锻造2
魔兽世界锻造1-450升级攻略

魔兽世界锻造1-450升级攻略1.锻造1-450升级说明:黄色的技能是以2倍材料去计算(实际上可能花不到1.5倍);绿色的技能是以3倍的材料去计算(实际上可能花不到2倍);提升等级的机率,橘色是100%,黄色大约是67%,绿色是不足25%,灰色则无法提升等级;除非运气差到一个极限,不然材料只会多不会少;2.1-75级:技能等级成品名称 - (所需材料) -升级大约次数 [习得等级-黄色-绿色-灰色等级] 1-35劣质磨刀石 - (劣质的石头x1) -54[1-15-35-55]35-65劣质砂轮 - (劣质的石头x2) -50[25-45-65-85]65-75粗制磨刀石 - (粗糙的石头x1) -23[65-65-72-80]3.76-150级:技能等级成品名称 - (所需材料) -升级大约次数 [习得等级-黄色-绿色-灰色等级] 75-90粗制砂轮 - (粗糙的石头x2) -33[75-75-87-100] (需要约95个)90-110铜质符文腰带 - (铜锭x10) -20[70-110-130-150]90-115铜质符文护腕 - (铜锭x10劣质砂轮x3) -5[90-115-128-140]因为青铜锭x2- (铜锭x1锡锭x1),以数量而言,是1:1。
差别只在一铜要配一锡才能做出两个青铜,所以这边可以自行选择要用铜继续升,还是换青铜来升。
115-125劣质青铜护肩 - (青铜锭x5粗制砂轮x1) -15[110-140-155-170]125-135重砂轮 - (沉重的石头x3) -20[125-125-137-150]135-140重磨刀石 - (沉重的石头x1) -15[125-125-133-140]这边用 [重磨刀石] 升级可以省很多石头,但因为后期会用到20个 [重砂轮] ,所以我是先用 [重砂轮] 来升等级 (方便算数量)。
各位可以先用 [重磨刀石] 升到140,然后再做 [重砂轮] ,这样可以多赚几个等级。
第二章 锻造

1.锤上模锻
动画演示
(一)锻模结构
(二)模膛的分类Leabharlann 模膛预锻模膛 模锻模膛
终锻模膛
拔长模膛
制坯模膛
摩擦压力机上模锻生产特点
4.胎模锻造
动画演示
1) 扣模 2) 筒模
3) 合模
§2-2 锻造工艺规程的制订
1. 锻件图的绘制 1)敷料、余量及公差的确定 2)分模面的选择 3)设计模锻斜度、圆角半径 4)确定冲孔连皮
b
a
a
c
d
cd
b
2. 坯料重量和尺寸的计算
3. 锻造工序的确定
G坯料 = G锻件+G料头+G烧损 模锻件的工序确定
自由锻的结构工艺性
模锻件结构工艺性
滚压模膛 弯曲模膛
切断模膛
根据模锻件的复杂程度,所需变形的模膛数 量不等,可将锻模设计成单膛锻模或多膛锻模。
单膛锻模:一副锻模上只具有一个终锻模膛。
多膛锻模:是在一副锻模上具有两个以上模膛的 锻模。
弯曲连杆零件
