品质检验表格不合格品报告单
不合格品控制程序(含表格)

不合格品的控制1.0目的对经检验和试验后因质量和不含有有害物质方面被判为不合格的产品进行有效的控制2.0适用范围适用于本公司在进料、制程及成品各阶段的物料或产品的质量和不含有有害物质方面经检验和试验后,判定为不合格时的处理和控制。
3.0职责3.1董事总经理3.1.1审阅及确认《进料不合格品评审报告》(质量和不含有有害物质方面)及对该进料作出的最终的处理方案。
3.1.2审阅及确认《制品不合格品评审报告》(质量和不含有有害物质方面)及以该制品不合格品作出的最终的处理方案。
3.3采购部3.3.1负责向供应商反映在进货检验中出现的因质量或不含有有害物质方面的不合格情况。
3.4生产部3.4.1主要是对制程中、成品及客户退货之不合格产品分区存放及对不合格品的最终处理方案的执行。
3.5品质部3.5.1负责对进货检验,过程中检验或最终检验时因物料或产品的质量和不含有有害物质方面出现不合格时,填写相应的不合格品评审报告,并作出初步评审。
3.5.2跟进货仓、采购对进料不合格品的处理结果及协助采购部跟进《供应商品质改善通知单》的回复。
3.5.3跟进生产部对生产制程中、成品及客户退回之不合格品的处理结果及相关不合格品评审报告的提交。
3.6货仓部3.6.1负责对进料不合格品的隔离存放,特别是当出现不含有有害物质方面不合格时,避免交叉污染.4.0培训所有负责进货检验及试验的品质部品管员,必须由有资格的员工担任,为使有关操作人员具有适当资格,有关部门须提供足够在职培训或聘请具有适当经验的测检人员,对于培训及培训记录的控制,可参考“QECOP6201人力资源管理程序”。
5.0运作程序5.1流程图(见6.0附图)5.2 进料不合格(质量和不含有有害物质方面)的控制:5.2.1进料检验员(IQC)负责对不合格进料以盖章和贴标签的方式进行标识,具体依“COP7503检验和试验状态管理程序”,并呈报上级主管决定处理方法。
5.2.2货仓部仓管员负责对不合格进料进行隔离、存放及协助供应商处理不合格进料。
部品、资材、成品检验管理规则(三级文件专用)
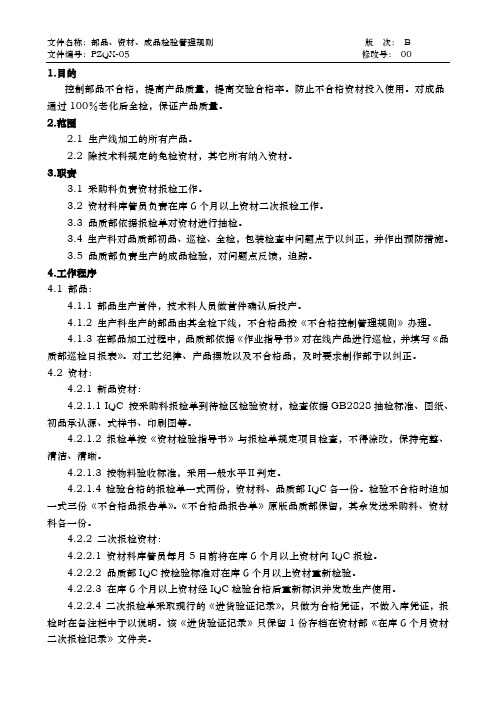
1.目的控制部品不合格,提高产品质量,提高交验合格率。
防止不合格资材投入使用。
对成品通过100%老化后全检,保证产品质量。
2.范围2.1 生产线加工的所有产品。
2.2 除技术科规定的免检资材,其它所有纳入资材。
3.职责3.1 采购科负责资材报检工作。
3.2 资材科库管员负责在库6个月以上资材二次报检工作。
3.3 品质部依据报检单对资材进行抽检。
3.4 生产科对品质部初品、巡检、全检,包装检查中问题点予以纠正,并作出预防措施。
3.5 品质部负责生产的成品检验,对问题点反馈,追踪。
4.工作程序4.1 部品:4.1.1 部品生产首件,技术科人员做首件确认后投产。
4.1.2 生产科生产的部品由其全检下线,不合格品按《不合格控制管理规则》办理。
4.1.3 在部品加工过程中,品质部依据《作业指导书》对在线产品进行巡检,并填写《品质部巡检日报表》。
对工艺纪律、产品摆放以及不合格品,及时要求制作部予以纠正。
4.2 资材:4.2.1 新品资材:4.2.1.1 IQC 按采购科报检单到待检区检验资材,检查依据GB2828抽检标准、图纸、初品承认源、式样书、印刷图等。
4.2.1.2 报检单按《资材检验指导书》与报检单规定项目检查,不得涂改,保持完整、清洁、清晰。
4.2.1.3 按物料验收标准,采用一般水平Ⅱ判定。
4.2.1.4 检验合格的报检单一式两份,资材科、品质部IQC各一份。
检验不合格时追加一式三份《不合格品报告单》。
《不合格品报告单》原版品质部保留,其余发送采购科、资材科各一份。
4.2.2 二次报检资材:4.2.2.1 资材科库管员每月5日前将在库6个月以上资材向IQC报检。
