输送设备模块化设计的研究及应用
LNG接收站模块化建造研究

LNG接收站模块化建造研究LNG(液化天然气)接收站是将液化天然气从输送船舶转换为气态天然气,并通过管道输送到终端用户的设施。
随着天然气作为清洁能源的重要性不断增加,LNG接收站的建设和运营也变得越来越重要。
而在LNG接收站建造领域,模块化建造是一种新兴的建造方法,它可以提高建造效率、降低成本,并且更加环保和可持续。
因此,本文将探讨LNG接收站模块化建造的研究。
首先,我们需要了解LNG接收站的结构和工作原理。
一个典型的LNG接收站由岸边泵船系统、储液罐、卸船臂、再气化装置等组成。
接收站的主要功能是接收来自LNG船舶的液化天然气,经过卸船臂进行卸载,然后通过再气化装置将其转化为气态天然气,最终输送给用户。
而LNG接收站的建设需要考虑到安全性、环保性、经济性等因素。
传统建造方法会面临一些问题,如建造周期长、成本高、施工难度大等。
而模块化建造方法通过将建造过程模块化,即将各个功能单元分解成不同的模块,然后在工厂进行组装,最后再进行现场拼装,这样可以大大提高建造效率,减少施工周期和成本。
模块化建造还能降低现场安装风险,提高工人安全性,减少对环境的影响。
在LNG接收站模块化建造方面,需要考虑以下几个关键因素:1.模块设计:模块化建造需要进行精细设计,包括结构设计、管道设计、设备选型等。
设计要考虑模块之间的连接方式和设备之间的配合关系,确保各个模块可以在现场无缝拼装。
2.模块制造:模块化建造需要在工厂进行大量的模块制造,制造过程需要遵循相关标准和规范,确保质量和安全。
3.现场安装:模块化建造的最后一步是在现场进行模块的拼装和安装。
现场安装需要考虑到现场环境、物流、安全等因素,确保模块安装顺利进行。
4.运行维护:模块化建造后的LNG接收站需要进行运行维护,保证其正常运行。
为了提高接收站的可靠性和安全性,需要定期检修和维护。
总的来说,LNG接收站模块化建造是一种有效、高效、环保的建造方法。
通过模块化建造,可以提高建造效率、降低成本、减少施工风险,同时也有利于可持续发展。
汽车制造总装车间生产线的输送设备研究

汽车制造总装车间生产线的输送设备研究汽车在生产和制造的环节是非常复杂的,每个环节都要做好才可以保证汽车制造的质量。
每个环节都要进行物品的运输,而各个生产线中设备的选择是该行业比较重视的问题。
汽车总装是汽车生产制造中的最后一项工作,也是最重要的一环,在输送设备的选择时,不但要节约成本、减少各个方面的资金投入,还要满足汽车制造的实际需求。
因此,本文对汽车制造总装车间生产线的输送设备进行了研究。
關键词:汽车制造;总装车间;生产线输送设备一、汽车制造总装的工艺1、汽车制造总装工艺流程为了能够满足产能的需求,实现精确化生产,汽车制造总装车间都使用了模块化工艺流程,主线模块主要包括PBS 线、底盘线、调试线、内饰线等,分装模块主要包括动力总成、车门、座椅等。
模块化装配主要是实现汽车零件的分装,之后通过主线工位组装,以此实现整车的装配。
汽车制造总装工艺的流程为:车身PBS线→内饰线→底盘装配线→合成线→检测线→淋雨线→道路试验。
2、汽车制造总装的工艺参数工位之间的间距一般选择最大车型的长度加长700-1100mm,比如最大车长为4000mm,那么科学的工位间距就是5000mm。
在进行输送设备的选择和应用的过程中,需要考虑到不同生产线之间输送设备的应用间隔,不允许输送设备对车间生产的实际效率造成影响,要根据在汽车制造的实际情况来进行输送设备的选择。
二、汽车制造总装的输送设备1、积放链积放链运输设备在实际应用时,其内部空间是非常大的,可以将工件堆积在一起进行运输,可以进行多种物品的共同运输,提升整体应用效率。
