湿型砂有效煤粉量(及英文摘要)-铸铁
铸造用煤粉技术指标
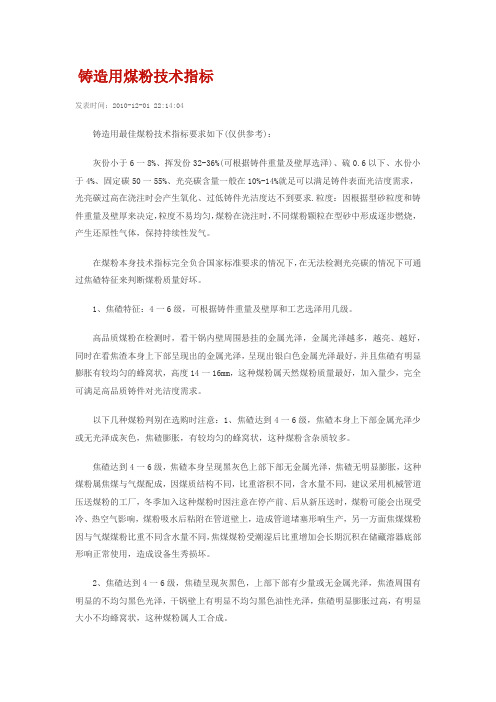
铸造用煤粉技术指标发表时间:2010-12-01 22:14:04铸造用最佳煤粉技术指标要求如下(仅供参考):灰份小于6一8%、挥发份32-36%(可根据铸件重量及壁厚选泽)、硫0.6以下、水份小于4%、固定碳50一55%、光亮碳含量一般在10%-14%就足可以满足铸件表面光洁度需求,光亮碳过高在浇注时会产生氧化、过低铸件光洁度达不到要求.粒度:因根据型砂粒度和铸件重量及壁厚来决定,粒度不易均匀,煤粉在浇注时,不同煤粉颗粒在型砂中形成逐步燃烧,产生还原性气体,保持持续性发气。
在煤粉本身技术指标完全负合国家标准要求的情况下,在无法检测光亮碳的情况下可通过焦碴特征来判断煤粉质量好坏。
1、焦碴特征:4一6级,可根据铸件重量及壁厚和工艺选泽用几级。
高品质煤粉在检测时,看干锅内壁周围悬挂的金属光泽,金属光泽越多,越亮、越好,同时在看焦渣本身上下部呈现出的金属光泽,呈现出银白色金属光泽最好,并且焦碴有明显膨胀有较均匀的蜂窝状,高度14一16mm,这种煤粉属天然煤粉质量最好,加入量少,完全可满足高品质铸件对光洁度需求。
以下几种煤粉判别在选购时注意:1、焦碴达到4一6级,焦碴本身上下部金属光泽少或无光泽成灰色,焦碴膨胀,有较均匀的蜂窝状,这种煤粉含杂质较多。
焦碴达到4一6级,焦碴本身呈现黑灰色上部下部无金属光泽,焦碴无明显膨胀,这种煤粉属焦煤与气煤配成,因煤质结构不同,比重溶积不同,含水量不同,建议采用机械管道压送煤粉的工厂,冬季加入这种煤粉时因注意在停产前、后从新压送时,煤粉可能会出现受冷、热空气影响,煤粉吸水后粘附在管道壁上,造成管道堵塞形响生产,另一方面焦煤煤粉因与气煤煤粉比重不同含水量不同,焦煤煤粉受潮湿后比重增加会长期沉积在储藏溶器底部形响正常使用,造成设备生秀损坏。
2、焦碴达到4一6级,焦碴呈现灰黑色,上部下部有少量或无金属光泽,焦渣周围有明显的不均匀黑色光泽,干锅壁上有明显不均匀黑色油性光泽,焦碴明显膨胀过高,有明显大小不均蜂窝状,这种煤粉属人工合成。
谈砂型铸造表面缺陷

漫谈湿砂型铸件表面缺陷与其它铸造方法相比,湿型铸件是较容易产生粘砂、砂孔、夹砂、气孔等缺陷的。
如果铸造工厂注意控制湿型砂的品质,这些缺陷本来是有可能减少或避免。
以下用实例说明型砂性能与铸件表面缺陷的关系。
一.粘砂研究工作表明,一般湿砂型铸件,不论铸钢还是铸铁,粘砂缺陷都是属于机械粘砂,而不是化学粘砂。
机械粘砂的产生原因有多种,最多见的如下的实例:1.砂粒太粗和透气性过高,金属液容易钻入砂粒间孔隙,使铸件表面粗糙,或将砂粒包裹固定在表面上。
江苏某外资工厂的铸铁旧砂中不断混入大量30/50目粗粒芯砂,以致型砂透气性达到220以上,铸件表面极为粗糙。
内蒙某工厂铸钢车间的气动微震造型机生产中、小铸件。
使用主要集中在40目的40/70粗粒石英砂混制型砂,铸件表面产生严重粘砂。
平时不检测型砂透气性,认为已经符合工艺规程规定的≥80。
为了找到粘砂原因而专门检测一次,发现透气性居然高达1070左右,表明这就是产生粘砂的原因。
因此型砂透气性必须有上限,型砂粒度粗细和透气性应当处于适宜范围内。
一般震压机器造型单一砂最适宜的型砂粒度大多为70/140目,透气性大致为70~100,高密度造型的型砂粒度最好是50/140或100/50,透气性为80~140。
有些生产发动机的铸造厂大量使用50/100目粗原砂制造砂芯,落砂时不断混入旧砂中,使型砂透气性可能达到180以上,就应加入100/140目细砂,或将旋流分离器中的细颗粒部分返回到旧砂中,以便纠正型砂粒度。
2.铸铁型砂中煤粉含量不足或煤粉品质不良。
北京某铸造厂生产高速列车刹车盘,铸件材质符合要求,而表面有严重粘砂,需整体打磨后才能交货。
型砂中所用煤粉来自郊区一家关系密切的私营小供应商。
粘砂的产生原因可能是煤粉品质太差,还可能是型砂中有效煤粉量也不足够。
