加压水电解制氢装置控制系统
水电解制氢装置远程控制系统

与状态监测,远程故障诊断以及软件网络升级过程中数据传输及网络通讯的安全性问题。
(7)gI八“冗余设计”概念设计了以太网络以及现场总线系统,分析了不同位置网络 故障以及对水电解制氢装置远程控制系统运行性能的影响,从而使系统具有在阿络故障F准 确传输数据的功能。
(8)远程控制端既可以采用诸如LoginAny、PCAnywhere、TearaViewer等简单的通用
时,系统具各独有的■次开发应用接口可以满足高端用户多方面需隶:a)提供数擗库接u 方式:为用户提供了方便快捷的ODBC数据库接口,为用户把收发短信的工作简化为读写 表操作。b)提供控件接u控件接_u提供一系列控制甬数库,用户通过在自行开发的软件 中调用这些控件,就可实现短信的收发功能.适用于主流开熊平台(VB、VC、JAVA)。罔
制,宴现系统的无人值二1、全程自动化、集中管理以厦远程故障诊断等功能是该领域的种
趋势.但由于受阿络传输韵速串、距离还有安全性等彤响,相关技术及其应用还不是十分成
熟。
水电解制氢装置控制系统的远程,有利于提高水电解制鲺世备的运行可靠性,大幅度降
低设备的绯护成本.进而显著提高水电梓制氧设备的市场竞争力。
2.系统整件框架 本项目针对图1-l所示水电解工艺流程的控制特点和图L-2的水电解设备虬及市场篙 求,采用的远程控制系统如图1-3所示。主要采用工业以太阿技术和西门子公司的PROFIBUS
远程控制软件对远方服务器进行控制,也可以利用太陆制氢公司自主开发的远程控制软件进 行控制。既保证了远程控制的功能,叉保证了系统的可靠性运行。
本项目具有以下显著优越性:①通过构建现场中央控制平台、设计相关软件程序、分类 处理通讯数据进而集中调控菩装置的运行状态,实现了分散站点的无人值守,提高了设备运 行可靠性;②利用远程控制系统进行故障诊断,提供在线点持和控制软件升级服务,有利于
水电解制氢装置工艺流程

水电解制氢装置工艺流程第三节水电解制氢装置工艺流程水电解制氢装置由电解槽、气液处理器、整流装置、控制柜(计算机管理系统)、加水泵、碱箱、水箱等组成。
气体系统的工艺流程如下:当电解槽接通直流电源后,电解电流上升到一定数值时,电解槽内的水被电解成氢气和氧气。
制氢量大于等于80m3/h的氢气和碱液从电解小室阴极侧进入氢分离洗涤器的分离段,然后在重力的作用下氢气和碱液分离。
分离后的气体经过冷却、洗涤(制氢量大于等于175m3/h的无需洗涤)和除雾,进入贮罐待用(对CNDQ型制氢装置,气体再经过干燥处理才进入贮罐)。
氧气分离过程基本相同。
氧气放空或进入贮罐待用。
电解液循环系统的目的在于向电极区域补充电解消耗的纯水,带走电解过程中产生的氢气、氧气和热量,增加电极区域电解液的搅拌,减少浓差极化电压,降低碱液中的含气度,降低小室电压,减少能耗等,以使电解槽在稳定条件下工作。
碱液循环量的大小影响槽内小室电压和气体纯度。
对于一个特定的电解槽,应有一个合适的循环量。
一般槽内电解液更换次数每小时2~4次。
在常压电解系统中,通常用自然循环,而在压力电解系统中,采用强制循环。
气体排空(氮气置换)系统用于系统的气密检查与开机前的氮气置换。
制氢系统开车后,氢气纯度达到要求后才能被送到贮罐(或净化设备),在未达到要求纯度以前的氢气可通过调节阀后的气体放空阀放空。
原料水补充系统用于保证水电解的连续进行。
