HB-3耐硫变换催化剂应用小结
变换催化剂的使用效果评价
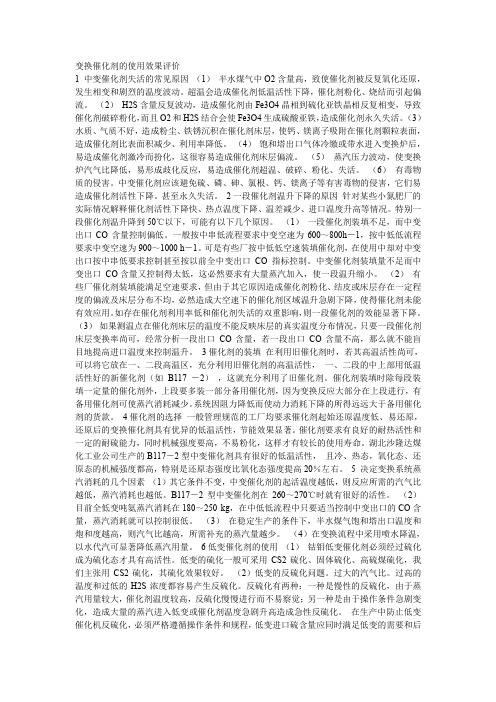
变换催化剂的使用效果评价1 中变催化剂失活的常见原因(1)半水煤气中O2含量高,致使催化剂被反复氧化还原,发生相变和剧烈的温度波动。
超温会造成催化剂低温活性下降,催化剂粉化、烧结而引起偏流。
(2)H2S含量反复波动,造成催化剂由Fe3O4晶相到硫化亚铁晶相反复相变,导致催化剂破碎粉化,而且O2和H2S结合会使Fe3O4生成硫酸亚铁,造成催化剂永久失活。
(3)水质、气质不好,造成粉尘、铁锈沉积在催化剂床层,使钙、镁离子吸附在催化剂颗粒表面,造成催化剂比表面积减少、利用率降低。
(4)饱和塔出口气体冷缴或带水进入变换炉后,易造成催化剂激冷而扮化,这很容易造成催化剂床层偏流。
(5)蒸汽压力波动,使变换炉汽气比降低,易形成歧化反应,易造成催化剂超温、破碎、粉化、失活。
(6)有毒物质的侵害。
中变催化剂应该避免硫、磷、砷、氯根、钙、镁离子等有害毒物的侵害,它们易造成催化剂活性下降。
甚至永久失活。
2一段催化剂温升下降的原因针对某些小氮肥厂的实际情况解释催化剂活性下降快、热点温度下降、温差减少、进口温度升高等情况。
特别一段催化剂温升降到50℃以下,可能有以下几个原因。
(1)一段催化剂装填不足,而中变出口CO含量控制偏低。
一般按中串低流程要求中变空速为600~800h-1,按中低低流程要求中变空速为900~1000 h-1。
可是有些厂按中低低空速装填催化剂,在使用中却对中变出口按中串低要求控制甚至按以前全中变出口CO指标控制。
中变催化剂装填量不足而中变出口CO含量又控制得太低,这必然要求有大量蒸汽加入,使一段温升缩小。
(2)有些厂催化剂装填能满足空速要求,但由于其它原因造成催化剂粉化、结皮或床层存在一定程度的偏流及床层分布不均,必然造成大空速下的催化剂区域温升急剧下降,使得催化剂未能有效应用。
如存在催化剂利用率低和催化剂失活的双重影响,则一段催化剂的效能显著下降。
(3)如果测温点在催化剂床层的温度不能反映床层的真实温度分布情况,只要一段催化剂床层变换率尚可,经常分析一段出口CO含量,若一段出口CO含量不高,那么就不能盲目地提高进口温度来控制温升。
预硫化耐硫变换催化剂在煤化工生产中的应用
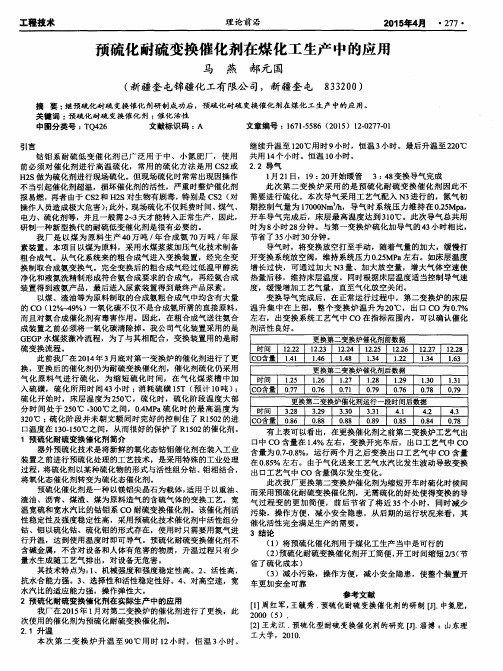
