S6000-LC8R-V1.5修改说明
朗林式式 模式 8005 智能门系统快速启动指南说明书

7”7”40.5” Fixed Position90°Securely mount a control box near the actuator armwith appropriate hardware (notsupplied).Gate Hinge Pivot Point Coaxial CableAntenna Actuator CableP o w e r C o n d u i tL o o p s C o n d u i tFront Bracket Pivot PointFront BracketRear Bracket(Adjustable, See Manual)Rear Bracket Pivot PointClosed PositionOpen to the Inside PositionControl BoxActuator arm and brackets MUST be level !6003-066-P-6-17LimitSlow DownU ns c re w 4 s cr e ws t or em o v ec o ve r .L o os e n nu tt o ad j u s t l i mi t se n s o r .Note: This illustration shows NO gate hinge inset. If gate hinge is inset on wall, see “Rear Bracket Configurations for Different Gate Hinge Insets” in the 6003 Actuator Arm and Control Box Mounting manual.Circuit board power must be ON to adjust limit sensors, LEDs will light.Cut Off Excess BracketCut Off Excess BracketBottomMiddle TopThe 6003 is intended for installation only on swing gates used for vehicles.Pedestrians must be supplied with a separate access opening. For safety and installation instructions, please refer to 6003 Actuator Arm and Control Box Mounting manual, 115 VAC or Solar Control Box Wiring/Owner’s manuals .3 Li m i t5 L i m it 4 Sl oD w n 6 Sl o D wn 120 S. Glasgow Avenue Inglewood, California 90301U.S.A.THIS PRODUCT IS TO BE INSTALLED AND SERVICED BY A TRAINED GATE SYSTEMS TECHNICIAN ONLY . Visit to find a professional installing and servicing dealer in your area.M anually release the arm and fully extend the powered shaft. Rotate it back two full turns before installing the arm.Unlock operator to manually move gate.Prevent Powered Shaft from Bottoming OutRotate back 2 turns before installing.Manual ReleaseFully Extended (Bottomed Out)Powered ShaftBrown wire Blue wire Orange wire Red wire Yellow wire Green wire Green/Yellow wireNOT USED7-Wire Operator Actuator CableA support bar must be installed the entire length of the gate to support the pickets.Coaxial Cable Antenna Kit P/N 1514-073 (Sold separately)G a t e C l o s e d21”Typical27.5”Max Photo Sensors HeightClose BeamOpen BeamOpen BeamClose BeamReversing EdgePhoto SensorPhoto SensorSensor mounted just below actuator arm cable.G a t e O p e n e dCopyright 2017 DoorKing, Inc. All rights reserved.External Entrapment Protection DevicesOutside PropertyInside PropertyDO NOT cycle operator before limit sensors andDIP-switches have been adjusted, damage could occur to gate and operator.Single operator connects to PRIMARY connection ONLY on the 115 VAC OR Solar control box circuit board.17865432PRIMARY4302430243025” or lessOpening Direction DIP-Switch 1 (SW 1)Refer to YOUR chosen 115 VAC OR Solar powered control box manuals for complete DIP-switch settings.Manually move the gate to the desired open or closed position. Loosen the limit nuts and slowly slide the limit assemblies until the LIMIT LEDs on the circuit board light up.Rear Bracket ConfigurationsWall2”21/2”3”Straight51/2”Reversing Edge is mounted along ENTIRE end of gate.Potential Entrapment AreaFactory wired jumpers MUST be removed.Operator Opens to the InsideOperator Opens to the InsideNote: Only 1 monitored Device can be connected for each cycling direction. An OPTIONAL Expansion Kit (sold separately) will allow connection for additional devices.Refer to YOUR chosen 115 VAC OR Solar powered control box manuals to wire entrapment protection devices.Open to the InsideOpen to the Outside - Refer to 6003 manualNote: Refer to 6003 manual for “Open to the Outside” installation.The operator MUST OPEN GATE upon initial power up and OPEN command.If the operator closes gate after giving open command, shut off power and reverse this switch setting otherwise operator will NOT function correctly.。
S600说明书

德众尚杰S600示例说明书S600目录一、注意事项 (3)二、产品特点 (3)三、按键的功能说明 (4)四、基本操作 (6)五、设置 (7)六、收音机功能操作 (13)七、GPS卫星导航功能操作 (14)八、光碟播放基本操作 (14)九、U盘,SD卡播放操作 (16)十、虚拟多碟(可选功能) (17)十一、IPOD播放(可选功能) (18)十二、蓝牙免提系统操作 (19)十三、蓝牙音乐播放(A2DP) (20)十四、AVIN(辅助源输入)操作 (20)十五、移动电视操作 (20)十六、行车记录仪操作 (20)十七、安装GPS天线 (20)十八、常见故障排除向导 (21)S600一、注意事项为了您的安全,请尽量不要在驾驶时观看视频和操作机器;开车时请将音量调到能清楚听到外界声音的水平。
开始操作前,请详细阅读本手册以及系统的其他手册,了解本使用手册和机器上的相关安全提示和警告标识,阅读完之后放在随手可及的地方以备随时参考。
●首先请注意交通安全。
●如您在操作本系统遇到困难时,请将车停放在安全的地方后操作。
●勿让儿童操作本机器,以免造成人身伤害或机器损坏。
●在使用卫星导航功能时请遵照交通规则驾驶。
●请不要在禁止使用电子设备或严禁明火的地方使用,如:加油站、酒厂、电磁强干扰地区等,否则可能造成危险。
●不要自行保养、维护、安装本机器。
在接通电源的情况下请勿安装或维修本机,由未受过电子设备或车辆附件安装训练或缺乏经验的人员安装及维修本机器非常危险。
●不要把本机器贮藏或安装在阳光直射的地方,也不要将其置于其他有害物质环境里,特别是液晶屏。
如果安装的时候,液晶屏正好处于空调器通风道附近,请保证凉风或者热风不要直接吹到机器上,否则可能损坏机器,甚至对汽车或者人身产生伤害。
