Frequency Domain Techniques for Operational Modal Analysis
数字频率计设计与实现说明书

6th International Conference on Machinery, Materials, Environment, Biotechnology and Computer (MMEBC 2016)Design and Implementation of FPGA-Based Digital Frequency MeterHUANG rui1,a1Chongqing college of electronic engineering, Chongqing, 401331,China)a*****************Keywords: FPGA, Digital Frequency Meter, Design and ImplementationAbstract. Development of EDA technology has changed the traditional electronic design methods. Widely used in large-scale FPGA and other programmable logic devices, electronic design and software programming becomes as easy and quick. Advances in electronic design technology, but also changed the traditional frequency meter design. It exists conventional frequency measurement method using an analog circuit frequency characteristic measurement frequency, but also the use of a digital pulse counting frequency measurement method. With the development of digital circuit technology to pulse count based on the law derived from a variety of improved digital frequency measurement method, measurement accuracy, fast response measurement and other aspects have been greatly improved. This paper analyzes the direct frequency measurement method and measurement principle cycle frequency measurement method, which are explained in frequency measurement method of producing ± 1 count error reasons.IntroductionFrequency meter design technology with the development of electronic circuit technology and gradually move forward, the early frequency meter design using discrete components, long design cycles, poor stability, and the finished product volume, high power consumption. Development of digital electronic technology and integrated circuits, so that the digital frequency meter wide applications, digital frequency meter circuit and microcontroller unit can be used to design and implementation. Compared to a discrete piece of frequency meter, a digital frequency meter to improve the stability, reducing the volume, but there is still a digital frequency meter circuit complex, long design cycles and other shortcomings, digital frequency meter measuring range is limited, to measure signals of different frequencies are designed to be a part of the circuit, poor flexibility. 20th century, with the development of microelectronics technology advances and computer technology, both in the mutual promotion to FPGA family, represented by application of programmable logic devices becoming more common. Programmable logic device programmed by the universal integrated circuit integrated onto a single silicon chip the size of a small, exponentially reducing the size of the circuit, and because traces short, reduce interference and increase system reliability. Because such devices can be reconstructed through software programming and its structure and working methods of the hardware, such as hardware design software design as convenient, it brings a great deal of flexibility in the design of digital circuit system. With the integration of programmable logic devices have been expanding, continuously improve and enhance their own computer-aided design technology capabilities, EDA in modern electronic system design field was born.Study of Frequency Measurement TechniqueCurrently, many methods for measuring the frequency accuracy of the measurement depends on the frequency characteristics of the frequency range of the measurement and the measured object. The measurement accuracy can be achieved, as the clock frequency depends not only on the accuracy of the criteria used, but also on measuring apparatus and methods used. Next, several types of commonly is used frequency measurement methods briefly. Direct Reading frequency measurement using the frequency characteristics of the circuit is the frequency interpretation. Direct Reading measured frequency of the bridge frequency measurement method, resonance frequency measurement method, frequency - voltage conversion frequency measurement method.Comparison of frequency measurement method is to use standard frequency fc and compare the measured frequency fx, when the standard frequency is adjusted to the measured frequency equal means zero meter (zero indicator) it means zero, and the value that is measured frequency standard frequency value. Comparison of measured frequency can be divided into the beat frequency measured and difference frequencies measured frequency models. The former is to be measured frequency signal and standard frequency signal superimposed on the linear element to generate a beat frequency. The latter is to be measured frequency signal and standard frequency signal in the non-linear mixing element. Currently beat frequency absolute error measurement frequency of about a few tenths of hertz, the frequency of the difference frequency measurement error can be orders of magnitude better than 10-5, the minimum detectable signal level of 0.1μV ~ 1μV. Beat frequency and differential frequency method in routine situations rarely used.Measurement frequency counting method is commonly used in digital frequency meter, the basic frequency measurement method. Count is the number per unit time of the periodic signal is counted. The accuracy of counting frequency measurement depends on the accuracy and error counts the reference time. The design uses a counting frequency measurements, the following notation for frequency measurement and frequency measurement principle based on several methods of counting method for detailed analysis.FPGA Structure and Working PrincipleFPGA is a field programmable logic array (Field Programmable Gate Array) abbreviation. It CPLD (Complex Programmable Logic Device, complex programmable logic devices), is currently used for a class of large-scale programmable logic devices.For combinational logic circuit, the current output is always a function of the current input, and when the fixed circuit configuration, the same amount of input, output does not change. The combinational logic circuits are shown in Fig.1.Fig.1 Combinational logic circuit examplesTruth table determines the logical relationship between input and output. The truth table and random access memory link, we will see if the input A, B, C as random access memory address input A2, A1, A0, the output P, Q can be seen as corresponding to the address memory the data stored in the storage unit D1, D0. . The memory cells each store different data, data (output) Address (input) and the storage unit may be constituted of a combination of different logic. This basic principle is implemented with random access memory (RAM) programmable combinational logic. FPGA programmable logic forming method is based on this principle programmable lookup tables (LookUp Table, LUT) structure. LUT is programmable logic constitutes the smallest unit. Most of the structure is formed using FPGA-based SRAM (static random access memory) look-up table logic, SRAM is used to form the logic function generator. Currently FPGA Multi-use 4-input LUT, so every LUT can be viewed as a 4-bit address lines 16 × 1 of RAM. All possible outcomes when the user development environment by the EDA schematic or HDL language to describe a logic circuit, the development of EDA software will automatically calculate the logic circuit, and the results pre-write RAM, so that each input signal logic operation is equivalent to input an address look-up table to find the address of the corresponding content, then the output can.FPGA-Based Frequency Meter DesignFrequency measurement and display the entire frequency meter control module is the core module for the fully digital circuit, using FPGA devices using VHDL programming to achieve. Frequency measurement part of multi-period synchronous frequency measurement method which achieve equal precision frequency measurement, measurement accuracy only and the reference frequency signal frequency, accuracy and relevant gate opening time, and frequency of the signal is independent, enabling a wide range of equal precision frequency measurement. The signal frequency measurement portion from the signal shaping module, as all pulse counting frequency measurement can only receive pulse signal, the signal must be shaped to form a pulse signal and the signal with the frequency. Reference frequency measurement part (clock) signal generated by the "reference frequency (clock) signal modules." Gate signal generator preset gate signal, because it is programmed, long can be programmed to modify all open gate signal. Operator by the formula fx = (Nx / Nc) • fc calculate the frequency value of the measured signal, the operator of multiplication and division operations include two operations. The display control section includes a BCD code converter, decoder latch two sub-modules. Frequency operator is obtained in binary form, to be displayed in decimal form and it must be BCD code converter, in the form of BCD code to decimal. Frequency meter display portion using 7-segment, so the decoder, the latch complete display decoder BCD code, and also has stored decoding function.The module generates a reference frequency signal frequency measurement using the standard clock pulse signal, also known as the clock signal module. The module uses a crystal oscillator and the corresponding hardware circuit to generate the standard clock signal, in addition to providing a reference clock signal frequency signal frequency measurement section 1 of the counter, but also provides the timing clock signal to the gate signal generator.The form of the signal is varied, based on the pulse count after the frequency measurement can only accept pulse frequency signal, the signal must be shaped to form the measured signal with the