄铜及铜合金 绿化铜盐酸溶液氯化铜1g 氯化镁4g 盐酸2ml 灰铸铁共晶团
酒精100ml 硫酸铜-盐酸溶液硫酸铜4g 盐酸20ml 水20ml 灰铸铁共晶团 硫酸铜-盐酸溶液硫酸铜5g 盐酸50ml 水50ml 高温合金 盐酸-硫酸-硫酸铜溶液硫酸铜5g 盐酸100ml 硫酸5ml 高温合金 复合试剂硝酸30ml 盐酸15ml 重铬酸钾5g 酒精30ml 苦味酸1g 氯化高铁3g 高温合金 硬质合金试剂A饱和的三氯化铁 盐酸溶液 B新配置的20%氢氧 化钾水溶液+20%铁 氰化钾水溶液 硬质合金先在A试剂中浸蚀 1min,然后在B试剂中浸蚀3min, WC相(灰白色),TiC-WC相(黄 色)Co(黑色) 氢氧化钾-铁氰化钾水新配置的10%氢氧 化钾水溶液+10%铁 氰化钾水溶液 硬质合金的n相 混合酸硝酸2.5ml 氢氟酸1ml 盐酸1.5ml 水95ml 显示硬铝组织 氢氟酸水溶液氢氟酸0.5ml 水99.5ml 显示一半铝合金组织 苛性钠水溶液苛性钠1g 水100ml 显示铝与铝合金组织
金相实验腐蚀剂
金相实验腐蚀剂 低倍组织浸蚀剂 [1] 大多数钢种 1:1(容积比工业盐酸水溶液、60-80℃热蚀) 时间: 易切削钢5-10min 碳素钢等5-20min 合金钢等15-20min 酸蚀后防锈方法: a.中和法:用10%氨水溶液浸泡后再以热水冲洗。b.钝化法:浸入浓硝酸5秒再用热水冲洗。c.涂层保护法:涂清漆和塑料膜。 [2]奥氏体不锈钢.耐热钢 盐酸:10份硝酸:1份水:10份(容积比) 60-70℃热蚀时间: 5-25min [3]碳素钢合金钢高速工具钢 盐酸:38份硫酸:12份水:50份(容积比) 60-80℃热蚀时间: 15-25min [4]大多数钢种 盐酸:500ml 硫酸:35ml 硫酸铜:150g 室温浸蚀在浸蚀过程中,用毛刷不断擦拭试样表面, 去除表面沉淀物可用 [8]号浸蚀剂作冲刷液 [5]大多数钢种 三氯化铁:200g 硝酸:300ml 水:100ml 室温浸蚀或擦拭1-5min [6]大多数钢种 盐酸:30ml 三氯化铁:50g 水:70ml 室温浸蚀 [7]碳素钢合金钢 10%-40%硝酸水溶液(容积比、室温浸蚀、25%硝酸水溶液为通用浸蚀剂)a.可用于球墨铸铁的低倍组织显示。b.高浓度适用于不便作加热的钢锭截面等大试样。 [8]碳素钢合金钢显示技晶及粗晶组织
10%-20%过硫酸铵水溶液,室温浸蚀或擦拭。 [9]碳素钢合金钢 三氯化铁饱和水溶液:500ml、硝酸:10ml 室温浸蚀 [10]不锈钢及高铬.高镍合金钢 硝酸:1份盐酸:3份 [11] 奥氏体不锈钢 硫酸铜:100ml 盐酸: 500ml 水:500ml 室温浸蚀也可以加热使用,通用浸蚀剂[12]精密合金高温合金 硝酸:60ml 盐酸:200ml 氯化高铁:50g 过硫酸铵:30g 水:50ml 室温浸蚀 [13]钢的技晶组织 工业氯化铜铵12g 盐酸:5ml 水:100ml 浸蚀30-60min后对表面稍加研磨则能获得好的效果 [14]显示铸态组织和铸钢晶粒度 硝酸:10ml 硫酸:10ml 水:20ml 室温浸蚀 [15]高合金钢高速钢铁-钴和镍基高温合金 盐酸:50ml 硝酸:25ml 水:25ml 稀王水浸蚀剂 [16]铁素体及奥氏体不锈钢 重铬酸钾 25g (K2Cr2O7)盐酸:100ml 硝酸:10ml 水:100ml 60-70℃热蚀时间:30-60min 碳钢、合金钢显微组织 [1]碳钢合金钢 硝酸:1-10ml乙醇 90-99ml
铝合金应力腐蚀开裂ASTM G139(中文翻译版)
