互换性第四章表面粗糙度及检测
互换性04第三章10
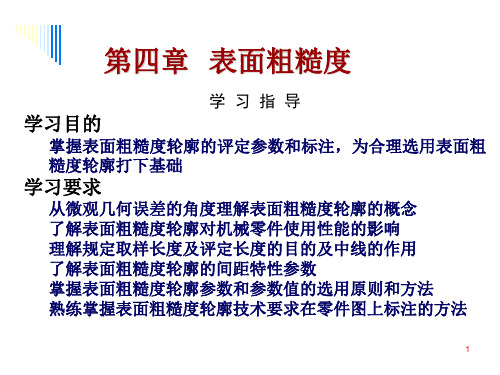
2、表面粗糙度、表面波纹度、形状误差的划分
(1)波距小于1mm,属于微观几何形状误差——表面粗糙度。 (2)波距10mm以上的且不呈明显周期性变化的——宏观的几何形 状误差。 (3)波距介于1~10mm的并呈周期性变化的——表面波纹度
3
3、表面粗糙度对零件性能的影响
⑴影响零件的耐磨性
⑵影响零件配合性质 ⑶影响零件的疲劳强度 ⑷影响零件的接触刚度 ⑸影响零件的抗腐蚀性
22
2、表面粗糙度代号
23
2、表面粗糙度代号
24
2、表面粗糙度代号
a 上限或下限符号U或L • 在完整符号中表示双向极限时应标注极限代号 •上限值在上方用U表示,下极限在下方用L表示,上 下极限值为16%规则或最大化规则的极限值。 •如果同一参数具有双向极限要求,在不引起歧义的情 况下,可以不加U、L。 • 上下极限值可以用不同的参数代号和传输带表达。
用带字母的完整符号的简化注法 可用带字母的完整符号,以等式的形式,在图形或标题 栏附近,对有相同表面结构要求的表面进行简化标注
45
3、表面粗糙度标注
表面结构要求的简化注法
只用表面结构符号的简化注法
未指定工艺方法的多个表面结构要 求的简化注法
要求去除材料的多个表面结构要 求的简化注法
不允许去除材料的多个表面结构要 求的简化注法
46
铣 6.3 0.8 3.2 (5) 3.2 3.2
a)
b)
c)
d)
图4-10表面粗糙度其它项目的标注
3.2
30
3.2
3.2 12.5
c 45
其余
25
12.5
1.6
3.2
30
《互换性与测量技术基础》用光切显微镜测量表面粗糙度实验

《互换性与测量技术基础》用光切显微镜测量表面粗糙度实验一、实验目的1.掌握用光切显微镜评定工件表面粗糙度的方法。
2.加深对表面粗糙度评定参数的理解。
二、实验仪器和工具光切显微镜、被测工件三、实验原理光切显微镜是以光切法原理,测量和观察机械零件加工表面的微观几何形状误差的,又称表面粗糙度显微镜。
在不破坏零件表面的条件下测出工件截面轮廓最大高度和沟糟宽度的实际尺寸。
此外,还可测量零件表面上个别位置的加工痕迹和破损情况。
该仪器用于测量零件表面轮廓最大高度Rz值,其测量范围取决于选用的物镜的放大倍数,通常适用于测量Rz等于 0.8—63 微米的表面粗糙度。
此种仪器只能对外表面进行测量,除对金属进行测量外,也可对纸张、木材和人工材料进行测量。
光切显微镜的外形及成像原理图如图 2-1和图 2-2所示。
图 2-1 光切显微镜外形图图 2-2 光切显微镜成像原理图由光源1发出的光,穿过夹缝2,形成带状光束,经物镜组O1O1′,斜向45°射向工件,凹凸不平的表面上呈现出曲折光带,再以45°反射,经物镜组O2O2′,到达分划板3上。
人眼通过目镜可以看到如图2-3所示。
图 2-3 光切显微镜的目镜视野四、测量步骤1、根据被测工件表面粗糙度的要求,选择合适的物镜组,分别安装在投射光管和观察光管的下端。
2、接通电源。
3、擦净被测工件,把它安放在工作台上,并使被测表面的切削痕迹的方向与光带垂直。
当测量圆柱形工件时,应将工件置于V形块上。
4、粗调节:用手托住支臂,松开锁紧螺钉,缓慢旋转支臂调节螺母,使支臂上下移动,直到目镜中观察到绿色光带和表面轮廓不平度的影象。
