07-sensor-models
Model 399 General Purpose pH ORP Sensor说明书

CAUTIONWARNINGSENSOR/PROCESS APPLICATION COMPATIBILITYGraph 1 below)Flow Rate:up to 2 ft/secMODEL 399Insertion/Submersion Sensor with integral cableFor additional information, please visit our website at/raihome/liquid/.STORAGE1.It is recommended that electrodes be stored in theiroriginal shipping containers until needed.2.Do not store at temperatures below -5°C (23°F).3.Electrodes should be stored with a protective capcontaining KCl solution (PN 9210342).4.For overnight storage, immerse the sensor in tapwater or 4 pH buffer solution.5. A pH glass electrode has a limited shelf life of oneyear.ELECTRODE PREPARATION1.Remove electrode from shipping container.2.Remove the protective boot covering the electrodebulb.3.Rinse away salt film with clean water, then shakethe electrode so that the internal solution fills the bulb, thus removing any air trapped there.NOTEDo not allow lubricant to coat electrode bulb orreference junction. If it does, wipe it clean beforeinstallation.INSTALLATIONFor sensor orientation, see Figure 1.For sensor dimensions, see Figure 2.For wiring, see Figure 3 - 29.TWO POINT BUFFER CALIBRATION Select two stable buffer solutions, preferably pH 4.0 and 10.0 (pH buffers other than pH 4.0 and pH 10.0 can be used as long as the pH values are at least two pH units apart).NOTEA pH 7 buffer solution reads a mV value ofapprox. zero, and pH buffers read approximately± 59.1 mV for each pH unit above or below pH 7.Check the pH buffer manufacturer specificationsfor millivolt values at various temperatures sinceit may affect the actual value of the buffersolution mV/pH value.1. Immerse sensor in the first buffer solution. Allowsensor to equilibrate to the buffer temperature (to avoid errors due to temperature differences between the buffer solution and sensor tempera-ture) and wait for reading to stabilize. Value of buffer can now be acknowledged by analyzer/ transmitter.2. Once the first buffer has been acknowledged by theanalyzer/transmitter, rinse the buffer solution off of the sensor with distilled or deionized water.3. Repeat steps 1 and 2 using the second buffersolution.4. The theoretical slope value, according to the Nernstequation for calculating pH, is approximately 59.17 mV/pH. Over time the sensor will age, both in the process and in storage, and will result in reduced slope values. To ensure accurate readings, it is recommended that the electrode be replaced when the slope value falls below 47 to 49 mV/pH. RECOMMENDED pH SENSORSTANDARDIZATIONFor maximum accuracy, the sensor can be standard-ized on-line or with a process grab sample after a buffer calibration has been performed and the sensor has been conditioned to the process. Standardization accounts for the sensor junction potential and other interferences. Standardization will not change the sensor’s slope but will simply adjust the analyzer’s reading to match that of the known process pH.MAINTENANCE FOR pH ELECTRODE Electrodes should respond rapidly. Sluggishness, offsets, and erratic readings are indicators that the electrodes may need cleaning or replacement.1.To remove oil deposit, clean the electrode with amild non-abrasive detergent.2.To remove scale deposits, soak electrodes for 30 to60 minutes in a 5% hydrochloric acid solution.3.Temperature effect on life expectancy: If glasselectrode life expectancy is 100% @ 25°C (77°F), then it will be approximately 25% @ 80°C (176°F), and approximately 5% @ 120°C (248°F).2FIGURE 1. Sensor OrientationTEMP COMP1” MNPT1” MNPT1” WRENCH OPENINGpHDia251 80 3.151445.67FIGURE 2. Sensor DimensionsINCH MILLIMETER3ORP CALIBRATION1. After making an electrical connection between thesensor and the instrument, obtain a standard solution of saturated quinhydrone (PN R508-8OZ).This can also be made quite simply by adding a few crystals of quinhydrone to either pH 4 or pH 7buffer. Quinhydrone is only slightly soluble, there-fore only a few crystals will be required.2. Immerse the sensor in the standard solution. Allow1-2 minutes for the ORP sensor to stabilize.3. Adjust the standardize control of the instrument tothe solution value shown in the table below. The resulting potentials, measured with a clean plat-inum electrode and saturated KCl/AgCl reference electrode, should be within +/- 20 millivolts of the value shown in the table below. Solution temperaturemust be noted to ensure accurate interpretation of results. The ORP value of saturated quinhydrone solution is not stable over long periods of time.Therefore, these standards should be made up fresh each time they are used.4. Remove the sensor from the buffer, rinse, andinstall in the process.MAINTENANCE FOR ORP ELECTRODEElectrodes should respond rapidly. Sluggishness, off-sets, and erratic readings are indicators that the elec-trodes may need cleaning or replacement.1.To remove oil deposit, clean the electrode with amild non-abrasive detergent.2.To remove scale deposits, soak electrodes for 30 to 60 minutes in a 5% hydrochloric acid solution.3.ORP (metallic) electrodes should be polished with moistened baking soda.ORP of Saturated Quinhydrone Solution (millivolts)FIGURE 3. BNC PreparationFIGURE 7. Models 399-12, 399-13, and 399-33 wiring for use with the Solu Comp analyzerFIGURE 5. Wiring Models 399-02 and 399-09 to Model 1181 integral analyzer/ transmitter preamplifierNOTE: BNC must be cut and prepped. See Figures 3 and 4.4FIGURE 4. Wire Functions for Models 399-02 and 399-09FIGURE 6. Models 399 and 399-09 wiring for use with Models 54, 54e, 81, 3081, 4081, 5081, 2081,1054, 1054A, 1054B, and 2054 integral analyzer/ transmitter preamplifierNOTE: BNC from sensor cable (see Figure 4) must be cut and prepped, except 399-09-62. See Figure 3.WIRINGMODEL 399WIRINGFIGURE 10. Wiring Model 399-01, -03, -05, -06, -07, and -08 (preamplifier integral to sensor) toTransmitter Models 2054, 1054A, 1054B, 2081, 1181, and other various models.FIGURE 8. Model 399-02 or -09 wiring for use with preamplifier integral to remote junction box,and Models 1054, 1054A, 1054B, 2054, 2081, and other various analyzer/transmitter models.FIGURE 9. Wiring Model 399-14 or 399-10 to Model 54epH5FIGURE 11. Wiring Model 399-14, 399-10, or 399-34 to Models 3081, 4081, and 5081-PFIGURE 12. Wiring Model 399-14, 399-10, or 399-34 to Model 1055-22-326FIGURE 13. Wiring Model 399-09-62 to Model 1055-22-32 through Remote Junction Boxes7WIRE FUNCTIONS FOR 399-12, -13, -33WIRE FUNCTIONS FOR 399-09-62WIRE FUNCTIONS FOR 399-01, -03, -06, -07, -0889FIGURE 15. Wiring Model 399-09 to Model 1055-10-22-32DWG. NO.REV.40105548D10FIGURE 16. Wiring Model 399-09-62, 400, 401, 402, 403, and 404 to Model 1055 (Panel Mount)DWG. NO.REV.41055105C11FIGURE 17. Wiring Model 399-14, 399-10, or 399-34 and 400, 401, 402, 403, or 404 to Model 1055(Pipe/Wall Mount)DWG. NO.REV.41055106C12FIGURE 18. Wiring Model 399-09-62 and 400, 401, 402, 403, or 404 to Model 1055 (Pipe/Wall Mount) DWG. NO.REV.41055109C13FIGURE 19. Wiring Model 399-14, 399-10, or 399-34 and 400, 401, 402, 403, or 404 to Model 1055(Panel Mount)DWG. NO.REV.41055110D14399-14, 399-10, 399-34FIGURE 22. Wiring Model 399-14, 399-10, or 399-34 sensor to Model Xmt-P-XX-10 Transmitter15399-14, 399-10, 399-34 16FIGURE 27. Wiring Models 399-33 to 608117FIGURE 28. Wiring Model 399-09-62 sensor to 6081399-14, 399-10, 399-34 1819The right people,the right answers,right now.Emerson Process Management2400 Barranca ParkwayIrvine, CA 92606 USATel: (949) 757-8500Fax: (949) 474-7250© Rosemount Analytical Inc. 2011Sira MC070110/00。
Toyota 2GR-FE 3.5L 引擎故障代码与诊断指南说明书

ESP light illuminated, DTC(s) stored. Some 2007 Dodge Calibers and Nitros, along with Jeep Wrangler, Patriot and Compass models, may illuminate the ESP light on the dash and log steering angle sensor-related DTCs C121A and/or C2205 in computer memory.