●切勿用一些尖锐的物体刮划显示屏,不要拿硬物大力按压显示屏,否则会造成显示屏或触摸屏的损坏。
●为了保证机器正常运转,防止火灾或电击发生,请不要将机器暴露在潮湿的空气中,更不能将液体洒落机器上。
c6000中文说明书-精密空调机组微处理控制器操作手册
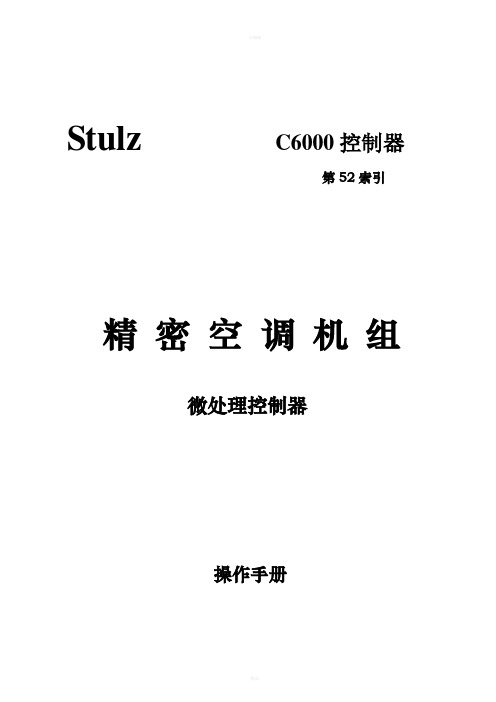
Stulz C6000控制器第52索引精密空调机组微处理控制器操作手册目录页码简介 (3)安全须知 (3)页码代号 (3)控制器说明 (4)操作界面 (6)控制器操作 (7)菜单对话框和参数说明启动窗口.............................................................................. .. (8)标准窗口 (9)“信息”菜单..................................................................... ......... .. 10“控制”菜单................................................................................. .... .12“服务”菜单................................................................................. . (17)功能说明监控器操作.................................................................................... (26)GE操作 (27)干冷器操作 (28)两套系统的顺序控制 (29)总线顺序控制 (31)数字自控连接 (32)备份运行 (34)传感器的故障 (36)信号....................................................................................... (37)控制器出厂时的设........................................................................ (40)控制图....................................................................................... (42)硬件说明控制器.......... .. (44)下载新软件 (45)标准I/O板 (48)扩展I/O板 (52)温度/湿度传感器 (54)系统配置带I/O板的C6000的电路图 (55)第一模块带监控器的C6000的电路图 (55)第二模块带监控器的C6000的电路图 (56)打印机连接 (57)电脑连接 (57)故障排除 (58)信息水平概述 (59)控制水平概述 (60)服务水平概述 (61)简介本手册对控制器的操作和设计进行了说明,控制器组成了空调单元的中央控制站,整个空调都是由控制器控制和检测的。
RG-S6000系列交换机安装手册-WuhanUniversity

RG-SU For Mac 1.33_Build20150327版本使用说明版权声明锐捷网络©2015锐捷网络版权所有,并保留对本手册及本声明的一切权利。
未得到锐捷网络的书面许可,任何人不得以任何方式或形式对本手册内的任何部分进行复制、摘录、备份、修改、传播、翻译成其他语言、将其全部或部分用于商业用途。
、、、、、、、、、、、都是锐捷网络的注册商标,不得仿冒。
免责声明本手册内容依据现有信息制作,由于产品版本升级或其他原因,其内容有可能变更。
锐捷网络保留在没有任何通知或者提示的情况下对手册内容进行修改的权利。
本手册仅作为使用指导,锐捷网络在编写本手册时已尽力保证其内容准确可靠,但并不确保手册内容完全没有错误或遗漏,本手册中的所有信息也不构成任何明示或暗示的担保。
技术支持4008-111-000前言感谢您使用锐捷网络产品,本手册为您提供了使用说明指导。
适用对象适用于在安装和维护网络硬件方面具有一定经验的用户,同时假定该款产品的用户熟知相关术语和概念。
技术支持⏹锐捷网络官方网站:/⏹锐捷网络在线客服:⏹锐捷网络官方网站服务与支持版块:/service.aspx⏹7×24小时技术服务热线:4008-111-000⏹锐捷网络技术论坛:/portal.php⏹常见问题搜索:/service/know.aspx⏹锐捷网络技术支持与反馈信箱:4008111000@文档格式约定本书采用各种醒目标志来表示在操作过程中应该特别注意的地方,这些标志的意义如下:注意、警告、提醒操作中应注意的事项。
说明、提示、窍门、对操作内容的描述进行必要的补充☑对于产品的支持情况进行必要的补充。
技术支持4008-111-000安装卸载指南1 安装指南该部分主要介绍了RG-Supplicant认证客户端的软硬件配置要求,安装过程的详细步骤,以及需要注意的事项。
1.1RG-Supplicant软件安装说明1.1.1 硬件和操作系统要求下表说明安装RG-Supplicant 认证客户端的硬件和操作系统要求。
卡索金属检测机说明书

金屬檢測機 METAL SHARK® 型號 操作手冊 / 使用說明【中文】
項目:
項目名稱 訂單/項目編號 oc
METAL SHARK®
目錄
目錄 .................................................................................................... 1-2 1. 一般資料......................................................................................... 1-5
2.1. CE–質量符合聲明 ....................................................................... 2-6 2.2. 生產商的聲明 ............................................................................. 2-7 3. 應用及限制範圍................................................................................ 3-8 3.1. 正常使用 ................................................................................... 3-8 3.2. 錯誤使用 ................................................................................... 3-8 3.3. 如何行使擁有人責任的應有注意...................................................... 3-8 3.4. 操作人員的要求 .......................................................................... 3-9 3.5. 服務和維護人員的要求.................................................................. 3-9 4. 一般的安全指示...............................................................................4-10 4.1. 安全符號 ..................................................................................4-10 4.2. 一般的安全指示 .........................................................................4-10 4.3. 金屬檢測機的安全指示.................................................................4-11
福让冰机操作与维护手册说明书

HCC700A, HCC700W,HCD700A, HCD700W Ice Machines801 Church Lane • Easton, P A 18040, USAOperation and Service ManualOrder parts onlineTable of contentsWelcome to FollettFollett equipment enjoys a well-deserved reputation for excellent performance, long-term reliability and outstanding after-the-sale support. T o ensure that this equipment delivers the same degree of service, we ask that you review the installation manual (provided as a separate document) before beginning to install the unit. Our instructions are designed to help you achieve a trouble-free installation. Should you have any questions or require technical help at any time, please call our technical service group at (877) 612-5086 or +1 (610) 252-7301.Before you beginAfter uncrating and removing all packing material, inspect the equipment for concealed shipping damage. If damageis found, notify the shipper immediately and contact