Suspension Kinematics and Compliance Measuring and Simulation
中英文文献翻译—基于ADAMS的麦弗逊悬架运动学仿真分析

附录APerformance Kinematics Simulation of Macpherson Suspension Based on ADAMSWANG Yuefang, WANG Zhenhua(Department of Vehicle & Power Engineering,College of MechatronicsEngineering,North University of China, Taiyuan, Shanxi, 030051, China) Phone:+863513920300Fax:+863513922364E-Mail:***********************.cnAbstract: The paper discusses a basic simulation way on founding a front suspension simulation model. It applies on method of multi-body dynamics and uses virtual prototyping technology software ADAMS building up Macpherson suspension entity mold. It analyzes the relations between a Macpherson suspension system and wheel alignment characteristic through kinematics simulation, and obtains the changing trend of the wheel alignment parameters. This provides theoretical foundation with further optimization design.Key words: Macpherson Suspension; Kinematics Simulation; ADAMS1. IntroductionSuspension system is a key part for cars, and has decisive effect on car drivability, stability, and comfortability. Because of its characteristics of simple structure, low cost and space economy, Macpherson suspension has become the most popular independent suspension since its emergence. Hence, the kinematics analysis of Macpherson suspension has great significance. ADAMS (Automatic Dynamic Analysis of Mechanical System) is a simulation software of mechanical system used most widely in the world. Based on the ADAMS virtual model technology, the automobile suspension is regard as a multi-body system which parts connect and motion each other. With the help of ADAMS/View, this paper established multi-body dynamics model of Macpherson front suspension of some car which is increasingly wide used in modern car, and the effects of suspension parameters when wheel travel or turn were studied. The ADAMS entity numeric suspension kinetics simulation provides an efficient and updated tool for developing suspension system.2. Simulation model2.1 Front suspension subsystem simulation modelFirstly, three-dimensional model of Macpherson suspension system in the Pro/E according to acquired geometric parameters is established. Secondly, ADAMS/CAR model is imported by utilizing MECHANISM/Pro, and the geometric characteristicparameters can be obtained from Pro/E three-dimensional documents. The founding model time is short and very accurate. Fig.1 is the model of Macpherson suspension subsystem. Table 1 is the constraints relationship between rigid bodies of front Macpherson suspension.Fig.1 Front Macpherson suspension subsystem1-lower triangle swinging arm 2-universal joint3-subsidiary car frame4-upper suspension support 5-tie rod 6-wheel rim 7-driving axle8-driving joint axle9-shock absorber 10-rubber liner2.2 Steering subsystem simulation modelGear and rack steering system model adopts partial coordinate system. The base point lies in center of circle of steering wheel. The direction of x, y, z axle is radial, tangential, normal of steering wheel separately. Figure 2 is the model which contains six rigid bodies that are rack, rack shell, gear axle, middle axle, steering limb and steering wheel axle. Three assembled bodies connect tie rod, subsidiary car frame and car body. Fig.2 is the model of steering system. Table 2 is the constraints relationship between rigid bodies of steering subsystem.Fig.2 The model of steering subsystem2.3 Simulation model of front Macpherson suspension systemFront Macpherson suspension subsystem and steering subsystem models from ADAMS/CAR that have been established are invoked. Then, combined parameters are input. So far , front Macpherson suspension model is finished. Figure 3 is the kinematics simulation model of Macpherson suspension.Fig.3 Suspension simulation model3. Kinematics simulation analyses3.1 Data processInitial simulation conditions uniform actual parameters of the researched car. Utilizing ADAMS/CAR model simulates bilateral parallel travel and opposite direction travel. So, the alteration of camber angle, kingpin inclination angle, caster angle and toe angle are analyzed. The structure of Macpherson suspension’s left and right is symmetrical, it is totally the same to alignment parameters, only the left wheel alignment parameters are analyzed[3]. The range that this car beats is 150mm -130mm actually. Under two kinds of operating modes, the comparison of changed curves on wheel alignment parameters are shown in Fig. 4-7.Fig.4 Camber angle vs wheel travelFig.5 Caster angle vs wheel travelFig.6 Toe angle vs wheel travelFig.7 Kingpin inclination angle vs wheel travel3.2 Discussion and analysis(1)In the process of wheel parallel travel and opposite travel, the alignment parameters change with the change of wheel vertical shift. In Fig.4, camber angle reduces firstly and increases secondly. The changing amount is 0.9786. The change of camber angle contains two parts: the change of camber angle that comes from car body roll and the changing amount of camber angle that relates car body travel. In Fig.5, the change of caster angle with the wheel vertical shift rise sharply.(2)Under two kinds of operating modes of wheel parallel travel and opposite travel, Fig.6 is shown , the change of toe angle is obviously. Under the operating modes of opposite travel, toe angle increases from -0.8029 to 1.6844. Its change affects car drivability and stability.(3)As we can see in Fig.4 and Fig.7, when the wheel travels downward, the change range that is from 0~-130mm, the changing trend of kingpin inclination angle is opposite to camber angle. This could aggravate the wheel wear. But, according to the theoretical relationship and adjust, proper and acceptedcorresponding relation can be obtained.4. ConclusionThis paper discusses kinematics simulation analysis on founding a front Macpherson suspension simulation model that uses technology software ADAMS. Three conclusions are as follows:(1)ADAMS/CAR model is imported from Pro/E by utilizing MECHANISM/Pro, but model can also be imported to SolidWork or UG in STEP format, then, imported to ADAMS in ParaSolid format.(2)The original wheel orientation parameters of Macpherson suspension meet the require. These indicate that the model is rational. The wheel wear range is accepted.(3)The change trend of the wheel alignment parameters is gained through kinematics simulation analysis of Macpherson suspension. Wheel alignment characteristic has effect on full-vehicle capability through suspension and Camber angle. On contrary, full-vehicle motion characteristic affects wheel alignment characteristic through suspension. In a word, virtual prototyping technology software ADAMS can greatly predigest design program and shorten exploitive cycle, greatly reduce exploitive expense and cost, clearly improve product quality and system capability to get optimized and innovated product.附录B基于ADAMS的麦弗逊悬架运动学仿真分析王月芳,王振华(中北大学车辆与动力工程系, 山西太原030051)摘要:本文讨论了一种建立麦弗逊前悬架模型的基本仿真分析方法。
麦弗逊悬架分析16翻译---译
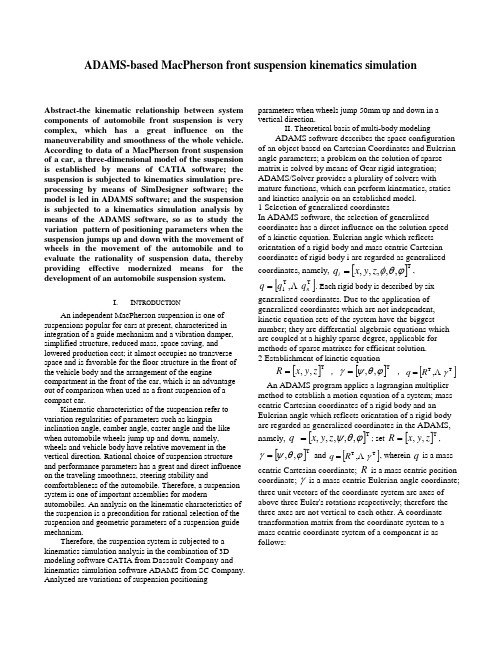
ADAMS-based MacPherson front suspension kinematics simulationAbstract-the kinematic relationship between system components of automobile front suspension is very complex, which has a great influence on the maneuverability and smoothness of the whole vehicle. According to data of a MacPherson front suspension of a car, a three-dimensional model of the suspension is established by means of CATIA software; the suspension is subjected to kinematics simulation pre-processing by means of SimDesigner software; the model is led in ADAMS software; and the suspension is subjected to a kinematics simulation analysis by means of the ADAMS software, so as to study the variation pattern of positioning parameters when the suspension jumps up and down with the movement of wheels in the movement of the automobile and to evaluate the rationality of suspension data, thereby providing effective modernized means for the development of an automobile suspension system.I.I NTRODUCTIONAn independent MacPherson suspension is one of suspensions popular for cars at present, characterized in integration of a guide mechanism and a vibration damper, simplified structure, reduced mass, space saving, and lowered production cost; it almost occupies no transverse space and is favorable