硬质合金发展简史
《硬质合金-》课件

硬质合金,也称为钨钢,是一种高硬度、高耐磨损的材料,广泛应用于切削 工具、矿山机械、石油钻采工具等领域。
介绍硬质合金的概念和发展历史
1 概念定义和特点
硬质合金是由金属硬质相和结合相组成的复 合材料,具有优异的硬度、耐磨性和耐腐蚀 性。
2 发展历史回顾
硬质合金的历史可以追溯到20世纪初,经过 多年的研发和改进,如今已成为重要的工程 材料。
硬质合金具有优异的硬度、耐磨性、耐腐蚀 性和热稳定性,适用于各种恶劣的工作环境。
硬质合金在高温和高压条件下仍能保持较好 的硬度和强度,适用于高速切削和重载工况。
硬质合金的应用领域和案例分析
制造行业中的应用
硬质合金广泛应用于切削工具、模具、矿山机 械等领域,提高生产效率和降低成本。
典型应用案例分析
以切削工具为例,硬质合金刀具在加工高硬度 材料和复杂形状零件时表现出色,提供了更高 的精度和寿命。
硬质合金的发展趋势和展望
1
未来发展方向
将更多先进材料和制造技术应用于硬质合金,提高硬质合金的性能和适用范围。
2
对未来的展望和分析
硬质合金在工程领域有着广阔的应用前景,随着各行业的需求增加,硬质合金的 市场潜力巨大。
总结与展望
通过本次PPT课件的学习,我们对于硬质合金的概念、组成、性能和应用有了 更深入的了解。在未来,硬质合金将持续发展,为各行业带来更多创新和突 破。
硬质合金的组成和制备式
1 主要成分介绍
硬质合金的主要成分是金属硬质相(钨碳化 物)和结合相(钴、镍等),不同成分比例 会影响其性能。
2 常见制备方式
硬质合金的制备方式包括粉末冶金、溶液法、 化学气相沉积等,每种方式都有其适用的场 景和优劣势。
硬质合金的发展及现状现代工程材料

硬质合金的发展及现状现代工程材料硬质合金,也被称为金属陶瓷材料或硬质质体材料,是一种由金属粉末与其他化学元素进行混合和烧结而成的高性能材料。
它的硬度和耐磨性通常比传统的金属材料高得多。
因此,硬质合金在现代工程中得到广泛应用。
硬质合金的发展可以追溯到19世纪末和20世纪初。
当时,工程师和科学家们开始研究不同金属粉末及其合金化的方法,以提高材料的硬度和耐磨性。
他们发现,通过在钨钢中加入钴等金属粉末,可以显著提高材料的硬度。
这一发现奠定了硬质合金的基础。
随着科学技术的进步和材料工艺的发展,硬质合金逐渐得到改进和优化。
在20世纪50年代,高压烧结技术被引入到硬质合金的制造中,这使得硬质合金的硬度和耐磨性得到了进一步提高。
随后,相继出现了化学性能均匀、晶粒细化、添加钛等新技术,进一步改进了硬质合金的性能。
目前,硬质合金已经成为许多行业的重要工程材料。
它被广泛用于切削工具、矿山工具、铣刀、钻头、锯片和零件等领域。
硬质合金的高硬度和耐磨性使得它能够在高速切削和重负荷工况下保持较长的使用寿命,提高生产效率和降低成本。
此外,硬质合金还被应用于汽车工业、航空航天领域和石油钻探等领域。
