塑料模块50年长期蠕变试验方法
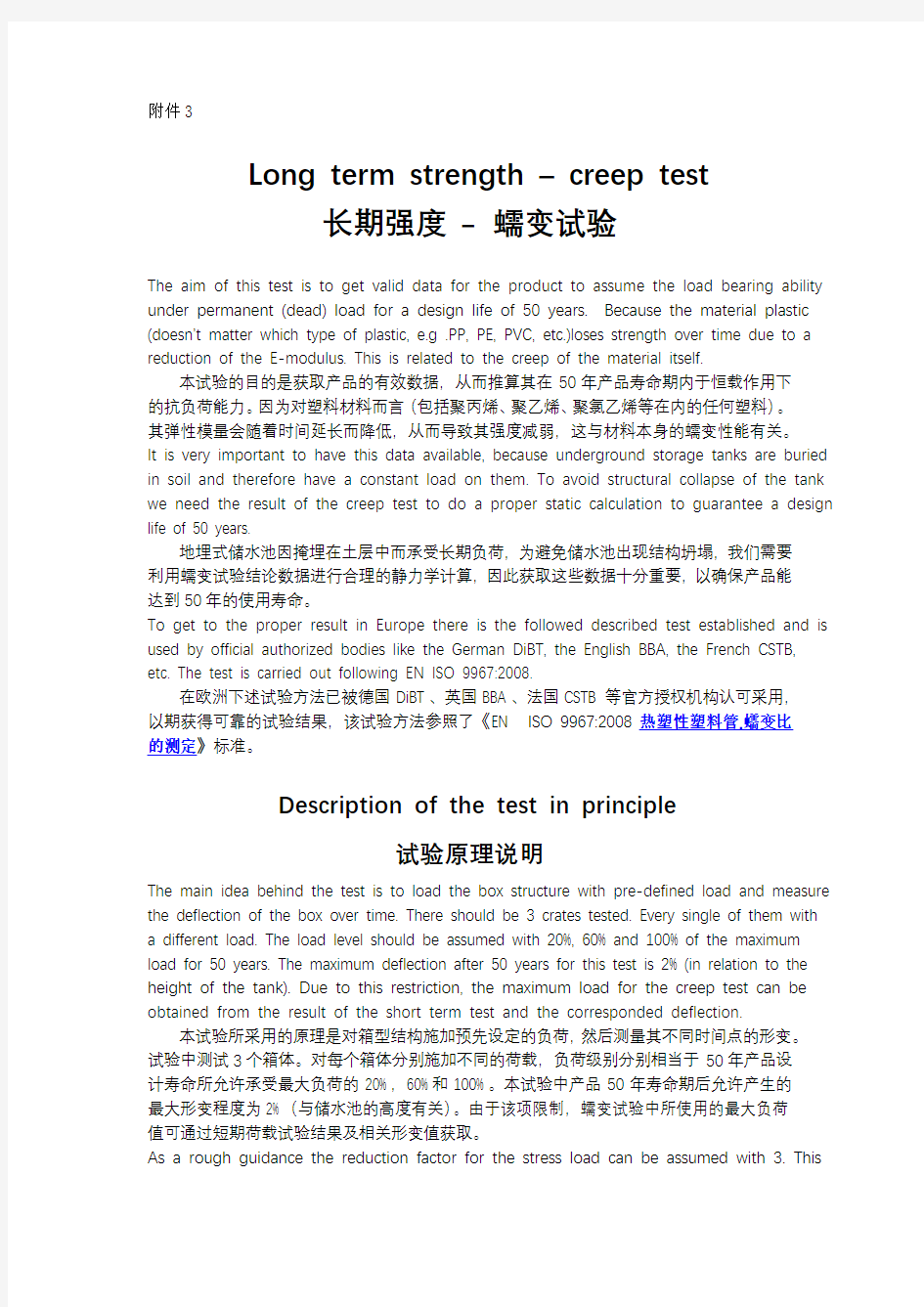

附件3
Long term strength – creep test
长期强度– 蠕变试验
The aim of this test is to get valid data for the product to assume the load bearing ability under permanent (dead) load for a design life of 50 years. Because the material plastic (doesn’t matter which type of plastic, e.g .PP, PE, PVC, etc.)loses strength over time due to a reduction of the E-modulus. This is related to the creep of the material itself.
本试验的目的是获取产品的有效数据,从而推算其在50年产品寿命期内于恒载作用下的抗负荷能力。因为对塑料材料而言(包括聚丙烯、聚乙烯、聚氯乙烯等在内的任何塑料)。其弹性模量会随着时间延长而降低,从而导致其强度减弱,这与材料本身的蠕变性能有关。It is very important to have this data available, because underground storage tanks are buried in soil and therefore have a constant load on them. To avoid structural collapse of the tank we need the result of the creep test to do a proper static calculation to guarantee a design life of 50 years.
地埋式储水池因掩埋在土层中而承受长期负荷,为避免储水池出现结构坍塌,我们需要利用蠕变试验结论数据进行合理的静力学计算,因此获取这些数据十分重要,以确保产品能达到50年的使用寿命。
To get to the proper result in Europe there is the followed described test established and is used by official authorized bodies like the German DiBT, the English BBA, the French CSTB, etc. The test is carried out following EN ISO 9967:2008.
在欧洲下述试验方法已被德国DiBT、英国BBA、法国CSTB等官方授权机构认可采用,以期获得可靠的试验结果,该试验方法参照了《EN ISO 9967:2008热塑性塑料管.蠕变比的测定》标准。
Description of the test in principle
试验原理说明
The main idea behind the test is to load the box structure with pre-defined load and measure the deflection of the box over time. There should be 3 crates tested. Every single of them with a different load. The load level should be assumed with 20%, 60% and 100% of the maximum load for 50 years. The maximum deflection after 50 years for this test is 2% (in relation to the height of the tank). Due to this restriction, the maximum load for the creep test can be obtained from the result of the short term test and the corresponded deflection.
本试验所采用的原理是对箱型结构施加预先设定的负荷,然后测量其不同时间点的形变。试验中测试3个箱体。对每个箱体分别施加不同的荷载,负荷级别分别相当于50年产品设计寿命所允许承受最大负荷的20%,60%和100%。本试验中产品50年寿命期后允许产生的最大形变程度为2%(与储水池的高度有关)。由于该项限制,蠕变试验中所使用的最大负荷值可通过短期荷载试验结果及相关形变值获取。
As a rough guidance the reduction factor for the stress load can be assumed with 3. This
means, if you divide the maximum stress from the short term test by 3 you will get the 100% stress load for the creep test. This is just a rough approximation. Some trial error approaches may be done to get the final load.
作为参考可将压力荷载的折减因数视为3。即可将短期压力荷载试验中得出的最大应力值除以3后作为蠕变试验中100%压力值。由此得出的值仅为近似值,可通过尝试误差法获得最终负荷值。
An example how the load is applied and a setup of the test is shown in the following picture. 下图为施加负荷和试验设置的示例。
After the definition of the different loadings for the boxes the test can be started. Therefore the boxes should be set up in temperature conditioned environment and the boxes should be equipped with a deflection measurement tool. A pre load should be applied before the starting of the test. Please refer to section 8 of the ISO 9967 for this. The test duration should be 10.000 hours. If, after a test duration of 3.000 hours, the correlation coefficient R is between 0,99 and 1,00, the extrapolation to 10.000 hours test time (and afterwards to calculate the strength for 50 years) could be done in advance. The test should then also last until 10.000 hours to verify the assumptions but the final result can be pretty good guessed after 3.000 hours.
