齿轮齿条设计
齿轮齿条的设计
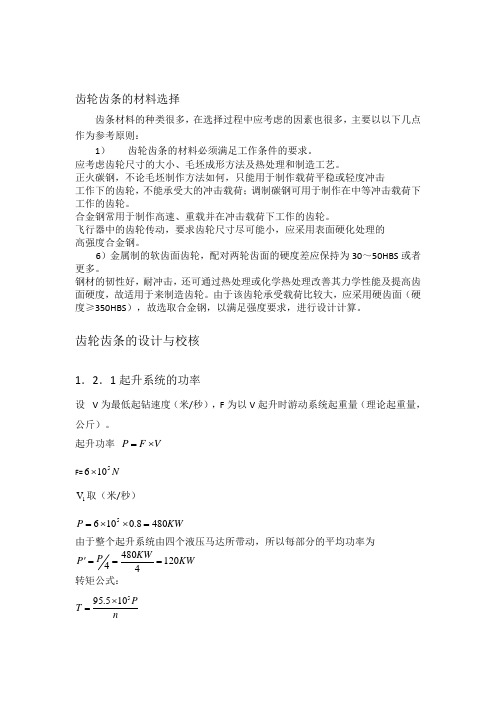
齿轮齿条的材料选择齿条材料的种类很多,在选择过程中应考虑的因素也很多,主要以以下几点作为参考原则:1) 齿轮齿条的材料必须满足工作条件的要求。
应考虑齿轮尺寸的大小、毛坯成形方法及热处理和制造工艺。
正火碳钢,不论毛坯制作方法如何,只能用于制作载荷平稳或轻度冲击工作下的齿轮,不能承受大的冲击载荷;调制碳钢可用于制作在中等冲击载荷下工作的齿轮。
合金钢常用于制作高速、重载并在冲击载荷下工作的齿轮。
飞行器中的齿轮传动,要求齿轮尺寸尽可能小,应采用表面硬化处理的 高强度合金钢。
6)金属制的软齿面齿轮,配对两轮齿面的硬度差应保持为30~50HBS 或者更多。
钢材的韧性好,耐冲击,还可通过热处理或化学热处理改善其力学性能及提高齿面硬度,故适用于来制造齿轮。
由于该齿轮承受载荷比较大,应采用硬齿面(硬度≥350HBS ),故选取合金钢,以满足强度要求,进行设计计算。
齿轮齿条的设计与校核1.2.1起升系统的功率设V 为最低起钻速度(米/秒),F 为以V 起升时游动系统起重量(理论起重量,公斤)。
起升功率 VF P ⨯=F=N 5106⨯ 1V 取(米/秒)KW P 4808.01065=⨯⨯=由于整个起升系统由四个液压马达所带动,所以每部分的平均功率为KW KW P P 12044804===' 转矩公式:595.510P T n⨯=所以转矩 T=mm N n.120105.955⨯⨯ 式中n 为转速(单位r/min )1.2.2 各系数的选定计算齿轮强度用的载荷系数K ,包括使用系数A K 、动载系数V K 、齿间载荷分配系数K α及齿向载荷分配系数K β,即K=A V K K K K αβ1)使用系数A K是考虑齿轮啮合时外部因素引起的附加载荷影响的系数。
该齿轮传动的载荷状态为轻微冲击,工作机器为重型升降机,原动机为液压装置,所以使用系数A K 取。
2)动载系数V K齿轮传动不可避免地会有制造及装配误差,轮齿受载后还要产生弹性变形,对于直齿轮传动,轮齿在啮合过程中,不论是有双对齿啮合过渡到单对齿啮合,或是有单对吃啮合过渡到双对齿啮合的期间,由于啮合齿对的刚度变化,也要引起动载荷。
齿轮齿条的设计计算与校核
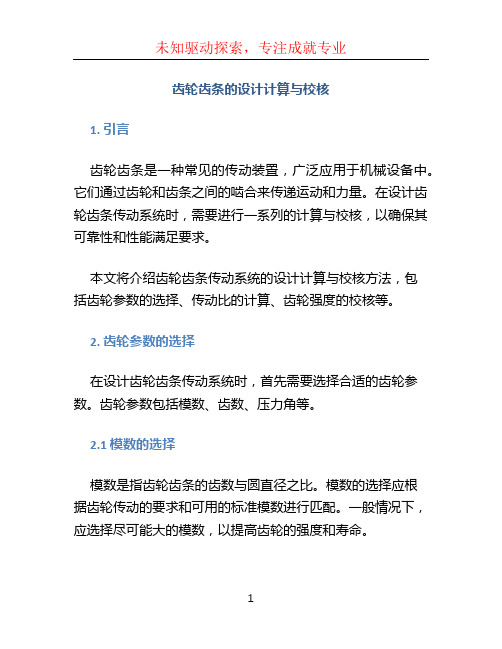
齿轮齿条的设计计算与校核1. 引言齿轮齿条是一种常见的传动装置,广泛应用于机械设备中。
它们通过齿轮和齿条之间的啮合来传递运动和力量。
在设计齿轮齿条传动系统时,需要进行一系列的计算与校核,以确保其可靠性和性能满足要求。
本文将介绍齿轮齿条传动系统的设计计算与校核方法,包括齿轮参数的选择、传动比的计算、齿轮强度的校核等。
2. 齿轮参数的选择在设计齿轮齿条传动系统时,首先需要选择合适的齿轮参数。
齿轮参数包括模数、齿数、压力角等。
2.1 模数的选择模数是指齿轮齿条的齿数与圆直径之比。
模数的选择应根据齿轮传动的要求和可用的标准模数进行匹配。
一般情况下,应选择尽可能大的模数,以提高齿轮的强度和寿命。
2.2 齿数的选择齿数的选择主要考虑齿轮传动的传动比和齿轮的工作条件。
传动比是指齿轮输入轴的转速与输出轴的转速之比。
2.3 压力角的选择压力角是指齿轮齿条啮合面上法线与齿轮轴线之间的夹角。
压力角的选择应根据齿轮传动的要求和可用的标准压力角进行匹配。
一般情况下,应选择尽可能小的压力角,以减小齿轮齿条的侧向力和噪声。
3. 传动比的计算传动比是齿轮齿条传动系统中重要的性能指标之一,它影响着输出轴的转速和扭矩。
传动比的计算可以根据齿轮齿数的比值来确定。
