直齿圆柱齿轮精锻成形工艺和模具设计的研究现状
基于上限法的直齿圆柱齿轮精锻成形研究

分 ,每 个 部分 又划 分 3 个 区域 , 假设 = , 卢为 力角 。 阱 ,r 分 别表 示 区域 用 。), 1 2 I、 、 I Ⅲ的径 向速 度 。), I 、 2 分 别表 示 域 I、 Ⅲ的 I F 0 Ⅱ、 周 向速度 , 表达式 分别如 下 : 域 】: 。 = O () 2
(口,)r—[C2 J r1 =(l1 - ) ' ± 9 ( 0 。 ) 一 抒
‘ 3 ’
域: Ⅱ
,) 砉lC2 —) = 1 干 I( j + z
‘ 4 )
( 5 )
非均匀分布动可容速度场。 直齿 网值 齿轮精 锻成形 的T作 简 图如图 1a所 示 , () 建
维普资讯
设计 与计算
基于上限法的 直齿圆 轮精锻成形研究 柱齿
陈丰 。 夏显 明 , 张华 ( 安徽 科技学院 工学院 , 安徽 蚌埠 2 3 0 3 10
摘
要: 精锻成 形是直齿 圆柱齿轮加工 的重 要方法, 其能够提高齿 轮的强度 、 耐磨性并节省加工材 料。 利用上 限法, 由有
行程曲线进行了计算机模拟 。但 由于直齿 柱齿轮精锻 J 成形的复杂性 , 影响因素众多 , 目前的研究战果还不足以
得到 实用 性 强 的生 产 模 型 本 文 利用 E限法 建 讧了直 齿
变形体的非均匀速度分
布。 如 2所爪 , 整个 变 形L 为 2 叠分 n个 l 同部 卞 目
如 图 1 }所 示 的 圆柱 坐 标 系 , 标 系 的原 点 住 中心 线 () 】 坐 ( ) , 柱坯 料 以 中心 面 为荩 准变 形 , 同 中心 基准 而 I 削定 不 动 , 而我 们假设 的非均 匀 动 可容速 度场 不 同= ・ 的 ^ 殳 r 般 均 匀速 度 场 , 比较 接 近浮 动 『模 的模 型 , 样 我 f假 设 毛 L r 】 这 r 】
论精密锻造设备研究现状及发展

3.1采用新型多元化材料
针对当前我国的机械零部件加工制造过程进行分析,往往的制造原材料都是选择为黑色金属,当前,随着社会需求的多样化发展,以及对于生产加工器械方面的要求越来越高,单一化的材料组成往往难以符合机器零部件的生产要求。所以,在未来的零部件加工制造产业中,原材料的新型多元化发展则是必然的趋势所在,也是发展的方向所在。
3.2工件质量进一步提高
针对零部件的精密锻造环节来说,相应工序相互间存在着比较大的压力,这样的情况下,所涉及到的生产设备、模具以及工业零部件都可能存在着弹性变形的问题,这种情况难以避免,但这种问题不引起重视则会影响到锻造工件的精密程度。随着我国工业建设进程的快速发展,各行各业呈现出快速的发展速度,其必然涉及到多样化的设备用途,在此过程中,相应的设备中的不同机械零部件往往具有较大的差异化情况,这样传统的单一化生产工艺难以符合实际的生产需求[3,4]。在实践情况中,则应该重视如何提升符合实际需求的多样化零部件的加工计划,并能有效结合实践中存在的问题,相互协作来提供满足机械零部件具有更为广泛的应用空间,从而能全面实现工件质量的提升。
2.2精密锻造模具的设计要点
