Chapter16 by 冯仁青 Compressed by NHivNOiii
vasp侯柱峰

. . . . . . . . . . . . . . . . . . . . . . . . . . . . . 25
. . . . . . . . . . . . . . . . . . . . . . . . . . . . . . . . . . . . . . . . . . 26
. . . . . . . . . . . . . . . . . . . . . . . . . . . . . . . . . . . . . 26
POTCAR
POSCAR
KPOINTS
k
k
5
§3.1 INCAR vasp
•
SYSTEM
•
ISTART, ICHARG, INIWAV
•
–
ENCUT, ENAUG
–
ALGO, IALGO, LDIAG
–
IMIX, AMIX, AMIN, BMIX, AMIX MAG, BMIX MAG, WC,
INIMIX, MIXPRE, MAXMIX
slab
. . . . . . . . . . . . . . . . . . . . . . . . . . . . . . . . . 31
. . . . . . . . . . . . . . . . . . . . . . . . . . . . . . 32
. . . . . . . . . . . . . . . . . . . . . . . . . . . . . . 33
Linux
makefile linux ”
PGI fortan
pgf90 ATLAS
VASP4.6
/home/xxxx/VASP SRC
Birtel-paper(损伤因子定义)

Abstract: A spatial finite element model of reinforced concrete (RC) beams with rectangular cross sections, typical side aligned stirrups and distributed or edge concentrated longitudinal reinforcement is presented. It is parameterised in its properties of geometry, material, discretisation and loads in biaxial directions. The concrete volume is discretisised into 8 or 20node solid elements. Truss elements discretely model each single reinforcement bar. They are coupled to the concrete elements using the ″embedded modelling″ technique. The ″concrete damage plasticity″ model of ABAQUS is used to describe the nonlinear material behaviour of concrete. Suitable material functions and material parameters are derived and verified to experimental data of (cyclic) uniaxial, biaxial or triaxial stress tests. Energy criteria and internal length parameters ensure almost mesh independent results of the simulations. An elasto-plastic material model with a gradually rising plastic branch is adopted for the reinforcing steel. The parametric model is verified to experimental data of uniaxial shear tests taken from the literature. Afterwards, it is used to establish a data base of biaxial shear resistances to check developed biaxial shear design formulas that base on simple strut and tie models. More than 100 simulations guarantee an extended and reliable verification that experiments – almost none of them are available in the literature – are not able to give. Moreover, the arrangement of the stirrups is optimised in dependence upon the distribution of the longitudinal reinforcement to minimise reinforcement amounts and increase bearing capacities.
冯至 十四行诗

十四行集(二十七首)一我们准备着我们准备着深深地领受那些意想不到的奇迹,在漫长的岁月里忽然有彗星的出现,狂风乍起。
我们的生命在这一瞬间,仿佛在第一次的拥抱里过去的悲欢忽然在眼前凝结成屹然不动的形体。
我们赞颂那些小昆虫,它们经过了一次交媾或是抵御了一次危险,便结束它们美妙的一生。
我们整个的生命在承受狂风乍起,彗星的出现。
二什么能从我们身上脱落什么能从我们身上脱落,我们都让它化作尘埃:我们安排我们在这时代象秋日的树木,一棵棵把树叶和些过迟的花朵都交给秋风,好舒开树身伸入严冬;我们安排我们在自然里,象蜕化的蝉蛾把残壳都丢在泥里土里;我们把我们安排给那个未来的死亡,象一段歌曲,歌声从音乐的身上脱落,归终剩下了音乐的身躯化作一脉的青山默默。
三有加利树你秋风里萧萧的玉树——是一片音乐在我耳旁筑起一座严肃的殿堂,让我小心翼翼地走入又是插入晴空的高塔在我的面前高高耸起,有如一个圣者的身体,升华了全城市的喧哗。
你无时不脱你的躯壳,凋零里只看着你成长;在阡陌纵横的田野上我把你看成我的引导:祝你永生,我愿一步步化身为你根下的泥土。
四鼠曲草我常常想到人的一生,便不由得要向你祈祷。
你一丛白茸茸的小草不曾辜负了一个名称但你躲避着一切名称,过一个渺小的生活,不辜负高贵和洁白,默默地成就你的死生。
一切的形容、一切喧嚣到你身边,有的就凋落,有的化成了你的静默:这是你伟大的骄傲却在你的否定里完成。
我向你祈祷,为了人生。
五威尼斯我永远不会忘记西方的那座水城,它是个人世的象征,千百个寂寞的集体。
一个寂寞是一座岛,一座座都结成朋友。
当你向我拉一拉手,便象一座水上的桥;当你向我笑一笑,便象是对面岛上忽然开了一扇楼窗。
只担心夜深静悄,楼上的窗儿关闭,桥上也断了人迹。
六原野的哭声我时常看见在原野里一个村童,或一个农妇向着无语的晴空啼哭,是为了一个惩罚,可是为了一个玩具的毁弃?是为了丈夫的死亡,可是为了儿子的病创?啼哭的那样没有停息,象整个的生命都嵌在一个框子里,在框子外没有人生,也没有世界。
冯源:黑刍键上的海外之旅
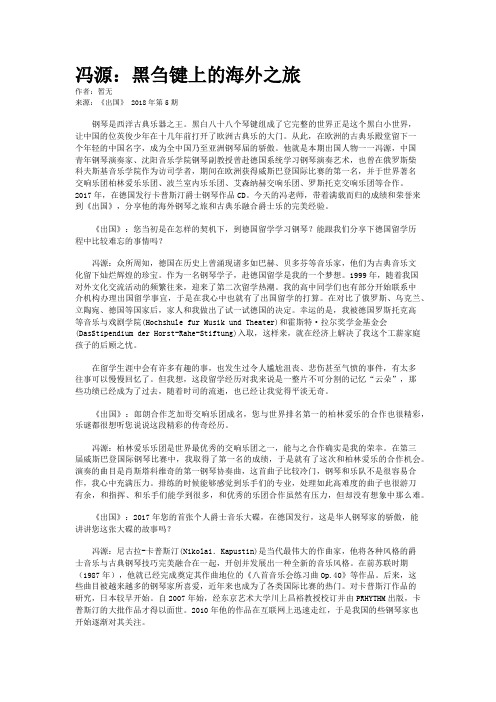
冯源:黑刍键上的海外之旅作者:暂无来源:《出国》 2018年第5期钢琴是西洋古典乐器之王。
黑白八十八个琴键组成了它完整的世界正是这个黑白小世界,让中国的位英俊少年在十几年前打开了欧洲古典乐的大门。
从此,在欧洲的古典乐殿堂留下一个年轻的中国名字,成为全中国乃至亚洲钢琴届的骄傲。
他就是本期出国人物一一冯源,中国青年钢琴演奏家、沈阳音乐学院钢琴副教授曾赴德国系统学习钢琴演奏艺术,也曾在俄罗斯柴科夫斯基音乐学院作为访司学者,期间在欧洲获得威斯巴登国际比赛的第一名,并于世界著名交响乐团柏林爱乐乐团、波兰室内乐乐团、艾森纳赫交响乐团、罗斯托克交响乐团等合作。
2017年,在德国发行卡普斯汀爵士钢琴作品CD。
今天的冯老师,带着满载而归的成绩和荣誉来到《出国》,分享他的海外钢琴之旅和古典乐融合爵士乐的完美经验。
《出国》:您当初是在怎样的契机下,到德国留学学习钢琴?能跟我们分享下德国留学历程中比较难忘的事情吗?冯源:众所周知,德国在历史上曾涌现诸多如巴赫、贝多芬等音乐家,他们为古典音乐文化留下灿烂辉煌的珍宝。
作为一名钢琴学子,赴德国留学是我的一个梦想。
1999年,随着我国对外文化交流活动的频繁往来,迎来了第二次留学热潮。
我的高中同学们也有部分开始联系中介机构办理出国留学事宜,于是在我心中也就有了出国留学的打算。
在对比了俄罗斯、乌克兰、立陶宛、德国等国家后,家人和我做出了试一试德国的决定。
幸运的是,我被德国罗斯托克高等音乐与戏剧学院(Hochshule fur Musik und Theater)和霍斯特·拉尔奖学金基金会(DasStipendium der Horst-Rahe-Stiftung)入取,这样来,就在经济上解决了我这个工薪家庭孩子的后顾之忧。
在留学生涯中会有许多有趣的事,也发生过令人尴尬沮丧、悲伤甚至气愤的事件,有太多往事可以慢慢回忆了。
但我想,这段留学经历对我来说是一整片不可分割的记忆“云朵”,那些功绩已经成为了过去,随着时司的流逝,也已经让我觉得平淡无奇。
Masoneilan Control Valve Sizing Handbook

Masoneilan
DRESSER
VALVE
DIVISION
2
Foreword