安徽某阀门总厂使用的“煤粉”是生产焦炭洗选下来的废料,灰分高达76%。
使用后整个型砂性能遭破坏,铸件废品超过一半。
铸造工厂应该对购入的煤粉品质加强检验。
湿型砂性能

湿型砂参考文集第二部分湿型砂性能(清华大学于震宗)目录湿型砂性能1 引言为了保证湿型铸件具有良好的表面品质,必须使用良好品质型砂。
凡是生产重要和表面品质优良铸件的铸造工厂,其型砂实验室的仪器设备大多比较完善齐全,型砂检验项目较多,每日多次检验。
一个正规的铸造工厂型砂实验室中对型砂品质检测管理应当包括:①型砂组成物如砂粒、有效膨润土、有效煤粉、水、灰分、团块等;②型砂特性如紧实率、透气率、强度、韧性、流动性、温度、起模性、表面耐磨性、抗粘砂能力、抗夹砂能力等。
上述的组成物含量和型砂特性统称为型砂性能,这两部分性能是密切联系在一起的。
本文将介绍高品质湿型砂对性能的要求、测试方法、工厂实际应用实例,并分析它们的内在联系以及与铸件品质之间的关系。
旧砂的组成物与型砂基本相同,只是含量多少有一些区别。
在本文中将与型砂一并讨论。
一般认为使用造型紧实压力150~400kPa的普通震压式造型机,砂型平面硬度才只有70~80度,垂直面下端硬度可能只有50~60度,铸件局部极易产生缩孔、缩松、胀砂和粘砂缺陷。
由于砂型平均密度仅1.2~1.3 g/cm3,称为低密度造型或低压造型。
为了克服上述缺点,出现了气动微振造型机。
在压实的同时增添了振动作用,改善了砂型紧实时型砂的流动性能,使压实比压几乎相当于提高了一倍,达到400~700kPa左右,砂型平面硬度大约为80~90度,平均密度可能在1.4~1.5g/cm3范围内。
密度比较均匀,减少了局部缩松、胀砂和粘砂缺陷。
近代化造型机的压实比压有可能提高到700kPa或稍高,所得到砂型表面硬度大约为90~95度,平均密度可达1.5~1.6g/cm3,称为高密度造型方法。
高密度造型的生产效率高、铸件尺寸精度高,机械加工余量少。
应用多触头高压、气冲、挤压、射压、静压、真空吸压等造型机制成砂型都可能达到上述的紧实密度,因而国内外应用日益普遍。
但是紧实压力能够满足铸件品质要求即可,并不过多提高,以免起模性下降和落砂时砂块不易破碎。
潮模砂中加入煤粉的理论

铸铁用湿型砂中为何加入煤粉?在铸铁用粘土湿型砂中加入煤粉的作用在于:①浇注时发出大量还原性气体,能够防止铁液氧化,避免与石英砂产生化学反应;②煤粉受热后成为固、液、气三相的胶质体,能够堵塞砂粒孔隙,使铁液难以钻入;③煤粉的挥发分在高温下气相热解,析出微细结晶的光亮碳沉积在砂粒表面,使砂粒不被铁液润湿,不能借助表面张力向砂粒孔隙中渗透。
因此,湿型铸铁件的型砂中加入良好品质的煤粉不仅能提高铸件的表面质量,而且可提高铸件尺寸的一致性,改善铸件轮廓的清晰度。
长期以来,煤粉一直是铸铁用粘土湿型砂中不可或缺的添加剂。
效果较好的煤粉具有以下几种特性:①灰分(wB)≤10%(质量分数);②挥发分(wB)30%~38%(质量分数);③胶渣特征4~6级;④光亮碳(wB)量10%~18%(质量分数);⑤硫分(wB)≤0.6%.煤粉灰分检测方法按照GB/T212-91,希望煤粉灰分(w B)不超过10%.其作用机理主要是:1、气膜隔离理论浇注时型砂中的煤粉产生大量的还原性气体,使砂型/金属界面形成一层气膜,阻止铁水钻入型砂的砂粒孔隙中。
2、胶质体封孔理论型砂中的煤粉受热后成为固、液、气三相的胶质体,胶质体的膨胀能够堵塞砂粒孔隙,阻止铁水钻入砂粒孔隙中。
3、气体防氧化理论煤粉中的挥发分在高温下气相热解,产生大量的还原性气体,能够防止铁液氧化,避免氧化铁与石英砂产生化学反应。
4、光亮碳防润湿理论浇注时型砂中的煤粉析出微细晶粒的光亮碳,沉积在砂粒表面,使砂粒不被铁液润湿,避免铁水借助表面张力向砂粒孔隙中渗透。
从其作用机理可知:煤粉的挥发分、光亮碳、焦渣特性是煤粉防粘砂效果的主要影响因素。
