直径2470大导程多头梯形螺纹数控编程
数控车床上加工梯形螺纹

数控车床上加工梯形螺纹内容摘要:在数控车床上加工梯形螺纹是一个全新的课题,本文通过对梯形螺纹加工的工艺分析和加工方法的研讨,探索出一套可以在数控车床上加工出合格梯形螺纹的方法在普通车床的生产实习过程中,加工梯形螺纹课题是最基本的实习课题,但在数控车床实习过程中,常常由于加工工艺方面的原因,却很少进行梯形螺纹的加工练习,甚至有人提出在数控车床上不能加工梯形螺纹,显然这种提法是错误的.其实,只要工艺分析合理,使用的加工指令得当,完全可以在数控车床上加工出合格的梯形螺纹.一、梯形螺纹加工的工艺分析1.梯形螺纹的尺寸计算梯形螺纹的代号梯形螺纹的代号用字母“Tr”及公称直径×螺距表示,单位均为mm。
左旋螺纹需在尺寸规格之后加注“LH”,右旋则不用标注。
例如Tr36×6,Tr44×8LH等.国标规定,公制梯形螺纹的牙型角为30°.梯形螺纹的牙型如图(1),各基本尺寸计算公式如表1—1。
图1 梯形螺纹的牙型2。
梯形螺纹在数控车床上的加工方法直进法螺纹车刀X向间歇进给至牙深处(如图2a)。
采用此种方法加工梯形螺纹时,螺纹车刀的三面都参加切削,导致加工排屑困难,切削力和切削热增加,刀尖磨损严重.当进刀量过大时,还可能产生“扎刀”和“爆刀”现象。
这种方法数控车床可采用指令G92来实现,但是很显然,这种方法是不可取的。
斜进法螺纹车刀沿牙型角方向斜向间歇进给至牙深处(如图2b)。
采用此种方法加工梯形螺纹时,螺纹车刀始终只有一个侧刃参加切削,从而使排屑比较顺利,刀尖的受力和受热情况有所改善,在车削中不易引起“扎刀”现象。
该方法在数控车床上可采用G76指令来实现。
交错切削法螺纹车刀沿牙型角方向交错间隙进给至牙深(如图2c)。
该方法类同于斜进法,也可在数控车床上采用G76指令来实现。
切槽刀粗切槽法该方法先用切槽刀粗切出螺纹槽((如图2d),再用梯形螺纹车刀加工螺纹两侧面。
这种方法的编程与加工在数控车床上较难实现.表1—1 梯形螺纹各部分名称、代号及计算公式名称代号计算公式P 1.5~5 6~12 14~44 牙项间隙a ca c0.25 0.5 1大径d、D4d=公称直径,D4=d+a c中径d2、D2d2=d—0。
数控车床加工梯形螺纹的方法与技巧
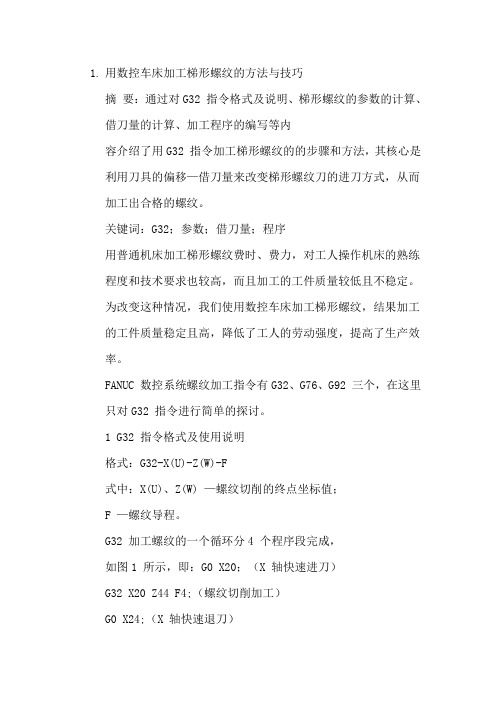
1.用数控车床加工梯形螺纹的方法与技巧摘要:通过对G32 指令格式及说明、梯形螺纹的参数的计算、借刀量的计算、加工程序的编写等内容介绍了用G32 指令加工梯形螺纹的的步骤和方法,其核心是利用刀具的偏移—借刀量来改变梯形螺纹刀的进刀方式,从而加工出合格的螺纹。
关键词:G32;参数;借刀量;程序用普通机床加工梯形螺纹费时、费力,对工人操作机床的熟练程度和技术要求也较高,而且加工的工件质量较低且不稳定。