4. 齿轮强度的校核齿轮强度是齿轮齿条传动系统设计中关键的校核指标之一,它决定了齿轮的承载能力和寿命。
齿轮强度的校核可以通过齿轮的材料强度和几何参数来确定。
4.1 齿轮模数的校核齿轮模数的校核可以通过计算齿轮的接触应力和弯曲应力来进行。
应保证齿轮的接触应力和弯曲应力不超过齿轮材料的强度极限。
4.2 齿轮齿数的校核齿轮齿数的校核可以通过计算齿轮的接触比和模数来进行。
应保证齿轮的接触比和模数满足设计要求。
4.3 齿轮强度的校核齿轮强度的校核可以通过计算齿轮的接触疲劳寿命来进行。
应保证齿轮的接触疲劳寿命不低于设计要求。
5. 结论齿轮齿条的设计计算与校核是确保齿轮齿条传动系统可靠性和性能的重要环节。
齿轮齿条设计计算公式

齿轮齿条设计计算公式齿轮和齿条是机械传动中常见的元件,用于传递动力和转速。
齿轮齿条的设计计算是设计师在进行齿轮齿条设计时所必须掌握的知识。
本文将介绍齿轮齿条设计计算的一些基本公式和原理。
一、齿轮设计计算公式1. 齿数计算公式齿数是齿轮设计中最基本的参数之一,可以通过以下公式计算:N = (π * D) / m其中,N为齿数,D为齿轮直径,m为模数。
2. 齿轮间距计算公式齿轮间距是指两个相邻齿轮之间的中心距离,可以通过以下公式计算:P = (N1 + N2) / 2 * m其中,P为齿轮间距,N1和N2分别为两个相邻齿轮的齿数,m为模数。
3. 齿轮传动比计算公式齿轮传动比是指两个相邻齿轮的转速之比,可以通过以下公式计算:i = N2 / N1其中,i为传动比,N1和N2分别为两个相邻齿轮的齿数。
4. 齿轮模数计算公式齿轮模数是指齿轮齿数和齿轮直径之间的比值,可以通过以下公式计算:m = D / N其中,m为模数,D为齿轮直径,N为齿数。
二、齿条设计计算公式1. 齿条模数计算公式齿条模数是指齿条齿数和齿条长度之间的比值,可以通过以下公式计算:m = L / N其中,m为模数,L为齿条长度,N为齿数。
2. 齿条传动比计算公式齿条传动比是指齿条的移动距离与齿轮转动角度之间的比值,可以通过以下公式计算:i = L / (π * D)其中,i为传动比,L为齿条的移动距离,D为齿轮的直径。
3. 齿条齿数计算公式齿条齿数是指齿条上的齿数,可以通过以下公式计算:N = L / m其中,N为齿数,L为齿条长度,m为模数。
三、齿轮齿条设计计算实例假设有一对齿轮,其中一个齿轮的齿数为20,直径为40mm,另一个齿轮的齿数为40,直径为80mm,模数为2mm。
我们可以通过上述公式进行计算。
根据齿数计算公式,可得第一个齿轮的齿数为20,第二个齿轮的齿数为40。
根据齿轮间距计算公式,可得齿轮间距为(20+40)/2*2=60mm。
齿轮齿条选型计算

齿轮齿条选型计算齿轮齿条计算选型(仅供参考)一、设计要求直线速度V=120m/min 、nmotor=4500rpm、加速时间200ms 、冲击因素系数fs=1.25(2000次/每小时)移动部件重量m=460Kg、摩擦系数µ=0.15、齿轮-齿条啮合系数η=95% 水平双边驱动工况按间歇工作制S5来计算,二、切向力计算及齿条选型(折算到单侧):加速度a=9.8m/s2摩擦系数µ=0.15效率:η=95%移动部件重量m=230Kg(折算到单侧)摩擦力 f=µmg=0.15*230*9.8=338N加速力 F加速=ma=230*9.8=2254N加速时总的驱动力F=(F加速+f)/η=2600N考虑冲击因素F总=F*fs* =2600*1.25=3250N(最大切向力) 根据alpha-rack&pinion 技术资料的数据:系统TP050、M3、Z=31、F2T=12442N(切向力)、T2B=500(加速扭矩),系统TP025、M2、Z=40、F2T=5891N、T2B=250Nm 可选用alpha PREMUM(5级)模数3或模数2的齿条。
