淬火介质的淬火冷却过程
淬火介质冷却过程中的数值计算

淬火介质冷却过程中的数值计算淬火技术是一种常用的金属热处理工艺,旨在改变金属的组织结构以提高其机械性能。
淬火介质冷却(MICC)过程包含在介质内部金属的冷却过程,这是淬火介质最重要的环节。
这个过程是决定淬火介质最终成品质量的重要因素,因此其介质冷却特性的计算变得尤为重要。
在MICC过程中,介质内的金属集体会受到外界的热流,但介质会缓慢的释放热量,使金属逐渐冷却,从而影响金属的组织结构和性能。
有多种不同的淬火介质,他们具有不同的物理特性,例如热传导率、热容量、比热等,都会影响MICC过程的特性,因此需要进行介质冷却特性的计算。
为了研究淬火介质冷却过程,需要采用数值计算的方法来模拟介质冷却过程。
数值计算方法在模拟复杂物理场中的微观过程中具有重要的作用,可以有效的提取热传导方程的精确解,从而更准确的模拟介质冷却过程。
由于MICC过程具有复杂的物理特性,数值计算方法显得尤为重要,以便更准确的计算介质冷却特性,从而优化淬火介质的成品质量。
具体而言,介质冷却特性的计算采用逐步迭代的方法,使用有限元的方法研究介质内金属的变形和热量转移的全过程。
先使用有限元方法,建立出包含介质-金属复合体系的有限元模型,之后再通过数值的方法计算得出介质冷却特性的参数,例如热传导率、热容量等。
在这个过程中,要考虑多种参数,例如介质原始温度、冷却温度时间变化等。
为了得到更准确的计算结果,需要采用高精度的方法,例如改进的全正则化技术,改善存在的参数精度,从而使计算更准确。
通过数值计算MICC过程可以得到准确的介质冷却特性参数,给出合理的介质淬火参数,提高产品质量。
多种数值的技术方法,可以更准确的模拟介质冷却的过程,使金属在热处理过程中得到合理的冷却,达到理想的淬火介质质量要求。
因此,数值计算技术在淬火介质冷却过程中显得尤为重要,可以为金属热处理提供准确的参考依据,提高淬火介质的质量。
通过数值计算得出介质冷却特性参数,更准确地模拟MICC过程,从而使淬火介质的成品质量和性能得到提高。
淬火介质冷却过程中的数值计算

文 章 编 号 :07—1 10  ̄X(02 0 —0 12 4 2 0 )4 0 4 —0
淬 火 介 质 冷 却 过 程 中的 数 值 计 算
胡 志 东 , 晓 莉 鲍
.
( 武汉理工 大学 材料 科学与工程学院 , 湖北 武汉 4 0 化情况来 分析淬火介 质的冷 却能力 。着重论 述 了测得探 头 中心温 度之 后 , 反推
现在 已知 导 热微 分 方 程 , 应 的初 始 条 件 和 对 中心点 温度 , 要反 推 出边 界 条 件 即表 面 温度 值 。 需 人 们 提 出 了多 种方 案 构 建 此 时 的数 学 模 型 , 此处 介 绍 反 问题解 析 法 , 点 分析 有 限差 分 法 。 重
2 1 反 问题解 析 法 .