在定义各箱体的施加负荷值后可开始试验。将箱体放于温度可控的环境中,并安装形变测量工具。在试验开始前应加载预负荷,具体请参照ISO 9967标准第8节内容。试验时长为10,000小时。如果在试验进行3,000小时后,相关系数R在0.99到1.00之间,可提前外推10,000小时的形变(之后计算出50年所受强度)。试验应继续进行至10,000小时以检验外推假设的准确性,但3,000小时后的计算结果已能很好地估测出最终结果。
Below you will find an excerpt of the ISO 9967 for the evaluation
以下摘自ISO 9967标准中的有关估算过程
9.蠕变比率的测定
9.1对三件试样中的每个样品,在半对数坐标图(见图3)上做形变(单位:m)对试验时间
(单位:h)的半对数曲线,并利用线性回归确定直线方程:
Y t=B + M log t (4)
分别对所有11个数据点,最后10个点,最后9个点……直到最后的5个点(参见表2)作
线性回归分析,这里常数B、M及相关系数R按公式(5)至(7)计算(运用最小二乘法)。
式中:
B——在t=1h 时理论上的形变,单位mm;
M——直线斜率;
N——用作线性回归分析的形变-时间曲线上的数据点数;
R——相关系数(如果R值在0.99到1.00之间,则认为图中的点基本处于一条直线上);Y2——外推两年时间(17520小时)后的形变值,单位mm;
t i——在i点的时间;
x i = log (t i);
y i——在t i时的总形变,单位mm。
由给定试样通过不同数据点的范围导出的公式Y t=B + M log t,计算外推两年的形变Y2=(t=2年=17520小时)(参见表2)。
选择相关系数分布在0.990到0.999(R值包含0.999)之间的R值最高值时对应的Y2值为两年形变量,当R值相同时,取R值相应的Y2最高计算值为两年形变量,然后将Y2用于对试验样品蠕变比率的计算。当R值最高值小于0.990(包含0.990)时,参见9.3。
在得出Y2值后用公式(8)、公式(9)、公式(10)计算三个试样的蠕变比率:
利用公式(11)取他们的算术平均值作为管材蠕变比率并做好记录:
节内容,Y2的值基于至少五个数据点范围以及R值为大于0.990以上的最高值所确定。
表2 :图3对应数据
数据点数时间
t
h
形变
Y t
mm
数据点
范围
M B R Y2
1 0.1 6.53 1到11 0.505 6.684 0.951 8.825
2 1 6.65 2到11 0.611 6.425 0.967 9.017
3 4 6.78 3到11 0.709 6.172 0.972 9.179
4 24 7.02 4到11 0.88
5 5.69
6 0.982 9.436
5 168 7.53 5到11 1.195 4.830 0.997 9.914
6 336 7.85 6到11 1.299 4.51
7 0.997 10.060
7 504 8.05 7到11 1.410 4.174 0.998 10.211
8 600 8.13
9 696 8.23
10 840 8.38
11 1008 8.46
图例
t 时间,单位h y0初始形变
y 形变,单位mm y2外推两年时间的形变
图3 某试样的形变-时间关系图
9.2在某些计算方法中,仍需要50年的外推数据。50年的形变量Y50可依据9.1所述进行计算,将公式中的2年替换为50年(438000小时)即可。
9.3在回归分析中,对于三件试样中的任何一个,如果在最后5个点的范围内仍得不到高于0.990的相关系数值,那么就需要在所有三件试样上继续进行试验,分别再测量1200小时,1400小时,1680小时,2000小时,2400小时,2818小时,3400小时或4000小时时的形
变,各测量时间允许偏差为±48小时,或直到最后5个点范围的相关系数值超过0.990为止,继续使用最后五点测量直到关系系数超过0.990为止,视哪种方法先得出结论而定。Attached you will also find the official certificates of our Product from the German DiBt and the British BBA.
附件为德国DiBt和英国BBA为我们的产品出具的官方证书。
高温蠕变疲劳试验机
高温蠕变疲劳试验机 一、主要技术参数 工作介质液压油 试验压力范围0.5-10MPa,,1-20Mpa,21-30 Mpa 试验环境温度室温 时间显示电脑显示 压力曲线显示数据采集软件实时显示 打印报告试验完毕可以打印试验报告并保存 试验数据 试验数据保存可以保存报告及试验过程记录 压力显示精度0.01MPa 控压精度1% 工作温度高温 电源380V 应用范围容器 二、产品介绍 高温蠕变疲劳试验机主要用于各种容器、管件、阀门、管道等的脉冲试验。可对试验压力,试验温度,试验次数等进行控制,最大试验压力30Mpa,支持断电自动保存数据。 试验机箱体是由液压系统和热交换系统,控制仪表等组成的一个有机体。在门都安装闭合检测开关,进行测量检测,以满足试验安全性。整个控制系统采用工业控制计算机+二次控制仪表系统+传感器开关控制模式,并对所有的开关量进行闭合PLC监控,采用逻辑关系,保证系统的安全和可靠,能够进行故障记录,
自动系统锁定逻辑,保证无人值班的试验安全。 三、典型应用: 换热器高温蠕变疲劳试验 热交换器高温蠕变持久松弛试验 四、特点 1.使用安全。工件自动检漏和停机; 2.可存储最近30万次循环的脉冲压力波形。 3.实验数据可回访,可以按照实验时间、实验次数等查询实验结果。 4.支持断电自动保存数据; 5.计算机数据采集处理,打印输出压力、疲劳次数和疲劳压力波形; 6.可实时显示脉冲压力波形(设定波形和实际波形)、压力值、循环次数、流体 温度、环境温度等参数; 7.拆卸被试管路后的泄漏介质自动回收; 8.试验压力-时间曲线能够在屏幕上显示并能打印或存储在存储器内,计算机 控制,存储器有USB接口,可打印实验压力曲线; 9.内部采用保温层,可以控制环境温度与液体温度。 五、高温蠕变疲劳试验机安全保护 1.回路中设有过滤装置,在过滤器的两端装有压差发讯报警器。 2.设备设有过压报警功能,试验回路中的压力发生突变时,设备自动报警,其 超过安全范围时,设备自动停机。 3.设备设有试验间内管道、工件失效的泄漏报警功能。 4.超温保护:设备设置了超温保护装置,当油温超过设定极限温度时,自动停
疲劳分析方法