虽然不符合要求的煤粉也能用于防止铸件粘砂缺陷,但是在型砂中的加入量需提高,这将使型砂需水量增多,如果用于生产高密度造型铸件和品质要求高的铸件,就会增大产生气孔和砂孔缺陷的倾向。
挥发分过高时,型砂发气量过大,将导致铸件产生气孔缺陷。
焦渣特征等级过高时,型砂中焦渣生成量过多,将影响旧砂的回用性。
高密度湿型的型砂原材料品质要求

高密度湿型的型砂原材料品质要求于震宗(清华大学)2002年5月摘要高密度湿型对型砂的原材料提出比较高的要求。
应当选购高品质的膨润土和煤粉。
使用淀粉的铸造工厂应注意其中是否含有杂质。
文章还对回用砂和原砂的性能提出要求。
此外,也不可使用含电解质过多的和被污染的水。
关键词高密度湿型型砂原材料The Quality Requirement of Raw Materials for High Density MoldingYu Zhenzong (Tsinghua University)Abstract The high density molding set a comparative higher requirement on the quality of raw materials for molding sand. Bentonite and seacoal of excellent quality should be choiced. The starch user should be aware whether it contains any impurities. This paper also speaks of the property requirements of reused sand and new sand. In addition, the water containing high level electrolyte or contaminated water cannot be used for sand preparation.Keywords High Density Molding Raw Materials of Molding Sand前言高密度造型(或称高紧实度造型)包括多触头高压、气冲、挤压、射压、静压、吸压等造型方法对型砂品质的要求比较严格[1]。
制备出高品质型砂的最主要关键之一是选用优良品质的型砂原材料。
湿型铸造工艺方法和特点

湿型铸造-唐山百事通提供定义和有关概念砂型造好后,不烘干就进行浇注的铸型称为湿型。
优点是成本低、生产率高,劳动条件得到改善,易于实现机械化自动化;但铸型水分多、强度低。
易产生呛火、夹砂、气孔、冲砂、粘砂、涨箱等铸造缺陷。
铸造在中国发展的很深远,其中湿型砂是使用最广泛的、最方便的造型方法,大约占所有砂型使用量的60~70%,但是这种方法还不适合很大或很厚实的铸件。
表面烘干型与干型比,可节省烘炉,节约燃料和电力,缩短生产周期,所以曾在中型和较大型铸铁件的生产中推广过。
通常采用较粗砂粒(使有高的透气性),加入较多粘土和水分,有时还在型砂中加1~2%的木屑(提高抗夹砂结疤能力),其型腔表面必须涂敷涂料。
工艺特点湿型铸造法的基本特点是砂型(芯)无需烘干,不存在硬化过程。
其主要优点是生产灵活性大,生产率高,生产周期短,便于组织流水生产,易于实现生产过程的机械化和自动化;材料成本低;节省了烘干设备、燃料、电力及车间生产面积;延长了砂箱使用寿命等。
但是,采用湿型铸造,也容易使铸件产生一些铸造缺陷,如:夹砂、结疤、鼠尾、粘沙、气孔、砂眼、胀砂等。
随着铸造科学技术的发展,对金属与铸型相互作用原理的理解更加深刻;对型砂质量的控制更为有效;加上现代化砂处理设备使型砂质量得到了一定保证;先进的造型机械使型砂紧实均匀,起模平稳,铸型的质量较高,促进了湿型铸造方法应用范围的扩大。
例如汽车、拖拉机、柴油机等工业中,质量在300~500kg以下的薄壁铸铁件,现都已成功地采用湿型铸造。
现代化造型方法有:普通机器造型、微震压实造型、多触头高压造型、射压造型、冲击造型及静压造型等。
