各种人造板的制造过程都包括下述5个主要工艺
板材的生产工艺
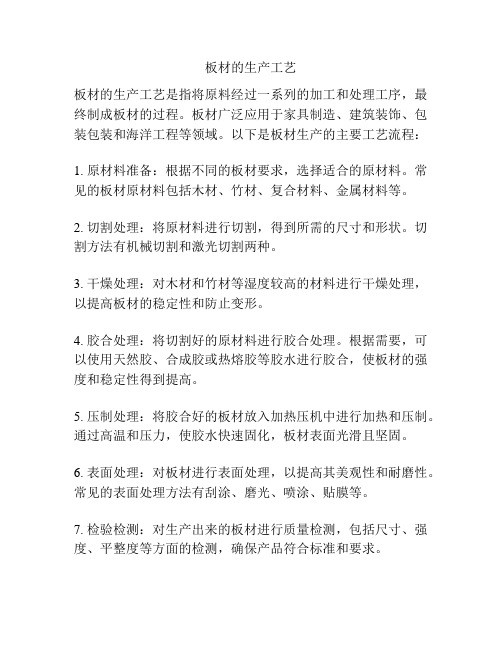
板材的生产工艺
板材的生产工艺是指将原料经过一系列的加工和处理工序,最终制成板材的过程。
板材广泛应用于家具制造、建筑装饰、包装包装和海洋工程等领域。
以下是板材生产的主要工艺流程:
1. 原材料准备:根据不同的板材要求,选择适合的原材料。
常见的板材原材料包括木材、竹材、复合材料、金属材料等。
2. 切割处理:将原材料进行切割,得到所需的尺寸和形状。
切割方法有机械切割和激光切割两种。
3. 干燥处理:对木材和竹材等湿度较高的材料进行干燥处理,以提高板材的稳定性和防止变形。
4. 胶合处理:将切割好的原材料进行胶合处理。
根据需要,可以使用天然胶、合成胶或热熔胶等胶水进行胶合,使板材的强度和稳定性得到提高。
5. 压制处理:将胶合好的板材放入加热压机中进行加热和压制。
通过高温和压力,使胶水快速固化,板材表面光滑且坚固。
6. 表面处理:对板材进行表面处理,以提高其美观性和耐磨性。
常见的表面处理方法有刮涂、磨光、喷涂、贴膜等。
7. 检验检测:对生产出来的板材进行质量检测,包括尺寸、强度、平整度等方面的检测,确保产品符合标准和要求。
8. 包装包装:将合格的板材进行包装和打包,以便运输和销售。
以上是板材的基本生产工艺流程,不同类型的板材可能还会有其他特殊的加工工艺步骤。
板材生产工艺的不断改进和创新,可以提高板材的质量和性能,满足不同领域的需求。
同时,合理使用原材料、减少能源消耗和环境污染也是板材生产工艺中应考虑的重要因素。
板材的工艺流程是什么

板材的工艺流程是什么在建筑、家具、制作等各个领域中,板材被广泛应用。
无论是常见的胶合板、颗粒板,还是复合板、硬质板材等,都需要经过一系列的工艺流程才能生产出最终的产品。
本文将介绍板材的常见工艺流程。
板材的预处理在制作板材之前,原料需要进行预处理。
预处理的目的是清除原料中的杂质,提高板材的质量和耐用性。
1. 木材的预处理木材是制作板材最常用的原材料之一。
在木材预处理中,通常包括以下几个步骤:a. 原料采购原材料采购是木材预处理的第一步。
在采购木材时,需要选择优质的木材,并检查木材的湿度和杂质情况。
b. 去皮和修整去皮是指将原木表面的树皮去除,以免树皮影响后续工艺流程。
修整是将原木两端的不平整部分切割去除,使原木的两端平整。
c. 切割和锯齿处理原木需要根据所需板材的规格进行切割,常见的切割方法包括横切和纵切。
锯齿处理是在切割过程中,使用锯齿将木材切成所需厚度的板材。
2. 其他原料的预处理除了木材之外,制作板材的原料还包括胶水、颗粒等。
这些原料通常需要进行除尘、筛选等预处理过程,以保证原料的纯净度。
板材的制作工艺经过预处理的原料将进入板材制作工艺流程。
板材的制作工艺多样,下面将介绍常见的几种制作工艺。
1. 胶合板的制作工艺胶合板是使用胶水将多层木材热压在一起制成的板材。
其制作工艺包括以下几个步骤:a. 原料贴合将经过预处理的木材按照一定规格和厚度贴合在一起,形成多层结构。
b. 胶合处理将胶水均匀涂在木材层之间,以保证木材之间的粘合度。
c. 热压处理将胶合前的木材放入胶合机中,并施加一定的温度和压力,使胶水充分固化,确保板材的强度和稳定性。
