硫回收尾气处理工艺分析与选择
硫磺回收系统的操作要求和工艺指标

一、制硫工艺原理硫磺回收系统的操作要求和工艺指标Claus制硫总的反应可以表示为:2H2S+02/X S x+2H20在反应炉内,上述反应是部分燃烧法的主要反应,反应比率随炉温变化而变化,炉温越高平衡转化率越高;除上述反应外,还进行以下主反应:2H2S+3O2=2SO2+2H2O在转化器中发生以下主反应:2H2S+SO23/XS x+2H2O由于复杂的酸性气组成,反应炉内可能发生以下副反应:2S+2CO2COS+CO+SO22CO2+3S=2COS+SO2CO+S=COS在转化器中,在300摄氏度以上还发生CS2和COS的水解反应:COS+H2O=H2S+CO2二、流程描述来自上游的酸性气进入制硫燃烧炉的火嘴;根据制硫反应需氧量,通过比值调节严格控制进炉空气量,经燃烧,在制硫燃烧炉内约65%(v)的H2S进行高温克劳斯反应转化为硫,余下的H2S中有1/3转化为SO2燃烧时所需空气由制硫炉鼓风机供给。
制硫燃烧炉的配风量是关键,并根据分析数据调节供风管道上的调节阀,使过程气中的H2S/SO2比率始终趋近2:1,从而获得最高的Claus转化率。
自制硫炉排出的高温过程气,小部分通过高温掺合阀调节一、二级转化器的入口温度,其余部分进入一级冷凝冷却器冷至160℃,在一级冷凝冷却器管程出口,冷凝下来的液体硫磺与过程气分离,自底部流出进入硫封罐。
一级冷凝冷却器管程出口160℃的过程气,通过高温掺合阀与高温过程气混合后,温度达到261℃进入一级转化器,在催化剂的作用下,过程气中的H2S和SO2转化为元素硫。
反应后的气体温度为323℃,进入二级冷凝冷却器;过程气冷却至160℃,二级冷凝冷却器冷凝下来的液体硫磺,在管程出口与过程气分离,自底部流出进入硫封罐。
分离后的过程气通过高温掺合阀与高温过程气混合后温度达到225℃进入二级转化器。
在催化剂作用下,过程气中剩余的H2S和SO2进一步转化为元素硫。
反应后的过程气进入三级冷凝冷却器,温度从246℃被冷却至1.60~C。
硫回收尾气处理技术及超级克劳斯工艺
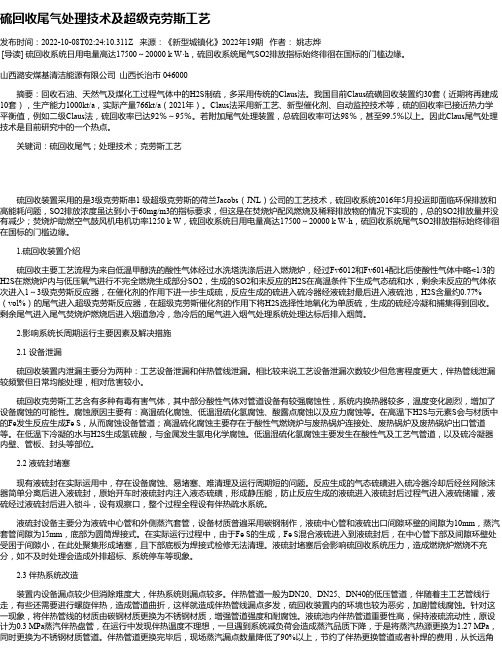
硫回收尾气处理技术及超级克劳斯工艺发布时间:2022-10-08T02:24:10.311Z 来源:《新型城镇化》2022年19期作者:姚志烨[导读] 硫回收系统日用电量高达17500~20000 k W·h,硫回收系统尾气SO2排放指标始终徘徊在国标的门槛边缘。
山西潞安煤基清洁能源有限公司山西长治市 046000摘要:回收石油、天然气及煤化工过程气体中的H2S制硫,多采用传统的Claus法。
我国目前Claus硫磺回收装置约30套(近期将再建成10套),生产能力1000kt/a,实际产量766kt/a(2021年)。
Claus法采用新工艺、新型催化剂、自动监控技术等,硫的回收率已接近热力学平衡值,例如二级Claus法,硫回收率已达92%~95%。
若附加尾气处理装置,总硫回收率可达98%,甚至99.5%以上。
因此Claus尾气处理技术是目前研究中的一个热点。