然后,将螺钉固紧。
要注意防止物镜与工件表面相碰,以免损坏物镜组。
5、细调节:缓慢而往复转动调节手轮,调焦环和调节螺钉,使目镜中光带最狭窄,轮廓影象最清晰并位于视场的中央。
6、松开螺钉,转动目镜测微器,使目镜中十字线的一根线与光带轮廓中心线大致平行(此线代替平行于轮廓中线的直线)。
(重点)互换性与技术测量知识点

互换性和技术测量知识点绪言互换性是指在同一规格的一批零件或部件中,任取其一,不需任何挑选或附加修配就能装在机器上,达到规定的功能要求,这样的一批零件或部件就称为具有互换性的零,部件。
通常包括几何参数和机械性能的互换。
允许零件尺寸和几何参数的变动量就称为公差。
互换性课按其互换程度,分为完全互换和不完全互换。
公差标准分为技术标准和公差标准,技术标准又分为国家标准,部门标准和企业标准。
第一章圆柱公差和配合基本尺寸是设计给定的尺寸。
实际尺寸是通过测量获得的尺寸。
极限尺寸是指允许尺寸变化的两个极限值,即最大极限尺寸和最小极限尺寸。
最大实体状态是具有材料量最多的状态,此时的尺寸是最大实体尺寸。
和实际孔内接的最大理想轴的尺寸称为孔的作用尺寸,和实际轴外接的最小理想孔的尺寸称为轴的作用尺寸。
尺寸偏差是指某一个尺寸减其基本尺寸所得的代数差。
尺寸公差是指允许尺寸的变动量。
公差=|最大极限尺寸—最小极限尺寸|=上偏差—下偏差的绝对值配合是指基本尺寸相同的,相互结合的孔和轴公差带之间的关系。
间隙配合:孔德公差带完全在轴的公差带上,即具有间隙配合。
间隙公差是允许间隙的变动量,等于最大间隙和最小间隙的代数差的绝对值,也等于相互配合的孔公差和轴公差的和。
过盈配合,过渡配合T=ai当尺寸小于或等于500mm时,i=0.45+0.001D(um)当尺寸大于500到3150mm时,I=0.004D+2.1(um)孔和轴基本偏差换算的条件:1.在孔,轴为同一公差等级或孔比轴低一级配合2.基轴制中孔的基本偏差代号和基孔制中轴的基本偏差代号相当3.保证按基轴制形成的配合和按基孔制形成的配合相同。
通用规则,特殊规则例题基准制的选用:1.一般情况下,优先选用基孔制。
2.和标准件配合时,基准制的选择通常依标准件而定。
3.为了满足配合的特殊需要,允许采用任一孔,轴公差带组合成配合。
公差等级的选用:1.对于基本尺寸小于等于500mm的较高等级的配合,由于孔比同级轴加工困难,当标准公差小于等于IT8时,国家标准推荐孔比轴低一级相配合,但对标准公差大于IT8级或基本尺寸大于500mm的配合,由于孔德测量精度比轴容易保证,推荐采用同级孔,轴配合。
互换性与技术测量
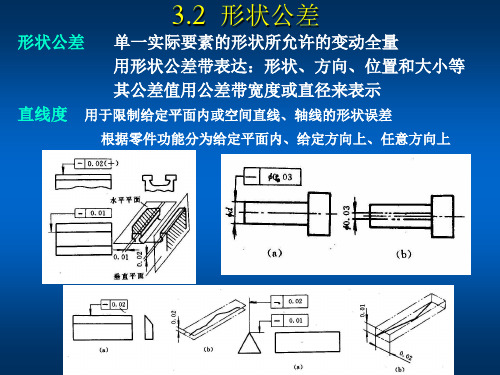
(2)评定参数及数值 评定参数由幅度(高度)参数、间距参数和混合(形状)参数组成 高度参数共三个,是基本的评定参数: o 轮廓算术平均偏差Ra 在取样长度 l 内,轮廓偏距绝对值的算术平均值
4.1 表面粗糙度的国家标准3
o
微观不平度十点高度Rz 在取样长度 l 内5个最大的轮廓峰高的平均值和5 个最大的轮廓谷深的平均值之和。 由于测量点不多,故在反映微观几何形状高度方面的特性不如Ra参数充分
3.6 形位误差的检测2
