地铁车站钢支撑轴力自动补偿施工工艺工法
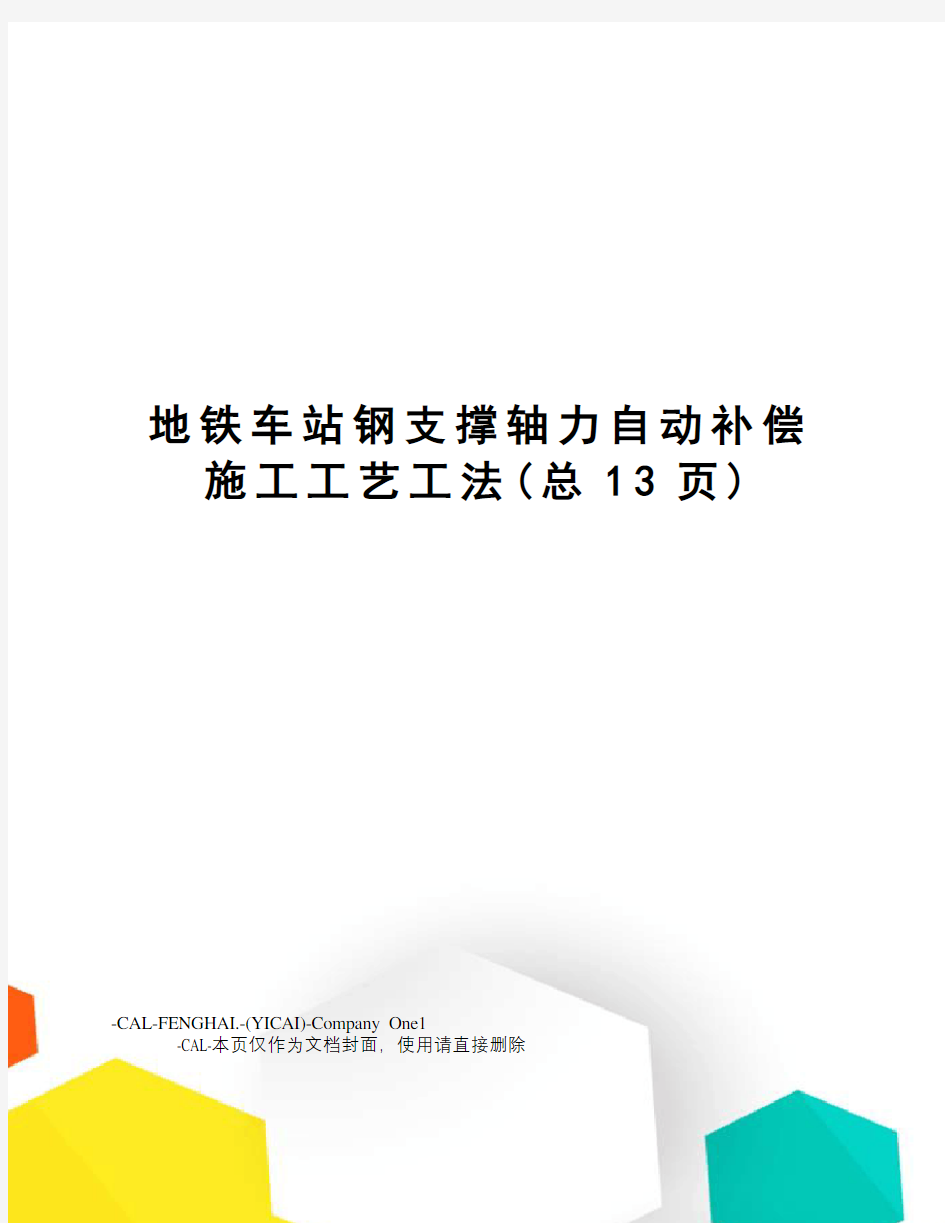
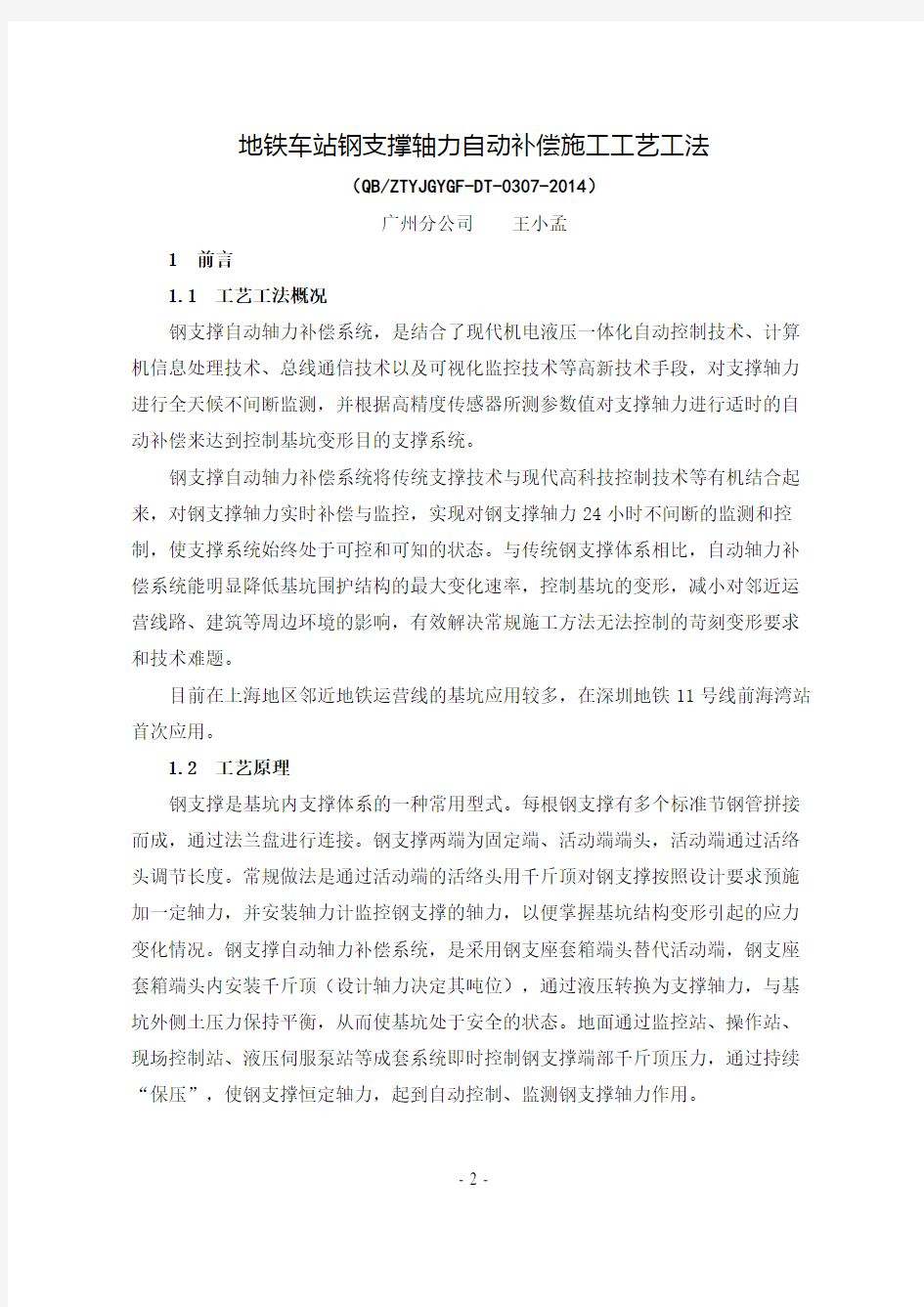
地铁车站钢支撑轴力自动补偿施工工艺工法(总13页)
-CAL-FENGHAI.-(YICAI)-Company One1
-CAL-本页仅作为文档封面,使用请直接删除
地铁车站钢支撑轴力自动补偿施工工艺工法
(QB/ZTYJGYGF-DT-0307-2014)
广州分公司王小孟
1 前言
1.1 工艺工法概况
钢支撑自动轴力补偿系统,是结合了现代机电液压一体化自动控制技术、计算机信息处理技术、总线通信技术以及可视化监控技术等高新技术手段,对支撑轴力进行全天候不间断监测,并根据高精度传感器所测参数值对支撑轴力进行适时的自动补偿来达到控制基坑变形目的支撑系统。
钢支撑自动轴力补偿系统将传统支撑技术与现代高科技控制技术等有机结合起来,对钢支撑轴力实时补偿与监控,实现对钢支撑轴力24小时不间断的监测和控制,使支撑系统始终处于可控和可知的状态。与传统钢支撑体系相比,自动轴力补偿系统能明显降低基坑围护结构的最大变化速率,控制基坑的变形,减小对邻近运营线路、建筑等周边环境的影响,有效解决常规施工方法无法控制的苛刻变形要求和技术难题。
目前在上海地区邻近地铁运营线的基坑应用较多,在深圳地铁11号线前海湾站首次应用。
1.2 工艺原理
钢支撑是基坑内支撑体系的一种常用型式。每根钢支撑有多个标准节钢管拼接而成,通过法兰盘进行连接。钢支撑两端为固定端、活动端端头,活动端通过活络头调节长度。常规做法是通过活动端的活络头用千斤顶对钢支撑按照设计要求预施加一定轴力,并安装轴力计监控钢支撑的轴力,以便掌握基坑结构变形引起的应力变化情况。钢支撑自动轴力补偿系统,是采用钢支座套箱端头替代活动端,钢支座套箱端头内安装千斤顶(设计轴力决定其吨位),通过液压转换为支撑轴力,与基坑外侧土压力保持平衡,从而使基坑处于安全的状态。地面通过监控站、操作站、现场控制站、液压伺服泵站等成套系统即时控制钢支撑端部千斤顶压力,通过持续“保压”,使钢支撑恒定轴力,起到自动控制、监测钢支撑轴力作用。
1.2.1 系统组成
系统设计采用了“树状即插分布式模块,结构、多重安保体系”的总体工艺技术路线,将机电液压自动控制技术、PLC电气自动控制技术、总线通信技术以及现代HMI人机界面智能技术和计算机数据处理技术等多项现代高科技技术有机集成起来,自动轴力补偿系统主要有以下部件组成:
监控站、操作站、现场控制站、液压伺服泵站系统、总线系统、配电系统、通信系统、移动诊断系统、组合增压千斤顶、液压站接线盒装置等组成。
1自动轴力补偿系统总体工艺设计采用树状结构,更贴近、更适合地铁边长条形基坑的结构特点,便于现场布置和使用。
2自动轴力补偿系统总体工艺设计采用模块结构,便于现场维护和使用,控制精度高。
3自动轴力补偿系统总体工艺设计采用即插分布式结构,也便于现场维护和使用,也更适合基坑边设备的布设和移动。
4自动轴力补偿系统总体工艺设计采用了多重安保体系,大大提高了系统运行的可靠性、安全性,确保深基坑开挖施工所引起的基坑变形控制效果,从而确保邻近地铁运营线、周边建(构)筑物的安全。
5由于自动轴力补偿系统设计采用了冗余设计,所以系统的工作能力强,适应能力强,可以应用在各种轴力范围、各种深度大小和各种支撑数量并要求钢支撑轴力需要实时补偿的深基坑工程中。
6自动轴力补偿系统对钢支撑轴力实时补偿的能力强、精度高、速度快,响应精度达95%以上,响应时间缩短至2秒。
7系统设计并配置了基于移动诊断技术的多功能移动诊断控制箱,在中央监控系统(监控站)或操作站或现场控制站等模块通信失效的情况下能实现故障单元的轴力自动补偿和故障诊断;在控制模块硬件故障情况下能实现故障单元的轴力手动补偿,提高了系统的应急处理能力,从而大大增加了系统的安全性和可靠性。
8现场控制站、多功能移动诊断控制箱等都采用了HMI人机界面智能控制技术,使简单,使用十分方便。
9自动轴力补偿系统采用CAN总线来实现数据采集和控制指令发送,站与站之间采用方便的接插件技术并赋以新型可靠的稳定技术,包括如①高性能的总线拓朴结构技术;②方便实用的现场接线技术;③高可靠性的触点连接技术;④总线传输波特率的计算并优化技术;⑤完善的诊断和错误恢复技术;⑥终端电阻的灵活接入或关闭技术;⑦总线成员自由增减技术,从而确保数据传输可靠、安全,同时满足了工地现场的方便使用。
10自动轴力补偿系统采用独特的钢支撑轴力支顶结构设计,千斤顶设计采用体积小重量轻便于现场安装的增压结构,设计了自动调平机构,具有自动调平功能,头部系统结构上还独特设计了机械锁+液压锁的双重安全装置,确保安全。
1.2.2 主要技术参数
主要技术参数见表1。
表1 自动轴力补偿系统主要技术参数
图1 钢支撑自动轴力补偿系统三维示意图
2 工艺工法特点
2.1取代了传统钢支撑人工预加轴力,实现了自动化“保压、加压”,并做到“可视、可控、可调”。
2.2 加强了深基坑钢支撑施工过程中控制和管理,对施工过程中的轴力监测数据等进行动态监管,有效控制了施工风险。
2.3 将动态信息与移动设备绑定,实现远程终端控制、离场操作,实现信息化管理。
2.4通过监测数据分析不同地层基坑变形规律,验证设计理论计算变形值,可预先设置轴力值大小主动控制基坑变形,实现施工指导设计。
3 适用范围
适用于各类软弱复杂地质条件下的深基坑围护结构钢支撑体系,尤其是邻近运营线或重要建(构)筑物的深基坑。
4 主要引用标准
《地铁设计规范》(GB50157-2013)
《建筑基坑支护技术规程》(JGJ120-2012)
《地下铁道工程施工及验收规范》(GB50299-1999)(2003版)
《建筑桩基技术规范》(JGJ94-2008)
《建筑工程施工现场供用电安全规范》(GB50194-2014)
《建筑地基基础设计规范》(GB50007-2011)
《建筑钢结构焊结技术规程》(JGJ81-2002)
5 施工方法
钢支撑自动轴力补偿系统施工与钢支撑架设密不可分,自动轴力补偿系统需提前3个月加工、组装,提前15d现场布置设备和线路供电系统。根据基坑形状及开挖方案,将自动轴力补偿系统的现场控制站及泵站沿基坑边缘一字排开。现场控制站及泵站的布置位置坚持线路最短原则,即现场控制站与泵站间的线路最短、泵站与千斤顶间的油管最短,并完成设备安装、单系统、总系统程序调试。钢支座套箱端头与钢支撑预先拼装,根据基坑开挖进度,架设钢支撑,并安装千斤顶,在监控站(或操作站)上按照设计轴力设定系统压力控制值(精度控制偏差±3%),完成设计预加轴力的逐级施加。同时,采集各种监测数据初始值,进行同步监测。自动轴力补偿系统开始运作,形成持续“保压”状态,开始自动控制、监测钢支撑轴力。
在基坑开挖的前30~50m长度范围,竖向每道支撑选取10~15根的钢支撑轴力监测数据,通过对施工监测、自动化监测数据分析变形规律,与设计理论计算变形值进行对比,以便调整钢支撑预加轴力,达到施工指导设计目的,动态指导现场施工,更好的控制变形。现场监测期间,如基坑或邻近运营线或重要建(构)筑物变
形突然增大时,现场值班人员在监控站(或操作站)快速调大钢支撑设计控制轴力,实现“增压”增大支撑轴力,达到即时有效控制变形。
6. 工艺流程及操作要点
