液相氧化环己烷制备环己酮的鼓泡塔新工艺
环己烷氧化法制环己酮装置分解反应釜的工艺放大设计
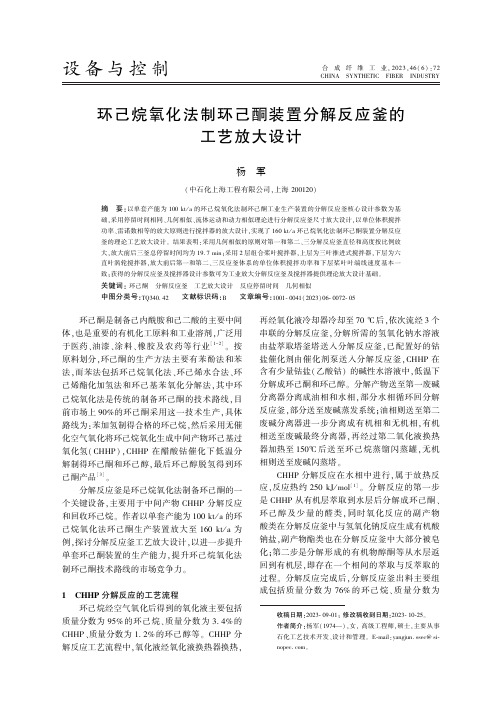
环己酮是制备己内酰胺和己二酸的主要中间
再经氧化液冷却器冷却至 70 ℃ 后,依次流经 3 个
。 按
由盐萃取塔釜塔送入分解反应釜,已配置好的钴
体,也是重要的有机化工原料和工业溶剂,广泛用
己烷氧化法环己酮生产装置放大至 160 kt / a 为
酸类在分解反应釜中与氢氧化钠反应生成有机酸
单套环己酮装置的生产能力,提升环己烷氧化法
化;第二步是分解形成的有机物醇酮等从水层返
例,探讨分解反应釜工艺放大设计,以进一步提升
钠盐,副产物酯类也在分解反应釜中大部分被皂
制环己酮技术路线的市场竞争力。
回到有机层,即存在一个相间的萃取与反萃取的
釜设计仍采用此搅拌器型式,以下层六直叶涡轮
搅拌器为主、上层三叶推进搅拌器为辅。
体现搅拌器混合传质效果的重要指标为 P d ,
体现流体运动和动力相似的重要指标为雷诺数
( Re) [6] ,因此本次放大设计采用 P d 不变的准则
对下层涡轮搅拌器的桨叶进行放大,见式(4) ; 采
用 Re 不变的准则对于上层推进式搅拌器的桨叶
0. 4
0. 7
3
2 CHHP 分解反应釜的关键设计参数
CHHP 分解反应釜的关键设计参数包括反应
小的液滴分散到主液相,若搅拌强度过低,则碱水
相在有机相中分散度低,分解反应在釜内进行不
彻底; 若搅拌强度过高,则碱水相液滴粒径太小,
在后续工序中难以从有机相中去除,影响装置运
行周期。 搅 拌 强 度 通 常 用 单 位 体 积 搅 拌 功 率
(7)
(8)
环己烷氧化制环己酮主要生产工艺及其改进情况

环己烷氧化制环己酮主要生产工艺及其改进情况摘要:介绍了当前环己烷氧化制备环己酮的主要生产工艺的优缺点以及在工艺上的改进情况。
关键词:环己烷环己酮催化氧化环己酮是一种重要的有机化工原料,其在下游市场的应用越来越广泛,成为近几年的热点产品,它是生产己内酰胺和己二酸的中间原料,也是生产各种高档油漆的重要溶剂。
随着下游产品的扩能、新建,在未来一段时间内仍有较大的市场需求。
目前在世界范围内,环己酮生产工艺中90%以上采用环己烷氧化法,该工艺方法根据使用催化剂的不同,又分为无催化氧化法和有催化氧化的钴盐法、硼酸法。
一、无催化氧化工艺无催化氧化法由法国Rhone-Ponlene公司最先开发,此法把反应过程分为两步:第一步,在160~170℃的温度条件下,环己烷与空气混合发生氧化反应,生产环己基过氧化氢;第二步,在碱性和催化剂作用下,环己基过氧化氢发生分解反应,生产环己醇、环己酮的混合物。
此法的优点是反应过程分两步进行,不使用催化剂,解决了反应器结渣的问题,反应可连续进行,氧化过程中环己基过氧化氢的收率达到95%以上;缺点是环己基过氧化氢分解需要大量的碱,环己醇、环己酮的选择性≤88%,此工艺单程转化率比较低,大约在 3.5~4%之间,工艺流程比较长,装置消耗高。
在改善此工艺方面,人们针对不同环己酮装置的特点,从改善环己基过氧化氢分解条件、提高环己烷转化率和环己醇、环己酮的收率方面,采取了以下工艺方法:1.在改变环己基过氧化氢分解条件方面:肖藻生从改变有机相和无机相的混合比例,使碱液通过外部循环和静态混合器,强化环己烷氧化混合液与含过渡金属盐的碱性水溶液的混合,将分解过程分为两步,第一步控制碱液中碱浓度在0.25~0.5 mol/L之间,第二步控制碱液中碱浓度在0.5~1.5mol/L之间,从而改善环己基过氧化氢的分解环境,使环己醇、环己酮的选择性高达94%。
2.在提高环己醇、环己酮收率方面:黄敬等从改变氧化反应器温度分布状况着手,通过改变循环环己烷进氧化反应器的入口位置和入口温度,合理的控制各个反应器的温度,达到减少环己基过氧化氢在氧化阶段的热分解,从而提高环己醇、环己酮的收率。
环己酮工艺技术
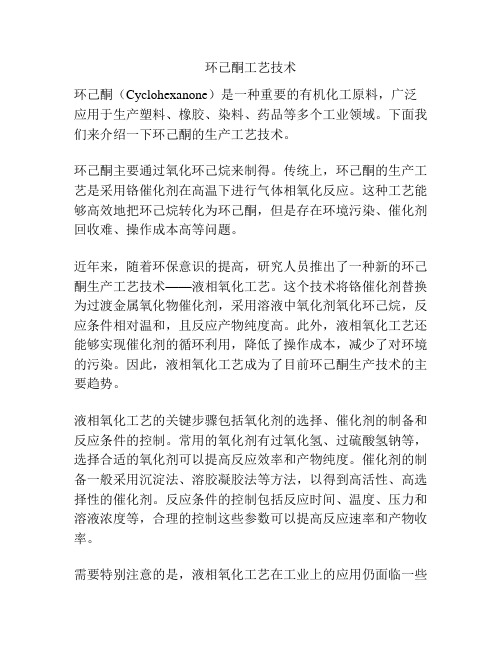
环己酮工艺技术环己酮(Cyclohexanone)是一种重要的有机化工原料,广泛应用于生产塑料、橡胶、染料、药品等多个工业领域。
下面我们来介绍一下环己酮的生产工艺技术。
环己酮主要通过氧化环己烷来制得。
传统上,环己酮的生产工艺是采用铬催化剂在高温下进行气体相氧化反应。
这种工艺能够高效地把环己烷转化为环己酮,但是存在环境污染、催化剂回收难、操作成本高等问题。
近年来,随着环保意识的提高,研究人员推出了一种新的环己酮生产工艺技术——液相氧化工艺。