形状误差及其评定2 最小包容区域 包容被测实际要素且具有最小宽度或直径的区域。其形状与 形状公差带相同,而其大小、方向及位置则随实际要素而定 按近似方法评定的误差值通常大于最小区域法评定的误差值,更能保证质量 位置误差及其评定 形状公差应小于或等于定向公差 定向公差应小于或等于定位公差
四、最大实体要求
•
3.4 公差原则9
应用于基准要素
最大实体要求
3.4 公差原则10
零形位公差 被测要素采用最 大实体要求,且形位误差 为零
五、最小实体要求
3.4 公差原则11
适用于中心要素有形位公差的情况,控制被测要素的实际轮廓处于其最小实 体实效边界(即尺寸为最小实体实效尺寸的边界)之内 当其实际尺寸偏离最小实体尺寸时,允许其中心要素的形位误差值超出给出 的公差值,仅用于中心要素,以保证零件的最小壁厚和设计强度
圆柱度
3.2 形状公差3
线轮廓度
用于限制平面曲线的形状误差 用于确定被测要素的理想形状、方向、位置的尺寸 设计时对被测要素的理想要求,不轮廓度
用于限制一般曲面的形状误差
3.2 形状公差5
3.3 位置公差
位置公差 关联实际要素的位置对基准所允许的变动全量 位置公差带是限制关联实际要素变动的区域
互换性与技术测量知识点

互换性与技术测量知识点第1章绪言互换性是指在同一规格的一批零、部件中任取一件,在装配时不需经过任何选择、修配或调整,就能装配在整机上,并能满足使用性能要求的特性。
互换性应具备的条件:①装配前不换②装配时不调整或修配③装配后满足使用要求按互换性程度可分完全互换(绝对互换)与不完全互换(有限互换)。
按标准零部件和机构分外互换与内互换。
互换性在机械制造中的作用1.从使用方面看:节省装配、维修时间,保证工作的连续性和持久性,提高了机器的使用寿命。
2.从制造方面看:便于实现自动化流水线生产。
装配时,由于零部件具有互换性,不需辅助加工和修配,可以减轻装配工的劳动量,缩短装配周期。
3.从设计方面看:大大减轻设计人员的计算、绘图的工作量,简化设计程序和缩短设计周期。
标准与标准化是实现互换性的基础。
标准分类(1)按一般分:技术标准、管理标准和工作标准。
(2)按作用范围分:国际标准、国家标准、专业标准、地方标准和企业标准。
(3)按标准的法律属性分:强制性标准和推荐性标准。
国家强制性标准用代号“GB”表示。
国家推荐性标准用代号“GB/T”表示。
优先数系的种类(1)基本系列R5、R10、R20、R40(2)补充系列R80(3)派生系列选用优先数系的原则按“先疏后密”的顺序。
第2章测量技术基础测量过程的四要素:测量对象、计量单位、测量方法和测量精度。
测量仪器和测量工具统称为计量器具。
计量器具分类按其原理、结构和用途分为:(1)基准量具(2) 通用计量器具(3)极限量规类(4)检验夹具按测量值获得方式的的不同,测量方法可分为:1.绝对测量和相对(比较)测量法2.直接测量和间接测量法测量误差:测得值与被测量真值之差。
基本尺寸相同用∆评定比较测量精度高低基本尺寸不相同用ε评定(1)绝对误差Δ——测得值与被测量真值之差。
0x x -=∆(2)相对误差ε——测量的绝对误差的绝对值与被测量真值之比。
%100||||||000⨯∆≈∆=-=xx x x x ε (3)极限误差——测量的绝对误差的变化范围。
互换性与技术测量第四章--表面粗糙度及检测概要

Ra
1 lr
lr
Z ( x) dx
0
或
Ra
1 n
n i1
Zi
Z(x)
Zi
lr
Ra
算术平均 偏差Ra
X