积放链的组成结构是非常复杂的,由多种装置、设备和系统构成,通常被应用在底盘线的运输作业中。
在该运输系统中,可以将不同生产线之间的运输工作结合在一起整合成一个物流运输系统,可以对不同类型的物品进行放置、运输、管理和储存,实际应用效率比较高。
这种运输系统中所应用的技术是比较可靠的,并且在使用的过程中不同投入过多的成本,但是产生的噪音很大,需要消耗大量的能源资源才能完成相关的运输工作。
控制系统的模块化设计与应用研究

控制系统的模块化设计与应用研究随着现代科技的发展,控制系统在工业自动化制造中扮演着越来越重要的角色。
为了提高控制系统的可靠性、稳定性和可维护性,控制系统的模块化设计成为了不可或缺的一环。
本文将从控制系统模块化设计的原理、应用案例以及未来发展趋势三个方面进行探讨。
一、控制系统模块化设计的原理在传统控制系统中,所有的控制功能都会被集成在一台设备或者一个程序中,这种设计方式遇到了很多问题。
例如,在系统故障的情况下,我们很难准确定位问题所在,也很难快速排除故障。
此外,传统控制系统的扩展性也很差,无法根据实际需要快速修改或者增加新的功能模块。
为了解决这些问题,控制系统的模块化设计开始被广泛应用。
模块化设计的主要原理在于,将不同的控制功能分离成独立的模块,通过模块之间的通信实现控制功能。
每个模块都有相应的接口,可以方便地进行组合和拆卸。
控制系统中的每个模块都可以独立运行,相互之间没有依赖关系,因此可以有效提高整个控制系统的可靠性和稳定性。
二、控制系统模块化设计的应用案例控制系统模块化设计在工业自动化领域得到广泛的应用。
以汽车制造行业为例,传统的生产线需要大量的人力资源来完成车身焊接、涂装、组装等工艺过程。
这些生产线通常由数百台设备和大量的传感器、执行器等元件组成。
其中涂装机器人、输送设备、激光焊接机器人等等都可以看作是控制系统的模块。
通过模块化设计,我们可以将所有的控制功能分离成独立的模块,实现一个模块的独立升级和维护。
这不仅可以提高生产效率,而且可以有效降低维护成本。
除了工业自动化制造领域,控制系统的模块化设计也成功地应用在了智能家居、医疗设备、机器人等领域。
例如,智能家居系统中的智能灯具、温控器、智能插座等都是控制系统的模块,通过模块化设计实现了相互独立和协作工作。
三、控制系统模块化设计的未来发展趋势随着物联网技术的不断发展,未来的控制系统将更加智能化和集成化。
控制系统模块化设计将更加注重模块之间的互联互通,从单一的控制模块逐渐演变为多模块、跨领域控制系统。
基于Creo的带式输送机三维参数化设计
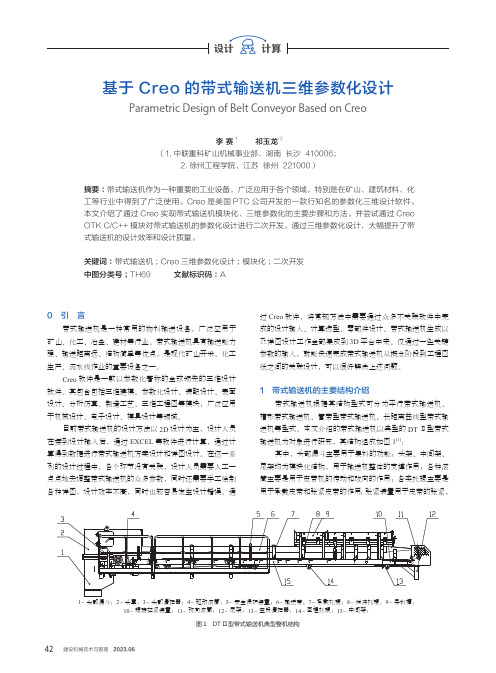
42 建设机械技术与管理 2023.06 0 引 言带式输送机是一种常用的物料输送设备,广泛应用于矿山、化工、冶金、建材等行业。
带式输送机具有输送能力强、输送距离远、结构简单等优点,是现代矿山开采、化工生产、流水线作业的重要设备之一。
Creo 软件是一款以参数化著称的全球领先的三维设计软件。
其包含包括三维建模、参数化设计、装配设计、表面设计、分析仿真、制造工艺、三维工程图等模块,广泛应用于机械设计、电子设计、模具设计等领域。
目前带式输送机的设计方法以2D 设计为主,设计人员在接到设计输入后,通过EXCEL 等软件进行计算,通过计算得到数据进行带式输送机方案设计和详图设计。
在这一系列的设计过程中,各个环节没有关联,设计人员需要人工一点点地去调整带式输送机的众多参数,同时还需要手工绘制各种详图,设计效率不高,同时也较容易发生设计错误。
