高炉强化冶炼
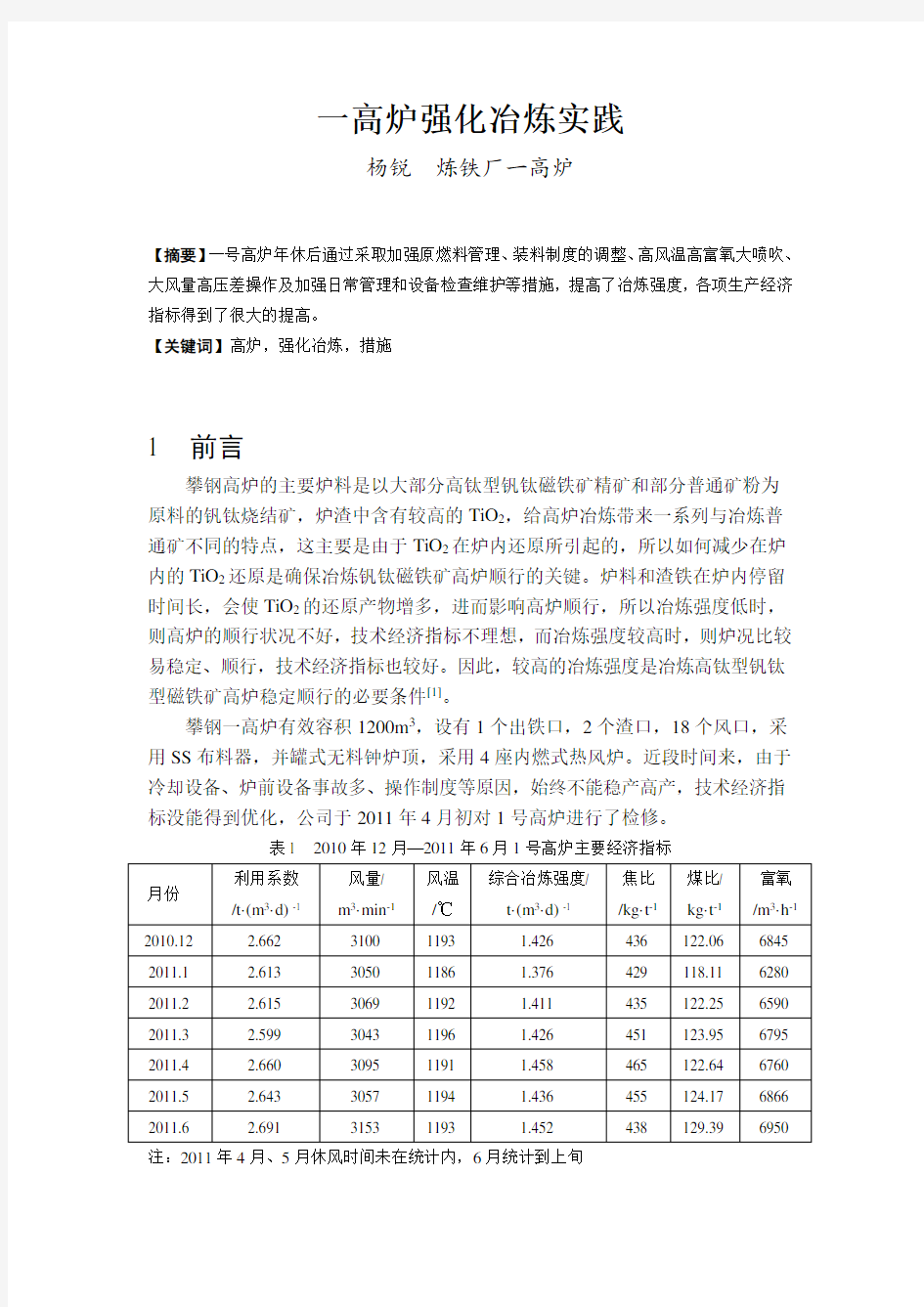
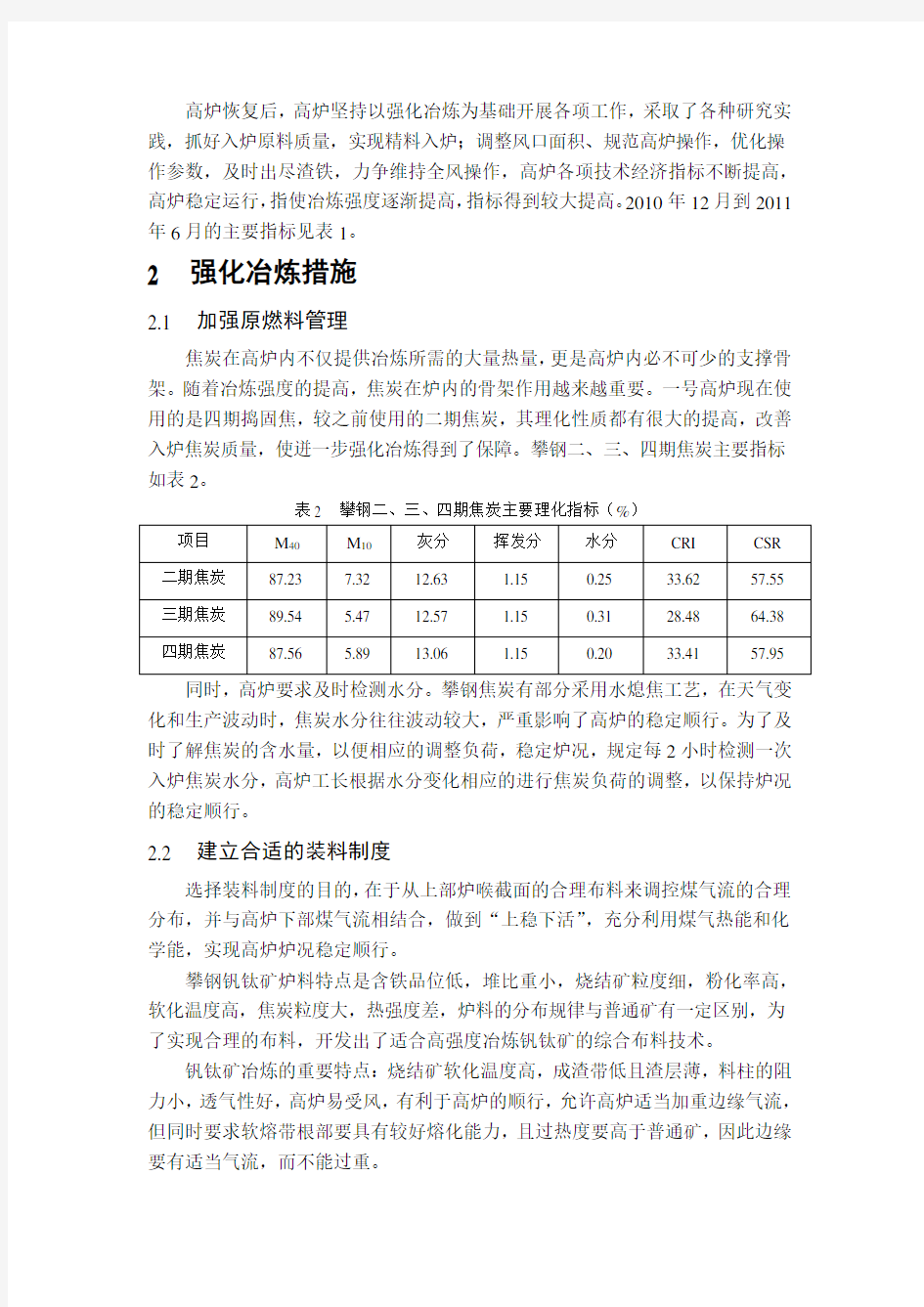
一高炉强化冶炼实践
杨锐炼铁厂一高炉
【摘要】一号高炉年休后通过采取加强原燃料管理、装料制度的调整、高风温高富氧大喷吹、大风量高压差操作及加强日常管理和设备检查维护等措施,提高了冶炼强度,各项生产经济指标得到了很大的提高。
【关键词】高炉,强化冶炼,措施
1 前言
攀钢高炉的主要炉料是以大部分高钛型钒钛磁铁矿精矿和部分普通矿粉为原料的钒钛烧结矿,炉渣中含有较高的TiO2,给高炉冶炼带来一系列与冶炼普通矿不同的特点,这主要是由于TiO2在炉内还原所引起的,所以如何减少在炉内的TiO2还原是确保冶炼钒钛磁铁矿高炉顺行的关键。炉料和渣铁在炉内停留时间长,会使TiO2的还原产物增多,进而影响高炉顺行,所以冶炼强度低时,则高炉的顺行状况不好,技术经济指标不理想,而冶炼强度较高时,则炉况比较易稳定、顺行,技术经济指标也较好。因此,较高的冶炼强度是冶炼高钛型钒钛型磁铁矿高炉稳定顺行的必要条件[1]。
攀钢一高炉有效容积1200m3,设有1个出铁口,2个渣口,18个风口,采用SS布料器,并罐式无料钟炉顶,采用4座内燃式热风炉。近段时间来,由于冷却设备、炉前设备事故多、操作制度等原因,始终不能稳产高产,技术经济指标没能得到优化,公司于2011年4月初对1号高炉进行了检修。
表1 2010年12月—2011年6月1号高炉主要经济指标
月份利用系数
/t·(m3·d) -1
风量/
m3·min-1
风温
/℃
综合冶炼强度/
t·(m3·d) -1
焦比
/kg·t-1
煤比/
kg·t-1
富氧
/m3·h-1
2010.12 2.662 3100 1193 1.426 436 122.06 6845 2011.1 2.613 3050 1186 1.376 429 118.11 6280 2011.2 2.615 3069 1192 1.411 435 122.25 6590 2011.3 2.599 3043 1196 1.426 451 123.95 6795 2011.4 2.660 3095 1191 1.458 465 122.64 6760 2011.5 2.643 3057 1194 1.436 455 124.17 6866 2011.6 2.691 3153 1193 1.452 438 129.39 6950 注:2011年4月、5月休风时间未在统计内,6月统计到上旬
高炉恢复后,高炉坚持以强化冶炼为基础开展各项工作,采取了各种研究实践,抓好入炉原料质量,实现精料入炉;调整风口面积、规范高炉操作,优化操作参数,及时出尽渣铁,力争维持全风操作,高炉各项技术经济指标不断提高,高炉稳定运行,指使冶炼强度逐渐提高,指标得到较大提高。2010年12月到2011年6月的主要指标见表1。
2 强化冶炼措施
2.1 加强原燃料管理
焦炭在高炉内不仅提供冶炼所需的大量热量,更是高炉内必不可少的支撑骨架。随着冶炼强度的提高,焦炭在炉内的骨架作用越来越重要。一号高炉现在使用的是四期捣固焦,较之前使用的二期焦炭,其理化性质都有很大的提高,改善入炉焦炭质量,使迸一步强化冶炼得到了保障。攀钢二、三、四期焦炭主要指标如表2。
表2 攀钢二、三、四期焦炭主要理化指标(%)
项目M40M10灰分挥发分水分CRI CSR 二期焦炭87.23 7.32 12.63 1.15 0.25 33.62 57.55 三期焦炭89.54 5.47 12.57 1.15 0.31 28.48 64.38 四期焦炭87.56 5.89 13.06 1.15 0.20 33.41 57.95 同时,高炉要求及时检测水分。攀钢焦炭有部分采用水熄焦工艺,在天气变化和生产波动时,焦炭水分往往波动较大,严重影响了高炉的稳定顺行。为了及时了解焦炭的含水量,以便相应的调整负荷,稳定炉况,规定每2小时检测一次入炉焦炭水分,高炉工长根据水分变化相应的进行焦炭负荷的调整,以保持炉况的稳定顺行。
2.2 建立合适的装料制度
选择装料制度的目的,在于从上部炉喉截面的合理布料来调控煤气流的合理分布,并与高炉下部煤气流相结合,做到“上稳下活”,充分利用煤气热能和化学能,实现高炉炉况稳定顺行。
攀钢钒钛矿炉料特点是含铁品位低,堆比重小,烧结矿粒度细,粉化率高,软化温度高,焦炭粒度大,热强度差,炉料的分布规律与普通矿有一定区别,为了实现合理的布料,开发出了适合高强度冶炼钒钛矿的综合布料技术。
钒钛矿冶炼的重要特点:烧结矿软化温度高,成渣带低且渣层薄,料柱的阻力小,透气性好,高炉易受风,有利于高炉的顺行,允许高炉适当加重边缘气流,但同时要求软熔带根部要具有较好熔化能力,且过热度要高于普通矿,因此边缘要有适当气流,而不能过重。
一高炉是无料钟式炉顶,采用的SS环形布料器,布料方式以多环布料和中心加焦相结合。在生产实践中,通过不断摸索,总结出了比较适合一高炉强化操作的思想,即“适当维持边缘气流,打开中心气流”,同时适当考虑中间环带的矿焦比对煤气流的阻力因素,中心焦碳适宜在30%,边缘矿石宜在50~60%,这样能保证稳定顺行[2]。如表3所示的装料制度,中心焦炭保持在30%,边缘矿石在50%。随着冶炼强度的提高,矿石批重由原来的23.3t,逐渐加到现在的24t,促进了煤气流的均匀分布,稳定了高炉上部气流,改善了煤气流利用率。
表3 一高炉布料制度
布料角度α/°36.5 35.5 34.5 28
布料圈数矿石(O)0 5 5 0 焦炭(C) 3 0 3 4
2.3 调整合适的鼓风动能,活跃炉缸
选择送风制度的目的,在于保证均匀而活跃的炉缸状态,及初始煤气流均匀合理分布,对钒钛磁铁矿冶炼的防稠与消稠有较大的影响。对冶炼钒钛磁铁矿具有重要意义。
鼓风动能是高炉下部调节的重要参数之一,鼓风动能适宜,则高炉炉缸工作状态均匀活跃,炉内初始煤气流分布合理,炉况稳定顺行。在上部调节的配合下,适宜的鼓风动能可使煤气热能、化学热能得以充分利用,对高炉节能降耗、强化冶炼以及延长使用寿命都十分有利。就冶炼高钛型钒钛磁铁矿的高炉而言,采用合适的鼓风动能以保持均匀活跃的炉缸工作状态,对于降低高钛渣的粘度,改善渣的流动性,进而降低铁损,节焦增产和强化高炉冶炼,效果尤为明显。
攀钢用钒钛烧结矿的品位低、高炉渣量大,并且钒钛烧结矿的低温还原粉化率高、软化温度高、高炉软熔带位置低、料柱透气性差,由于钛渣粘度大使得中心不易吹透。因此必须维持大风量操作,配之合适的风口面积,以保证维持较高的鼓风动能吹透中心活跃炉缸。
送风制度的主要标志,以鼓风参数-鼓风动能(风速)来表示,即在一定的冶炼条件下,欲达到一定的冶炼强度,必须选择适宜的风口数目,风口直径、风量、风温、富氧率、喷煤比等,才能获得良好的炉缸工作状态。
一号高炉风口直径和数目为Φ130×5+140×13,风口总进风面积为0.266m2,5月休风后对5号风口加圈,所以现在风口直径分布为Φ110×1+130×5+140×13,风口总进风面积为0.263m2。同时鼓风机由原来的2号换至现在的4号鼓风机,鼓风能力有所提高。风口面积缩小,风量增加,鼓风动能逐渐增加,炉缸逐渐活跃,中心气流充足,炉况顺行,下部更容易易接受风量,强化了高炉冶炼,如表4所示。
表4 2011年上半年风量和风口面积变化情况
月份
风量/
m3·min-1
风口面/
m2
风速/
m·s-1
煤比/
kg·t-1
综合冶炼强度/
t·(m3·d) -1
2011.1 3050 0.266 191 118.11 1.426