2. 轮廓的最大高度 Rz(幅度参数或高度参数)
指在一个取样长度lr内,最大轮廓峰高Zp和最大轮廓谷深Zv 之和的高度。
Z(x)
Z P1
Z Pmax
中线 Rz Zpmax Zvmax
Rz
Z v1
用一条平行于X轴的线与轮廓单元相截所获得的各段截线长度
Mli 之和。
Ml(c) Ml1 Ml2 b1 b2
C是轮廓截面高度(即距峰顶线的距离),用微米或轮廓的 最大高度Rz的百分数表示。
C = Rz %
三、评定参数的数值 在幅度参数常用的范围内,优先选用Ra,Rz用于目前公厂仪 器。 各参数均分别由优先数系中的派生数系确定,见表4-1到4-5。
Rsm
1 m
m i 1
Xsi
中线
l
7r轮
廓 宽 度
4. 轮廓的支承长度率Rmr(c)
指在给定的水平位置c上,轮廓的实体材料长度Ml(c)与评定 长度ln的比率。
n
Rmr (c) bi / ln
i1
Ml(c) 100% ln
轮廓的支承长度率
轮廓的实体材料长度 Ml(c) 是指在一个给定水平位置c上,
6. 粗糙度轮廓中线 用标称形式的线穿过粗糙度轮廓,按最小二乘法拟合所确 定的线。即粗糙度轮廓上的点至中线的距离 Z(x) 的平方和为最
小(即 Z(x)2 min )。
7. 取样长度lr
用于评定轮廓粗糙度在X轴向上的一段长度,数值上它与轮 廓滤波器λc的标志波长相等。
表面粗糙度4

• 形状误差 :零件表面中峰谷的波距大于 10mm的不平程度属于形状误差。
二、表面粗糙度对零件使用性能的影响 影响零件的检测精度及外形美观,影响零件 的使用性能及寿命。 1、影响零件的耐磨性 2、影响配合性质的稳定性 3、影响零件的疲劳强度 4、影响零件的抗腐蚀性 5、影响零件的密封性
4.2 表面粗糙度的评定标准
A.使测量方便; B.等于; C.减少波度的影响 E.小于; D.考虑加工表面不均匀; F.大于; G.等于
• 某轴的尺寸为f60h7,其表面粗糙度Ra值可选 A mm。 A.0.8~1.6; B.0.2~0.4; C.1.6~ 3.2 • 轮廓仪是根据 D 原理制成的,双管显微镜是根 据 B 原理制成的。 A.印模; B.光切; C.干涉; D.针描
• 将表面粗糙度符号标注在图上,要求: 1 )用任何方法加工圆柱面φd 3 , R a最大允 许值为3.2μm。 2)用去除材料的方法获得孔φd1,要求R a 最大允许值为3.2μm。 3 )用去除材料的方法获得表面 a ,要求 R y 最大允许值为3.2μm。 4)其余用去除材料的方法获得表面,要求 Ra允许值均为25μm 。
学习要求: (1)掌握表面粗糙度的高度特性参数,了解 与间距特性和与形状特性有关的参数 (2)掌握表面粗糙度的基本选用原则和标注 方法 (3)了解表面粗糙度的测量方法
4.1 概述
一、表面粗糙度的形成 零件表面的形貌可分为三种情况: 表面粗糙度: 零件表面所具有的微小峰谷的 不平程度,其波距小于 1mm 。属于微观几何形 状误差。 表面波纹度:零件表面中峰谷的波距在 1 ~ 10mm的不平程度称为波纹度。 国际标准化组织第 57 技术委员会正在制定表 面波度的有关标准。
4、轮廓的最小二乘中线(m)(简称中线) 中线:是测量表面粗糙度的基准线,它具有 与被测表面一致的几何轮廓形状(如直线、圆 弧线等)。 最小二乘中线:在取样长度内使轮廓线上各 点的轮廓偏距Yi的平方和为最小的那条线。
