先进过程控制系统软件
先进控制系统介绍
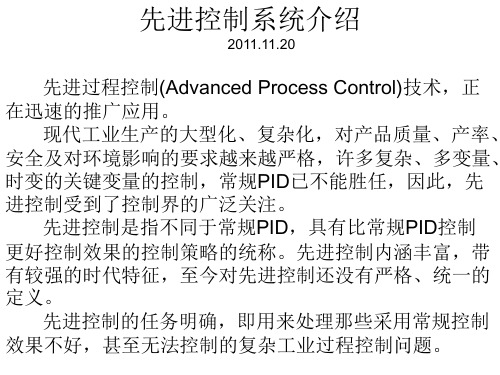
如图8-1所示为软测量结构图,表明在软测量中各模 块之间的关系。
图8-1软测量结构图
软测量的核心是建立工业对象的精确可靠的模型。 软测量初始模型是对过程变量的历史数据进行辨识。 现场测量数据中可能含有随机误差甚至显著误差,须经 数据变换和数据校正等预处理,才能用于软测量建模或 作为软测量模型的输入。软测量模型的输出就是软测量 对象的实时估计值。
8.3解耦控制 8.3.1耦合现象影响及分析
在一个生产装置中,往往需要设置若干个控 制回路,来稳定各个被控变量。在这种情况下, 多个控制回路之间就有可能存在某种程度的相互 耦合,这样的相互耦合可能妨碍各被控变量之间 的独立控制,甚至会破坏各系统的正常工作。
图8-3所示精馏塔温度控制是典型的耦合实例。
(2)整定控制器参数,减小系统关联
具体实现方法:通过整定控制器参数,把两个回路 中次要系统的比例度和积分时间放大,使它受到干扰作 用后,反应适当缓慢一些,调节过程长一些,这样可达 到减少关联的目的。 在采用这种方法时,次要被控变量的控制品质往往 较差,这一点在工艺允许的情况下是值得牺牲的,但在 另外一些情况下却可能是个严重缺点。
8.2时滞补偿控制
控制通道不同程度存在纯滞后(时滞)。例如,热交换 器载热介质(流量)对出口温度影响滞后一段时间;反应 器、管道混合、皮带传送及分析仪表测量流体成分等都 存在纯滞后。纯滞后存在,使被控变量不能及时反映扰 动影响,即使执行器接收信号后立即动作,也需经过纯 滞后时间,才能作用于被控变量。 衡量纯滞后常采用纯滞后时间τ和时间常数T之比。 当τ/T<0.3,是一般纯滞后过程;当τ/T>0.3,为大纯 滞后过程。一般纯滞后可采用常规控制,而当纯滞后较 大时,则用常规控制往往较难奏效。 大纯滞后过程较难控制,目前已有一些可行控制方 案,Smith预估补偿控制就是一种较好的控制方案。
SIMATIC_PCS_7过程控制系统
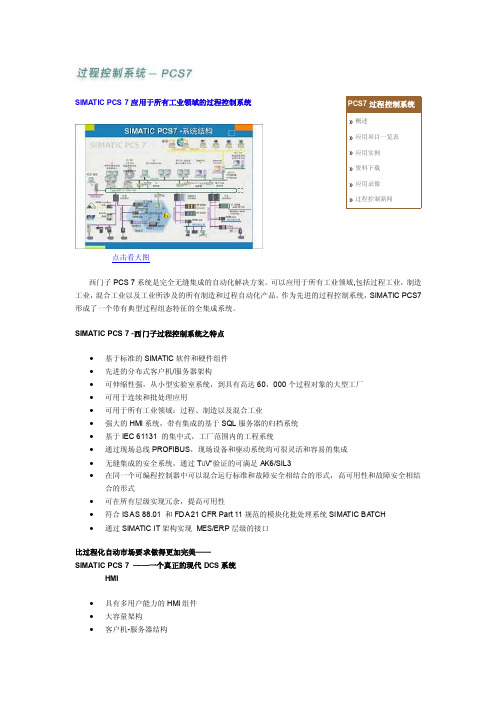
SIMA TIC PCS 7应用于所有工业领域的过程控制系统点击看大图西门子PCS 7系统是完全无缝集成的自动化解决方案。
可以应用于所有工业领域,包括过程工业,制造工业,混合工业以及工业所涉及的所有制造和过程自动化产品。
作为先进的过程控制系统,SIMATIC PCS7 形成了一个带有典型过程组态特征的全集成系统。
SIMATIC PCS 7 -西门子过程控制系统之特点∙基于标准的SIMATIC软件和硬件组件∙先进的分布式客户机/服务器架构∙可伸缩性强,从小型实验室系统,到具有高达60,000个过程对象的大型工厂∙可用于连续和批处理应用∙可用于所有工业领域:过程、制造以及混合工业∙强大的HMI系统,带有集成的基于SQL服务器的归档系统∙基于IEC 61131 的集中式,工厂范围内的工程系统∙通过现场总线PROFIBUS,现场设备和驱动系统均可很灵活和容易的集成∙无缝集成的安全系统,通过TüV*验证的可满足AK6/SIL3∙在同一个可编程控制器中可以混合运行标准和故障安全相结合的形式,高可用性和故障安全相结合的形式∙可在所有层级实现冗余,提高可用性∙符合ISA S 88.01 和FDA 21 CFR Part 11规范的模块化批处理系统SIMA