Experimental investigation on surface roughness of KDP crystal processed face milling
中文小论文格式要求

中文小论文格式要求【篇一:中文期刊、小论文格式和要求(工学)】题目三号粗体居中,段前空1行,段后空0.5行学号,姓名(小四粗体居中,段前后各0.5行)日期(五号居中,段前0.5行,段后1行)摘要:这是文献报告写作要求。
排版格式要求包括用纸,页面设置、字体、行距等。
基本要求中强调独立撰写,不可简单剪贴现成资料。
对文献的数量和质量做出规定,提供文献清单实例,指出一些通病,并给出评分依据。
关键词:english title uses the same format as the chinese titleabstract: an english abstract must be included, which shouldbe 400~500 words in length. this will be a part of the basis for the assessment of your technical english proficiency. youmust write it in your own words, rather than just copy from a reference. mind you that anyone who simply copies from materials written by others will not pass the examination.keywords:1. 引言文献报告格式要求:用a4纸,通栏排版。
页边距:上2.2厘米,下2厘米,左2.7厘米,右2.3厘米。
必须插入居中页码。
除摘要和文献清单用单倍行距外,其余(包括正文、标题、姓名、日期)一律用1.25倍行距。
中文一律用宋体,英文和数字一律用times new roman。
摘要和文献用小五号字,正文用五号,段前段后不留空行。
中文摘要段前段后各空0.5行。
英文摘要段前空0.5行,段后空1行。
BSEN13697-2015Chemicaldisinfectantsandantiseptics.Quantitativenon-poroussurfacetestforthe

British Standards Institution Provided by IHS under license with BSI - Uncontrolled Copy No reproduction or networking permitted without license from IHS
--`,``,``,``,,```````,``,-`-``,```,,,`---
British Standards Institution Provided by IHS under license with BSI - Uncontrolled Copy No reproduction or networking permitted without license from IHS
British Standards Institution Provided by IHS under license with BSI - Uncontrolled Copy No reproduction or networking permitted without license from IHS
EUROPEAN COMMITTEE FOR STANDARDIZATION COMITÉ EUROPÉEN DE NORMALISATION EUROPÄISCHES KOMITEE FÜR NORMUNG
CEN-CENELEC Management Centre: Avenue Marnix 17, B-1000 Brussels
© 2015 CEN
All rights of exploitation in any form and by any means reserved worldwide for CEN national Members.
Experimental investigation on capillary force of composite wick structure

Experimental investigation on capillary force of composite wick structure by IR thermal imaging cameraYong Tang,Daxiang Deng *,Longsheng Lu,Minqiang Pan,Qinghui WangSchool of Mechanical and Automotive Engineering,South China University of Technology,Wushan Road,Guangzhou 510640,Chinaa r t i c l e i n f o Article history:Received 1January 2009Received in revised form 3October 2009Accepted 19October 2009Keywords:Composite wick Meniscus Heat pipes Capillary forceIR thermal imaginga b s t r a c tA novel sintered–grooved composite wick structures has been developed for two-phase heat transfer devices.With ethanol as the working fluid,risen meniscus test is conducted to study the capillary force of wick structures.Infrared (IR)thermal imaging is used to identify and locate the liquid meniscus.The effects of sintered layer,V-grooves and powder size on capillary force are explored.The results show that the capillary force of composite wick structures is larger than that of grooved and sintered ones.Interac-tion wetting between groove and sintered powder happens during the liquid rise in composite wick,which provides an additional source of capillary force.It exhibits a variation of capillary force of compos-ite wicks with different powder size due to the difference of open pore size and quantity in sintered por-ous matrix.Ó2009Elsevier Inc.All rights reserved.1.IntroductionDevelopment of heat pipes,vapor chambers and capillary pumped loops (CPL)is motivated by the thermal management of electronic components.These heat transfer devices work via two-phase flow.By evaporation and condensation,heat is transported from one end to the other or spread to a large area.Two-phase heat transfer devices consist of a number of components,such as evap-orator,wick and condenser.The wick shows great effects on the heat transfer performances of these devices.Wick structures are generally grooved or sintered.Sintered wicks have large capillary force but low permeability,while grooved wicks have high perme-ability but small capillary force [1].Capillary force and permeabil-ity are somehow contradictory in a single wick.However,composite wicks can balance these two competing factors and im-prove heat transfer performances.Currently,researches have been focused on composite wick structures [2–4].Hwang et al.[2]ob-tained modulated composite wicks by making grooves over a thin uniform porous layer.The modulated composite wick improved heat transfer performance by providing extra cross-sectional area for enhanced axial capillary liquid flow and extra evaporation sur-face area.Wang and Catton [3]investigated a composite structure with a thin porous layer on the triangular groove.It was found that evaporation heat transfer in the composite structure was three to six times higher than that in the groove without a porous layer.Capillary force of wick plays the driving force of the circulation of working liquid in two-phase heat transfer rge capil-lary force makes these devices work well.Capillary force of wick has been determined mainly through two methods.One is the bub-ble point test [5].Pressurized gas is applied to one end of a wick saturated with liquid.With the pressure gradually increasing,the point that bubbles appear on the opposite end of the wick is re-corded for the capillary force.The other method is the risen menis-cus test [6,7].One end of a wick is dipped into the working liquid.Then the liquid level rises in the wick sample until the pressure on both sides of the meniscus equilibrates.Nowadays,the latter method has been widely used due to its convenience.Chen et al.[8]observed the liquid fronts in the inclined wick by optical micro-scope (OM)and CCD camera.Holley and Faghri [9]obtained the closed form solution of effective pore radius and permeability of wicks by sight and weight change.Nevertheless,visualization of the meniscus by sight may be not accurate because most of the working liquid is colorless and transparent.In the case of micro grooved or sintered wick structures,it is difficult to locate the meniscus.This problem may be solved with the technique of infra-red (IR)thermal imaging.IR thermal imaging can provide accurate and non-contact measurement of temperature field [10].It has been used for the test of thermal performance and heated flow of liquid film of two-phase heat transfer devices [11–15].Due to the infrared emissivity difference between wick samples and working liquid,the meniscus can be accurately located by IR ther-mal imaging.Thus,the rising of the wetted height driven by capil-lary force can be investigated.0894-1777/$-see front matter Ó2009Elsevier Inc.All rights reserved.doi:10.1016/j.expthermflusci.2009.10.016*Corresponding author.Tel./fax:+862087114634.E-mail address:dengdaxiang88@ (D.Deng).Experimental Thermal and Fluid Science 34(2010)190–196Contents lists available at ScienceDirectExperimental Thermal and Fluid Sciencejournal homepage:www.else v i e r.c o m /l o c a t e /e t fsThe present study proposes a novel sintered–grooved compos-ite wick structure by covering a layer of sintered copper powderon micro V-grooves.With the risen meniscus test method,the cap-illary force of the wick is investigated by the visualization of IR thermal imaging camera.2.Experimental2.1.Fabrication of composite wick structureSintered–grooved composite wick structure is shown in Fig.1.Micro V-grooves were made in copper base with the thickness of 1.0mm.Then copper powders were sintered on the grooves.Dur-ing sintering,adhesion and mass transfer happened by the driving of surface tension.Different powder particles bonded together.Due to the same material of copper,powder particles and groove fins also partially bonded together,as seen in Fig.2.Thus,sintered–grooved composite wick formed.The copper powders (supplied by ACuPowder International,LLC,USA)are of irregular morphol-ogy,with purity of 99.3%,produced by water atomization method [16].To optimize the sintered powder size,four composite wick samples were made.A grooved sample without powder and a sin-tered sample without grooves were also studied for comparison.For the sintered sample,a 0.5mm thick powder layer was sintered on 1.0mm thick copper base .All the samples had the same dimen-sions,with length 100mm and width 10mm,as shown in Table 1.Copper powder layer was sintered at temperatures 950±10°C in a tube furnace for half an hour under a reduction stream of 10%hydrogen and 90%argon.2.2.Experimental apparatusAn apparatus of the risen meniscus test is set up to determine the capillary force of wick structures,as shown in Fig.3.It consists of vertically adjusting device,sample fixing device,reservoir,IR thermal imaging camera,glass cover with a hole for IR thermal imaging visualization,PLC controller and PC.The classical working liquid,ethanol,is used in the experiment.At first,test sample is fixed in vertical in the sample fixing device.Secondly,the sample moves down to dip into ethanol by the vertically adjusting device in a constant speed.The dipped length of samples in the liquid is 2mm.At last,IR camera records the meniscus rising process in 1min from the point that the sample just dips into ethanol.Ambi-ent temperature is 30°C.The glass cover is used to ensure the cir-cumstance airflow stable.The volatilization of ethanol is in a constant speed.Therefore,the difference between samples can be observed accurately.2.3.Meniscus locating method in IR thermal imagingA FLIR ThermaCAM SC3000IR camera was used with a thermal sensitivity of 0.02K at 30°C and an accuracy of 1%for tempera-tures below 150°C of the full scale.The back-side of the samples was painted black to provide a uniform emissivity.Due to the infrared emissivity difference between copper and ethanol,differ-ent temperature distributions between samples and ethanol were displayed in IR thermal images.The meniscus could be accurately located as follows.As shown in Fig.4,a measuring line was drawn along the sample from the fixing device to the dipping end.It stoodNomenclature D powder size,l mg gravity acceleration,m/s 2h capillary wetted height,mm h g depth of grooves,mmh t height of total grooves,mm K permeability,mm 2M mass of powder,gr eff effective pore radius,mms spacing interval of grooves,mm T thickness of wick,mm wwidth of grooves,mmGreek symbols4P capcapillary force,Pa 4P cap ,com capillary force of composite wicks,Pa4P cap ,sin capillary force provided by sintered porous zone,Pa 4P cap ,gro capillary force provided by groove bottom zone,Pa 4P cap ,int capillary force provided interaction wetting zone,Pa e porosity,dimensionless l dynamic viscosity,Pa s h liquid–solid contact angle,rad q density,kg/m 3r surface tension,N/mFig.1.Schematic of sintered–grooved composite wickstructure.Fig.2.Sintered bonding of composite wick structure.Y.Tang et al./Experimental Thermal and Fluid Science 34(2010)190–196191for the sample and its length had been measured before the sample dipped into ethanol.A locating point was added in the measuring line.As this point moved vertically along the measuring line,the vertical line moved along the temperature distribution curve until arriving at the inflection point.The position of this inflection point stood for the meniscus.The height result of the point could be cal-culated.Thus,the wetted height,h ,was obtained.Besides,the wet-ted height over time during the whole visualization process could be accurately obtained.Thus,the rising velocity of wetted height could be also studied.3.Analysis of liquid flow characteristic in composite wick structureDuring the risen meniscus test,working liquid rises in a wick.The following assumptions are given:(i)steady-state laminar flow in the wick,(ii)uniform saturation with liquid along the wetted length and (iii)neglecting inertial effects and evaporation of liquid.In the initial time after the composite wick dips into ethanol,the liquid rises along two channels,micro groove and sintered por-ous layer.In the groove channel,liquid flows along a straight line on the groove surface,whereas in the sintered porous channel,li-quid flows tortuously by the open pores in sintered porous layer.The friction resistance of liquid flow in groove is smaller than that in sintered porous layer.Therefore,the liquid rises faster in the groove channel than in the sintered porous layer.However,there are small voids which interconnect the groove and sintered porous layer (Fig.2).The liquid in the groove channel and sintered porous layer does not flow separately.There is an interaction effect be-tween these two rising channels,that is,the fast liquid in groove channel drags the slow liquid in sintered porous layer.By this interaction effect,the liquid in these two channels converges to-gether and a balanced rising velocity reaches between groove and sintered porous layer.We name this kind of flow in composite wick as interaction wetting.It is somewhat similar to the plate-particle interaction during water saturation in the channels with particles in contact with a plate of the same material,which was analyzed by Lechman [17].Due to the interaction wetting,the composite wick is completely saturated except the closed poresTable 1Samples code and specifications.Sample code Powder size,D mm Mass ofpowder,M g Thickness of wick,T mm Height of total grooves,h t mm Spacing interval of grooves,s mm Depth of grooves,h g mm Width of grooves,w mm Porosity,e (%)Grooved ––– 1.360.80.650.85–Sintered 80–110 2.00 1.5––––55C40–6040–60 2.00 1.5 1.360.80.650.8554C60–8060–80 2.00 1.5 1.360.80.650.8554C80–11080–110 2.00 1.5 1.360.80.650.8554C110–140110–1402.001.51.360.80.650.8554Fig.3.Schematic of the risen meniscus testapparatus.Fig.4.Meniscus locating method of wick structure in IR images (sample:C110–140).192Y.Tang et al./Experimental Thermal and Fluid Science 34(2010)190–196in sintered porous layer.The interaction wetting repeats as the li-quid rises in wicks until a final equilibrium height reaches.As shown in Fig.5,the composite wick can be mainly divided into three parts for liquid flow,sintered porous zone,groove bot-tom zone and interaction wetting zone.Each flow zone provides a source of capillary force.Thus,we can obtain:D P cap ;com ¼D P cap ;sin þD P cap ;gro þD P cap ;int ð1Þwhere D P cap ,com is the capillary force of composite wicks,D P cap ,sin ,D P cap ,gro ,and D P cap ,int is defined to be the capillary force provided by sintered porous zone,groove bottom zone and interaction wet-ting zone,respectively.It should be noted that D P cap ,int is induced by the drag force of the fast liquid in groove,which acts on the slow liquid in sintered porous layer.4.Results and discussionsFor the rise of liquid during the risen meniscus test,capillary force of the wicks,D P cap ,plays the driving force.The total pressure loss,D P total ,plays the flow resistance,which consists of two parts,friction pressure loss and hydrostatic pressure loss,as follows:D P total ¼l e K h d hd tþq ghð2Þwhere l is the viscosity of working liquid,e is the porosity of wick structure,K is the permeability of wick structure,h is the wettedheight,d his the rising velocity of the wetted height,q is the liquid density,g is the gravitational acceleration.Because of the neglect of inertial effects,these are the only source of pressure change dur-ing the liquid rise.Thus,capillary force is equal to the total pressure loss:D P cap ¼l e h d hþq ghð3Þtherefore,the capillary force of different wicks can be compared byh and d hof liquid rise.For different wicks during the same test time,the sample with larger wetted height and rising velocity has larger capillary force.4.1.Effect of sintered layer on capillary forceAs can be seen in Fig.6,the liquid in all samples rose quickly at the early time of the rise process.As the wetted height increased,the rising velocity of the wetted height reduced -pared with the composite samples,the grooved sample had higher rising velocity in the first 15s.Without sintered powder in grooves,the friction resistance of liquid flow was small.Ethanol rose very fast in the grooves.The wetted height reached 30mm at 15s and the equilibrium height was obtained at 30s.After that the meniscus did not rise.While in the composite samples,the meniscus rose continuously for a longer time than grooved wick.The equilibrium height had not yet been obtained at the end of one minute.Fig.7shows the meniscus rising process of a compos-ite wick by IR thermal images.At the end of the test time,the wet-ted heights of all the four composite samples were larger than grooved wick.It can be concluded that composite wicks had larger capillary force than grooved one.This can be attributed to the anal-ysis in Wang’s report [3].Capillary force can be also obtained by the Laplace–Young equation as defined below:D P cap ¼2r r effð4Þwhere r is the surface tension of liquid and r eff is the effective cap-illary radius.As the sintered layer covered the grooves,a lot of small menisci formed in the sintered layer.The effective capillary radius decreased from the radius of big meniscus of the groove in grooved wick to the radius of small menisci in the sintered layer in compos-ite wick.Thus,from Eq.