2. 颗粒板的制作工艺颗粒板是将木屑、秸秆等颗粒状原料添加胶水后,进行热压制成的板材。
其制作工艺包括以下几个步骤:a. 原料混合将经过预处理的颗粒原料与胶水进行混合,以保证颗粒均匀分布。
b. 颗粒板成型将混合好的原料放入颗粒板成型机中,通过热压使颗粒固化成板状。
c. 硬化处理颗粒板经过热压后,需要进行硬化处理,以增加板材的硬度和耐久性。
板材工艺流程

板材工艺流程板材工艺流程是指将木材加工成板材的全过程,包括选材、修整、切割、干燥、拼接、压制等各个环节。
下面将详细介绍板材工艺流程的七个步骤。
第一步:选材。
首先需要选择优质的木材作为原材料。
选择木材时需要注意木材的品种、质量及尺寸。
优质的原材料是制作出高质量板材的基础。
第二步:修整。
选材后,需要将木材进行修整,即将木材的表面修平。
修整的目的是为了使木材紧密贴合并且表面平整,以便后续的切割和拼接工艺。
第三步:切割。
修整后的木材需要进行切割,根据生产需求将其切成适当的尺寸,以便后续工艺加工。
切割可以手动进行,也可以使用机械设备进行。
第四步:干燥。
切割后的木材含有大量的水分,需要通过干燥工艺将其水分含量降低到合适的水平。
木材的干燥是一个非常重要的环节,如果木材干燥不充分或者过度干燥都会对板材的品质产生影响。
第五步:拼接。
干燥后的木材需要进行拼接,也就是将多块木材拼接在一起形成大块的板材。
拼接可以使用多种方法,如刮切、折半、接缝等。
拼接工艺的好坏决定了板材的强度和整体质量。
第六步:压制。
拼接成型后的板材需要进行压制,将其加热并用压力使各个木材块紧密贴合在一起。
压制是将板材制成所需厚度和形状的关键环节。
第七步:表面处理。
板材制作完成后,还需要进行表面处理。
表面处理包括修整、砂光、涂漆等。
这些步骤可以使板材表面更加光滑、美观,并起到保护作用。
以上是板材工艺流程的七个步骤,每个步骤都十分重要。
只有严格按照每个步骤进行操作,才能制作出高质量的板材。
板材工艺流程是一个复杂而精细的过程,需要经验丰富的技术员工才能进行操作。
同时,科学合理的工艺流程能够提高产量和质量,降低生产成本,是木材加工产业发展的重要保障。
人造板各类贴面工艺详解!(转载)

人造板各类贴面工艺详解!(转载)2021-07-17贴面装饰是板式家具生产中非常重要的,它具有遮盖材面的缺陷,改善基材的物理性质等作用。
下面让我们通过对薄木贴面、PVC贴面,以及装饰纸贴面的详细介绍来了解下人造板整容术——贴面吧!一、薄木贴面薄木贴面是板式部件最重要的装饰方法,是将薄木(素面或各类拼花)胶贴到各类基材(人造板、实木镶边板、实木拼板等)表面的一种技术。
1.贴面前后的砂光处理面前的定厚砂光,经厚度校正后的板料通常要求同一批板料厚度差应控制在0.2mm以内,且板料表面无明显的砂痕及波浪纹,用手摸或粉笔画无明显的表面不平现象,但板料厚度与公称厚度允许有一定的偏差,通常控制在士0.5mm即可。
贴面后的表面砂光,表面砂光的常用是宽带砂光机,通常为三砂架,且采用硬度较低的橡胶砂光轮或气囊式砂光垫作为砂光头,并安装150~240号的细砂纸带。
表面砂光一次性砂光量应控制在0.1~0.2mm之间,将表面水胶纸砂掉80%~90% 即可。
对于有少许弯曲的板件,应该减少砂光量,以最大砂光量处不被砂破为宜;弯翘较严重的板件不能用宽带砂光机作业,通常采用窄带式手压砂光机。