these troubles to software issues in the
PCM. Reprogramming the module
with revised calibration files is the only
reliable fix.
To do the flash, you’ll need an
P0304) stored in computer memory.
Furthermore, if you pull the spark
plugs from the cylinders with the mis-
fire, you’ll likely find them fouled. The
Japanese carmaker attributes all of
According to Dodge/Jeep, the
38
October 2012
Tom Rosario
problem occurs only on vehicles built on or before 4/12/07, may be intermittent (the ESP light will remain on only until the end of the drive cycle) and is due to software anomalies in the steering angle sensor. Reprogramming the sensor with a StarSCAN scanner and updated software is the only sure-fire fix. The new flash files can be retrieved directly off the internet.
Prism

Prism TM Series Reflex SensorsMAXIMUM INPUT VOLTAGE FOR DC OPERATION IS 30 VDC; MAXIMUM FOR AC OPERATION IS 132 VAC. APPL YING VOLT -AGE ABOVE THIS LIMIT WILL RESULT IN DAMAGE TO THE SENSOR.USE #4 MOUNTING HARDWARE ONL Y! LARGER HARDWARE WILL DAMAGE THE SENSOR AND MA Y CREATE AN ELECTRI-CAL SHOCK HAZARD. TIGHTEN THE HARDWARE JUST TO THE SENSOR BODY SO THAT NO DEFLECTION OF THE BODY OCCURS.DO NOT USE TOOLS TO APPL Y TORQUE DIRECTL Y TO SEN-SOR BODY . ALIGN SENSOR BY HAND BEFORE TIGHTENING MOUNTING HARDWARE.THE GAIN P OT IS A 3/4 TURN P OT . ANY RESISTANCE EN-COUNTERED WHILE ADJUSTING THIS P OT INDICATES YOU HAVE REACHED THE ADJUSTMENT LIMIT STOP. TURNING PAST THIS STOP WILL DAMAGE THE SENSOR.USE ONL Y A SUITABLE ADJUSTMENT TOOL OR FLATBLADE SCREWDRIVER WHEN TURNING ADJUSTMENT OTS.SHARP OBJECTS CAN DAMAGE THE P OT AND RESULT INELECTRICAL SHOCK.SHORT CIRCUIT PROTECTION WILL AUTOMATICALL Y RESETONCE SHORT IS REMOVED.AC/DC CONNECTOR VERSION SENSORS ARE EQUIP P ED WITH AN AC-TYP E CONNECTOR. THE USE OF DC P OWER WITH AC-TYP E CONNECTORS MA Y NOT CONFORM WITH ESTABLISHED STANDARDS.ISOLATED OUTPUTS ALLOW THE SENSOR TO SWITCH A DIF-FERENT VOLTAGE FROM THAT OF THE OPERATING SUPPL Y . AVOID USING CONNECTOR VERSIONS IN MIXED AP P LICA-TIONS SUCH AS SWITCHING AC VOLTAGE WITH A DC SEN-SOR.MOUNTINGT he Prism sensor features a threaded housing and includes jam nuts and washers. T his allows mounting into any 0.75 inch hole, or bracket. Use caution to avoid cross-threading the jam nuts on the sensor body. Tighten nuts to less than 4 N•m (36 in.-lbs. or 3 ft.-lbs.) torque to avoid stripping threads.INTRODUCTIONA reflex sensor has both a light source and detector in the same unit. The source sends a beam of light to a retroreflector which returns it back to the detector. A break in the light beam causes the sensor to change output state. The sensors feature visible red sources to aid in alignment of the sensor with its retroreflector. Polarized models are used to reliably detect shiny targets that may reflect the light beam back to the sensor instead of inter-rupting the beam. The polarizing filter conditions the beam so that light reflected off the retroreflector is detected, but light reflected by the target is not.This manual covers both forward viewing and right angle viewing models. Although the units differ in the location of the lenses, the basic fundamentals of installation, set-up, and operation are nearly identical.A second mounting method is to use #4 hardware in the 0.125 inch diameter mounting holes in the flat sides of the sensor. This is ideal for mounting the Prism against a wall, piece of equipment,rail, mounting bracket, etc.Models covered AC/DC Models w/ Cable DC-only Models w/ Cable DC-only Models in this manual:w/ ConnectorViewing Style:Forward Right Angle Forward Right Angle Forward Right Angle Forward Right Angle Reflex Light Operate 14150AL1414150RL1414150AL0414150RL0414150AL1714150RL1714150AL0714150RL07 15 foot Range Dark Operate 14150AD1414150RD1414150AD0414150RD0414150AD1714150RD1714150AD0714150RD07Polarized Reflex Light Operate 14151AL1414151RL1414151AL0414151RL0414151AL1714151RL1714151AL0714151RL07 10 foot Range Dark Operate14151AD1414151RD1414151AD0414151RD0414151AD1714151RD1714151AD0714151RD07AC/DC Models w/ Connector Right Angle ViewingForward Viewing2Installation Instructions 110210-400Effective March 2012Prism TM Series Reflex SensorsEATON CORPORATION USING RETROREFLECTIVE TAPERetroreflective tapes can have vastly different properties than corner-cube reflectors. Polarized reflex sensors will not function with glass bead tape but will function with corner-cube tape. Also, signal strength can drop dramatically as the distance be-tween tape and sensor is reduced. If you are using a polarized sensor, or intend to mount the tape closer than 12 inches from the sensor, we recommend that you test your particu-lar tape prior to installation.MOUNTING LOCATION AND SET -UPLocate the sensor and retroreflector on opposite sides of the target. Ensure that the area of the target to be detected will block the entire beam.With power applied to the sensor, aim the unit directly at the center of the retroreflector. Move the sensor back and forth in one plane to find the extreme positions where the LED goes “off” (for light-operate models, or “on” for dark-operate models). Y ou can also look at the retroreflector with your eye as close to the sensor as possible and align the sensor until