维普资讯
第 2 卷第 4期 4
胡 志东等 : 淬火介 质冷却过程 中的数值计算
13 4
阶导 数 , 易 产 生较 大 的误 差 。 容 对 于银 探 头 , 述 级数 收 敛很 快 , 般 求前 几 上 一 阶导 数 即可 。但 不 锈 钢 材 料 的探 头 导 热 性 差 、 导 温 系数 小 , 级 数形 式 精 确 收敛 很慢 , 使 在进 行 多 次
是 圆 柱 探 头 的 半 径 。此 边 界 条 件 是 建 立 数 学模 型 需要 求 解 的量 。
初 始 条件 : t r r ; ( , )I 0= t 6
式中, 6 t是探头放人加 热炉 中冷却前 的初 始 温 度 , r =0时 刻探 头 各 点 温度 相 同。 在 除上面条件外 , 探头 的中心温度 t r 可 以 ) ( 通过实验装置 , 比较精确地测得 , 也是已知条件。 t( )= t r r , 0 r ( , )I;
淬火介质、淬火加热温度及冷却方法介绍

淬火介质、淬火加热温度及冷却方法介绍淬火工艺是将钢加热到AC3或AC1点以上某一温度,保持一定时间,然后以适当速度冷却获得马氏体和(或)贝氏体组织的热处理工艺。
淬火的目的是提高硬度、强度、耐磨性以满足零件的使用性能。
淬火工艺应用最为广泛,如工具、量具、模具、轴承、弹簧和汽车、拖拉机、柴油机、切削加工机床、气动工具、钻探机械、农机具、石油机械、化工机械、纺织机械、飞机等零件都在使用淬火工艺。
(1)淬火加热温度淬火加热温度根据钢的成分、组织和不同的性能要求来确定。
亚共析钢是AC3+(30~50℃);共析钢和过共析钢是AC1+(30~50℃)。
亚共析钢淬火加热温度若选用低于AC3的温度,则此时钢尚未完全奥氏体化,存在有部分未转变的铁素体,淬火后铁素体仍保留在淬火组织中。
铁素体的硬度较低,从而使淬火后的硬度达不到要求,同时也会影响其他力学性能。
若将亚共析钢加热到远高于AC3温度淬火,则奥氏体晶粒回显著粗大,而破坏淬火后的性能。
所以亚共析钢淬火加热温度选用AC3+(30~50℃),这样既保证充分奥氏体化,又保持奥氏体晶粒的细小。
过共析钢的淬火加热温度一般推荐为AC1+(30~50℃)。
在实际生产中还根据情况适当提高20℃左右。
在此温度范围内加热,其组织为细小晶粒的奥氏体和部分细小均匀分布的未溶碳化物。
淬火后除极少数残余奥氏体外,其组织为片状马氏体基体上均匀分布的细小的碳化物质点。
这样的组织硬度高、耐磨性号,并且脆性相对较少。
过共析钢的淬火加热温度不能低于AC1,因为此时钢材尚未奥氏体化。
若加热到略高于AC1温度时,珠光体完全转变承奥氏体,并又少量的渗碳体溶入奥氏体。
此时奥氏体晶粒细小,且其碳的质量分数已稍高与共析成分。
如果继续升高温度,则二次渗碳体不断溶入奥氏体,致使奥氏体晶粒不断长大,其碳浓度不断升高,会导致淬火变形倾向增大、淬火组织显微裂纹增多及脆性增大。
同时由于奥氏体含碳量过高,使淬火后残余奥氏体数量增多,降低工件的硬度和耐磨性。
淬火介质的冷却曲线、冷却性能及选用
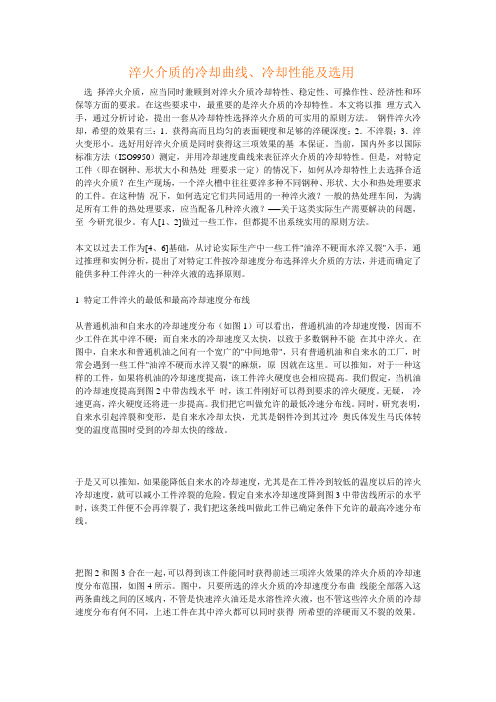
淬火介质的冷却曲线、冷却性能及选用选择淬火介质,应当同时兼顾到对淬火介质冷却特性、稳定性、可操作性、经济性和环保等方面的要求。
在这些要求中,最重要的是淬火介质的冷却特性。
本文将以推理方式入手,通过分析讨论,提出一套从冷却特性选择淬火介质的可实用的原则方法。
钢件淬火冷却,希望的效果有三:1.获得高而且均匀的表面硬度和足够的淬硬深度;2.不淬裂;3.淬火变形小。
选好用好淬火介质是同时获得这三项效果的基本保证。
当前,国内外多以国际标准方法(ISO9950)测定,并用冷却速度曲线来表征淬火介质的冷却特性。
但是,对特定工件(即在钢种、形状大小和热处理要求一定)的情况下,如何从冷却特性上去选择合适的淬火介质?在生产现场,一个淬火槽中往往要淬多种不同钢种、形状、大小和热处理要求的工件。