通基于Creo 的带式输送机三维参数化设计Parametric Design of Belt Conveyor Based on Creo李 赛1 祁玉龙2(1.中联重科矿山机械事业部,湖南 长沙 410006;2.徐州工程学院,江苏 徐州 221000)摘要:带式输送机作为一种重要的工业设备,广泛应用于各个领域,特别是在矿山、建筑材料、化工等行业中得到了广泛使用。
Creo 是美国PTC 公司开发的一款行知名的参数化三维设计软件。
本文介绍了通过Creo 实现带式输送机模块化、三维参数化的主要步骤和方法。
并尝试通过Creo OTK C/C++模块对带式输送机的参数化设计进行二次开发。
通过三维参数化设计,大幅提升了带式输送机的设计效率和设计质量。
关键词:带式输送机;Creo 三维参数化设计;模块化;二次开发中图分类号;TH69 文献标识码:A过Creo 软件,将常规方法中需要通过众多不关联软件中完成的设计输入、计算选型、零部件设计、带式输送机生成以及详图设计工作全部集成到3D 平台中来。
大倾角下运带式输送机控制技术的研究与应用
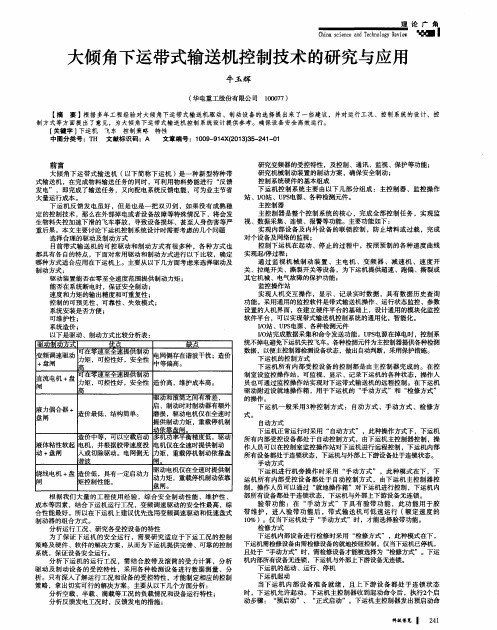
研究变频器的受控特性 , 及控制 、通讯 、监视、保护等功能; 研究机械制动装置的制 动方案 ,确保安全制动 ; 控制系统硬件的基本组成 下运机 控制系统 主要 由以下几部分组 成 :主控 制器 、监 控操作 站 、I , O 站 、U P S 电源 、各种检测元件 。 主控制器 主控 制器是整个 控制 系统 的核心 ,完成全部 控制任务 ,实现监 视 、数据采集 、连锁、报警 等功能 。主要功能如下 : 实现 内部设备及 内外设备 的联锁控 制 ,防止 堵料或过 载 ,完成 对个设备及网络的监 视 ; 控制下 运机在起 动 、停止 的过程 中 ,按照预 制的各种速 度 曲线 实现起, 停过程 ; 通 过监 视机 械制 动 装置 、 主电机 、变频 器 、减速 机 、速 度开 关 、拉绳开关 、撕裂开关等设 备 ,为下运机 提供超速 、跑偏 、撕裂或 其它机械 、电气故障的保护功能;
软件平台 ,可以实现带式输送机控制系统的通用化 ,智 能化 。 I / 0 站 、U P S 电源、各种检测元件 I / 0 站完成数据采集 和命令发送功能 。U P S 电源在掉 电时,控制系
缺 点
优 点
变频调速驱动 可在零速至全速提供制动 电网侧存在谐波干扰 力矩 ;造价 可控性好 ,安全性 + 盘闸 高 中等偏高。
( 华 电重工股份有 限公司 1 0 0 0 7 7 )
【 摘 要】 根据 多年工程经验 对大倾 角下运带式输送机驱 动、制动设备的选择提 出来 了一些建议 ,并对运行工况、控制系统 的设计 、控 制方式等方面提 出 了意见,为大倾角 下运 带式输送机控制 系统设计提供参考。确保设备 安全高效运行。 【 关键 字 】 下运机 飞车 控制策略 特性 中图分类号 :T H 文献标识码 :A 文章编号 :1 0 0 9 — 9 1 4 X ( 2 0 1 3 ) 3 5 — 2 4 1 — 0 1
石油化工行业大型设备模块化施工工艺研究

石油化工行业大型设备模块化施工工艺研究摘要:随着经济的持续发展,促使我国石油化工行业的规模越来越大,同时对石化行业施工技术安全性与高效性有较高要求。
如今,石油化工行业能够生产2千吨重的大装置,并能完成现场装置安装及热处理工作。
而如今石化行业在管理中,使用的是统一采购与设计标准,这样也在某种程度上推动了模块化施工在石化行业中的持续开展与运用。
关键词:石油化工,大型设备,模块化施工石油化工行业在其快速发展过程中建立规范化,产业化与安全化管理新思想。
模块化施工理论是二十世纪九十年代国内才宣布选用,当时国内把从进口乙烯装置用以建筑塔吊提高,对裂解炉零件进行模块化设计处理,并进行地面预制装配。