alpha PREMUM(5级)齿条齿间误差fp:0.003mm,累计误差Fp:0.012mm(500mm 长)。
三、小齿轮、齿轮箱选型1、小齿轮根据alpha-rack&pinion技术资料的数据选小齿轮为 M3、Z=31个齿,节圆半径R=49.35mm 选小齿轮为 M2、Z=40个齿,节圆半径R=42.45mm 2、齿轮箱a、 M3、Z=31个齿,节圆半径R=49.35mm折算到齿轮箱的最大输出扭矩T=F总*R=3250*49.35/1000=160Nm (加速力矩)b、 M2、Z=40个齿,节圆半径R=42.45mm折算到齿轮箱的最大输出扭矩T=F总*R=3250*42.45/1000=138Nm (加速力矩根据 alpha-rack&pinion 技术资料的数据M3、Z=31,T2B=500Nm (实际为T=160Nm)M2、Z=40,T2B=250Nm (实际为T=138Nm)3、速比电机的转速nmotor=4500rpm,直线速度V=120m/min,a、 M3、Z=31个齿,节圆半径R=49.35mm减速箱转速n2 =V/(2R*3.14 /1000 )=120/(2*49.35*3.14/1000)=387速比 I=nmotor/n2 = 4500/387=11,取I=10{I=10,R=49.35mm,n1=4500rpm ,V=(4500/10)*2*49.35*3.14/1000=139.5m/min}b、 M2、Z=40个齿,节圆半径R=42.45mm减速箱转速n2 =V/(2R*3.14 /1000 )=120/(2*42.45*3.14/1000)=450速比 I=nmotor/n2 = 4500/450=10{I=10,R=42.45mm,n1=4500rpm ,V=(4500/10)*2*42.45*3.14/1000= 128m/min}4、齿轮箱背隙与小齿轮-齿条间隙对传动系统定位精度的影响a、 M3、Z=31个齿,节圆半径R=49.35mm齿轮箱背隙/定位精度 =2R*3.14/360/60=2*49.35/360/60=0.014mm/arcminb、 M2、Z=40个齿,节圆半径R=42.45mm齿轮箱背隙引起的误差 =2R*3.14/360/60=2*42.45*3.14/360/60=0.012mm/arcmin c、小齿轮-齿条间隙小齿轮-齿条间隙调整为0.01mm+齿条齿间误差,0.01mm+0.003mm=0.013mm齿条累计误差可通过校准仪消除d、传动系统定位精度1、M3、Z=31个齿,节圆半径R=49.35mm(齿轮箱背隙引起的误差)+(小齿轮-齿条间隙)=0.014mm/arcmin*jt(背隙)+(0.01mm+0.003mm)=0.014mm+(0.01mm+0.003mm)( 齿轮箱背隙1弧分)=0.027mm( 齿轮箱背隙1弧分)2、M2、Z=40个齿,节圆半径R=42.45mm(齿轮箱背隙引起的误差)+(小齿轮-齿条间隙)=0.012mm/arcmin*jt(背隙)+(0.01mm+0.003mm)=0.012mm+(0.01mm+0.003mm)( 齿轮箱背隙1弧分)=0.025mm( 齿轮箱背隙1弧分四、结论1、 M3、Z=31个齿,节圆半径R=49.35mm、齿轮箱TP050S /I=10V=140m/min,加速度5GG=(F2T*η/fs-µmg)/m/9.8=(12442*0.95/1.25-0.15*175*9.8)/9.8=5 定位精度小于0.03mm2、 M2、Z=40个齿,节圆半径R=42.45mm、齿轮箱TP025S/ I=10V=128m/min加速度2.5GG=(F2T*η/fs-µmg)/m/9.8=(5891*0.95/1.25-0.15*175*9.8)/9.8=2.5 定位精度小于0.03mm。