在汽车工业中,硬质合金被用于发动机和传动系统的零件,提高了汽车的性能和耐用性。
在航空航天领域,硬质合金被用于制造飞机发动机叶片和轴承等关键部件,以提高航空器的飞行性能和安全性。
在石油钻探中,硬质合金被用于制造钻头,以提高钻井效率和降低生产成本。
然而,尽管硬质合金在各个领域的使用广泛,但仍然存在一些挑战。
首先,硬质合金的制造过程相对复杂,需要高温和高压等特殊条件,造成生产成本较高。
其次,硬质合金的可加工性较差,在制造和修复过程中受到限制。
此外,硬质合金的生产对环境也会造成一定影响,需要认真考虑可持续性发展问题。
总体而言,硬质合金在现代工程中发挥着重要作用,不断迈向更高的性能水平。
随着材料科学和工程技术的发展,相信硬质合金将会在各个领域得到更广泛应用,并在未来的工程材料中持续发展。
金属陶瓷(硬质合金)

1.3 硬质合金的性能特点、分类及应用
1.3.1硬质合金的性能特点 (1)高硬度、耐磨性好、高热硬性 高硬度、耐磨性好、 (2)抗压强度、弹性模量高 抗压强度、 抗压强度高可达6000MPa, 抗压强度高可达6000MPa,但抗弯强度 6000MPa 低,只有高速钢的1/3~1/2。弹性模 只有高速钢的1 量很高,韧性很差。 量很高,韧性很差。
TIC 刀具
(3)通用硬质合金 ) 主要成分是碳化钨、碳化钛、碳化钽(或碳化铌)及钴。 主要成分是碳化钨、碳化钛、碳化钽(或碳化铌)及钴。这 类硬质合金又称通用硬质合金或万能硬质合金。 类硬质合金又称通用硬质合金或万能硬质合金。 其牌号由“ 两字汉语拼音字首) 其牌号由“YW”(“硬”、“万”两字汉语拼音字首)加顺 ( 序号组成, 序号组成,如 YW1。 。
1.4 烧结成型
硬质合金烧结成型就是将粉末压制成坯料,再进烧结炉加热到 硬质合金烧结成型就是将粉末压制成坯料, 一定温度(烧结温度),并保持一定的时间(保温时间), ),并保持一定的时间 ),然后 一定温度(烧结温度),并保持一定的时间(保温时间),然后 冷却下来, 冷却下来,从而得到所需性能的硬质合金材料 。 硬质合金烧结过程可以分为四个基本阶段: 硬质合金烧结过程可以分为四个基本阶段: 1:脱除成形剂及预烧阶段,在这个阶段烧结体发生如下变化: :脱除成形剂及预烧阶段,在这个阶段烧结体发生如下变化: 成型剂的脱除,烧结初期随着温度的升高, 成型剂的脱除,烧结初期随着温度的升高,成型剂逐渐分解 或汽化,排除出烧结体,与此同时, 或汽化,排除出烧结体,与此同时,成型剂或多或少给烧结体增 增碳量将随成型剂的种类、数量以及烧结工艺的不同而改变。 碳,增碳量将随成型剂的种类、数量以及烧结工艺的不同而改变。 粉末表面氧化物被还原,在烧结温度下, 粉末表面氧化物被还原,在烧结温度下,氢可以还原钴和钨的 氧化物,若在真空脱除成型剂和烧结时,碳氧反应还不强烈。粉 氧化物,若在真空脱除成型剂和烧结时,碳氧反应还不强烈。 末颗粒间的接触应力逐渐消除,粘结金属粉末开始产生回复和再 末颗粒间的接触应力逐渐消除, 结晶,表面扩散开始发生,压块强度有所提高。 结晶,表面扩散开始发生,压块强度有所提高。