关键词:硫回收尾气;处理技术;克劳斯工艺硫回收装置采用的是3级克劳斯串1 级超级克劳斯的荷兰Jacobs(JNL)公司的工艺技术,硫回收系统2016年5月投运即面临环保排放和高能耗问题,SO2排放浓度虽达到小于60mg/m3的指标要求,但这是在焚烧炉配风燃烧及稀释排放物的情况下实现的,总的SO2排放量并没有减少;焚烧炉助燃空气鼓风机电机功率1250 k W,硫回收系统日用电量高达17500~20000 k W·h,硫回收系统尾气SO2排放指标始终徘徊在国标的门槛边缘。
1.硫回收装置介绍硫回收主要工艺流程为来自低温甲醇洗的酸性气体经过水洗塔洗涤后进入燃烧炉,经过Fv6012和Fv6014配比后使酸性气体中略<1/3的H2S在燃烧炉内与低压氧气进行不完全燃烧生成部分SO2,生成的SO2和未反应的H2S在高温条件下生成气态硫和水,剩余未反应的气体依次进入1~3级克劳斯反应器,在催化剂的作用下进一步生成硫,反应生成的硫进入硫冷器经液硫封最后进入液硫池,H2S含量约0.77%(vol%)的尾气进入超级克劳斯反应器,在超级克劳斯催化剂的作用下将H2S选择性地氧化为单质硫,生成的硫经冷凝和捕集得到回收。
硫磺回收装置尾气处理工艺探讨
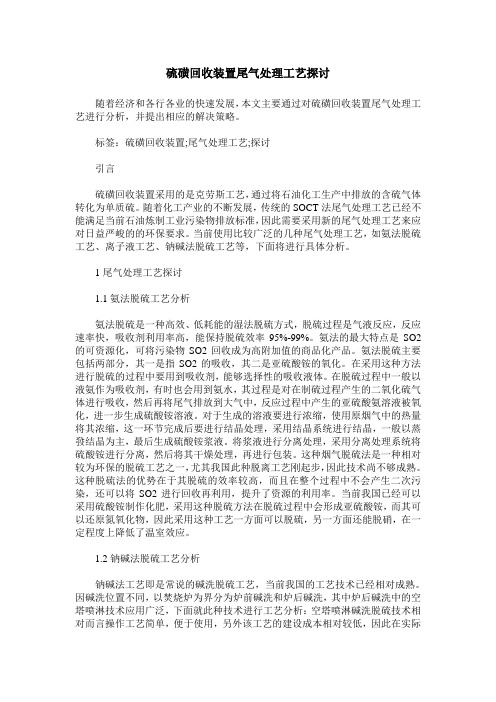
硫磺回收装置尾气处理工艺探讨随着经济和各行各业的快速发展,本文主要通过对硫磺回收装置尾气处理工艺进行分析,并提出相应的解决策略。
标签:硫磺回收装置;尾气处理工艺;探讨引言硫磺回收装置采用的是克劳斯工艺,通过将石油化工生产中排放的含硫气体转化为单质硫。
随着化工产业的不断发展,传统的SOCT法尾气处理工艺已经不能满足当前石油炼制工业污染物排放标准,因此需要采用新的尾气处理工艺来应对日益严峻的的环保要求。
当前使用比较广泛的几种尾气处理工艺,如氨法脱硫工艺、离子液工艺、钠碱法脱硫工艺等,下面将进行具体分析。
1尾气处理工艺探讨1.1氨法脱硫工艺分析氨法脱硫是一种高效、低耗能的湿法脱硫方式,脱硫过程是气液反应,反应速率快,吸收剂利用率高,能保持脱硫效率95%-99%。
氨法的最大特点是SO2的可资源化,可将污染物SO2回收成为高附加值的商品化产品。
氨法脱硫主要包括两部分,其一是指SO2的吸收,其二是亚硫酸铵的氧化。
在采用这种方法进行脱硫的过程中要用到吸收剂,能够选择性的吸收液体。
在脱硫过程中一般以液氨作为吸收剂,有时也会用到氨水,其过程是对在制硫过程产生的二氧化硫气体进行吸收,然后再将尾气排放到大气中,反应过程中产生的亚硫酸氨溶液被氧化,进一步生成硫酸铵溶液。
对于生成的溶液要进行浓缩,使用原烟气中的热量将其浓缩,这一环节完成后要进行结晶处理,采用结晶系统进行结晶,一般以蒸發结晶为主,最后生成硫酸铵浆液。
将浆液进行分离处理,采用分离处理系统将硫酸铵进行分离,然后将其干燥处理,再进行包装。
这种烟气脱硫法是一种相对较为环保的脱硫工艺之一,尤其我国此种脱离工艺刚起步,因此技术尚不够成熟。
这种脱硫法的优势在于其脱硫的效率较高,而且在整个过程中不会产生二次污染,还可以将SO2进行回收再利用,提升了资源的利用率。
当前我国已经可以采用硫酸铵制作化肥,采用这种脱硫方法在脱硫过程中会形成亚硫酸铵,而其可以还原氮氧化物,因此采用这种工艺一方面可以脱硫,另一方面还能脱硝,在一定程度上降低了温室效应。
关于硫回收工艺总结