为改变这种情况,我们使用数控车床加工梯形螺纹,结果加工的工件质量稳定且高,降低了工人的劳动强度,提高了生产效率。
FANUC 数控系统螺纹加工指令有G32、G76、G92 三个,在这里只对G32 指令进行简单的探讨。
1 G32 指令格式及使用说明格式:G32-X(U)-Z(W)-F式中:X(U)、Z(W) —螺纹切削的终点坐标值;F —螺纹导程。
G32 加工螺纹的一个循环分4 个程序段完成,如图1 所示,即:G0 X20;(X 轴快速进刀)G32 X20 Z44 F4;(螺纹切削加工)G0 X24;(X 轴快速退刀)G0 Z5;(Z 轴快速退刀),提醒注意:设定δ1、δ2 的数值要合适恰当。
图1 车刀走刀路线2 梯形螺纹参数的计算以图2 为例说明梯形螺纹参数的计算。
图2 零件图表1 梯形螺纹参数表名称代号计算公式计算结果/mm螺距牙顶间隙大径中径小径牙高Pacdd2d3h4 mm0.25 mm公称直径d2 =d-0.5Pd3=d-2hh=0.5P+ac40.25222017.502.253 采用偏移刀具的方法加工梯形螺纹G32 加工螺纹的进刀是直进法,如图3 所示,这种进刀法是车刀的三棱同时切削,容易产生震动和扎刀现象。
如采用偏移刀具的方法,即使车刀沿着Z轴方向移动一定的量(普通车床中的借刀量),那么车刀的进刀方式就变成图4 所示的方式,这样车刀的两棱切削能有效的防止震动和扎刀,提高了梯形螺纹的质量。
图3 车刀直进法图4 车刀斜进法以表2 为例说明借刀量的计算:总借刀量的计算:h×tan150=2.25×0.2679=0.603 mm每刀借刀量的计算:ap×tan150每刀借刀量的数值如表2 所示。
大直径大导程多头梯形内螺纹的数控加工

!" #$%&’()(*+
大直径大导程多头梯形内螺纹的数控加工
郝宏伟
( 河北工业职业技术学院, 河北 石家庄 !"!!#$)
摘 要 ! 介绍了采用数控化改造的 !"#$#% 立车设备,加工大直径零件上的大导程多头梯形左旋内螺纹的加工方法。 阐述了螺纹车刀的选用、 螺纹分度法的确定、 螺纹加工工艺的确定、 螺纹的数控加工程序, 以及叶轮硬化后使用轴头螺 纹规修螺纹的方法。利用该数控加工方法加工叶轮上的螺纹, 既能够保证螺纹的加工精度, 又可以减少刀具重磨和重定 位次数, 缩短辅助时间, 提高生产效率。 关键词 !大直径; 大导程; 多头内螺纹; 数控加工 , %$$(& $)&$$*)&$$ 中图分类号 !!&’#( 文献标识码 !" 文章编号 !#$$%&%’’’
/%$ 01# /#$ 0$ 234$,$ 5367 /4$ 6%3$ 643# 6#3&%$ 613%$ 6&3&$ 683%1 6738,7 /9$ 0$ 23$ 53$ /1$ 0$ 53:;<(6#= /&$ 0$ 236% /8$ )%%%$$$4 ’364 /7$ 0$ 23 (4$,$ />$ 0$ 53$ /%$$ -9$ ?@A
! !"