for the floor structure in the front of the vehicle body and the arrangement of the engine compartment in the front of the car, which is an advantage out of comparison when used as a front suspension of a compact car.Kinematic characteristics of the suspension refer to variation regularities of parameters such as kingpin inclination angle, camber angle, caster angle and the like when automobile wheels jump up and down, namely, wheels and vehicle body have relative movement in the vertical direction. Rational choice of suspension structure and performance parameters has a great and direct influence on the traveling smoothness, steering stability and comfortableness of the automobile. Therefore, a suspension system is one of important assemblies for modern automobiles. An analysis on the kinematic characteristics of the suspension is a precondition for rational selection of the suspension and geometric parameters of a suspension guide mechanism.Therefore, the suspension system is subjected to a kinematics simulation analysis in the combination of 3D modeling software CATIA from Dassault Company and kinematics simulation software ADAMS from SC Company. Analyzed are variations of suspension positioning parameters when wheels jump 50mm up and down in a vertical direction.II. Theoretical basis of multi-body modeling ADAMS software describes the space configuration of an object based on Cartesian Coordinates and Eulerian angle parameters; a problem on the solution of sparse matrix is solved by means of Gear rigid integration; ADAMS/Solver provides a plurality of solvers with mature functions, which can perform kinematics, statics and kinetics analysis on an established model.1 Selection of generalized coordinatesIn ADAMS software, the selection of generalized coordinates has a direct influence on the solution speedof a kinetic equation. Eulerian angle which reflects orientation of a rigid body and mass centric Cartesian coordinates of rigid body i are regarded as generalized coordinates, namely, []T,,,,,ϕθφzyxqi=,[]TT1,nqqq=. Each rigid body is described by six generalized coordinates. Due to the application of generalized coordinates which are not independent, kinetic equation sets of the system have the biggest number; they are differential-algebraic equations which are coupled at a highly sparse degree, applicable for methods of sparse matrixes for efficient solution.2 Establishment of kinetic equation[]T,,zyxR=,[]T,,ϕθψγ=,[]TT,γRq=An ADAMS program applies a lagrangian multiplier method to establish a motion equation of a system; mass centric Cartesian coordinates of a rigid body and an Eulerian angle which reflects orientation of a rigid body are regarded as generalized coordinates in the ADAMS, namely, []T,,,,,ϕθψzyxq=; set []T,,zyxR=, []T,,ϕθψγ= and []TT,γRq=, wherein q is a mass centric Cartesian coordinate; R is a mass centric position coordinate; γ is a mass centric Eulerian angle coordinate; three unit vectors of the coordinate system are axes of above three Euler's rotations respectively; therefore the three axes are not vertical to each other. A coordinate transformation matrix from the coordinate system to a mass centric coordinate system of a component is as follows:⎥⎥⎥⎦⎤⎢⎢⎢⎣⎡-=01cos sin 0cos sin cos 0sin sin θθφθθφθB Angular velocity of the component can be expressedas γω B =; a variable e ω in introduced in ADAMS as a component of the angular velocity in an Euler's rotationaxis coordinate system: γω =e In consideration of a constraint equation, ADAMS takes advantages of an energy form of a lagrangianequation of the first category with a lagrangian multiplier to result the following equation:ji n i j jj q Q q T q T t ∂Φ∂∑+=∂∂-⎪⎪⎭⎫⎝⎛∂∂=λ1d d (1) T is kinetic energy expressed in generalized coordinates ofthe system; j q is generalized coordinates; j Q is a generalized forced in the direction of generalizedcoordinates j j q ; the final item relates to a constraint equation and a lagrangian multiplier which express a constraining force in the direction of the generalized coordinate j q .III. Establishment of suspension modelingA 3D model of an automobile suspension is established in CATIA and ADAMS by the following steps as shown in figure 1.According to data of a MacPherson front suspension of a car, the 3D model of the suspension established in CATIA is as shown in figure 2 below:The model comprises a lower cross arm, a king pin, a steering rod, a steering knuckle, wheels and a test platform.Based on a multi-body system dynamics theory, the establishment of the model is subjected to the following hypothesis by means of kinematics simulation SimDesigner software of a mechanical system andaccording to the structural analysis on a real car: all parts and components in the suspension are regarded as rigid bodies; a damping system is simplified linear helical spring and damping; friction forces in all kinematic pairs are ignored; tires are simplified as rigid bodies.One end of the lower cross arm is connected with a carriage (herein referred to as ground) via a rotational hinge; the other end thereof is connected with the steering knuckle via a spherical hinge. A wheel isconnected with the steering knuckle via a fixing hinge. During a kinematic analysis, a vehicle body is considered to be in contact with the ground via the fixing hinge. Thesteering tie rod is connected with steering knuckle via thespherical hinge; and the other end thereof is connected with the carriage (namely, ground) via the spherical hinge. Furthermore, movement pair constraint is present between the test platform and the ground in a vertical direction; and in plane constraint is present between a wheel and the test platform in the vertical direction, as shown in figure 3.Finally, a SimDesigner model is introduced in ADAMS for a kinematic analysis.IV Suspension motion simulation analysisBased on practical application of the suspension, up-and-down jumping distance of a wheel is set to be 50mm to the maximum; and the time thereof is set to be 1s; the driving function is applied to simulating a situation when a wheel passes a rough road. In the simulation analysis, front wheel positioning parameters mainly comprisekingpin inclination angle, caster angle, camber angle, toe angle and transverse slippage of a wheel. Through the simulation analysis, 4 parameters for positioning frontwheels and a variation characteristic curve of the transverse slippage with the variation of the up-and-down jumping distance of the wheel are resulted. 1 Kingpin inclination angleIt can be concluded based on the simulation curves in figures 4 and 5 that when a virtual sample model of the present suspension is in a static balancing position, the value of the kingpin inclination angle is 11.448°; the variation range of the kingpin inclination angle is 9.960°~12.634° within the jump variation range of the whole wheel; the variation is 1.186°~1.488° with respect to the static balancing position; and the kingpin inclination angle has a bigger variation when the wheel jumps downward.II.C ONCLUSIONThrough a kinematic simulation of the MacPherson suspension, resulted are variation regularities and range of main performance parameters of the suspension when a wheel jumps, so as to verify the rationality for selecting structural parameters and positioning parameters of the MacPherson suspension, which has a certain reference value and important significance for designers of MacPherson suspensions.。
摩缇马帝multimatic底盘及调教简介
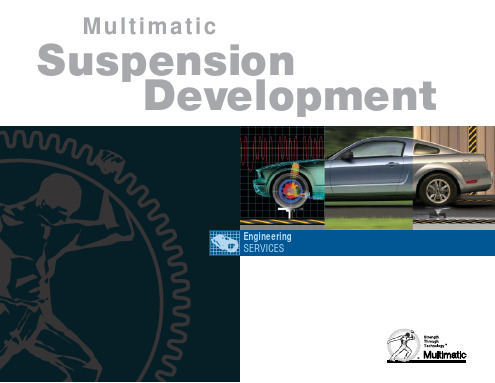
Objective Testing
Multimatic’s unique multi-post rig testing and vehicle characterisation techniques offer an easily interpreted objective-based methodology for assessing a vehicle’s ride and handling performance. Using in-house developed servo-hydraulic actuators in conjunction with a proprietary controller and software suite, a vehicle’s dynamic signature can be identified. The analysis returns data on the dynamic characteristics of the vehicle’s structure, suspension and tires as well as an overall assessment of performance.
Closed-Loop Vehicle Closed-Loop Vehicle Dynamics Optimisation Dynamics Optimization
Multimatic provides development and tuning services that integrate three crucial testing and evaluation disciplines into a “Closed-Loop Vehicle Dynamics Optimisation” process.