Follett Corporation so that we can help in the fi ling of a claim,if necessary.Check your paperwork to determine which model you have. Follett model numbers are designed to provide information about the type and capacity of Follett equipment. Following is an explanation of the different model numbers in the 700 series.Specifi cationsElectricalEach ice machine requires its own separate circuit with electrical disconnect within 10 ft (6m).Equipment ground required.Standard electrical:HCC700: 208-230/60/1 (6 ft (2m) NEMA 6-15 cord and plug provided)HCD700: 115/60/1 (6 ft (2m) NEMA 5-15 cord and plug provided)Maximum ice machine fuse – 15 amps eachAmperage – 115V: 10A, 220V: 5APlumbing3/8" OD push-in water inlet3/4" MPT drain1/4" FPT condenser inlet (water-cooled condenser only)1/4" FPT condenser drain (water-cooled condenser only)Notes:3/4" vented drain line must slope a minimum of 1/4" per foot (6mm per 30.4cm run).Drain to be hard piped and insulated.To prevent back fl ow, do not connect drains.Separate drains for ice machine and condenser.Water shut-off recommended within 10 feet (3m).Water supply must be treated by a scale-inhibiting fi lter (Follett item# 00130286).AmbientAir temperature 100 F/38 C max. 50 F/10 C min.Water temperature 90 F/32 C max. 45 F/7 C min.Water pressure – potable 70 psi max. (483 kPa) 10 psi min. (89 kPa)Note: Water-cooled condenser pressure 150 psi (1034 kPa)Heat rejectionAir-cooled rejects 8850 BTU/hrWater-cooled rejects 10150 BTU/hrIce productionNote: Water regulating valve set to maintain a 215 PSIG (95°F Saturated R404A) discharge pressure at all conditions.Dimensions and clearancesEntire front of ice machine must be clear of obstructions/connections to allow removal.1" (26mm) clearance above ice machine for service.1" (26mm) minimum clearance on sides.The intake and exhaust air grilles must provide at least 160 sq in (1032 sq cm) of open area.Air-cooled model HCC700A ice machines – 18" (458mm) minimum clearance between discharge and airintake-grilles.Y)3/4"1. T o clean – Remove cover. Press the CLEAN button.The machine will drain. Wait for the LO WATER lightto come on (Fig. 1).Fig. 12. Mix 1 gallon (3.8L) 120 F (49 C) water and7 ounces (198g) (one 7 ounce packet of FollettSafeCLEAN ice machine cleaner, part# 00132001).Locate cleaning cup. Fill until CLEANER FULL lightcomes on (Fig. 2).Note: Do not use bleach to sanitize or clean the icemaker.CLEANER FULL Fig. 2Fig. 33. Replace cover on cleaning cup. Wait until machinerestarts. Machine will clean, then fl ush 3 times in approximately 15 minutes (Fig. 3).4. T o sanitize – Press CLEAN button. The machinewill drain. Wait for LO WA TER light to come on(Fig. 4).CLEANER FULLFig. 5Fig. 65. Mix 1 gallon 120 F (49 C) water and 1.6 ounces(48ml) NU-CALGON IMS-II SANITIZER. Fill until CLEANER FULL light comes on (Fig. 5).Place one Sani-Sponge ™ in remaining sanitizing solution and retain for Step 9.Note: Do not use bleach to sanitize or clean theicemaker.6. Replace cover on cleaning cup. Wait until machinerestarts. Machine will sanitize, then fl ush 3 times in approximately 15 minutes (Fig. 6).Fig. 8Fig. 98. Using disposable food service grade gloves, insertdry Sani-Sponge ™ (kit part# 00132068). Next, insert Sani-Sponge soaked in Nu-Calgon IMS-II sanitizer solution (from Step 5). Push both Sani-Sponges down ice transport tube with supplied pusher tube (Fig. 8).9. Remove and discard 16" (407mm) pusher tube(Fig. 9).Fig. 11 11. Place a sanitary (2 gallon or larger) container inbin or dispenser to collect Sani-Sponges and icefor 10 minutes. Collect 5.5 lbs (3kg) of ice from unit.Discard ice and Sani-Sponges (Fig. 11).ServiceIce machine operation (all models)Follett’s ice machine consists of fi ve distinct functional systems covered in detail as follows:• Water system• Electrical control system• Mechanical assembly• Refrigeration system• Bin fullThe Horizon ice machine overviewThe Follett Horizon ice machine uses a horizontal, cylindrical evaporator to freeze water on its inner surface. The refrigeration cycle is continuous; there is no batch cycle. The evaporator is fl ooded with water and the level is controlled by sensors in a reservoir. A rotating auger (13 RPM) continuously scrapes ice from the inner wall of the evaporator. The auger moves harvested ice through the evaporator into an ice extrusion canal. The ice is forced through a restrictive nozzle that squeezes out the water and creates the Chewblet. The continuous extrusion process pushes the Chewblets through a transport tube