当前硫回收方法主要有湿法和干法脱硫,干法又分为:传统克劳斯法、亚露点类克劳斯工艺,还原吸收类工艺、直接氧化类克劳斯工艺、富氧克劳斯工艺、和氧化吸收类克劳斯工艺;湿法主要有鲁奇的低、高温冷凝工艺、托普索的WSA工艺。
1干法脱硫1.1常规克劳斯(Claus)法克劳斯法是一种比较成熟的多单元处理技术,是目前应用最为广泛的硫回收工艺。
其工艺过程为:含有硫化氢的酸性气体在克劳斯炉内燃烧,使部分硫化氢氧化为二氧化硫,二氧化硫再与剩余的未反应的硫化氢在催化剂上反应生成硫磺。
传统克劳斯法的特征为:1)控制n(O2):n(H2S)=1:2,若氧气含量过高有SO2溢出,过低则降低H2S的脱除效率;2)需要安装除雾器脱除气流中的硫以提高硫回收量;3)克劳斯法硫总回收率为94%-96%;4)对含可燃性成分的气体如煤气,或当硫质量分数低于40%时不宜用克劳斯法。
1.2亚露点类克劳斯工艺所谓的亚露点工艺是以在低于硫露点的温度下进行克劳斯反应为主要特征的工艺。
主要包括Sulfreen、Hydrosulfreen、Carbonsulfreen、Oxysulfreen、CBA、ULTRA、MCRC、Clauspol 1500、Clauspol 300、Clisulf SDP、ER Claus、Maxisulf等工艺。
1.3还原吸收类工艺还原吸收类工艺由于将有机硫及SO2等转化为H2S再行吸收,故总硫回收率可达99.5%以上。
主要有SCOT、Super-SCOT、LS-SCOT、BSR/Amine、BSR/Wet Oxidation、Resulf、AGE/Dual Solve、HCR、Parsons/BOC Recycle、Sulfcycle和ELSE工艺。
1.4直接氧化类工艺直接氧化是指H2S在固体催化剂上直接氧化成硫,实际上乃是克劳斯原型工艺的新发展。
直接氧化法工艺技术的关键是研制出选择性好、对H2O 和过量O2不敏感的高活性催化剂,目前用铁基金属氧化物的不同混合物制备。
常见硫磺回收及尾气处理技术

常见硫磺回收及尾气处理技术本文系统的介绍常见的硫磺回收及尾气处理技术,旨在拓宽大家的视野,请根据操作规程或本文资料做好如下题目:1、本装置制硫催化剂和尾气加氢催化剂是什么?2、本装置一、二级转化器入口温度控制在多少度?3、为什么要保证加氢尾气氢气含量2~6%?4、C-302尾气采用什么方法进行处理?5、在线分析仪坏应该如何配风?随着我国国民经济的快速增长,我国的石油、天然气工业也得到高速发展。
与此同时,含硫原油加工量和含硫天然气处理量随之相应增加,从2000年至今国内硫磺回收装置从62套猛增到100多套,其中万吨级以上大型硫磺回收和尾气处理装置已有60多套,年加工回收硫磺能力已由80万t/a增长到约200万t/a,带尾气处理的硫磺回收装置(石油、石化系统)占装置总量的93%,因此,伴随着产生的脱硫与硫磺回收技术问题是不容忽视的。
在该技术领域,我国经过几十年的发展,在依靠自身力量开发脱硫、硫磺回收及尾气处理工艺的同时,先后全套或部分引进国外先进技术。
经过消化吸收,我们已经形成配套的脱硫、硫磺回收及尾气处理工艺技术,但与国外先进水平相比仍然存在一定差距。
本文参考部分已出版的硫磺回收协作组相关论文资料,在此基础上,经过2003—2006年的专利文摘检索,从脱硫、硫磺回收和尾气处理工艺及催化剂几个方面进行了详细的介绍。