粗合成气 。从 气化 系统来的粗合成气进入变 换装 置,经完全变 换制取合成氨 变换气 。完全变换后 的粗合成 气经过低温 甲醇洗 净化和液氮洗 精制形成符合氨合成要求 的合成气 ,再经氨合成 装置得到液氨 产品,最后进入尿素装置得 到最终产品尿素 。 以煤 、渣 油等为原料制取 的合成氨 粗合成气 中均含有大量 的 CO( 1 2 %- - 4 9 %)一氧化碳不仅不是合成氨所 需的直接原料 , 而且对 氨合成催化剂有毒害作用 。因此 ,在粗合成气送往氨合 成装置之 前必须将一氧化碳清 除掉 。我公司气化装置采用 的是 GE GP水煤 浆激冷流程 ,为 了与其相配合 ,变换装置用 的是耐
温宽硫和宽水汽 比的钴钼系 C O耐硫变 换催化剂 。该催化 剂活
性稳定性及强度稳定性 高,采 用预硫化技术催化剂 中活性 组分 钴、钼 以硫化钴 、硫化钼 的形式存在 ,使用时 只需要用氮 气进 行 升 温 ,达 到 使 用 温 度 时 即 可 导 气 。预 硫 化 耐 硫 变 换 催 化 剂 不 含碱金属,不含对设 备和人 体有危害的物质 ,升温过程 只有少 量水生成随工艺气排 出,对 设备无危害 。 其技术特点为 : 1 、机 械强度和强度稳定性高 。2 、活性高 , 抗水合能力强 。3 、选择性和活性稳 定性好。4 、对 高空速 ,宽 水汽比的适应能力强 ,操作弹 性大 。 2 预硫化耐硫变换催化剂在 实际生 产中的应用 我厂在 2 0 1 5 年1 月对 第二变换炉的催化剂进行 了更换,此 次使用的催化剂为预硫化 耐硫 变换催化剂 。 2 . 1 升 温 本 次第 二 变 换 炉升 温 至 9 0 ℃用 时 l 2小 时,恒 温 3小时 。
变换 导气完成后 ,在正常运行过程 中,第二变换炉的床层 温 升集 中在 上部 ,整个 变换 炉温 升为 2 0 ℃ ,出 口 C O为 0 . 7 % 左右 ,出变换系统工 艺气中 C O在指标 范围内,可 以确认催化 剂 活 性 良好 。
变换催化剂交流总结报告

水煤浆 德士古 96.10
4 大化公司合成氨厂 低硫渣油 德士古 97.4
5 山西化肥厂
碎煤 鲁奇 97.6
6 中石化镇海炼化公司化肥厂 高硫渣油 德士古 99.5
7 上海焦化厂
水煤浆 德士古 2003.8
9 哈尔滨煤气厂
碎煤 鲁奇 98.1
10云南解放军化肥厂
碎煤 鲁奇 2000.1
11 安徽淮化集团公司化肥厂 水煤浆 德士古 2000.9
神木化学工业公司、神华 装置、陕西神木化工 份公司 、陕西神木化
宁夏煤业公司 、内蒙伊 有限公司制甲醇装 学工业公司、神华宁
泰煤制油有限公司、重庆 置、新奥年产60万吨 夏煤业公司 、内蒙
万盛化工有限公司、久泰 制甲醇装置、新能凤 伊泰煤制油有限公
能源内蒙古有限公司 、陕 凰年产45万吨制甲醇 司、重庆万盛化工有
适用压力 1.0~10.0 Mpa