在这种情况下,如何选定它们共同适用的一种淬火液?一般的热处理车间,为满足所有工件的热处理要求,应当配备几种淬火液?──关于这类实际生产需要解决的问题,至今研究很少。
有人[1、2]做过一些工作,但都提不出系统实用的原则方法。
本文以过去工作为[4、6]基础,从讨论实际生产中一些工件"油淬不硬而水淬又裂"入手,通过推理和实例分析,提出了对特定工件按冷却速度分布选择淬火介质的方法,并进而确定了能供多种工件淬火的一种淬火液的选择原则。
1 特定工件淬火的最低和最高冷却速度分布线从普通机油和自来水的冷却速度分布(如图1)可以看出,普通机油的冷却速度慢,因而不少工件在其中淬不硬;而自来水的冷却速度又太快,以致于多数钢种不能在其中淬火。
在图中,自来水和普通机油之间有一个宽广的"中间地带",只有普通机油和自来水的工厂,时常会遇到一些工件"油淬不硬而水淬又裂"的麻烦,原因就在这里。
可以推知,对于一种这样的工件,如果将机油的冷却速度提高,该工件淬火硬度也会相应提高。
我们假定,当机油的冷却速度提高到图2中带齿线水平时,该工件刚好可以得到要求的淬火硬度。
淬火冷却介质的特性曲线及应用

冷却特性曲线的说明淬火介质的冷却过程分三个阶段:蒸汽膜阶段、沸腾冷却阶段、对流冷却阶段(见下图所示)。
用符合ISO9950标准的ivf冷却特性测试仪测出的冷却特性曲线(如下图)有几个特征值对淬火油的淬硬能力有重要影响。
第一个是油蒸汽膜冷却阶段向沸腾冷却阶段转变的温度,即图中A点对应的温度,叫做(上)特征温度;第二个是出现最高冷却速度的温度,即图中B点对应的温度;第三个是最高冷却速度值,即B点对应的冷却速度值;第四个是对流开始温度,即C点对应的温度。
如何从冷却特性选用淬火介质热处理淬火介质,用的首先是它的冷却性能。
因此,在确定介质的类别后,我们主张按介质的冷却特性来选择介质的品种。
比如,当我们确定应当选用快速淬火油后,具体的品种就应当根据工件特点和热处理要求从油的冷却速度分布上去选。
不管选用何种淬火介质,大致都可以按以下五条原则进行选择。
一看钢的含碳量多少── 含碳量低的钢有可能在冷却的高温阶段析出先共析铁素体,其过冷奥氏体最易发生珠光体转变的温度(即所谓"鼻尖"位置的温度)较高,马氏体起点(Ms)也较高。
因此,为了使这类钢制的工件充分淬硬,所用的淬火介质应当有较短的蒸汽膜阶段,且其出现最高冷却速度的温度应当较高。
相反,对含碳量较高的钢,淬火介质的蒸汽膜阶段可以更长些,出现最高冷却速度的温度也应当低些。
二看钢的淬透性高低——淬透性差的钢要求用冷却速度快的淬火介质,淬透性好的钢则可以用冷却速度慢一些的介质。
通常,随着钢的淬透性提高,过冷奥氏体分解转变的“C”曲线会向右下方移动。
所以,对淬透性差的钢,选用的淬火介质出现最高冷却速度的温度应当高些;而淬透性好的钢则低些。
有些淬透性好的钢过冷奥氏体容易发生贝氏体转变,要避开其贝氏体转变,也要求有足够快的低温冷却速度。
三看工件的有效厚度大小——如果工件的表面一冷到Ms点,就立即大大减慢介质的冷却速度,则工件内部的热量向淬火介质散失的速度也就立即放慢,这必然使工件表面一定深度以内的过冷奥氏体冷不到Ms点就发生非马氏体转变,其结果,淬火后工件只有很薄的马氏体层。
淬火时间、介质以及冷却方式的选择

淬火加热过程中,需要使用确定的内容有很多,例如淬火时间、淬火介质、冷却方法等等都需要根据加工工件的特性来进行选择与确定的。
本文就来从这三个方面具体介绍一下,淬火时间、介质以及冷却方式的选择方法。
一、淬火时间的确定淬火加热的时间应该包括工件整个截面加热到预定淬火温度,并使之在该温度下完成组织转变、碳化物溶解和奥氏体成分均匀化所需的时间,因此,淬火加热时间包括升温和保温两段时间。
在实际生产中,只有大型工件或装炉量很多情况下,才把升温时间和保温时间分别进行考虑。
一般情况下把升温和保温两段时间通称为淬火加热时间。
当把升温时间和保温时间分别考虑时,由于淬火温度高于相变温度,所以升温时间包括相变重结晶时间。