into a dispenser or bin.A solid state PC board controls and monitors the functionality of the ice machine. In addition to sequencing electrical components, the board monitors various operational parameters. A full complement of indicator lights allows visual status of the machine's operation. Additionally, the PC board controls the self-fl ushing feature of the ice machine. The evaporator water is periodically drained and replenished to remove minerals and sediment.A unique “bin full” detection system is incorporated in the Horizon ice machine. A switch located at the ice discharge port of the machine detects the position of the transport tube. When the bin fi lls up with ice, the transport tube moves out of the normal running position, and the switch turns the ice maker off. A domed housing at the end of the transport tube contains the ice extrusion loads during shut down.Harvest system diagramElectrical systemNormal control board operationThe PC board indicator lights provide all the information necessary to determine the machine's status. Green indicator lights generally represent “go” or normal operation; Y ellow indicators represent normal off conditions; Red indicators generally represent alarm conditions, some of which will lock the machine off.A fl ashing green light labeled POWER indicates power to the machine. All other normal operation status indicators are covered as follows:DIP Switch SettingsSensor safe NOT USEDFiltration message NOT USED NOT USED60 minute time delay Flush enabledMaintenance timer OFFCapacitive touchNOT USED No filtration NOT USED NOT USED30 minute time delayFlush disabledMaintenance timer ONThe Horizon PC board monitors various operating parameters including high pressure, auger gearmotor amperage limits, clogged drain, and low water alarm conditions. There are two types of errors namely “hard” or “soft”. A hard error is one that shuts the machine off and will not allow restart until the reset button is pressed. Even cycling power will not reset a hard error. A soft error can either be automatically reset should the condition rectify, or if power is cycled. Should an error occur, consult the troubleshooting guide in this manual or a Follett service technician.Soft errors:HI AMPS: The PC board monitors the amperage of the auger motor. Should the gear motor experience current draw above the allowable limit, the machine will shut down and the TIME DELAY and HI AMP will be illuminated. After the time delay the machine will restart and the TIME DELAY and HI AMP will clear.LO WA TER: During operation, the water level cycles between the normal low and normal high sensors. Should the water be shut off to a running machine, a soft error will occur. The error sequence is as follows: During operation, the water level falls to the normal low sensor, and when it does the water feed solenoid is energized. If water is not detected at the normal low sensor within 10 seconds, a soft error will occur. The machine will shut down, but the water feed solenoid will remain energized. Should water return, it will fi ll to the normal low sensor and the machine will resume normal operation. The error will clear automatically.HI PRESSURE: Should the refrigeration pressure rise above 425 psi, the machine will shut down and the TIME DELAY and HIGH PRESSURE will be illuminated. After the time delay, and if the pressure has fallen back below the reset point of 295 psi, the machine will restart and the TIME DELAY and HIGH PRESSURE will clear.Hard error:DRAIN CLOG: The drain clog sensor, located in the chassis, underneath the rear drain pan, will detect the presence of water just below the top edge of the pan. If water does not properly fl ow out of the drain pan it will overfl ow into the chassis and rise to the sensor (especially during a self-fl ushing purge cycle). Turning the power switch off and then back on again will restart the ice machine.Relay output indication:Each relay on the board has an indicator light associated with its output. For example, when the relay for the water feed solenoid is energized, the adjacent indicator light glows green.Time delay on start-up:ATTENTION!Unit has 15 minute start up delay when power is applied toprevent circuit overload. Depressing the reset button on thecontrol board will bypass this delay.Flushing logicFlush on fl y: For every one (1) hour of ice making time, the machine will open the drain valve for a duration of 60 seconds. While the drain valve is open, the machine will continue to make ice and the water feed valve will cycle to maintain water level.Off cycle: At the completion of off-cycle time delay, the machine checks for a cumulative one (1) hour of ice making time since the last off-cycle fl ush. If the cumulative ice making time exceeds one (1) hour, the machine will open the drain valve for 60 seconds to drain the evaporator in its entirety. It will then refi ll with water and begin making ice. If the ice making time is less than 1 hour, the machine will start and begin making ice without draining the evaporator.Mechanical SystemFig. 