半成品标识卡
标识卡管理应用规范

标识卡管理应用规范-标准化文件发布号:(9456-EUATWK-MWUB-WUNN-INNUL-DDQTY-KII5.1.3检验状态使用《产品状态标识卡》,检验结果附注《工艺流程卡》5.1.4当顾客有要求时,最终产品按顾客的要求进行标识。
5.2标识的实施5.2.1原材料进厂,由仓库安排存放到“待检”区域,并依据订购单、送货单对产品进行核对标识,明确显示物料名称,物料编号,规格,生产批次号,来料数量(数量标识必须涵盖产品范围,如一个批次号一拖产品为21箱,数量为2020,则可标识为20箱*100+20=2020只,凡填写标识卡人员都参照此方式填写数量),日期等;5.2.2由仓库填写《进料送检单》通知品质验货;5.2.3品质部检验员依据检验标准、承认样品、相应的采购信息或取少量样品等对来料进行检验/验证,并依据检验/验证结果进行产品状态标识,标识需清晰完整;合格产品办理入库手续,并由检验员填写相应《产品状态标识卡》;不合格产品存放到不合格区域和进行不合格标识,并通知相关职能部门按《不合格品控制程序》执行;5.2.4生产过程中,操作者自检出的不合格品,由操作者进行隔离,生产班组长及品质部检验员进行确认,并由生产班组长进行产品标识,检验员进行检验状态标识;不合格品按《不合格品控制程序》进行处理;5.2.5生产的最终产品由仓库以《物料标识卡》标识和填写《成品送检单》报检,品质部检验员依据检验结果进行检验状态标识;5.2.6产品生产批次号的标识:在产品生产完成后,生产线负责填写产品的生产记录,记录入产品的制造时间或日期,品质部OQC须在包装外箱上盖检验合格章(表明检验之状态与日期)。
5.3标识的管理5.3.1各种标识由产品存放所在地的管理人员进行管理,任何人不得随意撕毁和移动,应保持各种标识的完整性和准确性;5.3.2当标识发生丢失或移动时,根据相关记录或重新检验后进行标识;●同产品质量相关的流程单、印章等标识的使用应由品质部全面监控和管理。
产品追溯管理制度
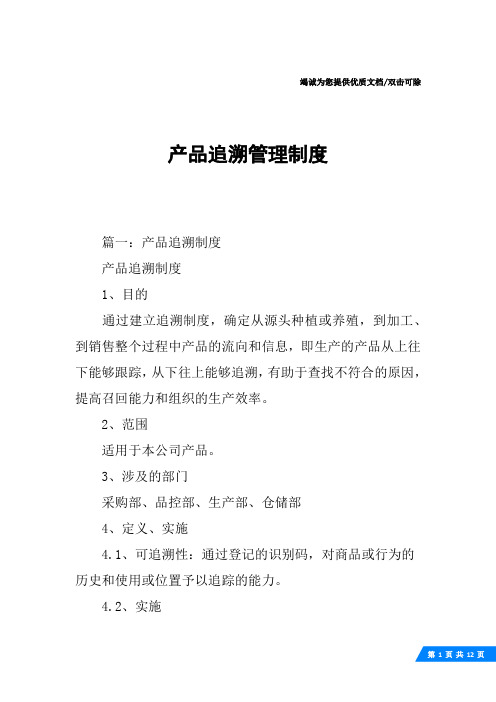
竭诚为您提供优质文档/双击可除产品追溯管理制度篇一:产品追溯制度产品追溯制度1、目的通过建立追溯制度,确定从源头种植或养殖,到加工、到销售整个过程中产品的流向和信息,即生产的产品从上往下能够跟踪,从下往上能够追溯,有助于查找不符合的原因,提高召回能力和组织的生产效率。
2、范围适用于本公司产品。
3、涉及的部门采购部、品控部、生产部、仓储部4、定义、实施4.1、可追溯性:通过登记的识别码,对商品或行为的历史和使用或位置予以追踪的能力。
4.2、实施4.2.1本公司通过对原辅料和产成品实施批号管理,建立进货验收记录、生产记录、入库记录、出库发货记录、销售记录,根据批号管理实现追溯。
4.2.2蔬菜类原料,需由采购部要求供应商提供“品质保证书”(包含:品名、生产批号、重量、种植地及种植地的土壤状况、农药使用情况等);4.2.3肉类原料需由采购部要求供应商提供“品质保证书”(包含:品名、生产批号、重量、养殖地、饲料情况、兽药的使用情况等);4.2.4原料进厂,由仓储部通知品控部,对货物进行进厂检查。
