结晶器种类及主要特点
连铸圆坯结晶器铜管分类、形式及技术要求

连铸圆坯结晶器铜管分类、形式及技术要求2010年10月15日星期五 08:17除按钢种分类外,一般情况下,按截面尺寸可将圆坯分为以下几种:直径小于350mm为小圆坯;直径350~500mm为大圆坯;直径大于500mm为超大截面圆坯。
目前,世界上已经浇注出的最大规格的圆坯为直径为700mm.,而国内已自行研发能够生产直径为600mm特种钢圆坯,浇注直径超过800mm的圆坯连铸机国内正在自主研发中。
圆坯结晶器的形势比较单一。
一个典型的圆坯结晶器由铜管、内水套、外水套、给水管、排水管、水环、足锟、底部和顶部法兰以及润滑法兰等部件组成。
通常情况下,圆坯结晶器浇注绝大多数只采用保护渣作为润滑剂,所用的浸入式水口也是直通式水口。
采用这种直通式浸入形式水口的好处是结晶器表面处的钢水流速比较小,液面平静,有利于防止液面的卷渣。
其不利之处在于,结晶器内钢液流股的冲击深度较深,即结晶器内钢液高温区下移,将会对结晶器液面上保护渣的溶化、夹杂物上浮等均产生负面影响,从而有可能导致铸坯表面和内部出现质量缺陷,故应利用外力来改善结晶器内钢液流动状态,这就是圆坯连铸机一般都配置结晶器电磁搅拌的理由之一。
与其他种类连铸坯不同,圆坯无角部的优先凝固,而且没有鼓肚危险,因此圆坯结晶器设计主要是要保持结晶器的均匀冷却,使坯壳均匀收缩,防止铸坯产生椭圆物理变形和表面裂纹。
对于一个给定的铸坯尺寸,圆坯结晶器受热面积比方坯要小一些,因而拉速要低一些。
为保证圆坯质量,连铸生产上的一些有效质量控制技术(如全程保护浇注、大容量中间包、二次冷却控制、液面自动控制、结晶器电磁搅拌等)在圆坯连铸上均要使用,尤其是大截面圆坯除采用上述技术外,根据质量要求,二冷区还要使用电磁搅拌、末端电磁搅拌技术以及三次冷却控制技术。
对特殊钢种而言,圆坯下线后的缓冷控制依然十分重要。
电磁搅拌(EMS)。
蒸发结晶工艺及设备

蒸发结晶工艺及设备一、蒸发结晶工艺的概述蒸发结晶是化学工业中常见的分离和纯化方法,通过调节温度和压力控制溶液中溶质的浓度,使溶质从溶液中析出形成晶体,从而实现纯化的目的。
蒸发结晶工艺广泛应用于化工、制药、食品等行业,是一种高效、经济、环保的分离技术。
二、蒸发结晶的工艺过程蒸发结晶工艺一般包括物料供给、蒸发浓缩、冷却结晶和产物分离等步骤。
具体工艺过程如下:1. 物料供给物料供给是蒸发结晶的起始步骤,需要将原始溶液或浓缩液注入蒸发器中。
溶液的供给方式有多种,如自流式供给、泵送供给、气力输送等。
根据溶液的性质和工艺要求选择适合的物料供给方式。
2. 蒸发浓缩在蒸发器中,溶液受热蒸发,蒸发介质带走部分水分,使溶液中溶质浓度升高。
蒸发浓缩过程需要根据溶液的性质和要求选择适合的蒸发器类型,如单效蒸发器、多效蒸发器、蒸发塔等。
3. 冷却结晶经过蒸发浓缩后的溶液进一步降温,使溶质超过饱和度,从而形成结晶核并逐渐生长,最终形成晶体。
冷却结晶过程需要控制降温速度、搅拌强度和时间等参数,以获得所需的晶体形态和尺寸。
4. 产物分离结晶过程结束后,需要将产物与溶液分离,通常通过离心、过滤、洗涤等方法实现。
分离后的产物可以用于进一步的处理和利用,溶液则可以回收和再利用。
三、蒸发结晶设备的种类和选择蒸发结晶设备的选择应根据溶液的性质、结晶目标和工艺要求来确定。
