聚合物成型工艺学复习提纲
《聚合物合成工艺学》期末复习资料
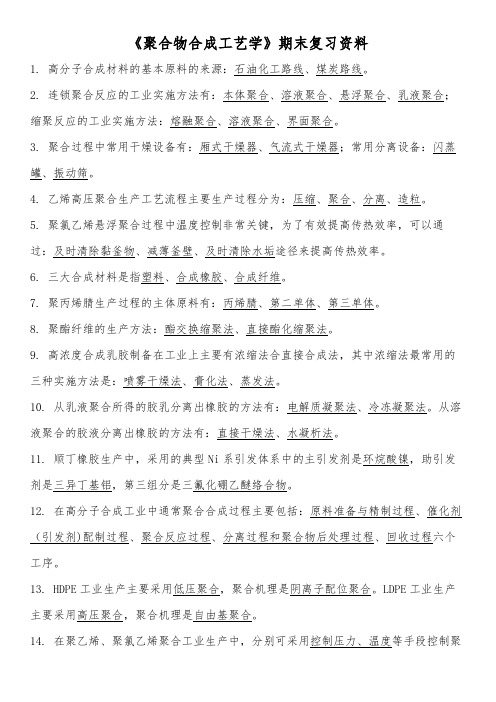
《聚合物合成工艺学》期末复习资料1. 高分子合成材料的基本原料的来源:石油化工路线、煤炭路线。
2. 连锁聚合反应的工业实施方法有:本体聚合、溶液聚合、悬浮聚合、乳液聚合;缩聚反应的工业实施方法:熔融聚合、溶液聚合、界面聚合。
3. 聚合过程中常用干燥设备有:厢式干燥器、气流式干燥器;常用分离设备:闪蒸罐、振动筛。
4. 乙烯高压聚合生产工艺流程主要生产过程分为:压缩、聚合、分离、造粒。
5. 聚氯乙烯悬浮聚合过程中温度控制非常关键,为了有效提高传热效率,可以通过:及时清除黏釜物、减薄釜壁、及时清除水垢途径来提高传热效率。
6. 三大合成材料是指塑料、合成橡胶、合成纤维。
7. 聚丙烯腈生产过程的主体原料有:丙烯腈、第二单体、第三单体。
8. 聚酯纤维的生产方法:酯交换缩聚法、直接酯化缩聚法。
9. 高浓度合成乳胶制备在工业上主要有浓缩法合直接合成法,其中浓缩法最常用的三种实施方法是:喷雾干燥法、膏化法、蒸发法。
10. 从乳液聚合所得的胶乳分离出橡胶的方法有:电解质凝聚法、冷冻凝聚法。
从溶液聚合的胶液分离出橡胶的方法有:直接干燥法、水凝析法。
11. 顺丁橡胶生产中,采用的典型Ni系引发体系中的主引发剂是环烷酸镍,助引发剂是三异丁基铝,第三组分是三氟化硼乙醚络合物。
12. 在高分子合成工业中通常聚合合成过程主要包括:原料准备与精制过程、催化剂(引发剂)配制过程、聚合反应过程、分离过程和聚合物后处理过程、回收过程六个工序。
13. HDPE工业生产主要采用低压聚合,聚合机理是阴离子配位聚合。
LDPE工业生产主要采用高压聚合,聚合机理是自由基聚合。
14. 在聚乙烯、聚氯乙烯聚合工业生产中,分别可采用控制压力、温度等手段控制聚合物分子量。
15. 丁苯橡胶生产过程中分子量分布和支链的多少主要与停留时间有关,工业上采用8~12台聚合釜串联方法,可使分子量分布窄和支链少。
1. 液体橡胶的定义:液体橡胶是一种在室温下为黏稠状流动性液体,经过适当化学反应可形成三维网状结构,从而获得和普通硫化胶具有类似的物理机械性能的低聚物。
聚合物成型加工基础 复习

聚合物成型加工基础复习
聚合物成型加工基础复习
[聚合物成型加工基础]复习
《聚合物成型加工基础》备考
高分子一次结构、二次结构、高分子三次结构
聚合物温度-应力曲线(图两张),tx、tg、tm、tf、td;聚合物的采用温度
非牛顿流体中,假塑性流体、胀塑性流体、宾汉流体的加工特性注射螺杆与挤出螺杆相比,结构上的差别
聚合物分子之间的作用力
交联与支化的高分子区别
对于结晶聚合物制品膨胀性
高聚物的粘性流动是怎样产生的
单螺杆挤出机的螺杆职能区分割
挤出成型过程中的能量来源
熔体运送理论中,熔体在螺槽中的几种流动
结构改进后的新型螺杆
压缩比,抽走口服螺杆的压缩比
注射成型中的背压、注射压力、锁模力等重要概念
热处理成型成型方法,热处理的必要条件
热塑性塑料的特点
增塑剂的促进作用及具备的效能
聚合物的结晶与取向;结晶聚合物的取向,取向聚合物的结晶非结晶聚合物和结晶聚合物的透明性
银纹与裂缝区别
聚合物熔体在挤出时的挤出胀大、不稳定流动,与分子量的关系。
筛板的作用。
如何消解或者集中制品的内应力
降解的概念以及如何避免
高分子聚合物与高分子物质在力学性质上的有何区别?