2.薄木热压贴面技术薄木贴面通常采用热压贴面工艺,热压贴面工艺包括板料涂胶、组坯和热压等具体工序。
3.基材涂胶技术常见的有双面涂胶机、单面涂胶机及手动涂胶机,其中最常用的为双面涂胶机。
胶水采用脲醛树脂胶( UF)或聚醋酸乙烯酯乳液(PVAc,俗称白乳胶)。
其中UF因黏结强度高,操作性好,固化速度快(2分钟以内)、价格便宜,是目前使用最为广泛的胶水。
近年来因环保的要求,热压贴面用改良 PVAc 的越来越多。
4.组坯技术热压贴面技术组坯:利用快速固化胶水热压贴面加工时,涂胶后直接把薄木覆贴到板面上即可送入热压机进行压合处理。
贴面薄木规格通常应较基材大10mm左右。
冷压贴面技术组坯:在板料涂胶组坯后,通常还要求有一段时间的陈放时间再上压机,使胶水与薄木充分接触润湿,提高贴面品质。
人造板材制造工艺
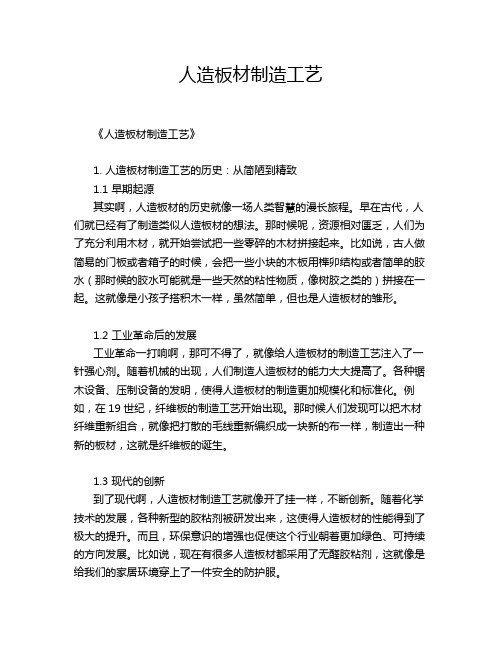
人造板材制造工艺《人造板材制造工艺》1. 人造板材制造工艺的历史:从简陋到精致1.1 早期起源其实啊,人造板材的历史就像一场人类智慧的漫长旅程。
早在古代,人们就已经有了制造类似人造板材的想法。
那时候呢,资源相对匮乏,人们为了充分利用木材,就开始尝试把一些零碎的木材拼接起来。
比如说,古人做简易的门板或者箱子的时候,会把一些小块的木板用榫卯结构或者简单的胶水(那时候的胶水可能就是一些天然的粘性物质,像树胶之类的)拼接在一起。
这就像是小孩子搭积木一样,虽然简单,但也是人造板材的雏形。
1.2 工业革命后的发展工业革命一打响啊,那可不得了,就像给人造板材的制造工艺注入了一针强心剂。
随着机械的出现,人们制造人造板材的能力大大提高了。
各种锯木设备、压制设备的发明,使得人造板材的制造更加规模化和标准化。
例如,在19世纪,纤维板的制造工艺开始出现。
那时候人们发现可以把木材纤维重新组合,就像把打散的毛线重新编织成一块新的布一样,制造出一种新的板材,这就是纤维板的诞生。
1.3 现代的创新到了现代啊,人造板材制造工艺就像开了挂一样,不断创新。
随着化学技术的发展,各种新型的胶粘剂被研发出来,这使得人造板材的性能得到了极大的提升。
而且,环保意识的增强也促使这个行业朝着更加绿色、可持续的方向发展。
比如说,现在有很多人造板材都采用了无醛胶粘剂,这就像是给我们的家居环境穿上了一件安全的防护服。
2. 人造板材的制作过程:从原料到成品的奇妙变身2.1 原料准备制作人造板材的原料那可真是多种多样,就像做一道大餐需要各种食材一样。
主要的原料当然是木材啦,不过这里的木材可不光是整根的大树,还包括很多木材加工后的剩余物,像木屑、木片之类的。
就好比我们吃西瓜,不光吃西瓜瓤,西瓜皮也能加工利用起来。
除了木材,还有胶粘剂、添加剂等辅料。
这些辅料就像是做菜时加的调料,虽然量不多,但是对最终的“口味”(也就是板材的性能)有着很重要的影响。
2.2 不同类型板材的制作2.2.1 胶合板胶合板的制作就像是做千层饼一样。
人造板工艺流程

人造板工艺流程人造板是一种由天然木材或其他植物纤维材料制成的人工板材。
它具有均匀的纹理、平整的表面和较高的稳定性,广泛应用于家具制造、建筑装饰、包装箱等领域。
下面将介绍一下人造板的工艺流程。