相比于一般的锻造技术来说,精密锻造中的磨具往往承压更高,相关的模具形态以及尺寸则会使得锻造成型的工件质量直接受到影响,这样往往会造成综合质量的更高要求。所以,在具体的设计精锻模具的环节中,则应该重视相应的设计要点,全面有效实现模具的综合性能得到提升。针对锻造中的零部件进行分析,其在相应的摩擦力、变形压力的作用下,往往会出现精锻模具存在相应的弹性变形问题,这个方面则是设计人员所不应该忽视的重要内容,设计模具则应重点考虑这方面的影响因素,结合合理计算以及反复实验的方式,能较为科学合理地来测算相应的模具变形程度,并结合实际情况开展模具形态设计时,选择合理的补偿方案[2]。
国内齿轮研究现状及问题研究
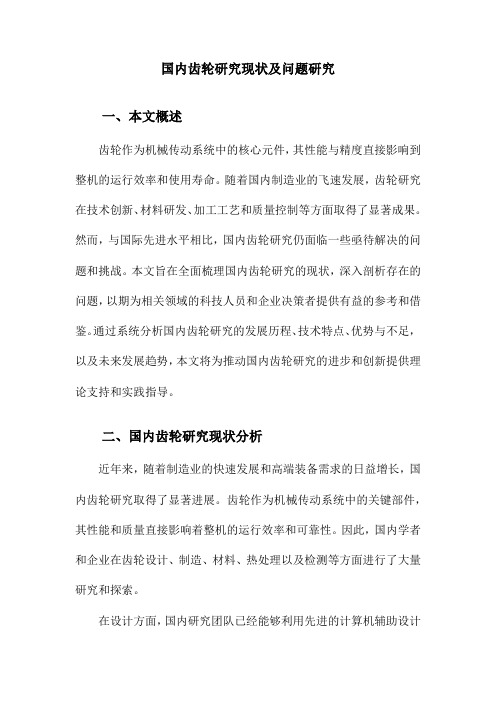
国内齿轮研究现状及问题研究一、本文概述齿轮作为机械传动系统中的核心元件,其性能与精度直接影响到整机的运行效率和使用寿命。
随着国内制造业的飞速发展,齿轮研究在技术创新、材料研发、加工工艺和质量控制等方面取得了显著成果。
然而,与国际先进水平相比,国内齿轮研究仍面临一些亟待解决的问题和挑战。
本文旨在全面梳理国内齿轮研究的现状,深入剖析存在的问题,以期为相关领域的科技人员和企业决策者提供有益的参考和借鉴。
通过系统分析国内齿轮研究的发展历程、技术特点、优势与不足,以及未来发展趋势,本文将为推动国内齿轮研究的进步和创新提供理论支持和实践指导。
二、国内齿轮研究现状分析近年来,随着制造业的快速发展和高端装备需求的日益增长,国内齿轮研究取得了显著进展。
齿轮作为机械传动系统中的关键部件,其性能和质量直接影响着整机的运行效率和可靠性。
因此,国内学者和企业在齿轮设计、制造、材料、热处理以及检测等方面进行了大量研究和探索。
在设计方面,国内研究团队已经能够利用先进的计算机辅助设计(CAD)和仿真分析技术,对齿轮的几何形状、齿面接触、载荷分布等进行精确计算和模拟。
这不仅提高了齿轮的设计精度,也缩短了新产品的开发周期。
在制造工艺方面,国内齿轮加工设备不断更新换代,高精度、高效率的加工技术得到广泛应用。
数控机床、激光切割、精密磨削等先进加工技术的使用,显著提升了齿轮的加工精度和表面质量。
在材料研究领域,国内已经开发出多种高性能齿轮材料,如高强度钢、渗碳钢、粉末冶金材料等。
这些新型材料的应用,极大地提高了齿轮的承载能力和耐磨性。
在热处理技术和检测手段方面,国内也取得了显著进步。
通过优化热处理工艺,可以显著改善齿轮的力学性能和抗疲劳性能。
先进的无损检测技术和精密测量设备的应用,使得齿轮的质量控制更加严格和准确。
尽管国内齿轮研究取得了诸多成果,但仍存在一些亟待解决的问题。
例如,与国际先进水平相比,国内齿轮在高端应用领域仍存在一定的差距,齿轮的可靠性和寿命有待进一步提高。
直齿圆柱齿轮精锻技术的发展现状与趋势
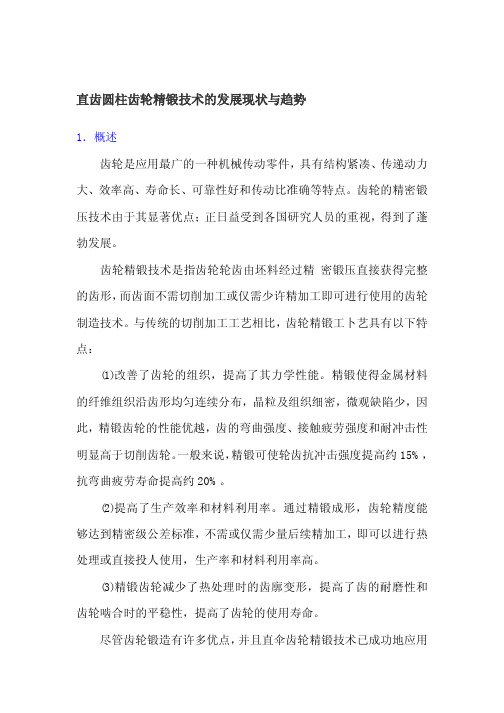
直齿圆柱齿轮精锻技术的发展现状与趋势1.概述齿轮是应用最广的一种机械传动零件,具有结构紧凑、传递动力大、效率高、寿命长、可靠性好和传动比准确等特点。
齿轮的精密锻压技术由于其显著优点;正日益受到各国研究人员的重视,得到了蓬勃发展。
齿轮精锻技术是指齿轮轮齿由坯料经过精密锻压直接获得完整的齿形,而齿面不需切削加工或仅需少许精加工即可进行使用的齿轮制造技术。
与传统的切削加工工艺相比,齿轮精锻工卜艺具有以下特点:(1)改善了齿轮的组织,提高了其力学性能。
精锻使得金属材料的纤维组织沿齿形均匀连续分布,晶粒及组织细密,微观缺陷少,因此,精锻齿轮的性能优越,齿的弯曲强度、接触疲劳强度和耐冲击性明显高于切削齿轮。