(4),the capillary force of composite wicks was larger than that of grooved one.Meanwhile,as analyzed in Sec-tion 3,from Eq.(1),sintered powder layer and interaction wetting provided two additional important portions of capillary force for composite wick.Thus,composite wicks have larger capillary force than grooved one.4.2.Effect of V-grooves on capillary forceA sintered sample,which has the same powder size with com-posite sample (80–110l m),was tested for comparison.The result was shown in Fig.8.During the first 10s,the wetted height andtheFig.5.Schematic of three liquid flow zones in a compositewick.Fig.6.Effects of sintered layer and powder size on wetted height of wicks.Y.Tang et al./Experimental Thermal and Fluid Science 34(2010)190–196193rising velocity were almost equal for both sintered and composite sample.It is due to that the capillary force difference between these two samples was small.Sintered porous layer in both wicks provided large capillary force for liquid rise.As the wetted height grew,the rising velocity reduced gradually.During this time,the capillary force difference between these two samples played an important role in liquid rise.Results show that the wetted height and the rising velocity of composite sample were larger than thatof sintered sample after 10s.It resulted from that the groove bot-tom zone and interaction wetting zone provided additional sources of capillary force for composite wick.Besides of the capillary force provided by sintered porous layer,the driving force of groove bot-tom zone and the drag force in interaction wetting zone increased the total capillary force of composite wicks.Thus,the capillary force of composite wick is a little larger than that of sintered wick.4.3.Effect of powder size on capillary force of composite wicks Experimental results in Fig.6shows that the wetted height of sample C80–110is the largest.Following was C110–140and C40–60.The smallest was C60–80.The rising velocity generally fol-lowed a similar order.Thus,the composite sample with the 80–110l m powder had the largest capillary force.It could be found that the capillary force of composite samples with large powder size (C80–110and C110–140)was larger than that with small powder size (C40–60and C60–80).This is mainly due to the porous matrix difference of composite wicks.As shown in Table 1,identi-cal porosity was obtained for these four samples.According to the definition of porosity [18],the volume sum of open pores and closed pores equaled for the samples,due to the same volume of the sintered layer in these four composite wicks.However,as shown in Fig.9,the open pore size and quantity varied,which strongly affected the liquid flow in wick structures.In porous ma-trix,only open pores could provide channels for liquid flow.Closed pores can not be saturated.Due to the existence of closed pores,li-quid would turn to flow by the adjacent open pores.Thus,theflow-Fig.7.IR images of the meniscus rising process of composite wick structure during one minute (sample:C110–140).parison between composite wick and sintered wick with the same powder size (80–110l m),wetted height versus time.194Y.Tang et al./Experimental Thermal and Fluid Science 34(2010)190–196ing channels became longer and the friction resistance of liquid flow increased.For the samples with small powder size (samples C40–60,C60–80),the voids among powder particles were apt to be filled or covered by other particles during sintering.A lot of closed pores existed.While for the samples with large powder size (samples C80–110,C110–140),there were larger voids among dif-ferent particles than that with small powder size.They could not be filled or covered by other particles due to their large size.More open pores formed.The open pores were bigger and they were eas-ier to interconnect with each other.Thus,there were more flowing channels for the liquid rise in sintered porous layer.The friction resistance of liquid flow was smaller.The liquid rose higher and faster.As a result,composite samples with large powder size have larger capillary force than that with small powder size.However,it was found in the experiments that capillary force does not increase linearly with powder size.It may be attributed to the difference of the interaction wetting effect.For the sample with large powder size (C80–110,C110–140),the interaction effect in sample C80–110with comparatively smaller powder size may be a little stronger in the liquid rise process,and the liquid in grooves may provide a little larger drag force acting on liquid in sintered porous layer than sample C110–140.Thus,the capillary force of sample C80–110is a little larger than sample C110–140.Similarly for the sample with small powder size,sample C40–60has slightly larger capillary force than sample C60–80.Other stud-ies,such as theoretical verification of powder size and other parameters’effects on interaction wetting,are still required in the future work.5.ConclusionsSintered–grooved composite wick has been presented for two-phase heat transfer devices.IR thermal imaging camera was usedin the risen meniscus test of capillary parison of the wetted height and rising velocity among composite,grooved and sintered wicks was conducted.Four composite wicks with different powder size ranged from 40–60l m to 110–140l m were tested.The conclusion can be summarized as follows:(1)For the infrared emissivity difference between liquid andsolid at a given temperature,the liquid meniscus in a wick can be accurately located by IR thermal images,including grooved,sintered and composite wicks.(2)Interaction wetting between groove and sintered powderhappens during the liquid rise,and composite wick can be mainly divided into three parts for liquid flow,sintered por-ous zone,groove bottom zone and interaction wetting zone.Each flow zone provides a source of capillary pos-ite wicks have larger capillary force than grooved and sin-tered ones.(3)Composite wicks with large powder size provide larger cap-illary force than that with small powder size.Friction resis-tance difference of liquid flow exists due to the variation in open pore size and quantity in different porous matrix of composite wicks.But the capillary force varies nonlinearly with the powder size.The optimal powder size of composite wick is suggested to be 80–110l m.Future work is needed for theoretically modeling of the liquid flow in composite wicks.Besides,theoretical analysis of powder size and other parameters’effect on interaction wetting and capil-lary force will be carried out.AcknowledgementsThis work is financially supported by the National Natural Sci-ence Foundation of China,Project No.U0834002andNo.Fig.9.SEM photograph of sintered porous matrix of composite samples showing variation in open pore size and quantity:(a–d)correspond to samples C40–60to C110–140,respectively.Y.Tang et al./Experimental Thermal and Fluid Science 34(2010)190–19619550705031,50975092,and Guangdong Natural Science Foundation, Project No.07118064,and No.8151064101000058.References[1]I.Sauciuc,M.Mochizuki,K.Mashiko,Y.Saito,T.Nguyen,The design and testingof the superfiber heat pipes for electronics cooling applications,in: Proceedings of16th IEEE Semiconductor Thermal Measurement and Management Symposium,San Jose,USA,2000,pp.27–32.[2]G.S.Hwang,M.Kaviany,W.G.Anderson,J.Zuo,Modulated wick heat pipe,Int.J.Heat Mass Transfer50(7–8)(2007)1420–1434.[3]J.L.Wang,I.Catton,Enhanced evaporation heat transfer in triangular groovescovered with a thinfine porous layer,Appl.Therm.Eng.21(17)(2001)1721–1737.[4]G.Franchi,X.Huang,Development of composite wicks for heat pipeperformance enhancement,Heat Transfer Eng.29(10)(2008)873–884. [5]D.R.Adkins,R.C.Dykhuizen,Procedures for measuring the properties of heatpipe wick materials,in:Proceedings of the28th Intersociety Energy Conversion Engineering Conference,Washington DC,1993,pp.911–917. [6]A.Das,A.K.Chatterjee,S.P.Basu,A method of measuring capillary rise in a heatpipe,Int.J.Heat Mass Transfer28(10)(1985)1959–1960.[7]A.Faghri,Heat Pipe Science and Technology,Taylor&Francis,Washington,DC,1995.[8]S.W.Chen,J.C.Hsieh,C.T.Chou,H.H.Lin,S.C.Shen,M.J.Tsai,Experimentalinvestigation and visualization on capillary and boiling limits of micro-grooves made by different processes,Sens.Actuat.A:Phys.139(1–2)(2007)78–87.[9]B.Holley, A.Faghri,Permeability and effective pore radius measurementsfor heat pipe and fuel cell applications,Appl.Therm.Eng.26(4)(2006) 448–462.[10]H.Kaplan,Practical applications of infrared thermal sensing and imageequipment,O’Shea Series Editor,Georgia Institute of Technology,USA, 1993.[11]R.Boukhanouf,A.Haddad,M.T.North,C.Buffone,Experimental investigationof aflat plate heat pipe performance using IR thermal imaging camera,Appl.Therm.Eng.26(17–18)(2006)2148–2156.[12]C.Buffone,K.Sefiane,Controlling evaporative thermocapillary convectionusing external heating:an experimental investigation,Exp.Therm.Fluid Sci.32(6)(2008)1287–1300.[13]M.Cerza,B.Boughey,The effects of air infiltration on a largeflat heat pipe athorizontal and vertical orientations,ASME J.Heat Transfer125(2)(2003)349–355.[14]D.T.Queheillalt,G.Carbajal,G.P.Peterson,H.N.G.Wadley,A multifunctionalheat pipe sandwich panel structure,Int.J.Heat Mass Transfer51(1-2)(2008) 312–326.[15]F.Zhang,J.Peng,J.Geng,Z.X.Wang,Z.B.Zhang,Thermal imaging study on thesurface wave of heated falling liquidfilms,Exp.Therm.Fluid Sci.33(3)(2009) 424–430.[16]D.F.Berry, E.Klar,Powder metal technologies and applications.In:ASMHandbook,vol.7.ASM International,Materials Park,USA,1998.p.309. [17]J.Lechman,N.Lu,Capillary force and water retention between two uneven-sized particles,J.Eng.Mech.ASCE134(5)(2008)74–384.[18]J.Banhart,Manufacture,characterisation and application of cellular metalsand metal foams,Prog.Mater.Sci.46(6)(2001)559–632.196Y.Tang et al./Experimental Thermal and Fluid Science34(2010)190–196。
汽车发动机英文参考文献(精选120个最新))

汽车发动机是为汽车提供动力的装置,是汽车的心脏,决定着汽车的动力性、经济性、稳定性和环保性。
下面是搜索整理的汽车发动机英文参考文献,欢迎借鉴参考。
汽车发动机英文参考文献一:[1]Barouch Giechaskiel,Ricardo Suarez-Bertoa,Tero L?hde,Michael Clairotte,Massimo Carriero,Pierre Bonnel,Maurizio Maggiore. Evaluation of NO x emissions of a retrofitted Euro 5 passenger car for the Horizon prize “Engine retrofit”[J]. Environmental Research,2018,166.[2]Shixuan Wang,Ying Liu,Carla Di Cairano-Gilfedder,Scott Titmus,Mohamed M. Naim,Aris A. Syntetos. Reliability Analysis for Automobile Engines: Conditional Inference Trees[J]. Procedia CIRP,2018,72.[3]Kévin Rosset,Violette Mounier,Eliott Guenat,Jürg Schiffmann. Multi-objective optimization of turbo-ORC systems for waste heat recovery on passenger car engines[J]. Energy,2018,159.[4]Mohamed Kamal Ahmed Ali,Hou Xianjun,Mohamed A.A. Abdelkareem,M. Gulzar,A.H. Elsheikh. Novel approach of the graphene nanolubricant for energy saving via anti-friction/wear in automobile engines[J]. Tribology International,2018,124.[5]Shweta Tripathi,K.A. Subramanian. Control of fuel spray wall impingement on piston bowl in palm acid oil biodiesel fueled direct injection automotive engine using retarded injection timing, EGR and increased compression ratio[J]. Applied Thermal Engineering,2018,142.[6]Gianfranco Gagliardi,Francesco Tedesco,Alessandro Casavola. A LPV modeling of turbocharged spark-ignition automotive engine oriented to fault detection and isolation purposes[J]. Journal of the Franklin Institute,2018.[7]Gritsada Sua-Iam,Natt Makul. Innovative utilization of foundry sand waste obtained from the manufacture of automobile engine parts as a cement replacement material in concrete production[J]. Journal of Cleaner Production,2018.[8]Kanhu Charan Nayak,Prashant P. Date. Manufacturing of light automobile engine piston head using sheet metal[J]. Procedia Manufacturing,2018,15.[9]Yisong Chen,Jinqiu Ma,Bin Han,Peng Zhang,Haining Hua,Hao Chen,Xin Su. Emissions of automobiles fueled with alternative fuels based on engine technology: A review[J]. Journal of Traffic and Transportation Engineering (English Edition),2018.[10]Xinfeng Zhang,Minghui Luo,Wei Dai,Chuanqi Yao,Jiwen Wang,DaojinHuang,Chunyang Wang. Automotive fuel cell engine test cell design and its thermal flow analysis[J]. International Journal of Hydrogen Energy,2018.[11]K. Sato,T. Sadahiro,M. Yamazaki,M. Iwase. Throttle Valve Control of Automotive Engine based on Boundary Model[J]. IFAC PapersOnLine,2018,51(13).[12]Ajay Kumar Maddineni,Dipayan Das,Ravi Mohan Damodaran. Numerical Investigation of Pressure and Flow characteristics of Pleated Air Filter System for Automotive Engine Intake Application[J]. Separation and Purification Technology,2018.[13]Masahiro Yamazaki,Kotoru Sato,Katsuya Shinozaki,Masami Iwase. Boundary Modeling and Identification of Normal Operation for Automobile Engine[J]. IFAC PapersOnLine,2018,51(31).[14]Guo Bin,Chen Hong,Song Dafeng. Research on Fast Matching Method of Power System Parameters of Parallel Hybrid Electric Vehicles[J]. IFAC PapersOnLine,2018,51(31).[15]Natália de Assis Brasil Weber,Bárbara Pacheco da Rocha,Paulo Smith Schneider,Luiz Carlos Daemme,Renato de Arruda Penteado Neto. Energy and emission impacts of liquid fueled engines compared to electric motors for small size motorcycles based on the Brazilian scenario[J]. Energy,2019,168.[16]Francesco Del Pero,Massimo Delogu,Marco Pierini. Life Cycle Assessment in the automotive sector: a comparative case study of Internal Combustion Engine (ICE) and electric car[J]. Procedia Structural Integrity,2018,12.[17]Shan Lin,Li Zhao,Shuai Deng,Jiaxin Ni,Ying Zhang,Minglu Ma. Dynamic performance investigation for two types of ORC system driven by waste heat of automotive internal combustion engine[J]. Energy,2019,169.[18]Zhang Jian,Piao Zhong-yu,Liu Shi-ying,Su Sheng-wei,Deng Li-jun. Investigation of wear behavior of graphite coating on aluminum piston skirt of automobile engine[J]. Engineering Failure Analysis,2019.[19]Karsten Wittek,Frank Geiger,Jakob Andert,Mario Martins,Vitor Cogo,Thompson Lanzanova. Experimental investigation of a variable compression ratio system applied to a gasoline passenger car engine[J]. Energy Conversion and Management,2019,183.[20]Adnan Kadhim Rashid,Mohd Radzi Abu Mansor,Alexandru Racovitza,Radu Chiriac. Combustion Characteristics of Various Octane Rating Fuels for Automotive Thermal Engines Efficiency Requirements[J]. Energy Procedia,2019,157.[21]Marlon Cadrazco,Alexander Santamaría,John R. Agudelo. Chemical and nanostructural characteristics of the particulate matter produced by renewable diesel fuel in an automotive diesel engine[J]. Combustion and Flame,2019,203.[22]Kenneth Holmberg,Ali Erdemir. The impact of tribology on energy use and CO 2 emission globally and in combustion engine and electric cars[J]. Tribology International,2019,135.[23]Hongli Gao,Fujun Zhang,Sufei Wang,Hao Wu,Zhengkai Wang. Effect of Characteristic Parameters on the Magnetic Properties of Voice Coil Motor for Direct Fuel Injection in Gasoline Engine[J]. Energy Procedia,2019,158.[24]Xunan Gao,Bojan Savic,Roland Baar. A numerical procedure to model heat transfer in radial turbines for automotive engines[J]. Applied Thermal Engineering,2019,153.[25]Senthil Kumar Kandasamy,Arun Saco Selvaraj,Thundil Karuppa Raj Rajagopal. Experimental investigations of ethanol blended biodiesel fuel on automotive diesel engine performance, emission and durability characteristics[J]. Renewable Energy,2019,141.