齿轮齿条传动设计计算完整版
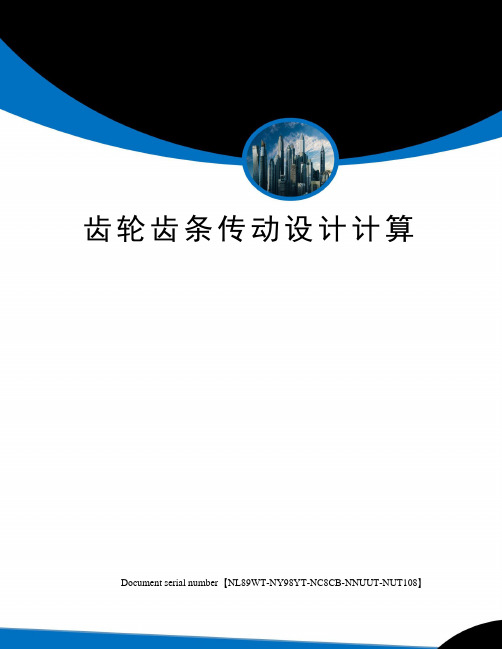
齿轮齿条传动设计计算 Document serial number【NL89WT-NY98YT-NC8CB-NNUUT-NUT108】1.选定齿轮类型、精度等级、材料级齿数1)选用直齿圆柱齿轮齿条传动。
2)速度不高,故选用7级精度(GB10095-88)。
3)材料选择。
由表10-1选择小齿轮材料为40Cr(调质),硬度为280HBS,齿条材料为45钢(调质)硬度为240HBS。
4)选小齿轮齿数Z1=24,大齿轮齿数Z2=∞。
2.按齿面接触强度设计由设计计算公式进行计算,即d1t≥2.32√K t T1φdu+1u(Z E[σH])23(1)确定公式内的各计算数值1)试选载荷系数K t=。
2)计算小齿轮传递的转矩。
(预设齿轮模数m=8mm,直径d=160mm)T1=95.5×105P1n1=95.5×105×0.24247.96=2.908×105N?mm3) 由表10-7选齿宽系数φd=0.5。
4)由表10-6查得材料的弹性影响系数Z E=189.8MPa12。
5)由图10-21d按齿面硬度查得小齿轮的接触疲劳强度极限σHlim1=600MPa;齿条的接触疲劳强度极限σHlim2=550MPa。
6)由式10-13计算应力循环次数。
N1=60n1jL h=60×7.96×1×(2×0.08×200×4)=6.113×1047)由图10-19取接触疲劳寿命系数K HN1=1.7。
8)计算接触疲劳许用应力。
取失效概率为1%,安全系数S=1,由式(10-12)得[σH]1=K HN1σHlim1S=1.7×600MPa=1020MPa(2)计算1)试算小齿轮分度圆直径d t1,代入[σH]1。
d 1t ≥2.32√K t T 1φd u +1u (Z E [σH ])23=2.32√1.3×2.908×1050.5∞+1∞ (189.81020)23=68.89mm2) 计算圆周速度v 。
齿轮齿条设计计算公式
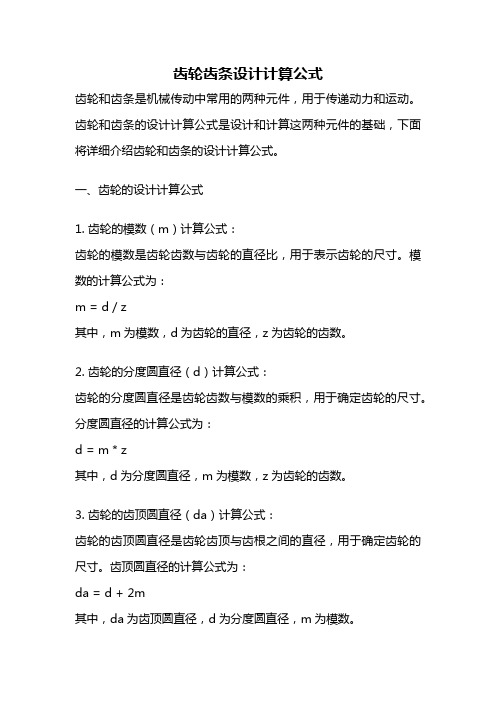
齿轮齿条设计计算公式齿轮和齿条是机械传动中常用的两种元件,用于传递动力和运动。
齿轮和齿条的设计计算公式是设计和计算这两种元件的基础,下面将详细介绍齿轮和齿条的设计计算公式。
一、齿轮的设计计算公式1. 齿轮的模数(m)计算公式:齿轮的模数是齿轮齿数与齿轮的直径比,用于表示齿轮的尺寸。
模数的计算公式为:m = d / z其中,m为模数,d为齿轮的直径,z为齿轮的齿数。
2. 齿轮的分度圆直径(d)计算公式:齿轮的分度圆直径是齿轮齿数与模数的乘积,用于确定齿轮的尺寸。
分度圆直径的计算公式为:d = m * z其中,d为分度圆直径,m为模数,z为齿轮的齿数。
3. 齿轮的齿顶圆直径(da)计算公式:齿轮的齿顶圆直径是齿轮齿顶与齿根之间的直径,用于确定齿轮的尺寸。
齿顶圆直径的计算公式为:da = d + 2m其中,da为齿顶圆直径,d为分度圆直径,m为模数。
4. 齿轮的齿根圆直径(df)计算公式:齿轮的齿根圆直径是齿轮齿根与齿顶之间的直径,用于确定齿轮的尺寸。
齿根圆直径的计算公式为:df = d - 2.2m其中,df为齿根圆直径,d为分度圆直径,m为模数。