6.1 工艺流程
工艺流程见图2。
图2 钢支撑自动轴力补偿系统施工工艺流程
6.2 操作要点
6.2.1 系统现场布置合理,线路最短控制
根据现场基坑形状、区段划分、开挖顺序及现场环境等综合因素,根据钢支撑设计轴力,进行钢支撑轴力自动补偿系统的负荷设计、合理性设计。
现场布置设备、供电系统线路及网络系统线路,现场控制站及泵站沿基坑边缘一字排开。现场布置控制站及泵站位置坚持线路最短原则,即现场控制站与泵站间的线路最短、泵站与千斤顶间的油管最短。
6.2.2 钢支撑及千斤顶安装
钢支撑与钢支座套箱提前在地面进行拼装,随基坑开挖及时架设,将千斤顶吊装至钢支座套箱内,就位居中,与泵站的液压油管连接,按设计施加预加轴力。
6.2.3 实时监控
监控站安排专人进行全天值班,监控系统24小时开机,对钢支撑轴力进行实时监控并整理日报。必要时根据基坑施工监测、邻近运营线或重要建构筑物的自动化监测数据重新调整钢支撑轴力,达到快速控制变形目的。
6.2.4 设备校核及标定
根据基坑开挖及钢支撑倒用周期,千斤顶标定不超过6个月一次;液压伺服泵站、现场控制站、操作站按每移动一次进行一次调试,监控站按3个月检查一次;加强日常巡检,对网络线路、用电线路、液压油管等破损及时更换,确保系统运行期间完好。
7 劳动力组织
劳动力组织见表2。
表2 劳动力组织表
8 主要机具设备
主要机具设备见表3。
表3 主要机具设备配置表
9 质量控制
9.1 易出现的质量问题
9.1.1 钢支撑、围檩加工质量不达标,影响系统使用。
9.1.2 钢支撑拼装不平直,钢围檩背后回填不密实,影响自动轴力补偿系统保压。
9.1.3 车站盖挖逆作工况下,钢支撑安装和自动轴力补偿系统千斤顶安拆存在难度,需要机械配合。
9.1.4 现场施工监测主要靠人工量测、整理数据,需要一定时间;而自动轴力补偿系统快速调取钢支撑“即时轴力值”。施工监测与自动轴力补偿系统监测的钢支撑轴力难以同步,不易实现“实时”控制基坑及邻近运营线或重要建(构)筑物的变形。
9.2 保证措施
9.2.1 钢支撑拼装不平直,误差较大:加强钢支撑加工质量控制,进场验收必须严格,进行焊接探伤、壁厚等指标检验检测,不合格的必须退场。钢围檩连接部位焊接不牢固,特别是阴阳角部位焊接质量不达标现象较多,加强现场管制作、安装、焊接过程管理和检查验收。
9.2.2 钢支撑提前试拼检查,连接时必须对称上高强螺栓,按顺序紧固,拼装成型的支撑是否平直,检查轴线偏差≤3cm,不平直(或存在变形)的要禁止使用。
现场安装时,两端安装标高≤3cm。加强现场控制钢围檩背后回填,确保砼密实,严禁喷砼的干拌料、回填料,不得回填其他杂物。
9.2.3盖挖逆作板下进行钢支撑和自动轴力补偿系统千斤顶的安装、拆除,操作空间受限,无法采用单根整体吊装,需要在板下分段拼装,根据跨度、高度提前做好分段试拼;钢支撑和千斤顶安装选用合适的挖掘机进行,拆除采用叉车。
9.2.4钢支撑自动轴力补偿系统不仅实现“保压”,根据基坑及邻近建筑物变形来快速增加轴力,达到控制变形的作用。现场条件受限仅邻近运营线或重要建(构)筑物采用自动化监测,基坑施工测斜等监测主要靠人工,监测数据不及时,应根据邻近运营线或重要建(构)筑物自动化监测数据,快速“调压”增大轴力,有效控制基坑及邻近运营线或重要建(构)筑物的变形。
10 安全措施
10.1 主要安全风险分析
10.1.1 钢支撑架设不及时,导致基坑围护结构严重变形甚至失稳,危及邻近运营线或重要建(构)筑物的变形。
10.1.2 安装不牢固,造成支撑脱落。
10.1.3 基坑施工监测数据不及时,基坑施工监测、邻近运营线或重要建(构)筑物自动化监测信息不畅通,对基坑安全状态及钢支撑轴力掌握不及时。
10.1.4 钢支撑拼装、千斤顶安装作业不规范,容易造成物体打击事故。
10.2 保证措施
10.2.1 加强现场管理与协调,配合盖挖土方开挖,及时架撑、按照千斤顶,保证钢围檩背后回填质量。
10.2.2 对施工人员加强安全施工的教育,定期进行专业安全检查,进入施工现场人员一律戴安全帽。
10.2.3 钢支撑加工前由负责加工的工长对加工机械的安全操作规程及注意事项进行交底,并由机械工程师对所有机械性能进行检查,合格后方可使用。
10.2.4 钢支撑在运输过程中要注意交通安全,运输车尾应设置警示灯等安全设备。
10.2.5 在安装牛腿支架、钢围檩时一定要注意在基坑顶部设防护栏,并同时安排专人将边坡上部将杂物清理干净,防止坠物伤人。
10.2.6 支撑、千斤顶吊装时其吊车下方及支撑回转半径内严禁站人,高空作业要系安全带。由于钢支撑跨度较大,活荷载对其影响较大,易使支撑因震动而失稳,所以严禁在其上放置各种物体及人员攀登和行走。
10.2.7 土方开挖时避免挖掘机碰撞已经架设的钢支撑,钢支撑采用钢丝绳防坠落,钢围檩采用角钢托架防坠落。
10.2.8 控制钢支撑安装过程中的轴线、标高安装偏差,千斤顶安放居中,钢围檩侧面垂直。
10.2.9 加强与基坑施工监测、邻近运营线或重要建(构)筑物自动化监测信息之间的联系,及时根据监测数据,“调压”增大轴力,控制变形。
11 环保措施
11.1 钢支撑及自动轴力补偿系统作业对环境造成不良影响的因素
钢支撑、钢围檩、钢支座套箱加工,钢支撑运输、拼装、吊装和自动轴力补偿系统运输、安装、调试、投入使用等,对周边环境照成了一定的影响,影响因素主要为:
11.1.1钢支撑、钢围檩、钢支座套箱加工造成的光污染。
11.1.2钢支撑、千斤顶架设时造成的噪音污染。
11.1.3液压泵站、千斤顶、液压油管破损造成的漏油水污染。
11.2 采取措施
11.2.1 起重吊装作业尽量减少噪音,可以安装消音装置。拼装过程,轻吊轻放,减少噪音。
11.2.2 电焊作业必须配备齐全的劳保用品。
1 切割焊接等作业,施工完成后,每天做到工完料清,及时打扫焊渣并清理。
2 严禁在晚上进行焊接作业,如确有必要时吗,必须搭建遮光棚,防止造成光污染。
3 对余料、废料同意堆放管理,增强节能减排意识。
4 加工的成品半成品应分类堆放整齐。采用标识标牌进行标识。
5 现场做好文明施工和安全用电。
12 应用实例
12.1 工程简介
深圳地铁11号线为机场快线,接驳深圳宝安机场T3新航站楼。采用BT模式,前海湾站位于与香港隔海相望的深圳前海深港合作区,原始地貌为滨海滩涂,现状为填海区,该区域存在为普遍分布不规则的填石和较厚的流塑状、软塑状淤泥等软弱不良地层。前海湾站与已建1、5号线及后建的前海综合交通枢纽工程穗莞深城际
线、深港西部快线将形成“三条地铁+两条轻轨”的平行大换乘。车站为地下三层两柱三跨岛式车站,长830m,标准宽25.7m,深18.1m,建筑面积7.8万平米,工程造价11.79亿元,规模相当于三~四个标准地铁车站,是国内最长的在建地铁车站。由于车站所处填海区地层复杂,东侧且距已运营5号线地铁车站平行最小净距仅有
9.1m,故主要采用盖挖逆作法,仅南端110m采用明挖顺作法。
车站东侧围护桩设计为φ1200@1300+φ900三管旋喷桩止水及帷幕,西侧围护桩设计为φ1500@1600+φ900三管旋喷桩止水及帷幕,底板下方沿车站纵向设置四排抗拔桩。车站南端110m采用明挖顺筑法进行施工,共设置4道支撑体系,其中第一道为钢筋混凝土支撑,第二~四道为φ600钢支撑,在施工结构底板时需进行一次换撑,支撑间距平均为3m。北端720m采用盖挖逆筑法进行施工,在车站第二道钢支撑(负一层板上方1m)、第二道钢支撑(负二层底板上方2m)带自动轴力补偿系统,共354根钢支撑。