硬质合金的发展及现状 现代工程材料

硬质合金的发展及现状硬质合金是用粉末冶金法生产的由难熔金属化合物(硬质相)和粘结金属(粘结相)所构成的复合材料。
具有高硬度、高耐磨性,高弹性模量,高抗压强度,化学稳定性好(耐酸、碱、高温氧化),冲击韧性较低,膨胀系数低,导热、导电与铁及其合金相近。
硬质合金在耐磨件、刀具等方面有着广阔应用前景,今后相当长一段时间中国的国民经济仍将快速发展,将持续为硬质合金提供良好发展空间。
随着工业高速发展以及数控机床、加工中心在机械加工各领域的应用不断扩大,高性能高精度研磨涂层刀片及配套工具等高附加值硬质合金制品需求将不断增加。
在未来几年里中国会成为世界上硬质合金行业最有竞争力的国家。
硬质合金大范围的持续增长,大规模的市场应用在中国国民经济迅速发展的今天是不可逆转的趋势,目前中国硬质合金市场应用是鱼龙混杂,高精端的产品及技术也参次不齐,更高精度,高技术的硬质合金产品的市场需求要靠厂商去开发;面对庞大的市场需求,行业对硬质合金产品提出的更高要求,激烈的竞争中,有挑战也有机遇,虽然目前硬质合金的应用还有不少的局限性,很多更高标准,更高精度还不能普遍满足工业市场的需求。
但是在未来5年内,中国硬质合金高精度高性能研磨涂层合金,高性能超细和纳米硬质合金,功能梯度合金等都会不断的研发生产,得到广泛的应用,从而更进一步满足工业制造的应用需求,促进硬质合金在不同行业和不同领域的应用需求不断扩大,形成一个良性,合理,有序的硬质合金发展市场。
一、中国硬质合金工业的现状在钨工业中,硬质合金耗钨量约占总耗钨量的50%。
因此,硬质合金工业的发展对整个钨工业的发展起着十分重要的作用。
中国硬质合金工业是从20世纪50年代初建设株洲硬质合金厂开始的,50多年来,从无到有,不断发展,取得了令世人瞩目的成就,但整体技术水平特别是高附加值制品的生产与世界先进水平比较仍存在较大差距。
1、取得的快速发展硬质合金产量:20世纪80年代初期,世界硬质合金年产量2.5万吨左右时,中国硬质合金年产量约5千吨。
硬质合金发展简史
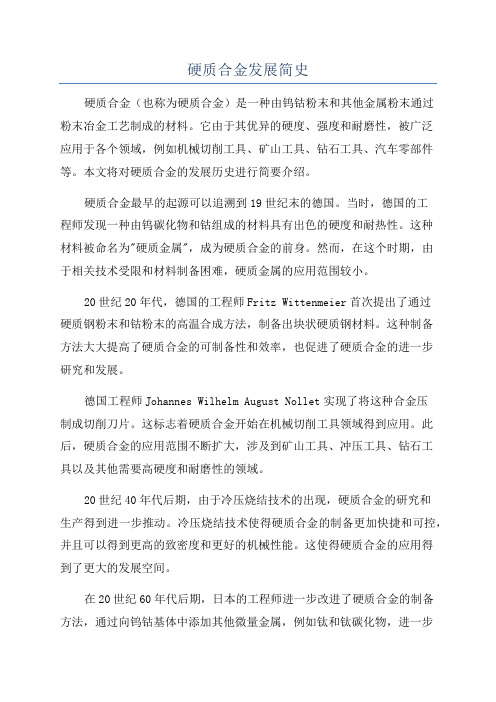
硬质合金发展简史硬质合金(也称为硬质合金)是一种由钨钴粉末和其他金属粉末通过粉末冶金工艺制成的材料。
它由于其优异的硬度、强度和耐磨性,被广泛应用于各个领域,例如机械切削工具、矿山工具、钻石工具、汽车零部件等。
本文将对硬质合金的发展历史进行简要介绍。
硬质合金最早的起源可以追溯到19世纪末的德国。
当时,德国的工程师发现一种由钨碳化物和钴组成的材料具有出色的硬度和耐热性。
这种材料被命名为"硬质金属",成为硬质合金的前身。
然而,在这个时期,由于相关技术受限和材料制备困难,硬质金属的应用范围较小。