保温时间实际上只要考虑无溶解和奥氏体成分均匀化所需时间即可。
在具体生产条件下,淬火加热时间常用经验公式计算,通过试验最终确定。
常用公式为:加热时间=加热系数*装炉量修正系数*工件有效厚度二、淬火介质的确定淬火介质的选择,首先应该按照工件所采用的材料及其淬透层深度的要求,根据该种材料的端淬曲线,通过一定的图表来进行选择。
若仅从淬透层深度角度考虑,凡是淬火烈度大于按淬透层深度所要求的淬火烈度的淬火介质都可采用;但是从淬火应力变形开裂的角度考虑,淬火介质的淬火烈度越低越好。
所以,选择淬火介质的第一个原则应是在满足工件淬透层深度要求的前提下,选择淬火烈度最低的淬火介质。
结合过冷奥氏体连续冷却转变曲线及淬火本质选择淬火介质时,还应考虑其冷却特性,即淬火介质应作如下选择:在相当于被淬火钢的过冷奥氏体最不稳定区有足够的冷却能力,而在马氏体转变区其冷却速度却很缓慢。
此外,淬火介质的冷却特性在使用过程中应该稳定,长期使用和存放不易变质,价格低廉,来源丰富,且无毒及无环境污染。
在实践中,往往把淬火介质的选择与冷却方式的确定结合起来考虑。
例如,根据钢材不同温度区域对冷却速度的不同要求,在不同温度区域采用不同淬火烈度的淬火介质的冷却方式;又如为了破坏蒸气膜,以提高高温区的冷却速度,采用强烈搅拌或喷射冷却的方式等等。
淬火介质冷却过程中的数值计算

淬火介质冷却过程中的数值计算淬火是一种重要的热处理工艺,它通过对金属材料进行抗拉力强度和抗压强度的强化,来改善材料的力学性能,使其在受力状态下更加稳定。
然而,如何确定淬火工艺参数以及淬火过程中各项参数的变化规律,仍然存在未解决的问题。
通常情况下,为了避免材料在淬火过程中产生热损耗,使淬火获得较好的效果,采取冷却介质冷却的方法,这种方法可以确保材料受到稳定的热流,并且热损耗较小,淬火效果较好。
本文的主要内容是研究冷却介质冷却过程中的数值计算方法,通过计算来验证淬火过程中的温度分布、温度时间曲线以及淬火效果的变化情况,为进一步优化淬火工艺提供依据。
首先,在研究过程中,首先要分析淬火过程中材料内部微观结构及其力学特性,并将其以一定的数学模型以及相应的数值求解方法进行研究。
根据材料的微观结构特性和淬火温度对金属材料表面及内部热量传递规律,建立适当模型,确定模型的参数,利用数值计算方法来求解,得出淬火过程中材料的圆柱状表面温度及其温度时间曲线的变化规律。
其次,在淬火过程中,采用冷却介质冷却的方法,从而使材料受到稳定的热流,并降低热损耗。
为了确定冷却介质冷却过程中各参数的变化规律,我们可以通过采用数值计算的方式,计算冷却介质流体的温度、速度分布,从而确定冷却介质的热效果和热损耗,为淬火工艺的优化提供技术支持。
最后,本文将对数值计算方法进行深入的研究,以确定淬火过程中温度分布、温度时间曲线以及淬火效果的变化情况,计算出冷却介质冷却过程中参数的变化规律,分析淬火工艺参数及其优化,为金属材料在淬火过程中获得较好的淬火效果提供参考和启发。
综上所述,研究冷却介质冷却过程中的数值计算,不仅可以分析淬火过程中材料表面及内部热量传递规律,并确定冷却介质流体的温度、速度分布,还能为淬火过程中的温度分布、温度时间曲线以及淬火效果的变化情况,提供参考和启发,为优化淬火工艺提供重要的依据。
淬火的冷却方式_理论说明以及概述

淬火的冷却方式理论说明以及概述1. 引言1.1 概述淬火是金属热处理中一项重要的工艺,在材料的强度和硬度提升方面起着关键作用。
淬火的冷却方式是决定材料性能的关键因素之一。
本文旨在理论上探讨不同冷却方式对材料性能的影响,并介绍常见的淬火冷却方式及其原理。
此外,我们还将分析选择和优化淬火冷却方式时需要考虑的因素。
1.2 文章结构本文分为五个部分进行阐述,分别是引言、冷却方式的理论说明、热处理中常用的淬火冷却方式介绍、淬火冷却方式选择与优化考虑因素分析以及结论与展望。