reflected light is brightest. Position the sensor midway between the two extremes. Repeat this procedure for the other plane. After align-ment, tighten all mounting screws.Adjustments are provided for gain. See Warning concerning pot adjustment.Stretch wrap material over a shiny surface may reflect enough light to false trigger a polarized reflex sensor. In this case, reduce the gain slightly or tilt the alignment axis of the sensor relative to the shiny surface.WIRING PRISM FOR LOGICLow leakage (10 µA) and resistance ratings (25 Ω) allow Prism sensor outputs to be wired in series or parallel to perform logic functions. Two common examples are shown below:no i t c n u F ”D N A “no i t c n u F ”R O“A off ON off offB off off ONoffC off off off ON OUTPUT off ON ON ONAoff ON off ONB off off ON ON OUTPUT off off off ONPolarized models “see” only light rotated 90°.Center theretroreflector in theThe output indicator will change state if retroreflector moves of range.3Installation Instructions 110210-400Effective March 2012Prism TM Series Reflex SensorsEATON CORPORATION DC Models NOTE: Sensor operates on DCvoltage, but isolated outputs can switch AC or DC loads .+VD C 10 t o 30 VConnector Version-Face View Male Cable Version( - )+VBlack wires are shown as switched output, however black and gray wires are bidirectional.WIRING DIAGRAMSCable Versions: The color codes shown are the actual wire colors emanating from the sensor.Connector Versions: The pin numbering and wire colors, shown in ( ), are typical of several manufacturers, however, variations are possible.In case of discrepancies, rely on function indicated and pin location rather than pin number or wire color.Installation Instructions 110210-400Effective March 2012Prism TM Series Reflex SensorsEaton CorporationElectrical Sector1111 Superior Ave.Cleveland, OH 44114United States877-ETN-CARE (877-386-2273)© 2011 Eaton CorporationAll Rights Reserved Publication No. 110210-400 / 007 March 2012Eaton is a registered trademark of Eaton Corporation.All other trademarks are property of their respective owners.AC/DC MODELS DC-ONLY MODELSInput Voltage20 to 132 V AC, 50/60 Hz or 15 to 30 V DC10 to 30 V DCPower Dissipation m u m i x a mW1m u m i x a mW5.1Output Type Solid State RelayOutput Isolation400 V maximumVoltage Switching Capacity200 VAC peak; 180 VDCCurrent Switching Capacity80 mA AC load; 110 mA @ 132 VDC (derate to 100 mA @ 180 VDC)Off-State Leakage10 µA maximum 1On-State Resistance25 ΩmaximumShort Circuit Protection Protected (current limited) for loads less than 32 Volts AC or DC.IMPORTANT: Output will reset automatically when short is removed. (There is no visual indication of a short circuit condition) Response Time 3 mSLight/Dark Operation Specified by model numberTemperature Range Operating: -25° to +55° C (-13° to +131° F); Storage: -25° to +70° C (-13° to +158° F)Material of Construction Lens: Polycarbonate; Cable jacket: PVC; Body: Structural polyurethane foam(do not expose to concentrated acids, alcohols, or ketones)Cable/Connector6-foot cable, 4-wire; Micro Connector, 4-pin maleVibration and Shock Vibration: 30 g over 10 Hz to 2 kHz; Shock: 50 g for 10 mS 1/2 sinewave pulseSunlight Immunity1,000 foot-candlesIndicator LED Lights steady when output is ONEnclosure Ratings NEMA 1, 2, 3, 4, 4X, 6, 12, and 13(See note below)Approvals UL and C-UL recognized, CE compliantSPECIFICATIONSNOTE:Our products conform to NEMA tests as indicated, however, some severe washdown applications can exceed these NEMA test specific ations. If you have questions about a specific application, contact our Applications Department.1 When used with AC loads, the Off-State leakage of Model numbers below is less than 450uA. 14150AL17,14150AD17,14151AL17,14151AD17,14150AL07,14150AD07,14151AL07,14151AD071415014151Source Visible red, 680 nmMaximum Range15 feet (4.5M)10 feet (3M)Optimum Range0.1 to 12 feet0.1 to 8 feet(0.03-3.7M)(0.03-2.4M)Field of View 3 inch diameter at 12 feet (76mm diameter at 3.7M)1000101RANGE (feet)EXCESSGAIN100RANGE (m)1.14150 Typical2.14150 Minimum3.14151 Typical4.14151 MinimumPerformance to 3-inch retroreflectorOPTICAL PERFORMANCEAll optical specifications are guaranteed to be the minimum per-formance under clean conditions of any product delivered from stock. Typical performance may be higher.Dirt in the environment will affect optical performance by reduc-ing the amount of light the control receives. For best results, sensors should be used at distances where excess gain is high-er than 1.5 (1.5 times the amount of sensing power required to detect an object under ideal conditions). Higher excess gain will allow the sensor to overcome higher levels of contamination on the lens. All ranges and excess gain graphs are based on a 3 inch retroreflector.。
Ohmic Instruments Company 温湿度传感器说明书
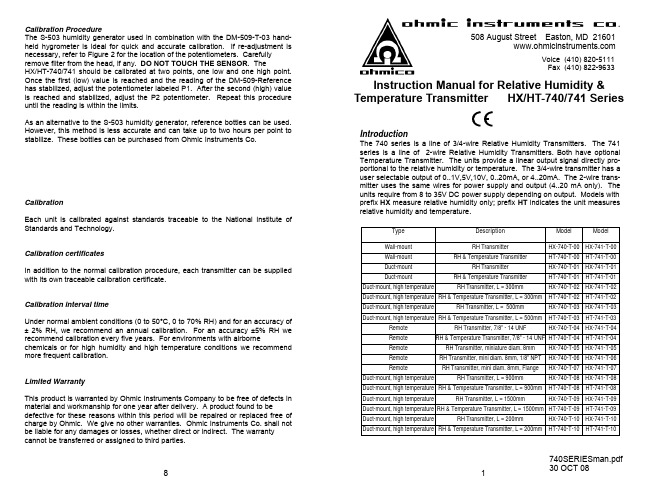
740SERIESman.pdf
1
30 OCT 08
T-00 Wall-Mount
1 .65" (42mm)
4.72" (1 20mm)
PG-7
3.15" (80mm) 3.15" (80mm)
2.16 " (5 5mm)
1.14" (29m m) 2 .16" (55mm)
0.79 " (20 mm)
As an alternative to the S-503 humidity generator, reference bottles can be used. However, this method is less accurate and can take up to two hours per point to stabilize. These bottles can be purchased from Ohmic Instruments Co.