2011.2 3069 0.266 192 122.25 1.376
2011.3 3043 0.266 191 123.95 1.411
2011.4 3095 0.266 194 122.64 1.426
2011.5 3057 0.263 194 124.17 1.458
2011.6 3153 0.263 200 129.39 1.436
2.4 大风量高压操作
在正常生产过程中,风口直径确定后,为此和适合稳定的风量操作,是保持炉缸工作状况均匀活跃、煤气流合理分布的重要手段。
高压操作是强化高炉冶炼的有效措施,既能提高冶炼强度又能改善煤气利用率,降低焦比,从而提高产量。
实际生产中,一号高炉保证风量维持在3100~3200m3/min,高炉压差维持在0.150MPa~0.160MPa。实现大风量高压操作后,炉况稳定,炉顶煤气中的CO2
含量提高。风量增加提高了风速和鼓风动能,有利于活跃炉缸和打通中心气流,可以吹出较多的原、燃料带入的粉末,改善料柱的透气性,提高冶炼强度,改善高炉各项技术经济指标。
2.5 富氧大喷煤操作
富氧和喷煤是高炉冶炼钒钛磁铁矿控制炉温的最有效手段,有利于稳定炉况,强化冶炼。高炉喷吹煤粉可以活跃炉缸工作,促进高炉富氧率和风温使用水平的提高,推动高炉冶炼的强化。高炉加大喷煤后,矿焦比增加,料柱自身增重,可适当加大风量提高压差操作,炉温发生波动时,使用喷煤进行调节也灵活可行。
富氧鼓风后,由于鼓风中含氮量相对减少,冶炼单位生铁所需的风量和产生的煤气量减少;对于同体积的鼓风量来说,则可多烧碳量,生成的煤气量也增加。因此大富氧鼓风可以提高高炉冶炼强度,增加产量。富氧加速煤粉的燃烧,活跃炉缸,改善渣铁流动性,降低铁损,提高风口前理论燃烧温度,补偿因喷煤引起的炉缸气化和顶温升高的影响,减少渣中未燃煤粉,提高冶炼强度,降低焦比。一般富氧1%,可提高理论燃烧温度35~45℃,增加喷煤率4%。
在操作上,炉内实行高富氧大喷煤方针,富氧维持在最为合理的7000m3/h,除1#﹑18#铁口上方两风口外,其余16个风口全部喷煤,喷煤瞬时速率能达到20t/h,在操作调剂上,尽量避免停煤操作,减少煤量波动,规定喷煤上下限,早动少动。在设备维护上做到“勤检查,早发现”,杜绝了因为堵枪而造成的煤量
损失。
2.6 稳定的高风温操作
当前强化高炉冶炼生产,发展高风温冶炼技术是有力推动冶炼技术发展的动力,是高炉炼铁节能降耗的有效措施。高炉热平衡计算表明,热风带入的热量约占全部热量收入的15%~20%,并且基本能被全部利用。因此,高风温冶炼技术是高炉强化冶炼的需要。
根据攀钢高炉生产实践表明,每提高100℃风温,可降焦比4%左右,增加4%左右的产量[3]。一号高炉配有4座高温内燃式热风炉,实行的是“两烧两送”的送风制度,能稳定提供1200℃以上的高风温。
一号高炉一方面强化烧炉工作,加强设备管理,减少事故率,提高蓄热能力;另一方面要求工长统一操作思路,操作上坚持使用高风温,风温水平能够保证在1180℃以上(如图1所示),以提高煤粉燃烧率,保证炉缸充沛的热量。高风温的使用不但活跃了炉缸,提高了渣铁物理热,改善了渣铁流动性及炉渣脱硫能力、及时出净渣铁、保持炉况稳定顺行,而且有利于节焦降耗,改善技术经济指标。
图1 一号高炉近期风温使用情况
2.7 合理的炉缸热制度和造渣制度
热制度是指在工艺操作制度上控制高炉内热状态的方法的总称。热状态是用热量是否充沛、炉温是否稳定来衡量,即是否有足够的热量以满足冶炼过程加热炉料和各种物理化学反应,渣铁的熔化的过热到要求的温度。高炉生产操作者特别重视炉缸的热状态,因为决定高炉热量需求和燃料比的是高炉下部,所以常用说明炉缸热状态的一些参数作为热制度的指标。
充沛的炉缸热制度是高炉顺行的基础,冶炼强度高时,炉料在炉内停留时间短,因此要求对炉料加热熔化的热量传输要快,这就要求有一大的温度梯度,即提高炉缸温度。富氧大喷煤时,如果炉温低,中心易堆积,顺行不好,滑料,风压高,造成风不全或炉况失常,所以在高冶炼强度、富氧大喷煤时,炉温应控制
在中上限。攀钢冶炼钒钛矿,高炉以[Ti]含量衡量炉温的标准。在原燃料不变的情况下,尽量稳定负荷,减少炉温波动;当原燃料变差时,炉温取上限;原燃料好时以中限为主。现一高炉坚持以炉温为基础的方针,要求每次出铁铁水[Ti]量控制在[0.16,0.30],在此范围内,既可保证铁水的质量,又可减少炉渣中TiO2的还原。控制连续低炉温不超过3炉以上,严防出号外铁(生铁[S]大于0.100%)。小时料批量连续超出上限,或渣﹑铁排放量超出间批数,操作上应及时补足焦炭或临时调负荷,以补充炉缸热量充沛。
攀钢高炉入炉品位低﹑渣量大,渣中TiO2含量高。既要保证炉渣的流动性,又要保证其脱硫能力。而高炉是双渣口单铁口,这就要求上渣要好放,因此要求炉渣流动性要好,为提高炉渣流动性,就要降低其熔化性温度,适当降低碱度,但又要考虑炉渣脱硫能力,所以炉渣碱度应控制在中偏下限。一号高炉规定炉渣二元碱度R2控制在1.10~1.15。当炉缸热制度维持在较高水平时,为了炉前能按间批出净渣铁,二元碱度维持在下限;当炉温下限时,维持较高的二元碱度有利于气流的稳定。由于烧结碱度波动大,高炉球团配比波动大,导致炉渣二元碱度及渣中TiO2波动,操作人员要“勤观察,多分析,早调剂”减少炉渣碱度的大幅度波动。
2.8 重视日常管理
加强炉内炉前操作与管理高炉炼铁日常操作与管理十分重要,高炉炼铁日常的操作与管理非常重要,即使操作制度和原燃料条件再好,如果没有一套严格的操作管理制度,也很难长久取得良好的技术经济指标。一高炉加强对炉前炉内的管理,为技术经济指的创新创造了条件。
车间根据炉况的发展,及时指定适宜的操作方针,作为高炉的基本操作思想,将各种参数进行量化管理,明确各种参数的控制范围。以高炉顺行为基础,以风量为纲,严格管理高炉工长对各种操作制度的执行情况,使炉温、炉渣碱度等参数控制在适宜范围内,保证炉况长期顺行,稳产高产,强化高炉冶炼。
随着冶炼强度的提高,炉前渣铁能否及时出净成为高炉顺行的关键之一。攀钢钒钛磁铁矿的特点就是不能憋,要求炉前必须及时出尽渣铁。车间经过努力,将炉前操作进行量化,要求放好上渣,保证渣口出渣量;铁口必须打足够的泥,确保铁口深度在1.8m以上,并对每次铁的铁口深度、使用钻头的大小、打泥量、冒泥情况、出渣铁量等项目进行记录。由于高强度的冶炼对铁口泥套损坏较快,为了杜绝冒泥和炉前事故的发生,规定每班必须做新泥套。
通过一系列的制度和措施,为一号高炉的强化冶炼和增产降耗提供了有利条件。
3 结论
一号高炉强化冶炼的实践表明,通过采取相应的措施,可以提高冶炼高钛型钒钛磁铁矿的高炉的冶炼强度:
(1)加强入炉原燃料的管理,提高入炉原燃料质量,是高炉强化冶炼的基础。(2)建立合理的装料制度,是上部调剂的重要手段,稳定炉顶煤气流分布,是强化冶炼的重要条件。
(3)根据原料条件和风温的使用情况及时调整进风面积,调整适宜的鼓风动能,使炉缸工作活跃,以保证炉缸初始煤气流分布的合理性,促过强化冶炼进程。(4)采用高富氧大喷煤操作,控制合理的风口理论燃烧温度,使炉况顺行,促进了高炉强化冶炼。
(5)建立合适的炉缸热制度,根据高炉的不同条件确立不同的炉温控制范围,控制炉渣合适的碱度,提高炉渣流动性,保证每次渣铁出尽,为强化冶炼创造了有利条件。
(6)对高炉日常操作进行量化管理和经济责任制,制定科学适宜的高炉操作方针,确保高炉强化冶炼的顺利进行。
参考文献
[1]孙希文,刁日升,范云东等.攀钢二号高炉强化冶炼实践[J].高炉冶炼钒钛磁铁矿理论与实践.冶金工业出版社2000年:554~557