pulse signal frequency to frequency values measuring. Frequency response characteristic of the signal shaping module also determines the frequency measurement frequency range of the upper frequency.To simplify the design, frequency meter to display only the integer portion of the measured signal frequency value. Display module uses six seven-segment LED display. Because the seven-segment decoder, the latch circuit has the frequency measurement display module design is completed, the six digital tube directly to the FPGA pins to the corresponding output, but also consider the issue of digital drive tube.Power modules provide the required standard for the entire voltage frequency meter modules. After the power module 220V AC power input, transformer rectifier, regulator device through the output DC voltage required by the system stable.Frequency Meter Design and Implementation of the Functional ModulesFrequency measurement and display control module design using top-down design approach. First, the module is according to the functions are divided into several sub-modules, and then were using VHDL, and finally through the top-level design file to each sub-module assembled together to complete frequency measurement and display control functions.A reference frequency signal is measured based on the frequency, and in the design of the reference frequency signal is also used as a timing clock signal multiplier, divider, BCD code converters, etc. Cyclone series FPGA devices contained in the present design uses high-performance embedded analog phase-locked loop (DPLL performance is far superior), the phase-locked loop (PLL) can be synchronized with the clock signal input, and the input clock as PLL reference implementation, and the input clock frequency multiplier or do 1 to 32 division. Compared with the clock directly from the external, internal clock this chip can reduce the clock delay and clock distortion, reduce chip interference, but also can improve the set-up time and holdtime clock.Although the measured signal is a periodic signal, its form may be varied. But the frequency measurement signal module can only be measured in the form of pulses, so before the measurement to the measured signal shaping, the different forms of signals organized into periodic pulse signal.Frequency measurement system consists of different chips, each chip required supply voltage have different requirements, so the requirements of the power supply module to provide multiple voltage value. FPGA devices are used in this design Altera's EP1C3T144C8, core voltage of the device is 1.5V, I / O voltage of 3.3V, FPGA need to provide + 1.5V and + 3.3V dual voltage; inverting oscillator circuit 74LS04 devices require + 5V voltage; LM361 the standard voltage Vcc is + 5V, V + and V- voltage range is wide, V + requires 5V ~ 15V, V- between -6V ~ -15V.The design of frequency values are measured by the six seven-segment LED display. Since the latch function display decoder and decoding of digital values in the FPGA design has been completed, so the FPGA output can directly access input digital tube display frequency value. However, due to limited FPGA drive capability, it said only a theoretical point of view, the actual application, but also to access the digital front tube drive circuit, here we use ULN2003 as digital tube driver.ConclusionFrequency meter is one of the commonly used electronic measuring equipment. With the development of electronic technology, design methodology frequency meter are gradually moving forward. Discrete pieces from the early to the integrated circuit, LSI, this process must have the appropriate design features components to complete. When the development of electronic design EDA technology, the emergence of large-scale, ultra-large-scale programmable logic device, the electronic circuit includes a frequency meter design becomes more simple and convenient, and without changing the hardware structure on the basis and may be changed according to design requirements design, different functions and even complete systems with the same hardware circuit design. Based on the analysis and comparison of several commonly used based on the frequency measurement method, synchronous frequency measurement method according to the design need to use a multi-cycle frequency meter design. As a result of EDA design technology, most of the design work is done on the computer and logic simulation is completed by the middle of the computer. References[1] W. Zhou. Systematic Reseach on High-Accuracy Frequency Measurements and Control.Shizuoka University.Doctor Dissertation, 2000:15-24,90-96[2] M.A.A .Sour, H.I.Saleh. An FPGA Inplem Entation Guide for Some Different TypesOfserial-Parallel Multiplier Structures. Microelectronics Fournal, 2000, 31(3):161-168[3] W.Zhou. Some New Method for Precision Time Interval Measurement. Proceedings Of The1977Ieee International Frequency Control Symposium, 1997,418-421[4] R.A.James, F. Gallgray. Vhdl Design Expression and Synthesis of Vhdl. Cambridge: HarvardUniversity Press, 2001[5] C.Altera. Configuration Devices For Sram-Based Lut Devices. 2002.[6] F.W.John. Digital Design Principles And Practices,2001.[7] M.M.Mano. Digital Design, 3rd Ed. Prentice Hall Usa,2002.。
Finite field polynomial multiplication in the frequency domain with application to elliptic

Dual-frequency ferromagnetic resonance

a r X i v :c o n d -m a t /0604519v 1 [c o n d -m a t .m t r l -s c i ] 21 A p r 2006Dual-frequency ferromagnetic resonanceY.Guan and W.E.BaileyMaterials Science Program,Department of Applied Physics,Columbia University,New York,New York 10027(Dated:February 5,2008)We describe a new experimental technique to investigate coupling effects between different layers or modes in ferromagnetic resonance (FMR).Dual FMR frequencies are excited (2-8GHz)simul-taneously and detected selectively in a broadband RF circuit,using lock-in amplifier detection at separate modulation frequencies.I.INTRODUCTIONFerromagnetic resonance (FMR)precession of ferro-magnetic alloys and heterostructures is technologically important since it determines the GHz dynamics of spin electronic devices.Recently,novel long-ranged dynamic coupling mechanisms between layers in heterostructures,through the transient excitation of spin currents,have been observed experimentally(1).Some of these pro-cesses could be elucidated if motions of individual lay-ers can be excited independently,allowing the effects of higher amplitude motion at one layer to be characterized in the resonance at an opposite layer.Experiments on driven FMR modes in ferromagnetic multilayers so far have typically focused on the situation with single drive excitation.Dual-drive excitations can-not be found in the literature except in a few studies of nonlinear interactions between magnetostatic waves in yttrium-iron-garnet films(2;3).We have developed a dual-frequency FMR technique to study interactions be-tween FMR modes.Through the adjustment of pumping power at mode 1(excited at f 1),we can examine effects on FMR line intensity,width,or shape at mode 2(excited at f 2).In this article,we describe the apparatus for dual-frequency FMR measurements.FMR is excited at two frequencies using dual RF sources,combined at a power divider,and delivered to the ferromagnetic sample using a broadband coplanar waveguide (CPW).The response of individual FMR modes is detected by modulating each RF source at a separate low modulation frequency and locking in to these two frequencies with separate lock-in amplifiers.The technique is validated with a Ni 81Fe 19thin film sample,where dual-frequency FMR is proved to be selective of resonance frequency.With this technique,investigations have been made in a Ni 81Fe 19/Cu/Co 93Zr 7multilayer,where some influence of pumped Ni 81Fe 19precession on the Co 93Zr 7resonance may be seen.II.APPARATUSThe block diagram of the experimental setup of dual-frequency FMR is shown in Fig.1,where broadband (2-8GHz)swept-field ferromagnetic resonance (FMR)is measured.Lock-in amplifier detection through frequencymodulation is used in our FMR measurements.Apart from the dual frequency capability,our measurements are similar to conventional FMR cavity measurements(4),al-though network analyzers are often used instead of lock-in amplifier for phase-sensitive detection in conventional broadband FMR spectrometers(5).The microwave sources consist of two independently controllable frequency sweepers:RF source 1and RF source 2.RF source 1is a home-built,fixed-frequency source at 2.3GHz (f 1),variable in output from -50to 22dBm.We used a filtered amplified higher harmonic of a 88MHz signal from a Waveteck 3000signal with FM capability.RF source 2is a Wiltron 6668B sweep generator operated in cw mode,with tunable frequency (f 2)in the range of 0-40GHz,variable output from -50to 15dBm,and FM capability.The dual microwave generators are used to generate dual rf signals (f 1,f 2)simultaneously.The two independent rf sources modu-lated at separate frequencies (f 1mod ,f 2mod )are combined with a Anaren 42020broadband power combiner/divider (2-8GHz),which attenuates each input by 3dB in trans-mission,and then delivered to the ferromagnetic thin film sample through a lithographic coplanar waveguide (CPW)with a 100µm center conductor width.The RF field delivery configuration here is similar to that used in PIMM (pulsed inductive microwave magnetometer)measurements(6),substituting cw microwave sources for the pulse generator.The thin film sample is placed film-side down onto the top of the CPW,with a thin layer of photoresist spin-coated onto the film to prevent it from shorting the CPW.The CPW,used to pump the thin film sample with com-bined microwave (2-8GHz)excitations