Duct-mount, high temperature
RH Transmitter, L = 200mm
HX-740-T-10 HX-741-T-10
Duct-mount, high temperature RH & Temperature Transmitter, L = 200mm HT-740-T-10 HT-741-T-10
Remote
RH & Temperature Transmitter, 7/8” - 14 UNF HT-740-T-04 HT-741-T-04
Remote
RH Transmitter, miniature diam. 8mm HX-740-T-05 HX-741-T-05
Honeywell TR21、TR22、TR23、TR24 壁模块说明书

INSTALLATION INSTRUCTIONS62-0267-09TR21, TR22, TR23, and TR24 Wall ModulesFEATURESThe TR21, TR22, TR23, and TR24 family of wall modules include:•Models with setpoint adjustment.•Models with humidity output.•Models with occupied/unoccupied override (bypass) with LED.•Models with 3-position (auto/0/1) or 5-position (auto/0/1/2/3 speed) fan switch.•L ON W ORKS ® bus jack on all models except the TR21 and TR21-A models.•Locking cover on all models.•Operating range 45° to 99° F (7° to 37° C).•Models (TR22 and TR23) with user-selectabletemperature setpoint dials in Fahrenheit, Celsius, and Relative (- to +).PRODUCT DESCRIPTIONThe TR21, TR22, TR23, and TR24 are a family of direct-wired wall modules for use with:—Spyder Unitary Controllers: PUL, PVL—Excel 10 W7750, W7751a , W7752, and W7753controllers—Honeywell Excel 800, 600, 500, 100, and 80 (all fullyprogrammable) controllers —W7761 Controller—ComfortPoint LON Controllers: CP-UL, CP-VL All models have a space temperature sensor. Some models have a temperature dial, setpoint adjustment, L ON W ORKS bus jack, override (bypass) with LED, and fan switch.NOTE:Refer to the TR21, TR22, TR23, and TR24 WallModules – Specification Data , form 63-1321, for specific model features and additional information.SPECIFICATIONSModels: For specific model information, see TR21, TR22,TR23, and TR24 Wall Modules – Specification Data , form 63-1321.Environmental Ratings:•Operating Temperature: 45° to 99° F (7° to 37° C).•Shipping Temperature: -40° to 150° F (-40° to 65.5° C).Accessories: 50007298-001 (pack of 12) medium, coverplate; 6-7/8 x 5in. (175 x 127 mm).Approvals: CE; UL94 plastic enclosure; FCC Part 15, Class BTemperature SensorTR21, TR22, TR23, and TR24 20K Ohm Nonlinearized Sensor:All models are furnished with a 20K Ohm nonlinear NTC temperature sensor that follows a specific temperature resistance curve. See Fig. 1 on page 2.NOTE:The TR21-A wall module model has two (2) 20KOhm nonlinear NTC temperature sensors in parallel, which provide 10K NTC temperature sensingnecessary for averaging.a The TR21, TR22, TR23, and TR24 wall modules are notcompatible with W7751A,C,E,G Controllers.TR21, TR22, TR23, AND TR24 WALL MODULES62-0267—092Fig. 1. Temperature vs. Resistance for Nonlinear Sensor.CommunicationsAll wall modules (except the TR21 and TR21-A models) havea L ON M ARK ® bus communications port. If needed, the jack plug must be removed in the field, and terminals 3 and 4 wired according to the installation instructions.The recommended wire size for the L ON M ARK ® bus is Level IV, 22 AWG (0.34 sq.mm) plenum or non-plenum rated, non-shielded, twisted pair, solid conductor wire.Fig. 2. Wall Module Features (TR23-F Shown).BEFORE INSTALLATIONFailure to follow proper wiring practices canintroduce disruptive electrical interference (noise).Keep wiring at least one foot away from large inductive loads such as motors, line starters, lighting ballasts, and large power distribution panels.Shielded cable is required in installations where these guidelines cannot be met.Ground shild only to grounded controller case.IMPORTANTAll wiring must comply with local electrical codes and ordinances or as specified on installation wiring diagrams.—Wall module wiring can be sized from 16 to 22 AWG (1.31 to 0.33 sq. mm) depending on the application.—The maximum length of wire from a device to a wall module is 1000 ft. (305 m).—Twisted pair wire is recommended for wire runs longer than 100 ft. (30.5 m).INSTALLATIONMount the wall module on an inside wall approximately 54 in. (1372 mm) from the floor (or in the specified location) to allow exposure to the average zone temperature. Do not mount the wall module on an outside wall, on a wall containing water pipes, or near air ducts. Avoid locations that are exposed to discharge air from registers or radiation from lights,appliances, or the sun. See “Cover Disassembly” on page 3.The wall module can be mounted on a wall, on a standard utility conduit box using No. 6 (3.5 mm) screws or on a 60mm wall outlet box (see Fig.3). When mounting directly on a wall, use the type of screws appropriate for the wall material.Fig. 3. Mounting on Standard Utility Conduit Box or60 mm Wall Outlet Box (TR23 Shown).FRONT COVERTR21, TR22, TR23, AND TR24 WALL MODULES362-0267—10Fig. 4. Wall Module Subbase Dimensions in Inches (mm) and Temperature Limit Set Screw Locations (TR23Shown).Cover DisassemblyA snap-fit locking mechanism is used to attach the cover of the wall module to its subbase. To disassemble the cover from the subbase:1.Insert a thin, flat blade screwdriver into each of the twoslots at the bottom of the module to release the two locking tabs. See Fig.2 on page 2.2.Tilt the cover out and away from the subbase to releasethe top two locking tabs.3.To change the dial (e.g. from Fahrenheit to Celsius)release the two tabs on the inside of the front cover and remove the old dial.WiringAttach the wires from the device sensor terminals to the appropriate wall module terminals. See Table 1 on page4.Screw type terminal blocks are designed to accept no more than one 16 AWG (1.31 sq. mm) conductor.Connect multiple wires that are 16-18 AWG(1.31-0.82 sq. mm) with a wire nut. Include a pigtail with this wire group and attach the pigtail to the individual terminal block.Wiring Wall ModulesWire the terminal block as follows:1.For single wires, strip 3/16 in. (5 mm); for multiple wiresgoing into one terminal, strip 1/2 in. (13 mm) insulation from the conductor.2.If two or more wires (20 to 22 AWG only) are beinginserted into one terminal, twist the wires together before inserting. See Fig. 5.3.Insert the wire in the required terminal location and tighten the screw to complete the