重点指出,要根据某些行业及现有引进技术的需要,应加快SuperClaus、富氧Claus工艺、RAR工艺等硫回收及尾气处理技术消化吸收,积极推广国内自主开发的SSR工艺,并开展进一步提高硫回收率的研究。
根据不同反应器过程气组成、操作温度不同的特点,开发并完善Claus反应转化率高、有机硫水解性能好的系列硫磺回收催化剂,加快低成本、高性能硫磺回收催化剂的开发研究步伐。
原油加工与硫磺回收我国是一个原油资源并不丰富的国家,在市场经济条件下,各大炼油厂(尤其是沿海、沿江炼油厂)由过去的以加工低硫原油为主向加工含硫原油转变。
硫回收技术选择浅析
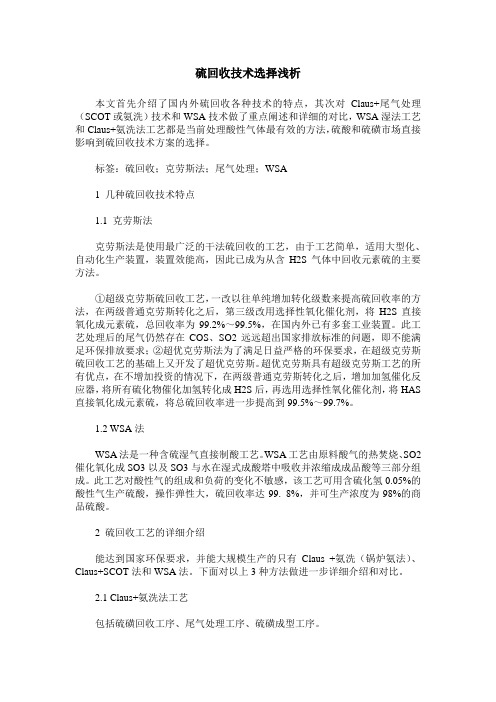
硫回收技术选择浅析本文首先介绍了国内外硫回收各种技术的特点,其次对Claus+尾气处理(SCOT或氨洗)技术和WSA技术做了重点阐述和详细的对比,WSA湿法工艺和Claus+氨洗法工艺都是当前处理酸性气体最有效的方法,硫酸和硫磺市场直接影响到硫回收技术方案的选择。
标签:硫回收;克劳斯法;尾气处理;WSA1 几种硫回收技术特点1.1 克劳斯法克劳斯法是使用最广泛的干法硫回收的工艺,由于工艺简单,适用大型化、自动化生产装置,装置效能高,因此已成为从含H2S气体中回收元素硫的主要方法。
①超级克劳斯硫回收工艺,一改以往单纯增加转化级数来提高硫回收率的方法,在两级普通克劳斯转化之后,第三级改用选择性氧化催化剂,将H2S直接氧化成元素硫,总回收率为99.2%~99.5%,在国内外已有多套工业装置。
此工艺处理后的尾气仍然存在COS、SO2远远超出国家排放标准的问题,即不能满足环保排放要求;②超优克劳斯法为了满足日益严格的环保要求,在超级克劳斯硫回收工艺的基础上又开发了超优克劳斯。
超优克劳斯具有超级克劳斯工艺的所有优点,在不增加投资的情况下,在两级普通克劳斯转化之后,增加加氢催化反应器,将所有硫化物催化加氢转化成H2S后,再选用选择性氧化催化剂,将HAS 直接氧化成元素硫,将总硫回收率进一步提高到99.5%~99.7%。
1.2 WSA法WSA法是一种含硫湿气直接制酸工艺。
WSA工艺由原料酸气的热焚烧、SO2催化氧化成SO3以及SO3与水在湿式成酸塔中吸收并浓缩成成品酸等三部分组成。
此工艺对酸性气的组成和负荷的变化不敏感,该工艺可用含硫化氢0.05%的酸性气生产硫酸,操作弹性大,硫回收率达99. 8%,并可生产浓度为98%的商品硫酸。
2 硫回收工艺的详细介绍能达到国家环保要求,并能大规模生产的只有Claus +氨洗(锅炉氨法)、Claus+SCOT法和WSA法。
下面对以上3种方法做进一步详细介绍和对比。
2.1 Claus+氨洗法工艺包括硫磺回收工序、尾气处理工序、硫磺成型工序。
硫磺回收尾气处理工艺技术措施

分析硫磺回收尾气处理的工艺流程,对生产工艺设备的运行状况进行分析,保证各种硫磺回收设备安全运行,达到设计的作用效果。
同时,设计最佳的尾气处理方案,结合硫磺回收工艺的特点,强化对尾气的处理,使其中的二氧化硫的含量达到环保的标准,促使硫磺回收尾气处理达到更好的效果,满足硫磺回收工艺的技术要求。