加工程序 利用周向分度法基本原理进行分度 ! 运用斜向单面
683(%1 673 (7,1’&6%3%$ 673 (8,%&’’ 6%34$ 673(1,74 ’ (6%39$ 6434# 673 (#,#7 (
再次 ! 使用若干次循环 ! 分别对上 ) 下面光刀 ! 直至轴 头螺纹规下去为止 !并预留出螺纹硬化变形收缩量 " 6%3$
在数控车床上用宏程序加工梯形螺纹

不是理想的加工方法。
ቤተ መጻሕፍቲ ባይዱ
为了解决“直进分”和“斜进法”的缺点,就
必须改善刀具的切削方式。通过分析,最后选用
(见图3)“分层切削法”。“分层切削法”是先
把螺纹X向分成若干层,
每层Z向再进行若干次粗
切削,再进行左、右精车
切削。每层刀具只需沿左
右牙型线切削,背吃刀量
小,从而使排屑比较顺
利,刀具的受力和受热情
图3 分层切削法
起刀点Z轴偏 移量(CE)的计 算公式为
图7
CE=BE-BC=(AH+tan15°×HE)-BC =(P/4+tan15°×HE)-BC 即起刀点Z轴偏移量(螺纹右侧留0.1mm的精 加工量)参数变量为
#8=#2/4+TAN[15]*[#1-#3]/2-#6/2-0.1;
每层Z轴的切削余量(DF)的计算公式为
M 机床自动化 achine Tools Automation
在数控车床上用宏程序加工梯形螺纹
中国北车永济新时速电机电器有限责任公司 (山西 044502) 陈建军 永济电机高级技工学校 (山西 044500) 张丽波
一、梯形螺纹在数控车床上的加工工艺
数控车加工螺纹有三种指令:G32、G92、 G76。其中G32、G92的进刀方式为“直进法” (见图1);G76的进刀方式为“斜进法”(见图 2)。
DF=BF-BD=2(AH+tan15°×HE)-BD
即每层Z轴的切削余量(螺纹左侧留0.1mm的 精加工量)参数变量为
#9=#2/2+TAN[15]*[#1-#3]-#6-0.1
(3)外螺纹Tr36×6程序
O8888; M03S200; G00X100Z50; T0101; G00X40Z10; #1=36;(螺纹大径及公称直径) #2=6;(螺距) #3=#1-#2/2;(螺纹中径) #4=0.5;(牙顶间隙) #5=#1-#2-2*#4;(螺纹小径) #6=1(T型螺纹刀刀尖宽) #7=0.366*#2-2*TAN[15]*#4;(牙底槽宽) #8=#2/4+TAN[15]*[#1-#3]/2-#6/2-0.1;(起 到点Z轴偏移量,右侧留0.1mm) #9=#2/2+TAN[15]*[#1-#3]-#6-0.1;(每层Z 轴的切削余量,左侧留0.1mm) #10=0.5(X轴的吃刀量) N1IF[#1LE#5]GOTO4;(判断切削直径,如果X值 ≤小径,则执行N4程序段) N2IF[#9LE0.1]GOTO3;(判断每层Z轴切削余量如 果余量≤0.1mm,则执行N3程序段) G00Z[10+#8];(Z轴起刀点) G92X#1Z-42F#2;(切削螺纹) #8=#8-0.3;(重新计算Z轴起刀点偏移量,递减0.3mm) #9=#9-0.3;(重新计算每层Z轴切削余量,递减0.3mm) GOTO2;(无条件执行N2程序段) N3#1=#1-#10;(重新计算切削直径X值) #8=#2/4+TAN[15]*[#1-#3]/2-#6/2-0.1(重新 计算Z轴起刀点偏移量) #9=#2/2+TAN[15]*[#1-#3]-#6-0.1;(重新计 算每层Z轴切削余量) IF[#1GE33]THEN#10=0.5(判断切削直径,对X轴吃刀 量重新赋值)