常见的蒸发结晶设备有:1. 蒸发器蒸发器是蒸发结晶过程中最主要的设备之一,根据传热方式的不同可以分为直接加热蒸发器和间接加热蒸发器。
常见的蒸发器类型有: - 管式蒸发器 - 挤管蒸发器- 浴式蒸发器2. 结晶器结晶器是用于冷却结晶过程的设备,常见的结晶器类型有: - 槽式结晶器 - 挂篮结晶器 - 充填床结晶器3. 分离设备分离设备用于将产物与溶液分离,常见的分离设备有: - 离心机 - 过滤机 - 离心过滤机根据溶液的性质和工艺要求选择合适的设备,同时要考虑设备的操作方便性、效率和经济性等因素。
结晶器的原理

结晶器的原理结晶器是一种常见的实验设备,用于从溶液中分离出晶体。
它的原理基于溶解度和结晶过程的物理化学规律。
在结晶器中,溶液中的溶质随着溶剂的挥发逐渐饱和,导致溶质逐渐凝结成晶体,从而实现了分离的目的。
首先,溶液中的溶质在溶剂中的溶解度是一个关键因素。
溶解度取决于溶质和溶剂的性质,温度和压力等因素。
当溶质在溶剂中的溶解度达到饱和状态时,就会出现过饱和现象,这时溶质会开始凝结成晶体。
其次,结晶器中的温度控制也是至关重要的。
通常情况下,通过控制结晶器的温度,使溶剂逐渐挥发,从而导致溶质逐渐饱和并凝结成晶体。
温度的控制可以影响结晶速率和晶体的质量,因此在实验过程中需要精确控制温度。
此外,结晶器的设计也对结晶过程有着重要影响。
结晶器通常采用圆底烧瓶或结晶皿等容器,通过表面积和形状的设计来影响溶剂的挥发速率和晶体的形成。
合适的结晶器设计可以提高结晶效率和晶体的纯度。
总的来说,结晶器的原理是通过控制溶质在溶剂中的溶解度和温度,以及结晶器的设计,实现溶质从溶液中凝结成晶体的过程。
这一原理在化学、生物、药物等领域都有着广泛的应用,是一种重要的分离和纯化技术。
结晶器的原理虽然看似简单,但在实际操作中需要注意许多细节。
例如,在控制温度时需要避免温度波动,以免影响结晶过程;在结晶器的设计中需要考虑溶剂的挥发速率和晶体的收集等因素。
只有充分理解结晶器的原理,并在实验操作中严格控制各项条件,才能获得理想的结晶效果。
总之,结晶器作为一种重要的分离和纯化技术,其原理基于溶解度和结晶过程的物理化学规律。
通过控制溶质在溶剂中的溶解度和温度,以及结晶器的设计,可以实现溶质从溶液中凝结成晶体的目的。
在实际操作中,需要注意各项条件的控制,以获得理想的结晶效果。
连铸圆坯结晶器

连铸机结晶器总成1、结晶器总成组合式结晶器由结晶器本体、支撑框架以及足锟等部件组成。
结晶器本体由4块铜板及支撑板组合而成,用螺栓连接为一体;支撑框架带有定位、固定装置和冷却水通道;足锟包括支架、锟子、轴承、水管和喷嘴等。
组合式结晶器可以配置液位检测装置、外置式电磁搅拌装置。
2、结晶器结构特点A、结晶器本体两块弧面铜板和两块侧面铜板组合成结晶器内腔,铜板上加工有若干冷却水槽(即水缝),用螺钉将铜板与支承板(也称为背板)连接。
支承板上设有冷却水通道,冷却水从振动台上的供水孔进入支撑框架再进入支承板,再通过支撑框架流回到振动台上的回水孔。
设计时,需要根据冷却水压强核算螺钉连接的受力及强度,并调整连接螺钉数量,直至满足要求。
一般情况下,两排螺钉之间布置5~6条水缝。
结晶器内腔角部的倒角一般采用早弧面和侧面铜板的结合部位垫有带45°斜面的铜质垫板形成;也有直接在侧面铜板上加工出倒斜角斜面的。