用断裂负荷法测定热处理铝合金制品抗应力腐蚀开裂性的标准试验方法(等同采用ASTM G139-05(R2011))(中文翻译版) 编制: 日期: 审核: 日期: 批准: 日期: 修订历史 修订序号对应的条号修订内容修改人批准人日期
1. 目的Purpose 本标准试验方法涵盖了通过断裂荷载试验方法评估抗应力腐蚀开裂(SCC)性的程序,该方法使用剩余强度作为损伤演化(在这种情况下为环境辅助开裂)的测量方法。包括试样类型和复制、试验环境、应力水平、暴露时间、最终强度测定和原始残余强度数据的统计分析。 2. 范围Scope 本标准试验方法适用于热处理铝合金,即2XXX合金和7XXX,含1.2%至3.0%铜,且试样的取向与晶粒结构相关,横向较短。然而,用于分析数据的残余强度测量和统计数据并非针对可热处理铝合金,可用于其他试样取向和不同类型的材料。 3. 职责Responsibility 程序执行:实验室授权制样人员 程序监督:实验室技术负责人及相关责任人 4. 原理Principle 4.1本试验方法描述了使用暴露于腐蚀环境后的残余强度评估热处理铝合金产品形式(如板材、板材、挤压件、锻件和棒材)的应力腐蚀开裂敏感性的程序。这些产品通常在板材的长横方向、板材、挤压件和锻件的短横方向以及棒材和棒材的横方向上最易发生应力腐蚀开裂。在本试验中,根据规程G49制备的拉伸钢筋或直接拉伸板试样暴露于3.5重量%的氯化钠水溶液(规程G44)中,在其失效前移除,并进行拉伸试验,以确定已发生的腐蚀损伤量。然后计算平均剩余强度,并使用Box-Cox变换对结果进行统计分析。 4.2该程序要求暴露无应力试样,用于排除点蚀、晶间腐蚀和一般腐蚀的影响。这些现象会降低残余强度,但不
废旧有色金属回收技术标准
废旧有色金属回收技术标准 我国对于废杂有色金属的评价与回收利用管理,目前尚没有明确的规定。据悉,新的《铜及铜合金废料废件分类和技术条件》、《铝及铝合金废料废件分类和技术条件》等一系列技术标准正在编制中。预计,将会有较多的参考美国和欧洲的成功经验。对于废旧有色金属,本书暂引用1992年由国家技术监督局颁布的推荐GB和1996年国家环境保护局颁布的进口废物控制标准,备读者查阅。 1.标准号 GB/T13587~1992《铜及铜合金废料、废件分类和技术条件》 GB/T13588~1992《铅及铅合金废料、废件分类和技术条件》 GB/T13889~1992《锌及锌合金废料、废件分类和技术条件》 GB/T13586~1992《铝及铝合金废料、废件分类和技术条件》 GB16487.7~1996《进口废物环境保护控制标准,废有色金属(试行)》 GBl6487.8~1996《进口废物环境保护控制标准,废电机(试行)》 GB16487.9~1996《进口废物环境保护控制标准,废电线电缆(试行)》 GB16487.10~1996《进口废物环境保护控制标准,废五金电器(试行)》 2.有色金属废料、废件的种类 铜、铝、铅、锌、锡、镍 锑、钴、镁、钛、锰、镉、铬、金、银、铂、钯、钉、铑、锇、铱 锂、铍、铷、铯、钨、钼、钮、钽、锆、铪、钒、钛、铼、镓、铟、铊、锗、硒、碲、镧、铈、镨、钕、 钐、铕、钆、铽、镱、钇、钪、钜、镝、铒、镥、铥、钬 紫铜板、带、箔、管、棒、杆、线、型材 黄铜板、带、箔、管、棒、线、型材 锌白铜板、带、管、丝材 镍自铜板、带、管、丝材 锡磷青铜带材、铍青铜带材 铝合金板、带、箔、管、棒、线、型材 铅合金材、铅锡合金焊丝、金、银、铂、钯、铱及其合金带、箔、丝材 铝铜复合板带、紫铜复银带、青铜复银带、镀锡黄铜带 铜、铝、铅、锌合金锭及铸件 钛及钛合金带、箔、管、棒和铸件 锆及锆合金管、棒材 铌及铌合金管材 钼带、箔材 高纯稀土金属、单一稀土氧化物、共沉淀稀土氧化物 彩电荧光粉、灯用三基色荧光粉、计算机用终端显示粉 钐钴粉、钐钴磁钢