首先,原材料准备。
需要根据不同的需求选择不同的原材料,如杨木、松木、胶合板、刨花板等。
原材料需要经过切割、去皮、去杂质等处理,确保原料的质量。
接下来是材料的蒸煮和浸泡。
将原材料放入大锅中进行蒸煮,以软化木材纤维。
然后,将木材纤维放入浸渍槽中进行浸泡,以去除木材中的杂质。
然后是纤维的分解和磨制。
将浸泡后的木材纤维放入分解机中进行分解。
分解后的纤维经过一系列的磨制和筛分,使其粒度均匀,以确保板材的质量。
接下来是纤维的粘合。
将经过磨制的纤维放入筒式混合机中,加入适量的胶粘剂,进行充分混合。
然后将混合好的纤维和胶粘剂放入造板机的模具中,经过高温高压的作用,使纤维与胶粘剂充分结合。
然后是板材的成型和修整。
将制成的原始板材放入热压机中进行热压,使其形成初始形状。
然后,将初始形状的板材经过修整机修整,使其尺寸和表面的平整度达到要求。
接下来是板材的烘干和修边。
成型后的板材还含有大量的水分,需要进行烘干处理,以提高板材的稳定性。
然后,对板材进行修边,使其四边平整,去除毛刺和凹凸。
最后是板材的表面处理和包装。
将修整好的板材放入涂装机中,进行表面处理,如上漆、贴膜等。
最后,对板材进行检验,对合格的板材进行包装,以供销售和运输。
以上就是人造板的工艺流程。
人造板工艺流程相对简单,但其中涉及到的工艺环节决定了板材的质量。
不同的原材料和工艺参数的选择,会产生不同的板材品质,因此在生产过程中需要严格控制每个环节,确保制成的人造板达到客户的要求。
同时,也需要注意环保问题,选择低甲醛或无甲醛的胶粘剂,以减少对人体和环境的危害。
人造板工艺

原料
↓
削片
↓
刨花贮存
↓
刨花干燥
↓
废料分仓←刨花分选→过大刨花再碎
↓←┘└→↓
粗刨花贮存调胶细刨花贮存
↓↓↓
粗刨花计量←计算胶量→细刨花计量
└→↓←┘
↓
将拌胶的刨花混合
↓
铺装→预压→热压→冷却→锯边→堆放→
分等入库
原木→横截→木段→木段水热处理→木段剥皮→木段定心
→上木→旋切→单板干燥→干单板剪切分选→单板修补胶拼
→芯板涂胶→陈化→组坯→预压→热压→合板冷却→齐边
→砂光或刮光→检验分等→成品.
干法中密度纤维板的工艺流程:
原料→纤维分离→纤维干燥→纤维拌胶→定向铺装→预压→热压→冷却→锯边→检验→入库堆放
薄木贴面工艺
干贴:
薄木制造→干燥→组坯→热压→堆放→刮边→砂光→涂面漆
基材整理→涂胶
湿贴:(薄木W=60%~80%薄木不易碎,易透胶,不脱胶,薄木干缩易留裂缝)
薄木制造→堆放→组坯→热压→堆放→刮边→砂光→涂面漆
基材整理→涂胶。
人造板生产工艺操作规程
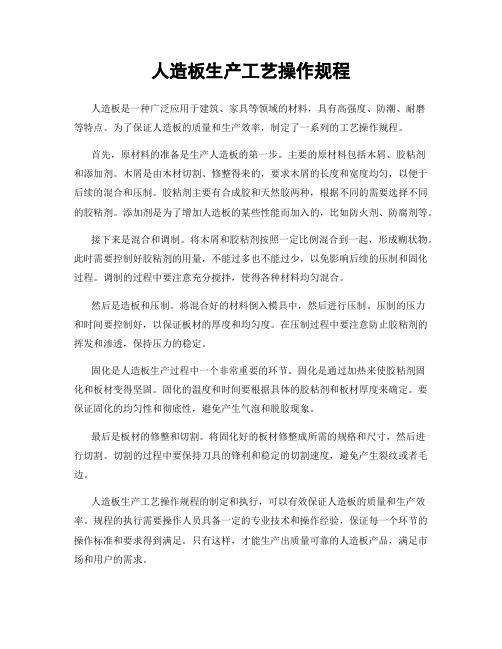
人造板生产工艺操作规程人造板是一种广泛应用于建筑、家具等领域的材料,具有高强度、防潮、耐磨等特点。
为了保证人造板的质量和生产效率,制定了一系列的工艺操作规程。
首先,原材料的准备是生产人造板的第一步。
主要的原材料包括木屑、胶粘剂和添加剂。
木屑是由木材切割、修整得来的,要求木屑的长度和宽度均匀,以便于后续的混合和压制。
胶粘剂主要有合成胶和天然胶两种,根据不同的需要选择不同的胶粘剂。
添加剂是为了增加人造板的某些性能而加入的,比如防火剂、防腐剂等。
接下来是混合和调制。
将木屑和胶粘剂按照一定比例混合到一起,形成糊状物。