一般来说,精锻可使轮齿抗冲击强度提高约15%,抗弯曲疲劳寿命提高约20%。
(2)提高了生产效率和材料利用率。
通过精锻成形,齿轮精度能够达到精密级公差标准,不需或仅需少量后续精加工,即可以进行热处理或直接投人使用,生产率和材料利用率高。
(3)精锻齿轮减少了热处理时的齿廓变形,提高了齿的耐磨性和齿轮啮合时的平稳性,提高了齿轮的使用寿命。
尽管齿轮锻造有许多优点,并且直伞齿轮精锻技术已成功地应用于生产,但由于直齿圆柱齿轮精锻具有齿形型腔(特别是上下角隅处)充填困难、成形力大、模具设计与制造精度要求严格等特点,成形中遇到了许多困难。
多年来,各国研究人员运用各种理论、技术手段和试验方法,对直齿圆柱齿轮精锻技术进行了不懈的研究。
2.直齿圆柱齿轮精锻的理论研究英国曼彻斯特大学科技学院的Chitkara N R等人对直齿圆柱齿轮的塑性成形作了数值模拟分析,用能量法和上限法分析了镦锻直齿轮的变形规律;Dohamann F等人用数值逼近法和主应力法分析了冷精锻齿轮时的金属流动和模具应力情况,给出了沿齿面轮廓的法向应力分布图。
韩国学者J.H.Song和Y.T.Im开发了一种直齿圆柱齿轮冷正挤压辅助系统,这个系统可根据输人的齿轮参数给定可供实用的齿轮成形工装。
模具设计与制造的现状及进展趋势-加工工艺

自动器械普及率高,适合加大规模的模具生产。特别适用于深槽、深型腔、 汽车和家电行业中使用越来越广泛。气体帮助注射成形包括塑料熔体注射
筋肋、多型腔及多件制造。如深型腔通常结构繁杂、过渡曲面冗杂、型腔 和气体(一般均接受氮气)注射成形两面部份, 比传统的一般注射工艺有
较深,间或还要求使用的刀具样子,因此不能确保制造样子和大小的精确 更多的工艺参数需要确定和操纵,而且气体帮助注射常用于较冗杂的大型
上下异型的性能,从而特别适用于一些特殊模具的制造。除此自动穿丝、
3 结束语
自动定位技术能够使操作更加便捷,而且运用与无人化的加工中去。因为
使用计算机先进的数控技术,现代的模具工有了更多的时间去检测产品的
综上所述,在模具的设计与制造过程中,进行科学合理的设计、制造
第3页共4页
本文格式为 Word 版,下载可任意编辑,页眉双击删除即可。
第1页共4页
本文格式为 Word 版,下载可任意编辑,页眉双击删除即可。
机机械完成审核、对模具结构的审核及对图样的审核。
技术和工艺二者在模具制造中的重要性发生了转变,西方工业发达国家的
模具生产已经从传统的加工技术(数控、自动),正在向着无人化生产的方
2 现代模具设计与制造业的进展趋势
式快速进展。但是目前我国仍旧处于机械制造向数操纵造的方面转变,从
是爱护生态环境和可持续进展的方面。此举将会推动模具行业的持续进展, 运用科学的技术,统筹的管理方式,来增加生产效率,来满足人们日益增 长的需求。
第4页共4页
国际市场分析模具制造行业的前景,能够与规模化
增添竞争力的重要方式就是降低产品生产本钱,缩短生产时间,提高产品
质量。设计方式的高效率、自动化器械的使用,快速的成型机械加上优秀
直齿圆柱齿轮精锻工艺的研究

直齿圆柱齿轮精锻工艺的研究摘要:无飞边模锻工艺应用越来越广泛,不仅降低了生产成本,也提高了材料利用率和生产效率,但是其模具承受荷载力过大,且寿命较低,需要通过合理设计和精锻工艺以提高生产水平。