铝合金及铜合金金相制样的制备
铝合金及铜合金金相制样的制备 材料成型实验室内部资料 2012.9.14 内容是根据个人经验总结得来,每个人的经验可能不同,具体操作技巧还有自己多磨多总结,本文仅供参考。刚开始一般几天都很难磨好一个样,但熟练后一天10-20个不成问题。如果谁有上面好的经验可以慢慢总结尽量,慢慢完善。 金相试样制备步骤:取样、镶样、标号、磨光、抛光、显示。 一、取样、镶样、标号 根据所需检测面的组织取样(手工锯或线切割),确定磨哪个面,然后再镶样机上镶样(样品大小如果合适就不必镶样),并对所取样品进行编号标示,以免样品多或放置时间长而导致样品混乱分不清。保证每个样品用一个样品袋装着并贴上标签纸。 二、磨光、抛光 1、磨光 原则(最终要求):一个平面、划痕朝一个方向 磨光一般包括粗磨和细磨两个阶段,每步都要达到上面要求即只有一个平面,划痕朝一个方向;粗磨一般在300-1000的砂纸上进行,细磨一般在1500-2000上砂纸上进行,样品比较平整的可以直接进行细磨。 技巧:手拿着样品放在预磨机上保证压力均匀的压着样品,用力要适中,手不动。细磨时也可以不在预磨机上直接把砂纸放在桌之上手工磨,手工磨时要保证磨的方向朝一个方向,用力均匀。 初学者容易出现的问题:a、磨出几个平面;b、磨成斜面;c、磨的时候没加水找出严重氧化;d、手指拿样品时靠砂纸太近,不知不觉把手机磨破; 2、抛光 原则(最终要求):光亮、无划痕、无污点 抛光在抛光机上进行,抛光布有软些的和较硬的,根据实际情况选择那种抛光布,也可以粗抛时在硬一点的布上抛,然后再在软一些的布上抛,抛光时一般都要不定期的加抛光粉,加入量根据实际情况确定,一般是开始时粗抛加多点,后面少加点。抛光时样品压在抛光布上的压力一定要把控好,一般也是开始时压力大点,到后面基本不用力,就让样品跟抛光布轻轻接触。最后保证样品达到上面要求。 抛光一般在5-30分钟即可抛好,如果超过30分钟样品表面容易出现颗粒掉落、应力等缺陷,建议用砂纸(1500-2000)细磨后重新抛光 技巧:手拿样品控制好压力,开始时可以用点力,多加点抛光粉,且手拿样品从抛光布中央向边缘(线速度大)游走,这样即可以使磨光过程产生的粗大划痕可以快点磨掉,也能延长抛光布的使用寿命;到后期则基本不用力,保证样品跟抛光布接触即可,同时抛光粉稍微少加点,但一般不建议不加用清水抛,清水抛容易出新划痕,手拿样品让样品从边缘向中
一些常用的金相腐蚀剂
低倍组织浸蚀剂 序号用途成份腐蚀方法附注 A101 大多数钢种1:1(容积比工业盐酸水溶液60-80℃热蚀时间: 易切削钢5-10min 碳素钢等5-20min 合金钢等15-20min 酸蚀后防锈方法: a. 中和法:用10%氨水溶液浸泡后再以热水冲洗。 b. 钝化法:浸入浓硝酸5秒再用热水冲洗。 c. 涂层保护法:涂清漆和塑料膜。 A102 奥氏体不锈钢.耐热钢盐酸10份硝酸1份水10份(容积比) 60-70℃热蚀时间: 5-25min A103 碳素钢合金钢高速工具钢盐酸38份硫酸12份水50份(容积比) 60-80℃热蚀时间: 15-25min A104 大多数钢种盐酸500ml 硫酸35ml 硫酸铜150g 室温浸蚀在浸蚀过程中,用毛刷不断擦拭试样表面, 去除表面沉淀物可用A108号浸蚀剂作冲刷液 A105 大多数钢种三氯化铁200g 硝酸300ml 水100ml 室温浸蚀或擦拭1-5min A106 大多数钢种盐酸30ml 三氯化铁50g 水70ml 室温浸蚀 A107 碳素钢合金钢10%-40%硝酸水溶液(容积比室温浸蚀25%硝酸水溶液为通用浸蚀剂 a.