[2]赵东辉.攀钢一高炉强化冶炼实践[J].四川冶金,2010,32(6):55~56
[3]曹勇.攀钢3号高炉提高风温后的生产实践[J].四川冶金,2008,30(3):29~31
高炉强化冶炼详解
高炉强化冶炼技术及其进步 高炉炼铁生产的原则 高炉冶炼生产的目标是在较长的一代炉龄(例如5年或更长)内生产出尽可能多的生铁,而且消耗要低,生铁质量要好,经济效益要高,概括起来就是“优质,低耗,高产,长寿,高效益”。长期以来,我国乃至世界各国的炼铁工作者对如何处理这五者间的关系进行过,而且还在进行着讨论,讨论的焦点是如何提高产量及焦比与产量的关系。 众所周知,表明高炉冶炼产量与消耗的三个重要指标—有效容积利用系数(ηY)、冶炼强度(I)和焦比(K)之间有着如下的关系:ηY=I/K 显然,利用系数的提高,也即高炉产量的增加,存在着四种途径: (1)冶炼强度保持不变,不断地降低焦比; (2)焦比保持不变,冶炼强度逐步提高; (3)随着冶炼强度的逐步提高,焦比有所降低; (4)随着冶炼强度的提高,焦比也有所上升,但焦比上升的幅度不如冶炼强度增长的幅度大。 在高炉炼铁的发展史上,这四种途径都被应用过,应当指出在最后一种情况下,产量增长很少,而且是在牺牲昂贵的焦炭的消耗中取得的,一旦在冶炼强度提高的过程中,焦比升高的速率超过冶炼强度提高的速率,则产量不但得不到增加,反而会降低。因此,
冶炼强度对焦比的影响,成为高炉冶炼增产的关键。 在高炉冶炼的技术发展过程中,人们通过研究总结出冶炼强度与焦比的关系如图1所示。 图1 冶炼强度与产量(I)和焦比(K)的关系 a一美国资料,b一原西德资料,c一前苏联资料
在一定的冶炼条件下,存在着一个与最低焦比相对应的最适宜的冶炼强度I适。当冶炼强度低于或高于I适时,焦比将升高,而产量稍迟后,开始逐渐降低。这种规律反映了高炉内煤气和炉料两流股间的复杂传热、传质现象。在冶炼强度很低时,风量及相应产生的煤气量均小,流速低,动压头很小,造成煤气沿炉子截面分布极不均匀,表现为边缘气流过分发展,煤气与矿石不能很好地接触,结果煤气的热能和化学能不能得到充分利用,炉顶煤气中CO,含量低,温度高,而进入高温区的炉料因还原不充分,直接还原发展,消耗了大量宝贵的高温热量,因此焦比很高。随着冶炼强度的提高,风量、煤气量相应增加,煤气的速度也增大,从而改变了煤气流的流动状态,由层流转为湍流,风口前循环区的出现,大大改善了煤气流分布和煤气与炉料之间的接触,煤气流的热能和化学能利用改善,间接还原的发展减少了下部高温区热量的消耗,从而焦比明显下降,直到与最适宜冶炼强度儿相对应的最低焦比值。之后冶炼强度继续提高,煤气量的增加进一步提高了煤气流速,这将带来叠加性的煤气流分布,导致中心过吹或管道行程,在煤气流速过大时,它的压头损失可变得与炉料的有效质量相等或超过有效质量,炉料就停止下降而出现悬料。所有这些将引起还原过程恶化,炉顶煤气温度升高,炉况恶化,最终表现为焦比升高。 高炉炼铁工作者应该掌握这种客观规律,并应用它来指导生产,即针对具体生产条件,确定与最低焦比相适应的冶炼强度,使高炉顺行,稳定地高产。然而高炉的冶炼条件是可以改变的,随着技术的进步,例如加强原料准备,采取合理的炉料结构,提高炉顶
高炉炼铁工艺流程(经典)61411
本文是我根据我的上传的上一个文库资料继续修改的,以前那个因自己也没有吃透,没有条理性,现在这个是我在基本掌握高炉冶炼的知识之后再次整理的,比上次更具有系统性。同时也增加了一些图片,增加大家的感性认识。希望本文对你有所帮助。 本次将高炉炼铁工艺流程分为以下几部分: 一、高炉炼铁工艺流程详解 二、高炉炼铁原理 三、高炉冶炼主要工艺设备简介 四、高炉炼铁用的原料 附:高炉炉本体主要组成部分介绍以及高炉操作知识 工艺设备相见文库文档:
一、高炉炼铁工艺流程详解 高炉炼铁工艺流程详图如下图所示:
二、高炉炼铁原理 炼铁过程实质上是将铁从其自然形态——矿石等含铁化合物中还原出来的过程。 炼铁方法主要有高炉法、 直接还原法、熔融还原法等,其 原理是矿石在特定的气氛中(还 原物质CO、H2、C;适宜温度 等)通过物化反应获取还原后的 生铁。生铁除了少部分用于铸造 外,绝大部分是作为炼钢原料。 高炉炼铁是现代炼铁的主 要方法,钢铁生产中的重要环节。 这种方法是由古代竖炉炼铁发展、改进而成的。尽管世界各国研究发展了很多新的炼铁法,但由于高炉炼铁技术经济指标良好,工艺简单,生产量大,劳动生产率高,能耗低,这种方法生产的铁仍占世界铁总产量的95%以上。 炼铁工艺是是将含铁原料(烧结矿、球团矿或铁矿)、燃料(焦炭、煤粉等)及其它辅助原料(石灰石、白云石、锰矿等)按一定比例自高炉炉顶装入高炉,并由热风炉在高炉下部沿炉周的风口向高炉内鼓入热风助焦炭燃烧(有的高炉也喷吹煤粉、重油、天然气等辅助燃料),在高温下焦炭中的碳同鼓入空气中的氧燃烧生成的一氧
化碳和氢气。原料、燃料随着炉内熔炼等过程的进行而下降,在炉料下降和上升的煤气相遇,先后发生传热、还原、熔化、脱炭作用而生成生铁,铁矿石原料中的杂质与加入炉内的熔剂相结合而成渣,炉底铁水间断地放出装入铁水罐,送往炼钢厂。同时产生高炉煤气,炉渣两种副产品,高炉渣铁主要矿石中不还原的杂质和石灰石等熔剂结合生成,自渣口排出后,经水淬处理后全部作为水泥生产原料;产生的煤气从炉顶导出,经除尘后,作为热风炉、加热炉、焦炉、锅炉等的燃料。炼铁工艺流程和主要排污节点见上图。
高炉炼铁工艺流程(经典)教学教材
高炉炼铁工艺流程(经 典)
本文是我根据我的上传的上一个文库资料继续修改的,以前那个因自己也没有吃透,没有条理性,现在这个是我在基本掌握高炉冶炼的知识之后再次整理的,比上次更具有系统性。同时也增加了一些图片,增加大家的感性认识。希望本文对你有所帮助。 本次将高炉炼铁工艺流程分为以下几部分: 一、高炉炼铁工艺流程详解 二、高炉炼铁原理 三、高炉冶炼主要工艺设备简介 四、高炉炼铁用的原料 附:高炉炉本体主要组成部分介绍以及高炉操作知识 工艺设备相见文库文档:
一、高炉炼铁工艺流程详解 高炉炼铁工艺流程详图如下图所示:
二、高炉炼铁原理 炼铁过程实质上是将铁从其自然形态——矿石等含铁化合物中还原出来的过程。 炼铁方法主要有高炉法、直接 还原法、熔融还原法等,其原理 是矿石在特定的气氛中(还原物 质CO、H2、C;适宜温度等) 通过物化反应获取还原后的生 铁。生铁除了少部分用于铸造 外,绝大部分是作为炼钢原料。 高炉炼铁是现代炼铁的主要方 法,钢铁生产中的重要环节。这 种方法是由古代竖炉炼铁发展、改进而成的。尽管世界各国研究发展了很多新的炼铁法,但由于高炉炼铁技术经济指标良好,工艺简单,生产量大,劳动生产率高,能耗低,这种方法生产的铁仍占世界铁总产量的95%以上。 炼铁工艺是是将含铁原料(烧结矿、球团矿或铁矿)、燃料(焦炭、煤粉等)及其它辅助原料(石灰石、白云石、锰矿等)按一定比例自高炉炉顶装入高炉,并由热风炉在高炉下部沿炉周的风口向高炉内鼓入热风助焦炭燃烧(有的高炉也喷吹煤粉、重油、天然气等辅助燃料),在高温下焦炭中的碳同鼓入空气中的氧燃烧生成的一氧化碳和氢气。原料、燃料随着炉内熔炼等过程的进行而下降,
高炉炼铁炼钢工艺
本次将高炉炼铁工艺流程分为以下几部分: 一、高炉炼铁工艺流程详解 二、高炉炼铁原理 三、高炉冶炼主要工艺设备简介 四、高炉炼铁用的原料 附:高炉炉本体主要组成部分介绍以及高炉操作知识 工艺设备相见文库文档: 一、高炉炼铁工艺流程详解 高炉炼铁工艺流程详图如下图所示:
