涂装技术条件
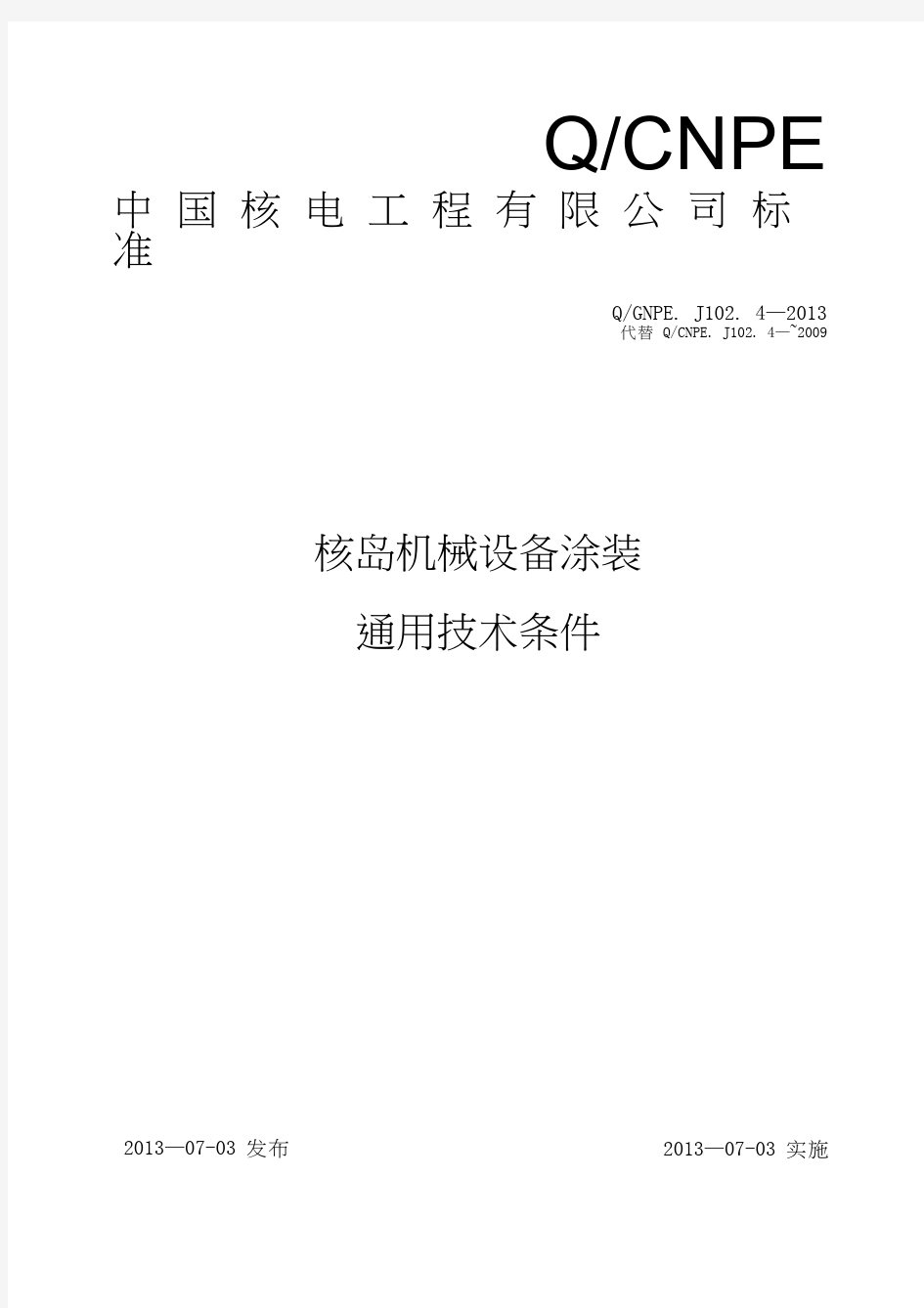

铸件涂漆作业指导书
铸件涂漆作业指导书 涂漆前要求: 操作者要对产品进行检查确认是否达到喷漆要求各个表面是否有毛刺、铁包、粘砂或其他的缺陷,如有必须进行必要的打磨。 待涂漆铸件经抛丸后,表面清理干净,符合涂漆要求。 铸件抛丸到涂漆的时间间隔不超过8小时(有特殊要求的按其要求执行)。 涂料准备: 操作者根据铸件种类按技术要求调配、使用涂料。检查涂料、稀释剂和防锈油以及其他材料是否符合规定要求准备齐全。 检查压缩空气装置、喷漆设备等是否能正常运转。 各种工装辅具、辅助材料是否准备齐全。 喷涂前的涂料要搅拌均匀,双组份漆须先单独搅拌均匀后,再按比例定量配置、均匀调配。调配好的双组份漆放置超过6小时者不可使用。 严格禁止不同漆种(包括不同颜色)交替使用相同容器。 涂漆操作: 涂漆时先喷(涂刷)内腔后刷涂外表,先涂加工部位的一面(上表面),然后再翻转喷另一面,达到覆盖整个铸件表面。 底漆需涂覆两遍,应在漆膜表干后再进行第二遍的喷(刷)漆操作,铸件表面不准有起皱、堆积、流挂,死角不得漏漆和露底。 每层漆膜厚度为3050微米,最终厚度应确保在60100微米内,如顾客有 特殊要求按顾客要求控制。 双组份漆硬化时间在5小时以上方可转运铸件。铸件喷刷底漆后要防止表面被污染。 涂漆中翻转、装车、转运应有防护措施,防止损坏漆膜,因翻转、装车、转运损伤的漆膜必须及时补涂。 检查员负责对每日漆膜质量进行抽查,采用划痕法、比较法或用涂层测厚仪检查漆膜厚度,并记录,不合格的涂漆需返工,无法弥补时将重新抛丸去掉不合格漆膜后重新涂漆。 顾客有特殊要求的按其专项指导书执行。
安全环境 操作者经培训上岗,易燃物品专人管理,工作场地和库房严禁烟火保持工作场地通风,涂漆作业前按要求配带好防护口罩或通风面具。 工作场地环境温度必须达到5℃以上,低于5℃时不得进行涂漆操作。相对湿度RH<85%。 每天工作完毕,按“5S管理要求”清理整顿工作场所。 编制校对审批日期
变速箱通用技术条件
费城搅拌器变速箱通用技术条件 JT 第105册共19页 河南中光学集团有限公司 2003年5月
费城搅拌器变速箱通用技术条件 1范围 1.1主题内容 本技术条件规定了费城搅拌器变速箱(以下简称变速箱)的技术要求、试验方法、检验规则及标志、包装、运输、贮存。 1.2适用范围 本技术条件适用于变速箱系列产品及其零、部件。 2引用标准 GB/T1031-1995 《表面粗糙度参数及其数值》 GB/T131-1993 《机械制图表面粗糙度符号、代号及其注法》 GB/T1182-1996 《形状和位置公差通则、定义、符号和图样表示法》 GB/T1184-1996 《形状和位置公差未注公差值》 GB10095-1988 《渐开线圆柱齿轮精度制与侧隙》 JB/T5000.12-1988 《重型机械通用技术条件涂装》 GB/T13384-1992 《机电产品包装通用技术要求》 GB191-1990 《包装储运图示标志》 GB/T2828-1987《逐批检查计数抽样程序及抽样表》 3 技术要求 3.1总则 变速箱及其零部件应按经规定程序审批的产品图样及技术文件制造与验收,并符合本技术条件的规定。 3.2图纸转化中的一般要求 3.2.1对于图纸中的表面粗糙度,应在不降低原设计要求的基础上符合下述标准要求: GB/T1031-1995 《表面粗糙度参数及其数值》 GB/T131-1993 《机械制图表面粗糙度符号、代号及其注法》 3.2.2图纸中尺寸、尺寸公差及形位公差的转化要求: a)尺寸及各项公差的转化,原则上保持原有精度,只将其数值大小由英制转化为公制即可。 b)形位公差的转化,应符合GB/T1182-1996《形状和位置公差通则、定义、符号和图样 表示法》及GB/T1184-1996《形状和位置公差未注公差值》的要求。 3.2.3齿轮精度在对等原则下,转化为符合GB10095-1988《渐开线圆柱齿轮精度制与侧隙》
摩托车涂装通用技术条件
摩托车涂装通用技术条件 1适用范围 本技术条件规定了公司各种摩托车部件零部件的涂装技术要求及试验方法,它适用所有本公司摩托车的涂漆零部件。 2引用标准 下列文件中的条款通过本标准的引用而成为本标准的条款。凡是注日期的引用文件,其随后所有的修改单(不包括勘误的内容)或修订版均不适用于本标准,然而,鼓励根据本标准达成协议的各方单位沟通是否可使用这些文件的最新版本。凡是不注日期的引用文件,其最新版本适用于本标准。 GB/T1720 漆膜附着力测定法 GB/T1727 漆膜一般制备法 GB/T1732 漆膜耐冲击测定法 GB/T1733 漆膜耐水性测定法 GB/T1734 漆膜耐汽油性测定法 GB/T1740 漆膜耐湿热测定法 GB/T1743 漆膜光泽测定法 GB/T1763 漆膜耐化学试剂性测定法 GB/T1764 漆膜厚度测定法 GB/T1765 测定耐湿热、耐盐雾、耐候性(人工加速)的漆膜制备法 GB/T1766 色漆和清漆涂层老化的评级方法 GB/T1769 漆膜磨光测定法 GB/T1865 色漆和清漆人工气候老化和人工辐射暴露(滤过的氙弧弧辐射) GB/T3181 漆膜颜色标准 GB/T3186 涂装产品的取样 GB/T6514 涂装作业安全规程涂装工艺通风净化 GB/T6739 漆膜硬度铅笔测定法 GB/T6807 钢铁工件涂装前磷化处理技术条件 GB8264 涂装技术术语 GB/T9276 涂层自然气候暴露试验方法 GB/T9969.1 工业产品使用说明书总则 GB/T11186.3 漆膜颜色的测量方法第三部分色差计算 GB/T12334 金属和其他非有机覆盖层关于厚度测量的定义和一般规则 JB/T7504 静电喷涂装备技术条件 JB/T6978 涂装前表面准备——酸洗 QC/T29117.3-93 摩托车和轻便摩托车产品质量检验评定:整车外观质量评定方法3定义 本标准采用下列定义,涂装技术其它术语引用GB 8264。 3.1 油漆涂层缺陷用语 3.1.1 起泡 涂层表面呈现鼓包现象。 3.1.2针孔 漆膜表面呈现针孔状小孔或毛孔的现象。 3.1.3起皱 漆膜表面呈现凹凸不平且无规则线状褶皱的现象。 3.1.4桔皮 漆膜表面呈现桔皮状纹路的现象。
