设置回流焊温度曲线的方法
回流焊PCB温度曲线讲解

回流焊PCB温度曲线讲解1. 引言回流焊是电子元器件表面贴装的主要连接工艺之一。
在回流焊过程中,合适的温度曲线对于保证焊点质量以及避免元器件损坏至关重要。
本文将介绍回流焊的基本原理,并详细讲解回流焊PCB温度曲线的设计和特点。
2. 回流焊的基本原理回流焊是利用热风或蒸汽将焊料预热至熔点,通过表面张力作用使焊料润湿焊盘,然后快速冷却固化焊点的方法。
其基本原理如下:•加热:通过预热炉或沿焊点方向移动的加热头,将焊盘、元器件表面和焊料加热至熔点附近。
•润湿:在焊料熔化后,焊料会润湿焊盘和元器件表面,形成液态焊接材料。
•冷却:在焊料润湿后,迅速冷却焊点,使焊料固化,固定连接元器件和焊盘。
3. PCB温度曲线的设计为了确保回流焊质量和避免元器件受损,需要设计合适的PCB温度曲线。
PCB温度曲线由预热阶段、高温阶段和冷却阶段组成。
3.1 预热阶段在预热阶段,PCB温度逐渐升高,热量逐渐传导到焊盘和元器件表面。
此阶段的温度升高速度较慢,以免过快的温度变化引发热应力而损坏元器件。
3.2 高温阶段在高温阶段,PCB温度达到焊料的熔点。
此阶段的温度需要保持一定时间,以确保焊料充分熔化并使焊点质量达到要求。
在高温阶段,焊料的表面张力会促使其润湿焊盘和元器件表面。
3.3 冷却阶段在冷却阶段,PCB温度迅速下降。
冷却阶段的温度变化速度需要适当控制,以避免焊点在急剧温度变化中产生冷焊、裂纹等缺陷。
4. 回流焊PCB温度曲线的特点回流焊PCB温度曲线的设计需考虑以下几个因素:4.1 元器件耐热温度不同的元器件有不同的耐热温度。
在设计温度曲线时,需要确保元器件能够耐受高温环境,避免损坏。
4.2 焊料熔点根据焊料的熔点来确定高温阶段的温度和时间。
高温阶段的温度需要高于焊料熔点以保证焊料能够充分熔化。
4.3 焊接质量要求回流焊的质量要求取决于焊接应用的具体要求,如焊点的可靠性、电气性能等。
根据焊点的要求,调整高温阶段的温度和时间,以保证焊接质量。
回流焊八温区标准曲线

回流焊八温区标准曲线
回流焊八温区标准曲线
回流焊是一种用于电子元件焊接的工艺,其八温区标准曲线是回流焊温度设置的参考。
以下是回流焊八温区标准曲线的各个阶段:
1.预热阶段
在预热阶段,温度从室温逐渐上升到预热温度。
这个阶段的目的是使回流焊炉内的温度稳定,以确保焊接效果的一致性。
预热阶段通常持续几分钟,并且在这个阶段,元件逐渐加热到足够温度,以便进行下一步操作。
2.浸温阶段
在浸温阶段,温度继续上升到浸温温度。
这个阶段的目的是使元件的焊接部分达到熔点,以便进行焊接操作。
浸温阶段通常持续几秒钟,并且在这个阶段,元件焊接部分会融化并准备好进行焊接。
3.回流阶段
在回流阶段,温度继续上升到回流温度。
这个阶段的目的是使焊接部分的金属完全熔化并形成焊点。
回流阶段通常持续几秒钟,并且在这个阶段,元件被放置在回流焊炉中,以形成焊接点。
4.冷却阶段
在冷却阶段,温度逐渐降低到室温。
这个阶段的目的是使焊接部分的金属冷却并固定下来。
冷却阶段通常持续几分钟,并且在这个阶段,元件被取出并放置在冷却架上,以加速冷却过程。