分子量和分子量分布对机械性能和成型加工性能的影响?影响挤出物胀大的因素?影响皮德盖段液态运送的原因?
什么是螺杆压缩比?确定压缩比的依据是什么?为什么要有压缩比?。
聚合物成型加工复习材料
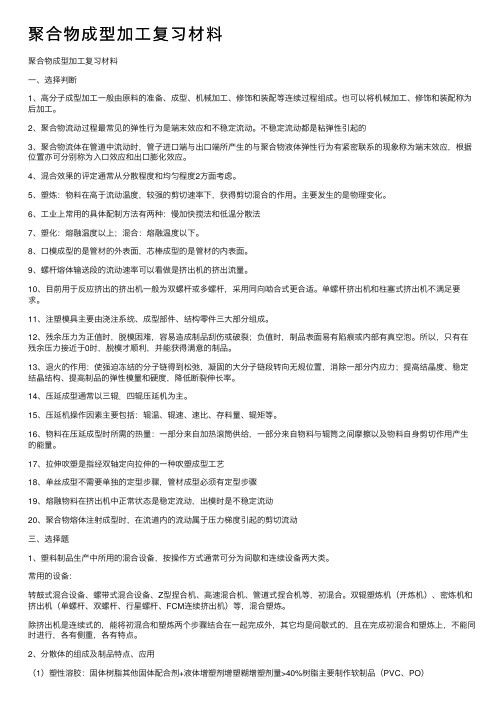
聚合物成型加⼯复习材料聚合物成型加⼯复习材料⼀、选择判断1、⾼分⼦成型加⼯⼀般由原料的准备、成型、机械加⼯、修饰和装配等连续过程组成。
也可以将机械加⼯、修饰和装配称为后加⼯。
2、聚合物流动过程最常见的弹性⾏为是端末效应和不稳定流动。
不稳定流动都是粘弹性引起的3、聚合物流体在管道中流动时,管⼦进⼝端与出⼝端所产⽣的与聚合物液体弹性⾏为有紧密联系的现象称为端末效应,根据位置亦可分别称为⼊⼝效应和出⼝膨化效应。
4、混合效果的评定通常从分散程度和均匀程度2⽅⾯考虑。
5、塑炼:物料在⾼于流动温度,较强的剪切速率下,获得剪切混合的作⽤。
主要发⽣的是物理变化。
6、⼯业上常⽤的具体配制⽅法有两种:慢加快搅法和低温分散法7、塑化:熔融温度以上;混合:熔融温度以下。
8、⼝模成型的是管材的外表⾯,芯棒成型的是管材的内表⾯。
9、螺杆熔体输送段的流动速率可以看做是挤出机的挤出流量。
10、⽬前⽤于反应挤出的挤出机⼀般为双螺杆或多螺杆,采⽤同向啮合式更合适。
单螺杆挤出机和柱塞式挤出机不满⾜要求。
11、注塑模具主要由浇注系统、成型部件、结构零件三⼤部分组成。
12、残余压⼒为正值时,脱模困难,容易造成制品刮伤或破裂;负值时,制品表⾯易有陷痕或内部有真空泡。
所以,只有在残余压⼒接近于0时,脱模才顺利,并能获得满意的制品。
13、退⽕的作⽤:使强迫冻结的分⼦链得到松弛,凝固的⼤分⼦链段转向⽆规位置,消除⼀部分内应⼒;提⾼结晶度、稳定结晶结构、提⾼制品的弹性模量和硬度,降低断裂伸长率。
14、压延成型通常以三辊.四辊压延机为主。
15、压延机操作因素主要包括:辊温、辊速、速⽐、存料量、辊矩等。
16、物料在压延成型时所需的热量:⼀部分来⾃加热滚筒供给,⼀部分来⾃物料与辊筒之间摩擦以及物料⾃⾝剪切作⽤产⽣的能量。
17、拉伸吹塑是指经双轴定向拉伸的⼀种吹塑成型⼯艺18、单丝成型不需要单独的定型步骤,管材成型必须有定型步骤19、熔融物料在挤出机中正常状态是稳定流动,出模时是不稳定流动20、聚合物熔体注射成型时,在流道内的流动属于压⼒梯度引起的剪切流动三、选择题1、塑料制品⽣产中所⽤的混合设备,按操作⽅式通常可分为间歇和连续设备两⼤类。
聚合物成型加工资料重点

背压:螺杆转动后退时螺杆顶部熔体物料所受到的压力,也 就是阻力。可由液压系统中的溢流阀来调节。
注射:当螺杆后退到碰到限位开关时,螺杆就停止运动。即 料筒前端物料达到一次注射量时,螺杆就停止后退,然后向前移 动,将塑料熔体推入模腔。
25-Oct-20
25 Dept. Polym. Sci. & Eng.,
的摩擦热,使料温升高,有利于塑料的混合与塑化。
25-Oct-20
22 Dept. Polym. Sci. & Eng.,
④螺杆
a.从作用上与挤出机螺杆相比
注射机螺杆除了送料、压实、塑化外,还有注射作用,对于塑 化能力、压力稳定以及操作连续性和对操作稳定性的要求没有挤出 机螺杆的高。
b.从螺杆运动形式比较
旋转式: 模具是安放在可旋转的转盘上的。 优点是适合成型大批量小制品,生产周期短。 缺点是结构复杂,锁模力不高。
25-Oct-20
13 Dept. Polym. Sci. & Eng.,