铜板厚度一般为45~50mm,主要取决于水缝深度和再加工要求。
可采用的材质有Cu—Ag和Cu—Cr—Zr。
如果连铸机拉速不高,相应铜板热面温度不超过250℃,可以采用Cu—Ag。
随着连铸技术发展和操作水平提高,连铸机拉速也相应提高,结晶器铜板有必要采用Cu—Cr—Zr合金,可以满足热面温度为350℃甚至更高的工况。
目前,国内方坯结晶器铜板次用Cu—Ag和Cu—Cr—Zr的都有,采用Cu—Cr—Zr的日趋增多。
为了提高结晶器使用寿命,铜板都会经过表面处理,即镀层。
典型的镀层材料有Cr、Ni、Ni—Fe、Ni—Co、Co—Ni。
Cr的硬度高,督促呢个化学稳定性好,但Cr与Cu的线膨胀系数差距较大,镀层结合力差,镀层易剥落。
Ni与Cu的结合力好,但其镀层硬度相对较低,高温耐磨性差。
现已很少采用单独镀Cr或Ni得铜板。
Ni—Fe、Ni—Co、Co—Ni都有硬度高、耐磨性好的特点,其中Ni—Fe的化学稳定性较差,其镀层韧性随着硬度增加会降低;Ni—Co的抗热交变性稍差;Co—Ni的材料成本较高。
结晶器种类及主要特点

结晶器种类及主要特点2010-9-279:09:27薄板坯和中薄板坯连铸技术的核心是结晶器。
对于结晶器的研究主要有以下种类:1、漏斗形结晶器1)几何形状德马克公司ISP工艺的第一代立弯式结晶器,上部是垂直段,下部是弧形段,侧板可调,上口断面是矩形,尺寸为(60-80)mm×(650-1330)mm。
意大利阿维迪厂采用了该工艺,并略作修改,上口断面形状,由原平行板形改为小漏斗形。
西马克公司CSP工艺所用的漏斗形结晶器,上口宽边两侧均有平行段,再与圆弧段相连接,上口断面较大。
这个漏斗形状在结晶器内保持到长700mm,结晶器出口处铸坯厚度为50-70mm。
2)主要特点漏斗形结晶器打破了传统板坯连铸结晶器在任意横截面均相同的限制,其结晶器腔内凝固壳的形状及大小按非矩形截面逐步缩小的规律变化。
但是,钢液在这种结晶器内凝固时要产生变形,特别是拉坯过程中机械变形产生的应力可能导致固液界面裂纹发生,并最终影响热轧带卷的质量。
因此,漏斗形结晶器的理想形状是尽量减小坯壳间两相区的弯曲变形率,使坯壳在固液变形率小于发生裂纹的临界应变率。
2、H2结晶器1)几何形状意大利达涅利公司FISC工艺是其代表FISC工艺优点是内部容积达,通过的钢液流量大,且有更好的钢液自然减速效应。
该结晶器长度为1200mm,宽度为1220-1620mm,厚度为50、60、65、70mm。
2)主要特点该结晶器鼓肚形状由上至下贯穿整个铜板,并一直延续到扇形I段的中部。
结晶器出口处为将铸坯鼓肚形状矫平而特别设计了一组带孔型的辊子,对铸坯鼓肚进行矫平的设备长度比仅用连铸机结晶器时长两倍,即与仅用结晶器来矫平坯壳的鼓肚相比,坯壳上所受应力大大降低。
并且H2结晶器内部体积增大,可以盛装更多的钢液。
同时,结晶器上部尺寸加大,可使水口形状设计更合理,保证结晶器内液面稳定,提高保护渣的润滑效果,改善热交换条件,提高拉速,减少裂纹倾向。
3、平行板形直结晶器1)几何形状奥钢联公司CONROLL工艺是其代表。
化工设备基础知识试题答案(第三版)前五章

《化工设备机械基础》单元测试题第一章化工设备基础知识一、填空题1.化工设备广泛地应用于化工、食品、医药、石油及其相关的其他工业部门。
虽然它们服务的对象、操作条件、内部结构不同,但是它们都有一个外壳,这一外壳称为容器。