以上是回流焊八温区标准曲线的四个阶段。
在设置回流焊温度时,应该根据具体的元件和焊接需求进行调整,以确保焊接效果的最佳化。
如何设定回流焊温度曲线

如何设定回流焊温度曲线如何设定回流焊温度曲线首先我们要了解回流焊的几个关键的地方及温度的分区情况及回流焊的种类.影响炉温的关键地方是:1:各温区的温度设定数值2:各加热马达的温差3:链条及网带的速度4:锡膏的成份5:PCB板的厚度及元件的大小和密度6:加热区的数量及回流焊的长度7:加热区的有效长度及泠却的特点等回流焊的分区情况:1:预热区(又名:升温区)2:恒温区(保温区/活性区)3:回流区4 :泠却区那么,如何正确的设定回流焊的温度曲线下面我们以有铅锡膏来做一个简单的分析(Sn/pb)一:预热区预热区通常指由室温升至150度左右的区域,在这个区域,SMA平稳升温,在预热区锡膏的部分溶剂能够及时的发挥。
元件特别是集成电路缓慢升温。
以适应以后的高温,但是由于SMA表面元件大小不一。
其温度有不均匀的现象。
在些温区升温的速度应控制在1-3度/S 如果升温太快的话,由于热应力的影响会导致陶瓷电容破裂/PCB变形/IC芯片损坏同时锡膏中的溶剂挥发太快,导致锡珠的产生,回流焊的预热区一般占加热信道长度的1/4—1/3 时间一般为60—120S二:恒温区所谓恒温意思就是要相对保持平衡。
在恒温区温度通常控制在150-170度的区域,此时锡膏处于融化前夕,锡膏中的挥发进一步被去除,活化剂开始激活,并有效的去除表面的氧化物,SMA表面温度受到热风对流的影响。
不同大小/不同元件的温度能够保持平衡。
板面的温差也接近最小数值,曲线状态接近水平,它也是评估回流焊工艺的一个窗口。
选择能够维持平坦活性温度曲线的炉子将提高SMA的焊接效果。
特别是防止立碑缺陷的产生。
通常恒温区的在炉子的加热信道占60—120/S的时间,若时间太长也会导致锡膏氧化问题。
导致锡珠增多,恒温渠温度过低时此时容易引起锡膏中溶剂得不到充分的挥发,当到回流区时锡膏中的溶剂受到高温容易引起激烈的挥发,其结果会导致飞珠的形成。
恒温区的梯度过大。
这意味着PCB的板面温度差过大,特别是靠近大元件四周的电阻/电容及电感两端受热不平衡,锡膏融化时有一个延迟故引起立碑缺陷。
八温区回流焊各温区的温度设置
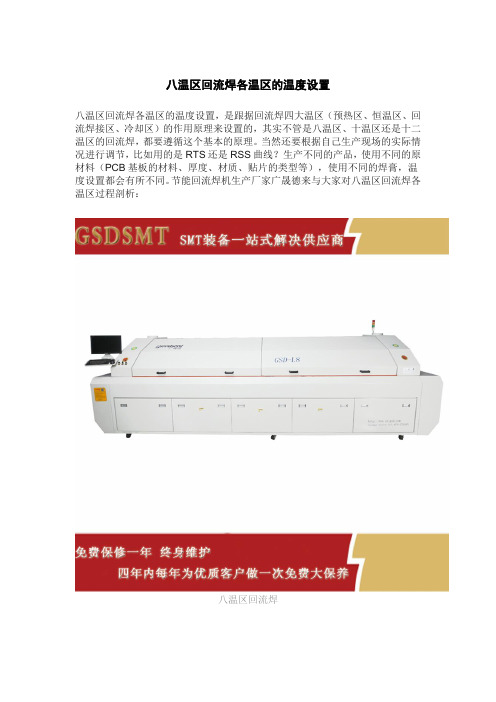
八温区回流焊各温区的温度设置八温区回流焊各温区的温度设置,是跟据回流焊四大温区(预热区、恒温区、回流焊接区、冷却区)的作用原理来设置的,其实不管是八温区、十温区还是十二温区的回流焊,都要遵循这个基本的原理。
当然还要根据自己生产现场的实际情况进行调节,比如用的是RTS还是RSS曲线?生产不同的产品,使用不同的原材料(PCB基板的材料、厚度、材质、贴片的类型等),使用不同的焊膏,温度设置都会有所不同。
节能回流焊机生产厂家广晟德来与大家对八温区回流焊各温区过程剖析:八温区回流焊预热区的作用是为了使锡膏先经过预热提高活性,避免在浸锡的时个因为急剧升温引起产品不良。
预热区的温度从室温~150℃,温度提升的速率应该控制在2℃/s 左右,预热区升温时间控制在60~150s。