[26]Ganesh Duraisamy,Murugan Rangasamy,Nagarajan Govindan. A comparative study on methanol/diesel and methanol/PODE dual fuel RCCI combustion in an automotive diesel engine[J]. Renewable Energy,2020,145.[27]Nosratollah Izadiamoli,Hoseyn Sayyaadi. Conceptual design, optimization, and assessment of a hybrid Otto-Stirling engine/cooler for recovering the thermal energy of the exhaust gasses for automotive applications[J]. Energy Conversion and Management,2018,171.[28]Federico Millo,Pranav Arya,Fabio Mallamo. Optimization of automotive diesel engine calibration using genetic algorithm techniques[J]. Energy,2018,158.[29]Yonggyu Lee,Seungmook Oh,Changup Kim,Junsun Lee,Kanghun Lee,Junghwan Kim. The dual-port fuel injection system for fuel economy improvement in an automotive spark-ignition gasoline engine[J]. Applied Thermal Engineering,2018,138.[30]S. d'Ambrosio,A. Ferrari,D. Iemmolo,A. Mittica. Dependence of combustion noise on engine calibration parameters by means of the response surface methodology in passenger car diesel engines[J]. Applied Thermal Engineering,2019.汽车发动机英文参考文献二:[31]Ivan Bortel,Ji?í Vávra,Michal Takáts. Effect of HVO fuel mixtures onemissions and performance of a passenger car size diesel engine[J]. Renewable Energy,2019,140.[32]Jaeho Cho,Kangjin Kim,Sungha Baek,Cha-Lee Myung,Simsoo Park. Abatement potential analysis on CO 2 and size-resolved particle emissions from a downsized LPG direct injection engine for passenger car[J]. Atmospheric Pollution Research,2019.[33]Jamie Sleigh,Catherine E. Warnaby. Finding the starter motor for the engine of consciousness[J]. British Journal of Anaesthesia,2019,123(3).[34]S. Prakash,M. Prabhahar,S. Sendilvelan,R. Venkatesh,Sanjay Singh,K. Bhaskar. Experimental studies on the performance and emission characteristics of an automobile engine fueled with fish oil methyl ester to reduce environmental pollution[J]. Energy Procedia,2019,160.[35]Sabino Caputo,Federico Millo,Giulio Boccardo,Andrea Piano,Giancarlo Cifali,Francesco Concetto Pesce. Numerical and experimental investigation of a piston thermal barrier coating for an automotive diesel engine application[J]. Applied Thermal Engineering,2019,162.[36]Nicole D?rr,Adam Agocs,Charlotte Besser,Andjelka Risti?,Marcella Frauscher. Engine Oils in the Field: A Comprehensive Chemical Assessment of Engine Oil Degradation in a Passenger Car[J]. Tribology Letters,2019,67(3).[37]Sumanchandran Devendran,Rajeshkumar Ramasamy,Varatharaj Neelakandan,Thulasirajan Ganesan,Praveen Chakrapani Rao. Failure assessment using accelerated testing on IC engine’s starter motor for reliability improvement[J]. Life Cycle Reliability and Safety Engineering,2019,8(2).[38]Jaegu Choi,Jongmin Lee,Namgyu Jun,Chang-Sung Seok,Sunghwan Park,Gayeon Kim. Development of Laboratory Fatigue Testing Apparatus for Automotive Vehicle Engine Valve Simulating Actual Operating Conditions[J]. International Journal of Precision Engineering and Manufacturing,2019,20(7).[39]Pavel Nicolaie,Chiriac Radu,Birtas Adrian,Draghici Florin,Dinca Mihai. On the improvement by laser ignition of the performances of a passenger car gasoline engine.[J]. Optics express,2019,27(8).[40]Ahmadipour Fatemeh,Esmaeili Sari Abbas,Bahramifar Nader. Characterization, concentration and risk assessment of airborne particles using car engine air filter (case study: Tehran metropolis).[J]. Environmental geochemistry and health,2019.[41]Sleigh Jamie,Warnaby Catherine E. Finding the starter motor for the engine of consciousness.[J]. British journal of anaesthesia,2019,123(3).[42]Derry Matthew J,Smith Timothy,O'Hora Paul S,Armes Steven P. Block Copolymer Nanoparticles Prepared via Polymerization-Induced Self-Assembly Provide Excellent Boundary Lubrication Performance for Next-Generation Ultralow-Viscosity Automotive Engine Oils.[J]. ACS applied materials & interfaces,2019.[43]. Hyundai Motor Company; Patent Issued for Continuous Variable Valve Duration Apparatus And Engine Provided With The Same (USPTO 10,060,307)[J]. Journal of Engineering,2018.[44]. Mazda Motor Corporation; Patent Issued for Engine Control Device (USPTO 10,060,372)[J]. Journal of Engineering,2018.[45]. Automotive Engine Market 2018 Global Industry Outlook By Size, Key Players, Trends, Share, Suppliers, Statistics, Sales, Growth, And Regional Forecast To 2023[J]. M2 Presswire,2018.[46]. Mathematics - Applied Mathematics; Researchers at University of Calabria Report New Data on Applied Mathematics (A LPV modeling of turbocharged spark-ignition automotive engine oriented to fault detection and isolation purposes)[J]. Journal of Transportation,2018.[47]. Ford Global Technologies LLC; "Hybrid Module, Hybrid Unit And Motor Vehicle As Well As Starting Process For An Internal Combustion Engine" in Patent Application Approval Process (USPTO 20180238291)[J]. Politics & Government Week,2018.[48]. Mazda Motor Corporation; Patent Application Titled "Engine Control Device" Published Online (USPTO 20180245529)[J]. Energy Weekly News,2018.[49]. Hitachi Automotive Systems Ltd.; "Cooling Device For Internal Combustion Engine Of Vehicle And Control Method Thereof" in Patent Application Approval Process (USPTO 20180245504)[J]. Journal of Transportation,2018.[50]. Automotive Engine Valves Market 2018 Global Industry Size, Key Player, Share, Mergers, Acquisition, Growth Analysis By Valves Type, Technology, Fuel Type, Vehicle And Region To 2023[J]. M2 Presswire,2018.[51]. Litens Automotive Partnership; Patent Issued for Isolator For Use With Engine That Is Assisted Or Started By An MGU Or A Motor Through An Endless Drive Member (USPTO 10,060,502)[J]. Journal of Engineering,2018.[52]. Honda Motor Co. Ltd.; Patent Issued for Supercharged Engine (USPTO 10,060,337)[J]. Journal of Engineering,2018.[53]. Hyundai Motor Company; Patent Issued for Method Of And System For Generating Virtual Engine Sound (USPTO 10,059,260)[J]. Journal of Engineering,2018.[54]. Suzuki Motor Corporation; Researchers Submit Patent Application, "Lubrication Structure For Internal Combustion Engine", for Approval (USPTO 20180238203)[J]. Politics & Government Week,2018.[55]. Energy; Studies from Brunel University in the Area of Energy Described (Expander Technologies for Automotive Engine Organic Rankine Cycle Applications)[J]. Journal of Engineering,2018.[56]. Hitachi Automotive Systems Ltd.; Patent Application Titled "Cooling Device For Internal Combustion Engine Of Vehicle And Control Method Thereof" Published Online (USPTO 20180245503)[J]. Journal of Transportation,2018.[57]. Honda Motor Co.Ltd.; Patent Application Titled "Internal Combustion Engine For Vehicle" Published Online (USPTO 20180245509)[J]. Politics & Government Week,2018.[58]. Honda Motor Co. Ltd.; Patent Issued for V Engine Having Valve Property Varying Mechanism (USPTO 10,066,553)[J]. Journal of Engineering,2018.[59]. Nissan Motor Co. Ltd.; Patent Issued for Vehicle Engine Stop Control Device (USPTO 10,065,646)[J]. Journal of Transportation,2018.[60]. Yamaha Motor Power Products Kabushiki Kaisha; Patent Issued for Engine (USPTO 10,066,522)[J]. Journal of Engineering,2018.汽车发动机英文参考文献三:[61]. Continental Automotive Systems Inc.; Patent Application Titled "Connected Energy Management And Autonomous Driving Strategy For Engine Cylinder Deactivation" Published Online (USPTO 20180238249)[J]. Journal of Transportation,2018.[62]. Honda Motor Co. Ltd.; Patent Issued for Variable Valve Mechanism For Internal Combustion Engine (USPTO 10,066,518)[J]. Journal of Engineering,2018.[63]. Suzuki Motor Corporation; Patent Issued for Engine For Outboard Motor (USPTO 10,059,416)[J]. Journal of Engineering,2018.[64]. MAHLE International GmbH; "Internal Combustion Engine For A Motor Vehicle" in Patent Application Approval Process (USPTO 20180216583)[J]. Energy Weekly News,2018.[65]. Hyundai Motor Company; "Engine Cooling System" in Patent Application Approval Process (USPTO 20180163608)[J]. Energy Weekly News,2018.[66]Jedd Cole. Grinder Simplifies Automotive Engine Part Production[J]. Modern Machine Shop,2018,91(3).[67]. Energy; Reports Outline Energy Study Results from Swiss Federal Institute of Technology in Lausanne (Multi-objective optimization of turbo-ORC systems for waste heat recovery on passenger car engines)[J]. Energy Weekly News,2018.[68]. Science - Applied Sciences; Researchers from Inha University Provide Details of New Studies and Findings in the Area of Applied Sciences (A New Method for Active Cancellation of Engine Order Noise in a Passenger Car)[J]. Science Letter,2018.[69]. Honda Motor Co. Ltd.; Researchers Submit Patent Application, "Engine Generator", for Approval (USPTO 20180283340)[J]. Energy Weekly News,2018.[70]. Mazda Motor Corporation; Patent Application Titled "Control Device Of Compression Self-Ignition Engine" Published Online (USPTO 20180283296)[J]. Energy Weekly News,2018.[71]. Continental Automotive GmbH; "High-Pressure Fuel Pump And Fuel Supply Device For An Internal Combustion Engine, In Particular Of A Motor Vehicle" in Patent Application Approval Process (USPTO 20180283336)[J]. Energy Weekly News,2018.[72]. Kia Motors Corporation; "Hybrid Vehicle And Method Of Controlling Engine Start" in Patent Application Approval Process (USPTO 20180297578)[J]. Energy Weekly News,2018.[73]. Mazda Motor Corporation; Patent Issued for Fuel Injection Control Device For Direct-Injection Engine (USPTO 10,119,492)[J]. Energy Weekly News,2018.[74]. Nissan Motor Co. Ltd.; Patent Issued for Engine Control Device And Engine Control Method (USPTO 10,119,486)[J]. Energy Weekly News,2018.[75]. Johnson Electric S.A.; "Motor, Circuit Board, And Engine Cooling Module Including The Motor" in Patent Application Approval Process (USPTO 20180337578)[J]. Electronics Business Journal,2018.[76]. Mazda Motor Corporation; Patent Application Titled "Structure Of Mounting Intake Air Temperature Sensor Of Engine With Supercharger" Published Online (USPTO 20180340496)[J]. Energy Weekly News,2018.[77]. Kia Motors Corporation; "System And Method For Controlling Engine Clutch" in Patent Application Approval Process (USPTO 20180335096)[J]. Energy Weekly News,2018.[78]. Kia Motors Corporation; "Method For Starting Engine For Hybrid Electric Vehicle" in Patent Application Approval Process (USPTO 20180340503)[J]. Energy Weekly News,2018.[79]. Kia Motors Corporation; "Piston For Engine" in Patent Application Approval Process (USPTO 20180340491)[J]. Energy Weekly News,2018.[80]Maniatis P,Wagner U,Koch T. A model-based and experimental approach for the determination of suitable variable valve timings for cold start in partial load operation of a passenger car single-cylinder diesel engine[J]. International Journal of Engine Research,2019,20(1).[81]Tauzia Xavier,Maiboom Alain,Karaky Hassan,Chesse Pascal. Experimental analysis of the influence of coolant and oil temperature on combustion and emissions in an automotive diesel engine[J]. International Journal of Engine Research,2019,20(2).[82]. Kia Motors Corporation; Patent Issued for Engine Idle Operation Control Method And System For Heating Of Hybrid Electric Vehicle (USPTO 10,220,828)[J]. Energy Weekly News,2019.[83]. Suzuki Motor Corporation; Patent Issued for Engine Control Device And Engine Control Method (USPTO 10,232,924)[J]. Computers, Networks & Communications,2019.[84]. Kia Motors Corporation; "Gasoline Direct Injection Engine" in Patent Application Approval Process (USPTO 20190078500)[J]. Energy Weekly News,2019.[85]. Proposed Information Collection Request; Comment Request; Motor Vehicle and Engine Compliance Program Fees (Renewal), EPA ICR 2080.07, OMB Control No. 2060-0545[J]. The Federal Register / FIND,2019,84(070).[86]. Energy; Findings from Federal University of Santa Maria in the Area of Energy Reported (Experimental Investigation of a Variable Compression Ratio System Applied To a Gasoline Passenger Car Engine)[J]. Energy Weekly News,2019.[87]. Energy; Studies from Federal University in the Area of Energy Described (Energy and Emission Impacts of Liquid Fueled Engines Compared To Electric Motors for Small Size Motorcycles Based On the Brazilian Scenario)[J]. Energy Weekly News,2019.[88]. Central Motor Wheel Co. Ltd.; Patent Application Titled "Thermoacoustic Engine, And Designing Method For Thermoacoustic Engine" Published Online (USPTO 20190085833)[J]. Energy Weekly News,2019.[89]. Kia Motors Corporation; Researchers Submit Patent Application, "Apparatus For Improving Efficiency Of Turbocharger Engine", for Approval (USPTO 20190093548)[J]. Energy Weekly News,2019.[90]. Engineering - Automobile Engineering; University of Birmingham Reports Findings in Automobile Engineering (On-board Thermochemical Energy Recovery Technology for Low Carbon Clean Gasoline Direct Injection Engine Powered Vehicles)[J]. Energy Weekly News,2019.汽车发动机英文参考文献四:[91]. Kia Motors Corporation; "Method And Device For Controlling Engine During Idle Purge Of Canister" in Patent Application Approval Process (USPTO 20190112993)[J]. Energy Weekly News,2019.[92]. Hitachi Automotive Systems Ltd.; Patent Issued for Fuel Injection System For Internal Combustion Engine (USPTO 10,267,253)[J]. Energy Weekly News,2019.[93]Song Kang,Upadhyay Devesh,Xie Hui. A physics-based turbocharger model for automotive diesel engine control applications[J]. Proceedings of the Institution of Mechanical Engineers,2019,233(7).[94]. Hitachi Automotive Systems Ltd.; Patent Issued for Engine Control Device (USPTO 10,309,366)[J]. Energy Weekly News,2019.[95]. Continental Automotive GmbH; "Gas Internal Combustion Engine With Auxiliary Starting System" in Patent Application Approval Process (USPTO 20190162123)[J]. Energy Weekly News,2019.[96]. Fuel Research; Studies from Volvo Car Group Add New Findings in the Area of Fuel Research (Impact of Closely-coupled Triple-pilot and Conventional Double-pilot Injection Strategies In a Ld Diesel Engine)[J]. Energy Weekly News,2019.[97]. Kia Motors Corporation; Patent Issued for Engine Start Control Method (USPTO 10,316,814)[J]. Biotech Business Week,2019.[98]. Kia Motors Corporation; "Apparatus And Method For Starting Engine Of Mild Hybrid Electric Vehicle" in Patent Application Approval Process (USPTO 20190184972)[J]. Energy Weekly News,2019.[99]. Energy; Findings from K.N. Toosi University of Technology Provides New Data on Energy (Conceptual design, optimization, and assessment of a hybrid Otto-Stirling engine/cooler for recovering the thermal energy of the exhaust gasses for automotive ...)[J]. Energy Weekly News,2019.[100]. Toyota Jidosha Kabushiki Kaisha; "Automotive Engine Coolant Composition, Automotive Engine Concentrated Coolant Composition, And Method Of Operating Internal Combustion Engine" in Patent Application Approval Process (USPTO 20190194516)[J]. Energy Weekly News,2019.[101]. Kia Motors Corporation; "Engine Control Method For Heating Of Hybrid Electric Vehicle" in Patent Application Approval Process (USPTO 20190193516)[J]. Energy Weekly News,2019.[102]. Kia Motors Corporation; "Vehicle And Method For Controlling Engine Startup Reference Power" in Patent Application Approval Process (USPTO 20190202432)[J]. Energy Weekly News,2019.[103]. Energy; Technical University Details Findings in Energy (A fully automated smooth calibration generation methodology for optimization of latest generation of automotive diesel engines)[J]. Energy Weekly News,2019.[104]. Black &Decker Inc.; "Battery And Motor System For Replacing Internal Combustion Engine" in Patent Application Approval Process (USPTO 20190238083)[J]. Energy Weekly News,2019.[105]. Mazda Motor Corporation; "Exhaust Gas Control Device, Method, And Computer Program Product For An Engine" in Patent Application Approval Process (USPTO 20190234330)[J]. Energy Weekly News,2019.[106]Dongha Kim,JongRoul Woo,Jungwoo Shin,Jongsu Lee,Yongdai Kim. Can search engine data improve accuracy of demand forecasting for new products? Evidence from automotive market[J]. Industrial Management & Data Systems,2019,119(5).[107]R. Ellappan,S. Arumugam. The effect of corrosion inhibitor on corrosion of automotive materials in Biodegradable engine oil[J]. IOP Conference Series: Materials Science and Engineering,2018,390(1).