可用于球墨铸铁的低倍组织显示。 b.高浓度适用于不便作加热的钢锭截面等大试样。 A108 碳素钢合金钢显示技晶及粗晶组织10%-20%过硫酸铵水溶液室温浸蚀或擦拭 A109 碳素钢合金钢三氯化铁饱和水溶液500ml 硝酸10ml 室温浸蚀 A110 不锈钢及高铬.高镍合金钢硝酸1份盐酸3份 A111 奥氏体不锈钢硫酸铜100ml 盐酸500ml 水500ml 室温浸蚀也可以加热使用通用浸蚀剂 A112 精密合金高温合金硝酸60ml 盐酸200ml 氯化高铁50g 过硫酸铵30g 水50ml 室温浸蚀 A113 钢的技晶组织工业氯化铜铵12g 盐酸5ml 水100ml 浸蚀30-60min后对表面稍加研磨则能获得好的效果 A114 显示铸态组织和铸钢晶粒度硝酸10ml 硫酸10ml 水20ml 室温浸蚀 A115 高合金钢高速钢铁-钴和镍基高温合金盐酸50ml 硝酸25ml 水25ml 稀王水浸蚀剂 A116 铁素体及奥氏体不锈钢重铬酸钾25g (K2Cr2O7) 盐酸100ml 硝酸10ml 水100ml 60-70℃热蚀时间:30-60min 碳钢、合金钢显微组织 序号用途成份腐蚀方法附注 A201 碳钢合金钢硝酸1-10ml乙醇90-99ml 硝酸加入量按材料选择,常用3%-4%溶液,1%溶液适用于碳钢中温回火组织及CN共渗黑色组织最常用浸蚀剂。但热处理组织不如苦味酸溶液的分辩能力强 A202 钢的热处理组织苦味酸2-4g乙醇100ml必要时加入4-5滴润湿剂室温浸蚀浸蚀作用缓慢能清晰显示珠光体、马氏体、回火马氏体、贝氏体等组织,F3C染成黄色 A203 显示极细珠光体戊醇100ml苦味酸5g 通风柜内操作不能存放 A204 显示淬火马氏体与铁素体的反差苦味酸1g水100ml 70-80℃热蚀时间:15-20秒也可以使用饱和溶液 A205 显示铁素体与碳化物的组织苦味酸1g盐酸5ml乙醇100ml 室温浸蚀Vilella试剂经300-500℃回火效果最佳,也可显示高铬钢中的板条马氏体与针状马氏体的区别 A206 显示合金钢回火马氏体1%硝酸乙醇1份4%苦味酸乙醇1份室温浸蚀 A207 用于区分奥氏体、马氏体和回火马氏体4%硝酸乙醇100ml4%苦味酸乙醇10ml硝酸2ml 水20ml 室温浸蚀
铜及其合金的腐蚀问题
铜及其合金的腐蚀问题 材研1001 杜伟 602080502038 第一章绪论 一研究铜及铜合金腐蚀的意义 铜及铜合金色泽美观,性能优异,广泛应用于机械、化学、电子等众多工业领域。铜的化学性质较为活泼,长时间暴露于空气或水中,尤其是在有腐蚀介质存在的环境中很容易发生腐蚀。因此铜的腐蚀与防护问题是腐蚀学领域一个亟待解决的重要问题。 在有色金属的生产中,铜的产量仅次于铝,居第二位。在电化学顺序中,铜具有比氢更高的正电位(+0.35 VSHE),故铜有较高的热力学稳定性,不会发生氢的去极化作用,被列为耐腐蚀金属之一。但是在湿度较高、腐蚀性介质(如含二氧化硫的空气、含氧的水、氧化性酸以及在含有CN-、NH4+等能与铜形成络合离子的液体)中,铜则发生较为严重的腐蚀。 铜合金表现出比纯铜更高的耐腐蚀性,如:黄铜(Cu Zn合金)耐冲击腐蚀性好;铜镍合金具有耐酸耐碱、耐海水的性能以及抗应力腐蚀开裂的特性;锡青铜合金可耐各种腐蚀;硅青铜合金机械强度高、耐应力腐蚀开裂性能好。 