12Evaporator disassembly1.power OFF when LO WA TER lights.2. louvered docking assembly.3.Unplug gear motor.4. Remove shuttle housing:§Remove vent tube (Fig. 14.1).§Disconnect shuttle housing switch connections (Fig. 14.2).§Remove two screws and lift shuttle housing (Fig. 14.3).Fig. 15 5. Remove gear motor:§Remove gear motor insulation (Fig. 15.1).§Remove 11/16" auger nuts and washer (Fig. 15.2).§Remove two 1/2" bolts (Fig. 15.3).§Pull gear motor from auger (Fig. 15.4).§Remove main housing insulation (Fig. 15.5).6. Remove all traces of petro-gel from auger shaft.7. Remove main housing:§Use an allen wrench to remove 3/16" allen screws (3) (Fig. 16.1).§Remove shaft insulation (Fig. 16.2).§Remove main housing (Fig. 16.3).8. Remove and discard mating ring and seal(Fig. 17.1).9. Carefully remove auger (Fig. 17.2).ARNING!very sharp - handle with care to avoid personalinjury.10. Press the lever on the back of the reservoir(Fig. 18.1) to release and remove the solenoid (Fig. 18.2).11. Remove three screws to remove the reservoirinsulation (Fig. 19).12. Remove three screws to remove the reservoir(Fig. 20).13. T o remove the rear bushing, place the auger into theevaporator and use it to gently tap and dislodge therear bushing housing (Fig. 21).Evaporator reassembly Fig. 22 1. Remove and inspect O ring seal. Replace ifdamaged in any way.2. Place rear bushing into evaporator.3. Install the three bolts: partially tighten each bolt,alternating bolts until the rear bushing is fully seatedand properly aligned (Fig. 22).4. When fully seated, remove the bolts.5. Install the reservoir with three bolts (Fig. 23).6. Install the reservoir insulation, tube clamp, andsolenoid lever with three screws.7.Install solenoid.1. Remove and inspect O ring seal. Replace ifdamaged in any way (Fig. 25.1).2. Clean O ring groove. Lubricate O ring with petrol-geland reinstall (Fig. 25.2).3. Use cardboard disc to press new mating ring intomain housing (Fig. 26.1).4. Lube the shaft with liquid soap in the area shown(Fig. 26.2) and slip on seal and spring (Fig. 26.3).Note: Do not touch the sealing surfaces with barehands. Contact with bare skin will cause premature seal failure.5. Install auger (Fig. 26.4).6. Install main housing:§Slide main housing onto auger shaft (Fig. 27.1).§Install main housing insulation (Fig. 27.2).§Use an allen wrench to install 3/16" allen screws (3) (Fig. 27.3).7. Apply a coat of petrol-gel to the auger shaft.8. Install gear motor:§Install main housing insulation (Fig. 28.1).§Slide gear motor onto the auger shaft (Fig. 28.2).§Install two 1/2" bolts (Fig. 28.3).§Install 11/16" auger nuts and washer (Fig. 28.4). 9. Use 3/16" allen wrench to orient auger shaft withkeyway in the upward position (Fig. 29.1).10. Install key into keyway (Fig. 29.2).11. Install washer and fi nger tighten 11/16" jam nut.12. Tighten jam nut with adjustable wrench while usingallen wrench to prevent auger from turning.13. Install and tighten 11/16" auger nut with adjustablewrench while using another adjustable wrench tohold jam nut.14. Install gear motor insulation.Fig. 3215. Install shuttle housing:§(Fig. 32.1).§Plug in shuttle housing connections §Connect vent tube (Fig. 32.3).16. Plug in gear motor.§BROWN to BLUE §BLACK to BLACK §WHITE to GRAY17. assembly.Refrigeration system Refrigerant pressure dataRefrigeration system diagramRefrigeration chargeAll service on refrigeration systems must be performed in accordance with all federal, state and local laws. It is the responsibility of the technician to ensure that these requirements are met. Recharging ice machine to other than factory specifi cations will void the warranty.Refrigerant replacement requirements1. Non-contaminated refrigerant removed from any Follett refrigeration system can be recycled and returned tothe same system after completing repairs. Recycled refrigerant must be stored in a clean, approved storage container. If additional refrigerant is required, virgin or reclaimed refrigerant that