[108]P. Wi?niowski,M ?l?zak,A Niewczas,T Szczepański. Method for synthesizing the laboratory exhaust emission test from car engines based on road tests[J]. IOP Conference Series: Materials Science and Engineering,2018,421(4).[109]J Kaszkowiak,M Markiewicz-Patalon. The impact on the manner of loading theengines powered with biogas and natural gas on the selected parameters of the motor oil[J]. IOP Conference Series: Materials Science and Engineering,2018,421(4).[110]A Wolff. Numerical analysis of gas flow through the labyrinth seal of piston rings of an automotive IC engine[J]. IOP Conference Series: Materials Science and Engineering,2018,421(4).[111]Z Kneba. Research on the phenomena of warming up and free cooling down the car engine[J]. IOP Conference Series: Materials Science and Engineering,2018,421(4).[112]N C Nutu,C Pana,N Negurescu,A Cernat,D Fuiorescu,L Nemoianu. An experimental approach on fuelling a passenger car diesel engine with LPG[J]. IOP Conference Series: Materials Science and Engineering,2018,444(7).[113]T Ulian,V Vornicu,E Rakosi,G Manolache,S Talif,I Agape. The study of the performance improvement possibilities by using the principle of zonal cooling for the automotive engine[J]. IOP Conference Series: Materials Science and Engineering,2018,444(7).[114]V Serevina,A A Azhar,T Sutandi,K Sumeru. Effect Of Engine Speed On The Performance Of Automotive Air Conditioning System Using R134a And R152a As Refrigerants[J]. Journal of Physics: Conference Series,2019,1150(1).[115]Willyanto Anggono,Sutrisno,Fandi D Suprianto,Muji Setiyo,Rendy Wibisono,Gabriel Jeremy Gotama. Experimental investigation of the effect of Nephelium Lappaceum seed biodiesel to the automotive diesel engine performance[J]. IOP Conference Series: Earth and Environmental Science,2019,257(1).[116]Guorui Jia,Huanhuan Ren,Dongchang Zhao,Chuan Chen,Rujie Yu,Peng Ge,Shaohui Liu. Numerical Simulation of Multiple Injections on the Combustion of Reactivity Distribution in Automotive Engine[J]. IOP Conference Series: Earth and Environmental Science,2019,252(3).[117]Xitong Zhang,Tao Peng,Fuxin Mao,Ming Cheng. Research on Key Technologies of Integrated Teaching Platform for Automotive Engine ECU Control System[J]. Journal of Physics: Conference Series,2019,1237(4).[118]Huanhuan Ren,Guorui Jia,Dongchang Zhao,Chuan Chen,Rujiex Yu,Peng Ge,Shaohui Liu. Simulation Study of Injection Strategy on the Emission in Automotive Engine[J]. IOP Conference Series: Earth and Environmental Science,2019,252(3).[119]Olufemi Sylvester Bamisaye,Anthony Yinka Oyerinde,Ubong Akpan Essien. Investigation of the Effects of Air-Conditioning System on the Temperature and Speed of Automobile Engine Using Paired T-Test and Regression Analysis[J]. Open AccessLibrary Journal,2019,06(01).[120]Huali Guo,Jia Cui,Guofu Wang,Hongwang Zhao. Analysis and Research on the Teaching Principle of Automotive Engine Based on CDIO Concept[P]. Proceedings of the 2018 International Conference on Sports, Arts, Education and Management Engineering (SAEME 2018),2018.以上就是关于汽车发动机英文参考文献的分享,希望对你有所帮助。
Modelling, simulation and experimental investigation
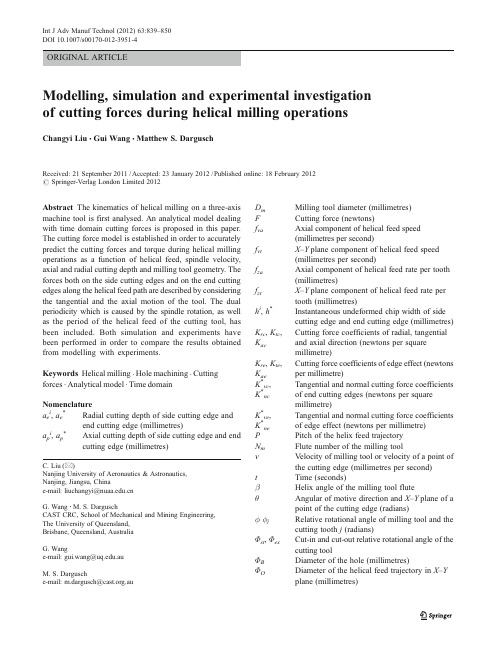
ORIGINAL ARTICLEModelling,simulation and experimental investigation of cutting forces during helical milling operationsChangyi Liu &Gui Wang &Matthew S.DarguschReceived:21September 2011/Accepted:23January 2012/Published online:18February 2012#Springer-Verlag London Limited 2012Abstract The kinematics of helical milling on a three-axis machine tool is first analysed.An analytical model dealing with time domain cutting forces is proposed in this paper.The cutting force model is established in order to accurately predict the cutting forces and torque during helical milling operations as a function of helical feed,spindle velocity,axial and radial cutting depth and milling tool geometry.The forces both on the side cutting edges and on the end cutting edges along the helical feed path are described by considering the tangential and the axial motion of the tool.The dual periodicity which is caused by the spindle rotation,as well as the period of the helical feed of the cutting tool,has been included.Both simulation and experiments have been performed in order to compare the results obtained from modelling with experiments.Keywords Helical milling .Hole machining .Cutting forces .Analytical model .Time domainNomenclature a e i ,a e *Radial cutting depth of side cutting edge andend cutting edge (millimetres)a p i ,a p *Axial cutting depth of side cutting edge and endcutting edge (millimetres)D m Milling tool diameter (millimetres)F Cutting force (newtons)f va Axial component of helical feed speed (millimetres per second)f vt X –Y plane component of helical feed speed (millimetres per second)f za Axial component of helical feed rate per tooth (millimetres)f zt X –Y plane component of helical feed rate per tooth (millimetres)h i ,h *Instantaneous undeformed chip width of side cutting edge and end cutting edge (millimetres)K rc ,K tc ,K ac Cutting force coefficients of radial,tangential and axial direction (newtons per square millimetre)K re ,K te ,K ae Cutting force coefficients of edge effect (newtons per millimetre)K *vc ,K *nc Tangential and normal cutting force coefficients of end cutting edges (newtons per square millimetre)K *ve ,K *ne Tangential and normal cutting force coefficients of edge effect (newtons per millimetre)P Pitch of the helix feed trajectory N m Flute number of the milling toolv Velocity of milling tool or velocity of a point of the cutting edge (millimetres per second)t Time (seconds)βHelix angle of the milling tool fluteθAngular of motive direction and X –Y plane of a point of the cutting edge (radians)ϕϕj Relative rotational angle of milling tool and the cutting tooth j (radians)Φst ,Φex Cut-in and cut-out relative rotational angle of the cutting toolΦB Diameter of the hole (millimetres)ΦODiameter of the helical feed trajectory in X –Y plane (millimetres)C.Liu (*)Nanjing University of Aeronautics &Astronautics,Nanjing,Jiangsu,Chinae-mail:liuchangyi@G.Wang :M.S.DarguschCAST CRC,School of Mechanical and Mining Engineering,The University of Queensland,Brisbane,Queensland,Australia G.Wange-mail:gui.wang@.au M.S.Dargusche-mail:m.dargusch@.auInt J Adv Manuf Technol (2012)63:839–850DOI 10.1007/s00170-012-3951-4ΩSpindle rotating angular velocity(radians per second)Ωh Helix feed rotating angular velocity(radians per second)1IntroductionHelical milling has been applied to generate boreholes by means of a milling tool to some difficult-to-cut materials. This innovative method was found to facilitate hole making in AISI D2tool steel in its hardened state,resulting in an enhancement in cutting tool life and the ability to machine H7quality holes with a surface finish of0.3μm Ra[1].The operation has also been applied to hole making in composite-metal compounds as a substitute for drilling operations.The impact of the axial and tangential feed per tooth on the process forces[2]has been investigated. Employing helical milling to aluminium with minimum quantity lubrication has shown an improvement in geometri-cal accuracy and a reduction in burr formation,lower cutting temperature and a smaller cutting force compared to drilling operations[3].The prediction of cutting force through modelling and simulation is an important research area in order to improve process ling is the most complex machining operation.Previously in the literature,machining mechanisms have been derived from a general model[4,5]and applied to the specific application,for example,five-axis milling, three-axis milling,peripheral milling,face milling and plunge milling.Modelling peripheral milling is a fundamental requirement in order to model more complex milling operations.A theoretical model based on the oblique cutting principle and cutting force coefficients has been developed in order to predict the cutting forces during peripheral milling[6–8].Considering the helical flute(or side cutting edge)of the milling cutters,an attempt to accurately simulate milling forces including the effects of engaged flute length and the number of engaged flutes caused by the radial and axial depths of cut has been previously presented[9].A common approach to facilitate the modelling of this complex situation including the milling tool geometry and the interaction with the workpiece involves analysing the cutting forces on axial discrete milling tools,then integrating these force elements.The intersection of the tool path swept envelope with the workpiece Z-buffer elements has been used to find the contact area between the cutter and the workpiece. An axial slice cutting tool discrete mechanistic model was used to estimate the cutting force vectors[10].Cutter entry and exit angles,along with the immersion angles,were used as boundary conditions in order to predict cutting forces when flank milling ruled surfaces with tapered,helical and ball end mills[11].The effect of lead and tilt angles between the cutter and the workpiece on the milling forces,tool deflections and form errors during multi-axis end milling have been analysed[12,13].During modelling of the cutting forces and system dynamics,one of the outstanding characteristics is that both side cutting edges and end cutting edges interact with the workpiece during helical milling processing.An accurate predictive model should describe and sum up the mechanics on both edges simultaneously.Ball end milling tools are most often used in three-axis or five-axis milling.Ball end milling tool processing models have been separated into ball end and cylindrical sections in order to obtain accurate prediction[10,14,15].A mechanistic force model describing the cutting force as a sum of the cutting and edge forces has been developed for a general end milling cutter(cylindrical,taper,ball,bull nose)with the specific cutting and edge force coefficients identified[16].As one type of three-axis milling operation,axial feed is a typical characteristic of helical milling operations. This operation uses a flat end mill not a ball end mill that is used in typical3-axis and5-axis milling situations.Axial feed using a flat end mill is also applied in plunge milling which is a two-axis operation.Considering rigid body motion of the cutter,the cutting force model and dynamics model for the plunge milling process in the time domain have been established[17,18].The cutting forces associated with plunge milling operations are predicted by considering the feed,radial engagement,tool geometry,spindle speed and the regenera-tion of the chip load due to vibrations[19].Considering the flexibility of the workpiece,tool setting errors and tool kine-matics and geometry,a horizontal approach was used to compute the chip area including the contribution of the main and side edge in the cutting zone[20].Drilling operations and boring operations typically involve axial feed.Both these operations are similar to helical milling and plunge milling operations but with different cutting tools.The drilling cutting forces and dynamics have been integrated into the model in order to obtain drilled hole profiles[21].A mechanistic model for predicting thrust force and torque during the drilling process using a drill tool with double-point angle edges [22].To predict temperatures and forces on both the drilling and ball end milling operations,the cutting edges of the twist drill lip and the ball end mill were divided into oblique cutting elements[23].A theoretical model to predict thrust and torque in high-speed drilling has been presented[24,25].The methodology for extracting cutting force coefficients for drilling operations has also been investigated[26].When modelling the drilling process, the axial feed effect was not considered explicitly because the lip of the twist drill has a taper angle(point angle),and the interaction between the lip and workpiece caused by spindle rotation could lead to a spontaneous axial force(thrust).In the literature,helical milling has been introduced as an enabling technology to substitute for drilling operations [1–3].In recent years,research on modelling the mechanics of the helical milling process has been published [27,28].Although both the side cutting edges and the end cutting edges have been considered to participate in the machining process,the detail interaction between the end cutting edges and workpiece still needs more elaborate investigation and description.Modelling,simulation and experimental investigation during cutting forces of the helical milling operation will be discussed in this paper including the influence of helical feed.This research aims to develop an analytical cutting force model in the time domain including both the axial cutting depth and the radial cutting depth associated with helical milling operations.The model considers the effects of both the tangential feed and axial feed,and the combination of both mechanics on the side cutting edges and the end cutting edges.2Kinematics of helical millingIn helical milling,the trajectory of a point on the milling toolcutting edge is the result of the spiral curve movement of the axis of the tool (reference frame)and the circular movement of the edge point relative to the axis (relative motion).Two sets of coordinates are defined to describe the motion of the cutter and the cutting force on the cutter;an X,Y ,Z global coordinate frame fixed to the workpiece and an x,y,z local coordinate frame fixed to the cutting tool with the origin at the centre of the end flat surface which defines the reference frame.A description of helical milling with tool feed using helical trajectory and the coordinate settings are depicted inFig.1.The feed motion of the tool is decomposed into two components,f va and f vt .f vt ¼ΦB ÀD m ðÞΩh 2¼N m Ωf zt2p mm =s ðÞð1Þf va ¼P Ωh 2p ¼N m Ωf za 2pmm =s ðÞð2ÞThe flat-end cylinder milling tools suitable for helical milling operations have two types of cutting edges:the side cutting edge (peripheral cutting edge)and the end cutting edge through the centre.The interaction characteristics of these two types with the workpiece are different.The side edges participate in the peripheral cutting component,while the end edges participate in the plunge cutting component.Therefore,these two movements will be initially analysed separately before being assembled or composed.The side edge cutting process is typical intermittent cutting.The undeformed chip geometry,width,depth,and thickness have been described in the literature [2].The side edge cutting process that is typical intermittent cutting is depicted in Fig.2(using superscript i ).The velocity composition of an arbitrary point on the side cutting edge is described in cross section perpendicular to the tool axis.The undeformed chip geometry can be described as a i e ¼D m ;hole generating ΦB ÀΦO2;hole enlarging&ð3Þa i p ðt Þ¼f va t ;t 2p =Ωh P ;t >2p =Ωh&ð4Þh i ¼f zt sin fð5ÞFig.1Kinematics of helical millingwhere ϕ¼2p ΩÆΩh ðÞt is the relative rotational angle of the cutter (+up milling,−down milling).The end edge cutting process,which is continuous cutting,is depicted in Fig.3(using superscript *).The velocity composition of an arbitrary point on the end cutting edge is described in the cross section perpendicular to the end cutting edge.The undeformed chip geometry,width and height can be described as:a Ãe ¼D m ;hole making ΦB ÀΦO 2;hole enlarging &ð6Þh üf za cos θð7Þ3Cutting force model for helical milling 3.1Cutter feed influence on the cutting forcesThe influence of cutter feed movement on the cutting forces during machining processing is almost always neglected.Similar to spindle rotation resulting in the relative movement between cutter and workpiece,cutter feed motion leads to relative movement also.This relative movement between the cutter and workpiece could influence the directionand magnitude of the cutting forces.The premise that the influence of the feed can be neglected is based on the assumption that the relative displacement and velocity from spindle rotation are much larger than the feed.Thus,in most situations,the influence of feed is insignificant and can be ignored.However,when