铜会发生腐蚀早已为人们所知,可以说人类一开始使用铜就发现了这一现象。虽然金属腐蚀现象极其广泛和常见,但作为一门科学对其进行研究却还是近百年的事。在现代科学中,金属腐蚀的定义是:“金属在环境介质的作用下,由于化学反应、电化学反应或物理作用而产生的破坏”[1,2]。由此定义可见,金属腐蚀的发生必须有包括金属材料和环境介质在内的相界面上的作用体系,金属发生腐蚀需要外部环境。腐蚀是对金属材料的一种破坏,这种破坏使许多金属设备的使用寿命大为缩短甚至报废,带来巨大的经济损失,它会使生产停顿、物质流失、资源耗损、产品质量降低、环境受到污染、影响新技术的发展。 二铜的腐蚀环境 铜的腐蚀按铜的使用环境可分为气相腐蚀和液相腐蚀,而液相腐蚀可按酸碱度进一步分为酸性液体、中性液体和碱性液体中的腐蚀。在过去的数十年里,人们对铜在酸性溶液中、碱性溶液中和中性盐类溶液中以及自来水供水系统中的腐蚀进行了深入广泛的研究。铜及其合金暴露在通常的中性大气环境中,在其表面
行业标准冶炼用铜废料取制样方法
《冶炼用铜废料取制样方法》 编制说明 (预审稿) 东营方圆有色金属有限公司
《冶炼用铜废料取制样方法》编制说明 1、任务由来及说明 工业和信息化部办公厅“工业和信息化部办公厅关于印发2015年第批行业标准制修订计划的通知”(工信厅科[2015]号)《冶炼用铜废料取制样方法》行业标准由东营方圆有色金属有限公司负责起草 2、标准制定的目的和意义 2.1 现状 根据我国目前废杂铜拆解企业的工艺水平和设备能力,可将原装进口和国内的废杂铜分类拆解、加工为以下种类:光亮铜、马达线、铜米、红多支铜米、锡米、油米、杂米、铜粉、1#、2#铜管、烧线、水洗铜、覆铜板、线头线尾、杂铜、洗银铜、磷青铜、喇叭铜线、铜针等。 当前国内废杂铜的分类有一个国家标准GB/T13587-2006《铜及铜合金废料》,而废杂铜的品位检验,没有具有指导性的行业标准。而废杂铜准确的品位检验是与废杂铜企业的金属平衡、经济效益密切相连的。 目前原料市场上,大多数商家采购废杂铜多以目估法来估算品位进行结算,其原理为根据废杂铜性质特征,市场认同度和工艺成熟程度目测评估,得出最终废杂铜铜品位。其优点为可以针对各类废杂铜,检验速度快,适用于大批量检验;但最主要的缺点为,对评估人员的技能要求较高,需要长期工作经验和大量的市场、工艺调查,评估结果受人为因素影响较大,由于其中多种不确定因素,严重影响到了铜品位的准确性。 2.2存在问题 目视评估法,主要存在的问题有: (1)对评估的技能要求较高,专业技能人员较少,无法应付多批次大批量的到货。 (2)评估结果人为影响因素过大,存在争议的时候只能够协商解决。 (3)相当部分原料无法通过目视评估法进行判断。 目前国内年回收废铜约60.70万吨,进口400万吨。到2015年,再生铜占当年铜产量的比例将达到40%。对废杂铜进行合理分类以及准确检验时非常重要的。 2.3目前国内外废杂铜标准的现状 当前中国国内废杂铜的检验,没有国家标准和行业标准,废杂铜的特殊性也导致取样很那具有代表性,采用常规的取样化验方法来进行废杂铜检验时不科学的。目前该废杂铜原料市场上,大多数商家采购废杂铜多以目测法来估算铜品味,其中有很多不确定因素,严重影响了铜品味的准确度,产生很多争执。 因此,将废杂铜进行合理的细化分类,制订科学的取制样方法,对规范废杂铜市场,减少争议,良性发展是必不可少的。 3、标准编写原则和编写格式 本标准是根据GB/T1.1-2009《标准化工作导则第1部分:标准的结构和编写规则》和GB/T20001.4-2001《标准编写规则第4部分:化学分析方法》的要求进行编写的。 4、标准适用范围 本标准适用的废杂铜区间为以下三类: 一类:1#铜废料,纯度在96%以上,铜边角料,铜圈、干净铜管或管道、1#铜线和粗导线(不包括被烧焦的和易碎的细铜线)等干净的非合金铜材料。 二类:2#铜废料,纯度在94%-96%之间,干净的、氧化的、带皮的铜边角料、铜圈、整流器部件、较干净的带少量焊锡的铜管材,氧化或带皮铜线(不是被烧焦的铜线)等铜废料。