数控车-梯形螺纹编程
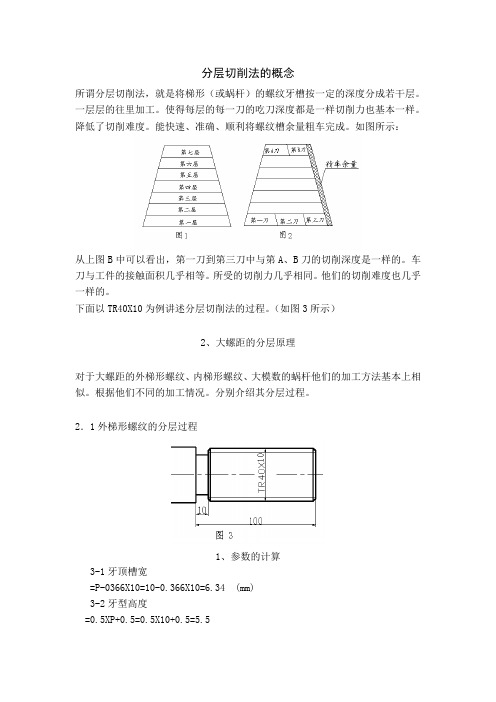
分层切削法的概念所谓分层切削法,就是将梯形(或蜗杆)的螺纹牙槽按一定的深度分成若干层。
一层层的往里加工。
使得每层的每一刀的吃刀深度都是一样切削力也基本一样。
降低了切削难度。
能快速、准确、顺利将螺纹槽余量粗车完成。
如图所示:从上图B中可以看出,第一刀到第三刀中与第A、B刀的切削深度是一样的。
车刀与工件的接触面积几乎相等。
所受的切削力几乎相同。
他们的切削难度也几乎一样的。
下面以TR40X10为例讲述分层切削法的过程。
(如图3所示)2、大螺距的分层原理对于大螺距的外梯形螺纹、内梯形螺纹、大模数的蜗杆他们的加工方法基本上相似。
根据他们不同的加工情况。
分别介绍其分层过程。
2.1外梯形螺纹的分层过程1、参数的计算3-1牙顶槽宽=P-0366X10=10-0.366X10=6.34 (mm)3-2牙型高度=0.5XP+0.5=0.5X10+0.5=5.5(如图4所示)设刀宽为2mm,留0.2mm的精车余量,每1mm深分一层.则各层粗车时应车的宽度为:(图6用于宏程序)X=1Xtan15=0.268≈0.273-3第一层粗车时应车的槽宽为:AB =6.34(顶宽)-0.2(精车余量)-0.27(左边减小量)-0.27(右边减小量)=5.6mm3-4第二层粗车时的槽宽:C、D两端分别比A、B两端缩小0.27,所以CD长为(以下第层都缩小0.27)CD=5.6-0.54=5.063-5第三层粗车时的槽宽:EF=5.06-0.54=4.52mm3-6第四层粗车时的槽宽:GH=4.52-0.54=3.983-7第五层粗车时的槽宽:IJ=3.98-0.54=3.443-8第六层(0.5mm深)粗车时的槽宽:KL=3.44-0.28=3.16设车螺纹时车刀的起刀点为(X42,Z5),各项参数如下图所示:备注栏为采用子程序时,在原来每刀基础上再分出3刀后的每层总刀数。
2.2 加工程序粗车完后再进行精加工,上述螺纹部分的加工程序为:O0001……T0303(梯形螺纹刀,刀宽为1.2)G00 X42 Z5G92 X38 Z-95 F10G00 Z7G92 X38 Z-95 F10G00 Z8.6G92 X38 Z-95 F10G00 Z5.27G92 X36 Z-95 F10G00 Z7.27G92 X36 Z-95 F10G00 Z8.33G92 X36 Z-95 F10G00 Z5.54G92 X34 Z-95 F10G00 Z7.54G92 X34 Z-95 F10G00 Z8.06G92 X34 Z-95 F10G00 Z5.81G92 X32 Z-95 F10G00 Z7.79 G92 X32 Z-95 F10G00 Z6.08G92 X30 Z-95 F10G00 Z7.52G92 X30 Z-95 F10G00 Z6.22G92 X29 Z-95 F10G00 Z7.38G92 X29 Z-95 F10。
数控车床加工梯形螺纹的方法与技巧
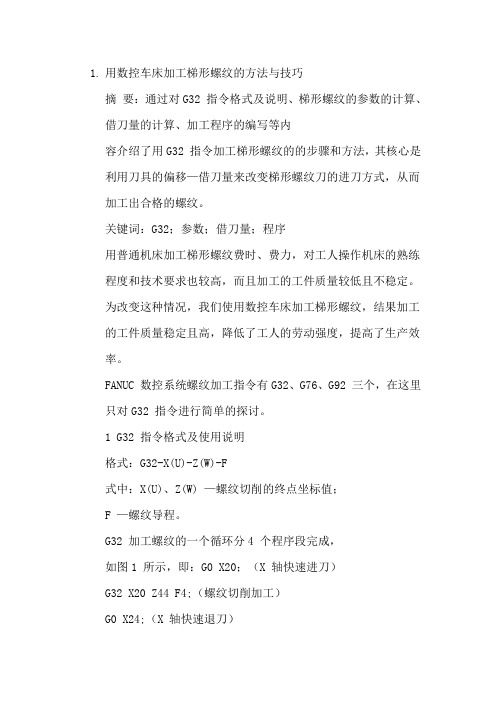
1.用数控车床加工梯形螺纹的方法与技巧摘要:通过对G32 指令格式及说明、梯形螺纹的参数的计算、借刀量的计算、加工程序的编写等内容介绍了用G32 指令加工梯形螺纹的的步骤和方法,其核心是利用刀具的偏移—借刀量来改变梯形螺纹刀的进刀方式,从而加工出合格的螺纹。