GM通用缩略语

Acronym Definition DepartmentA Ampere (unit of electrical current)ENGA Frontal Area (a symbol)VTSA/C Air Cleaner.A/C Air Conditioning.PSEO, VTS, GVDP, ENG A/CL Air Cleaner.ENGA/D Analog to Digital PSEO, ENGA/D,D/A Analog-to-Digital, Digital-to-Analog.ENGA/D/V Analysis / Development / Validation GVDP, GMPTA/D/VP&R Analysis/Development/Validation Plan & ReportA/DFL Air Deflector. An abbreviation.ENGA/DM Authoring & Data ManagementA/F Air/Fuel Ratio.PSEO, ENG, GMPTA/H Air over Hydraulic ENGA/Nut Anchor Nut ENGA/P Accounts PayableA/P Air Pump ENGA/R Accounts ReceivableA/R Appropriation Request GMPTA/Rst Armrest ENGA/Rtl Anti-Rattle ENGA/S Auto Sequence.ENGA/Susp Air Suspension ENGA/T Automatic Transmission.PSEO, ENGA/Trns Automatic Transmission ENGA/V Audio/VisualGVDP, ENG, GMU, GMPT A1R Alpha 1 Release. To mark that point in time as which the design,manufacturing, and engineering information for the Alpha 1 vehiclebuild is released.A1VA Alpha 1 Virtual Assessment ENGA2LA American association of Laboratory Accreditation GMPTGVDP, ENG, GMU, GMPT A2R Alpha 2 Release. To mark that point in time as which the design,manufacturing, and engineering information for the Alpha 2 vehiclebuild is released.A2VA Alpha 2 Virtual Assessment ENGA3Automatic Three Speed Transmission (No longer built or used)ENGA4Automatic Four Speed Transmission ENGAA Algorithmic ArchitectureAA Alternate AnalysisAA Aluminum AssociationGVDP, ENG, GMU, GMPT AA Approve Architecture. To mark that point in time at which there is aregular meeting of the Automotive Strategy Board (ASB) wherethe Architecture Contract is brought forward for approval. Thisresults in deliverables that document the Global Corporateapproval of the proposed new architecture (or the significantmodification to an existing architecture), and also givesauthorization (but not funding) to complete the development,implement the architecture at the Bill of Process and Bill ofMaterial level, and approve its use for the identified current and/orfuture Portfolio Plan products.AA Atomic AbsorptionAAA American Automobile Association.ENGAAAAA American Association Against Acronym AbuseAAAD Association of Automotive Aftermarket DistributorsAAC Advanced Audio CompressionAAC Automotive Advertisers Council ENGAACA Antique Automobile Club of AmericaAACA Amphibious Auto Club of AmericaAAD Assembly Aid Devices.ENGAADT Average Annual Daily Travel [number of vehicles on a highwaysegment]AAES American Association of Engineering SocietiesAIAGAALA American Automobile Labeling Act. Requires a label placed on newcars identifying the country of origin of certain major parts of autossuch as engine and transmission, and identifying whose totalcontent in the vehicle is greater than 15%.AAM Alliance of Automobile Manufacturers (replaces AAMA)ENG, GMPTAAM American Axle & ManufacturingAAMA American Automobile Manufacturers Association (disbanded).ENG, GMPTAAMI American Association of Medical Instrumentation ENGAAOL Automotive Aftermarket On LineAAP Appearance Approval Report.AAPA American Association of Port AuthoritiesAAR Appearance Approval Report.ENG, GMPTAARS Affirmative Action Reporting System ENGAASHTO American Association of State Highway and TransportationOfficialsAAT Ambient Air Temperature.PSEOAB Auxiliary Battery ENGABA Agreement to Build Alpha (4ØVDP).ENGABA American Banking Association EAGABA American Bus AssociationFINABAP Advanced Business Application Programming. (Programs writtenin this language are referred to as ABAPs). ABAP/4 is a fourthgeneration programming language developed by SAP to developbusiness applications.ABB Agreement To Build Beta (4ØVDP).ENGABC Acceleration Boundary CurveABC Active Body Control (DC suspension system).GMPTABC Activity Based Costing.ENG, GMPTABCM Activity Based Cost Management.ABE Advanced Body EngineeringABEL Advanced Boolean Expression Language [a Data-I/O Trademark]ABF Abdomen ForceABIOS Advanced BIOS [Basic Input / Output System]ABL Assembly Breakdown List.ENGABM Assistant Brand Manager GMUABMF Assistant Brand Manager - Finance GMUABMM Assistant Brand Manager of Marketing GMUABMP Assistant Brand Manager of Product GMUABNT Associacao Brasileria de Normas Teonicas (Brazil).ENGABP Acquisition Business Process. A GM business which is under FSS(Financial Shared Services ).ABP Advanced Business Processes (part of PC&L)ENGABP Agreement To Build Prototype.ENGABR Available Bit Rate ENGAbs Absorber. An abbreviation.ENGABS Acrylonitrile Butadiene Styrene (a plastic).ENGABS Anti-Block Steering.ENGABS Antilock Brake System.VTS, GVDP, ENG, GMU, GMPT ABS Anti-Skid Braking System.ENGABS Automated Billing System. Owned by EAG Invoicing & AccountsEAG, FIN Receivable.ABTS All Belts To Seat. Used with reference to passenger restraints.ENGAbv Above. An abbreviation ENGENGABWO Administrative Build Work Order. It communicates the quantity,detail option content and desired build completion date of prototypeand development vehicles required for test and validation.AC Acceleration Complete.ENGAC Air Conditioning.GMU, GMPTAC Alternating Current.ENGAC Annual CostAC Auxiliary ControlACB Adaptive Cylinder Balance GMPTAcc Access. An abbreviation.ENGACC ACCumulator (an abbreviation)ENG, GMPTACC Adaptive Cruise Control (radar/laser controlled)ENGACCA Adaptive Cruise Control with AlertAccel Acceleration (an abbreviation)PSEO, ENG Acclrm Accelerometer. (an abbreviation).ENGAcclrtm Acceleration. (an abbreviation).ENGAccum ACCumulator (an abbreviation)PSEO, ENGAccy Accessory (an abbreviation)PSEOGVDP, ENG, GMU ACD Actual Completion Date. Confirmation that the deliverable has beenachieved.ACD Automatic Call DistributionACD Automotive Component DivisionACDS Automatic Change Detection System GMPTACE Accelerated Cost Estimate ENGACE Alliance for Clean EnergyACE Army Corps of EngineersACE Assistant Chief Engineer ENGACEA(European Car Manufacturers Association)ENGACEC American Consulting Engineers CouncilACEEE American Council for an Energy Efficient Economy ENGACF Access Control Facility.ENGACG Administrative Certification Group.ENGENGACG Allied (Automotive) Component Group. No longer used; nowDelphi.ACGW Automotive Components Group, Worldwide ENGACH Air Changes per HourACI Alloy Cast Iron ENGACI American Concrete InstituteACI Applied Ceramics, Inc.ENGACI Automatic Cargo IdentificationACIA Asynchronous Communications Interface Adapter ENGACL Access Control List. Used in Lotus Notes to control access tovarious databases.ACL Advanced CMOS LogicACL Air Cleaner PSEOACM Adjusting Credit Memo EAGACM Association of Computing Machinery.ENGACM Air Conditioning Module.PSEO, ENG ACMT Action Center Management Team.ENGACN Automated Crash Notification (SDM output of a GMLAN messagewhen any air bag is deployed)ACN Automatic Crash NotificationAcnt Accent (an abbreviation).ENGACPI Advanced Configuration and Power Interface (specification)ENG ACRONYM Abbreviated Coded Rendition Of Name Yielding MeaningACRS Air Cushion Restraint System (no longer used, replaced with SIR).ENGFINACRS Accelerated Cost Recovery System. A depreciation method underUS tax law allowing for the accelerated write-off of property undervarious classification. Also see MACRS.ACS Accredited Standards Committee (ANSI)ACS Automatic Clearance SensingACSI American Customer Satisfaction IndexAcsry Accessory (an abbreviation)ENGAct Actual (an