This handbook on control valve sizing is based on the use of nomenclature and sizing equations from ISA Standard S75.01 and IEC Standard 534-2. Additional explanations and supportive information are provided beyond the content of the standards. The sizing equations are based on equations for predicting the flow of compressible and incompressible fluids through control valves. The equations are not intended for use when dense slurries, dry solids or non-Newtonian liquids are encountered. Original equations and methods developed by Masoneilan are included for two-phase flow, multistage flow, and supercritical fluids. Values of numerical factors are included for commonly encountered systems of units. These are United States customary units and metric units for both kilopascal and bar usage. The principal use of the equations is to aid in the selection of an appropriate valve size for a specific application. In this procedure, the numbers in the equations consist of values for the fluid and flow conditions and known values for the selected valve at rated opening. With these factors in the equation, the unknown (or product of the unknowns, e.g., Fp Cv) can be computed. Although these computed numbers are often suitable for selecting a valve from a series of discrete sizes, they do not represent a true operating condition. Some of the factors are for the valve at rated travel, while others relating to the operating conditions are for the partially open valve. Once a valve size has been selected, the remaining unknowns, such as Fp, can be computed and a judgement can be made as to whether the valve size is adequate. It is not usually necessary to carry the calculations further to predict the exact opening. To do this, all the pertinent sizing factors must be known at fractional valve openings. A computer sizing program having this information in a database can perform this Cv
17.机动战士高达 闪光的哈萨维 第十六章 逃脱

机动战士高达闪光的哈萨维第十六章逃脱 - [闪光的哈萨维]哈萨维乘着凯奈斯上校为他安排好的豪华轿车去了达沃的购物中心。
变成一个人之后,渐渐地,哈萨维觉得,琪琪或许隐瞒了她所感觉到的东西,并没有把这些告诉凯奈斯。
“……虽然看起来很可能会说,但却并没有那样做……为什么……”看上去对于初次见面只要是男性对谁都献媚的她,其实完全不是这样。
在看到了这样的事实后的思考中,哈萨维心中有了回到凯奈斯的基地的冲动。
然而,他已经被如果能做到就必须自己回收高达的义务感所驱使。
“不得出对琪琪的结论也没事……现在,在这段时间里,她说不定正和凯奈斯说我是马夫蒂的一员。
”他像是抛开了自己心底的那一丝期待,这么想着。
要逃出虎口,哈萨维已经没有时间了。
他必须尽快。
“在哪里下车?”驾驶席上的下士官问道。
“啊,在那旁边方便停车的地方就行了。
”哈萨维并不相信照着这些话去做的司机,因为在助手席上还有一个下士官。
他内心焦虑着,心想绝对不能做出让人怀疑的举动。
在观光导游所附近,一定会有硬币锁柜。
哈萨维进了银行,接着换了点现金,把手提箱寄在了锁柜里,走进信息中心确认了去往梅纳德的船的时间。
“……要坐傍晚的船吗……”哈萨维在窗口的女性面前有意地自言自语着,走向了出达沃港的方向。
在信息等窗口有人,这是为了监视人流,检查非法居住者。
毫无疑问,想要留在地球上的人们利用着官僚组织,也有的是为了安排出多余的职业,但前者更多一些。
哈萨维一边在不同的大街上买着看起来老教授会比较喜欢的东西,一边注意着是否被跟踪,等待着和同伴接触。
“……认为多多少少给一般人造成伤害,人类居住在地球,这是罪恶。
这样一个时代,我们希望你们从心里去理解它。
”那是电波干扰所正播放的马夫蒂演说的声音。
这并不是哈萨维的声音,在这定型化的演说录音声中,哈萨维站了起来。
“少开玩笑了!你们正打算随兴轰炸!”“今天的空袭如此残酷,这不是马夫蒂啊。
你们知道吗?金伯利的MS才是过分的,你们各位知道吧?”对于人们交错而起高声说出的话,哈萨维耳朵发疼。
《肖申克的救赎》中英双语剧本

肖申克的救赎(剧本)1 INT -- CABIN -- NIGHT (1946) 内景--小屋--夜晚A dark, empty room. 一所黑黑的、空洞的房子The door bursts open. A MAN and WOMAN enter, drunk and giggling, horny as hell. No sooner is the door shut than they're all over each other, ripping at clothes, pawing at flesh, mouths locked together.门突然被撞开,一个男人和一个女人醉意地走了进来,吃吃地笑着,很是暧昧。
不等门关上,他们就缠在了一块,互相撕扯着衣服,搓摸着对方的身体,两张嘴紧紧地贴在了一起。
He gropes for a lamp, tries to turn it on, knocks it over instead. Hell with it. He's got more urgent things to do, like getting her blouse open and his hands on her breasts. She arches, moaning, fumbling with his fly. He slams her against the wall, ripping her skirt. We hear fabric tear.男人摸索着想打开台灯,却弄翻了它。
顾不上管台灯,他有更急的事要做,他掀起她的上衣,用手按住她的乳房。
她仰着身子,呻吟着,慌乱地解着他的钮扣。
他猛地将她顶在墙上,撕扯她的裙子。
可以听到织物被撕破的声音。
He enters her right then and there, roughly, up against the wall. She cries out, hitting her head against the wall but not caring, grinding against him, clawing his back, shivering with the sensations running through her. He carries her across the room with her legs wrapped around him. They fall onto the bed.他粗鲁的进入了她,顶着墙壁。
Particle erosion on CNF coated CF composites