互换性与测量技术重点知识点总结
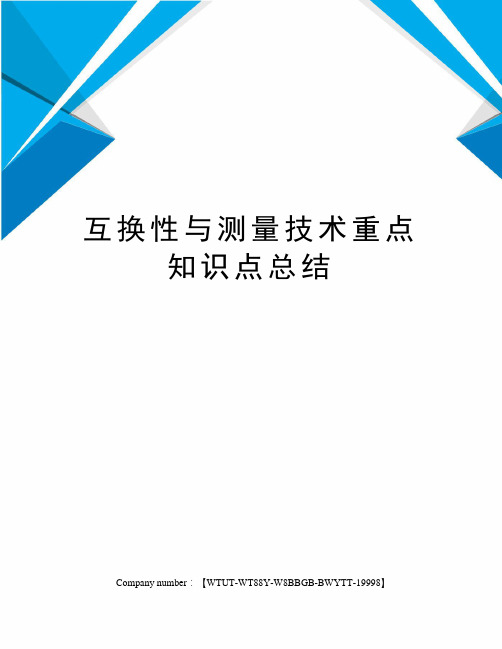
互换性与测量技术重点知识点总结Company number:【WTUT-WT88Y-W8BBGB-BWYTT-19998】互换性与测量技术重点知识点总结绪言互换性是指在同一规格的一批零件或部件中,任取其一,不需任何挑选或附加修配就能装在机器上,达到规定的功能要求,这样的一批零件或部件就称为具有互换性的零,部件。
通常包括几何参数和机械性能的互换。
允许零件尺寸和几何参数的变动量就称为公差。
互换性课按其互换程度,分为完全互换和不完全互换。
公差标准分为技术标准和公差标准,技术标准又分为国家标准,部门标准和企业标准。
第一章圆柱公差与配合基本尺寸是设计给定的尺寸。
实际尺寸是通过测量获得的尺寸。
极限尺寸是指允许尺寸变化的两个极限值,即最大极限尺寸和最小极限尺寸。
最大实体状态是具有材料量最多的状态,此时的尺寸是最大实体尺寸。
与实际孔内接的最大理想轴的尺寸称为孔的作用尺寸,与实际轴外接的最小理想孔的尺寸称为轴的作用尺寸。
尺寸偏差是指某一个尺寸减其基本尺寸所得的代数差。
尺寸公差是指允许尺寸的变动量。
公差=|最大极限尺寸 - 最小极限尺寸|=上偏差-下偏差的绝对值配合是指基本尺寸相同的,相互结合的孔与轴公差带之间的关系。
间隙配合:孔德公差带完全在轴的公差带上,即具有间隙配合。
间隙公差是允许间隙的变动量,等于最大间隙和最小间隙的代数差的绝对值,也等于相互配合的孔公差与轴公差的和。
过盈配合,过渡配合T=ai,当尺寸小于或等于500mm时,i=+(um),当尺寸大于500到3150mm时,I=+(um).孔与轴基本偏差换算的条件:1.在孔,轴为同一公差等级或孔比轴低一级配合2.基轴制中孔的基本偏差代号与基孔制中轴的基本偏差代号相当3.保证按基轴制形成的配合与按基孔制形成的配合相同。
通用规则,特殊规则例题基准制的选用:1.一般情况下,优先选用基孔制。
2.与标准件配合时,基准制的选择通常依标准件而定。
3.为了满足配合的特殊需要,允许采用任一孔,轴公差带组合成配合。
- 1、下载文档前请自行甄别文档内容的完整性,平台不提供额外的编辑、内容补充、找答案等附加服务。
- 2、"仅部分预览"的文档,不可在线预览部分如存在完整性等问题,可反馈申请退款(可完整预览的文档不适用该条件!)。
- 3、如文档侵犯您的权益,请联系客服反馈,我们会尽快为您处理(人工客服工作时间:9:00-18:30)。
`
理想要素位置的确定: 对轮廓要素
被测实际要素
f
f2 f1
` 最小区域
理想要素位置的确定: 对中心要素
理想轴线
被测实际轴线
最小区域
`
4 最小包容区域: 以理想要素为基准,包容实际要素,具有的最小高 度或直径的区域 理想平面 被测实际面
f
最小区域 包容面
`
5 公差带的各项形状
t s t
t a) b)
`
二 形位公差研究的对象
要素: 构成零件几何特征的点、 线、面 · 理想要素:具有几何学意义的要素 · 实际要素:实际存在的要素
· 被测要素: 具有形位公差要求 的要素
单一要素: 只对自身形状 有要求的要素
· 基准要素: 确定其它要素方位 的要素
轮廓要素 关联要素:
中心要素
`
对其它 要素有功能 要求的要素
Dft dft
实际外表面 `