一直到二十一世纪我国模块化施工才获得了大规模发展。
1模块化施工主要特点(1)模块化施工技术性具备其他施工现场所无可比拟的先天性资源优势。
选用模块化施工技术性可进一步降低工装设备安全隐患、提高工作服质量、完成产品化预制构件。
(2)选用模块化施工技术,可以有效地减少施工期。
运用模块化设计可按照安装顺序流水线作业,同时还可以和工厂诸多操作同时实行。
(3)全方位,系统化管理理念为控制模块工程施工之最。
主要包括吊装,运送一体化,工程施工系统化,建设工程规范化等系列的部分。
并且也可有效提升规范化管理水准,拓展吊装,运输统一管理范畴,促进系统化施工开展,为项目节省更大耗能。
(4)模块化施工针对设计图有很高的要求,设计方案必须按相关要求规定进行,而且要高品质、迅速地进行,如此不仅会加快设计,而且也会减少未来项目变更概率。
(5)模块化施工绝大部分在地面开展,大大减少高处作业造成安全,效率和质量低。
(6)模块化施工可以有效地减少工程材料和工程机械设备在建筑工地所占用的面积,给工程项目的顺利推进创造一个好的环境,这般降低不必要的携带,同时还可以达到减少施工工期效果。
2石油化工大中型装备模块化设计建设现状由于经济发展及科技进步发展需求,石化装备经营规模特别大,与其同行业在工程施工质量,安全性及进度上要求与日俱增。
输送类设备模块化设计的研究及应用

A Su y o d lrz t n De in a d i p iain td n Mo ua iai sg n t Ap lc t o s o
fr Co v y n u p n s o n e i g Eq i me t
L UO u - i J n bn
c n e i g e u p n n a u o td l gs c y t m i su id B s d o h h o y o d lr ai n d — o v yn q i me t n a t mae o it s s se s t d e . a e n t e t e r f mo ua i t e i i z o
摘 要 : 块化设 计是一 种现代设 计 方法 , 中以模 块化设 计理论 对 自动 化物 流 系统 中输 送类设备 模块 模 文
化 设计 方法展 开研 究, 出基 于 S LSre 20 推 Q e r 0 0数 据库 、 v 应用 Mi oo i a C +6 0开发 的 产品设计 c sfV s l + . r t u
0 引 言
在 A / S自动化 物流 系统 中 , SR 应用 了大 量 的输送 类设 备 ( 如辊 道 输 送 机 、 式 输送 机 、 式 输送 机 、 带 链 升 降输 送机 等 ) 但 该 类 型输 送 设 备 的 日常 设 计 工 作 大 ,
部 分是变 型设计 , 即设 备 的工 作 原 理 和功 能结 构 未 改 变, 只是模 仿变更 现有产 品 的尺寸或 配置 , 目前 这样 的
d t b s s d s rb d,a d a ne fc o s ri v le ntfrt e p o ucin mo u aia in d sg lto m aa a e i e c e i n n it ra e f ru e n o v me h r d to d lrz t e in p af r o o i sa ls e .Th ai iy o d lrz to sg sp o e y a s c e su p lc t n t o lrc n e o . se tb ih d e v ld t fmo u aiai n de in i r v d b u c s f la p ia i o r l o v y r o e Ke r s: o v yn q i me t e in meh d;mo u a ia in y wo d c n e i g e u p n ;d sg to d lrz t o