Particle erosion on carbon nanofiber paper coated carbon fiber/epoxycompositesNa Zhang a ,b ,1,Fan Yang a ,1,2,Changyu Shen b ,Jose Castro c ,L.James Lee a ,⇑aDepartment of Chemical and Biomolecular Engineering,The Ohio State University,OH 43210,USA bDepartment of Materials Science and Engineering,Zhengzhou University,Zhengzhou 450052,China cDepartment of Integrative Systems Engineering,The Ohio State University,OH 43210,USAa r t i c l e i n f o Article history:Received 2October 2012Accepted 1May 2013Available online 15May 2013Keywords:A.Carbon fiberB.WearC.Finite element analysis (FEA)D.Electron microscopya b s t r a c tCarbon fiber (CF)woven fabric (52%by weight)reinforced epoxy composite and carbon nanofiber (CNF,12%by weight)paper coated on the surface of the CF/epoxy composite were fabricated by resin transfer molding (RTM).The surface erosion characteristics of molded CF composites were investigated by sand erosion test using silica particles with a size around 150l m as the erodent.The eroded surfaces were examined by scanning electron microscopy (SEM)and weight loss.The CNF paper was able to provide a much stronger erosion resistance compared to the CF reinforced epoxy composites,which is attributed to the high strength of CNFs and their nanoscale structure.Finite element (FE)computer simulations were used to qualitative interpret the underlying mechanisms.Ó2013Elsevier Ltd.All rights reserved.1.IntroductionPolymer composite materials often exhibit poor erosion resis-tance [1–6].Improving erosion resistance of light weight compos-ite materials is crucial for many industrial applications such as wind turbine blades [7–9].Tilly [3–5,10]presented a thorough analysis of various parameters affecting erosion,including particle properties,impact parameters,particle concentration,type of rein-forcement and temperature.For erosive wear resistance,materials can be classified into ductile and brittle categories according to their behavior with respect to the impinging angle and erosion process [12].In brittle erosion,the weight loss increases linearly with time,while in a ductile type the particles may be embedded in the target surface causing a weight gain initially,followed with a linear weight loss as a function of time by further impingement.The maximum weight loss was found at about 90°and 30°impact angles for brittle and ductile erosions,respectively [10–12].Both glass fiber and carbon fiber reinforced epoxy composites show brittle characteristics [12–15].In this study,we present a new approach for improving the erosive resistance of composites using a thin protective layer of paper made of carbon nanofibers (CNFs)on the composite surface.A series of sand erosion experiments were carried out to compare the particle erosion performance of CF based composites with and without surface protection by the CNF puter simulations of finite element (FE)meth-od were used to explain the underlying mechanisms for the ob-served performance difference between the two composites made of microscale CFs and nanoscale CNFs.2.Experimental 2.1.MaterialsThe CNF used in this study was a vapor grown carbon nanofiber,Pyrograf Ò-III (PR-24-XT-HHT),obtained from Applied Sciences Inc.(Cedarville,OH).The length of CNFs is about 30–100l m and the average diameter is about 100nm.The carbon fiber woven fabric used in this work was an IM7-12k,5harness,370g/m 2fabric obtained from Textile Industries,Inc.An epoxy resin,EPIKOTETM RIM 135with an epoxy equivalent weight (EEW)of about 166–185,and a diamine curing agent,EPIKURETM RIM H 137with an amine value of about 400–600mg [KOH]/g,were provided by Hexion Specialty Chemicals (Houston,TX).This is a low tempera-ture and low viscosity resin designed for manufacturing wind tur-bine blades.Silica sand,blocky,sharp edged green particles with a size about 150l m and a hardness of 2600Knoop were selected as the erodent.A scanning electron micrograph of the silica sand is shown in Fig.1.1359-8368/$-see front matter Ó2013Elsevier Ltd.All rights reserved./10.1016/positesb.2013.05.003Corresponding author.Address:The Ohio State University,125A Koffolt Laboratories,140West 19th Avenue,Columbus,OH 43210,USA.Tel.:+16142922408;fax:+16142923769.E-mail addresses:zhangna163163@ (N.Zhang),yangyangyang99@ (F.Yang),shency@ (C.Shen),castro.38@ (J.Castro),lee.31@ (L.J.Lee).1These authors contributed equally to this work.2Present address:Department of Mechanical and Industrial Engineering,Univer-sity of Toronto,Toronto,ON,Canada M5S 3G8.2.2.Fabrication of CNF nanopaper and CNF nanopaper coated glass fiber/epoxy compositesA vacuum filtration technique was used for preparing the nano-paper.In this set up,a 