适用温度范围 200 ~500 ℃
适应水/气 0.3~2.0 mol/mol
工艺气硫含量 200 ppm
主要业绩:
序号 应用单位
原料 气化工艺 时间
1 中石油乌鲁木齐石化化肥厂 低硫渣油 德士古 94.7
2 中石油宁夏化工总厂 低硫渣油 德士古 95.5
3 渭河化肥厂
3.99
50-150nm 10.45 17.86 8.12
7.10
耐硫变换催化剂及其制备方法
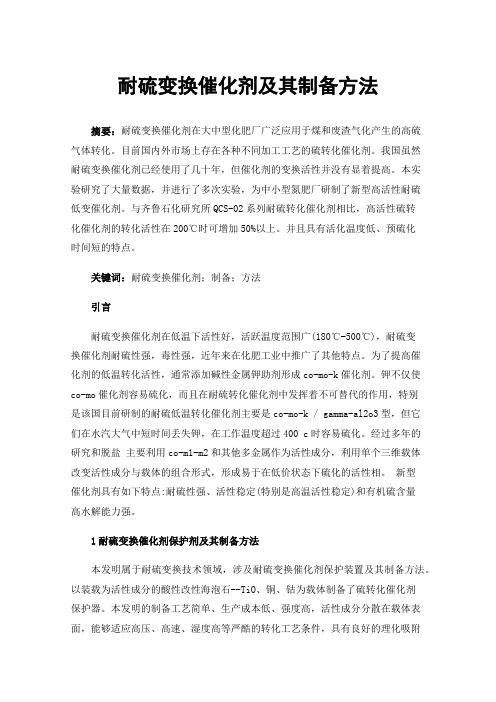
耐硫变换催化剂及其制备方法摘要:耐硫变换催化剂在大中型化肥厂广泛应用于煤和废渣气化产生的高硫气体转化。
目前国内外市场上存在各种不同加工工艺的硫转化催化剂。
我国虽然耐硫变换催化剂已经使用了几十年,但催化剂的变换活性并没有显着提高。
本实验研究了大量数据,并进行了多次实验,为中小型氮肥厂研制了新型高活性耐硫低变催化剂。
与齐鲁石化研究所QCS-02系列耐硫转化催化剂相比,高活性硫转化催化剂的转化活性在200℃时可增加50%以上。
并且具有活化温度低、预硫化时间短的特点。
关键词:耐硫变换催化剂;制备;方法引言耐硫变换催化剂在低温下活性好,活跃温度范围广(180℃-500℃),耐硫变换催化剂耐硫性强,毒性强,近年来在化肥工业中推广了其他特点。
为了提高催化剂的低温转化活性,通常添加碱性金属钾助剂形成co-mo-k催化剂。
钾不仅使co-mo催化剂容易硫化,而且在耐硫转化催化剂中发挥着不可替代的作用,特别是该国目前研制的耐硫低温转化催化剂主要是co-mo-k / gamma-al2o3型,但它们在水汽大气中短时间丢失钾,在工作温度超过400 c时容易硫化。
经过多年的研究和脱盐主要利用co-m1-m2和其他多金属作为活性成分,利用单个三维载体改变活性成分与载体的组合形式,形成易于在低价状态下硫化的活性相。
新型催化剂具有如下特点:耐硫性强、活性稳定(特别是高温活性稳定)和有机硫含量高水解能力强。
1耐硫变换催化剂保护剂及其制备方法本发明属于耐硫变换技术领域,涉及耐硫变换催化剂保护装置及其制备方法。
以装载为活性成分的酸性改性海泡石--TiO、铜、钴为载体制备了硫转化催化剂保护器。
本发明的制备工艺简单、生产成本低、强度高,活性成分分散在载体表面,能够适应高压、高速、湿度高等严酷的转化工艺条件,具有良好的理化吸附废油、稠油、一定的初始活性和良好的主动稳定性,有助于降低转换催化剂的负荷、延长转换催化剂的使用寿命、使用范围广泛、成本低廉且经济实惠的原材料。
耐硫变换催化剂循环硫化方案
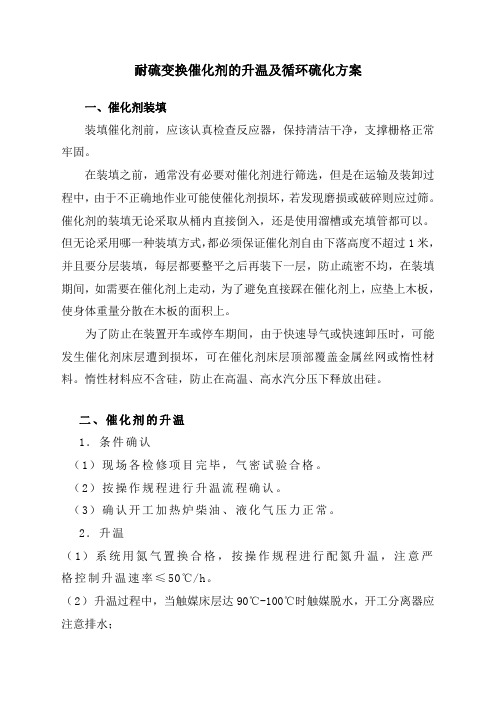