2. 曲柄压力机上模锻 动画演示
曲柄压力机上模锻生产特点
曲柄压力机上模锻所用模具 ⒊摩擦压力机上模锻
4、锻造工艺规程中的其它内容
材料种类 低碳钢 中碳钢 合金结构钢
始锻温度/℃ 1200~1250 1150~1200 1100~1180
终锻温度/℃ 800 800 850
温度(℃) 火色
1300 1200 1100 900 800 700 小于600 白色 亮黄 黄色 樱红 赤红 暗红 黑色
塑性成形的特点与基本生产方式

(二).锤上模锻
(1)锤上模锻设备:锤上模锻所用设备有蒸 汽—空气锤、高速锤等。 (2)锻模结构:锤上模锻所用的锻模都由上模 和下模组成。如图所示。
(2)锻模结构
1-锤头 2-上模 3-飞边槽 4-下模 5-模垫 6、7、10-紧固楔铁 8-分模面 9-模膛
(3)模膛分类
模膛
模锻模膛 制坯模膛
抗力 塑性 变形抗力曲线
塑变化曲线
a
变形速度
变形速度对塑性及变形抗力的影响示意图
(3)应力状态: 压应力数目多,塑性好
挤压时金属应力状态
拉拔时金属应力状态
3.1 塑性成形方法
3.1.1 锻造 一、自由锻 play
利用冲击力或压力使金属在上下两个砥铁之间产生变 形,从而获得所需形状及尺寸的锻件。
(四) 选择锻造设备 (五) 确定锻造温度范围和加热火次 (六) 热处理及锻件后续热处理 (七) 编写工艺卡片 (八) 估算锻件价格及成本
3.2.2模锻工艺规程制订
(一) 根据零件图绘制锻件图
(1)确定分模面(分型面) 分模面:上下锻模在模锻件上的分界面。
①分模面应选在锻件的最大截面处; ②分模面的选择应使模膛浅而对称; ③分模面的选择应使锻件上所加敷料最少; ④分模面应最好是平直面。
3.1.2 板料冲压
概述 1、概念
板料冲压是利用装在冲床上的设备(冲模)使板 料产生分离或变形的一种塑性成形方法。它主要用 于加工板料(10mm以下,包括金属及非金属板料) 类零件,故称为板料冲压。
2.设备 play
冲压常用的设备有剪床和冲床等。
剪床
冲床
冲压设备
3.板料冲压的特点
① 生产率高(靠模具设备成形,操作简便,易实现“两化”) ② 可成形复杂形状的制件, 而且废料少,材料利用率高 ③ 制件尺寸精度高、表面质量好、互换性好,不需机加工 ④ 制件强度高、刚性好、重量轻 ⑤ 加工成本低 ⑥ 冲模制造复杂,成本高
第二章锻造

弯曲模膛:对于弯曲的杆类模锻件,需采用弯 曲模膛来弯曲坯料。坯料可直接或先经其它 制坯工步后放入弯曲模膛进行弯曲变形。
切断模膛:它是在上模与下模的角部组成的一 对刃口,用来切断金属。单件锻造时,用它 从坯料上切下锻件或从锻件上切下钳口;多 件锻造时,用它来分离成单个锻件。
4.模锻圆角半径
模锻圆角:指模锻件中断面形状和平面形状变
化部位棱角的圆角和拐角处的圆角。
作用:圆角结构可使金属易于充满模膛,避免锻