90mm diameter glass filter holder with a stainless steel screen membrane support was placed over a conical flask.Once the hydrophilic polycarbonate membrane filter with a pore size of 0.4l m (Millipore Inc.)was placed plain flat in the set up and clamped,it was connected to a vacuum aspirator pump.The nanoparticle solution was prepared as follows:the CNF parti-cles were dispersed in deionized (DI)water and sonicated using a Branson Digital Sonifier [(S450D),75%amplitude]for 30min.The resulting suspension was cooled down for 30min in a refrigerator and sonicated for 30sec again,then filtered through the filtration set up previously described under a pressure of $400kPa.Vacuum was applied for about 20min after all the water was filtered away.The CNF nanopapers were dried overnight at room temperature.The thickness of CNF nanopapers was 0.28±0.02mm with a poros-ity of 94%.Vacuum assisted resin transfer molding (VARTM)was used to impregnate the CF and CNF nanopaper coated CF preforms,which consisted of three layers of CF fabrics with andwithout a single layer of CNF nanopaper.The performs were placed and sealed a vacuum bag.Before mold filling,vacuum was applied to force the bag to press tightly against the fiber stack.The epoxy mixture was degassed in a vacuum chamber for 15min,and the resin was introduced into the fiber preforms.The samples were cured room temperature (around 25°C)for 24hr and post-cured 80°C for an additional 15hr.The CF and CNF nanopaper contents in the composites were controlled at 52and 12wt.%,respectively,measured by a thermo-gravimetric analyzer (TGA).2.3.Particle erosion testRectangular samples of size 12.5Â80mm molded composite plaques for the erosion epoxy and CNF/epoxy composites showed brittle with the maximum erosion rate at normal impinging angle was chosen as 90°in this frame with a rectangular opening was placed the test specimens to keep the eroded area The conditions under which the erosion are listed in Table 1.A standard test procedure each erosion test.Before testing,the samples were burnished to re-move the pollutants from the sample surface.After each test,spec-imens were degreased with acetone,dried in a jet of cold air and weighted with a precision balance (Explore,ep214C).The weight loss by sand abrasion (with an accuracy of 0.1mg)was used to quantify the erosion resistance.Each data point was obtained from the average value of five measurements.Scanning electron microscopy (SEM)images were collected using a field emission scanning electron microscope,Hitachi S-4300(Tokyo,Japan).The samples were gold-sprayed to reduce charging of the surface.3.Finite element simulationTo investigate the mechanisms of particle erosion,Finite ele-ment (FE)simulations were carried out for CF/epoxy composites with and without CNF nanopaper coating.It is difficult to track the actual erosion process which involves a large number of colli-sion events.Most of the existing work simulated only one or a few particle collision events [16–20].However,the trend can still be obtained for the erosion rate as a function of various parameters such as impinging angle,velocity,and target properties [16,19].In this study,one collision event with periodically distributed par-ticles was simulated.Qualitative comparisons were made between the experiments and the simulations.This study aims at providing insights into the mechanisms underlying the particle erosion per-formance of CF and CNF reinforced epoxy composites.Three-dimensional simulations were carried out using the gen-eralized FE codes ABAQUS/EXPLICIT version 6.9.Fig.2illustrates the configuration for the simulation of CF/epoxy composite.The eroding particles were simplified as spheres which were projected to the target surface in periodic arrays.The CF woven fabric has an Fig.1.Scanning electron micrograph of silica sand particles.Table 1Erosion test conditions.Impingement angle (°)90Impingement area (mm 2)600Impingement time (s)15Erodent feed rate (g/min)453.4Test temperature (°C)20Nozzle to sample distance (mm)25.4Nozzle diameter (mm)8Air pressure (MPa)0.47Fig.2.FE configuration of the particle erosion on surface of CF/epoxy composite.Part B 54(2013)209–214Fig.3a.The diameter of the eroding particle is0.15mm according to the experiments.The diameter of the CFs