TIC BA TCH∙通过SIMATIC IT架构实现MES/ERP层级的接口比过程化自动市场要求做得更加完美——SIMATIC PCS 7 ——一个真正的现代DCS系统HMI∙具有多用户能力的HMI组件∙大容量架构∙客户机-服务器结构∙冗余∙在线修改AS, I/O 模块, I/O∙热插拔(运行中插入和拔出模块)∙运行中可进行扩展/ 修改∙用于危险区域的I/O 模块∙冗余(控制器、模块和PROFIBUS)∙集成的故障安全技术∙智能现场设备/驱动设备的集成通讯∙快速以太网和PROFIBUS DP/PA∙光纤交换技术∙冗余(系统总线和现场总线)∙在线扩展工程∙集中式工程工具,简单易用,通用操作∙批量工程,具有导入/导出功能∙应用图形化和面向PLT的工具进行全面、有效的工程∙集成的SIMATIC PDM软件对智能现场设备进行集中参数化∙软件模拟和测试∙修改跟踪功能∙分布式、并行工程功能Batch∙配方与单元和设备无关∙层级配方,符合ISA S88.01∙从小型工厂到超大型工厂,灵活伸缩-单用户系统或客户机-服务器结构∙冗余性∙符合21 CFR Part 11 规范,查账索引,路径保护,电子签名∙紧密集成在HMI和工程系统中产品部门:AS 所属行业:城市工业水处理工程来源:SIAS工程概述:该工程设计规模为日处理污水50万吨, 主要收集某市区的城市污水及某县极大部分的工业废水和生活污水。
MES对过程控制系统(PCS)的数据采集
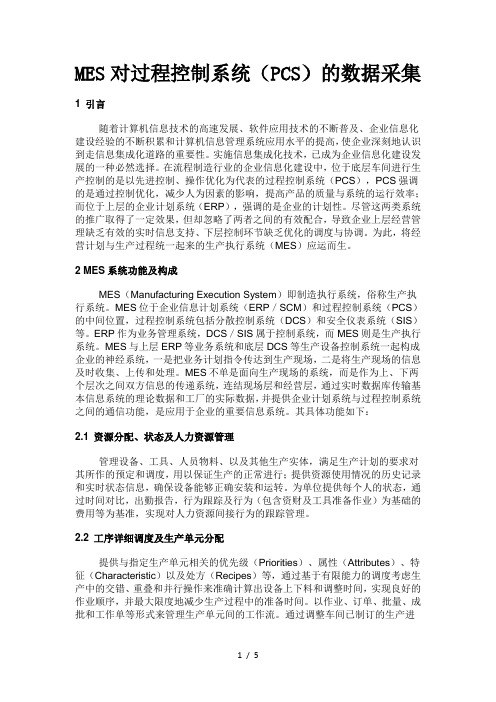
MES对过程控制系统(PCS)的数据采集1 引言随着计算机信息技术的高速发展、软件应用技术的不断普及、企业信息化建设经验的不断积累和计算机信息管理系统应用水平的提高,使企业深刻地认识到走信息集成化道路的重要性。
实施信息集成化技术,已成为企业信息化建设发展的一种必然选择。
在流程制造行业的企业信息化建设中,位于底层车间进行生产控制的是以先进控制、操作优化为代表的过程控制系统(PCS),PCS强调的是通过控制优化,减少人为因素的影响,提高产品的质量与系统的运行效率;而位于上层的企业计划系统(ERP),强调的是企业的计划性。
尽管这两类系统的推广取得了一定效果,但却忽略了两者之间的有效配合,导致企业上层经营管理缺乏有效的实时信息支持、下层控制环节缺乏优化的调度与协调。
为此,将经营计划与生产过程统一起来的生产执行系统(MES)应运而生。
2 MES系统功能及构成MES(Manufacturing Execution System)即制造执行系统,俗称生产执行系统。
MES位于企业信息计划系统(ERP/SCM)和过程控制系统(PCS)的中间位置,过程控制系统包括分散控制系统(DCS)和安全仪表系统(SIS)等。
ERP作为业务管理系统,DCS/SIS属于控制系统,而MES则是生产执行系统。
MES与上层ERP等业务系统和底层DCS等生产设备控制系统一起构成企业的神经系统,一是把业务计划指令传达到生产现场,二是将生产现场的信息及时收集、上传和处理。
MES不单是面向生产现场的系统,而是作为上、下两个层次之间双方信息的传递系统,连结现场层和经营层,通过实时数据库传输基本信息系统的理论数据和工厂的实际数据,并提供企业计划系统与过程控制系统之间的通信功能,是应用于企业的重要信息系统。