关联要素的体外作用尺寸 与实际外表面 体外接触的最小理 想面的直径,该理想 面应与基准保持图 样上规定的几何关 系(图中垂直关系)
基准A
给定长度
da ≤dfe单 ≤ dfe关
最 小 理 想 面(定向) 实际外表面
分度值为0.02mm/m的水平仪,是指将水平仪放在1m长的桥板 上,当桥板前端升高0.02mm时,水平仪中的气泡正好移动一 水平仪 被测实际表面 格。若实测时桥板节距长度为L,水平仪读数值为a格,则以 水平仪移动方向 线性值表示的直线度误差值按比例折算应为
f=L × a × 0.02 /1000 L 1 最小条件法:
第四章
形状和位置公差及其检测
`
第一节
第二节 第三节
概述
形状公差和误差 位置公差和误差
第四节
第五节
形位误差的检測
公差原则
第六节
第七节
形位公差的选择
形位公差的标注
`
第一节
一 标准
概述
GB/T1182—1996 《形状和位置公差 通则、定义、 符号和图样表示法》 GB/T1184—1996 《形状和位置公差 未注公差值 》 GB/T4249—1996 《公差原则》 GB/T16671—1996 《形状和位置公差 最大实体要 求、最小实体要求和可逆要求》
单一基准使用的基准
(3)多基准: 由两个或三个相互垂直的平面所构成的基准
(4)目标基准:在零件表面上指定一些点、线或局部表面 作为基准
`
二 位置公差
(一) 概述 1 定向公差:关联实际要素对基准在方向上允许的变动量 2 定位公差:关联实际要素对基准在位置上允许的变动量 3 定向误差:被测实际要素对一具有确定方向的理想要素 的变动量,理想要素的方向由基准确定 4 定位误差:被测实际要素对一具有确定位置的理想要素 的变动量,理想要素的位置由基准和理论正确 尺寸确定
t
c)
f) d) e)
t
g)
h)
i)
`
二 各项形状公差
1 直线度:用于限定平面内或空间直线的形状误差
(1) 给定平面内
`
二 各项形状公差
1 直线度:用于限定平面内或空间直线的形状误差 (1)给定平面内 公差带是距离为公差值t的两平 行直线间的距离
(2) 给定一个方向 公差带的距离为公差值t的两平 行平面之间的区域
三 形位公差的分类
分类 项 直线度 形 状
目 符号 位
分
类 定
项目 平行度 垂直度 倾斜度
号符
平面度
置
向
定 位
圆 公
圆柱度 差
度
公 差
同轴度 对称度 位置度
线轮廓度
面轮廓度 ` 跳 动
圆跳动 全跳动
第二节
形状公差和误差
一 基本概念 1 形状公差:单一实际要素的形状所允许的变动全量
2 形状误差:被测实际要素对理想要素的变动量,理想 要素的位置应符合最小条件 3 最小条件:确定实际要素最大变动量为最小的理想 要素位置
③ 用复合位置度定位
复合位置度:用两个位置度公差联合控制孔组各孔 实际轴线的位置
几何图框可在小范围内平移和旋转
`
二 位置公差项目 (一) 概述 (二) 定向公差项目
(三) 定位公差项目
(四) 跳动公差项目
1 圆跳动:被测实际要素绕基准轴线作无轴向移动回转 一周时,由位置固定的指示表在给定方向上 测得的最大与最小读数之差。
`
位置度: 被测要素(点、线、面)对基准的位置的要求 位置度公差控制点的位置度误差
(1)位置度公差控制点的位置度误差
点的位置度公差,其公差带是以被测点的理想位置 为球心,以公差值0.08mm为直径的球内区域.