from two synthe-sized microwave generators,is constructed by standard lithographic techniques and placed inside a Fe core elec-tromagnet.The electromagnet has a gap of ∼2cm and a maximum field of ∼1.0Tesla at 40Ampere,controlled by parallel KEPCO-BOP-20/20M current sources.The Fe core electromagnet provides applied magnetic bias field along the center conductor of CPW,which is measured directly using a transverse hall probe monitored by a Lakeshore 421Gaussmeter.Transmitted rf signals through the magnetic thin film sample are detected at a microwave diode (0-18GHz),the output of which is sent to the A inputs of two lock-in amplifiers (lock-in 1of SR810,and lock-in 2of SR830).The sine outputs of the lock-in amplifiers provide the modulation to the transmitted rf signals at separate mod-ulation frequencies:f1mod(∼120Hz)for f1,and f2mod(∼540Hz)for f2.A microcomputer equipped with a GPIB bus communicates with the SR810/830and the Wiltron 6668B;analog inputs(±10V)at the SR830read the corrected output of the Lakeshore421Gaussmeter,and parallel analog outputs(±5V)control the Kepco power supplies.All these features allow the system to be fully automated.In operation,the dual-frequency FMR measurement can sweep frequencies at f2andfields H B,while monitor-ing the diode signals at f1mod(f1)and f2mod(f2).Power levels at f1are set manually through a variable attenua-tor.A high-precision(Keithley2000)DMM,also under GPIB control,was available to monitor the DC diode signals in the same measurements.FIG.1(Color online)Block diagram of the experimental setup of dual-frequency FMR.III.EXPERIMENTA single layer sample of Ni81Fe19(25nm)and a trilayer structure of Ni81Fe19(25nm)/Cu(20nm)/Co93Zr7(25 nm),were grown by UHV magnetron sputtering from al-loy targets at a base pressure of4×10−9torr onto Si/SiO2 substrates.A20Oe depositionfield was applied to in-duce unidirectional anisotropy in thefilm plane.More details on deposition conditions can be found in our pre-vious work(7).Conventional broadband FMR measurements(RF source1is off,and RF source2is on)were made on both Ni81Fe19and Ni81Fe19/Cu/Co93Zr7thinfilm sam-ples at several selected frequencies(from0to5GHz)to determine the Kittel relations(8)between microwave fre-quency(ωp/2π)and resonancefield(H res).For in-plane magnetization in a thinfilm,the Kittel relation can be expressed as(8):ω2p≈µ20γ2M s(H res+H k),(1) where H k is an effectivefield due to anisotropy.The Ni81Fe19thinfilm sample was then measured using dual-frequency FMR,where two different FMR modes were excited independently,using separate reso-nance frequencies(f1=2.3GHz,f2=4.5GHz)atfixed field.In the Ni81Fe19/Cu/Co93Zr7trilayer sample,both the Ni81Fe19layer and the Co93Zr7layer were excited near resonance simultaneously,choosing H res for f1= 2.3GHz,through the adjustment of f2(to3.8GHz).The effects of variable power at f1on the Co93Zr7resonance at f2were investigated.IV.RESULTS AND DISCUSSIONThe results of conventional broadband FMR measure-ments on both Ni81Fe19and Ni81Fe19/Cu/Co93Zr7thin film samples are presented in Fig.2.We show(ωp/2π)2 as a function of H res.f1and f2denote the selected fre-quencies of excited FMR modes in dual-frequency FMR measurements on the same samples(shown in Fig.3and Fig.4).Solid lines are linearfits based on Eq.(1).Two branches were observed for the Ni81Fe19/Cu/Co93Zr7 thinfilm sample,corresponding mostly to the separate resonances of the Ni81Fe19layer and the Co93Zr7layer, with some weak ferromagnetic coupling(∼5Oe). Validation of frequency selectivity in dual-frequency FMR is shown in Fig. 3.Two different FMR modes were excited in the Ni81Fe19thinfilm sample at two se-lective resonance frequencies(f1=2.3GHz,f2=4.5 GHz)and then detected selectively using dual lock-in amplifiers(lock-in1,lock-in2),respectively.Two ab-sorption peaks were observed for the total transmitted signal,where the positions and widths of the two absorp-tion peaks correspond closely with those found selectively at f1and f2.Dual-frequency FMR measurement on the Ni81Fe19/Cu/Co93Zr7trilayer thinfilm sample is presented in Fig.4,where the effects of pumped Ni81Fe19precession at f1=2.3GHz were investigated on the Co93Zr7resonance at f2= 3.8GHz.This frequency(f1)sets the Ni81Fe19layer into FMR at H B =72.5Oe.With rf power of RF source2fixed at a low value(-5dBm),we varied the pumping power of RF source1,from-20dBm to+10dBm,measured at the diode.As shown in Fig.4,two separate FMR modes were observed for each value of the pumping power of RF source1,where the mode at the low-field side corresponded primarily to the resonance of the Co93Zr7layer.Some variations can be seen in both the line intensity and the symmetry of the Co93Zr7FMR modes as a function of power pumped into the Ni81Fe19FIG.2(Color online)(a)Kittel plot of the single layer of Ni81Fe19thinfilm.(b)Kittel plot of the trilayer structure of Ni81Fe19/Cu/Co93Zr7thinfilm.Solid lines are linearfits.FIG.3(Color online)Dual-frequency FMR spectra(f1=2.3 GHz,f2=4.5GHz)of Ni81Fe19thinfilm using dual lock-in detection.resonance.It is also evident that the high power excited at f1has no discernible influence on the Ni81Fe19 resonance measured at f2,as expected.However,a quantitative estimate of any dynamic coupling between Ni81Fe19and Co93Zr7layers could not be made,as the residual influence of the static(∼5Oe)coupling could not be excluded.It is additionally important to drive the Ni81Fe19resonance symmetrically over the low-field region,which requires a second variable frequency source at f1.By using dual-frequency FMR technique,we can se-FIG.4(Color online)Dual-frequency FMR spectra at f2= 3.8GHz as a function of pumped power at f1=2.3GHz in Ni81Fe19(25nm)/Cu(20nm)/Co93Zr7(25nm)thinfilm.The field H B for simultaneous FMR of Ni81Fe19and Co93Zr7is indicated.lectively excite several different FMR modes in a fer-romagnetic alloy and heterostructures,and the nature of coupling interactions between multiple FMR modes could thus be probed.We remark that the technique pre-sented could be extended tofixed-field,swept-frequency measurement,or to track the Kittel resonance at f1as field H res is swept.With much higher power amplifica-tion and some cooling capability,nonlinear interactions between magnetostatic spin-wave modes(MSSW)could be studied as well.Finally,the frequency range can be extended to20GHz,or even to40GHz,through the use of different power dividers.V.CONCLUSIONA new experimental technique,dual-frequency ferro-magnetic resonance(FMR),has been developed to in-vestigate coupling effects between different FMR modes. This new technique is able to excite different FMR modes simultaneously and independently,while separating the properties of each.VI.ACKNOWLEDGEMENTSThis work was partially supported by the Army Re-search Office with Grant No.ARO-43986-MS-YIP,and the National Science Foundation with Grant No.NSF-DMR-02-39724.This work has used the shared experi-mental facilities that are supported primarily by the MR-SEC(Columbia)program of the National Science Foun-dation under Contract No.NSF-DMR-0213574. References[1]Y.Tserkovnyak,A.Brataas,G.E.W.Bauer,and B.I.Halperin,Rev.Mod.Phys.77,1375(2005).[2]D.J.Mar,T.L.Carroll,L.M.Pecora,J.F.Heagy,andF.J.Rachford,J.Appl.Phys.80,1878(1996).[3]D.J.Mar,T.L.Carroll,L.M.Pecora,and F.J.Rachford,J.Appl.Phys.81,5734(1997).[4]B.Heinrich,Ultrathin Magnetic Structures II,edited byB.Heinrich and J.A.C.Bland(Springer-Verlag,Berlin,1994).[5]V.P.Denysenkov and A.M.Grishin,Rev.Sci.Instrum.74,3400(2003).[6]A.Kos,T.Silva,and P.Kabos,Rev.Sci.Instrum.73,3563(2002).[7]Y.Guan,Z.Dios,D.A.Arena,L.Cheng,and W.E.Bailey,J.Appl.Phys.97,10A719(2005).[8]Charles Kittel,Introduction to Solid State Physics(Wiley,2005)。
电化学交流阻抗测试拟合-2
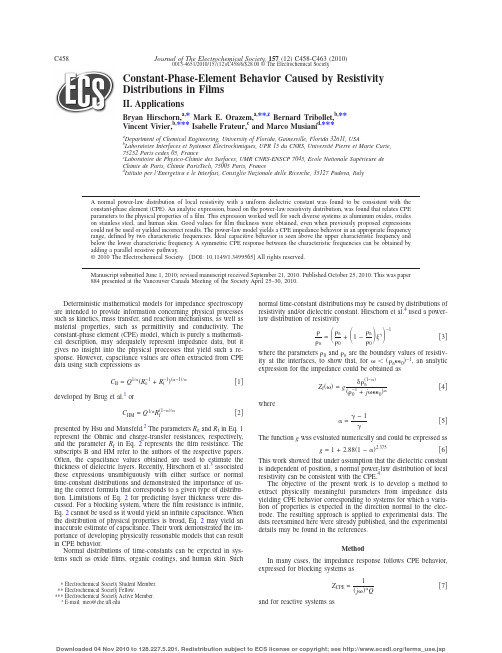
ͩ ͩ ͪͪ
͑1−␣͒ ␦␦
−1
͓3͔
where the parameters 0 and ␦ are the boundary values of resistivity at the interfaces, to show that, for Ͻ ͑ ␦⑀⑀0͒−1, an analytic expression for the impedance could be obtained as Z f͑ ͒ = g where
−1 ͑␣−1͒/␣ CB = Q1/␣͑R−1 e + Rt ͒
normal time-constant distributions may be caused by distributions of resistivity and/or dielectric constant. Hirschorn et al.4 used a powerlaw distribution of resistivity ␦ ␥ ␦ = + 1− ␦ 0 0
␣ ͑−1 0 + j ⑀⑀0͒
͓1͔
͓4͔
developed by Brug et al.1 or CHM =
͑1−␣͒/␣ Q 1/␣R f
͓2͔
presented by Hsu and Mansfeld.2 The parameters Re and Rt in Eq. 1 represent the Ohmic and charge-transfer resistances, respectively, and the parameter Rf in Eq. 2 represents the film resistance. The subscripts B and HM refer to the authors of the respective papers. Often, the capacitance values obtained are used to estimate the thickness of dielectric layers. Recently, Hirschorn et al.3 associated these expressions unambiguously with either surface or normal time-constant distributions and demonstrated the importance of using the correct formula that corresponds to a given type of distribution. Limitations of Eq. 2 for predicting layer thickness were discussed. For a blocking system, where the film resistance is infinite, Eq. 2 cannot be used as it would yield an infinite capacitance. When the distribution of physical properties is broad, Eq. 2 may yield an inaccurate estimate of capacitance. Their work demonstrated the importance of developing physically reasonable models that can result in CPE behavior. Normal distributions of time-constants can be expected in systems such as oxide films, organic coatings, and human skin. Such
ImageProcessing3-1-ImageEnhancement(PointProcessing)bwz

16 of 52
Point Processing Example: Negative Images (cont…)
17 of 52
Thresholding(阈值法、二值法)
Thresholding transformations are particularly useful for segmentation in which we want to isolate an object of interest from background
思考:为什么前面提到可以提高对比度,这里又说可以压缩 动态范围?