4.2.2.2 品质部IQC按检验标准对在库6个月以上资材重新检验。
4.2.2.3 在库6个月以上资材经IQC检验合格后重新标识并发放生产使用。
4.2.2.4 二次报检单采取现行的《进货验证记录》,只做为合格凭证,不做入库凭证,报检时在备注栏中予以说明。
产品检测不合格整改报告
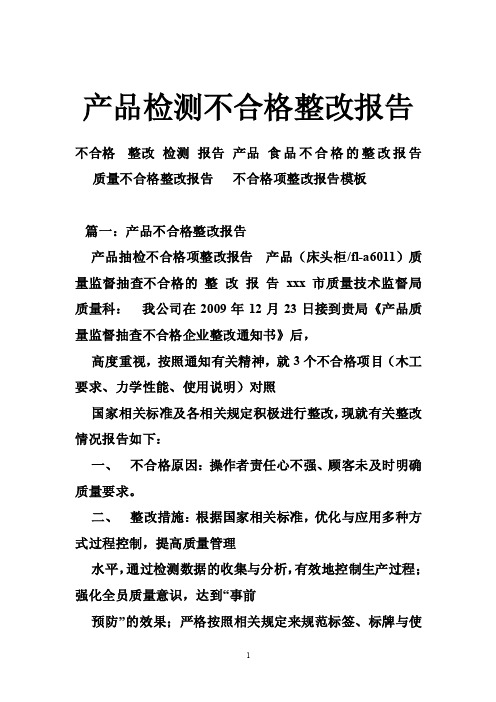
产品检测不合格整改报告不合格整改检测报告产品食品不合格的整改报告质量不合格整改报告不合格项整改报告模板篇一:产品不合格整改报告产品抽检不合格项整改报告产品(床头柜/fl-a6011)质量监督抽查不合格的整改报告xxx市质量技术监督局质量科:我公司在2009年12月23日接到贵局《产品质量监督抽查不合格企业整改通知书》后,高度重视,按照通知有关精神,就3个不合格项目(木工要求、力学性能、使用说明)对照国家相关标准及各相关规定积极进行整改,现就有关整改情况报告如下:一、不合格原因:操作者责任心不强、顾客未及时明确质量要求。
二、整改措施:根据国家相关标准,优化与应用多种方式过程控制,提高质量管理水平,通过检测数据的收集与分析,有效地控制生产过程;强化全员质量意识,达到“事前预防”的效果;严格按照相关规定来规范标签、标牌与使用说明。
三、落实时间:2010年01月23日前申请复查检验(送检)。
四、联系部门:生产管理部联系电话:0757-xxxxx 、xxxxx 传真:0757-xxxxx邮政编码:528300地址:xxxxxxx镇某某酒店家具有限公司呈报2009年12月22日篇二:不合格产品整改措施关于xxxxxxxx衣服不合格的整改措施尊敬的北京市消费者协会领导:首先xxx集团公司感谢北京市消费者协会本着以对消费者负责的工作理念开展商品比较试验,促进对我们商品质量的提高,使我们更好地为消费者提供高品质的羽绒制品。
本公司于2013年12月16日收到贵协会的通知后,得知xxx的q-1881款纤维含量指标不符合国家标准,xxx公司给予了高度重视,立即通知各门店对不合格商品进行了下架,返回厂家,召开中层质量管理人员会议,分析原因,查找不足,并按照协会的通知精神制定了整改措施:一、每批次商品在进入市场后先进行商品质量检测,对不合格商品决不投放市场。
二、加大服装面料自检的管理力度,调整并提升更高水平的业务管理人员进行商品质量把关。
产品不良分析报告表格

产品不良分析报告表格1. 引言该报告旨在对公司的产品不良情况进行分析并提供解决方案。
通过对不良产品的统计和分析,我们将揭示不良产生的原因,并提出相应的改进措施,以提高产品质量。
2. 数据搜集和分析为了获取产品不良的数据,我们对以下方面进行了调查和分析:2.1 不良产品的类型及数量我们对过去一个月的生产批次进行了不良产品的统计。
统计结果如下:产品类型不良数量A 50B 30C 20D 10总计110从上表可以看出,不良产品最多的是产品A,共有50个。
2.2 不良产品的产生原因通过对不良产品的分析和追溯,我们归纳了以下主要原因:•材料质量不合格:20%的不良产品是因为使用了不合格的材料。
•设计问题:30%的不良产品是由于产品设计存在缺陷导致。
•加工过程问题:40%的不良产品是由于生产过程中的操作失误或技术问题引起的。
•人员技术水平问题:10%的不良产品是由于操作人员技术水平不达标导致的。
2.3 不良产品的影响不良产品不仅会给公司带来经济损失,还会影响公司声誉和客户满意度。
具体影响如下:•经济损失:出现不良产品会造成材料和劳动力的浪费,增加公司成本。
•客户满意度下降:不良产品会影响客户使用体验,降低客户满意度。
•公司声誉受损:频繁出现不良产品会对公司品牌形象造成负面影响。
3. 改进方案针对以上不良产品产生的原因,我们提出了以下改进方案:3.1 材料质量管控•加强对供应商的材料质量审核和监督。