1 硫磺回收尾气处理工艺流程国产装置的应用,直接选择氧化硫磺回收装置进行硫磺回收和尾气的处理,设置具有等温和绝热效果的二级反应器,H2S与O2在催化剂作用下直接反应生成硫磺。
回收更多的硫磺,同时将尾气进行处理,优化尾气处理的生产工艺流程,对各个不同的生产单元进行控制,设计最佳的处理程序,促使尾气处理达到更高的标准。
1.1 氧化焚烧单元的生产工艺流程硫磺回收装置来的含硫酸性气体进入焚烧炉,与燃料气和空气混合燃烧后,产生的高温烟气进入烟气冷却器冷却,温度达到230℃左右后去碱洗装置。
经碱洗装置脱硫后排入大气。
烟气冷却器产生的1.5MPa饱和蒸汽在空冷器冷凝后,返回烟气冷却器循环利用。
1.2 碱洗单元的生产工艺流程焚烧后含硫烟气从洗涤塔底部进入,水洗降温除尘后从塔顶出至脱硫塔。
洗涤热水冷却降温后从洗涤塔上部送入,循环使用。
洗涤塔出来的烟气从脱硫塔底部进入,在塔中与从上而下喷淋的NaOH溶液在填料表面接触,将含硫烟气中SO2吸收脱除后,从塔顶直接排放大气。
吸收SO2的富液一部分从脱硫塔顶部返回脱硫塔循环使用,一部分调节塔底液位后送至氧化罐。
脱硫富液与新鲜的N a O H溶液在管道中混合,调节PH值后进入氧化罐,将溶液中的Na2SO3氧化成Na2SO4。
从氧化罐来的硫酸钠溶液直接进中和脱色罐,中和、脱色工作结束后,将溶液送入板框压滤机过滤,除去溶液中的固体杂质,硫酸钠溶液送入产品溶液池。
1.3 蒸发结晶单元的生产工艺流程硫酸钠溶液经过两级预热器加热后,注入一效蒸发器。
在一效加热室和分离室内循环浓缩。
一部分浓缩液排入二效蒸发器,在二效加热室和分离室中循环,进一步浓缩达到过饱和,从而结晶出硫酸钠。
硫磺回收工艺比较

硫磺回收工艺比较部分燃烧四级转化及过程气催化氧化脱硫工艺简述一、工艺技术概况炼油厂含H2S酸性气硫磺回收技术经过几十年的发展,已经非常成熟,目前我国石化和天然气工业主要采用克劳斯法回收硫磺,并配以适宜的尾气处理工艺以达到越来越严格的环境排放要求。
炼油厂加工过程中产生的含H2S酸性气均含有不同浓度的烃类、氨以及较多的CO2气体。
在石油化工企业中一般均采用工艺路线成熟的高温热反应和两级催化反应的克劳斯硫回收工艺,根据酸性气中H2S含量不同,通常采用部分燃烧法和分流法,部分燃烧法是将全部原料气引入制硫燃烧炉,在炉中按制硫所需的O2量严格控制配风比,使H2S在炉中约65%发生高温反应生成气态硫磺。
未反应的H2S和SO2再经过转化器,在催化剂的作用下,进一步完成制硫过程。
对于含有少量NH3及烃类的原料气,用部分燃烧法可将NH3及烃类完全燃烧分解为N2、CO2和H2O,使产品硫磺的质量得到保证。
部分燃烧法工艺成熟可靠,操作控制简单,能耗低,是目前国内外广泛采用的制硫方法。
制硫催化剂的选用是提高转化率的关键。
目前国内外均使用人工合成制硫催化剂,山东讯达化工集团有限公司开发的QS系列人工合成制硫催化剂的性能已达到了目前国外同类催化剂的水平,已在国内石化企业硫磺回收装置上广泛使用。
由于制硫催化剂的性能要求,进入转化器的过程气温度需要控制在220~260℃左右,而经冷凝冷却回收液态硫后的过程气温度为160℃,需提高温度后方可在催化剂作用下完成转化过程。
采用制硫燃烧炉后高温气掺合提高反应温度,方法简单易行,温度控制准确。