is adjusted so that the carbon content is52%by weight,consistent with experiment mea-surements.The model contained117,153linear solid elements with reduced integration(type C3D8R).Fig.3b shows the RVE for the CNF nanopaper.The dimensions are the same as the CF/epoxy case except the coating thickness,for which a smaller value of 0.05mm was applied.Utilizing the geometric symmetry,the RVE for CNF nanopaper only needs to contain one fourth of the config-uration of that for CF/epoxy composite.The right graph in Fig.3b is a magnification of thefiber skeleton for a small portion of the CNF nanopaper model.Since the randomly interweavedfiber configura-tion in experiments cannot be easily constructed in meshing,a uni-formly distributed orthogonal frame of beams is used instead to represent the highly interlaced CNF network.A square cross sec-tion instead of a circular section is used for CNF for simplicity. Thefiber diameter of CNF in simulation is chosen as0.5l m which is larger than that observed in the experiments.This is because thinner CNFs would needfiner mesh and hence more computa-tional expense.In spite of this,a large number of elements are needed due to the huge difference between the CNF diameter and the dimension of simulation RVE which depends on the size of eroding particles.The CNF inter-space is chosen as2.82l m so that the carbon content would be12%by weight in the nanopaper, consistent with our experiments.The obtained model contains 1,060,428C3D8R elements,corresponding to more than100CPU hours for a typical run on a2.6GHz computer for3l s of simula-tion time.Although this simplified model is different from the actual composites,we expect that it can provide qualitative inter-pretation of the experimental observations.Periodic boundary conditions are applied on the lateral bound-aries by coupling the degrees of freedom of the corresponding nodes on the opposite faces using the linear equations for CF/epoxy version2.1.For all configurations the mesh is refined near theimpinging location so that the eroded mass could be accuratelycaptured.The silica particles are modeled using the linear elastic constitu-tive law.While epoxy,CF and CNF are modeled using the elastic–plastic constitutive law with linear isotropic hardening.The mate-rial parameters are listed in Table2[22–25],where q is the density, E is the Young’s modulus,v is the Poisson’s ratio,r y is the yield stress,E is the Young’s modulus,E p is the hardening modulusand r s is the material strength.The physical meaning of the parameters can be revealed by the stress–strain(r–e)relation for uni-axial stretch deformation in small deformation range as in Eq.(1).e¼rE;r<r yrþrÀr yp;r P r y(ð1ÞIt can be seen from Table2that the plastic strain set is very small,reflecting the brittle property of these materials.In order to model the erosion of the target materials,a criterion is needed for the element removal.For the brittle erosion,the mass removal is caused by the spalling mechanism involving the evolu-tion of micro-cracks,which is very difficult to model by the FE method.Some researchers used Johnson–Holmquist model and the corresponding equation of state to model the failure behavior of the brittle materials[21].However,the large amount of ele-ments and the multi-phase properties of composites would cause huge computational expense if complex models are applied.There-fore a simplified criterion based on equivalent stress is applied here for the element removal.The element is removed once the equivalent stress r at its integration point reaches the critical value r cri as in Eq.(2).Here r0is the deviatoric stress tensor, r cri is cho-sen as the material strength r s.This criterion can be simply imple-mented in the dynamic shear failure option available in ABAQUS/Computational RVEs with mesh for(a)CF/epoxy composite and(b)CNF nanopaper.The inset graph shows the enlarged view of the skeleton of CNFs in portion indicated by the square.N.Zhang et al./Composites:Part B54(2013)209–214211r ¼ffiffiffiffiffiffiffiffiffiffiffiffiffiffiffiffiffi3r 0:r 0r ¼ rcri4.Results and discussionsImages of the CF woven fabric and CNF Fig.4a and b,respectively.After uniformly stream impacting for a given time,the CF/epoxy was severely eroded while the surface protected by paper