5. 齿轮的齿宽(b)计算公式:齿轮的齿宽是齿轮齿根与齿顶之间的宽度,用于确定齿轮的尺寸。
齿宽的计算公式为:b = m * zc其中,b为齿宽,m为模数,zc为齿轮齿数系数。
二、齿条的设计计算公式1. 齿条的模数(m)计算公式:齿条的模数是齿条齿数与齿条的厚度比,用于表示齿条的尺寸。
模数的计算公式为:m = t / z其中,m为模数,t为齿条的厚度,z为齿条的齿数。
2. 齿条的分度圆直径(d)计算公式:齿条的分度圆直径是齿条齿数与模数的乘积,用于确定齿条的尺寸。
分度圆直径的计算公式为:d = m * z其中,d为分度圆直径,m为模数,z为齿条的齿数。
3. 齿条的基圆直径(db)计算公式:齿条的基圆直径是齿条齿槽底部的直径,用于确定齿条的尺寸。
基圆直径的计算公式为:db = d - 2m其中,db为基圆直径,d为分度圆直径,m为模数。
齿轮齿条设计

4.1 齿轮参数的选择[8]齿轮模数值取值为m=4,齿轮齿数为z=150,压力角取α=20°,标准齿轮各部分尺寸都与模数有关,且都与模数成正比。
规定齿顶高ha=h *a m, h *a 和c *分别称为齿顶高系数和顶隙系数。
正常齿制齿轮h *a =1, c *=0.25。
齿轮选用20MnCr5材料制造并经渗碳淬火,而齿条常采用45号钢或41Cr4制造并经高频淬火,表面硬度均应在56HRC 以上。
为减轻质量,壳体用铝合金压铸。
4.2 齿轮几何尺寸确定[2]齿顶高 h a =h *a m=1×4, h a =4 mm齿根高 h f =( h *a + c *)m , h f =(1+0.25)×4=5 mm齿高 h = h a + h f =4+5, h=9 mm分度圆直径 d =mz d=4×150=600 mm齿顶圆直径 d a =d+2 h a d a =608 mm齿根圆直径 d f = d-2 h f =600-2×5=590mm基圆直径 d b =d αcos =564mm齿厚为 s=p/2=πm/2=6.28齿槽宽 e= p/2=πm/2=6.28齿距 p=πm=3.14×4=12.564.3 齿根弯曲疲劳强度计算[11]4.3.1齿轮精度等级、材料及参数的选择(1) 由于转向器齿轮转速低,是一般的机械,故选择8级精度。
(2) 齿轮模数值取值为m=4,齿轮齿数为z=150,压力角取α=20°.(3) 齿轮选用20MnCr5或15CrNi6材料制造并经渗碳淬火,硬度在56-62HRC 之间,取值60HRC.4.3.2齿轮的齿根弯曲强度设计。
σF =z bm KT 22Y F Y S ≤[σF ]m ≥32][2F S F d Y Y z KT σψ• T=9.55×106×ωωn P [σF ]=FF N S Y limσ式中 K —载荷因数,由表7—8,取K=1.2;T —齿轮的理论转矩,T=105845N ·mσF —齿根实际最大弯曲应力(Mpa )[σF ]—齿轮的许用弯曲应力(Mpa )b —轮齿的工作宽度(mm )d ψ—齿宽因数,见表7-12Y F —齿形修正因数,见表7-11Y S —应力修正因数,见表7-11Y N —弯曲疲劳寿命因数,见图7-30lim F σ—弯曲疲劳极限,见图7-31S F —弯曲疲劳强度安全因数,见表7-10取齿宽系数 d ψ=0.8齿轮齿数 z=150许用弯曲应力 201.25MpaσF =189≤201.25= [σF ]m ≥4,取m=44.3.3齿面接触疲劳强度校核校核公式为σH =3.53Z E μμ121±⨯bdKT ≤[σH ] 式中K 为载荷因数,见表7-8,取K=1.2Z E —材料的弹性因数MPa ,见表7-9,取 Z E =144σH —齿面的实际最大接触应力μ—齿数比[σH ]=HH N S Z lim σ 式中[σH ]—齿轮的许用接触应力N Z —接触疲劳寿命因数,如图7-27取N Z =1.6lim H σ—接触疲劳极限,如图7-28,取lim H σ=600H S —接触疲劳强度安全因数,见表7-10,取H S =1.2[σH ]=800MpaσH =600Mpa ≤[σH ]=800Mpa第五章 齿条的设计5.1齿条的设计[6]根据齿轮齿条的啮合特点:(1) 齿轮的分度圆永远与其节圆相重合,而齿条的中线只有当标准齿轮正确安装时才与其节圆相重合.(2) 齿轮与齿条的啮合角永远等于压力角.因此,齿条模数m=4,压力角 20=α齿条断面形状选取圆形选取齿数z =60齿顶高系数1=*an h 顶隙系数 25.0=*n C 齿顶高 h a =h *a m=1×4, h a =4 mm齿根高 h f =( h *a + c *)m , h f =(1+0.25)×4=5 mm齿高 h = h a + h f =4+5, h=9 mm最终确定齿条为650mm 长(注:专业文档是经验性极强的领域,无法思考和涵盖全面,素材和资料部分来自网络,供参考。
齿轮设计手册docx(一)2024
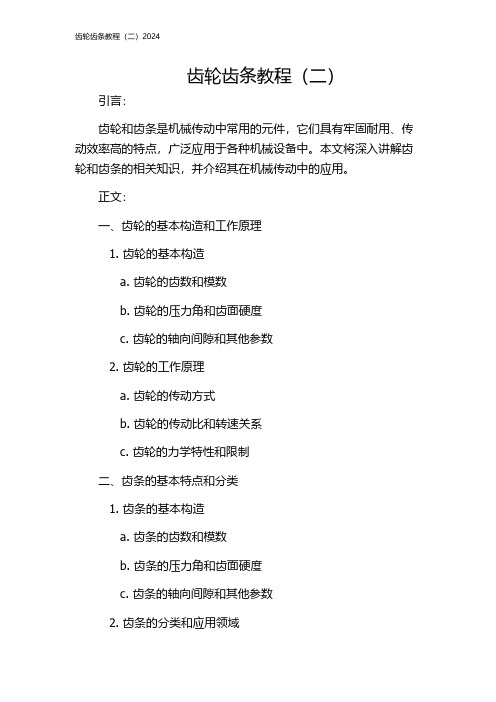
齿轮齿条教程(二)引言:齿轮和齿条是机械传动中常用的元件,它们具有牢固耐用、传动效率高的特点,广泛应用于各种机械设备中。
本文将深入讲解齿轮和齿条的相关知识,并介绍其在机械传动中的应用。
正文:一、齿轮的基本构造和工作原理1. 齿轮的基本构造a. 齿轮的齿数和模数b. 齿轮的压力角和齿面硬度c. 齿轮的轴向间隙和其他参数2. 齿轮的工作原理a. 齿轮的传动方式b. 齿轮的传动比和转速关系c. 齿轮的力学特性和限制二、齿条的基本特点和分类1. 齿条的基本构造a. 齿条的齿数和模数b. 齿条的压力角和齿面硬度c. 齿条的轴向间隙和其他参数2. 齿条的分类和应用领域a. 直齿齿条和斜齿齿条b. 齿条的传动效率和精度要求c. 齿条的常见应用场景三、齿轮和齿条的配合原理和计算方法1. 齿轮和齿条的配合原理a. 齿轮与齿条的接触及动力传递b. 齿轮和齿条的重合度和配合精度c. 齿轮和齿条的噪声和振动2. 齿轮和齿条的计算方法a. 齿轮和齿条的齿面间隙和轴向间隙b. 齿轮和齿条的传动功率和转速匹配c. 齿轮和齿条的选择和校核准则四、齿轮和齿条的加工和装配要点1. 齿轮和齿条的加工工艺a. 齿轮的铣削和齿条的滚切b. 齿轮和齿条的热处理和整形c. 齿轮和齿条的表面处理和精度修整2. 齿轮和齿条的装配要点a. 齿轮和齿条的配合间隙和预紧力b. 齿轮和齿条的润滑和密封措施c. 齿轮和齿条的对中和调整方法五、齿轮和齿条的维护和故障处理1. 齿轮和齿条的日常维护a. 齿轮和齿条的润滑和清洁b. 齿轮和齿条的负荷和温度监测c. 齿轮和齿条的磨损和裂纹检测2. 齿轮和齿条的故障处理a. 齿轮和齿条的故障类型和原因分析b. 齿轮和齿条的修理和更换方法c. 齿轮和齿条的故障预防和控制策略总结:齿轮和齿条作为机械传动中的重要构件,具有传动效率高、承载能力强的优势。
本文系统地介绍了齿轮和齿条的基本构造和工作原理,深入剖析了它们的配合原理和计算方法,并重点强调了加工和装配的要点,同时也提供了维护和故障处理的指导。
- 1、下载文档前请自行甄别文档内容的完整性,平台不提供额外的编辑、内容补充、找答案等附加服务。
- 2、"仅部分预览"的文档,不可在线预览部分如存在完整性等问题,可反馈申请退款(可完整预览的文档不适用该条件!)。
- 3、如文档侵犯您的权益,请联系客服反馈,我们会尽快为您处理(人工客服工作时间:9:00-18:30)。