这个技术将铬催化剂替换为过渡金属氧化物催化剂,采用溶液中氧化剂氧化环己烷,反应条件相对温和,且反应产物纯度高。
此外,液相氧化工艺还能够实现催化剂的循环利用,降低了操作成本,减少了对环境的污染。
因此,液相氧化工艺成为了目前环己酮生产技术的主要趋势。
液相氧化工艺的关键步骤包括氧化剂的选择、催化剂的制备和反应条件的控制。
常用的氧化剂有过氧化氢、过硫酸氢钠等,选择合适的氧化剂可以提高反应效率和产物纯度。
催化剂的制备一般采用沉淀法、溶胶凝胶法等方法,以得到高活性、高选择性的催化剂。
反应条件的控制包括反应时间、温度、压力和溶液浓度等,合理的控制这些参数可以提高反应速率和产物收率。
需要特别注意的是,液相氧化工艺在工业上的应用仍面临一些挑战。
首先,液相氧化反应需要较高的选择性,以防止副反应产生,保证产物的纯度。
其次,在催化剂循环利用过程中,需要对催化剂进行再生和处理,以减少资源浪费和环境污染。
第三,液相氧化工艺的工艺优化和生产规模化仍需进一步研究。
总体来说,环己酮的生产工艺技术正朝着更加环保、高效的方向发展。
液相氧化工艺作为一种新的技术,相比传统的气相氧化工艺具有很多优势,但仍需进一步研究和改进。
相信随着工艺技术的不断突破和创新,环己酮的生产将更加高效、环保,为各个工业领域的发展提供更好的支持。
环己酮装置工艺流程资料

2)氢气干燥压缩、分子筛再生
界区送来的氢气含水超过规定指标,也要进行脱水干燥, 氢气干燥分两步进行。
首先用低温水冷却氢气,使氢气中大部分水冷凝下来。随 后用分子筛吸附氢气中剩余的少量水,使氢气含水达到控制 指标。
干燥塔中的分子筛达到饱和后,用尾气换热器出口的尾气 进行再生,操作周期约为24小时,再生时间约8小时。
三、工艺流程明
1)苯的原处理及进料 界区外送入的苯进入苯进料预热器,加热到 60℃后进入苯 干燥塔,使苯中所含水份以苯、水共沸物的形式从塔顶蒸出, 经苯干燥塔顶冷凝器冷凝,在苯水分离器中进行苯水分离, 苯溢流回干燥塔,含微量苯的污水排往污水处理站。
脱除水分的苯从苯干燥塔底出来与进料苯在苯进料预热器 中换热,再经出料冷却器用循环水冷却至常温流入苯储槽备 用。加氢催化剂从运输槽车中卸入催化剂贮罐,贮罐用氮气 封闭。开车时,通过开车用催化剂泵把催化剂注入主反应器 底部出料管。当催化剂活性逐渐降低后,通过催化剂泵适时 补加催化剂,以维持反应活性。
来自分解釜的分解液由分解反应器出料泵抽出,送至第一 废碱分离器、第二废碱分离器和废碱最终分离器,油相分别 经过第二氧化物回收换热器、分解进料冷却器换热和进料加 热器加热至 150℃后送至环己烷蒸馏闪蒸罐。无机相则送至 废碱闪蒸塔。
9)环己烷蒸馏
环己烷精馏采用三塔二效塔精馏流程。来自第一氧化液换热器的有机液加热至 150℃后进入闪蒸罐,闪蒸产生的气相进入烷三塔上部,液相则进入烷一塔。烷 一塔再沸器的热量由中压蒸汽供给;烷一塔塔顶气相作为烷二塔再沸器的热源, 冷凝后自流入烷一塔冷凝槽,再排至烷二塔冷凝槽。烷一塔塔釜物料压入烷二塔, 烷一塔回流液由烷一、 二塔回流泵提供。烷二塔塔顶气相作为烷三塔装置再沸 器的热源,换热冷凝下来后进入烷二塔冷凝槽。由热烷泵将烷二塔冷凝槽中环己 烷送至氧化工序的热交换塔。烷二塔的回流液同样由烷一、二塔回流泵从烷二塔 冷凝槽中抽出,送至烷二塔顶部。烷二塔塔釜物料进入烷三塔,在再沸器中蒸发, 烷三塔顶出来的气体在烷塔冷凝器中冷凝,冷凝液流入烷三回流槽。未冷凝的气 体分别进入烷塔气体冷却器和烷塔尾气冷却器,经冷却水 和冷冻水冷却后,不 凝气经压缩机升压至 1.3MPa 后送至吸收塔,以回收尾气中的烷。自脱氢来的补 充环己烷加入到烷三塔回流槽中,一部分由烷三塔回流泵送回烷三塔塔顶回流, 其余则由冷烷泵抽出送到氧化工序的洗涤塔洗涤。烷三塔釜液由烷三塔釜液泵抽 出送往皂化槽。烷三塔回流槽中分离的水相用烷三塔回流槽废水泵抽出排往废水 汽提塔。
环己烷氧化制备环己酮工艺技术

Pr e p a r a t i o n 0 f c y c l 0 h e x a n 0 n e b y o x i d a t i o n o f c y c l o h e x a n e
Du an Xi a o . b i n g, Zhu Li - z h e n g
酮工 艺流 程 详 见 图 1 。
( 2 )通 过催化剂 或者碱 性条件 的作用 ,将环 己基过氧 化 氢 分 解 成 为 环 己酮 。 这 种 工 艺 最 大 的 优 点 就 是 其 氧 化 不 需 要