B基准平面
A基准轴线
公差带
`
位置度公差控制线的位置度误差
A基准平面
公差带
C基准平面
B基准平面
C
B
A
`
(3)位置度公差控制平面的位置度误差
50
第二基准 60° 第一基准
60°
A
t
`
(4)位置度公差控制孔组的位置度误差
孔组:根据零件的功能要求,对一些孔需按一定 的位置成组分布
几何图框:确定一组理想要素之间和(或)它们与 基准之间正确几何关系的图形。 对零件上孔组的位置度精度有两方面的要求:
( 1 )径向全跳动:整个被测要素相对于基准要素的跳动量
( 2 )端面全跳动:整个端面相对于基准要素的跳动量
`
1 圆跳动
(1) 径向圆跳动
基准轴线
测量平面
公差带的位置固定
`
1 圆跳动
(2) 端面圆跳动
基准轴线
测量圆柱面
`
1 圆跳动
(3) 斜向圆跳动
基准轴线
测量圆锥面
t
`
2 全跳动
(1) 径向全跳动
`
5 定向最小包容区域:按理想要素的方向来包容被测实 际要素,具有的最小宽度或直径 6 定位最小包容区域:按理想要素定位包容被测实际要 素,具有的最小宽度或直径
`
定向最小包容区域: 按理想要素的方向来包容被测实际要素,具 有的最小宽度或直径
实际被测要素 定向最小包容区域 被测实际要素
与基准平面 平行的理想要素
基准轴线
B
(2) 端面全跳动
基准轴线
`
第四节 形位误差的检测
GB1958-80(形状和位置误差检测规定)
检验原则: 与理想要素比较原则 测量坐标值原则
测量特征参数原则
测量跳动原则 控制实效边界原则 一 与理想要素比较原则 1 直线度误差
`
(1) 直线度误差的检测
水平仪 桥板
L
节距法
被测零件
将被测要素调整到水平位置,水平仪按节距沿被测要 素移动,并使水平仪首尾点相连。
2 全跳动:被测实际要素绕基准轴线作无轴向移动回转, 同时指示表沿理想素线连续移动,指示表在 给定方向上测得的最大与最小读数之差。
`
1 圆跳动 按测量方向相对于基准轴线的不同:
( 1 )径向圆跳动:圆柱回转体任一横截面上的跳动量
( 2 )端面圆跳动:端面任一直径处,在轴向方向的跳动量
( 3 )斜向圆跳动:圆锥面在法向方向的跳动量 2 全跳动
2 垂直度:控制被测要素相对于基准要素成90º 角
面对面的垂直度
基准平面
`
面对线的垂直度
基准直线
`
线对面的垂直度
一个方向
基准平面
`
线对面的垂直度
二个方向
φd
基准平面
`
线对面的垂直度 任意方向
φt
基准平面
`
二 位置公差项目
(二) 定向公差项目
3 倾斜度:控制被测要素相对于基准要素成0~90º 之间 某一确定角度的要求 面对面的倾斜度
↓ ↑
基准直线
f
基准平面
定向最小区域
`
二 位置公差项目
(二) 定向公差项目
1 平行度:控制被测要素相对于基准要素成0角 面对线平行度
基准直线
`
面对面平行度
`
线对线的平行度 一个方向
给定方向
基准直线
`
线对线的平行度 φD
`
二 位置公差项目 (二) 定向公差项目
理想轮廓线
基准直线B
基准直线A
`
5 线轮廓度:限制平面曲线或轮廓线的形状误差
`
二 各项形状公差 6 面轮廓度:限制空间曲面或轮廓面的形状误差
理想轮廓面
`
第三节
位置公差和误差
一 基准和基准体系 1 基准:是确定被测要素方向或位置的依据 2 基准要素的实现 模拟法、分析法、直接法、目标法
基准实际要素
(3)最大内切圆法 适用于内圆表面
(4)最小二乘圆法
近似法
`
第五节
公差原则
研究:尺寸公差与形位公差的关系 一 基本概念 1 局部实际尺寸(Da da): 在实际要素的任意正截面上,两对应点之间测得的距离
↑ ↑ ↑ ↓ ↓ ↓
↑
↑ ↑
↓ ↓ ↓
`
一 基本概念 1 局部实际尺寸(Da da):
2 体外作用尺寸(Dfe dfe): 在被测要素的给定长度上,与实际内表面体外接触的最大理 想面,或与实际外表面体外接触的最小理想面的直径或宽度
单一要素的体外作用尺寸 实际内表面
dfe
实际外表面 `
Dfe
一 基本概念 1 局部实际尺寸(Da da): 2 体外作用尺寸(Dfe dfe):
3 体内作用尺寸(Dft dft): 在被测要素的给定长度上,与实际内表面体内接触的最小理想面,或与实 际外表面体内接触的最大理想面的直径或宽度