根据排列方式不同分类:卧式、立式、角式
25-Oct-20
14 Dept. Polym. Sci. & Eng.,
25-Oct-20
8 Dept. Polym. Sci. & Eng.,
25-Oct-20
9 Dept. Polym. Sci. & Eng.,
二.注射成型的特点
1.生产周期短,自动化程度高,因此生产效率高;
2.适应性强,几乎所有的热塑性塑料都可用这种方法成型,一 些厂家还用此法成型热固性塑料;
25-Oct-20
3 Dept. Polym. Sci. & Eng.,
6.1 概述
一.注射过程 注射过程是 三个条件:热量、压力、时间 三个要素:模塑材料、注射机、注射模
聚合物加工工艺学考试要点

1、熔体破裂:剪切速率超过某一临界值后,随剪切速率的继续增大,挤出物的外观依次出现表面粗糙、尺寸周期性起伏,直到破裂成碎块等种种畸变现象。
2、塑化:通过热能和机械能使热塑性塑料软化并赋予可塑性的过程。
3、假塑性流体:粘度随剪切速率的增大而降低的流体。
4、固化:指物质从低分子变为高分子的过程。
5、增塑剂:添加到线型高聚物中使其塑性增大的物质(高沸点、低挥发性)。
6、材料:是具有一定的性能,可用于制作有用物品的物质。
一般指固体。
7、高分子材料成型加工:高分子材料(由高分子化合物和添加剂组成)是通过成型加工工艺得到具有实用性的材料或制品过程的工程技术。
1、高分子材料的定义和分类?(1)定义:以高分子化合物为基础的材料。
是由相对分子质量较高的化合物构成的材料。
(2)分类:橡胶、塑料、纤维、涂料、胶粘剂和高分子基复合材料。
2、交联能影响高分子材料的哪些性能?哪些材料或产品是经过交联的?(1)力学性能、耐热性能、化学稳定性、使用性能。
(2)PF、UF、MF、EP、UP、硫化橡胶、(PE、PVC、PU等泡沫塑料)3、聚合物成型过程中为什么会发生取向?形式有哪几种?取向对高分子材料制品的性能有何影响?(1)聚合物在成型加工时,受到剪切和拉伸力的作用,聚合物分子链和结构单元按特定方向排列,发生取向。
(2)分为流动取向和拉伸取向。
(3)影响:高分子材料经取向后,拉伸强度、冲击强度、透气性等增加。
单轴拉伸时,取向方向的强度增加,垂直于取向方向的强度减少。
结晶聚合物拉伸取向后,结晶度增加,玻璃化温度上升。
4、高分子材料中添加助剂的目的是什么?改善高分子材料的成型加工性能,提高其制品的使用性能,赋予某些特殊的功能性或者降低产品成本。
5、试述增塑剂的作用机理?增塑剂分子插进聚合物分子链之间,削弱了聚合物分子链间的应力,结果增加了聚合物分子链的移动性、降低了聚合物分子链的结晶度,从而使聚合物的塑性增加,也就是对抗塑化作用的主要因素聚合物分子链间的应力和聚合物的分子链的结晶度,而他们则取决于聚合物的化学机构和物理结构。
聚合物合成工艺学 复习重点

1、简述四种自由基聚合生产工艺的定义及他们的特点和优缺点?本体聚合(又称块状聚合):在不用其它反应介质情况下,单体中加有少量或不加引发剂发生聚合的方法。
可分为均相本体聚合非均相本体聚。
均相本体聚合指生成的聚合物溶于单体(如苯乙烯、甲基丙烯酸甲酯)。
非均相本体聚合指生成的聚合物不溶解在单体中,沉淀出来成为新的一相(如氯乙烯)。
特点:产品纯净,电性能好,可直接进行浇铸成型;生产设备利用率高,操作简单,不需要复杂的分离、提纯操作优点:(1)本体聚合是四种方法中最简单的方法,无反应介质,产物纯净,适合制造透明性好的板材和型材。