文章主要结合某直齿圆柱齿轮展开论述,讨论如何开展齿轮精锻工艺内容,通过数值模拟提出具体实行方案,以此来实现实际改进,促进生产有序进行。
关键词:无飞边模锻;直齿圆柱齿轮;精锻工艺;载荷前言:无飞边模锻具有较多优势:材料利用率高;生产产品质量佳;精度有所保障;容易实现自动化生产,目前在不同复杂构件的生产中均有应用。
在进行模锻时,由于其模具会承受较大的荷载,且磨损速度快,因此整体来看使用周期较短,不利于降低生产成本。
为延长其使用寿命,一般可以从材料质量入手,结合润滑技术减少摩擦和构件结构。
1 某直齿圆柱齿轮概况该直齿圆柱齿轮参数如下:齿数:18;法向模数:3;变位系数:0.225;精度要求:9级。
一端属于轴部,外径尺寸:35mm;内径尺寸:19mm;轴部长度:10mm;另外一端属于齿轮部,齿顶圆直径:61.15mm;分度圆直径:54mm;带轴齿轮长度:20mm;轴部和齿轮部之间的过渡:圆弧过渡,尺寸:3mm。
齿轮成形主要采用了温锻工艺;齿部成形采用了精锻工艺[1]。
图1 圆柱齿轮锻造成形之后,其齿部不需要再次进行加工。
其中,轴部和内径预留了一定的加工余量,以此来完成后续机加工。
齿轮主要材料为20CrMnTi合金钢(主要化学成分可见表1),这种材料属于渗碳合金钢,其性能良好,且淬透性高。
经过渗碳淬火之后,表面硬度高耐磨性好,心部韧性好,在低温状态下具备一定冲击韧性;正火之后,其切削性能极佳。
表1 20CrMnTi合金钢化学成分表元素含量C0.17~0.23Cr 1.0~1.30Mn0.80~1.10Cu≤0.03Si0.17~0.37Ni≤0.03Fe余量Ti0.04~0.102 建立仿真模型2.1 明确建立方向在建立模型之前,相关人员需要了解锻造与材料之间的关系,以此来提高模型建立的科学性和可使用性。
直齿圆柱齿轮精锻成形工艺和模具设计的研究现状
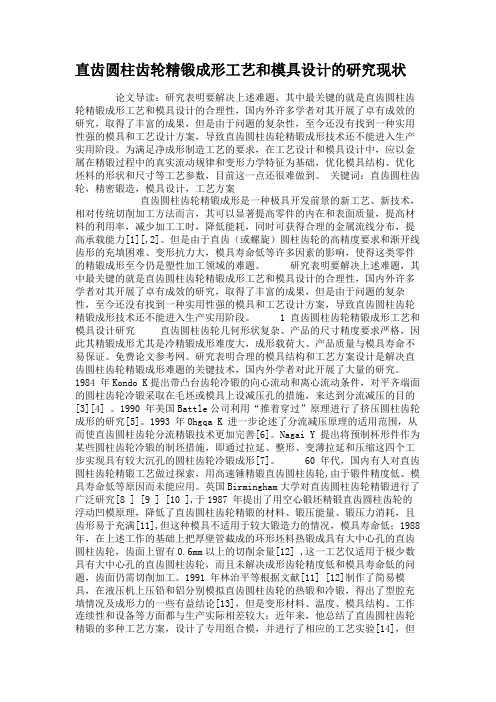
直齿圆柱齿轮精锻成形工艺和模具设计的研究现状论文导读:研究表明要解决上述难题,其中最关键的就是直齿圆柱齿轮精锻成形工艺和模具设计的合理性,国内外许多学者对其开展了卓有成效的研究,取得了丰富的成果,但是由于问题的复杂性,至今还没有找到一种实用性强的模具和工艺设计方案,导致直齿圆柱齿轮精锻成形技术还不能进入生产实用阶段。
为满足净成形制造工艺的要求,在工艺设计和模具设计中,应以金属在精锻过程中的真实流动规律和变形力学特征为基础,优化模具结构、优化坯料的形状和尺寸等工艺参数,目前这一点还很难做到。
关键词:直齿圆柱齿轮,精密锻造,模具设计,工艺方案直齿圆柱齿轮精锻成形是一种极具开发前景的新工艺、新技术,相对传统切削加工方法而言,其可以显著提高零件的内在和表面质量,提高材料的利用率,减少加工工时,降低能耗,同时可获得合理的金属流线分布,提高承载能力[1][,2]。
但是由于直齿(或螺旋)圆柱齿轮的高精度要求和渐开线齿形的充填困难、变形抗力大,模具寿命低等许多因素的影响,使得这类零件的精锻成形至今仍是塑性加工领域的难题。
研究表明要解决上述难题,其中最关键的就是直齿圆柱齿轮精锻成形工艺和模具设计的合理性,国内外许多学者对其开展了卓有成效的研究,取得了丰富的成果,但是由于问题的复杂性,至今还没有找到一种实用性强的模具和工艺设计方案,导致直齿圆柱齿轮精锻成形技术还不能进入生产实用阶段。