abbreviation)PSEOACT Acoustic Change TransportACT Assembly Component Tracking. A detailed list of parts contained inENGan assembly. ACT is available in the Product Description System(PDS).ACTC Air Conditioning Technical CommitteeActr Actuator (an abbreviation)ENGACTS Adaptive Computerized Training SystemACTS Advanced Car Technology SystemsACTS American Coalition for Traffic SafetyACTV Activate PSEOACV Actual Cash ValueACV Air Cushion VehicleAD Accommodated Device.PSEOAD Automatic Disconnect ENGADA Accident Data AnalysisADA Americans with Disabilities ActENGADAMS Automatic Dynamic Analysis of Mechanical Systems (A generalpurpose kinematics / dynamics analysis program used to modelvehicle handling and suspension performance.)Adap Adapter (an abbreviation)ENGAdapt Adaptive (an abbreviation)PSEOAdapts Adapters (an abbreviation)PSEOADC Analog-to-Digital Converter.ENGADD Advanced Development Directories ENGAddt Additive (an abbreviation).ENGADG Accommodated Device Gateway PSEOAdhes Adhesive (an abbreviation).ENGADI Analog Devices, Inc.ADI Area of Dominant Influence ENGAdj Adjust (an abbreviation)PSEO, ENGAdjr Adjuster (an abbreviation).ENGADL Assembly Diagnostic Link ENGADL Automatic Door Lock.PSEO, VTS, ENG ADM Accessory Drive Motor ENGADM Adjusting Debit Memo EAGADN Advanced Digital Network (Usually refers to a 56Kbps leased-line)ADP Advanced Development Process ENGADP Alternative Durability Process ENGADP Automatic Data Processing.ENGADP Advanced Development Process.ADPCM Adaptive Differential Pulse Code ModulationADPCM Adaptive Pulse Code Modulation.ENGADQA Automated Drive Quality AnalysisADR Alternate Dispute Resolution. Part of CARS VSSMADR Australian Design RulesAds Adsorber (an abbreviation). An emission control device which actsENGto take up gases and/or liquids by physical and/or chemical forces,such as with activated charcoal or the like, and releases it at a latertime.ADS Anti Dieseling Solenoid ENGADS Audio Distribution System ENGADS Auxiliary Discriminating Sensor PSEOADS Alternating Simultaneous Double Fire.ENGADSG Automotive Diagnostic Systems GroupADSIM Automotive Display Simulator ENGADSL Asymmetric Digital Subscriber Line (Usage is similar to a leasedENGline.)ADSL Asynchronous Data Subscriber Line [Supports data speeds over 2Mbps downstream (to the user) and slower speeds upstream (tothe Internet).]ADT Average Daily TrafficADTS Advanced Drive Train System ENGADTT Average Daily Truck TrafficAdv Advanced (an abbreviation).ENGADV Analysis, Development and Validation. (Should be written as A/D/V)GVDP, ENG, GMU, GMPTAE Acceleration Enrichment.ENGAE Advanced EngineeringAE Architectural EngineeringAEC Appearance Engineering Committee.AIAGAEC Automotive Electronics Council. The AEC was originally establishedby Chrysler, Delco Electronics, and Ford for the purpose ofestablishing common part-qualification and quality standards.Components meeting these qualification specifications areconsidered suitable for use in the harsh automotive environmentwithout additional component-level testing.AEC Atomic Energy CommissionAEC Automotive Emission Control.ENGAECD Automotive Emission Control Device.ENGAED Automotive Electronics Development.ENGAEEP Automotive Energy Efficiency Program.ENGAEI Automated Equipment IdentificationAERA Automotive Engine Rebuilders AssociationAES Advanced Engineering Staff.ENGAETR Advanced Electronically Tuned Radio.AF Actual Forecast.ENG, GMUAF Air Fuel Ratio. (see A/F at beginning of section).AF Alternative Fuel. See AltFuel.AF Axial FeedAFAIK As Far As I Know.AFC Accessory Function Controller ENGAFC Alkaline Fuel CellAFC Authorization for Check EAG, GMPTAFC Automatic Frequency ControlAFD Abrasive Flow Deburring.ENGAFD Architecture Flow Diagram.ENGAFECM Alternative Fuel Engine Control Module.PSEOAFIM Air-Fuel Imbalance Monitor.SO, GMPTAFL American Federation of Labor.ENGAFL-CIO American Federation of Labor and Congress of IndustrialOrganizationsAFM Air Flow Meter GMPTAFO Alternative Fuel Operation.PSEOAFR Air Fuel Ratio GMPTAFS Adaptive Frontlighting SystemAFS American Foundrymen’s SocietyAFSM Area Financial Services Manager. GMAC Market Area TeamMember, responsible for financial growth at the dealership throughGMAC.Aft After (an abbreviation)PSEOAFV Alternative Fuel Vehicle.ENGAg Silver (Argentium)AGA American Gas Association ENGAGC Automatic Gain Control ENGAGM Absorbent Glass Mat. Next generation of battery technology.ENGAGND Analog GrouND.ENGENGAGP Accelerated Graphics Port (circa 1997. A dedicated graphics portwhich allows higher throughput from the graphics card to theprocessor for speedier 3D graphics.)AGV Automatic Guided Vehicle ENGAGVS Automatic Guided Vehicle System ENGAh Ampere – Hours ENGAHAR Automatic Highway Advisory RadioAHDL Analog Hardware Descriptive LanguageAHESI Auburn Hills ESI (database)AHIPC Auburn Hills Information Processing Center ENGAHL Automatic HeadlampsAHLD Automatic Headlamp Leveling DeviceAHP Analytical Hierarchy Process ENGAHRS Adjustable Head Restraint SystemAHRS Amp-Hours (an abbreviation)PSEOAHS Automated Highway SystemsAHS Average Highway SpeedAI Air Inlet.ENGAI Artificial Intelligence.GVDP, ENG, GMUAIAGAI Automatic Identification - those technologies that provide methodsfor machine-readable data. The most popular AI medium is BarCoding.AIA American Institute of ArchitectsAIA Automobile Importers of America, Inc.ENGAIAG Automotive Industry Action Group. Automotive Industry ActionAIAG, GVDP, ENG, GMU, GMPT Group - A trade association working to increase memberproductivity through a cooperative effort of North American vehiclemanufacturers and their suppliers.AIAG, ENGAIAM Association of International Automobile Manufacturers. Theassociation of carmakers with operations in the U.S. and Canada.Membership is not restricted to U.S.-based companies. (seeAAMA)AIB ASI Input BufferAIC Automotive Information Council.ENGAICC Auxiliary Information & Control Center ENGAID Architecture Interconnect Diagram.ENGAIEG Automotive & Industrial Electronics Group (Div. Of Motorola)AIIM Association for Information & Image ManagementAIM Analog Input Module.ENGAIM Automatic Identification ManufacturersAIM Automatic Identification Manufacturers Association - Association ofAIAGcompanies that manufacture products for automatic identification,such as bar code readers, scanners, etc.AIMI American Isuzu Motors Inc.AIN Advanced Intelligent NetworkAIN Analog INput.ENGAIP ASI Input PackageAIPE American Institute (of) Plant EngineersAIR Air Injection Reactor (or Reaction).ENG, GMPTAIR Secondary Air Injection.PSEOAIS Abbreviated Injury ScaleAIS Architecture Interconnect Specification ENGAISI American Iron and Steel InstituteAITC Aerodynamics Integration Technical CommitteeAITPM American Institute of Total Productive MaintenanceAIW ASI Input WorkshopAKS Aluminum Killed Steel (The term "killed" is used because aluminumadditions cause the steel to lie quietly in the mold duringsolidification.)Al Aluminum (an abbreviation).ENGAL2All Seasons touring. A tire specification.ENGAL3All Seasons performance. A tire specification.ENGALAPCO Association of Local Air Pollution Control OfficesGVDP, ENG, GMU, GMPT ALBS Assembly Line Balance System. Computer system that helpsestablish and track assembly plant direct labor work assignments.ALC Automatic Lamp Control.PSEOALC Automatic Level Control.PSEO, ENGALCL