12.2 施工情况
前海湾车站盖挖段长720m,根据设计支撑数量和工期安排,共加工3套自动轴力补偿系统(一套系统控制72根钢支撑),系统调试完毕,运至现场车站顶板上方,将现场控制站及泵站沿基坑边缘一字排开布置,板上采用集装箱设两个监控站,24小时值班作业。钢支撑拼装、钢围檩及钢支座套箱加工均在现场提前加工。盖挖土方开挖至钢支撑下0.5m,再进行桩间网喷的同时,立即安排施工人员,进行打眼植入膨胀螺栓安装角钢托架,安装钢围檩,并进行背后回填。钢支撑分三节在板下拼装,采用PC120型挖掘机配合架设,吊装千斤顶,连接液压油管,按照设计分级施加轴力。自动轴力补偿系统开始运作,形成持续保压,开始自动控制、监测钢支撑轴力,有效控制基坑变形。运营线(五号线)自动化监测情况见表4。
表4 运营线(五号线)自动化监测区间统计表
运营线水平变形和沉降变形均在设计要求的10mm以内,确保了邻近运营线的运营安全。
12.3 工程结果评价
自动轴力补偿系统装置钢支撑对深基坑施工的变形控制真正实现了动态、实时及24小时不间断的监测与控制。在前海片区如此复杂的地质条件下,而又有邻近的地铁运营线,对基坑变形和沉降要求极其苛刻的情况下,彻底避免钢支撑轴力衰减而引起的围护结构的位移变形,从而有效控制基坑结构的位移变形,确保了基坑开挖安全。同时,有效控制了相邻运营线的沉降和变形,保证运营线的安全运营。
12.4 建设效果及施工图片
图3 钢支撑自动轴力补偿系统图片
地铁站钢支撑轴力计算新
地铁站钢支撑轴力计算 新 Document serial number【NL89WT-NY98YT-NC8CB-NNUUT-NUT108】
地铁站钢支撑轴力计算书 庆丰路站: 根据基坑施工方案图,考虑基坑两头45度处单根米最长的钢支撑 和对基坑垂直的钢支撑单根米最长的钢支撑进行受力分析计算,已 知单根钢支撑承受的最大轴心垂直压力设计值为1906KN,考虑基坑两头45度支撑处钢支撑所承受的轴向力N=1906√2=2695KN。 钢材为:Q235-B型钢。取的安全系数。 一、单头活动端处受力计算: 由单头活动端结构受力图可知,受力面积最小的截面为A-A处截面。查表得,单根槽钢28c的几何特性为: 截面面积A= cm2, Ix=268cm^4, Iy= 5500cm^4。 该截面f取205N/mm2,截面属于b类截面。 (一)、受力截面几何特性 截面积:A=×2+4×30= cm2 截面惯性矩: Ix=2×268+30×43/6=856 cm^4 Iy=2×5500+4×303/6=29000 cm^4 回转半径: ix=√Ix/A=√856/= iy=√Iy/A=√29000/= (二)、截面验算 1.强度
σ=A=(×2695×103)/(×102)=mm2 临地铁深基坑综合施工技术的研究 顾小强、台登红、曾海霞、王诚、刘建明 (中建三局第三建设工程有限责任公司,上海,200333) 摘要:本工程地处上海市中心,紧邻地铁8号线,与地铁最近水平距离为9.6m。作为城市综合体,设置三层地下室,基坑总占地面积超过一万平米,建成后是该地段的商业核心,充分发挥了地铁带来的人员流动优势,是一个非常典型的城市工程。伴随着轨道交通的发展,在未来一很长一个时期内,在地铁边的城市综合体工程,地铁边的深基坑工程将是建筑市场上的竞争重点。在地铁沿线的深基坑施工经验,在深基坑施工工程中的地铁保护经验将是抢占地铁沿线建筑市场的核心竞争力。 关键词:邻近地铁,深基坑,自动轴力补偿系统 1、临地铁深基坑综合施工技术的研究现状 1.1国内基本情况 伴随着我国经济的高速发展,城镇化建设的日益推进势头,我国城市轨道交通建设也一并跨入了高速发展的阶段。“十二五”规划中,对城市轨道交通的发展预期目标是不久的将来,我国将成为世界上城市轨道交通里程最多的国家。因而目前在城市建筑施工工程中进行邻地铁深基坑的施工,既能确保地铁运营安全有序,又要保证深基坑施工的正常进行,将成为未来一阶段建筑施工中的重点课题。 1.2未来发展趋势 目前国内一线城市,特别是北京、上海,已经建成了较为完备的城市轨道交通系统,在轨道交通沿线已经有大量建成,在建的工程项目,且项目多为城市综合体,基坑较深,基坑较大,在这些工程的施工过程中也积累了大量的工程施工经验和地铁隧道保护经验,为后续的类似工程打下了一定的基础,也促进了地铁沿线工程施工的管理要求和地铁保护标准的提高。但是在这些工程的施工过程中也多多少少的出现了一些问题,获得了一些教训,也正因此需要我们进一步的加强地铁深基坑综合施工技术的研究,进一步完善地铁沿线深基坑施工的保护要求和标准,进一步提高地铁沿线深基坑施工的施工和管理水平。 2、项目概况 2.1项目概况 上海大悦城一期西北地块商业项目地处西藏北路海宁路交界处,占地面积12898㎡,总建筑面积为98500㎡,其中地下建筑面积约3万㎡,地上建筑面积约6.5万㎡。建设工程性质为集商业、餐饮休闲用房为一体的商业综合开发项目。 围护结构钢支撑施工工艺工法 1前言 工艺工法概况 钢支撑是明挖结构内支撑体系重要组成部分,每根钢支撑有多个短节钢管拼接而成,通过法兰盘进行连接,钢支撑一头安放在钢围檩的托板上,另一头通过活络头安装在对面的一侧,通过活络头用千斤顶对钢支撑按照设计要求预施加一个轴力,并对该轴力实行监控,以便掌握结构变形情况。在结构拐角处由于距离比较小,不适合架设钢支撑,可以用型钢焊接成短节的型钢支撑作为支撑体系。工艺原理 钢支撑是支撑体系的一种形式。目前较为广泛的应用于地下工程,特别是深基坑开挖工程中最为常见,它主要是将基坑一侧土压力通过钢支撑的作用,传递到另一侧,与另一侧的土压力保持平衡,从而使基坑处于安全的状态,钢支撑轴力的变化能间接的反应出基坑两侧土压力变化情况,因此可以通过对钢支撑轴力监测,正确的指导安全施工。 基坑在开挖过程中,随着深度的增大,两侧土压力也随之增大,土压力通过力的传递到围护结构上,向基坑内侧侵斜,采用刚性的型钢对撑之后,将基坑两侧的土压力很好的平衡。以达到预期效果。 2工艺工法特点 钢支撑施工简单,适用性强,操作方便,时效性强,可周转重复使用。 3适用范围 主要使用在地下工程、深基坑工程。 4主要引用标准 《地铁设计规范》(GB50157) 《建筑基坑工程技术规范》(YB9258) 《建筑基坑支护技术规程》(JGJ120) 《地下铁道工程施工及验收规范》(GB50299) 《建筑桩基技术规范》(JGJ94) 《建筑工程施工现场供用电安全规范》(BG50104) 《建筑地基基础设计规范》(GB50007) 《建筑钢结构焊结技术规程》(JGJ81) 5施工方法 钢支撑架设与基坑土方开挖是深基坑施工密不可分的两道关键工序,支撑架设极具时间性和协调性,支撑架设的方法、时间、位置及预加力的大小直接关系到深基坑稳定的成败。支撑架设必须严格满足设计工况要求。 钢支撑拼装过程 钢支撑在拼装时保证支撑接头的承载力符合设计要求。钢支撑连接时必须对称上螺栓,按顺序紧固。要有钢支撑支托措施,防止坠落。 钢支撑安装前一定要检查钢管的平直度,若不平直要进行矫正。 钢支撑架设方法 每节段分层开挖至钢支撑架设的高度后,立即放出支撑位置线及标高线。 