其具体功能如下:2.1 资源分配、状态及人力资源管理管理设备、工具、人员物料、以及其他生产实体,满足生产计划的要求对其所作的预定和调度,用以保证生产的正常进行;提供资源使用情况的历史记录和实时状态信息,确保设备能够正确安装和运转。
艾默生简介

DeltaV 由艾默生过程控制有限公司于1996年推出的用于过程控制的软件。
DeltaV 系统提供强大易用的设计和操作过程控制软件。
DeltaV 采用标准Windows特征来提供熟悉的用户界面。
最新版本为DeltaV10.4,在各种DCS中市场占有率第一,且其系统在国际上非常流行,与全球知名石油化工企业有着广泛的合作。
DeltaV 包括以下应用:1先进控制Advanced control:InSight监察识别;Neural神经网络;redict预测控制;redictPro专家预测控制;SimulatePro仿真专家;Tune with Insight应用识别整定;2 工程应用;3设置与安装;4操作员应用;5批量应用;6DeltaV自学引导;DeltaV系统不但拥有BPCS而且拥有集成的SIS。
DeltaV系统只在v4和v8中出现过汉化版,但汉化的内容也只限于帮助手册Books Online和操作界面Operator Interface,其它的应用程序以及产品手册(Product Data Sheet)和帮助说明,白皮书等都是英文的。
有些用语也非常难以翻译,找不到中文恰当的说法,例如Decommission a controller,各位如有读过DeltaV的中文手册,就会发现这样的问题不在少数。
在此建议各位最好还是使用英文版,好在自控专业文章对英文的要求并不高,这样也可以提高各位的英文阅读水平。
如果有机会合Emerson的工程师交流,使用英文(至少使用英文术语)也可以减少对DeltaV系统理解的歧义。
至于DeltaV系统的功能,Web发布确实很差,这是因为该功能的用户较少,所以功能上几乎没有改进。
不过自2002年DeltaV v7.2后DeltaV迁移到了WinXP和Win Server 2003平台上,利用Windows的Terminal Serveice所形成的DeltaV Remote Client功能更为强大且使用方便,Web发布已没有太多的意义。
DCS简介

DCS简介
一、DCS的概念
DCS是英文(Distributed Control System)的缩写,在国内自动控制行业又称之为集散控制系统。
DCS是计算机技术、控制技术和网络技术高度结合的产物,是目前最先进、最合理的过程控制系统,可以适应各种过程控制的要求。
系统具有很高的可靠性。
它通过集中的操作和监控,管理分散的受控点,所以DCS可理解为“分散控制,集中管理”。
二、DCS的应用状况
自1975 年Honeywell 公司推出第一套DCS 以后,全世界有60 余家公司生产了1500 余种产品,目前约有10 000套DCS 在运行。
我国DCS 发展较晚,大约在20 世纪80 年代末才开始逐渐使用。
目前还处在从大型工程逐步向中、小型工程,从主要应用领域(如石化、化工、电力、冶金等行业) 逐步向全工业范围扩展阶段,市场远没有饱和。
特别在最近一段时期,将会有大量的国内企业采用先进的DCS 来改造传统产业,不但大型、中型工程项目采用,不少小型项目也开始采用。
它们的技术改造为DCS 提供了十分巨大的市场空间。
三、 DCS系统结构。
最新一代高级多功能过程控制实训系统SMPT-1000介绍