Assembly Line Communication Link.ENGALDL Assembly Line Data Link GMPTALDL Assembly Line Diagnostic Link.PSEO, ENGALDM Attachment Level Design Method.FINALE Application Link Enabling. ALE facilitates the coupling of businessapplications which are distributed on different databases andprovides the functionality to distribute and receive data.ALG Automotive Lease Guide GMUALGOL Algebraic Oriented Language ENGALGOL ALGOrithmic Language.ENGAlgorithm A specific rule used to determine red/green status of a RigorousTracking and Throughput Management (RT&TM) measure.ALI Automotive Lift Institute.ENGALM Automatic Level Module.PSEOALN Actuator Line Nozzle ENGALR Alpha Level Release.GVDP, ENG, GMU, GMPT ALR Automatic Locking RetractorALRR Appropriation Line Revision RequestALS All Seasons (an abbreviation). A tire specification.ENGAlt Alternative (an abbreviation)PSEOAlt Altitude (an abbreviation).ENGAltFuel Alternative Fueled Vehicles. Vehicles that operated on fuels otherthan gasoline or diesel./eng/alto/ ALTO Accelerated Learning of Test Operations (New employees enteringspecific departments within Design Confirmation and Analysis willbegin an ALTO job simulation with the support of an assignedguide.)ALU Arithmetic & Logical Units.ENGAM Account Manager ENGAM Amplitude Modulation (an abbreviation). i.e. AM Radio.PSEO, VTS, ENGAMA American Marketing AssociationAMA American Medical AssociationAMA Area Module AdvisorAmb Ambient (an abbreviation).ENGAMC Air Management Control ENGAMD Accessory Motor Drive ENGAMDSG Automotive Manufacturers’ Dealer Systems GroupAME Advanced Manufacturing Engineering ENGAMECS Austerity Mode Emission Control System ENGAMEX American Express ENGAMFA Alternative Motor Fuel ActAMIC Automotive Multimedia Interface Collaboration (An organization,formed by a legal agreement between 5 automotive companies,with the mission of defining the auto industry’s first set of hardwareand software interface standards for automotive information,communications and entertainment systems.)AML Adaptive Modeling LanguageAmm Ammeter (an abbreviation). A diagnostic instrument used forENGmeasuring electric current in amperes.Amp Ampere (an abbreviation).Amp Amplifier (an abbreviation)PSEOAmpf Amplifier (an abbreviation)ENGAMPO Association of Metropolitan Planning OrganizationsAmps Amperages (an abbreviation)PSEOAMPS Advanced Mobile Phone Service ENGAMPS Automated Material Procurement and Scheduling ENGAMPTS Allied Productive Material Transfer SystemAMR Anisotropic Magneto ResistanceAMRC Automotive Market Research Council.ENGAMS American Mathematical SocietyAMS Attendance Management System.ENGAMSL Above Mean Sea Level.ENGAmt Armature (an abbreviation).ENGAMT Analysis as Marketing Tool.AMuS Auto Motor und Sport (a German automotive magazine)AN Application Notes.ENGAnc Anchor (an abbreviation).ENGANC Active Noise Cancellation.ENGANDS Alpha-Numeric Display SystemANFIA Association Nationale Fra Industrie Automobilistich.VTSAutomobilistiche (National Association among AutomobileIndustries). Italian equivalent of Motor Vehicle ManufacturersAssociation.ANL Argonne National Laboratories ENG, GMPTANMC American National Metric Council.ENGANOVA ANalysis Of VAriance.ENG, GMPTANPRM Advance Notice of Proposed Rule Making.ENGANS American National Standard ENGANSI American National Standards Institute. The standards bodyAIAG, ENG, GMU, GMPT responsible for formalizing the U.S. voluntary standardsdevelopment process. ANSI is the U.S. representative to non-treatyinternational standards bodies such as ISO, IEC, and EDIFACT.Founded in 1918, ANSI ensures that a single set of non-conflictingstandards are developed for an area.ANSI/ASQ Q90 See ISO-9000.AIAGANT Antenna. An abbreviation.ENGANT Assemblies Navigation ToolAIAG, ENG, GMPT, AVDC ANX Automotive Network eXchange. A project administered by theAIAG to assure efficient and secure electronic communicationamong subscribers, so that an ANX subscriber company in theautomotive industry would require only a single access circuit tocommunicate with any other ANX subscriber. ANX is composed ofa TCP/IP network that includes trading partner subscribers, certified(Internet) service providers, and network exchange points.AOA Analysis Of AlternativesAOB Any Other Business.ENGAOIB Adjustable Off Idle Bleed (Carburetor).ENGAOL America On Line.AOQL Average Outgoing Quality Limit.ENGAORC Automotive Occupant Restraints CouncilAORS Advanced Occupant Restraint SystemAOS Automatic Occupant Suppression / Automatic Occupation detectingSensor.AOT Automotive Organization Team ENGAP Accounts Payable ENG, GMU, EAGAP Achievement Plan ENGAP Advanced Purchasing.GVDP, ENG, GMU, GMPTAIAGAP Application Protocol. An ISO standard, contained within ISO 10303(STEP), which specifies the STEP product data construct requiredfor the communication of information in a defined applicationcontext.AP Asian Pacific GVDP, ENG, GMUAP&P Accounting Practices & Procedures ENG, FINAP/S Achievement Plan / Scheduler ENGAPA Acquisition Process Analyst.ENGAPA Authorized Payment Approval EAGAPAA Automotive Parts and Accessories Association, Inc.ENGAPAC Auto Parts Advisory Commission ENGAPB Automatic Powertrain Braking GMPTAPC Automated Passenger CountingAPC Acquisition and Production Costs. Pertains to fixed assets.FINAPD Alliance Planning Director.ENG, GMU, GMPTAPD Assembly Plant Designator (used in PDS).APD Assembly Process Deviation.ENGAPD Avalanche Photo Diode ENGAPE Annual Program Execution.GVDPAPE Advanced Product Engineering (no longer used)ENGAPEAL Auto Performance Execution and Layout (J. D. Power)ENGAPEC Asian Pacific Economic Corporation ENGAPET Advanced Program Execution Team.GVDPAPEX Advanced Portfolio Exploration GVDP, ENGAPEX Advanced Product Exploration GVDP, GMUAPG Advanced Process Group GMPTAPI Advanced Product Information.GVDP, ENGAPI Advanced Programmable Interrupt control ENGAPI American Petroleum Institute.ENGAPI Annual Physical Inventory.FIN, ENG, GMU, GMPTAPI Application Programming Interface. A set of functions and/orENG, GMU, FINintegration points that system developers can use to enablecommunication between processes and/or applications. APIs allowfor interoperability and integration of systems by providing vendor-or product-independent communication between the systems,provided the systems share the same software and/or hardwareplatform.APIC Advanced Programmable Interface ControlAIAG, ENG, GMPTAPICS American Production & Inventory Control Society. A professionalsociety devoted to the improvement and advancement of inventoryand control management.APL Associative Programming Language.ENGAPLQ Applique. An abbreviation.ENGAPM Accelerator Pedal Module.ENGAPM Accessory Power Module (With a PIM, makes up PEB)ENGAPM Application Processor ModuleAPM Area Parts Manager VSSMAPM Automotive Process Model GVDP, ENG, GMU, AVDCAPM Area Parts Manager (Dealership contact/sales person for GMParts)APMES Advanced Product & Manufacturing Engineering Staff ENGAPMM Assembly Plant Material Management ENGAPMT Allied Productive Material Transfer FIN, EAGAPMTS Allied Productive Material Transfer System.ENG, GMPTAPO Asian Pacific Operations ENGAPP Accelerator Pedal Position PSEOAPP Applied Practices & Procedures ENGAPPL Application. An abbreviation.ENGMFD, GMPT, GVDP, ENG, GMU APQP Advanced Product Quality Planning. APQP is required for everypart coming