modelling some specific machining operations including axial feed,such as drilling,plunge milling and helical milling,to ignore the feed motion is unreasonable.If the axial feed effect is not considered,the cutting force along the axial direction might not be expressed accurately.For this reason,analysis of the influence of axial feed on cutting forces when modelling helical milling operations is necessary.In this paper,the feed motion effect on cutting forces has been analysed completely.Firstly,the movement of an arbitrary point P at the side cutting edge could be decomposed to cylinder helical move-ment (reference movement)and circular movement perpen-dicular to the cutter axis,as depicted in Fig.1.The reference movement can be decomposed to horizontal tangential feed and perpendicular axial feed,shown in Fig.2.The horizon-tal velocity of point P is defined as v P 0v PO +v O ,where v O is identical to f vt .For Ω>>Ωh ,means |v PO |>>|v O |,and therefore,v P ≈v PO .The influence of horizontal tangential feed on the side edge cutting force can beignored.Fig.2Kinematics of the side cuttingedgeFig.3Kinemics of the end cutting edgeSecondly,axial feed f vz may result in a portion of the axial cutting force being on the side edge.For every axial feed,the cutting volume of the side edge is proportional to f za a e h i ,but the cutting volume of the end edge is proportional to f za a e p ΦB ÀD m ðÞ=sin θ.That means that the side edge undergoes intermittent cutting while the end edge undergoes continuous cutting.In the same time period,the cutting force derived from axial feed on the side edge is much smaller than that on the end side.So,the influence of axial feed on the side edge cutting force can also be ignored.Then,assuming the top points on an end cutting edge in a straight line,the radial distance of point P to the cutting axis is variable.The influence of the horizontal feed f vt is more outstanding when P is near to the axis.The horizontal movement of point P at the end edge can be decomposed into the relative tangential part v t and relative radial part v r ,as described in pared to drilling or plunge milling operations in which tangential cutting forces are vanished andtangential velocity of the z -axis is zero,tangential forces and axis tangential velocity of the helical milling are not zero,as depicted in Fig.4.For the aforementioned reason,the influence of horizontal tangential feed on end edge cutting forces can be ignored.The existence of the relative radial part v r of the end edge implies that the radial force also exists.If we consider the end cutting edge of the flat-end milling cutter as approximately a straight line,the cutting edge along the radial direction slides rather than shears.F r *should be the friction force that is smaller than the shear force.Therefore,the radial force onthe end edge can be neglected,or F Ãa ¼0.Finally,due to the axial feed associated with f va ,the dis-placement direction of the end edge is not horizontal but having an angle θrelative to f va and f vz .After calculating this angle,the actual direction of the machined surface,the variation of the rake angle and the clearance angle can be defined.The cutting force on the end edge derived from axial feed can be defined within the plane to which the machined surface belongs.3.2Side cutting edgeBased on the kinematics of the helical milling process,two new features that may influence the cutting force and dynamics of the helical milling process have been considered.One was the periodic force variation created by the circular or tangential feed of the tool,and the other is the additional force component generated by the axial feed of the tools.The axial feed force mostly occurs at the end cutting edge of the milling tools.The interaction conditions between the tool and the workpiece are the combination of side edge cutting forces and end edge cutting forces.F !¼F !i þF!Ãð8ÞWhere,F !i is the side cutting edge component and F !Ãis end cutting edge component.Considering a point P on the (jth)Fig.4Horizontal feed influence to forces on end cuttingedgesFig.5Cutting forces on the side cutting edgecutting tooth,shown in Fig.5,the integration cutting force F !i(defined in the local coordinate system)along the in-cut por-tion of the flute j is similar to that presented in the referenced literature [4].F i x ;jϕj ðz ÞÀÁ¼f zt 4k b ÀK tc cos2ϕj ðz ÞþK rc 2ϕj ðz ÞÀsin2ϕj ðz ÞÀÁÂÃþ1k b K te sin ϕj ðz ÞÀK re cos ϕj ðz ÞÂÃ&'ϕj ;z z j ;1ðÞϕj ;z z j ;1ðÞð9ÞF iy ;j ϕj ðz ÞÀÁ¼Àf zt 4k b K tc 2ϕj ðz ÞÀsin2ϕj ðz ÞÀÁþK rc cos2ϕj ðz ÞÂÃþ1k b K te cos ϕj ðz ÞþK re sin ϕj ðz ÞÂÃ&'ϕj ;z z j ;1ðÞϕj ;z z j ;1ðÞð10ÞF iz ;jϕj ðz ÞÀÁ¼1k bK ac f zt cos ϕj ðz ÞþK ae ϕj ðz ÞÂÃϕj ;z z j ;1ðÞϕj ;z zj ;1ðÞð11Þwhere k b ¼2tan b D m=The detail of the integration of these forces is complicated because the contours of the side edge of the generic milling cutter are helical circles.To get the details of the forces at an arbitrary time,the integration procedure at one period (e.g.from zero to 2π)of the forces on the discrete cutter has to beFig.6Different intervals of a cutting period.a a p >Φex ÀΦst ðÞ=k b ,b a p <Φex ÀΦst ðÞ=k bFig.7Cutting forces on theend cutting edgedivided into several time intervals,as shown in Fig.6.The oblique lines represent the unfolding of the milling tool flutes in a plane.If a p >Φex ÀΦst ðÞ=k b is as shown in Fig.6a ,axial cutting depth is large.Φst and Φex is the cut-in and cut-out relative rotational angle of the cutter,respectively.0.0050.010.0150.020.0250.030.035−1,500−7500750bTime (sec)F o r c e (N )0.0050.010.0150.020.0250.030.035−1,500−75007501500Time (sec)F o r c e (N )Cutting force of Side edge No. 20.0050.010.0150.020.0250.030.035−1,500−75007501,500Time (sec)F o r c e (N )Result Cutting force of Side edges−4000−2000020004000Time (sec)F o r c e (N )Cutting force of End edge No. 1−4000−2000020004000Time (sec)F o r c e (N )Cutting force of End edge No. 20.0050.010.0150.020.0250.030.035−20000200040006000Time (sec)F o r c e (N )Result Cutting force of End edgesFig.8Simulation of the cutting forces during helical milling (milling tool diameter D m 16mm,five flutes,cutting speed v c 100m/min,axial feed rate per tooth f za 0.2mm,tangential feed rate per tooth f zt 0.5mm,radial cutting depth a e 8mm,up milling)In intervals 1and 5,there are no interactions between the cutter and workpiece,and therefore,the cuttingforce 0 ϕj <Φst ;F !j ¼0;Φq ϕj <2p ;F !j ¼0During interval 2,the cutting tooth begins to cut into the workpiece,where Φst ϕj <Φex ;ϕj z 1ðÞ¼ϕj ;ϕj z 2ðÞ¼ΦstDuring interval 3,the cutting tooth is fully involved in cutting the workpiece until the maximum axial cutting depth a p ,where Φex ϕj <Φp ;ϕj z 1ðÞ¼Φex ;ϕj z 2ðÞ¼Φst is obtained.During interval 4,the cutting tooth completes the cutting and quits the interaction finally,where Φp ϕj <Φq ;ϕj z 1ðÞ¼Φex ;ϕj z 2ðÞ¼ϕj ÀΦp ÀΦst ðÞIf a p <Φex ÀΦst ðÞ=k b as shown in Fig.6b ,axial cutting depth is large.In interval 1and 5,there is no interaction between the cutter and workpiece,and therefore no cutting force.0 ϕj <Φst ;F !j ¼0;Φq ϕj <2p ;F !j ¼0During interval 2,the cutting tooth begins to cut into the workpiece and progress towards the maximum axial cutting depth a p ,where Φst ϕj <Φp ;ϕj z 1ðÞ¼ϕj ;ϕj z 2ðÞ¼ΦstDuring interval 3,the cutting tooth interacts with the workpiece with a p ,where Φp ϕj <Φex ;ϕj z 1ðÞ¼ϕj ;ϕj z 2ðÞ¼ϕj ÀΦp ÀΦst ðÞDuring interval 4,the cutting tooth completes the cutting operation and quits the interaction finally,where Φex ϕj <Φq ;ϕj z 1ðÞ¼Φex ;ϕj z 2ðÞ¼ϕj ÀΦp ÀΦst ðÞ3.3End cutting edgeSince both the tangential feed f vt and axial feed f va are present during helical milling,the end cutting edge force component and the edge of these teeth are assumed to be a straight line and coincide with the radial line during analysis.If the friction force is neglected along the endcutting edge,the radial force F Ãa ¼0.As shown in Fig.7,the end cutting edge force component can be represented asd F Ãv¼K Ãvc f za cos θd r þK Ãve d r ð12Þd F Ãn ¼K Ãnc f za cos θd r þK Ãne d rð13Þd F Ãt ¼d F Ãv cos θÀd F Ãn sin θð14Þd F Ãa¼d F Ãv sin θþd F Ãn cos θð15Þd T ür d F Ãt ð16Þ00.0050.010.0150.020.0250.030.035−5000Time (sec)F o r c e (N )00.0050.010.0150.020.0250.030.035−50005000Time (sec)F o r c e (N )Cutting force of cutting edge No. 20.0050.010.0150.020.0250.030.035−20000200040006000Time (sec)F o r c e (N )Result Cutting force of milling toolFig.8(continued)Denote A ¼N m f za 2p ,B ¼N m f zt cos ϕj 2p ,θ¼argtan v av t¼argtan A r þB ,Θ½ ¼R D m 2D m 2Àa eÃd r cos θÀsin θ0sin θcos θ0000r cos θÀr sin θ026643775;K ý ¼K Ãvc K Ãve K ÃncK Ãne K ÃrcK Ãre2435,therefore,F Ãt ;j F Ãa ;jF Ãr ;j T Ãj8>><>>:9>>=>>;¼Θ½ K ý f za 1&'ð17ÞTransform to the local coordinate,F Ãx ;j F Ãy ;j F Ãz ;j T Ãj 8>><>>:9>>=>>;¼ÀF Ãt ;j cos ϕj ðt ÞÀÁF Ãt ;j sin ϕj ðt ÞÀÁF Ãa ;j T Ãj8>><>>:9>>=>>;ð18ÞSum up side cutting edge forces and end cutting forces onthe j th tooth and convert to global coordinates.F x ;j F Y ;j F Z ;j T Z ;j 8>><>>:9>>=>>;¼cos Ωh t sin Ωh t00Àsin Ωh tcos Ωh t 0000100126643775F i x ;j þF Ãx ;j F i y ;j þF Ãy ;j F i z ;j þF Ãz ;j T Ãj8>><>>:9>>=>>;ð19ÞThen,sum up all the cutting forces on the cutting teeth toobtain the cutting force model.246810−400400Time (sec)F o r c e (N )Experimental Cutting Force of X directionab246810−400400Time (sec)F o r c e (N )Experimental Cutting Force of Y direction0200400Time (sec)F o r c e (N )Experimental Cutting Force of Z direction−4000400Time (sec)F o r c e (N )Simulate Cutting Force of X direction246810−4000400Time (sec)F o r c e (N )Simulate Cutting Force of Y direction0200400Time (sec)F o r c e (N )Simulate Cutting Force of Z directionFig.9Cutting force result from experiment and simulation during helical milling cutting (milling tool M.A.Ford 20-mm five-flute end mill 17878703A,cutting speed v c 100m/min,axial feed rate per toothf za 0.005mm,tangential feed rate per tooth f zt 0.1mm,radial cutting depth a e 1mm,down milling)12345678x 10−3−300−200−100100200300400Time (sec)F o r c e (N )Experimental cutting force of single tooth periodcd12345678x 10−3−300−200−100100200300400Time (sec)F o r c e (N )Simulation cutting force of single tooth periodFig.9(continued)F X F Y F Z T Z8>><>>:9>>=>>;¼X N m j ¼1F X ;j Ωt þj À1ðÞ2pN ÀÁF Y ;j Ωt þj À1ðÞ2p N ÀÁF Z ;j Ωt þj À1ðÞ2pN ÀÁT Z ;j Ωt þj À1ðÞ2p NÀÁ8>><>>:9>>=>>;ð20ÞThe cutting force model during helical milling operationsin the time domain has therefore been established analyti-cally.This model defines both the cutting force on the side cutting edge and on the end cutting edge,incorporating the interactions between the cutter and the workpiece on the effect of the spindle rotation and the helical feed.4Simulations and experimental resultsCutting forces during helical milling have been simulated on the MATLAB platform using the models presented previ-ously,and experiments have been performed to compare with the model predictions.The process parameters includ-ed the workpiece material,cutting conditions,tool material and geometry.The Ti6Al4V alloy was cast and then HIPed (hot isostatic pressing,HIP)at a pressure of 100–140MPa at 920°C for 2.5h;then,the casting was rough milled to the end geometry (160×160×20mm)with a hole in a diameter of 60mm in the centre of the plate as shown in Fig.1.There were two types of cutting tools,the M.A.Ford 20-mm five-flute carbide end mill (17878703A)and the M.A.Ford 16-mm five-flute carbide end mill (17862903A).Experiments were carried out on a five-axis high-speed Mikron UCP-710CNC machining centre.A three-axis piezo-electric Kistler 9265B type dynamometer was set up on the fixture with the workpiece.The accessory data ac-quisition system of the dynamometer consisted of a Kistler 5019A type multi-channel charge amplifier and signal pro-cessing software DynoWare.Before commencing the experiments,the dynamometer was calibrated using static loads.The simulated cutting forces in an entire milling tool revolution on the side edges,end edges and whole cutter during the typical cutting conditions are depicted in Fig.8.In this simulation,the up milling and large radial cutting depth are considered as the significant characteristics of the operation.Figure 8a shows the simulated cutting forces that acted on first side cutting edge,second side cutting edge and cutting forces that acted on the milling tool from both the five cutting edges,respectively.For the up milling condi-tion,the j th edge engages with the workpiece,and the (j -1)th edge engages following.The large radial cutting depth means that before the previous cutting edge has completed cutting,the next cutting edge has engaged the workpiece.Therefore,there is a period of time that forces overlap between the consecutive cutting edges.Figure 8b shows thesimulated cutting forces that acted on the end cutting edges.There are similar cutting forces superposing between consec-utive side cutting edges.However,the sum of the X ,Y direc-tion forces are nearly zero,that is one of the important features of helical milling and plunge milling operations.Figure 8c shows the cutting forces that acted on the milling tool.These results are the integration of the component forces from Fig.8a and b .The simulated and experimental cutting force results are compared in Fig.9.In this case,cutting tools travel along an entire helical curve and machine an entire helical milling period.The X ,Y ,Z coordinates are fixed to the workpiece,during the helical feed motion of the tool,the amplitude of F X and F Y change with time following a sine relationship.The amplitude of Fig.9a and b counter profile is the maximum result of F X and F Y .Figure 9c and d shows the experimental and simulated cutting forces in detail in a single tooth period.The comparison result from experiment and simulation are shown in Table 1.This figure depicts the simulation results to an accuracy of about 10%in these selected indicators.The maximum value of F X ,F Y and F Z indicates for a single tooth period for both simulation and experimental results shown.The maximum of ffiffiffiffiffiffiffiffiffiffiffiffiffiffiffiffiffiF 2X þF 2Yp indicates the amplitude of force of F X and F Y during helical milling.The errors probably result from cutting tool deflection and cutting tool wear.5ConclusionIn this paper,cutting forces during helical milling operations have been modelled in the time domain.The cutting forces both on the side cutting edges and on the end cutting edges along the helical feed path have been modelled by considering the tangential and the axial motion of the tool.The cutting force model can be used to predict cutting forces both on the side cutting edges and the end cutting edges.The model can also predict forces on the whole helix milling tool considering the process parameters and tool geometry.The experimental results show that for the given helix milling operation param-eters,the result of simulation predicts the cutting forces effec-tively and accurately.Table 1Comparison of experiment and simulation resultsExperiment (average)SimulationErrorHelical feed period (s)9.509.4750.263%Maximum of F X (N)371.1341.2−8.06%Maximum of F Y (N)253.2283.211.8%Maximum of F Z (N)287.7269.4−6.36%Maximum of ffiffiffiffiffiffiffiffiffiffiffiffiffiffiffiffiffiF 2X þF 2Yp (N)365.3397.68.84%。
Experimental investigation of air–water, two-phase flow regimes in
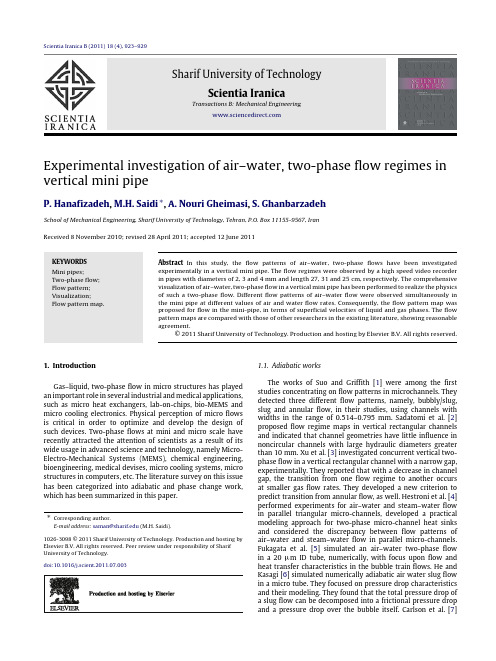