油漆厚度检测作业指导书
油漆厚度检测作业指导书-标准化文件发布号:(9456-EUATWK-MWUB-WUNN-INNUL-DDQTY-KII
油漆厚度检测作业指导书 1.0范围 该作业指导书描述了的油漆厚度检验过程和验收方法。 2.0 最终检验员负责油漆的湿膜厚度检验,和干膜厚度检验。 3.0湿膜厚度检验: 膜厚度测厚仪的优点在于可以在涂覆过程中检查和改正不适当的涂膜厚度。如果涂覆者知道了湿膜厚度,当以此数据乘以涂料固体份的体积百分率,就可估算出干膜厚度。 干膜厚度(μm)=湿膜厚度(μm)*涂料固体分(体积%)。 湿膜厚度的测定,只是保证干膜膜厚的辅助手段,由于干、湿膜比例变化很大,仅用湿膜厚度估算干膜厚度,会带来偏差,评价总厚度,还是以干膜厚度为准。 3.1设备:湿膜厚度梳规 3.2测量方法:把试板固定在一合适的水平基础上,这样在测定漆膜过程中试板就不会 产生移动或跳动,将该仪器放在待测厚度湿膜上,使其最小读数在顶部,而仪器偏心轮和湿膜之间最大间隙正好在湿膜上方,然后将其向前滚动半周(180°)并反方向重复滚动半周(180°)后移动,检查仪器中央轮缘与湿膜表面首先接触的位置,读出读数并计算平均值成为一个读数。当使用每个标度的线性中心区段,即使用标度总量程的80%左右的区段,精度最高。
3.3抽样比例:湿膜厚度是参照数值,用于油漆工艺认证和过程监视。常规油漆不定期 巡检。工艺认证时每批抽检一个。 3.4检验记录:油漆湿膜厚度巡检记录。 4.0干膜厚度检验 4.1设备:易高345 超声波膜厚检测仪。 4.2测量方法:
校正错误处理: 如果在校正中显示屏上出现1Err表明校正没有正确的进行,可能是不正确的基材、数值和单位造成的,按θ键可以消除错误信息,仪器会自动恢复到工厂校正模式,请重新进行校正即可。 光滑表面校正: 放置探头在裸露金属上,等到有读数显示,然后把它打开。按“0”键把显示复0。 紧密贴近裸露金属放置校准膜片,然后读数。按+和-键来调节显示值到测试箔值。 按θ键来确定这次校验或等待7秒让仪器自动确定已被校准。显示器会闪烁然后重复显示读数。在“0”和膜片上确认仪器的读数。简单重复以上步骤即可重新校准。 4.3抽样比例:参照批准的油漆程序,或者客户批准的规范。 检验位置:阀体上正反面各5点,阀盖正反各4点,共计18点。 4.4验收标准和检验记录:验收标准按照程序文件或客户批准规范,检验结果记录在 阀门最终检验记录上。 5.0其它要求: 5.1涂装和油漆厚度检测期间, QC 必须按照公司的要求正确佩戴防护用品。 5.2 湿膜厚度计使用后,需要采用相应的稀释剂或清洗剂清洁干净,放置干燥处。长期 不用时应将仪器涂上油进行防锈处理。 5.3 干膜厚度计需要按照公司的要求进行检定或校准,使用前需要采用标准片进行复 校。 使用完毕,防止干燥整洁处。
金属件涂装通用技术条件讲解
金属零部件涂装通用技术条件 1范围 本标准规定了金属零部件上的涂装的种类和等级、要求、试验方法、检验规则、包装、运输及贮存。 本标准适用于在不同金属底材零件(以下简称“零件”)表面上进行的、主要以装饰及防 腐蚀为目的的一般装饰用涂装(以下简称“涂装”)。 本标准适用如下涂装: a)以酸洗磷化处理的金属; b)真空镀膜的涂装; c)以指向性反射或萤光性为目的的涂装; d)电绝缘性为目的涂装。 2规范性引用文件 下列文件中的条款通过本标准的引用而成为本标准的条款。凡是注日期的引用文件,其随后所有的修改单(不包括勘误的内容)或修订版均不适用于本标准,然而,鼓励根据本标准达成协议的各方研究是否可使用这些文件的最新版本。凡是不注日期的引用文件,其最新版本适用于本标准。 GB/T 1731-1993 GB/T 1732-1993 GB/T 1733-1993 GB/T 1734-1993 GB/T 1735-1979 GB/T 1743-1979 GB/T 1763-1979 GB/T 1764-1979 GB/T 1766-1995 GB/T 1771-1991 GB/T 1865-1989 GB/T 2828-1987 GB/T 6739-1996 GB/T 6807-2001 GB/T 9276-1996 GB/T 9286-1988 GB/T 9754-1988 GB/T 9761-1988 GB/T 13452.2-1992色漆和清漆漆膜厚度的测定漆膜柔韧性测定法漆膜耐冲击性测定法漆膜耐水性测定法漆膜耐汽油性测定法漆膜耐热性测定法漆膜光泽测定法漆膜耐化学试剂性测定法漆膜厚度测定法色漆和清漆涂层老化评级方法色漆和清漆耐中性盐雾性能的测定漆膜老化(人工加速)测定法逐批检查计数抽样程序及抽样表(适用于连续批次的检查)漆膜硬度铅笔测定法 钢铁工件涂装前磷化处理技术条件漆层自然气候曝露试验方法色漆和清漆色漆和清漆色漆和清漆 漆膜的划格试验 60度镜面光泽的测定 色漆的目视比色
涂装通用技术条件