关键词:G32;参数;借刀量;程序用普通机床加工梯形螺纹费时、费力,对工人操作机床的熟练程度和技术要求也较高,而且加工的工件质量较低且不稳定。
为改变这种情况,我们使用数控车床加工梯形螺纹,结果加工的工件质量稳定且高,降低了工人的劳动强度,提高了生产效率。
FANUC 数控系统螺纹加工指令有G32、G76、G92 三个,在这里只对G32 指令进行简单的探讨。
1 G32 指令格式及使用说明格式:G32-X(U)-Z(W)-F式中:X(U)、Z(W) —螺纹切削的终点坐标值;F —螺纹导程。
G32 加工螺纹的一个循环分4 个程序段完成,如图1 所示,即:G0 X20;(X 轴快速进刀)G32 X20 Z44 F4;(螺纹切削加工)G0 X24;(X 轴快速退刀)G0 Z5;(Z 轴快速退刀),提醒注意:设定δ1、δ2 的数值要合适恰当。
图1 车刀走刀路线2 梯形螺纹参数的计算以图2 为例说明梯形螺纹参数的计算。
图2 零件图表1 梯形螺纹参数表名称代号计算公式计算结果/mm螺距牙顶间隙大径中径小径牙高Pacdd2d3h4 mm0.25 mm公称直径d2 =d-0.5Pd3=d-2hh=0.5P+ac40.25222017.502.253 采用偏移刀具的方法加工梯形螺纹G32 加工螺纹的进刀是直进法,如图3 所示,这种进刀法是车刀的三棱同时切削,容易产生震动和扎刀现象。
如采用偏移刀具的方法,即使车刀沿着Z轴方向移动一定的量(普通车床中的借刀量),那么车刀的进刀方式就变成图4 所示的方式,这样车刀的两棱切削能有效的防止震动和扎刀,提高了梯形螺纹的质量。
图3 车刀直进法图4 车刀斜进法以表2 为例说明借刀量的计算:总借刀量的计算:h×tan150=2.25×0.2679=0.603 mm每刀借刀量的计算:ap×tan150每刀借刀量的数值如表2 所示。
数控车床螺纹编程

三、螺纹加工单一循环指令G92
1、功能
退出
切削 返回
切入
三、螺纹加工单一循环指令G92
2、格式
G92 X(U) Z(W) I(R) F ; 其中:
X,Z—螺纹终点绝对坐标值 U,W—螺纹终点相对于循环
起点的增量坐标值
I(R)—切削起点的半径值-
C
切削终点的半径值
F—螺纹的导程(单头为螺距)
oz x
编程步骤
2、确定加工工艺
(1)手动车端面, 对刀,设置 编程零点
oz x
编程步骤
2、确定加工工艺
(2)用900偏刀粗车 M22×20, M27×40, φ32×50外圆, 留0.25精车量
oz A
x
编程步骤
2、确定加工工艺
(2)用900偏刀粗车 M22×20, M27×40, φ32×50外圆, 留0.25精车量
M22×1.5螺纹
G92 X20.7 Z-18. F1.5;
oz A
x
编程步骤
2、确定加工工艺 (5)换尖刀加工
M22×1.5螺纹
G92 X20.2 Z-18. F1.5;
oz A
x
编程步骤
2、确定加工工艺 (5)换尖刀加工
M22×1.5螺纹
G92 X20.05 Z-18. F1.5;
oz A
x
oz A
x
编程步骤
2、确定加工工艺
(2)用900偏刀粗车 M22×20, M27×40, φ32×50外圆, 留0.25精车量
oz A
x
编程步骤 O0001;
G40 G97 G99 M03 S800 F0.25; T0101;