水箱中的水通过加水泵分别打入氢、氧洗涤器,然后通过溢流管,注入分离器下部的液相部分和循环碱液一并进入电解小室进行连续电解,同时使电解液中碱的浓度保持在最佳浓度范围。
原料水首先注入洗涤器,然后溢流到分离器,这样可以稀释洗涤器中的碱含量,降低产品中的气的含碱度。
为了防止水电解制氢装置压力系统中的气体和碱液在加水泵停转期间外漏,加水管道上都装有止回阀。
在运行过程中,只需要开启单个补水回路,即只开氢侧或氧侧补水回路。
2.5排污系统排污管道共分为四处:第一处:碱液过滤器底部,通过过滤器排污阀排出碱液和过滤下来的石棉绒杂质及污物。
电解水制氢装置分析

电解水制氢装置分析
一、电解水制取氢装置结构
电解水制取氢的装置主要有电极、溶液容器、控制器、电源、气体收
集管线、氢气和氧气压缩机、氢气分配器和氧气分配器等组成。
电极包括
电极材料、电极支架和连接器,电极材料有锂钛石猪笼状结构和聚乙烯四
氟乙烯晶格状结构等,型号有柱状和片状;溶液容器主要用来安装电极和
储存溶解液,常用材料有碳钢、不锈钢、钛合金、氟塑料及塑料等;控制
器用于控制和维护整套电解装置,其功能包括电压控制、温度控制和缓蚀
保护等;电源可以是电网电源也可以是发电机电源,用以提供电解装置运
行所需的电能;气体收集管线用来将产生的氢气和氧气连接到气体压缩机;气体压缩机用以将氢气和氧气的压力增加,使其能够被安全运输、分配和
储存;氢气分配器和氧气分配器分别用于将氢气和氧气导向相应的应用场合。
二、电解水制取氢装置原理
电解水制取氢的装置利用电极将水分解成氢气和氧气,这是一种不用
燃料就能将水分解成氢气和氧气的方式。
当水在电极上受到电场的作用时,水分子被彻底解离,水分子的原子组成了氢气和氧气。
水电解制氢AEM自动控制系统设计
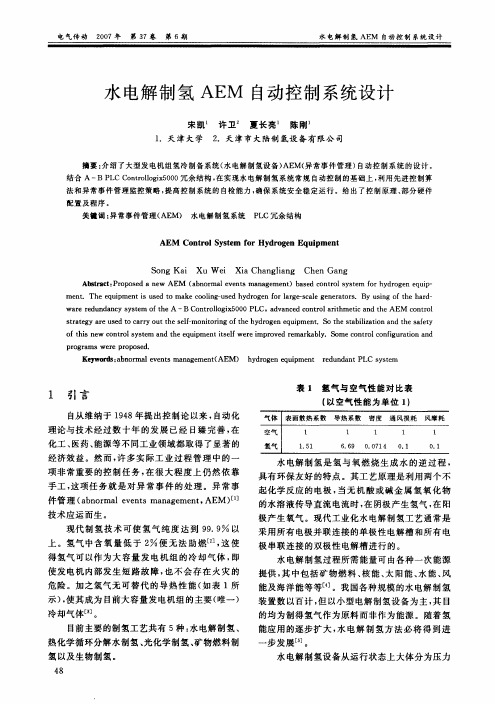
FP 一Nol PU FB [ . CT A i - SN ! } iB F" w M' 2 R Rt N2 2 l l R N C E m
图 2 双 C U冗余控制的硬件解决方案示意图 P
电气传动 20 年 07
第3 卷 7
第6 期
1 引言
自 14 年提出控制论以来, 从维纳于 98 自动化 理论与技术经过数十年的发展已经 日臻完善, 在 化工、 医药、 能源等不同工业领域都取得了显著的 经济效益。然而, 许多实际工业过程管理中的一 项非常重要的控制任务, 在很大程度上仍然依靠 手工, 这项任务就是对异常事件的处理。异常事
水电解制氢是氢与氧燃烧生成水的逆过程 具有环保友好的特点。其工艺原理是利用两个不 起化学反应的电极, 当无机酸或碱金属氢氧化物 的水溶液传导直流电流时, 在阴极产生氢气, 在阳 极产生氧气。现代工业化水电解制氢工艺通常是 采用所有电极并联连接的单极性电解槽和所有电 极串联连接的双极性电解槽进行的。
水电解制氢过程所需能量可由各种一次能源 提供, 其中包括矿物燃料、 核能、 太阳能、 水能、 风
图 1 水电解制氢控制系统结构图
C U模块插在不同的 2 P 个机架上, 每个机架上除
了 C U模块外 , P 还需有通讯模块 C B 、 N R 同步模