机械制造作业指导书 HZ\WI7.5-20-2002 涂装过程控制规定 文件提出部门: 编写: 审核: 批准: 2002年9 月 2 日发布 2002年9 月 2 日实施
⒈主题内容与适用范围 本指导书规定了机械产品涂装的通用技术要求与检验规则。 本指导书适用于机械产品的防护和装饰性涂装。 ⒉术语 ⒉1底漆 直接涂于物体表面打底,是基层用漆。其防锈能力强,附着力强,对金属起防锈作用。 ⒉2腻子 用于预先涂有底漆的表面,填平凹坑、缝隙、碰伤及划伤等缺陷;腻子应具备良好的结合力和打磨性能,经打磨后呈平整光滑的表面。 ⒉3面漆 用于底漆和腻子之后,保护底漆和腻子,对金属起防蚀作用。面漆应具有良好的耐候性、化学稳定性及物理机械性能。涂膜光亮,色彩绚丽,使产品外形光滑、整洁、美观。 ⒉4稀释剂 用于稀释涂料,是涂料的辅助材料之一。 ⒊涂料要求 ⒊1涂装所用的底漆、腻子、二道底漆、面漆、稀释剂,应具有良好的配套性。必须配套使用,具体品种按表1规定选用,图样或技术文件有特殊要求时按其要求选用。 ⒊2涂料的质量必须符合化工部标准或有关标准的规定。 表1 ⒋涂层部位与涂层颜色 ⒋1产品机身外部表面的涂料颜色一般按图纸要求执行,也允许按用户要求
确定。 ⒋2机身上可以根据具体情况采用不同的装饰性线条或颜色。 ⒋3齿轮箱体和箱盖、轴承盖、油箱的未加工内壁,以及经常浸在油中的零件未加工表面,应涂耐油涂料。 ⒋4装配后不易或不能涂装的部件或表面应在装配前涂装。 ⒋5需要引起注意部位的涂装,应涂鲜艳色彩的涂料。裸露的转动零件如飞轮、皮带轮、齿轮等轮辐及转动罩壳,应涂红色涂料。 ⒋6产品上各种特殊标志,如厂名、商标、指示符号、警戒标志等,应涂与该标志所在部位的颜色有明显区别、协调而醒目的颜色。 ⒋7已涂装的外购件和外协件,如涂膜未被破坏且装配后不影响整机美观时,可不再涂装。否则必须用与原色相同的涂料补涂。 ⒌涂装施工 涂装施工时,必须严格遵守各种涂料对温度、湿度、重涂间隔时间、调配方法、注意事项等各种规定。 ⒌1施工条件的要求 ⒌⒈1涂装施工应在清洁、干燥、空气流通、光线充足的地方进行,环境温度应保持在10~35℃。相对温度不大于75%。 ⒌⒈2涂装用具必须清洁。喷涂用的压缩空气应保持清洁干燥。 ⒌2涂面清洁的要求 ⒌⒉1经喷丸(砂)处理的零件表面,应呈金属本色,不得有残存氧化皮、型砂、锈迹等。经预处理喷底漆的型材组焊后,焊缝处必须手工除锈补漆。⒌⒉2经酸洗、磷化处理的零件,其表面应无氧化皮、锈迹、油污、酸碱液等。磷化膜应结晶致密、连续、均匀,不允许有绿斑、严重挂灰、结晶疏松等缺陷。 ⒌⒉3经手工打磨的零件表面,不应残存浮锈、氧化皮、型砂、焊渣、油污等。 ⒌3涂装的要求 ⒌⒊1涂底漆 ⒌⒊⒈1涂面清理完后,应在4小时内涂一道底漆。 ⒌⒊⒈2除下列情况不涂底漆之外,其他金属零件均应涂底漆。 a.零件加工表面; b.标准件;
喷漆作业指导书
喷漆作业指导书 1、前期处理 1.1坯面清理:根据车辆修复后的状况,采用除锈剂、砂纸、铁刷等进行。 1.2除锈后,用清水将坯面清洗干净,用棉丝等将须抹腻部位擦拭干净,干燥10分钟。 1.3用2号60目粗砂布将须喷漆部位进行打磨。 1.4用清水清洗后,用棉丝等将打磨部位擦拭干净,干燥10分钟。 1.5坯面清理后自检要求:无锈、无剩余不牢固漆皮、无油污。 2、车身修复 2.1调配原子灰,原子灰和固化剂的比例为50: 1。 2.2用调配后的原子灰填在金属表面凹处补修复表面。 2.3干燥: a)大气温度20C以上时,自然干燥,干燥时间不少于20分钟。 b)大气温度低于20C,红外线烤干,干燥不少于5分钟。 c)温度过高、过低时,适当延长或缩短干燥时间,每低5度干燥时间延长10 分钟。每高5度干燥时间缩短5分钟。用红外线烤干时,干燥时适当缩短。 d)当环境湿度大于85%以上时,禁止用原子灰填补修复操作。 e)第一道腻子干燥后,用2号60目干砂布将填补修复表面进行曲打磨。 2.4第二遍用原子灰填补修复不平表面。 2.5干燥(同2. 3.) 2.6第二道腻子干燥后,用P150-P240号水砂纸将填补修复表面进行打磨。 2.7第三遍用原子灰填补修复不平表面。 2.8干燥(同2. 3.) 2.9第三道腻子干燥后,用P600-P800号水砂纸将填补修复表面进行打磨。 2.10个别有砂眼的地方用砂眼灰找平。 2.11用P800-P1000号水砂纸将修补表面磨平。 2.12 干燥(同2. 3.) 2.13填补修复表面后自检要求:无砂眼,无砂纸道痕、完全平整、光滑。
3、喷底漆 3.1配合比例:稀料与底漆比例为2: 1用搅拌尺充分搅匀。 3.2喷底漆:喷枪喷嘴直径①1.5— 1.8mm 将喷枪的压力调至0.3土0.1Mpa,使喷枪喷出的液体呈直角、扇面形、喷嘴至漆 面约15-20 cm0 3.3干燥:大气温度常温时(20度以上),干燥时间不低于10分钟,大气温度过高、过低时,适当延长或缩短干燥时间。 3.4打磨:用P1000号水砂纸将喷漆表面进行打磨至平整、光滑。 3.5干燥:大气温度常温时(20度以上),干燥时间不低于15分钟,大气温度过高、过低时,适当延长或缩短干燥时间。 3.6使用压缩空气将喷漆表面吹干净。 3.7喷底漆表面自检要求:无滑痕、平整、光滑。 4、喷普通面漆 4.1喷面漆 a)使用已调制好的漆料进行喷漆作业。 b)漆在使用前加的固化剂、稀料比例为:漆和固化剂2:1加30%稀料。 c)喷枪喷嘴直径:①1.5—1.8伽 d)使用压缩空气压力:0.4—0.8Mpa e)喷漆每遍相隔时间:每次喷完漆后自然干燥5—10分钟,最后一遍面漆需要烘干,60C± 5C烘干30分钟。 f)干燥:整车喷好后,在大气温度20C时,至少干燥6—8小时。大气温度过高、过低时,适当延长或缩短干燥时间。 4.2喷漆表面要求:平滑、光亮、色泽均匀、边界整齐、漆面无泡、无龟裂、无皱纹、无流痕、不须喷的部位不得有漆痕。 5、喷金属面漆 5.1.喷面漆 a)使用已调制好的漆料进行喷漆作业。 b)漆在使用前加的稀料比例为:漆和稀料2:1o c)喷枪喷嘴直径:①1.5—1.8伽