In the following example the Fourier transform of an image is put through a log transform to reveal more detail
26 of 52
假定我们感兴趣的灰度级范 围是[r1, r2]:
Note that (r1-r2)<(s1-s2). The gray values in the rang [r1, r2] is stretched into the rang[s1, s2].
对比度拉伸的目的是增加输入图像的动态灰度级范围
21 of 52
Images taken from Gonzalez & Woods, Digital Image Processing (2002)
s=
1.0 r > threshold 0.0 r <= threshold
18 of 52
Thresholding
s=
1.0 r > threshold 0.0 r <= threshold
PolyMAX

LMS PolyMAXA Revolution in Modal Parameter EstimationCurrent Limitations of Experimental Modal Analysis Experimental Modal Analysis (EMA) is currently one of the key technologiesin structural dynamics analysis. Based on the academic fundaments of system identification, it has evolved to become a “standard” approach in mechanical product development. Essential inthis evolution is that modal analysis research has, from the start, taken the point of view of industrial applicability, focusing on solving the specific problems related to testing and modeling large industrial structures. The merit of each new method or new approach has always been checked against the added value it brought in terms of helping the application engineers to derive better models. The result is that EMA is now considered as a “commodity” tool, continuously expanding its application base.While the range of applications where EMA is used is continuously expanding, also the complexity of the tested structures is increasing. While inthe past isolated structures with low damping were analyzed, modal analysis is nowadays also explored on complex structures with high damping, such as on trimmed car bodies. Next to this, EMA has evolved to a standard tool for Finite Element Model updating and is exploited in combination with numerical technologies for hybrid engineering. These recent evolutions have highlighted the current limitations of the EMA process:The task of selecting the correct modelorder and discriminating betweenspurious and structural system poles isquite complex, in particular in the caseof high-order and/or highly dampedstructures. This inevitably results inhighly operator-dependant results, andrequires numerous iterations in theanalysis procedure.Whereas the quality of the currentmodal parameter estimationtechnology is satisfying for undampedor slightly damped structures, thereis an increasing need for better modalparameters estimations for highlydamped structures.Instead of a variety of parameterestimation techniques, each optimizedfor a specific test situation, there is aneed for a single reliable and robustmethod that can be used in a widevariety of applications.In an area where many critics claimno substantial advances were to beexpected, the new LMS LMS PolyMAXmethod brings a revolutionary modalparameter estimation technique thatis easy to use, quick to perform,substantially reduces operator-dependantjudgment, and that delivers high qualitymodal parameter estimations, even oncomplex data.In this application note, the LMS PolyMAXmethod was used on two “historically”difficult data sets: a trimmed car body(high damping) and flutter data (highdata noise). This application note alsoincludes a summary on the analyticalfoundation of the LMS PolyMAX method.•••Figure 1: Stabilization diagrams obtained byapplying different parameter estimation methodsto the Porsche data: (Top) FDPI; (Middle) LSCE;(Bottom) the new LMS PolyMAX method.Using LMS PolyMAX on a Trimmed Car BodyA typical example of a challenging modal analysis application is the identification of a trimmed car. The trim material turns a nicely resonating car body into a highly damped system with large modal overlap. In the present example, data from a Porsche 911 Targa Carrera 4 was used. The accelerations of the fully equipped car were measured at 154 degrees of freedom (DOF), while 4 shakers were simultaneously exciting the structure. This gives a total of 616 FRFs (Frequency Response Functions) used in the modal analysis procedure. More details about the test can be found in [1].The data were analyzed in a frequencyrange from 3.5 to 30 Hz using threetechniques:The frequency domain direct parameteridentification (FDPI) technique, whichhas traditionally been used to analyzedata from highly damped structures[2,3,4,5].The least squares complex exponential(LSCE) method, which is the “industry-standard” time domain estimationmethod [2,3,6].The new LMS PolyMAX method.Figure 1 shows the stabilization diagramsfor the 3 methods. FDPI yields aclearer diagram than LSCE, confirmingthe common assumption that FDPI is•••the preferred method in case of highdamping. However, both are clearlyoutperformed by the LMS PolyMAXmethod: especially at lower frequenciesit is much clearer than the FDPI diagramand also a larger number of stable polesis found.For the subset of LMS PolyMAX polesthat have an FDPI counterpart, Table 1shows that the resulting estimations forfrequency and damping are very close.Also the mode shapes are very similar,which is evidenced by the MAC valuesrepresented in Figure 2.The excellent identification resultsobtained with the LMS PolyMAXmethod are confirmed by comparing theFDPI method LMS PolyMAX method [Hz] [%] [Hz] [%]Figure 3: Comparison of the measured FRFs (grey/green) with FRFs synthesized from the identified modal model (black/red). The FRFs between 2 of the 4inputs and 1 typical output are shown.Figure 4 Stabilization diagrams obtained by applying different parameter estimation methods to data from a partially trimmed car: (Left) FDPI; (Right) the new LMS PolyMAX method.Whereas in the previous example, anexperienced user could have used FDPI to identify a subset of the structural modes, in this case the FDPI stabilization diagram is hardly to be interpreted at all. Again, LMS PolyMAX shows a much better, easy to interpret, stabilization diagram.measured FRFs with the FRFs that can be synthesized from the modal parameters. Figure 3 shows both measured and synthesized FRFs at one response location (FRFs with respect to 2 out of 4 input points). Overall, an impressive 93% correlation between measured and synthesized FRFs was reached.Figure 4 shows the FDPI and LMS PolyMAX stabilization diagrams ofanother trimmed body dataset, where 2 inputs and 500 outputs were measured.Figure 6: Stabilization diagrams obtained by applying different parameter estimation methods to the flight flutter test data: (Left) LSCE; (Right) the new LMS PolyMAX method.LMS PolyMAX: Historical backgroundThe LMS PolyMAX method is a further evolution of the least-squares complex frequency-domain (LSCF) estimation method. That method was first introduced to find initial values for the iterative maximum likelihood method [7]. The method estimates a so-called common-denominator transfer function model [8]. Quickly it was found that these “initial values” yielded already very accurate modal parameters witha very small computational effort [7, 9,10]. The most important advantage of the LSCF estimator over the available and widely applied parameter estimation techniques [2] is the fact that very clear stabilization diagrams are obtained. A thorough analysis of different variantsof the common-denominator LSCF method can be found in [10]. A complete background on frequency-domain system identification can be found in [11].It was found that the identified common-denominator model closely fitted the measured frequency response function (FRF) data. However, when converting this model to a modal model by reducing the residues to a rank-one matrix using the singular value decomposition (SVD), the quality of the fit decreased [9]. Another feature of the common-denominator implementation is thatthe stabilization diagram can only be constructed using pole information (eigenfrequencies and damping ratios). Neither participation factors nor mode shapes are available at first instance [12]. The theoretically associated drawback is that closely spaced poles will erroneously show up as a single pole.These two reasons provided the motivation for a polyreference versionof the LSCF method, using a so-called right matrix-fraction model. In this approach, also the participation factors are available when constructing the stabilization diagram. The main benefits of the polyreference method are the facts that the SVD step to decompose the residues can be avoided and that closely spaced poles can be separated. The method was introduced in [12, 13]. Herewe briefly review the theory.Figure 7: Comparison of the measured FRFs (green/grey) with FRFs synthesized from the identified modal model (black/red). (Top) Sensor at the wing tip; (Bottom) Sensor at the back of the plane.LMS PolyMAX: Theoretical Foundation Data modelJust like the FDPI (Frequency-domain direct parameter identification) method1 [4,5], the LMS PolyMAX method uses measured FRFs as primary data. Time-domain methods, such as the polyreference LSCE method2 [6], typically require impulse responses (obtained as the inverse Fourier transforms of the FRFs) as primary data. In the LMSPolyMAX method, following so-called right matrix-fractionmodel is assumed to represent the measured FRFs:(1)where is the matrix containing the FRFsbetween all m inputs and all l outputs; are thenumerator matrix polynomial coefficients; are the denominator matrix polynomial coefficients and is the model order. Please note that a so-called -domain model (i.e. a frequency-domain model that is