•加强对材料检验过程的把控,确保只使用符合质量标准的材料。
3.2 产品设计优化•设计部门应跟踪客户反馈和市场需求,及时修改产品设计,并通过有效的测试验证产品质量。
3.3 加强生产过程管控•加强对生产过程的监控,确保操作规范和操作人员技术水平达标。
•实施严格的生产工艺流程,避免操作失误和技术问题。
3.4 培训和技术提升•加强对操作人员的培训和技术提升,提高其技术水平和质量意识。
4. 结论通过对产品不良情况的分析,我们发现不良产品主要是由于材料质量、设计问题、加工过程和人员技术水平等多方面原因导致的。
进料检验流程图及表格

1、进料检验流程图
1.1进料检验通知单(送检单)
被通知部门:________________ 通知单编号:______________
仓储部主管:______________ 收料仓管专员:______________ 1.2进料检验记录表
1.3进料检验报告表
编号:日期:
限,则判定物料验收结果为“合格”;若检验物料的不合格数量达到或超过企业规定的数量,则判定物料验收结果为“不合格”
进厂零件质量检验表
零件编号:零件名称:号码:
检验主管:检验员:检验日期:年月日进厂零件检验报告表
编号:填写日期:年月日
进厂材料试用检验表
编号:填写日期:
进料检验质量异常处理报告
编号:____________ 填表日期:______________
进料检验日统计表
原材料供应商质量检测表
供应商名称:编号:
外协厂商质量检查表
填写日期:年月日
检验主管:检验人员:
十二、供应商不合格品记录表
年度:月份:编号:
十三、供应商物料拒收月统计表
月份:日期:
主管:制表:
十四、供应商质量评价体系表
十五、供应商综合评价表
编号:填写日期:
岗位职责
1、进料检验主管
2、进料检验专员。
不合格和纠正措施程序(含表格)

不合格和纠正措施管理程序(ISO9001-2015)1.目的:确保不合格发生后能及时调查原因,采取有效纠正措施,防止再发生同样的问题。
2.范围:本公司所采取的纠正措施及改善统计技术的运用。
3.权责:当以下情况发生时按下表执行纠正措施:4.定义:(无)5.作业流程5.1.1以上质量异常发生时,应由以上表中规定的部门填写适合表单送相关部门。
5.1.2供方的纠正措施:若供方来料不良,则由IQC填写《进料异常通知单》,采购部联络供方,由其分析原因并完成纠正措施;品质部应予以跟踪、确认。
5.1.3 本厂内部的纠正措施:a)本厂内部制程出现严重不良/不良连续发生或成品抽检不合格时,,由品质部开出《巡回检查异常联络书》或《品质异常处理单》交责任部门分析原因并采取纠正措施,品质部应予以跟踪、确认。
b)当质量/环境目标或环境绩效出现不符合时,管理部发出《纠正措施报告》,并由管理部进行跟踪确认直至问题改善。
c)内审发现不符合项依《内部审核控制程序》执行。
d)管理评审决议事项依《管理评审控制程序》执行。
e)客户满意度测量发现客户不满意时依《客户满意度测量控制程序》执行。
5.1.4客户投诉、退货之纠正状况:a)客户投诉/退货之纠正,由品质部负责组织相关部门填写《客户投诉处理单》,相关责任部门采取纠正措施直至问题改善,待品质部验证合格后将完成情况回复客户以取得客户满意。
具体参照《客户投诉控制程序》执行。
5.1.7 改善效果与确认:a)由(表一)所列权责部门依责任部门拟订措施及预估完成日期追踪。
b)若未改善,应要求重新分析原因及拟订对策,直到完全纠正。
5.1.5需要时,更新策划期间确定的风险和机遇,具体参见《风险管理程序》。
5.1.6如有必要,经确认有效的纠正措施应修订于相关的体系文件之中,具体的修订作业遵照《文件控制程序》执行。
5.1.7品质部或管理部应将所有纠正措施汇总登记在《纠正措施一览表》。
纠正措施实施情况应提交管理评审会议予以效果检讨、确认其合理性与有效性。