恒温区的作用是让回流炉内部各元器件的温度逐渐保持稳定,让炉内的元器件在恒温区里有足够的时间来降低温差。
使不同大小的元件温度趋于一致,并让焊锡膏里面的助焊剂充分得到挥发。
恒温区的温度从150℃~200℃,要保持温度稳定缓慢的上升,升温速率小于1℃/s,升温时间控制在60~120s,尤其要注意的是:恒温区一定要缓慢的受热,不然极易导致产品焊接出现品质问题。
当PCB板进入回流焊接区时,炉膛内温度迅速上升使焊锡膏熔化,液态的焊锡对元器件形成焊点。
在回流焊接区温度设置得比较高,使炉膛内温度迅速上升至峰值温度,峰值温度一般是由焊锡膏的熔点温度、PCB基板和元器件的耐热温度决定的。
回流焊接区的温度从217℃~Tmax~217℃,整个区间保持在60~90s。
如果有BGA的话,峰值温度应该设置在240至260度以内并保持40秒左右。
另外在回流区需要注意的是,回流焊接时间不要太长,以免对炉膛造成损伤,或者造成PCB板被烤焦或元件功能不良等问题。
冷却区的作用是让温度下降使焊点凝固,冷却速率的快慢会影响焊点的强度。
如果冷却的速率过慢,会导致在焊接点处产生共晶金属化合物和大的晶粒,造成焊接点强度过低。
67 回流焊温度曲线设定
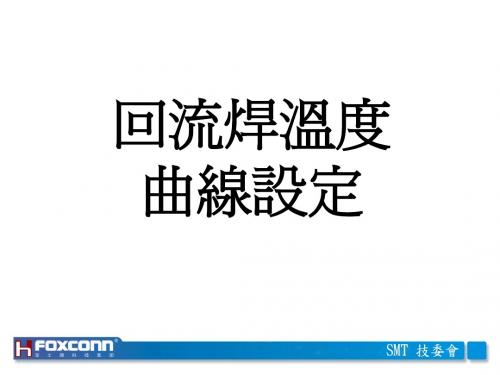
(2)熱電偶浮起的情況下,熱電偶沒有接觸到測定點測定值 是固定材料的自身的溫度,產生誤差。熱電偶的打結部從固 定材料中露出,直接感受爐內溫度會影響溫度Profile,不能 達到正確的曲線。另外,如下圖所示打結部分頭部露出在外 面或者熱電偶線接觸同樣影響測量結果。
IC等作為測定對象時,固結果。
但是,現在精密元件,在腳和銅箔之間固定很困難,只 要是接近底部測定的話就可以。
3.影響爐溫曲線的因素 测試时,必须使用已完全装配过的板。首先对印制板元 器件进行热特性分析,由于印制板受热性能不同,元器件体 积大小及材料差异等原因,各点实际受热升温不相同,找出 最热点,最冷点,分别设置热电偶便可测量出最高温度与最 低温度。 尽可能多设置热电偶测试点,以求全面反映印制板各部 分真实受热状态。例如印制板中心与边缘受热程度不一样, 大体积元件与小型元件热容量不同及热敏感元件都必须设置 测试点。
線經不同測定數據的平均值也可能不同,所以用不同線 經的測定的數據不可以用于比較。
C:锡膏参数表 锡膏特性参数表也是必要的,其包含的信息对温度曲线 是至关重要的,如:所希望的温度曲线持续时间、锡膏活性 温度、合金熔点和所希望的回流最高温度。 D:热电偶附着于PCB的方法 较好的方法是使用高温焊锡如银/锡合金,焊点尽量最小。 少量的热化合物(也叫热导膏或热油脂)斑点覆盖住热电 偶,再用高温胶带(如Kapton)粘住。
熱電偶固定材料的選擇方法 固定材料是接著劑和高溫焊錫,理由是使用其中任何一 種,也不會改變測量精度。固定材料不同測定數據的平均值 也會不同,所以不要將固定材料不同的測量數據混在一起。 耐熱膠紙,容易使熱電偶浮起,引起很大的測量誤差, 所以不要使用。
E:用高温胶,如氰基丙烯酸盐粘合剂,通常是将热电偶尖 附着在PCB焊盘和相应的元件引脚或金属端之间。 (图一、将热电偶尖附着在PCB焊盘和相应的元件引脚或金 属端之间)