使用 催 化剂 ,从而避 免 了渣 滓 的产生 。反应 过程 分为 两步 , 反应 过程 明确,再加上 设备没 有渣滓可 以连 续运转工作 ,一 定程 度上 简化 了反应 步骤 。通过 这种方法 进行 环 己基过氧 化 氢 的氧 化可 以使收率达 到9 5 % 以上。但 是通 过这种方法制 备
Ab s t r a c t:Th e s y n t h e t i c me t ho d s o f c v c l o he x a n o n e a r e t h r e e ma i n me t ho d s:c y c l o he x e n e h yd r a t i o n me t h o d ,p h e n o l
h y d r o g e n a t i o n me t h o d a n d c y c l o h e x a n e o x i d a t i o n me t h o d . Th i s p a p e r ma i n l y d e a l s wi t h t h e t r a d i t i o n a l p r o c e s s o f c y c l o h e x a n o n e o x i d a t i o n
环己酮的生产工艺及技术进展

环己酮的生产工艺及技术进展2.1 环己酮传统生产工艺世界上传统的环己酮生产工艺主要有苯酚加氢法、苯加氢氧化法、环己烷液相氧化法,生产环己酮的原材料是苯和氢。
2.1.1 苯酚加氢法苯酚合成环己酮工艺是最早应用于工业化生产环己酮的工艺, 该工艺早期分为两步: 第一步苯酚加氢为环己醇, 第二步环己醇脱氢生成环己酮:20世纪70年代开发成功了一步加氢法合成环己酮的新工艺。
苯酚一步加氢有气相和液相两种方式。
工业上主要是采用气相法,该工艺采用3--5个反应器串联,温度为140--170℃、压力为0.1MPa,收率可达95%。
苯酚加氢法生产的环己酮质量较好,安全性高, 但因为苯酚价格昂贵, 并使用了贵金属催化剂, 使环己酮的生产成本较高, 因此该工艺的应用受到了很大的限制。
2.1.2 苯加氢氧化法苯加氢氧化法工艺中苯与氢气在镍催化剂存在下, 在120--180℃下加氢反应生成环己烷, 环己烷于空气中在150--160℃、0.908Mpa下发生氧化反应生成环己醇和环己酮的混合物:混合物经分离后得环己酮, 副产品环己醇在锌、钙催化剂存在下脱氢生成环己酮:2.1.3 环己烷液相氧化法目前90%以上的环己酮是采用环己烷氧化法生产的。
工业生产中环己烷液相氧化法有两条氧化工艺路线,一种为催化氧化工艺,另一种为无催化氧化工艺。
……2.2 现有工艺技术的改进针对上述环己酮生产工艺存在的不足,许多生产企业与研究部门对环己酮生产技术进行了多方面的改进。
<1)延长开车周期。
钴盐法的优点是反应条件温和、温度低、压力低、停留时间短,对设备要求不严格。
但钴盐法最大的难题是反应过程中生成的羧酸钴盐残留在设备及管道上,结渣堵塞管道和阀门。
为了解决此难题,各国都进行了大量的研究。
工艺方面,氧化后未反应的环己烷被分离后循环使用,在氧化前的水用共沸蒸馏等方法除去,避免了反应器的结渣。
反应器方面,捷克斯洛伐克专利提出环己烷液相氧化采用卧式反应器,以垂直挡板将其分割成几个反应器。
环己烷氧化制备环己酮和环己醇工艺研究进展
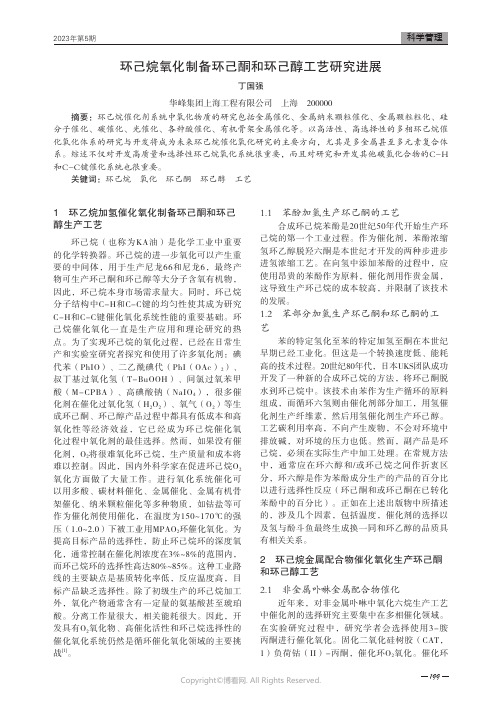
1991 环乙烷加氢催化氧化制备环己酮和环己醇生产工艺环己烷(也称为KA油)是化学工业中重要的化学转换器。
环己烷的进一步氧化可以产生重要的中间体,用于生产尼龙66和尼龙6,最终产物可生产环己酮和环己醇等大分子含氧有机物,因此,环己烷本身市场需求量大。
同时,环己烷分子结构中C-H和C-C键的均匀性使其成为研究C-H和C-C键催化氧化系统性能的重要基础。
环己烷催化氧化一直是生产应用和理论研究的热点。
为了实现环己烷的氧化过程,已经在日常生产和实验室研究者探究和使用了许多氧化剂:碘代苯(PhIO)、二乙酰碘代(PhI(OAc)2)、叔丁基过氧化氢(T-BuOOH)、间氯过氧苯甲酸(M-CPBA)、高碘酸钠(NaIO 4),很多催化剂在催化过氧化氢(H 2O 2)、氧气(O 2)等生成环己酮、环己醇产品过程中都具有低成本和高氧化性等经济效益,它已经成为环己烷催化氧化过程中氧化剂的最佳选择。
然而,如果没有催化剂,O 2将很难氧化环己烷,生产质量和成本将难以控制。
因此,国内外科学家在促进环己烷O 2氧化方面做了大量工作。