第一道钢支撑架设在冠梁预埋钢板上,其它各层钢支撑安装钢围檩支架牛腿后,安装加工好的钢围檩,钢支撑两端的钢围檩应保持同一水平位置。 将焊接好的三角形钢支架在钢支撑中心位置与钢围檩相焊接,并与其背后的抗剪加强肋板相焊接。 将厂家制作的单根支撑钢管与活接头采用高强螺栓进行现场连接,组装成为成型的单根钢支撑。 用2台25t汽车吊或1台50t履带吊(或龙门吊)吊放钢支撑到钢支座上,并使活动端较宽位置支撑于围护桩上。 钢支撑的长度由现场实际长度确定。微调采用特制钢楔,完成钢支撑组装的各种工作。 为防止钢支撑在施加轴力时由于自重产生过大的挠度,在对钢支撑施加预应力时汽车吊(或龙门吊)吊装钢丝绳必须持力,不得放松。 在钢支撑支架处焊接防坠钢板,完成施加预应力前的各种准备。 钢支撑及轴力自动补偿系统 施 工 方 案 上海竖河建设工程有限公司 2018年3月10日 目录 1. 工程概况 (3) 1.1 工程概述 (3) 1.2 参建单位 (3) 1.3 方针目标 (3) 1.3.1 方针目标 (3) 1.3.2 目标实现措施 (3) 2. 编制依据 (4) 3. 施工准备及平面布置 (4) 3.1 施工准备 (4) 3.2 施工平面布置 (5) 4. 施工方案 (5) 4.1 钢支撑工程概况 (5) 4.2 轴力自补偿系统(智能自动节)介绍 (6) 4.2.1 智能自动节系统总体架构 (6) 4.2.2系统主要特点 (6) 4.2.3系统主要功能 (6) 4.2.4系统主要组成 (6) 4.3 ф609钢管节点构造 (8) 4.4 钢支撑拼接 (8) 4.5 安装总要求 (9) 4.6 主体支撑安装方法 (9) 4.6.1 施工流程 (9) 4.6.2 安装方法 (10) 4.7 支撑拆除 (13) 4.8 检验批抽检计划 (14) 4.9 相关单位协调配合 (15) 5. 钢支撑施工工期 (15) 5.1施工进度计划及进度保证措施 (15) 5.2工期保证措施 (15) 6. 质量保证措施 (16) 6.1 钢支撑施工质量保证具体措施 (16) 6.2 钢支撑安装允许偏差 (17) 7、安全生产管理措施 (17) 7.1 安全保证体系 (17) 7.2安全保证措施 (17) 8. 文明施工措施 (22) 8.1文明施工管理网络 (22) 8.2文明施工措施 (22) 9. 主要设备(机械、仪器)配置计划 (25) 10. 施工管理人员配备及项目组织架构 (26) 11. 劳动力配备计划 (26) 12. 地下管线保护 (26) 13. 应急预案 (27) 14.信息管理 (27) 14.1 电子档案信息管理 (27) 14.2工程档案及资料管理 (28) 地铁车站钢支撑轴力自动补偿施工工艺工法 (QB/ZTYJGYGF-DT-0307-2014) 广州分公司王小孟 1 前言 1.1 工艺工法概况 钢支撑自动轴力补偿系统,是结合了现代机电液压一体化自动控制技术、计算机信息处理技术、总线通信技术以及可视化监控技术等高新技术手段,对支撑轴力进行全天候不间断监测,并根据高精度传感器所测参数值对支撑轴力进行适时的自动补偿来达到控制基坑变形目的支撑系统。 钢支撑自动轴力补偿系统将传统支撑技术与现代高科技控制技术等有机结合起来,对钢支撑轴力实时补偿与监控,实现对钢支撑轴力24小时不间断的监测和控制,使支撑系统始终处于可控和可知的状态。与传统钢支撑体系相比,自动轴力补偿系统能明显降低基坑围护结构的最大变化速率,控制基坑的变形,减小对邻近运营线路、建筑等周边环境的影响,有效解决常规施工方法无法控制的苛刻变形要求和技术难题。 目前在上海地区邻近地铁运营线的基坑应用较多,在深圳地铁11号线前海湾站首次应用。 1.2 工艺原理 钢支撑是基坑内支撑体系的一种常用型式。每根钢支撑有多个标准节钢管拼接而成,通过法兰盘进行连接。钢支撑两端为固定端、活动端端头,活动端通过活络头调节长度。常规做法是通过活动端的活络头用千斤顶对钢支撑按照设计要求预施加一定轴力,并安装轴力计监控钢支撑的轴力,以便掌握基坑结构变形引起的应力变化情况。钢支撑自动轴力补偿系统,是采用钢支座套箱端头替代活动端,钢支座套箱端头内安装千斤顶(设计轴力决定其吨位),通过液压转换为支撑轴力,与基坑外侧土压力保持平衡,从而使基坑处于安全的状态。地面通过监控站、操作站、现场控制站、液压伺服泵站等成套系统即时控制钢支撑端部千斤顶压力,通过持续“保压”,使钢支撑恒定轴力,起到自动控制、监测钢支撑轴力作用。 1.2.1 系统组成 地铁站钢支撑轴力计算书 庆丰路站: 根据基坑施工方案图,考虑基坑两头45度处单根14.5米最长的钢支撑和对基坑垂直的钢支撑单根23.2米最长的钢支撑进行受力分析计算,已知单根钢支撑承受的最大轴心垂直压力设计值为1906KN,考虑基坑两头45度支撑处钢支撑所承受的轴向力N=1906√2=2695KN。 钢材为:Q235-B型钢。取1.2的安全系数。 一、单头活动端处受力计算: 由单头活动端结构受力图可知,受力面积最小的截面为A-A处截面。 查表得,单根槽钢28c的几何特性为: 截面面积A=51.234 cm2, Ix=268cm^4, Iy= 5500cm^4。 该截面f取205N/mm2,截面属于b类截面。 (一)、受力截面几何特性 截面积:A=51.234×2+4×30=222.5 cm2 截面惯性矩: Ix=2×268+30×43/6=856 cm^4 Iy=2×5500+4×303/6=29000 cm^4 回转半径: ix=√Ix/A=√856/222.5=1.96cm iy=√Iy/A=√29000/222.5=11.42cm (二)、截面验算 1.强度 σ=1.2N/A=(1.2×2695×103)/(222.5×102) =145.4N/mm2 1.2N/φA=(1.2×2695×103)/(0.791×22 2.5×10 2)=183.7N/mm2 目录 1.富水饱和软黄土地质条件下WSS全断面深孔注浆施工工艺工法 (3) 2.钢套筒密闭始发接收施工工艺工法 (14) 3.地铁盖挖逆作结构板下顺筑侧墙单侧悬臂液压模板台车施工工艺工法 (40) 4.地铁车站钢支撑轴力自动补偿施工工艺工法 (53) 5.城轨工程运输调度指挥管理系统工艺工法 (66) 6.“距安宝”新技术 (82) 7.二次衬砌定型组合钢端模施工工艺工法 (93) 8.水沟电缆槽门式移动台车施工工艺工法 (100) 9.隧道衬砌拱顶带模注浆施工工艺工法 (108) 10.隧道衬砌分层逐窗浇筑混凝土施工工艺工法 (119) 11.隧道防水板电磁法焊接施工工艺工法 (129) 12.隧道水压爆破施工工艺工法 (138) 13.仰拱弧形模板与定型组合端模施工工艺工法 (149) 14.变频、低能耗高效隧道通风系统 (157) 富水饱和软黄土地质条件下WSS全断面深孔注浆施工工艺工法 1 前言 “WSS”是无收缩双液注浆的缩写,该技术源自日本,在世界范围内工程施工领域应用比较广泛。WSS全断面深孔注浆工法是在暗挖隧道轮廓线以内,按照一定的布孔间距要求,采用二重管钻机钻孔至预定深度后,使用一台同步注浆机后退注浆,对隧道进行超前预注浆加固,最后进行暗挖隧道掘进的一种施工工法。 