二、高炉炼铁原理 炼铁过程实质上是将铁从其自然形态——矿石等含铁化合物中 还原出来的过程。 炼铁方法主要有高炉法、直 接还原法、熔融还原法等,其原 理是矿石在特定的气氛中(还原 物质CO、H2、C;适宜温度等) 通过物化反应获取还原后的生 铁。生铁除了少部分用于铸造外, 绝大部分是作为炼钢原料。 高炉炼铁是现代炼铁的主要
方法,钢铁生产中的重要环节。这种方法是由古代竖炉炼铁发展、改进而成的。尽管世界各国研究发展了很多新的炼铁法,但由于高炉炼铁技术经济指标良好,工艺简单,生产量大,劳动生产率高,能耗低,这种方法生产的铁仍占世界铁总产量的95%以上。 炼铁工艺是是将含铁原料(烧结矿、球团矿或铁矿)、燃料(焦炭、煤粉等)及其它辅助原料(石灰石、白云石、锰矿等)按一定比例自高炉炉顶装入高炉,并由热风炉在高炉下部沿炉周的风口向高炉内鼓入热风助焦炭燃烧(有的高炉也喷吹煤粉、重油、天然气等辅助燃料),在高温下焦炭中的碳同鼓入空气中的氧燃烧生成的一氧化碳和氢气。原料、燃料随着炉内熔炼等过程的进行而下降,在炉料下降和上升的煤气相遇,先后发生传热、还原、熔化、脱炭作用而生成生铁,铁矿石原料中的杂质与加入炉内的熔剂相结合而成渣,炉底铁水间断地放出装入铁水罐,送往炼钢厂。同时产生高炉煤气,炉渣两种副产品,高炉渣铁主要矿石中不还原的杂质和石灰石等熔剂结合生成,自渣口排出后,经水淬处理后全部作为水泥生产原料;产生的煤气从炉顶导出,经除尘后,作为热风炉、加热炉、焦炉、锅炉等的燃料。炼铁工艺流程和主要排污节点见上图。
钢铁的冶炼原理及生产工艺流程
钢铁的冶炼原理及生产工艺流程 炼铁过程实质上是将铁从其自然形态——矿石等含铁化合物中还原出来的过程。 炼铁方法主要有高炉法、直接还原法、熔融还原法等,其原理是矿石在特定的气氛中(还原物质CO、H2、C;适宜温度等)通过物化反应获取还原后的生铁。生铁除了少部分用于铸造外,绝大部分是作为炼钢原料。 1、高炉炼铁的冶炼原理(应用最多的) 一)炼铁的原理(怎样从铁矿石中炼出铁)用还原剂将铁矿石中的铁氧化物还原成金属铁。铁氧化物(Fe2O3、Fe3O4、FeO)+还原剂(C、CO、H2)铁(Fe) 二)炼铁的方法 (1)直接还原法(非高炉炼铁法) (2)高炉炼铁法(主要方法) 三)高炉炼铁的原料及其作用 (1)铁矿石:(烧结矿、球团矿)提供铁元素。 冶炼一吨铁大约需要1.5—2吨矿石。 (2)焦碳: 冶炼一吨铁大约需要500Kg焦炭。 提供热量;提供还原剂;作料柱的骨架。 (3)熔剂:(石灰石、白云石、萤石)
使炉渣熔化为液体;去除有害元素硫(S)。 (4)空气:为焦碳燃烧提供氧。 2、工艺流程 生铁的冶炼虽原理相同,但由于方法不同、冶炼设备不同,所以工艺流程也不同。下面分别简单予以介绍。 高炉生产是连续进行的。一代高炉(从开炉到大修停炉为一代)能连续生产几年到十几年。生产时,从炉顶(一般炉顶是由料种与料斗组成,现代化高炉是钟阀炉顶和无料钟炉顶)不断地装入铁矿石、焦炭、熔剂,从高炉下部的风口吹进热风(1000~1300摄氏度),喷入油、煤或天然气等燃料。装入高炉中的铁矿石,主要是铁和氧的化合物。在高温下,焦炭中和喷吹物中的碳及碳燃烧生成的一氧化碳将铁矿石中的氧夺取出来,得到铁,这个过程叫做还原。铁矿石通过还原反应炼出生铁,铁水从出铁口放出。铁矿石中的脉石、焦炭及喷吹物中的灰分与加入炉内的石灰石等熔剂结合生成炉渣,从出铁口和出渣口分别排出。煤气从炉顶导出,经除尘后,作为工业用煤气。现代化高炉还可以利用炉顶的高压,用导出的部分煤气发电。 生铁是高炉产品(指高炉冶炼生铁),而高炉的产品不只是生铁,还有锰铁等,属于铁合金产品。锰铁高炉不参加炼铁高炉各种指标的计算。高炉炼铁过程中还产生副产品水渣、矿渣棉和高炉煤气等。 高炉炼铁的特点:规模大,不论是世界其它国家还是中国,高炉的容积在不断扩大,如我国宝钢高炉是4063立方米,日产生铁超过10000吨,炉渣4000多吨,日耗焦4000多吨。
柳钢新1号高炉强化冶炼操作经验
炉温的波动。 定期开展技术和工作经验交流,不断提高工长的综合素质,培养高炉工长的预见性,把要出现的问题解决在萌芽中;能够做到早动、少动、尽量保持生产的稳定性。杜绝一个班高产,而另一个班低产的 现象,保持每个班班产在1550~1650t。 3.2加强炉前管理 由于受150t转炉生产配套装罐制度的限制,新1号高炉经常有渣、铁出不净现象,造成高炉憋风,透气性变差,风压升高。渣、铁能否及时排出是影响高炉强化冶炼的一个重要环节。要保证渣、铁的及时排出,丁长做好对外联系,及时掌握好开口罐的情况,控制好开铁口时间和出铁时问。车间制定了对炉前工操作技能的培训及考核制度,确保了铁口泥套完整性,铁口深度在2.6—2.8m。高炉设计了2个铁口,在修主沟时存在单面出铁情况,为保证炉内不憋压,35min必须打开另一铁口。 3.3炉前液压炮改造 (1)KT)400泥炮炮帽的技术改造。将原有的套筒式连接改为旋扣式,将炮帽分成前端和后端两部分。后端焊在炮嘴合适的位置上(如图2),前端旋扣住后端完成快速装配;减少炮帽与炮嘴的配合面 图2柳钢新l号高炉KIⅫ00泥炮炮帽 积,重量和体积均减少了50%;简化更换上序,更换时1~3min即可完成;极大提高二次堵门的安伞性,降低r堵不上U的风险,减轻炉前上的劳动强度。 (2)液压设备油管喷淋装置系统。由于设计原因,液压炮与主铁钩距离太近,开炉初期在H{铁过程中容易将油管烤爆,造成堵不上口,炉内必须采取放风措施。油管喷淋装置系统,将高压水雾化,对油管进行时时喷水降温,防止了油管的爆裂,提高了油管的使用寿命,杜绝了由于油管爆裂而堵不上口的现象。 4强化冶炼的效果 新l号高炉开炉以来由于受到原燃料的影响,采取“稳”和“守攻兼备”的方针,通过不断摸索逐步对高炉进行强化冶炼操作,使高炉的技术经济指标不断更新(见表2)。 表2柳钢新l号高炉技术经济指标 .,。.甲均日产利用系数入炉焦比煤比人炉t几l位炉顶压力平均风温休风率 。…。 tL/(m3?d)k∥tk∥t%kPa℃%5月9日一5月30F130121.5245881256.0514l1()043.4l 6月42272.1204507855.93176113l2.03 7月40232.0204309355.9417611222.93 8月38701.9804459755.8718211583.65 9月444l2.23040512255.818911782.3lO月44002.2lO35915156.0221011832.9l11月46002.30034314555.80199118l2.68 5结语 (1)在现有的原、燃料条件下,加强筛分系统的管理和改造。 (2)在大喷煤时,确保风温和富氧量与喷煤量相适宜。煤比达到150kg/t时富氧量不小于4000m。/h,风温不低于1180℃。 (3)采用上下部调解相适应,保持炉缸的活跃。选用边缘和中心两道气流装料制度,在焦炭发生变化时及时压住中心,保持一道气流。 (4)加强管理制度,培养工长对大高炉操作的认识,增强工长操作的预见性。加强炉前设备的改造,提高炉前T的操作技能。 5参考文献 [1]王维兴.谈高炉炼铁牛产的条件[c].中国钢铁技术论坛,2006.1:18—20. [2]千维必.我国大高炉炼铁技术发展[N].中国金属导报,2008.39(10). [3]项钟庸.用高炉炉腹煤气量指数来衡量高炉强化程度.炼铁[J],2007,26(2):2—4. 联系人:闭市钢 (545002)广西柳州I仃柳州钢铁股份有限公司炼铁厂 收稿日期:2008一12一lO ?47?
高炉冶炼工艺