涂装上挂作业指导书(1)
2.定义:(无) 3.适用范围:涂装2号、3号线 4.要求: 4.1作业前准备: 4.1.2作业前按规定戴好手套、穿上围裙等劳保用品; 4.1.3按照生产计划及组长工作安排,准备好相关吊具、挂具,并将工件移到指定区域。 4.2作业过程: 4.2.1首先检查吊具的完好、适用性;变形、散架的吊具、挂具挑出作修整,挂具导电不佳的挑出作退漆处理(以点面接触的工件必须确保接触点面无漆膜;以线面接触的工件必须确保接触线面漆膜不超过200UM);吊具漆膜超过800UM的挑出作退漆处理; 4.2.2上挂时按相关工艺卡要求上挂; 4.2.3所挂的吊具,挂具需确保平稳,无缺挂具等现象; 4.2.4所有上挂的工件必须是经过品管人员确认合格后,方可上挂; 4.2.5工件上挂前,需作全面的检查,检查项目为: A.工件规格、数量应与物料卡相符合,有异常需及时向上级主管汇报,并知会相关人员及时处理; B、工件外形结构应与样品相符合,检查工件外观,如有碰伤、变形、喷丸不均而产生的凹点超过1MM深的不良工件,经修整合格以后再上挂; C、检查工件各焊接点、线面处,打磨点面,如有漏焊、焊渣、焊瘤及有无磨伤;磨不到位等,按《涂装部修整作业指导书》修整以后上挂; D、检查工件内、外表面及焊接处的表面状况,如有锈斑无法用锉刀或砂纸打磨克服的工件请挑出; E、经过酸处理的工件,必须检查其表面锈斑状况,确认合格后,方可上挂。 4.2.6经过酸处理工件的上挂过程: A、经酸处理的工件,必须优先投入生产; B、经酸处理的工件,当其发黄面积超过3CM2时需重新处理,小于改面积先用布条擦干
到位; 4.2.8在上挂过程中,绝不允许有空挂和空钩的现象。 4.3作业结束: 4.3.1作业结束确定暂不使用的吊具、挂具需及时的分类归位。 4.3.2各工件筐、工件架及生产工具、辅助材料及时归位或存放。 5.罚则:未按作业规范作业人员、处警告以上处分。 6.发行范围:事业一二部涂装部,事业一二部品管课,事业一二部技术设备部,技术开发中心生技部 7.相关文件:《涂装修改作业指导书》 8.附件:(无) 9.作业流程图:
汽车车身涂装的新技术和发展趋势
汽车车身涂装的新技术和发展趋势 河南机电 姓名: 班级: 学号: 2013/5/3
一、汽车车身涂装的基本概述 1.1、汽车车身涂装的定义:将涂料涂至清洁的车身表面上干燥成膜的工艺。 1.2、汽车车身涂装的基本工序:漆前表面处(包括净化表面和化学处理),涂布,固化(包 括烘干,干燥)。 1.3、汽车车身涂装的功能 (1)保护作用:保护车身,使其免受周围介质的侵蚀,起到防腐蚀,防老化和耐各种介质的作用。 (2)装饰作用:车身涂装可使其具有色彩,光泽,鲜映性,平滑性,立体感,和标志等,给人以美的,舒适的感觉。 (3)特种功能:涂装可以调节热,电,等的传导性,防止生物的附着(杀菌),示温,控制声波的散发,反射和吸收,产生夜光等。 1.4、车身涂装得到发展历史 汽车涂装经过了一百多年的发展,已经由最初的作坊式涂装发展到适应于现代大量流水线生产的典型的工业涂装,尤其在进二十多年里,历经了多次质的变革。漆前处理磷化,涂底漆阴极电泳涂装实现现代化,其中涂面漆实现了静电自动喷涂,计算机智能化控制技术等高科技的应用,使汽车车身涂装成为高度自动化和现代化的工艺。涂层质量(外观装饰性和耐腐蚀性等)跟上了时代潮流的要求,达到和超过了汽车的使用寿命。 1.5、涂装的三要素 (1)涂装材料。涂装材料的质量和作业配套性是获得优质涂层的基本条件。在选用涂料时,要从涂膜性能,作业性能和经济效果等方面综合衡量。 (2)涂装工艺。涂装工艺包括所采用的涂装技术(工艺参数)的合理性和先进性,涂装设备和涂装工艺的先进性和可靠性,涂装环境条件以及涂装操纵人员的技能,素质等。 (3)涂装管理涂装管理包括材料管理,设备管理,工艺纪律管理,质量管理,现场环境管理,人员管理等。 二、汽车车身涂装新技术 2.1、新材料应用
各种防腐涂料的国家相关标准
各种防腐涂料的国家相关标准混凝土防腐涂料 1.海港工程混凝土结构防腐蚀技术规 范 JTJ275-2000 2.混凝土桥梁结构表面涂层防腐技术条件JT/T695-2007 3.火力发电厂烟囱(烟道)内衬防腐材料DL/T901-2004 4.烟囱混凝土耐酸耐腐蚀涂料DL/T693-1999 5.水电水利工程金属结构设备防腐蚀技术规 范 DL/L5358-2006 钢结构防腐 1.建筑用钢结构防腐涂料JG/T224-2007 2.交通钢构件聚苯胺防腐涂料JT/T657-2006 3.钢结构桥梁漆HG/T3656-1999 4.铁路钢桥保护涂装TB/T1527-2004 5.富锌底漆HG/T3668-2009 6.喷涂聚脲防护材料HG/T3831-2006 7.交通钢结构聚苯胺防腐涂料JT/T695-2006 8.喷涂聚脲规范JGJ210—2010石油防腐 1.钢质石油储罐防腐工程技术规程GB50393-2008 2.钢制储罐液体环氧涂料内防腐层技术标准SY/T0319-1998 3.钢制管道液体环氧涂料内防腐层技术标准SY/T0457-2000 4.管道无溶剂聚氨酯涂料内外防腐层技术规 范 SY/T4106-2005 船用漆 1.船底防锈通用技术条件GB13351-1992 2.船用防锈漆通用技术条件GB6748-1986 3.船壳漆GB/T6745-2008 4.船用油舱漆GB/T6746-2008 5.船用车间底漆GB/T6747-2008 6.船用防锈漆GB/T6748-2008 7.船舶压载舱漆GB/T6823-2008 8.货舱漆GB/T9262-2008 铁路客运 1.客运专线铁路CRTSI型板式无砟轨道水泥乳化沥青砂浆暂行技术条件