进行氧化系统催化可以用多酸、碳材料催化、金属催化、金属有机骨架催化、纳米颗粒催化等多种物质,如钴盐等可作为催化剂使用催化,在温度为150~170℃的强压(1.0~2.0)下被工业用MPAO 2环催化氧化。
为提高目标产品的选择性,防止环己烷环的深度氧化,通常控制在催化剂浓度在3%~8%的范围内,而环己烷环的选择性高达80%~85%。
这种工业路线的主要缺点是基质转化率低,反应温度高,目标产品缺乏选择性。
除了初级生产的环己烷加工外,氧化产物通常含有一定量的氨基酸甚至琥珀酸。
分离工作量很大,相关能耗很大。
因此,开发具有O 2氧化物、高催化活性和环己烷选择性的催化氧化系统仍然是循环催化氧化领域的主要挑战[1]。
1.1 苯酚加氢生产环己酮的工艺合成环己烷苯酚是20世纪50年代开始生产环己烷的第一个工业过程。
- 1、下载文档前请自行甄别文档内容的完整性,平台不提供额外的编辑、内容补充、找答案等附加服务。
- 2、"仅部分预览"的文档,不可在线预览部分如存在完整性等问题,可反馈申请退款(可完整预览的文档不适用该条件!)。
- 3、如文档侵犯您的权益,请联系客服反馈,我们会尽快为您处理(人工客服工作时间:9:00-18:30)。
2005 年12月 The Chinese Journal of Process Engineering Dec. 2005收稿日期:2004−12−27,修回日期:2005−05−23作者简介:郭志武(1971−),男,湖南省益阳市人,本科,工程师,化学工艺专业;靳海波,通讯联系人,E-mail: jinhaibo@.液相氧化环己烷制备环己酮的鼓泡塔新工艺郭志武1, 靳海波1, 项志军1, 佟泽民1, 程立泉2, 胡镇华2(1. 北京石油化工学院化工系,北京 102617;2. 中国石化股份有限公司巴陵分公司,湖南 岳阳 414007)摘 要:在连续无搅拌鼓泡塔反应器中,以环烷酸钴为催化剂,研究了空气液相氧化环己烷制备环己酮的氧化过程. 考察了空气流速、环己烷停留时间、催化剂浓度、压力及温度对反应效果的影响. 结果表明,在无搅拌鼓泡塔中,采用空气氧化环己烷制备环己酮的适宜操作条件为:反应温度413~423 K ,压力1.2~1.5 MPa ;当空气表观气速为2.5~3.5 cm/s 、环己烷停留时间为30~40 min 时,反应转化率为5%~7%,选择性达到80%~85%. 关键词:鼓泡塔;氧化;环己烷中图分类号:TQ234 文献标识码:A 文章编号:1009−606X(2005)06−0631−051 前 言环己酮是一种重要的化工原料,广泛应用于合成纤维、合成橡胶、工业涂料、医药、农药、有机溶剂等产品的制备. 由于聚酰胺行业的迅速发展,使国内、国际市场上作为生产己内酰胺原料的环己酮也得到了快速发展. 目前,国内外生产环己酮的主要方法是环己烷氧化法,其中以环己烷的催化氧化最为重要. 对传统催化氧化的改进集中在催化反应和反应工程方面[1,2],主要包括:(1) 寻找合适的催化剂、抑制剂以及相转移试剂和合适的反应条件,提高反应的转化率、选择性和单程收率;(2) 通过对反应器的改进解决工艺中的结渣难题,提高生产的连续性;(3) 反应条件温和化、生产安全化;(4) 控制反应,避免深度氧化和污染环境. 因此,有关环己酮合成的新工艺与新技术的研究开发一直受到学术界和企业的广泛关注.目前,工业环己烷催化氧化反应大都采用搅拌反应器,如荷兰Sramicarbon 公司的钴盐催化氧化工艺、荷兰DSM 法以及国内采用的环己烷钴盐催化氧化工艺,其目的在于加快含氧气体与环己烷的混合. 由于环己烷的氧化产物环己酮和环己醇比环己烷反应活性高,更容易被氧化,因此,为减少反应混合物的返混而采用多级串联反应器(5~6级最常见),有利于缩短氧化产物的停留时间,可避免反应产物的深度氧化,从而提高目的产物的选择性和收率[3,4]. 一般情况下,此类工艺的反应温度在423 K 左右,压力为0.8~1.2 MPa ,转化率约为4%,环己酮和环己醇总收率为75%~85%[5]. 另外,由于环己烷的催化氧化在高压下进行,搅拌装置不仅增加了过程设备的投资,而且还增加了设备的复杂性、安全性和生产成本.本工作目的在于采用不带搅拌装置的立式鼓泡反应器,以多段进气方式来研究环己烷催化氧化制备环己酮反应工艺,考察了空气流量、环己烷平均停留时间、反应压力以及反应温度等操作条件对均相催化氧化反应效果的影响,以期获得一种适宜的环己烷催化反应器形式及反应工艺条件.2 实 验2.1 试剂和原料原料为环己烷,北京化工厂,分析纯;液相氧化反应的催化剂为环烷酸钴,北京化工厂,实验级. 2.2 实验装置实验装置主要由反应器、进料系统和冷凝回流系统3部分组成,如图1所示. 