第四章高炉冶炼工艺 课时:2学时 授课内容: 第三节热风炉操作 目的要求: 1.了解热风炉燃料; 2.知道影响热风的因素; 3.掌握热风炉的操作特点、燃烧制度; 4.掌握送风制度和换炉操作。 重、难点: 1.影响热风的因素、热风炉的燃烧制度、送风制度和换炉操作。 教学方法: 利用多媒体以课堂讲授为主,结合实际范例进行课堂讨论。 讲授重点内容提要 第三节热风炉操作 一.热风炉燃料 1.燃料品种及其化学成分、发热量 热风炉的燃料为煤气。 表4—15分别列出几种热风炉常用煤气的成分和发热值。 表4—15 热风炉常用煤气成分及发热值 2.煤气及助燃空气的质量 含尘量:煤气含尘量低于10mg/m3。助燃空气含尘量尽量减少。 煤气含水量:在热风炉附近的净煤气管道上设置脱水器或,使用干法除尘。 净煤气压力:净煤气支管处的煤气应有一定的压力,见表4—16。 表4—16 热风炉净煤气吉管处的煤气压力 3.气体燃料可燃成分的热效应 气体燃料可燃成分的热效应(见表4—17) 表4—17 1 m3气体燃料中各可燃成分l%体积的热效应 二.影响热风温度的因素 1.拱顶温度 ◆限制拱顶温度的因素:
①耐火材料理化性能。实际拱顶温度控制在比拱顶耐火砖平均荷重软化点低l00℃左右(也有按拱顶耐火材料最低荷重软化温度低40~50℃控制)。 ②煤气含尘量。不同含尘量允许的拱顶温度不同(见表4—18)。 表4—18 不同含尘量允许的拱顶温度 ③燃烧产物中腐蚀性介质。为避免发生拱顶钢板的晶间应力腐蚀,必须将拱顶温度控制在不超过l400℃或采取防止晶间应力腐蚀的措施。 ◆热风炉实际拱顶温度低于理论燃烧温度70~90℃。 ◆大、中型高炉热风炉拱顶温度比平均风温高120~220℃。小型高炉拱顶温度比平均风温高l50~300℃。 2.废气温度 允许的废气温度范围:大型高炉废气温度不超过350~400℃,小型高炉不得超过400~450℃。 废气温度与热风温度的关系:提高废气温度可以增加热风温度。在废气温度为200~400℃范围内,每提高废气温度100℃约可提高风温40℃。 影响废气温度的因素:单位时间燃烧煤气量、燃烧时间、蓄热面积。 3.热风炉工作周期 热风炉一个工作周期:燃烧、送风、换炉三个过程自始至终所需的时间。 送风时间与热风温度的关系:随着送风时间的延长,风温逐渐降低。 合适的工作周期:合适的送风时间最终取决于保证热风炉获得足够的温度水平(表现为拱顶温度)和蓄热量(表现为废气温度)所必要的燃烧时间。 4.蓄热面积与格子砖重量 当格子砖重量相同并采用相同工作制度时,蓄热面积大的供热能力大。 格子砖重量大,周期风温降小,利于保持较高风温。 单位风量的格子砖重量增大时,热风炉送风期拱顶温度降减少,即能提高风温水平。 单位风量的格子砖重量相同时,蓄热面积大的拱顶温度降小。 5.其他因素 ◆燃烧器形式和能力 陶瓷燃烧器的煤气和空气、混合较好,燃烧能力大,完全可以满足要求。 ◆煤气量(煤气压力) 煤气量不足或煤气压力波动,拱顶温度不能迅速稳定地升高,热风炉蓄热量减少。 ◆高炉操作 高炉顺行、热风炉工作稳定,能最大限度地保持较高风温水平。 三.热风炉的操作 1.蓄热式热风炉的传热特点 热风炉内的传热主要是指蓄热室格子砖的热交换。 高炉热风温度的高低,取决于蓄热室贮藏的热量及拱顶温度。 2.热风炉的操作特点 ◆热风炉操作是在高温、高压、煤气的环境中进行。 ◆热风炉的工艺流程: ①送风通路:热风炉除冷风阀、热风阀保持开启状态外,其他阀门一律关闭; ②燃烧通路:热风炉冷风阀和热风阀关闭外,其他阀门全部打开; ③休风:所有热风炉的全部阀门都关闭。 ◆蓄热式热风炉要储备足够的热量。 ◆热风炉各阀门的开启和关闭必须在均压下进行。 ◆高炉热风炉燃烧可以使用低热值煤气,提供较高的风温。
高炉强化冶炼
一高炉强化冶炼实践 杨锐炼铁厂一高炉 【摘要】一号高炉年休后通过采取加强原燃料管理、装料制度的调整、高风温高富氧大喷吹、大风量高压差操作及加强日常管理和设备检查维护等措施,提高了冶炼强度,各项生产经济指标得到了很大的提高。 【关键词】高炉,强化冶炼,措施 1 前言 攀钢高炉的主要炉料是以大部分高钛型钒钛磁铁矿精矿和部分普通矿粉为原料的钒钛烧结矿,炉渣中含有较高的TiO2,给高炉冶炼带来一系列与冶炼普通矿不同的特点,这主要是由于TiO2在炉内还原所引起的,所以如何减少在炉内的TiO2还原是确保冶炼钒钛磁铁矿高炉顺行的关键。炉料和渣铁在炉内停留时间长,会使TiO2的还原产物增多,进而影响高炉顺行,所以冶炼强度低时,则高炉的顺行状况不好,技术经济指标不理想,而冶炼强度较高时,则炉况比较易稳定、顺行,技术经济指标也较好。因此,较高的冶炼强度是冶炼高钛型钒钛型磁铁矿高炉稳定顺行的必要条件[1]。 攀钢一高炉有效容积1200m3,设有1个出铁口,2个渣口,18个风口,采用SS布料器,并罐式无料钟炉顶,采用4座内燃式热风炉。近段时间来,由于冷却设备、炉前设备事故多、操作制度等原因,始终不能稳产高产,技术经济指标没能得到优化,公司于2011年4月初对1号高炉进行了检修。 表1 2010年12月—2011年6月1号高炉主要经济指标 月份利用系数 /t·(m3·d) -1 风量/ m3·min-1 风温 /℃ 综合冶炼强度/ t·(m3·d) -1 焦比 /kg·t-1 煤比/ kg·t-1 富氧 /m3·h-1 2010.12 2.662 3100 1193 1.426 436 122.06 6845 2011.1 2.613 3050 1186 1.376 429 118.11 6280 2011.2 2.615 3069 1192 1.411 435 122.25 6590 2011.3 2.599 3043 1196 1.426 451 123.95 6795 2011.4 2.660 3095 1191 1.458 465 122.64 6760 2011.5 2.643 3057 1194 1.436 455 124.17 6866 2011.6 2.691 3153 1193 1.452 438 129.39 6950 注:2011年4月、5月休风时间未在统计内,6月统计到上旬
高炉炼铁生产工艺流程简介
高炉炼铁生产工艺流程简介 [导读]:高炉炼铁生产是冶金(钢铁)工业最主要的环节。高炉冶炼是把铁矿石还原成生铁的连续生产过程。铁矿石、焦炭和熔剂等固体原料按规定配料比由炉顶装料装置分批送入高炉,并使炉喉料面保持一定的高度。焦炭和矿石在炉内形成交替分层结构。矿石料在下降过程中逐步被还原、熔化成铁和渣,聚集在炉缸中,定期从铁口、渣口放出。高炉生产是连续进行的。一代高炉(从开炉到大修停炉为一代)能连续生产几年到十几年。本专题将详细介绍高炉炼铁生产的工艺流程,主要工艺设备的工作原理以及控制要求等信息。由于时间的仓促和编辑水平有限,专题中难免出现遗漏或错误的地方,欢迎大家补充指正。 高炉冶炼目的:将矿石中的铁元素提取出来,生产出来的主要产品为铁水。付产品有:水渣、矿渣棉和高炉煤气等。 高炉冶炼原理简介: 高炉生产是连续进行的。一代高炉(从开炉到大修停炉为一代)能连续生产几年到十几年。生产时,从炉顶(一般炉顶是由料种与料斗组成,现代化高炉是钟阀炉顶和无料钟炉顶)不断地装入铁矿石、焦炭、熔剂,从高炉下部的风口吹进热风(1000~1300摄氏度),喷入油、煤或天然气等燃料。装入高炉中的铁矿石,主要是铁和氧的化合物。在高温下,焦炭中和喷吹物中的碳及碳燃烧生成的一氧化碳将铁矿石中的氧夺取出来,得到铁,这个过程叫做还原。铁矿石通过还原反应炼出生铁,铁水从出铁口放出。铁矿石中的脉石、焦炭及喷吹物中的灰分与加入炉内的石灰石等熔剂结合生成炉渣,从出铁口和出渣口分别排出。煤气从炉顶导出,经除尘后,作为工业用煤气。现代化高炉还可以利用炉顶的高压,用导出的部分煤气发电。 高炉冶炼工艺流程简图: [高炉工艺]高炉冶炼过程: 高炉冶炼是把铁矿石还原成生铁的连续生产过程。铁矿石、焦炭和熔剂等固体原料按规定配料比由炉顶装料装置分批送入高炉,并使炉喉料面保持一定的高度。焦炭和矿石在炉内形成交替分层结构。矿石料在下降过程中逐步被还原、熔化成铁和渣,聚集在炉缸中, 定期从铁口、渣口放出。 高炉冶炼工艺--炉前操作