(2) 后处理过程简单,可以省去复杂的分离回收等操作过程,生产工艺简单,流程短,所以生产设备也少,是一种经济的聚合方法。
(3) 反应器有效反应容积大,生产能力大,易于连续化,生产成本比较低。
缺点:(1) 放热量大,反应热排除困难,不易保持一定的反应温度(2) 单体是气或液态,易流动。
聚合反应发生以后,生成的聚合物如溶于单体则形成粘稠溶液,聚合程度越深入,物料越稠,甚至在常温下会成为固体。
(3) 任何一种单体转化为聚合物时都伴随有体积的收缩。
(4)聚合物粒子的形态和结构(均相聚合过程得到的粒子是一些外表光滑、大小均匀、内部为实心及透明有光泽的小圆珠球。
非均相聚合过程所生成的产物则不同,聚合物粒子是不透明的,外表比较粗糙,内部有一些孔隙)。
悬浮聚合:将单体在强烈机械搅拌及分散剂的作用下分散、悬浮于水相当中,同时经引发剂引发聚合的方法。
优点:(1)以水为分散介质,价廉、不需要回收、安全、易分离。
(2)悬浮聚合体系粘度低、温度易控制、产品质量稳定。
(3)由于没有向溶剂的链转移反应,其产物相对分子质量一般比溶液聚合物高。
(4)与乳液聚合相比,悬浮聚合物上吸附的分散剂量少,有些还容易脱除,产物杂质较少。
(5)颗粒形态较大,可以制成不同粒径的颗粒粒子。
聚合物颗粒直径一般在0.05-0.2mm,有些可达0.4 mm,甚至超过1mm。
高分子材料成型加工基础复习提纲 高分子材料成型加工基础复习

高分子材料成型加工基础复习提纲绪论及第一章:混合与混炼1、聚合物加工:高聚物的成型加工,通常是在一定的温度下使弹性固体、固体粉状或粒状、糊状或溶液状态的高分子化合物变性或熔融,经过模具或口型流道的压塑,形成所需的形状,在形状形成的过程中有的材料会发生化学变化(如交联,最终得到能保持所取得形状的制品的工艺过程。
P52、聚合物的加工工艺过程一般可以分为混炼、成型、后加工等三大部分。
P53、混合混炼的目的:为获得综合性能优异的聚合物材料,除继续研制合成新型聚合物外,通过混合、混炼方法对聚合物的共混改性已成为发展聚合物材料的一种卓有成效的途径。
P74、共混的方法:a 机械共混法 b 液体共混法 c 共聚—共混法 d 互穿网络聚合物IPN 制备技术P75、共聚物的均匀性是指被分散的物在共混体中浓度分布的均一性,或者说分散相浓度分布的变化大小。
6、共聚物的分散程度是指被分散的物质(如橡胶中掺混部分塑料)破碎程度如何,或者说分散相在共混体中的破碎程度。
P117、常见的共混体系有:a固体 / 固体混合、b液体 / 液体混合、c固体 / 液体混合。
P208、混炼三要素及其作用:a压缩;物料在承受剪切前先经受压缩,使物料的密度增加,这样剪切时,剪切力作用大,可提高剪切效率,同时当物料被压缩时,物料内部会发生流动,产生由于压缩引起的流动剪切 b剪切剪切的作用是把高粘度分散相的粒子或凝聚体分散于其它的分散介质中 c分配置换分布由置换来完成。
P229、混合与混炼设备根据操作方式分为间歇式和连续式两大类。
P2510、常见初混合设备概念及类型:初混合设备是指物料在非熔融状态下(粉料、粒料、液体添加剂)进行混合所用的设备。
常用的典型初混合设备有 a 转鼓式混合机 b 螺带混合机 c Z 型捏合机 d 高速混合机p25-2811、混炼和塑化的概念及它们的区别:将各种配合剂混入并均匀分散在橡胶中的过程叫混炼;将各种配合剂混入并均匀分散在塑料熔体中的过程叫塑化。
聚合物成型工艺学复习提纲(重点)

聚合物成型工艺学复习提纲第二章 聚合物成型的理论基础1、非牛顿流体的类型和特征由黏度分a 宾哈流体:这种流体与牛顿流体相同,其剪切应力和剪切速率的关系表现为直线。