疲劳寿命分析方法 摘要:本文简单介绍了在结构件疲劳寿命分析方法方面国内外的发展状况,重点讲解了结构件寿命疲劳分析方法中的名义应力法、局部应力应变法、应力应变场强度法四大方法的估算原理。 疲劳是一个既古老又年轻的研究分支,自Wohler将疲劳纳入科学研究的范畴至今,疲劳研究仍有方兴未艾之势,材料疲劳的真正机理与对其的科学描述尚未得到很好的解决。疲劳寿命分析方法是疲分研究的主要内容之一,从疲劳研究史可以看到疲劳寿命分析方法的研究伴随着整个历史。 金属疲劳的最初研究是一位德国矿业工程帅风W.A.J.A1bert在1829年前后完成的。他对用铁制作的矿山升降机链条进行了反复加载试验,以校验其可靠性。1843年,英国铁路工程师W.J.M.Rankine对疲劳断裂的不同特征有了认识,并注意到机器部件存在应力集中的危险性。1852年-1869年期间,Wohler对疲劳破坏进行了系统的研究。他发现由钢制作的车轴在循环载荷作用下,其强度人大低于它们的静载强度,提出利用S-N 曲线来描述疲劳行为的方法,并是提出了疲劳“耐久极限”这个概念。1874年,德国工程师H.Gerber开始研究疲劳设计方法,提出了考虑平均应力影响的疲劳寿命计算方法。Goodman讨论了类似的问题。1910年,O.H.Basquin提出了描述金属S-N曲线的经验规律,指出:应力对疲劳循环数的双对数图在很大的应力范围内表现为线性关系。Bairstow通过多级循环试验和测量滞后回线,给出了有关形变滞后的研究结果,并指出形变滞后与疲劳破坏的关系。1929年B.P.Haigh研究缺口敏感性。1937年H.Neuber指出缺口根部区域内的平均应力比峰值应力更能代表受载的严重程度。1945年M.A.Miner 在J.V.Palmgren工作的基础上提出疲劳线性累积损伤理论。L.F.Coffin和S.S.Manson各自独立提出了塑性应变幅和疲劳寿命之间的经验关系,即Coffin—Manson公式,随后形成了局部应力应变法。 中国在疲劳寿命的分析方面起步比较晚,但也取得了一些成果。浙江大学的彭禹,郝志勇针对运动机构部件多轴疲劳载荷历程提取以及在真实工作环境下的疲劳寿命等问题,以发动机曲轴部件为例,提出了一种以有限元方法,动力学仿真分析以及疲劳分
铜及铜合金弯曲应力松弛试验方法
《铜及铜合金弯曲应力松弛试验方法》 国家标准送审稿编制说明 一、任务来源 根据国标委综合[2017]128号及全国有色金属标准化技术委员会下发的有色标委[2018]2号《关于转发2018年第一批有色金属国家标准制(修)订项目计划》文件,《铜及铜合金弯曲应力松弛试验方法》国家标准(计划号:20173798-T-610),由宁波兴业盛泰集团有限公司、宁波兴业鑫泰新型电子材料有限公司、安徽鑫科铜业有限公司、凯美龙精密铜板带(河南)有限公司、山西春雷铜材有限责任公司、江西金品铜业科技有限公司、中色(宁夏)东方集团有限公司、国家铜铝冶炼及加工产品质量监督检验中心(山东)负责起草,项目于2019年完成。 二、工作简况 1立项目的 随着电子元器件向着微型化、薄型化、高密度和高度集成化发展,电子元器件在长时间使用中产生的热效应不断增加,部分元器件还可能在更高的温度下长时间使用,为了保持端子连接器弹片的嵌合力,这就要求材料具有优良的抗应力松弛性能。国内接插件市场占有率比较高,但均以中低端市场为主,而高端的汽车连接器、精密接插件及大规模集成电路等产品则长期依赖进口。造成这种现象的原因主要有两个方面,一方面是我国对于高弹铜基合金的基础研究起步较晚,且我国铜合金制备加工能力与发达国家相比还有一定差距,工艺条件、装备水平等方面都有待进一步提高;另一方面是随着客户对铜基弹性材料性能的要求不断提高,许多客户对材料提出了具有抗应力松弛特性的隐性需求,而国内应力松弛试验方法标准少,限制了我国对高端连接器及精密接插件等材料进行更深层次的研发工作。 国外对应力松弛试验方法已制定相应的标准,主要有美国ASTM E328“材料和结构的应力松弛试验标准推荐方法”、日本伸铜协会技术标准JCBA-T309-2004 薄板条弯曲应力松弛缓和试验方法等。报据以上国外标准可以看出,评价材料松弛性能的主要方法两种,一种是拉伸应力松弛,另外是弯曲应力松弛。而目前国内仅有GB/T 10120-2013“金属材料拉伸应力松弛试验方法”,缺少相应的弯曲应力松弛试验方法,且此标准中对测试样的要求较高、试验周期长、效率低,对设备的要求比较高,且绝大多数铜基弹性材料的下游企业,并未配备检测机器和具有检测能力。目前各种弹性接插件的工作环境,更与弯曲应力松弛试验条件相接近,采用弯曲应力松弛试验方法,更能代表实际材料的工作条件,更可满足多元条件下的应力松弛试验要求;另外,由于各企业也只是独立地进行应力松弛试相关的简单的试验性工作,试验方法五花八门,但由于缺乏统一评价标准,致使更多企业未对其进行展开系统地、深层次的研究,限制着其高端方面的使用。因此,制定铜及铜合金弯曲应力松弛试验方法就显得十分重要,对规范弯曲应力松弛试验,统一数据评价标准,有利于我国中高端连接器、集成电路用材料的研发,具有良好的现实意义。为满足国内外市场对铜及铜合金应力松弛性能的需求,更有效的确保产品质量,因此制定本标准。
拉伸应力松弛金属检测的试验方法
森博检测服务中心 拉伸应力松弛金属检测的试验方法 按照国家规定,其部分所引用的标准如下: GB/T228.1 金属材料拉伸试验第一部分:室温试验方法 GB/T2039 金属材料单轴拉伸蠕变试验方法 GB/T10623 金属材料力学性能试验术语 GB/T12160 单轴试验用引伸计的标定 GB/T16825.1 静力单轴试验机的检验第一部分:拉力和压力试验机测力系统的检验与校准 下面,我们来简单看一下室温弹性模量的测定 为了保证伸长测量的正确操作,应测定室温弹性模量。弹性模量的测量值应在弹性模量预期值的±10%范围内。弹性模量预期值通常是通过拉伸试验确定的,使用的引伸计的性能与应力松弛试验使用的引伸计具有同等性能。 试样应加热至试验规定温度(T)。调整试验炉加热控制系统使温度分布符合表一要求。试样,夹持装置和引伸计在试验开始前都应达到热平衡。 试样应在加载前至少保温1h,除非产品标准另有规定。试样加载前的保温时间不得超过24h。升温过程中,任何时间试样温度不得超过规定温度(T)上偏差。 试验力应施加在试样的轴线上。尽量减少试样上的弯曲和扭转。初始总应变和对应的初始应力的测定精度至少为±1%加载可以采用应变控制也可以采用里控制。应变或力的增加应平稳,无冲击,初始总应变的施加过程应在10min内完成,记录加载时间。在加载过程中,采用自动记录装置或通过递增的方式施加试验力并记录每个力的增量对应的伸长量来获得应力-应变或力-位移图。应绘制和评估高温应力=应变图,保证伸长测量的正确。 字整个试验过程中,总应变值应保持基本恒定。根据控制方式的不同,总应变的控制不同。对于采用力控制加载的方式,总应变值应控制在初始总应变的测量值的±1%的范围内;对于采用应变控制加载的方式,通过逐渐减少应力使总应变值应控制为总应变的规定值。对于人工进行力调整的方式,实际上只是采用力的逐减方式使测量应变返回到总应变ε;对于伺服控制总应变来讲,力的调整是通过递减或递增的方式进行的,应变波动范围大约控制在±1%以内。
铜及铜合金弯曲应力松弛试验方法国家标准讨论稿编制说明
《铜及铜合金弯曲应力松弛试验方法》国家标准讨论稿编制说明 一、工作简况 1立项目的 随着电子元器件向着微型化、薄型化、高密度和高度集成化发展,电子元器件在长时间使用中产生的热效应不断增加,部分元器件还可能在更高的温度下长时间使用,为了保持端子连接器弹片的嵌合力,这就要求材料具有优良的抗应力松弛性能。国内接插件市场占有率比较高,但均以中低端市场为主,而高端的汽车连接器、精密接插件及大规模集成电路等产品则长期依赖进口。造成这种现象的原因主要有两个方面,一方面是我国对于高弹铜基合金的基础研究起步较晚,且我国铜合金制备加工能力与发达国家相比还有一定差距,工艺条件、装备水平等方面都有待进一步提高;另一方面是随着客户对铜基弹性材料性能的要求不断提高,许多客户对材料提出了具有抗应力松弛特性的隐性需求,而国内应力松弛试验方法标准少,限制了我国对高端连接器及精密接插件等材料进行更深层次的研发工作。 国外对应力松弛试验方法已制定相应的标准,主要有美国ASTM E328“材料和结构的应力松弛试验标准推荐方法”、日本伸铜协会技术标准JCBA-T309-2004 薄板条弯曲应力松弛缓和试验方法等。报据以上国外标准可以看出,评价材料松弛性能的主要方法两种,一种是拉伸应力松弛,另外是弯曲应力松弛。