高炉冶炼目的
高炉炼铁生产是冶金(钢铁)工业最主要的环节。高炉冶炼是把铁矿石还原成生铁的连续生产过程。铁矿石、焦炭和熔剂等固体原料按规定配料比由炉顶装料装置分批送入高炉,并使炉喉料面保持一定的高度。焦炭和矿石在炉内形成交替分层结构。矿石料在下降过程中逐步被还原、熔化成铁和渣,聚集在炉缸中,定期从铁口、渣口放出。高炉生产是连续进行的。一代高炉(从开炉到大修停炉为一代)能连续生产几年到十几年。本专题将详细介绍高炉炼铁生产的工艺流程,主要工艺设备的工作原理以及控制要求等信息。由于时间的仓促和编辑水平有限,专题中难免出现遗漏或错误的地方,欢迎大家补充指正。 高炉冶炼目的:将矿石中的铁元素提取出来,生产出来的主要产品为铁水。付产品有:水渣、矿渣棉和高炉煤气等。 高炉冶炼原理简介: 高炉生产是连续进行的。一代高炉(从开炉到大修停炉为一代)能连续生产几年到十几年。生产时,从炉顶(一般炉顶是由料种与料斗组成,现代化高炉是钟阀炉顶和无料钟炉顶)不断地装入铁矿石、焦炭、熔剂,从高炉下部的风口吹进热风(1000~1300摄氏度),喷入油、煤或天然气等燃料。装入高炉中的铁矿石,主要是铁和氧的化合物。在高温下,焦炭中和喷吹物中的碳及碳燃烧生成的一氧化碳将铁矿石中的氧夺取出来,得到铁,这个过程叫做还原。铁矿石通过还原反应炼出生铁,铁水从出铁口放出。铁矿石中的脉石、焦炭及喷吹物中的灰分与加入炉内的石灰石等熔剂结合生成炉渣,从出铁口和出渣口分别排出。煤气从炉顶导出,经除尘后,作为工业用煤气。现代化高炉还可以利用炉顶的高压,用导出的部分煤气发电。 高炉冶炼工艺流程简图: [高炉工艺]高炉冶炼过程: 高炉冶炼是把铁矿石还原成生铁的连续生产过程。铁矿石、焦炭和熔剂等固体原料按规定配料比由炉顶装料装置分批送入高炉,并使炉喉料面保持一定的高度。焦炭和矿石在炉内形成交替分层结构。矿石料在下降过程中逐步被还原、熔化成铁和渣,聚集在炉缸中,定期从铁口、渣口放出。 高炉冶炼工艺--炉前操作: 一、炉前操作的任务 1、利用开口机、泥炮、堵渣机等专用设备和各种工具,按规定的时间分别打开渣、铁口,放出渣、铁,并经渣铁沟分别流人渣、铁罐内,渣铁出完后封堵渣、铁口,以保证高炉生产的连续进行。
高炉强化冶炼论文:钢铁企业中的高炉强化冶炼探讨
高炉强化冶炼论文:钢铁企业中的高炉强化冶炼探讨 摘要高炉强化冶炼是近年炼铁生产发展的主要任务,高炉要获得“优质、高产、低耗、长寿”,必须强化冶炼。本文从高炉强化冶炼的意义入手,指出我国高炉强化冶炼的几项主要措施。 关键词高炉强化冶炼;意义;措施 高炉强化冶炼,是指使高炉生产达到高产、优质、低耗的一系列技术措施,主要是通过采用精料、大风量、高风温、高顶压、低硅冶炼、提高喷煤比和富氧率及强化高炉操作管理等手段。炉强化冶炼是决定炼铁生产系统及高炉操作状态的重要指标,是一项重大的节能增产技术,既可降低高炉燃料比,又可提高利用系数,也可减少炼钢熔剂消耗,缩短炼钢冶炼时间,降低工序能耗,是炼铁生产技术现代化的一项重要内容。随着高炉冶炼技术的不断革新进步,能源和资源的日益紧张和短缺,高炉强化冶炼技术越来越受到倍加重视。 1高炉强化冶炼的意义 高炉强化冶炼是实现高炉增产、节能,是高炉各项冶炼技术综合合理利用,是增铁降耗的重要途径,是高炉冶炼发展的趋势。对炼钢来说,优质的炼钢铁水可实现无渣或少渣冶炼,缩短炼钢冶炼时间,也可减少炼钢熔剂消耗,降低能耗和费用。强化冶炼是提高高炉利用系数、提高产量、减少
燃料消耗、降低生铁成本、降低工序能耗的重要因素。同时,也是改善生铁质量的重要途径。高炉强化冶炼技术的应用,利用系数的提高、焦比和生铁含硅量的降低是炼铁生产水平的一大进步,是炼铁操作技术的一个新水平,成为近年来引人注目的一项技术。 铁水是氧气顶吹转炉的主要金属料,占装入量的 70 %-100 %,铁水的化学热与物理热是氧气顶吹转炉炼钢的主要热源。铁水含硅量直接关系到转炉炼钢的经济技术指标,是铁钢系统平衡的关键。随着炼钢技术的飞速发展和新技术的应用,炼钢生产的节奏越来越快,在原燃料供应和资源日趋紧张的条件下,铁前系统明显能力不足,为了进一步满足后续生产的需求,增产节焦,节能降耗,高炉强化冶炼是必然的发展趋势。 2我国高炉强化冶炼的主要措施 最近10年来,国内外高炉强化冶炼技术有了新一的进展和突破。 为了提高高炉各项生产技术经济指标,降低生铁含硅量,降低焦比,提高生铁产量,强化冶炼的主要措施可归纳为以下几个方面。 2.1高炉精料 精料是高炉强化的物质基础;强化高炉冶炼必须把精料放在首位。随着高炉大型化和自动化以及强化和节能日益提
450m3高炉强化冶炼实践
450m3高炉强化冶炼实践 张伟王忠晓 ( 西宁特钢股份公司) 摘要:西钢高炉经过改变原燃料状况,采取富氧鼓风、喷吹煤粉、高风温、高顶压、多环布料等强化措施,各项技术经济指标不断进步,取得了十分明显的冶炼效果。 关键词:高炉强化冶炼多环布料高风温富氧喷煤 1、前言 2#高炉于2005年9月11日点火投产。投产后设备故障频发,休风率较高,很长一段时间各项指标难以达标。经过2006年、2007年的多次检修(更换部分设备、热风炉换球),尤其是2009年不断采取强化冶炼措施后,利用系数逐月更新。10月高炉日产量突破1800t。其中6日产量为1817.085t,利用系数达到了4.04 t/ (m3.d),实现了炉况长期稳定顺行。 2、存在问题 高炉强化冶炼的主要途径是提高冶炼强度和降低燃料比。而强化生产的主要措施是在精料的基础上采取高风温、高压、富氧鼓风、脱湿鼓风、喷吹燃料等技术。我厂由于存在原燃料成分不稳定、入炉原料品位低、基础设施薄弱等因素,严重影响着高炉顺行和强化。 3、强化冶炼的措施方案 高炉冶炼过程受许多主客观因素影响,炉况总是有波动的。高炉操作者必须善于掌握各种波动因素,进行综合判断和分析,随时掌握炉温发展趋势,抓住炉况失常萌芽,及时果断地运用各种行之有效的调节方法,才能保持炉况持续稳定运行。冶金参数对焦比的影响见表1 3.1实施精料方针 精料不仅有利于提高冶炼强度,而且有利于降低焦比、提高煤比,是高炉提高利用系数的基础。努力改善原燃料条件,达到精料要求水平是各钢铁企业的追求目标。2009年以来,公司采取措施使原燃料质量得到大幅度提升,并提高了综合入炉品位,给高炉强化冶炼创造了条件。高炉炼铁对精料的要求见表2、表3
高炉炼铁基本理论知识1