西安地铁四号线火车站站一期暗挖工程下穿西安火车站既有国铁站场,暗挖施工对站场内地表既有线路、道岔的沉降要求为-15mm~0mm,施工需通过超前预注浆达到控制地表沉降、不影响国铁既有线路运营安全的目的,施工难度高,施工风险极大。 项目部通过四循环WSS全断面注浆试验确立了适合富水饱和软黄土地层条件下的各项施工原则、注浆参数。目前,对同类地层条件下全断面注浆施工的加固、止水效果明显,可以有效控制地表变形。 2 工法特点 2.0.1 钻孔、注浆工序连续,相互转换灵活。 2.0.2 设备小巧,适用于暗挖隧道空间狭小的施工环境。 2.0.3 浆液凝结时间可人工调整,复合注入,浆液对土层有很强的渗透性。 3 适用范围 该工法主要适用于地铁暗挖隧道、山岭隧道、沉降控制标准高的黄土地层。 4 工艺原理 WSS全断面深孔注浆工法是按照一定孔位间距要求,通过二重管钻机钻孔至预定深度后,使用一台同步注浆机后退注浆,对隧道进行超前预注浆加固。在不改变地层组成的情况下,达到加固围岩、降低地层透水性的作用,最后进行暗挖隧道掘进的一种施工工法。该工法能有效发挥设备在狭小工作空间环境中,各类土层地质条件下预加固目的,保证了特殊、复杂围岩条件下暗挖隧道施工的周边环境和人员安全。 5 工艺流程及操作要点 5.1 施工流程 暗挖隧道台阶法施工条件下全断面WSS深孔注浆对于注浆孔位的分布、注浆先后顺序的安排、注浆参数的确定都有严格要求,具体流程如图5.1。 深基坑钢支撑轴力作用指导书 随着城市建设的迅猛发展,城市中心深基坑工程也越来越多,深基坑支护体系的结构计算和现场测试信息化施工也显示出其重要的意义。钢支撑轴力监测则是反映支撑结构计算成果与施工工况的差距是否合理。同时也是深基坑开挖施工过程中预警的一个最直观的方法。 测量目的: 基坑围护支撑体系处于动态平衡之中,随着基坑施工工况的变化建立新的平衡。通过支撑轴力监测,可及时了解钢支撑受力及其变化情况,准确判断基坑围护支撑体系稳定情况和安全性,以指导基坑施工程序、方法,确保基坑施工安全。 测量原理: 通过设置在仪器内部的振弦,感知仪器轴向应变,通过其自身频率的变化反映出来的,他们之间的差别主要就是在于安装及费用方面。 观测方法: 使用FX-180型多功能读数仪进行测量,一般情况下轴力计的电缆线分为红色和黑色,先打开读数仪,将仪器模式切切换到F模式下,测量时将读数仪的鳄鱼夹红色的夹子夹到轴力计红色的电缆线上,黑色的夹子夹到黑色的电缆线上,读取读数仪显示屏上F值并做好记录。计算方法: 将现场记录的数据检查时间、观测员、记录员是否准确、清晰。在将 检查合格的数据输入电脑,计算出刚支撑的受力p,计算公式如下: P=K(f02-fi2) P:应力(单位KN); f0:初始频率; fi:本次频率; k:标定系数; 将计算出的受力整理成表、画出曲线图。做好分析报告,上报有关单位。 报警应急措施: 支撑轴力计是随基坑开挖围护结构变形或位移直接影响支撑受力的。当支撑受力达到报警时,分析报警的原因及因素,做好书面报告。及时通知各有关单位,特别是施工单位,采取相应措施,以保证基坑的安全性和稳定性。 注意事项: 装有轴力计的基坑一般为深基坑,在观测时必须做好安全三宝(安全帽、安全绳、安全网),雨天观测注意仪器的保护。我们使用的仪器都是电子仪器,雷雨天最好别进行观测,以防雷击。 钢支撑架设技术要求 一、钢支撑场外组装 钢支撑在运送到场后,根据基坑开挖宽度尺寸和钢支撑长度进行选材配节,拼装成完全能吊装的单根成型钢支撑。预拼装完毕后,需按设计文件允许值要求检查钢支撑轴线偏差。 二、三角托架施工 按照设计要求的材料及尺寸制作三角托架,焊好后的钢三角托架应保证两直角边相互垂直,焊接牢靠,并有足够的稳定性,不得出现歪扭、虚焊现象。 每层土方开挖至指定标高后,测量放出三角托架轴线位置及标高,按设计间距、设计标高在围护结构上安装三角支撑,安装完毕后应检查相邻三角托架之间是否在同一水平面及标高。 膨胀螺栓钻孔后,应检查孔内是否存在地下水,若有地下水,应及时除水处理。 三、钢围檩施工 钢围檩一般采用双拼工字钢。分段加工,一般分段长度取2~3个支撑间距,同时确保每根钢支撑安装位置避开钢 围檩与钢围檩接缝。转角部位应根据实际长度加工。 钢围檩随支撑架设顺序逐段吊装,人工配合吊机将钢 围檩安放于钢三角托架上,并及时按设计要求安装防脱落装置。钢围檩安装后应检查钢三角托架是否因撞击而松动。钢围檩就位后,应检查与钢支撑接触面垂直度是否满足设计要求。若有设计要求,需在检查无误后在钢围檩与围护结构之间空隙填嵌设计填充物,一般为细石混凝土。本段钢围檩上的钢支撑预应力施加完毕后,应及时与上段钢围檩三面焊接,接成连续梁,避免出现悬臂现象。每段钢围檩接缝处,安装平面位置和高程位置应一致,不允许出现错台等现象。每层钢围檩须设置抗剪凳,,抗剪凳位置应与实际护披桩位置相 对应,凿出护披桩保护层内钢筯,与抗剪凳钢板相焊接,焊接长度应与钢板长度相对应。 三面焊接 四、钢支撑架设 采用吊车将在基坑外预拼装完毕的钢支撑吊入安装位置,吊装过程应严格按照起重吊装规范施工。 将钢支撑吊装就位在固定于钢围檩上的挂板处,安装必须保证钢支撑端头与围檩或预埋钢板密贴,钢支撑就位后应初步固定活络头。若施工场地及操作空间允许,应初步施加预应力后,再解开吊装钢丝绳。钢支撑安装完成后,为了防止钢支撑因轴力变化而产生不稳定现象,可利用钢丝绳和U 型卡拴住钢支撑两端头,并将钢丝绳一端采用膨胀螺栓固定在围护结构上,防止支撑掉落或倾覆。 背后填充 生命绳 钢支撑防脱落 钢围檩防脱落 五、施加预应力 钢支撑安装就位并复核位置、水平合格后,根据设计预加轴力确定千斤顶,预应力施工前,必须对油泵及千斤顶进行标定,并出具有效的标定报告。 钢支撑轴力施加分三次进行,支撑第一次施加设计轴力的40%,第二次施加设计轴力的70%,第三次施加设计轴力的100%。支撑的第一、二次加压完成后保持压力不小于3min,第三次加压完成后保持压力不小于5min,稳定后采用45号铸钢制作的楔块楔牢锁定,并设置插销。锁定后进行观察,3分钟无明显回压,保证轴力锁定及稳压情况符合设计及规 DZB3600S钢支撑轴力智能补偿系统 随着我国地下工程的高速发展,基坑开挖过程中安全问题也被越来越多的关注。基坑支护的轴力监测问题在许多国家基础建设中都存在,并得到高度重视,日本、德国、英国、新西兰等国家很早就在这方面开展了相关工作,并取得了一定的进展。钢支撑在我国使用以来,多次出现重大安全事故,给施工单位、业主的资产造成严重损坏和伤亡等问题。 DZB3600S钢支撑轴力智能补偿系统是徐州盾安重工机械制造有限公司研制的最新基坑支护轴力实时监测、补偿系统,由补偿节、泵站、控制柜及软件系统共同组成的一套完整的基坑支护、实时监测装置。 轴力实时补偿对应土体压变化,极大的减少基坑位移的影响,系统通过各单元元件冗余进行原件的故障进行控制,降低了因系统故障而影响整体安全的事故因素。通过自主设计的随动自锁油缸,保证在系统全部瘫痪的前题下依然能保证基坑不会失稳。通过集成通信模块对系统数据进行压缩传输到网络,使整个系统信息实现实时传输与远程控制功能,降低了施工成本与数据传输的滞后性,让施工更准确更轻松更安全。 系统特点及功能:输出液压管路排线式布置,外型紧凑美观,集成度高;三组液压系统相互独立运行,每组液压系统可独立控制8根补偿节,输出推力可根据需要实时调节并进行监控;三组液压系统相互间顺序监控,如某一路的压力源出现故障(如电机或是泵出现故障,无法打出压力油),故障自动诊断系统会自行识别,并在极短的时间内切换到旁边的液压系统供油,以保证系统安全运行。 