品控部接到通知后对原料进行验收,并按时做好记录,需包含:品名、生产日期、供应商、规格、数量、感官或技术要求等,检验合格后通知仓储部。
4.2.5入库:仓储部接到品控部通知后,将原料入库,并做好原料入库记录(包含:来货日期、品名、生产日期、数量、供应商、原料状态(合格/不合格)、库位),原料入库上架后,库房应做好标识管理(包含:品名、进货日期、数量、供应商、生产日期、保质期);4.2.6车间领用,库房应做好原料出库记录(包含:日期、品名、出库数量、剩余数量、去向、领用人等),车间应做好原料领用记录(包含:日期、品名、数量、用途、领用人等);4.2.7车间生产,应做好生产记录(包含:日期、成品名称及生产批次、成品数量、所用的所有原辅料的数量及批次、记录人、审核人等)。
4.2.8成品入库:由生产部和仓储部做好成品交付记录(日期、品名、数量、批次、生产人员、仓储部人员签字),仓储部做好成品入库记录(包含:日期、品名、生产日期、数量、成品状态(合格/不合格/待检),成品进库上架,库房做好标识管理(包含:品名、数量、生产日期、保质期、成品状态(合格/不合格/待检)等)。
生产车间数据管理规范
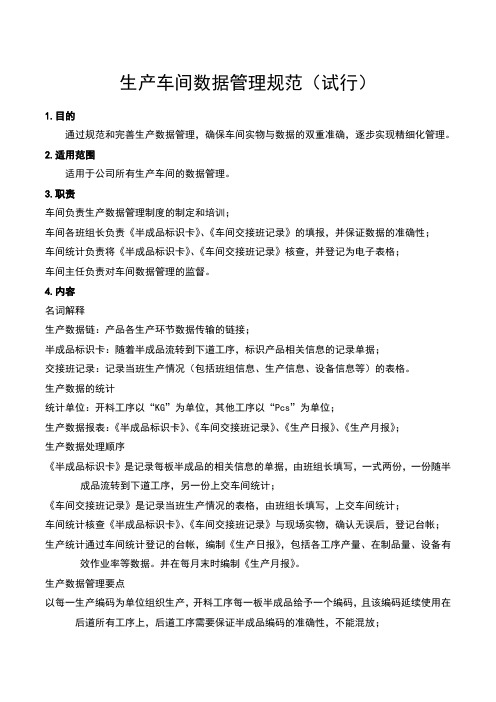
生产车间数据管理规范(试行)1.目的通过规范和完善生产数据管理,确保车间实物与数据的双重准确,逐步实现精细化管理。
2.适用范围适用于公司所有生产车间的数据管理。
3.职责车间负责生产数据管理制度的制定和培训;车间各班组长负责《半成品标识卡》、《车间交接班记录》的填报,并保证数据的准确性;车间统计负责将《半成品标识卡》、《车间交接班记录》核查,并登记为电子表格;车间主任负责对车间数据管理的监督。
4.内容名词解释生产数据链:产品各生产环节数据传输的链接;半成品标识卡:随着半成品流转到下道工序,标识产品相关信息的记录单据;交接班记录:记录当班生产情况(包括班组信息、生产信息、设备信息等)的表格。
生产数据的统计统计单位:开料工序以“KG”为单位,其他工序以“Pcs”为单位;生产数据报表:《半成品标识卡》、《车间交接班记录》、《生产日报》、《生产月报》;生产数据处理顺序《半成品标识卡》是记录每板半成品的相关信息的单据,由班组长填写,一式两份,一份随半成品流转到下道工序,另一份上交车间统计;《车间交接班记录》是记录当班生产情况的表格,由班组长填写,上交车间统计;车间统计核查《半成品标识卡》、《车间交接班记录》与现场实物,确认无误后,登记台帐;生产统计通过车间统计登记的台帐,编制《生产日报》,包括各工序产量、在制品量、设备有效作业率等数据。
并在每月末时编制《生产月报》。
生产数据管理要点以每一生产编码为单位组织生产,开料工序每一板半成品给予一个编码,且该编码延续使用在后道所有工序上,后道工序需要保证半成品编码的准确性,不能混放;各工序也需要对本工序的原料及产品堆放进行区分,分区域集中放置,并做好现场标识。
生产数据管理的其他问题各报表填制的数量必须严格按照当班生产数量,不得私自调整数量和更改车间报表;期初库存:是指每月月底实盘数量结转为下月期初库存,起止时间与财务核算时间一致;5.相关表格《半成品标识卡》;《车间交接班记录》;《生产日报》;《生产月报》。
检验规范(B类)