高炉炼铁基本理论知识(判断题) 1.由动力学角度分析,标准生成自由能越大的氧化物越稳定,在氧势图上曲线位置越低。( ) 答案:× 2.当温度高于810℃时,CO+H 2O=CO 2 +H 2 向右进行,只有此温度区域H 2 的利用率高于CO的 利用率。 ( ) 答案:× 3.高炉内直接还原反应是借助碳素溶解损失反应与间接还原反应叠加而实现的。 ( ) 答案:√ 4.高炉内锰的各级氧化物的还原都要比铁的级氧化物的还原困难,特别是MnO比FeO更难还原。 ( ) 答案:× 5.煤气流经固体散料层时,单位高度上的压降与煤气流速平方成正比,这在炉内形成了强化和顺行的矛盾。 ( ) 答案:× 6.高炉操作线图中,0<X<1的区间,用来描述还原性气体的利用。 ( ) 答案:× 7.采用高风温操作后,中温区扩大,间接还原发展,是导致焦比降低的根本原因。 ( ) 答案:× 8.炉内煤气的水当量变化不大,炉料的水当量变化很大,随温度的升高而逐渐加大。( ) 答案:× 9.据炉内动力学分析,当煤气流的压降梯度升高至与炉料的堆积密度相等时,悬料故障。( ) 答案:√ 10.高炉内间接还原的发展,主要取决于还原的动力学条件:矿石的空隙度、还原性和煤气流的合理分布等。 ( ) 答案:√ 11.直接还原和熔融还原炼铁工艺的特点是:用块煤或气体还原剂代替高炉炼铁工艺所必需的焦炭来还原天然块矿(烧结矿或球团矿),具有相当大的适应性,特别适用于某些资源匮乏、环保要求特别严格的地区和国家。 ( ) 答案:√
12.水煤气置换反应(CO+H2O=CO2+H2)的存在,使H2有促进CO还原的作用,相当于是CO 还原反应的催化剂。 ( ) 答案:× 13.实际的直接还原反应无需借助碳素溶损反应(C+CO2=2CO),只须借助于水煤气置换反应与间接还原反应即可实现。 ( ) 答案:× 14.根据Si在高炉的还原行为,选用有利于高温区下移的技术措施和操作制度,使炉缸有稳定的充足热量,使铁水的物理热维持在较高水平。是冶炼低硅的必备条件之一。( ) 答案:√ 15.高炉中最重要的流体力学现象是煤气流经固体散料层以及流经固液相共存区(软熔带、滴落带及其以下直至风口平面)时的压降及液泛等。 ( ) 答案:√ 16.从热力学角度看,凡是有利于提高高炉下部温度的措施都有利于降低生铁含硅量。( ) 答案:× 17.高炉冶炼条件下,氧化物由易到难的还原顺序:CuO→PbO→MnO→FeO→SiO 2→Al 2 O 3 → MgO→CaO。 ( ) 答案:× 18.一般讲低级氧化物分解压力比高级氧化物分解压力大。 ( ) 答案:× 19.炼锰铁的高炉炉顶温度显著高于炼普通生铁的高炉,主要是锰的高级氧化物转变为低级氧化物时为放热反应,而铁的高级氧化物转变为低级氧化物时为吸热反应。 ( ) 答案:× 20.渣铁温度和理论燃烧温度之间无严格的线性关系,因此,理论燃烧温度并不能代表炉缸温度和硅含量的高低。 ( ) 答案:√ 21.离子理论认为,随渣的碱度下降(O/Si比下降),共用O2-越多,硅氧复合离子越来越大,越来越复杂,这是酸性渣粘度大的原因,SiO 2 含量约35%时粘度最低。 ( ) 答案:√ 22.第一热平衡和第二热平衡的碳素燃烧的热收入分别约为70%和60%,前者更接近于高炉实际。 ( ) 答案:×
高炉炼铁工艺流程
高炉炼铁工艺流程 本文是我根据我的上传的上一个文库资料继续修 改的,以前那个因自己也没有吃透,没有条理性,现在这个是我在基本掌握高炉冶炼的知识之后再 次整理的,比上次更具有系统性。同时也增加了一些图片,增加大家的感性认识。希望本文对你有所帮助。 本次将高炉炼铁工艺流程分为以下几部分: 一、高炉炼铁工艺流程详解 二、高炉炼铁原理 三、高炉冶炼主要工艺设备简介 四、高炉炼铁用的原料 附:高炉炉本体主要组成部分介绍以及高炉操作知识 高炉炼铁工艺流程
工艺设备相见文库文档: 一、高炉炼铁工艺流程详解高炉炼铁工艺流程详图如下图所示:高炉炼铁工艺流程
二、高炉炼铁原理 炼铁过程实质上是将铁从其自然形态——矿石等含铁化合物中还原出来的过程。 炼铁方法主要有高炉法、直接还原法、熔融还原法等,其原理是矿石在特定的气氛中(还原物质CO、H2、C;适宜温度等)通过物化反应获取还原后的生铁。生铁除了少部分用于铸造外,绝大部分是作为炼钢原料。 高炉炼铁是现代炼铁的主要方法,钢铁生产中的重要环节。这种方法是由古代竖炉炼铁发展、改进而成的。尽管世界各国研究发展了很多新的炼铁法,但由于高炉炼铁技术经济指标良好,工艺简单,生产量大,劳动生产率高,能耗低,这种方法生产的铁仍占世界铁总产量的95%以上。 炼铁工艺是是将含铁原料(烧结矿、球团矿或铁矿)、燃料(焦炭、煤粉等)及其它辅助原料(石灰石、xx、锰矿等)按一定比例自的风口向高炉内xx高炉炉顶装入高炉,并由热风炉在高炉下部沿炉. 高炉炼铁工艺流程 鼓入热风助焦炭燃烧(有的高炉也喷吹煤粉、重油、天然气等辅助燃料),在高温下焦炭中的碳同鼓入空气中的氧燃烧生成的一氧化碳和氢气。原料、燃料随着炉内熔炼等过程的进行而下降,在炉料下降和上升的煤气相遇,先后发生传热、还原、熔化、脱炭作用而生成生铁,铁矿石原料中的杂质与加入炉内的熔剂相结合而成渣,炉底铁水间断
高炉炼铁原理与工艺知识问答
高炉炼铁原理与工艺知识问答 1.高炉原料中的游离水对高炉冶炼有何影响? 答:游离水存在于矿石和焦炭的表面和空隙里。炉料进入高炉之后,由于上升煤气流的加热作用,游离水首先开始蒸发。游离水蒸发的理沦温度是100℃,但是要料块内部也达到100℃,从而使炉料中的游离水全部蒸发掉,就需要更高的温度。根据料块大小的不同,需要到100℃,或者对大块来说,甚至要达到200℃游离水才能全部蒸发掉。 一般用天然矿或冷烧结矿的高炉,其炉顶温度为100~300℃,因此,炉料中的游离水进入高炉之后,不久就蒸发完毕,不增加炉内燃料消耗。相反,游离水的蒸发降低了炉顶温度,有利于炉顶设备的维护,延长其寿命。另一方面,炉顶温度降低使煤气体积缩小,降低煤气流速,从而减少炉尘吹出量。(炉顶温度用来蒸发炉料的游离水,减少燃料消耗保护炉顶设备,降低煤气体积) 2、高炉原料中的结晶水对高炉冶炼有何影响? 答:炉料中的结晶水主要存在于水化物矿石(如褐铁矿和高岭土)中间。高岭土是黏土的主要成分,有些矿石中含有高岭土。试验表明,褐铁矿中的结晶水从200℃开始分解,到400~500℃才能分解完毕。高岭土中的结晶水从400℃开始分解,但分解速度很慢,到500~600℃迅速分解,全部除去结晶水要达到800~1000℃。可见,高温区分解结晶水,对高炉冶炼是不利的,它不仅消耗焦炭,而且吸收高温区热量,增加热消耗,降低炉缸温度。
3、高炉内碳酸盐分解的规律如何?对高炉冶炼有何影响? 答:炉料中的碳酸盐主要来自熔剂(石灰石或白云石),有时矿石也带入一少部分。炉料中的碳酸盐在下降过程中逐渐被加热发生吸热分解反应。它们的开始分解温度和激烈分解温度(即化学沸腾温度)是由各自的分解压(即分解反应达到平衡状态时分压)与高炉内煤气中分压和煤气的总压决定的。碳酸盐的分压随温度升高而增大的,当分解压超过高炉内煤气的分压时,它们就开始分解,而分解压超过煤气的总压时就激烈分解,即化学沸腾。由于高炉冶炼条件不同,不同高炉内的总压力和分压也有差别,碳酸盐在不同高炉内开始分解和化学沸腾分解温度也有差别。碳酸盐分解一般都发生在低温区,对高炉冶炼无大影响。而石灰石就不一样,它的开始分解温度在700℃以上,而沸腾分解温度在960℃以上,而且分解速度受到物料粒度影响很大,一方面是分解出的CO2向外扩散制约分解;另一方面反应生成的CaO的导热性很差,阻挡外部热量向中心部位传递,石灰石块中心不易达到分解温度,这样石灰石总有部分进入高温区分解。此时分解反应产物CO2就会与焦炭发生碳素溶解损失反应,此反应是吸热 反应。这样进入高温区分解的CaCO3会消耗自身分解的热和部分分解出的CO2与C反应热,生产实践表明,高炉炼铁每使用100Kg 石灰石,焦比要升高30~40Kg。因此生产中要求去除高炉配料中的石灰石。其途径是将石灰石加入烧结配料生产自熔性或高碱度烧结矿。在用天然矿冶炼时,小高炉上可用生石灰代替石灰石;大高炉上控制其粒度在25~30mm 以改善石灰石分解条件。