第四章 齿轮设计
4.1 齿轮参数的选择[8]
齿轮模数值取值为m=10,主动齿轮齿数为z=6,压力角取α=20°,齿轮螺旋角为β=12°,齿条齿数应根据转向轮达到的值来确定。
齿轮的转速为n=10r/min ,齿轮传动力矩2221Nm ⋅,转向器每天工作8小时,使用期限不低于5年. 主动小齿轮选用20MnCr5材料制造并经渗碳淬火,而齿条常采用45号钢或41Cr4制造并经高频淬火,表面硬度均应在56HRC 以上。
为减轻质量,壳体用铝合金压铸。
4.2 齿轮几何尺寸确定[2] 齿顶高 ha =
()
()mm
h m n an n 25.47.015.2=+⨯=+*
χ,ha=17
齿根高 hf ()
()mm
c h m n n an n 375.17.025.015.2=-+⨯=-+=*
*χ
,hf=5.5
齿高 h = ha+ hf =17+5.5=22.5
分度圆直径 d =mz/cos β=mm
337.1512cos 6
5.2=⨯
d=61.348
齿顶圆直径 da =d+2ha =61.348+2×17=95.348
齿根圆直径 df =d-2hf =61.348-2×11
基圆直径
mm
d d b 412.1420cos 337.15cos =⨯== α db=57.648
法向齿厚为 5
.2364.07.022tan 22⨯⎪⎭⎫
⎝⎛⨯⨯+=⎪⎭⎫ ⎝⎛+=παχπn n n n m s
mm 593.4=×4=18.372
端面齿厚为 5253.2367.0cos 7.022tan 222⨯⎪⎪⎭⎫ ⎝⎛⨯⨯+=⎪⎭⎫
⎝⎛+=βπαχπt t t t m s
mm 275.5=×4=21.1
分度圆直径与齿条运动速度的关系 d=60000v/πn1=⇒v 0.001m/s
齿距 p=πm=3.14×10=31.4
齿轮中心到齿条基准线距离 H=d/2+xm=37.674(7.0)
4.3 齿根弯曲疲劳强度计算[11]
4.3.1齿轮精度等级、材料及参数的选择
(1) 由于转向器齿轮转速低,是一般的机械,故选择8级精度。
(2) 齿轮模数值取值为m=10,主动齿轮齿数为z=6,压力角取α=20°. (3) 主动小齿轮选用20MnCr5或15CrNi6材料制造并经渗碳淬火,硬度在56-62HRC
之间,取值60HRC.
(4) 齿轮螺旋角初选为β=12° ,变位系数x=0.7
4.3.2齿轮的齿根弯曲强度设计。
3
2114
.12P
s
F m F n z Y kT m σΦ≥
(1)试取K=3.1
(2)斜齿轮的转矩 T=2221N ·m (3)取齿宽系数
8.0=m φ
(4)齿轮齿数 61=z (5)复合齿形系数
s F Y =32
.3
(6)许用弯曲应力 FP σ=0.7⨯FE σ=0.7⨯920=644N/2
mm
FE σ为齿轮材料的弯曲疲劳强度的基本值。
n
m ≧9.9
试取
n
m =10mm
(7) 圆周速度 d=61.348mm b=
m φd=0.8×61.348=49.0784 取b=49mm
s
m dn
v /008.01000
6010
337.151000
60=⨯⨯⨯=
⨯=
ππv=0.032m/s
(8)计算载荷系数
1) 查表得 使用系数A K =1
2) 根据v=0.032m/s ,和8级精度,查表得4
.0=V K
3) 查表得 齿向载荷分布系数
15
.1=βK
4) 查表得 齿间载荷分布系数1.1==F H K K 759
.015.11.14.01=⨯⨯⨯==βK K K K K H V A
5) 修正
t
K 值计算模数
n
m =9.215故前取10mm 不变.