21 控制系统功能要求 . 正常运行时, 除了按工艺要求保证系统各设 备的启停, 运行状态的显示, 各工艺参数的显示 外, 对氢站控制系统的主要功能要求还包括:) 1系 统应能使合格的氢气进人氢气储存系统, 不合格 的氢气 自 动安全地排人大气;) 2 系统在储氢装置 压力超过设定值时自动停止充氢, 低于设定值时 自动启动充氢;) 3系统设有所有必要的事故报警、 自 动联锁保护功能, 且在设备停运时具有闭锁功 能, 避免误报警;) 4如果控制系统程序发生异常故 障, 控制系统应能 自动在 1 s 0 内对系统进行 自动 复位, 并切断整流柜电源, 使系统 自动保压, 由充 罐状态转到排空状态;) 5控制系统应能接受 2 个 受控制氢站火灾报警信号, 并发出远程报警信号。
高压电解水控制系统设计

摘 要随着科学技术的发展和人类生活水平的提高,清洁能源受到人们越来越多的关注,可再生、无污染逐渐成为选择能源的重要标准之一。
经长期研究发现,氢气是最理想的能源之一。
首先,氢气的热效率较高;其次,氢气燃烧后产物是水,没有任何污染物产生,是一种清洁性的能源。
目前,电解水普遍采用的方法是双电解槽电解法,该方法由于隔膜的存在,无法承受较大的压强,更不能产生高压下的氢气和氧气。
本文所描述的是一款用于实现高压电解水设备自动运行的控制系统的设计。
该设备由电解槽、氢气储气仓、氧气储气仓、水箱、连接管及九路开关构成,采用从乌克兰引进的新型铁镍合金电极材料。
该电极材料可在单电解槽中电解水,间接性产生氢气和氧气,实现氢气和氧气的时空分离。
现在工业电解水每产生1标准立方米氢气和0.5标准立方米氧气所消耗的电能平均约为4.5kwh,该电极材料耗能约为 4.1kwh,处于较低水平。
此外,该电极材料可产生压强为10MPa 以上的气体,不需外界加压就能实现高压储存气体,解决了双电解槽电解水中由于隔膜作用而不能达到高压的难题。
该电极材料相当于一个变阻负载,产生同一种气体时,随时间的推移而电阻逐渐变大。
在产生氢气时,需要为电极材料提供0.4V~1.4V的恒流电源;在产生氧气时,需要为电极材料提供-0.6V~-1.6V的恒流电源。
该系统通过实时检测电极电压、电极电流、氢气储气仓和氧气储气仓的压强以及氢气储气仓和氧气储气仓的液位高度,实现自动控制电流参数的调整、电极电位的转换、电磁阀开关的开合、设备加水以及故障提示等功能,并可以通过外部8个按钮实现人工操作。
此外,为方便了解设备的工作状态,使用液晶屏实时显示系统采集的数据信息;为能实现远程监控,使用C#语言开发了上位机显示与控制界面。
本文给出了控制系统的硬件设计与软件设计,并进行了系统的实际测试和数据的采集与分析。
本设计从模块上划分为:外部信号输入模块、控制信号输出模块、电极电源模块、信号采集模块、设备信息显示模块以及上位机界面开发。
中压水电解制氢装置控制系统改造分析

中压水电解制氢装置控制系统改造李兰峰(南阳鸭河口发电有限责任公司河南南阳474671)摘要:介绍了南阳鸭河口发电有限责任公司制氢装置的配置,原气动控制系统存在的问题及在改造前的运行状况;简要介绍了国内制氢装置控制系统方式及鸭电公司制氢装置控制系统最终改造方式的确定,提出并阐述了将鸭电公司制氢装置原气动控制系统改造为PLC +上位机的控制系统;并对改造后达到的效果及存在的问题进行了介绍。
关键词:制氢装置;可编程控制器;上位机;iFIX监控软件;程序控制目前,国内很多大型机组发电机的冷却方式采用水-氢-氢冷却方式,氢气冷却具有比重小、导热系大,通风损耗和通风噪声小的特点,所以氢气冷却在火电厂汽轮发电机组冷却方式的选用上得到了广泛应用。