回流焊温度与温度曲线设置规范

回流焊温度与温度曲线设置规范
1目的
1.1指导技术人员正确设置温度
2 范围
2.1本司SMT技术人员适用
2.2本司回流焊适用
3 内容
3.1设定原则:根据锡膏、胶水供应商所提供有关锡膏、胶水的温度曲线图与性
能数据等资料作为参考,以实际生产产品不同适当设定各温区温度;
3.2设定温度依据测试温度为准,若不合格需做相应修改后再测试,直到合格为
止;
3.3无特殊要求下,本司回流焊温度曲线应符合如下条件:
3.3.1 无铅锡膏(一般以Sn96 /Ag3.5/Cu0.5、Sn96.5/ Ag3/ Cu0.5、、Sn96.5/
Ag3.5为准);
150℃-190℃之时间段为: 60ses-120ses
高于220℃之时间段为: 30 ses-90 ses;
峰值温度为:235℃~255℃
3.32胶水:130℃~155℃之间保持时间为:120 ses-180 ses
3.4我公司回流焊显示器实际温度与设置温度相差5℃以上(不含5℃)时为异常,
此时不可使用回流焊.
4 温度测试
4.1 每个班次需对运行中的回流炉进行一次温度测量确认,如有转线之机型重新设置温度曲线后需要再次测量温度达到合格。
12温区回流焊标准炉温曲线
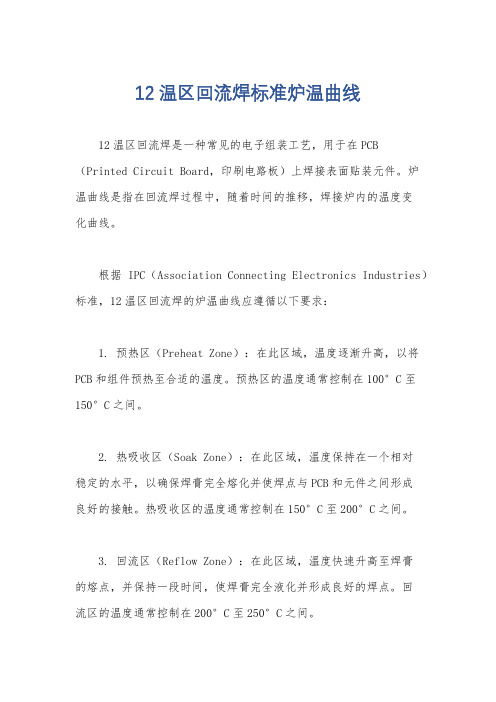
12温区回流焊标准炉温曲线12温区回流焊是一种常见的电子组装工艺,用于在PCB(Printed Circuit Board,印刷电路板)上焊接表面贴装元件。
炉温曲线是指在回流焊过程中,随着时间的推移,焊接炉内的温度变化曲线。
根据IPC(Association Connecting Electronics Industries)标准,12温区回流焊的炉温曲线应遵循以下要求:1. 预热区(Preheat Zone):在此区域,温度逐渐升高,以将PCB和组件预热至合适的温度。
预热区的温度通常控制在100°C至150°C之间。
2. 热吸收区(Soak Zone):在此区域,温度保持在一个相对稳定的水平,以确保焊膏完全熔化并使焊点与PCB和元件之间形成良好的接触。
热吸收区的温度通常控制在150°C至200°C之间。
3. 回流区(Reflow Zone):在此区域,温度快速升高至焊膏的熔点,并保持一段时间,使焊膏完全液化并形成良好的焊点。
回流区的温度通常控制在200°C至250°C之间。
4. 冷却区(Cooling Zone):在此区域,温度逐渐降低,以使焊点迅速冷却并固化。
冷却区的温度通常控制在室温附近。
炉温曲线的具体形状和温度范围可能因不同的焊接要求、焊膏类型和组件类型而有所变化。
因此,在实际应用中,根据具体的焊接工艺要求和组件特性,可以进行适当的调整和优化。
总之,12温区回流焊的炉温曲线是一个关键参数,它对焊接质量和元件的可靠性有着重要影响。
合理设计和控制炉温曲线可以确保焊接过程的稳定性和一致性,从而提高产品的质量和可靠性。
十温区回流焊温度参数设定