模的尖角处产生裂纹,减缓锻件外尖角处的磨损, 从而提高锻模的使用寿命。同时可增大锻件的强 度。
大小:模锻件外圆角半径(r)取1.5~12mm,内
圆角半径(R)比外圆角半径大 2~3倍。模膛越深 圆角半径的取值就越大。
二、坯料重量和尺寸的确定
坯料重量可按下式计算:
G坯料=G锻件+G烧损+G料头
式中:G坯料——坯料重量; G锻件——锻件重量; G烧损——加热中坯料ቤተ መጻሕፍቲ ባይዱ面因氧化而烧损的重量; 第一次加热取被加热金属重量的2%~3%; 以后各次加热的烧损量取1.5%~2.0%。 G料头——锻造过程中冲掉或被切掉的那部分金属
第4二.2节锻锻造造
锻造:在加压设备及工具作用下,使坯料、 铸锭产生局部或全部的塑性变形,以获得 一定尺寸、形状和质量的锻件的加工方法。
第一节 锻造方法
一、自由锻
定义:指用简单的通用工具,或在锻造设备的上
下砧间直接使坯料变形而获得所需的几何形状及 内部质量锻件的方法。
设备:
锻锤 中小型锻件 液压锤 大型件
适用范围:大批量生产中锻制中小型锻件。
优点:锻件精度高、生产率高、劳动条件好、节
模块二(锻造)讲述
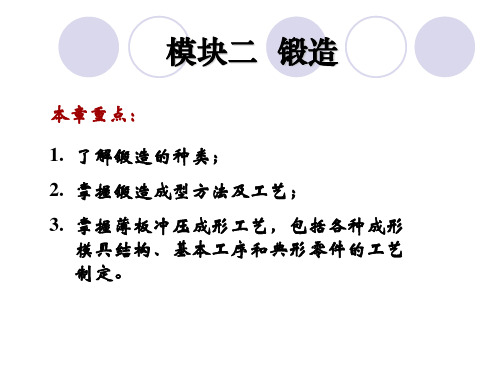
d)落下部分的放大图
落料和冲孔时金属板料的分离过程示意图
冲裁件断裂面有明 显的区域特征
光亮带:冲头挤压 切入所形成的光滑 表面,断面质量最 佳
剪裂带:是材料在 剪断分离时所形成 的断裂带,表面粗 糙
冲裁时 金属板 料的分 离过程 示意图
✓2. 凸凹模间隙
凹凸模之间间隙z不仅严重影响冲裁件的断
面质量,而且影响模具寿命、卸料力、推件 力、冲裁力和冲裁件的尺寸精度。因此正确 选择间隙值对冲裁生产至关重要。
2.2.2 金属的可锻性
一、金属的可锻性(塑性加工性能)
定义:金属断崖难易程度的工艺性能。
衡量指标:金属的塑性和变形抗力。塑性↑,变
形抗力↓,可锻性↑。
2.2.3金属的加热
1.加热目的 加热目的是指提高金属的塑性,降低变形能力,以改善其可
锻性,获得良好的锻后组织。 2.锻造温度范围 大谤范围是指锻件由始锻温度到终锻温度之间的温度间隔。 3.烧损与脱碳 烧损是指钢件在加热过程中因氧化铁皮脱落而造成的损失。 脱碳是指钢件在加热过程中其表层的碳因氧化而损失。 4.过烧与过热 过热是指将金属加热到过高温度或高温下保温时间过长而引
单边间隙c的经验公式
c m
(δ板料厚度)
(m相关系数)
✓凸凹模间隙对冲裁件质量的影响
间隙过大:断面质量差,光亮 带小一些,剪裂带和毛刺均较 大
间隙过小:断面质量好,光亮 带增大,但毛刺也增大,模具 磨损严重,寿命受影响。
合理选择模具间隙,主要考虑 冲裁件断面质量和模具寿命这 两个主要的因素。一般说来, 当对冲裁件断面质量要求较高 时,应选取较小的间隙值,而 当冲裁件的质量要求不高时, 则应可能地加大间隙值,以利 于提高冲模的寿命。
锻造工艺学第二部分

,含有大量杂质,必须将缩孔与冒口一起切除。