不同的是它的流动只有当剪切应力高至一定值τy 后才发生塑性流动b 假塑性流体:它所表现的流动曲线是非直线的,但并不存在屈服应力。
流体的表观粘度随剪切应力的增加而降低。
大多数聚合物的熔体,也是塑料成型中处理最多的一类物料,以及所有聚合物在良溶剂中的溶液,其流动行为都具有假塑性流体的特征。
c 膨胀性液体(高固含量的悬浮液) 这种流体的流动曲线也不是直线,而且也不存在屈服应力,但与假塑性流体不同的是它的表现粘度会随剪切应力的增加而上升。
由时间依赖性这一系统的流体,其剪切速率不仅与所施加的剪切应力的大小有关,而且还依赖于应力施加时间的长短。
当所施加的应力不变时,这种流体在恒温下的表观粘度会随着所施加应力的持续时间而逐渐上升或下降,上升或下降到一定值后达到平衡不再变化。
这种变化是可逆的,因为流体中的粒子或分子并没有发生永久性的变化。
a 摇溶性(或触变性)流体:表观粘度随剪切应力持续时间下降的流体。
如:涂料、油墨。
b 震凝性流体:表观粘度随剪切应力持续时间上升的流体。
如:石膏水溶液。
3、聚合物熔体的黏度的影响因素对流体粘度起作用的因素有温度、压力、施加的应力和应变速度等。
温度:0()0a T T e -η=η聚合物分子链刚性越大和分子间的引力越大时,表现粘度对温度的敏感性也越大。
但这不是很肯定的结论,因为敏感程度还与聚合物相对分子质量和相对分子质量分布有关 表现粘度对温度的敏感性一般比它对剪切应力或剪切速率要强些。
压力:由于液体的剪切粘度(包括表观粘度下同)依赖于分子间的作用力,而作用力又与分子间的距离有关,因此当液体受有压力而达到减小分子间距离时,分子间作用力增大,黏度增大。
假塑性流体的粘度随剪切应力或剪切速率的增加而下降4、符合指数定律流体在圆形流道中的流动方程(推导流量、压力、几何参数之间的关系)剪切应力和真正剪切速率之间应存在如式所示的关系 m k drdv τ=- 规定圆管的半径为R ,管长为L ,于是在任意半径r 处所受剪切应力即为 L RP 2=τ 将上述两式合并求其积分,得液体在任意半径处的流速v r 为:⎪⎪⎭⎫ ⎝⎛+-⎪⎭⎫ ⎝⎛=++1211m r R L P k v m m mr 液体在管中的体积流速q 为: dr rv q r Rπ⎰=02 ⎪⎪⎭⎫ ⎝⎛+⎪⎭⎫ ⎝⎛=∴+323m R L P k q m mπ 如果m=1 为牛顿流体424⋅=L pR k q π 442pR L q k π=◆ 5、符合指数定律流体在狭缝( h/w>20)流道中的流动方程(推导)m k dydv τ=- 离中心线为y 处而与中心层平行的流层所受的剪切应力即为:y Lp =τ 积分得⎥⎥⎦⎤⎢⎢⎣⎡-⎪⎭⎫ ⎝⎛⎪⎭⎫ ⎝⎛+⎪⎭⎫ ⎝⎛=++11211m m m y y h m L p k v 体积流速:dy Wv q hy ⎰=22 ()2212+⎪⎭⎫ ⎝⎛=++m h L p kW q m m m◆ 6、聚合物成型的流动缺陷的种类及产生的原因(1.管壁上的滑移塑料熔体在高剪切应力下的流动并非如此,贴近管壁处的一层流体会发生间断的流动。
- 1、下载文档前请自行甄别文档内容的完整性,平台不提供额外的编辑、内容补充、找答案等附加服务。
- 2、"仅部分预览"的文档,不可在线预览部分如存在完整性等问题,可反馈申请退款(可完整预览的文档不适用该条件!)。
- 3、如文档侵犯您的权益,请联系客服反馈,我们会尽快为您处理(人工客服工作时间:9:00-18:30)。