最新一代高级多功能过程控制实训系统SMPT-1000介绍(西门子杯全国大学生控制仿真挑战赛指定比赛设备)北京化工大学计算机模拟与系统安全工程研究中心(教育部化工安全工程中心,原仿真中心)西门子(中国)A&D有限公司联合推出一、 产品背景与理念过程工业包括石油、化工、电力、核能、水处理、食品、生物、制药、水泥、冶金等诸多行业,过程控制是自动化专业中一个重要的组成部分,过程控制技能也是控制工程师所应具备的重要技能之一。
近年来,教育部强调教育人才要与市场相结合,突出工程能力的培养,并对实验环节提出了设计型、综合型、创新型和探索型等更高的教学目标。
这就要求我们过程控制专业的学生在校期间能够尽可能多地进行动手训练,从实践中获得工程技能。
然而,由于过程工业具有流程复杂、规模庞大等特点,生产过程常常伴有高温、高压等环节,因此很难在实验室中构建与工业装置相近的实验对象。
缺乏理想的过程控制实验装置是目前国内高校、职校等在过程控制工程型人才培养方面面临的最重要的问题之一。
该问题直接导致了学生工程实践能力较弱,无法很好地满足行业对人才的需求。
过去,许多学校采用以水槽液位为主要被控对象的过程控制实验装置。
这类实物仿真装置具有外形直观的优点,学生可以看到变送器、控制器、执行机构的实物,在入门阶段对于认识控制系统组成具有相当好的教学意义。
但是,其表现的对象特性、系统复杂程度与工业真实装置相差太远,仅仅能够满足认知型实验的要求。
这类实验装置的突出不足在于:●实验对象过于简单,与真实生产装置差别太大。
实验装置在相当小的尺寸范围内采用水作为介质进行模拟生产装置。
实验系统过于简单,时间常数过小,动态特性与实际装置相比差异很大。
非线性环节、大滞后、高阶等过程工业常见的被控对象特性都无法在实验装置中体现。
除了流体流动与传热实验外,化学反应、物料混合、组分变化、气体压缩、复杂的传质过程等过程工业的精髓内容都无法实现。
许多在这类实验装置上进行训练的学生都误以为过程控制就是流量与液位的控制。
apc控制系统培训小结 -回复
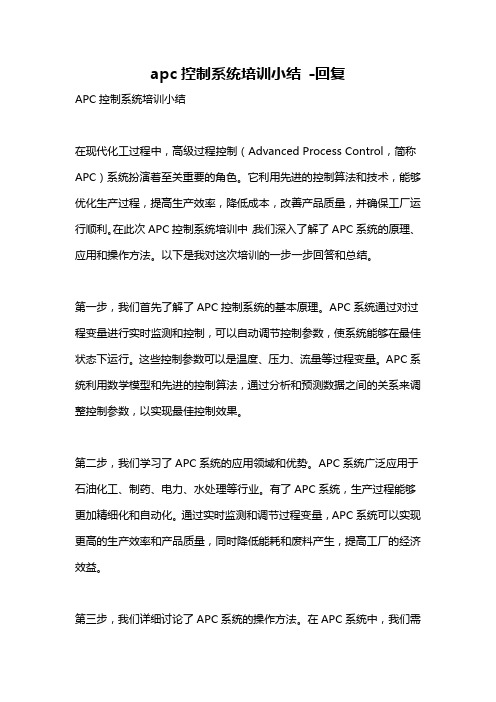
apc控制系统培训小结-回复APC控制系统培训小结在现代化工过程中,高级过程控制(Advanced Process Control,简称APC)系统扮演着至关重要的角色。
它利用先进的控制算法和技术,能够优化生产过程,提高生产效率,降低成本,改善产品质量,并确保工厂运行顺利。
在此次APC控制系统培训中,我们深入了解了APC系统的原理、应用和操作方法。
以下是我对这次培训的一步一步回答和总结。
第一步,我们首先了解了APC控制系统的基本原理。
APC系统通过对过程变量进行实时监测和控制,可以自动调节控制参数,使系统能够在最佳状态下运行。
这些控制参数可以是温度、压力、流量等过程变量。
APC系统利用数学模型和先进的控制算法,通过分析和预测数据之间的关系来调整控制参数,以实现最佳控制效果。
第二步,我们学习了APC系统的应用领域和优势。
APC系统广泛应用于石油化工、制药、电力、水处理等行业。
有了APC系统,生产过程能够更加精细化和自动化。
通过实时监测和调节过程变量,APC系统可以实现更高的生产效率和产品质量,同时降低能耗和废料产生,提高工厂的经济效益。
第三步,我们详细讨论了APC系统的操作方法。
在APC系统中,我们需要掌握安装、配置和调试的技巧。