十温区回流焊温度参数设定摘要:I.引言- 介绍十温区回流焊II.温度参数设定的重要性- 影响焊接质量- 影响设备使用寿命III.参数设定步骤- 确定预热温度- 确定回流焊温度曲线- 调整焊接时间和冷却时间IV.参数设定实例- 以某型号十温区回流焊为例- 设定温度参数V.参数调整与优化- 根据实际焊接效果进行调整- 考虑不同材料和产品的要求VI.总结- 强调温度参数设定的重要性- 提出优化建议正文:I.引言十温区回流焊是一种高精度的焊接技术,通过设置不同的温度区域,实现对焊接过程的精确控制。
这种技术的应用范围广泛,从电子制造到汽车制造等行业均有涉及。
然而,要想充分发挥十温区回流焊的优势,必须对温度参数进行科学合理的设定。
II.温度参数设定的重要性温度参数设定对焊接质量有着直接的影响。
设定的温度过高或过低,都可能导致焊接不良,如虚焊、冷焊、桥接等。
这些问题不仅影响产品的性能,还可能对设备造成损害,缩短设备使用寿命。
III.参数设定步骤设定温度参数是一个复杂的过程,需要根据焊接材料、产品结构等因素综合考虑。
一般来说,参数设定步骤如下:1.确定预热温度:预热是为了使焊接材料达到一定的热度,以减少焊接过程中的热应力。
预热温度的确定需要考虑材料的性质、产品的结构等因素。
2.确定回流焊温度曲线:回流焊温度曲线是焊接过程中的关键参数,决定了焊接的质量和速度。
设定温度曲线时,需要根据焊接材料的热膨胀系数、熔点等因素,以及焊接设备的特点,选择合适的温度阶段和过渡方式。
3.调整焊接时间和冷却时间:焊接时间和冷却时间是影响焊接效果的重要参数。
焊接时间过长可能导致焊接材料过度熔化,影响焊接质量;冷却时间过短则可能导致焊接材料未完全固化,影响产品性能。
因此,需要根据实际焊接效果和焊接材料的特点,合理调整焊接时间和冷却时间。
IV.参数设定实例以某型号十温区回流焊为例,设定温度参数的过程如下:1.确定预热温度:根据产品材料(如铜、锡等)的性质,以及焊接设备的特点,确定预热温度为150℃。
- 1、下载文档前请自行甄别文档内容的完整性,平台不提供额外的编辑、内容补充、找答案等附加服务。
- 2、"仅部分预览"的文档,不可在线预览部分如存在完整性等问题,可反馈申请退款(可完整预览的文档不适用该条件!)。
- 3、如文档侵犯您的权益,请联系客服反馈,我们会尽快为您处理(人工客服工作时间:9:00-18:30)。
一、回流温度曲线在生产中地位:回流焊接是在SMT工业组装基板上形成焊接点的主要方法,在SMT工艺中回流焊接是核心工艺。
因为表面组装PCB的设计,焊膏的印刷和元器件的贴装等产生的缺陷,最终都将集中表现在焊接中,而表面组装生产中所有工艺控制的目的都是为了获得良好的焊接质量,如果没有合理可行的回流焊接工艺,前面任何工艺控制都将失去意义。
而回流焊接工艺的表现形式主要为回流温度曲线,它是指PCB的表面组装器件上测试点处温度随时间变化的曲线。
因而回流温度曲线是决定焊接缺陷的重要因素。
因回流曲线不适当而影响的缺陷形式主要有:部品爆裂/破裂、翘件、锡粒、桥接、虚焊以及生半田、PCB脱层起泡等。
因此适当设计回流温度曲线可得到高的良品率及高的可靠度,对回流温度曲线的合理控制,在生产制程中有着举足轻重的作用。