而目前国内仅有GB/T 10120-2013“金属材料拉伸应力松弛试验方法”,缺少相应的弯曲应力松弛试验方法,且此标准中对测试样的要求较高、试验周期长、效率低,对设备的要求比较高,且绝大多数铜基弹性材料的下游企业,并未配备检测机器和具有检测能力。目前各种弹性接插件的工作环境,更与弯曲应力松弛试验条件相接近,采用弯曲应力松弛试验方法,更能代表实际材料的工作条件,更可满足多元条件下的应力松弛试验要求;另外,由于各企业也只是独立地进行应力松弛试相关的简单的试验性工作,试验方法五花八门,但由于缺乏统一评价标准,致使更多企业未对其进行展开系统地、深层次的研究,限制着其高端方面的使用。因此,制定铜及铜合金弯曲应力松弛试验方法就显得十分重要,对规范弯曲应力松弛试验,统一数据评价标准,有利于我国中高端连接器、集成电路用材料的研发,具有良好的现实意义。为满足国内外市场对铜及铜合金应力松弛性能的需求,更有效的确保产品质量,因此制定本标准。 2任务来源 全国有色金属标准化技术委员会在广泛征求意见的基础上下发了有色标委[2018]2号《关于转发2018年第一批有色金属国家标准制(修)订项目计划》文件,正式下达了《铜及铜合金弯曲应力松弛试验方法》国家标准(计划号:20173798-T-610)的起草任务。宁波兴业盛泰集团有限公司为负责起草单位。 3项目编制组单位简况 3.1编制组成员单位 本标准由宁波兴业盛泰集团有限公司、宁波兴业鑫泰新型电子材料有限公司、安徽鑫科铜业有限公司、北京有色金属研究总院、中铝华中铜业有限公司、山西春雷铜材有限责任公司、江西金品铜业科技有限公司、中色(宁夏)东方集团有限公司、国家铜冶炼及加工产品质量监督检验中心(山东)、凯美龙精密铜带(河南)有限公司、西北有色金属研究院等共同起草,以上编制组成员单位均是《铜及铜合金弯曲应力松弛试验方法》的应用单位。
蠕变-疲劳载荷下25 Cr2 MoVA 钢的循环应力松弛行为
试 验 研 究 蠕变—疲劳载荷下25Cr2MoVA钢的 循环应力松弛行为 张红才1,3,郑小涛2,轩福贞1,王正东1 (1.华东理工大学承压系统与安全教育部重点实验室,上海 200237;2.武汉工程大学机电工程学院,湖北武汉 430205;3.中国石化湖北化肥分公司,湖北枝江 443200) 摘 要:试验测试了500℃时高温螺栓材料25Cr2MoVA在应变控制的蠕变—疲劳载荷下的循环应力松弛行为,重点考虑了不同应变幅和峰值保持时间对材料应力松弛行为的影响。研究表明,保持阶段的蠕变变形和循环加载阶段的粘塑性变形共同加速了25Cr2MoVA的应力松弛速率,且应变幅小的时候,材料的循环松弛速率更大。 关键词:25Cr2MoVA钢;蠕变—疲劳;应力松弛;螺栓 中图分类号:TH142;TQ050.2;O346.1 文献标志码:A 文章编号:1001-4837(2014)09-0023-05 doi:10.3969/j.issn.1001-4837.2014.09.004 CyclicStressRelaxationBehaviorof25Cr2MoVASteelunder Creep-FatigueLoadings ZHANGHong-cai1,3,ZHENGXiao-tao2,XUANFu-zhen1,WANGZheng-dong1(1.KeyLaboratoryofPressureSystemandSafety(MinistryofEducation),EastChinaUniversityofSci-enceandTechnology,Shanghai200237,China;2.SchoolofMechanicalandElectricalEngineering,Wu-hanInstituteofTechnology,Wuhan430205,China;3.SINOPECHubeiChemicalFertilizerBranch,Zhi-jiang443200,China) Abstract:Cyclicstressrelaxationbehaviorofhigh-temperatureboltmaterial25Cr2MoVAwasinvestiga-tedbystrain-controlledcreep-fatiguetestsat500℃.Theeffectsofdifferentstrainamplitudesandpeakholdtimeonthestressrelaxationbehaviorof25Cr2MoVAsteelwerestressed.Resultsshowedthatcreepdeformationproducedduringpeakholdtimetogetherwiththevisco-plasticdeformationtookplaceduringcyclicloadingstagecommonlyacceleratethestressrelaxationrateof25Cr2MoVAsteel,andthestrainrelaxationrateisgreaterwhenthestrainamplitudeisrelativelysmaller. Keywords:25Cr2MoVAsteel;creep-fatigue;stressrelaxation;bolt 基金项目:国家自然科学基金项目(51305310) ? ?32
蠕变应力松弛
蠕变 定义:蠕变是在应力影响下,固体材料缓慢永久性的移动或者变形的趋势。它的发生是低于材料屈服强度的应力长时间作用的结果。这种变形的速率与材料性质、加载时间、加载温度和加载结构应力有关。取决于加载应力和它的持续时间和环境温度,这种变形可能变得很大,以至于一些部件可能不再发挥它的作用。 阶段过程:1初步蠕变,形变率相对较大,但是随着应变的增加减慢。 2稳态蠕变,形变率达到一个最小值并接近常数,“蠕变应变率”就是指这一阶 段的应变率。 3颈缩现象,应变率随着应变增大指数性的增长。 晶体蠕变(考虑金属) 公式:Q m kT b d C e dt d εσ-= 其中:ε是蠕变应变,C 是一个依赖于材料和特别蠕变机制的常数,m 和b 是依赖于蠕变机制的指数,Q 是蠕变机制的激活能,σ是加载应力,d 是材料的晶粒尺寸,k 是波尔兹曼常数,T 是绝对温度。 位错蠕变 在相对于剪切模量的高应力条件下,蠕变是一个受位错控制的运动。当应力加载在材料上时,由于滑移面中的位错移动而塑性变形发生。 位错蠕变中,self diffusion Q Q -=,46m = ,0b =。因此位错蠕变强烈依赖于加载应力而不依赖于晶粒尺寸。引入初始应力0σ,低于初始应力时无法测量。这样,方程就写成 0()Q m kT d C e dt εσσ-=-。 Nabarro-Herring 蠕变 在N-H 蠕变中,原子通过晶格扩散,造成晶粒沿着应力轴伸长。k 和原子通过晶格的扩散系数有关,self diffusion Q Q -=,1m =,2b =。因此N-H 蠕变是一种弱应力依赖、中等晶
粒尺寸依赖的蠕变,它的蠕变形变率随着晶粒尺寸增长而降低。故公式变化成: 2Q kT d C e dt d εσ- = 上图是相关文献中的表格,按蠕变机理不一样确定指数m (在表中是n ),以及常见金属对应的激活能。 注意:金属蠕变在受力元件温度超过0.3T α(T α是熔点温度)时才开始显现出来,把常见金属熔点温度列出来。 虑蠕变,而铝、锡等金属常常会受到蠕变的影响。所以我们要格外留意长期承受压力的铝合
P91钢蠕变—疲劳交互作用损伤模型及寿命评估.