带式输送机的发展与应用
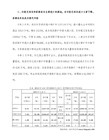
中有详细的数据对比,本文不再一一赘述。带式输
送机的以上特点决定了它在国民经济领域的广泛应用。我国的带式输送机由最初的
TD62 型发展至现在的 DTⅡ ( A)型,使用范围不断扩大,可以满足堆积密度为
500~2500Kg/m
3
物料的输送要求,输送机的适用工作环境温度为-25~40℃。对于有特殊
布的输送机设计准则
[3]
。以上所述各国设计规范中的设计方法与计算方法都有所不同,
国内输送机研究学者参考国外设计规范研究出了以一般机械设备的选型设计和主要零
部件的选择为主的整机选型设计方法。我国早期制定了国家标准 GB/T17119-1997《连
续搬运设备带承载托辊的带式输送机运行功率和张力计算》,并于 2008 年公布了
要求的工作环境,例如耐热、耐寒、防腐、防爆和阻燃等,可采用特种橡胶输送带并辅
以相应防护措施;对于应用于复杂地形的带式输送机可采用凹弧、凸弧和直线组合的输
送形式,使用单机或多机组合系统。
1.2 课题的国内外研究现状概述
1.2.1 带式输送机设计的研究现状
带式输送机的常规设计主要是.1 带式输送机的发展状况
1892 年,在矿物工程领域 Thomas Robins 发明了具有槽形结构的带式输送机,正式
确立了带式输送机的基本形式并沿用至今
[1]
。此后,带式输送机经过了两个多世纪的发
展,历经三次工业革命,新设计技术、新兴材料的研究使带式输送机的发展进入新纪元。
应用也大大促进了带式输送机的发展。输送带由早期的简单帆布带发展到至今的织物芯
输送带和钢绳芯输送带,提高了输送带的承载能力和输送能力;通用型、耐热型、耐寒
- 1、下载文档前请自行甄别文档内容的完整性,平台不提供额外的编辑、内容补充、找答案等附加服务。
- 2、"仅部分预览"的文档,不可在线预览部分如存在完整性等问题,可反馈申请退款(可完整预览的文档不适用该条件!)。
- 3、如文档侵犯您的权益,请联系客服反馈,我们会尽快为您处理(人工客服工作时间:9:00-18:30)。
输送设备模块化设计的研究及应用
在AS/RS自动化物流系统中,应用了大量的输送设备(如辊道输送机、皮带输送机、链式输送机、升降输送机等),但该类型输送设备的日常设计工作大部分是变型设计,即输送设备的工作原理和功能结构未改变,只是模仿变更现有产品的尺寸或配置。
目前这样的变型设计大多采用传统的设计方法,多属重复性的劳动。
随着经济全球化的发展和市场竞争的加剧,传统的以具体产品结构为中心组织产品数据,按需进行产品设计、生产和管理的模式越来越难以适应多变的市场需求,促使企业在提高产品的性能和质量的同时,还要求产品具有更大的适应性,以满足多变的市场对小批量、多品种、多规格产品的需要,并力争为企业争取最大的利润。
模块化设计作为一种先进的设计方法,是快速开发新产品的有效手段,也是进行CAD及形成柔性生产的基础;模块化设计就单个部件来说仍是以传统机械设计方法为基础的,而从总体上来说则是对传统机械设计方法的进一步发展和完善。
针对物流输送设备产品品种多、系列性强、产品较成熟等特点,以现有产品为对象,选择一种结构先进、性能稳定的产品为基型,在综合分析用户需求的基础上,设计出一系列功能模块,通过对这些功能模块的选择和组合来构造不同类型的产品。
采用模块化设计不仅能使产品的设计与制造过程趋于合理化,而且可以增加产品的柔性和适应性,兼顾了制造企业与用户双方的利益,使低成本、快速批量生产多样化、多变性的产品成为可能。