20世纪20年代,德国的工程师Fritz Wittenmeier首次提出了通过硬质钢粉末和钴粉末的高温合成方法,制备出块状硬质钢材料。
这种制备方法大大提高了硬质合金的可制备性和效率,也促进了硬质合金的进一步研究和发展。
德国工程师Johannes Wilhelm August Nollet实现了将这种合金压制成切削刀片。
这标志着硬质合金开始在机械切削工具领域得到应用。
此后,硬质合金的应用范围不断扩大,涉及到矿山工具、冲压工具、钻石工具以及其他需要高硬度和耐磨性的领域。
20世纪40年代后期,由于冷压烧结技术的出现,硬质合金的研究和生产得到进一步推动。
冷压烧结技术使得硬质合金的制备更加快捷和可控,并且可以得到更高的致密度和更好的机械性能。
这使得硬质合金的应用得到了更大的发展空间。
在20世纪60年代后期,日本的工程师进一步改进了硬质合金的制备方法,通过向钨钴基体中添加其他微量金属,例如钛和钛碳化物,进一步提升了硬质合金的性能。
这种改进使得硬质合金能够在更具挑战性的切削条件下工作,提高了切削效率和刀具寿命。
随着电子技术的高速发展,21世纪初,硬质合金也迎来了新的发展机遇。
例如,利用钨钴合金制备出的薄膜硬质合金可以应用于石墨烯生长和光纤领域。
此外,通过纳米颗粒添加和纳米结构的设计,进一步优化硬质合金的力学性能和耐磨性。
硬质合金简介
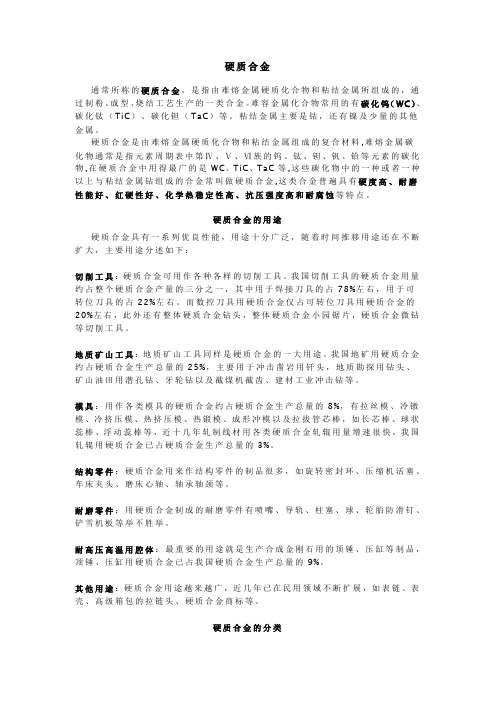
硬质合金通常所称的硬质合金,是指由难熔金属硬质化合物和粘结金属所组成的,通过制粉、成型、烧结工艺生产的一类合金。
难容金属化合物常用的有碳化钨(WC)、碳化钛(TiC)、碳化钽(TaC)等。
粘结金属主要是钴,还有镍及少量的其他金属。
硬质合金是由难熔金属硬质化合物和粘结金属组成的复合材料,难熔金属碳化物通常是指元素周期表中第Ⅳ、Ⅴ、Ⅵ族的钨、钛、钽、钒、铪等元素的碳化物,在硬质合金中用得最广的是WC、TiC、TaC等,这些碳化物中的一种或者一种以上与粘结金属钻组成的合金常叫做硬质合金,这类合金普遍具有硬度高、耐磨性能好、红硬性好、化学热稳定性高、抗压强度高和耐腐蚀等特点。
硬质合金的用途硬质合金具有一系列优良性能,用途十分广泛,随着时间推移用途还在不断扩大,主要用途分述如下:切削工具:硬质合金可用作各种各样的切削工具。
我国切削工具的硬质合金用量约占整个硬质合金产量的三分之一,其中用于焊接刀具的占78%左右,用于可转位刀具的占22%左右。
而数控刀具用硬质合金仅占可转位刀具用硬质合金的20%左右,此外还有整体硬质合金钻头,整体硬质合金小园锯片,硬质合金微钻等切削工具。
地质矿山工具:地质矿山工具同样是硬质合金的一大用途。
我国地矿用硬质合金约占硬质合金生产总量的25%,主要用于冲击凿岩用钎头,地质勘探用钻头、矿山油田用潜孔钻、牙轮钻以及截煤机截齿、建材工业冲击钻等。
模具:用作各类模具的硬质合金约占硬质合金生产总量的8%,有拉丝模、冷镦模、冷挤压模、热挤压模、热锻模、成形冲模以及拉拔管芯棒,如长芯棒、球状蕊棒、浮动蕊棒等,近十几年轧制线材用各类硬质合金轧辊用量增速很快,我国轧辊用硬质合金已占硬质合金生产总量的3%。