P91钢蠕变—疲劳交互作用损伤模型及寿命评估 随着现代工业的迅速发展,对于在高温条件下工作的设备,为了保证其 安全性和可靠性,必须考虑蠕变、疲劳及其交互作用对材料寿命的影响。因此, 蠕变/疲劳交互作用下的寿命预测方法对高温部件的设计要求、合理选材以及安全性评估等都具有非常重要的作用。本文对新型耐热钢P91钢的蠕变、疲劳及 其交互作用试验结果进行了分析研究,发现在交互作用下的疲劳寿命比纯疲劳下的寿命值降低了,而蠕变寿命却比纯蠕变下的寿命值提高了。证明在交互作用下蠕变损伤和疲劳损伤的相互影响并非都是促进和加速作用,有时也表现出抑制的作用。采用细观损伤力学的分析方法,当材料受损变形产生微空洞和微裂纹时, 一部分微空洞在循环加载过程中产生拉伸变形逐渐变得细长,最终转化成微裂纹,即每一循环过程中都有一部分蠕变损伤产生的微空洞被消耗掉,转化成了疲劳损伤的微裂纹形式。因此,在这种交互作用的影响下蠕变损伤被抑制,蠕变寿命得 到了提高,而疲劳损伤得到了促进,疲劳寿命值降低。本文在研究线性损伤累积 法及其修正方法中,将蠕变损伤指数和疲劳损伤指数引用到蠕变/疲劳交互作用 损伤模型中。提出了交互作用影响量的概念,根据材料特点定义该影响量为一次循环过程中循环加载对蠕变应变的影响(抑制或促进)量。引入疲劳等效应力作 为疲劳损伤模型的控制参量.建立了以蠕变损伤指数和疲劳损伤指数为基础的蠕变/疲劳交互作用寿命预测模型。应用该模型预测P91钢蠕变/疲劳交互作用下 的寿命值,并与试验值及其他模型的计算值对比。最后应用本文的方法对应变控制模式下的2.25Cr-1Mo钢进行寿命预测。 【相似文献】 [1]. 盛予宁,周纪芗.几个正交表列间的交互作用[J].应用概率统计, 1994,(01) [2]. 沈开锸.对待“交互作用”的两种不同观点的比较[J].数理统计与管理, 1983,(01) [3]. 王钟灵,赵晓燕.也谈正交试验设计法[J].滁州师专学报, 2003,(02) [4]. 刘永政,章志敏.混合型正交表交互作用的考察[J].曲阜师范大学学报(自 然科学版), 1983,(01) [5]. 姬振豫.又证正交表L_(12)(2~(11))列间交互作用的均匀分布性[J].河海 大学常州分校学报, 1995,(04) [6]. 金良超.正交试验法(二)[J].系统工程理论与实践, 1981,(02) [7]. 卢侃,黄来友.美的生物物理学[J].自然杂志, 1991,(05) [8]. 杨锦忠,郝建平.复合污染系统中交互作用分类方法研究[J].中国生态农业学报, 2002,(04) [9]. 刘春光,金相灿,邱金泉,孙凌.光照与磷的交互作用对两种淡水藻类生长的影响[J].中国环境科学, 2005,(01) [10]. 徐联仓.关于人—机交互作用之我见——下一世纪的中心问题之一[J].生命科学, 1990,(05) 【关键词相关文档搜索】:固体力学; P91钢; 蠕变; 疲劳; 交互作用; 损伤 指数; 保载时间 【作者相关信息搜索】:西南交通大学;固体力学;戴振羽;魏峰;
金属材料疲劳研究综述
金属材料疲劳研究综述 摘要:人会疲劳,金属也会疲劳吗?早在100多年前,人们就发现了金属也是会疲劳的,并且发现了金属疲劳带给人们各个方面的危害,所以研究金属材料的疲劳是非常有必要的。本文主要讲述了国内外关于金属疲劳的研究进展,概述了金属产生疲劳的原因及影响因素,以及金属材料疲劳的试验方法。 关键词:金属材料疲劳裂纹疲劳寿命 一.引言 金属疲劳的概念,最早是由J.V.Poncelet 于1830 年在巴黎大学讲演时采用的。当时,“疲劳”一词被用来描述在周期拉压加载下材料强度的衰退。引述美国试验与材料协会( ASTM) 在“疲劳试验及数据统计分析之有关术语的标准定义”( EZ06-72) 中所作的定义: 在某点或某些点承受挠动应力,且在足够多的循环挠动作用之后形成裂纹或完全断裂时,材料中所发生的局部永久结构变化的发展过程,称为“疲劳”。金属疲劳是指材料、零构件在循环应力或循环应变作用下,在一处或几处逐渐产生局部永久性累积损伤,经一定循环次数后产生裂纹或突然发生完全断裂的过程。在材料结构受到多次重复变化的载荷作用后,应力值虽然始终没有超过材料的强度极限,甚至比弹性极限还低的情况下就可能发生破坏,这种在交变载荷重复作用下材料和结构的破坏现象,就叫做金属的疲劳破坏。据统计金属材料失效80%是由于疲劳引起的,且表现为突然断裂,无论材料为韧性材料还是塑性材料都表现为突然断裂,危害极大,所以研究金属的疲劳是
非常有必要的。 由于金属材料的疲劳一般难以发现,因此常常造成突然的事故。早在100多年以前,人们就发现了金属疲劳给各个方面带来的损害。由于但是条件的限制,还不能查明疲劳破坏的原因。在第二次世界大战期间,美国的5000艘货船共发生1000多次破坏事故,有238艘完全报废,其中大部分要归咎于金属的疲劳。2002 年 5 月,华航一架波音747-200 型客机在由台湾中正机场飞往香港机场途中空中解体,19 名机组人员及206名乘客全部遇难。调查发现,飞机后部的金属疲劳裂纹造成机体在空中解体,是导致此次空难的根本原因。直到出现了电子显微镜之后,人类在揭开金属疲劳秘密的道路上不断取得了新的成果,才开发出一些发现和消除金属疲劳的手段。 二.金属疲劳的有关进展 1839年巴黎大学教授在讲课中首先使用了“金属疲劳”的概念。1850一1860年德国工程师提出了应力-寿命图和疲劳极限的概念。1870一1890年间,Gerber研究了平均应力对疲劳寿命的影响。Goodman提出了考虑平均应力影响的简单理论。1920年Griffith发表了关于脆性材料断裂的理论和试验结果。发现玻璃的强度取决于所包含的微裂纹长度,Griffith理论的出现标志着断裂力学的开端。1945年Miner用公式表达出线性积累损伤理论。五十年代,力学理论上对提出应力强度因子K的概念。六十年代,Manson—Coffin公式概括了塑性应变幅值和疲劳寿命之间的关系。Paris在1963年提出疲劳裂纹扩展速率da/dN和应力强度因子幅值?k之间的关系。1974年,美
金属材料蠕变