coating did not show much erosion.The inspected by SEM (Fig.4c and d).As can be seen,sists of the removal of matrix materials in the resin that the exposed fibers are no longer bonded to when the epoxy matrix fails to support the fibers.fibers could easily break into fragments,removal during erosion.The failure mode in process involving surface matrix removing,surface micro-cracking,fiber/matrix debonding,fiber breakage and material removal [10–12].As shown in Fig.4c,many micro-cracks caused by the im-pact of erodent particles can be seen in carbon fibers,and many small fragments of fibers also can be seen on the eroded surface.For the surface protected by the CNF nanopaper coating,there are few exposed segments of carbon nanofibers after particle ero-sion as shown in Fig.4d.many CNFs can partake the impact force and the fiber network be-haves as a whole shielding during particle collision.While for CF/epoxy composites,the fiber spacing is comparable or even larger than the size of the eroding particles,therefore,the resin matrix is not well protected.The pure epoxy plaque shows a better parti-cle erosion resistance than its CF/epoxy composite,but the resis-tance is not as good as the CNF nanopaper coating.Our FE simulation results further interpret the experimental served differences between CF/epoxy composite with and without nanopaper during particle erosion.The eroded volume is calcu-as the amount caused by the single impingement.The eroded volume for CF/epoxy is about three times as that for CNF nanopaper.addition,the erosion results are more sensitive to the impinging location for CF/epoxy composite than for CNF pares the eroded volume at different impinging positions CF/epoxy composite and CNF nanopaper.The eroded volume plotted versus a surface distance of several times of the REV range utilizing periodicity.Five representative positions A,B,C,D,and investigated for CF/epoxy composites while two positions woven fabric,(b)SEM image of CNF nanopaper,(c)SEM images of eroded CF/epoxy composite surface,composite surface.Fig.5.Mass loss of different materials after 15sec erosion test.212N.and G are investigated for CNF nanopaper as indicated in Fig.6b.For CF/epoxy composite the eroded volume at position E is nearly40% smaller than that at position A.While for CNF nanopaper the rela-tive difference for eroded volume between the two positions is below10%.The largest erosion rate occurs when particle impinges at the resin rich position in both cases.The simulation results pro-vide qualitative explanation to the fact that the eroded surface of CNF nanopaper is much smoother than that of CF/epoxy composite.Comparison of the effect of impinging positions on the eroded volume for CF/epoxy composite and CNF nanopaper.(a)The eroded volume versus curve for CNF nanopaper and right for CF/epoxy;(b)Top view of the different impinging positions,where L is the distance betweenfiberContour plot of von Mises stress for(a)CF/epoxy and(b)CNF nanopaper at maximum erodent indentation,(c)von Mises stress versus the distance from position along the x axis on the target surface.The horizontal dash lines in(c)indicate the critical stresses for CNF/CF and epoxy,respectively.The much smaller erosion rate of CNF nanopaper can be attrib-uted to its nano-sized structure.For CF/epoxy composite thefiber spacing is larger or comparable to the eroding particle size and the relative weak resin cannot be effectively protected.While for the nanopaper thefiber spacing is much smaller,a large number of in-ter-connectedfibers can partake the impact force of the particle to-gether at the impinging position.This effect can be demonstrated by comparing the stress distribution for the two target materials. Fig.7a and b plot the contour of von Mises stress at maximum ero-dent indentation for CF/epoxy composite and CNF nanopaper, respectively.For both targets the erodent impinges at the positions corresponding to the largest erosion,i.e.position A for CF/epoxy composite and F for CNF nanopaper.It shows that for CNF nanopa-per the stress endured by the CNFs is much higher than that by the epoxy resin while for CF/epoxy composite the stresses infiber and resin do not differ much.In both cases,the resin is the main source for eroded volume due to its much lower strength