Scientia Iranica B(2011)18(4),923–929Sharif University of TechnologyScientia IranicaTransactions B:Mechanical EngineeringExperimental investigation of air–water,two-phase flow regimes in vertical mini pipeP.Hanafizadeh,M.H.Saidi∗,A.Nouri Gheimasi,S.GhanbarzadehSchool of Mechanical Engineering,Sharif University of Technology,Tehran,P.O.Box11155-9567,IranReceived8November2010;revised28April2011;accepted12June2011KEYWORDSMini pipes;Two-phase flow; Flow pattern; Visualization; Flow pattern map.Abstract In this study,the flow patterns of air–water,two-phase flows have been investigated experimentally in a vertical mini pipe.The flow regimes were observed by a high speed video recorder in pipes with diameters of2,3and4mm and length27,31and25cm,respectively.The comprehensive visualization of air–water,two-phase flow in a vertical mini pipe has been performed to realize the physics of such a two-phase flow.Different flow patterns of air–water flow were observed simultaneously in the mini pipe at different values of air and water flow rates.Consequently,the flow pattern map was proposed for flow in the mini-pipe,in terms of superficial velocities of liquid and gas phases.The flow pattern maps are compared with those of other researchers in the existing literature,showing reasonable agreement.©2011Sharif University of Technology.Production and hosting by Elsevier B.V.All rights reserved.1.IntroductionGas–liquid,two-phase flow in micro structures has played an important role in several industrial and medical applications, such as micro heat exchangers,lab-on-chips,bio-MEMS and micro cooling electronics.Physical perception of micro flows is critical in order to optimize and develop the design of such devices.Two-phase flows at mini and micro scale have recently attracted the attention of scientists as a result of its wide usage in advanced science and technology,namely Micro-Electro-Mechanical Systems(MEMS),chemical engineering, bioengineering,medical devises,micro cooling systems,micro structures in computers,etc.The literature survey on this issue has been categorized into adiabatic and phase change work, which has been summarized in this paper.∗Corresponding author.E-mail address:saman@(M.H.Saidi).1.1.Adiabatic worksThe works of Suo and Griffith[1]were among the first studies concentrating on flow patterns in microchannels.They detected three different flow patterns,namely,bubbly/slug, slug and annular flow,in their studies,using channels with widths in the range of0.514–0.795mm.Sadatomi et al.[2] proposed flow regime maps in vertical rectangular channels and indicated that channel geometries have little influence in noncircular channels with large hydraulic diameters greater than10mm.Xu et al.[3]investigated concurrent vertical two-phase flow in a vertical rectangular channel with a narrow gap, experimentally.They reported that with a decrease in channel gap,the transition from one flow regime to another occurs at smaller gas flow rates.They developed a new criterion to predict transition from annular flow,as well.Hestroni et al.[4] performed experiments for air–water and steam–water flow in parallel triangular micro-channels,developed a practical modeling approach for two-phase micro-channel heat sinks and considered the discrepancy between flow patterns of air–water and steam–water flow in parallel micro-channels. Fukagata et al.[5]simulated an air–water two-phase flow in a20µm ID tube,numerically,with focus upon flow and heat transfer characteristics in the bubble train flows.He and Kasagi[6]simulated numerically adiabatic air water slug flow in a micro tube.They focused on pressure drop characteristics and their modeling.They found that the total pressure drop of a slug flow can be decomposed into a frictional pressure drop and a pressure drop over the bubble itself.Carlson et al.[7]1026-3098©2011Sharif University of Technology.Production and hosting by Elsevier B.V.All rights reserved.Peer review under responsibility of Sharif University of Technology.doi:10.1016/j.scient.2011.07.003924P.Hanafizadeh et al./Scientia Iranica,Transactions B:Mechanical Engineering18(2011)923–929investigated characteristics of multiphase dynamics,especially two-phase gas–liquid flow,by means of advanced numerical simulations.They compared two Computational Multi-Fluid Dynamic(CMFD)codes,Fluent and TransAT,and reported a prediction of recirculating flow in the bubbly flow case using TransAT,while significant recirculation was not observed in the solution using Fluent.Saison and Wongwises[8]performed a series of experiments in a horizontal circular micro channel with an inner diameter of0.15mm.They presented a flow pattern map in terms of the phase superficial velocities, and proposed a new pressure drop correlation for practical application.1.2.Phase change worksThe pool boiling heat transfer,in a vertical narrow annular with closed bottoms,was observed through a transparent quartz shroud by Yao and Chang[9],and stages of evolving boiling phenomena with an increase in heat flux were reported. Several researchers observed three basic flow patterns,namely, bubbly,slug and annular flow,in the mini pipe and channel. Damianides and Westwater[10]performed experiments with a1mm tube,and Mertz et al.[11]and Kasza et al.[12] studied the flow visualization of water nucleation in a single rectangular channel of2.5mm by6mm.Lin et al.[13]used a single round tube with2.1mm inside diameter for their experiments,and compared the flow transitions with those predicted by Bernea et al.[14].Sheng and Palm[15]performed their experiments with1–4mm diameter tubes.Cornwell and Kew[16]found three different flow patterns for R-113, namely,isolated bubbles confined bubbles and slug/annular flow,in rectangular channels with cross sectional areas of 1.2–0.9mm and3.5–1.1mm.Ory et al.[17]considered the effects of capillary,inertia,friction and gravity forces on the velocity distribution and temperature field along a single capillary two-phase flow in a heated micro-channel.Research dealing with gas–liquid,two-phase flow in micro-channels,in situations where fluid inertia was significant in comparison with surface tension,was reviewed by Ghiaasiaan and Abdel-Khalik[18].Jiang et al.[19]studied the boiling of water in triangular micro-channels,having widths of50and100µm. They observed individual bubbles at low heat fluxes,and an abrupt change in flow pattern to an unstable slug flow with increasing heat flux.Chedester and Ghiaasiaan[20]addressed the hydro-dynamically controlled Onset of a Significant Void (OSV)in heated micro tubes.They derived a simple semi-empirical correlation for the radius of departing bubbles at the OSV point to show the accuracy of their hypothesis.Some experimental studies have been reported on gas liquid two-phase flow in mini and micro conduits by Kandlikar[21],Lee and Mudawar[22]and Serizawa et al.[23].The three zone boiling heat transfer model was developed by Thome et al.[24]. Revellin and Thome[25]used an optical measurement method for two-phase characteristics of R-134a and R-245fa,in0.5mm and0.8mm diameter channels,to determine the frequency of bubbles existing in the microevaporator.They detected four flow patterns,namely,bubbly,slug,semi-annular and annular flow,whose transitions were not well compatible with neither the macroscale map of refrigerants nor the microscale map of air–water flow.Sobierska et al.[26] experimentally investigated the water boiling phenomena in a vertical rectangular microchannel,with a hydraulic diameter of0.48mm.They observed three main flow patterns,namely, bubbly,slug and annularflow.Figure1:Schematic of test apparatus.Due to the effects of surface tension,two-phase flows at mini and micro scale have different behavior in comparison with the macro scale.The aim of the present work is to visualize flow regimes in air–water two-phase flows and propose a flow regime map for such flows in vertical mini pipes.The neural network technique is implemented to recognize and predict a gas–liquid,two-phase flow pattern in mini tubes,having diameters of2,3and4mm.2.Experimental setupThis study is carried out by experimental apparatus schematically shown in Figure1.Air and water are used as gas and liquid phases in the experiments.The water flow rates are regulated by the needle valves and are measured by the cali-brated rotameter.Air and water are mixed together in a mixer made of acrylic glass and placed at the bottom of the riser pipe. The compressed air is fed by the compressor via an air injec-tor,which is schematically depicted in Figure2.The water flows from the center hole of a mixer,with a diameter of2mm,while air is injected into the holes around the center hole,each having 1mm diameter.The air flow rates are set by the regulator valve and are continuously measured by the calibrated gas rotameter. The overall height and inside diameter of the riser pipe are sum-marized in Table1.In order to have the opportunity to visually observe the two-phase flow patterns,the riser pipe was made of transparent glass.The air water mixture was directed upward through the riser,separated in the separation tank at the top of the riser and the air was discharged into the atmosphere.Differ-ent flow regime images were captured by a digital high speed camera,with a frame rate of1200fps,from the test section of the upriser.The test section is placed after the entrance section to diminish the effect of the entrance region.The length of the entrance section is about500mm.The superficial air and water velocities are0.5–10m/s and0.05–1m/s,respectively.P.Hanafizadeh et al./Scientia Iranica,Transactions B:Mechanical Engineering 18(2011)923–929925Figure 2:Schematic of air and watermixer.Figure 3:(a)RGB picture;(b)gray picture;and (c)subtracting and median process of flow in the pipe (3mm diameter).3.Experimental results 3.1.Image processingImage processing techniques must be performed in order to extract features from the images of the two-phase flow.Each picture has 8bit RGB (red,green and blue)color format,being converted from RGB to a grey scale mode.The output image has 256grey levels from 0(black)to 255(white).It is difficult to extract the bubbles directly from an original digital image and therefore preprocessing procedures must be undertaken to reduce noise and improve the quality of the images.An image-subtracted algorithm was used to reduce background noise by subtracting the background image from each dynamic image.In order to smooth the image border,a median filter was also used.A sliding window (3×3)was used in this process,and the median gray level of the pixels in the window was ter,the gray level of the pixels located at the center of the window was replaced by the median.The result of these processes is shown in Figure 3.3.1.1.Inverting binary imageThe images were converted from grayscale to binary mode by threshold segmentation,and an iterative procedure was used to calculate the optimizing threshold as follows [27]:Figure 4:Binary image of two-phase flow in the mini pipe.(a)The minimum and maximum of the gray level,namely Z land Z k ,are found in the image,and the initial value of the threshold is derived from their arithmetic average as:T 0=(Z k +Z l )/2.(1)(b)According to the initial value of threshold T K ,the imageis divided into two parts,namely,object and background,and the average value of the gray level in each part is calculated as:Z O =−Z (i ,j )<T kZ (i ,j )N O,(2)Z B =−Z (i ,j )>T kZ (i ,j )N B,(3)where Z (i ,j )is the gray level of the pixel (i ,j )in the image,N O is the number of the pixels in which Z (i ,j )is less than T K ,and N B is the number of pixels in which Z (i ,j )is more than T K .(c)The new threshold is calculated based on the arithmeticaverage of the object and background segments of the image as:T k +1=(Z O +Z B )/2.(4)If T K =T K +1,then the algorithm is finished,else K ≪=K +1,and turn to step (b).The binary image of the bubbles in the vertical pipe,which is the result of the above procedure,is shown in Figure 4.3.1.2.Image morphology processingSome morphological functions,such as dilation,erosion,opening and closing operations,were applied to modify the shapes of bubbles.Dilation adds pixels to the boundaries of the objects in an image,while erosion removes pixels on the object boundaries.The definition of a morphological opening of an image is erosion followed by dilation,using the same structuring element for both operations.The related operation,morphological closing of an image,is the reverse.It consists of dilation followed by erosion,with the same structuring element.Both of them do not significantly alter the area or shape of objects.The opening operation removes small objects and smoothes boundaries.Borders removed by erosion are restored by dilation,but small objects that were absorbed during erosion do not reappear after dilation.The closing operation was used to fill tiny holes and smooth boundaries.Objects were expanded by dilation and then reduced by erosion,so borders were smoothed and holes were filled [28,29].After926P.Hanafizadeh et al./Scientia Iranica,Transactions B:Mechanical Engineering 18(2011)923–929Figure 5:Final image of two-phase flow in the mini pipe.these operations,the result of image processing is shown in Figure 5.Bubble images of two-phase flow were clear using the above image processing,and it prepared bubbles for quantitative analysis,such as measuring area,perimeter and diameter.3.2.Flow pattern mapIn the experimental procedure while varying gas or liquid mass flow rate,a 10s film was recorded from the flow regime at a speed of 1200fps.The recorded film was replayed in slow motion for recognition of flow regimes.Each film converted to separate frames in a picture format using Adobe Premiere software.The achieved pictures were used as inputs of image processing techniques.The final binary pictures were used for the mentioned post processing procedure,such as flow regimedetection,void fraction and bubble velocity calculation,etc.Figure 6shows those typical flow regimes observed in the vertical,co-current,air–water,two-phase flows,in the 3mm mini pipe.Four basic flow patterns,namely,bubbly,slug,churn and annular,accompanied by their transitions,are illustrated in these figures.The visualization shows that air–water two-phase flows in mini pipes do not have three dimensional behaviors,especially in bubbly and slug flows.The final processed images of different flow regimes in air–water,two-phase flow in mini pipes have been presented in Figure 7.Figures 8–10show the flow pattern map for a vertical round tube with inner diameters of 2,3and 4mm,respectively.The proposed maps are in terms of superficial velocities of phases,and the four main flow patterns are depicted in these maps.In Figure 11,the achieved flow pattern for the pipe with 2mm ID was compared to the work of Ide et al.[30],shown by a solid line.They divided the flow pattern map into the four main regions,namely,dispersed bubbly flow,intermittent flow,churn flow and annular flow.The comparison shows that the bubbly and annular flows in the present work are not well in accordance with those of Ide et al.In the present work,the dispersed bubbles were not seen,because the air bubble injector did not have very thin holes.As a result,the created bubbles mostly have diameters in the range of the pipe diameter.Even the existence of air injectors with thin holes cannot guarantee the creation of bubbly flow.In the case of small bubbles occurring,as a result of thin holes in the air injector and the developed two-phase flow,they would collapse,resulting in large bubbles know as intermittent flow.Bubbly flows are mainly promoted by bubble breaking mechanisms,due to turbulence effects.It seems that in small diameter pipes,the formation of a specific flowpatterns(a)Bubbly.(b)Bubbly-slug.(c)Slug.(d)Messy-slug.(e)Churn.(f)Wispy-annular.(g)Ring.(h)Wavy-annular.(i)Annular.Figure 6:Different flow patterns in a vertical pipe with 2mm diameter.P.Hanafizadeh et al./Scientia Iranica,Transactions B:Mechanical Engineering18(2011)923–929927(a)Bubbly.(b)Slug.(c)Messy-slug.(d)Churn.(e)Ring.(f)Wavy-annular.Figure7:Final processed image of different two-phase flow regimes in the minipipe.Figure8:Flow patterns for2mm innerdiameter.Figure9:Flow patterns for3mm inner diameter.mainly depends on mixer configuration.The radial air supplierused in this study makes intermittent flow patterns,such asslug and churn flows,while the air supply in the tube centerfavors annular flow.This can be the reason for an absence ofannular flow in the proposed flow patterns.The comparison offlow patterns also reveals that the slug,messy slug andsemi-Figure10:Flow patterns for4mm inner diameter.annular flows in the proposed map are in accordance with theintermittent flow of Ide et al.