1 直齿圆柱齿轮精锻成形工艺和模具设计研究直齿圆柱齿轮几何形状复杂、产品的尺寸精度要求严格,因此其精锻成形尤其是冷精锻成形难度大,成形载荷大、产品质量与模具寿命不易保证。
免费论文参考网。
研究表明合理的模具结构和工艺方案设计是解决直齿圆柱齿轮精锻成形难题的关键技术,国内外学者对此开展了大量的研究。
1984 年Kondo K提出带凸台齿轮冷锻的向心流动和离心流动条件,对平齐端面的圆柱齿轮冷锻采取在毛坯或模具上设减压孔的措施,来达到分流减压的目的[3][4] 。
齿轮精锻工艺及模具探讨

齿轮精锻工艺及模具探讨摘要:本文介绍了一种新的齿轮精锻工艺和模具结构,对所得齿轮的精度、材料消耗、表面缺陷等与常规的铣齿、滚齿、插齿等常规切削加工方法进行了对比,精锻工艺具有明显的技术经济效益。
关键词:铣齿;剃齿;滚齿;插齿; 齿轮精锻1 引言生产实践中绝大部分齿轮的加工仍然采用切削加工,其机加工工作量是整个制造工作量的40~60%,其材料的利用率不超过35%,还占用大量的齿轮加工机床,在生产中造成大量的人力和金属材料的消耗。
运用塑性成形方法制造齿轮与切削加工相比,具有很多优点,如减少了金属消耗量,提高了劳动生产率,由于塑性成形加工可以最大限度地利用材料的纤维方向性,获得更加合理的金属内部组织分布,从而增强了齿轮的机械性能等等,能取得明显的技术经济效益和社会效益。
目前采用塑性成形制造齿轮的方法很多,如精锻、精冲、挤压、滚辗、轧制等。
用这些成型加工方法取代常规切削加工需要解决的关键问题是如何提高成形精度,减小齿廓精修加工量及减少金属的消耗量。
本课题设计了一种不带毛边槽的齿轮精锻模具。
凹模采用可分式结构,在机械压力机上,能进行批量生产。
该模具价格不高,结构简单,但如何更换模具的易磨损件,是提高经济效益的关键因素。
2 毛坯的制备和加热2.1毛坯重量的确定为了保证精锻时材料完全充满模膛,获得较高精度的锻件,并尽量减少材料流动阻力和流动距离,防止发生齿廓折断,合理确定毛坯下料重量十分重要,相关资料及工艺实践表明,对精锻后采用铣齿、插齿时毛坯重量偏差控制在5%以内,可保证所得齿轮精度在公差范围之内,且不会引起模具折断;若要采用剃齿、滚齿加工,则毛坯的重量偏差应超过1~1.5%,否则零件尺寸就可能超出规定的公差范围。
2.2 毛坯下料方法可由热轧圆钢在压力机上利用剪刃剪切下料;也可采用经光整加工的轧制毛坯,用全封闭的剪切模具下料。
2.3 毛坯预热可利用室式工频感应炉,对于是18CrMnTi的齿轮材料,加热温度在900~1100℃范围内。
- 1、下载文档前请自行甄别文档内容的完整性,平台不提供额外的编辑、内容补充、找答案等附加服务。
- 2、"仅部分预览"的文档,不可在线预览部分如存在完整性等问题,可反馈申请退款(可完整预览的文档不适用该条件!)。
- 3、如文档侵犯您的权益,请联系客服反馈,我们会尽快为您处理(人工客服工作时间:9:00-18:30)。
直齿圆柱齿轮精锻成形是一种极具开发前景的新工艺、新技术,相对传统切削加工方法而言,其可以显著提高零件的内在和表面质量,提高材料的利用率,减少加工工时,降低能耗,同时可获得合理的金属流线分布,提高承载能力[1][2]。
但是由于直齿(或螺旋)圆柱齿轮的高精度要求和渐开线齿形的充填困难、变形抗力大,模具寿命低等许多因素的影响,使得这类零件的精锻成形至今仍是塑性加工领域的难题。