高炉冶炼工艺
第一章概述 课时:2学时 授课内容: 一、钢铁工业发展简史 二、高炉冶炼产品 三、高炉生产主要技术经济指标 目的要求: 1.了解炼铁、炼钢工业的发展简史; 2.掌握炼铁产品及炼铁技术经济指标。 重、难点: 1.炼铁产品及炼铁技术经济指标。 教学方法: 利用多媒体以课堂讲授为主,结合实际范例进行课堂讨论。 讲授重点内容提要 一、钢铁工业发展简史 1、我国炼铁工业的发展简史 ◆早在2500年前的春秋、战国时期,就已生产和使用铁器,逐步由青铜时代过渡到铁器时代。 ◆公元前513年,赵国铸的“刑鼎”。 ◆1891年,清末洋务派首领张之洞首次在汉阳建造了两座日产lOOt生铁的高炉,迈出了我国近代炼铁的第一步。 ◆之后,先后在鞍山、本溪、石景山、太原、马鞍山、唐山等地修建了高炉。 ◆l943年是我国解放前钢铁产量最高的一年(包括东三省在内),生铁产量180万t,钢产量90万t,居世界第十六位。 ◆1949年,生铁年产量仅为25万t,钢年产量l5.8万t。 ◆新中国成立后,我国于l953年生铁产量就达到了190万t,当时超过了历史最高 水平。 ◆1957年生铁产量达到了597万t,高炉利用系数达到了l.321,我国在这一指标 上跨入世界先进行列(美国当时高炉利用系数为1.0)。 ◆1958年生铁产量为l364万t。 ◆1978年生铁产量突破了3000万t。 ◆1988年生铁产量达到了6000万t。 ◆1993年生铁产量为8000万t,跃居世界第二位。 ◆1995年生铁产量为1亿t,居世界第一位。 ◆1998年生铁产量为l.2亿t。 2、现代炼钢方法及其发展趋势 ◆1855年英国冶金学家亨利2贝塞麦发明酸性空气底吹转炉炼钢方法。 ◆平炉炼钢法由于用重油、成本高、冶炼周期长、热效率低等致命弱点,已基本上被淘汰。 ◆氧气转炉炼钢法以氧气顶吹转炉炼钢法为主,同时还有底吹氧气转炉炼钢法、顶底复合吹炼氧气转炉炼钢法。 ◆l996年我国钢产量已达到一亿多吨,其中氧气转炉炼钢法所炼钢约占70%。 ◆2005年我国粗钢产量已达到3.49亿吨,其中氧气转炉炼钢法所炼钢约占75%。 ◆电炉炼钢法以交流电弧炉炼钢为主,同时也有少部分直流电弧炉炼钢、感应炉炼钢及电渣重熔等。
高炉炼铁工艺流程(经典)
高炉炼铁工艺流程分为以下几部分: 一、高炉炼铁工艺流程详解 二、高炉炼铁原理 三、高炉冶炼主要工艺设备简介 四、高炉炼铁用的原料 附:高炉炉本体主要组成部分介绍以及高炉操作知识
一、高炉炼铁工艺流程详解 高炉炼铁工艺流程详图如下图所示: 二、高炉炼铁原理 炼铁过程实质上是将铁从其自然形态
——矿石等含铁化合物中还原出来的过程。 炼铁方法主要有高炉法、直接还原法、熔融还原法等,其原理是矿石在特定的气氛中(还原物质CO、H2、C;适宜温度等)通过物化反应获取还原后的生铁。生铁除了少部分用于铸造外,绝大部分是作为炼钢原料。 高炉炼铁是现代炼铁的主要方法,钢铁生产中的重要环节。这种方法是由古代竖炉炼铁发展、改进而成的。尽管世界各国研究发展了很多新的炼铁法,但由于高炉炼铁技术经济指标良好,工艺简单,生产量大,劳动生产率高,能耗低,这种方法生产的铁仍占世界铁总产量的95%以上。 炼铁工艺是是将含铁原料(烧结矿、球团矿或铁矿)、燃料(焦炭、煤粉等)及其它辅助原料(石灰石、白云石、锰矿等)按一定比例自高炉炉顶装入高炉,并由热风炉在高炉下部沿炉周的风口向高炉内鼓入热风助焦炭燃烧(有的高炉也喷吹煤粉、重油、天然气等辅助燃料),在高温下焦炭中的碳同鼓入空气中的氧燃烧生成的一氧化碳和氢气。原料、燃料随着炉内熔炼等过程的进行而下降,在炉料下降和上升的煤气相遇,先后发生传热、还原、熔化、脱炭作用而生成生铁,铁矿石原料中的杂质与加入炉内的熔剂相结合而成渣,炉底铁水间断地放出装入铁水罐,送往炼钢厂。同时产生高炉煤气,炉渣两种副产品,高炉渣铁主要矿石中不还原的杂质和石灰石等熔剂结合生成,自渣口排出后,经水淬处理后全部作为水泥生产原料;产生的煤气从炉顶导出,经除尘后,作为热风炉、加热炉、焦炉、锅炉等的燃料。炼铁工艺流程和主要排污节点见上图。 三、高炉冶炼主要工艺设备简介 高护炼铁设备组成有:①高炉本体;②供料设备;③送风设备;④喷吹设备;⑤煤气处理设备;⑥渣铁处理设备。 通常,辅助系统的建设投资是高炉本体的4~5倍。生产中,各个系统互相配合、互相制约,形成一个连续的、大规模的高温生产过程。高炉开炉之后,整个系统必须日以继夜地连续生产,除了计划检修和特殊事故暂时休风外,一般要到一代寿命终了时才停炉。 高炉炼铁系统(炉体系统、渣处理系统、上料系统、除尘系统、送风系统)主要设备简要介绍一下。
高炉冶炼学
1.影响高炉软熔带形状的因素有哪些? 答:根据高炉解剖研究及矿石的软熔特性,软熔带形状与炉内等温线相适应,而等温线又与煤气中CO2分布相适应。在高炉操作中炉喉煤气CO2曲线形状主要靠改变布料制度调节,其次是受送风制度影响。因此,软熔带的形状主要是受装料制度与送风制度影响,前者属上部调剂,后者属下部调剂,对正装比例为主的高炉,一般都是接近倒V 形软熔带;对倒装为主或全倒装的高炉,基本上属V形状软熔带;对正、倒装各占一定比例的高炉,一般接近W形软熔带。 2.高炉冶炼过程中铁水含P、Cu能否控制?为什么? 答:在高炉的冶炼过程中不能控制铁水中的P、Cu。原因是根据化学热力学的基本原理,通过查看多种氧化物的氧势图可知:Cu极易被CO所还原,因此在高炉的条件下Cu几乎100%被还原为金属态,可溶入液态Fe中形成合金。而P在较高温度下可被固体C还原,其还原反应的开始温度大约是870oC,所以,P在高炉中几乎100%还原。 3.高炉中降低rd的措施有哪些? 答:生产中采用降低r d的主要措施有:高压操作、高风温、富氧、喷吹燃料及加入精料等。 压力对还原的影响是通过压力对反应CO2+C=2CO的影响体现的,压力的增加有利于反应向左进行,有利于的CO2存在,这就有利于间接还原的进行。 富氧对间接还原发展有利的方面是炉缸煤气中CO浓度的提高与氮含量降低。 喷吹燃料以后,改变了铁氧化物还原和碳气化的条件,炉内温度变化使焦炭中的碳与CO2发生反应的下部区温度降低,而氧化铁间接还原的区域温度升高,这样明显有利于间接还原的发展和直接还原度的降低。
由于精料是使用高品位、低渣量、高还原性、低FeO的自熔性富矿,这有助于间接反应的进行。 4.为什么高压操作的高炉有利于降低焦比和炉况顺行? 答:高炉采用高压操作后,使炉内煤气流速降低,从而减小煤气通过料柱的阻力可使炉况顺行。 如果维持高压前煤气通过料柱的阻力,则可获得增加产量的效果,并且减少炉尘吹出量,所以根据焦比的公式可知,高压操作可降低焦比。 5.为什么铁水含[Si]可作为炉热状态的标志? 答:由于Si还原是强吸热反应,一般还原出1kgSi需热量约相当于从FeO中荒原出1kgFe所需的热量的8倍。所以生铁中含Si量愈高,炉温也升高,生产中常以生铁含Si的高低来反应炉温变化。 6.影响焦比的因素有哪些? 答:焦比是指冶炼每吨生铁消耗的干焦(或综合焦炭)的千克数: 影响焦比的因素主要有入炉品位,精料的使用,直接还原度,以及利用煤气的热能和化学能的状况;高炉采用的改进操作制度,如是否采用高压操作,喷吹燃料,高温风,高富氧等技术在改变焦比方面有重要的影响。 7 .影响炉渣粘度的因素有哪些? 答:对于均相的液态炉渣来说,决定其粘度的主要因素是成分及温度。而在非均相状态下,固态悬浮物的性质和数量对粘度有重大影响。 温度降低到一定值后,粘度急剧上升称为“短渣”;随温度下降粘度上升缓慢者称为“长渣”。高炉渣多为短渣。