2.要保证化工容器能长期安全运转,化工容器必须具备足够的强度、密封性、耐蚀性及稳定性。
3.化工容器是一个钢制圆筒形结构,主要由钢制圆筒体和两端的封头组成,并设有各种化工工艺接管。
4.按压力容器的设计压力(p),可将容器分为低压压力容器、中压压力容器、高压压力容器和超高压压力容器四个压力等级。
5.根据容器所受压力的大小、介质的毒性和易燃、易爆程度以及压力和体积乘积的大小,可将压力容器分为三类,即一类压力容器、二类压力容器、三类压力容器。
二、简答题1.化工容器与其他行业的容器相比较有哪些特点?它经常在高温、高压下工作,它里面的介质有可能是易燃、易爆、有毒、有害且具有腐蚀性。
2.按照压力容器在生产过程中的作用原理,可将压力容器分为哪几种?①反应压力容器(代号为R)。
它主要用于完成介质的物理、化学反应,如反应釜、分解塔、合成塔、变换炉、煤气发生炉等。
②换热压力容器(代号为E)。
它主要完成介质的热量交换,如热交换器、冷凝器、蒸发器、冷却器等。
③分离类容器(代号为S)。
它主要完成介质的净化分离,如分离器、洗涤塔、过滤器、吸收塔、干燥塔等。
④储存类容器(代号为C,其中球罐的代号为B)。
它主要用于储存或盛装生产用的原料气体、液体、液化气体等,如各种形式的储罐。
3.化工设备在使用年限内,安全可靠是化工生产对其最基本的要求,要达到这一目的,必须对化工设备提出哪几方面的要求?(1)强度(2)刚度(1)强度(2)刚度(3)稳定性(4)耐蚀性(5)密封性4.什么是强度?什么是刚度?化工设备的强度是指设备及其零部件抵抗外力破坏的能力,或在外力作用下不被破坏的能力。
刚度是指容器及其零部件抵抗外力作用下变形的能力。
CSP的设备特点和工艺特点
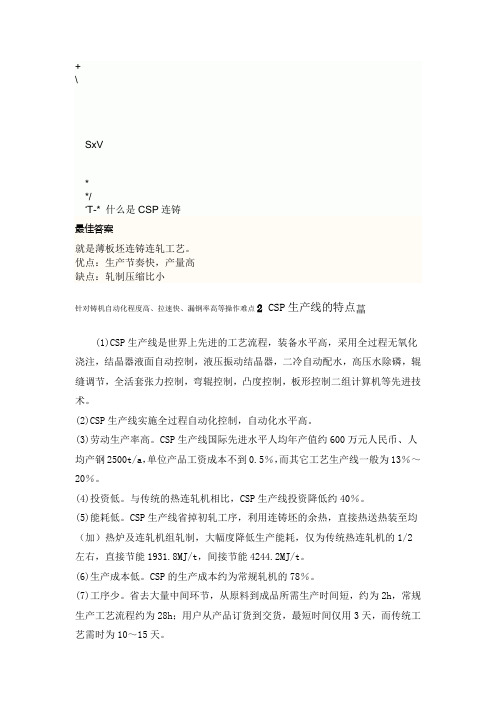
+\SxV**/‘T-* 什么是CSP连铸最佳答案就是薄板坯连铸连轧工艺。
优点:生产节奏快,产量高缺点:轧制压缩比小针对铸机自动化程度高、拉速快、漏钢率高等操作难点2 CSP生产线的特点(1)CSP生产线是世界上先进的工艺流程,装备水平高,采用全过程无氧化浇注,结晶器液面自动控制,液压振动结晶器,二冷自动配水,高压水除磷,辊缝调节,全活套张力控制,弯辊控制,凸度控制,板形控制二组计算机等先进技术。
(2)CSP生产线实施全过程自动化控制,自动化水平高。
(3)劳动生产率高。
CSP生产线国际先进水平人均年产值约600万元人民币、人均产钢2500t/a,单位产品工资成本不到0.5%,而其它工艺生产线一般为13%~20%。
(4)投资低。
与传统的热连轧机相比,CSP生产线投资降低约40%。
(5)能耗低。
CSP生产线省掉初轧工序,利用连铸坯的余热,直接热送热装至均(加)热炉及连轧机组轧制,大幅度降低生产能耗,仅为传统热连轧机的1/2左右,直接节能1931.8MJ/t,间接节能4244.2MJ/t。
(6)生产成本低。
CSP的生产成本约为常规轧机的78%。
(7)工序少。
省去大量中间环节,从原料到成品所需生产时间短,约为2h,常规生产工艺流程约为28h;用户从产品订货到交货,最短时间仅用3天,而传统工艺需时为10~15天。
(8)占地面积少。
CSP生产工艺线流程短,布局紧凑,比传统生产工艺占地面积少。
(9)污染少。
(10)成材率比常规轧机高1.8%。