此时需要控制好胶粘剂的用量,不能过多也不能过少,以免影响后续的压制和固化过程。
调制的过程中要注意充分搅拌,使得各种材料均匀混合。
然后是造板和压制。
将混合好的材料倒入模具中,然后进行压制。
压制的压力和时间要控制好,以保证板材的厚度和均匀度。
在压制过程中要注意防止胶粘剂的挥发和渗透,保持压力的稳定。
固化是人造板生产过程中一个非常重要的环节。
固化是通过加热来使胶粘剂固化和板材变得坚固。
固化的温度和时间要根据具体的胶粘剂和板材厚度来确定。
要保证固化的均匀性和彻底性,避免产生气泡和脱胶现象。
最后是板材的修整和切割。
将固化好的板材修整成所需的规格和尺寸,然后进行切割。
切割的过程中要保持刀具的锋利和稳定的切割速度,避免产生裂纹或者毛边。
人造板生产工艺操作规程的制定和执行,可以有效保证人造板的质量和生产效率。
规程的执行需要操作人员具备一定的专业技术和操作经验,保证每一个环节的操作标准和要求得到满足。
只有这样,才能生产出质量可靠的人造板产品,满足市场和用户的需求。
- 1、下载文档前请自行甄别文档内容的完整性,平台不提供额外的编辑、内容补充、找答案等附加服务。
- 2、"仅部分预览"的文档,不可在线预览部分如存在完整性等问题,可反馈申请退款(可完整预览的文档不适用该条件!)。
- 3、如文档侵犯您的权益,请联系客服反馈,我们会尽快为您处理(人工客服工作时间:9:00-18:30)。
各种人造板的制造过程都包括下述5个主要工艺。
切削加工 原材料处理和产品最终加工,都要应用切削工艺,如单板的旋切、刨切,
木片、刨花的切削,纤维的研磨分离,以及最终加工中的锯截、砂磨等。将木材切削
成不同形状的单元,按一定方式重新组合为各种板材,可以改善木材的某些性质,如
各向异性、不均质性、湿胀及干缩性等。大单元组成的板材力学强度较高,小单元组
成的板材均质性较好。精确控制旋切单板的厚度误差,可提高出材率2~3%。切削
出的刨花形态影响刨花板的全部物理力学性能;纤维形态对纤维板的强度同样有密切
关系。板材最终的锯切、磨削等也影响产品的规格质量。
干燥 包括单板干燥、刨花干燥、干法纤维板工艺中的纤维干燥,及湿法纤维板
的热处理。干燥的工艺和过程控制与成材干燥有所不同。成材干燥的过程控制是以干
燥介质的相对湿度为准,必须注意防止干燥应力的产生;而人造板所用片状、粒状材
料的干燥则是在相对高温、高速和连续化条件下进行的,加热阶段终了立即转入减速
干燥阶段。单板及刨花等材料薄,表面积大,干燥应力的影响甚小或者不存在。加之在
切削过程中木材组织发生不同程度的松弛,水分扩散阻力小,木材内部水分扩散规律
对单板、刨花等就失去意义。
干燥的热源,大都是用蒸气或燃烧气体。红外线干燥能量消耗太大,每蒸发1千
克水需要5500~18000千焦;而蒸气干燥仅需4200~5000千焦。高频干燥优点是
被干物料含水率高时的干燥速度快、终含水率均匀,但干燥成本过高。若与蒸气联合
使用实现复式加热则有利的。真空干燥不仅费用大,生产效率也低。当以蒸气为热源
时,每蒸发1千克水分,单板干燥需1.75~2千克蒸气,刨花干燥需1.8千克左右的蒸
气,软质纤维板坯干燥需1.6~1.8千克蒸气。
施胶 包括单板涂胶、刨花及纤维施胶。单板涂胶在欧洲仍沿用传统的滚筒涂胶,