M20、8;确定加工工艺
用西门子数控立车加工大导程多头螺纹数控编程
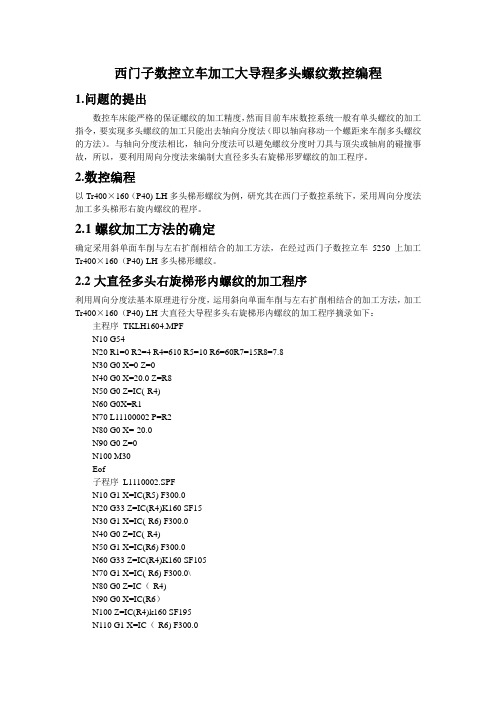
西门子数控立车加工大导程多头螺纹数控编程1.问题的提出数控车床能严格的保证螺纹的加工精度,然而目前车床数控系统一般有单头螺纹的加工指令,要实现多头螺纹的加工只能出去轴向分度法(即以轴向移动一个螺距来车削多头螺纹的方法)。
与轴向分度法相比,轴向分度法可以避免螺纹分度时刀具与顶尖或轴肩的碰撞事故,所以,要利用周向分度法来编制大直径多头右旋梯形罗螺纹的加工程序。
2.数控编程以Tr400×160(P40)-LH多头梯形螺纹为例,研究其在西门子数控系统下,采用周向分度法加工多头梯形右旋内螺纹的程序。
2.1螺纹加工方法的确定确定采用斜单面车削与左右扩削相结合的加工方法,在经过西门子数控立车5250上加工Tr400×160(P40)-LH多头梯形螺纹。
2.2大直径多头右旋梯形内螺纹的加工程序利用周向分度法基本原理进行分度,运用斜向单面车削与左右扩削相结合的加工方法,加工Tr400×160(P40)-LH大直径大导程多头右旋梯形内螺纹的加工程序摘录如下:主程序TKLH1604.MPFN10 G54N20 R1=0 R2=4 R4=610 R5=10 R6=60R7=15R8=7.8N30 G0 X=0 Z=0N40 G0 X=20.0 Z=R8N50 G0 Z=IC(-R4)N60 G0X=R1N70 L11100002 P=R2N80 G0 X=-20.0N90 G0 Z=0N100 M30Eof子程序L1110002.SPFN10 G1 X=IC(R5) F300.0N20 G33 Z=IC(R4)K160 SF15N30 G1 X=IC(-R6) F300.0N40 G0 Z=IC(-R4)N50 G1 X=IC(R6) F300.0N60 G33 Z=IC(R4)K160 SF105N70 G1 X=IC(-R6) F300.0\N80 G0 Z=IC(-R4)N90 G0 X=IC(R6)N100 Z=IC(R4)k160 SF195N110 G1 X=IC(-R6) F300.0N120 G0 Z=IC(-R4)N130 G0 Z=IC(R6)N140 G33 Z=IC(R4)k160 SF285N150 G1 X=IC(-R6) F300.0N160 R4=R4+R5*TAN(R7)/2N170 G0 Z=IC(-R4)N180 G0 X=IC(R6)N190 RET其中:R1:X轴定位点(直径量);R2:车削次数,即子程序调用次数;R4:起刀点;R5:每次吃刀深度;R6:退刀距离;R7:刀具角度(15度为牙型上面,-15度为牙型下面);R8:Z轴定位点。
- 1、下载文档前请自行甄别文档内容的完整性,平台不提供额外的编辑、内容补充、找答案等附加服务。
- 2、"仅部分预览"的文档,不可在线预览部分如存在完整性等问题,可反馈申请退款(可完整预览的文档不适用该条件!)。
- 3、如文档侵犯您的权益,请联系客服反馈,我们会尽快为您处理(人工客服工作时间:9:00-18:30)。
直径2470大导程多头梯形螺纹数控编程研究对象:耐磨钢;HRC:35~40;外径为2470mm。
T,400*160(P40)-I,H的大导程多头梯形螺纹左旋。
确定螺纹升角