反应器高1.8 m ,内径Φ 0.06 m ,反应器有效体积约为5 L ,外壁设有加热装置,由几组热电偶和温控仪控制反应器内不同反应区的反应温度. 反应器内部设有与进气管道相连的多管式气体分布器,分布器为26个Φ1.0 mm 的孔,在管上呈等边三角形排列. 进料系统包括空气进料和环己烷进料两部分,空气经压缩机加压后,通过流量计计量,进入反应器. 环己烷经计量泵、再经预热器加热到反应所需温度后进入反应器. 在反应器上端,氧化产物可以从反应器一侧的溢流管流出,经冷凝器冷却后收集. 冷凝回流系统由冷凝器、气液分离器和回料泵组成. 未反应完的气体、部分环己烷蒸汽以及少部分低沸点氧化产物(主要是水)从反应器顶部引出,经冷凝后,环己烷重新打回到反应器底部继续氧化,反应生成的水和未反应的气体则被移出反应体系.图1 实验装置图 Fig.1 Experimental setup工业上采用的催化剂环烷酸钴为均相催化剂,在进入反应器前与环己烷料液进行预混,反应后催化剂随产物带走,不回收. 本研究也采用这一方式. 2.3 试样分析与数据处理 2.3.1 分析方法反应混合物中的环己基过氧化氢采用碘量法测定,酸和酯通过酸碱滴定法测量,反应混合物中环己烷、酮和醇用内标气相色谱分析方法测定,用工作曲线法计算烷、酮、醇含量. 气相色谱法测定的醇含量减去通过碘量法测定的过氧化物含量即为样品中的醇含量. 2.3.2 数据处理环己烷转化率X (%)=(产物摩尔数/环己烷投料摩尔数)×100%.环己醇选择性S 1(%)=(生成环己醇摩尔数/环己烷转化摩尔数)×100%.环己酮选择性S 2(%)=(生成环己酮摩尔数/环己烷转化摩尔数)×100%.过氧化物选择性S 3(%)=(生成过氧化物摩尔数/环己烷转化摩尔数)×100%.总选择性S =S 1+S 2+S 3.3 结果与讨论3.1 空气流量对反应效果的影响在催化剂浓度2.0×10−6 mol/L 、反应温度419 K 、压力1.1 MPa 、环己烷平均停留时间75 min 、环己烷和空气采用连续进料方式(空气由底部进料)的条件下,考察了表观空气流速对反应效果的影响,结果如表1所示.表观空气流速大小可从两个方面影响环己烷的氧化反应效果. 首先,空气流速增加,增加了反应器内单位体积氧含量,即氧浓度增加,有利于提高氧化反应的速率. 研究[3]表明,在环己烷氧化生成环己酮和环己醇阶段,氧的反应级数为1,而环己酮和环己醇进一步氧化的反应级数则大于1,因此氧浓度过高导致副反应加快,对目标反应不利. 有关液相中氧浓度对各氧化反应中间产物的影响还不十分清楚. 本研究发现,增加空气流速可引起产物中过氧化物浓度下降;其次,空气流速还影响反应器内的流体力学行为,空气流速增加将导致液相轴向返混程度的增加,最终导致反应效果的降低.表1 空气流量对反应效果的影响Table 1 Effect of air flow on product compositionProduct composition (mol%)Superficial air velocity (cm/s)Cyclohexanol Cyclohexanone Cyclohexyl hydroperoxide ByproductSelectivity, S (%) Conversion (%)1.77 24.4 38.1 21.6 15.9 84.1 3.202.36 30.4 38.1 17.5 14.0 86.03.78 2.95 35.5 37.5 10.1 16.9 83.14.45 3.54 38.5 36.05.5 20.0 80.0 5.253.2 环己烷停留时间对反应效果的影响在催化剂浓度2.0×10−6 mol/L 、反应温度419 K 、压力1.3 MPa 、空气流量3.5 L/min 、环己烷和空气采用连续进料方式(空气由底部进料)的条件下,考察环己烷平1. Bubble column reactor2. Condenser3. Compressor4. Valve5. Gas −liquid separator6. Preheater7. Flow meter8. Manometer9. Heating jacket 10. Pump第6期 郭志武等:液相氧化环己烷制备环己酮的鼓泡塔新工艺633均停留时间对反应效果的影响,结果如表2所示.环己烷在反应器内停留的时间越长,被氧化的几率越大,同时氧化产物环己醇和环己酮的停留时间也相应延长. 