该方法设计的输送类产品,设计试制周期短,产品更新快,而且质量稳定可靠,对提高产品的市场竞争力有着不可低估的作用。
1、面向设计的模块划分
模块化设计需将用户经常定制的部分独立出来形成模块,以快速满足用户的个性化需求,重点考虑的是结合部位的接口要求,同时要求模块的功能相对独立、结构完整,便于模块的修改与替换,且必须考虑相邻机型的零部件的组合更换。
进行模块化设计时,必须首先把产品合理地划分成若干模块,然后以模块为基本单元进行设计,模块划分是模块化设计中最基础的工作,模块划分的合理性对模块化产品的性能、外观以及模块划分的通用化程度和成本都有很大影响,设计者可以从不同的角度对产品进行模块划分。
面向设计的模块划分的重点是考虑产品的功能,即主要根据产品各组成部分功能上的相关程度来进行模块划分;面向设计的模块化的主要目的就是把可能发生变化的功能需求所对应的部分独立出来,当用户需求发生变化时,只影响到产品某个局部,设计者可以只针对用户需求对某个局部进行改进或重新设计而不必改变产品的其它部分。
这样,可以最大限度地利用以往的设计成果,方便新产品的设计,加快新产品的开发速度。
下面以自动化物流系统中用于输送木制托盘类物料的辊道输送机为实例分析其功能与结构,并进行模块的划分。
2、辊道输送机与模块划分原则
从辊道输送机的需求和功能出发,根据模块化设计原理,把总功能按层次分解成相对独立的子功能,并将各层功能转化为相应结构单元,这些结构单元经典型化处理,使之成为具有相对独立的特定功能和规范化接口(包括其联接部位的形状、尺寸及联接件之间的配合参数等)的通用单元(模块)。
对一些为适应用户需求变化的单元,则作为变型模块或专用模块处理。
模块划分的合理性对模块化产品的性能、外观以及模块的通用化程度和成本都有很大影响,在进行模块划分过程中,如果模块划分过细,则模块数量数目过大,组装过程复杂、工作量大,也不便管理;如果模块划分过粗,则模块结构复杂,柔性差。
据上述原则,辊道输送机的模块划分如下:
(1)用不变要素(零部件)集合构成的单元作为模块。
这样的模块具有通用性和稳定性,可不加修改地直
接用来组合成产品系统,容易保证装配质量和效率。
在模块划分过程中,应注意模块和部件的区别,模块的划分应强调功能的独立性,部件的划分强调结构的完整性,应充分注意模块的互换性;
(2)将产品系统设计中变化活跃的单元,作为独立的变型模块或专用模块处理,这样处理有利于适应不同用户的个性化需求和实现产品的技术改进;
(3)模块应具有相对独立性。
即对于已分解的功能单元在结构上尽可能做到独立化,这样的模块易于拼组和搭配,便于构成多种变型产品。
在模块划分过程中,同时还要考虑在模块中留有一定的发展空间,以便引入新技术时不会影响模块的基本功能和结构。
典型的辊道输送机的结构如图1所示,它主要由杯形支脚、支腿组件、非驱动侧机架、驱动侧机架、辊子组件、汇线槽组件、驱动装置、光电检测装置等部件构成。
1-可调支脚;2-支腿组件;3-非驱动侧机架;4-驱动侧机架;5-辊子组件;6-汇线槽组件;7-驱动装置;8-光电检测
装置
图1 辊道输送机结构示意图
3、辊道输送机模块划分
图2 辊道输送机模块划分示意
根据功能与模块的映射关系,考虑整个辊道输送机产品系列的特点和结构形式,运用模块划分原则,可规划出辊道输送机较为通用的模块划分原则,如图2所示。
辊道输送机分为传动模块、机架模块、支承模块、辅助模块四大一级模块,并继续往下细分成各功能模块。
通过对同一功能模块进行分析,由于用途和结构不同,可以得到能够互换并具有相同接口的结构模块,通过更换或加减某些结构模块能够组合得到不同系列的辊道输送机。