由于发电机内氢气必须维持规定纯度需定期排污,运行过程中也有部分氢气泄漏,因此需要及时补充新鲜氢气,所以一般火电厂都配备有制氢装置,而应用最广泛的是水电解制氢装置。
1南阳鸭电公司制氢装置简介及存在问题的探讨1.1南阳鸭河口发电有限责任公司(以下简称南阳鸭电公司)制氢装置简介南阳鸭电公司安装2*350MW燃煤机组,汽轮发电机组采用水-氢-氢冷却方式。
配套制氢站安装一套ZHDQ3.2/10型中压水电解制氢装置,以电解槽为主体,主要附属设备包括氢气分离洗涤器、氧气分离洗涤器、氢气冷却器、碱液冷却器、碱液过滤器、碱液循环泵等。
同时配套的还有可控硅整流柜、控制柜、原料水箱、碱液箱、补水泵、储氢罐、型氢气干燥装置。
1.2水电解制氢原理简介电解制氢的原理是将直流电通入含有电解液的水中,使水电解为氢气和氧气。
其反应式为: 阴极:2H2O+2e→H2↑+2OH-阳极:20H--2e→H2O+(1/2)O2↑总反应式:2H2O→2H2↑+O2↑南阳鸭电公司水电解制氢装置采用硅整流柜将380V AC电源整流为72VDC电源,供电解槽使用,正常制氢工作压力为2.80MPa。
电解槽以NaOH作为电解质,电解除盐水来获得高纯度的氢气,经干燥装置脱湿后,送入发电机,以满足350MW机组氢气冷却需要。
章水电制氢控制系统

第十五章水电解制氢自动控制系统第一节水电解制氢干燥装置自动控制系统成水电解制氢及干燥装置的自动控制系统一般地,是由本地上位数据管理机、制氢控制柜、动力柜及现场控制仪器、仪表等组成,由此完成水电解制氢及干燥装置的系统控制及运行数据管理。
装置的各个运行数据是由安装在制氢控制柜内的可编程序控制器(PLC)进行采集、处水电解制氢及干燥装置所用的现场自控仪器、仪表按位置可分为四个部分:框架1,即制氢及干燥装置主体,包括电解槽槽体、气液分离器、氢气洗涤器、碱液循环泵、氢气干燥塔(A塔及B塔)、冷却器等;框架2,即产品氢配气装置,经干燥后合格的产品氢气经此装置进入氢气储罐或向发电机组补氢;框架3,包括原料水箱、碱液箱及系统加水泵;氢气储罐等。
(1)框架1:本部分的自控仪器、仪表主要有以下四类:变送器:包括压力变送器、差压变送器(氢液位变送器及氧液位变送器)、铂电阻等。
装置的工作压力经压力变送器后变成4~20mA的电信号传送到制氢控制柜;两套差压变送器分别把氢气液分离器中的氢液位及氧气液中的分离器中的氧液位变换成标准的4~20mA信号传送到制氢控制柜;铂电阻共有五支,一支用来测量装置运行时循环碱液的温度。
两支分别用来测量干燥A塔和干燥B塔的上部温度,还有两支分别用来测量干燥A塔和干燥B塔的上部温度信号全部送入制氢控制柜。
●执行器:包括有三个气动薄膜调节阀及七个气动球阀。
●检测仪表:包括氢中氧分析仪、氧中氢分析仪及氢气露点仪等。
●防爆电接点压力表或压力开关:一般设置了两块压力表,其中一块用来检测装置运行时的氢阀后压力,当氢阀后压力超过了报警设定值时,氢阀后压力超限报警信号即送入制氢控制柜内;另一块作用是,当自动控制系统失灵时,用来检测装置运行时的系统压力,并由此发出联锁信号直接传送给整流柜,切断整流柜的输出电流,起到二次保护的作用。
(2)框架2:框架2上的自控仪器、仪表及执行器机构视不同的要求进行的配置:当要求自动充罐功能且氢气储罐进行选择时,则对应每一个氢气储罐,此框架上安装一个气动球阀及一个压力变送器;当要求具有自动向发电机组自动补氢功能时,则在每一个补氢管路上增加一个气动球阀,补氢母管上安装一套压力变送器。