termination.4.Review and verify the terminal connection wiring and DIP switch settings illustrated in Table 1 on page 4.NOTE:Wire the Lon connection (terminals 3 and 4) usingLevel IV 22 AWG (0.34 mm 2) plenum or non-plenum rated, unshielded, twisted pair, solid conductor wire.Wiring ExamplesTable 1 on page 4 illustrates DIP switch settings and terminal connections for the wall modules. Refer to the TR21, TR22, TR23, and TR24 Wall Modules – Specification Data , form 63-1321, for additional DIP Switch information.IMPORTANTSW 2 on DIP Switch S2 is used for factory calibration of the temperature setpoint potentiometer.Depending on calibration, this switch may be set in either the On or Off position.DO NOT change the position of this switch.NOTES:1.The TR21 and TR22 models do not use DIP Switch S1 and S3.2.DIP Switch S1 is used only on the humidity models, TR21-H and TR23-H.3.Models TR21 and TR21-A use terminals 1 and 2 only. Model TR21-J uses terminals 1, 2, 3, and 4 only.Fig. 5. Attaching Two Wires (20 to 22 AWG) to Wall ModuleTerminals.Attaching the CoverWhen all wiring is complete, attach the cover of the Wall Module as follows:1.Optional : For models with a temperature dial, insert thetwo setpoint screws into the inside of the cover to set the desired temperature range limit. See Fig.4.2.Press the cover straight down onto the subbase until itsnaps into place.3.For models with a temperature dial, insert the desireddial through the opening in the cover. Align the keyed shaft on the knob with the keyed slot into the fitting on the subbase, then press down until it snaps into place.TR21, TR22, TR23, AND TR24 WALL MODULESWiring and DIP switch settings:See Table 1 to determine DIP switch positions and terminal usage for each controller.Table 1. DIP Switch Settings and Terminal Connections.62-0267—094TR21, TR22, TR23, AND TR24 WALL MODULES562-0267—09TR22 and TR23 Setpoint AdjustmentFor the TR22 and TR23 Wall Modules with a setpointadjustment, the controller must be programmed for the values in Table 2 and Table 3.TR23-KL and TR23-H-KLThe TR23-KL and TR23-H-KL ship in packs of 20 and are supplied without setpoint adjustment knobs. Knobs can be ordered separately. See Table 4 for Knob model numbers.Humidity Settings (DIP switch S1)The humidity sensing control mode is set with this 2-position DIP switch. Refer to Fig.4 on page 3 for location of DIP switch S1.NOTE:These switch settings apply only to the TR21-H andTR23-H models.To change the setting, first disconnect the power, then set SW1 and SW2 according to Table 5.TR23 and TR24 Wall Module Override (Bypass) Pushbutton and LED OperationWhen Used With Excel 10 Controllers:The Excel 10 controllers (W7750, W7751, W7752, andW7753) provide timed occupied and unoccupied temperature setpoints for the Wall Module, see Fig. 6. The override pushbutton is used to change the controller into the modes shown in Table 6 and illustrated in Fig.7 on page 6. The override (bypass) LED displays the override status of the controller.Fig. 6. LED and override pushbutton locations(TR23-F Wall Module shown).Table 2. Setpoint Values.Setpoint Value Program Setting55°F (13°C) 2.773 V 65°F (18°C) 2.148 V 75°F (24°C) 1.345 V 85°F (29°C)0.43 VTable 3. Wall Module Setpoint Configuration.Model Setpoint Resistance (Ohms)°F Absolute 55°F 957485°F1426Relative -9°F offset from 70°F 9574+9°F offset from 70°F1426°C Absolute12°C 994530°C1150Table 4. Knob Model NumbersModel DescriptionKNOB-C Celsius scale knob (pack of 20)KNOB-F Fahrenheit scale knob (pack of 20)KNOB-ORelative scale knob (pack of 20)Table 5. DIP Switch S1 Settings.Wall Module Model Sensing Control Individual Switches 12TR21-H TR23-H0-10 Vdc OFF OFF 0-5 Vdc OFF ON 4-20 mAONOFFTR21, TR22, TR23, AND TR24 WALL MODULES62-0267—096Fig. 7. Override pushbutton operation.When Used With Excel 600/500/100/80/50 Controllers:The application engineer/programmer can program theoverride (bypass) and LED to operate in any manner desired. The override (bypass) input is a dry contact, normally open, momentary digital input when the wall module does not have a fan switch. When a fan speed switch (basically a series of resistances based on fan switch position) is present, the override button is an analog input. See Table 4 for resistances.When Used With T7350 Thermostat:TR21, TR21-A, TR21-H, TR22, TR23, and TR24 are the models compatible with the T7350 thermostat. When using with the T7350 thermostat be sure to use the relative +/- offset knob only. The Celsius and Fahrenheit knobs will not work properly with the T7350 Thermostat.TR22-F5, TR23-F3, and TR23-F5 Wall Module Fan SwitchWith the switch in the far left position (Auto), the fanautomatically runs at the speed determined by the controller temperature control algorithm.With the switch in the 0 position, the fan is off. Position 1 is fan speed 1, etc.The wall module fan speed switch overrides the temperature control algorithm.When Used With Excel 10 Controllers:The Excel 10 Controllers (W7750, W7751, W7752, andW7753) can be programmed so that the fan speed switch and override button function the way that the application engineer/programmer wants. See Table 7 for controller-programming resistances. Switch 1 on Dip Switch S2 adds 10k Ohms resistance when OPEN (for Excel 600-80 controllers) and removes it when CLOSED (for Excel 10 controllers).When Used With Excel 600/500/100/80/50 Controllers:Excel 600/500/100/80 Controllers can be programmed so that the fan speed switch and override button function the way that the application engineer/programmer wants. See Table 8 for controller-programming resistances. Switch 1 on Dip Switch S2 adds 10k Ohms resistance when OPEN (for Excel 600-80 controllers) and removes it when CLOSED (for Excel 10 controllers).Table 6. Wall Module Operation.Pushbutton Held Down Controller Model LED Status0 to 1 second No override Off 1 to 4 seconds Timed occupied override On4 to 7 seconds Unoccupied override Single blink per secondLonger than 7 seconds No overrideOffnot applicableContinuous occupied override aaRemote function, which is generated