所用基本原材料湿型砂是由原砂、粘土、附加物及水按一定配比组成的。
常用的加料顺序是先将回用砂和新砂、粘土粉、煤粉等干料混匀,再加水混至要求的水分。
型砂的配方应根据浇注合金种类、铸件特征和要求、造型方法和工艺、清理方法等因素确定型砂应具有的性能范围,然后再根据各种造型原材料的品种和规格、砂处理方法和设备性能、砂铁比等因素拟定。
2006湿型砂性能对铸铁件质量的影响及控制

关键词: 建模; STL; 装配; OpenGL; 凝固模拟
中图分类号: TG248
文献标识码: A
文章编号: 1003- 8345( 2006) 01- 0091- 04
Development of An Embedded Modeling System for the Solidification Simulation
造
Moulding Materials
型
材
料
湿型砂性能对铸铁件质量的影响及控制
孟雪峰, 张芝彬, 张华静
( 北京仁创铸造有限公司, 北京 100085)
摘要: 介绍了湿型砂性能和铸造缺陷之间的关系, 分析了型砂性能对铸件质量的影响, 以实例说明型砂综合性
能分析。提出了加强型砂性能控制的有效办法, 避免因型砂性能波动过大给工厂生产经营带来巨大损失。
1 5 9 13 17 21 25 29 日期
图 1 型砂性能曲线 Fig.1 Property curve of moulding sand
2006 / 2 现代铸铁 89
计
Computer Application
算
机
应
用
凝固模拟 CAE 嵌入式造型系统的研究与开发
陈扬全, 陈立亮, 刘瑞祥
(华中科技大学 材料科学与工程学院凝固模拟研究室, 湖北 武汉 430074)
型砂的透气率不可太低以免浇注过程中发生呛 火和铸件产生气孔缺陷, 但绝不能理解为型砂透气 率越高越好, 因为透气率过高表明砂粒间孔隙较大, 金属液易于渗透而造成表面粗糙、还可能产生机械 粘 砂 。湿 型 砂 的 透 气 率 根 据 浇 注 金 属 的 种 类 和 温 度 、 铸 件 的 大 小 和 壁 厚 、造 型 方 法 、型 砂 的 发 气 量 大 小 等 决定, 一般控制在 90~160。 1.3 湿态强度
铸造高密度湿型砂的型砂性能要求

高密度湿型的型砂性能要求于震宗(清华大学100084)摘 要高密度造型方法对湿型砂性能的要求较普通机器造型更高。
作者在文章中分别说明了高密度型砂的紧实率、含水量、透气率、湿态强度、含泥量、粒度、有效膨润土量、有效煤粉量、韧性、起模性、流动性、可紧实性等性能对铸件品质的影响和控制范围。
为此,作者还用附表中的工厂实际情况作为例证。
在本文的最后还提出获得品质优良型砂的条件。
关键词高密度湿砂型湿型砂性能The Property Requirements of Molding Sand for High Density Green MoldsYu Zhenzong (Tsinghua University, 100084)Abstract As compared with the common jolt-squeeze molding, the high density molding method demands more strict properties of molding sand. This paper describes the infuenced casting quality and the controlled limit of different molding sand properties, such as compactability, water content, permeability, green strength, AFS clay content, grain fineness, effective bentonite content, effective coal dust content, toughness, stripping