升 0.5 常温~120
30
3
0.5
120
6
温
0.5
120~220
30
3
0.5
220
6
备注 氮气量 20000Nm3/h 恒温释放吸附水
恒温拉平床层温差
三、催化剂的硫化 1、当催化剂床层温度达到 200℃~220℃时,把氢气加到氮气中,控
制反应器入口温度在 200℃~220℃,分析变换炉入口氢气含量 10%(干基) 左右。
耐硫变换催化剂的升温及循环硫化方案
一、催化剂装填 装填催化剂前,应该认真检查反应器,保持清洁干净,支撑栅格正常 牢固。 在装填之前,通常没有必要对催化剂进行筛选,但是在运输及装卸过 程中,由于不正确地作业可能使催化剂损坏,若发现磨损或破碎则应过筛。 催化剂的装填无论采取从桶内直接倒入,还是使用溜槽或充填管都可以。 但无论采用哪一种装填方式,都必须保证催化剂自由下落高度不超过 1 米, 并且要分层装填,每层都要整平之后再装下一层,防止疏密不均,在装填 期间,如需要在催化剂上走动,为了避免直接踩在催化剂上,应垫上木板, 使身体重量分散在木板的面积上。 为了防止在装置开车或停车期间,由于快速导气或快速卸压时,可能 发生催化剂床层遭到损坏,可在催化剂床层顶部覆盖金属丝网或惰性材 料。惰性材料应不含硅,防止在高温、高水汽分压下释放出硅。
H2S 分析 1 次/ 半小时
四、硫化过程中不正常情况的处理 1、床层温升缓慢 配氢量或氮气量过高,入口温度控制较低,可通过增加开工加热器的
蒸汽量,提高变换炉入口温度来控制。 2、床层温度急剧上升 二硫化碳加入过快或入口温度调节过高都可能导致温度急剧上升。可
采取的措施为:降低变换炉入口温度;减少直到停止加入二硫化碳。
耐硫变换催化剂及其使用技术
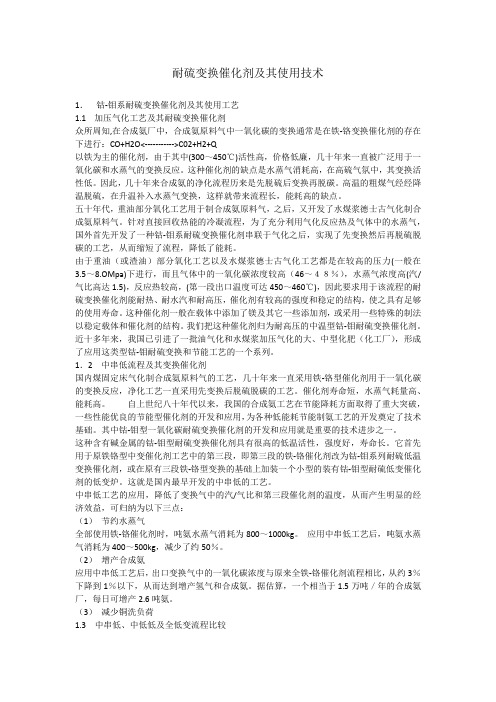
耐硫变换催化剂及其使用技术1.钴-钼系耐硫变换催化剂及其使用工艺1.1加压气化工艺及其耐硫变换催化剂众所周知,在合成氨厂中,合成氨原料气中一氧化碳的变换通常是在铁-铬变换催化剂的存在下进行:CO+H2O<----------->C02+H2+Q以铁为主的催化剂,由于其中(300~450℃)活性高,价格低廉,几十年来一直被广泛用于一氧化碳和水蒸气的变换反应。
这种催化剂的缺点是水蒸气消耗高,在高硫气氛中,其变换活性低。
因此,几十年来合成氨的净化流程历来是先脱硫后变换再脱碳。
高温的粗煤气经经降温脱硫,在升温补入水蒸气变换,这样就带来流程长,能耗高的缺点。
五十年代,重油部分氧化工艺用于制合成氨原料气,之后,又开发了水煤浆德士古气化制合成氨原料气。