且由于环己醇与环己酮比环己烷的反应活性更高,更容易被进一步氧化为酸或酯等副产物. 另外,过氧化物在反应器内停留时间越长,被分解得越多,因此表2给出的产物组成中过氧化物浓度随停留时间缩短而增加. 若环己烷的停留时间过短,反应器内不能积累足够浓度的氧化产物(如环己基过氧化氢、环己酮和环己醇等),即不能为自催化游离基反应的环己烷氧化过程提供足够浓度的自由基,反应就会冷却下来,无法实现连续操作. 实验还发现,当环己烷停留时间短于25 min 时,已很难将反应控制在合适的温度.3.3 温度对反应效果的影响在催化剂浓度2.0×10−6 mol/L、环己烷平均停留时间40 min、压力1.3 MPa、环己烷和空气都采用连续进料方式(空气采用分段进气)、总流量5.5 L/min的条件下,考察了温度对反应效果的影响,结果如表3所示.表2 环己烷停留时间对反应效果的影响Table 2 Effect of cyclohexane residence time on product compositionProduct composition (mol%)Residence time (h)Cyclohexanol Cyclohexanone Cyclohexylhydroperoxide ByproductSelectivity, S (%) Conversion (%)2.00 27.1 39.6 6.0 27.3 72.7 4.871.60 22.6 37.6 14.3 25.5 74.5 4.391.20 23.7 35.7 23.7 16.9 83.2 3.760.80 25.8 35.7 22.3 16.2 83.8 3.140.60 26.5 34.5 27.2 11.8 88.2 2.72表3 温度对反应效果的影响Table 3 Effect of temperature on product compositionProduct composition (mol%)Temperature (K)Cyclohexanol Cyclohexanone Cyclohexylhydroperoxide ByproductSelectivity, S (%) Conversion (%) 413 41.3 31.2 12.7 14.885.2 5.67418 39.0 33.7 13.2 14.185.9 6.31423 36.8 39.5 9.1 14.685.4 6.93428 30.2 36.5 8.4 2.1475.1 8.58表4 温度序列对反应效果的影响Table 4 Effect of temperature sequences on product compositionProduct composition (mol%)Temperature (K)Cyclohexanol Cyclohexanone Cyclohexylhydroperoxide ByproductSelectivity, S (%) Conversion (%)418 418 418 39.0 33.7 13.2 14.1 85.9 6.31423 418 418 40.3 35.2 11.3 13.2 86.8 6.62423 418 415 38.5 33.1 15.3 13.1 86.9 6.52研究发现,在低于413 K时,环己烷氧化的速率很低. 随着温度升高,环己烷转化率也相应提高,但当温度高于423 K时,氧化产物的选择性明显降低. 因为升高温度不仅能增加环己烷氧化反应的速率,同样也能增加环己醇或环己酮进一步氧化的速率,所以选择性随反应温度升高而减小. 在反应区沿着反应进行的方向,氧化产物(环己醇、环己酮和环己基过氧化氢)的浓度逐渐累积增加,因此在反应区末端适当降低反应温度,有利于提高反应的选择性. 在其他条件相同时,依照反应段分段控制温度,温度沿反应器从下至上按降序排列,结果如表4所示.对比表4与3可以发现,按降序方式分段控制温度的反应效果优于均匀控制温度. 反应器底端是氧化反应的起始区,升高温度能加快自由基反应的引发过程,随着反应不断进行,反应区内氧化产物浓度也相应增加,此时适度降低反应温度可减少氧化产物进一步氧化的反应速率,提高反应的选择性.3.4 压力对反应效果的影响在催化剂浓度2.0×10−6 mol/L、环己烷和空气都采用连续进料方式(空气采用分段进气)、总流量4 L/min、环己烷平均停留时间40 min、温度419 K条件下,考察了压力对反应效果的影响,结果如表5所示.