property, flowability. The actually used sand properties of several foundries are presented in appended list. Finally, the conditions of molding sand for obtaining best quality castings are also provided.Keywords High density green sand mold Green sand property前言高密度造型方法(或称高紧实度造型,包括多触头高压、气冲、挤压、射压、静压、真空吸压等造型方法)的生产效率高、铸件品质较好,因而国内应用日益普遍。
- 1、下载文档前请自行甄别文档内容的完整性,平台不提供额外的编辑、内容补充、找答案等附加服务。
- 2、"仅部分预览"的文档,不可在线预览部分如存在完整性等问题,可反馈申请退款(可完整预览的文档不适用该条件!)。
- 3、如文档侵犯您的权益,请联系客服反馈,我们会尽快为您处理(人工客服工作时间:9:00-18:30)。
湿型砂的有效煤粉含量于震宗(清华大学机械工程系北京100084)摘要:发气量试验方法的优点是能够迅速和准确地确定型砂中有效煤粉的具体含量。
国外常用的灼减量等方法则只能大致估计型砂的抗粘砂能力如何。
简易形式的发气量测定仪可以方便地自行组装,并且具有良好的使用效果。
关键词:湿型砂;有效煤粉含量; 铸铁件Effective Coal Dust Content of Green Molding SandYu Zhenzong(Tsinghua University, Beijing 100084, China)Abstract: The gas evolution test method has advantage of determining the effective coal dust content in green sand rapidly and accurately. The LOI and other test methods common used in foreign countries can only roughly estimate the tendency to prevent the sand burning-on defect. A simple gas evolution test apparatus can be easily constructed by DIY, it works quite satisfactorily.Key words: green molding sand; effective coal dust content; iron castings用来生产铸铁件的湿型砂中通常都要加入煤粉。
煤粉所起的作用是防止铸铁件表面粘砂和改善表面光洁程度,而且能够减轻夹砂倾向。
煤粉还有利于防止球墨铸铁件皮下气孔缺陷。
型砂中原来含有的煤粉中有一部分经浇注铁液的加热作用变成不起作用的焦炭。
混制湿型砂时需要补充加入适量的新煤粉,新加入煤粉量取决于旧砂中含有多少有效煤粉,以及型砂应当含有多少有效煤粉。
但是多年来人们不掌握如何测定型砂和旧砂中的有效煤粉含量。
1 国外估计型砂中煤粉量的方法国外工厂为了估计湿型砂抗机械粘砂能力,应用最普遍的办法是测定灼减量(即LOI)。
实验方法是将型砂试料装入敞开的瓷坩埚中,在规定温度的马福炉内加热。
使挥发性物质和可燃物质跑掉或烧掉,以总共减少重量比值为灼减量。
美国规定在坩埚中称量25g烘干型砂,放置到982℃马福炉中加热2~3h[1]。
德国规定称量5g型砂在850℃马福炉中加热至少3h[2]。
Buhr测得76家加拿大灰铁和球铁铸造厂型砂灼减量在1~10%[3];Bruemmer 测得105家欧洲铸铁厂的型砂灼减量在1.0~15.0%范围内[4]。