(11)维修费用约为常规轧机的39%。
1结晶器的种类及主要特点薄板坯和中薄板坯连铸设备的核心是结晶器。
设计要求结晶器弯月面区域必须有足够的空间,以插入浸入式水口,且满足水口壁与结晶器壁之间无凝固桥形成,钢液温度分布均匀,有利于保护渣熔化;弯月面区钢液流动平稳,防止过大紊流而卷渣;结晶器几何形状应满足拉坯时坯壳承受的应力最小。
CSP工艺设备技术特点及采用的新技术1 CSP连铸工艺设备技术特点及采用的新技术1)连铸部分工艺介绍连铸部分工艺如图2所示。
结晶器种类及主要特点

结晶器种类及主要特点2010-9-27 9:09:27薄板坯和中薄板坯连铸技术的核心是结晶器。
对于结晶器的研究主要有以下种类:1、漏斗形结晶器1)几何形状德马克公司ISP工艺的第一代立弯式结晶器,上部是垂直段,下部是弧形段,侧板可调,上口断面是矩形,尺寸为(60-80)mm×(650-1330)mm。
意大利阿维迪厂采用了该工艺,并略作修改,上口断面形状,由原平行板形改为小漏斗形。
西马克公司CSP工艺所用的漏斗形结晶器,上口宽边两侧均有平行段,再与圆弧段相连接,上口断面较大。
这个漏斗形状在结晶器内保持到长700mm,结晶器出口处铸坯厚度为50-70mm。
2)主要特点漏斗形结晶器打破了传统板坯连铸结晶器在任意横截面均相同的限制,其结晶器腔内凝固壳的形状及大小按非矩形截面逐步缩小的规律变化。
但是,钢液在这种结晶器内凝固时要产生变形,特别是拉坯过程中机械变形产生的应力可能导致固液界面裂纹发生,并最终影响热轧带卷的质量。
因此,漏斗形结晶器的理想形状是尽量减小坯壳间两相区的弯曲变形率,使坯壳在固液变形率小于发生裂纹的临界应变率。
2、H2结晶器1)几何形状意大利达涅利公司FISC工艺是其代表FISC工艺优点是内部容积达,通过的钢液流量大,且有更好的钢液自然减速效应。
该结晶器长度为1200mm,宽度为1220-1620mm,厚度为50、60、65、70mm。
2)主要特点该结晶器鼓肚形状由上至下贯穿整个铜板,并一直延续到扇形I段的中部。
结晶器出口处为将铸坯鼓肚形状矫平而特别设计了一组带孔型的辊子,对铸坯鼓肚进行矫平的设备长度比仅用连铸机结晶器时长两倍,即与仅用结晶器来矫平坯壳的鼓肚相比,坯壳上所受应力大大降低。
并且H2结晶器内部体积增大,可以盛装更多的钢液。
同时,结晶器上部尺寸加大,可使水口形状设计更合理,保证结晶器内液面稳定,提高保护渣的润滑效果,改善热交换条件,提高拉速,减少裂纹倾向。
3、平行板形直结晶器1)几何形状奥钢联公司CONROLL工艺是其代表。
- 1、下载文档前请自行甄别文档内容的完整性,平台不提供额外的编辑、内容补充、找答案等附加服务。
- 2、"仅部分预览"的文档,不可在线预览部分如存在完整性等问题,可反馈申请退款(可完整预览的文档不适用该条件!)。
- 3、如文档侵犯您的权益,请联系客服反馈,我们会尽快为您处理(人工客服工作时间:9:00-18:30)。
结晶器种类及主要特点2010-9-27 9:09:27薄板坯和中薄板坯连铸技术的核心是结晶器。
对于结晶器的研究主要有以下种类:1、漏斗形结晶器1)几何形状德马克公司ISP工艺的第一代立弯式结晶器,上部是垂直段,下部是弧形段,侧板可调,上口断面是矩形,尺寸为(60-80)mm×(650-1330)mm。