[30].In the present study,a noticeable difference between flowpattern maps for vertical pipes with various diameters of2,3and4mm is not seen.This can be justified in regard tothe fact that the dominant forces acting on the air–watermixture in the small diameter pipes,namely,gravitation,inertia,surface tension and buoyancy forces,are in the sameorder of magnitude.This concept clearly indicates that thesethree flow patterns can be combined to form a new flow patternfor the gas–liquid,two-phase flow in small diameter pipes.A combination of these three flow patterns results in a newflow pattern map,which is illustrated in Figure12.A FuzzyC-Means clustering technique(FCM)was used to classify theflow patterns.The solid lines in the figure show the transitionregion of the flow patterns.This figure shows the achieved flowmap for mini pipes with diameters in the range of2–4mm.4.ConclusionIn this paper,air–water,two-phase flow patterns wereinvestigated experimentally for mini pipes with diameters of2,3and4mm.An image processing technique was used fordetection of flow patterns from pictures derived from filmsrecorded with a high speed camcorder.The obtained flowpatterns reveal that there is no noticeable difference between928P.Hanafizadeh et al./Scientia Iranica,Transactions B:Mechanical Engineering 18(2011)923–929Figure 11:Comparison between the achieved flow patterns with the work of Ide et al.[30]for a pipe with diameter of 2mm.Figure 12:Proposed two-phase vertical upward flow pattern map.two-phase,upward flow patterns in this range of diameters.A new flow pattern map was achieved for vertical mini pipes,due to a comparison of the flow patterns of these three diameters of pipe.The proposed map was compared with existing research.A comparison of the present work and previous research shows that the flow patterns of slug,messy slug and semi-annular in the present work are compatible with the intermittent flow pattern of Ide et al.[30].However,in the present study,the annular flow is seen at a lower superficial air velocity than that in the work of Ide et al.[30].AcknowledgmentsThis research was funded by Iran Supplying Petrochemical Industries,Parts,Equipment and Chemical Design Corporation (SPEC),as a joint research project with Sharif University of Technology (project No.KPR-8628077).References[1]Suo,M.and Griffith,P.‘‘Two-phase flow in capillary tubes’’,Int.J.Basic Eng.,86,pp.576–582(1964).[2]Sadatomi,Y.,Sato,Y.and Saruwatari,S.‘‘Two-phase flow in verticalnoncircular channels’’,Int.J.Multiphase Flow ,8,pp.641–655(1982).[3]Xu,J.L.,Cheng,P.and Zhao,T.S.‘‘Gas–liquid two-phase flow regimes inrectangular channels with mini/micro gaps’’,Int.J.Multiphase Flow ,25,pp.411–432(1999).[4]Hetsroni,G.,Mosyak, A.,Segal,Z.and Pogrebnyak, E.‘‘Two-phaseflow patterns in parallel micro-channels’’,Int.J.Multiphase Flow ,29,pp.341–360(2003).[5]Fugakata,K.,Kasagi,N.,Ua-arayaporn,P.and Himeno,T.‘‘Numericalsimulation of gas liquid two-phase flow and convective heat transfer in a micro tube’’,Int.J.Heat and Fluid Flow ,28,pp.72–82(2007).[6]He,Q.and Kasagi,N.‘‘Numerical investigation on flow pattern andpressure drop characteristics of slug flow in a micro tube’’,6th Int.ASME Conf.on Nanochannels,Microchannels and Minichannels ,Darmstadt,Germany,pp.24–35(2008).[7]Carlson,A.,Kudinov,P.and Narayanan,C.‘‘Prediction of two-phase flowin small tubes:a systematic comparison of state-of-the-art CMFD codes’’,5th Europe Thermal-Sci.Conf.,The Netherlands,pp.138–150(2008).[8]Saisorn,S.and Wongwises,S.‘‘An experimental investigation of two-phaseair–water flow through a horizontal circular micro-channel’’,Exp.Thermal Fluid Sci.,33,pp.306–315(2009).[9]Yao,S.C.and Chang,Y.‘‘Pool boiling heat transfer in a confined space’’,Int.J.Heat Mass Transf.,26,pp.841–848(1983).[10]Damianides,D.A.and Westwater,J.W.‘‘Two-phase flow patterns in acompact heat exchanger and in small tubes’’,2nd UK National Conf.on Heat Transf.,11,United Kingdom,London,pp.1257–1268(1988).[11]Mertz,R.,Wein,A.and Groll,C.‘‘Experimental investigation of flow boilingheat transfer in narrow channels’’,Calore e Technologia ,14(2),pp.47–54(1996).[12]Kasza,K.E.,Didascalou,T.and Wambsganss,M.W.‘‘Microscale flow visu-alization of nucleate boiling in small channels:mechanisms influencing heat transfer’’,Int.Conf.on Compact Heat Exchanges for the Process Indus-tries ,New York,USA,pp.343–352(1997).[13]Lin,S.,Kew,P.A.and Cornwell,K.‘‘Two-phase flow regimes and heattransfer in small tubes and channels’’,11th Int.Heat Transf.Conf.,Kyongju,Korea,2,pp.45–50(1998).[14]Barnea,D.,Luninsky,Y.and Taitel,Y.‘‘Flow pattern in horizontal andvertical two-phase flow in small diameter pipes’’,Canadian J.Chem.Eng.,61,pp.617–620(1983).[15]Sheng, C.H.and Palm, B.‘‘The visualization of boiling in small-diameter tubes’’,Int.Conf.on Heat Transport and Transport Phenomena in Microsystems ,Banff,Canada,pp.44–53(2001).[16]Cornwell,K.and Kew,P.A.‘‘Boiling in small parallel channels’’,CEC Conf.on Energy Eff.in Process Tech.,Athens,Greece,pp.624–638(1992).[17]Ory, E.,Yuan,H.,Prosperetti, A.,Popinet,S.and Zaleski,S.‘‘Growthand collapse of a vapor bubble in a narrow tube’’,Phys.Fluids ,12,pp.1268–1277(2000).[18]Ghiaasiaan,S.M.and Abdel-Khalik,S.I.‘‘Two-phase flow in micro-channels’’,Adv.Heat Transf.,34,pp.145–253(2001).[19]Jiang,L.,Wong,M.and Zohar,Y.‘‘Forced convection boiling in a micro-channel heat sink’’,Int.J.Micro-Electro-Mech.Sys.,10,pp.80–87(2000).[20]Chedester,R.C.and Ghiaasiaan,S.M.‘‘A proposed mechanism for hydrodynamically-controlled onset of significant void in microtubes’’,Int.J.Heat Fluid Flow ,23,pp.769–775(2002).[21]Kandlikar,S.G.‘‘Fundamental issues related to flow boiling in minichan-nels and microchannels’’,Exp.Therm.Fluid Sci.,26,pp.389–407(2002).[22]Lee,J.and Mudawar,I.‘‘Two phase flow in high heat flux micro channelheat sink for refrigeration cooling applications’’,Int.J.Heat Mass Transf.,48,pp.928–955(2005).[23]Serizawa,A.‘‘Gas liquid two-phase flow in microchannels’’,In MultiphaseFlow Handbook ,C.T.Crowe,Ed.,2nd ed.,pp.830–887,CRC Press (2006).[24]Thome,J.R.,Dupont,V.and Jacobi, A.M.‘‘Heat transfer model forevaporation in micro channels’’,Int.J.Heat Mass Transf.,47,pp.3375–3385(2004).P.Hanafizadeh et al./Scientia Iranica,Transactions B:Mechanical Engineering18(2011)923–929929[25]Revellin,R.and Thome,J.R.‘‘Experimental investigation of R-134a andR-245fa two-phase flow in microchannels for different flow conditions’’, Int.J.Heat Fluid Flow,28,pp.63–71(2007).[26]Sobierska, E.,Kulenovic,R.and Mertz,R.‘‘Heat transfer mechanismand flow pattern during flow boiling of water in a vertical narrow channel experimental results’’,Int.J.Thermal Sci.,46,pp.1172–1181 (2007).[27]Shi,L.‘‘Fuzzy recognition for gas–liquid two-phase flow pattern based onimage processing’’,Proc.of13rd IEEE Int.Conf.on Control and Automation, pp.1424–1427(2007).[28]Heijmans,H.J.A.M.,Morphological Image Operators,Academic Press,NewYork(1994).[29]/help/toolbox/images/index.html.[30]Ide,H.,Kariyasaki,A.and Fukano,T.‘‘Fundamental data on the gas–liquidtwo-phase flow in minichannels’’,Int.J.Thermal Sci.,46,pp.519–530 (2007).Pedram Hanafizadeh received his M.S.and Ph.D.Degrees in Mechanical Engineering from the Centre of Excellence in Energy Conversion at Sharif University of Technology,Tehran,Iran,in2005and2010,respectively.His work is mainly concentrated on the field of Multiphase Flow,Experimentally, Numerically and Analytically.His research interests include Characteristics of Multiphase Flow,Heat Transfer,Boiling and Condensation,Instrumentation in Fluid Flow,Image Processing for Flow Field Analysis,and Industrial and Applicable Usage of Multiphase Flow.Mohammad Hassan Saidi is Professor and Chairman of the School of Mechanical Engineering at Sharif University of Technology,Tehran,Iran. His current research interests include Multiphase Flows,Heat Transfer Enhancement in Boiling and Condensation,Modelling of Pulse Refrigeration, Vortex Tube Refrigerator,Indoor Air Quality and Clean Room Technology, Energy Efficiency in Home Appliances and Desiccant Cooling Systems.Arash Nouri Gheimasi obtained his B.S.Degree in Mechanical Engineering in2010,and is currently an M.S.student at the Centre of Excellence in Energy Conversion at the School of Mechanical Engineering,Sharif University of Technology,Tehran,Iran,under the supervision of Professor Saidi.His B.S. thesis involved work on the Characteristics of Gas-Liquid Two-Phase Flow in Mini Pipes and he is now working on Application of Visual Techniques in Two-Phase Flow.His research interests include the area of Two Phase Flow and Its Industrial Applications.Soheil Ghanbarzade received his B.S.and M.S.Degrees in Mechanical Engineering from the Centre of Excellence in Energy Conversion at Sharif University of Technology in2008and2010,respectively.Since then he has worked under the supervision of Professor M.H.Saidi as research staff in the Multiphase Group.His research interests include:Analytical,Numerical and Experimental Methods to Study Characteristics of Large Scale and Mini Scale Air-Water,Two-Phase Flows.He holds a Gold medal from the13th National Olympiad of Mechanical Engineering in Iran,and is currently a Ph.D.student of Petroleum Engineering at the University of Texas,Austin,USA.。
物理实验报告 英文
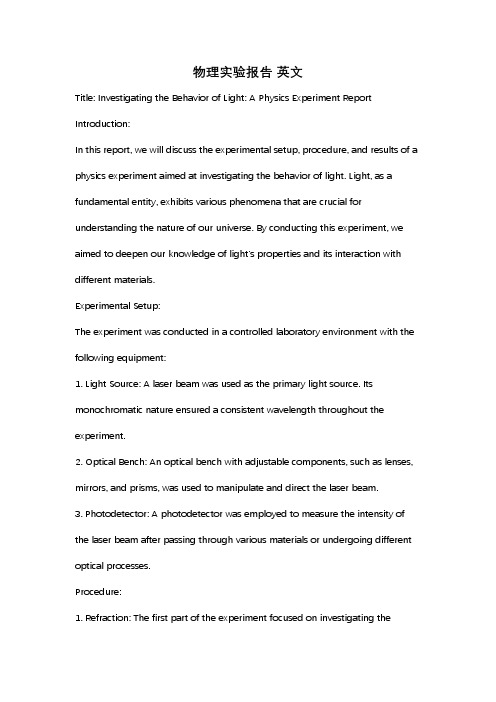
物理实验报告英文Title: Investigating the Behavior of Light: A Physics Experiment Report Introduction:In this report, we will discuss the experimental setup, procedure, and results of a physics experiment aimed at investigating the behavior of light. Light, as a fundamental entity, exhibits various phenomena that are crucial for understanding the nature of our universe. By conducting this experiment, we aimed to deepen our knowledge of light's properties and its interaction with different materials.Experimental Setup:The experiment was conducted in a controlled laboratory environment with the following equipment:1. Light Source: A laser beam was used as the primary light source. Its monochromatic nature ensured a consistent wavelength throughout the experiment.2. Optical Bench: An optical bench with adjustable components, such as lenses, mirrors, and prisms, was used to manipulate and direct the laser beam.3. Photodetector: A photodetector was employed to measure the intensity of the laser beam after passing through various materials or undergoing different optical processes.Procedure:1. Refraction: The first part of the experiment focused on investigating thephenomenon of refraction. A glass prism was placed on the optical bench, and the laser beam was directed towards it. By varying the angle of incidence, we observed the corresponding change in the angle of refraction. The intensity of the laser beam was measured using the photodetector at different angles.2. Diffraction: In the second part, we explored the phenomenon of diffraction. A diffraction grating was placed in the path of the laser beam. By rotating the grating, we observed the diffraction pattern formed on a screen placed at a specific distance from the grating. The intensity of the diffracted light was measured using the photodetector.3. Interference: The final part of the experiment focused on the interference of light waves. Two narrow slits were placed in the path of the laser beam, creating two coherent sources of light. A screen was placed at a specific distance from the slits, and the interference pattern was observed. The intensity of the interference pattern was measured using the photodetector.Results and Discussion:1. Refraction: As the angle of incidence increased, the angle of refraction also increased. This confirmed the relationship between the two angles predicted by Snell's law. The intensity of the laser beam decreased as the angle of refraction increased, indicating the loss of energy during the refraction process.2. Diffraction: By rotating the diffraction grating, we observed a series of bright and dark fringes on the screen. The distance between the fringes decreased as the grating rotation angle increased, indicating a smaller wavelength ofdiffracted light. The intensity of the laser beam varied at different angles, demonstrating the constructive and destructive interference of light waves.3. Interference: The interference pattern displayed alternating bright and dark fringes. The intensity of the bright fringes was higher, indicating constructive interference, while the dark fringes represented destructive interference. The distance between the fringes increased as the distance from the slits to the screen increased, confirming the relationship between fringe separation and wavelength.Conclusion:Through this experiment, we gained valuable insights into the behavior of light. We observed and analyzed the phenomena of refraction, diffraction, and interference, which are fundamental to the understanding of optics. The results obtained aligned with the theoretical predictions, reinforcing our understanding of light's properties and its interaction with various materials. Conducting experiments such as these allows us to bridge the gap between theoretical knowledge and practical applications, ultimately leading to advancements in the field of physics.。
机械专业毕业论文外文翻译--实验研究激光加工表面微观造型平行的推力轴承
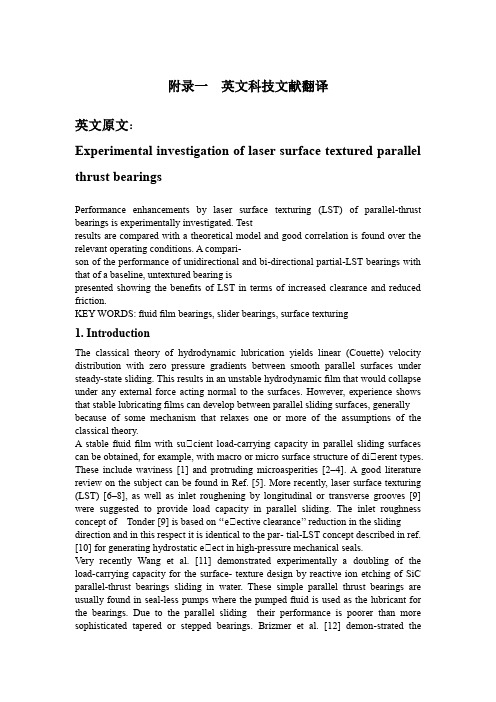
附录一英文科技文献翻译英文原文:Experimental investigation of laser surface textured parallel thrustbearingsPerformance enhancements by laser surface texturing (LST) of parallel-thrust bearings is experimentally investigated. Testresults are compared with a theoretical model and good correlation is found over the relevant operating conditions. A compari-son of the performance of unidirectional and bi-directional partial-LST bearings with that of a baseline, untextured bearing ispresented showing the benefits of LST in terms of increased clearance and reduced friction.KEY WORDS: fluid film bearings, slider bearings, surface texturing1. IntroductionThe classical theory of hydrodynamic lubricationyields linear (Couette) velocity distribution with zeropressure gradients between smooth parallel surfacesunder steady-state sliding. This results in an unstablehydrodynamic film that would collapse under anyexternal force acting normal to the surfaces. However,experience shows that stable lubricating films candevelop between parallel sliding surfaces, generally because of some mechanism that relaxes one or moreof the assumptions of the classical theory.A stable fluid film with sufficient load-carryingcapacity in parallel sliding surfacescan be obtained,for example, with macro or micro surface structure ofdifferent types. These include waviness [1] and protruding microasperities [2–4]. A good literature review onthe subject can be found in Ref. [5]. More recently,laser surface texturing (LST) [6–8], as well as inletroughening by longitudinal or transverse grooves [9]were suggested to provide load capacity in parallelsliding. The inlet roughness concept of Tonder [9] isbased on ……effective clearance‟‟ reduction in the s lidingdirection and in this respect it is identical to the par-tial-LST concept described in ref.