结构零件:硬质合金用来作结构零件的制品很多,如旋转密封环、压缩机活塞、车床夹头、磨床心轴、轴承轴颈等。
耐磨零件:用硬质合金制成的耐磨零件有喷嘴、导轨、柱塞、球、轮胎防滑钉、铲雪机板等举不胜举。
耐高压高温用腔体:最重要的用途就是生产合成金刚石用的顶锤、压缸等制品,顶锤、压缸用硬质合金已占我国硬质合金生产总量的9%。
中国硬质合金工业现状及发展趋势
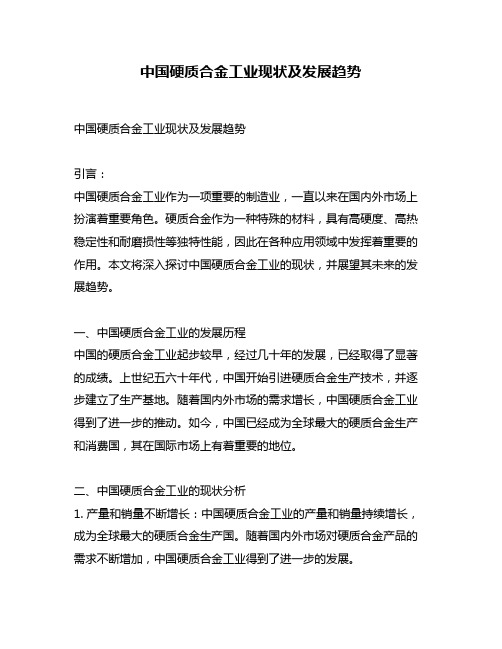
中国硬质合金工业现状及发展趋势中国硬质合金工业现状及发展趋势引言:中国硬质合金工业作为一项重要的制造业,一直以来在国内外市场上扮演着重要角色。
硬质合金作为一种特殊的材料,具有高硬度、高热稳定性和耐磨损性等独特性能,因此在各种应用领域中发挥着重要的作用。
本文将深入探讨中国硬质合金工业的现状,并展望其未来的发展趋势。
一、中国硬质合金工业的发展历程中国的硬质合金工业起步较早,经过几十年的发展,已经取得了显著的成绩。
上世纪五六十年代,中国开始引进硬质合金生产技术,并逐步建立了生产基地。
随着国内外市场的需求增长,中国硬质合金工业得到了进一步的推动。
如今,中国已经成为全球最大的硬质合金生产和消费国,其在国际市场上有着重要的地位。
二、中国硬质合金工业的现状分析1. 产量和销量不断增长:中国硬质合金工业的产量和销量持续增长,成为全球最大的硬质合金生产国。
随着国内外市场对硬质合金产品的需求不断增加,中国硬质合金工业得到了进一步的发展。
2. 技术水平逐步提高:中国硬质合金工业在技术水平上也有了显著的提高。
多家企业进行技术创新和研发投入,提高了硬质合金产品的质量和性能。
中国硬质合金工业也在加强国际合作,吸收和引进国外先进技术,提升产业竞争力。
3. 应用领域广泛:硬质合金产品的应用领域非常广泛,涉及到机械制造、汽车工业、电子工业等多个行业。
中国硬质合金工业在满足国内市场需求的也积极开拓国际市场,出口到世界各地。
三、中国硬质合金工业的发展趋势展望1. 技术创新持续推动发展:随着中国硬质合金工业的不断发展壮大,技术创新将成为未来发展的关键。
中国企业需要加大研发投入,不断提高产品的技术含量和附加值,以在激烈的市场竞争中占得先机。
2. 优化产品结构和提升品质:中国硬质合金工业需要优化产品结构,提高产品的品质和性能,以满足市场对高端产品的需求。
要加强质量管理,建立健全的质量标准和认证体系,提高企业的竞争力。
3. 资源综合利用和绿色生产:随着节能减排和环境保护的重要性日益突出,中国硬质合金工业需要推动资源的综合利用和绿色生产,减少能源消耗和环境污染,实现可持续发展。
硬质合金生产工艺介绍
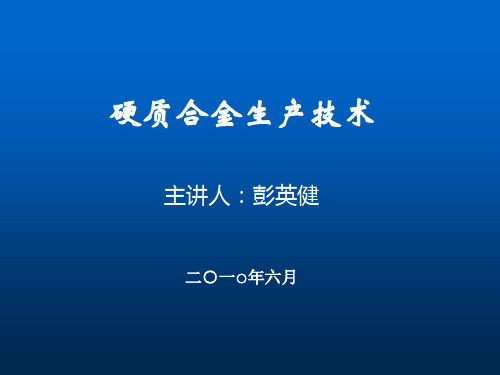
2、硬质合金技术发展趋势及研究开发重点 :