derived from adiscrete-time model) is used in (1), with:(2)whereis the sampling time.Equation (1) can be written down for all values of thefrequency axis of the FRF data. Basically, the unknown modelcoefficientsare then found as the Least-Squares solution of these equations (after linearization). More details about this procedure can be found in [12,13].Poles and modal participation factorsOnce the denominator coefficients are determined, the poles and modal participation factors are retrieved as theeigenvalues and eigenvectors of their companion matrix:(3)The modal participation factors are the last m rows of; the matrix contains the (discrete-time) poles on its diagonal. They are related to theeigenfrequencies[rad/s] and damping ratios [-] asfollows ( •* denotes complex conjugate):(4)This procedure is similar to what happens in the time-domain LSCE method and allows constructing a stabilization diagram for increasing model orders and using stability criteria for eigenfrequencies, damping ratios and modal participation factors.Mode shapesAlthough theoretically, the mode shapes could be derivedfrom the model coefficients, we proceed in a different way.The mode shapes can be found by considering the so-calledpole-residue model:(5)where n is the number of modes; denotes complexconjugate transpose of a matrix; are the modeshapes;are the modal participation factors andare the poles (4). are respectively the lower and upper residuals modeling the influence of the out-of-band modes in the considered frequency band. The interpretationof the stabilization diagram yields a set of poles andcorresponding participation factors Since the modeshapes and the lower and upper residuals are the only unknowns, they are readily obtained by solving (5) in a linear least-squares sense. This second step is commonly called least-squares frequency-domain (LSFD) method [2,3]. The same mode-shape estimation method is normally also used in conjunction with the time-domain LSCE method.1This method is implemented as “Frequency – domain MDOF” in Cada-X [3].2This method is implemented as “Time – domain MDOF” both in b and Cada-X [3].,.Comparing LMS PolyMAX with other Modal Parameter Estimators LMS PolyMAX versus LSCEAs may be clear from previous section, the LMS PolyMAX method proceeds along similar lines as the polyreference LSCE time-domain method:Establishment of a set of linear equations for themaximum required model order, from which the matrixpolynomial coefficients can be computed in a least-squares sense.Construction of a stabilization diagram by solving the eigenvalue problem (3) for increasing model orders. The information regarding eigenfrequencies, damping ratios and modal participation factors is contained in this diagram.Based on the user-interpretation of the stabilizationdiagram, computation of the mode shapes and the lower and upper residuals by solving (5) in a least-squares sense.The difference between LSCE and LMS PolyMAX lies in the first step. LSCE uses impulse responses to find the polynomial coefficients, whereas LMS PolyMAX requires frequency response functions.However, this seemingly small difference has bigconsequences for the modal parameter estimation process. It turns out that the new LMS PolyMAX estimator yields extremely clear stabilization diagrams making it very simple to select the “physical” poles. In the LSCE method, the non-physical (and sometimes even the physical) poles tend to “wander” in the stabilization diagram, especially at large model orders. The LMS PolyMAX method has the interesting property that the non-physical poles are estimated with a negative damping ratio so that they can be excluded before plotting them. Such a clear diagram does not mean that some of the poles are missing; on the contrary, more poles can be found with the LMS PolyMAX method, as evidenced by the examples in this application note. Other validation studies also revealed that the LMS PolyMAX method has no problems in correctly estimating modes having a low damping ratio. It is sometimes stated that time-domain methods are preferred in case of low damping, andfrequency-domain methods in case of high damping. The LMS PolyMAX method excels in both cases.LMS PolyMAX versus other frequency-domain methodsTypical for many frequency-domain parameter estimation methods is that they involve the inversion of a matrix containing powers of the frequency-axis of the data.•••Therefore one quickly runs into numerical conditioningproblems and severe constraints apply to both the frequency range as the model order range of the analysis. In the past, it has been proposed to use an orthogonal polynomial basis for the frequency-domain model to solve the numerical problems. However this increases significantly the computational time and memory requirements.The LMS PolyMAX method does not suffer from numerical problems as it is formulated in the -domain (i.e. afrequency-domain model that is derived from a discrete-time model), whereas the existing frequency-domain methods use a Laplace-domain formulation (i.e. a frequency-domain model that is derived from a continuous-time model). In LMS PolyMAX, the frequency axis that extends betweenand is shifted and mapped into a half unit circle in thecomplex plane (2):, (6)Similar to other frequency-domain methods, the LMSPolyMAX method involves the inversion of a matrix containing powers of the frequency-axis of the data. The main advantage of LMS PolyMAX is that taking powers of the -variable does not increase the range of the values, as it boils down to a rotation in the complex plane: . As a result, the LMS PolyMAX method can deal with a large frequency range and very large model orders, speeding up the modal parameter estimation process considerably, as in many cases the complete frequency-band of interest can be processed at once.There was some common belief that the numericalconditioning of frequency-domain methods is worse than time domain methods and that broadband analyses are preferably performed in time-domain [2]. When using the LMS PolyMAX approach, these statements are definitely no longer true.Computational efficiencyThe advantages discussed here have no price in terms of computational time: LMS PolyMAX is as fast as LSCE. LSCE became the industry-standard because of its high speed even for a very large number of measured outputs. A lot of research efforts were spent to achieve this computational efficiency. On current PC platforms, calculation and display of the stabilization diagram for a typical full car body model (like the trimmed car body example discussed here) is in the order of some seconds.References [1] VAN DER AUWERAER H., C. LIEFOOGHE, K. WYCKAERT AND J.DEBILLE. Comparative study of excitation and parameter estimation techniques on a fully equipped car. In Proceedings of IMAC 11, the International Modal Analysis Conference, 627–633, Kissimmee (FL), USA, 1–4 February 1993[2] HEYLEN W., S. LAMMENS AND P. SAS. Modal Analysis Theory and Testing. Department of Mechanical Engineering, Katholieke Universiteit Leuven, Leuven, Belgium, 1995.[3] LMS INTERNATIONAL. The LMS Theory and Background Book, Leuven, Belgium, 2000.[4] LEMBREGTS F., J. LEURIDAN, L. ZHANG AND H. KANDA. Multiple input modal analysis of frequency response functions based direct parameter identification. In Proceedings of IMAC 4, the International Modal AnalysisConference, 589–598, Los Angeles (CA), USA, 1986.[5] LEMBREGTS F., R. SNOEYS AND J. LEURIDAN. Application and evaluation of multiple input modal parameter estimation. International Journal of Analytical and Experimental Modal Analysis, 2(1), 19–31, 1987.[6] BROWN D.L., R.J. ALLEMANG, R. ZIMMERMAN AND M. MERGEAY. Parameter estimation techniques for modal analysis. Society of Automotive Engineers, Paper No. 790221, 1979.[7] GUILLAUME P., P. VERBOVEN AND S. VANLANDUIT. Frequency-domain maximum likelihood identification of modal parameters with confidenceintervals. In Proceedings of ISMA 23, the International Conference on Noise and Vibration Engineering, Leuven, Belgium, 16–18 September 1998.[8] GUILLAUME P., R. PINTELON AND J. SCHOUKENS. Parametric identification of multivariable systems in the frequency domain - a survey. In Proceedings of ISMA 21, the International Conference on Noise and Vibration Engineering, 1069–1082, Leuven, Belgium, 18–20 September 1996.LMS PolyMAX: Executing Modal Testing Jobs at Unrivaled Speedand AccurayWith the new LMS PolyMAX method,a breakthrough in Experimental Modal Analysis has been achieved. Whereas the method equals or even outperforms the current standard LSCE technique on common test structures, it brings a solution for problems -like trimmed body and flutter data- where current EMA technology has shown its limits. By substantially simplifying the analysis process, LMS PolyMAX will be enjoyed by many new users in the field. For advanced applications, its powerfulclear stabilization, and the quality of the modal parameter estimation are real breakthroughs, widely expanding theapplication range and drastically reducing the number of iterations needed.LMS PolyMAX is not yet-another-parameter-estimation-technique, but a global solution for Experimental Modal Analysis.The new LMS PolyMAX is part of the LMS b Structures solution for Modal testing and analysis. LMS b Structures is an integrated suite of applications covering the range of structural dynamic engineering completely. Dedicated applications serve impact hammer measurements, single shaker testing and advanced multiple-input, multiple-output (MIMO) analysis. These starting points measure the motion/force transfer or Frequency Response Functions (FRF) required for modal analysis. A dedicated modal analysis module automatically accesses these measurements to compute the modal parameters: mode shape vector, resonant frequency, damping factor and modal mass. All applications are tightly integrated so that data streams smoothly from acquisition, through analysis, to display and reporting.