首先,我们需要选择适合的硬件设备和软件平台,并根据具体的工厂特点进行安装配置。
然后,我们需要编写数学模型和控制算法,并进行参数的调整和优化。
最后,我们需要对APC 系统进行监测和诊断,以确保其正常运行和优化性能。
在这次培训中,我还学到了一些APC系统优化的技巧和注意事项。
首先,我们需要在实施APC系统之前进行充分的工艺优化和改进。
只有在工艺已经达到一定的水平后,才能通过APC系统进一步提高。
其次,我们需要对数据进行准确的采集和处理,以确保APC系统能够得到精确的输入和输出。
此外,我们还需要密切关注系统的稳定性和安全性,并进行定期的维护和更新。
总的来说,这次APC控制系统培训对我来说是一次宝贵的学习机会。
先进过程控制系统简介[1]
![先进过程控制系统简介[1]](https://img.taocdn.com/s3/m/8ef12020192e45361066f5dc.png)
人工神经网络的自动控制:无可比拟的优势
大规模的复杂系统 可提供大量可调变量 极力模仿所描述的对象 实现了并行处理机制 全部神经元集体参与计算,具有很强的计算能力 和信息处理能力 信息分布储存,提供联想、全息记忆的能力 网络拓扑结构具有很大的可塑性,提供了很高的 自适应能力 提供了高度的容错能力 提供了系统自组织能力和协同的潜力等
控制策略和控制算法的发展: 控制策略和控制算法的发展: 简单控制系统 复杂控制系统 先进控制系统
2、自适应控制系统 自适应控制系统
基本概念 自适应控制系统是指能够适应被控过程 参数的变化, 参数的变化,自动地调整控制的参数从而 补偿过程特性变化的控制系统。 补偿过程特性变化的控制系统。 自适应控制系统的适用对象: 自适应控制系统的适用对象:非线性的 工业对象和非定常而具有时变特性的工业 对象。 对象。 自适应控制系统的工作特点:辨识、决 自适应控制系统的工作特点:辨识、 策、控制
基本思想类似:采用工业过程中较容易得 到的对象脉冲响应或阶跃响应曲线,把它 们在采样时刻的一系列值作为描述对象动 态特性的信息,从而构成预测模型。
5、模糊控制系统 、
Model Predictive Heuristic Control, 美国控制理论学者查得于1965年创立模糊 集全理论。 英国马丹尼于1974年建立模糊控制器 定量的精确现象王国→定性的不精确王国
神经网络已渗透到自动控制各个领域:
系统辨识 控制器设计 优化计算 控制系统的故障诊断与容错等
先进过程控制系统简介
1、概述 概述
控制系统体系结构发展阶段: 控制系统体系结构发展阶段: 第一阶段:气动控制系统(简称PCS) Pneumatic Control System 第二阶段:电动模拟控制系统(简称ACS) Analogy Control System 第三阶段:集中式计算机控制系统(简称CCS) Centralized Control System 第四阶段:分布式计算机控制系统(简称DCS) Distributed Control System 第五阶段:现场总线网络控制系统(简称FCS) Fieldbus Control System FCS系统:21世纪的主流
- 1、下载文档前请自行甄别文档内容的完整性,平台不提供额外的编辑、内容补充、找答案等附加服务。
- 2、"仅部分预览"的文档,不可在线预览部分如存在完整性等问题,可反馈申请退款(可完整预览的文档不适用该条件!)。