各厂的型砂灼减量控制范围相差非常悬殊。
其原因主要是测得的灼减量除了包含了煤粉以外,还包括煤粉受热丧失挥发分后形成的焦炭状物质。
由于各厂型砂中积累的焦炭状物质数量多少不等,使得测出灼减量有很大差异。
因而也就无法从灼减量推算出型砂中含有多少有效煤粉。
还有极个别工厂试图使用定碳仪测定型砂含碳量来判断抗粘砂能力,也存在同样缺点。
有些国外工厂测定型砂的挥发分来估计湿型砂抗机械粘砂能力。
将型砂试料装入有盖的瓷坩埚中,在规定温度的马福炉内加热。
使挥发性物质跑掉后减少的重量为挥发分。
美国测定挥发分方法较为特殊,称量50g试料,加热温度为482℃或649℃,加热1h。
其他国家很少仿照采用。
欧洲一般采用称量型砂5g,在900℃马福炉中加热5min。
Hofmann 从德、荷、法等国5家工厂气冲线取样测得挥发分0.9~1.7%[5]。
de May测定一家比利时工厂BMD冲击造型的型砂挥发分为0.96~1.96%[6]。
与灼减量相比,各厂挥发分比较接近。
从很多工厂的型砂挥发分测定数值看出,每1g型砂的挥发分重量大致在10~30mg左右。
研究表明膨润土受热分解发出水分5~6%,假定通常机器造型的型砂含有膨润土5~7%,则1g型砂中膨润土分解产生水分约为2.5~4mg,成为由型砂挥发分推算出含有的煤粉量的障碍。
到上世纪70年代以后,铸造工厂开始掌握用亚甲基蓝滴定方法测定型砂的有效膨润土量。
有人提出测定出型砂的有效膨润土量后,将膨润土受热分解出水分量从挥发分总量中扣除,然后计算出有效煤粉量。
但是整个测试过程比较繁琐费时,不适合在实际生产中做为快速检测方法控制型砂品质。
2 用发气量仪器测定有效煤粉量上世纪六十年代初期,清华大学与洛阳第一拖拉机厂共同组成联合攻关小组,研究解决重量达274kg汽缸体等大型铸铁件表面粘砂和夹砂缺陷。
工厂为生产大型铸铁件专门配制的面砂是用一半旧砂,一半新砂另加黏土和煤粉混制成的。
当时发现一个难以解释的现象:用面砂造型铸造出汽缸体的表面品质还不如全部用背砂造型的铸件。
虽然也怀疑混砂时补充加入的煤粉量可能太少,由于不知道旧砂中究竟含有多少未被烧损的有效煤粉,不知道面砂中应当含有多少有效煤粉,也不知道混砂时应该新补充加入多少煤粉。
因此迫切需要找到能够检测出型砂和旧砂中有效煤粉含量的方法。
从资料中了解到国外有的单位靠测定铸铁湿型砂的灼减量等方法做为推测型砂抗粘砂能力的根据。
考虑这些方法都无法得出型砂中所含有有效煤粉的具体数值,而且大多操作比较麻烦和费时,不适合铸造车间的型砂实验室快速检验应用。
当时认为煤粉防铸铁件粘砂作用主要靠的是挥发分。
如果在测定挥发分时,设法将黏土分解发出的水汽凝结成液体。
就可以根据冷凝后的气体体积代表试料中的有效煤粉量。
那时工厂中央实验室有一台用于测定芯砂发气量的仪器,主要由管式电炉、热电偶和炉温控制仪、冷凝管、滴定管和平衡瓶组成,并以橡胶管相联接。
结构示意图见图1。
冷凝管的作用是使水汽凝结成液态而不占体积。
滴定管用于衡量气体容量。
平衡瓶用于保持整个系统的压力相当于图1 发气量测定仪简化示意图1—加热炉2—瓷舟3—冷凝管4—平衡瓶5—滴定管大气压力,容易准确测量所发出气体量,而且避免仪器在使用中漏气。
当年煤炭工业部标准测定煤样挥发分的加热温度为850℃和7min,便引用同样规范来测定型砂发气量。
如今国家标准GB/J 212-2001《煤的工业分析方法》中挥发分的测定炉温改为900±10℃[7]。
机械行业标准JB/T 9221–1999《铸造用湿型砂有效膨润土及有效煤粉实验方法》规定试料的加热温度也改为900℃。
为了检验发气量测定仪是否能够用于测定型砂的有效煤粉含量。
将烘干和磁选除掉铁粒的试料均匀称取1.00g装入瓷质试样舟,送入管式炉中加热,测出试料的发气量。