疏松集中在中心部位,降低组织的致密度,破坏
了金属的连续性,锻造时用大变形才能消除。
Seite 10
⑸溅疤
当采用上注法浇注时,钢液将冲击钢锭模
底而飞溅至模壁上,溅珠和钢锭不能凝为一体,在 钢锭表面形成溅疤。锻前应铲除,否则会在锻件上 形成夹层。
一般来说,钢锭越大,产生上述缺陷 的可能性就越大,缺陷性质就越严重。
Seite 13
2、材料内部缺陷:
⑹碳化物偏析 在高碳合金钢中易产生。原因是碳化 物在开坯和轧制时未被打碎和不均匀分布造成的。碳化 物偏析容易引起锻件开裂等。消除碳化物偏析,其最有 效的办法是采用反复镦—拔工艺,彻底打碎碳化物并均 匀分布。 ⑺非金属夹杂 夹杂物被轧成带状,破坏金属的连续性 ,严重时,会引起锻件开裂。
Seite 11
五、型材的常见缺陷
1、表面缺陷:
⑴划痕 轧制中的意外原因在其表面划出伤痕,深度达 0.2~0.5mm,会影响锻件的质量 ⑵折迭 已氧化的表层金属被压入金属内部而形成折迭, 折缝内有氧化物而不能锻合。在折迭处易产生应力集中,影 响锻件质量。 ⑶发裂 钢锭皮下气泡被轧扁、拉长、破裂形成发状裂纹 ,深度约为0.5~1.5mm。在高碳钢和合金钢中易产生此缺陷
Seite 17
其它材料的下料工作,一般都在锻造车间的下料工段 进行。 常用的下料方法有:剪切、冷折、锯切、车削、砂轮 切割、剁断及特殊精密下料等。 各种下料方法都有其特点,它们的毛坯质量、材料 利用率、加工效率等往往有很大不同。选用何种方法 ,应视材料性质、尺寸大小、批量和对下料质量的要 求而定。
Seite 15
总之
表面缺陷,锻前应去除,以免影响锻件质量。 内部缺陷,严重时不应投入生产。
第二节 锻造工艺
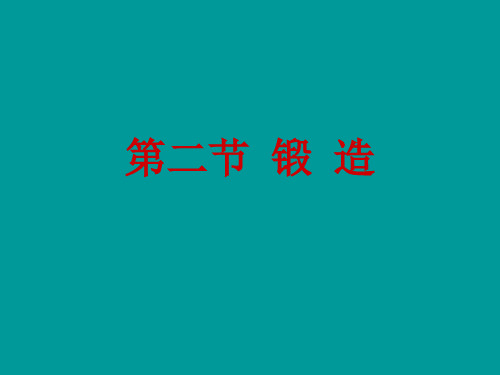
胎模锻与自由锻相比有如下优点 :
( 1) 由于坯料在模膛内成形,所以锻件尺 寸比较精确,表面比较光洁,流线组织的 分布比较合理,所以质量较高。 ( 2) 由于锻件形状由模膛控制,所以坯 料成形较快,生产率比自由锻高1~5倍。 ( 3) 胎模锻能锻出形状比较复杂的锻件。 ( 4)余块少,因而加工余量较小,既可节 省金属材料,又能减少机加工工时。
镦粗
作用力沿轴向,增大横截面积,用于齿轮,圆盘,圆环坯。 长径比H/D2.5。
全镦粗
局部镦粗
【冲孔】是在坯料上冲出透孔或不透孔的
锻造工序。
冲孔的方法主要有以下两种 : 1) 双面冲孔法。 2) 单面冲孔法。
双面冲孔示意图
单面冲孔示意图
冲
用于孔径 25的齿轮,套 筒,圆环等空心 件。
孔
冲头
曲柄压力机滑块行程固定不变,且 坯料在静压力下一次成形,金属不易充 填较深的模膛,不宜用于拔长、滚挤等 变形工序,需先进行制坯或采用多模膛 锻造。此外,坯料的氧化皮也不易去除, 必须严格控制加热质量。 曲柄压力机与同样锻造能力的模锻 锤相比,结构复杂、造价高,因此适合 在大批、大量生产中制造优质锻件。