聚合物成型工艺复习题1、非牛顿流体的类型和特征?答:(1)粘性系统在受到外力作用而发生流动时的特性是:其剪切速率只依赖于所施加剪切应力的大小。
根据其剪切应力和剪切速率的关系。
又可分为宾哈(汉)流体、假塑性流体和膨胀性流体三种。
特征:<1>宾哈流体:与牛顿流体相比,剪切应力与剪切速率之间也呈线性关系。
但此直线的起始点存在屈服应力τу,只有当剪切应力高于τу时,宾哈流体才开始流动。
宾哈流体因流动而产生的形变完全不能恢复而作为永久变形保存下来,即这种流动变形具有典型塑性形变的特征,故又常将宾哈流体称为塑性流体。
<2>假塑性流体:非牛顿流体中最为普通的一种。
流动曲线不是直线,而是一条斜率先迅速变大而后又逐渐变小的曲线,而且不存在屈服应力。
流体的表观粘度随剪切应力的增加而降低。
即:剪切变稀。
<3>膨胀性流体:流动曲线非直线的,斜率先逐渐变小而后又逐渐变大的曲线,也不存在屈服应力。
表观粘度会随剪切应力的增加而上升。
即:剪切变稠。
(2)有时间依赖性的系统:这类液体的流变特征除与剪切速率与剪切应力的大小有关外,还与施加应力的时间长短有关,即在恒温、恒剪切力作用下,表观粘度随所施应力持续时间而变化(增大或减小,前者为震凝液体,后者为触变性液体),直至达到平衡为止。
特征:<1>摇溶性(或触变性)流体:表观粘度随剪切应力持续时间下降的流体。
如:涂料、油墨。
<2>震凝性流体:表观粘度随剪切应力持续时间上升的流体。
如:石膏水溶液。
3、聚合物熔体的黏度的影响因素?答:在给定剪切速率下,聚合物的粘度主要取决于实现分子位移和链段协同跃迁的能力(大分子长链之间的缠结解开)以及在跃迁链段的周围是否有可以接纳它跃入的空间(自由体积)两个因素,凡能引起链段跃迁能力和自由体积增加的因素,都能导致聚合物熔体粘度下降。
自由体积:自由体积大,分子间距就大,分子间作用力小,大分子链段容易活动,聚合物粘度小。
因此凡能引起自由体积增大的因素都能使聚合物粘度降低。
大分子长链之间的缠结:它使分子链运动变得非常困难。
分子间缠结程度大,分子间作用力增大,大分子形成网络,分子不容易活动,聚合熔体粘度就大。
因此凡能减小缠结作用的因素都能使熔体粘度降低。
主要影响因素:(1)温度对剪切粘度的影响:对于处于粘流温度以上的聚合物,很多研究结果表明:热塑性聚合物熔体的粘度随温度升高而呈指数函数的方式降低。
(2)压力对剪切粘度的影响:聚合物在高压下体积收缩,自由体积减小,分子间距离缩短,链段活动范围减小,分子间作用力增大,粘度增大。
(3)聚合物的结构因素和组成对粘度的影响:<1>分子结构:①链的刚柔性:链的柔性越大,缠结点越多,链的解缠和滑移越困难,聚合物流动时非牛顿性越强,对剪切速率越敏感。
链的刚性增加和分子间吸引力越大,熔体粘度对温度的敏感性越大,提高加工温度有利于增大流动性。
②支链:a.短支链:相同分子量时,η短支链〈η无支链,自由体积↑,η↓;b.长支链:相同分子量时,η无支链〈η长支链,长链与周围分子缠结成网,η↑。
另外长支链对剪切速率敏感;c.含有较大侧基的聚合物对压力、温度比较敏感。
<2>分子量与分子量分布:①平均分子量大,粘度随分子量增加而增加。
②粘度与分子量分布有关,一般在平均分子量相同时,熔体的粘度随分子量分布增宽而迅速下降,其流动行为表现出更多的非牛顿性。
<3>组成对粘度的影响:填充剂、着色剂、润滑剂、溶剂、增塑剂、稀释剂、稳定剂等添加剂在不同程度上会影响塑料的流变行为。