同样方法测定0.10g煤粉的发气量,即可计算出型砂(或旧砂)的有效煤粉量,按下式计算:Q1-ΣQ2X = –––––––––⨯ 100%Q式中:X-型砂(或旧砂)中有效煤粉量,%;Q1-1g型砂(或旧砂)的发气量,mL;ΣQ2-1g型砂(或旧砂)中除煤粉以外的膨润土及其它附加物的总发气量,mL ;Q-0.01g煤粉的发气量(0.10 g煤粉的发气量除以10),mL。
型砂的膨润土中可能含有少量碳酸盐等杂质,这些物质受热发气量比煤粉发气量少很多。
例如大同煤粉0.10g发气27.2mL,即1g型砂中含有煤粉10%时发气27.2 mL。
虽然理论计算900℃高温时1g型砂试料的黏土分解产生水蒸汽占容积有十余mL,但离开高温区的水蒸汽容积立即减小,在瓷管低于100℃部位凝结成露水而不占容积。
因而九台膨润土0.10g发气只有1.4mL,即1g型砂中含有膨润土10%时发气只有1.4 mL。
通常型砂含膨润土5~7%,发气体积不过仅为0.70~0.98mL,为了简化计算可以忽略不计。
旧砂中可能含有少量残留树脂,机油或其它有机砂芯粘结剂,虽然它们也会发出一些气体,但也能起煤粉类似的抗粘砂作用,可以与煤粉同样看待而无需区分清楚。
因此,在生产中可以用1g型砂或旧砂的发气量除以单独测出的煤粉发气量即可推算得出大致的有效煤粉含量(%)。
计算式简化如下:Q1X = ––––––⨯ 100%Q使用上述方法检验1963年底以前汽缸体面砂每1g发气量大致在18~20mL,推算得出大同煤粉含量平均约只有5.5%。
而填充砂的发气量大致在22mL左右,折合煤粉含量也只有6.2%。
推算出煤粉含量约只有6.6~7.4%。
这对于用震击造型机造型,砂型表面无涂料,用大同煤粉生产大型汽缸体等铸件是容易产生粘砂缺陷的。
由此搞清楚了铸件表面粘砂的原因是型砂中有效煤粉量不够多。
当即决定提高混制面砂的煤粉补加量,使面砂发气量提高到30 mL/g左右,折算成大同煤粉有效量约9.5%,使铸件表面得到了一些改善。
随后又对大件面砂配方做了较大改变,使发气量提高到35~40 mL/g左右,汽缸体等大型铸件落砂后即显露出极其光洁蓝色表面,毫无粘砂缺陷。
1964年上半年用发气量仪器进行了大量检测试验,配制全新材料的型砂,测定得出型砂的有效煤粉量与配方中加入煤粉量完全相同。
混制生产中各类不同铸铁件用型砂,测定出的有效煤粉量与浇铸出铸件的表面品质完全相符合。
在1964年11月的全国潮模会议上将此项工作结果做了介绍[8]。
2 发气量测定仪器的改进以上所介绍仪器的发气量测量是靠眼睛直接观看,不能自动记录气体的体积变化情况和最终发气结果。
为了更改成自动化记录仪器,上世纪八十年代初期清华大学研制出一种改进型的发气量测定仪。
原理示意图如图2,其特点是改用压力传感器测定发气压力折算成发气容积。
由记录仪自动绘出发气量与时间的关系曲线。
还用石英管代替陶瓷管,提高了炉管的高温耐压性和使用寿命;用不锈钢舟代替瓷舟,使其重量一致,避免试样升温速度波动;改进管塞与试样钩的结构(见图3),用2mm 直径的不銹钢焊条制成特殊形状的试样钩。
钩的端部尖形弯头插入试样舟小孔中。
另一端插在胶塞的中心部位。
中间有一段弯曲部分可以沿石英管內底面滑动,保证试样钩的尖端总是保持在试样舟的小孔中保证试料在炉管中位置正确。
测定过程中试样钩就畄在炉管中不必拨出,测试完毕后试样钩连同试样舟一起抜出,使操作时间大为缩短。
由于仪器使用极为方便,已在国内铸造工厂大量使用[9]。
3 有效煤粉量测定在生产中的应用铸铁件型砂中应有的有效煤粉量因铸件大小和厚薄、浇注温度、面砂或单一砂、造型方法、砂型紧实程度等因素而异。
更重要的是因煤粉品质不同而异。
上面所述的例子中,当时所用大同煤粉的品质并不够理想,煤粉灰分12~14%,挥发分26~28%,焦渣特征1~2级。
所以型砂中须要含有较多的有效煤粉量。
如果当时使用高效煤粉,有效煤粉量估计可以减少一半左右。
如果铸件重量稍低和厚度稍薄,有效煤粉量还可以再少一些。
以100kg 以内的中小灰铁铸件为例,应用普通煤粉的高密度造型的型砂中有效煤粉量多为6~7%,应用优质煤粉的有效煤粉量可降低到4~5%,使用高效煤粉时只要3~4%即可。