1)高精度高性能硬质合金及配套刀具:由于刀具,特别是刀具材料的进 步,促进了机床业的发展,反过来新型机床对刀具提出了更高要求。在机械 加工中,采用价格昂贵的数控机床、加工中心,必须靠高性能的刀具,高速、 高效和高精度的完成加工任务才能取得良好经济效益。1台加工中心配备的全 部刀具以金额计,刀具费用可达加工中心价格的30%。一般情况下,1台数控 机床年均消耗刀具费用为机床价格的12%左右。因此,工业发达国家都高度重 视刀具技术的发展。当今能满足上述工艺要求的高精度高性能硬质合金刀片 及配套刀具的需求继续处于强劲上升势头,从而带动相关技术不断进步。以 数控涂层刀片为例,从最初的CVD为主到目前的CVD、PVD、PCVD共存,涂层基 体不断更新,涂层种类也从单一化合物涂层,朝着多元复杂化合物涂层发展, 涂层数也从几层到十几层。据资料报导正研究中的纳米涂层,涂层数可达百 层,因此其使用寿命可达普通CVD涂层合金刀片4倍以上。此外,金刚石涂层、 CBN涂层等都以其高技术含量和高附加值越来越受到世界大公司的追求,部分 产品已经推向市场。中国硬质合金工业因这一方面与国外先进水平的差距是 导致其经济效益低下的重要原因。
大的科研成果。
二、硬质合金发展
4)进入80年代以来,世界硬质合金工业发展的突出特点是:一方面,涂层 硬质合金发展迅速,其产量大幅度增加,应用领域不断扩大,已成功地应用于 切削等重加工工序。著名硬质合金生产厂家如山特维克公司、肯纳公司、依斯 卡等的涂层刀片生产已占可转位刀片的85%以上。同时在涂层技术方面也取得 了较大进展,在进一步改进和完善传统的高温化学气相沉积方法的同时,还研 制成功并推广应用了中温化学气相沉积方法以及各种物理气相沉积方法和兼有 物理及化学气相沉积特点的等离子体化学气相沉积方法等。此外,在硬质合金 涂层基体方面,不仅研制出各种加工用的涂层专用基体,而且日本、瑞典等国 还开发出带富钴层或脱β的涂层基体,从而明显地提高了涂层硬质合金的强度, 扩大了涂层硬质合金的应用范围。另一方面,70年代初出现超细合金,最早是 山特维克的R19,接着美国、日本的一些公司也相继推出超细硬质合金牌号。 随着电子工业、机械加工工业的迅速发展,推动超细硬质合金在八十年代迅速 发展,质量不断提高、产量不断扩大。1984年前后,日本住友电气公司试制出 了双高的AF1合金,硬度RA93.0,强度5000N/mm2,创世界之最,随后美国、瑞 典、德国等著名厂家也都相继开发出性能越来越好的超细硬质合金,对于许多 世界著名硬质合金厂家而言,超细硬质合金同高精度、高性能涂层硬质合金一 样是他们引以自豪的一类硬质合金产品。
- 1、下载文档前请自行甄别文档内容的完整性,平台不提供额外的编辑、内容补充、找答案等附加服务。
- 2、"仅部分预览"的文档,不可在线预览部分如存在完整性等问题,可反馈申请退款(可完整预览的文档不适用该条件!)。