金属材料蠕变 早期,人们对金属材料强度的认识不足,设计金属构件时仅以短时强度作为设计依据。不少构件,即使使用应力低于弹性极限,使用一段时间后仍然会发生因塑性受形而失效或因破断而失效的现象。随着科学技术的发展,金属材料的使用温度逐步提高,这种矛盾越来越突出。这就使人们进一步认识到材料强度与使用期限之问尚有密切的联系,从而相继开拓了蠕变、蠕变断裂、松弛、疲劳、断裂力学等长时强度研究领域。蠕变则是其中研究最早、内容较丰富而成果较显著的一个领域,成为其他几个研究领域的基础。 金属在持续应力作用下(即使在远低于弹性极限的情况下)会发生缓慢的塑 性变形。熔点较低的金属容易产生这种现象;金属所处的温度越高,这种现象越明显。在一定温度下,金属受持续应力的作用而产生缓慢的塑性变形的现象称为金属的蠕变。引起蠕变的这一应力称蠕变应力。在这种持续应力作用下,蠕变变形逐渐增加,最终可以导致断裂,这种断裂称蠕变断裂。导致断裂的这一初始应力称蜕变断裂应力。在有些情况下(特别是在工程上),把蠕变应力及蠕变断裂应力作为材料在特定条件下的一种强度指标来讨论时,往往又把它们称为蠕变强度及蠕变断裂强度,后者又称为持久强度。蠕变现象的发生是温度和应力共同作用的结果。温度和应力的作用方式可以是恒定的,也可以是变动的。常规的蠕变试验则是专门研究在恒定载荷及恒定温度下的蠕变规律。为了与变动情况相区别,把这种试验称为静态蠕变试验。 蠕变现象很早就被人们发现,远在1905年F. Philips等就开始进行专门研究。最初研究的是铅、锌等低熔点纯金属,因为这些金属在室温下就已表现出明显的蠕变现象。以后逐步研究了较高熔点的铝、镁等纯金属的蠕变现象,进而又研究了铁、镍以至难熔金属钨、铂等的蠕变规律。对纯金属的研究后来又发展到对铁、钴、镍基合金及其他各种高温合金的研究。对这些合金,要求它们在几百度的高温下才能表现出明显的蠕变现象(例如碳钢>0.35Tm,不锈钢>0.4Tm)。 蠕变现象的研究是与工业技术的发展密切相关的。随着工作温度的提高,材料蠕变现象越来越明显,对材料蠕变强度的要求越来越高。不同的工作温度需选用具有不同蠕变性能的材料,因此蠕变强度就成为决定高温金属材料使用价值的重要因素。 蠕变曲线 在恒定温度下,一个受单向恒定载荷(拉或压)作用的试样,其变形e与时间t的关系可用如图9.76所示的典型的蠕变曲线表示。曲线可分下列几个阶段:
蠕变应力松弛相关介绍
蠕变应力松弛相关介绍
————————————————————————————————作者: ————————————————————————————————日期:
蠕变应力松弛相关介绍 百若试验仪器服务范围:全系列电子萬能试验机、全系列电液伺服萬能试验机、全系列电液伺服压力试验机、全系列电液伺服疲劳试验机、应力腐蚀裂纹扩展速率试验机、应力腐蚀慢应变速率试验机、板材成形试验机、杯突试验机、紧固件横向振动疲劳试验机、多功能螺栓紧固分析系统、扭矩轴力联合试验机、松弛试验机、锚固试验机、扭转试验机、冲击试验机、压剪试验机、液压卧式拉力试验机、光缆成套试验设备等。 百若试验仪器就来说说蠕变应力松弛相关介绍 蠕变 定义:蠕变是在应力影响下,固体材料缓慢永久性的移动或者变形的趋势。它的发生是低于材料屈服强度的应力长时间作用的结果。这种变形的速率与材料性质、加载时间、加载温度和加载结构应力有关。取决于加载应力和它的持续时间和环境温度,这种变形可能变得很大,以至于一些部件可能不再发挥它的作用。 阶段过程:1初步蠕变,形变率相对较大,但是随着应变的增加减慢。 2稳态蠕变,形变率达到一个最小值并接近常数,“蠕变应变率” 就是指这一阶段的应变率。 3颈缩现象,应变率随着应变增大指数性的增长
晶体蠕变(考虑金属) 公式: Q m kT b d C e dt d εσ-= 其中:ε是蠕变应变,C 是一个依赖于材料和特别蠕变机制的常数,m 和b 是依赖于蠕变机制的指数,Q 是蠕变机制的激活能,σ是加载应力,d 是材料的晶粒尺寸,k 是波尔兹曼常数,T 是绝对温度。 位错蠕变 在相对于剪切模量的高应力条件下,蠕变是一个受位错控制的运动。当应力加载在材料上时,由于滑移面中的位错移动而塑性变形发生。 位错蠕变中,self diffusion Q Q -=,46m =,0b =。因此位错蠕变强烈依赖于加载应力而不依赖于晶粒尺寸。引入初始应力0σ,低于初始应力时无法测量。这 样,方程就写成0()Q m kT d C e dt εσσ-=-。 N abarro -Herri ng 蠕变 在N -H 蠕变中,原子通过晶格扩散,造成晶粒沿着应力轴伸长。k 和原子通过晶格的扩散系数有关,self diffusion Q Q -=,1m =,2b =。因此N -H 蠕变是一种弱应力依赖、中等晶粒尺寸依赖的蠕变,它的蠕变形变率随着晶粒尺寸增长而降 低。故公式变化成:2Q kT d C e dt d εσ- =
对蠕变的初步认识
对蠕变的初步认识 温度对金属材料力学性能的影响很大,随着温度升高,材料的强度降低而塑性增加;而材料在高温下,载荷持续时间对力学性能也会产生影响。因此,在高温下工作的材料,其力学性能与温度和时间两个因素有关。所谓高温,是指金属 的服役温度超过了它的再结晶温度约0.4~0.5T m ,T m 是金属的熔点。在这样的高温 下长时服役的金属,其微观结构、形变和断裂机制都会发生变化,在宏观上则会出现高温蠕变、持久断裂、应力松弛、高温腐蚀等现象。 材料在恒定应力作用下,其应变随时间的延长而逐渐增加的现象称为蠕变。由于蠕变而导致的断裂称为蠕变断裂。金属在低温下也会产生蠕变,但通常只有当温度升高到0.3T m 以上时,蠕变现象才会比较显著。金属在高温下还会发生应力松弛现象,即在保持应变恒定的情况下,应力随着时间延长而减小的现象。由于蠕变和应力松弛的发生,应力和应变之间已不是单值的对应关系,而必须考虑温度和时间的影响。 温度对金属材料力学性能的影响很大,随着温度升高,材料的强度降低而塑性增加;而材料在高温下,载荷持续时间对力学性能也会产生影响。因此,在高温下工作的材料,其力学性能与温度和时间两个因素有关。所谓高温,是指金属 的服役温度超过了它的再结晶温度约0.4~0.5T m ,T m 是金属的熔点。在这样的高温 下长时服役的金属,其微观结构、形变和断裂机制都会发生变化,在宏观上则会出现高温蠕变、持久断裂、应力松弛、高温腐蚀等现象。 1. 蠕变曲线 蠕变:材料在恒定应力作用下,其应变随时间的延长而逐渐增加的现象称为蠕变。由于蠕变而导致的断裂称为蠕变断裂。金属在低温下也会产生蠕变,但通常只有当温度升高到0.3T m 以上时,蠕变现象才会比较显著。金属在高温下还会发生应力松弛现象,即在保持应变恒定的情况下,应力随着时间延长而减小的现象。由于蠕变和应力松弛的发生,应力和应变之间已不是单值的对应关系,而必须考虑温度和时间的影响。 蠕变曲线:常载荷条件下的典型单轴蠕变曲线见图1 , 从图中可以看出蠕变的3 个典型阶段: 第一蠕变阶段AB (减速蠕变阶段),第二蠕变阶段BC (稳定蠕变阶段),第三阶段蠕变CD(加速蠕变阶段) 。在第二蠕变阶段(稳定蠕变阶段) , 蠕变速率近似为常数; 而在第三蠕变阶段, 蠕变速率逐渐增加,直至试件完全破坏。图1 中εe 代表瞬时弹性(或弹塑性) 应变,εp表示塑性应变,εc代表蠕变应变。