pdf 水电解制氢设备 说明书
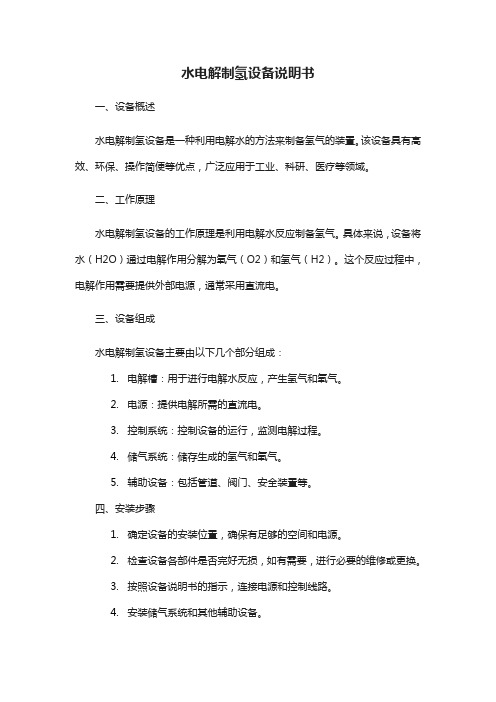
水电解制氢设备说明书一、设备概述水电解制氢设备是一种利用电解水的方法来制备氢气的装置。
该设备具有高效、环保、操作简便等优点,广泛应用于工业、科研、医疗等领域。
二、工作原理水电解制氢设备的工作原理是利用电解水反应制备氢气。
具体来说,设备将水(H2O)通过电解作用分解为氧气(O2)和氢气(H2)。
这个反应过程中,电解作用需要提供外部电源,通常采用直流电。
三、设备组成水电解制氢设备主要由以下几个部分组成:1.电解槽:用于进行电解水反应,产生氢气和氧气。
2.电源:提供电解所需的直流电。
3.控制系统:控制设备的运行,监测电解过程。
4.储气系统:储存生成的氢气和氧气。
5.辅助设备:包括管道、阀门、安全装置等。
四、安装步骤1.确定设备的安装位置,确保有足够的空间和电源。
2.检查设备各部件是否完好无损,如有需要,进行必要的维修或更换。
3.按照设备说明书的指示,连接电源和控制线路。
4.安装储气系统和其他辅助设备。
5.完成安装后,进行必要的调试和测试,确保设备正常运行。
五、操作流程1.开启设备前,检查所有部件是否正常,确保电源已连接。
2.打开电源开关,启动设备。
设备将自动进行电解水反应,生成氢气和氧气。
3.观察电解过程,确保没有异常情况发生。
如有异常,立即关闭电源,检查并排除故障。
4.当储气系统达到一定压力时,可以开始使用氢气或氧气。
5.使用完毕后,关闭电源,结束设备的运行。
六、维护保养为了确保设备的正常运行和使用安全,建议定期进行以下维护保养工作:1.清洁设备表面,保持整洁。
2.检查电解槽和储气系统,确保没有泄漏或损坏。
3.定期检查电源和控制线路,确保连接牢固,没有破损。
4.根据使用情况,适时更换电解槽中的电极。
5.定期对设备进行全面检查和调试,确保设备性能良好。
七、常见问题及处理1.电解效率下降:可能是由于电极老化或电解液浓度降低,需要更换电极或调整电解液浓度。
2.设备漏气:可能是由于密封圈老化或损坏,需要更换密封圈。
- 1、下载文档前请自行甄别文档内容的完整性,平台不提供额外的编辑、内容补充、找答案等附加服务。
- 2、"仅部分预览"的文档,不可在线预览部分如存在完整性等问题,可反馈申请退款(可完整预览的文档不适用该条件!)。
- 3、如文档侵犯您的权益,请联系客服反馈,我们会尽快为您处理(人工客服工作时间:9:00-18:30)。
加压水电解制氢装置控制系统
(天津市大陆制氢设备有限公司许卫) 摘要:本文叙述了水电解制氢控制系统控制点的选择及各种控制方式。
关键词:水电解制氢控制系统
电解水是直流电通过KOH或NaOH水溶液将水分解为氢气和氧气的过程,其化学反应如下:阴极:2H2O+2e→H2+2OH-;阳极:2OH --2e→H2O+1/2O2;
总反应式:H2O= H2+ 1/2O2
水电解制氢装置所制氢气作为冷却气、保护气、原料气、还原气和燃料气,已广泛用于电力、电子、冶金、化工、建材、宇航、原子、气象等需要氢气的行业。
我国自行生产加压水电解制氢装置已有四十年的历史,其控制系统随着仪表、控制系统的发展而不断更新。
控制点的选择,控制方式的选择经过多年实践运行,被证明是安全可靠的,是可以满足工艺要求的。
一控制点
1 被调参数的选择