6、聚合物成型的流动缺陷的种类及产生的原因?答:(1)管壁上的滑移:滑移产生原因:1剪切速率的径向不均匀分布(靠管壁附近剪切速率最大);2流动中出现分级效应(即相对分子质量低的级分较多地集中在管壁附近);3管壁附近的弹性形变的不均匀性(管壁处弹性形变大)。
(2)端末效应::不管是那种截面流道的流动方程,都只能用于稳态流动的流体,但总有不稳态流动。
(包括入口效应和离模膨胀)末端效应产生原因:1入口效应:1>.物料从料筒进入口模时由于熔体粘滞流动,流线在入口处产生收敛所引起的能量损失;2>.在入口处由于聚合物熔体产生弹性变形,因弹性能的贮蓄所造成的能量损失;3>.熔体流经入口时,由于剪切速率的剧烈增加所引起的速度的激烈变化,为达到流速分布所造成的。
2离模膨胀:1>取向效应:聚合物熔体流动期间处于高剪切场内,其大分子在流动方向取向,但在口模处发生解取向。
2>记忆效应:当聚合物熔体由大直径的料筒进入小直径的口模时,产生了弹性形变,而熔体离开口模时,弹性变形获得恢复。
3>正应力效应:由于粘弹性流体的剪切变形,在垂直于剪切方向上引起了正应力的作用。
(3)弹性对层流的干扰:1塑料熔体在成型过程中的雷诺准数通常均小于10,故不应出现湍流。
2塑料熔体的可逆弹性形变的回复引起湍流。
3弹性湍流对塑料熔体的剪切流动来说,只有当γR的值超过4.5-5时才会发生。
(4)“鲨鱼皮”症:产生原因:挤压口模对挤出物表面所产生的周期性的张力和流体在管壁上的滑移(时粘时结的间断性流动)的结果。
(5)熔体破裂:产生原因:熔体在导管(流道)内流动时,各点所受应力作用的经历不尽相同,因此在离开导管后所出现的弹性恢复就不可能一致,如果弹性恢复的力不为熔体强度所容忍,则挤出物就会出现表面毛糙、螺旋型的大规则性、细微而密集的裂痕,一致成块地断裂。
9、结晶度和性能之间的关系?答::结晶态聚合物抵抗形变的能力优于非晶态下的同一聚合物。
结晶度高的优于低的。
绝大多数结晶聚合物,在其Tg~Tm之间,出现屈服点。
12、成型操作过程中,仅凭增加温度来增加流动性,是否适合于任何聚合物?答:不是,用升高温度增加流动性,只适用于对粘度的温度敏感性大的聚合物,即刚性聚合物,而不适合于对温度敏感性较小的热塑性聚合物。
17、同种聚合物结晶度的变化如何影响熔点、弹性模量、密度、透明度?答:结晶度增加熔点上升、弹性模量增加、密度增加、透明度降低1、聚合物成型用物料的形态类型?答:•粉料:主要用于双螺杆挤出机的挤出成型,压延成型,滚塑。
•粒料:主要用于单螺杆挤出机的挤出成型,注射成型。
•分散体:主要用于涂覆成型,搪塑。
•溶液:主要用于流涎成型,浇铸成型。
2、成型用粉料与粒料的组成?答:由聚合物和助剂两类物质组成,聚合物为主要成分。
聚合物助剂:助剂是为了使复合物或制品具有某种特性所加入的物质。
常用的助剂有:增塑剂、稳定剂、填充剂、增强剂、着色剂、润滑剂、防静电剂、防火剂、防静电剂等二十多类。
3、增塑剂的作用机理和种类?答:(1)作用机理:聚合物分子链常会以次价键力而彼此形成聚合物-聚合物联结点,从而使聚合物具有刚性,这些联结点在分子热运动中会解而复结的,但是在一定温度下,联结点的数目却相对稳定,所以是一种动平衡。
加入增塑剂后,增塑剂的分子因溶剂化及偶极力等作用而“插入”聚合物分子之间并与聚合物分子的活性中心发生时解时结的联结点。
这种联结点也处于一种动平衡。
但是聚合物-增塑剂联结点会使聚合物原有的联结点减少,从而使分子间的力减弱,导致聚合物材料性能改变。