from suppliers.Apr April (an abbreviation)PSEO, ENGAPR Annual Percentage Rate ENG, GMUAPR Appropriation Request Process.APR Automatic Password RequestAPR Automatic Password Reset.ENGAPRA Automotive Parts Rebuilders Association, Inc.ENGAPS Advanced Photo SystemAPS American Physical SocietyAPS American Psychological SocietyAPS Asynchronous Protocol SpecificationAPS Automated Patent SystemAPS Auxiliary Power Supply ENGAPSC Advanced Product Service Committee ENGAPSMB Accessory Power Supply Mother Board ENGAPT Adjustable Part Throttle ENGAPT Alliance Planning Team ENGAPT Automatic Programmed Tool ENGAPTA American Public Transit AssociationAIAG, ENGAPTA American Public Transport (or Transit) Authority. Group formed toset and represent industry requirements for public transit systems inNorth America.AIAGAPTA Automotive Products Trade Agreement. That portion of theU.S./Canadian Free Trade Agreement that referred to automotiveparts.APU Auxiliary Power Unit ENGAPV All Purpose Vehicle ENG, GMPTAPY Annual Percentage Yield.GMUAQ Air Quality.ENGAQC Air Quality Committee ENGAQL Acceptable Quality Level ENGAQMD Air Quality Management District.GMUAQNS Accelerated Quality Network Strategies GMPTAr ArgonAR Academic Relations HRAR Accounts Receivable.ENG, GMU, EAGAR Anti-Reflection.ENGAR Appropriation Request.GVDP, ENG, GMUAR As Required.ENGARA Automotive Recyclers AssociationARAN Automated Road AnalyzerARB Anti- Rollover BreakingARC Advanced Radio Concept.ENGARC Atlantic Research Corporation (air bag inflators: Knoxville, TN)ARC Awareness, Recognition, and CommunicationGVDP, ENG, GMU, GMPT ARC Architecture Requirements Complete. To mark that point in time atwhich the requirements for the architecture have been completelydefined.ARD Acceptance Requirements Document ENGARD Application Requirements Document (IT)ARG Asset Recovery GroupARI Automatic Road Information.ENGARM Application Resource ModelARM Automated Requirement Measurement (NASA software tool toassess requirements written in "natural language." The tool isaimed at "writing the requirements right." It does not address"writing the right requirements.")ARMS Account Reconciliation Monitoring System EAGARO After Receipt of OrderARP Appropriations Request Process GVDP, ENG, GMUARP Association of Retired Persons.GMUAIAGARPA Advanced Research Projects Agency.A government agency, whichhas been assigned to manage Defense Technology Conversion,Reinvestment, and Transition Assistance. One of the projects theagency is involved in is the Technology Reinvestment Project (SeeTRP).ARR Architectural Requirements Review.GVDP, ENG, GMU ARRANT Advanced Research Projects Agency Network ENGARS Adaptive Receptive System PSEOARS Angular Rate SensorARTBA American Road & Transportation Builders Association.ENGENGARTEMIS A computer system used to calculate overall program timing andgenerate Gantt charts, critical path diagrams, and timing plots.ARTS Adaptive Restraint Technology SystemAs ArsenicAS Active Suspension.ENGAS Administrative Services.ENGAS Allied Signal Inc.ENGAS American Standards association.ENGAS As Specified.ENGAS Assembly System.ENGASA Agreement to Ship Alpha.GVDP, ENG, GMUASAM Association for Standardization of Automation and MeasuringGMPTSystemsASAP As Soon As Possible.ENGASB Agreement to Ship Beta.GVDP, ENG, GMUASB Automotive Strategy Board.GVDP, GMUASBC American Seat Belt Council.ENGASBE American Society of Body Engineers.ENGASC Accredited Standards Council. An ANSI committee that developsAIAG, GMPTstandards.ASC Anti-Slip Control GMPTASC Architecture Selection Complete. To mark the point in time at whichGVDP, ENG, GMU, GMPT the architecture decisions have been completed and a singlearchitecture has been chosen.AIAGASC MH10Accredited Standards Committee MH10 - The ANSI committee forstandards for Unit Loads and Transport Packages, including thenational standard for bar code labeling.AIAGASC X12Accredited Standards Committee X12 - The ANSI committee forUS EDI standards, commonly called "ANSI X12."ASC X3Accredited Standards Committee X3 - The ANSI committee forAIAGInformation Processing.ENGASCII American Standard Code for Information Interchange (Mostcommonly refers to a plain-text file.)ASD Actual Start Date. Refers to date the design was started by aENGspecific stage/Dept.ASD Advanced Serviceability of Design.SOASD Anti Slide DeviceASDF Alternating Simultaneous Double FireASDM Automotive Steel Design Manual (CARS Section: ASDM is aCARS on-line reference that gives access to 700 pages of text,charts, equations, tables, and figures concerning the use of steel invarious automotive designs. Hypertext links and search featuresassist in readily locating needed information.)ASE Automotive Safety Engineering.ENGASE Automotive Service Excellence.VTS, VSSMASEP Automotive Service Education Program VSSMASG Administrative Support GroupASI Architecture Studies Initiation. To mark that point in time at whichGVDP, ENG, GMU, GMPT the vehicle architecture study and limited program activities begin.ASIA Automotive Service Industry Association.ENGASIAN Association of South Eastern Asian Nations ENGASIC Application Specific Integrated Circuit.ENGASK Amplitude Shift Keying ENGASLE American Society of Lubrication Engineers.ENGAsm Assembly. (abbreviation)PSEO, GMPT, ENG, GVDP ASM Alarm Siren Module.PSEOVSSMASM Area Sales Manager. Dealership contact for sales/vehiclepromotions.ASM Area Service Manager. (No longer used by VSSM; refer to AVM).ASME American Society of Mechanical Engineers.ENG。
Trucksim_Steer_Controller

912 North Main, Suite 210, Ann Arbor MI, 48104, USA Phone: 734 668-2930 • Fax: 734 668-2877 • Email: info@
Technical Memo
In the above equations, A is an n x n matrix. In the general case, u, v, and y could be arrays involving more than one control, disturbance and/or output variable. However, this derivation only considers the one case in which u, v, and y are scalars. B and H are n x 1 matrices and C is a 1 x n matrix. There is a further simplification, namely, that the output y does not depend explicitly on u or v. Thus, the D and E matrices are not used.
If the system has initial conditions xo at time t=0, a constant control input u, and a constant disturbance v, then the time response is:
ò ò x(t) = eAt xo +
t 0
eAh B u dh +
汽车动力学

40
பைடு நூலகம்
•
Chassis Design(底盘设计)
• Slip angle and cornering performance (侧偏 角&侧偏刚度)
5
Tire Properties (轮胎特性)
• Affecting factors of cornering stiffness (侧偏角&侧偏刚度)
6
Tire Properties (轮胎特性)
9
Tire Properties (轮胎特性)
• Tire Testing (轮胎试验)
10
Tire Properties (轮胎特性)
• Handling tire Magic Formula (操 纵稳定性轮胎模型)
11
Tire Properties (轮胎特性)
• Ride and Durability tire (平顺性路、可 靠性轮胎模型)
– Bicycle model (线性二自由度模型)
δ=57.3L / R + α f − α r
15
Handling(操纵稳定性)
– Bicycle model (线性二自由度模型)
Fyf + Fyr = MV 2 / R Fyf × b − Fyr × c = 0
V 1 αf = × × g R Cαf Wr V 2 1 αr = × × g R Cαr Wf
汽车操纵稳定性介绍(中英文)

Andrew Middleton, Technical Director, Anthony Best Dynamics Ltd
Vehicle handling is closely related to ride and steering. 车辆的操纵性与行驶平顺性和转向特性是密切相关的。 Ride is not dealt with in this presentation, but vehicle characteristics optimised for ride will affect handling. 行驶平顺性在这次讲座中没有提及,但是关于车辆行驶平顺 性的优化将影响到操纵性。 The art of ride and handling is to find the “best compromise” for the type of vehicle. 平顺性和操纵性的技术在于取得车辆的“最佳折衷”的办法。
The total force between tyre and ground is proportional to the shaded area.