针对直接回收热能的冷凝流程,为了充分利用气化反应热及气体中的水蒸气,国外首先开发了一种钴-钼系耐硫变换催化剂串联于气化之后,实现了先变换然后再脱硫脱碳的工艺,从而缩短了流程,降低了能耗。
由于重油(或渣油)部分氧化工艺以及水煤浆德士古气化工艺都是在较高的压力(一般在3.5~8.OMpa)下进行,而且气体中的一氧化碳浓度较高(46~48%),水蒸气浓度高(汽/气比高达1.5),反应热较高,(第一段出口温度可达450~460℃),因此要求用于该流程的耐硫变换催化剂能耐热、耐水汽和耐高压,催化剂有较高的强度和稳定的结构,使之具有足够的使用寿命。
这种催化剂一般在载体中添加了镁及其它一些添加剂,或采用一些特殊的制法以稳定载体和催化剂的结构。
我们把这种催化剂归为耐高压的中温型钴-钼耐硫变换催化剂。
近十多年来,我国已引进了一批油气化和水煤浆加压气化的大、中型化肥(化工厂),形成了应用这类型钴-钼耐硫变换和节能工艺的一个系列。
1.2中串低流程及其变换催化剂国内煤固定床气化制合成氨原料气的工艺,几十年来一直采用铁-铬型催化剂用于一氧化碳的变换反应,净化工艺一直采用先变换后脱硫脱碳的工艺。
耐硫变换催化剂的介绍

耐硫变换催化剂的介绍1. 耐硫变换催化剂的介绍耐硫变换催化剂(hydrodesulfurization catalyst)是一类用于石油加工中的重要催化剂,其主要功能是去除石油中的硫化物。
在石油炼制过程中,硫化物是一种常见的杂质,不仅对环境造成污染,还会对燃料的使用和储存带来很大的问题。
耐硫变换催化剂的研发和应用对于石油工业具有重要的意义。
2. 硫化物的危害和需求硫化物是一种存在于石油中的有害杂质,它不仅会对人类健康和环境造成危害,还会对燃料的使用带来不利影响。
硫化物是一种有毒物质,在燃烧过程中会产生硫气和硫氧化物,对空气质量和生态环境造成污染。
硫化物会影响石油产品的质量和性能,例如汽车尾气中的硫氧化物会导致汽车排放超标。
减少硫化物含量是石油工业中的一项重要任务。
3. 耐硫变换催化剂的原理耐硫变换催化剂的工作原理是通过催化剂的表面上存在的活性金属位点,将硫化物中的硫分解为硫氢化物,然后再将硫氢化物转化为无毒的硫化氢。
这样,就能实现对石油中硫的去除,从而达到净化石油的目的。
4. 耐硫变换催化剂的组成和结构耐硫变换催化剂的基本组成是载体和活性金属。
载体的选择是非常重要的,常见的载体材料包括氧化铝、硅铝酸酯和氧化钛等。
而活性金属主要是镍(Ni)、钼(Mo)、钴(Co)等。
载体和活性金属的选择会影响催化剂的催化性能和耐硫性能。
5. 催化剂的耐硫性能评价催化剂的耐硫性能直接影响催化剂的寿命和催化效率,因此对催化剂的耐硫性能进行评价是非常重要的。