锻造按成形方法则可分为自由锻、 模锻、冷镦、径向锻造、挤压、成形轧 制、辊锻、辗扩等。 锻造用料主要是各种成分的碳素钢 和合金钢,还有铝、镁、铜、钛等及其 合金。 材料的原始状态有棒料、铸锭、金 属粉末和液态金属。
第一节 自由锻
【自由锻】利用冲击力或压力,使金属在上、
下砧铁之间,产生塑性变形而获得所需形状、 尺寸以及内部质量锻件的一种加工方法。 自由锻造时,除与上、下砧铁接触的金属 部分受到约束外,金属坯料朝其它各个方向均 能自由变形流动,不受外部的限制,故无法精 确控制变形的发展。 采用自由锻方法生产的锻件称为 自由锻
3-2锻造技术

3)模锻斜度与模锻圆角
模锻斜度:为便于从模膛中顺利取出锻件, 平行于锤击方向的侧面(垂直于分模面方向) 应具有的斜度。(图3-17,内外侧斜度)
模锻圆角:为利于金属液流动而充满模膛, 避免锻模凹入尖角处产生应力集中而造成裂 纹,在凸起尖角处阻碍金属流动而产生磨损, 需把锻件转角处设计为圆角。
4)绘制模锻件图
由M坯可计算出坯料尺寸。还需对照钢材规 格标准加以修正,选用与计算坯料尺寸一 致的标准尺寸或相邻的较大尺寸。
锻造比=原始坯料尺寸/锻件尺寸 轧制碳钢锻造比:1.3~1.5
三、模锻
定义:将加热好的金属坯料放在一定形状 (与锻件形状一致)的锻模模膛里,施加 外力时坯料发生塑性变形而充满模膛,从 而获得锻件的方法。
外围实线:锻件轮廓(包括余块、加工余 量、公差、圆角等)
双点划线:零件轮廓 图3-18
四、胎模锻简介
在自由锻设备上使用简单模具(胎模) 生产锻件的工艺方法。 一般用自由锻方法制坯,然后在胎模 中终锻成形。
二、自由锻
定义:加热后的坯料放在上、下两个铁砧 之间,通过上铁砧向下运动施加冲击力或 压力,从而使坯料向四周产生自由的塑性 变形的锻造方法。
设备:锻锤和液压机 锻锤:空气锤和蒸汽-空气锤,中小型锻件 液压机:以液体产生的静压力使坯料变形, 是生产大型锻件(500t)的唯一方式。
1.自由锻特点
§2 锻造技术
锻造:利用冲击力或静压力使加热后的坯料在 锻压设备上、下砧之间产生塑性变形,以获得 所需尺寸、形状和质量的锻件。 常用锻造方法:自由锻、模锻、胎模锻。
体积不变定律
定律内容:V后 = V前 定律依据:金属塑性变形的过程实际是通过
金属流动而使坯料体积进行再分配的过程, 因而遵循体积不变定律。 应用:由锻件尺寸计算所需原始材料的尺寸。
- 1、下载文档前请自行甄别文档内容的完整性,平台不提供额外的编辑、内容补充、找答案等附加服务。
- 2、"仅部分预览"的文档,不可在线预览部分如存在完整性等问题,可反馈申请退款(可完整预览的文档不适用该条件!)。
- 3、如文档侵犯您的权益,请联系客服反馈,我们会尽快为您处理(人工客服工作时间:9:00-18:30)。
第二章 锻造
§2锻造工艺规程的制订
一 、自由锻工艺规程 (重点内容!)