[9] VAN DER AUWERAER H., P. GUILLAUME, P. VERBOVEN AND S. VANLANDUIT. Application of a fast-stabilizing frequency domain parameter estimation method. ASME Journal of Dynamic Systems, Measurement, and Control, 123(4), 651–658, 2001.[10] VERBOVEN, P. Frequency domain system identification for modal analysis. PhD Thesis, Vrije Universiteit Brussel, Belgium, 2002.[11] PINTELON R. AND J. SCHOUKENS. System Identification: a FrequencyDomain Approach. IEEE Press, New York, 2001.[12] GUILLAUME P., P. VERBOVEN, S. VANLANDUIT, H. VAN DER AUWERAER AND B. PEETERS. A poly-reference implementation of the least-squares complex frequency-domain estimator. In Proceedings of IMAC 21, the International Modal Analysis Conference, Kissimmee (FL), USA, February 2003.[13] PEETERS B., P. GUILLAUME, H. VAN DER AUWERAER, B. CAUBERGHE, P. VERBOVEN AND J. LEURIDAN.Automotive and aerospace applications of the LMS PolyMAX modal parameter estimation method. In Proceedings of IMAC 22, Dearborn (MI), USA, January 2004.LMS International, Empowering Engineering InnovationLMS enables customers to engineer functional performance targets intotheir products, creating and maintaining distinctive brand values. LMS’ unmatched understanding of the product development process is captured through a unique combination of products and services supporting physical and virtual product development: Test systems, CAE software products and engineering services. Critical attributes such as noise and vibration, ride, handling, motion, acoustics and fatigue are turned into a competitive advantage.LMS bLMS b is the world’s first integrated software environment for the functional performance engineering of critical design attributes, such as noise and vibration, ride, handling, comfort, safety and durability.LMS bLMS b provides the most complete portfolio of applications for test-based noise and vibration engineering. It comprises modules for structural, rotating machinery and acoustic testing and analysis, environmental testing, reporting and data sharing.LMS Engineering ServicesThrough its Engineering Services Division, LMS provides vehicle development support from overload contracting and troubleshooting, technology transfer, up to co-development projects.。
Frequency reuse technique for a high data rate sat

专利名称:Frequency reuse technique for a high datarate satellite communication system发明人:Rosen, Harold A.,Reinhardt, VictorS.,Strodtbeck, Andrew L.,Vollbrecht, JenniferL.申请号:EP94307753.7申请日:19941021公开号:EP0650271A3公开日:19960228专利内容由知识产权出版社提供专利附图:摘要:Frequency reuse (70) and data coding methods (80, 90) for use in a high datarate satellite communication system (10). The frequency reuse method (70) provides for dual polarization and spatial reuse of transmit and receive beams to provide for a twelve-fold increase in the effective bandwidth and number of users that may be supported by the system (10). Transmit and receive antennas provides multiple, inter-leaved transmit and receive antenna beams. Digital input data at a source user terminal is coded and transmitted from a source user terminal on one of the plurality of receive antennas is demodulated. The received data is demodulated demodulated and is routed so that it may be transmitted to a destination user terminal. The data is then remodulated, multiplexed, and transmitted to the destination user terminal on one of the plurality of transmit beams. The transmitted data is decoded at the destination user terminal to produce the output data. The input and output data processed by the system is digital, and the coding (concatenated coding forward error correction processing) is employed to reduce the sensitivity of communicated data to interference. The presently preferred encoding method comprises Reed-Solomon encoding (42) input data, interleaving (43) the encoded data, and convolutionally encoding (44) the interleaved data and then time division multiplexing (45) and modulating (46) the data. The presently preferred decoding method comprises demodulating (56) and demultiplexing (57) received time division multiplexed data, Viterbi decoding (58) the demultiplexed data, deinterleaving (59) the Viterbi decoded data, and Reed-Solomon decoding (60) the deinterleaved data to produce the output data. Other multiplexing schemes may alternatively be employed. The demodulating and remodulating steps regenerates a high quality digital data stream on the satellite that is communicated to the destination terminal to reduce the effects of uplink interference upon the downlink data stream.申请人:Hughes Aircraft Company地址:7200 Hughes Terrace P.O. Box 45066 Los Angeles, California 90045-0066 US 国籍:US代理机构:Jackson, Richard Eric 更多信息请下载全文后查看。
Agilent Technologies 53131A 132A 181A高性能计数器说明书

•225 MHz bandwidth (optional 1.5, 3, 5, or 12.4 GHz)•10- or 12-digit resolution with 1sgate time•GPIB interface and IntuiLink connectivity software standard •Data transfer rate of up to 200fully formatted measurements/ secondA family of universal and RF counters to meet your needsAgilent Technologies 53131A/132A/ 181A high-performance counters give you fast, precise frequency measurements at an affordable price. These counters feature an intuitive user interface and one-but-ton access to frequently used func-tions so you can make accurate measurements quickly and easily. Real-time digital signal processing technology is used to analyze data while simultaneously taking new readings, speeding measurement throughput. The technology, devel-oped for Agilent’s high-end line of modulation domain analyzers, allows the counters to gather more data for each measurement, so you get higher-resolution measurements in a fraction of the time it takes other counters. The 53131A/132A/181A counters offer built-in statistics and math functions so you can scale measure-ments and simultaneously measure and track average, min/max and standard deviation. Automated limit testing lets you set upper and lowerlimits for any measurement. An ana-log display mode lets you see at aglance whether a measurementis within pass/fail limits. The coun-ters flag out-of-limit conditions andcan generate an output signal to trig-ger external devices when a limit isexceeded. For quick access to fre-quently used tests, a single key-stroke recalls up to 20 differentstored front-panel set-ups.For computer-controlled systemsapplications, each counter includes astandard GPIB interface with fullSCPI-compatible programmabilityand a data transfer rate of up to 200fully formatted measurements persecond. The standard RS-232 talk-onlyinterface provides printer support ordata transfer to a computer througha terminal-emulation program.Agilent 53131A Universal CounterThe two-channel 53131A counteroffers 10 digits per second of fre-quency/period resolution anda bandwidth of 225 MHz. Time inter-val resolution is specified at 500 ps.An optional third channel providesfrequency measurements up to3GHz, 5 GHz, or 12.4 GHz. Standardmeasurements include frequency,period, ratio, time interval, pulsewidth, rise/fall time, phase angle,duty cycle, totalize, and peak voltage.Agilent 53132A Universal CounterFor applications requiring higherresolution, the 53132A offers thesame features and functions as the53131A, with up to 12digits/secfrquency/period resolution and150ps time interval resolution.In addition, the 53132A offersadvanced arming modes for timeinterval measurements.Agilent 53181A RF CounterOptimized for RF applications,the single-channel 10 digit/s 53181Ameasures frequency, period andpeak voltage. A digit-blanking func-tion lets you easily eliminate unnec-essary digits when you want to readmeasurements quickly. For higher-frequency measurements,choose anoptional second channel that pro-vides measurements up to 1.5GHz,3GHz, 5 GHz, or 12.4 GHz. A self-guided shallow menu makes thiscounter exceptionally easy to use. Agilent 53131A/132A/181A CountersHigh-performance, low-cost counters simplify and speed systems and bench frequency measurementsProduct Overview1981Agilent IntuiLink provides easy access to the counter’s data from your PC The Agilent 53131A/132A/181A counters capture precise frequency and time measurements. IntuiLink software allows that data to be put to work easily. You work in a famil-iar environment at all times, using PC applications such as Microsoft Excel® or Word® to analyze,inter-pret, display, print, and document the data you get from the counter. Also available is BenchLink Meter software, a standalone application. It gives you the flexibility to con-figure and run tests from your PC,making data gathering more con-venient.BenchLink Meter lets you:•configure tests, including measure-ment type, number of readings,measurement speed, and more.•choose display modes fromreal-time strip chart, histogram,readout, and table mode.•scale measurements data.