二、回流温度曲线的一般技术要求及主要形式:1.回流温度曲线各环节的一般技术要求:一般而言,回流温度曲线可分为三个阶段:预热阶段、回流阶段、冷却阶段。
①预热阶段:预热是指为了使锡水活性化为目的和为了避免浸锡时进行急剧高温加热引起部品不具合为目的所进行的加热行为。
•预热温度:依使用锡膏的种类及厂商推荐的条件设定。
一般设定在80~160℃范围内使其慢慢升温(最佳曲线);而对于传统曲线恒温区在140~160℃间,注意温度高则氧化速度会加快很多(在高温区会线性增大,在150℃左右的预热温度下,氧化速度是常温下的数倍,铜板温度与氧化速度的关系见附图)预热温度太低则助焊剂活性化不充分。
•预热时间视PCB板上热容量最大的部品、PCB面积、PCB厚度以及所用锡膏性能而定。
一般在80~160℃预热段内时间为60~120sec,由此有效除去焊膏中易挥发的溶剂,减少对元件的热冲击,同时使助焊剂充分活化,并且使温度差变得较小。
•预热段温度上升率:就加热阶段而言,温度范围在室温与溶点温度之间慢的上升率可望减少大部分的缺陷。
对最佳曲线而言推荐以0.5~1℃/sec的慢上升率,对传统曲线而言要求在3~4℃/sec以下进行升温较好。
②回流阶段:•回流曲线的峰值温度通常是由焊锡的熔点温度、组装基板和元件的耐热温度决定的。
一般最小峰值温度大约在焊锡熔点以上30℃左右(对于目前Sn63 - pb 焊锡,183℃熔融点,则最低峰值温度约210℃左右)。
峰值温度过低就易产生冷接点及润湿不够,熔融不足而致生半田,一般最高温度约235℃,过高则环氧树脂基板和塑胶部分焦化和脱层易发生,再者超额的共界金属化合物将形成,并导致脆的焊接点(焊接强度影响)。
•超过焊锡溶点以上的时间:由于共界金属化合物形成率、焊锡内盐基金属的分解率等因素,其产生及滤出不仅与温度成正比,且与超过焊锡溶点温度以上的时间成正比,为减少共界金属化合物的产生及滤出则超过熔点温度以上的时间必须减少,一般设定在45~90秒之间,此时间限制需要使用一个快速温升率,从熔点温度快速上升到峰值温度,同时考虑元件承受热应力因素,上升率须介于2.5~3.5℃/see之间,且最大改变率不可超过4℃/sec。
③冷却阶段:高于焊锡熔点温度以上的慢冷却率将导致过量共界金属化合物产生,以及在焊接点处易发生大的晶粒结构,使焊接点强度变低,此现象一般发生在熔点温度和低于熔点温度一点的温度范围内。
快速冷却将导致元件和基板间太高的温度梯度,产生热膨胀的不匹配,导致焊接点与焊盘的分裂及基板的变形,一般情况下可容许的最大冷却率是由元件对热冲击的容忍度决定的。
综合以上因素,冷却区降温速率一般在4℃/S 左右,冷却至75℃即可。
2.目前应用较广泛的两种回流温度曲线模式:①升温—保温方式(传统温度曲线)•解说:由起始快速温度上升至140~170℃范围内某一预热温度并保持,TPHH—TPHL要根据回流炉能力而定(±10℃程度),然后温度持平40~120S左右当作预热区,然后再快速升温至回流区,再迅速冷却进入冷却区(温度变化速率要求在4℃/sec以下)。
•特点:因为一般都取较低的预热温度,因而对部品高温影响小(给部品应力小)故可延长其加热时间,以便达到助焊剂的活性化。