液相氧化反应的压力和温度应相互匹配,只有反应压力大于相应反应温度下环己烷的饱和蒸汽压,氧化反应才会在液相中发生. 所选压力范围为0.9~1.5 MPa. 有研究[6,7]表明,使用均相催化剂的环己烷其氧化反应主要在液相中进行,而不是以前认为的在气液两相界面进行,因此,升高反应体系的压力,提高体系的溶氧能力,634 过程工程学报第5卷可以加快氧化反应速率. 如表5所示,压力对环己烷氧化反应的选择性影响不大,但转化率会随着压力的升高而增加,到1.5 MPa时,压力对提高转化率的作用已经不大,所以适宜的反应压力为1.3~1.4 MPa,这一压力比现行工业上的压力高. 压力增加可以加快氧从气相到液相的传质速率,因此适当提高反应压力是可取的. 同时,提高压力还会降低环己烷蒸汽在尾气中的含量,从而减少冷凝回流的环己烷的量,有利于降低热能消耗.表5 压力对反应效果的影响Table 5 Effect of pressure on product compositionProduct composition (mol%)Pressure (MPa)Cyclohexanol Cyclohexanone Cyclohexylhydroperoxide ByproductSelectivity, S (%) Conversion (%)0.9 46.333.9 6.2 13.6 86.4 4.491.1 44.437.9 5.6 12.1 87.9 4.801.3 44.839.8 5.0 10.4 89.6 5.851.5 43.038.2 4.6 14.2 85.8 6.05表6 催化剂浓度对反应效果的影响Table 6 Effect of catalyst concentration on product compositionProduct composition (mol%)Catalyst (mol/L)Cyclohexanol Cyclohexanone Cyclohexylhydroperoxide ByproductSelectivity, S (%) Conversion (%)0 38.026.3 19.0 16.783.3 5.120.5×10−6 45.2 36.3 7.6 10.9 89.1 6.121.0×10−6 42.8 36.6 8.5 12.1 87.9 6.293.0×10−6 43.1 34.9 8.2 13.8 86.2 6.905.0×10−6 43.3 33.5 9.1 14.1 85.96.963.5 催化剂浓度对反应效果的影响环己烷和空气都采用连续进料方式(空气采用分段进气)、总流量5.5 L/min、环己烷平均停留时间40 min、反应温度419 K、压力1.3 MPa条件下,考察了催化剂环烷酸钴浓度对反应效果的影响,结果如表6所示.在给定的实验条件下考察的催化剂浓度范围内,催化剂对氧化反应效果的影响不大,环己烷的转化率随催化剂浓度增加而增加,但效果不明显. 但对比无催化的氧化(表6),催化的反应效果明显优于无催化. 因为环己烷氧化为复杂自催化自由基的反应历程,催化剂对产物的影响不是线性关系,一般认为,钴盐的作用在于加快引发环己烷与分子氧反应产生自由基的过程,还可以加快过氧化物的分解[8]. 如表所示,在催化反应产物中,过氧化物的组成比例较无催化的低,这也说明钴盐催化剂的确加快了过氧化物的分解过程.4 结 论(1) 在连续无搅拌鼓泡塔反应器中,以环烷酸钴为催化剂,采用空气液相氧化环己烷,当环己烷的转化率为5%~7%时,酮醇和环己基过氧化氢的选择性达到80%~85%.(2) 与传统的带搅拌装置的工业多级串联反应器相比,在连续无搅拌鼓泡塔反应器中,反应压力增加0.2~ 0.5 MPa是合适的. 实验表明,当反应温度为413~423 K 及反应压力为1.3 MPa时,反应效果最好.(3) 温度对氧化反应的影响十分明显,当进行连续氧化时,合适的反应温度为413~423 K,反应器采用降温序列操作的效果优于单一温度操作.(4) 当空气表观流速为2.5~3.5 cm/s及液相停留时间为30~40 min时,氧化反应效果最好.参考文献:[1] 贾义霞,高建荣,黄敏,等. 环己烷催化氧化反应及工艺的研究进展 [J]. 化工纵横, 2001, 3: 8−13.[2] 薛冠申. 环己烷液相氧化反应动力学研究进展 [J]. 化学工程,1990, 18(2): 31−36.[3] 萨克拉迪⋅阿佐托⋅茨辛斯基格.环己烷液相氧化法 [P]. 中国专利:ZL 87106968, 1987−10−19.