预应力钢材拉伸应力松弛实验作业指导书
预应力钢绞线应力松弛性能试验作业指导书 一目的 明确预应力钢绞线松弛试验程序、操作流程、工艺要点以及控制标准,检测预应力钢绞线应力松弛性能,指导检测员按规程正确操作,保证检测结果科学、准确。 二适用范围 本作业指导书适用于钢绞线松弛性能任务。 三预应力钢绞线选用 a、预应力钢绞线符合1×7-15.2-1860-GB/T5224-2003的要求。供应商提供每批钢绞线的实际弹性模量值,质量保证单。 b、每批钢绞线附有出厂合格证,由同一批号、同一强度等级的钢绞线组成。实验前,外观检查合格后,再按GB/T228-2002的要求做钢绞线应力松弛性能试验和最大应力试验,合格后方可使用。 c、钢绞线的力学性能 ①见钢绞线尺寸及力学性能指标表。 表4-1 钢绞线尺寸及力学性能指标表 钢绞线结构钢绞线公 称直径mm 抗拉强 度MPa 整根钢绞 线的最大 力KN 规定非比 例延伸力 KN 最大力 总伸长 率% 应力松弛性能 初始负荷相 当于公称最 大力的百分 数(%) 1000h后应力松 弛率,(%) 不大于 1×7 标 准 型 15.20 不小于 1860 260 234 3.5 80 4.5 注:①规定非比例延伸力值不小于整根钢绞线公称最大力的90%。 ②每一交货批钢绞线的实际强度不能高于其抗拉强度级别200MPa。
③钢绞线弹性模量为(195±10)GPa。 ④采用推算法确定1000h松弛率。 d、表面质量:钢绞线表面不得有油、润滑脂等物质,允许有轻微的浮锈,但不 得有目视可见的锈蚀麻坑,表面允许存在回火的颜色。 f、取样数量 序号检验项目取样数量取样部位检验方法要求 1 表面逐盘卷目视见表面质量要求 2 应力松弛性能不小于1根/ 每合同批 [注] 2.5m 在每 (任)盘 卷中任意 一端截取 按TB10120执行 注:合同批为一个订货合同的总量。在特殊情况下,松弛试验可以由工厂连续检验提供同一原料、同 一生产工艺的数据所代替。 四预应力试验设备及工具配置 试验设备、工具配置及性能指标 序号设备及工具名称型号单位数量性能指标要求 1 微机控制拉伸应力松弛 试验机 WSC-300 台 1 2 卷尺把 1 3 砂轮切割机台 1 五检测步骤 1、将钢绞线套上夹具,放在试验机上(试验温度20±2℃,试样置于此环境中足够时间,确保 达到温度平衡后施加初始力试验) 2、打开软件,依照委托信息设定好钢绞线直径和强度等信息。 3、启动试验(除非相关标准或协议另作规定,应在3—5分钟内均与施加全部初始应力) 4、达到100小时后,试验结束,记录推算的1000小时应力松弛率 5、打印试验记录,关闭计算机和电源 6、取出试验机上的钢绞线,填写仪器使用记录。
复杂加载条件下压力容器典型用钢疲劳蠕变寿命预测方法
第45卷第2期2009年2月 机械工程学报 JOURNAL OF MECHANICAL ENGINEERING Vol.45N o.2 Feb. 2009 DOI:10.3901/JME.2009.02.081 复杂加载条件下压力容器典型用钢 疲劳蠕变寿命预测方法* 陈学东范志超江慧丰董杰 (合肥通用机械研究院国家压力容器与管道安全工程技术研究中心合肥 230031) 摘要:针对多轴应力状态,探讨压力容器典型用钢16MnR缺口试样的高温疲劳与循环蠕变交互作用行为,在延性耗竭理论和损伤力学基础上,建立一种半寿命平均位移速率寿命预测模型,采用该方法对不同缺口半径试样的高温疲劳寿命进行了较好的预测。针对多级加载条件,研究316L钢的循环变形行为,探讨疲劳蠕变与动态应变时效之间的耦合作用,在延性耗竭理论基础上,建立非线性损伤演化模型,考虑多级加载时的载荷历程效应,提出一种新的损伤累积准则,采用该方法对二级加载条件下的疲劳蠕变寿命进行了较好的预测。 关键词:多轴多级疲劳蠕变损伤寿命预测 中图分类号:O346.2 TG142.33 Creep-fatigue Life Prediction Methods of Pressure Vessel Typical Steels under Complicated Loading Conditions CHEN Xuedong FAN Zhichao JIANG Huifeng DONG Jie (National Engineering Technology Research Center on PVP Safety, Hefei General Machinery Research Institute, Hefei 230031) Abstract:With emphasis on complicated loading conditions, i.e. multi-axial loading condition and multi-step loading condition, creep-fatigue behavior and life prediction methods are investigated for typical steels of pressure vessels. As to multi-axial loading condition, the interaction behavior between high temperature fatigue and cyclic creep is discussed for 16MnR notched specimens and a mean displacement rate life prediction method is proposed on the basis of ductility exhaustion theory and damage mechanics. By this method, high temperature fatigue lives are well predicted for specimens with different notch radiuses. As to multi-step loading condition, cyclic