表一:钢支撑轴力智能补偿系统主要技术参数 二、DZB3600S钢支撑轴力智能补偿系统简介 1、钢支撑轴力智能补偿系统的构成 钢支撑轴力智能补偿系统由动力系统、补偿系统、控制系统组成的成套基坑支撑压力自动补偿装置,可以在无人值守情况下全天候实现稳定可靠的自动补偿运作,保证补偿系统的压力自动维持在设定的范围内。一个控制中心(控制柜)同时控制3套液压动力站,1套液压动力站同时控制8个补偿油缸(即补偿节,对应8个钢支撑),一套钢支撑轴力智能补偿系统可同时实现对24个钢支撑轴向力的自动补偿控制(见图一),具有响应速度快,控制精度高等一系列优点。 图一钢支撑轴力智能补偿系统构成分配图 2、适用范围 钢支撑轴力智能补偿系统适用于周围环境变形敏感、基坑围护变形控制要求较高的深基坑工程。广泛应用于地下连续墙工程,特别是针对地铁沿线、高层建筑周边的基坑支护,由于其特殊的地理位置,为了确保工程施工不影响到地铁隧道、周边建筑物的安全,有效控制地面沉降,严格控制基坑围护结构变形等情况。 3、动力系统的特点及功能 动力系统有电源系统和液压体统两部分组成: 1)液压系统 1.3.2 工程重点及主要对策 1.3. 2.1车站基坑开挖确保安全的技术措施及应对暴雨、台风、汛期的安全措施是工程重点 (1)车站基坑开挖确保安全的技术措施是工程重点 本标段地处太湖平原地带,车站基坑深度较深,地下水埋深较浅,工程地质水文条件较为复杂,有特殊土和不良地质,地下水丰富。车站基坑开挖确保安全是工程重点。 ①软土地区深基坑开挖围护施工应注意的问题 基坑支护工程既要保证整个支护结构在施工过程中的安全,又要控制结构和周围土体的变形,以保证周围环境(相邻建筑物和地下公共设施等) 的安全。因此,如何确保基坑工程的安全可靠、经济合理、实用可行是一重要和迫切的问题。本车站在基坑施工过程中应注意以下问题: A、基坑开挖深度较大,且土质软弱,主动土压力较大,而被动土压力较小,悬壁墙承 受较大弯矩,应根据开挖进展情况及时采取内支撑方案。 B、基坑开挖范围内的软土,必须分层均衡开挖,层高不超过1m。 C、基坑开挖到坑底标高后应及时封闭并进行基础施工,由于基坑底部以软弱粘性土为 主,基坑开挖过程中应尽量减少对坑底原状土的扰动。 D、基坑周边避免堆载渣土及原材料等,对交通车辆采取适当的隔离措施。 E、在支护系统设计中,支护状态的动态监测与控制,是一个不容忽视的重要环节。挖 土过程中如出现土体较大位移,应立即停止挖土,分析原因。 F、坑周围的地表水应及时排除,及时发现周边水管的破裂渗漏事故,并采取相应措施。 严禁地表水或基坑排除的水倒流回渗入基坑。 G、深基坑开挖后土体会有一定的回弹,同时由于坑底土的回弹,会对基坑支护结构、 周围邻近已有建筑物、地下管线等产生不利影响 H、基坑开挖时应加强对基坑位移、周边建筑物及构筑物(如地下管线等)监测,以保证基 坑的正常施工及对临近建(构)筑物不致产生过大的影响。监测项目应包括边坡土体顶部的水平位移,边坡土体顶部的垂直位移,围护结构的水平位移,围护结构的垂直位移,基坑周围地表沉降及地表裂缝,围护结构的裂缝,内支撑的应力和轴力,地下水位,周围建(构) 筑物的沉降人裂缝,周围重要设施(包括市政管线)的变位与破损,基坑周围地面超载状况,基坑渗、漏水状况等。 明挖基坑的工艺标准是否严格、失水控制是否有效、变形控制是否及时等诸多因素是保证明挖结构施工安全的技术核心。 ②基坑开挖对策: A、保证围护结构质量 认真做好围护结构施工,特别是连续墙施工精度、质量控制和防水混凝土浇捣,保证围护结构不漏水。 B、及时施加支撑(含封闭基坑底板) 能非常有效地调整地层的应力状态,控制基坑施工过程中的地层、围护结构及相临建筑物的变形。因此在施工中采用加快挖基速度,同时做到在最短的时间及时施加支撑和封闭基坑底板。 C、认真做好基坑工程施工过程中地下水的处理 在基坑工程施工过程中对地下水的处理以封堵、降排为主,施工内衬前对基坑内侧渗水点进行封堵。基坑采用自流渗井降水,基坑周边设臵排水沟和集水井,自流渗井降水每次降深控制在开挖基面以下0.5m。基坑开挖过程中加强地下水位、基坑周围地面建筑、地下管线的监控量测,如周围建筑地基不均匀沉降和地下管线变形超过警戒值,立即采取回灌措施。 回灌量根据观测到水位变化量而定。降水井在顶板覆土回填后进行封堵,以满足车站施工阶段的抗浮要求,防止基底隆起,地下严重失水引起地面沉降,危及路面、既有建筑物和管线 建设十一路站主体第三道支撑预加轴力支撑设计参数预加轴力 间距轴力设围檩预加施工控 支撑支撑轴计值角度轴力制轴力编号线位置 轴力预加锁定 m KN/m°轴力轴力 (KN) (KN)(KN) B3- 6-7轴 3.017090510510561.0 10 B3- 6-7轴 3.017090510510561.0 11 B3- 7-8轴 3.017090510510561.0 12 B3- 7-8轴 3.017090510510561.0 13 B3- 7-8轴 3.017090510510561.0 14 B3- 8-9轴 3.017090510510561.0 15 B3- 8-9轴 3.017090510510561.0 16 B3- 9-10轴 3.017090510510561.0 17 B3- 9-10轴 3.017090510510561.0 18 分级控制预加力 回归方程 标定系数 Y=a+bX(X:千斤第1级顶,Y:油压表) 千斤预加 油表油表 理论实际 顶编a b轴力 读数读数 号(KN) (MPa)(MPa) 1-0.440.0655181287.9 20.030.0664681288.5 1-0.440.0655181287.9 20.030.0664681288.5 1-0.440.0655181287.9 20.030.0664681288.5 1-0.440.0655181287.9 20.030.0664681288.5 1-0.440.0655181287.9 20.030.0664681288.5 1-0.440.0655181287.9 20.030.0664681288.5 1-0.440.0655181287.9 20.030.0664681288.5 1-0.440.0655181287.9 20.030.0664681288.5 1-0.440.0655181287.9 20.030.0664681288.5 基坑钢支撑轴力应力伺服自动补偿系统技术的原理和应用 针对上海绿地恒滨置业集团龙华路1960地块项目紧邻地铁深基坑开挖具体情况,运用钢支撑轴力应力伺服系统,减少钢支撑轴力损失。并对基坑临近地铁侧变形最大位置点进行监测,使基坑邻地铁侧围护地下连续墙的变形控制在20mm之内,地铁沉降控制在5mm以内,确保了周边居民建筑的安全和地铁运行安全。 Key words:deep pit;steel support;stresses servo system;envelope underground continuous wall;deformation control 本工程地下室与7#线共用地下连续墙,为了确保7#线地铁正常运营安全,申通地铁公司对紧邻地铁基坑工程基坑变形提出了更高标准和更严要求,变形控制在20mm之内,工期由5个月改为3个月,施工难度逐渐加大。