意大利阿维迪厂采用了该工艺,并略作修改,上口断面形状,由原平行板形改为小漏斗形。
西马克公司CSP工艺所用的漏斗形结晶器,上口宽边两侧均有平行段,再与圆弧段相连接,上口断面较大。
这个漏斗形状在结晶器内保持到长700mm,结晶器出口处铸坯厚度为50-70mm。
2)主要特点漏斗形结晶器打破了传统板坯连铸结晶器在任意横截面均相同的限制,其结晶器腔内凝固壳的形状及大小按非矩形截面逐步缩小的规律变化。
但是,钢液在这种结晶器内凝固时要产生变形,特别是拉坯过程中机械变形产生的应力可能导致固液界面裂纹发生,并最终影响热轧带卷的质量。
因此,漏斗形结晶器的理想形状是尽量减小坯壳间两相区的弯曲变形率,使坯壳在固液变形率小于发生裂纹的临界应变率。
2、H2结晶器1)几何形状意大利达涅利公司FISC工艺是其代表FISC工艺优点是内部容积达,通过的钢液流量大,且有更好的钢液自然减速效应。
该结晶器长度为1200mm,宽度为1220-1620mm,厚度为50、60、65、70mm。
2)主要特点该结晶器鼓肚形状由上至下贯穿整个铜板,并一直延续到扇形I段的中部。
结晶器出口处为将铸坯鼓肚形状矫平而特别设计了一组带孔型的辊子,对铸坯鼓肚进行矫平的设备长度比仅用连铸机结晶器时长两倍,即与仅用结晶器来矫平坯壳的鼓肚相比,坯壳上所受应力大大降低。
并且H2结晶器内部体积增大,可以盛装更多的钢液。
同时,结晶器上部尺寸加大,可使水口形状设计更合理,保证结晶器内液面稳定,提高保护渣的润滑效果,改善热交换条件,提高拉速,减少裂纹倾向。
3、平行板形直结晶器1)几何形状奥钢联公司CONROLL工艺是其代表。
CONROLL工艺的平行板形直结晶器,浸入式水口也是扁平,钢液从水口两侧壁流出。
结晶器断面尺寸为(70-135)mm×1500mm。
2)主要特点平行板形直结晶器内腔的横截面从上到小均为全等矩形,在铸坯厚度较薄情况下,可避免因铸坯变形产生的坯壳应力,而且在宽度和长度方向上,结晶器热量能够保证均匀散失。
漏斗形结晶器、H2结晶器、平行板形直结晶器各有特点,从坯壳受力情况来看,平行板形直结晶器优于漏斗形和H2结晶器,从空间大小来看,漏斗形和H2结晶器优于平行板形直结晶器。
目前,国内研发主要集中在漏斗形结晶器,并应用于多条薄板坯连铸连轧生产线。
今后应在H2结晶器、平行板形直结晶器方面的关注研究。
(成王)薄板坯连铸机结晶器的主要特点及其技术进步潘秀兰;梁慧智;王艳红作者单位:鞍钢股份有限公司文摘:介绍了薄板坯和中薄板坯连铸机结晶器的形状和主要特点,对比分析了不同类型结晶器内钢液的表面积、钢液流动、结晶器传热、薄板坯厚度、拉坯速度等对连铸过程和铸坯性能的影响,讨论了鞍钢ASP 采用的先进技术,指出近年来新建和改造的薄板坯连铸机结晶器厚度呈现增加的趋势,从而解决了设备运行的一些问题,改善了铸坯的品种质量。
关键词:薄板坯;结晶器;主要特点;铸坯质量Analysis on main features and technology progress of thin slabcontinuous caster moldPAN Xiu-lan,LIANG Hui-zhi,WANG Yan-hong(Angang Steel Co.,Ltd.)Abstract:The paper introduces the sharp and main features of