常用金相腐蚀剂汇总
一些常用的金相腐蚀剂 低倍组织浸蚀剂 序号用途成份腐蚀方法附注 A101 大多数钢种1:1(容积比工业盐酸水溶液60-80℃热蚀时间: 易切削钢5-10min 碳素钢等5-20min 合金钢等15-20min 酸蚀后防锈方法: a. 中和法:用10%氨水溶液浸泡后再以热水冲洗。b. 钝化法:浸入浓硝酸5秒再用热水冲洗。c. 涂层保护法:涂清漆和塑料膜。 A102 奥氏体不锈钢.耐热钢盐酸10份硝酸1份水10份(容积比) 60-70℃热蚀时间: 5-25min A103 碳素钢合金钢高速工具钢盐酸38份硫酸12份水50份(容积比) 60-80℃热蚀时间: 15-25min A104 大多数钢种盐酸500ml 硫酸35ml 硫酸铜150g 室温浸蚀在浸蚀过程中,用毛刷不断擦拭试样表面, 去除表面沉淀物可用 A108号浸蚀剂作冲刷液 A105 大多数钢种三氯化铁200g 硝酸300ml 水100ml 室温浸蚀或擦拭1-5min A106 大多数钢种盐酸30ml 三氯化铁50g 水70ml 室温浸蚀 A107 碳素钢合金钢10%-40%硝酸水溶液(容积比室温浸蚀25%硝酸水溶液为通用浸蚀剂 a.可用于球墨铸铁的低倍组织显示。b.高浓度适用于不便作加热的钢锭截面等大试样。 A108 碳素钢合金钢显示技晶及粗晶组织10%-20%过硫酸铵水溶液室温浸蚀或擦拭 A109 碳素钢合金钢三氯化铁饱和水溶液500ml 硝酸10ml 室温浸蚀 A110 不锈钢及高铬.高镍合金钢硝酸1份盐酸3份 A111 奥氏体不锈钢硫酸铜100ml 盐酸500ml 水500ml 室温浸蚀也可以加热使用通用浸蚀剂 A112 精密合金高温合金硝酸60ml 盐酸200ml 氯化高铁50g 过硫酸铵30g 水50ml 室温浸蚀 A113 钢的技晶组织工业氯化铜铵12g 盐酸5ml 水100ml 浸蚀30-60min后对表面稍加研磨则能获得好的效果
ZL101铝合金应力腐蚀特性研究_李晨
第32卷第3期 2011年9月 力 学 季 刊 CHINESE QUART E RLY OF MECHANIC S Vol.32No.3 Sep.2011 ZL101铝合金应力腐蚀特性研究 李 晨,孟祥琦,刘 畅,许金泉 (上海交通大学船舶海洋与建筑工程学院工程力学系,上海200240) 摘要:研究了初始应力对于ZL101铝合金应力腐蚀的影响。采用自制载荷传感器确定试样加载线上的载荷从而确定其应力强度因子。通过ZL101铝合金在腐蚀溶液中的应力腐蚀实验,测定了不同应力状态下的起裂时间,分析了初始应力与起裂时间的关系。结果表明:ZL101铝合金在拉伸状态下的腐蚀裂纹扩展比较剧烈,而压缩状态下的裂纹扩展比较缓慢平稳。压缩应力状态下的起裂时间比拉伸应力状态下的要长,拉伸状态下材料对于应力腐蚀更为敏感。 收稿日期:2011-01-11 作者简介:李晨(1986-),男,上海人,硕士研究生.研究方向:金属应力腐蚀与腐蚀疲劳. 