为确保基坑及地铁安全,基坑施工过程中必须运用有效的控制变形工具、施工工艺及相关控制措施。 本文介绍了钢支撑轴力应力伺服系统的原理和施工应用,并结合基坑、地铁围护变形数据的整理分析,总结应力伺服系统在施工中基坑地铁变形曲线趋势,为钢支撑轴力应力伺服系统应用提供现场依据,从而确保基坑施工与地铁正常运营安全。 1.应力伺服自适应支撑系统介绍 应力伺服自适应支撑系统是结合了现代机电液一体化自动控制技术、计算机信息处理技术以及可视化监控系统等高新技术手段,对支撑轴力进行全天候不间断监测,并根据高精度传感器所测参数值对支撑轴力进行适时的自动或手动补偿来达到控制基坑变形目的的支撑系统。运用自适应支撑系统,实现了对钢支撑轴力的实时监测和控制,解决常规施工方法无法控制的苛刻变形要求和技术难题,使工程始终处于可控和可知的状态,具有良好的社会效益、经济效益和环境保护效益。 2.应力伺服系统施工原理 钢支撑轴力应力伺服系统主要分为4部分:PC人机交流系统,DCS控制系统,油压泵压力系统和钢支撑系统(见图1),其中DCS控制系统为整个系统的控制枢纽,连接其他3大系统。DCS将数据反映至PC系统,显示给监测人员;控制油压泵开启或关闭,增压保压;接收钢支撑端部千斤顶轴力数据,与设计数据进行比较。PC系统将设计数据输入,转换成视觉可操作平面,油压泵提供支撑轴力支持,支撑直接进行压力输出(施予地下连续墙),同时通过传感器将实时轴力数据反馈给DCS控制系统。当反馈数据低于设计轴力数据范围时,DCS 控制系统输出信号驱动油压泵系统开启工作,油压泵不断输送给钢支撑千斤顶压力,待传感器传回数据在一段时间(一般5~10min)稳定在设计数据之上时, 温差对钢支撑轴力的影响及调整方法 摘要:为了探明和量化在特定条件下温差对钢支撑的影响并针对该影响采取相应措施指导施工,本文根据南宁轨道交通一号线广西大学站基坑工程的成功实例,分析了温差影响的相对幅度,并采用相应措施使“温差影响”变为“温差控制”。 关键词:钢支撑;支撑内力;温差影响;c abstract: in order to proven and quantify the temperature difference between the impact of the steel support under certain conditions and for the effects to take appropriate measures to guide the construction, this paper based on the successful examples of the station foundation pit one line of rail transportation in nanning guangxi university, analyzed the difference in temperature affect the relative amplitude, and to adopt appropriate measures so that the “temperature influence” to “temperature control”.key words: steel support; brace force; temperature difference influence; temperature control 中图分类号:tb61+9.2 文献标识码:a文章编号: 温差条件下钢支撑伸长率的实验 实验目的:自由状态下或未施加预应力条件下单位温差及单位长度钢支撑伸长率 技术交底记录(轨道交通工程) 钢丝绳,吊具采用20mm吊环。钢丝绳使用前仔细检查其安全性,若有破损、起毛、断股等现象,及时更换钢丝绳。 ③钢支撑需事先在地面上试拼好,然后再吊运至基坑,及时架设。钢支撑法兰盘连接螺栓采用对角和分等分顺序扳紧,一般分两次拧紧,支撑拼接采用扭矩扳手检测其力矩是否符合要求,保证法兰螺栓连接强度。拼接好的支撑经质检工程师及监理工程师检查验收合格后方可安装。 ④吊放钢支撑要缓慢放在钢围檩托架上,不得冲击、碰撞钢围檩。 ⑤轴力监测点布置:按监控量测施工布置图,确定钢支撑轴力监测点位置,拼接钢支撑时,考虑轴力计的长度,实际拼接长度要比普通钢支撑短20cm。轴力计布置在受力集中的典型断面上。 ⑥在确保钢板与钢围檩的焊接质量的同时,还应保证钢围檩与围护桩之间的稳定性。为了防止钢围檩松动、滑落,采用悬挂的方法,将钢拉钩一端用膨胀螺栓固定在桩上,另一端挂起钢围檩,将其悬挂在围护桩上,详见钢围檩悬挂保护详细构造图1。 图1 钢围檩悬挂保护详细构造图 ⑦钢支撑施加轴力后,用Φ14钢丝绳配合绳卡将钢支撑悬挂固定在围护桩上。悬挂方法同钢围檩悬挂保护。如图2所示 图2 钢支撑防脱落措施示意图 ⑧钢支撑安装完成后,在横抬梁设置抱箍,防止钢支撑因挠度变化移位。抱箍采用L80×80×5角钢制作。 (4)钢支撑施加轴向预应力和复加预应力 设计钢支撑预加轴力如下表1。 钢支撑轴力表表1 计算结果断面第一道 支撑 第二道 支撑 第三道 支撑 第四道 支撑 围护桩最大 水平位移 (mm) 基坑深 度(m) 西侧盾构段 预加轴力 (kN) 0400500400 20.7625.11轴力计算值 (kN) 462166834142398 东侧盾构段 预加轴力 (kN) 0400500400 20.2525.66轴力计算值 (kN) 819155336662889 标准段 预加轴力 (kN) 0400500400 19.2924.55轴力计算值 (kN) 579163032822138 说明:以上轴力为每根钢支撑的轴力,支撑轴力为设计值。 (1)钢支撑施加轴向力 ①在基坑开挖过程中随挖随撑,同时要对随挖随撑好的钢支撑及时施加的轴向预应力,以此减小由于支撑不及时而引起的围护结构变形。 ②采用汽车吊将加力器的两个100t千斤顶吊放到活络头加压处,定位加压,观察压力表,达到设计预加轴力值后,停止加压,将钢楔用大锤打入活络头预留 地铁车站钢支撑轴力自动补偿施工工艺工法集团标准化小组:[VVOPPT-JOPP28-JPPTL98-LOPPNN] 地铁车站钢支撑轴力自动补偿施工工艺工法 (QB/ZTYJGYGF-DT-0307-2014) 广州分公司王小孟 1前言 1.1工艺工法概况 钢支撑自动轴力补偿系统,是结合了现代机电液压一体化自动控制技术、计算机信息处理技术、总线通信技术以及可视化监控技术等高新技术手段,对支撑轴力进行全天候不间断监测,并根据高精度传感器所测参数值对支撑轴力进行适时的自动补偿来达到控制基坑变形目的支撑系统。 钢支撑自动轴力补偿系统将传统支撑技术与现代高科技控制技术等有机结合起来,对钢支撑轴力实时补偿与监控,实现对钢支撑轴力24小时不间断的监测和控制,使支撑系统始终处于可控和可知的状态。与传统钢支撑体系相比,自动轴力补偿系统能明显降低基坑围护结构的最大变化速率,控制基坑的变形,减小对邻近运营线路、建筑等周边环境的影响,有效解决常规施工方法无法控制的苛刻变形要求和技术难题。 目前在上海地区邻近地铁运营线的基坑应用较多,在深圳地铁11号线前海湾站首次应用。 1.2工艺原理 钢支撑是基坑内支撑体系的一种常用型式。