from the network.Two blinks per secondTable 7. Program Settings for Wall Modules withFan Switch using Excel 10 Controllers.For Switch Position Resistance (Ohms)Comment Auto 1861 ±119Left most position 02686 ±127Fan Off position13866 ±13923041 ±13034601 ±146Right most positionOverride button closed Closed circuitTable 8. Program Settings for Wall Modules with Fan Switch using Excel 600/500/100/80 Controllers.For Switch Position Resistance (Ohms)Comment Auto 11.861K ±119Left most position 012.686K ±127Fan Off position113.866K ±139213.04K ±130314.60K ±146Right most positionOverride button closed 10K ±100TR21, TR22, TR23, AND TR24 WALL MODULES 762-0267—09TR21, TR22, TR23, AND TR24 WALL MODULESAutomation and Control Solutions Honeywell International Inc.Honeywell Limited-Honeywell Limitée 1985 Douglas Drive North 35 Dynamic DriveGolden Valley, MN 55422Toronto, Ontario M1V 4Z9® U.S. Registered Trademark© 2009 Honeywell International Inc.62-0267—09E.K. Rev. 09-09L ON W ORKS ® is a registered trademark of Echelon ® Corporation.L ON M ARK ® and the LonMark Logo are trademarks of the LonMark Association.By using this Honeywell literature, you agree that Honeywell will have no liability for any damages arising out of your use or modification to, the literature. You will defend and indemnify Honeywell, its affiliates and subsidiaries, from and against any liability, cost, or damages, including attorneys’ fees, arising out of, or resulting from, any modification to the literature by you.。
MEMS07-sensors - Print

图2-8 ADXL150敏感单元接口原理 Fig.2-8 Capacitive interface principle diagram of ADXL150 sense element
F
F
r(e) = r0(1+ GP e ) • R(e) = R0(1+(GP+G) e ) • GP ~ -20, 30 (poly), ~100 (SCS);G ~ 1.5, 2 (metal)
• Strain generates charge, charge generates strain
HIT-MEMS chen 11
HIT-MEMS chen 11
ADXL50 Sensing Microstructure
HIT-MEMS chen 11
Po11
ADXL50 – block diagram
HIT-MEMS chen 11
ADXL50 – block diagram
2pre 0 Cx = dr d - W (r ) 0
r0
Cx =
e Opr02
d
1 4 3(1 - 2 ) P 4 R 1 + (1 - g + g ) 3 3 16dh E
2
HIT-MEMS chen 11
3 Micro Pressure Sensor
HIT-MEMS chen 11
HIT-MEMS chen 11
ADXL50 – Microstructure
•
Sensitivity
S=
6meq L bEh 2
•
Natural frequency
K 0 = 0.23m + M
TG-320 数码相机规格说明书
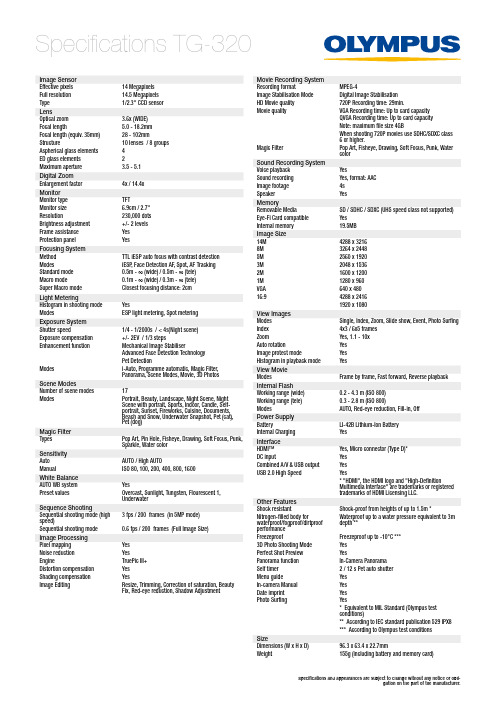
Specifications TG-320Specifications and appearances are subject to change without any notice or obli-gation on the part of the manufacturer.Image Sensor Effective pixels 14 Megapixels Full resolution 14.5 Megapixels Type1/2.3'' CCD sensor LensOptical zoom 3.6x (WIDE)Focal length5.0 - 18.2mm Focal length (equiv. 35mm)28 - 102mmStructure10 lenses / 8 groups Aspherical glass elements 4ED glass elements 2Maximum aperture 3.5 - 5.1Digital Zoom Enlargement factor 4x / 14.4x Monitor Monitor type TFTMonitor size 6.9cm / 2.7''Resolution230,000 dots Brightness adjustment +/- 2 levels Frame assistance Yes Protection panel YesFocusing System Method TTL iESP auto focus with contrast detection ModesiESP , Face Detection AF, Spot, AF Tracking Standard mode 0.5m - ∞ (wide) / 0.5m - ∞ (tele)Macro mode0.1m - ∞ (wide) / 0.3m - ∞ (tele)Super Macro mode Closest focusing distance: 2cm Light MeteringHistogram in shooting mode YesModesESP light metering, Spot metering Exposure System Shutter speed1/4 - 1/2000s / < 4s(Night scene)Exposure compensation +/- 2EV / 1/3 stepsEnhancement functionMechanical Image StabiliserAdvanced Face Detection Technology Pet DetectionModesi-Auto, Programme automatic, Magic Filter, Panorama, Scene Modes, Movie, 3D Photos Scene ModesNumber of scene modes 17ModesPortrait, Beauty, Landscape, Night Scene, Night Scene with portrait, Sports, Indoor, Candle, Self-portrait, Sunset, Fireworks, Cuisine, Documents, Beach and Snow, Underwater Snapshot, Pet (cat), Pet (dog)Magic Filter Types Pop Art, Pin Hole, Fisheye, Drawing, Soft Focus, Punk, Sparkle, Water colorSensitivity Auto AUTO / High AUTOManual ISO 80, 100, 200, 400, 800, 1600White Balance AUTO WB system YesPreset valuesOvercast, Sunlight, Tungsten, Flourescent 1, UnderwaterSequence ShootingSequential shooting mode (high speed)3 fps / 200 frames (in 5MP mode)Sequential shooting mode 0.6 fps / 200 frames (Full Image Size)Image Processing Pixel mapping Yes Noise reduction YesEngineTruePic III+ Distortion compensation Yes Shading compensation YesImage EditingResize, Trimming, Correction of saturation, Beauty Fix, Red-eye reduction, Shadow AdjustmentMovie Recording System Recording formatMPEG-4Image Stabilisation Mode Digital Image Stabilisation HD Movie quality 720P Recording time: 29min.Movie qualityVGA Recording time: Up to card capacity QVGA Recording time: Up to card capacity Note: maximum file size 4GBWhen shooting 720P movies use SDHC/SDXC class 6 or higher.Magic FilterPop Art, Fisheye, Drawing, Soft Focus, Punk, Water colorSound Recording System Voice playback YesSound recording Yes, format: AAC Image footage 4s SpeakerYesMemoryRemovable MediaSD / SDHC / SDXC (UHS speed class not supported)Eye-Fi Card compatible Yes Internal memory 19.5MB Image Size 14M 4288 x 32168M 3264 x 24485M 2560 x 19203M 2048 x 15362M 1600 x 12001M 1280 x 960VGA 640 x 48016:94288 x 24161920 x 1080View Images Modes Single, Index, Zoom, Slide show, Event, Photo Surfing Index 4x3 / 6x5 frames ZoomYes, 1.1 - 10x Auto rotationYes Image protect modeYes Histogram in playback mode YesView Movie ModesFrame by frame, Fast forward, Reverse playback Internal Flash Working range (wide)0.2 - 4.3 m (ISO 800) Working range (tele)0.3 - 2.8 m (ISO 800)ModesAUTO, Red-eye reduction, Fill-in, Off Power Supply BatteryLI-42B Lithium-Ion Battery Internal ChargingYesInterface HDMI™Yes, Micro connector (Type D)*DC inputYes Combined A/V & USB output Yes USB 2.0 High SpeedYes* "HDMI", the HDMI logo and "High-DefinitionMultimedia Interface" are trademarks or registered trademarks of HDMI Licensing LLC.Other Features Shock resistantShock-proof from heights of up to 1.5m *Nitrogen-filled body forwaterproof/fogproof/dirtproof performance Waterproof up to a water pressure equivalent to 3m depth **FreezeproofFreezeproof up to -10°C ***3D Photo Shooting Mode Yes Perfect Shot Preview YesPanorama function In-Camera Panorama Self timer 2 / 12 s Pet auto shutter Menu guideYes In-camera Manual Yes Date imprint Yes Photo SurfingYes* Equivalent to MIL Standard (Olympus test conditions)** According to IEC standard publication 529 IPX8*** According to Olympus test conditions SizeDimensions (W x H x D)96.3 x 63.4 x 22.7mmWeight155g (including battery and memory card)。