- 3、如文档侵犯您的权益,请联系客服反馈,我们会尽快为您处理(人工客服工作时间:9:00-18:30)。
先进过程控制系统软件
1、先进过程控制系统简述
现代工业生产过程的大型化、复杂化,对产品质量、产率、安全及对环境影响的要求越来越严格,许多复杂、多变量、时变得关键变量的控制,常规PID控制已经不能胜任。
先进过程控制(Advanced Process Control,简称APC)不同于常规PID控制,是具有比常规PID控制更好控制效果的控制策略的统称,是指动态环境中基于模型、充分借助于计算机能力,为工厂获得最大利润而实施的运行和技术策略。
APC的投用将会使系统运行在最佳工况,实现所谓的“卡边”控制。
目前常见的APC类型包括:状态反馈控制、预测控制、解耦控制、推断控制(软测量技术)、自适应控制、鲁棒控制、时滞补偿控制、智能控制(专家系统、模糊控制、神经网络控制等)等。
2、上德先进过程控制系统软件平台
上德公司于2000年开始研究先进控制技术,成功推出集先进过程控制系统软件平台、智能软测量软件、多变量鲁棒预测控制软件,并成功应用于多套石化生产装置的控制中,已成为国内领先的先进控制软件和服务供应商。
先进过程控制系统软件平台由核心实时数据库、应用组件、组态组件等模块组成,是实现先进控制、软测量、工艺计算和过程模拟优化的基础数据平台,可提供以下功能:
●统一、完整的实时数据采集;
●强大的数据处理和整合功能;
●有效的数据分析和数据管理功能;
●可靠的二次开发工具,支持自定义控制器的实施。
2.1智能软测量软件
智能软测量软件以神经网络、工艺机理建模等技术方法为核心,集数据预处理、辅助变量选择、离线建模与仿真、在线运行等功能为一体,是生产操作和先进控制的重要辅助软件,可提供以下功能:
●提供生产过程关键工艺参数及时、可靠和准确的计算值;
●提供炼油、化工过程特定工艺对象的机理计算模型;
●采用独特的在线模型滚动校正和化验室数据偏差校正的双重
校正技术,提高在线预测精度。
该软件成功应用于燕山石化炼油生产质量预警系统中。
2.2多变量鲁棒预测控制软件
多变量鲁棒预测控制软件包括建模、控制器设计、仿真、组态和在线应用等多个组件,可提供以下功能:
●实现定值控制和区域控制:既可以对被控变量(CV)指定为
设定值控制,也可以指定为区域控制,具有很好的平稳性和很
强的鲁棒性;
●有效抑制可测扰动:对可测扰动同时建模、预测扰动变量(DV)
对过程的影响,有效地对其补偿;
●提供多目标动态优化:对操纵变量(MV)、被控变量以及各变
量之间的线性组合可定义理想的驻留值、极大化和极小化等次
优目标,所有次优目标按控制自由度和变量的权重优先级依次
满足;
●适用于多变量、强耦合、大时滞、带约束的复杂生产过程的平
稳控制和动态优化。
3、上德先进过程控制系统软件的目标
●增强装置的稳定性和安全性;
●提高系统整体控制性能;
●提供准确的关键工艺参数在线计算值,提高产品品质的一致性;
●确保装置长周期运行,并接近其最大能力限;
●“卡边”控制、优化生产,降低成本,使装置效益最大化。
4、上德先进过程控制系统软件的典型效益
●减少关键工艺变量波动的标准差,通常达到50%以上;
●提升装置负荷1~5%;
●增加目标产品收率1~5%;
●节约能源1~5%;
●降低物料消耗1~5%;
●减少不合格产品、降低重新加工的成本;
●减少污染物排放,实现环境友好生产。