同时因为从预热区到回流区,其温度上升较为激剧,易使焊接流变性恶化而致移位,且助焊剂活性化温度也低。
②逐步升温方式(最佳温度曲线):•解说:以慢的上升率(0.5~1℃/sec)加热直到大约175℃,然后在20~30S内梯度上升到180℃左右,再以2.5~3.5℃/sec快速上升到220℃左右,最后以不超过4℃/sec快速冷却下降。
其管理要点是保持一定的预热温度上升率,预热的终点接近锡的熔点温度。
•特点:部品不受激剧的温度变化,助焊剂的活性化温度可以设定较高,但助焊剂的活性化时间短,同时预热温度高而使部品受高温影响。
③比较以上两种回流温度曲线模式,主要的不同是后者无高原结构(即恒温加热区)的温度曲线部分。
④由于基板结构及其元件吸热性的差异,以及设备可控制加热率的限制,在穿过回流炉的基板不同点温度仍然会存在差异,借由一个减少温度梯度的高原形式的平衡区,在热点温度到焊锡溶点温度以下时,保持此温度一段时间,则冷点温度将有力赶上它,在每个元件达到相同温度之后,另一个快温升程序将使元件上升到峰值温度,这样可有效避免局部生半田或局部高温焦化的现象。
⑤另一方面,前者高原结构的获得,则在室温至恒温预热段以及恒温段至焊锡熔融段必然会出现一个快速升温的过程,而此快速升温过程对因溅落而引起的焊锡球,在焊锡融点前部品两侧润湿不平衡而引起翘件等不良又有密切关系,很多品质问题都希望在室温到焊锡溶点之间采用线性上升加热温度曲线来预防消除。
3.常见回流浸锡不良与温度曲线关系(仅是基于回流工艺的考虑)①锡桥接(短路)不良是焊锡热融落造成的结果,只发生在熔点以下的焊膏阶段。
由于分子热运动效应,固定成份和化学结构的材料的粘度随温度上升而下降,在较高温下粘度的下降将产生较大的热融落;另一方面,温度的上升常使助焊剂脱出较多的溶剂并导致固态含量的增加而致使粘度上升。
因为前者仅与温度有关,后者即溶剂的总减少量是时间和温度的函数,在任一已知的温度下,低温升率的锡膏粘度比高温升率回流曲线下的锡膏粘度要高,因此我们在预热阶段的温升率一般要求较低,从而减少短路不良的发生。
②锡粒的产生:在预热阶段,伴随除去焊膏中易挥发溶剂的过程,焊膏内部会发生气化现象,这时如果焊膏中金属粉末之间的粘结力小于气化产生的力,就会有少量焊膏从焊盘上流离开,有的则躲到Chip元件下面,回流时这部分焊膏也会熔化,而后从片状阻容元件下挤出,形成焊锡珠。
由其形成过程可见,预热温度越高,预热速度越快,就会加大气化现象中飞溅,就越易形成锡珠。
同时温度越高,焊锡的氧化会加速、焊锡粉表面的氧化膜会阻止焊锡粉之间很好地熔融为一体,会产生焊锡球。
但这一现象采用适当的预热温度与预热速度可有效控制。
③毛细管现象:是指溶融焊锡润湿到元件引脚且远离接点区,造成假焊,其原因是在焊锡熔融阶段引脚的温度高于PCB焊盘温度。
改善办法:使用较多的底面加热(上、下加热方式回流炉)或非常慢的温升率(在预热至焊锡溶点温度附近),使焊锡润湿发生前引脚与焊盘温度达到平衡。
三、回流温度曲线的测试:回流温度曲线的测试,一般采用能随PCB板一同进入炉膛内的温度采集器(即温度记忆装置)进行测试,测量采用K型热电偶(依测量温度范围及精度而采用不同材质制成各种类型热电偶),偶丝直径0.1~0.3mm为宜,测试后将记忆装置数据输入PC 专用测试软件,进行曲线数据分析处理,打印出PCB组件温度曲线。