thin slab and medium-thin slab continuous caster,andcomparatively analyzes that the main factors on the effect of slab quality on steel surface area,steel flow,mold heattransfer,thin slab thickness and withdrawal speed and so on for the different types of mold. The advanced technologies ofASP are discussed in Angang. It points out the trend of mold thickness increased in the new and reconstruction thin slabcontinuous caster,solving the problems in the equipment operation,improving slab variety and quality.Key words:thin slab; mold; main feature; slab quality0前言结晶器是连铸机上的铸坯成型装置,也是连铸机的核心设备之一,其作用是通过强制冷却连续注入结晶器内腔的钢液,导出热量,使钢液逐渐凝固成具有所要求断面形状和一定坯壳厚度的铸坯,并将芯部仍为液相的铸坯连续地从结晶器下口拉出。
在钢液注入结晶器逐渐形成一定厚度坯壳的凝固过程中,结晶器同时受机械应力和热应力的综合作用,其运行状况直接关系到连铸机的顺行、铸坯的质量和产量。
目前,国内外常规大板坯、大方坯和小方坯连铸机结晶器技术基本成熟,此文仅探讨薄板坯和中薄板坯连铸机的结晶器的相关技术。
截至2008 年底,世界上共建设薄板坯( 包括中薄板坯) 连铸连轧生产线65条,年生产能力达到11 008 万t。
其中,CSP 生产工艺占世界薄板坯连铸-连轧总产能的50% 以上;其次是FTSR工艺,占总产能的18.35%。
其中,中国共建设不同类型的薄板坯连铸连轧生产线14 条,年产能3 530 万t。
1结晶器的种类及主要特点薄板坯和中薄板坯连铸设备的核心是结晶器。
设计要求结晶器弯月面区域必须有足够的空间,以插入浸入式水口,且满足水口壁与结晶器壁之间无凝固桥形成,钢液温度分布均匀,有利于保护渣熔化;弯月面区钢液流动平稳,防止过大紊流而卷渣;结晶器几何形状应满足拉坯时坯壳承受的应力最小。
1.1 漏斗形结晶器1.1.1 几何形状德马克公司ISP 工艺的第一代立弯式结晶器,上部是垂直段,下部是弧形段,侧板可调,上口断面是矩形,尺寸为(60~80) mm×(650~1 330) mm。
意大利阿维迪生产线采用该结晶器后,发现这种形状的结晶器只能使用薄片形浸入式水口,而且即使这种特殊形状的长水口很薄,插入结晶器内与结晶器壁也只能保持10~15 mm 的间隙,造成水口插入处宽面侧保护渣熔化不好,且很难获得可恒定控制的保护渣层,薄板坯的表面质量较差。
阿维迪厂在1993 年开始改进该结晶器,重新设计了其上口断面形状,由原平行板形改为小漏斗形,结晶器上口宽边最大厚度为60+(10×2) mm,这种形状一直保持到结晶器下口仍有(1.5×2)mm 的小鼓肚。