研究表明要解决上述难题,其中最关键的就是直齿圆柱齿轮精锻成形工艺和模具设计的合理性,国内外许多学者对其开展了卓有成效的研究,取得了丰富的成果,但是由于问题的复杂性,至今还没有找到一种实用性强的模具和工艺设计方案,导致直齿圆柱齿轮精锻成形技术还不能进入生产实用阶段。
1.直齿圆柱齿轮精锻成形工艺和模具设计研究直齿圆柱齿轮几何形状复杂、产品的尺寸精度要求严格,因此其精锻成形尤其是冷精锻成形难度大,成形载荷大、产品质量与模具寿命不易保证。
研究表明合理的模具结构和工艺方案设计是解决直齿圆柱齿轮精锻成形难题的关键技术,国内外学者对此开展了大量的研究。
1984年Kondo K 提出带凸台齿轮冷锻的向心流动和离心流动条件,对平齐端面的圆柱齿轮冷锻采取在毛坯或模具上设减压孔的措施,来达到分流减压的目的[3][4]。
1990年美国Battle 公司利用“推着穿过”原理进行了挤压圆柱齿轮成形的研究[5]。
1993年Ohgqa K 进一步论述了分流减压原理的适用范围,从而使直齿圆柱齿轮分流精锻技术更加完善[6]。
Nagai Y 提出将预制杯形件作为某些圆柱齿轮冷锻的制坯措施,即通过拉延、整形、变薄拉延和压缩这四个工步实现具有较大沉孔的圆柱齿轮冷锻成形[7]。
60年代,国内有人对直齿圆柱齿轮精锻工艺做过探索,用高速锤精锻直齿圆柱齿轮,由于锻件精度低、模具寿命低等原因而未能应用。
英国Birmingham 大学对直齿圆柱齿轮精锻进行了广泛研究[8][9][10],于1987年提出了用空心锻坯精锻直齿圆柱齿轮的浮动凹模原理,降低了直齿圆柱齿轮精锻的材料、锻压能量、锻压力消耗,且齿形易于充满[11],但这种模具不适用于较大锻造力的情况,模具寿命低。
1988年,在上述工作的基础上把厚壁管截成的环形坯料热锻成具有大中心孔的直齿圆柱齿轮,齿面上留有0.6mm 以上的切削余量[12],这一工艺仅适用于极少数具有大中心孔的直齿圆柱齿轮,而且未解决成形齿轮精度低和模具寿命低的问题,齿面仍需切削加工。
1991年林治平等根据文献[11][12]制作了简易模具,在液压机上压铅和铝分别模拟直齿圆柱齿轮的热锻和冷锻,得出了型腔充填情况及成形力的一些有益结论[13],但是变形材料、温度、模具结构、工作连续性和设备等方面都与生产实际相差较大;近年来,他总结了直齿圆柱齿轮精锻的多种工艺方案,设计了专用组合模,并进行了相应的工艺实验[14],但上述研究均是在实验室中进行的,尚未应用到生产实践中。
Drecun V M 等开发了一套参数化的直齿圆柱齿轮精锻模CAD 软件。
青岛科技大学的田福祥对直齿圆柱齿轮热精锻进行了深入研究,发明了直齿圆柱齿轮热精锻和冷推挤联合成形工艺,研制了用于生产的模具,精度达到9级,齿面无须切削加工即可使用[15][16];提出了渐开线齿廓线膨胀定理和推论,并论述了直齿圆柱齿轮精锻模具齿形参数的设计计算方法及惯用公式[17]。
田福祥等研究开发了带有强力脱模装置的内齿轮热精锻模具和工艺,彻底解决了热精锻时成形难和脱模难的问题,并成功的应用于生产,取得了显著的经济效益[18]。
吉林大学的寇淑清等用三维大变形弹塑性有限元法对齿轮冷精锻成形过程进行了数值模拟,对以闭式模锻为预锻和以闭式模锻、孔分流及约束分流为终锻的两步成形模式的变形流动情况进行了数值模拟分析。