为了追求较高的H2S转化率和硫的总回收率,在原来燃烧炉加二级转化的基础上,又发展了三级转化甚至四级转化技术。
研究指出,理论上硫的露点对H2S平衡转化率起决定作用。
因此,H2S所能达到的总转化率取决于最后一个反应器出口过程气的温度。
近代发展的亚露点法(MCRC)和超级克劳斯法(super claus)就是在这一思想支持下发展起来的。
- 1、下载文档前请自行甄别文档内容的完整性,平台不提供额外的编辑、内容补充、找答案等附加服务。
- 2、"仅部分预览"的文档,不可在线预览部分如存在完整性等问题,可反馈申请退款(可完整预览的文档不适用该条件!)。
- 3、如文档侵犯您的权益,请联系客服反馈,我们会尽快为您处理(人工客服工作时间:9:00-18:30)。
亚露点 工艺 , 是指在 低于 硫露 点的条 件下 , 尾气 中 将
的H s和 s 2 0 继续进行 C a s lu 反应 , 生成元素硫 。 该工
艺 总硫 回收率 9 . % 右 。第 三 类 直接 选 择氧 化 工 95 左
21 S oT工 艺 . C
.
2 国 内应 用 较 多 的几 种 工 艺 浅析
自2 世纪 6 0 O年代尾气处 理工艺 问世 以来 , 国内 外开发并实 现工业化 的工艺有 数十种 , 化学原理 可 按
分 为 4大类 : 气还原 吸收工艺 、 尾 低温 Ca s lu 工艺 、 直 接 氧化工艺 和尾气燃烧氨 吸收工艺 。 一类尾气还原 第
艺, 是将 尾气 中的 HS 接氧化成 硫磺 。该工 艺总硫 2直
回收 率 在 9 . % 右 , 目前 国 内 运 用 较 多 的 超 级 95 左
Cas lu 工艺 为此 类型 。第 四类尾气燃烧 氨吸收工艺是
将 尾 气 中 的硫 或 硫 化 物 通 过 焚 烧 变 成 S 0,然 后 用 氨
第 4期 ( 总第 1 1 6 期)
21 0 2年 8月
煤 化 工
C a h mia n o lC e c lId
N .(o l o11 o T t N .6) 4 a
Au .2 2 g 01
硫 回收尾 气处 理工 艺分 析与选择
杨瑞华
( 辽宁大唐 国际阜新煤制天然气有 限责任公司 , 辽宁
积 小的优 势 。
关 键词
硫 回收 , 尾气处 理 , 氨法工 艺
文章编 号 :0 5 9 9 (0 2 ~ 4 0 1— 3 中图分类号 :Q 2 文献标识码 : 1 0 — 5 8 2 1 ) 0 — 04 0 T 5 A
1 硫 回收 尾 气 处 理 工艺 技 术 进展
自2 0世 纪 3 代改 良 C a s 回收实 现 工业 O年 lu 硫 化 以来 , 经过 了几 十年 的发 展改进 , 已经成熟 、 善 , 完 但 由于 C a s 应 为可逆 反应 ,受 到化 学平 衡 的制 lu 反 约, 即使 采用 三级甚 至 四级 转化 , 硫 回收率最 多达 总 到 9% 8 左右 , 尾气指 标达不 到环保标 准要求 。我 国 目
吸收工 艺是通过加 氢反应 , 尾气 中的 s S 还原 为 将 O、
H , 后 采 用 选 择 性 吸 收溶 剂 ( 液 ) 收 , 收 后 的 然 S 溶 吸 吸
富液 经 再生 , 释放 出含 HS的酸 性气 , 性气 则 返 回 2 酸