轮胎与地面之间所有的力与阴影区域面积成比例。
Hence up to a point, as the slip angle increases, the shaded area and the cornering force increase. 因此当横向偏移角增加时,阴影区域和侧向 力增加。 At higher slip angles the increase becomes non linear. 在更大的横向偏移角下,增加变成非线性。
Cornering force, slip angle and vertical load. 横向力、横向偏移角和垂直力 For a greater vertical load there is more cornering force at a given slip angle. 对于更大的垂直 力在相同的横向 偏移角下有更大 的横向力。
9m空气悬架大客车后悬架毕业设计汽车悬挂系统设计

汽车悬挂系统设计【摘要】:悬挂系统是指由车身与轮胎间的弹簧和避震器组成的整个支持系统。
悬挂系统的功能是支持车身,改善乘坐的感觉,不同的悬挂设置会使驾驶者有不同的驾驶感受。
外表看似简单的悬挂系统综合多种作用力,决定着轿车的稳定性、舒适性和安全性,是现代轿车十分关键的部件之一。
论文回顾了汽车悬挂系统的发展历程,介绍了悬挂系统的分类和组成,详细分析了各种悬挂系统的优劣,进行了对比。
最后根据汽车的要求,选定了悬挂系统的组合,前悬架为麦弗逊式独立悬挂,后悬架为钢板弹簧整体式悬挂。
并且确定了前后悬挂的技术参数,在设计中着重考虑了汽车的稳定性和操控性,对整个系统进行了运动学和力学分析计算。
最后使用AUTOCAD绘制出了汽车悬挂的装配图和部分零件图。
【关键字】: 汽车悬挂独立悬挂非独立悬挂麦弗逊式独立悬挂钢板弹簧整体式悬挂The Design Of Car Suspension System【Abstract】Suspension is means that the body and tires between spring and shock absorber for the entire support system. The function of suspension system is to support the body, improve the ride feel different suspension settings the driver will have different driving experience. Appeared to be a simple suspension system integrated a variety of forces, determine the car's stability, comfort and safety of modern cars is one of key components. This thesis reviews the development history of the suspension systems and introduces the classification and composition of it. Secondly, the thesis detailed analysis the pros and cons of various suspension systems, were compared. Finally, according to the requirements of vehicles, decided on a combination of the suspension, front suspension is McPherson independent suspension, leaf spring rear suspension for the whole suspension. And determined the two suspensions of the technical parameters considered in the design focused on stability and control of the car, the whole system of calculation of the kinematics and mechanics. Finally out of the car hanging AUTOCAD drawing, assembly drawing and part of the parts drawing.【Key words】:car suspension system; independent suspension; solid axle suspension; macpherson type; leaf-spring dependent suspension目录【摘要】 (I)1.绪论.......................................................... - 1 -1.1汽车悬挂的基本原理....................................... - 1 -1.2汽车悬挂的发展史......................................... - 2 -2.汽车悬挂的组成和分类.......................................... - 4 -2.1汽车悬挂的组成........................................... - 4 -2.2非独立悬架的类型及特点................................... - 5 -2.2,1钢板弹簧式非独立悬架............................... - 5 -2.2.2螺旋弹簧非独立悬架................................. - 5 -2.2.3空气弹簧非独立悬架................................. - 6 -2.3独立悬架的类型及特点..................................... - 6 -2.3.1双横臂式........................................... - 7 -2.3.2麦弗逊式(滑柱连杆式)............................. - 8 -2.3.3 双叉臂式悬挂....................................... - 9 -2.3.4 拖拽臂式悬挂...................................... - 12 -2.3.5 连杆支柱悬挂...................................... - 14 -2.3.6 多连杆独立悬挂.................................... - 15 -3.悬挂系统的选择............................................... - 18 -3.1前独立悬架的选择............................ 错误!未定义书签。
- 1、下载文档前请自行甄别文档内容的完整性,平台不提供额外的编辑、内容补充、找答案等附加服务。
- 2、"仅部分预览"的文档,不可在线预览部分如存在完整性等问题,可反馈申请退款(可完整预览的文档不适用该条件!)。
- 3、如文档侵犯您的权益,请联系客服反馈,我们会尽快为您处理(人工客服工作时间:9:00-18:30)。
400 Commonwealth Drive, Warrendale, PA 15096-0001 U.S.A.Tel: (724) 776-4841 Fax: (724) 776-5760SAE TECHNICAL PAPER SERIES980897Suspension Kinematics and Compliance -Measuring and SimulationPeter Holdmann, Philip Köhn and Bertram MöllerInstitut für Kraftfahrwesen Aachen (ika), RWTH AachenRalph WillemsForschungsgesellschaft Kraftfahrwesen mbH Aachen (fka)Reprinted From: Developments in Tire, Wheel, Steering, and Suspension Technology(SP-1338)International Congress and ExpositionDetroit, Michigan February 23-26, 1998The appearance of this ISSN code at the bottom of this page indicates SAE’s consent that copies of the paper may be made for personal or internal use of specific clients. This consent is given on the condition,however, that the copier pay a $7.00 per article copy fee through the Copyright Clearance Center, Inc.Operations Center, 222 Rosewood Drive, Danvers, MA 01923 for copying beyond that permitted by Sec-tions 107 or 108 of the U.S. Copyright Law. This consent does not extend to other kinds of copying such as copying for general distribution, for advertising or promotional purposes, for creating new collective works,or for resale.SAE routinely stocks printed papers for a period of three years following date of publication. Direct your orders to SAE Customer Sales and Satisfaction Department.Quantity reprint rates can be obtained from the Customer Sales and Satisfaction Department.T o request permission to reprint a technical paper or permission to use copyrighted SAE publications in other works, contact the SAE Publications Group.No part of this publication may be reproduced in any form, in an electronic retrieval system or otherwise, without the prior written permission of the publisher.ISSN 0148-7191Copyright 1998 Society of Automotive Engineers, Inc.Positions and opinions advanced in this paper are those of the author(s) and not necessarily those of SAE. The author is solely responsible for the content of the paper. A process is available by which discussions will be printed with the paper if it is published in SAE T ransactions. For permission to publish this paper in full or in part, contact the SAE Publications Group.Persons wishing to submit papers to be considered for presentation or publication through SAE should send the manuscript or a 300word abstract of a proposed manuscript to: Secretary, Engineering Meetings Board, SAE.Printed in USAAll SAE papers, standards, and selected books are abstracted and indexed in the Global Mobility Database980897Suspension Kinematics and Compliance -Measuring and SimulationPeter Holdmann, Philip Köhn and Bertram MöllerInstitut für Kraftfahrwesen Aachen (ika), RWTH AachenRalph WillemsForschungsgesellschaft Kraftfahrwesen mbH Aachen (fka) Copyright © 1998 Society of Automotive Engineers, Inc.ABSTRACTIn this paper, a new kinematics and compliance test rig will be presented. Particularly the design and construc-tion of the test bench is explained. Moreover a typical measuring procedure will be presented in which a certain driving situation is going to be simulated at the test bench.It will also be shown how to validate the computer model of a vehicle for the simulation tool ADAMS with the results of the test bench. By simulating a certain driving maneuvers with ADAMS, the influence of the compliance steer on the road performance of a motor vehicle will be shown in conclusion.INTRODUCTIONFor the understanding of vehicle handling characteristics, investigations on suspension kinematics and compliance steer are of major interest. Kinematics means the move-ments of the wheel relative to the body that result from spring travel. Compliance steer results from additional forces in the contact area of the tires. These forces caused by lateral or longitudinal accelerations of the vehi-cle deform the suspension parts and its bushings and lead to additional camber and toe angles [DIN94]. Compliance steer of axles has a great influence on the handling performance of vehicles. By a specific interpre-tation of the suspension elements, the engineer is being forced to get a compliance steer that supports a con-trolled road performance of the complete vehicle. Some types of axles have however conceptionally caused dis-advantages regarding compliance steer such as twist-beem rear axles [ZOM87]. These shall be minimized in the most effective way by constructive features. Because of the diminution of vehicle development time it is necessary to get object measuring results from new axles very fast and easily. These results are also neces-sary to validate the compliance steer of vehicle models for the simulations of vehicle dynamics. The quality of the model compliance steer influences very clearly the results of the multy-body-simulations. Pure static mechanical models do not deliver adequate simulation results for modern vehicles.CONCEPT AND DESIGN OF THE TEST BENCH The ika kinematics and compliance Test Rig can be used for the measurement of the influences of vertical deflec-tions and both lateral and longitudinal forces on the axle geometry of complete vehicles or of axle-systems. By the help of four hydraulic cylinders that are fixed to the four wheels arbitrary wheel suspension positions can be real-ized [Fig. 1].The test bench mainly consists of 12 hydraulic actuators (one for longitudinal, lateral and vertical force generation on each wheel) that can be operated individually. In Fig.2 two possible designs for the test bench are demon-strated. In order to simulate a contact zone between wheel and the ground the test bench can be equipped with aerostatic bearings. Highly sophisticated sensors, amplifiers and measurement data acquisition systems record any value in the course of time that might be of interest. Fig. 2 shows the optical Autocollimator sensors that are used to measure the camber and toe angles.A large number of fastening devices, which serve to fix the vehicle body to the test rig, eliminate the influence of body stiffness on the measurement. Moreover, the fas-tening systems allow the easy fixing of any car to be tested without the need to produce costly adapters. Apart from that it is also possible to fix and to examine single axles and wheel suspensions without examining the complete vehicle.Figure 