T,400*160(P40)-I,H是公称直径为400mm,导程为160mm,螺距为40mm,牙型角为30度的4头梯形左旋内螺纹,计算螺纹升角为7.6度
设备选择
数控立车:西门子802D SL
要求:主轴编码器良好
螺纹车刀的选用
耐磨钢:软化时硬度HRC为25~30,硬化后硬度HRC为35~40。
要在软化车螺纹,硬化修螺纹的车削工艺,刀具要具有耐用度和耐冲击性,首选YG类焊接刀(俗话说称铸铁刀或者YG3,YG8,YG6X等)。
刀具侧切削刃的后角选择(3~5度)+7.6度和(3~5度)-7.6度。
加工方法
第一种笨方法
径向进刀配合左右进刀法自行编程,分8刀进行粗加工,一共是26次粗车循环。
每次只需要调整几个参数即可完成粗加工。
降低操作难度,减少刀具重磨和重新定位次数。
缩短辅助时间,提高效率。
第二种方法
质量要求过高的话第一种的可行性就低了。
更加符合精车螺纹的还是斜向单面车削的方法好用,程序也不同。
下面采用周向分度法编程
TM400160.MPF
N10G54 G0 X=20 Z=8
N20 R1=0 R2=4 R4=610 R5=10 R6=60 R7=15 R8=7.8
N30 G0 X=0 Z=0
N50 G0 Z=IC(-R4)
N60 G0 X=R1
N70 L01012 P=R2
N80 G0 X=-20
N90 G0 Z=0
N100 M30
01012.SPF
N10 G1 X=IC(R5) F300
N20 G33 Z=IC(R4) K160 SF=15
N30 G1 X=IC(-R6) F300
N40 G0 Z=IC(-R4)
N50 G0 X=IC(R5)
N60 G33 Z=IC(R4) K160 SF=105
N70 G1 X=IC(-R6) F300
N80 G0 Z=IC(-R4)
N90 G0 X=IC(R6)
N100 G33 Z=IC(R4) K160 SF=195
N110 G1 X=IC(-R6) F300
N120 G0 Z=IC(-R4)
N130 G0 Z=IC(R6)
N140 G33 Z=IC(R4) K160 SF=285
N150 G1 X=IC(-R6)F300
N160 R4=R4+R5*TAN(R7)/2
N170 G0 Z=IC(-R4)
N180 G0 X=IC(R5)
N190 RET
该程序中
R1:X轴定位点(mm)
R2:加工次数
R4:起到点(mm)
R5:每刀吃刀深度(mm)
R6:退刀距离(mm)
R7:刀具角度(15度为牙型上面,-15度为牙型下面)
R8:Z轴定位退刀点(mm)
分三部
第一步分4次循环,斜向单面加工,消除牙型上面不整齐现象
1)R1=0, R2=20,R4=610,R5=0.5,R6=60,R7=15,R8=8.5;
2)R1=10,R8=7.16;
3)R1=20, R8=5.82;
4)R1=30,R2=24, R8=4.48;
第二步
再分4刀加工牙型下面,斜向单面加工,消除牙型上面不整齐现象
5)R1=0, R2=20,R4=610,R5=0.5,R6=60,R7=-15,R8=-8.5;
6)R1=10,R8=-7.16;
7)R1=20, R8=-5.82;
8)R1=30,R2=24, R8=-4.48.;
第三步
使用若干次循环,分别对上,下面光出,直至轴头螺纹规能够旋和下去为止,并留螺纹硬化变形收缩量。
R1=0,R2=4,R4=610,R5=11,R=60,R7=正负15, R8=调整量(每次0.1mm)。