meets ARI standard 700-88 must be used.2. In the event of system contamination (for example, a compressor burn out, refrigerant leak, presence ofnon-condensibles or moisture), the system must be repaired, evacuated and recharged using virgin orreclaimed refrigerant that meets ARI standard 700-88.3. Follett Corporation does not approve of recovered refrigerants. Improper refrigeration servicing procedureswill void the factory warranty.EvacuationEvacuate the system to a level of 500 microns. When the 500 micron level is reached, close all valves. Allow the system to sit for approximately 20 minutes. During this period the system pressure should not rise. If the system pressure rises and stabilizes there is moisture in the system and further evacuation is needed. If the pressure continues to rise check the system for leaks.Ambients MinimumMaximumAir temperature150 F/10 C 100 F/37.8 CWater temperature245 F/7 C 90 F/32.2 C1Ambient air temperature is measured at the air-cooled condenser coil inlet.2Ambient water temperature is measured in the ice machine water reservoir.Ice capacity testIce machine production capacity can only be determined by weighing ice produced in a specifi c time period.1. Replace all panels on ice machine.2. Run ice machine for at least 15 minutes.3. Weigh and record weight of container used to catch ice.4. Catch ice for 15 or 20 minutes.5. Weigh harvested ice and record total weight.6. Subtract weight of container from total weight.7. Convert fractions of pounds to decimal equivalents (ex. 6 lbs 8oz = 6.5 lbs).8. Calculate production using following formula:9. Calculated amount per 24 hours should be checked against rated capacity for same ambient and watertemperatures in Ice Production Tables.“Bin full” detection systemThe Follett Horizon ice machine incorporates a unique “bin full” detection system that consists of the shuttle and actuator. The shuttle incorporates a fl ag and sensor. Referencing the fi gure below, the normal running position of the fl ag is down, out of the sensor. When the bin fi lls to the top and ice can no longer move through the tube, the machine will force the shuttle fl ag up into the sensor, shutting the machine off. The shuttle actuator, located above the ice bin allows the ice to curl up within it when the bin is full. In this way, there are no loads generated that would tend to lift off the lid of the bin.Shuttle fl ag and sensorShuttle actuatorTroubleshootingPlease see “Service” section for a description of each function.Order parts online Order parts online Water-cooled assembly Order parts onlineOrder parts online Order parts online Integration kit – top-mount and RIDE remote ice delivery Order parts onlineOrder parts online Horizon, Harmony, Ice Manager, SafeCLEAN, Sani-Sponge, RIDE and Vision are trademarks of Follett Corporation. Chewblet and Follett are registered trademarks of Follett Corporation, registered in the US.。
西德摩商业网络5口开关用户指南说明书

©W e s t e r m o T e l e i n d u s t r i A BUser Guide6644-2240Legal informationThe contents of this document are provided “as is”. Except as required by applicablelaw, no warranties of any kind, either express or implied, including, but not limited to,the implied warranties of merchantability and fitness for a particular purpose, are madein relation to the accuracy and reliability or contents of this document. Westermoreserves the right to revise this document or withdraw it at any time without priornotice.Under no circumstances shall Westermo be responsible for any loss of data or incomeor any special, incidental, and consequential or indirect damages howsoever caused.More information about Westermo can be found at the following Internet address:26644-224036644-2240SafetyBefore installation:Read this manual completely and gather all information on the unit. Make sure that you understand it fully. Check that your application does not exceed the safe operating specifications for this unit.This unit should only be installed by qualified personnel.This unit should be built-in to an apparatus cabinet, or similar, where access is restricted to service personnel only.The power supply wiring must be sufficiently fused, and if necessary it must be possible to disconnect manually from the power supply. Ensure compliance to national installation regulations.This unit uses convection cooling.T o avoid obstructing the air flow around the unit, follow the spacing recommendations (see Installation section).Before mounting, using or removing this unit:Prevent access to