1. ika-kinematics and compliance test rigThe complete system is controlled by a reliable computer system to reduce the operator’s influence on the results and to achieve an optimum reliability and repeatability of the measurements. Extensive routines shall exclude a malfunction of the test bench to avoid a damage of the vehicle.T ypical characteristics which are supposed to be exam-ined are: roll axis position, roll stiffness or steering com-pliance. But also complete driving maneuvers such as ‘steady state cornering’ or ‘breaking maneuvers’ can besimulated at the test bench. Knowledge can be gained about the self steering properties of the vehicle by using this method.The technical data of the test rig are:•variable wheelbase: 2000 to 3250 mm •variable track width: 1180 to 1650 mm•max. vertical displacement at the wheel: 400 mm •max. wheel load: 14 kN•max. lateral force (per wheel): 10 kN •max. brake force (per wheel): 10 kN •max. traction force (per wheel): 5,5 KnBecause of the compliance steer forces, and moments between the tire and the ground cause changes to the kinematic qualities of a suspension.In Fig. 4 - 6 typical measurement results of the test bench are shown. Fig.4 shows the toe and camber angle as function of the suspension travel of an typical twist-beam rear suspension. Fig.5 shows th same curves for an McPherson front suspension system. In Fig.6 toe and camber angle are shown as function of the lateral force in Fig. 7 as function of braking force for an twist-beam rear suspension.Figure 2.Measuring of camber and toe angles withoptical AutocollimatorsFigure 3. Configurations for the simulation of lateral and longitudinal forces in the wheel contact area to the groundFigure 4.toe angle and camber angle as function of suspension travel of an twist-beamsuspension Figure 5.toe angle and camber angle as function of suspension travel of an McPherson-SuspensionFigure 6.toe angle and camber angle as function oflateral force of an twist-beam suspension Figure 7.toe angle and camber angle as function ofbreaking force of an twist-beam suspension SIMULATIONComputer aided simulation of vehicle handling character-istics is nowadays universally acknowledged as an effi-cient method in the process of developing new vehicles. Simulation software tools are used both by automobile manufacturers and suppliers to an increasing extent. The outstanding quality of simulation results for chassis development is acknowledged without exception. ADAMS® as a multybody-simulation-tool is in service in automotive engineering all over the world. The dynamics of rigid bodies can hereby be analyzed mathematically very exactly.Figure 8.ADAMS®-Model of a complete vehicleBy the connection of different bodies with joints, models of complete vehicles become reality. This can be used in the simulation of standard driving maneuvers to examine the road performance of the vehicle. T o get more detailed simulation models, the joints have to be replaced by elas-tic elements, the so called ‘bushings’. These bushings can be characterized by defined spring and damper char-acteristics in any direction. By this the compliance steer of a suspension can be integrated in the simulation model. In Fig.8 an ADAMS®-model of a complete vehicle is being shown, which shall be used for the simulations described in this chapter. The model is equiped with an double-wishbone suspension at front and with the twist-beam rear axle, that was examined before oh the K&C test bench.VALIDATION OF THE COMPUTER MODEL – The kine-matic qualities of vehicle axles are obviously defined by the geometry of the suspension bearing points. But for the elastic qualities of the axles more than design infor-mation are necessary to create an exact model of the axle. Particularly the assembly of all the different flexible elements of a suspension have to be verified only by measuring the complete axle on a test rig.In the simulation, a similar procedure has to be carried out. Therefore the complete kinematics and compliance test rig has to be built up in simulation to verify the actual simulation model which is equipped with elastic ele-ments, as is shown schematically in Figure9.Similar to reality, the vehicle body has to be fixed to the ground. Common tire models are not designed for simu-lations without any velocity [STR96]. Therefore the tire model in this simulation has to be replaced by simple springdamper elements. This, however, doesn't influence the results. In the contact area between the tire and the test bench, forces or moments can be applied like has been done on the real test rig. In this way any displace-ments or angles between the wheels and the body can also be determined as function of the applied forces and moments in the simulation.After comparing the results from the simulation and the testing, the simulation results can be changed by modify-ing the qualities of the elastic bushing-elements in the computer model. This modification will be repeated as long as the results of the simulation and the testing don’t match. In Fig.9 the results of the test bench are com-pared to the results of the ADAMS-Model. The similarity of both curves is so precisly that the validation of the model can be considered as quite perfect.Figure 9.toe angle and camber angle as function oflateral force of an twist-beam suspension insimulation and testingFigure 10.In principle construction of the test rig in the simulationSIMULATION OF STANDARD DRIVING MANEUVERSSimulations of standard driving maneuvers are carried out with the validated ADAMS®-vehicle model. These maneuvers are used worldwide to characterize the qual-ity road performance of vehicles [ZOM87, ROM94].In this paper the maneuver ‘Steady state cornering’ is presented. Fig.10 shows the results of this simulation: steering angle as function of lateral acceleration. In addi-tion to the results of the model with compliance steer, results of a rigid body model without compliance steer are also shown.The figure shows that both vehicles have understeering self-steering properties. The steering wheel curve of the model with compliance steer is little bit lower than the one of the rigid model. That means that the rigid model under-steers more than the model with comliance steer.T o explain this effect we have to look at the compliance steer angles of the rear axle. Particularly the outer wheel must be observed. As Fig. 11 shows, the angle of the rigid model is as expected zero. The compliance angle of the outer wheel of the model with compliance steer rises proportionally to the lateral accelaration.Figure 11.Steering wheel angle as function of lateralaccelerationThe compliance steer behaviour of the vehicle shown in this simulation leads to a decreasing understeering ten-dency of the complete vehicle. This effect has to be judged of course negatively but is typical for a twist-beam rear axle that was simulated here.Figure pliance Steer Angle of the Outer Rear Wheel as Function of Lateral Acceleration SUMMARY AND CONCLUSIONAt the ‘Institut für Kraftfahrwesen Aachen’ a new test bench has been built up for the measuring of axle kine-matics and compliance for complete vehicles and for sus-pension systems. By using this test bench, even prototypes can be analyzed to get all characteristic val-ues of the axle geometry and the compliance steer. The complete system ist controlled by a computer system that produces values to simulate certain driving situations, as for example ‘steady state cornering’. Based on this infor-mation, the self steering properties can be determined. By the help of the multybody simulation tool it has been shown how to validate a computer model of a vehicle regarding its compliance steer values. With that model the maneuvers ‘steady state cornering’ and ‘straitline braking’ have been carried out. Moreover the difference was determined particularly between the elastic and the rigid model in terms of road performance. It could be pointed out, in what way the interpretation of the compli-ance steer improves the road performance of the vehicle. By further modifications to the elastic elements of the model, it will be possible to obtain further improvements in the road performance. If the result is satisfactory, requirements on the construction can be made from the simulation. As a consequence, the number of suspension prototypes can be reduced clearly.Therefore a way was shown within this contribution how modern test benches and the use of modern simulation software can help to develop a complex new suspension systems with defined compliance steer. By using this method time and costs for the development of a new vehicle-chassis can be reduced.REFERENCES1.[DIN94]DIN 70 000Straßenfahrzeuge, Fahrzeugdynamik, Begriffe19942.[PAE96]P AEFGEN, F.-J.; TIMM, H.Der neue Audi A3Automobiltechnische Zeitschrift 98 (1996), Nr. 7/8, S. 370-3783.[ROM94]ROMPE, H.; HEIßING, B.Objektive T estverfahren für die Fahreigenschaften von KraftfahrzeugenVerlag TÜV Rheinland GmbH, Köln, 19944.[STR96]STRAETEN, F.Theoretische Reifenmodelle in der ComputersimulationStudienarbeit am Institut für Kraftfahrwesen Aachen, RWTH Aachen, Aachen, 19965. [ZOM87]ZOMOTOR, A.Fahrwerktechnik: FahrverhaltenVogel BuchverlagWürzburg, 1987CONTACTIf you are in interest in further informations on the test bench or the driving simulation work please contact: Dipl.-Ing. Peter HoldmannInstitut für Kraftfahrwesen Aachen (ika)RWTH AachenSteinbachstraße 10D-52074 AachenT el.:+49 / 241 / 80-56 11Fax.:+49 / 241 / 88 88-147e-mail: holdmann@ika.rwth-aachen.de。