常州市捷阜电子有限公司检验文件汇编版本号:2011年A版实施日期: 2011年8月15日目录1、原辅材料进货检验规范------------------JF/JS-JY-01A2、过程检验规范--------------------------JF/JS-JY-02A3、成品检验规范--------------------------JF/JS-JY-03A4、成品抽样检验规范----------------------JF/JS-JY-04A5、原辅材料重检检验规范--------------------JF/JS-JY-05A原辅材料进货检验规范JF/JS-JY-01A过程检验规范JF/JS-JY-02A 1、作业内容:1.1下表中所列出的每一道工序批量生产前,都应由过程检验人员进行首件检查,合格后方可继续生产。
1.2产品正常生产过程中,每一道工序,至少巡回检查一次。
1.3抽样数:首检检查1件或1件以上,巡回检验至少2件或2件以上。
2、过程检验人员依据下表所列项目和要求进行检查并填写“生产工序流转卡”。
成品检验规范JF/JS-JY-03A成品抽样检验规范JF/JS-JY-04A1、主题内容本标准规定了本公司以合格质量水平为质量指标的一次抽样方案及抽样程序。
2、适用范围本程序适用本公司所有的出厂产品的抽样程序的允收标准。
3、引用标准GB2828.1—2003 逐批检查计数抽样程序及抽样表GB2828.1—2003 一般检查水平Ⅱ4、术语和符号4.1样本大小(n):样本中所包含的样本单位数,称为样本大小。
4.2合格质量水平(AQL):在抽样检查中,认为可以接受的连续提交检查批的过程平均上限值,称为合格质量水平。
4.3合格判定数(Ac):作出批合格判断样本中所允许的最大不合格品数或不合格数,称为合格判定数。
4.4不合格判定数(Re):作出批不合格判断样本中所不允许的最小不合格品数或不合格数,称为不合格判定数。
车间物料标识卡

车间物料标识卡车间物料标识卡是一种用于标识车间内各种物料的工具,它能够提供物料的基本信息和使用指导,方便车间人员进行物料管理和使用。
下面是车间物料标识卡的标准格式文本:一、物料基本信息1. 物料名称:XXX(根据实际物料名称填写)2. 物料编号:XXX(根据实际物料编号填写)3. 物料规格:XXX(根据实际物料规格填写)4. 物料材质:XXX(根据实际物料材质填写)5. 物料分量:XXX(根据实际物料分量填写)6. 物料体积:XXX(根据实际物料体积填写)7. 物料颜色:XXX(根据实际物料颜色填写)8. 物料供应商:XXX(根据实际物料供应商填写)二、物料使用指导1. 使用方法:XXX(根据实际物料使用方法填写)2. 注意事项:XXX(根据实际物料使用注意事项填写)3. 存放要求:XXX(根据实际物料存放要求填写)4. 使用环境:XXX(根据实际物料使用环境填写)5. 维护保养:XXX(根据实际物料维护保养方法填写)三、物料安全信息1. 安全等级:XXX(根据实际物料安全等级填写)2. 防护措施:XXX(根据实际物料防护措施填写)3. 废弃处理:XXX(根据实际物料废弃处理方法填写)4. 紧急救援:XXX(根据实际物料紧急救援方法填写)四、物料更换记录1. 