铸件涂漆作业指导书
铸件涂漆作业指导书 1.0涂漆前要求: 1.1操作者要对产品进行检查确认是否达到喷漆要求各个表面是否有毛刺、铁包、粘砂或其他的缺陷,如有必须进行必要的打磨。 1.2待涂漆铸件经抛丸后,表面清理干净,符合涂漆要求。 1.3铸件抛丸到涂漆的时间间隔不超过8小时(有特殊要求的按其要求执行)。 2.0涂料准备: 2.1操作者根据铸件种类按技术要求调配、使用涂料。检查涂料、稀释剂和防锈油以及其他材料是否符合规定要求准备齐全。 2.2检查压缩空气装置、喷漆设备等是否能正常运转。 2.3各种工装辅具、辅助材料是否准备齐全。 2.4喷涂前的涂料要搅拌均匀,双组份漆须先单独搅拌均匀后,再按比例定量配置、均匀调配。调配好的双组份漆放置超过6小时者不可使用。 2.5严格禁止不同漆种(包括不同颜色)交替使用相同容器。 3.0涂漆操作: 3.1涂漆时先喷(涂刷)内腔后刷涂外表,先涂加工部位的一面(上表面),然后再翻转喷另一面,达到覆盖整个铸件表面。 3.2底漆需涂覆两遍,应在漆膜表干后再进行第二遍的喷(刷)漆操作,铸件表面不准有起皱、堆积、流挂,死角不得漏漆和露底。 3.3每层漆膜厚度为3050微米,最终厚度应确保在60100微米内,如顾客有 特殊要求按顾客要求控制。 3.4双组份漆硬化时间在5小时以上方可转运铸件。铸件喷刷底漆后要防止表面被污染。 3.5涂漆中翻转、装车、转运应有防护措施,防止损坏漆膜,因翻转、装车、转运损伤的漆膜必须及时补涂。 4.0检查员负责对每日漆膜质量进行抽查,采用划痕法、比较法或用涂层测厚仪检查漆膜厚度,并记录,不合格的涂漆需返工,无法弥补时将重新抛丸去掉不合 格漆膜后重新涂漆。
2007重型机械通用技术条件
重型机械通用技术条件 1 概况 2007年版《重型机械标准》(以下简称新《重标》)第一卷第3部分“通用技术条件”,共编入标准二十六项。其中包括:生产设备安全卫生设计标准一项,重型机械通用技术条件JB/T5000.1~15-2007及JB/ZQ4722-2006十六项,液压、气动系统通用技术条件三项,以及运输包装方面的标准六项。与1998年版《重型机械标准》(以下简称原《重标》)第一卷第三部分“通用技术条件”的项目相比,删除了一项标准,增加了五项标准,该套标准包含从原材料、外购件、铸件、焊件、锻件、切削加工件、配管、涂装、装配到产品包装全生产过程中各主要工序通用的,也是必须执行的技术规范。是新《重标》的重点部分。新、旧《重标》通用技术条件标准项目对照。见表1。 JB/ZQ 4722-2006 重型机械通用技术条件锻钢件补焊、JB/T 10607-2006 液压系统工作介质使用规范、GB/T 18923-2002 运输包装件质量界限、道路车辆外廓尺寸、GB 1589-2004轴荷及质量限值五项标准。取消了GB/T 1834- 80通用集装箱最小内部尺寸,GB/T 1413- 1998 系列1集装箱分类、尺寸和额定质量中已包含GB/T 1834- 80通用集装箱最小内部尺寸的内容,GB/T 1413-1998将二项标准合并为一项标准。下面重点介绍JB/T5000.1~15新、旧标准的主要差异。 2 JB/T 5000.1 《重型机械通用技术条件产品检验》 2.1 产品检验的一般要求
2.1.1 增加了2.1条对半成品(原材料)的定义。 2.1.2 新《重标》根据使用要求,增加了2.1.3条对半成品的检验要求。 2.1.3 增加了2.3 C)条对外协配套件的选用要求。 2.1.4 新《重标》中的表2将焊缝缺陷等级、焊接件尺寸偏差及形位公差等级的图样标注由原来的4个等级改为3个等级,取消了原《重标》焊缝质量评定级别DS、DK级、焊缝缺陷等级Ⅳ级及尺寸与角度偏差等级D级和形位公差等级H级。 2.1.5 修改了铸件尺寸公差图样标注的毛坯基本尺寸范围及尺寸公差等级,新、旧标准对比见表2。 2500mm和有色金属铸件毛坯基本尺寸≥10~250mm的尺寸分段,增加了铸铁件尺寸公差等级CT11和有色金属铸件尺寸公差等级CT9并规定在图样上不标注。取消了铸钢件毛坯基本尺寸≤16mm的尺寸分段及尺寸公差等级CT12。 2.1.6 修改了涂装除绣等级与腐蚀类别及在图样上标注的规定,新、旧标准差异见表3。 a)新《重标》增加了除绣等级及其在图样上标注的规定; b)根据ISO12944将涂装类别改为腐蚀类别。 c)除绣等级、腐蚀类别、涂层厚度及面漆颜色均按JB/T 5000.12-2007的规定。 2.1.7 增加了2.13条对生产厂家的产品制造质量要求及2.14条对特殊装置的检验要求。 2.2 检验记录 2.2.1 产品质量检验记录种类的C)条增加了粘结剂的检验记录。 2.2.2 原《重标》的5.3条规定“产品质量检验记录由制造厂质量检验部门填报与汇总并建立产品质量档案”,新《重标》在原基础上增加了“如合同约定由第三方对产品质量进行监理,监理方可以见证制造厂的检验过程和检验结果。” 3 JB/T 5000.2 《重型机械通用技术条件火焰切割件》 3.1 适用范围 修改了火焰切割件的适应范围,由原“本标准适用于重型机械产品中碳钢、低合金钢、钛及钛合金板材的火焰切割件”改为“本标准适用于厚度为6~300mm的低碳钢、中碳钢及普通低合金钢的火焰切割件”增加了厚度为6~300mm的低碳钢及取消了钛及钛合金板材的适用范围。 3.2 术语和定义 3.2.1 增加了1.1条火焰切割件、1.7条表面缺陷、1.8条上缘熔化及1.9条挂渣的定义。 3.2.2 修改了垂直度和倾斜度公差及表面粗糙度的定义 a) 垂直度公差原定义是“指在理论正确角度条件(与工件基准面成90°),通过切割面轮廓最高点和最低点的两条平行直线间的距离。垂直度公差用u表示”(见原标准的图1),现定义为“在本部分