数值分析结果及工艺实验表明在终锻中采取分流,尤其是约束孔分流措施对于降低工作载荷和提高角隅充填能力等方面十分有效[19][20]。
山东大学的张清萍等利用正交试验法与数值模拟技术相结合的方法,解决了预锻模具型腔优化设计问题[21]。
安徽科技学院的陈丰等利用自制的浮动模具研究了直齿圆柱齿轮精锻成形的力能参数、齿轮参数和冲压成型相关参数的关系,认为精锻成形的力能参数受到齿轮参数的影响,这一结论为齿轮精锻成形的实用化提供了可靠的参考依据[22]。
西安交通大学的程羽等对采用浮动凹模进行精锻成形的工艺进行了研究,指出单纯的浮动凹模对于成形作用不大,采用浮动凹模浮动模式可调的精锻方法可以提高成形的质量,但没有给出模具的具体结构和调节方式[23]。
2.直齿圆柱齿轮精锻成形工艺和模具设计方面存在的主要问题直齿圆柱齿轮几何形状复杂、产品的尺寸精度、表面质量、组织性能、力学性能要求严格。
多年来,尽管国内外许多学者研究其精锻工艺和模具结构设计,也取得了一些成果,但与实际生产应用还有一定距离。
今后,需要解决的工艺和模具方面的主要问题如下:(1)工艺优化、模具结构优化问题。
齿轮精锻是一种净成形或近净成形制造工艺。
为满足净成形制造工艺的要求,在工艺设计和模具设计中,应以金属在精锻过程中的真实流动规律和变形力学特征为基础,优化模具结构、优化坯料的形状和尺寸等工艺参数,目前这一点还很难做到。
(2)齿轮锻件出模问题。
直齿圆柱齿轮精锻没有拔模斜度,出模困难,需要较大的顶出力才能将锻件从模具中顶出。
因此,对模具结构和锻造设备有较高的要求。
如何解决好锻件出模,是一个必须重点解决的问题。
(3)润滑问题。
在精锻中选用的润滑剂,在锻造温度范围内应该具有良好的润滑性能,使锻件与模具隔离,避免金属变形时直接与模具接触,使金属流动阻力最小;具有良好的绝热和脱模性能,从而减少锻件热量传导到模具上,延长模具寿命。
另外,润滑剂应具有良好的高温湿润性能和成膜性能,在模具型腔中均匀分布,形成润滑膜,并且成形后在模具型腔中不应留有残渣,或者留有极少的残渣,容易清除。
(4)模具寿命问题。
模具寿命问题是关系到直齿圆柱齿轮精锻工艺能否应用于生产实践的关键因素。
然而,影响模具寿命的因素很多。
如何有效地改善模具的受力状况、减少磨损、提高寿命,是一个摆在研究者面前的不能回避的问题。
3.直齿圆柱齿轮精锻成形工艺和模具设计研究的发展趋势直齿圆柱齿轮精锻研究已经取得了较大进展,但还有许多方面需要进一步研究和探索,今后直齿圆柱齿轮精锻成形工艺和模具设计方面将从以下几个方面发展:(1)充分利用计算机技术,研究塑性成形过程的金属流动规律。
目前关于直齿圆柱齿轮精锻方面的理论研究仅能得出变形金属的部分特征,而不能研究在整个塑性变形过程中金属的流动规律和所具有的变形力学特征,即不能得出应力场、应变速率场和温度场,只能粗糙的分析金属的整体流动。
今后应充分利用高新计算机技术,结合塑性或弹塑性有限元方法,模拟直齿圆柱齿轮整个锻压变形过程的金属流动,找出变形坯料自由表面和内部的金属流动及应力应变分布规律,以期通过控制材料的流动达到零件的精确成形。
(2)优化模具结构和工艺,控制精锻齿轮的质量和精度。
质量和精度控制是直齿圆柱齿轮精锻研究的重点内容,目前关于这方面的研究还比较少,今后要进一步优化模具结构,选用优质模具材料,提高模具加工精度和使用寿命,使用合适的锻压设备;研究精确下料的新途径,提高毛坯的下料精度和表面质量;采用少无氧化加热,尽量减少毛坯的氧基金项目:本文系安徽高校省级自然科学研究一般项目(KJ2007B314ZC)。