更换时间:XXX(根据实际物料更换时间填写)2. 更换原因:XXX(根据实际物料更换原因填写)3. 更换人员:XXX(根据实际物料更换人员填写)4. 更换结果:XXX(根据实际物料更换结果填写)五、物料验收记录1. 验收时间:XXX(根据实际物料验收时间填写)2. 验收人员:XXX(根据实际物料验收人员填写)3. 验收结果:XXX(根据实际物料验收结果填写)4. 备注:XXX(根据实际物料验收情况填写)六、其他信息1. 供应商联系方式:XXX(根据实际物料供应商联系方式填写)2. 物料生产日期:XXX(根据实际物料生产日期填写)3. 物料有效期:XXX(根据实际物料有效期填写)4. 物料批次:XXX(根据实际物料批次填写)以上是车间物料标识卡的标准格式文本,通过填写相关信息,可以提供物料的基本信息和使用指导,匡助车间人员进行物料管理和使用。
QC管控流程图
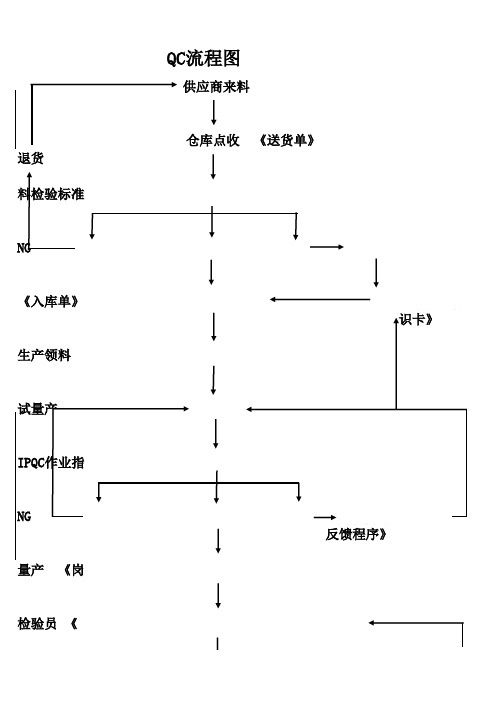
标识卡》
《来料检验标准书》 IQC检验 《来料检验记录表》
NG
OK
NG
特采《特采管制程序》
《入库单》 原材料入库
IQC标示
《半成品标识卡》 生产领料 《领料单》
试量产
《IPQC作业指引》 IPQC首检 《装配()线首检/巡检记录表》
NG
OK
NG
《品质异常反馈单》 《品质异常反馈程序》
供应商来料仓库点收送货单退货半成品标识卡生产领料领料单试量产品质异常反馈程序量产岗位作业指引检验员制程检验标准书返工品质异常反馈程序成品包装仓库点收入库单qc流程图来料检验标准书iqc检验来料检验记录表ngokng特采特采管制程序入库单原材料入库iqc标示ipqc作业指引ipqc首检装配线首检巡检记录表ngokng品质异常反馈单ipqcipqc作业指引ng报废okng不良品质异常反馈单出货检验标准书oqc出货检验记录表品质异常反馈程序不良标示成品出货不良品管制程序ng报废okng不良品质异常反馈单
量产
《岗位作业指引》
检验员 《制程检验标准书》
返工 IPQC《IPQC作业指引》
NG报废
OK
NG不良
《品质异常反馈单》 《品质异常反馈程序》
成品包装
仓库点收
入库单
《出货检验标准书》 OQC 《出货检验记录表》
NG报废
OK
NG不良
《品质异常反馈单》 《品质异常反馈程序》
不良标示
成品出货
《不良品管制程序》
标识卡管理应用规范
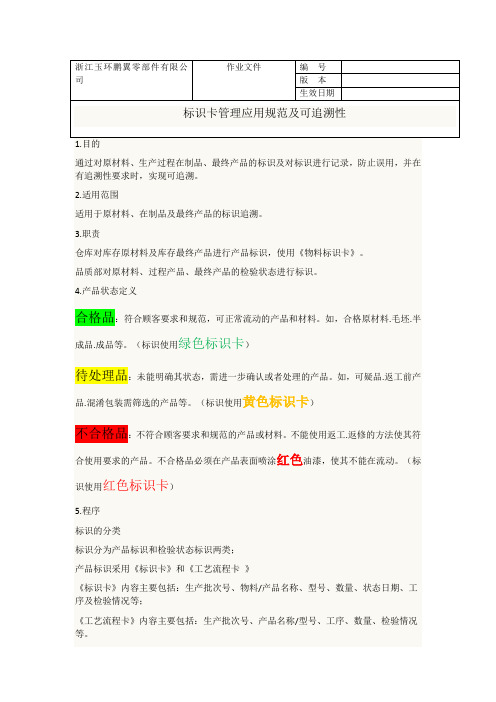
检验状态使用《产品状态标识卡》,检验结果附注《工艺流程卡》当顾客有要求时,最终产品按顾客的要求进行标识。
标识的实施原材料进厂,由仓库安排存放到“待检”区域,并依据订购单、送货单对产品进行核对标识,明确显示物料名称,物料编号,规格,生产批次号,来料数量(数量标识必须涵盖产品范围,如一个批次号一拖产品为21箱,数量为2020,则可标识为20箱*100+20=2020只,凡填写标识卡人员都参照此方式填写数量),日期等;由仓库填写《进料送检单》通知品质验货;品质部检验员依据检验标准、承认样品、相应的采购信息或取少量样品等对来料进行检验/验证,并依据检验/验证结果进行产品状态标识,标识需清晰完整;合格产品办理入库手续,并由检验员填写相应《产品状态标识卡》;不