电动三轮车篷车涂装通用技术条件
电动三轮车/篷车涂装通用技术条件 1 范围 本标准规定了三轮摩托车、三轮电动车涂装的要求、试验方法、检验规则、包装、运输及贮存。 本标准适用于三轮摩托车、三轮电动车零部件防护装饰性涂装(以下简称“涂装”)。 2引用文件 2.1 GB/T 1723-1993 涂料粘度测定法 2.2 GB/T 1725-2007 色漆、清漆和塑料不挥发物含量的测定 2.3 GB/T 1731-1993 漆膜柔韧性测定法 2.4 GB/T 1732-1993 漆膜耐冲击性测定法 2.5 GB/T 1733-1993 漆膜耐水性测定法 2.6 GB/T 1735-2009 色漆和清漆耐热性的测定 2.7 GB/T 1771-2007 色漆和清漆耐中性盐雾性能的测定 2.8 GB/T 1865-2009 色漆和清漆人工气候老化和人工辐射曝露滤过的氙弧辐射 2.9 GB/T 6739-2006 色漆和清漆铅笔法测定漆膜硬度 2.10 GB/T 6807-2001 钢铁工件涂装前磷化处理技术条件 2.11 GB/T 9276-1996 漆层自然气候曝露试验方法 2.12 GB/T 9286-1998 色漆和清漆漆膜的划格试验 2.13 GB/T 9753-2007-T 色漆和清漆杯突试验 2.14 GB/T 9754-2007 色漆和清漆不含金属颜料的色漆漆膜的20°、60°和85°镜面光泽的测定2.15 GB/T 9761-2008 色漆和清漆色漆的目视比色 2.16 GB/T 13452.2-2008 色漆和清漆漆膜厚度的测定 2.17 GB/T 13893-2008色漆和清漆耐湿性的测定连续冷凝法 3术语和定义 下列术语和定义适用于本标准。 3.1 起泡:涂层表面呈现鼓包的现象。 3.2 针孔:涂层表面呈现针状小孔或毛孔的现象。 3.3 起皱:涂层表面呈现凹凸不平且无规则线状折皱的现象。 3.4 桔皮:涂层表面呈现桔皮状纹路的现象。 3.5 露底:未能完全覆盖前道涂层或材料色泽的现象。 3.6 裂纹:漆膜表面呈现不规则、深浅不同断裂纹路的现象。 3.7 脱落:漆膜从涂面呈现片状脱离的现象。 3.8 凹陷:涂层表面因水、油等异物影响致使涂料不能均匀附着、产生抽缩形式泡疤而呈现凹坑现象。
汽车车身涂装生产线工艺流程
卓科工业汽车车身涂装工艺流程 主要内容; 1涂料和涂装基本知识; 2汽车及零部件涂装工艺; 3涂装工艺方法; 4涂装三废处理;涂料和涂装基本知识 1.1涂料和涂装的概念;涂料:是以高分子材料为主体,以有机溶剂、水或空气;涂装:将涂料均匀地涂布在基体表面并使之形成一层连;?§1涂料和涂装基本知识; 1.2涂料和涂装的作用;1.保护作用;主要是金属防腐蚀; 2.装饰作用;装饰产品表面,主要内容1 涂料和涂装基本知识2 汽车及零部件涂装工艺3 涂装工艺方法4 涂装三废处理涂料和涂装基本知识1.1 涂料和涂装的概念 涂料:是以高分子材料为主体,以有机溶剂、水或空气为分散介质的多种物质的混合物。 涂装:将涂料均匀地涂布在基体表面并使之形成一层连续、致密涂膜的操作工艺称为涂装。 1 涂料和涂装基本知识 1.2 涂料和涂装的作用 1.保护作用:主要是金属防腐蚀。 2.装饰作用:装饰产品表面,美化产品和生活环境。 3.标志作用:做色彩广告标志,起到警告、危险、安全、禁止等信号作用。 4.特殊作用:电气绝缘漆、船底防污漆、超温报警示温涂料、抗红外线涂料 1 涂料和涂装基本知识1.3 涂料的组成 1 涂料和涂装基本知识1.4 涂料的分类和命名 1.分类
一般可以下几种: 1.)根据组成形态分类(溶剂型、无溶剂型、粉末涂料、水性涂料、高固体份等) 2.)按用途分类(建筑涂料、汽车涂料、飞机蒙皮漆、木器漆等) 3.)按涂装方法分类(喷漆、浸漆、烘漆、电泳漆等) 4.)按涂装工序分类(底漆、面漆、腻子、罩光漆) 5.)按效果分类(绝缘漆、防锈漆、防污漆等) 6.)按成膜物质分类 以涂料基料中主要成膜物质为基础。分为18类(17类成膜 物质,1类辅助材料)。 A 氨基树脂涂料Q 硝基涂料 B 丙烯酸树脂涂料 C 醇酸树 脂涂料 H 环氧树脂涂料G 过氯乙烯涂料L 沥青树脂涂料 2.命名 全名=颜色或颜料名称+成膜物质+基本名称 (红醇酸磁漆锌黄酚醛防锈漆) 2 涂装工艺
《汽车涂装技术》模块化教学设计