Crouzet Syrelec控制继电器系列说明书

CONTROL RELAYSCrouzet offers several variations of Syrelec control relays.Five models for liquid level controls, 3 phase 230V, 380V, 440V and 480V for phase loss or reversal protection, current and voltage detection and control, motion detection, and alternating relays are also available.If a standard control requires modification or a special product is needed to meet your exact needs, please call us or the Crouzet Sales Representative nearest you.Crouzet has controls to meet your CE, UL, and CSA requirements.SERIES FUNCTIONFEATURES SERIES F U N C T I O N FEATURES NNR SeriesLiquid LevelControlPC Board liquid levelcontrol.Pumpup/Pump down.4.7 to47K ohm sensitivity.SPDT 10A output relay3.62˝ x 2.16˝Liquid LevelControlNR SeriesLLC PumpDownNRU SeriesLLC Pump UpPlug-in or Din-Railmount.4.7 to 100Kohm sensitivity.1.89˝H x 1.89˝W x3.9˝LLiquid LevelControl PumpDownLiquid LevelControl PumpUpEN SeriesEND SeriesLiquid LevelControlLiquid LevelControlDin-Rail/surface mount.Pump up/Pump down.5K to 100K ohm sensi-tivity.80mmH x22.5mmW x 100mmLIR.T SeriesCurrentControl RelayMonitorsCurrent withRelay OutputPlug-in or Din-Railmount.Adjustableinhibit time for start up.LED Relay output indi-cator.3mAmp to7Amps-AC, 5mA to10Amps DC.1.89˝H x1.89˝W x 3.9˝LEIL EIH EITSeriesCurrentControl RelayMonitorsCurrent withRelay OutputDin-Rail/surfacemount.Adjustable timeinhibits.2mAmp to10Amps AC/DC.forEIL/EIH .01 to100Amps for EITw/transformer.80mmHx 22.5mmW x 100mmLUR SeriesVoltageControl RelayMonitorsVoltage withRelay OutputPlug-in or Din-Railmount .1 to 400 VoltsAC/DC.With latchingfunction selectable.LED output indication.1.89˝H x 1.89˝W x3.9˝LCTD/CTHSeriesT emperatureControllersP, PI, PIDOn/OffAuto TuningHeat/CoolSingle and dual displaymodels.Thermocoupleand RTD inputs.Auto-tuning for PID mod.Soft start function.WRL SeriesPhaseMonitorPhase ControlRelayMonitors:- PhaseSequence- Loss of Phase- Under VoltagePlug-in or Din-Railmount.3 x 230 VAC, 3x 380 VAC, 3 x 480VAC, 1.89˝H x 1.89˝Wx 3.9˝LHDU SeriesVoltageControl RelayMonitorsVoltage.With RelayOutput.With LCDDisplay..2 to 600 Volt AC/DC v o l t-age monitoring ra n g e.O v er and under v o l t a g ef u n c t i o n s.With LCD dis-p l a y.S h o ws actual ands e t p o i n t s.Din-Rail mount.81mmH x 36mmW x81m m LFW SeriesPhaseMonitorMonitors:- Phase Loss- PhaseReversal- UndervoltageDin-Rail or surface mount.3 x 230 VAC, 3 x 380VAC, 3 x 480 VAC, 3 x600 VAC.45mm widee n c l o s u r e.A d j u s t a b le timei n h i b i t.LED power on andr e l a y status.79mmH x45mmW x 100mmLEUL,EUHSeriesVoltageControl RelayMonitorsVoltage withRelay OutputD i n-R a i l/s u r f ace mount.A d j u s t a b le time inhibit..2 to 600 Volts AC/D C.S e l e c t a b le latching fe a-t u r e.80mmH x22.5mmW x 100mmLJR SeriesAlternatingRelayDuplexAlternatingRelayPlug-in style.Designedfor dual pump system.Selector switch ver-sions available.1.89˝Hx 1.89˝W x 3.9˝LMCI SeriesCurrentControl RelayMonitorsCurrent.WithRelay Output.With Built-inTr ansformer1 to 20Amp AC/DC cur-rent monitoring ra n g e.Built-in tra n s f o r m e r.R e l a youtput-SPDT Over andunder current functions.81mmH x 17.5mmW x83m m LF3I SeriesMotorProtectionRelayMotorProtection forPhase LossPhaseUnbalanceCurrent Surge8 to 630Amp currentra n g e.LED diagnostics.A d j u s t a b le trip timers.Phase loss test s w i t c h.Front panel reset.79m m Hx 45mmW x 95mmLFWIT SeriesMotorProtectionRelayMotor Protectionfor Phase LossPhase UnbalancePhase Rev e r s a lCurrent SurgeO v e r h e a t i n g7 to 630Amp currentrange.LED diagnos-tics.Adjustable triptimers Phase loss testswitch.Front panelreset.80mmH x78mmW x 99mmLHDI SeriesCurrentControl RelayMonitorsCurrent.WithRelay Output.With LCDDisplay.2mA to 10Amp;AC/D Ccurrent monitoring r a n g e.O v er and under currentf u n c t i o n s.With LCD dis-p l a y.S h o ws actualand setpoints.D i n-R a i lm o u n t.81mmH x36mmW x 66mmL83311CONTROLS&SENSORS Toll Free 1-800-526-5376Fax 201-337-1862201-337-1000Control Relays845Toll Free 1-800-526-5376Fax 201-337-1862201-337-1000Protective Relays & Alternating RelaysAdjustableProduct Number Product Number Operating Voltage UndervoltagePlug-inCase Socket Surface-Mount 50/60 Hz Drop-out Range(8 pin octal socket)Case*208/240V 180-230VPMP24070169-D PMD240480V 360-460V PMP480**70175PMD480PHASE MONITOR RELAYSProvides microprocessor-based protection for 3 phase systems against phase loss, phase rever-sal, phase unbalance, and under voltage.These devices are designed to be compatible with most Wye or Delta systems.In Wye systems, a connection to a neutral is not required.Phase Monitoring Relays protect against unbalanced voltages or single phasing regardless of any regenerative voltages.The relay is energized when the phase sequence and all voltages are correct.Any one of four fault conditions will de-energize the relay.Re-energization is automatic upon correction of the fault condition.An LED indicates normal and tripped conditions.The per-cent phase unbalance is adjustable from 2-10%, and the undervoltage drop-out can be set at 75-95% of operating voltage.The adjustable time delay dropout on undervoltage (0.1-20 sec-onds) eliminates nuisance tripping caused by momentary voltage fluctuations.Output :10A SPDT (PMP) or DPDT (PMD) @ 240VAC/30VDC.Dimensions :PMP-1.7”x 2.4”x 3.5”.PMD-1.8”x 2.75”x 4.4”.PMP Plug-in PMD Surface-Mount File LR45565File LR45565File E109461Provides protection to equipment where an over or under voltage condition is potentially damaging.They monitor either AC single phase (50-400hz) or DC (independent of polarity) voltages.No supply (input) voltage is required.The pick-up voltage setting is user-adjustable