合格产品存放到不合格区域和进行不合格标识,并通知相关职能部门按《不合格品控制程序》执行;生产过程中,操作者自检出的不合格品,由操作者进行隔离,生产班组长及品质部检验员进行确认,并由生产班组长进行产品标识,检验员进行检验状态标识;不合格品按《不合格品控制程序》进行处理;生产的最终产品由仓库以《物料标识卡》标识和填写《成品送检单》报检,品质部检验员依据检验结果进行检验状态标识;产品生产批次号的标识:在产品生产完成后,生产线负责填写产品的生产记录,记录入产品的制造时间或日期,品质部OQC须在包装外箱上盖检验合格章(表明检验之状态与日期)。
标识的管理各种标识由产品存放所在地的管理人员进行管理,任何人不得随意撕毁和移动,应保持各种标识的完整性和准确性;当标识发生丢失或移动时,根据相关记录或重新检验后进行标识;●同产品质量相关的流程单、印章等标识的使用应由品质部全面监控和管理。
追溯性实施物品批次的相关追溯要记录在《标识卡》、《进料验收单》上,详细记录供应商(或客供品名)、收料日期、送货单NO、采购单NO等。
可能时记录物品的生产日期(来料日期)。
入库时在物品《标识卡》上记录部品的品名、来料批号、出入库情况。
仓库先进先出管理制度

仓库先进先出管理制度1.目的规范物料的管理,提高物料在有效期内使用率和产品的合格率,根据生产日期、入库日期与月+年份标识先进先出。
2.范围与定义2.1本公司所有库存物料。
(成品、半成品、原材料)2.2先进先出:物料出库的时间按入库时间的顺序进行,把最先入库的最先出库。
2.3物料有效期:物料规定的有效期限。
3.职责3.1物管部:仓管员负责对物料的先进先出管制和送检。
3.2品管部:负责对超过库存期限的物料进行重检。
4.相关表单:《入库单》《领料单》《仓库物料管制卡》《产品标识卡》《成品标识卡》。
5.工作流程和内容5.1半成品的入库:半成品入库时,收货仓管员核对产品《产品标示卡》信息,若属于外购料需有采购单号,经品管部盖有QC合格章,无误后定位摆放,并在《仓库物料管制卡》填写年月日、入仓数量、结存数量,最后在经手人栏签名。
5.2原材料入库:原材料入库时,收货仓管员必须核对供应商的产品《标识卡》,内容有供应商、采购单号、物料编号、产品名称、交货数量、检验结果、来料日期,经IQC检验合格后加贴月+年份颜色标识,方可安排入库,并在《仓库物料管制卡》填写年月日、入仓数量、结存数量,最后在经手人栏签名。
5.3成品入库:包装部根据客户要求包装后,收货仓管员核对《成品标示卡》信息,且经OQC检验合格后安排入库。
入库时加贴月+年份颜色标识,并在《仓库物料管制卡》填写年月日、入仓数量、结存数量,最后在经手人栏签名。
5.4半成品、成品、原材料摆放指定区域仓位时,应做到以下要求:A:对于货架摆放的物料,必须先把里面的物料腾出外面来,把新进的物料放入里面,并整齐摆放好。
B:对于叠加式物料摆放,必须先把原先的物料腾放在一边,然后将新进物料置于底部,再把原先材料放置上面。
5.5仓管员在发放半成品、原材料、成品时,按以下四步操作:第一步:了解《仓库物料管制卡》结存构成情况关系,再运算应发数量中具体的数量对应的日期范围。
第二步:通过目视找出月+年份标识与《产品标示卡》的来料具体日期的物料。