•copy captured data to other pro-grams.Optional timebases offerincreased stabilityOptional timebases are availablefor 53131A/132A/181A countersto increase measurement accuracy.Option 010 provides a high stabilityoven timebase with aging of lessthan 5 x 10-10per day.3-year warrantyEach counter comes with operat-ing, programming and service man-uals, IntuiLink software, a powercord and a full 3-year warranty.Microsoft Excel and Word are US registered trademarksof Microsoft Corporation.Time BaseInternal Time Base Stability (see graph 3 for timebase contribution of measurement error)Standard Medium Oven High Oven Ultra High Oven(0°to 50°C) (Option 001)(Option 010)(Option 012 for 53132A only) Temperature Stability (referenced to 25°C)< 5 x 10-6< 2 x 10-7< 2.5 x 10-9< 2.5 x 10-9Aging Rate Per Day:< 4 x 10-8< 5 x 10-10< 1 x 10-10(after 30 days)Per Month:< 3 x 10-7 < 2 x 10-7< 1.5 x 10-8< 3 x 10-9Per Year:< 2 x 10-8Turn-on stability vs. time(in 30 minutes) < 2 x 10-7 < 5 x 10-9< 5 x 10-9referenced to 2 Hr referenced to 24 Hr referenced to 24 Hr Calibration Manual Adjust Electronic Electronic ElectronicNote that power to the time base is maintained when the counter is placed in standby via the front panel switch. The internal fan will continue to operate when in standby to maintain long-term measurement reliability.Instrument InputsInput SpecificationsChannel 1 & 2 (53131A, 53132A)1 Channel 1 (53181A)Frequency Rangedc Coupled dc to 225 MHzac Coupled 1 MHz to 225 MHz (50 Ω)30 Hz to 225 MHz (1 MΩ) FM Tolerance25%Voltage Range and Sensitivity (Sinusoid)2dc to 100 MHz20 mVrms to ±5 V ac + dc 100 MHz to 200 MHz30 mVrms to ±5 V ac + dc 200 MHz to 225 MHz40 mVrms to ±5 V ac + dc(all specified at 75 mVrmswith opt. rear connectors)3Voltage Range and Sensitivity(Single-Shot Pulse)24.5 ns to 10 nsPulse Width100 mVpp to 10 Vpp(150 mVpp with optionalrear connectors)3>10 ns Pulse Width50 mVpp to 10 Vpp(100 mVpp with optionalrear connectors)3Trigger Level2Range±5.125 VAccuracy±(15 mV + 1% of triggerlevel)Resolution 5 mVDamage Level50 Ω 5 Vrms0 to 3.5 kHz, 1 MΩ350 Vdc + ac pk3.5 kHz to 100 kHz,1 MΩ350 Vdc + ac pk linearlyderated to 5 Vrms>100 kHz, 1 MΩ 5 VrmsInput CharacteristicsChannel 1 & 2 (53131A, 53132A)1Channel 1 (53181A)Impedance1MΩor 50Ω1 MΩCapacitance30 pFCoupling ac or dcLow-Pass Filter100 kHz, switchable-20 dB at > 1 MHzInput Sensitivity Selectable between Low,Medium, or High (default).Low is approximately 2xHigh Sensitivity.1.Specifications and Characteristics for Channels 1 and2 are identical for both common and separate config-urations.2.Values shown are for X1 attenuator setting. Multiplyall values by 10 (nominal) when using the X10 atten-uator setting.3.When the 53131A or 53132A are ordered with theoptional rear terminals (Opt. 060), the channel 1 and2 inputs are active on both front and rear of thecounter. When the 53181A is ordered with theoptional rear terminal, the channel 1 input is activeon both front and rear of the counter. For this condi-tion, specifications indicated for the rear connectionsalso apply to the front connections.23Trigger Slope Positive or Negative Auto Trigger Level Range 0 to 100% in 10% steps Frequency> 100 Hz Input Amplitude> 100 mVpp(No amplitude modulation)Attenuator Voltage Range x10Trigger Rangex10Input Specifications4Channel 3 (53131A, 53132A) Channel 2 (53181A)Frequency Range Option 015100 MHz to 1.5 GHz (for 53181A only)(see Opt. 030 for addi-tional specs)Option 030100 MHz to 3 GHz Option 050200 MHz to 5 GHz Option 124200 MHz to 12.4 GHzPower Range and Sensitivity (Sinusoid)Option 030100 MHz to 2.7 GHz:-27 dBm to +19 dBm 2.7 GHz to 3 GHz:-21 dBm to +13 dBm Option 050200 MHz to 5 GHz:-23 dBm to +13 dBm Option 124200 MHz to 12.4 GHz -23 dBm to +13 dBm4.When optional additional channels are ordered withOpt. 060, refer to configuration table for Opt. 060under ordering info on page 8. There is no degrada-tion in specifications for this input, as applicable.Damage Level Option 030 5 Vrms Option 050+25 dBm Option 124+25 dBmCharacteristics Impedance 50 ΩCoupling AC VSWR<2.5:1External Arm Input Specifications 5Signal Input RangeTTL CompatibleTiming Restrictions Pulse Width > 50 ns Transition Time < 250 ns Start-to-Stop Time > 50 ns Damage Level10 VrmsExternal Arm Input Characteristics 5Impedance1 k ΩInput Capacitance 17 pFStart/Stop SlopePositive or NegativeExternal Time Base Input SpecificationsVoltage Range 200 mVrms to 10 Vrms Damage Level 10 VrmsFrequency1 MHz, 5 MHz, and 10 MHz(53132A 10 MHz only)Time Base Output SpecificationsOutput Frequency 10 MHzVoltage> 1 Vpp into 50 Ω(centered around 0 V)Measurement SpecificationsFrequency (53131A, 53132A, 53181A)Channel 1 and 2 (53131, 53132); Channel 1 (53181)Range0.1 Hz to 225 MHzChannel 3 (53131A, 53132A) Channel 2 (53181A) Option 015(53181only)100 MHz to 1.5 GHz Option 030100 MHz to 3 GHz Option 050200 MHz to 5 GHz Option 124200 MHz to 12.4 GHz (Period 2 or 3 selectable via GPIB only)Period (53131, 53132, 53181)Channel 1 and 2 (53131, 53132);Channel 1 (53181)Range4.44 ns to 10 sChannel 3 (53131A, 53132A); Channel 2 (53181A)Option 015(53181 only)0.66 ns to 10 ns Option 0300.33 ns to 10 ns Option 0500.2 ns to 5 ns Option 12480 ps to 5 nsFrequency Ratio (53131, 53132, 53181)Measurement is specified over the full signal range of each input.Results Range 10-10to 1011“Auto” Gate Time100 ms5.Available for all measurements except Peak Volts.External Arm is referred to as External Gate for some measurements.orTime Interval (53131A, 53132A) Measurement is specified over the full signal ranges6of Channels 1 and 2.Results Range-1 ns to 105sLSD500 ps (53131)/150 ps (53132)Phase (53131A, 53132A)Measurement is specified over the full signal range of Channels 1 and 2.Results Range-180°to +360°Duty Cycle (53131A, 53132A) Measurement is specified over the full signal range of Channel 1. However, both the positive and negative pulse widths must be greater than 4 ns.Results Range0 to 1 (e.g. 50% duty cyclewould be displayed as .5) 6.See Specifications for Pulse Width and Rise/FallTime measurements for additional restrictions on sig-nal timing characteristics Rise/Fall Time (53131A, 53132A)Measurement is specified over the full signalranges of Channel 1. The interval between theend of one edge and start of a similar edge mustbe greater than 4 ns.Edge Selection Positive or NegativeTrigger Default setting is AutoTrigger at 10% and 90%Results Range 5 ns to 105sLSD500 ps (53131)/150 ps(53132)Pulse Width (53131A, 53132A)Measurement is specified over the full signalrange of Channel 1. The width of the opposingpulse must be greater than 4 ns.Pulse Selection Positive or NegativeTrigger Default setting is AutoTrigger at 50%Results Range 5 ns to 105sLSD500 ps (53131)/150 ps(53132)Totalize (53131A, 53132A)Measurement is specified over the full signalrange of Channel 1.Results Range0 to 1015Resolution±1 countPeak Volts (53131A, 53132A, 53181A)Measurement is specified on Channels 1 and 2for dc signals; or for ac signals of frequenciesbetween 100 Hz and 30 MHz with peak-to-peakamplitude greater than 100 mV.Results Range-5.1 V to +5.1 VResolution10 mVPeak Volts Systematic Uncertaintyfor ac signals: 25 mV + 10% of Vfor dc signals: 25 mV + 2% of VUse of the input attenuator multiplies all voltagespecifications (input range, results range, resolu-tion and systematic uncertainty) by a nominalfactor of 10.45Gate TimeAuto Mode, or 1 ms to 1000 sMeasurement ThroughputGPIB ASCII200 measurements/s (maximum)Measurement ArmingStart MeasurementFree Run, Manual, or ExternalStop MeasurementContinuous, Single,External, or Timed Time Interval 100 µs to 10 s (53131A)Delayed Arming100 ns to 10 s (53132A)Arming Modes(Note that not all arming modes are available for every measurement function.)Auto Arming:Measurements are initiated imme-diately and acquired as fast as possible, using a minimum number of signal edges.Timed Arming:The duration of the measurement is internally timed to a user-specified value (also known as the “gate time ”).Digits Arming:Measurements are performed to the requested resolution (number of digits)through automatic selection of the acquisition time.External Arming:An edge on the External Arm Input enables the start of each measurement.Auto Arming, Timed arming modes or another edge on the External Arm Input may be used to complete the measurement.Time Interval Delayed Arming:For Time Interval measurements, the Stop Trigger condition is inhibited for a user-specified time following the Start Trigger. The 53132A offers advanced time interval arming capabilities including use of user specified time or Channel 2 events to delay both Start and Stop Triggers.Measurement LimitsLimit Checking:The measurement value is checked against user-specified limits at the end of each measurement.Display Modes:The measurement result may be displayed as either the traditional numeric value or graphically as an asterisk moving between two vertical bars.Out-of-Limits Indications:•The limits annunciator will light on the front panel display.•The instrument will generate an SRQ if enabled via GPIB.•The limits hardware signal provided via the RS-232 connector will go low for the duration of the out-of-limit condition.