《汽车涂装技术》模块化教学设计方案 总学时数:108学时(理论课学时数:30学时实践课学时数:78学时) 1 课程概述 1.1课程的性质 1、《汽车涂装技术》是一门为学生日后在汽车行业发展做储备的专业拓展课程之一,是为了本专业培养人才的可持续发展所开设的课程。 2、本课程采用的是理论与实践教学相结合车间教学模式。在理论教学中主要让学生掌握汽车涂装技术的基本理论知识,能够根据会进行表面前处理、遮蔽、调漆、喷漆的基本作业。在实践教学上通过教师的示范,会基于整个汽车涂装的工作流程,进行打磨涂原子灰、车身遮盖、专业调漆及底漆(及中间涂料)、面漆的施涂等作业。 1.2、课程定位 汽车钣喷区是汽车售后维修企业中必备的工作区域,而汽车涂装技术作为钣喷区重要的作业内容,对学生在汽车维修检测行业中的可持续发展起到了重要作用。学生经过《汽车涂装技术》的学习,了解与熟悉汽车涂装的方法技术、使用设备,以及整体涂装流程,同时也是也是维修部门主管级技术员工所必备的专业知识。 本课程是在所有专业课程板块学完后的一门综合性课程,培养学生对汽车车身表面进行恢复的能力,是顶岗实习进入钣喷工作岗位前的专业综合技能训练。 1.3课程设计思路 本课程以校内实训基地和校外实习基地为依托,走“学校与企业结合和操作实训结合+顶岗实习和就业结合”的专业课程建设道路。在确保专业理论知识够用、实用的前提下,强化、优化专业实训、实习教学,实施“以就业为导向”的技能型人才培养模式。 在具体实施过程中,根据本课程自身条件和特点,通过企业特聘教师、本校专业教师和学生在教学上特别是在实践教学上的合作和互动,形成企业与学校教学平台合一,即“基础技能实训、综合技能实训、校外实习基地实习”三位一体的教学模式,真正实现校企结合和工学交替。在基础技能实训中突出单项技能训练的基础性,在综合技能实训中强调整车技能训练的整体性,在校外实习基地实习中重视专业技能的适应性训练,确保学生达到本课程既定的专业知识和技能目标,在整个教学过程中,以学生活动为中心、以“生产实训+顶岗实习”为重点,重视校外实习基地的建设与利用,派学生到校外实习基地进行顶岗实习,采取由校内主讲教师和校外实习基地企业特聘教师相结合的形式对学生进行全程实习指导和管理。 2. 课程基本目标
喷漆 作业指导书 - 制度大全
喷漆作业指导书-制度大全 喷漆作业指导书之相关制度和职责,1.?目的规定了喷漆的设备操作、工艺范围、工艺流程、工具、质量控制标准以及安全操作规程。2.适用范围本标准规定了设备内部各个构件及产品外观涂装的操作方法、技术要求和检验方法。:X^... 1.? 目的 规定了喷漆的设备操作、工艺范围、工艺流程、工具、质量控制标准以及安全操作规程。2.适用范围 本标准规定了设备内部各个构件及产品外观涂装的操作方法、技术要求和检验方法。: X& ^3 B0 3.术语及定义/ L+ Y6 @4 O" ^2 S (1)涂料:是一种有机高分子胶体混合物的溶液,将其涂布在物面上能干结成膜,学名叫“有机涂料”,俗称“油漆”。 (2)涂装:将涂料涂布在物面上的施工过程,即油漆施工。 (3)稀释剂:用来溶解及稀释涂料,以达到施工应用目的的物料。 (4)底漆:直接涂布在物体表面的打底涂料。 (5)防锈漆:由防锈颜料和适当的漆料配置而成,用以防止大气 中的氧气和水分对钢铁本体锈蚀的涂料。 (6)起泡:漆膜干结后,局部与被涂物体表面失去附着力,成直径不同的球状小泡向上膨胀隆起,内部包藏着液体或气体,或者发生破裂的现象。 (7)流挂:涂料施工于垂直物体表面,未干前涂层下流,干后漆膜厚度不匀,并成流痕的现象。 (8)针孔:漆膜在干结过程中,表面出现的一种凹陷的透底的针尖细孔现象。 (9)渗色:在底层漆上涂覆一层漆后,底层漆的颜色由于新漆层溶剂的作用而渗透于表面的现象。 (10)桔皮:涂料喷涂施工后,由于漆腊流平性差,干燥后的漆腊表面形成起伏不平的类似桔皮的现象。' v: t0 I* F" L. w" F (11)褪色:色漆漆膜在暴露中,由于光、热或其它因素的作用,颜色减退失去其原有的颜色的现象。 (12)附着力:指漆膜与被涂物件两种物质表面通过物理和化学力的作用结合在一起的坚牢程度。 (13)脱落与脱皮:由于涂层和物体表面或新旧涂层之间丧失了附着力,涂层表面形成小片或鳞片脱离的现象称为脱落。当涂层和底表面间的附着力完全丧失,使涂膜整张脱落时称为脱皮。 4.0作业程序:检查——挂钩——抛丸——清整——罩漆——烘烤——下架 5.0操作步骤:- Q$ O8 j/ g# R$ 5.1工作前2 L- {# C9 G- g& r 5.1.1上班首先阅读当天生产指令,了解并记录有特殊喷漆要求的单 号。 5.1.2检查工作过程中需要的工具,如挂钩、吹枪等是否到位,完好。 如果没有或损坏需及时上报。 5.1.3检查当天使用的原、辅材料,如果不够需向上级领导反映,班
钣金加工执行标准
标准编号:QJ A 262-2005 标准名称:钣金冲压件通用技术条件 标准状态:现行 实施日期:2006-5-1 出处: https://www.360docs.net/doc/d010621665.html,/detail/167524.html 标准编号:QJ 903.13A-1995 标准名称:航天产品工艺文件管理制度钣金、冲压工艺文件编制规则标准状态:现行 实施日期:1996-3-1 出处: https://www.360docs.net/doc/d010621665.html,/detail/178559.html 标准编号:QJ 262A-2005 标准名称:钣金冲压件通用技术条件 标准状态:现行 实施日期:2006-5-1 出处: https://www.360docs.net/doc/d010621665.html,/detail/179159.html
标准编号:QJ 261-1994 标准名称:电子产品钣金冲压件通用技术条件 标准状态:现行 实施日期:1994-10-27 出处: https://www.360docs.net/doc/d010621665.html,/detail/151775.html 标准编号:QJ 2096.2-1991 标准名称:模件式机柜钣金插箱结构型式及尺寸系列 标准状态:现行 实施日期:1991-9-1 出处: https://www.360docs.net/doc/d010621665.html,/detail/151101.html 标准编号:QJ 2033-1991 标准名称:钣金冲压零件结构要素 标准状态:现行 实施日期:1991-7-1 出处: https://www.360docs.net/doc/d010621665.html,/detail/150638.html 下 载:https://www.360docs.net/doc/d010621665.html,/upload/qy%2Fnn%2FQJ2033-1991.PDF