关键词:铸造铝合金;ZL101;应力腐蚀 中图分类号:O346.4 文献标识码:A 文章编号:0254-0053(2011)03-338-05 Research on Stress Corrosion Cracking of ZL101Alumin um Alloy LI Chen,MENG Xiang-qi,LIU Chang,XU Jin-quan (School of Naval Architecture,Ocean and Civil Engineering,S hanghai Jiaoto ng University,Shanghai200240,China) Abstract:The influence of initial stress on stress corrosion cracking of ZL101aluminum alloy was re-searched.The force of specimen loading line was measured by self-made loading sensors which could re-present the stress intensity factor.The stress corrosion cracking time at different stress state was tested and the relation between initial stress and cracking time was analyzed through stress corrosion cracking tests of ZL101.The results indicate that the crack growth is severe under tension stress and it is slow and gentle under pressure stress.The cracking time under pressure stress is later than which under tension stress and it is more sensitive to stress corrosion under tension stress. Key words:cast aluminum alloy;ZL101;stress corrosion ZL101铝合金具有良好的铸造性能、可热处理强化性能、流动性好、热裂倾向低等优点,成为汽车、航空领域广泛应用的Al-Si系铸造铝合金。近年来,关于铝合金成分、组织与性能之间的关系做了大量研究,以提高铝合金的力学性能[1~4],但对于ZL101铝合金抗腐蚀性能研究较少。 有研究表明,ZL101铝合金腐蚀的主要原因是共晶硅沿晶界分布,共晶硅和基体之间存在电位差,形成大阳极小阴极的腐蚀电池,基体作为阳极被腐蚀。晶界腐蚀敏感性低,但是内应力或杂质偏聚会增加晶间腐蚀敏感性,增大晶间腐蚀级别。另外,ZL101铝合金在3.5%NaCl水溶液中应力腐蚀敏感性较高,其应力腐蚀强度因子K1SC C=8.45MPa·m1/2。应力腐蚀开裂时阳极溶解和机械损伤共同作用的结果,以阳极溶解为主,其断口为穿晶脆断形貌[5,6]。 本文为了研究初始应力对ZL101铝合金应力腐蚀的影响,对不同初始应力状态下的试样进行应力腐蚀试验。在GB/T15970的基础上使用自制的螺栓传感器测量试样所受载荷。确定腐蚀溶液对ZL101铝合金破坏行为的影响,包括缺口处的起裂时间和开裂过程。试验结束后用扫描电镜观察断口形貌。 D OI:10.15959/https://www.360docs.net/doc/9d17018168.html, ki.0254-0053.2011.03.003