美国自70年代起许多胶合板厂已改用淋胶。中国胶合板厂也用滚筒涂胶。淋胶方法
适宜于整张化中板和自动化组坯的工艺过程。刨花及纤维施胶现在主要用喷胶方法。
70年代末期,欧美一些国家研究无胶胶合技术,较有进展的是使木质素分子活
化,在一定条件下利用木质素胶合;或者利用木材或其他材料中的半纤维素,经处理
使之转化为胶结物质进行胶合。80年代初,加拿大成功地利用蒸渣制成了无胶刨花
板。中国林业科学研究院和东北林业大学也都在进行无胶胶合技术的研究,已取得初
步成果。
成型和加压 胶合板的组坯,刨花板纤维板的板坯成型和加压都属于人造板制造
的成型工艺。木材学对木材构造的研究揭示了木纤维在天然木材中的排列方式有层次
性和方向性,因而能承受自然界对木材所施加的一定限度的外力。人造板制造工艺的
演变,无疑受到这一认识的影响:刨花板、纤维板板坯层次由单层改变为3层及多层
结构;板坯中刨花及纤维的排列也由随机型趋向于定向型;而胶合板的相邻层纤维方
向互相垂直排列则改善了木材在自然生长条件下形成的各向异性缺点,提高了尺寸稳
定性。
加压分预压及热压。使用无垫板系统时必需使板坯经过预压。它使板坯在推进热
压机时不致损坏。热压工序是决定企业生产能力和产量的关键工序,人造板工业中常
用的热压设备主要是多层热压机,此外,单层大幅面热压机和连续热压机也逐渐被采
用。刨花板工厂多用单层热压机,中密度纤维板制造中使用单层压机就可以实现高频
和蒸气联合使用的复式加热,有利于缩短加压周期和改善产品断面密度的均匀性。
最终加工 板材从热压机卸出后,经过冷却和含水率平衡阶段,即进行锯边、砂
光,硬质纤维板需经热处理及调湿处理。过去板材锯边都是冷态锯切,现在也用热态
锯切法,但决不能采用热态砂光方法,热砂会损坏成品表面质量。根据使用要求,有
些板材还需进行浸渍、油漆、复面、封边等特殊处理。
分类 人造板的新品种日益增多,其分类方法也随之不断变化。常用的分类方法
有下述几种:①按所用树种分针叶材胶合板、阔叶材胶合板等;②按用途性质分室外
用胶合板、室内用胶合板、结构用胶合板、装饰用胶合板等;③按成型工艺分湿法、
干法、半干法纤维板;④按加压方式分平压、挤压、辊压刨花板等;⑤按产品密度分,
有低密度、中密度、高密度刨花板;软质、中密度、高密度(硬质)纤维板等;⑥按
胶合材料分,有有机胶合人造板、无机胶合人造板等。
由于各种人造板之间互相渗透,加上复合板的出现,分类概念逐渐模糊,各种板
材之间的界限也将逐渐打破。
趋势 新一代的人造板,其组成单元和结构方式将会按特定的要求经过预先设计
制成,产品设计概念将进入人造板工业,复合结构和定向结构尤将经过产品设计。这
将在更大程度上提高木质材料的利用率并扩大其用途范围。
人造板工业所用的材料,也将由单一型向复合型发展。此时人造板在数量上和品
种上定会急剧增长。现在人造板所用的木质材料可按其形状从单板直到最小的木纤维
分成14种。如果人造板板坯结构由单一型改变为二元型和三元型(即用2或3种不
同形状的木质材料组成板坯),则14种形状的材料可制出上千种产品。而当前国际
市场上的人造板品种仅有64种,中国包括正在试产的品种在内仅18种。已有的产品
大都系单一结构。这说明人造板开发的潜力还很大,如果再进一步发展木质材料与金
属、塑料、非金属矿物等组成的复合结构,则人造板工业的前景将更为广阔。