[4] Wen Y, Potter O E, Sridhar T. Uncatalysed Oxidation of Cyclohexanein a Continuous Reactor [J]. Chem. Eng. Sci., 1997, 52: 4593−4605.[5] 吴鑫干,刘含茂. 环己烷氧化制环己酮工艺及研究进展 [J]. 化工科技, 2002, 10(2): 48−53.[6] Pohorecki R, Baldyga J, Moniuk W, et al. Kinetic Model ofCyclohexane Oxidation [J]. Chem. Eng. Sci., 2001, 56: 1285−1291.[7] Suresh A K, Sridhar T, Potter O E. Autocatalytic Oxidation ofCyclohexane⎯Mass Transfer and Chemical Reaction [J] AIChE J., 1988, 34(1): 81−93.[8] Kharkova T V, Arest-Yakubovich I L, Lipes V V. Kinetic Model ofLiquid Phase Oxidation of Cyclohexane⎯I. Homogeneous Proceeding of the Process [J]. Kinet. Catal. (Kinetika I Kataliz), 1989, 30: 954−958.第6期 郭志武等:液相氧化环己烷制备环己酮的鼓泡塔新工艺635Liquid-phase Oxidation of Cyclohexane to Cyclohexanone in a Bubble Column Reactor GUO Zhi-wu1, JIN Hai-bo1, XIANG Zhi-jun1, TONG Ze-min1, CHENG Li-quan2, HU Zhen-hua2(1. Department of Chemical Engineering, Beijing Institute of Petrochemical Technology, Beijing 102617, China;2. Baling Petrochemical Company, SINOPEC., Yueyang, Hunan 414007, China)Abstract: Liquid-phase air oxidation of cyclohexane to cyclohexanone and cyclohexanol with cobalt napthenate as catalyst was carried out in a continuous bubble column reactor. The effects of reaction conditions including temperature, pressure, residence time of cyclohexane, superficial air velocity and catalyst concentration on cyclohexane conversion and the selectivities to cyclohexanone, cyclohexanol and cyclohexanyl hydroperoxide were studied. When the reaction was conducted in the system temperature range from 413 to 423 K, system pressure range from 1.2 to 1.5 MPa, superficial air velocity range from 2.5 to 3.5 cm/s and cyclohexane residence time of 30~40 min, the cyclohexane conversion of 5%~7% and the total selectivity to cyclohexanone, cyclohexanol and cyclohexanyl hydroperoxide of 80%~85% were obtained.Key words: bubbling column; oxidation; cyclohexane。