hazardous voltage by disconnecting the unit from power supply.Warning! Do not open connected unit. Hazardous voltage may occur within this unit when connected to power supply.Class 1 Laser ProductDo not look directly into fibre optical fibre port or any connected fibre although this unit is designed to meet the Class 1 Laser regulations.Care recommendationsFollow the care recommendations below to maintain full operation of unit and to fulfil the warranty obligations.This unit must not be operating with removed covers or lids.Do not attempt to disassemble the unit. There are no user serviceable parts inside.Do not drop, knock or shake the unit, rough handling above the specification may cause damage to internal circuit boards.Do not use harsh chemicals, cleaning solvents or strong detergents to clean the unit.Do not paint the unit. Paint can clog the unit and prevent proper operation.Do not expose the unit to any kind of liquids (rain, beverages, etc). The unit is not waterproof. Keep the unit within the specified humidity levels.Do not use or store the unit in dusty, dirty areas, connectors as well as other mechanical part may be damaged.If the unit is not working properly, contact the place of purchase, nearest Westermo distributor office or Westermo T ech support.Fibre connectors are supplied with plugs to avoid contamination inside the optical port.As long as no optical fibre is mounted on the connector, e.g. for storage, service or transportation, should the plug be applied.SPECIAL CONDITION FOR SAFE USEAmbient temperature:This unit is designed for use in extreme ambient temperature conditions according to the following: –40 ºC to +74 ºC (–40 ºF to +165 ºF)Note. Fibre Optic HandlingFibre optic equipment needs special treatment. It is very sensitive to dust and dirt. Ifthe fibre will be disconnected from the modem the protective hood on the transmitter/ receiver must be connected. The protective hood must be kept on during transportation. The fibre optic cable must also be handle the same way.If this recommendation is not, it jeopardises the warranty.Cleaning of the optical connectorsIn the event of contamination, the optical connectors should be cleaned by the use of forced nitrogen and some kind of cleaning stick.Recommended cleaning fluids:• Methyl-, ethyl-, isopropyl- or isobutyl-alcohol• Hexane• NaphthaMaintenanceNo maintenance is required, as long as the unit is used as intended within the specified conditions.Agency approvals and standards compliance46644-2240Declaration of ConformityWestermo Teleindustri ABPierre Öberg6644-22405Type tests and environmental conditions66644-2240DescriptionThe SDW-541-F1G-T4G is an unmanaged 5-port switch with one SFP fibre port and four copper ports, all supporting 100 Mbit/s or Gbit Ethernet. The Westermo rangeof 100Mbit or Gbit Small Form-factor Pluggable (SFP) transceivers are available as multimode, singlemode or Bi-Di transceivers with distance up to 120 km.The SDW-550-T5G is an unmanaged 5-port Array switch with five copper ports, all supporting 10Mbit/s, 100 Mbit/s or Gbit Ethernet. Both aredesigned for easy use in heavy duty industrial,maritime and rail trackside applications. Theunits support 802.1Q long packets which allowall standard industrial Ethernet protocols tobe used.The units are designed for use in industrialapplications with dual 10 to 57 VDC powerinput. The unique “tri-galvanic” isolationprovides isolation between all ports, powersupply and between each chassis screenavoiding ground loop currents. The IP21rating ensures that the unit can be installed inlocations where condensed water may occur.Only industrial grade components are usedwhich gives an MTBF of 1.182.000 hours forthe SDW-541-F1T4G and 1.121.000 hours forthe SDW-550-T5G and thus ensures a longservice life. A wide operating temperaturerange of –40 to +74 °C (–50 to +165 °F) canbe achieved with no moving parts.The units have been tested both by Westermo and external test houses to meet EMC, isolation, vibration and shock standards, all to the highest levels suitable for heavy industrial, trackside and maritime environments.Network diagnostics are simplified with the inclusion of port mirroring on one port allowing data flow through the switch to be monitored using a network analyzer. All five ports can have data rate and flow control locked by DIP switch which can eliminateproblems with old legacy Ethernet equipment that is unable to support auto negotiation.6644-22407Interface specifications* Refer to Safety section.