被调参数的选择是自动控制系统设计的核心部分,它直接影响调节质量,是装置稳定运行的保证。
结合多年的压力电解槽开发实践,确定如下被调参数:槽压调节、循环碱温调节、氢氧分离器液位调节系统。
1. 1 槽压调节系统
操作压力是装置的主要被调参数,必须设置调节系统,使其维持在恒定值。
选用氧气压力为被调参数,氧气流量为调节参数,采用压力变送器,调节仪和气动薄膜调节阀构成单回路调节系统。
变送器取压点设在氧分离器顶部,调节阀安装在氧气出口管道上。
调节仪为比例、积分、微分式(正作用),调节阀为气开式。
1. 2 循环碱温调节系统
电解槽温度也是装置的一个重要参数。
实践证明,在气体产量,环境温度和碱液循环量固定的情况下,槽温和循环碱温有一个恒定的差值,因此可以利用调节循环碱温来达到调节槽温的目的。
温度变送器安装在循环碱液管道上,其输出信号送到调节仪,调节仪输出控制安装在冷却水管道上的调节阀,调节仪为比例、积分式(反作用),调节阀为气闭式。
1. 3 氢分离器液位调节系统
在电解过程中,原料水不断消耗,使氢氧分离器液位不断下降,因此需要通过补水泵补充原料水,而使液位维持在适当的高度。
本系统是一个双位调节系统,氢分离器液位由差压变送器测量,并通过联锁电路控制补水泵的开停,从而使液位维持在一定的范围内。
1. 4 氧分离器液位调节系统
本系统的任务是控制分离器液位,使氧分离器液位与氢分离器液位高度相同。
氧分离器液位由差压变送器测量。
差压变送器、调节仪和调节阀(安装在氢气出口管道上)组成单回路调节系统。
调节仪采用外给定,以氢液位变送器的输出信号作为调节阀的外给定信号,调节仪为比例、积分、微分式(正作用),调节阀为气开式。
2 检测系统
氢槽温、氧槽温、循环碱温、氢气纯度、氧气纯度、等参数在控制柜上进行显示;操作压力、氢液位、氧液位等参数除在控制柜设有显示仪表外,在现场还直接进行显示。
氢气温、氧气温、氢侧碱液循环量、氧侧碱液循环量等参数均为现场直接显示。
3 声光报警系统
电解槽工作压力上限,氧槽温超高,氢氧液位上、下限,氢氧侧碱液循环量下限,气源压力下限,氢气纯度下限,氧纯度下限等参数均设有声光报警。
4 联锁系统
槽压超高,氧槽温超高,氢、氧碱液循环量下限直接处于联锁状态,而氢液位上、下限,氧液位上、下限在装置开始运行时处于联锁消除状态,在装置正常运行后处于联锁状态,均直接联锁整流柜。
槽压超高,氢、氧液位上、下限,氧槽温超高,氢、氧碱液循环量下限,整流柜故障均联锁补水泵停止加水。
二控制方式
1 气动控制系统
早期的水电解控制系统采用气动控制方式,变送器和调节器采用气动单元组合仪表;报警和联锁部分采用继电器。
由于一次仪表和二次仪表折线距离不超过50米,气动管线较短,所以响应速度可以满足控制要求。
价格便宜,没有防爆问题,安全性好。
但现在订货已很少。
现在气动控制系统的报警和联锁部分一般采用可编程序控制器代替继电器
2 电III型控制系统
变送器和调节器采用电III型仪表,仪表间的联络信号为4-20mA。
由于使用本质安全型仪表,所以安全上没有问题。
精度一般为0.5%,比气动仪表要高,气动仪表为1%。
3 PLC控制系统
PLC是英文PROGRAMMABLE LOGIC CONTROLLER(可编程序控制器)的缩写。
它是计算机家族中的一员,是为工业控制应用而设计制造的。
早期的可编程控制器主要用来代替继电器实现逻辑控制。