than thefibers. The stress distribution can be more clearly seen in Fig.7c where the von Mises stress on the target surface is plotted against the dis-tance from the initial impinging position along the x axis.For Fig.7c the erosion criteria is switched off in the simulations for comparison convenience.The peaks and valleys on the curve of CNF nanopaper correspond to the high stresses on CNFs and low stresses on epoxy.It can be seen from Fig.7c that although the nanofibers in CNF nanopaper experience very high stress near the impinge location,the epoxy resin actually experiences a lower stress than that in CF/epoxy composite because the stress is mainly endured by the CNFs for CNF nanopaper as indicated by the dark strips in Fig.7b.The intensely distributedfibers play an important role in partaking the impacting force,leading to smaller stress in the weak resin.While for CF/epoxy composite thefiber may be far away from the impinge location due to the largefiber inter-space.The impact force is mainly endured by the weak resin. Fig.7c represents the instantaneous stress distribution for a case study.The nanopaper may not lose any weight at this time point because the endured stresses by both CNF and epoxy are lower than the critical CNF/CF and epoxy stresses marked on Fig.7c.On the other hand,some epoxy near the impinging point of the CF/ epoxy composite may be ablated away because the endured stress there reaches the critical value.Although qualitative,this simpli-fied analysis provides an explanation for the observed differences of particle resistance between the two composite materials.5.ConclusionsIn this study,carbon nanofiber(CNF)nanopaper was prepared by thefiltration method and used to protect the carbonfiber (CF)/epoxy composites through vacuum assisted resin transform molding(VARTM)process.The CNF nanopaper can achieve much better particle erosion resistance than the conventional CF/epoxy composites.Ourfinite element simulations of the particle erosion experiments,although highly simplified,are able to provide qual-itative insight regarding the underlying mechanisms.The CNF nanopaper is indicated as a good protective coating material for wind turbine blades and other related applications in aerospace and transportation industries.AcknowledgementsThefirst author would like to acknowledge the China Scholar-ship Council for theirfinancial support to enable the author to study at The Ohio State University.The authors would like to thank NSF and Nanomaterial Innovation Ltd.for partialfinancial support of this work.Carbonfiber mats were donated by Textile Industries, Inc.and the epoxy resin was donated by Hexion.References[1]Miyazaki N,Takeda N.Solid particle erosion offiber reinforced plastics.JCompos Mater1993;27(1):21–31.[2]Tsiang TH.Sand erosion offiber composites:testing and evaluation.In:ChamisCC,editor.Test Methods and Design Allowables for Fibrous Composites,vol.2.ASTM STP1989:1003;55–74.[3]Tilly GP.Sand erosion of metals and plastics:a brief review.Wear1969;14:241–8.[4]Tilly GP.Erosion caused by airborne particles.Wear1969;14:63–79.[5]Tilly GP,Sage W.The interaction of particles and material behaviour in erosionprocess.Wear1970;16:447–65.[6]Miyazaki N,Hamao T.Effect of interfacial strength on erosion behavior of FRPs.J Compos Mater1996;30(1):35–50.[7]<>.Last accessed on September262012.[8]Dalili N,Edrisy A,Carriveau R.A review of surface engineering issues critical towind turbine performance.Renew Sust Energy Rev2009;13(2):428–38. [9]Barkoula NM,Karger-Kocsis J.Review processes and influencing parameters ofthe solid particle erosion of polymers and their composites.J Mater Sci 2002;37(18):3807–20.[10]Tilly GP.A two stage mechanism of ductile erosion.Wear1973;23(1):87–96.[11]Pool KV,Dharan CKH,Finnie I.Erosive wear of composite materials.Wear1986;107(1):1–12.[12]Patnaika A,Satapathyb A,Chandc N,Barkoulad NM,Biswasb S.Solid particleerosion wear characteristics offiber and particulatefilled polymer composites:a review.Wear2010;268(1–2):249–63.[13]Zhou G,Movva S,Lee LJ.Preparation and properties of nanoparticle and long-fiber-reinforced unsaturated polyester composites.Polym Compos 2009;30(7):861–5.