- 3、如文档侵犯您的权益,请联系客服反馈,我们会尽快为您处理(人工客服工作时间:9:00-18:30)。
硬质合金发展简史
2008-04-11 12:48
自1923年硬质合金作为一种重要的工具材料和结构材料问世以来,至今已有八十多年的历史。
十九世纪末叶,人们为了寻找新的材料来取代高速钢,以进一步提高金属切削速度、降低加工成本和解决灯泡钨丝的拉拔等问题,开始了对硬质合金的研究。
早期的工作主要是着眼于各种难熔化合物,特别是碳化钨的研究。
从1893年以来,德国科学家就利用三氧化钨和糖在电炉中一起加热到高温的方法制取出碳化钨,并试图利用其高熔点、高硬度等特性来制取拉丝模等,以便取代金刚石材料,但由于碳化钨脆性大,易开裂和韧性低等原因,一直未能得到工业应用。
进入二十世纪二十年代,德国科学家Karl Schroter研究发现纯碳化钨不能适应拉拔过程中所形成的激烈的应力变化,只有把低熔点金属加入WC中才能在不降低硬度的条件下,使毛坯具有一定的韧性。
经过一年时间的努力。
Schroter于1923年首先提出了用粉末冶金的方法,即将碳化钨与少量的铁族金属(铁、镍、钴)混合,然后压制成型并在高于1300℃温度下于氢气中烧结来生产硬度合金的专利。
他在专利中提出的工艺,实质上就是今天许多厂仍在采用的WC—Co硬质合金生产工艺。
1923年德国的krupp公司正式成批生产这种合金,并以widia(类似金刚石)的商标在市场上销售。
随后美国、奥地利、瑞典、日本、原苏联和其他一些国家也相继生产硬质合金,于是硬质合金生产技术开始得到迅速发展。
起初,人们以为WC—Co硬质合金能加工各种材料,但很快发现,在加工钢材时,这种合金很容易因扩散磨损而损坏。
1929年还是德国科学家研究发现,用两种以上的碳化物组成的固溶体比用单一的碳化物作为硬质合金的基体更为优越,并提出了有关固溶体应用的专利。
同年,德国的krupp公司开始生产WC—TiC—Co的合金。
1932年美国根据schroter及其同事专利,也研究出WC—TiC—Co合金。
不久科学家又研究出WC—TiC—TaC—Co合金,从而使钢材加工问题得到妥善解决。
二次世界大战后,由于改进了车床的动力和刚性,切削量增大,人们开始研究可转位硬质合金刀具。
使用这种刀具无需焊接,可随时调换刀头,刀杆可长期使用,其经济效果十分显著,是硬质合金工业的重大进展之一。
自1953年12月可转位刀片问世并采用以来,其推广应用十分迅速,目前全世界的硬质合金生产厂家都在生产这种刀片。
六十年代末期,西德krupp公司成功地研制了涂层硬质合金,它的出现是硬质合金生产技术的又一重大进展。
这种用化学气相沉积的方法,把普通的硬质合金刀片涂上薄薄的一层硬质化合物(如TiC、TiN等)而得到的涂层刀片,在高速下切削铸铁和钢材时,可以比未涂层的硬质合金刀片寿命增加好几倍,而且切削速度可以提高25~30%左右,因此它不久就获得了广泛的工业应用。
目前世界上在所出售的可转位刀具中大约有一大半是使用涂层硬质合金。