每根钢支撑有多个标准节钢管拼接而成,通过法兰盘进行连接。钢支撑两端为固定端、活动端端头,活动端通过活络头调节长度。常规做法是通过活动端的活络头用千斤顶对钢支撑按照设计要求预施加一定轴力,并安装轴力计监控钢支撑的轴力,以便掌握基坑结构变形引起的应力变化情况。钢支撑自动轴力补偿系统,是采用钢支座套箱端头替代活动端,钢支座套箱端头内安装千斤顶(设计轴力决定其吨位),通过液压转换为支撑轴力,与基坑外侧土压力保持平衡,从而使基坑处于安全的状态。地面通过监控站、操作站、现场控制站、液压伺服泵站等成套系统即时控制钢支撑端部千斤顶压力,通过持续“保压”,使钢支撑恒定轴力,起到自动控制、监测钢支撑轴力作用。 1.2.1系统组成 系统设计采用了“树状即插分布式模块,结构、多重安保体系”的总体工艺技术路线,将机电液压自动控制技术、PLC电气自动控制技术、总线通信技术以及现代HMI人机界面智能技术和计算机数据处理技术等多项现代高科技技术有机集成起来,自动轴力补偿系统主要有以下部件组成: 基坑钢支撑支护总结 基坑支护是为保证地下结构施工及基坑周边环境的安全,对基坑侧壁及周边环境采用的支挡、加固与保护措施。 1、基坑支护特点 (1)基坑支护工程是个临时工程,设计的安全储备相对可以小些,但又与地区性有关。不同区域地质条件其特点也不相同。基坑支护工程又是岩土工程、结构工程以及施工技术互相交叉的学科,是多种复杂因素交互影响的系统工程,是理论上尚待发展的综合技术学科。 (2)由于基坑支护工程造价高,开工数量多,是各施工单位争夺的重点,又由于技术复杂,涉及范围广,变化因素多,事故频繁,是建筑工程中最具有挑战性的技术上的难点,同时也是降低工程造价,确保工程质量的重点。 (3)工程实践证明,要做好基坑支护工程,必须包括整个开挖支护的全过程,它包括勘察、设计、施工和监测工作等整个系列,因而强调要精心做好每个环节的工作。 (4)基坑支护工程包含挡土、支护、防水、降水、挖土等许多紧密联系的环节,其中的某一环节失效将会导致整个工程的失败。 (5)相邻场地的基坑施工,如打桩、降水、挖土等各项施工环节都会产生相互影响与制约,增加事故诱发因素。 (6)在支护工程设计中应包括支护体系选型、围护结构的承载力、变形计算、场地内外土体稳定性、降水要求、挖土要求、监测内容等,应注意避免“工况”和计算内容之间可能出现的“漏项”,从而导致基坑失误。在施工过程中,尤其在软土地区中施工时,应该认真研究合理安排好挖土的方法,以及支撑与挖土的配合,将会显著地减少基坑变形和基坑支护事故的发生。 (7)基坑支护工程造价较高,但又是临时性工程,一般不愿投入较多资金。可是,一旦出现事故,处理十分困难,造成的经济损失和社会影响往往十分严重。(8)基坑支护工程施工周期长,从开挖到完成地面以下的全部隐蔽工程,常需经历多次降雨、周边堆载、振动、施工不当等许多不利条件,其安全度的随机性较大,事故的发生往往具有突发性。 2、常见的基坑支护型式主要有: 基 坑 开 挖 钢支撑组拼 施工监测 吊 装 钢 支 撑 施 加 预 加 力 楔 块 锁 定 安设牛腿钢围檩 技术交底书 表格编号 1310 项目名称 杭州地铁2号线SG2-22标项目经理部 第 页 共 页 交底编号 工程名称 新月路站A 、D 出入口钢支撑安装 设计文件图号 HD2/2/S/HCY/04/Z07/JG/04/A 施工部位 新月路站A 、D 出入口 交底日期 2016年11月 日 技术交底: 1 工程概况 新月路站A 、D 出入口基坑采用钢支撑作为支撑体系,由冠梁、钢支撑和钢围檩等组成。钢支撑选用Φ609×16mm 钢管,由多节钢管拼成一道支撑,并用法兰盘、螺栓连接;钢围檩选用HW400×400×13×21双拼H 型钢。基坑支撑体系竖向分布三道钢支撑,其中第一道钢支撑架设在冠梁上,第二道和第三道钢支撑架设在钢围檩上。 2 施工工序流程 钢支撑施工流程图 3 施工准备 3.1 材料进场 按照计划用量备足各种长度的φ609×16钢管、活络头和不同规格的钢垫块、钢楔子、HW400×400×13×21型钢、角钢、连接螺栓、钢板等支撑材料,分类堆放在材料场。钢管 图4-1 钢支撑、钢围檩架设立面图 注:A出入口基底标高为-5.10,D出入口基底标高为-5.15。 (2)测量放线 基坑开挖到支撑设计底标高位置后,对钢支撑控制轴线和水准标高进行测放,准确定位钢支撑的轴线和标高位置,并采用十字交叉法划线标识。 (3)钢围檩的安装 钢围檩安装时要保证其紧密顶压在工法桩上,并按设计施工图的布置间距,在工法桩上定出支撑中心点位,在标出的支撑位置处凿出工法桩内H型钢,以支撑中心的水平线为基准,将支撑牛腿及拉结筋焊接到H型钢相应的位置。 DZB3600S钢支撑轴力智能补偿系统简介 陈建海金立源刘可可 (徐州盾安重工机械制造有限公司徐州泉山开发区 221000) (陈建海:联系电话1305202989 邮箱chenjh168@https://www.360docs.net/doc/ee13838992.html,) 摘要:文章介绍了“DZB3600S钢支撑轴力智能补偿系统”的构成、工作原理、主要设备的作用、现场安装的位置、安装流程。 关键词:钢支撑轴力智能补偿简介 一、概述 随着我国地下工程的高速发展,基坑开挖过程中安全问题也被越来越多的关注。基坑支护的轴力监测问题在许多国家基础建设中都存在,并得到高度重视,日本、德国、英国、新西兰等国家很早就在这方面开展了相关工作,并取得了一定的进展。钢支撑在我国使用以来,多次出现重大安全事故,给施工单位、业主的资产造成严重损坏和伤亡等问题。 DZB3600S钢支撑轴力智能补偿系统是徐州盾安重工机械制造有限公司研制的最新基坑支护轴力实时监测、补偿系统,由补偿节、泵站、控制柜及软件系统共同组成的一套完整的基坑支护、实时监测装置。 轴力实时补偿对应土体压变化,极大的减少基坑位移的影响,系统通过各单元元件冗余进行原件的故障进行控制,降低了因系统故障而影响整体安全的事故因素。通过自主设计的随动自锁油缸,保证在系统全部瘫痪的前题下依然能保证基坑不会失稳。通过集成通信模块对系统数据进行压缩传输到网络,使整个系统信息实现实时传输与远程控制功能,降低了施工成本与数据传输的滞后性,让施工更准确更轻松更安全。 系统特点及功能:输出液压管路排线式布置,外型紧凑美观,集成度高;三组液压系统相互独立运行,每组液压系统可独立控制8根补偿节,输出推力可根据需要实时调节并进行监控;三组液压系统相互间顺序监控,如某一路的压力源出现故障(如电机或是泵出现故障,无法打出压力油),故障自动诊断系统会自行识别,并在极短的时间内切换到旁边的液压系统供油,以保证系统安全运行。临地铁深基坑综合施工技术的研究
围护结构钢支撑施工工艺工法
钢支撑及轴力自动补偿系统施工方案
5、地铁车站钢支撑轴力自动补偿施工工艺工法
地铁站钢支撑轴力计算新
精选最新隧道与地铁工程施工新工艺工法
支撑轴力
钢支撑架设技术要求
DZB3600S钢支撑轴力智能补偿系统
工程重点、难点分析及对策
钢支撑轴力计算表.docx
基坑钢支撑轴力应力伺服自动补偿系统技术的原理和应用
温差对钢支撑轴力的影响及调整方法
钢支撑安装及拆除技术交底
地铁车站钢支撑轴力自动补偿施工工艺工法
基坑钢支撑支护总结
钢支撑技术交底
DZB3600S钢支撑轴力智能补偿系统及应用简介