随着技术的发展,这种装置的功能已经大大超过了逻辑控制的范围。
它连续检测输入设备(如开关、变送器等)的状态,根据用户的程序控制输出设备(如泵、调节阀等)。
修改控制逻辑时不需增加硬件和重新接线。
为现在应用最多的控制系统,一般变送器仍采用电III 型变送器,而调节系统和报警联锁系统由PLC完成。
人机接口采用工业控制计算机或触摸屏。
对于可编程控制器有多种品牌和型号,在水电解行业用到了西门子S7-400、S7-300、S7-200系列;施奈德的Quantum系列;罗克韦尔公司的ControlLogix系列;通用电气90-70、90-30系列。
对于PLC控制系统来讲,并不是越高级越好,控制系统越高级,价格也就越高。
不同的型号,应用的场合是不一样的。
以西门子PLC为例,对于S7-400系列,当需要CPU 冗余时才用到,而现在CPU出问题的可能性很小,只有在对于控制系统稳定性要求极其严格的情况下才使用。
而对于水电解制氢系统,当要求连续不间断供氢时,可以通过工艺流程的设置,而不是升级PLC控制系统来实现,升级PLC成本太高。
笔者认为S7-300系列足以满足控制要求。
在制氢设备的控制系统里,电厂氢站的要求是最高的,5-10m3/h制氢和干燥一体化设备。
一般都是PLC控制,所有现场变送器选用进口,PLC控制系统CPU冗余、电源冗余、通讯冗余。
一键开车,即按下开车按钮,设备自动充氮置换、升温、升压、气体纯度合格后,自动向储罐充氢。
两个CPU各有自己的以太网模版,有不同的IP地址,通过交换机、光纤将参数传输到几百米,甚至上千米外的集控室。
远程控制软件有多种,在制氢行业也有应用。
我们一般用PCanywhere。
在现场用于控制的计算机上安装上PCanywhere作为被控端,在我们的笔记本电脑上安装好PCanywhere主控端,两台电脑通过调制解调器用电话线连接起来,在我们的笔记本电脑上可以看到远控端电
脑的桌面,可以用笔记本的鼠标来操作远控端电脑,就像你坐在远控端电脑旁,利用此方法,我们可以上传和下载PLC程序,远程监视设备运行参数。
这样可以迅速判断故障原因,坐在办公室内就可以对现场程序进行修改。
4 DCS控制系统
DCS为分布式控制系统的英文缩写,主要应用在控制规模很大的系统。
DCS控制系统应用制氢行业较少,用户主要集中在石化行业和电厂。
石化厂一般都有DCS控制系统,在制氢设备的控制上,有的厂家仅要求制氢设备带一次仪表,所有信号进入用户的DCS系统,而设备的控制由制氢设备厂家提出控制要求,提供逻辑图。
由设备制造厂和DCS编程人员共同完成设备的调试工作。
对于电厂,发电机组的控制都是由DCS系统完成的,而氢站是电厂的辅助系统,一般用普通PLC进行控制,而现在有的也用单独的DCS控制。
5 现场总线控制系统
现场总线(Fieldbus)是以单个分散的、数字化、智能化的测量和控制设备作为网络节点,用总线相连接,实现相互交换信息,共同完成自动控制功能的网络系统与控制系统。
传统的现场级自动化监控系统采用一对一所谓I/O接线方式,传输的是4-20mA或24VDC信号。
现场总线使用一根通信电缆,将所有具有统一的通信协议通信接口的现场设备连接,在设备层传递的不再是I/O(4-20mA/24VDC)信号,而是基于现场总线的数字化通信,由数字化通信网络构成现场级自动化监控系统。
现场总线系统有它自己的优势,但由于是一种新兴的技术,在水电解制氢领域还未大规模使用。