deformation behavior is investigated for 316L steel and creep-fatigue interaction coupled with dynamic strain aging effect is also discussed. Based on the ductility exhaustion theory, a nonlinear damage evolution model is developed. Moreover, a new damage cumulated rule is proposed with the load history effect taken into account. By using this model, 2-step creep-fatigue lives are well predicted. Key words:Multi-axis Multi-step Creep-fatigue Damage Life prediction 0 前言 高温环境下长期服役的压力容器在设计和安全评定时除了要考虑疲劳损伤、蠕变损伤及疲劳蠕变交互作用损伤外,还要考虑多轴载荷、多级载荷 * “十一五”国家科技支撑计划专题(2006BAK02B02-02)和安徽省优秀青年基金(08040106827)资助项目。20081118收到初稿,20081225收到修改稿等复杂条件对承压设备寿命的影响。 本课题组在“十五”科技攻关期间,主要针对压力容器典型材料开展了高温疲劳及疲劳蠕变交互作用行为研究[1-3],分别从能量、韧性、延性角度提出了几种高温疲劳蠕变寿命预测和损伤评估方法[4]。但前期研究并没有考虑复杂应力状态和复杂加载历史对疲劳及疲劳蠕变行为的影响,而实际承压设备的缺口或应力集中部位始终是整个结构的薄
应力松弛试验机
应力松弛试验机 微机控制预应力松驰试验机 一、产品简介 WD-RE300型微机控制松弛试验机在设计过程中,吸收了德国、意大利等著名松弛试验机公司的设计理念和结构特点,并依据螺纹钢松弛试验、钢绞线松弛试验、PC钢棒松弛试验的相关国家标准研制而成的,专用于钢绞线、PC钢棒、镀锌钢丝及螺纹钢筋等材料的松弛试验。是专门针对制造、使用厂家而设计。该系列试验机主要用于螺纹钢筋、钢绞线、PC钢棒的松弛试验,可检测金属线材的单轴拉伸松弛强度等特性。可广泛用于质检部门、建筑施工单位、钢铰线和钢筋生产企业,是现代建筑力学试验的新型试验设备。满足 GB/T20065-2006《预应力混凝土用螺纹钢筋》,GB/T10120-1996《金属应力松弛试验方法》。技术参数 1.试验力 最大试验力:300kN 有效测量范围:2%~100%FS 示值相对误差:±1% 2.试验速度 调速范围:0.001-25mm/min 示值相对误差: ±0.5% 3.主机 试验机主机形式: 卧式结构 拉伸最大空间:1000-1200mm 同轴度:15%以内 4.试样规格 Φ11.10;Φ12.70;Φ15.24mm(公称直径) 5.保护功能: 超过最大试验力2%-5%时自动停机 6.主机尺寸(长*宽*高): 1800x710x1500mm 三、功能特点:
1.PC机实现了控制模式的闭环控制以及试验过程的程序控制,各种控制方式之间可无冲击切换。计算机自动完成试验过程的控制、数据采集、显示和保存(主要参数:试验力、松弛力、松弛率或对数松弛率),试验完成后可以对数据进行分析和处理,并打印输出用户要求的试验曲线及试验报告,可选择标准要求的各种试验曲线(可绘制剩余试验力或对数剩余力、松弛力或对数松弛力、松弛率或对数松弛率、温度等跟时间或对数时间的关系曲线)。 2. 计算机软件基于Windows98/Windows2000/Windows XP平台开发,界面美观,操作方便;试验力、变形显示采用组态仪表方式显示,十分醒目;内嵌数据库,便于数据历史追溯及联网要求;报表采用模板方式操作,用户只需简单培训即可掌握,整个软件封装性强,操作方便、功能全面;设有标准试验程序,按下快捷键,试验系统就可以按照标准要求在3-5分钟内将钢绞线加载公称最大力的70%或80%,保持1分钟内自动开始记录试验数据、到达设定时间后自动终止试验。试验曲线与理论拟合曲线的相关系数达到99%以上,因此计算机能以100小时以内的试验数据推算1000小时的试验结果,也可以进行1000小时的连续试验,缩短了实际实验时间。
疲劳分析方法
疲劳寿命分析方法摘要:本文简单介绍了在结构件疲劳寿命分析方法方面国内外的发展状况,重点讲解了结构件寿命疲劳分析方法中的名义应力法、局部应力应变法、应力应变场强度法四大方法的估算原理。 疲劳是一个既古老又年轻的研究分支,自Wohler将疲劳纳入科学研究的范畴至今,疲劳研究仍有方兴未艾之势,材料疲劳的真正机理与对其的科学描述尚未得到很好 的解决。疲劳寿命分析方法是疲分研究的主要内容之一,从疲劳研究史可以看到疲劳寿 命分析方法的研究伴随着整个历史。 金属疲劳的最初研究是一位德国矿业工程帅风W.A.J.A1bert在1829年前后完成的。他对用铁制作的矿山升降机链条进行了反复加载试验,以校验其可靠性。1843年,英国铁路工程师W.J.M.Rankine对疲劳断裂的不同特征有了认识,并注意到机器部件 存在应力集中的危险性。1852年-1869年期间,Wohler对疲劳破坏进行了系统的研 究。他发现由钢制作的车轴在循环载荷作用下,其强度人大低于它们的静载强度,提出 利用S-N曲线来描述疲劳行为的方法,并是提出了疲劳“耐久极限”这个概念。1874 年,德国工程师H.Gerber开始研究疲劳设计方法,提出了考虑平均应力影响的疲劳寿 命计算方法。Goodman讨论了类似的问题。1910年,O.H.Basquin提出了描述金属 S-N曲线的经验规律,指出:应力对疲劳循环数的双对数图在很大的应力范围内表现为 线性关系。Bairstow通过多级循环试验和测量滞后回线,给出了有关形变滞后的研究 结果,并指出形变滞后与疲劳破坏的关系。1929年B.P.Haigh研究缺口敏感性。1937 年H.Neuber指出缺口根部区域内的平均应力比峰值应力更能代表受载的严重程度。 1945年M.A.Miner在J.V.Palmgren工作的基础上提出疲劳线性累积损伤理论。 L.F.Coffin和S.S.Manson各自独立提出了塑性应变幅和疲劳寿命之间的经验关系,即 Coffin—Manson公式,随后形成了局部应力应变法。