from 85-115% of the nominal voltage rating.The drop-out voltage setting is fixed at 3% below the pick-up voltage setting.The relay energizes when the monitored voltage is above the pick-up setting.The relay de-energizes when the monitored voltage is below the drop-out setting.The time delay on drop-out is fixed at 50ms.Output :10A DPDT @ 240VAC/30VDC.Dimensions :1.7”x 2.4”x 2.9”.ALTERNATING R ELAYSUsed in special applications where the optimization of load usage is required by equalizing the run time of two loads.They are also used where additional capacity is required in case of excess load requirements.This alternating action is initiated by a control switch, such as a float switch, manual switch, timing relay, pressure switch, or other isolated contact.Each time the initiating switch is opened, the output relay contacts will change state, thus alternating the two loads.Tw o LED indicators show the status of the output relay.As listed, these units come with a three position selector switch.This allows the unit to alternate the two loads as normal, or lock the relay to one load or the other.By locking the Alternating Relay to one load, the other load can be removed for service without rewiring the first load for continuous operation.The selector switch has a low profile to prevent any accidental changes in status.Output :10A SPDT or DPDT Cross-Wired @ 240VAC/30VDC.Dimensions :1.7”x2.4”x 2.9”.Product NumberControlSPDT DPDT Cross-Voltage Contacts Wired Contacts Socket File E109461SPDT DPDT Cross-WiredNominalPick-up Drop-Out Product VoltageVoltage Range Voltage Range Number Socket 24V AC21-27V AC 20-26V AC VMP024A 120V AC102-138V AC 99-134V AC VMP120A 240V AC204-276V AC 198-267V AC VMP240A 12V DC10-14V DC 9-13V DC VMPO12D 24V DC 21-27V DC 20-26V DC VMP024D 8 PIN OCTAL 70169-D File E109461File LR45565**Requires 600V-rated socket* No socket required for PMD240 or PMD4801 1C O N T R O L S &S E N S OR S。
- 1、下载文档前请自行甄别文档内容的完整性,平台不提供额外的编辑、内容补充、找答案等附加服务。
- 2、"仅部分预览"的文档,不可在线预览部分如存在完整性等问题,可反馈申请退款(可完整预览的文档不适用该条件!)。
- 3、如文档侵犯您的权益,请联系客服反馈,我们会尽快为您处理(人工客服工作时间:9:00-18:30)。
• Again, independence between
different components is assumed.
23
Example
Likelihood field Map m P(z|x,m)
24
San Jose Tech Museum
Occupancy grid map
Likelihood field
2
Proximity Sensors
• The central task is to determine P(z|x), i.e., the • •
probability of a measurement z given that the robot is at position x. Question: Where do the probabilities come from? Approach: Let’s try to explain a measurement.
0.3 0.25 0.2 0.15 0.1 0.05 0 0 40 50 60 70
10 20 30 20 30 40 10 50 60 0 70
19
Influence of Angle to Obstacle
"sonar-3"
0.25 0.2 0.15 0.1 0.05 0 0 40 50 60 70
10 20 30 20 30 40 10 50 60 0 70
20
Summary Beam-based Model
• Assumes independence between beams.
• Justification? • Overconfident!
• Models physical causes for measurements.
1. Beams reflected by obstacles 2. Beams reflected by persons / caused by crosstalk 3. Random measurements 4. Maximum range measurements
6
Proximity Measurement
3
Beam-based Sensor Model
• Scan z consists of K measurements.
z = {z1 , z 2 ,..., z K }
• Individual measurements are
P ( z | x , m ) = ∏ P ( z k | x , m)
k =1 K
independent given the robot position.
4
Beam-based Sensor Model
P ( z | x , m ) = ∏ P ( z k | x , m)
k =1
K
5
Typical Measurement Errors of an Range Measurements
How can we determine the model parameters?
10
Raw Sensor Data
Measured distances for expected distance of 300 cm.
Sonar
Laser
11
Approximation
• Maximize log likelihood of the data P( z | zexp ) • Search space of n-1 parameters.
28
Additional Models of Proximity Sensors
• Map matching (sonar,laser): generate
small, local maps from sensor data and match local maps against global model. by scan endpoints, match scan into this map.
• • • • Sonar (time of flight) Radar (phase and frequency) Laser range-finders (triangulation, tof, phase) Infrared (intensity)
• Visual sensors: Cameras • Satellite-based sensors: GPS
~0.01 sec
27
Properties of Scan-based Model
• Highly efficient, uses 2D tables only. • Smooth w.r.t. to small changes in robot
position.
• Allows gradient descent, scan matching. • Ignores physical properties of beams. • Will it work for ultrasound sensors?
• Measurement can be caused by …
• • • • • • • • a known obstacle. cross-talk. an unexpected obstacle (people, furniture, …). missing all obstacles (total reflection, glass, …). in measuring distance to known obstacle. in position of known obstacles. in position of additional obstacles. whether obstacle is missed.
• • • • Hill climbing Gradient descent Genetic algorithms …
• Deterministically compute the n-th
parameter to satisfy normalization constraint.
12
Approximation Results
7
• Noise is due to uncertainty …
Beameasurement noise Unexpected obstacles
0
zexp
zmax
0
zexp
zmax
Phit ( z | x, m) = η
1 e 2πb
1 ( z − z exp ) − 2 b
Introduction to Mobile Robotics
Probabilistic Sensor Models
Wolfram Burgard Cyrill Stachniss Giorgio Grisetti
SA-1
Sensors for Mobile Robots
• Contact sensors: Bumpers • Internal sensors
• Mixture of densities for these causes. • Assumes independence between causes. Problem?
• Implementation
• Learn parameters based on real data. • Different models should be learned for different angles at which the sensor beam hits the obstacle. • Determine expected distances by ray-tracing. • Expected distances can be pre-processed.
1 z max
Pmax ( z | x, m) = η
1 z small
9
Resulting Mixture Density
α hit α unexp P ( z | x , m) = α max α rand
T
Phit ( z | x, m) Punexp ( z | x, m) ⋅ Pmax ( z | x, m) P ( z | x , m) rand
21
Scan-based Model
• Beam-based model is …
• not smooth for small obstacles and at edges. • not very efficient.
• Idea: Instead of following along the
beam, just check the end point.
25
Scan Matching
• Extract likelihood field from scan and
use it to match different scan.
26
Scan Matching
• Extract likelihood field from first scan
and use it to match second scan.
17
Influence of Angle to Obstacle
"sonar-1"
0.3 0.25 0.2 0.15 0.1 0.05 0 0 40 50 60 70
10 20 30 20 30 40 10 50 60 0 70
18
Influence of Angle to Obstacle