(2)种类:1按化学组成分为:邻苯二甲基酸酯、脂肪族二元酸酯、石油磺酸苯酯、磷酸酯、环氧化合物、含氯化合物等。
2按相容性分为:主增塑剂和次增塑剂。
3按结构分为:单体型和聚合体型。
4按用途分为:耐热、耐寒、电绝缘等增塑剂。
4、内外润滑剂的作用机理和种类?答:(1)作用机理:<1>内润滑剂:内润滑剂与聚合物有一定的相容性,加入后可减少聚合物分子间的内聚力,降低其熔体粘度,减少聚合物分子间的内摩擦;如硬脂酸及其盐类。
<2>外润滑剂:外润滑剂与聚合物仅有很低的相容性,故能保留在聚合物的表面,降低塑料与设备的摩擦。
石蜡、矿物油、硅油等。
(2)种类:脂肪酸及其皂类、脂肪酸酯类、脂肪醇类、酰胺类、石蜡、低分子量PE、合成蜡、丙烯酸酯类、某些有机硅化合物。
5、稳定剂的类型?答:按所发挥的作用分热稳定剂、光稳定剂、及抗氧剂等。
6、润性物料的混合方法?答:润性物料:树脂→增塑剂→稳定剂→其它助剂投料。
对于润性物料(加入相当数量的液态助剂如增塑剂),增塑剂需事先预热,强化传热过程,加速扩散速率,使聚合物加速溶胀,以提高混合效率。
10、混合作用的机理?答:混合一般是靠扩散、对流、剪切三种作用来完成的。
(1)扩散:利用物料各组分的浓度差,推动构成各组分的微粒,从浓度较大的区域中向较小的区域迁移,以达到组成均一。
(2)对流:靠各组分在外界因素下向其它组分所占空间流动,达到各组分在空间上的均匀分布(主要手段为机械搅拌)。
(3)剪切:依靠机械的作用产生的剪切力,促使物料组分均一的混合过程。
1、热固性塑料的模压过程?答:加热加压,熔融流动,充模,交联固化,开模取出制品。
2、为何要进行预压和预热?答:(1)预压原因:主要是针对压缩模塑周期长、效率低的特点而采取的措施。
(2)预热原因:为提高制品质量和便于模压进行,须预热4、简述聚四氟乙烯的烧结过程?答:(1)升温阶段:将型坯由室温加热至烧结温度。
聚四氟乙烯的传热性能差,加热应按一定的升温速率进行。
(2)保温:将达到烧结温度的型坯在该温度下保持一段时间使其完全“烧透”的过程。
(3)冷却:将已经烧结好的成型物从烧结温度降到室温的过程。
(4)成品检验和后加工。
1、挤出工艺及其特点?答:(1)定义:也称挤压模塑或挤塑,即借助螺杆或柱塞的挤压作用,使受热熔化的塑料在压力推动下,强行通过口模而成为具有恒定截面的连续型材的一种成型方法。
(2)特点:1挤出成型生产工艺分干法和湿法;2挤出过程分连续和间歇式挤出;3挤出成型工艺控制参数除与挤出温度、压力、速率有关外,挤出机结构参数、冷却、牵引等控制因素都会影响制品的质量;4挤出机因机头及辅机不同,可生产多种产品;5挤出成型工艺按用途可分为:挤出制品成型和成型用原料配制。
2、单螺杆挤出机的基本结构?3、挤出螺杆的主要参数?答:表示螺杆结构特征的基本参数有直径、长径比、各段长度比例以及螺槽深度等,对螺杆的工作特性均有重大的影响。
(1)螺杆直径(D):根据所制制品的形状、大小及需要的生产率来决定的。
一般45~150mm,螺杆直径增大,加工能力提高,挤出机的生产率与螺杆直径D的平方成正比。
(2)长径比(L/D):螺杆工作部分有效长度与直径之比。
通常为18~25,目前以25居多。
1L/D大,能改善物料温度分布,有利于塑料的混合和塑化,并能减少漏流和逆流,提高挤出机的生产能力。
2L/D大,螺杆适应能力强,能用于多种塑料的挤出。
3但L/D过大,使塑料受热时间增长而降解;螺杆自重增加,自由端挠曲下垂,引起料筒与螺杆间擦伤,使制造加工困难,增大功率消耗。