4.3.3齿面接触疲劳强度校核
校核公式为
u u bd KT Z Z Z Z H E H 122+=β
εσ
(1) 许用接触应力[]H σ
查表得MPa H 1650m in =σ 由图187-得
1
1=N Z
安全系数 1=H S
[]MPa
S Z H
N H H 16501
lim 1==
δδ
(2) 查表得 弹性系数 2
1180MPa Z E =.
(3) 查表得 区域系数 44.2=H Z .
(4) 重合度系数 εZ =
91
.02055
.11
1
==
α
ε
(5) 螺旋角系数
β
Z =
989.012cos cos ==
β =+⨯⨯⨯⨯⨯
⨯⨯⨯=7.41
7.4161225000759.02989.091.044.21802
H σ1513Map []=≤H σ1650
MPa
由以上计算可知齿轮满足齿面接触疲劳强度,即以上设计满足设计要求。
第五章 齿条的设计 5.1齿条的设计[6]
根据齿轮齿条的啮合特点:
(1) 齿轮的分度圆永远与其节圆相重合,而齿条的中线只有当标准齿轮正确安装时才与其
节圆相重合.
(2) 齿轮与齿条的啮合角永远等于压力角.
因此,齿条模数m=10,压力角
20=α
齿条断面形状选取圆形
选取齿数z =28,螺旋角
8=β
端面模数 mm
m m t 5253.28cos /5.2cos /=== β 10.1012 端面压力角 367
.08cos /20tan cos /tan === βααt
法面齿距
=
n P π
mm
m n 85.75.214.3=⨯= 31.4
端面齿距
mm
m P t t 929.75253.214.3=⨯==π =31.716
齿顶高系数 1
=*an h 法面顶隙系数 25
.0=*n C
齿顶高 ()
()mm
h m h n an n a 25.47.013=+⨯=+=*χ 17.85
齿根高
mm
c h m h n n an n f 375.1)7.025.01(5.2)(=-+⨯=-+=**χ 5.5
齿高 h = ha+ hf =23.35
法面
齿
厚
mm
m S n n n n 593.45.2364.07.022tan 22=⨯⎪⎭⎫
⎝⎛⨯⨯+=⎪⎭⎫ ⎝⎛+=παχπ18.372
端
面
齿
厚
mm
m S t t t t 275.55253.2367.0cos 7.022tan 222
=⨯⎪⎭⎫ ⎝⎛⨯⨯+=⎪⎭⎫ ⎝⎛+=βπαχπ21.1
第六章 齿轮轴的设计[4] 由于齿轮的基圆直径
=
b d 57.65,数值较小,若齿轮与轴之间采用键连接必将对轴和齿轮的
强度大大降低,因此,将其设计为齿轮轴.由于主动小齿轮选用20MnCr5材料制造并经渗碳淬火,因此轴的材料也选用20MnCr5材料制造并经渗碳淬火.
查表得:20MnCr5材料的硬度为60HRC,抗拉强度极限[]MPa B 1100=σ,屈服极限
[]MPa S 850=σ,弯曲疲劳极限[]MPa 5251=-σ,剪切疲劳极限[]MPa 3001=-τ,转速
n=10r/min 根据公式[5]
[]36
.150
2.025
2.033
1=⨯=≥T T d τ
忽略磨损,根据能量守衡,作用在齿轮齿条上的阻力矩为
328.8r M N m
=⋅,作用在齿
轮上的轴向力为
328.8
sin 20sin 2012.239.15r M F N r =
==,
作用在齿轮上的切向力为
328.8
cos 20cos 2033.779.15r M F N r =
==
弯曲疲劳强度校核
1-σ=F/2r π=33.77/3.14=⨯250.43MPa<MPa 525
剪切疲劳强度校核
1-τ=F/2r π=33.77/3.14240.672MPa ⨯=<300MPa
抗拉强度校核 满载时的阻力矩为
328.8r M N m
=⋅
齿轮轴的最小直径为d=8mm ,在此截面上的轴向抗拉强度为
B σ=F/2r π=155.1/3.141⨯42=229.0MPa<1100Mpa
本设计选择齿轮轴直径 D=20。