1.3 目的本文旨在为读者提供关于淬火冷却方式及其理论基础的详细说明,并介绍常见的淬火方法。
同时,我们还将分析选取合适冷却方式时需要考虑的因素,帮助读者了解如何在实际应用中进行选择和优化。
最后,通过对当前研究现状进行总结并展望未来发展方向,我们希望激发更多的研究兴趣并推动淬火冷却方式领域的进一步突破。
2. 冷却方式的理论说明2.1 理论基础在热处理过程中,淬火是一个关键步骤,它通过快速冷却来改变材料的结构和性能。
淬火冷却方式的选择取决于材料的类型、要求以及零件尺寸和形状复杂度等因素。
不同的冷却方式具有不同的原理和效果。
2.2 不同冷却方式的原理2.2.1 油淬火油淬火是一种较为常见的淬火方式。
其原理是通过将工件迅速放入预热至适当温度的油液中,使工件表面温度迅速下降,产生快速冷却效果。
由于油具有良好的热导性能,可以快速吸收工件表面的热量,从而使得工件表面达到较高硬度,并形成均匀的组织结构。
2.2.2 水淬火水淬火与油淬火相比,具有更快的冷却速率和更高的硬化效果。
其原理是将工件浸入水中,并迅速吸收热量来进行快速冷却。
由于水具有很高的热传导性能,可以迅速从工件表面吸收热量,使工件温度迅速下降。
水淬火可以在较短时间内形成较高的硬度和均匀的组织结构,但也容易产生过快冷却引起的裂纹和变形问题。
2.2.3 高压气体淬火高压气体淬火是一种使用惰性气体(例如氮气或氦气)进行淬火的方式。
- 1、下载文档前请自行甄别文档内容的完整性,平台不提供额外的编辑、内容补充、找答案等附加服务。
- 2、"仅部分预览"的文档,不可在线预览部分如存在完整性等问题,可反馈申请退款(可完整预览的文档不适用该条件!)。
- 3、如文档侵犯您的权益,请联系客服反馈,我们会尽快为您处理(人工客服工作时间:9:00-18:30)。
淬火介质的淬火冷却过程
1 蒸汽膜冷却阶段
当红热的工件浸入淬火介质后,淬火介质会受热发生汽化并立即在其表面形成一层蒸汽膜,这层蒸汽膜的导热率很低,工件的热量主要通过蒸汽膜的辐射和传导作用来传递出去.因此工件在该阶段冷却速度比较缓慢. 蒸汽膜阶段持续时间的长短,主要取决于淬火介质的构成成份.淬火介质具有非常短的蒸汽膜阶段是非常重要和必需的.首先可以有效避免被处理零件发生不希望的组织转变(非马氏体组织);其次,可以实现零件上不同位置的均匀冷却,能够有效降低组织转变应力,从而减少变形.
2 沸腾冷却阶段
经过一段时间,零件表面上的蒸汽膜开始破裂(蒸汽膜维持的时间主要取决于淬火介质的构成成份及被处理零件的几何形状尺寸)并迅速进入沸腾冷却阶段.此时工件与淬火介质直接接触,淬火介质在工件表面产生强烈沸腾,工件的热量被介质汽化所吸收,散热速度加快,冷却速度很快达到最大值.工件表面温度迅速下降,而后液体沸腾逐渐减弱直至工件表面温度低于液体沸点,沸腾冷却阶段结束.
3 对流冷却阶段
当淬火工件的表面温度低于介质沸点时,进入对流冷却阶段,此时工件与介质之间的散热是以对流传导方式进行.介质本身由于温度差则产生自然对流及介质与工件之间的温差产生的热传导将工件的热量带走,这一阶段的冷却速度通常比较缓慢,但是搅拌速度的大小对其有着很大的影响.
淬火液的几个重要参数
a 蒸汽膜冷却阶段的持继时间
b 沸腾冷却阶段的温度范围
c 对流冷却阶段的冷却速度及其开始的温度
最大冷却速度并不能反映出淬火介质冷却性能的优劣, 因为它只是温度-时间曲线上的最大斜率值,而非对应于TTT转变相图上C 曲线的位置(特别是鼻尖温度位置).
淬火介质具有一个短暂的蒸汽膜阶段是相当重要和必需的,因为,当零件浸入淬火介质的最初几秒钟(有些情况下甚至在一秒钟之内)温度就会降低到500~600度左右的临界温度,此时如果蒸汽膜阶段过长,非马氏体的一些软组织如珠光体,贝氏体,托氏体等就会产生.对于合金含量较高的材料,其在TTT相图上的C曲线会右移,有时淬火介质蒸汽膜阶段较长也不会影响其最终淬火冷却效果,但是,蒸汽膜阶段的缩短有助于整个工件不同位置得到均匀冷却,能够减少应力,降低淬火变形.。