作者简介:陈丰(1972-),男,安徽省固镇县人,硕士,讲师,主要从事机电方面的教学和科研。
直齿圆柱齿轮精锻成形工艺和模具设计的研究现状安徽科技学院工学院陈丰魏宝丽夏显明[摘要]直齿圆柱齿轮精锻成形是一种极具开发前景的新工艺、新技术,相对传统切削加工方法而言,具有许多不可替代的优点,文章对直齿圆柱齿轮精锻成形工艺和模具设计研究的国内外现状进行了详细的阐述,并指出了所存在的问题,对其进一步的发展趋势进行了预测。
[关键词]直齿圆柱齿轮精密锻造模具设计工艺方案377——37409万人,占第二、第三产业就业人数比重为85.3%,其中城镇内资民营企业就业人数达21880万人,增长5.7%,占城镇就业人数的比重为77.3%。
城乡个体私营经济就业人数为11746万人,增长14.9%。
以贵州为例,全省31家省级农业产业化重点龙头企业全部是民营企业,成为带动农业结构调整和吸纳农村剩余劳动力的中坚力量,仅2004年民营私营企业从业人员中农村转移劳动力已占40%。
截至2005年底,全省民营企业44.7万户,全省民营企业从业人员达216.3万人,2006年民营企业从业人员比上年增长3.6%。
贵州遵义县2000年全县有个体工商户1.52万户,注册资金1.45万元,从业人员19510人,私营企业296户,到2003年国有企业进一步转换机制,改革改制56家,个体工商户和私营企业1.74万户,从业人员增至22400人。
[2]以上数据均充分表明,民营经济是我国社会就业的一个主渠道,是缓解城乡就业压力的解压阀。
随着县域民营经济的快速发展,民营企业吸纳就业人员的作用还会进一步显现。
4.民营经济是解决农民增收和县乡财政困难的重要途径目前,我国有大量的农业劳动力闲置,这是我国农业劳动生产率低下,农民收入增长缓慢的重要原因。
在我省这样的情况也尤其突出。
据2005年数据,贵州省有人口3931万人,其中农业人口2874万人,占全省总人口的73.11%。
农村劳动力为2452万人,按行业划分,从事第二产业的人员290万人,从事第三产业的人员216万人,含未就业、未充分就业人员在内,滞留农业内部的劳动力多达1946万人。
[3]由于闲置人口众多导致农民整体收入的增长缓慢。
要解决农民增收问题,光靠农业本身不行,贵州农村人均资源少,目前大部分土地产出有限;靠农产品提价也不现实。
因此,农民增收问题解决的根本在于农民数量的减少。
实现农村剩余劳动力的转移才是重点。
只有依赖土地的人少了,农村的人均资源才会相应增加,土地的产出和农业的经营才会更有效益,留在农业中的劳动力才能从专业化、大规模的农业经营活动中获得更高的收入。
加快发展县域民营经济,使农民在未脱离土地的前提下,提供了更多的就业机会,增加了农民的收入。
据报告,目前,全国平均每个县的赤字约1个亿,全国赤字县占全国县域的比重达3/4,县级财政基本上是“吃饭财政”,县乡政府的债务风险仍未得到根本性控制。
西部地区县乡财政困难是普遍问题,而经济落后的贵州问题尤其突出。
以贵州省望漠县为例,农业税减免后,县乡财政陷入困境。
全县农业税含附加502万元,农业特产税230万元,这一笔收入减少后,乡镇几乎没有资金收入来源,全县16个乡镇,1个办事处,下达的税收任务仅为24.7万元。