1. 热电偶的安装 a. 感应温度用的热电偶,在使用和安装过程中,应确保除测试点外,无短接现象发生,否则无法保证试精度,测试点尽可能小. b. 热电偶在与记忆装置或其它测试设备相连接时,其极性应与设备要求一致,热电偶将温度转变为电动势,所以连接时有方向要求.(目前我们使用的热电偶插头有正负极区分)2. 测试点的选取一般至少三点,能代表PCB组件上温度变化的测试点(能反映PCB组件上高、中低温部位的温度变化);一般情况下,最高温度部位在PCB与传送方向相垂直的无元件边缘中心处,最低温度在PCB 靠近中心部位的大型元件之半田端子处(PLCC.QFP等),另外对耐热性差部品表面要有测试点,以及客户的特定要求.3. 测试点安装:热电偶与测试位置要可靠连接,否则会产生热阻,另外与热电偶接触的材料以及固定热电偶的材料应是最小的,因其绝热或吸热作用将直接影响热电偶测量值的真实性。
常用的四种热电偶连接方式:A 高温焊料:熔点高于290℃,导热性好,热电偶与PCB表面之间热阻小,机械强度高,连接可靠测量误差小,可连续测试. 焊接技术难度大,改变测试点不方便,容易因过热而损坏PCB焊盘或元器件,不能将热电偶与不浸锡表面连接. 适用于固定点连续测试。
B 胶粘剂:可将热电偶与不浸锡表面连接,能经受几个周期的再流焊温度. 粘接后固化,操作不便,残留胶清除困难. 适用于固定点连续测试。
C 高温胶带:可将热电偶与不浸锡表面连接,改变测试点简单方便. 随着温度升高,胶带粘着力下降,热电偶偏离测试点,引起测试误差,不能将热电偶固定在狭小位置. 适用于多点测试。
D 机械连接:连接结实可靠,经得住反复测试,可对狭小位置进行测试机械部件增加了热电偶附近热容量,测试成本高. 适用于高密度多点连续测试。
目前我们采用的多是高温焊料方式,用高温焊料贴片胶或高温胶带纸将记忆装置的热电偶测试头分别固定到PCB的测试点部位,再用高温度胶带/胶水把热电偶丝固定,以免因其移动影响测量数据,焊接固定时,焊接量尽量小和均匀,固定用胶水也尽量是很薄一层.4. 测试板的要求 a. 原则上要采用本机种的完整的回流后产品来制作,以保证真实地反映该产品在回流炉内的温度变化情况 b. 采用其他代替测试板要符合以下要求:基板材质相同,基板外形尺寸要相同,基板厚度相同,贴片部品数大致相当以及吸热或耐热性近部品.5. 其他注意事项 a. 将测试板与记忆装置一起放入炉膛时,注意记忆装置距测试PCB板距离在100mm以上,以免热量干扰. b. 相关实验数据表明:回流炉在开机30mim后才能达到炉体热平衡,因此要求在开启炉子至少运行30mim后才可进行温度曲线的测试及生产. c. 温度曲线图打印出来后依预热的温度时间,回流峰值温度,回流时间以及升降温速率等综合考虑调整设备至满足温度曲线要求,因测试点热容量的不同以及表征回流炉性能的温度不均匀性因素,三个测试点温度曲线将会存在一定差异. d. 温度曲线的记录:除打印出的温度曲线外,要表明各参数要求的范围及实际值;设备的设定值;测试点位置分布及测试板投入方向以及测定时间及结果判定等..。