自由锻件工艺规程的拟定过程:
一是,首先根据零件的形状、尺寸、技术 要求及生产条件,绘制锻件图; 绘制锻件图时应考虑:
1.敷料,又称:余块,
为了:填平补齐简化工艺
自由锻
锻件图
自由锻工艺规程
绘制锻件图
自由锻
1.敷料
自由锻工艺规程
留给锻工操作余地 绘图注意事项 ①锻件轮廓粗实线; ②双点划线示零件; ③尺寸线上下:
线上:锻件尺寸和公差 线下:零件尺寸加括号 二是,计算坯料的质量和尺寸; 重量:G坯料=G锻件+G烧损+G芯+G料头 尺寸:与锻造过程中的变形程度有关 例如: 碳素钢锭拔长:Y拔长=F0/F>2.5~3 轧材作坯料 : Y拔长=F0/F>1.3~1.5
•分模面为平面,使 上下锻模的模膛深 度 一 致
锤上模锻
1)定在最大截面处; (如图a-a则无法出 模) 2)错模现象易检查; (图中c-c不易查错 模) 3)利于充型好出模; (图中b-b充型难) 4)减少余块省工料; 5)平面分型易制造。 图 中 的 d-d 面 较 合 理
模锻工艺规程
1.分模面
Ho
V坯 F坯
三是,确定变形工序及工具;
盘类件:镦粗(拔长、镦粗)、冲孔
轴类件:拔长(镦粗、拔长)、切肩、锻台阶
筒类件:镦粗(拔长、镦粗)、冲孔、心轴上拔长 环类件:镦粗(拔长、镦粗)、冲孔、心轴上扩孔 弯曲类件:拔长(镦粗、拔长)、弯曲 曲轴类件:拔长(镦粗、拔长)、错移、锻台阶、扭转
四是,确定加热和冷却规范; 确定热处理规范; 提出锻件的技术条件和检验要求; 确定劳动组织和工时; 最后填写工艺卡片。
制定模锻件图
x
x x √
锤上模锻
模锻工艺规程
制定模锻件图
2.余量、公差、敷料、冲孔连皮 余量:1~4mm 公差: (0.3 ~ 3)mm 冲孔连皮:d>25mm
锤上模锻
模锻工艺规程
3.模锻斜度
制定模锻件图
不合理
合理
锤上模锻
模锻工艺规程
4.模锻圆角半径
制定模锻件图
锤上模锻
模锻工艺规程
制定模锻件图
例
锤上模锻
模锻工艺规程
制定模锻件图
例
分模面
a
a
锤上模锻
模锻工艺规程
制定模锻件图
例
余量
锤上模锻
模锻工艺规程
制定模锻件图
例
模锻斜度
锤上模锻
模锻工艺规程
制定模锻件图
例
圆 角
锤上模锻
长轴类模锻件
模锻工艺规程
确定模锻工步
拔长、滚压、弯曲、预锻、终锻等
锤上模锻
盘类锻件
模锻工艺规程
确定模锻工步
镦粗、预锻、终锻
4.平直对称又简单;
模锻件结构工艺性的图 5.高筋薄壁是麻烦; 例见教材P108所示。 6.多孔深孔要回避;
§4.模锻件结构工艺性 7.锻焊组合巧用劲。
二、模锻件工艺规程拟订
1.分模面
分模面选择原则
•要保证模锻件能从 模 膛 中 取 出 •上下两模沿分模面 的模膛轮廓一致 •分模面能使模膛深 度 最 浅 •分模面应使零件上 所加的敷料最少
尺寸:与锻造过程中的变形程度有关 例如: 镦粗法: 坯料高度H0应为直径Do或边长 Ao的1.25-2.5倍。 V 3 V ; H Do 0.8 1.0 3 V坯 ; Ao 0.74 0.93 坯 F
坯 o
坯
拔长法:
F坯 1.1 1.5F锻
Ao F坯
Do 1.13 F坯
自由锻件工艺规程的拟定举例
请同学们讨论“图示齿轮坯”的锻造工艺
1.查表,确定余块、余量和加工量。
2.分析、拟订自由锻基本工序。
§3自由锻件结构工艺性
1.避免锥形和斜形; 2.少用空间相贯线; 3.肋筋凸台不能锻; 4.遇繁化简再组合。 1.合理分模是关键;
2.锻模斜度要考虑;
3.相交面处用圆角;
锤上模锻
切边和冲孔 校正
模锻工艺规程
修整工序
热处理
清理
精压
绘制锻件图
敷料
自由锻
2.锻件余量
自由锻工艺规程
绘制锻件图
锻件余量
自由锻
3.锻件公差
自由锻工艺规程
绘制锻件图
120±3 ( 110)
280±2 (240)
350±12 (310) 760±12 (680)
142 -4 ( 130) 230±4 ( 190)
+3
2.加工余量 便于切削留余地
3.锻件公差