[14]Palmeri MJ,Putz KW,Ramanathan T,Brinson LC.Multi-scale reinforcement ofCFRPs using carbon nanofipos Sci Technol2011;71(2):79–86. [15]Cai ZQ,Movva S,Chiou NR,Guerra D,Hioe Y,Castro JM,et al.Effect ofpolyaniline surface modification of carbon nanofibers on cure kinetics of epoxy resin.J Appl Polym Sci2010;118(4):2328–35.[16]ElTobgy MS,Ng E,Elbestawi MA.Finite element modeling of erosive wear.Int JMach Tool Manu2005;45(11):1337–46.[17]Griffin D,Daadbin A,Datta S.The development of a three-dimensionalfiniteelement model for solid particle erosion on an alumina scale/MA956substrate.Wear2004;256(9–10):900–6.[18]Takaffoli M,Papini M.Finite element analysis of single impacts of angularparticles on ductile targets.Wear2009;267(1–4):144–51.[19]Shimizu K,Noguchi T,Seitoh H,Okadab M,Matsubara Y.FEM analysis oferosive wear.Wear2001;250(1–12):779–84.[20]Bielawski M,Beres W.FE modelling of surface stresses in erosion-resistantcoatings under single particle impact.Wear2007;262(1–2):167–75.[21]Wang YF,Yang ZG.Finite element model of erosive wear on ductile and brittlematerials.Wear2008;265(5–6):871–8.[22]Martienssen W,Warlimont H.Springer handbook of condensed matter andmaterials data.Berlin:Springer;2005.[23]Low KH,Wang Y.Modeling of multi-layer circuit boards by using a model ofbi-phase and elasto-plastic plies.Circuit World2007;33:9–20.[24]Tibbetts GG,Beetz JCP.Mechanical properties of vapour-grown carbonfibres.JPhys D:Appl Phys1987;20(3):292–7.[25]Grace NF,Ragheb WF,Sayed GA.Development and application of innovativetriaxially braided ductile FRP fabric for strengthening concrete pos Struct2004;64(3–4):521–30.214N.Zhang et al./Composites:Part B54(2013)209–214。
- 1、下载文档前请自行甄别文档内容的完整性,平台不提供额外的编辑、内容补充、找答案等附加服务。
- 2、"仅部分预览"的文档,不可在线预览部分如存在完整性等问题,可反馈申请退款(可完整预览的文档不适用该条件!)。
- 3、如文档侵犯您的权益,请联系客服反馈,我们会尽快为您处理(人工客服工作时间:9:00-18:30)。
The pyruvate dehydrogenase complex contans three enzymes and requires fymes
pyruvate
TPP
dehydrogenase(E1)
dihydrolipoyl
Lipoate, CoA-SH
The complete oxidation of pyruvate in
animal tissues was proposed to undergo
via a cyclic pathway
• O2 consumption and pyruvate oxidation in minced muscle tissues were found to be stimulated catalytically by some four-carbon dicarboxylic acids (Fumarate, succinate, malate and oxaloacetate, fivecarbon dicarboxylic acid (a-ketoglutarate ), or sixcarbon tricarboxylic acids (citrate, isocitrate, cisaconitate).
Cellular respiration: the processes by which cells consume O2 and produce CO2. Cellular respiration occurs in three major stages.
The citric acid cycle also called the tricarboxylic
The citric acid cycle is a hub in metabolism, with degradative pathways leading in and anabolic pathways leading out, and it is closely regulated in coordination with other pathways.
Chapter 16 The Citrc Acid Cycle
For most eukaryotic cells and many bacteria, living under aerobic conditions, the pyruvate produced by glycolysis is further oxidized to H2O and CO2.
acid cycle or the Krebs cycle. The acetyl-CoA is fed into
the citric acid cycle, which enzymatically oxidizes them to CO2. The energy released by oxidation is conserved in the reduced electron carriers NADH and FADH 2 .
• Malonate inhibits pyruvate oxidation regardless of which active organic acid is added!
transacetylase (E2)
dihydrolipoyl
FAD, NAD
dehydogenase (E3)
Coenzyme A (CoA-SH): discovered in 1945 by Fritz A. Lipmann, delivers activated acyl groups (with 2-24 carbons) for degradation or biosynthesis.
Entry of pyruvate into the mitochondrion
16.1 Production of acetate: Pyruvate, derived from glucose and other sugers by glycolysis, is oxidized to acetyl-CoA and CO2 by the pyruvate dehydrogenase complex, which located in the mitochondria of eukaryotic cells and in the cytosol of prokaryotes. The process is an oxidative decarboxylation.
Oxidative decarboxylation of pyruvate to acetyl-CoA by pyruvate dehydrogenase complex. Central to the mechanism of the pyruvate dehydrogenase complex are the swinging lipoyllysyl arms of E2, which accept from E1 the two electrons and the acetyl group derived from pyruvate, passing them to E3.
The pyruvate dehydrogenase complex is the prototype for two other important enzyme complexes: αketoglutarate dehydrogenase and branched-chain αketoacid dehydrogenase.
Beriberi, a disease that results from thiamine deficiency, is characterized by loss of neural function.
High efficiency multienzyme complex, “substrate channeling”