常见的评价方法包括硫负荷量、硫损失率和活性金属的表面积等。
通过这些评价指标,可以评估催化剂在实际应用中的耐硫性能。
6. 耐硫变换催化剂的应用前景随着环保意识的提高和对能源质量的要求越来越高,耐硫变换催化剂在石油工业中的应用前景非常广阔。
不仅可以用于石油炼制中的脱硫处理,还可以应用于煤化工、化肥等领域。
随着石油资源的日益稀缺和世界能源结构的变化,对于耐硫变换催化剂的研发和应用将越来越重要。
低温变换催化剂升温硫化总结

低温变换催化剂升温硫化总结1、概述随着我国合成氨工艺的不断改进,低温变换催化剂的应用越来越广泛。
本公司变换装置采用的就是钴钼系低变耐硫变换催化剂。
由于耐硫变换催化剂的活性组分钴和钼是以氧化态的形式分散在多孔载体上,而催化剂活性相为硫化态,因此在使用前须进行硫化处理。
催化剂的硫化是耐硫变换催化剂应用的关键步骤,直接影响着催化剂的变换活性和稳定性,也将直接影响变换工段的生产负荷、合成气质量和蒸汽消耗等。
本文以变换四段催化剂升温硫化为例,对低变催化剂升温硫化过程进行总结。
2、工艺流程叙述在低变工艺中,因催化剂装填量较大,为减少放空量,本装置采用气体循环硫化法。
工艺气从变换炉四段出来后,经气气换热器与硫化风机出口的工艺气换热,将气体热量回收,进人变冷器降温至常温,进入3#分离器分离液态水,之后工艺气进入硫化风机,维持硫化风机入口处正压,由硫化风机将工艺气送至气气换热器,然后进入电炉加热,最后进入变换炉四段。
由于在硫化过程中要消耗氢,在硫化风机入口处连续加入少量新鲜煤气。
为防止惰性气体在循环气中积累,在3#分离器处设一放空管,连续放空少量循环气,使循环气中H2体积分数维持在25%以上。
CS2从电炉出口加入。
3、升温硫化原理及过程一、硫化原理催化剂中的活性成分是以氧化态形式存在,生产时,须将其转化为硫化态才能显示出催化剂的高活性。
为加速硫化过程,通常采用外加硫化剂(CS2)方法进行,其反应方程式为:CS2 + 4H2 ←→2H2S + CH4 —246KJ/mo (氢解反应)MoO3 +2H2S +H2←→MoS2 +3H2O —48.1 KJ/molCoO + H2S ←→ COS +H2O —13.4 KJ/mol这些反应都是放热反应,特别是CS2的的氢解是很剧烈的放热反应。
二、升温硫化的过程1、升温阶段:四段硫化阀进出口保持全开,加大循环气量和严格控制电炉出口温度,在较低的温度下脱除催化剂的物理水,当触媒下层温度还在120℃以下,必须控制电炉出口温度不得超过150℃;触媒下层温度到120℃后,恒温4小时,以防脱水过猛和未脱除干净而升温使催化剂结块,物理水全部脱除干净后再升温,将温度升到220℃,再恒温2小时。