** T o minimise the risk of interference, a shielded cable is recommended when the cable is located inside 3 m boundary or the cable is longer than 30 m and inside 10 m boundary to the rails and connected to this port.86644-224096644-2240ConnectionsPower connectionNetworkfibre connectionLED indicatorsAvailable models:… SDW-541-F1G-T4G 10/100/1000Base-T/TX: 4 ports, 100/1000Base-FX: 1 port … SDW-550-T5G 10/100/1000Base-T/TX: 5 portsSDW-541-F1G-T4G SDW-550-T5G106644-22401234PowerThe SDW-500 series supports redundant power connection. The positive inputs are DC1 and DC2, the negative inputs for both supplies are –COM. The power is drawn from the input with the highest voltage.TXEthernet TX connection (RJ-45 connector), automatic MDI/MDI-X crossover.CAT 5 cable is recommended.Unshielded (UTP) or shielded (STP) connector might be used.87654321F1G, 1 SFP slotsThe F1G interface has one SFP slot supporting Ethernet 10/100/1000 BaseFX/X. Each slot can hold one SFP transceiver for copper or fibre cable. For supported transceivers see SFP transceivers user guide (art no. 6100-0000) available at www.westermo. com.DIP switch settings SDW-541-F1G-T4G and SDW 550-T5GDIP-switches are accessible under the lid on top of the unit. DIP-switches are used to configure the unit.Warning!discharging your body to a grounding point (e.g. use of wrist strap), before the lid on top/front of the unit is removed.Warning! Do not open connected equipment.Prevent access to hazardous voltages by disconnecting the unit from AC/DC mainssupply and all other electrical connections.NOTEWhen configuration via DIP-switches, the settings of DIP-switches configure the unit only after a reboot (power off/on).Observe this when the DIP-switches are configured… S peed and duplex setting only valid when auto-negotiation is disabled.… W hen monitoring selected all outgoing packets from the switch is also copied to the port 1.… S peed and duplex switch settings are ignored for FX ports.… I f auto-negotiation and auto MDI/MDI-X disabled all TX ports support MDI-X configuration.… I f Hub mode is selected, all incoming and outgoing packets are distributed on all other ports.ONLY VALID FOR SDW-541-F1G-T4G… S peed and duplex switch settings are ignored for FX ports.… I f auto-negotiation and auto MDI/MDI-X disabled all TX ports support MDI-X configuration.6644-224011126644-2240Port settings136644-2240G ig ab it T ra n sc00 seLED indicatorsLEDSFP T ransceiversThe unit supports Westermo labelled transceivers only.See Westermo's modular transceivers datasheets 100 Mbit and 1 Gbit for supportedSFP transceivers. See T ransceiver User Guide "6100-0000" for transceiver handlinginstructions.100 M b it TRe dF ox, L ynx se00 s er ie s146644-2240MountingCoolingThis unit uses convection cooling.T o avoid obstructing the airflow around the unit, use the following spacing rules. Minimum spacing 25 mm (1.0 inch) above / below and 10 mm (0.4 inches) left / right the unit. Spacing is recommended for the use of unit in full operating temperature range and service life.* S156644-2240REV . B 6644-2240 2016-02 Westermo T eleindustri AB, SwedenFor complete contact information, please visit our website at /contact or scan the QR codeChina********************* France*****************www.westermo.fr Germany****************www.westermo.deNorth America **************** Singapore******************.sg Sweden************************www.westermo.seUnited Kingdom *****************.uk Other OfficesSales UnitsWestermo Data Communications Westermo • SE-640 40 Stora Sundby, Sweden T el +46 16 42 80 00 Fax +46 16 42 80 01E-mail:*****************。
金贝尔智能锁说明书

金贝尔智能锁说明书
智能锁使用方法
首先,管理者密码设置,通常第一次设置的密码为管理者密码,具体以下步骤:操作步骤:1.打开电池盖; 2.按设置键一次响滴声;3.按启动键(位于键盘数
字3后面一位),输入密码(3-8位)按#键;4.响起滴声,操作成功。
其次,开门卡、密码、指纹锁、遥控设置,指纹锁生产厂家总结具体以下步骤:操作步骤:1.打开电池盖 2.按设置键一次. 3.按启动键,输入密码(3-8位)按#
键 4.按启动键,输入编号(00-99)按#键。
5.按启动键,输入开门(3-8位),按#号
键结束,密码设置成功。
需要用手指进行指纹的读取,滴声响后,要重复第二次。
等到出现相同的响声时,则代表录入成功,这时将要设置的卡靠近感应区,设置感应卡;按遥控器任意键,设置遥控器。
- 1、下载文档前请自行甄别文档内容的完整性,平台不提供额外的编辑、内容补充、找答案等附加服务。
- 2、"仅部分预览"的文档,不可在线预览部分如存在完整性等问题,可反馈申请退款(可完整预览的文档不适用该条件!)。
- 3、如文档侵犯您的权益,请联系客服反馈,我们会尽快为您处理(人工客服工作时间:9:00-18:30)。
S6000-LC8R-V1.5修改功能如下:
1.0.更改功能
1.1写序列号需要使用拨码开关第8位,当拨向ON状态,写序列号有效,否无效.
S6000-LC8R-V1.4修改功能如下:
1.0.拨码端子功能定义,新添加调试功能
1 0 0 0 8路继电器拨向ON:开;反之为关. ……
1 1 1 1 全部继电器拨向ON:开;反之为关.
注:CAN总线采用的是手拉手方式布线,终端电阻保证CAN总线可靠通信。
CAN总线终端电阻,只允许总线最远两端的控制器使用。
2.0.时间段自动控制
每个输出点(继电器,DALI镇流器,DALI组,DALI场景,DALI广播)可以设定由一个时间表自动控制。
每个输出点可关联一个时间表;
每个时间表最多可以自定义8个时间段;
每个时间段可具体定义一个星期7天和假日执行是否有效;
同时支持2张自定义的假日表.
上面为时间表的设置流程和执行流程,具体设置方法请看客户端软件操作说明。