•If the Analog Display mode is enabled, the asterisk appears outside the vertical bars,which define the upper and lower limits.Fractional Time Base Error (see graph 3)Time base error is the maximum fractional frequency variation of the time base due to aging or fluctuations in ambient temperature or line voltage:∆f ∆f ∆fTime Base Error = (------- aging rate +------- temperature +------ line voltage)f f fMultiply this quantity by the measurement result to yield the absolute error for that measurement. Averaging measurements will not reduce (fractional)timebase error. The counters exhibit negligible sensitivity to line voltage; consequently the line voltage term may be ignored.Trigger ErrorExternal source and input amplifier noise may advance or delay the trigger points that define the beginning and end of a measurement. The resulting timing uncertainty is a function of the slew rate of the signal and the amplitude of spurious noise spikes (relative to the input hysteresis band). The (rms) trigger error associated with a single trigger point is:whereE input = RMS noise of the input amplifier: 1 mVrms (350µVrms Typical). Note that the internal measurement algorithms significantly reduce the contribution of this term.E signal = RMS noise of the input signal over a 225 MHz bandwidth (100 kHz bandwidth when the low-pass filter is enabled). Note that the filter may substan-tially degrade the signal ’s slew rate at the input of the trigger comparator.For two-trigger-point measurements (e.g. Rise Time, Pulse Width), the Trigger Errors will be referred to independently as Start Trigger Error and Stop Trigger Error.Trigger Level Timing Error (see graph 6)Trigger level timing error results from a deviation of the actual trigger level from the specified level. The magnitude of this error depends on resolution and accuracy of the trigger level circuit, input amplifier fidelity, input signal slew rate, and width of the input hysteresis band.The following equations should be summed together to obtain the overall Trigger Level Timing Error. At the "High" sensitivity input setting, the hysteresis band can be assumed to be the sensitivity of the counter input (see page 2). Reduction of input sensitivity or use of the attenuator will increase the size of this band.Input Hysteresis Error:–Trigger Level Setting Error: ±±Differential Channel ErrorThe differential channel error term stated in several Systematic Uncertainty equations accounts for channel-to-channel mismatch and internal noise. Thiserror can be substantially reduced by performing a TI calibration (accessible via the Utility Menu) in the temperature environment in which future measure-ments will be made.0.5 x Hysteresis Band Input Signal Slew Rate at Start Trigger Point 15 mV±(1% x Start Trigger Level Setting)Input Signal Slew Rate at Start Trigger Point 15 mV±(1% x Stop Trigger Level Setting)Input Signal Slew Rate at Stop Trigger Point 0.5 x Hysteresis BandInput Signal Slew Rate at Stop Trigger Point6Graph 1:Agilent 53131A/181A –Worst Case RMS Resolution 7(Automatic or External Arming)The graphs may also be used to compute errors for Period Measurements.To find the Period error (DP), calculate the frequency of the input signal (F = 1/P) and find the frequency error (DF) from the chart.Then calculate the period error as:Graph 2:Agilent 53131A/181A –Worst Case RMS Resolution 7(Time or Digits Arming)Graph 3:Timebase Error1 ns100 ns 10 µs 1 ms 100 msInput Signal Frequency or Time∆P ϫP=7.Graphs 1, 2, 4 and 5 do not reflect the effects of trigger error. To place an upper bound on the added effect of this error term, determine the frequency error from the appropriate graph and add a trigger error term as follows:Measurement StatisticsAvailable Statistics Mean, Minimum,Maximum, StandardDeviationNumber of 2 to 1,000,000. Measurements Statistics may be collectedon all measurements oron only those which arebetween the limit bands.When the Limits functionis used in conjunctionwith Statistics, N (numberof measurements) refersto the number of in-limitmeasurements. In general,measurement resolutionwill improve in proportionto N , up to the numericalprocessing limits of theinstrument.Measurements Statistics may be collectedfor all measurementsexcept Peak Volts andTotalize.General InformationSave and RecallUp to 20 complete instrument setups may be saved and recalled later. These setups are retained when power is removed from the counter.Rack Dimensions88.5 mm x 212.6 mm x (HxWxD)348.3 mmWeight 3.5 kg maximumWarranty 3 yearsPower Supply100 to 120 VAC ±10% -50,60or 400 Hz ±10% 220to 240 VAC ±10% -50or60 Hz ±10%ac Line Selection AutomaticPower Requirements170 VA maximum(30 W typical)Environment0°C to 55°C operating–40°C to 71°C storageRemote Interface GPIB (IEEE 488.1-1987,IEEE 488.2-1987)Remote SCPI-1992.0 Programming (Standard Commands Language for ProgrammableInstruments)Safety Designed in compliancewith IEC-1010, UL-3111-1(draft), CAN/CSA 1010.1EMC CISPR-11, EN50082-1,IEC 801-2, -3, -4Radiated Immunity When the product is Testing operated at maximumsensitivity (20mVrms)and tested at 3V/maccording to IEC 801-3,external 100 to 200 MHzelectric fields may causefrequency miscounts.7。
- 1、下载文档前请自行甄别文档内容的完整性,平台不提供额外的编辑、内容补充、找答案等附加服务。
- 2、"仅部分预览"的文档,不可在线预览部分如存在完整性等问题,可反馈申请退款(可完整预览的文档不适用该条件!)。
- 3、如文档侵犯您的权益,请联系客服反馈,我们会尽快为您处理(人工客服工作时间:9:00-18:30)。
Svend Gade, Nis B. Møller, Henrik Herlufsen, Hans Konstantin-Hansen Brüel & Kjær Sound and Vibration Measurements A/S, Skodsborgvej 307, DK2850 Nærum, Denmark
The measurements were taken using the Brüel & Kjær PULSE Multi-analyzer system (Type 3560), and the Modal Test Consultant (Type 7753) to create the geometry, assign the measurement points and directions (DOF’s), and capture the data. The analysis was then done using the Brüel & Kjær Operational Modal Analysis software (Type 7760), where all the advanced signal processing and modal extraction procedures were performed. MEASUREMENT PROCEDURE In this paper the use of the Operational Modal Analysis method for a 1:5 scale wind turbine wing is described. The object is a detailed model of one of the blades from a 675 kW wind turbine. The wing has been made for lab investigations of static as well as dynamic parameters. Figure (2) shows a picture of the set-up used for the measurements. The wing itself is supported by a console which is regarded as stiff compared to the wing itself.
ABSTRACT Operational Modal Analysis, also known as Output Only Modal Analysis, has in the recent years, been used for determination of modal parameters of civil engineering structures and is now becoming widely used also for mechanical structures. The advantage of the method is that no artificial excitation needs to be applied to the structure, or force signals to be measured. In this paper, the non-parametric technique based Frequency Domain Decomposition (FDD), as well as the more elaborate Enhanced Frequency Domain Decomposition (EFDD) identification technique are discussed. The methods are illustrated by measurements on a wing from a wind turbine acoustically excited by a loudspeaker in the Brüel & Kjær laboratory. INTRODUCTION Operational Modal Analysis, also known as Ambient Modal Analysis and Output Only Modal Analysis is presented here. Traditionally, measuring the input forces and the output responses for a considered linear, time-invariant mechanical system performs a modal test of a structure. The excitation usually used is transient Combined Ambient System (Impact Hammer testing), or random, burst-random, or sinusoidal (Shaker testing). The advanced signal processing Stationary Zero Structural system Loading System Mean Gaussian Responses (linear, time-invariant) tools used in the Operational Modal White Noise Analysis technique allow us now to determine the inherent properties of a mechanical structure (Resonance Frequencies, Damping, Mode Shapes), by Unknown Excitation Forces measuring only the response of the Figure 1, Combined Ambient Model structure, without using an artificial excitation. The advantage of this technique is that it provides a complete modal model under operating conditions, meaning within true boundary conditions, and actual force and vibration levels. The measurement technique is similar to the “Operating Deflection Shapes” type procedure, where one or more accelerometers are used as reference(s), and a series of roving accelerometers are used for the responses at all the Degrees of Freedom (DOF’s), or all DOF’s are just measured simultaneously. Figure (1) shows a schematic description of an ambient response system.
24 accelerometers Brüel & Kjær Type 4507 B4 with a sensitivity of 10mV/ms-2 are mounted in two rows along the wing. Two time recordings were taken, one with the accelerometers perpendicular to the surface (Z-direction) and one pointing in the direction of wing rotation (X-direction). To determine the combined modes in this twodimensional model the results from the two recordings are linked together using a tri-axial accelerometer Type 4506 with a sensitivity of 10mV/ms-2 as a reference. The wing is considered as stiff in the length direction, Y, so vibrations in this direction are disregarded. Thus Type 4506 was used as a biaxial accelerometer. The total numbers of DOF’s are 50. The data acquisition system used was a portable PULSETM platform Type 3560D composed of a 31 channel front-end for the hardware, and a laptop computer for the software. The wing was exposed to an acoustic excitation by means of a loudspeaker Brüel & Kjær Type 4224 placed beneath the wing. Although the aim is to use Operational Modal Analysis for the test the sound level was measured using a microphone pl