近年来,其结晶器的小鼓肚越改越大,现使用的上口宽边最大厚度已达60+(25×2) mm,下口为60+(5×2) mm,浸水式水口仍是薄片形,尽管壁厚有所增加,但其距器壁两侧的间隙大大增加,改善了保护渣层的熔化状况,薄板坯表面质量也有了很大改进。
西马克公司CSP 工艺所用的漏斗形结晶器,上口宽边两侧均有平行段,再与圆弧段相连接,上口断面较大。
这个漏斗形状在结晶器内保持到长700 mm,结晶器出口处铸坯厚度为50~70 mm。
结晶器总长为1 120 mm。
上口的漏斗形状有利于浸入式水口的浸入,在结晶器的两宽面板间垂直方向形成了一个带锥度的空间,而漏斗区以外的两侧壁仍然是平行的,两侧壁间的距离相当于板坯厚度。
漏斗形结晶器在形状上满足了长水口插入、保护渣熔化和薄板铸坯厚度的要求,经多条生产线使用,均收到较好效果。
1.1.2 主要特点漏斗形结晶器的创新点在于其打破了传统板坯连铸结晶器在任意横截面均相同的限制,其结晶器腔内凝固壳的形状及大小按非矩形截面逐步缩小的规律变化。
但是,钢液在这种结晶器内凝固时要产生变形,特别是拉坯过程中机械变形产生的应力可能导致固液界面裂纹的发生,并最终影响热轧带卷的质量。
因此,漏斗形结晶器的理想形状是尽量减小坯壳间两相区的弯曲变形率,使坯壳在变形过程中其固液界面的实际变形率小于产生裂纹的临界应变率。
基于上述要求,漏斗形结晶器必须保证厚度过渡区的弯曲弧度设计准确,且拉速尽可能稳定。
我国钢铁研究总院等单位对薄板坯连铸结晶器技术进行了深入研究,认为漏斗形结晶器技术从根本上解决了浸入式水口的使用寿命问题,使得高效连续生产薄规格铸坯变为现实。
同时由于漏斗形结晶器上口表面积大,为保护渣的熔化创造了条件。
应该指出的是,漏斗形结晶器的缺点是坯壳在结晶器内变形易产生裂纹,限制了像包晶钢这类难浇品种的薄板坯连铸。
必须结合钢液本身收缩的计算来设计结晶器的过渡段。
尽管该类型结晶器由弧线变直线的过渡段仅100 mm,在5m/min 的拉速下铸坯通过此段仅需几毫秒,但仍要给予高度重视,一般采用有限元法优化设计变形段。
为了减少或减缓漏斗形结晶器内的铸坯变形,可采取以下措施:1) 尽量减小漏斗的开口度。
2) 将铸坯由漏斗形过渡到矩形,变形段加长。
3) 优化结晶器内腔形状设计,使结晶器内金属变形分布更加均匀、平缓,降低变形速率,降低铸坯产生裂纹的可能性。
漏斗形结晶器在维护上与常规连铸结晶器的维护没有太大区别,主要应注意避免铜板表面的划伤和残钢粘结。
浇铸过程中应确保足够的润滑,预防水口破裂导致溅钢、溢钢以及漏钢事故。
1.1.3 技术进步考虑到漏斗形结晶器不适合浇铸较窄的中等宽度薄板坯,而平行板形结晶器的薄片状浸入式水口成本太高,且难以实现浇注薄规格铸坯,因此对漏斗形结晶器做了两个关键性的改进:1) 漏斗形结晶器的图形方案在弦长的中间区域为圆弧区,圆弧半径由上到下连续变大,圆弧区的两边为倾斜的三角形平面区,此圆形方案的特点是平行于X 轴的任意截面。
角度相等,且等于起始角,因而任意截面上的中间圆弧与两边直线不相切而相交。
2) 漏斗形的开口度是设计此种结晶器的一个重要参数。
结晶器的开口度较大,坯壳向下运动时斜率也大,导致拉坯阻力增加。
通过适当改变浸入式水口横截面的形状,把开口度由170 mm 减小到120~140 mm,浇铸效果较好。