最新三轮摩托车涂装通用技术条件
三轮摩托车涂装通用 技术条件
三轮摩托车涂装通用技术条件2019-08-08 发布 2010-08-10实施
三轮摩托车涂装通用技术条件 1范围 本标准规定了三轮摩托车涂装的要求、试验方法、检验规则、包装、运输及贮存。 本标准适用于三轮摩托车零部件防护装饰性涂装(以下简称“涂装”)。 2规范性引用文件 下列文件中的条款通过本标准的引用而成为本标准的条款。凡是注日期的引用文件,其随后所有的修改单(不包括勘误的内容)或修订版均不适用于本标准,然而,鼓励根据本标准达成协议的各方研究是否可使用这些文件的最新版本。凡是不注日期的引用文件,其最新版本适用于本标准。 GB/T 1723-1993 涂料粘度测定法 GB/T 1725-2007色漆、清漆和塑料不挥发物含量的测定 GB/T 1731-1993 漆膜柔韧性测定法 GB/T 1732-1993 漆膜耐冲击性测定法 GB/T 1733-1993 漆膜耐水性测定法 GB/T 1734-1993 漆膜耐汽油性测定法 GB/T 1735-2009 色漆和清漆耐热性测定 GB/T 1743-1979 漆膜光泽测定法 GB/T 1763-1979 漆膜耐化学试剂性测定法 GB/T 1764-1979 漆膜厚度测定法 GB/T 1771-2007 色漆和清漆耐中性盐雾性能的测定 GB/T 1865-2009 色漆和清漆人工气候老化和人工辐射暴露 GB 6458-1986 金属覆盖层中性盐雾试验(NSS试验) GB/T 6739-2006 漆膜硬度铅笔测定法 GB/T 6807-2001 钢铁工件涂装前磷化处理技术条件 GB/T 9276-1996 漆层自然气候曝露试验方法 GB/T 9286-1998 色漆和清漆漆膜的划格试验 GB/T 9754-2007 色漆和清漆不含金属颜料的色漆漆膜元20°、60°和85°镜面光泽的测定 GB/T 9761-2008 色漆和清漆色漆的目视比色 GB/T 13452.2-2008 色漆和清漆漆膜厚度的测定 GB/T 13893-2008 色漆和清漆耐湿性的测定 3术语和定义 下列术语和定义适用于本标准。 3.1 起泡 涂层表面呈现鼓包的现象。 3.2 针孔 涂层表面呈现针状小孔或毛孔的现象。 3.3 起皱
涂装作业指导书
防腐作业指导书 编 写: 审 核: 批 准: 2015年3月
一、目的和范围 1.本指导书规定了结构钢的防腐涂装的工艺及操作和检验应遵守的规则。 2.本指导书适用于一般钢结构产品的防腐涂装。 二、 防腐要求 根据卫生间实际使用环境和ISO 12944-2对腐蚀环境的分类,卫生间的外表面腐蚀性类别为C5-M(高温、高湿的沿海气候环境),选用满足海洋气候的防腐涂料。 三、 涂装工艺流程 涂漆前工件表面准备——清除焊渣飞溅、油污等——喷砂、丸清理表面、风管吹干净表面——预涂底漆——表面打磨平整、清洁——预涂中间漆——表面打磨平整、清洁——预涂面漆、喷涂面漆——出厂前进行补漆。 四、 漆膜厚度要求 产品涂漆质量具有耐腐蚀性,耐热、耐潮湿性能,总体外观质量符合行业标准,漆膜厚度要求如下: 序号类别涂料名称干膜厚度 (μm) 施工方法备注 1 底漆环氧富锌底漆70 喷涂 房体 2 中间漆环氧中间漆80 喷涂 3 面漆(外)氯化橡胶白色面漆50 喷涂 4 底漆(内)环氧富锌底漆40 喷涂 5 底漆环氧富锌底漆50 喷涂 顶框 6 面漆氯化橡胶蓝色面漆50 喷涂 7 黑色重防腐沥青漆150 喷涂/刷图底座 五、 涂漆前的表面处理
5.1工作环境 喷砂、丸应满足下列条件,才能进行。 5.1.1压缩空气使用前,必须先装上油、水分离器,并定期清理分离器。 5.1.2喷砂、丸前,必须调整喷嘴喷出压缩空气的压力不低于0.6MPa。 5.1.3喷砂、丸所用的石英砂、铁丸等必须干燥、干净及无污染。 5.1.4喷砂、丸前,必须用溶剂清除工件表面油污后才能进行喷砂、丸工作。 5.1.5空气相对湿度要小于85%,严禁雨天、雪天在露天进行喷砂、丸工作,工件 表面温度应高于露点温度3℃以上。 5.2 表面处理要求 5.2.1清理工序 工件表面有油污及凸起、毛刺、锐边、坡锋、焊渣等缺陷,先用溶剂油清洗油污,再用手工及动力工具将表面缺陷打磨平整,然后进行有效的 喷砂、丸处理。 5.2.2 表面喷砂、丸要求 所有需喷砂、丸工件表面,经喷砂、丸表面处理后,表面必须达到SSPC-SP10(相当于ISO Sa2?:非常彻底的喷射清理)喷砂、喷丸等 级标准,粗糙度M级,Ry50-75μm。 5.2.3手工及动力工具除锈 加工面、不需要喷砂、丸表面(电镀层、有色金属等)及油漆漆膜破损处,在涂漆前应对表面进行有效的清理,使表面达到SSPC-SP2 、 SSPC-SP3等级标准。 5.3 检查 检查表面处理后的清洁度、外观质量、表面颜色和粗糙度等。 六、 涂漆 6.1 涂漆前基本要求 6.1.1 所用的涂料的厂家、型号、批号、颜色等应符合要求。 6.1.2 对任何一组特定的油漆系统,底漆、面漆要出自同一制造厂家,以保证最 好的兼容性。必要时应遵循油漆厂家的要求。