随着科学技术的发展,硬质合金的用途愈来愈广泛,人们对硬质合金的性能要求也愈来愈高。
因此在硬质合金领域除开展一些基础理论研究外,更多精力是集中在生产技术和工艺装备的改进创新上,以便能获得更多更好的产品。
六十年代末期研究开发并引入硬质合金生产领域中的热等压技术,是硬质合金科研的一项重大成果。
用这种方法生产的合金,其孔隙度极低,韧性、断裂应力和抗冲击性均有很大提高。
七十年代移植到硬质合金生产领域中的喷雾干燥技术也是一项重大的科研成果,应用这种方法能获得质量稳定、流动性好、压制性能优良的粉末粒料,加上不断推出的精度高、自动化程度高的自动压力机,使混合粒制备到压坯成型,工艺流程缩短、产品精度提高,并可实现连续化、自动化生产,有力推动可转位刀片生产。
进入80年代以来,世界硬质合金工业发展的突出特点是:一方面,涂层硬质合金发展迅速,其产量大幅度增加,应用领域不断扩大,已成功地应用于切削等重加工工序。
著名硬质合金生产厂家如山特维克公司、肯纳公司、依斯卡等的涂层刀片生产已占可转位刀片的85%以上。
同时在涂层技术方面也取得了较大进展,在进一步改进和完善传统的高温化学气相沉积方法的同时,还研制成功并推广应用了中温化学气相沉积方法以及各种物理气相沉积方法和兼有物理及化学气相沉积特点的等离子体化学气相沉积方法等。
此外,在硬质合金涂层基体
方面,不仅研制出各种加工用的涂层专用基体,而且日本、瑞典等国还开发出带富钴层或脱β的涂层基体,从而明显地提高了涂层硬质合金的强度,扩大了涂层硬质合金的应用范围。
另一方面,70年代初出现超细合金,最早是山特维克的R19,接着美国、日本的一些公司也相继推出超细硬质合金牌号。
随着电子工业、机械加工工业的迅速发展,推动超细硬质合金在八十年代迅速发展,质量不断提高、产量不断扩大。
1984年前后,日本住友电气公司试制出了双高的AF1合金,硬度RA93.0,强度5000N/mm2,创世界之最,随后美国、瑞典、德国等著名厂家也都相继开发出性能越来越好的超细硬质合金,对于许多世界著名硬质合金厂家而言,超细硬质合金同高精度、高性能涂层硬质合金一样是他们引以自豪的一类硬质合金产品。
八十年代研制成功并迅速普及的低压热等静压技术是硬质合金生产技
术领域中突破性的进展,从而使低成本地生产十分接近理论致密度的硬质合金产品成为现实。
自1989年美国超高压公司研制成功的第一台低压热等静压设备问世以来,在短短的几年内,该技术就取得了异常迅速的发展这种设备几乎遍及世界各地,对整个硬质合金质量的提高起重要作用。
进入八十年代世界硬质合金工业发展的还一个特点是,硬质合金制品正在向精密化、小型化方向发展,出现了微型麻花钻头、点阵打印针、精密工模具等高新技术产品。
切削工具尺寸精度的要求也越来越高,有的先进厂家已淘汰U 级硬质合金刀片精度标准,与此同时许多硬质合金模具尺寸精度已达到微米级、超微米级,加之设备、生产线自动化、智能化,推动硬质合金工业不断朝着更新、更高领域发展。