[10] for generatinghydrostatic effect in high-pressure mechanical seals.Very recently Wang et al. [11] demonstrated experimentally a doubling of the load-carrying capacity forthe surface- texture design by reactive ion etching ofSiC parallel-thrust bearings sliding in water. Thesesimple parallel thrust bearings are usually found inseal-less pumps where the pumped fluid is used as thelubricant for the bearings. Due to the parallel slidingtheir performance is poorer than more sophisticatedtapered or stepped bearings. Brizmer et al. [12] demon-stratedthepotential of laser surface texturing in theform of regular micro-dimples for providing load-carrying capacity with parallel-thrust bearings. A model of a textured parallel slider was developed and the effect of surface texturing on load-carrying capacitywas analyzed. The optimum parameters of the dimples were found in order to obtain maximum load-carrying capacity. A micro-dimple ……collective effect‟‟ was identi-fied that is capable of generating substantial load-carrying capacity, approaching that of optimumconventional thrust bearings. The purpose of the present paper is to investigate experimentally the validity of the model described in Ref. [12] by testing practical thrust bearings and comparing the performance of LST bearings with that of the theoretical predictions and with the performance of standard non-textured bearings2. BackgroundA cross section of the basic model that was analyzedin Ref. [12] is shown in figure1. A slider having awidth B is partially textured over a portion Bp =αB ofits width.The textured surface consists of multipledimples with a diameter,depth and area densitySp. As a result of the hydrodynamic pressure generatedby the dimples thesliding surfaces will be separated bya clearance depending on the sliding velocity U, thefluid viscosity l and the external load It was foundin Ref. [12] that an optimum ratio exists for the parameter that provides maximum dimensionlessload-carrying capacity where L isthe bearing length, and this optimum value is hp=1.25. It was further found in Ref. [12] that an optimumvalue exists for the textured portion a depending onthe bearing aspect ratio L/B. This behavior is shown infigure 2 for a bearing with L/B = 0.75 at various values of the area density Sp. As can be seen in the rangeof Sp values from0.18 to 0.72 the optimum a valuevaries from 0.7 to 0.55, respectively. It can also be seenfrom figure 2 that for a < 0.85 no optimum valueexists for Sp and the maximum load W increases withincreasing Sp. Hence, the largest area density that canbe practically obtained with the laser texturing isdesired. It is also interesting to note from figure 2 theadvantage of part ial-LST (a < 1) over the full LST(a = 1) forbearing applications. At Sp= 0.5, forexample, the load W at a = 0.6 is about three timeshigher than its value at a = 1. A full account of thisbehavior is given in Ref. [12].3. ExperimentalThe tested bearings consist of sintered SiC disks10 mm thick, having 85 mm outer diameter and40 mm inner diameter. Each bearing (see figure 3)comprises a flat rotor (a) and a six-pad stator (b). Thebearings were provided with an original surface finish by lapping to a roughness average Ra= 0.03 lm. Eachpad has an aspect ratio of 0.75 when its width is measured along the mean diameter of the stator. The photographs of two partial-LST stators are shown infigure 4 where the textured areas appear as brightermatt surfaces. The first stato r indicated (a) is a unidirectional bearing with the partial-LST adjacent to theleading edge of each pad, similar to the model showninfigure 1. The second stator (b) is a bi-directionalversion of a partial-LST bearing having two equal textured portions, a/2, on each of the pad ends. The lasertexturing parameters were the following; dimple depth, dimplediameter and dimple area density Sp= 0.60.03. These dimpledimensions were obtained with 4 pulses of 30 ns duration and 4 mJ each using a 5 kHz pulsating Nd:YAGlaser. The textured portion of the unidirectional bearing was a= 0.73 and that of the bi-directional bearingwas a= 0.63. As can be seen from figure 2 both thesea values should produce load-carrying capacity varyclose to the maximum theoretical value.The test rig is shown schematically in figure 5. An electrical motor turns a spindle to which an upperholder of the rotor is attached. A second lower holderof the stator is fixed to a housing, which rests on ajournal bearing and an axial loading mechanism that can freely move in the axial direction. An arm thatpresses against a load cell and thereby permits frictiontorque measurements prevents the free rotation of thishousing. Axial loading is provided by means of deadweights on a lever and is measured with a second loadcell. A proximity probe that is attached to the lowerholder of the stator allows on-line measurements ofthe clearance change between rotor and stator as thehydrodynamic effects causeaxial movement of thehousing to which the stator holder is fixed. Tap wateris supplied by gravity from a large tank to the centerof the bearing and the leakage from the bearing is collected and re-circulated. A thermocouple adjacent tothe outer diameter of the bearing allows monitoring ofthe water temperature as the water exit the bearing. APC is used to collect and process data on-line. Hence,the instantaneous clearance, friction coefficient, bearing speed and exit water temperature can be monitoredconstantly.The test protocol includes identifying a reference“zero” point for the clearance measurements by firstloading and then unloading a stationary bearing overthe full load range. Then the lowest axial load isapplied, the water supply valve is opened and themotor turned on. Axial loading is increased by stepsof 40 N and each load step is maintained for 5 minfollowing the stabilization of the friction coefficient ata steady-state value. The bearing speed and water temperature are monitored throughout the test for anyirregularities. The test ends when a maximum axialload of 460 N is reached or if the friction coefficientexceeds a value of 0.35. At the end of the last loadstep the motor and water supply are turned offandthe reference for the clearance measurements isrechecked. Tests are performed at two speeds of 1500and 3000 rpm corresponding to average sliding velocities of 4.9 and 9.8 m/s, respectively and each test isrepeated at least three times.4. Results and discussionAs a first step the validity of the theoretical modelin Ref. [12] was examined by comparing the theoretical and experimental results of bearing clearance versus bearing load for a unidirectional partial-LSTbearing. The results are shown in figure 6 for the twospeeds of 1500 and 3000 rpm where the solid anddashed lines correspond to the model and experiment,respectively. As can be seen, the agreement betweenthe model and the experiment is good, with differences of less than 10%, as long as the load is above150 N. At lower loads the measured experimentalclearances are much larger than the model predictions, particularly at the higher speed of 3000 rpmwhere at 120 N the measured clearance is 20 lm,which is about 60% higher than the predicted value.It turns out that the combination of such large clearances and relatively low viscosity of the water mayresult in turbulent fluid film. Hence, the assumptionof laminar flow on which the solution of the Reynolds equation in Ref. [12] is based may be violatedmaking the model invalid especially at the higherspeed and lowest load. In order to be consistent withthe model of Ref. [12] it was decided to limit furthercomparisons to loads above 150 N.It should be noted here that the first attempts to testthe baseline untextured bearing with the original surface finish of Ra= 0.03 lm on both the stator androtor failed due to extremely high friction even at thelower loads. On the other hand the partial-LST bearingran smoothly throughout the load range. It was foundthat the post-LST lapping to completely remove about2 lm height bulges, which are formed during texturingaround the rims of the dimples, resulted in a slightlyrougher surface with Ra= 0.04 lm. Hence, the baselineuntextured stator was also lapped to the same rough- ness of the partial-LST stator and all subsequent testswere performed with the same Ra value of 0.04 lm forall the tested stators. The rotor surface roughness remained, the original one namely, 0.03 lm. Figure 7presents the experimental resultsfor the clearance as afunction of the load for a partial-LST unidirectionalbearing (see stator in figure 4(a)) and a ba selineuntextured bearing. The comparison is made at the twospeeds of 1500 and 3000 rpm. The area density of thedimples in the partial-LST bearing is Sp= 0.6 and thetextured portion is a ¼ 0:734. The load range extendsfrom 160 to 460 N. The upper load was determined bythe test-rig limitation that did not permit higher loading. It is clear from figure 7 that the partial-LST bearing operates at substantially larger clearances than theuntextured bearing. At the maximum load of 460 Nand speed of 1500 rpm the partial-LST bearing has aclearance of 6 lm while the untextured bearing clearance is only 1.7 lm. At 3000 rpm the clearances are 6.6and 2.2 lm for the LST and untextured bearings,respectively. As can be seen from figure 7 this ratio ofabout 3 in favor of the partial-LST bearing is maintained over the entire load range.Figure 8 presents the results for the bi-directionalbearing (see stator in figure 4(b)). In this case the LSTparameters are Sp ¼ 0:614 and a ¼ 0:633. The clearances of the bi-directional partial-LST bearing arelower compared to these of the unidirectional bearingat the same load. At 460 N load the clearance for the1500 rpm is 4.1 lm and for the 3000 rpm it is 6 lm.These values represent a reduction of clearance between 33 and 10% compared to the unidirectional case. However, as can be seen from figure 8 the performance ofthe partial-LST bi-directional bearing is still substantially better than that of the untextured bearing.The friction coefficient of partial-LST unidirectionaland bi-directional bearings was compared with that ofthe untextured bearing in figures 9 and 10 for the twospeeds of 1500 and 3000 rpm, respectively. As can beseen the friction coefficient of the two partial-LSTbearings is very similar with slightly lower values inthe case of the more efficient unidirectional bearing.The friction coefficient of the untextured bearing is much larger compared to that of the LST bearings. At1500 rpm (figure 9) and the highest load of 460 N thefriction coefficient of the untextured bearing is about0.025 compared to about 0.01 for the LST bearings.At the lowest load of 160 N the values are about 0.06for the untextured bearing and around 0.02 for theLST bearings. Hence, the friction values of the untextured bearing are between 2.5 and 3 times higher thanthe corresponding values for the partial-LST bearingsover the entire load range. Similar results wereobtained at the velocity of 3000 rpm (figure 10) butthe level of the friction coefficients is somewhat higherdue to the higher speed. The much higher friction ofthe untextured bearing is due to the much smallerclearances of this bearing (see figures 7 and 8) thatresult in higher viscous shear.5. ConclusionThe idea of partial-LST to enhance performance ofthe parallel thrust bearing was evaluated experimentally.Good correlation was found with a theoretical model as long as the basic assumption of laminar flow in the fluidfilm is valid. At low loads with relatively large clearances, where turbulence may occur, the experimental clearance is larger than the prediction of the model.The performance of both unidirectional and bidirectional partial-LST bearings in terms of clearanceand friction coefficient was compared with that of abaseline untextured bearing over a load range in whichthe theoretical model is valid. A dramatic increase, ofabout three times, in the clearance of the partial-LSTbearings compared to that of the untextured bearingwas obtained over the entire load range. Consequentlythe friction coefficient of the partial-LST bearings ismuch lower, representing more than 50% reduction infriction compared to the untextured bearing.The larger clearance and lower friction make thepartial-LST simple parallel thrust bearing conceptmuch more reliable and efficient especially in seal-lesspumps and similar applicatio ns where the processfluid, which is often a poor lubricant, is the only available lubricant for the bearings.AcknowledgmentsThe authors would like to thank Mr. J. Boylan ofMorgan AM&T for providing the bearing specimensand Mr. N. Barazani of Surface Technologies Ltd. Forproviding the laser surface texturing.实验研究激光加工表面微观造型平行的推力轴承实验是研究激光处理的表面微观造型平行的推力轴承增强的某些性能。
- 1、下载文档前请自行甄别文档内容的完整性,平台不提供额外的编辑、内容补充、找答案等附加服务。
- 2、"仅部分预览"的文档,不可在线预览部分如存在完整性等问题,可反馈申请退款(可完整预览的文档不适用该条件!)。
- 3、如文档侵犯您的权益,请联系客服反馈,我们会尽快为您处理(人工客服工作时间:9:00-18:30)。
I. Introduction
Tsinghua University
Literature [2] studied the subsurface damage of KDP with ultrasonic assisted drilling Literature [4] reported an experimental investigation about the influence of process
II. Comparison of Kinematics Characteristic
Tsinghua University
1. Illustration of RUFM process
RUM combines ultrasonic machining and diamond grinding process. The material removal mechanism includes hammering, abrasion, and extraction.
C. Studying the influences of process variables on surface roughness
D. Comparison the performances of RUFM and CDM
Content
Tsinghua University
I. Introduction II. Comparison of Kinematics Characteristic of RUFM and CDM III. Experimental Conditions and Procedure IV. Experimental Results and Discussion V. Conclusions
However, there are quite a few reports on RUM of KDP crystals.
[2] 王强国,高航,裴志坚,等. KDP晶体超声辅助磨削的亚表面损伤研究[J]. 人工晶体学报. 2010(01): 67-71. [4] Wang Q, Cong W, Pei Z J, et al. Rotary ultrasonic machining of potassium dihydrogen phosphate (KDP) crystal: An experimental investigation on surface roughness[J]. Journal of Manufacturing Processes. 2009, 11(2): 66-73. [7] Wang Q, Pei Z J, Gao H, et al. Rotary Ultrasonic Machining of Potassium Dihydrogen Phosphate (KDP) crystal: an experimental investigation[J]. International Journal of Mechatronics and Manufacturing Systems. 2009, 2(4).
The preliminary experimental investigation contains four parts: A. Comparison the kinematics characteristic of RUFM and CDM
B. The nanoindentation to get the hardness and elastic moles and tool design on surface roughness in RUM of KDP Literature [7] presented an experimental investigation on RUM of KDP: grinding force and torque, surface roughness, and edge chipping were collected and analyzed
It’s found that the above mentioned studies are merely based on rotary ultrasonic drilling of KDP crystal. In literature [8] and [9], Pei et al. developed the rotary ultrasonic face milling (RUFM) process which keeps the material removal mechanisms and possesses the advantages of RUM process.
Content
Tsinghua University
I. Introduction II. Comparison of Kinematics Characteristic of RUFM and CDM III. Experimental Conditions and Procedure IV. Experimental Results and Discussion V. Conclusions
Content
Tsinghua University
Rotary ultrasonic machining (RUM) is a hybrid machining process that combines traditional rotary machining and ultrasonic vibration machining. Since its birth in 1960s, RUM has been applied to machine many types of materials: glass, ceramics, silicon carbide, and titanium. Generate high machining efficiency, excellent machining accuracy and surface quality.
Since each of these methods has its limitations, it is desirable to develop new methods for KDP crystal.
I. Introduction
Tsinghua University
2. Literature Review on RUM of KDP Crystal
This paper presents a preliminary experimental investigation on RUFM of KDP crystal.
I. Introduction
Tsinghua University
3. Mainly study contents of this paper
Fig.1, a hybrid that includes rotational motion, ultrasonic vibration and horizontal feed Fig.2. ultrasonic vibration is in the x-z plane or y-z plane, rotational motion and horizontal feed of diamond tool are in the x-y plane
II. Comparison of Kinematics Characteristic
Tsinghua University
2. Comparison of motion trajectory and velocity
(1) The motion trajectory of particle in RUFM is
I. Introduction
Tsinghua University
1. Introduction to KDP Crystal a good nonlinear optical and electro-optical crystal material widely used in various laser systems large-scale KDP is the unique used as nonlinear frequency conversion in the ICF
Chenglong Zhang (Ph.D. Candidate)
Department of Precision Instrument and Mechanology Tsinghua University
Content
Tsinghua University
I. Introduction II. Comparison of Kinematics Characteristic of RUFM and CDM III. Experimental Conditions and Procedure IV. Experimental Results and Discussion V. Conclusions
Tsinghua University
Experimental investigation on surface roughness of KDP crystal processed with rotary ultrasonic face milling
(Chenglong Zhang, Pingfa Feng, Zhijun Wu and Dingwen Yu)
(3) The velocity of particle in CDM is
VCDM r cos(t ) Vx r sin(t ) Vy
With equation (1), (2) and (3), it can be concluded that the effective machining length of particle in RUFM is larger than the effective length in CDM, and the effective processing velocity of particle in RUFM is also higher than the processing velocity in CDM with the same machining conditions, which make RUFM have better processing performance.