HSF不合格品管理程序(含表格)

HSF不合格品管理程序(QC080000-2017/ISO9001-2015)1.0目的为了在发现原材料、半成品、成品执行过程中不能满足或达不到规定(质量、有害物质)要求时,及时采取纠正与预防措施,以确保公司之产品质量。
2.0范围:公司进料产品,制程半成品﹑成品﹑库存品﹑客供品﹑客退品及生产过程中使用的设备﹑模具﹑检治具﹑副资材(含清洗线的槽液)等日常运作过程中所发生的相关问题。
3.0职责:3.1采购部:负责对不合格来料处理。
3.2品保部:负责对供货商来料、客供品、厂内半成品和成品之不合格品及客户退货品进行检验评审,并提出不合格品的处置建议。
3.3制造部:负责对不合格品进行处置。
3.4各部门:维护系统的正常运作。
4.0定义:4.1重工:指不合格品按规格要求重新加工。
4.2筛选:指不合格品100%的检查。
4.3修理:指不合格品缺点清除。
4.4特采:原物料、成品、经检验不符合标准,但急需使用该项原物料或成品时,在不影响产品使用功能或特性的前提下,而提出的特别采用。
4.5有害物质异常:相关测试资料(《有害物质测试报告》、《MSDS》)、《材质成份表》或实际检测数据表明有害物质含量超过《有害物质控制程序》最新版本的允收标准时。
4.6不合格品:即原材料、半成品、成品不能满足或达不到客户规定(质量、有害物质)的要求。
5.0程序5.1不合格品的发现5.1.1进料发现品质异常,立即将不合格品隔离处理并开立《不合格品处理单》,若为HSF不合格品,需隔离放置于HSF不合格品区,贴HSF不合格标签(见附件标签),呈报环境管理代表批示处理,并记录好相关不合格批之追溯记录。
IQC人员提出《纠正预防措施单》给厂商改善,厂商须在3天内回复书面报告,IQC人员负责对改善后产品前三批进行追踪确认,若无异常方可结案。
5.1.2制程中发现产品品质异常,立即隔离处理并开立《不合格品处理单》,若为HSF不合格品,需隔离放置于HSF不合格品区,贴HSF不合格标签,呈报环境管理代表批示处理,并记录好相关不合格批之追溯记录。
IATF16949体系审核检查表-品质部

7.事态升级程序 8.统计1 技术应用及 数据分析程序
5.3 6.1 6.2 8.6 8.7 9.1.1 9.1.3 10.2
1、过程中员工自检,合格放行; 2、客户退货率≤0.1%,已经达标,产品检 验满足要求 ; 3、此过程的风险“1.量具损坏; 2.受控发放使用图纸不清晰; 3.受控资料相互之间矛盾; 4.未按要求记录; 5.标签贴错; 6.不合格品的非正常使用; 7.检验员对检验标准,检验技能,仪器使 用不熟悉,导致流出不合格品
被审核的过程名称
输入(I)/输出(O)
输入:
1.待检原料、半成品、成品; 2.送货单; 3.生产计划; 4.产品规范; 5.检验和试验规范; 6.接收准则; 7.原材料/外发加工产品 8.不合格品; 9.退货品; 10.内外部产品不合格信息
输出:
S6 产品检验与 不合格品 管理过程
CCL
1.合格产品; 2.不良品处理结果; 3.合格/不合格标签; 4.来料检验报告; 5.过程巡检记录表 6.首件检验记录表 7.出货检验报告; 8.品质异常联络单; 9.物料报废申请单。 10.有明确标识的物品; 11.检验和试验记录;
8.由于标识或者抽样问题导致漏检 9.检验之后,由于搬运、储存方式不合 理,导致产品损坏,成为不合格品。
合格
管理过程
9.物料报废申请单。
10.有明确标识的物品; 被审核的CC过L 程名称 11.检验和试输验入记(录I);/输出(O)
1.客户投诉率≤1.2% 2.客户退货率≤0.1%
过程绩效指标
12.不合格品处理记录/通知; 13.纠正和预防措施记录; 14.相关流程更改要求
2.纠正与预防措施关闭 率100%
3.供应商异常处理单;