加 热炉 提供和 氢源需 外供 , 成操 作复 杂 , 造 操作 费用
超 级 C a s 艺是 由荷 兰 J c b lu 工 o a s公 司 开发 , 自
收 稿 日期 :0 20 — 0 2 1- 6 1
作者 简介 : 杨瑞 华( 9 2 ) 男 , 南兰考 , 17一 , 河 工程师 ,9 4年毕业 于郑 州工学 院化工 工艺专 业 , 19 长期 从事煤 化 工气体净 化生 产管 理工作 ,- a :08 a g u h a 13 CI E m i 2 0 y n r iu @6 . Ol l I 。
为此类型 , 并且具有不 同的实 施方案 。
的新 装置最 高允 许排放 s 量浓 度 ≤9 0m / a同 0质 6 gm , 时对硫化 物排放总量也 作了规 定 , 这就 要求装置硫 回
收率 只有 高于 9 . % 才能 达到此规定要求 。 95 , 为此 , 尾 气处理工艺 的开发和实施 势在必行并 日趋重 要 。
9 .% 9 8 以上 , 特点是利用装 置 自身热源 , 为反应器 其 作
SO C T工艺 为荷兰壳 牌公 司技 术 , 17 自 9 3年投 入
工业化应 用 以来 ,迄 今为止 已有近 2 0 S O 0 套 C T工艺
装置投产 , 量居所有尾气处 理工艺装 置之首 。该工 数 艺成熟 、 运转 可靠 、 操作 弹性大 、 干扰 能力 强 , 抗 总硫
回收率达 到 9 . % 排 放指标 能满足 环保标 准 。但 该 98 , 工艺装置投资 高 , 尤其是加氢 反应器所需 热源 由在线
液( 液) 铵 吸收 , 生化学反应 , 发 变成硫酸铵 。 该工艺 总
对 19 9 7年 1月 1日前建 成 的 旧装 置 最 高允 许 排 放
S2 0 质量浓度 ≤120m / 。 0 g m,对 19 年 1 1日后 建 97 月
硫 回收率 在 9 . % 9 8 以上 。近几年 国内开 发的氨法工艺
增加, 并且 占地 面积较大 。
22 超 级 C as工 艺 . lu
克 劳 斯 系 统 循 环 处 理 。 该 工艺 的硫 回 收率 可 达 到
9.% 9 8 以上 。 目前 国 内运用 较多 此类 工艺 有 SO C T工 艺 、A 工 艺 、S 工 艺 。第二 类低温 C a s 瑞华 : 回收尾气处 理工艺分析与 选择 硫
一1 5—
18 9 8年投入 工业 化应 用 以来 , 迄今 为 止 , 已有 近 10 0 套装 置投产或在建 中 。 该工艺 的特 点是 : H /0 要 对 2 S2 S
气 加 氢 还 原 吸 收类 工 艺 ,装 置 总 硫 回收 率 可 达 到
摘 要
阜新 130 ) 200
简述 了硫 回收尾 气处理 工艺 的发 展概况 和技术进展 , 介绍 了国内应用较 多 的几 种尾 气处理 工艺 :
SO C T工艺 、 级 C a s工艺 、A 超 lu P R工艺 、 S 艺和氨 法工艺 ; S R工 并对 氨法工艺 的 3种方案进 行 了详细对 比分 析 ; 通 过对 比可 知 , 有锅炉 烟气氨法脱 硫装置 作依托 的前提下 , 法工艺 的方 案三具有 投资省 、 作费 用低 、 在 氨 操 占地 面